THORLABS DDSM50 Series User manual

HA0335T
DDSM50
Direct Drive Translation Stage
User Guide
Original Instructions

Page 0 ETN014545-D02
DDSM50 Direct Drive Translation Stage
Contents
Chaper 1 Overview ..................................................................................................... 1
1.1 Introduction ........................................................................................ 1
Chaper 2 Safety .......................................................................................................... 2
2.1 Safety Information ............................................................................. 2
2.2 General Warnings .............................................................................. 3
Chaper 3 Installation .................................................................................................. 4
3.1 Unpacking ........................................................................................... 4
3.2 Mounting ............................................................................................. 4
3.2.1 Vertical Mounting .................................................................................... 4
3.2.2 General ................................................................................................... 4
3.2.3 Mounting the Stage to the Work Surface ................................................ 5
3.2.4 Mounting In Multi-Axis Configurations .................................................... 6
3.3 Electrical Connections ...................................................................... 7
Chaper 4 Operation .................................................................................................... 8
4.1 General ............................................................................................... 8
4.2 Using the Kinesis software ............................................................... 9
4.3 Using the APT Software .................................................................. 12
4.4 Position Error Messages. ................................................................ 14
4.5 Transportation .................................................................................. 15
Chaper 5 Maintenance and Parts List ..................................................................... 16
5.1 Maintenance ..................................................................................... 16
5.2 Parts List ........................................................................................... 16
Chaper 6 Specification ............................................................................................. 17
6.1 Stage Specification .......................................................................... 17
6.2 Motor Specification .......................................................................... 18
Chaper 7 Regulatory ................................................................................................ 19
7.1 Declarations Of Conformity ............................................................ 19
7.1.1 For Customers in Europe ...................................................................... 19
7.1.2 For Customers In The USA ................................................................... 19
7.2 CE Certification ................................................................................ 20
Chaper 8 Thorlabs Worldwide Contacts ................................................................ 21

Rev D Apr 2019 Page 1
Chapter 1 Overview
Chapter 1 Overview
1.1 Introduction
The Thorlabs’ DDSM50 low-profile, direct-drive stage provides 50 mm of travel with
500 nm resolution and a maximum speed of 500 mm/s. The stage is ideal for
applications that require high speeds and high positioning accuracy, including
automated alignment, surface inspection, mapping, and probing.
The stage has a compact low-profile design [145 x 52 x 35 mm (5.71” x 2.05” x 1.38”)]
with integrated, brushless linear motors eliminates the external housings that create
mechanical clash points and impede access to the moving platform. The direct-drive
technology removes the need for a lead screw, eliminating backlash. A precision-
grooved linear bearing provides superior rigidity and linearity with excellent on-axis
accuracy. This backlash-free operation coupled with high-resolution, closed-loop
optical feedback ensures a minimal bidirectional repeatability of 1.5 µm. Along with
the Thorlabs KBD101 controller and the Thorlabs APT software interface, it forms a
truely plug and play system.
The DDSM50 stage has been designed for easy XY configuration when used with the
DDSMP1 XY adapter plate. Two KBD101 controllers are then required to control two
stages in the XY configuration.
Characterized by high-speed translation and high-positional accuracy, the DDSM50
stage is well-suited for surface mapping and characterization applications where
there is a need to move a camera or probe at constant velocity while simultaneously
capturing data.
Fig. 1.1 Typical XY Configuration

Page 2 ETN014545-D02
DDSM50 Direct Drive Translation Stage
Chapter 2 Safety
2.1 Safety Information
For the continuing safety of the operators of this equipment, and the protection of the
equipment itself, the operator should take note of the Warnings, Cautions and Notes
throughout this handbook and, where visible, on the product itself.
The following safety symbols may be used throughout the handbook and on the
equipment itself.
Warning: Risk of Electrical Shock
Given when there is a risk of injury from electrical shock.
Warning
Given when there is a risk of injury to users.
Caution
Given when there is a risk of damage to the product.
Note
Clarification of an instruction or additional information.

Rev D Apr 2019 Page 3
Chapter 2 Safety
2.2 General Warnings
Warning
If this equipment is used in a manner not specified by the manufacturer, the
protection provided by the equipment may be impaired. In particular, excessive
moisture may impair operation.
Spillage of fluid, such as sample solutions, should be avoided. If spillage does
occur, clean up immediately using absorbant tissue. Do not allow spilled fluid to
enter the internal mechanism.
When bolting the stage to the work surface, high tightening torque of the
attachment bolts can result in an increased resistive force on the moving
platform. This in turn can lead to degraded performance and may require the
PID parameters to be adjusted. As a general guide, 70 N.cm is a recommended
nominal torque when tightening the attachment bolts.
The equipment is for indoor use only.
When running custom move sequences, or under fault conditions, the stage
may move unexpectedly. Operators should take care when working inside the
moving envelope of the stage.

Page 4
DDSM50 Direct Drive Translation Stage
Chapter 3 Installation
3.1 Unpacking
3.2 Mounting
3.2.1 Vertical Mounting
3.2.2 General
Note
During handling or shipping, the moving platform must be constrained to avoid
damage to the bearings.
Retain the packing in which the unit was shipped, for use in future transportation.
Caution
Once removed from its packaging, the stage can be easily damaged by
mishandling. The unit should only be handled by its base, not by any
attachments to the moving platform.
Caution
The stage is not suitable for mounting in a vertical (Z-axis) configuration.
Caution
The straightness of motion of the stage could be affected if the mounting
surface is not flat. Care should be taken when bolting the stage to the
worksurface, to ensure that the base plate does not warp. Shims should be
fitted as necessary - see Section 3.2. for more details.
When bolting the stage to the work surface, high tightening torque of the
attachment bolts can result in an increased resistive force on the moving
platform. This in turn can lead to degraded performance and may require the
PID parameters to be adjusted.
As a general guide, 70 N.cm is a recommended nominal torque when tightening
the attatchment bolts.
High drag forces can adversely affect phase initialization, homing, positioning
accuracy and general reliability. Take care to minimize drag caused by
attachments to the moving platform (cables, tubing, electrical wiring),
especially when the stage is changing direction.
When mounting the stage close to other equipment, ensure that the travel of the
moving platform is not obstructed. If equipment mounted on the moving
platform is driven against a solid object, damage to the internal mechanism
could occur. The range of travel is 100 mm (3.94“).

Rev D Apr 2019 Page 5
Chapter 3 Installation
3.2.3 Mounting the Stage to the Work Surface
The DDSM50 stage is mounted to the working surface by two M6 x 25mm (1/4-20 x 1”)
screws. The mounting holes are accessed from the top of the stage - see Fig. 3.1.
Fig. 3.1 Mounting
Caution
The performance of the stage could be affected if the mounting surface is not
flat. Care should be taken when bolting the stage to the worksurface, to ensure
that the base plate does not warp, which could cause stiffness to be
experienced in the bearing rails. Shims should be fitted as necessary.
After mounting the stage to the work surface, if any increased resistance is
experienced when moving the top platform, the likely cause is over tightening/
torquing of the mounting bolts. As a general guide, 70 N.cm is a recommended
nominal torque when tightening the attatchment bolts.
Please contact tech support for more information.

Page 6 ETN014545-D02
DDSM50 Direct Drive Translation Stage
3.2.4 Mounting In Multi-Axis Configurations
For dual-axis applications, two DDSM50 stages can be bolted together in an XY
configuration by using the DDSMP1 attachment plate.
Fig. 3.2 Typical XY Configuration
Regarding Fig. 3.2 above:
1) Using the four 8-32 UNC (M4) bolts supplied, fit the DDSMP1 plate to the lower
stage.
2) Using the two M3 bolts supplied, fit the upper stage to the adapter plate.
Caution
During item (1), use the bolts supplied. If these are not available, do not use
bolts longer than 3/32” (5 mm) as longer bolts could damage the internal
mechanism.
Caution
During step (2), use the bolts supplied. If these are not available, do not use
bolts longer than 8 mm as longer bolts could damage the internal mechanism.
Caution
When stages are mounted in an XY configuration, the accelerations stated in
Table 4.2 may require adjustment - see Section 4.1.
1
2

Rev D Apr 2019 Page 7
Chapter 3 Installation
3.3 Electrical Connections
The stage must be driven by a Thorlabs KBD101 controller. Connect the motor flying
lead to the MOTOR connector on the controller rear panel.
Fig. 3.3 Electrical connections
Pin out information for the connector on the motor lead is detailed below..
Fig. 3.4 MOTOR flying lead pin identification
Pin Description Pin Description
1 Quadrature A- 9 GND
2 Quadrature A+ 10 Motor Phase C (Black)
3 Quadrature B+ 11 Motor Phase A (Red)
4 Quadrature B- 12 Motor Phase B (White)
5 Encoder Index I- 13 +5 V
6 Encoder Index I+ 14 GND
7 Negative Limit 15 Stage ID
8 Positive Limit
87654321
1514131211109

Page 8 ETN014545-D02
DDSM50 Direct Drive Translation Stage
Chapter 4 Operation
4.1 General
The stage is connected to the controller via a flying lead, terminated in a D-type
connector.
For a complete tutorial on using the stage, see the manual supplied with the KBD101
controller. Basic steps in controlling the stage are as follows:
1) Make electrical connections as detailed in Section 3.3.
2) Manually position the moving platform to be around its central position.
3) Power up the KBD101 controller and wait until the Channel Enable LED starts
flashing (~3s).
4) Press and hold the ENABLE button for ~3 seconds to initiate a home sequence.
Alternatively, run the APTUser utility and click the ‘Home’ button on each GUI
panel. When homing is complete, the Channel Enable LED stops flashing.
Caution
The DDSM50 stage is designed to be driven by the Thorlabs KBD101
Brushless DC Motor K-Cube. For full compatibility, the controller should have
Firmware version 1.0.1 or higher. The Firmware version is displayed in
brackets, in the top right hand corner of the GUI panel for the Motor ActiveX
control.
Caution
The motor controller must be switched OFF before the stages are plugged in or
unplugged. Failure to switch the controller off may result in damage to either the
controller, the stage, or both.
Caution
3-phase brushless DC motors are commutated electronically, i.e. the controller
drives the coils with a precisely controlled waveform, that depends on the
position of the motor coil housing. On power up, the position of the coil housing
is not known. The controller establishes this by energising the coils and
measuring the resulting movement. This is why on power up, the stage (motor)
may make a slight buzzing noise and move slightly. Phase initialisation can only
take place if the motor can move unobstructed during this time. Before
powering up the KBD101 controller at item (2), ensure that the stage movement
is unobstructed.

Rev D Apr 2019 Page 9
Chapter 4 Operation
5) The stage can now be moved using the Pot, GUI panel, or by setting commands
to move each axis by relative and absolute amounts – see the handbook supplied
with the KBD101 controller, and the helpfile supplied with the APT server for more
information
6) The stage is shipped already loaded with default parameter settings, which should
give satisfactory performance in most cases. However, depending on the
application and load requirements, it may be necessary to adjust the PID loop
parameter settings to fine tune the response - see the following pages for more
information.
4.2 Using the Kinesis software
1) If it is not already running, start the Kinesis software - Start/Programs/Thorlabs/
Kinesis/Kinesis
The software reads in the stage and controller information on boot up and the GUI
panel shown below is displayed..
Fig. 4.1 Kinesis GUI screen
Note
The need for homing comes from the fact that on power up the motor (stage) is at a
random position, so the value of the position counter is meaningless. Homing
involves moving the motor to a known reference marker and resetting the position
counter to the associated absolute value. This reference marker can be one of the
limit switches or can be provided by some other signal. The DDSM series stages use
an electronic reference marker and therefore the limit switches are not used for
reference.

Page 10
DDSM50 Direct Drive Translation Stage
2) Click the Settings button on the GUI to display the Settings panel, then select the
‘Advanced’ tab.
Fig. 4.2 Advanced Control Loop Settings
3) Create a Custom Settings Group (see the Kinesis helpfile for more information)
and then adjust the acceleration and PID settings to fine tune the control loop for
your application - see Table 4.1 and Table 4.2 for more information.
Note
The MOTOR DRIVE connectors for each channel/axis contain an EEPROM, which
stores the factory default settings for the set up parameters. When the stage is
connected, these settings are loaded into the controller on start up, and are tuned
for loads up to the 250 g (0.55 lb) maximum, at speeds up to 500 mm/s.
However, depending on the load being driven and the speed/duty cycle of the
particular application, it may be necessary to further optimize the Position PID loop
settings. See Table 4.1 for suggested PID settings at a given load.
If problems are encountered (e.g. stability of the closed loop position control, lost
motion or incomplete moves) the position loop PID parameters should be adjusted
to tune the stage for the given application. Normally, only minor adjustment of the
Proportional, Integral and Derivative parameters should be necessary, and some
trial and error will be required before the ideal settings for a specific application are
achieved. In cases where further adjustment of the control loop parameters is
required, the following guidelines are provided in order to assist in the tuning
process.

Rev D Apr 2019 Page 11
Chapter 4 Operation
4) After the parameter changes have been performed, click the ‘Persist Settings to
Hardware’ box, then click ‘OK’. This will ensure that the same parameter settings
will be loaded next time the unit is powered up - even in the absence of a PC.
Depending on the shape of the mass and the accelerations and velocities used the
values quoted above may require adjustment to provide optimum performance.
The values quoted above are the maximum values recommended to avoid over
current errors. These values are a guideline only, and depending on the shape of the
mass and the velocities used, these values may require further adjustment,
particularly if the stages are mounted in an XY configuration.
Table 4.1 DDSM100 Position Loop Parameter Adjustment Guidelines
Load Range(g) Derivative Derivative Time Output Gain
0 to 250 4500 5 4000
250 to 500 5160 5 4660
500 to 750 5830 6 5330
750 to 900 6500 7 6000
Table 4.2 DDSM100 Load vs Maximum acceleration recommendations
Load (g) Approximate Max Acceleration (mm/s²)
0 5000
125 2400
250 1550
500 925
750 650
900 500
Note
Position PID Settings Summary
Stage overshoots the intended position - reduce the integral term, and increase the
derivative and proportional terms.
Stage fails to attain final position - increase the integral and proportional terms.
Motion is unstable - reduce the proportional and integral terms, increase the
derivative term.
Stage sounds noisy - reduce the derivative term.
Please see the handbook supplied with the controller, for more information on
changing these settings

Page 12 ETN014545-D02
DDSM50 Direct Drive Translation Stage
4.3 Using the APT Software
1) If it is not already running, start the APTUser utility - Start/Programs/Thorlabs/APT
User/APT User
The APT server reads in the stage and controller information on boot up and the
GUI panel shown below is displayed.
.
Fig. 4.3 APTUser GUI screen
Note
The MOTOR DRIVE connectors for each channel/axis contain an EEPROM, which
stores the factory default settings for the set up parameters. When the stage is
connected, these settings are loaded into the controller on start up, and are tuned
for loads up to 250 g (0.55 lb) maximum, at speeds up to 500 mm/s.
However, depending on the load being driven and the speed/duty cycle of the
particular application, it may be necessary to further optimize the Position PID loop
settings. See Table 4.1 for suggested PID settings at a given load.
If problems are encountered (e.g. stability of the closed loop position control, lost
motion or incomplete moves) the position loop PID parameters should be adjusted
to tune the stage for the given application. Normally, only minor adjustment of the
Proportional, Integral and Derivative parameters should be necessary, and some
trial and error will be required before the ideal settings for a specific application are
achieved. In cases where further adjustment of the control loop parameters is
required, the following guidelines are provided in order to assist in the tuning
process.

Rev D Apr 2019 Page 13
Chapter 4 Operation
2) Click the Settings button on the GUI to display the Settings panel, then select the
‘Advanced’ tab.
Fig. 4.4 Advanced Control Loop Settings
3) Adjust the acceleration and PID settings to fine tune the control loop for your
application see Table 4.1 and Table 4.2 for more information.
4) After the parameter changes have been performed, click the ‘Persist Settings to
Hardware’ box, then click ‘OK’. This will ensure that the same parameter settings
will be loaded next time the unit is powered up - even in the absence of a PC.
Depending on the shape of the mass and the accelerations and velocities used the
values quoted above may require adjustment to provide optimum performance.
Table 4.1 DDSM50 Position Loop Parameter Adjustment Guidelines
Load Range(g) Derivative Derivative Time Output Gain
0 to 250 4500 5 4000
250 to 500 5160 5 4660
500 to 750 5830 6 5330
750 to 900 6500 7 6000

Page 14 ETN014545-D02
DDSM50 Direct Drive Translation Stage
The values quoted above are the maximum values recommended to avoid over
current errors. These values are a guideline only, and depending on the shape of the
mass and the velocities used, these values may require further adjustment,
particularly if the stages are mounted in an XY configuration.
Table 4.2 DDSM50 Load vs Maximum acceleration recommendations
Load (g) Approximate Max Acceleration (mm/s²)
0 5000
125 2400
250 1550
500 925
750 650
900 500
Note
Position PID Settings Summary
Stage overshoots the intended position - reduce the integral term, and increase the
derivative and proportional terms.
Stage fails to attain final position - increase the integral and proportional terms.
Motion is unstable - reduce the proportional and integral terms, increase the
derivative term.
Stage sounds noisy - reduce the derivative term.
Please see the handbook supplied with the controller, for more information on
changing these settings

Rev D Apr 2019 Page 15
Chapter 4 Operation
4.4 Position Error Messages.
4.5 Transportation
Caution
The maximum velocity at which the encoder can operate is approximately 3000
mm/sec. Above this speed, encoder pulses may be lost and, as a result, the
position readout becomes incorrect. This renders normal operation impossible
because phase commutation of the motor is also based on the encoder reading.
When the stage is controlled by the KBD101 controller, the maximum velocity
is limited to safe values. However, if the output is disabled (with the controller
connected and monitoring the position) and the stage is moved manually at
high speeds, it is possible to exceed this limit. If the KBD101 controller is
subsequently used again to move the stage, the incorrect encoder reading will
cause incorrect operation, often resulting in sudden uncontrolled moves. It is
therefore important not to move the stage excessively quickly when it is moved
manually.
The KBD101 controller has fault monitoring to detect the loss of encoder
pulses. If this fault occurs, an error message will be generated and the
controller must be powered down and re-started so that correct phasing and
commutation can be established.
Caution
When packing the unit for shipping, use the original packing. If this is not
available, use a strong box and surround the unit with at least 100 mm of shock
absorbent material.
In particular, the moving platform must be constrained to avoid damage during
shipping.

Page 16
DDSM50 Direct Drive Translation Stage
Chapter 5 Maintenance and Parts List
5.1 Maintenance
Over time, the glass encoder scale can become dirty. To prevent errors due to lost
encoder counts, the encoder scale should be cleaned periodically with isopropyl
alcohol and a cotton bud as follows:
1) Move the top platform to one end of its travel.
2) Moisten a cotton bud with Isopropyl alcohol.
3) Insert the cotton bud into the slot as shown above, and apply gentle pressure
downwards and sideways to push the bud against the encoder scale.
4) Move the cotton bud up and down the slot, along the exposed length of the
encoder.
5) Move the top platform to the opposite end of its carriage, and repeat the procedure
to clean the portion of the encoder now exposed.
5.2 Parts List
Product Name Part Number
KBD101 Brushless DC Motor Controller K-Cube
DDSMP1 XY Adapter Plate

Rev D Apr 2019 Page 17
Chapter 6 Specification
Chapter 6 Specification
6.1 Stage Specification
Parameter Value
Travel Range 50 mm (1.97")
Velocity (Max) a500 mm/s
Acceleration (Max) 5000 mm/s2
Bidirectional Repeatability ±1.5 µm
Backlash N/A (No Leadscrew)
Min Incremental Movement 500 nm
Horizontal Load Capacity 0.9 kg (1.98 lbs)
Absolute On-Axis Accuracy ±5.0 µm
Straightness/Flatness ±5.0 µm
Pitch ±175 µrad
Yaw ±175 µrad
Continuous Motor Force b0.8 N
Peak Motor Force (5 sec) c2.0 N
Bearing Type High Rigidity Recirculating Precision Linear Bearing
Limit Switches Magnetic Sensor at Each End of Stage
Operating Temperature Range 5 to 40 °C (41 to 104 °F)
Motor Type Brushless DC Linear Motor
Cable Length 1 m (3.3’)
Dimensions 145 mm x 57 mm x 35 mm (5.71” x 2.25” x 1.38”)
Weight (with cables) 600 g (1.3 lbs)
Note
The default tuning parameters can be changed to optimise settling times for a
specific load - see Section 4.1.
a The stage is designed for translation at high speeds, up to 500 mm/sec. When
travelling at extremely low speeds (i.e. around 70 nm/sec) the discrete steps in the
movement may be noticable.
b The continuous force the motor can deliver without exceeding temperature limits.
c The absolute maximum force the motor can deliver before going out of position
error.

Page 18
DDSM50 Direct Drive Translation Stage
6.2 Motor Specification
Notes
c. The continuous current the motor can draw without exceeding temperature limits.
d. The absolute maximum current without exceeding temperature limits.
Caution
The maximum speed and acceleration values quoted can be safely achieved with the
maximum load and a high duty cycle. However in this case, some heating of the stage
may occur and dimensional stability of the stage may be affected. This could result in
less than optimal repeatability and accuracy. For cases were repeatability and accuracy
are critical it is recommended that the stage temperature is allowed to reach a steady
state before measurements are taken.
Alternatively the load, acceleration and duty cycle should be reduced from the maximum
values. Some trial and error in setting these values may be necessary before the ideal
settings are attained.
Parameter Value
Magnetic Pitch 30 mm
Maximum Continuous Current c1.2 A
Maximum Current (5 sec) d2 A
Motor Resistance at 20° C 1.3 Phase to Phase
Inductance 45 µH Phase to Phase
Force Constant 1 N/A
Caution
At more than the continuous current, the motor coil fields get saturated and
increasing current further does not necessarily give more force.
Table of contents
Other THORLABS Servo Drive manuals
Popular Servo Drive manuals by other brands
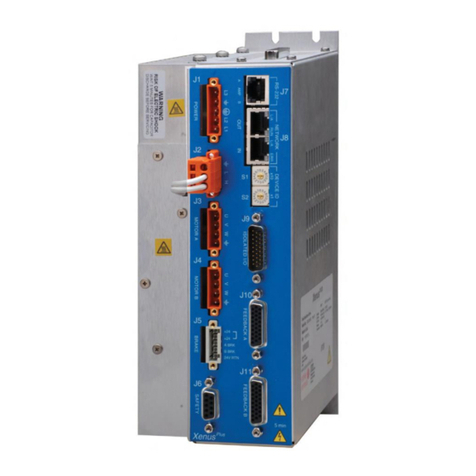
Copley Controls
Copley Controls Xenus Plus Series user guide

SEW-Eurodrive
SEW-Eurodrive DFS Series operating instructions
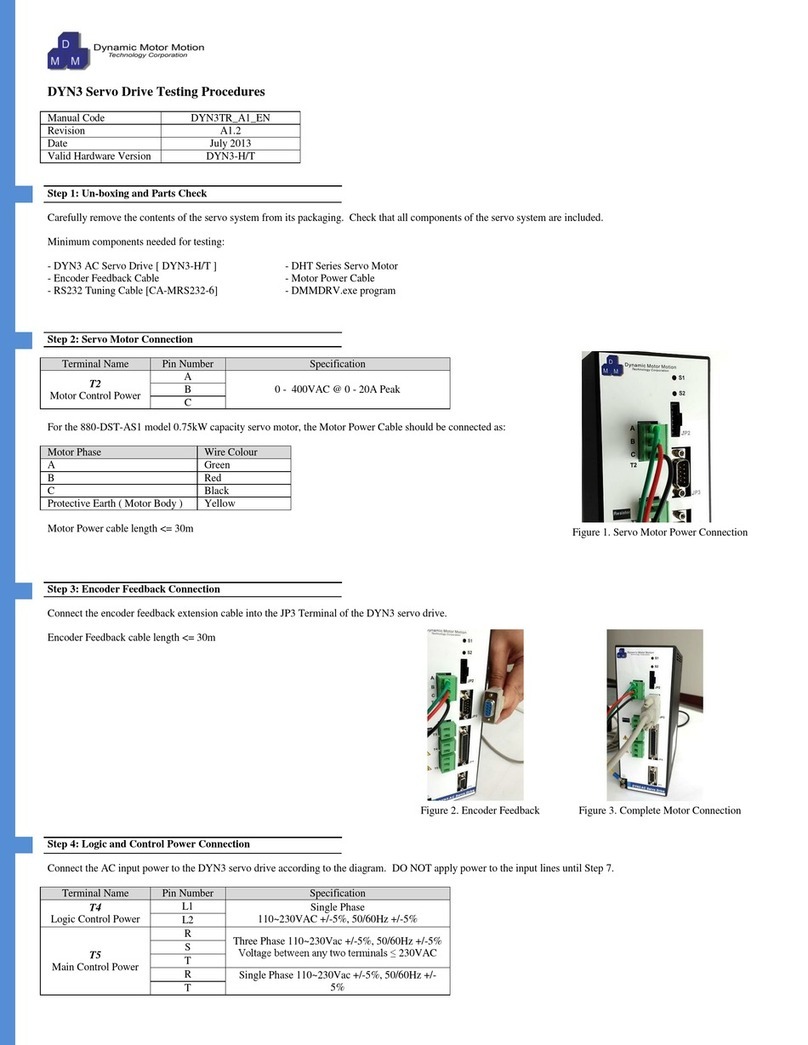
DMM
DMM DYN3 Installation, Commissioning, and Testing Procedures
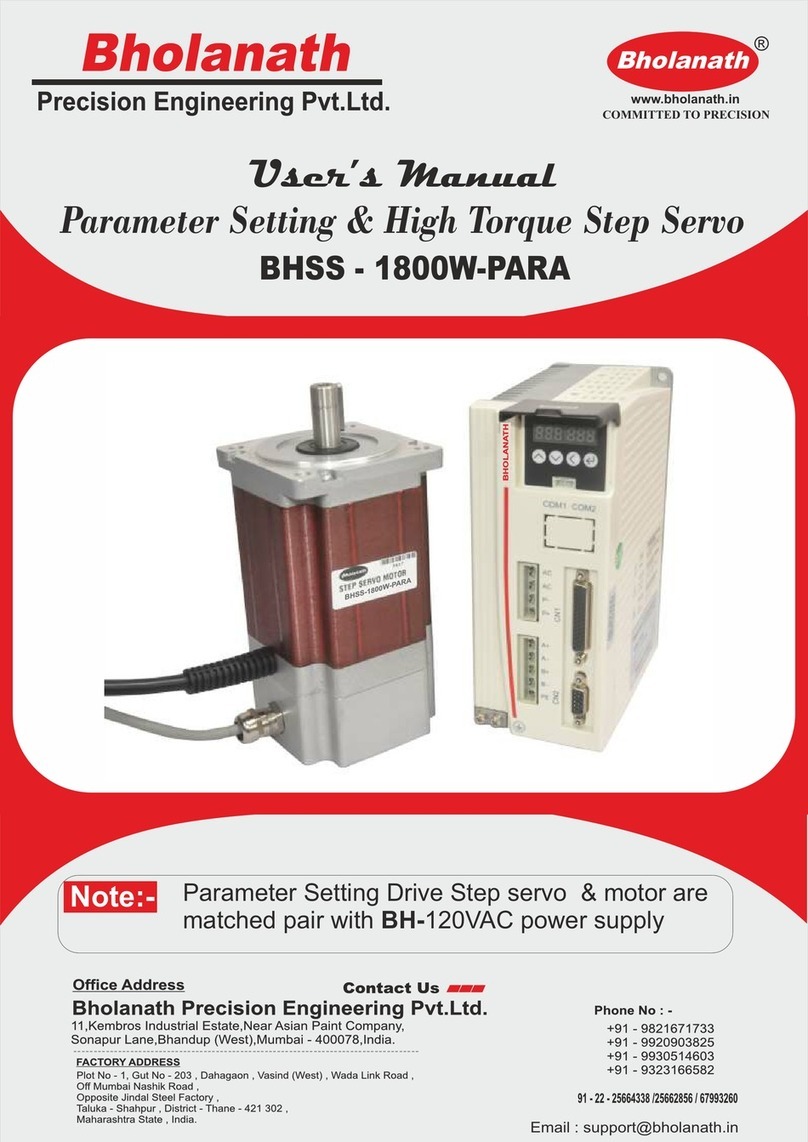
Bholanath
Bholanath BHSS-1800W-PARA user manual
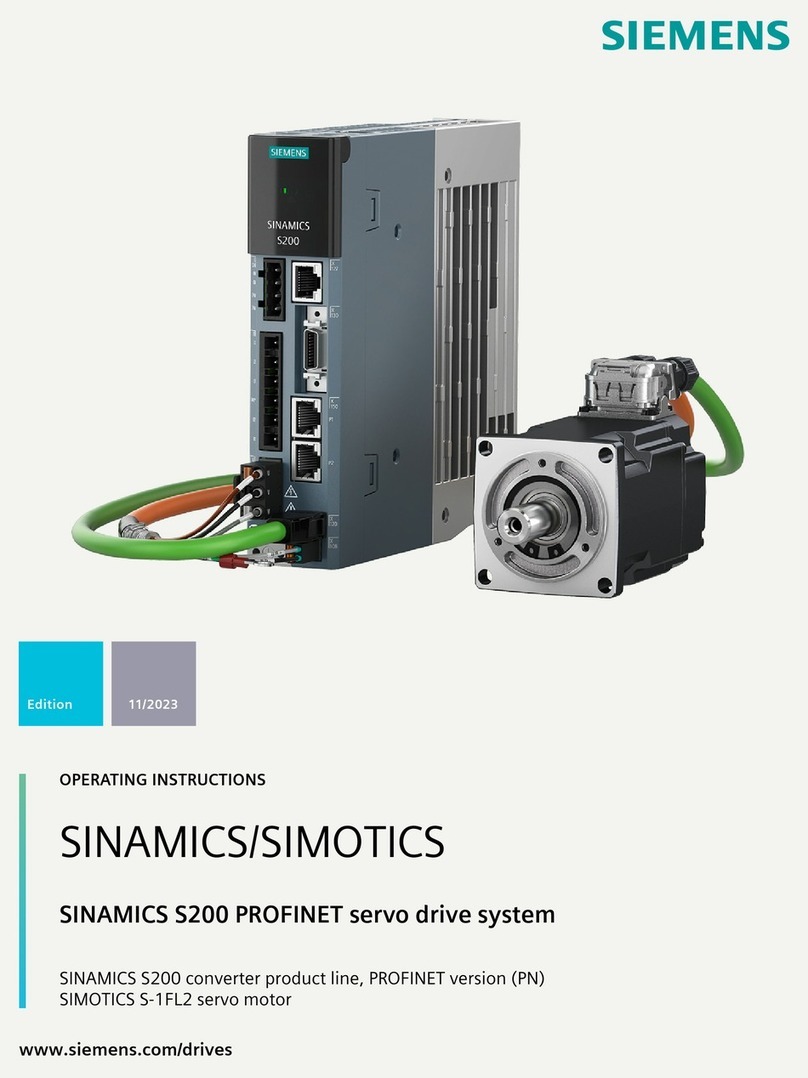
Siemens
Siemens SINAMICS SIMOTICS S200 PROFINET operating instructions
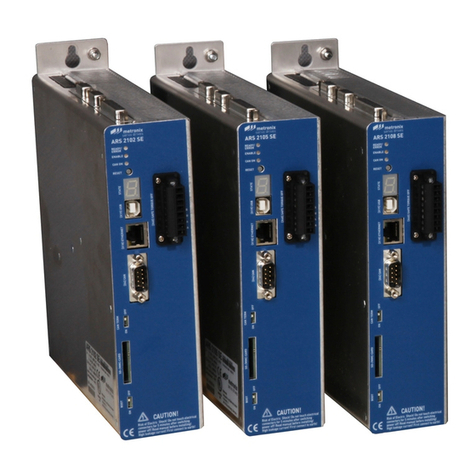
Metronix
Metronix ARS 2100 SE manual