Sysmac Omron NJ Series User manual

Machine Automation Controller NJ/NX-series
EtherNet/IPTM
Connection Guide
ifm electronic gmbh
IO-Link master
(AL1920)
P702-E1-01

About Intellectual Property Rights and Trademarks
Microsoft product screen shots reprinted with permission from Microsoft Corporation.
Windows is a registered trademark of Microsoft Corporation in the USA and other countries.
ODVA and EtherNet/IPTM are trademarks of ODVA.
EtherCAT®is registered trademark and patented technology, licensed by Beckhoff Automation
GmbH, Germany.
Sysmac is a trademark or registered trademark of OMRON Corporation in Japan and other
countries for OMRON factory automation products.
Company names and product names in this guide are the trademarks or registered trademarks
of their respective companies.

Table of Contents
1. Related Manuals........................................................................................ 1
2. Terms and Definitions............................................................................... 2
3. Precautions................................................................................................ 3
4. Overview .................................................................................................... 4
5. Applicable Devices and Device Configuration ....................................... 5
5.1. Applicable Devices ................................................................................ 5
5.2. Device Configuration ............................................................................. 6
6. EtherNet/IP Settings.................................................................................. 8
6.1. Parameters............................................................................................ 8
6.2. Global Variables.................................................................................. 10
6.3. Tag Sets.............................................................................................. 15
7. EtherNet/IP Connection Procedure........................................................ 16
7.1. Work Flow............................................................................................ 16
7.2. ifm electronic IO-Link Master Setup..................................................... 18
7.3. Controller Setup................................................................................... 24
7.4. Network Settings ................................................................................. 35
7.5. EtherNet/IP Communication Status Check.......................................... 52
8. Initialization Method................................................................................ 60
8.1. Initializing a Controller ......................................................................... 60
8.2. Initializing an ifm electronic IO-Link Master ......................................... 60
9. Revision History...................................................................................... 61

1
.
Related Manuals
1
1. Related Manuals
To ensure system safety, make sure to always read and follow the information provided in all
Safety Precautions and Precautions for Safe Use in the manuals for each device which is
used in the system.
The table below lists the manuals provided by ifm electronic gmbh (hereinafter referred to as
"ifm electronic") and OMRON Corporation (hereinafter referred to as "OMRON"), which
pertain to this guide.
Manufacturer
Cat. No.
Model
Manual name
OMRON W500 NJ501-□□□□
NJ301-□□□□
NJ101-□□□□
NJ-series CPU Unit
Hardware User's Manual
OMRON W535 NX701-□□□□ NX-series
CPU Unit
Hardware User's Manual
OMRON W593 NX102-□□□□ NX-series
NX102 CPU Unit
Hardware User's Manual
OMRON W578 NX1P2-□□□□□□
NX1P2-□□□□□□1 NX-series
NX1P2 CPU Unit
Hardware User's Manual
OMRON W501 NX701-□□□□
NX102-□□□□
NX1P2-□□□□□□
NX1P2-□□□□□□1
NJ501-□□□□
NJ301-□□□□
NJ101-□□□□
NJ/NX-series
CPU Unit
Software User's Manual
OMRON W506 NJ/NX-series
CPU Unit Built-in EtherNet/IPTM Port
User's Manual
OMRON W504 SYSMAC-SE2□□□ Sysmac Studio Version 1
Operation Manual
OMRON 0969584-7 W4S1-05□
W4S1-03B Switching Hub
W4S1-series
Users Manual
ifm electronic
7391165
AL1920
AL1920 Operating Instructions
IO-Link Master with EtherNet/IP interface
DataLine 8 Ports IP20
Hilscher
Gmbh DOC05040
2OI07EN
-Operating Instruction Manual
Ethernet Device Configuration
Address Setting for Ethernet capable
Hilscher Devices

2
.
Terms and Definitions
2
2. Terms and Definitions
The terms and definitions used in this guide are given below.
Term
Explanation and Definition
node A node refers to a relay point, a junction point or an end point on an
EtherNet/IP network made up of devices having an EtherNet/IP port. A
device with one EtherNet/IP port is recognized as one node and two
EtherNet/IP ports as two nodes on an EtherNet/IP network.
tag A tag is a unit that is used to exchange data with tag data links.
Data is exchanged between the local network variables and remote
network variables specified in the tags or between specified I/O memory
areas.
tag set When a connection is established, from 1 to 8 tags (including Controller
status) is configured as a tag set. . Each tag set represents the data that
is linked for a tag data link connection. Tag data links are therefore
created through a connection between one tag set and another tag set.
A tag set name has to be set for each tag set.
tag data links The standard EtherNet/IP implicit communications are called tag data
links. Tag data links enable cyclic tag data exchanges on an EtherNet/IP
network between Controllers or between Controllers and other devices.
connection A connection is used to exchange data as a unit within which data
concurrency is maintained.
connection type There are two kinds of connection types for tag data links.
One is a multi-cast connection, and the other is a unicast (point-to-point)
connection. The multi-cast connection sends an output tag set in one
packet to more than one node. The unicast connection separately sends
one output tag set to each node. Therefore, the multi-cast connection
can reduce the communications load if one output tag set is sent to more
than one node.
originator and target To perform tag data links, it is necessary to open connections between
nodes that perform tag data links. The node that requests the connection
is called the originator, and the node that receives the request is called
the target.
tag data link
parameters The information that is set to perform tag data links, including tags, tag
sets and connections, is called tag data link parameters.
EDS file
A file that describes information unique to a device such as the number
of I/O points for an EtherNet/IP device.

3
.
Precautions
3
3. Precautions
(1) Understand the specifications of devices which are used in the system. Allow some
margin for ratings and performance. Provide safety measures, such as installing a safety
circuit, in order to ensure safety and minimize the risk of abnormal occurrence.
(2) To ensure system safety, make sure to always read and follow the information provided
in all Safety Precautions and Precautions for Safe Use in the manuals for each device
which is used in the system.
(3) The user is encouraged to confirm the standards and regulations that the system must
conform to.
(4) It is prohibited to copy, to reproduce, and to distribute a part or the whole of this guide
without the permission of OMRON Corporation.
(5) The information contained in this guide is current as of August 2018. It is subject to
change for improvement without notice.
The following notations are used in this guide.
Indicates a potentially hazardous situation which, if not avoided,
may result in minor or moderate injury, or may result in serious
injury or death. Additionally there may be significant property
damage.
Indicates a potentially hazardous situation which, if not avoided,
may result in minor or moderate injury or property damage.
Precautions for Correct Use
Precautions on what to do and what not to do to ensure proper operation and performance.
Additional Information
Additional information to read as required.
This information is provided to increase understanding or make operation easier.
Symbol
The filled circle symbol indicates operations that you must do.
The specific operation is shown in the circle and explained in the text.
This example shows a general precaution for something that you must do.

4
.
Overview
4
4. Overview
This guide describes procedures for connecting an ifm electronic IO-Link Master AL1920
(hereinafter referred to as the "IO-Link Master") to an OMRON NJ/NX-series Machine
Automation Controller (hereinafter referred to as the "Controller") via EtherNet/IP and for
checking their communication status.
Refer to Section 6. EtherNet/IP Settings and Section 7. EtherNet/IP Connection Procedure to
understand setting methods and key points to operate EtherNet/IP tag data links.
The OMRON E2E-series IO-Link Proximity Sensor (hereinafter referred to as the "Proximity
Sensor") is used in this guide in order to check that data can be received by the Controller
from the IO-Link Master.

5
.
Applicable Devices and Device Configuration
5
5. Applicable Devices and Device Configuration
5.1. Applicable Devices
The applicable devices are as follows:
Manufacturer Name Model
OMRON
NJ/NX-series CPU Unit
NX701-□□□□
NX102-□□□□
NX1P2-□□□□□□
NX1P2-□□□□□□1
NJ501-□□□□
NJ301-□□□□
NJ101-□□□□
ifm electronic IO-Link Master AL1920
Precautions for Correct Use
In this guide, the devices with models and versions listed in
5.2. Device Configuration
are
used as examples of applicable devices to describe the procedures for connecting the
devices and checking their connection.
You cannot use devices with versions lower than the versions listed in 5.2.
To use the above devices with models not listed in 5.2. or versions higher than those listed in
5.2., check the differences in the specifications by referring to the manuals before operating
the devices.
Additional Information
This guide describes the procedures for establishing the network connection.
It does not provide information on operation, installation, wiring method, device functionality,
or device operation, which is not related to the connection procedures.
Refer to the manuals or contact the device manufacturer.

5
.
Applicable Devices and Device Configuration
6
5.2. Device Configuration
The hardware components to reproduce the connection procedures in this guide are as
follows:
Manufacturer
Name
Model
Version
OMRON
NJ-series CPU Unit
(Built-in EtherNet/IP port)
NJ501-1500
Ver.1.18
OMRON
Power Supply Unit
NJ-PA3001
OMRON
Switching hub
W4S1-05C
Ver.1.0
-
Switching hub power supply
(24 VDC)
-
OMRON
Sysmac Studio
SYSMAC-SE2□□□
Ver.1.22
OMRON
Network Configurator
(Included in Sysmac Studio)
Ver.3.62
OMRON
Proximity Sensor
E2E-X3B4-M1TJ-IL3
Ver.1.00
Hilscher
Gmbh
Ethernet Device Configuration
-
Ver.1.900.4.3
711
-
Personal computer
(OS: Windows 7)
-
-
USB cable
(USB 2.0 type B connector)
-
-
LAN cable (STP (shielded,
twisted-pair) cable of Ethernet
category 5 or higher)
-
ifm electronic
IO-Link Master
AL1920
Ver.1.01
ifm electronic
Connecting cable with socket
(Connector: 1 x M12, straight)
EVC196
ifm electronic
Icon file
EIP_CL_8P_IP20.ico
ifm electronic
EDS file
ifm_IOL_Master_AL1920.eds
Rev.1.3
-
IO-Link Master power supply
(24 VDC)
-
Precautions for Correct Use
Prepare the EDS file listed above beforehand.
To obtain the EDS file, contact ifm electronic gmbh.
Precautions for Correct Use
Store the icon file and EDS file in the same folder.
USB cable
LAN cable
NJ501-1500
(Built-in EtherNet/IP port)
W4S1-05C
AL1920
Personal computer
(Sysmac Studio, Network
Configurator and
Ethernet Device
Configuration installed,
OS: Windows 7)
IO-Link Master power supply
Switching hub power supply
LAN cable
E2E-X3B4-M1TJ-IL3
EVC196

5
.
Applicable Devices and Device Configuration
7
Precautions for Correct Use
Update Sysmac Studio and Network Configurator to the versions specified in this Clause 5.2.
or to higher versions. If you use a version higher than the one specified, the procedures and
related screenshots described in Section 7. and the subsequent sections may not be
applicable. In that case, use the equivalent procedures described in this guide by referring to
the Sysmac Studio Version 1 Operation Manual (Cat. No. W504) and Network Configurator
Online Help.
Additional Information
For power supply specifications of the switching hub, refer to the Switching Hub W4S1-series
Users Manual (Cat. No. 0969584-7).
Additional Information
For power supply specifications of the IO-Link Master, refer to the AL1920 Operating
Instructions IO-Link Master with EtherNet/IP interface DataLine 8 Ports IP20 (7391165).
Additional Information
The system configuration in this guide uses USB for the connection between the personal
computer and the Controller. For information on how to install the USB driver, refer to A-1
Driver Installation for Direct USB Cable Connection of the Sysmac Studio Version 1
Operation Manual (Cat. No. W504).
For NX1P2 Controllers, there is no need to install the USB driver because they do not have
USB ports.
Additional Information
The NX1P2 Controller, if used, must be connected to your personal computer with an
Ethernet cable. For information on how to connect the cable, refer to 6-2 Going Online with a
Controller of the Sysmac Studio Version 1 Operation Manual (Cat. No. W504).
Additional Information
In this guide, "Ethernet Device Configuration" by Hilscher Gmbh is used to set the IP address
of the IO-Link Master. "Ethernet Device Configuration" can be downloaded from the following
ifm electronic website.
https://www.ifm.com/jp/ja/downloadarea/IOMasterContent

6
.
EtherNet/IP Settings
8
6. EtherNet/IP Settings
This section describes the parameters, global variables and tag sets that are all defined in this
guide.
6.1. Parameters
The parameters set in this guide are shown below.
6.1.1. Personal Computer Communication Settings
The parameters of the IO-Link Master are set via Ethernet communications with the personal
computer.
The following parameters are required to connect the personal computer and the IO-Link
Master via Ethernet.
Setting item Personal computer IO-Link Master (EtherNet/IP port)
IP address 192.168.1.100 192.168.1.250 (default)
Subnet mask
255.255.255.0
255.255.255.0
6.1.2. EtherNet/IP Communications Settings
The following parameters are required to connect the Controller and the IO-Link Master via
EtherNet/IP.
Setting item Controller (Node 1) IO-Link Master (EtherNet/IP port) (Node 2)
IP address 192.168.250.1 192.168.250.2
Subnet mask 255.255.255.0 255.255.255.0

6
.
EtherNet/IP Settings
9
6.1.3. Parameters of the IO-Link Master
The parameters of the IO-Link Master are described below.
In this guide, an ON/OFF signal is sent under the following setting conditions:
- The Proximity Sensor (2-byte input data) is assigned to Port 1 of the IO-Link Master to
check data received by the Controller from the IO-Link Master.
- The Port 2 of the IO-Link Master is set to Digital Output to check data sent from the
Controller to the IO-Link Master.
The Ports 3 to 8 of the IO-Link Master are not used in this guide.
Setting item Setting value Remarks
0001 Assembly Input Size 206
*1
Input area size 206 bytes
0002 Assembly Output Size 62
*1
Output area size 62 bytes
0028 Communication Profile Keep setting (default) The previous setting is valid.
0029 Port Process Data Size 2 Bytes (In 206 / Out 62) 2-byte length
*2
of the
process input data and
process output data for
Ports 1 to 8
0030 Port Mode (Port 1) IO-Link (Pin 4) (default) Operation as IO-Link
interface
0031 Port Cycle Time (Port 1) As fast as possible (default) The device automatically
sets the fastest possible
cycle time.
0032 Swap (Port 1) 1 (default) Byte swapping for IO-Link
data activated
0033 Validation / Data Storage (Port 1) No check and clear (default) No validation
0036 Fail Safe Mode (Port 1) No Fail Safe (default) No Failsafe
0130 Port Mode (Port 2) Digital Output (Pin 4) Operation as digital output
0230 Port Mode (Port 3) Disabled Not used
0330 Port Mode (Port 4) Disabled Not used
0430 Port Mode (Port 5) Disabled Not used
0530 Port Mode (Port 6) Disabled Not used
0630 Port Mode (Port 7) Disabled Not used
0730 Port Mode (Port 8) Disabled Not used
*1 Set "0001 Assembly Input Size" and "0002 Assembly Output Size" after setting "0029 Port
Process Data Size" (common length of the process input data and process output data for Ports
1 to 8). In "0001 Assembly Input Size" and "0002 Assembly Output Size", enter the same values
(bytes) as those selected for the input assembly "In" and output assembly "Out" of "0029 Port
Process Data Size".
*2 The common length of the process input data and process output data for Ports 1 to 8 can be
selected from 2, 4, 8, 16 or 32 bytes.

6
.
EtherNet/IP Settings
10
6.2. Global Variables
The Controller treats data in tag data links as global variables.
The following tables show the global variables and their related settings.
■Output area (Controller to IO-Link Master)
Name Data type
Network
publish
Data size
(byte)
EIP002_Digitaloutputs_OUT
BYTE[2]
Output
2
EIP002_reserved_OUT
BYTE[2]
Output
2
EIP002_AcycliccommandRequest_OUT
BYTE[42]
Output
42
EIP002_Acyclicoutputdata_OUT
BYTE[16]
Output
16
■Relationship between the global variables and the IO-Link Master cyclic data
Global variable
Content (IO-Link Master cyclic data)
EIP002_Digitaloutputs_OUT[0]
Digital outputs of the IO-Link ports in the DO operating
mode
Ports X01 to X08: pin 4
EIP002_Digitaloutputs_OUT[1]
Reserved
EIP002_reserved_OUT[0] and [1]
Reserved
EIP002_AcycliccommandRequest_OUT[0]
Acyclic command area: Request channel
Port No.(LSB)
EIP002_AcycliccommandRequest_OUT[1]
Port No.(MSB)
EIP002_AcycliccommandRequest_OUT[2]
Index No.(LSB)
EIP002_AcycliccommandRequest_OUT[3]
Index No.(MSB)
EIP002_AcycliccommandRequest_OUT[4]
Sub-index.(LSB)
EIP002_AcycliccommandRequest_OUT[5]
Sub-index.(MSB)
EIP002_AcycliccommandRequest_OUT[6]
Handshake and Command
EIP002_AcycliccommandRequest_OUT[7]
Result
EIP002_AcycliccommandRequest_OUT[8]
Length of the response data (number of bytes)
EIP002_AcycliccommandRequest_OUT[9]
Data (byte 0) of diagnostic data
:
:
EIP002_AcycliccommandRequest_OUT[40]
Data (byte 31) of diagnostic data
EIP002_AcycliccommandRequest_OUT[41]
Reserved
EIP002_Acyclicoutputdata_OUT[0] and [1]
Port X01: Acyclic output data (2 bytes)
EIP002_Acyclicoutputdata_OUT[2] and [3]
Port X02: Acyclic output data (2 bytes)
EIP002_Acyclicoutputdata_OUT[4] and [5]
Port X03: Acyclic output data (2 bytes)
EIP002_Acyclicoutputdata_OUT[6] and [7]
Port X04: Acyclic output data (2 bytes)
EIP002_Acyclicoutputdata_OUT[8] and [9]
Port X05: Acyclic output data (2 bytes)
EIP002_Acyclicoutputdata_OUT[10] and [11]
Port X06: Acyclic output data (2 bytes)
EIP002_Acyclicoutputdata_OUT[12] and [13]
Port X07: Acyclic output data (2 bytes)
EIP002_Acyclicoutputdata_OUT[14] and [15]
Port X08: Acyclic output data (2 bytes)
Mapping: "Ports X01 to X08: pin 4" of "Digital outputs of the IO-Link ports in the DO operating
mode"
Global variable
Bit
7
6
5
4
3
2
1
0
EIP002_Digitaloutputs_OUT[0]
X08
pin 4
X07
pin 4
X06
pin 4
X05
pin 4
X04
pin 4
X03
pin 4
X02
pin 4
X01
pin 4
Mapping: "Handshake and Command" of "Acyclic command area Request channel"
Global variable
bit
7
6
5
4
3
2
1
0
EIP002_AcycliccommandRequest_OUT[6]
Hand
shake
Command

6
.
EtherNet/IP Settings
11
■Input area (IO-Link Master to Controller)
Name Data type
Network
publish
Data size
(byte)
EIP002_DigitalInputs_IN
BYTE[2]
Input
2
EIP002_Status_IN
BYTE[2]
Input
2
EIP002_AcycliccommandRespons_IN
BYTE[42]
Input
42
EIP002_PQI_PortInformation_IN
BYTE[144]
Input
144
EIP002_Cyclicinputdata_IN
BYTE[16]
Input
16
■Relationship between the global variables and the IO-Link Master cyclic data
Global variable
Content (IO-Link Master cyclic data)
EIP002_DigitalInputs_IN[0]
Digital inputs of the IO-Link ports in the DI operating
mode
Ports X01 to X08: pin 4
EIP002_DigitalInputs_IN[1]
Ports X01 to X08: pin 2
EIP002_Status_IN[0]
Status information
Ports X01 to X08: Short / OL
EIP002_Status_IN[1]
AUX PWR and Sensor PWR
EIP002_AcycliccommandRespons_IN[0]
Acyclic command area: Response channel
Port No.(LSB)
EIP002_AcycliccommandRespons_IN[1]
Port No.(MSB)
EIP002_AcycliccommandRespons_IN[2]
Index No.(LSB)
EIP002_AcycliccommandRespons_IN[3]
Index No.(MSB)
EIP002_AcycliccommandRespons_IN[4]
Sub-index(LSB)
EIP002_AcycliccommandRespons_IN[5]
Sub-index(MSB)
EIP002_AcycliccommandRespons_IN[6]
Handshake and Command
EIP002_AcycliccommandRespons_IN[7]
Result
EIP002_AcycliccommandRespons_IN[8]
Length of the response data (number of bytes)
EIP002_AcycliccommandRespons_IN[9]
Data (byte 0) of diagnostic data
:
:
EIP002_AcycliccommandRespons_IN[40]
Data (byte 31) of diagnostic data
EIP002_AcycliccommandRespons_IN[41]
Reserved
EIP002_PQI_PortInformation_IN[0]
Port X01: PQI
PQI
EIP002_PQI_PortInformation_IN[1]
Reserved
EIP002_PQI_PortInformation_IN[2]
Port X01: Diagnostic vendor ID
VID(LSB)
EIP002_PQI_PortInformation_IN[3]
VID(MSB)
EIP002_PQI_PortInformation_IN[4]
DID(LSB)
EIP002_PQI_PortInformation_IN[5]
DID
EIP002_PQI_PortInformation_IN[6]
DID(MSB)
EIP002_PQI_PortInformation_IN[7]
Reserved
EIP002_PQI_PortInformation_IN[8]
Event Mode, Event Type, Event Source and Event
Instance
EIP002_PQI_PortInformation_IN[9]
Event Code 1
EIP002_PQI_PortInformation_IN[10]
Event Code 2
EIP002_PQI_PortInformation_IN[11]
Event Mode, Event Type, Event Source and Event
Instance
EIP002_PQI_PortInformation_IN[12]
Event Code 1
EIP002_PQI_PortInformation_IN[13]
Event Code 2
EIP002_PQI_PortInformation_IN[14]
Event Mode, Event Type, Event Source and Event
Instance
EIP002_PQI_PortInformation_IN[15]
Event Code 1
EIP002_PQI_PortInformation_IN[16]
Event Code 2
EIP002_PQI_PortInformation_IN[17]
Reserved
EIP002_PQI_PortInformation_IN[18] and [19]
Port X02: PQI
Same assignment as "Port X01: PQI"
EIP002_PQI_PortInformation_IN[20] to [35]
Port X02: Diagnostic vendor ID
Same assignment as "Port X01: Diagnostic vendor ID"
EIP002_PQI_PortInformation_IN[36] and [37]
Port X03: PQI
Same assignment as "Port X01: PQI"
EIP002_PQI_PortInformation_IN[38] to [53]
Port X03: Diagnostic vendor ID
Same assignment as "Port X01: Diagnostic vendor ID"

6
.
EtherNet/IP Settings
12
Global variable
Content (IO-Link Master cyclic data)
EIP002_PQI_PortInformation_IN[54] and [55]
Port X04: PQI
Same assignment as "Port X01: PQI"
EIP002_PQI_PortInformation_IN[56] to [71]
Port X04: Diagnostic vendor ID
Same assignment as "Port X01: Diagnostic vendor ID"
EIP002_PQI_PortInformation_IN[72] and [73]
Port X05: PQI
Same assignment as "Port X01: PQI"
EIP002_PQI_PortInformation_IN[74] to [89]
Port X05: Diagnostic vendor ID
Same assignment as "Port X01: Diagnostic vendor ID"
EIP002_PQI_PortInformation_IN[90] and [91]
Port X06: PQI
Same assignment as "Port X01: PQI"
EIP002_PQI_PortInformation_IN[92] to [107]
Port X06: Diagnostic vendor ID
Same assignment as "Port X01: Diagnostic vendor ID"
EIP002_PQI_PortInformation_IN[108] and [109]
Port X07: PQI
Same assignment as "Port X01: PQI"
EIP002_PQI_PortInformation_IN[110] to [125]
Port X07: Diagnostic vendor ID
Same assignment as "Port X01: Diagnostic vendor ID"
EIP002_PQI_PortInformation_IN[126] and [127]
Port X08: PQI
Same assignment as "Port X01: PQI"
EIP002_PQI_PortInformation_IN[128] to [143]
Port X08: Diagnostic vendor ID
Same assignment as "Port X01: Diagnostic vendor ID"
EIP002_Cyclicinputdata_IN[0]
Port X01: Cyclic input data
Stores the process data (Byte1 (PD1)) of the
Proximity Sensor.
EIP002_Cyclicinputdata_IN[1]
Port X01: Cyclic input data
Stores the process data (Byte0 (PD0)) of the
Proximity Sensor.
EIP002_Cyclicinputdata_IN[2] and [3]
Port X02: Cyclic input data (2 bytes)
EIP002_Cyclicinputdata_IN[4] and [5]
Port X03: Cyclic input data (2 bytes)
EIP002_Cyclicinputdata_IN[6] and [7]
Port X04: Cyclic input data (2 bytes)
EIP002_Cyclicinputdata_IN[8] and [9]
Port X05: Cyclic input data (2 bytes)
EIP002_Cyclicinputdata_IN[10] and [11]
Port X06: Cyclic input data (2 bytes)
EIP002_Cyclicinputdata_IN[12] and [13]
Port X07: Cyclic input data (2 bytes)
Mapping: "Digital inputs of the IO-Link ports in the DI operating mode"
Global variable
Bit
7
6
5
4
3
2
1
0
EIP002_DigitalInputs_IN[0]
X08
pin 4
X07
pin 4
X06
pin 4
X05
pin 4
X04
pin 4
X03
pin 4
X02
pin 4
X01
pin 4
EIP002_DigitalInputs_IN[1]
X08
pin2
X07
pin2
X06
pin2
X05
pin2
X04
pin2
X03
pin2
X02
pin2
X01
pin2
Mapping "Status information"
Global variable
Bit
7
6
5
4
3
2
1
0
EIP002_Status_IN[0]
X08
Short /
OL
X07
Short /
OL
X06
Short
/ OL
X05
Short
/ OL
X04
Short /
OL
X03
Short
/ OL
X02
Short /
OL
X01
Short
/ OL
EIP002_Status_IN[1]
Reserved
Sensor
PWR
AUX
PWR
Mapping: "PQI" of "Port X01: PQI"
Global
variable
Bit
7
6
5
4
3
2
1
0
EIP002_PQI_Po
rtInformation_
IN[0]
Reserved
Wrong
PD Output
Length
Wrong
PD Input
Length
Wrong
Cycle
Time
Wrong
VID
/DID
Invalid
Data
Bit
Device
Conn
IOL
Mode

6
.
EtherNet/IP Settings
13
Mapping: "Event Mode, Event Type, Event Source and Event Instance" of "Port X01:
Diagnostic vendor ID"
Global variable
Bit
7
6
5
4
3
2
1
0
EIP002_PQI_PortInformation_IN[8]
Event
Mode Event Type Event
Source Event Instance
EIP002_PQI_PortInformation_IN[11]
EIP002_PQI_PortInformation_IN[14]
Additional Information
For more details on the cyclic data mappings of the IO-Link Master, refer to 13.2.2 Cyclic data
of the AL1322 Operating Instructions IO-Link Master with EtherNet/IP interface DataLine 8
Ports IP65/IP66/IP67 (7391158).
Additional Information
With Sysmac Studio, two methods can be used to specify an array for a data type.
After specifying, (1) is converted to (2), and the data type is always displayed as (2).
(1) BOOL[16] / (2) ARRAY[0..15] OF BOOL
In this guide, the data type is simplified by displaying BOOL[16].
(The example above means a BOOL data type with sixteen array elements.)

6
.
EtherNet/IP Settings
14
■Process data of the Proximity Sensor
(Data to be stored in the global variable EIP002_Cyclicinputdata_IN[0] listed in the table on
the previous page)
(Data to be stored in the global variable EIP002_Cyclicinputdata_IN[1] listed in the table on
the previous page)

6
.
EtherNet/IP Settings
15
6.3. Tag Sets
The tag sets to perform tag data links are shown below.
The data in the tag sets are assigned in ascending order of the following OUT No. and IN No.
■Output area (Controller to IO-Link Master)
Tag set name Data size (byte)
EIP002_OUT 62
OUT No. Tag name (global variable) Data size (byte)
1 EIP002_Digitaloutputs_OUT 2
2
EIP002_reserved_OUT
2
3 EIP002_AcycliccommandRequest_OUT 42
4 EIP002_Acyclicoutputdata_OUT 16
■Input area (IO-Link Master to Controller)
Tag set name Data size (byte)
EIP002_IN 206
IN No. Tag name (global variable) Data size (byte)
1 EIP002_DigitalInputs_IN 2
2 EIP002_Status_IN 2
3 EIP002_AcycliccommandRespons_IN 42
4 EIP002_PQI_PortInformation_IN 144
5 EIP002_Cyclicinputdata_IN 16

7
.
EtherNet/IP Connection Procedure
16
7. EtherNet/IP Connection Procedure
This section describes the procedures for connecting the IO-Link Master and the Controller
via EtherNet/IP. The procedures for setting up the Controller and the IO-Link Master in this
guide are based on the factory default settings.
For the initialization, refer to Section 8. Initialization Method.
7.1. Work Flow
Take the following steps to connect the IO-Link Master and the Controller via EtherNet/IP and
to perform tag data links.
7.2. ifm electronic IO-Link Master
Setup
Set up the ifm electronic IO-Link Master.
↓
7.2.1. Hardware Settings
Connect the cables to the IO-Link Master.
↓
7.2.2. Parameter Settings Set the IP address of the IO-Link Master.
↓
7.3. Controller Setup
Set up the Controller.
↓
7.3.1. IP Address Settings
Start Sysmac Studio and set the IP address of the
Controller.
↓
7.3.2. Setting Global Variables
Set global variables to use for tag data links, and
create and export a CSV file in order to use the
variables as tags with Network Configurator.
↓
7.3.3. Transferring the Project Data
Go online with Sysmac Studio and transfer the
project data to the Controller.
↓
7.4. Network Settings
Set EtherNet/IP tag data links.
↓
7.4.1. Starting Network Configurator
and Installing the EDS File Start Network Configurator and install the EDS file.
↓
7.4.2. Uploading the Network
Configuration Go online with Network Configurator and upload the
network configuration.
↓
7.4.3. Tag Registration
Import the created CSV file for use with Network
Configurator, and register tags and tag sets.
↓
7.4.4. Setting Connections
Set connections to associate the tag sets of the
target device with the tag sets of the originator
device.

7
.
EtherNet/IP Connection Procedure
17
↓
7.4.5. Transferring the Tag Data Link
Parameters Transfer the tag data link parameters to the
Controller.
↓
7.5. EtherNet/IP Communication
Status Check
Confirm that the EtherNet/IP tag data links are
performed normally.
↓
7.5.1. Checking the Connection
Status Check the EtherNet/IP connection status.
↓
7.5.2. Checking Sent and Received
Data Check that correct data is sent and received.
Other manuals for Omron NJ Series
2
This manual suits for next models
1
Table of contents
Other Sysmac Network Hardware manuals
Popular Network Hardware manuals by other brands
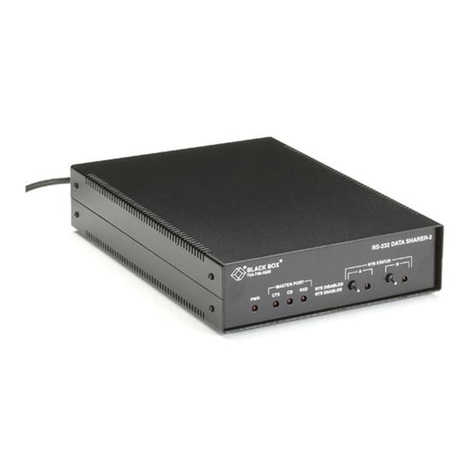
Black Box
Black Box TL553A-R3 manual
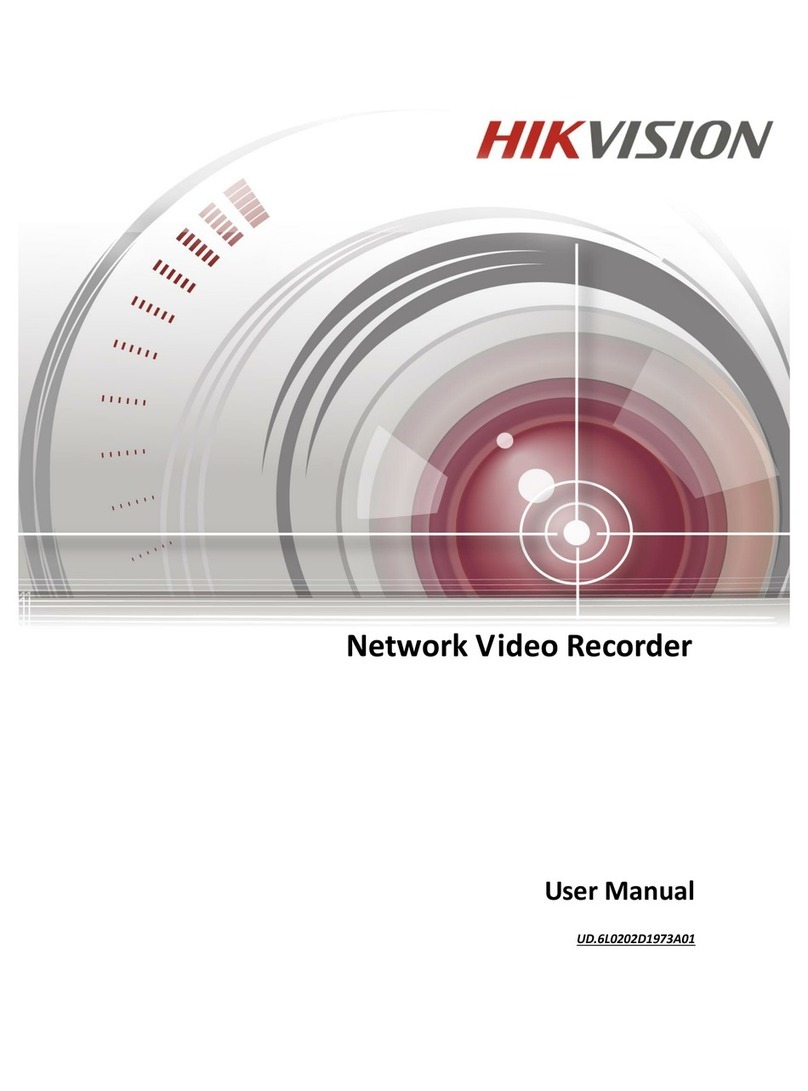
HIK VISION
HIK VISION DS-96128NI-H16DS-96128NI-H16/HDS-96128NI-H16/IDS-96128NI-H16/H/IDS-96128NI-F16DS-96128NI-F16/HDS-96128NI-F16/IDS-96128NI user manual
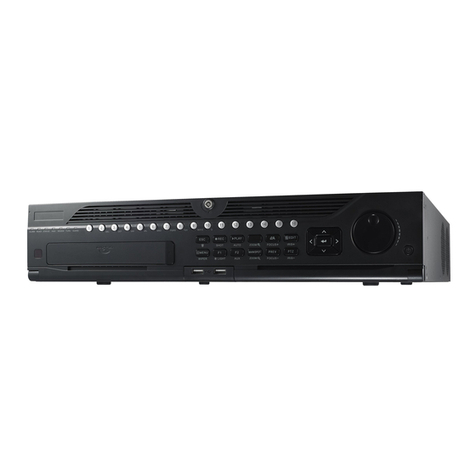
HIK VISION
HIK VISION DS-8600 Series user manual
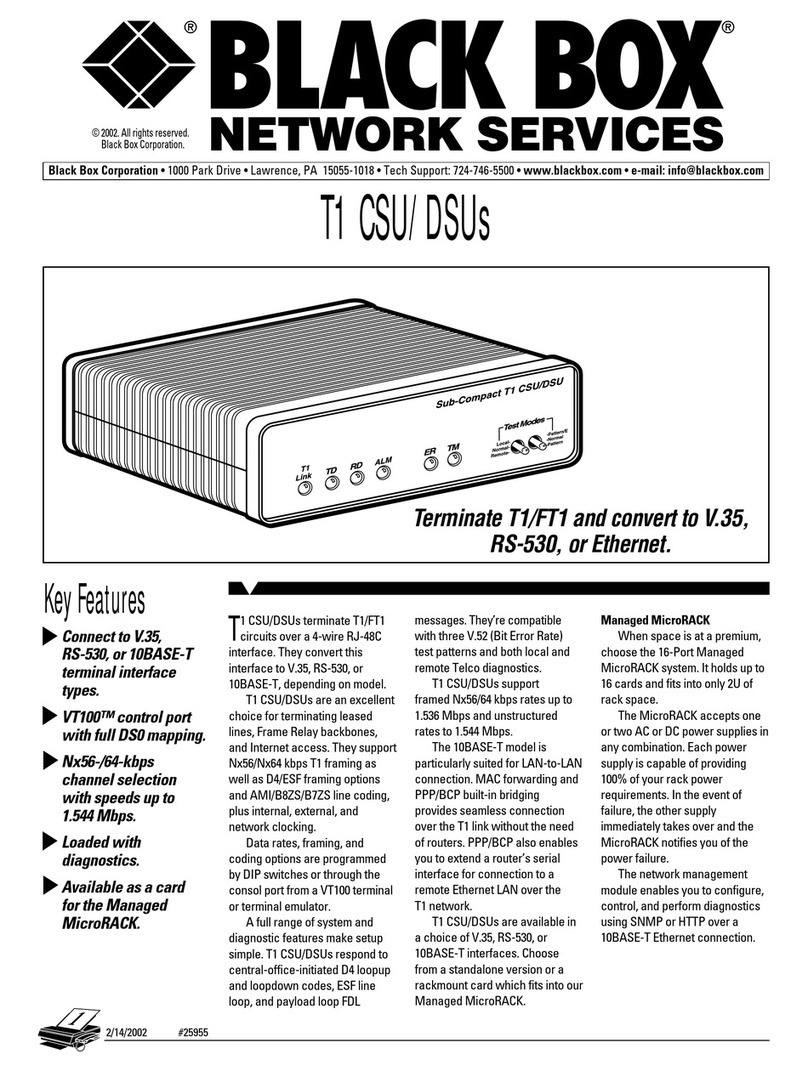
Black Box
Black Box MT910A Specifications
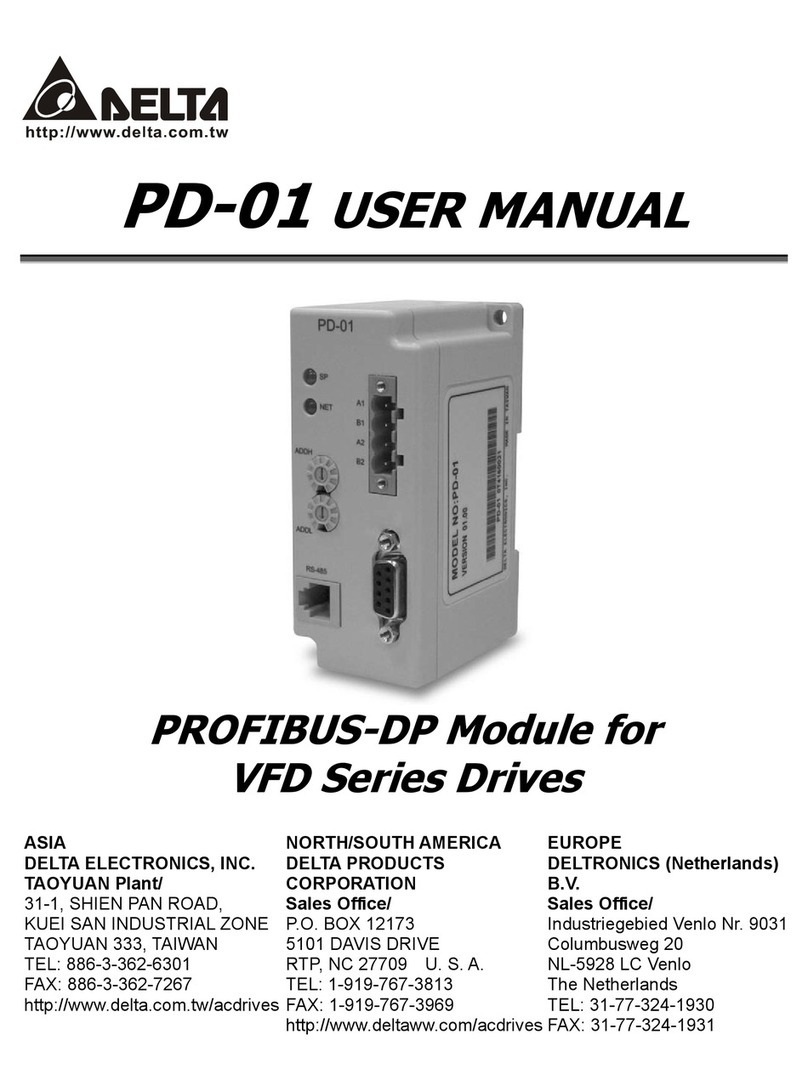
Delta
Delta PD-01 user manual
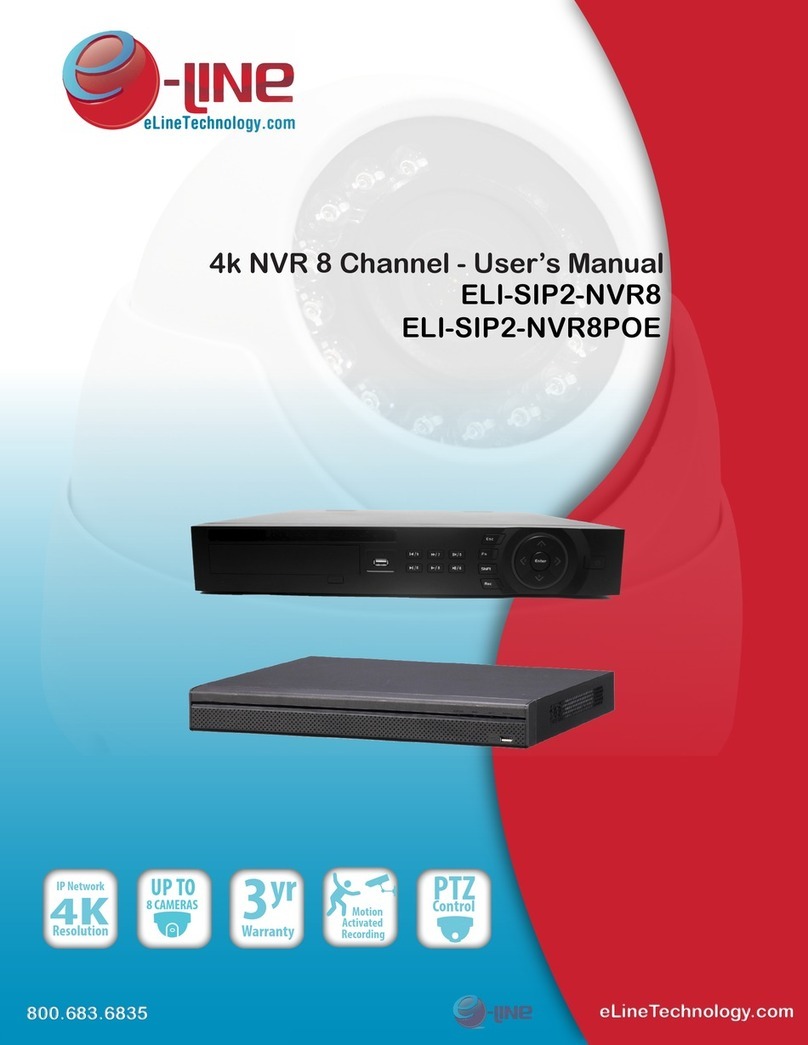
E-line
E-line ELI-SIP2-NVR8 user manual