Titan Attachments STANDARD Series User manual

STANDARD SERIES ROTARY CUTTERS
STSRC48, STSRC60
191585, 191586
Operator’s Manual
Read the Operator’s Manual entirely.
When you see thissymbol, the
subsequent instructions and warnings are
serious follow without exception. Your life
and the lives of others depend on it!

2
IMPORTANT SAFETY INFORMATION
THESE ARE STANDARD PRACTICES THAT MAY NOT APPLY TO THE PRODUCTS
DESCRIBED IN THIS MANUAL.
SAFETY AT ALL TIMES
Thoroughly read and understand the instructions given in this manual before operation. Refer
to the “Safety Label” section, read all instructions noted on them. Do not allow anyone to
operate this equipment who has not thoroughly read and comprehended this manual. Do not
allow anyone who has not adequately trained in the safe operation of the equipment.
•The operator should be familiar with all functions of the unit.
•Operate implement from the driver’s seat only.
•Make sure all guards and shields are in place and secured before operating the tool.
•Do not leave a tractor or implement unattended with the engine running.
•Dismounting from a moving tractor could cause severe injury or death.
•Do not allow anyone to stand between tractor and implement while backing up to
implement.
•Keep hands, feet, and clothing away from power-driven parts.
•Wear snug-fitting clothing to avoid entanglement with moving parts.
•Watch out for wires, trees, etc., when raising implements. Make sure all persons are
clear of the working area.
•Turning the tractor too tight may cause implement to ride upon wheels. This activity
could result in injury or equipment damage.
•Do not carry passengers on the tool at any time.
LOOK FOR THE SAFETY ALERT SYMBOL
The SAFETY ALERT SYMBOL indicates a potential hazard to personal safety, and individuals
must take safety precautions. When you see this symbol, be alert and carefully read the
message that follows it. In addition to the design and configuration of equipment, hazard
control and accident prevention depend on the awareness, concern, prudence, and proper
training of personnel involved in the operation, transport, maintenance, and storage.

3
BE AWARE OF SAFETY ALERT WORDS
DANGER: Indicates imminently hazardous practices. A situation that, if not avoided, will result in
death or severe injury. The signal word is limited to the most extreme situation, typically for
machine components that, for functional purposes, cannot be guarded.
WARNING: Indicates a potentially hazardous situation that, if not avoided, could result in death or
severe injury, and includes hazards that are exposed when guards remove. Use warnings to alert
against unsafe practices.
CAUTION: Indicates a potentially hazardous situation that may result in minor or moderate injury
if not avoided. It may also be used to alert against unsafe practices.
FOR YOUR PROTECTION
Thoroughly read and understand the “Safety Label” section, read all instructions noted on them.
SHUTDOWN AND STORAGE
•Lower machine to the ground, put the tractor in park, turn off the engine, and remove the
key.
•Detach and store implements in an area where children typically do not play
USE SAFETY LIGHTS AND DEVICES
•Slow-moving tractors, self-propelled equipment, and towed implements can create a hazard
when driven on public roads. They are challenging to see, especially at night.
•Flashing warning lights and we recommend turn signals whenever driving on the public
road.
TRANSPORT MACHINERY SAFELY
•Comply with state and local laws
•The maximum transport speed for implement is 20 mph, DO NOT EXCEED. Never travel at a
rate that does not allow adequate control of steering and stopping. Some rough terrain
requires a slower speed.
•Sudden braking can cause a towed load to swerve and upset. Reduce speed if the towed
load is not equipped with brakes.
Use the following maximum speed –tow load weight ratios as a guideline:
•20 mph when weight is less than or equal to the weight of the tractor.
•10 mph when weight is double the weight of the tractor.
IMPORTANT: Do not tow a load that is more than double the weight of the tractor.
KEEP RIDERS OFF MACHINERY
•Riders obstruct the operator’s view; they could be struck by foreign objects or thrown from
the machine.
•Never allow children to operate equipment.
•Practice Safe Maintenance
•Understand procedure before doing work. Use proper tools and equipment; refer to

4
Operator’s Manual for additional information.
•Work in a clean, dry area
•Lower the implement to the ground, put the tractor in park, turn off the engine, and remove
the key before maintenance.
•Allow implement to cool completely.
•Do not grease or oil implement while it is in operation.
•Inspect all parts. Make sure details are in good condition and installed correctly.
•Remove the buildup of grease, oil, or debris.
•Remove all tools and unused parts from implementation before operation.
PREPARE FOR EMERGENCIES
•Be prepared if a fire starts.
•Keep a first aid kit and fire extinguisher handy
•Keep emergency numbers for doctor, ambulance, hospital, and fire department near the
phone.
WEAR PROTECTIVE EQUIPMENT
•Wear protective clothing and equipment appropriate for the job. Avoid loose-fitting clothing.
•Prolonged exposure to loud noise can cause hearing impairment or hearing loss. Wear
suitable hearing protection such as earmuffs or earplugs.
•Operating equipment safety requires the full attention of the operator. Avoid wearing radio
headphones while operating machinery.
AVOID HIGH-PRESSURE FLUIDS HAZARD
•Escaping fluid under pressure can penetrate the skin causing severe injury.
•Avoid the hazard by relieving pressure before disconnecting hydraulic lines or performing
work on the system.
•Ensure all hydraulic fluid connections are tight and all hydraulic hoses and lines are in good
condition before applying pressure to the system.
•Use a piece of paper or cardboard, NOT BODY PARTS, to check for suspected leaks.
•Wear protective gloves and safety glasses or goggles when working with hydraulic systems.
•If an accident occurs, see a doctor immediately. Remember, any fluid injected into the skin
must be treated within a few hours, or gangrene may result
TIRE SAFETY
•Tire changing can be dangerous, and trained personnel should be the only ones using
correct tools and equipment.
•When inflating tires, use a clip-on chuck and extension hose long enough to allow you to
stand to one side and NOT in front of or over the tire assembly. Use a safety cage if
available.
•When removing and installing wheels, use wheel handling equipment adequate for the
weight involved.

5
Warning
Danger: Keep hands and feet away
SAFETY LABELS
Your rotary cutter comes equipped with all safety labels in place. They were designed tohelp
you safely operate your implement. Read and follow the directions.

6
This shows the grease position.
Caution: 540 RPM PTO speed
Caution: Fill gearbox
with SAE 90gear lube
SSAFETY LABELS

7
INTRODUCTION
APPLICATION
TITAN Standard Series Rotary Cutters (STSRC) are ideal for clearing grass, weeds, and light
brush.These cutters offer fast, clean, dependable mowing, and have been extensively
tested to ensure safety. High blade tip speeds assure a clean cut in a variety of field
conditions. This Rotary cutter is adapted for standard Category 1 –three-point hitch or
Quick-Hitchsystem mounting. It’s recommended to equip a slip clutch PTO shaft.
SECTION 1: ASSEMBLY AND SET-UP
TRACTOR REQUIREMENTS
Tractor horsepower should be within the range noted below. Tractors outside the
horsepower range must not be used. Must be using a minimum of 40 hp when operatingat
maximum capability. The lower 3-Point arms must be stabilized to prevent side to side
movement. Most tractors have sway blocks or adjustable chains for this purpose.
WARNING
To avoid serious injury or death:
Lightweight tractors with rear attached implements may need weights added to the front to
maintain steering control.
Consult your tractor Operator’s Manual to determine proper weight requirements and maximum
weight limitations.

8
PACKING DESCRIPTION
1. REMOVE AND CHECK
Remove the packing and check goods to if there are any defects or part omission.
Figure 1-1: Your New Standard Rotary Cutter as it is shipped to You
Figure 1-2: The STSRC cutter and Accessory in Package

9
2. PACKING LIST
The detailed packing list of the mower and accessory as the following table 1-1.
ITEM
DESCRIPTION
QTY
PACKAGE FORM
(1)
MAIN BODY
1
NONW
(2)
FRONT AND REAR BRACES
1
BUBBLE FILM
(3)
DRIVELINE SHAFT WITH CLUTCH
1
BUBBLE FILM
(4)
WHEEL TIRE ASSEMBLY AND FITTINGS
1
BUBBLE FILM
(5)
PIVOTING UPPER HITCH-BLACK AND FITTINGS
1
BUBBLE FILM
(6)
TAILWHEEL ADJUTING BRACKET AND FITTING
1
BUBBLE FILM
(7)
R&L SKUD WELDMENT AND FITTING
1
BUBBLE FILM
(8)
IRON CRATE
1
NONE
(9)
REMOVABLE ANGLE STEEL
2
CRATE ATTACHMENT
(10)
LOCK NUT M10
12
CRATE ATTACHMENT
(11)
BOLT M10*20
8
CRATE ATTACHMENT
(12)
REMOVABE ANGLE STEEL SUPPORT
2
CRATE ATTACHMENT
(13)
BOLT M10*25
4
CRATE ATTACHMENT
(14)
PLAIN WASHER 10
4
CRATE ATTACHMENT
Table 1-1: Packing List of The Standard Rotary Cutter and Accessory
The detailed description of front and rear braces
Figure 1-3: Front and Rear Braces
ITEM
DESCRIPTION
QTY
(1)
REAR BRACE
2
(2)
FRONT BRACE
2
Table 1-2: Front and Rear Braces

10
The detailed description of wheel tire assembly and fittings
Figure 1-4: Wheel Tire Assembly and Fittings
ITEM
DESCRIPTION
QTY
(1)
RUBBER TIRE ASSEMBLY
1
(2)
SPACER H=6
2
(3)
CAP SHAFT MOUNT
1
(4)
SAFETY LOCK PIN 8*45
1
Table 1-3: Wheel Tire Assembly and Fittings List
The detailed description of pivoting upper hitch-black and fittings
Figure 1-5: Pivoting Upper Hitch-Black and Fittings

11
ITEM
DESCRIPTION
QTY
(1)
SAFETY LOCK PIN 11*50
1
(2)
HITCH PIN –UPPER
1
(3)
PIVOTING UPPER HITCH –BLACK
1
(4)
PLAIN WASHER 16
2
(5)
BOLT M16*110
1
(6)
SPACER
2
(7)
LOCKNUT M16
1
Table 1-4: Pivoting Upper Hitch-Black and Fittings List
The detailed description of tailwheel adjusting bracket and fittings
Figure 1-6: Tailwheel Adjusting Bracket and Fittings
ITEM
DESCRIPTION
QTY
(1)
LOCKNUT M16
2
(2)
PLAIN WASHER 16
4
(3)
BOLT M16*55
2
(4)
GAUGE WHEEL MAINFRAME
WELDMENT
1
(5)
PLAIN WASHER 12
4
(6)
BOLT M12*40
2
(7)
LOCKNUT M12
2
Table 1-5: Tailwheel Adjusting Bracket and Fittings List

12
The detailed description of R&L skid weldment and fittings
Figure 1-7: R&L Skid Weldment and Fittings
ITEM
DESCRIPTION
QTY
(1)
SKID WELDMENT –R
1
(2)
RHSNB M10*25 GRID10.9
8
(3)
PLAIN WASHER 10
8
(4)
LOCKNUT M10
8
(5)
SKID WELDMENT - L
1
ASSEMBLY INSTRUCTIONS
The assembly instruction will guide you to finish the final assembly of your newstandard
rotary cutter.
TOOL REQUIRED
•1/2” Ratchet Wrench with 17mm, 19mm and 24mm sleeves
•17-19 spanner, 22-24 Spanner
TORQUE APPLICATION
Refer to bolt torque in Section 7 Appendix.
ASSEMBLY
STEP 1: INSTALLING FRONT & REAR BRACES, PIVOTING UPPER HITCH-BLACK,
TAILWHEEL ADJUSTINGBRACKET AND FITTINGS
Remove the packaging of front & Rear braces, pivoting upper hitch-black, tailwheel
adjusting bracket and fittings.
Installing front & rear braces, pivoting upper hitch-black, tailwheel adjusting bracket and
fittings onto main body of the rotary cutter according to the figure 1-8.

13
Tighten item 7, item 17 completely. Tighten item10 but make sure item6 & item13 can
rotate freely.
Item 1 –Main body of the rotary
cutter
Item 2 –Front brace (2pcs)
Item 3 –Rear brace (2pcs)
Item 4 –Plain washer16 (6pcs)
Item 5 –Bolt M16x55 (2pcs)
Item 6 –Gauge wheel mainframe
weldment (1 set)
Item 7 –Locknut M12 (2pcs)
Item 8 –Plain washer 12 (4pcs)
Item 9 –Bolt M12x40 (2pcs)
Item 10 –Locknut M16 (3pcs)
Item 11 –Bolt M16x110 (1pcs)
Item 12 –Spacer (2pcs)
Item 13 –Pivoting upper hitch-black
(1pcs)
Item 14 –Hitch pin lower (2pcs)
Item 15 –Plain washer 22 (2pcs)
Item 16 –Spring washer 22 (2pcs)
Item 17 –Hex Nut M16 (2pcs)
Pivoting Upper Hitch-Black, Tailwheel Adjusting Bracket andFittings

14
STEP 2: INSTALLING RIGHT & LEFT SKID WELDMENT AND FITTINGS
Remove the packaging of R&L skid weldment and fittings.
Align lower link arms of tractor to hitch and lower hitch pins into lower ball swivels.
Attach tractor top link arm to the pivoting upper hitch-black with hitch pin upper supplied. Secure
with safety lock pin.
Raise rotary cutter from the ground. Install R&L skid weldment onto the rotary cutter. Tighten
locknuts completely.
Item 1 –RHSNB M10x25 GR10.9 (8pcs)
Item 2 –Skid weldment –L (1pcs)
Item 3 –Plain washer 10 (8pcs)
Item 4 –Locknut M10 (8pcs)
Item 5 –Main body of the rotary cutter
Item 6 –Skid weldment –R (1pcs)
Figure 1-9: Installing R&L Skid Weldment and Fittings

15
STEP 3: INSTALLING WHEEL TIRE ASSEMBLY AND FITTINGS
Remove the packaging of wheel tire assembly and fittings.
Remove item4, item5 and one piece of item3 from wheel tire assembly. Insert the pivotshaft of
wheel tire assembly into the bushing of the gauge wheel mainframe weldment and reinstall item4
to item5.
Secure with item3.
Item 1 –Main body of the rotary cutter
Item 2 –Wheel tire assembly –(1 set)
Item 3 –Spacer H=6 (2pcs)
Item 4 –Cap shaft mount (1pcs)
Item 5 –Safety lock pin φ8x45 (1 pcs)
Figure 1-10: Installing Wheel Tire Assembly and Fittings
WARNING
SAE EP 90W Gear oil must be your first use.Overfilling or under filling gear oil may cause gearbox seizing
or damage.
4. GEAR OIL FILLING
Check oil level in gearbox by removing the cap located on the side of the gearbox. Oil should be
level with middle side of plug hole. Add necessary oil by removing top cap andside plug. Add oil until
it flows from middle side plug hole.
Item 1 –Cap for inlet gearbox oil
Item 2 –gearbox
Item 3 –Plug for gearbox oil level
Figure 1-11: Gearbox construction

16
TRACTOR HOOK UP
DANGER
To avoid serious injury or death:
A crushing hazard exists while hooking-up and unhooking the implement. Keep people and animals away
while backing-up to the implement or pulling away from the implement. Do not operate hydraulic
controls while a person or animal is directly behind the power machine or near the implement.
WARNING
To avoid serious injury or death:
Lightweight tractors with rear attached implements may need weights added to the front to maintain
steering control.
Consult your tractor Operator’s Manual to determine proper weight requirements and maximum weight
limitations.
Refer to Figure 1-12:
1. Slowly back tractor up to rotary cutter while using tractor’s 3-Point hydraulic control
lever to align lower lift arm hitch holes with cutter hitch pins. (Item 2)
2. Always Disengage power take-off, engage tractor park brake, shut tractor engine off,
and remove switch key before dismounting from tractor.
3. Slide lower 3-point lift arms onto cutter hitch pins (Item 2). Secure hitch pins with
safety lock pins (Item1).
4. Connect hitch hole in top center 3-Point link to upper clevis hitch with top hitch pin
(Item 4) and safety lock pins (Item1).
5. Ensure that the lower hitch arms are locked to prevent excessive side movement.
6. Return to tractor and slowly raise and lower implement carefully to ensure drawbar
tires, and other equipment on the tractor do not contact cutter frame and driveline.
Move or remove drawbar as needed.
7. Manually adjust one of the two lower 3-point lift arms up or down to level the rotary
cutter from left to right. Final adjustments will be made later during “Deck leveling &
Cutting Height” on page 21.
8. The arm lift rods on your tractor’s 3-point lift arm should be adjusted to allow for
lateral float. Please consult your tractor’s manual for adjusting instructions.

17
Figure 1-12: Tractor Hook-Up
DRIVELINE HOOK-UP
DANGER
To avoid serious injury or death:
•Tractor power take-off shaft shield, driveline shields, and implement input shield must be
installed and in good working condition to avoid driveline entanglement and projectiles
dislodging of the driveline.
•Do not engage power take-off while hooking-up or unhooking the driveline, or while
someone is standing near the driveline. A person’s body and/or clothing can become
entangled in the driveline.
•Do not use a power take-off adapter. The adapter will increase strain on the tractor’s
power take-off shaft causing possible damage to shaft and driveline. It will also defeat the
purpose of the tractor’s power take-off shield.
•Make sure driveline yokes are securely fastened at each end. A loose yoke can work free
allowing the driveline to rotate uncontrollably causing implement damage and bodily
injury or death to anyone nearby.
WARNING
To avoid serious injury or death:
•Always follow “Tractor Shutdown Procedure” provided in this manual before
dismounting the
tractor.
•Check driveline when lowering implement to make sure it does not interfere with the
tractor drawbar at maximum depth. If needed, shut tractor off and move or remove
drawbar to prevent driveline damage.

18
IMPORTANT:
An additional driveline may be required if implement is attached to more than one tractor or if a Quick
Hitch is used.
Drivelines with friction clutches must go through a “run-in” prior to initial use and after long periods of
inactivity. For detailed instructions, see “Slip-Clutch Protected Driveline” on page 30. Check driveline
minimum collapsible length before completing “Driveline Hook-Up” on page 17. Structural damage to
the tractor and implement can occur if this check is not made. Refer to “Check Driveline Collapsible
Length” on page 18.
1. If driveline collapsible length has not been checked, go to “Check Driveline Collapsible Length”
on page 18. Otherwise, continue with step 2.
2. Park tractor and implement on a level surface.
3. Shut tractor down before dismounting. Refer to “Tractor Shut down Procedure” on page 26.
4. If tractor drawbar interferes with the driveline during hook-up, disconnect driveline and move
drawbar forward, to the side, or remove.
5. Collapse driveline (Item3) by pushing tractor end of driveline toward the cutter gearbox.
6. Push in on push pin on the driveline and slide outer driveline universal joint over tractor power
take-off shaft.
7. Release push pin on the driveline and continue to slide universal joint over tractor power take-
off shaft until push pin releases and pops up.
8. Pull on driveline yokes at the tractor and implement end to make sure they are secured to the
tractor power take-off shaft and implement gearbox shaft.
9. The tractor’s lower 3-point arms should be adjusted for lateral float. Please consult your
tractor’s manual.
10. Continue with “Check Driveline interference” on Page 20.
CHECK DRIVELINE COLLAPSIBLE LENGTH
Refer to Figure 1-13:
IMPORTANT:
Two small chains are supplied with the driveline to keep driveline shields from rotating. These chains
must be attached to the outer and inner driveline shields and attach to the rotary cutter & tractor.
A driveline that is too long will bottom out causing structural damage to the tractor and mower.
Always check driveline collapsible length during initial setup and when connecting to a different
tractor. More than one driveline may be required to fit all applications.
The power take-off shaft and implement input shaft must be aligned and level with each other when
checking driveline minimum length. A driveline that is too long can damage tractor and implement.

19
1. With driveline attached only to the implement, remove outer driveline (tractor end)from
inner driveline to separate the two profiles.
2. Park tractor and implement on a level surface.
3. Raise implement until gearbox input shaft is level with tractor power take-off shaft.
Securely block implement at this height to keep until from lowering.
4. Shut tractor down without removing support blocks. See “Tractor Shutdown
Procedure”on page 26.
5. Attach outer driveline to the tractor’s power take-off shaft. Refer to steps 5-8 under
“Driveline Hook-Up”on page 17.
6. Hold inner and outer drivelines parallel to each other, or as close to parallel as possible. If
dimension “A” is greater thanor equal to 1”, then skip to “Reassemble Driveline” on page 20.
Otherwise continue with step 7.
a) Measure from end of inner shield
to scribed mark (“X” dimension)
and record.
b) Cutter off inner shield at the
mark. Cut same amount off the
inner shaft (“X1” dimension).
c) 10. Cut off non-yoke end of outer
driveline as follows:
d) Measure from end of outer shield
to scribed mark (“Y” dimension)
and record.
e) Cutter off outer shield at the
mark.
SHORTEN DRIVELINE LENGTH
Refer to Figure 1-14:
7. If dimension “A” is less than 1”, shorten
driveline as follows:
a. Measure 1" (“B1” dimension) back from outer driveline shield and make a mark
at this location on the inner driveline shield.
b. Measure 1" (“B2” dimension) back from the inner driveline shield and make a
mark at this location on the outer driveline shield.
8. Remove outer driveline from the tractor power take-off shaft and inner driveline from the
implement’s gearbox shaft.
9. Cut off non-yoke end of inner driveline as follows:

20
REASSEMBLE DRIVELINE
Refer to Figure 1-14:
1. Apply multi-purpose grease to the
inside of the outer shaft and
reassemble the driveline.
2. Reattach driveline to tractor power
take- off shaft and gearbox shaft,
Refer to “Driveline Hook-Up” on page
17.
3. Continue with “Check Driveline
interference” on page 20.
Figure 1-14: Driveline Shortening CHECK
DRIVELINE INTERFERENCE
Refer to Figure 1-15:
WARNING
To avoid serious injury or death:
A rotating driveline must not exceed an
angle of 25 degrees up or down, and never
engage a driveline while at an angle
exceeding 25 degrees up or down. The
driveline can break and send projectiles.
1. Start tractor and raise implement
slightly off the support blocks used to
“Check Driveline Collapsible
Length”. Drive forward until the
implement is clear of the support
blocks.
2. Slowly and carefully lower and raise
the implement to ensure drawbar,
tires, and other equipment on the
tractor do not contact the
implement’s frame. If there is an
interference:
a. Back implement over the support
blocks and lower it onto the
blocks.
b. Shut tractor down before
dismounting. Refer to “Tractor
Shutdown Procedure” on page
26.
c. Move or remove drawbar if
interferes with the implement
and make any other necessary
corrections
d. Repeat steps 1-2 to verify the
implement does not interfere
with the tractor.
3. Start tractor, raise implement fully up.
Back implement over the support blocks.
Do not lower implement onto the
support locks.
4. Without changing the 3-point lift height,
shut tractor down using
“Tractor Shutdown Procedure” on
page 26.
5. Check to make sure driveline does not
exceed 25°above horizontal.
6. Start tractor, raise implement slightly,
and drive forward enough to clear the
support blocks.
7. Lower implement to ground and shut
tractor down using “Tractor Shutdown
Procedure”on page 26.
Figure 1-15: Maximum PTO driveline movement
range during operation
This manual suits for next models
4
Table of contents
Other Titan Attachments Power Tools manuals
Popular Power Tools manuals by other brands
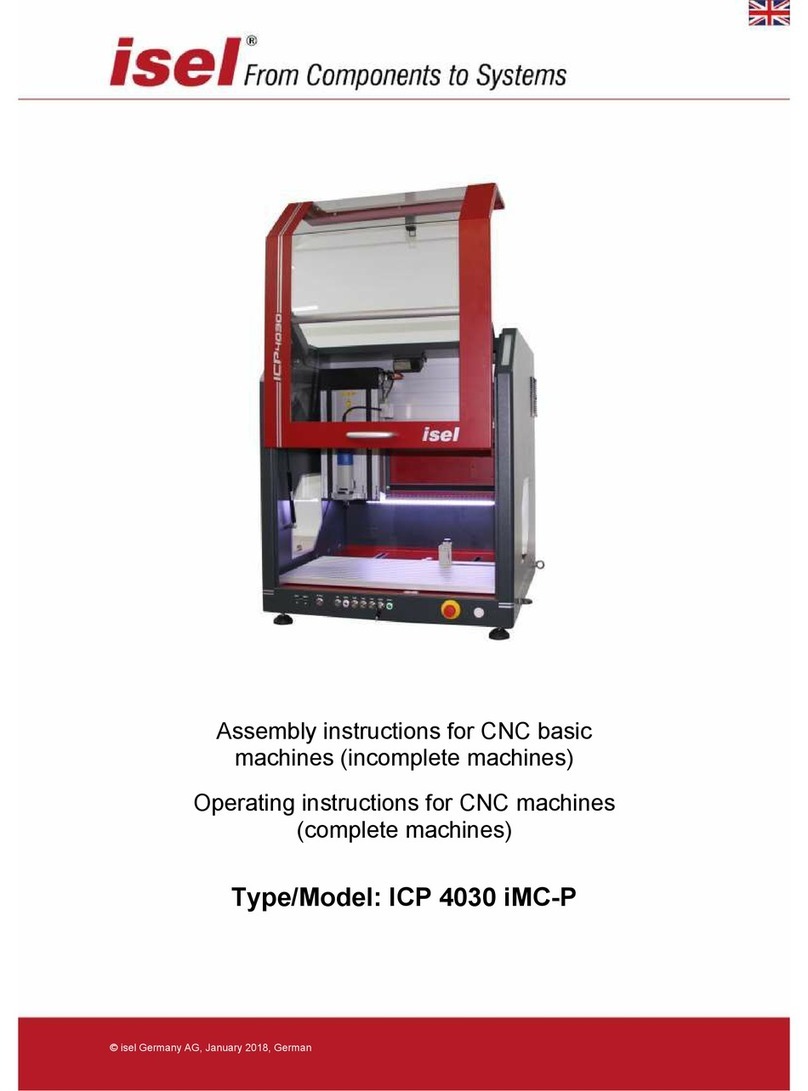
Isel
Isel ICP 4030 iMC-P Assembly instructions/Operating instructions
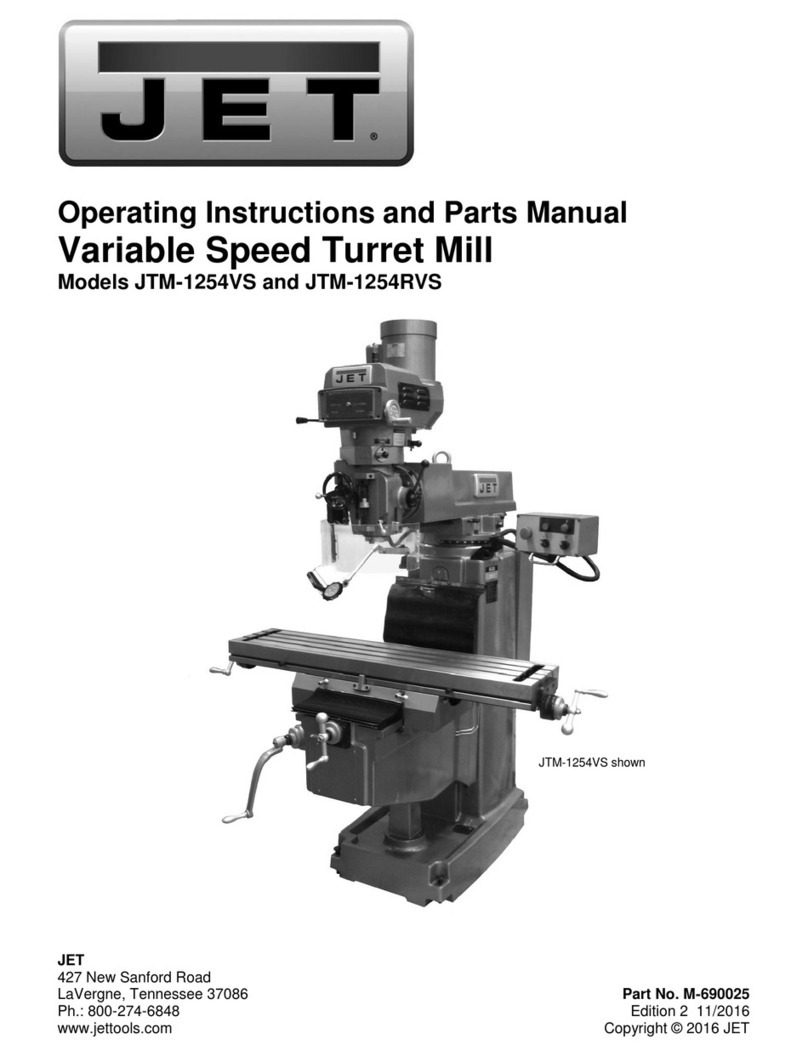
Jet
Jet JTM-1254VS Operating instructions and parts manual
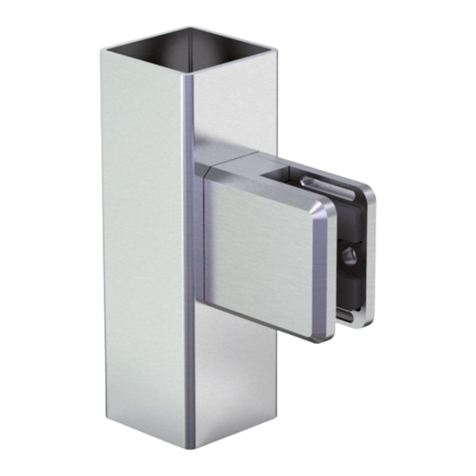
Pauli + Sohn
Pauli + Sohn 4845VA2-A2-V Assembly instructions
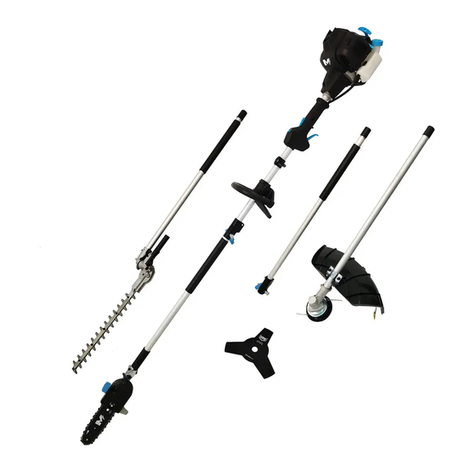
Mac allister
Mac allister M5MTP25-3 manual

Bosch
Bosch 1534 Operating/safety instructions
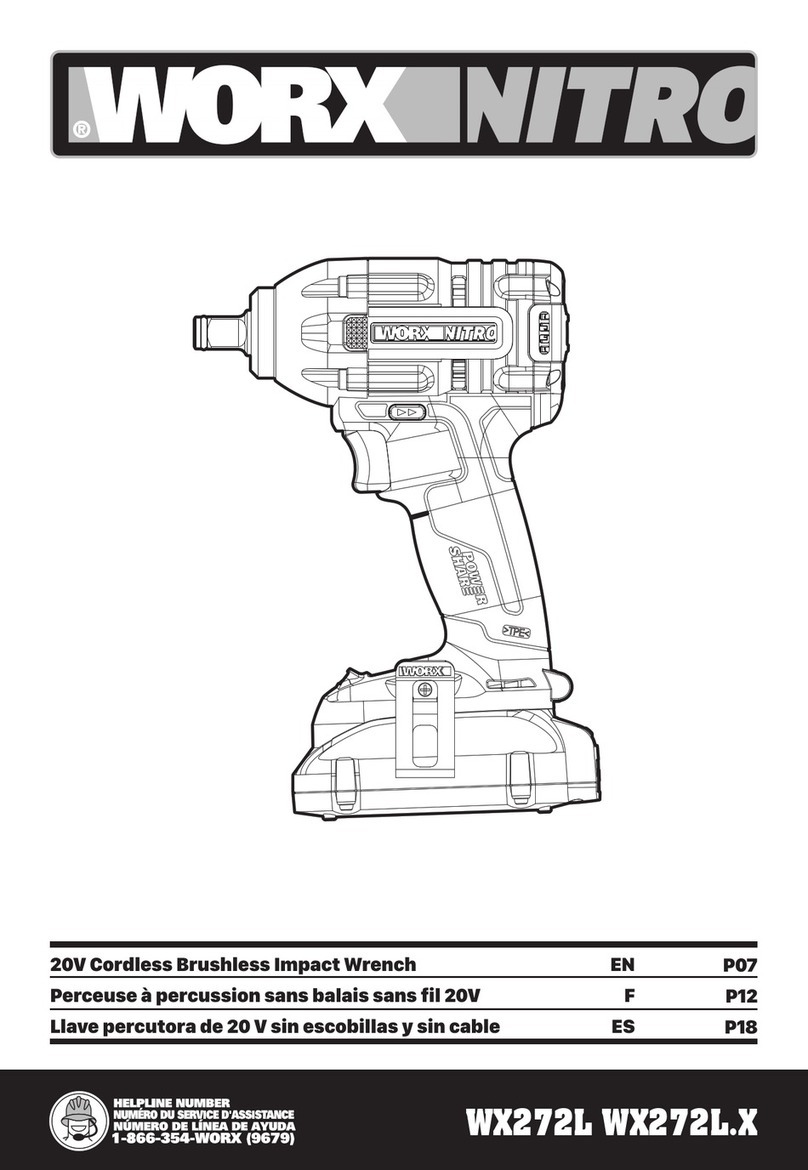
Worx Nitro
Worx Nitro WA3520 user manual