Toho Electronics TTM-300 Series User manual

TOHO ELECTRONICS INC.
TTM-300 SERIES
PROGRAM CONTROLLER
INSTRUCTION MANUAL
Thank you for purchasing model TTM-300 series Program Controller.
The units of Model TTM-300 series are The Easy-to-Use Program Controller
to drive the units as per program capa le 64 patterns(max.) x num ers of step,
and also equipped the communication functions using RS-485 as an option.
Please go through this Instruction Manual carefully and use the unit in proper
manner.
CONTENTS:
1. NOTICE/WARNING BEFORE USAGE
2. INSTALLATION METHOD AND PARTS INDICATION
3. WIRING METHOD
4. OPERATIONAL DEFINITIONS AND FUNCTIONS
5. PRECAUTION OF PROGRAM DRIVE
6. OPERATION FLOW AND PARAMETER INFORMATION
7. SETTING RANGE AND INDICATION RANGE TABLE
8. ORDERING INFORMATION
9. STANDARD SPECIFICATIONS
10. MAINTENANCE AND INSPECTIONS

1
1. NOTICE/WARNING BEFORE OPERATION
• Confirm the merchandises at hand shows the correct model and optional function.
For confirmation of model name, please refer to [8.
ORDERING INFORMATION
].
• The following sym ol marks are used in this Instruction Manual for handling this model safely.
In case of mishandling, serious danger may occur to the
operator such as death, electrocution and a skin burn.
In case of mishandling, it may cause some damage to the
unit or the operator getting slight injury.
CAUTION
・Do not push the keys by sharp points(i.e. Ball-point-
pen, metals) for prevention of its
malfunction.
WARNING
・ake sure the correct wiring connection before turning on electricity.
iswiring may cause malfunction of the unit and may cause a fire.
・Never remodel the unit for prevention of malfunction of unit and a fire.
• Types of Input(Thermocouple←→R.T.D.) and Output cannot e changed after receiving the unit.
• Check, if all the attachments are at your hand.
• Instruction Manual ·······································1 ooklet
• Installation attachment ·································1 piece (TTM-304)
• Fitting metals················································1 set (TTM-305,309)
• Unit seal ·······················································1 seal paper
In case any of the a ove is missing or found a different included, inform to us accordingly.
• If you have selected an optional communication function and requiring "Instruction Manual of Communication
Function", please ask us to mail it separately.
• Please put this Instruction Manual aside of the operator of unit.
• Copy or Reprint of this manual, wholly or partially, is not allowed.
• The contents of this manual may change without notice in future.
• Please e noted that we shall not e responsi le to all of the defaults resulted y using of the unit.
WARNING
CAUTION

2
2. INSTALLATION METHOD AND PARTS INDICATION
2.1 Name of Parts and Definition
LED LA P
RUN :Light On at RUN mode Indicate PV
OUT :Light On when output (Process Varia le)
of main controller. Blink Light on
according to the operation volume
at continuous proportion. Indicate SV
▲ :Light On when set value goes up. (Setting Value)
▼ :Light On when set value goes down.
OPERATION KEYS
MODE : Changing the display in each mode.
▲&▼ : Changing set values
TIME/TEMP : Changing "TIME" or "TEMPERATURE" indicate
RUN/STOP : Changing Reset mode or Run mode
PTTN/STEP : RUN mode→Changing PTTN/STEP confirmation mode
RESET : RUN mode→RESET mode
The details of Operation Keys to e referred to "6.OPERATION FLOW AND PARAMETER INFORMATION".
2.2 DIMENSIONS Panel Cut) 2.3 OUTER DIMENSIONS
P V
SV
RUN OUT
TTM -3 0 4
MODE TIME
TEMP
PTTN
STEP
RUN
STOP
RESET
※L
more than d
a
b
more than c
CD
A
B
PV
SV
RUN OUT
TT M - 3 0 4
MODE TIME
TEMP
PTTN
STEP
RUN
STOP
RESET
MODEL A B C D a b c d
TTM-304 48 48 8 100
45
0
0 6
−
+.
45
0
0 6
−
+.
60 48
TTM-305 96 48 11 80
45
0
0 6
−
+.
92
0
0 8
−
+.
120 48
TTM-309 96 96 11 80
92
0
0 8
−
+.
92
0
0 8
−
+.
120 96
※In case of Continuous Mounting to N:L=(d×N-3)
−
+
0
1
CART OF PANEL CUT & OUTER DIMENSIONS

3
2.4 Mounting Method
In case of TTM-304 In case of TTM-305 & TTM-309
・In case of using crimp-style terminals, eware of other
terminals not e damaged. ・Install one each of fitting metals
oth on upper/lower side and fasten
it with a screw driver.
2.5 Location of installation:
Install the unit at the following proper locations.
• Temperature and Humidity are within the limit of operation environment.
• Away from the gas of sulfide and corrosion.
• Less dust and oily smoke.
• Less mechanical vi ration and shock.
• Away from High-Voltage wire, Welding machine and the generator of electric noise.
• Far away from the equipments using high-voltage ignition devices.
• Away from the influence of electromagnetic field.
• Away from the direct sunshine and not to e exposed y wind and rain.

4
3. WIRING METHOD
3.1 Terminal Connection Drawing
1
2
3
4
5
6
7
8
9
11
12
13
14
10
1
2
3
4
5
6
7
8
9
10
11
12
13
14
15
16
17
18
19
20
1
2
3
4
5
6
7
8
9
10
11
12
13
14
15
16
17
18
19
20
21
22
23
24
25
26
27
28
29
30
1
2
24VAC or DC
1
2
85~264VAC
6
7
Event output1
8
9
Event output2
10
11 Comm.TR(A)
TR(B)
13
14
-
+
10
11 Run signal
13
14
Curr.
・
Volt.
-
+
TT M - 3 0 4
TT M - 3 0 5
2
3
24VAC or DC
1FG
2
3
85~264VAC
1FG
4
5
Comm.
TR(A)
TR(B)
4
5
RUN signal
3
4
SSR Drive Volt.
+
-
(Curr.,Volt. output)
5
Relay contact 3
NC
4NO
C
8
9
+
-
10
8
NC
9
NO
C
11
12
13
14
15 SG
9SG
13
14
12 b
B
A
19
20
-
+
19
20
-
+
19
20
18 b
B
A
Refer to
TTM-305
1~10
21
22
23
24
25 SG
29
30
-
+
29
30
-
+
29
30
28 b
B
A
TTM - 3 0 9
TC
R.T.D.
SSR Drive Volt. Relay contact
(Curr.,Volt. output)
Event output1
Event output2
TC
R.T.D.
Curr.
・
Volt.
Event output1
Event output2
TC
R.T.D.
Curr.
・
Volt.

5
3.2 Example of Wiring:
In case of the Heating Furnace with voltage of 85~265V AC, Thermocouple Input and Relay Contact Output.
85~264V AC
Power Source
TTM-300 magnet Heating Furnace
Relay Contact Heater
NC
C
NO
Output Signal Line
Load line
Thermocouple
Input Signal Line
3.3 CAUTION AT WIRING CONNECTION
WARNING
・For prevention of electric shock, please do wiring connection only after turning off Power.
CAUTION
・This unit does not function for approx. 4 seconds after turning on Power.
(No function at Output side)
Please e cautious when this unit is used as Interlock circuit.
・For prevention of miswiring, please make sure to confirm the name la els i.e. Input terminal
Power source terminal and Option terminals etc. eside the each wire.
・The crimp terminals for wiring should e fit with the nuts of M3.5. As for the wiring to center terminal, use the
lead-wire and fasten on it.
・The wiring material to connect R.T.D. and this unit should e used the one having wire resistance less than 5Ω per
wire.
・The wiring material to connect Thermocouple and this unit should e used the specified extension leadwire of
thermocouple or leadwire itself.
・In case this unit should e used close to the noise generators, please use shield-wires.
Please do not wire the Input/Output lines inside of the same duct and the pipes of electric wires.
・ The signal wire of Input/Output should e away from power supply and loaded lines at least 50cm.

6
4. OPERATIONAL DEFINITIONS AND FUNCTIONS
WAIT OPERATION: In case one step shifts to another step, the next step will not start even after step time elapsed
if the process varia le(PV) does not reach the wait zone or PV passed the wait zone.
However, the next step will start when the wait time elapsed.
At the wait operation, the indication at SV links.
: Wait Zone... This means the deviation area etween SV(Setting Value) and
PV(Process varia le) ena le to start next step.
RAMP STEP SOAK STEP
WAIT ZONE
WAIT ZONE
WAIT TIME
: Wait time... This means the maximum waiting period to start next step when
PV(Process varia le) does not reach to the SV(Setting Value).
RAMP STEP SOAK STEP
・ SV start: It will start from the setting value at the starting time of operation which to e treated as the PV(Process
varia le) or the target SV(Setting Value).
PV start...Operation will start from the Ramp step including the PV at the starting time of Program operation.
In case more than one step applied, it starts the one with smaller step num er.
Start operation from this point.
PV At these area, operation will
not start.
step 1 step2 step3 step4
SV start...At the set time of Step 1, operation starts from the specified SV(Set Value)
to the target set value(SV1) of Step 1.
Start operation from this point.
SV
step 1 step2 step3 step4
WAIT ZONE
WAIT ZONE
Soak step starts from this
Process varia le(PV) points
Target Setting Value(SV)
Soak step starts from this
Process varia le(PV) points
Target Setting Value(SV)
WAIT TIME

7
・EVENT OUTPUT: Process varia le(PV) to e used as Event Output, Time Signal and End Signal.
: PV a normal... In case Input indicates "Over" or "Under" y the cut-off of wire and short-circuit,
Event Output turns ON.
: Stand- y sequence...After starting operation of steps, Event Output does not turn ON unless the
process varia le(PV) reach the value of OFF stage of Event Output.
: Event Output Hold...Event Output holds "ON" stage unless altering setting of additional function or
resetting the power.
Process varia le(PV) Event Output: Starts Event Output function y setting of SV deviation or A solute Value
against Process varia le(PV). On the PV side indicator at "ON" stage, Outpiut1
indicates alternately PV and
,
and Output 2 indicates alternately PV and
.
Setting Value(SV) deviation(Example for Event Output 1) A solute Value(Example for Event Output 1)
1) High and Low limit 5) High and Low limit
2) High limit 6) High limit
3) Low limit 7) Low limit
4) High and Low limit range 8) High and Low limit range
・Time Signal, End Signal
Time Signal 1, 2 Time Signal 5
At step operation, Event Output turns ON
after passing ON Delay Time and turns OFF
after passing OFF Delay Time.
ON Delay time OFF Delay time
Event Output turns ON while Wait zone.
(Refer to page 6 Wait function)
Time Signal 3, 4 Time Signal 6, 7
Event Output turns ON when step operates and
turns OFF after passing Time Signal ON time.
Event Output turns ON when time signal reach
Wait zone and turns OFF after passing Time.
End Signal
Event Output turns ON after finishing pattern, and turns OFF after passing End Signal ON time.
P1C P1C
P1L P1H
SV
P1C
P1H
P1H
P1H
SV
P1C
P1L
SV
P1C P1C
P1L
P1C P1C
P1L P1H
P1H
SV
P1C P1C
P1L
O℃(
)
P1C
O℃(
)
P1C
P1L
O℃(
)
O℃(
)
ON
OFF
ON
OFF
WAIT ZONE
△ STEP START
ON
ON
OFF
OFF
SIGNAL ON
END SIGNAL ON TIME
△ WAIT ZONE
△ PATTERN FINISH
ON
OFF
TIME SIGNAL ON
△ STEP START

8
・LOOP ABNORMAL EVENT OUTPUT: A le to detect mis-attachment of the sensor.
Detecting function activates when the manipulated value lasts for a certain period either on its low or
high limit. On such condition ,EVENT OUTPUT turns ON.
In addition , the LOOP ABNORMAL EVENT will not provide any power failure compensation.
If the power falls down during detecting LOOP ABNORMAL EVENT OUTPUT, the time recorded
until such moment will e reset.
・OPERATION AT POWER ON:
RESET start... After the unit is activated from RESET mode, operation starts y pressing RUN/STOP key or RUN
Signal input.
OPERATION at
Power failure... In case of Power failure while the unit is running program, the unit runs program continuously if the
difference of the Process varia le(PV) etween
a)the one at Reset and b)the one efore Power failure limited within 10% or 10℃(18
). In
other cases, follow the same operation process of RESET start as descri ed a ove.
Continuous operation...
10% of a) or 10℃(18
) ≦ a -
・FUZZY Function: By Fuzzy logic, it compensates MV(Manipulation Value) worked out y PID control and controls
not to "Overshoot" or "Undershoot".
・FUZZY Strength: This means the strength of compensation (Strength 1 ~ 5) against MV worked out y PID
control.
Fuzzy strength 5 : Strongest compensation
Fuzzy strength 1 : Weakest compensation
・BLIND function: This function eliminates display of any mode.
・PROGRAM operation: It controls y the several patterns and steps(Inclination Straight line).
At the end of program, the display of Process varia le(PV) indicates alternately
and .
Pattern...One pattern means One program.
Step......One step means one straight line consisted of one pattern.
Ramp Step...The step that Setting Value(SV) changes.
Soak Step...The step that Setting Value(SV) is sta le.
Ramp step Soak step
Target Setting Value
step1 step2 step3 step4
・ RUN Signal Input:
RUN mode ... RUN operation starts when the external contact input is closed.
RESET mode.. RUN operation stops when the external contact input is open.
After Stop position, the operation starts from the top of pattern when the external contact is closed
again.
When the RUN signal input option is selected to e ON, RUN/RESET mode cannot e changed
from the operation key oard.
PV

9
. PRECAUTION OF PROGRAM DRIVE
・This unit can select the type of Input. The input type of Thermocouple can e selected from K, J, T, R, N and B. Also,
the input type of R.T.D can e selected from Pt100 and JPt100.
At actual usage, the initial setting of input type at this unit is desperately needed.
For the setting of input type, please refer to "6.TYPE OF INPUT/OUTPUT" of "f) COMMON PARAMETER SETTING
MODE". In case B Thermocouple is selected, the setting range elow 399℃(750
) is out of Instruction/Setting accuracy
range of this unit.
CAUTION
・In case of selection of Input type, the initial setting of input type at this unit is desperately needed.
・In case B Thermocouple is selected, do not control program elow 399℃(750
).
This unit is a le to control several types such as ON/OFF control, PID control and PID + Fuzzy control.
The setting of Input type should e done as per "5.TYPES OF CONTROL" of "f) COMMON PARAMETER
SETTING MODE". The parameter for control is independently separated y Low Temperature Area, Middle
Temperature Area and High Temperature Area, therefore, please make setting of each Control Temperature area. Also,
please make setting of other control parameter as required.
The setting of Key Input is valid in memory even if the power turned OFF.
High Temperature control Zone
Middle Temperature control Zone
Low Temperature control Zone
ON/OFF CONTROL 1 2 3 4 5 6 7 8 step
Initial Value of control sensitivity of this unit is set "0". Please alter the setting as required.
By setting the sensitivity, the point of ON and OFF can e differed.
The position of OFF point is the target Setting Value(SV) as shown elow.
The deviation etween the target Setting Value(SV) and the sensitivity Setting Value ecomes ON position.
Reset Mode
↓ Press ▲
▲▲
▲key and ▼
▼▼
▼key simultaneously for 3 seconds
Control constant setting mode
Control sensitivity at Low temperature REVERSE OPERATION
area to e set y ▲
▲▲
▲ and ▼
▼▼
▼key sensitivity
↓ Press MODE key ON
Upper limit of control zone at Low
temperature to e set y ▲
▲▲
▲ and ▼
▼▼
▼key. OFF SV
↓ Press MODE key
Control sensitivity at Middle temperature NORMAL OPERATION
area to e set y ▲
▲▲
▲ and ▼
▼▼
▼key sensitivity
↓ Press MODE key ON
Upper limit of control zone at Middle
temperature to e set y ▲
▲▲
▲ and ▼
▼▼
▼key. OFF SV
↓ Press MODE key
Control sensitivity at High temperature
area to e set y ▲
▲▲
▲ and ▼
▼▼
▼key
Press MODE key
Press RESET key for 3 seconds.
⇒
⇒

10
SELECT PID CONTROL
The initial value of this "Control Parameter" is set i.e.
Proportional Band(P) = 3.0, Integral time(I) = 0 and
Differential Time(D)=0. Though the control can e done
y this initial setting, ut please do Auto-Tuning for
getting etter result in control. At the time of Auto
Tuning, set the unit to the condition of actual control y
connecting heater and sensors.
SELECT PID + FUZZY CONTROL
The parameter of this PID + Fuzzy Control is set at Initial
setting Value eforehand.
Should do Auto-Tuning.
At the time of Auto-Tuning, please set the unit to the
condition of actual control y connecting heater and
sensors.
RESET mode
↓Press ▲
▲▲
▲ and ▼
▼▼
▼key simultaneously for 3 seconds
Control Constant Setting mode
Low Temperature Proportional and
↓ Press MODE key
Low Temperature Integral time
↓ Press MODE key
Low Temperature Differential time
↓ Press MODE key
Setting of High limit of Low Temp.
area y ▲
▲▲
▲ and ▼
▼▼
▼key.
↓ Press MODE key
Middle Temperature Proportional
and.
↓ Press MODE key
Middle Temperature Integral time
↓ Press MODE key
Middle Temperature Differential
Time.
↓ Press MODE key
Setting of High limit of Middle Temp
area y ▲
▲▲
▲ and ▼
▼▼
▼key.
↓ Press MODE key
High Temperature Proportional
and.
↓ Press MODE key
High Temperature Integral time
↓ Press MODE key
High Temperature Differential Time
↓ Press MODE key
Setting Proportional period y ▲
▲▲
▲
and ▼
▼▼
▼key. However, no indication at
the output of electric current/voltage.
↓ Press MODE key
Setting the strength of Fuzzy y ▲
▲▲
▲
and ▼
▼▼
▼key, ut only for control type "5,6"
PID+FUZZY. The strength of Fuzzy can
e adjusted for controlling value of
Overshoot.
Hold down MODE key for 3 seconds
Auto-Tuning start mode
Setting Auto-tuning temperature(Low
Temperature). Activate Auto-Tuning of
Low Temperature y RUN/STOP key.
↓ Press MODE key
Setting Auto-Tuning temperature(Mid.
Temperature). Activate Auto-Tuning of
Mid. Temperature y RUN/STOP key.
↓ Press MODE key
Setting Auto-Tuning temperature(High
Temperature). Activate Auto-Tuning of
High Temperature y RUN/STOP key.
↓ Press MODE key
Activate Auto-Tuning of Low / Middle /
High Temperature in turn y
RUN/STOP key.
While Auto-Tuning in effect, the following displays
shows alternately.
→
←
→
←
The parameter for each temperature area to e set when
Auto-Tuning finished. In case finishing Auto-Tuning
forci ly, press RUN/STOP key or hold down RESET
key for 3 seconds. In this case, parameter for each
temperature area does not function.
Low
-
SV
Low limit
Mid. limit
Mid.
-
SV
High
-
SV
PV
SV
*
SV
*
PV
SV

11
SETTING OF PROGRAM PATTERN
At first, set the num er of Pattern and Step, and then to set the target Setting Value of Step per each pattern, Step time,
Wait zone, Time Signal of Wait time, Operation num er and End Signal.
a) RESET Mode
↓Press MODE and ▲
▲▲
▲ keys simultaneously for 3
seconds
f) COMMON PARAMETER SETTING Mode
① Setting Pattern num er y ▲
▲▲
▲/▼
▼▼
▼ key.
↓Press MODE key
② Setting Step num er y ▲
▲▲
▲/▼
▼▼
▼ key.
↓Press MODE key
・
・
・
⑫ Select starting Setting Value PV or
SV y ▲
▲▲
▲/▼
▼▼
▼ key.
⑬ Select starting SV y ▲
▲▲
▲/▼
▼▼
▼ key
. Display shows if SV start
selected.
Hold down RESET key for 3 seconds.
a) RESET Mode
↓Press PTTN/STEP key
Select Pattern num er y ▲
▲▲
▲/▼
▼▼
▼ key.
Hold down MODE key for 3 seconds.
Hold down RESET key for 3 seconds.
e) At Parameter per pattern setting mode,
indicate ~ repeatedly until the
step num er set at "f) COMMON PARAMETER Mode".
Setting target SV y ▲
▲▲
▲/▼
▼▼
▼ key
In case the current step to e set as
final step, press TIME/TEMP key to
link target setting. For canceling this,
press TIME/TEMP key again.
Setting Step Time y ▲
▲▲
▲/▼
▼▼
▼ key.
If the control to e done y the
temperature setting of final step after
program operation, press TIME/
TEMP key to link time setting. For
canceling this, press TIME/TEMP key
again.
Setting step wait zone y ▲
▲▲
▲/▼
▼▼
▼ key
↓ Press MODE key
Setting step wait time y ▲
▲▲
▲/▼
▼▼
▼ key
↓ Press MODE key
Setting step Time signal ON time
y ▲
▲▲
▲/▼
▼▼
▼ key. Indicates setting
value if time signal function set at
“
,
,
” per step.
Setting step Time Signal OFF
time y ▲
▲▲
▲/▼
▼▼
▼ key. Indicates
setting value if time signal function
set at “
” per step hour.
Final Step
Num er of operation to e set y ▲
▲▲
▲/▼
▼▼
▼
key.
Indicate at final step.
↓ Press MODE key
Setting End Signal ON time y ▲
▲▲
▲/▼
▼▼
▼
key. Indicates when Event Output
function set at “
”as End signal.
*
*
*
*
**
*
□
□
□
target sv
Press
MODE
key
Press
MODE
key
□
step time
□
wait zone
□
wait time
□
on time
Press
MODE key
□
off time
Press
MODE key
num er
on time

12
6. OPERATION FLOW AND PARAMETER INFORMATION
6.1 Operation Flow
POWER "ON"
↓
RUN signal input(open)
Hold down ▲
▲▲
▲ and ▼
▼▼
▼ key
Hold down MODE and ▼
▼▼
▼ key simultaneously for
simultaneously for 3 seconds 3 seconds.
Press MODE key for 3 seconds.
PID Control
① Num er of pattern
Step SV
proportional and
(Low temp.)
↓ Press Mode key ↓ Press Mode key ↓ Press Mode key
② Num er of step
Step time
Integral time
(Low temp.)
↓ Press Mode key ↓ Press Mode key ↓ Press Mode key
③ PV correction
Step wait zone
Differential time
(Low temp.)
↓ Press Mode key ↓ Press Mode key ↓ Press Mode key
④ ℃/
selection
Step wait time ON/OFF Control
Control sensitivity
↓ Press Mode key ↓ Press Mode key (Low temp.)
⑤ Type of Control
Step Time Signal ↓ Press Mode key
ON time
Low Temp. area
↓ Press Mode key ↓ Press Mode key High limit
⑥ Type of Input/
Step Time Signal ↓ Press Mode key
Output OFF time To
. or
↓ Press Mode key ↓ Press Mode key PID Control
⑦ Select Decimal Return to
except final step.
Proportional and
point. (Middle temp.)
↓ Press Mode key final step. ↓ Press Mode key
⑧ Operation volume
Num er of
Integral time
lower limit operation (middle temp.)
↓ Press Mode key ↓ Press Mode key ↓ Press Mode key
⑨ Operation volume
End Signal
Differential Time
upper limit ON time (middle temp.)
↓ Press Mode key ↓ Press Mode key ↓ Press Mode key
⑩SV limiter low Return to
See next page
↓ Press Mode key ⑫ start SV function
⑪ SV limiter high
↓ Press Mode key
Press Mode key
⑬ SV start
↓ Press Mode key
See next page ⑭
a) RESET MODE
b) RUN MODE
c) PTTN/STEP confirmation mode
d) Suspension mode
f)Common Parameter setting mode
g)Parameter per Pattern setting mode
h) Control constant setting mode
e)PATTERN NUMBER SETTING mode
Keep on pressing RESET key for 3 seconds to change into
a)RESET mode from each mode of f)~i).
In case RUN Signal Input to e applied, please set "29.RUN
SIGN
AL SELECTION" into "ON".
RUN signal input(Close)
RUN signal input(open)
RUN signal input(Close)
RUN/STOP key
RESET key 3 sec.)
RESET key 3 sec.)
RUN/STOP key
PTTN/STEP key
PTTN/STEP key 3 sec.)
RUN signal input(open)
Initial Display
(Indicates for 4 seconds)
□
□
□
□
□
□
PTTN/STEP key

13
⑭ Operation Power ON
↓ Press Mode key
⑮ Event Output 1
Press Mode key
PV Event Output 1
⑯ Function
Event Output 1 Loop A normal
↓ Press Mode key Time Signal Event Output 1
⑰ Low limit ⑳ Function
↓ Press Mode key ↓ Press Mode key Press
⑱ High limit
ON time Mode key
↓ Press Mode key ↓ Press Mode key
⑲ Sensitivity
OFF
Delay Time
↓ Press Mode key Press Mode key
Event Output 2 function
Press Mode key
PV Event Output 2
Functions
Event Output 2 Loop A normal
↓ Press Mode key Time Signal Event Output 2
Low limit
Function
↓ Press Mode key ↓ Press Mode key Press
High limit
ON Time Mode key
↓ Press Mode key ↓ Press Mode key
Sensitivity
OFF
Delay Time
↓ Press Mode key Press Mode key
RUN Signal Input
Communication
Parameter
↓ Press Mode key
Communication
Speed
↓ Press Mode key
Communication
Address
↓ Press Mode key
Response Delay
Time
↓ Press Mode key
Change-over
Communication mode
Press Mode key
Key Lock function
↓ Press Mode key
Return to①.Num er of pattern
ON/OFF Control
Control sensitivity(Middle
temp.)
↓ Press Mode key
Middle Temp. area upper
limit
↓ Press Mode key
To
or
PID Control
Proportional and (High
temp.)
↓ Press Mode key
Integral time (High temp.)
↓ Press Mode key
Differential time (High
temp.)
↓ Press Mode key
Proportional cycle
↓ Press Mode key
To
or
.
PID Control + Fuzzy
Fuzzy strength
↓ Press Mode key
ON/OFF Control
Control sensitivity
↓ Press Mode key
Return to
.
PID CONTROL, PID+FUZZY Control
↓ Press Mode key for 3 seconds.
Auto-Tuning(Low temp.)
Temperature setting
↓ Press Mode key
Auto-Tuning(mid. temp.)
Temperature setting
↓ Press Mode key
Auto-Tuning(high temp)
Temperature setting
↓ Press Mode key
Auto-Tuning(All area)
Initial setting display
↓ Press Mode key
Return to
.
*
h) Control Constant Setting Mode
※※※
i) AUTO-TUNING START MODE

14
6.2 SPECIAL OPERATION
6.2.1 Setting of BLIND mode
a) RESET mode
↓ Hold down RESET key for 10 seconds.
a) RESET mode
All LED display fade out in a moment.
↓ Press ▲
▲▲
▲ key, ▼
▼▼
▼ key and MODE key in turn.
j) BLIND mode
Press ▲
▲▲
▲ key and ▼
▼▼
▼ key simultaneously for 3 seconds.
k)Pattern no.
BLIND mode
PTTN/STEP key
e)Pattern No. Setting mode
RESET key
Press MODE and Press MODE key for
▲
▲▲
▲ key for 3 sec. 3 seconds
simultaneously
l)COMMON PARAMETER m)PATTERN PER PARAMETER n)CONTROL CONSTANT setting o)AUTO-TUNING start
BLIND mode BLIND mode BLIND mode BLIND mode
↓Press MODE key ↓Press MODE key ↓Press MODE key ↓Press MODE key
・ ・ ・ ・
・ ・ ・ ・
・ ・ ・ ・
Indication at Setting Value means Display exist, and means no Display.
For canceling BLIND mode, turn the Power OFF once and turn ON the Power again.
6.2.2 Alteration of Parameter per Pattern Setting while operation.
)RUN mode e)Pattern No. Setting mode
Press MODE key for 10 seconds.
↓Press MODE key
g)Parameter per Pattern setting mode.
Press RUN/STOP key
↓Press MODE key
Press RUN/STOP key
↓Press MODE key
・
・
Press RUN/STOP key
BLIND mode cannot e applied to a)RESET mode, )RUN mode,
c)SUSPENSION mode and d)PATTERN STEP CONFIRMATION mode.
***
***
Alteration of each setting
value can e changed even
while program operation,
ut not setting value of step.

15
6.2.3 Advanced Function
It advances next step to operated hold down ▲ key 2 sec, when program is running(RUN mode).
6.3 Detailed description of each parameter
No Display Name Description
a) Reset mode If this is displayed, the control is inactivated.
← **:Displays the pattern num er selected.
) Run mode This mode indicates the program operation is at run.
LED lamp "RUN" lights on when it starts running.
While a period of the Ramp step, LED display lamps for rising or falling light up,
and they turn off when it moves to the Soak step.
Pressing the TIME/TEMP key ena les PV/SV display to e changed to
Passing Time/Set Time display.
← Indicates process value(PV) or the Passing Time.
← Indicates the set value(SV) on the run or the Set Time.
The Set value display links while the Wait is on operation.
Wait is on operation.
And the process value appear alternately on a PV display
area at the end of pattern
operation.
→
←
End of pattern operation
d) Suspension mode
The programmed operation is temporarily suspended on this mode. When the run is
suspended, the "RUN" LED lamp links and makes the time to e suspended, and
maintain the controlled temperature at the point.
By pressing TIME/TEMP key, PV/SV display is switc
hed to the Passing
Time/Set Time.
c)
Pattern/Step check
mode
Pattern No. and Step No. are indicated during the
RUN mode or Suspension mode.
These displays change ack automatically to either RUN mode or Suspension mode,
if the key is not pressed for 30 seconds.
← Indicates the Pattern No. at the run.
← Indicates the Step No. at the run.
e) Pattern No.
setting mode
This mode ena les to set the Pattern No. of the program to e run.
← ** Indicates the Pattern No.
**
**
link
**
**
**
**
**
**

16
f) Common Parameter setting mode
No Character Name Description Initial
Value Display conditions/Remarks
①
Num er of Pattern
Set Num er of program patterns
Setting range: 1 - 64 patterns
②
Num er of Steps Set Num er of steps of each pattern.
Setting range: 1 - 64 steps
The product of pattern No. and
Step Num er should not
exceeds 64 as the maximum.
③
PV correction
Add PV correction value to
a process value to e entered.
Setting range:-199.9 to 999.9℃/
-199 to 999℃/
or
Select ℃/
for the PV display.
℃
④
℃/
Selection
Select the control type from the ta le elow.
ON/OFF control, normal
ON/OFF control, reversed
PID control, normal
PID control, reversed
PID + fuzzy control, normal
⑤
Control type
PID + fuzzy control, reversed
Auto-tuning is always
Required, if Fuzzy control
selected.
I/O types are indicated and input
type can e selected.
*
or
The initial value varies y the
types.
※※**
*
Thermocouple Input Type RTD INPUT TYPE
※※
Input Type ※※ Input Type
K thermocouple
PT100
J thermocouple
JPT100
T thermocouple
R thermocouple No alteration possi le
N thermocouple ** Output type
B thermocouple
Relay contact output
SSR drive output
Voltage output
⑥
Input /Output
type
Current output
Select if elow decimal point is
required or not.
Decimal not required.
⑦
Decimal point
selection
Decimal required.
or
Decimal point is not displayed on
R, N, B thermocouples.
⑧
Manipulated
value lowest
limiter
On proportional control, set the lowest
value of manipulated control output.
Setting range: 0.0%~
(Relay contact, SSR Output)
-10.0%~
(Voltage, current output)
Displays when
are
,
,
,
.
⑨
Manipulated
value highest
limiter
On proportional control, set the highest
value of manipulated control output.
Setting range:
~100.0%
(Relay contact, SSR Output)
~110.0%
(Voltage, current output)
No Character Name Description Initial
value Display conditions/Remarks

17
⑩
SV Limiter Low
Set Num er of SV Limiter Low.
Setting range: Setting range low~
(
-50)℃/
⑪
SV Limiter
High
Set Num er of SV Limiter High.
Setting range: (
+50)℃/
~Setting range high
Initial value is different y input.
Refer to
“7.SETTING RANGE
AND INDICATION RANGE
TABLE”.
Select the start SV at the starting of
the run.
SV start
PV start
⑫
Start SV
selection
⑬
Starting
temperature
Set the temperature value of SV
start
Setting Range:
~
or
Displays when
is
.
Select operations for power input.
Reset and start
Operation at power
⑭
Power ON
operation
selection
Select Event output functions
1 and 2.
Release function
PV event output
Time signal
End signal
Loop a normal event
⑮
Event 1, 2
functions
Displays with options of Event
output 1, 2.
Select Process value for event
output functions 1 and 2.
□
*※
Displays when
□ is
.
*
FUNCTIONS(select with ▼ key) ※ ADDITIONAL FUNCTIONS
Release functions (select with ▲ key)
Deviation high/low limit
Release function
Deviation high limit
Event output hold
Deviation low limit
Stand- y sequence
Deviation range for
A normal process value
high and low limit
Event output hold +
A solute value high/low limit stand- y sequence
A solute value high limit
Event output hold +
A solute value low limit A normal process value
Range of a solute value
high and low limits
Stand- y sequence +
A normal process value
Event output hold +
Stand- y sequence +
A normal process value
⑯
Process value
event output
functions 1,2
⑰
⑱
Process value
event output
1 and 2.
High/Low
limit setting
Set the temperature of the process
value event output
Setting range:
-199.9to 999.9℃/
-199 to 999℃/
or
Displays according to the
setting of process value
event output function.

18
No Character Name Description Initial
value Display conditions/Remarks
⑲
Process value
event output
1 and 2.
sensitivity
Set the sensitivity of the process value
event output 1 and 2.
Setting range: 0.0 to 999.9℃/
0 to 999℃/
or
Displays when
□ is
.
Select Time signals and event output 1
and 2.
ON Delay/OFF Delay Time
for each step
ON Delay/Off Delay Time
common for all steps
Time signal ON Time for
each step
Time signal ON Time
common for all steps
Time signal ON Time
Time signal ON Time
for each step
⑳
Event output
1 and 2.
Time Signal
functions
Time signal ON Time
common for all steps
Display when
□ is
.
See "Time Signal and End
Signal" on Page 7,for setting
and operation of Time Signal
functions.
Event output 1
2 Time Signal
On Time.
On Delay time
Set the Time signal ON Time.
Setting range: 0 - 99 hrs.59 min.
If select 2 for Time signal
function, set ON Delay Time.
Displays when
□
are
,
,
.
Event output 1
,2 Time signal
OFF Delay Time
Set the Time signal OFF Delay Time
Setting range: 0 - 99 hrs.59 min.
Displays when
□
are
.
Loop A normal
Event Output 1,2
Set the detecting Time for loop
a normal event.
Setting range: 1 - 9999 sec.
Displays when
□
are
.
Run signal input valid/invalid .
Valid
Invalid
Selection of
RUN Signal
Displays in case of RUN signal
input option.
Set the Communication parameter.
□△○×
□
BCC check (change y ▼key)
Invalid
Valid
△
Data length(to e
changed y ▼ key)
7 it
8 it
○
Parity(to e changed y
▼ key)
None
Odd num er
Even num er
×
Stop it(to e changed y
▼ key)
1
Communication
parameter
2
Displays when Communication
option selected.
No Character Name Description Initial
Value Display condition/Remarks

19
Communication
speed
Set Communication speed.
Setting range: 1200,2400,4800,9600
Setting unit: BPS
Communication
Address
Set the own address.
Setting range: 1 to 99 stations
Response delay
Set the interval time to switch to the
transmission mode after receiving.
Setting range: 0 to 250 mSEC
Select Local/Communication mode.
Local mode
Communication mode
Communication
mode switch
Displays when any communication
option adopted.
Select Key lock setting.
Unlock
Lock all parameters
Lock temperature parameter
Lock time parameter
Key lock
function
Lock all parameters except program
parameters (Lock all modes except
for the pattern No. setting and the
parameter per pattern setting)
Communication mode
switch display(
) can
not e locked.
g) Parameter per pattern setting mode
No Character Name Description Initial
Value Display condition/Remarks
□
Step □
temperature
setting
Set the temperature value for step □.
Setting range:
~
.
□
Step □ time
setting
Set the time for step □.
Setting range: 0 - 99 hrs. 59 min.
□
Step □ wait
zone
Set a wait zone for step □.
Setting range: 0 to 100 ℃/
□
Step □ wait
time
Set a wait time for step □.
Setting range: 0 to 1 hr. 59 min.
□
Step □ time
signal
ON time
ON Delay
time
Set Time signal ON time.
Setting range: 0 - 99 hrs. 59 min.
When Time signal function 1 is
selected, then set ON Delay time.
Displays when
□
are
,
and
.
□
Step □ time
signal
OFF Delay time
Set Time signal OFF Delay time
Setting range: 0 - 99 hrs. 59 min.
Displays when
□
is
.
Num er of
running time
Set the No. of running times
per pattern.
Setting range: 0 - 99 times
(0 for infinite num er)
Displays at the last step.
End signal
ON time
Set the End signal ON time.
Setting range: 0 - 9999 sec.
(0 for continuation)
Displays when
□ is
at
the last step.
This manual suits for next models
3
Table of contents
Other Toho Electronics Controllers manuals
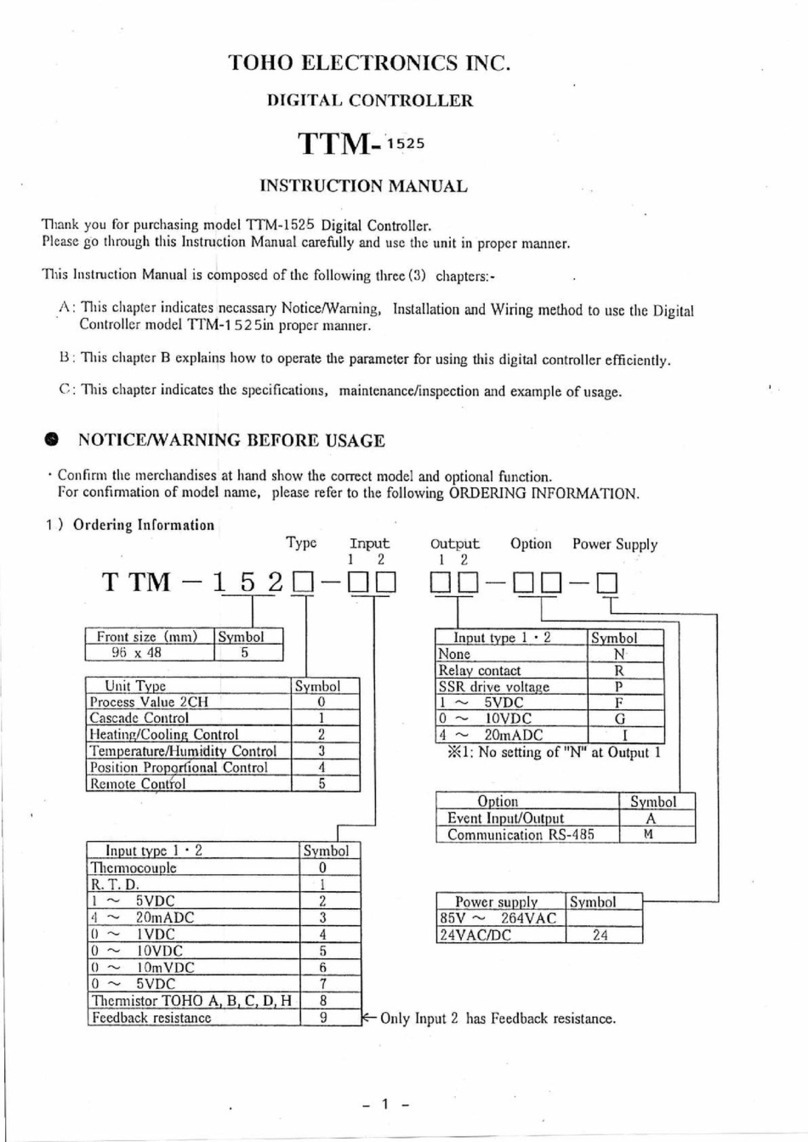
Toho Electronics
Toho Electronics TTM-1525 User manual
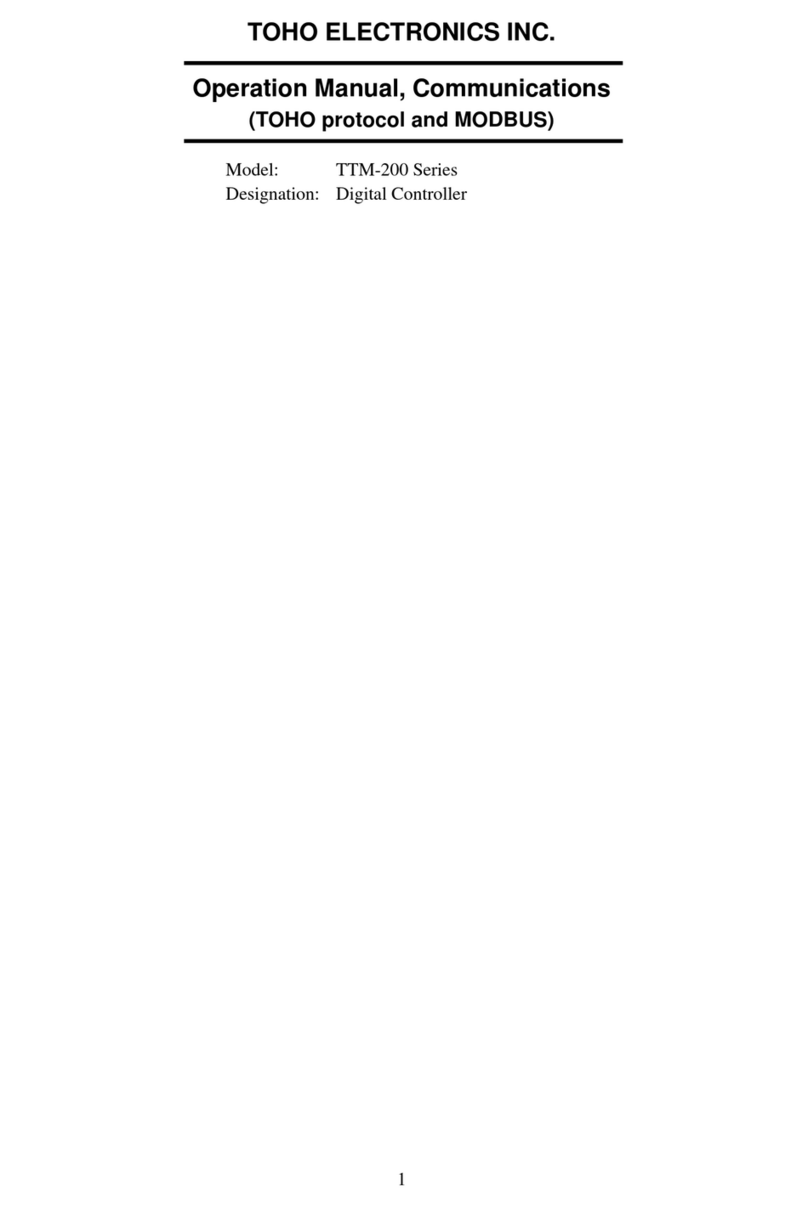
Toho Electronics
Toho Electronics TTM-200 Series Use and care manual

Toho Electronics
Toho Electronics TTM-210 Series Use and care manual
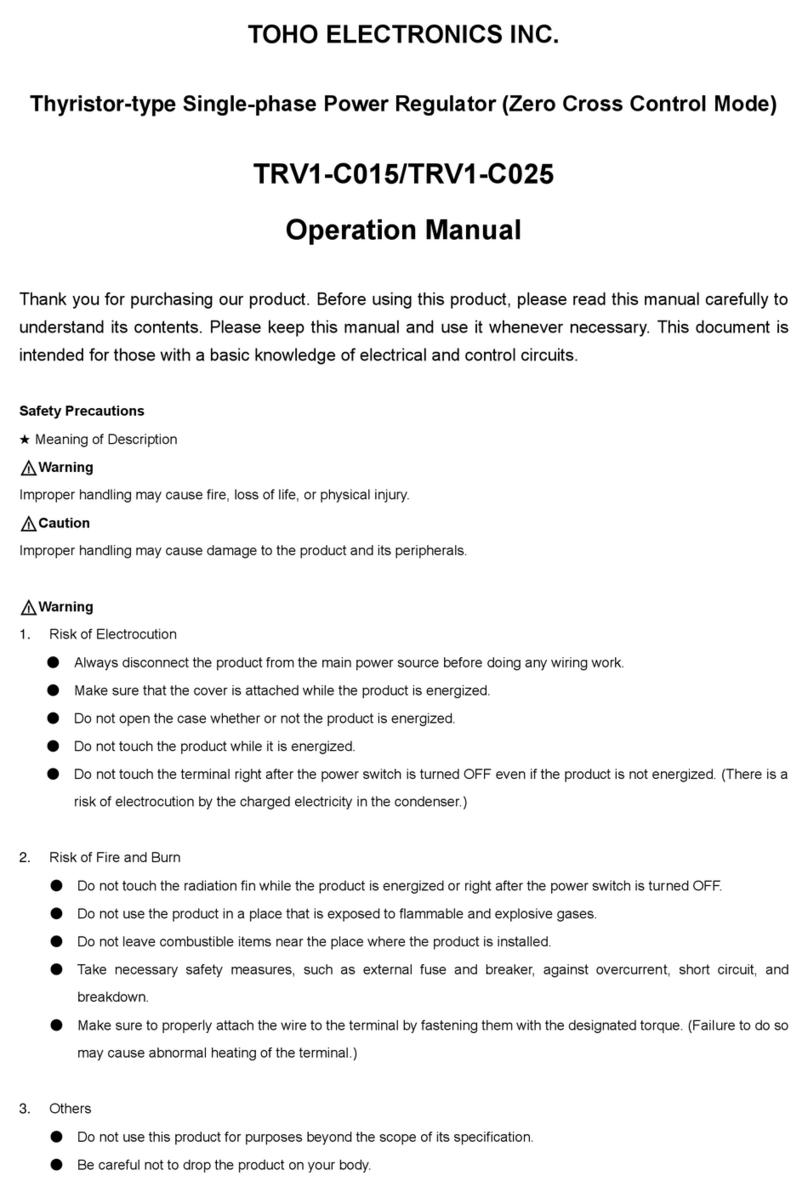
Toho Electronics
Toho Electronics TRV1-C015 User manual
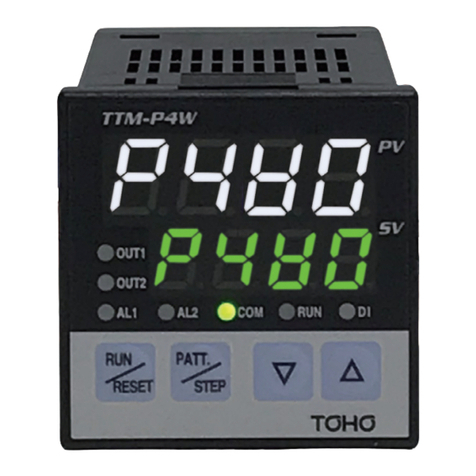
Toho Electronics
Toho Electronics TTM-P4W Series User manual
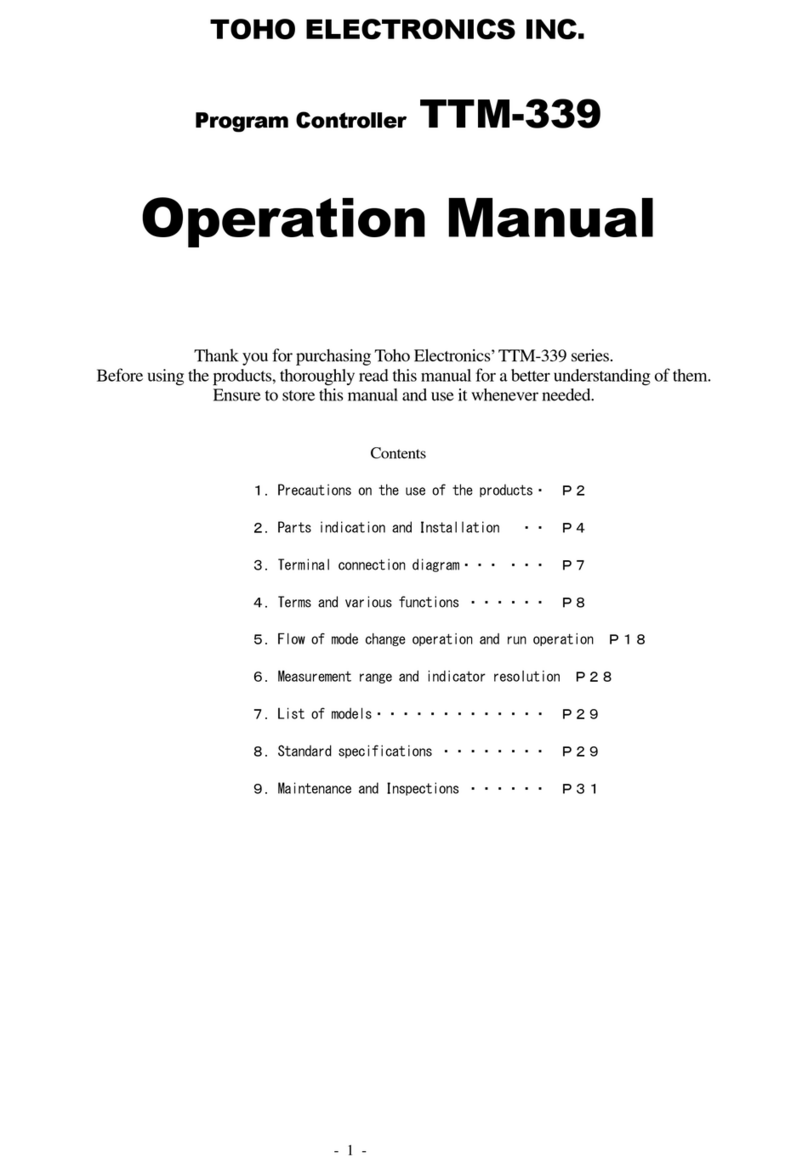
Toho Electronics
Toho Electronics TTM-339 User manual
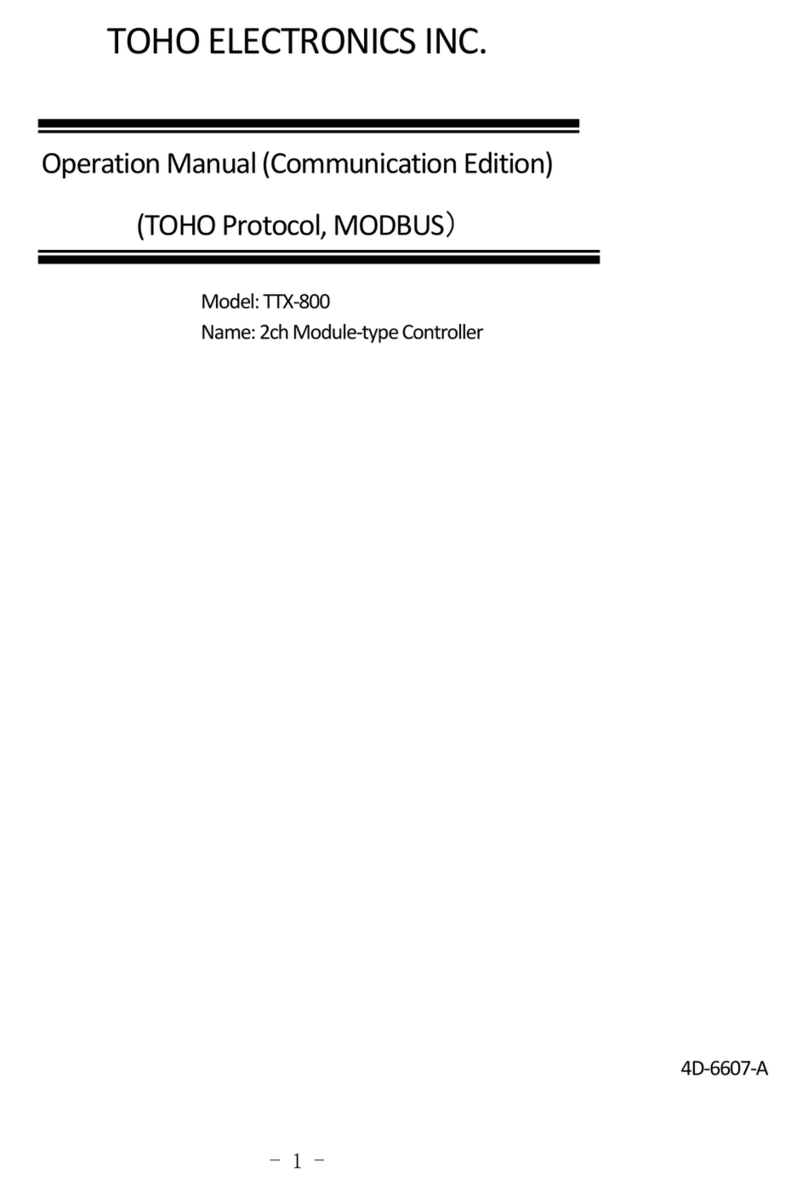
Toho Electronics
Toho Electronics TTX-800 User manual
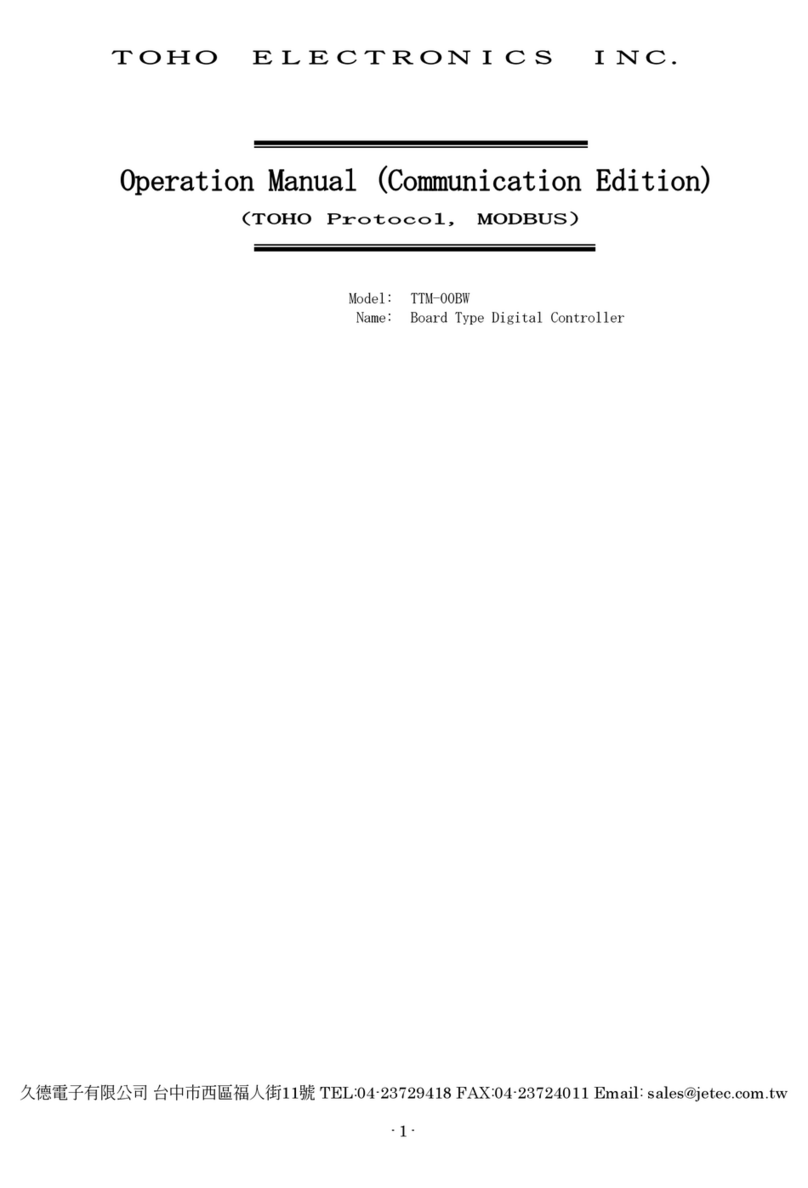
Toho Electronics
Toho Electronics TTM-00BW User manual