Thern TA10 Series User manual

Owner’s Manual
For TA10 Series
Planetary Gear
Air Winches
A9903C-0514
Read this Own
er’s Manual
thoroughly before operating
the equipment. Keep it with
the equipment at all times.
Replacements are available
from Thern, Inc., PO Box 347,
Winona, MN 55987,
507-454-2996.
www.thern.com
IMPORTANT: Please record
product information on
page 2. This information is
required when calling the
factory for service.

Owner's Manual for Thern TA10 Series Planetary Gear Air Winchespage 2
A9903C-0514
Warranty Statement
Thern, Inc. warrants each new products to be free from defects in material and workmanship under normal use and
service for a period of 24 months from the date of purchase by the original using buyer. Genuine Thern, Inc. replace-
ment parts and components will be warranted for 30 days from the date of purchase, or the remainder of the original
equipment warranty period, whichever is longer.
Under no circumstances will this warranty cover an product or component thereof, which, in the opinion of the
company, has been subjected to misuse, unauthorized modifications, alteration, an accident or shipping damage. This
warranty also shall not apply to products that are operated improperly, improperly maintained or improperly stored.
This warranty does not cover any costs for removal of our product, downtime, or any other incidental or consequential
costs or damages resulting from the claimed defects. Brake discs, wire rope or other wear components are not covered
under this warranty, as their life is subject to use conditions which vary between applications. Any alteration, repair or
modification of the product outside the Thern, Inc. factory shall void this warranty.
Thern, Inc. in no way warrants pneumatic, hydraulic or electric motors and control valves or other trade accessories
since these items are warranted separately by their respective manufacturers.
FACTORY AUTHORIZED REPAIR OR REPLACEMENT AS PROVIDED UNDER THIS WARRANTY IS THE
EXCLUSIVE REMEDY TO THE CONSUMER. THERN, INC. SHALL NOT BE LIABLE FOR ANY INCIDEN-
TAL OR CONSEQUENTIAL DAMAGES FOR BREACH OF ANY EXPRESS OR IMPLIED WARRANTY ON
THIS PRODUCT. EXCEPT TO THE EXTENT PROHIBITED BY APPLICABLE LAW, ANY IMPLIED WAR-
RANTY OF MERCHANTABILITY OR FITNESS FOR A PARTICULAR PURPOSE ON THIS PRODUCT IS
LIMITED IN DURATION TO THE DURATION OF THIS WARRANTY.
Some states do not allow the exclusion or limitation of incidental or consequential damages, or allow limitations on
how long an implied warranty lasts, so the above limitation or exclusion may not apply to you. This warranty gives
you specific legal rights, and you may also have other rights which vary from state to state.
To make a claim under this warranty, contact the factory for an RGA number. The product must be returned,
prepaid, directly to Thern, Inc. or to an authorized service center. A completed warranty claim form must ac-
company the product. If the product is found to be defective, it will be repaired or replaced free of charge, and
Thern, Inc. will reimburse the shipping costs.
Note: Thern, Inc. reserves the right to change the design or discontinue the production of any product without
prior notice.
About This Manual
The Occupational Safety and Health Act of 1970 states that it is the employer’s responsibility to provide a workplace
free of hazard. To this end, all equipment should be installed, operated, and maintained in compliance with applicable
trade, industrial, federal, state, and local regulations. It is the equipment owner's responsibility to obtain copies of
these regulations and to determine the suitability of the equipment to its intended use.
This Owner’s Manual, and warning labels attached to the equipment, are to serve as guidelines for hazard-free
installation, operation, and maintenance. They should not be understood to prepare you for every possible situation.
The information contained in this manual is applicable only to the Thern TA10 Series Planetary Gear Air Winches. Do
not use this manual as a source of information for any other equipment.
The following symbols are used for emphasis throughout this manual:
Failure to follow ‘WARNING!’ instructions may result in equipment damage,
property damage, and/or serious personal injury.
Failure to follow ‘CAUTION!’ instructions may result in equipment damage,
property damage, and/or minor personal injury.
Important!
Failure to follow ‘important!’ instructions may result in poor performance of the
equipment.
Please record the following:
Date Purchased:
Model No.:
Serial No.:
This information is required when
calling the factory for service.

Owner's Manual for Thern TA10 Series Planetary Gear Air Winches page 3
A9903C-0514
Figure 1 – Serial Tag
Figure 1A - Serial Tag Location
Serial Tag Location

Owner's Manual for Thern TA10 Series Planetary Gear Air Winchespage 4
A9903C-0514
Suggestions for Safe Operation
DO the following:
Read and comply with the guidelines set forth in this Owner’s Manual. Keep
this manual, and all labels attached to the winch, readable and with the
equipment at all times. Contact Thern, Inc. for replacements.
Check lubrication before use.
Install the wire rope securely to the winch drum.
Keep at least 5 wraps of wire rope wound on the drum at all times, to serve as
anchor wraps. With less than 5 wraps on the drum the wire rope could come
loose, causing the load to escape.
Keep hands away from the drum, gears, wire rope, and other moving parts of
the equipment.
Ensure brakes hold prior to making complete lift by lifting load a short
distance and releasing control.
If there is slack wire rope condition, the hoisting mechanisms shall be in-
spected to ensure all wire ropes are properly seated on drums and in sheaves,
before resuming winch operation.
Disconnect air supply before servicing the equipment.

Owner's Manual for Thern TA10 Series Planetary Gear Air Winches page 5
A9903C-0514
Suggestions for Safe Operation
DO NOT do the following:
Do not lift loads over people. Do not walk or work under a load or in the line
of force of any load.
Do not exceed the load rating of the winch or any other component in the
system. To do so could result in failure of the equipment.
Do not use more than one winch to move a load unless each winch was de-
signed for use in a multiple winch system.
Do not use damaged or malfunctioning equipment. To do so could result in
failure of the equipment.
Do not modify the equipment in any way. To do so could cause equipment
failure.
Do not wrap the wire rope around the load. This damages the wire rope and
could cause the load to escape. Use a sling or other approved lifting device.
Do not operate the winch with drive guards or gear covers removed or im-
properly installed.
Do not divert your attention from the operation. Stay alert to the possibility of
accidents, and try to prevent them from happening.
Do not jerk or swing the load. Avoid shock loads by starting and stopping the
load smoothly. Shock loads overload the equipment and may cause damage.
Do not leave a suspended load unattended unless specific precautions have
been taken to secure the load and keep people away from the winch and out
from under the load.
Do not adjust the brake with the load suspended.
Do not disassemble the air cylinder for the automatic band brake, improper
disassembly could cause personal injury. Contact factory.

Owner's Manual for Thern TA10 Series Planetary Gear Air Winchespage 6
A9903C-0514
1.1 Installing the Winch
All supporting structure, mounting hardware and attaching hardware must
be in accordance with all applicable standards codes and regulations.
Ensure proper selection and installation of wire rope and sheaves. Sheaves
and sheave mounting must be designed and selected in accordance with all
applicable standards, codes, and regulations. Improper installation of wire
rope or sheave can cause uneven spooling and wire rope damage that could
cause a load to escape.
Do not install the winch in an area defined as hazardous by the National Elec-
tric Code, unless installation in such an area has been thoroughly approved.
Do not install the winch near corrosive chemicals, flammable materials, ex-
plosives, or other elements that may damage the winch or injure the operator.
Adequately protect the winch and the operator from such elements.
Position the winch so the operator can stand clear of the load, and out of the
path of a broken wire rope that could snap back and cause injury.
Attach the winch to a rigid and level foundation that will support the winch
and its load under all load conditions, including shock loading.
Important!
• Inspect the winch immediately
following installation according
to the Instructions for Periodic
Inspection. This will give you
a record of the condition of the
winch with which to compare
future inspections.
• A qualified professional should
inspect or design the founda-
tion to insure that it will provide
adequate support.
• Locate the winch so it will be vis-
ible during the entire operation.
• When moving and positioning
the winch, lift using the lifting
eyes in the frame or with a sling
wrapped around drum.
• Do not weld the winch frame to
the foundation or support struc-
ture. Welding the frame may void
warranty, contact Thern, Inc. Use
fasteners as instructed.
Figure 2 – Maintaining the Fleet Angle
• When wire rope travels over a sheave or through a roller guide – main-
tain fleet angle by locating the sheave or guide an appropriate distance
from the drum, shown as distance “A”.
smooth drum
1/2 to 1-1/2 degrees
distance “A”
center
line
fixed sheave
or roller guide
• When wire rope travels directly to the load – maintain fleet angle by
controlling side-to-side movement of the load with tracks or guide rails.
Allowing the load to move too far to one side causes stress on the
drum flange which may cause damage.
1/2 to 1-1/2 degrees center
line
smooth drum
tracks or guide rails
load
Important!
• Use a sheave or roller guide to
direct the wire rope to the drum
whenever possible.
• Install sheaves, tracks and other
equipment so they will remain
fixed under all load conditions.
Follow the recommendations of
the equipment manufacturer.
• Use sheaves of proper diameter to
minimize wear on the wire rope.
Follow the recommendations of
the sheave manufacturer.

Owner's Manual for Thern TA10 Series Planetary Gear Air Winches page 7
A9903C-0514
1.1.1 CONSULT APPLICABLE CODES AND REGULATIONS for specific
rules on installing the equipment.
1.1.2 LOCATE THE WINCH in an area clear of traffic and other obstacles. Make
sure the winch is accessible for maintenance and operation.
1.1.3 LOCATE THE WINCH in an area with adequate temperatures. Check the
motor and reducer manufacturer’s information for ambient temperature rat-
ings.
1.1.4 INSTALL THE WINCH on a horizontal surface. The winch is designed and
assembled for horizontal base mounting. Special consideration must be taken
if mounting vertically or upside-down. Please contact Thern, Inc.
1.1.5 MAINTAIN A FLEET ANGLE between 1/2 and 1-1/2 degrees. The proper
fleet angle minimizes wire rope damage by helping the wire rope wind uni-
formly onto the drum. See Figure 2.
1.1.6 FASTEN THE WINCH SECURELY to the foundation.
a FOR STANDARD PRODUCTS referred to in this manual, use coarse thread
fasteners, grade 8 or better. Be sure to check the torque required for your
fastener selection before mounting winch. Make sure the winch is secured to
a solid foundation able to support the winch and the load under all conditions
with design factors based on accepted engineering practices.
b NON-STANDARD PRODUCTS that vary from the original design may
have different fastening requirements. Contact a structural engineer or Th-
ern, Inc. for this information.
CONTACT A QUALIFIED PROFESSIONAL FOR MOUNTING IN-
STRUCTIONS TO COMPLY WITH LOCAL CODES.

Owner's Manual for Thern TA10 Series Planetary Gear Air Winchespage 8
A9903C-0514
1.2 Installing the Breather Plug
Make sure the breather plugs are clean and open to vent heat and pressure.
Poor ventilation will cause overheating and result in damage to oil seals and
other equipment. See Figure 3.
For shipment, the winch motor, disc brake and reducer are filled with
lubricant and have breather plugs installed.
1.2.1 VERIFY THE BREATHER PLUGS are installed on the motor, disc brake
and reducer. Refer to the manufacturer’s information.
1.2.2 CHECK THE LUBRICANT LEVEL in the motor, brake and reducer to make
sure no lubricant was lost during shipment. See section 3.2 - Lubricating the
Winch.
Figure 3 – Installing the Breather Plug(s) - TA10
Brake Breather Plug
Motor Breather Plug
*Disc brake shown
Reducer Breather Plug

Owner's Manual for Thern TA10 Series Planetary Gear Air Winches page 9
A9903C-0514
1.3 Connecting the Air Supply
All control devices must be momentary type. Install all control devices so the
winch motor will stop when the operator releases the device.
Locate control devices so the operator will be able to view the load through
the entire operation.
Locate control devices so the operator will be clear of the load, the wire rope,
and the path of a broken wire rope that could snap back and cause injury.
Check that the direction indicators on control match load direction.
Remove port caps from exhaust ports for operation. Failure to do so may
result in equipment damage and limit performance. See Figure 10 on page 20.
It is the responsibility of the owner to provide equipment for controlling the
winch, The following guidelines are supplied as a reference for the installer.
INSTALL A F-R-L ON YOUR UNIT BEFORE WINCH OPERATION. A
FILTER-REGULATOR-LUBRICATOR UNIT MUST BE USED WHILE
OPERATING EQUIPMENT TO MAINTAIN WARRANTY. THERN
WILL NOT COVER ANY DAMAGE TO EQUIPMENT CAUSED BY
DIRTY, POOR, CONTAMINATED OR NON-LUBRICATED AIR
SUPPLY. SEE FIGURE 5.
1.3.1 CONSULT APPLICABLE CODES AND REGULATION for specific
instructions regarding power supply installation and backup.
1.3.2 CHECK THE COMPONENT MANUFACTURER'S INSTRUCTIONS for
installing and connecting the motor, brake and other equipment.
1.3.3 ENSURE an accessible shut off valve has been installed in the air supply
line and make sure others are aware of its location.
1.3.4 THE AIR SUPPLY must be clean and free from moisture.
a ALL AIR SUPPLY LINES should be purged with clean, moisture free air or
nitrogen before connecting to winch inlet.
b SUPPLY LINES should be as short and straight as installation conditions
will permit. Long transmission lines and excessive use of fittings, elbows,
tees, globe valves etc. cause a reduction in pressure due to restrictions and
surface friction in the lines.
1.3.5 ALWAYS USE an air line lubricator with these motors.
aTHE LUBRICATOR must have an inlet and outlet at least as large as the
inlet on the motor. Install the air line lubricator as close to the air inlet on the
motor as possible.
bLUBRICATOR must be located no more than 10 ft. (3 m) from the motor.
cAIR LINE LUBRICATOR should be replenished daily and set to provide 6
to 9 drops per minute of SAE 10W oil. A fine mist will be exhausted from
the throttle control valve when the air line lubricator is functioning properly.
1.3.6 INSTALL REGULATOR to regulate air pressure to the winch. Too high or
low air pressure may result in equipment damage and limit performance.
Important!
• Use components rated for the
power supply you will be using.
• Always disconnect the air supply
when the winch is not in use.
• The F-R-L must be compatible
with the required air supply.

Owner's Manual for Thern TA10 Series Planetary Gear Air Winchespage 10
A9903C-0514
1.3.7 IT IS RECOMMENDED that an air line strainer/filter be installed as close
as practical to the motor air inlet port, but before the lubricator, to prevent
dirt from entering the motor. The strainer/filter should provide 20 micron
filtration and include a moisture trap. Clean the strainer/filter periodically to
maintain its operating efficiency.
1.3.8 MOISTURE THAT REACHES THE AIR MOTOR through air supply lines
is a primary factor in determining the length of time between service over-
hauls.
aMOISTURE TRAPS can help to eliminate moisture.
bAIR RECEIVERS collect moisture before it reaches the motor.
cINSTALLING AN AFTERCOOLER at the compressor that cools the air to
condense and collect moisture prior to distribution through the supply lines
is also helpful.
1.3.9 THE AIR MOTOR SHOULD BE INSTALLED as near as possible to the
compressor or air receiver. Recommended pressures and volumes are mea-
sured at the point of entry to the air motor.
1.3.10 INSTALL MUFFLERS in both exhaust ports to reduce noise. For operation,
remove port caps from exhaust ports. See Figure 4.
1.3.11 CHECK THE AIR PRESSURE at the motor and make sure it agrees with
the pressure rating marked on the winch nameplate. Adjust regulator as
necessary
1.3.12 TEST AIR CONNECTIONS by operating the winch.
a ROTATION OF THE DRUM must agree with the labels on the control
device, either UP and DOWN, or FORWARD and REVERSE.
bCHECK THE AUTOMATIC LOAD BRAKE(S), make sure it releases
when the motor is ON, and engages when the motor is OFF.
CONTACT THE FACTORY OR A QUALIFIED PROFESSIONAL FOR HELP.
Air Out
PSI gauge installed on regulated
lubricator side
Figure 5 – Filter-Regulator-Lubricator Unit (F-R-L)
Air In
Filter
Regulator
Lubricator
Muffler installed in
valve exhaust port
Muffler installed in
motor exhaust port
Figure 4 – Mufflers

Owner's Manual for Thern TA10 Series Planetary Gear Air Winches page 11
A9903C-0514
1.4 Reversing the Air Valve Handle
Disconnect air power before disassembling valve handle to keep from
damaging equipment and prevent injury.
Make sure to check the adjustment of the air valve flow restrictor screw if
winch operating speeds differ from performance specifications during lower-
ing or pay out of wire rope. See section 2.5 Air Valve Adjustment.
1.4.1 TO REVERSE AIR VALVE HANDLE, do the following. See figure 6.
a REMOVE THE AIR VALVE HANDLE END CAP.
b REMOVE THE AIR VALVE END CAP.
cPUSH VALVE SPOOL ASSEMBLY, and remove from the valve body.
d RE-INSTALL VALVE SPOOL ASSEMBLY, in the opposite direction.
e RE-INSTALL THE AIR VALVE END CAP on the spring side of the valve
body.
f ALIGN BALL FROM INSIDE OF END CAP with hole on valve spool
assembly. This allows the handle to operate the valve shaft assembly move-
ment.
g RE-INSTALL THE AIR VALVE HANDLE END CAP.
1.4.2 VERIFY CABLE WRAPPING agrees with handle operation when lifting.
1.5 Installing the Wire Rope
Install the wire rope securely to the winch drum. A poorly secured wire rope
could come loose from its anchor and allow the load to escape.
1.5.1 DETERMINE WHICH DIRECTION the drum must rotate to wind and un-
wind wire rope.
1.5.2 PURCHASE THE PROPER WIRE ROPE for your application. Keep the
following in mind when selecting a wire rope. Contact a reputable wire rope
supplier for help.
a BREAKING STRENGTH of new wire rope should be at least 3 times
greater than the largest load placed on the winch. If loads are lifted or pulled
on an incline, the breaking strength must be at least 5 times greater than the
largest load. These are minimum values and will vary with the type of load
and how you are moving it.
b WIRE ROPE LAY must agree with the winding direction of the drum to
help insure proper winding.

Owner's Manual for Thern TA10 Series Planetary Gear Air Winchespage 12
A9903C-0514
Figure 6 – Reversing the Air Valve Handle
AB
CD
F
E
G

Owner's Manual for Thern TA10 Series Planetary Gear Air Winches page 13
A9903C-0514
c WE RECOMMEND 6 x 37 IWRC improved plow steel (IPS) or extra
improved plow steel (EIPS) wire rope.
1.5.3 ANCHOR THE WIRE ROPE to the drum using the cable anchor.
See Figure 7.
a PASS THE WIRE ROPE through the hole in the drum and over the groove
on the cable anchor. Make sure at least 1/2 inch of wire rope extends past the
cable anchor, and the end of the wire rope does not protrude out where it will
hit other components as the drum is turning.
b ROTATE THE CABLE ANCHOR and pull wire rope slightly to engage the
cable anchor.
c USE THE CABLE ANCHOR WRENCH TO TIGHTEN ANCHOR.
1.5.4 WIND FIVE FULL WRAPS of wire rope onto the drum by operating the
winch while holding the wire rope taught. These wraps serve as anchor
wraps and must remain on the drum at all times.
1.5.5 WIRE ROPE MUST BE SPOOLED on drum so that the anchor groove
tapers away from the wire rope exit hole.
1.5.6 TO REVERSE WIRE ROPE SPOOLING DIRECTION, do the following.
See figure 8.
a COMPLETELY REMOVE the wire rope from the drum.
bREMOVE THE CABLE ANCHOR. Flip the anchor so that the grooving
runs in the opposite direction.
cRE-ATTATCH THE CABLE ANCHOR.
dSPOOL THE WIRE ROPE onto the drum from the new side.
Important!
• Use wire rope and other rigging
equipment rated for the size of the
largest load you will be moving.
• Do not drag the wire rope
through dirt or debris that could
cause damage, or poor operation.
• Always wear protective clothing
when handling wire rope.
Figure 7b – Installing the
Wire Rope
Figure 7a – Installing the
Wire Rope
Install wire
rope
Anchor
wrench
Anchor
groove
Exit
hole

Owner's Manual for Thern TA10 Series Planetary Gear Air Winchespage 14
A9903C-0514
Figure 8 – Reversing the Cable Anchor
A B
C D
E F

Owner's Manual for Thern TA10 Series Planetary Gear Air Winches page 15
A9903C-0514
2.1 General Theory of Operation
2.1.1 THE PULL REQUIRED to move the load must not exceed the load rating of
the winch. Consider the total force required to move the load, not the weight
of the load.
2.1.2 THIS EQUIPMENT CAN develop forces that will exceed the load rating.
It is the responsibility of the equipment user to limit the size of the load.
Inspect the equipment regularly for damage according to the instructions
contained in this manual and in the component manufacturer’s information.
2.1.3 USE A LOAD BRAKE on all winches used to lift loads or drag loads on an
incline. Brakes are of two basic types, band brake and disc brake. The band
brake can be either manually or automatically engaged and the disc brake is
automatically engaged. When engaged, they lock the drive train to the winch
frame, thereby stopping drum rotation when the control is released or placed
in the neutral position.
2.1.4 PERFORMANCE RATINGS of the equipment are affected by the amount
of wire rope wound on the drum, the way in which it is wound, air power
supply, and the way the winch is used.
a DRUM CAPACITY depends on how tightly and evenly the wire rope is
wound on the drum. Actual drum capacities are usually 25-30% less than
values shown in performance tables, due to loose winding and overlapping.
b LINE SPEED increases with each additional layer of wire rope wound onto
the drum. Line speed will also vary with load weight and air power supply.
c LOAD RATING represents the maximum pull that can be placed on new
equipment. Load ratings are assigned values for specific amounts of load
travel or wire rope accumulation. The load rating decreases as layers of wire
rope accumulate on the drum.
2.1.5 DUTY RATINGS refer to the type of use the equipment is subject to. Con-
sider the following when determining duty rating.
a ENVIRONMENT: harsh environments include hot, cold, dirty, wet, corro-
sive, or explosive surroundings. Protect the equipment from harsh environ-
ments when possible.
b MAINTENANCE: poor maintenance, meaning poor cleaning, lubrication,
or inspection, leads to poor operation and possible damage of the equipment.
Minimize poor maintenance by carefully following the instructions con-
tained in this manual.
c LOADING: severe loading includes shock loading and moving loads that
exceed the load rating of the equipment. Avoid shock loads, and do not ex-
ceed the load rating of the equipment.
d FREQUENCY OF OPERATION: frequent start and stop functions increase
wear and shorten the life span of the gear train and load brake components.
Lengthy operations cause lubrication to become hot, which also decreases
the life span of the gear train and brakes. Increase maintenance of the equip-
ment if used in frequent operations.
CONTACT FACTORY FOR MORE INFORMATION.
Important!
• Limit nonuniform winding by
keeping tension on the wire rope
and by maintaining the proper
fleet angle.
• To help insure rated performance,
make sure the air pressure at the
motor is equal to the motor’s pres-
sure rating.
• It is your responsibility to detect
and account for different fac-
tors affecting the condition and
performance of the equipment.
• When determining whether the
load will exceed the load rating,
consider the total force required
to move the load.

Owner's Manual for Thern TA10 Series Planetary Gear Air Winchespage 16
A9903C-0514
2.2 Inspecting/Adjusting the Brakes
Do not adjust brakes with the winch holding a load. Accidental release of the
brake could allow the load to escape.
Keep hands away from the drum, gears, wire rope and other moving parts of
the equipment.
Do not disassemble the air cylinder for the automatic band brake, improper
disassembly could cause personal injury. Contact factory.
2.2.1 INSPECTING THE BAND BRAKE
a DRUM BAND BRAKE should be inspected for oil, grease and glazing.
These occurrences are not uncommon but need to be fixed before operation
continues. If the brake lining is oil-soaked, replace the brake bands as a set.
A fine grit emery cloth should be used to sand any glazed area to remove
them.
b MEASURE BAND THICKNESS to maintain brake effectiveness. The set of
brake bands must be replaced if they measure less than .125 inch thickness
anywhere on the band.
2.2.2 INDIVIDUALLY TEST BRAKES installed to ensure proper operation.
Brakes must hold a 125% rated load with full drum without slipping. If indi-
cated by poor operation or visual damage, contact factory and have brake(s)
repaired. Check all brake surfaces for wear, deformation or foreign deposits.
2.2.3 ADJUSTING THE MANUAL BRAKE
a MAKE SURE THERE IS NO LOAD on the winch.
b RELEASE WIRE ROPE TENSION on the drum.
c RELEASE TENSION OF BRAKE BANDS by disengaging the brake band
handle.
d
ROTATING THE ADJUSTMENT NUT clockwise will tighten the brake
band. Adjustments should be made in increments of 1/2 rotation. See Figure 9.
e CHECK THE ADJUSTMENT by engaging the band brake. The brake is
properly adjusted when it can be pushed into the lock position (with the
handle over center) with 50 to 100 lbs of force being applied to the handle
and holding the rated load for that model winch. If not, repeat step "d" until
correct.
2.2.4 ADJUSTING THE AUTOMATIC BAND BRAKE
a MAKE SURE THERE IS NO LOAD on the winch.
b RELEASE WIRE ROPE TENSION on the drum.
c RELEASE TENSION ON BRAKE BANDS by applying air to the brake
cylinder.
d ROTATE THE ADJUSTMENT NUT clockwise will tighten the brake band.
Adjustments should be made in increments of 1/2 rotation. See Figure 9.
e CHECK THE ADJUSTMENT by engaging the band brake. The brake is
properly adjusted when it holds the rated load for that model winch. If not,
repeat step "d" until correct.
2.2.5 AUTOMATIC DISC BRAKE ADJUSTMENT is not required. If the disc
brake does not hold the rated load contact the factory for repair instructions.
Figure 9 – Band Brake
Adjustment
Adjustment Nut

Owner's Manual for Thern TA10 Series Planetary Gear Air Winches page 17
A9903C-0514
2.3 Breaking-In The Winch
Remove exhaust port caps for operation. Failure to do so may result in equip-
ment damage and limit performance. See Figure 10.
2.3.1 BEFORE THE WINCH IS PLACED INTO SERVICE or for winches that
have been in storage for a period of more than one month, the following
start-up procedure is required. See Figure 10.
a INSPECT THE WINCH and other equipment according the Instructions for
Periodic Inspection.
b WHEN FIRST OPERATING THE WINCH it is recommended that the mo-
tor be driven slowly in both directions for a few minutes.
C ENSURE BRAKES HOLD prior to making complete lift by lifting load a
short distance and releasing control.
2.3.2 PRIOR TO INITIAL USE, all new, altered or repaired winches shall be
tested to ensure proper operation. See Figure 10.
aCHECK THAT THE OIL LEVEL in motor, reduction gear assembly and
disc brake are correct.
bALL NEW DRUM BRAKE BAND LININGS require a "run-in" period. Op-
erate the winch without load in the payout direction while gradually applying
the brake. Allow the brake to slip for approximately one minute. Winch mo-
tor may stall as drum brake band lining fully engages. Do not allow brake
to overheat. Check operation of brakes following run-in. See section 2.2
- Inspecting/Adjusting the Brakes
2.3.3 INSPECT THE WINCH following the break-in according to the Instructions
for Periodic Inspection. See section 3.3 - Inspecting the Equipment.

Owner's Manual for Thern TA10 Series Planetary Gear Air Winchespage 18
A9903C-0514
2.4 Preparing for Operation
Read and comply with the guidelines set forth in this Owner’s Manual.
Keep this manual, and all labels attached to the winch, readable and
with the equipment at all times. Contact Thern, Inc. for replacements.
Do not lift loads over people. Do not walk or work under a load or in the line
of force of any load.
Do not exceed the load rating of the winch or any other component in the
system. To do so could result in failure of the equipment.
The winch must be equipped with a load brake if it is used to lift loads or drag
loads on an incline.
Do not use more than one winch to move a load unless each winch was de-
signed for a multiple winch system.
Do not use damaged or malfunctioning equipment. To do so could result in
failure of the equipment.
Do not modify the equipment in any way. To do so could cause equipment failure.
Do not operate the winch with guards removed or improperly installed.
Check lubrication before use.
2.4.1 CONSIDER THE OPERATION. Do not begin until you are sure you can
perform the entire operation without hazard.
2.4.2 A PRE-OPERATION MEETING attended by the winch operator, ground
crew, signal person, persons to be lifted and the person in charge of the task
to be performed shall be held to plan and review the procedure to be fol-
lowed, including:
•Signals.
•Appropriate number of signal persons and ground crew.
•Designate responsibility.
aTHIS MEETING SHALL BE HELD prior to the beginning of operations at
each new work location and thereafter for any new employees assigned to
the operation.
bDURING THIS MEETING it is recommended that a comprehensive plan
to cover emergency procedures be worked out prior to exercising the winch
capabilities of this winch.
2.4.3 INSPECT ALL COMPONENTS of the system.
a INSPECT THE WINCH and other equipment according to the Instructions
for Frequent Inspection.

Owner's Manual for Thern TA10 Series Planetary Gear Air Winches page 19
A9903C-0514
b OPERATORS shall be physically competent and have no health condition
which might affect their ability to act, and they must have good hearing.
Operators who are fatigued or have exceeded their normal shift period shall
check all related regulations regarding approved work periods prior to opera-
tion. Refer to training program - See section 2.3.1. The operator must thor-
oughly understand proper methods of rigging and attaching loads and should
have a good attitude regarding safety.
c THE LOAD must be clear of other objects and free to move. Make sure the
load will not tip, spin, roll away, or in any way move uncontrollably.
2.4.4 KNOW YOUR LOAD and make sure you do not exceed the load rating of
the winch or any other equipment in the system.

Owner's Manual for Thern TA10 Series Planetary Gear Air Winchespage 20
A9903C-0514
2.5 Air Valve Adjustment
Remove port caps from exhaust ports for operation. Failure to do so may
result in equipment damage and limit performance. See Figure 10.
Make sure to check the adjustment of the air valve flow restrictor screw if
winch operating speeds differ from performance specifications during lower-
ing or pay out of wire rope.
Do not adjust the flow restrictor while suspending or hoisting a load.
2.5.1 ADJUSTMENT FOR LIFTING APPLICATIONS - SEE FIGURE 10
NOTE: This adjustment setting is only a recommendation for initial
startup in order to prevent over speeding while lowering. The actual
adjustment required is dependent on the load and the specific unit pur-
chased.
aLOOSEN NUT AND ADJUST SCREW located in the valve end cap.
bADJUST UNTIL DRUM SPEED for full load payout is equal to or less than
the drum speed for no-load haul in.
c TIGHTEN THE NUT when drum speed is adjusted.
2.5.2 ADJUSTMENT FOR PULLING APPLICATIONS - See Figure 10
a LOOSEN NUT AND ADJUST SCREW located in the valve cap end.
b ADJUST UNTIL DRUM SPEED for no-load payout equals the drum speed
for no-load haul in.
c TIGHTEN NUT when drum speed is adjusted.
speed adjusting screw
and lock nut
NOTE: Thern recommends installing
mufflers in exhaust ports to
reduce noise. For operation
remove port caps from
exhaust ports.
motor
exhaust port 2
valve
exhaust port 1
inlet port
Figure 10 – Motor and Valve
Table of contents
Popular Other manuals by other brands
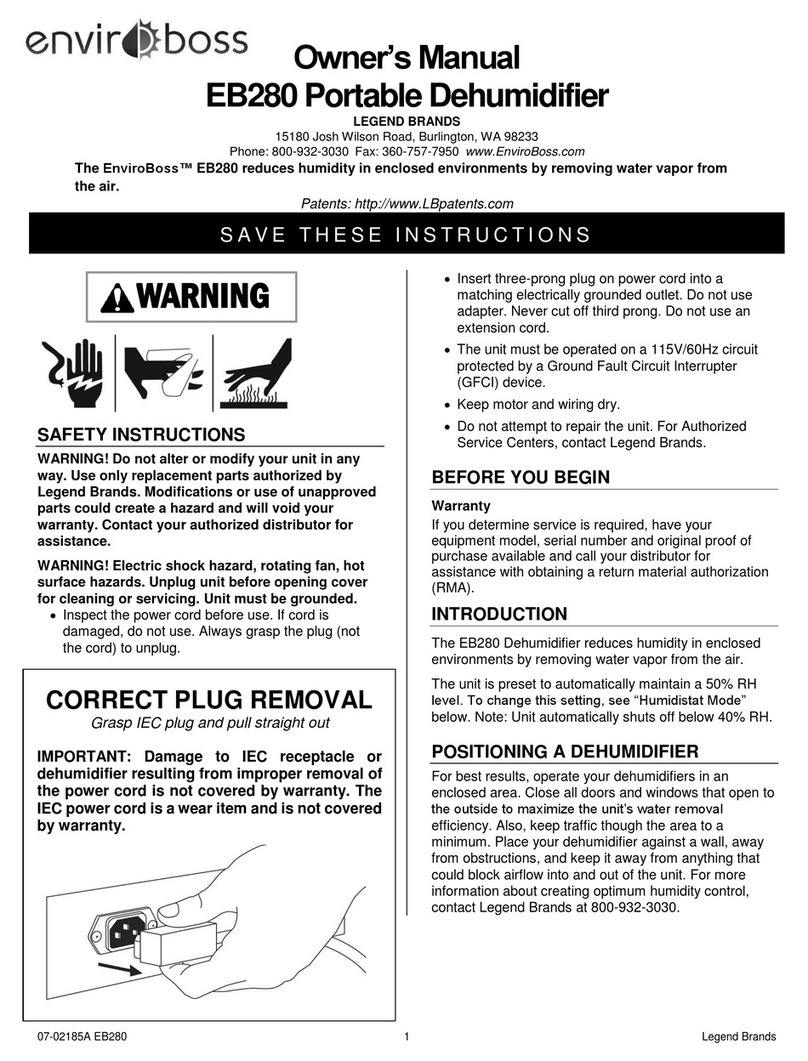
ENVIROBOSS
ENVIROBOSS EB280 owner's manual

White Industries
White Industries Diagnostic 1090AT Operation and maintenance manual
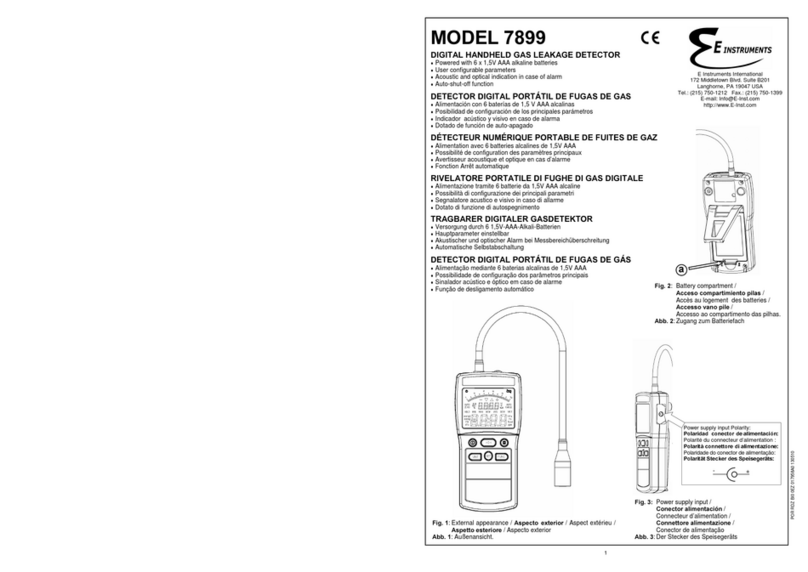
E Instruments
E Instruments 7899 manual
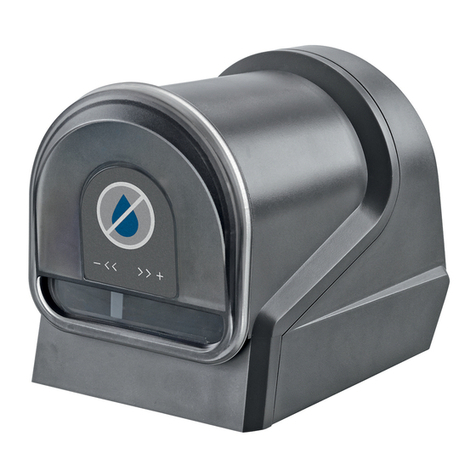
Oase
Oase FishGuard operating instructions
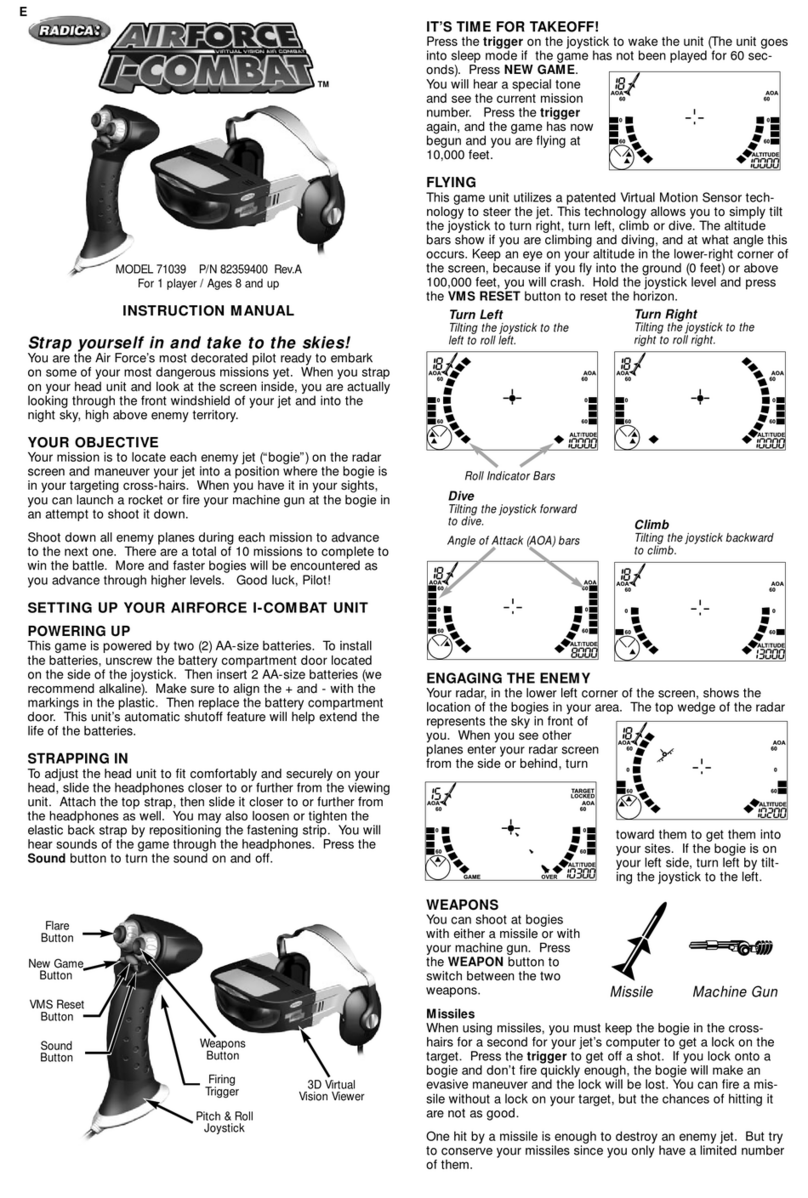
Radica Games
Radica Games Air Force I-COMBAT 71039 instruction manual
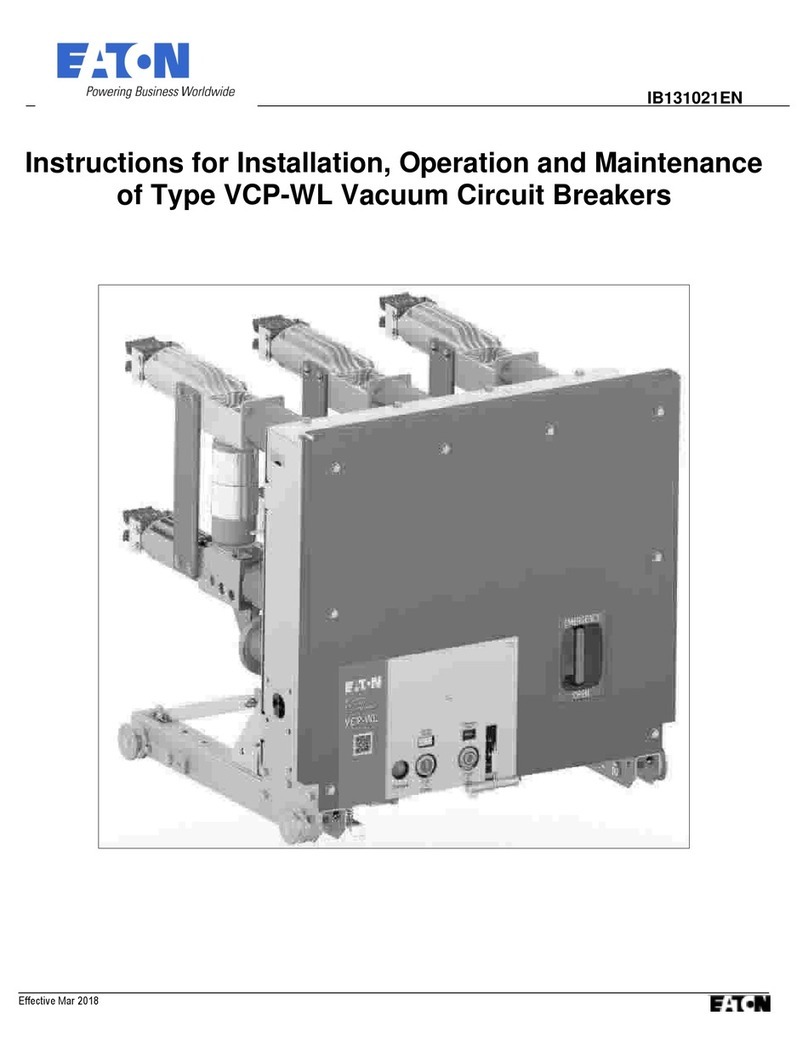
Eaton
Eaton 150 VCP-WL Instructions for installation, operation and maintenance