Temptek BG-N4 Series User manual

BG-N4 Series
Glycol Chiller
TEMPTEK, INC.
525 East Stop 18 Road Greenwood, IN 46142
317-887-6352 fax: 317-881-1277
Service Department fax: 317-885-8683
www.Temptek.com
E-mail: [email protected]
Model:
Serial Number :
Stop: If running at a uid temperature below 48°F or if the chiller will be installed in a climate
where the ambient temperature may get below 40°F you must use a water and glycol mixture
at a ratio that protects the uid from freezing to approximately 25°F below the lowest expected
set point temperature or the lowest expected ambient temperature whichever is lower. See
Section 8.1 and 8.2 of this manual before operating your chiller. Regular testing of your glycol
protection is critical.
I.O.M. #187 updated 02/18/2021
INSTRUCTION MANUAL • INSTALLATION • OPERATION • MAINTENANCE


INSTRUCTION MANUAL
With MG INSTRUMENT
& SCROLL COMPRESSORS
AIR-COOLED MODELS
COVERING
INSTALLATION
OPERATION
MAINTENANCE
BG-N4 Series
Glycol Chiller
TEMPTEK, INC. 525 East Stop 18 Road Greenwood, IN 46142
Phone: 317-887-6352 Fax: 317-881-1277 Service Department fax: 317-885-8683

BG-N4 Glycol Chiller
Page: 4
TEMPTEK, INC.
525 East Stop 18 Road Greenwood, Indiana 46142
317-887-6352 Fax: 317-881-1277
Email: [email protected]
TABLE OF CONTENTS
1.0 GENERAL 7
1.1 Introduction 8
1.2 Safety 8
1.3 Receiving instructions 9
1.4 Efciency 9
1.5 Clean air act 10
1.6 Water Treatment 10
2.0 INSTALLATION 13
2.1 General 14
2.2 Unit location 14
2.3 To and From process connections 15
2.4 Air-cooled condenser 16
2.5 Electrical connection 17
3.0 OPERATIONS 21
3.1 General 22
3.2 Start up/operations procedure 22
3.3 MG Instrument Operations 27
3.4 Instrument : Main Menu 30
3.5 Instrument : Setpoints Menu 30
3.6 Instrument : Utilities Menu 32
3.7 Instrument : Network Menu 33
3.8 Instrument : Flow Menu (optional) 34
3.9 Instrument : Options Menu 35
3.10 Instrument : Machine Menu 36
3.11 Shut Down Procedure 39
4.0 TROUBLESHOOTING 41
4.1 Unit Will Not Start 42
4.2 Compressor Hums But Will Not Start 42
4.3 Shuts Off On High Pressure 42
4.4 Shuts Off On Low Pressure 43
4.5 Compressor Shuts Off On Internal Overload 43
4.6 Low Or No Process Pressure Or Water Flow 43
4.7 Cooling Capacity Inadequate 44
4.8 Sensor 44
4.9 Coolant Pump 44
4.10 Chiller Controller 44
5.0 MAINTENANCE 47
5.1 Warranty service procedure 48
5.2 Periodic preventative maintenance 48
5.3 Special maintenance 48
5.4 Pump seal service 50
5.5 Checking the refrigerant charge 52
5.6 Proper cleaning procedure for brazed plate evaporators 52

BG-N4 Glycol Chiller
Page: 5
TEMPTEK, INC.
525 East Stop 18 Road Greenwood, Indiana 46142
317-887-6352 Fax: 317-881-1277
Email: [email protected]
6.0 COMPONENTS 55
6.1 Water system 56
6.2 Refrigeration system 56
6.3 Options 57
7.0 RELATED DRAWINGS 59
7.1 Typical Mechanical Schematic 60
8.0 APPENDIX 61
8.1 Operationsbelow48°Fuidor38°Fambient 62
8.2 Inhibited propylene glycol 63
8.3 Refrigerant pressure-temperature chart 64
8.4 Chiller capacity and derate chart 65
8.5 Standard MG Instrument Settings 66
8.6 Probe Calibration : MG Instrument 67
8.7 Status Indicators : MG Instrument 69
8.8 Water Quality 70
8.9 Modbus Registers 72
8.10 Remote&AutoStartFeatureConguration 73

Page: 6
THIS PAGE INTENTIONALLY BLANK

BG-N4 Glycol Chiller
Page: 7
TEMPTEK, INC.
525 East Stop 18 Road Greenwood, Indiana 46142
317-887-6352 Fax: 317-881-1277
Email: [email protected]
1.0 GENERAL
1.1 Introduction
1.2 Safety
1.3 Receiving Instructions
1.4 Efciency
1.5 Clean Air Act
1.6 Water Treatment

BG-N4 Glycol Chiller
Page: 8
TEMPTEK, INC.
525 East Stop 18 Road Greenwood, Indiana 46142
317-887-6352 Fax: 317-881-1277
Email: [email protected]
1.1 INTRODUCTION
A. This manual covers glycol chillers from 1.5 and 10 horsepower of cooling capacity using
theMGmicroprocessorcontrolinstrumentandxeddisplacementscrollcompressors
ordigitalscrollcompressors.Thestandarduidoperatingtemperaturerangeforthis
chiller is 20°F to 60°F for units using R410A refrigerant. Units using other refrigerants
havedifferentstandardoperatingranges.Unitsoperatingbelow48°Fuidrequirethe
use of a water/propylene glycol to prevent freezing. Customized units may have different
operating ranges. Consult the factory if you have questions about the operating range of
your chiller.
B. The intent of this manual is to serve as a guide in the installation, operation and
maintenance of your chiller. Improper installation can lead to equipment damage
and poor performance. Failure to follow the installation, operation and maintenance
instructions may result in damage to the unit that is not covered under the limited
warranty. This manual is for standard products. The information contained in this manual
is intended to be general in nature. The information is typical only and may not represent
the actual unit purchased.
C. Chemical refrigerants are used in this unit. The refrigerant is sealed and tested in a
pressurized system however a system failure will release it. Refrigerant gas can cause
toxicfumesifexposedtore.Installthisunitinawell-ventilatedareaawayfromopen
ames.Failuretofollowtheseinstructionsmayresultinahazardouscondition.Recover
refrigerant to relieve pressure before opening the system. See nameplate for refrigerant
type. Do not use non-approved refrigerants or refrigerant substitutes.
D. Customers should implement a refrigerant management program to document the type
and quantity of refrigerant in each chiller. All refrigeration service technicians performing
workonthischillermustbelicensedandcertied.
E. WhencallingforassistancefromtheManufacturer’sServiceDepartment,itisimportant
to know the model and serial number of the particular unit. The model number includes
criticalunitinformationwhichishelpfulwhentroubleshootingoperatingdifculties.The
serial number allows the service team to locate manufacturing and testing records which
can have additional information relating to a particular unit.
1.2 SAFETY
A. It is important to become thoroughly familiar with this manual and the operating
characteristics of the unit.
B. Itistheowner’sresponsibilitytoassureproperoperatortraining,installation,operation,
and maintenance of the unit.
C. Observe all warning and safety placards applied to the chiller. Failure to observe all
warnings can result in serious injury or death to the operator and severe mechanical
damage to the unit.
D. Observe all safety precautions during installation, startup and service of this equipment
duetothepresenceofhighvoltageandrefrigerantcharge.Onlyqualiedpersonnel
should install, startup and service this equipment.

BG-N4 Glycol Chiller
Page: 9
TEMPTEK, INC.
525 East Stop 18 Road Greenwood, Indiana 46142
317-887-6352 Fax: 317-881-1277
Email: [email protected]
Samples of Warning Labels applied to typical
chillers.
1. Alerts users to the danger of high voltage.
2. Alerts user to the danger of the rotating con-
denser fans on air condensed units.
3. Alerts user to the danger of belt drive systems
on unit with blowers.
4. This symbol is seen on all chillers to alert user
to the danger of the refrigeration system under
pressure. System should only be serviced by a
licensed technician.
E. When working on this equipment, observe precautions in literature and on tags, stickers
and labels located on the equipment. Wear work gloves and safety glasses.
WARNING: This equipment contains hazardous voltages that can cause severe injury or death.
Disconnect and lock out incoming power before installing or servicing the equipment.
WARNING: This equipment contains refrigerant under pressure. Accidental release of refrigerant
under pressure can cause personal injury and or property damage. Exercise care while working
on or around this equipment.
WARNING: Vent all refrigerant relief valves in accordance to ANSI/ASHRAE Standard 15,
Safety Code for Mechanical Refrigeration. This equipment should be located within a well-
ventilated area. Inhalation of refrigerant can be hazardous to your health and the accumulation
of refrigerant within an enclosed space can displace oxygen and cause suffocation
WARNING
J5318-BF 1
WARNING
2
3
4

BG-N4 Glycol Chiller
Page: 10
TEMPTEK, INC.
525 East Stop 18 Road Greenwood, Indiana 46142
317-887-6352 Fax: 317-881-1277
Email: [email protected]
1.3 RECEIVING INSTRUCTIONS
A. Chillers are shipped skid mounted and wrapped in plastic prior to shipment. Check the
overall condition of the equipment prior to accepting delivery.
B. Check for visible damage and document any evident damage on the delivery receipt.
Check the refrigerant gauges to be sure the system charge is intact. See the chart
in section 8.4 for proper pressure readings based on the ambient temperature and
refrigerant type used in the chiller. Shipping damage is the responsibility of the carrier.
C. In order to expedite payment for damages, should they occur, follow proper procedures
and keep detailed records. Take photographs of any suspected damage.
1.4 EFFICIENCY
A. Longtermefciencyofoperationislargelydeterminedbypropermaintenanceofthe
mechanical parts of the unit and the water quality. The Manufacturer recommends
lteringtheprocesswatertopreventsolidsfrompluggingcriticalparts.TheManufacturer
highlyrecommendsthattheservicesofaqualiedwatertreatmentspecialistbeobtained
and their recommendations be followed. The Manufacturer accepts no responsibility for
inefcientoperation,ordamagecausedbyforeignmaterialsorfailuretouseadequate
water treatment.
1.5 CLEAN AIR ACT
A. Units manufactured after January 1, 2010 may contain refrigerant HFC-410A, HFC-407C,
HFC-404A or HFC-134A. Most units manufactured prior to January 1, 2010 contain
refrigerant HCFC-22.
B. It is unlawful for any person in the course of maintaining, servicing, repairing, or disposing
of refrigeration equipment to knowingly vent or otherwise dispose of any substance used
as a refrigerant in the manner which permits such substance to enter the atmosphere.
C. Very small releases associated with good faith attempts to recapture, reclaim or
recycle such substance shall not be subject to the prohibition set forth in the preceding
paragraph.
D. Customers should implement a refrigerant management program to document the type
and quantity of refrigerant in each chiller. All refrigeration service technicians performing
workonthischillermustbelicensedandcertied.
E. Vent all refrigerant relief valves in accordance to ANSI/ASHRAE Standard 15.
WARNING: Vent all refrigerant relief valves in accordance to ANSI/ASHRAE Standard 15,
Safety Code for Mechanical Refrigeration. This equipment should be located within a well-
ventilated area. Inhalation of refrigerant can be hazardous to your health and the accumulation
of refrigerant within an enclosed space can displace oxygen and cause suffocation.

BG-N4 Glycol Chiller
Page: 11
TEMPTEK, INC.
525 East Stop 18 Road Greenwood, Indiana 46142
317-887-6352 Fax: 317-881-1277
Email: [email protected]
1.6 WATER TREATMENT
A. The use of untreated or improperly treated water in a portable chiller may result in
scaling, erosion, corrosion, algae or slime.
B. Itisrecommendedthattheservicesofaqualiedwatertreatmentspecialistbeengaged
to determine what water treatment is required.
C. The Factory assumes no responsibility for equipment failures which result from untreated
or improperly treated water.
D. Do not use deionized water in this unit. Some customized units may be compatible with
deionized water. Consult the factory before using deionized water.
WARNING: Improper water treatment will void unit warranty.

Page: 12
THIS PAGE INTENTIONALLY BLANK

BG-N4 Glycol Chiller
Page: 13
TEMPTEK, INC.
525 East Stop 18 Road Greenwood, Indiana 46142
317-887-6352 Fax: 317-881-1277
Email: [email protected]
2.0 INSTALLATION
2.1 General
2.2 Unit Location
2.3 To and From Process Connections
2.4 Air Cooled Condenser Installation
2.5 Electrical Connection

BG-N4 Glycol Chiller
Page: 14
TEMPTEK, INC.
525 East Stop 18 Road Greenwood, Indiana 46142
317-887-6352 Fax: 317-881-1277
Email: [email protected]
2.1 GENERAL
A. Chillers are shipped skid mounted and wrapped in plastic prior to shipment. Check the
overall condition of the equipment prior to accepting delivery. Check for visible damage
and document any evident damage on the delivery receipt. Shipping damage is the
responsibility of the carrier.
B. Allprocesspipingmaterials(suchashose,rigidpiping,valvesorlters)usedinprocess
water piping circuitry must be rated for 100°F minimum temperature and 100 PSI
minimum pressure.
C. All such materials must have the equivalent or larger diameter of the particular process
connection that length of process water piping is connected to.
2.2 UNIT LOCATION
A. Foundation. The chiller must be installed on a rigid and level mounting surface with
adequate strength to support the operating weight of the chiller including the weight of
water and attached piping.
This unit will contain water or water/glycol when operating. Locate the chiller
where an unforeseen uid leak will not cause damage to the surroundings or
install the unit in such a way that an unforeseen uid leak will not damage its
surroundings.
B. For air-cooled models:
1. These units are designed for indoor or outdoor use.
2. Formostefcientoperation,locatethechillerinalevel,cleanandwellventilated
environment.
3. The unit has an air-cooled refrigerant condenser. A motor driven fan generates
airowthroughthecondensertoremoveheatfromtherefrigerantsystem.The
air cooled condenser on the unit will discharge approximately 15,000 BTU per
hourforevery12,000Btuperhourofprocesscoolingandtheairowrateis
approximately 1,000 CFM per compressor horsepower.
4. The unit is designed to operate in a wide range of ambient temperatures. The
minimum recommended entering air temperature is -20°F and the maximum
recommendedenteringairtemperatureis95°Fforefcientoperation.
5. The unit must have a minimum of 4feet clearance at the air intake and 10 feet
at the vertical or horizontal exhaust air discharge and must have adequate
ventilation to dissipate the rejected heat. The unit must not be placed in non-
ventilated areas.
6. Vertical Air Discharge: all sides of the unit must be a minimum of 4 feet away
from any wall or obstruction. If enclosed by three walls, the top of the unit must
be level with or above the top of the wall and the minimum clearance must be
increased to 8 feet from the walls. If multiple units are placed side by side a

BG-N4 Glycol Chiller
Page: 15
TEMPTEK, INC.
525 East Stop 18 Road Greenwood, Indiana 46142
317-887-6352 Fax: 317-881-1277
Email: [email protected]
minimum of 8 feet is recommended between the units if placed side by side and
a minimum of 3 feet between the units if placed end to end. Louvers or fences
must have a minimum 80% free area and 4 feet clearance between the unit and
louver or fence. The height of the louver or fence must not exceed the top of the
unit.
7. Horizontal Air Discharge: the exhaust side must be a minimum of 10 feet
clearance from any wall or obstruction. The remaining sides must be a minimum
4 feet from any wall or obstruction. Do not position multiple units where hot air
discharges from a unit into the intake of another unit.
8. The unit must have all enclosure panels in place before operating the
compressor. Air will not be drawn through the condenser coil if the panels are not
in place. Starting the unit without all the enclosure panels in place will result in a
high pressure refrigerant fault.
9. Units with a motor-driven fan may not use duct work unless a booster fan of
equal volume rating has been installed in the duct.
2.3 TO AND FROM PROCESS CONNECTIONS
A. Useappropriatelyratedhoseoruidpipingtoconnecttheprocesspipinggoingtoyour
process to the “to process” connection on the chiller.
B. Useappropriatelyratedhoseoruidpipingtoconnecttheprocess
piping coming back from your process to the “from process”
connection on the chiller.
C. Install a high volume basket strainer in the From Process line with
isolationvalves.Abasketstrainerorbaglterwithameshscreen
of 20-40 will protect the unit. A “wye” type strainer is not
recommended because it does not have adequate debris
holding capacity.
D. Process water piping should be designed to avoid excessive
elbowsand/orlengthsofpipeorhose.Ifusingexiblehose
avoid tight twists or curls and excessive lengths.
From ProcessTo Process
This label marks the To
Process connection
From Process
This label marks the From
Process connection
Typical wye strainer -
Not recommended.
From Process
To Process
10 ton unit show. Typical process connections shown.

BG-N4 Glycol Chiller
Page: 16
TEMPTEK, INC.
525 East Stop 18 Road Greenwood, Indiana 46142
317-887-6352 Fax: 317-881-1277
Email: [email protected]
E. Valvesandltersmaybeinstalledintheprocesswaterpipingtofacilitateserviceand
maintenance provided that such devices maintain the full inside diameter of the process
connection. If installed, all such devices must be open and clean during unit operation.
F. It is important to check all external process connections for leaks prior to starting the unit.
It is also important to check external connections for leaks and internal hose clamps and
connections for leaks after servicing the unit.
2.4 AIR COOLED CONDENSER
A. Air-cooled condensers require ambient air temperatures between -20°F and 95°F for
efcientoperation.Operatingabove95°Fmayresultinelevatedcondensingpressures
and eventual shut-down on the high pressure limit switch. Air temperatures below -20°F
may result in over condensing pressures and cause a low pressure refrigerant fault.
B. Airowisgeneratedbythemotormountedfansorcentrifugalblowers.Airowisfrom
the outside of the chiller, through the condenser and exhausted through the top of the
unit. Exhaust air can not be ducted on motor mounted fan models.
C. The unit must have a minimum of 4feet clearance at the air intake and 10 feet at the
vertical exhaust air discharge and must have adequate ventilation to dissipate the
rejected heat. The unit must not be placed in non-ventilated areas.
D. Theunithasanair-cooledrefrigerantcondenser.Amotordrivenfangeneratesairow
through the condenser to remove heat from the refrigerant system. The air cooled
condenser on the unit will discharge approximately 15,000 BTU per hour for every 12,000
Btuperhourofprocesscoolingandtheairowrateisapproximately1,000CFMper
compressor horsepower.
H. All air cooled units must have all enclosure panels in place before operating compressor.
Air will not be drawn through the condenser coil if the panels are not in place. Starting the
unit without the enclosure panels in place will result in a refrigerant fault.
I. Condenser Air Filtering.Usealterthatproducesverylowairowrestrictions.
GenerallyadisposableberglasslterwithaMERVratingof2-3providesadequate
airltration.Thepurposeofthelteristopreventlargeparticlessuchasdust,lintand
debrisfromfoulingthecondenser.Youshouldbeabletoseethroughtheltermedia.
Usingrestrictiveltermediacancauselossofchillercapacity,difcultyrunninginwarm
weather and fan motor overheating.
Typical Filter materials.

BG-N4 Glycol Chiller
Page: 17
TEMPTEK, INC.
525 East Stop 18 Road Greenwood, Indiana 46142
317-887-6352 Fax: 317-881-1277
Email: [email protected]
2.5 ELECTRICAL CONNECTION
A. STANDARD MODELS
1. All electrical wiring must comply with local codes and
the National Electric Code.
2. Electrical power supply requirements for standard units
areidentiedontheequipmentdatatag.Determine
thattheplant’svoltagesupplyisthesameastheunit’s
voltage requirements, taking into account the SSCR
Rating.
3. A customer supplied, four conductor cable is
required for connection to a customer supplied fused
disconnecting means. The fused disconnecting means
shallbesizedandinstalledaccordingtotheunit’s
power supply requirements and local electrical codes.
(Some units may include a fused or non-fused disconnect
switch.)
4. Connect the four conductor power cable to the power entry terminal block on
theunit’selectricalpanel.Thenconnectthepowercabletothefuseddisconnect
switch. There is no power entry hole into the electrical cabinet. This allows the
matchingoftheentryholesizeandlocationtothecustomersuppliedttings.
5. Aunitspecicelectricaldrawingisshippedwiththeunit.
6. Voltage supplies must be within +/- 10% of the name plate voltage and must be
within 2% from leg to leg. Extreme voltage imbalance or using the wrong voltage
can damage your chiller and cause premature unit failure as well as a safety risk.
7. A proper ground is required for the unit.
WARNING: Do not attempt to duct exhaust air from a portable chiller using motor driven fans.
Exhaust air can only be ducted from a portable chiller using a blower assembly.
WARNING: Do not attempt to start or operate an air-cooled portable chiller without all cabinetry
panels in place. Air-cooled chillers require air to be drawn through the air-cooled condenser. This
will not occur if the panels are not in place.
WARNING: Do not connect the unit to a voltage supply not equal to the unit’s voltage
requirements as specied on the unit’s data plate. Use of incorrect voltage will void the unit’s
warranty and cause a signicant hazard that may result in serious personal injury and unit
damage.
Typical data tag.

BG-N4 Glycol Chiller
Page: 18
TEMPTEK, INC.
525 East Stop 18 Road Greenwood, Indiana 46142
317-887-6352 Fax: 317-881-1277
Email: [email protected]
B. CONTROL CIRCUIT WIRING
1. Theunit’ssuppliedcontrolcircuitis110volt,1phase,60cycle.
2. The control circuit is supplied by the factory installed transformer. A control circuit
fuse is provided.
C. GENERAL
1. Makecertainallgroundconnectionstotheunitareproperlyafxed.
2. Make certain power conductor, disconnecting means, and fusing are properly
sizedaccordingtotheunit’spowersupplyrequirements.
3. Follow all local and national codes.
4. Make certain that all owner and factory wire connections are tight before applying
power to the unit.
WARNING: Check that all electrical connections are tight before starting.
Disconnect power before servicing. Follow all facility lock-out tag-out procedures.
WARNING: Electric Shock Hazard. High Voltage is present in the electrical cabinet. Disconnect
power before servicing. Follow all facility lock-out tag-out procedures.

BG-N4 Glycol Chiller
Page: 19
TEMPTEK, INC.
525 East Stop 18 Road Greenwood, Indiana 46142
317-887-6352 Fax: 317-881-1277
Email: [email protected]
Transformer Power Entry / Disconnect (optional)
Coolant Pump Stater
Compressor Starter
Typical electrical panel shown

Page: 20
THIS PAGE INTENTIONALLY BLANK
Table of contents
Other Temptek Chiller manuals
Popular Chiller manuals by other brands

Thermal Care
Thermal Care Accuchiller NQ Series Operation, installation, and maintenance manual
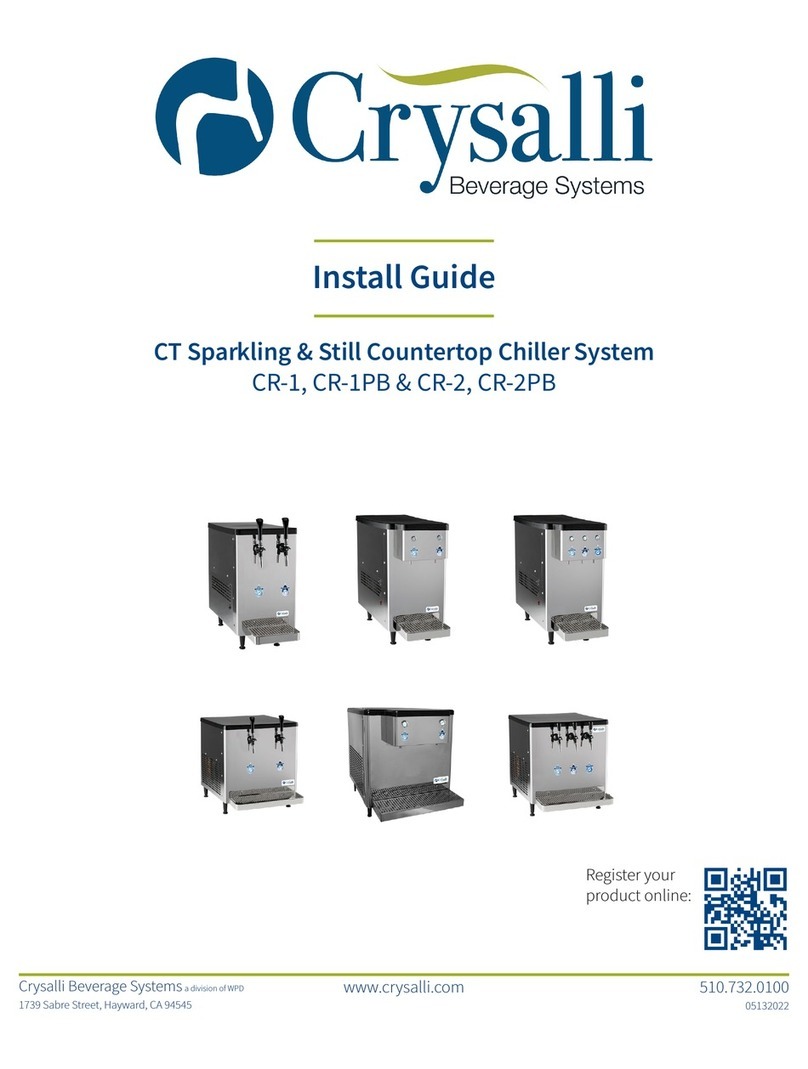
Crysalli
Crysalli CR-1 install guide

Data Aire
Data Aire DAC Series Operation and maintenance manual

Metos
Metos SC 500 Installation and operation manual
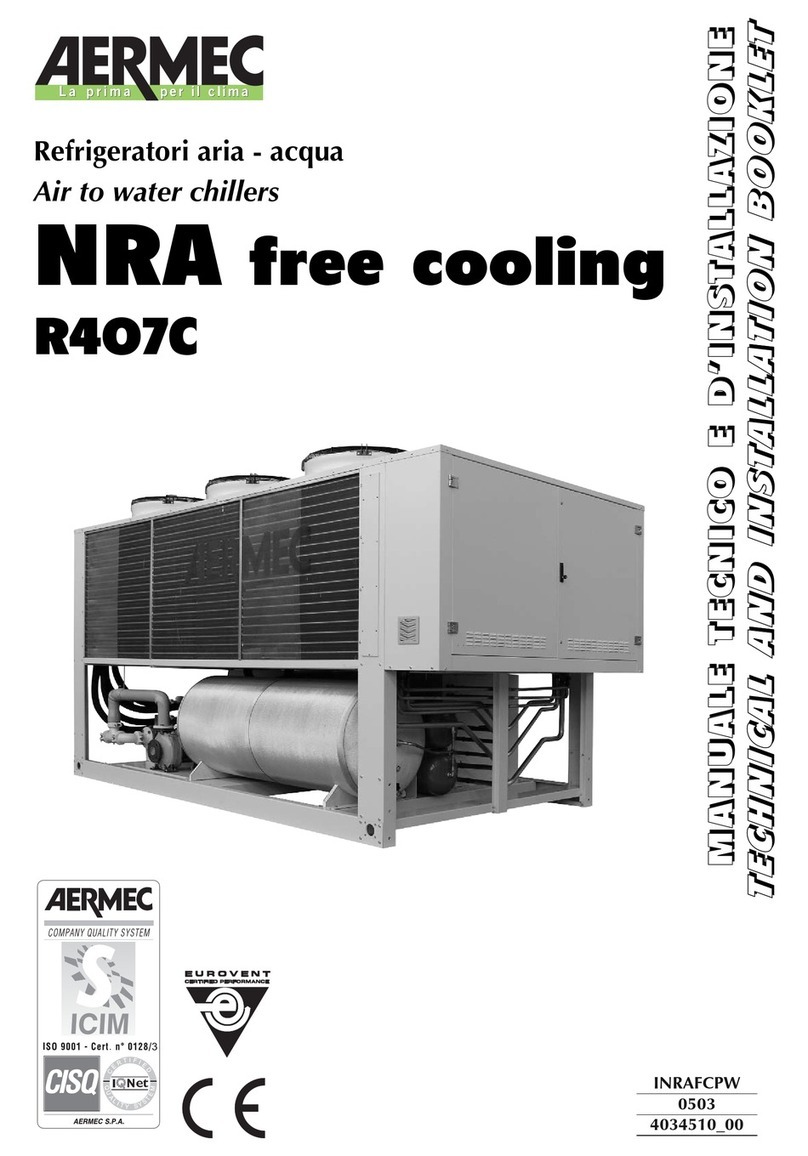
AERMEC
AERMEC NRA Technical and Installation Booklet
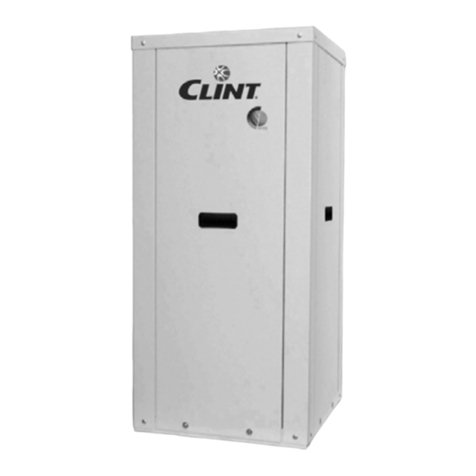
Clint
Clint R410A manual
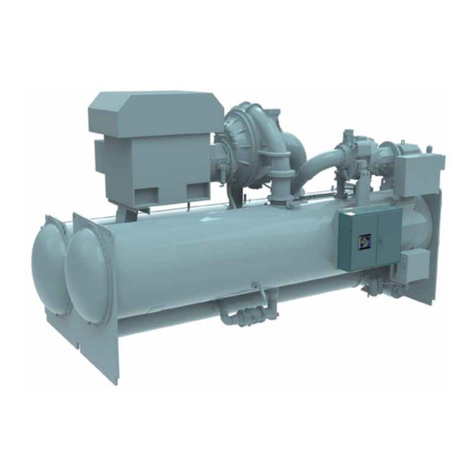
Johnson Controls
Johnson Controls York YKEP Series manual
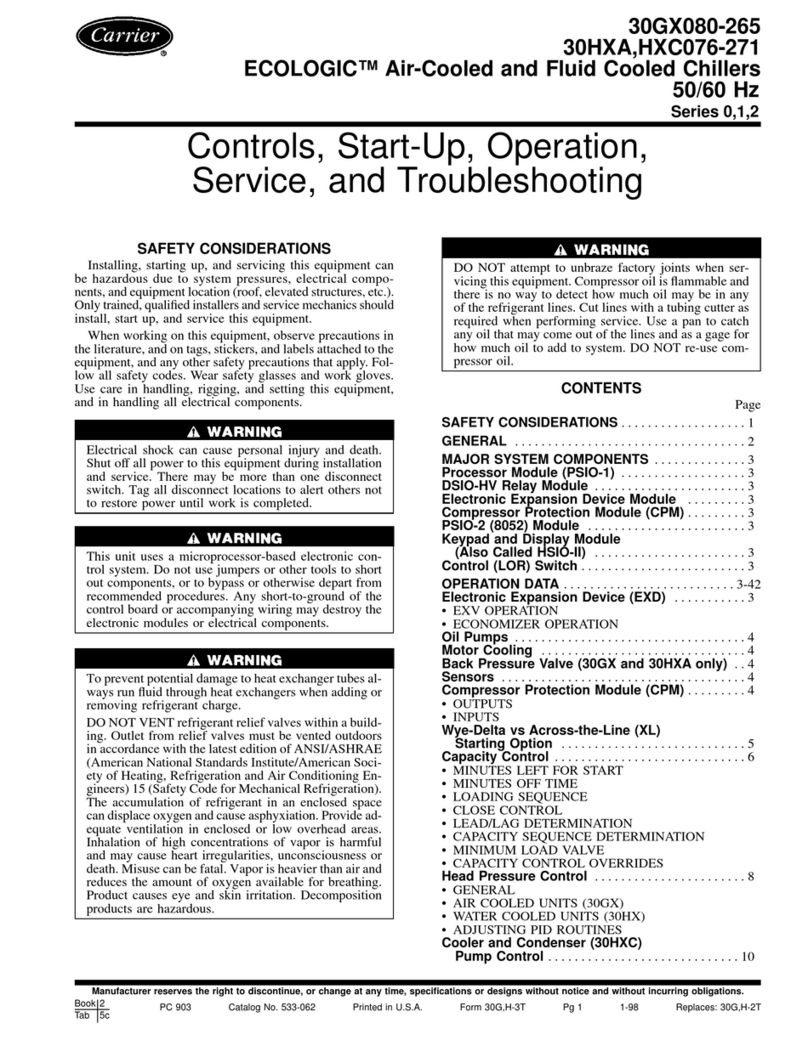
Carrier
Carrier 30GX080-265 Controls, start-up, operation, service, and troubleshooting

intensity
intensity ICHS-120KC-5 Installation & owner's manual
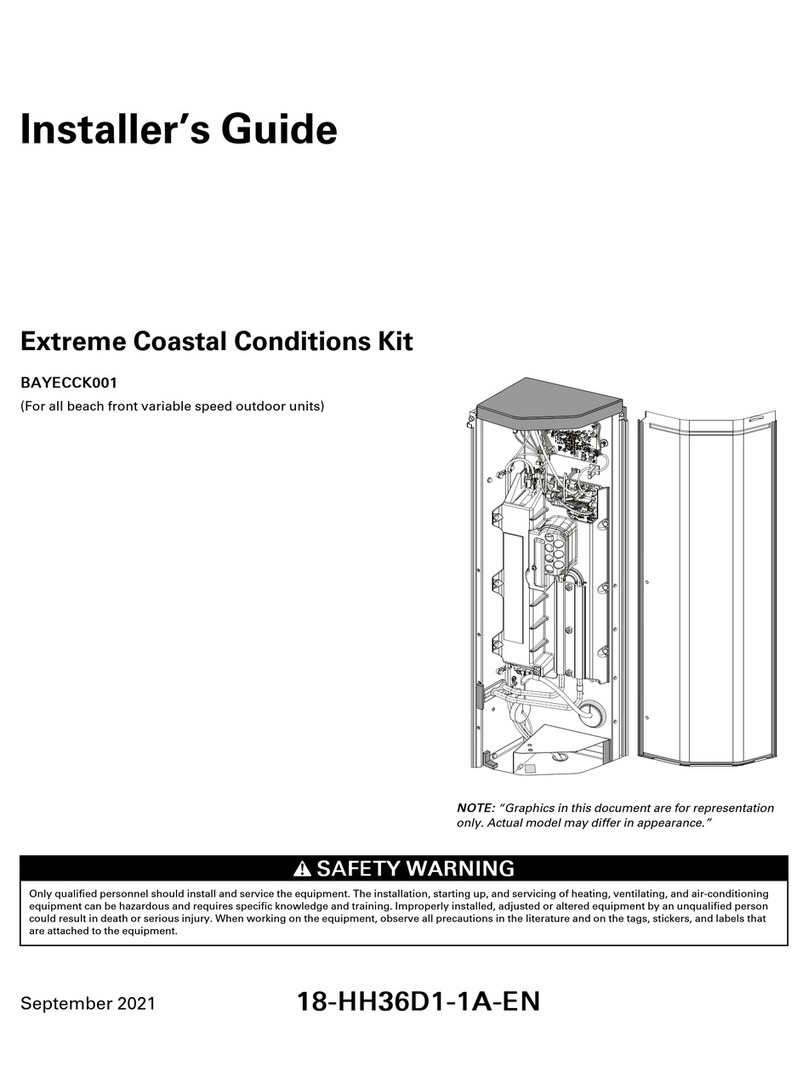
Trane
Trane BAYECCK001 Installer's guide

TECO
TECO ra 200 instruction manual

Bromic Heating
Bromic Heating MEDIFRIDGE MEDO374GD instruction manual