Toky GTD Series User manual

Caution of Install & Connection
1. Installation
1) This product is used in the following environmental standards.(IEC61010-1)[Overvoltage
categoryⅡ、class of pollution 2].
2) This product is used in the following scope:environment, temperature, humidity and
environmental conditions. Temperature:0~50℃;humidity:45~85%RH; Environment
condition:Indoor warranty.The altitude is less than 2000m.
3) Please avoid using in the following places:
The place will be dew for changing temperature;with corrosive gases and flammable
gas;with vibration and impact;with water, oil, chemicals, smoke and steam facilities with
Dust, salt, metal powder;and with clutter interference, static electric and magnetic fields,
noise;where has air conditioning or heating of air blowing directly to the site; where will be
illuminated directly by sunlight; where accumulation of heat will happen caused by radiation.
4) On the occasion of the installation, please consider the following before installation.
In order to protect heat saturated, please ensure adequate ventilation space. Please consider
connections and environment,and ensure that the products below for more than 50mm
space. Please avoid to installed over the machine of the calorific value (Such as heaters,
transformer, semiconductor operations, the bulk resistance). When the surrounding is more
than 50 , please using the force fan or cooling fans.But don't let cold air blowing directly to the
product. In order to improve the anti - interference performance and security, please try to stay
away from high pressure machines, power machines to install.
Don`t install on the same plate with high pressure machine and the product.
The distance should be more than 200mm between the product and power line.
2. Cable caution:
1) Please use specified compensation wire in the place of TC input. Please use insulated TC
if the measured device is heated metal.
2) Please use the cable of lesser resistance in the place of RTD input, and the cable(3 wire)
must be no resistance difference,but the total length is within 5m.
3) In order to avoid the effect of noise,please put the input dignal away from meter cable,
power cable, load cable to wiring.
4) In order to reduce the power cables and the load power cables on the effect of this
product, please use noise filter in the place where easy to effect. You must install it on the
grounding of the disk if you use the noise filter, and make the wiring to be shortest
between noise filter output side and power connectors. Don`t install fuse and switch on
the wiring of noice filter output side,otherwise it will reduce the effect of noise filter.
5) It takes 5s from input power to output.If there is a place with interlocking actions circuit
signal,please use timer relay.
6) Please use twisted pair with a shield for analog output line, can also connect the
common-mode coil to the front-end of the signal receiving device to suppress line interference
if necessary, to ensure the reliabilty of signal.
7) Please use twisted pair with a shield for remote RS485 communication cable, and deal
with the shield on the host side earth, to ensure the reliabilty of signal.
8) This product don’ t have the fuse; please set according to rated voltage 250V, rated
current 1A if you need; fuse type:relay fuse.
9) Please use suitable slotted screwdriver and wire.
Terminal distance: 5.0mm. Screwdriver size: 0.6X3.5, length of slotted screwdriver
>130mm. Recommended tightening torque: 0.5N.m.
Proper cables: 0.25 ~ 1.65mm single cable/multiple core cable
10) Please don`t put the Crimp terminal or bare wire part contact with adjacent connector.
广东东崎电气有限公司
TOKY electrical co.,ltd. http://www.toky.com.cn
National High-tech Enterprise/National Standard Drafting Unit
Version: KKGTD-16L-A01-A/0-20211013
Hotline: 400-0760-168
ISO9001
国家高新技 术企业
GTD Series 16 Channels
Temperature Controller
For GTD-A Version
1 2
⊙Multiple thermocouple signal types for option, weak isolation between signal
inputs, able to connect grounding probe.
⊙With many functions, measured display, control output, RS485 communication,
etc.
⊙Multi PID algorithm for option, with auto-tuning function.
⊙With power uniform distribution function for multi-channel loads.
⊙Suitalbe for industrial machinery, machine tools, measuring instruments.
Features:
III. Model description
Model
GTDF-T168
GTDF-T16
Control output
Transistor output
Transistor output
RS485
Yes
No
GTDF -T 16 8 A
II. Model Illustration
4
1
2
3
5
A: Version
T: transistor output
16: 16 channels
Blank: without RS485 comm. 8: with RS485 comm.
F: DC 24V power supply
6GTD series multi-channels temperature controller
1. Electrical parameters:
IV. Specification
Control output
Control output capacity
Display update rate
Power supply
Power consumption
Environment
Storage environment
Communication port
Insulation impedance
ESD
Pulse traip anti-interference
Surge immunity
Voltage drop & short
interruption immunity
Isolation withstand voltage
Shell material
Total weight
Panel material
Power-off data protection
Safety Standard
Transistor open collector outpution level 2
DC 24V, max 100mA, withstand voltage:100V
1 times per second per channel
DC 24V
< 4VA
Indoor use, temperature: 0~50℃no condensation,
humidity<85%RH, altitude<2000m
-10~60℃, no condensation
RS485 port, Modbus-RTU protocol
Input/output/power to shell>20MΩ
IEC/EN61000-4-2
Contact ±4KV /Air ±8KV perf.Criteria
IEC/EN61000-4-4 ±2KV perf.Criteria B
IEC/EN61000-4-5 ±0.5KV perf.Criteria B
IEC/EN61000-4-29 0%~70% perf.Criteria B
Circuit between power and other input/output
AC1000V,1min
About 400g
PC/ABS (Flame Class UL94V-0)
PVC film and PEM silicone key
10 years
Transistor open collector outpution level 2
2. Measurement signal parameter
Input Type Measurement
range
Symbol
Resolution
Accuracy
Input impedance/
Auxiliary current
Comm.
code
K1
K
J
K2
J1
J2
-50~1200
-50.0~999.9
0~1200
0.0~999.9
1℃
0.2℃
1℃
0.2℃
0.5%F.S±3digits
0.5%F.S±1℃
0.5%F.S±3digits
0.5%F.S±1℃
>500kΩ
>500kΩ
>500kΩ
>500kΩ
0
16
1
17
E
T
E2
T1
T2
E1 0~850
0.0~850.0
-50~400
-50.0~400.0
0.5%F.S±3digits
0.5%F.S±3℃
>500kΩ
>500kΩ
>500kΩ
>500kΩ
2
18
3
19
1℃
0.3℃
1℃
0.4℃
0.5%F.S±1℃
0.5%F.S±3℃
The instruction explain instrument settings, connections,name and etc, please read
carefully before you use the temperature controller. Please keep it properly for necessary
reference.
I. Safe Caution
Warning
1)When the failure or abnormal of products lead to a system of major accidents, please set
the proper protection circuit in the external.
2)Please don`t plug in before completing all the wire.Otherwise it may lead to electric shock,
fire, fault.
3)Not allow to use outside the scope of product specification,otherwise it may lead to
fire,fault.
4)Not allow to use in the place where is inflammable and explosive gas.
5)Do not touch power terminal and other high voltage part when the power on, otherwise
you may get an electric-shock.
6)Do not remove,repair and modify this product,otherwise it may lead to electric shock, fire,
fault.
Caution
1)The product should not be used in a nuclear facility and human life associated medical
equipment.
2)The product may occur radio interference when it used at home.You should take
adequate countermeasures.
3)The product get an electric shock protection through reinforced Insulation. When the
product is embedded in the devices and wiring,please subject to the specification of
embedded devices.
4)In order to prevent surge occurs,when using this product in the place of over 30m indoor
wiring and wiring in outdoor, you need to set the proper surge suppression circuitry.
5)The product is produced based on mounting on the disk.In order to avoid to touch the
wire connectors,please take the necessary measures on the product.
6)Be sure to observe the precautions in this manual, otherwise there is a risk of a major
injury or accident.
7)When wiring, please observe the local regulation.
8)To prevent to damage the machine and prevent to machine failure, the product is
connected with power lines or large capacity input and output lines and other methods
please install proper capacity fuse or other methods of protection circuit.
9)Please don't put metal and wire clastic mixed with this product,otherwise it may lead to
electric shock, fire, fault.
10)Please tighten screw torque according to the rules.If not,it may lead to electric shock and
fire.
11)In order not to interfere with this products to dissipate heat, please don't plug casing
around the cooling vent hole and equipment.
12)Please don’ t connect any unused terminal.
13)Please do the cleaning after power off, and use the dry cleaning cloth to wipe away the
dirt. Please don’ t use desiccant, otherwise, it may casue the deformation or discoloration
of the product.
14)Please don`t knock or rub the panel with rigid thing.
15)The readers of this manual should have basic knowledge of electrical,control, computer
and communications.
16)The illustration, example of data and screen in this manual is convenient to
understand,instead of guaranteeing the result of the operation.
17)In order to use this product with safety for long-term,regular maintenance is necessary.
The life of some parts of the equipments are by some restrictions, but the performance of
some will change for using many years.
18)Without prior notice, the contents of this manual will be change. We hope these is no
any loopholes, if you have questions or objections, please contact us.

No.
Name
Symbol
Illustration Setting
range
Factory
setting
a. In normal measurement control mode, keep pressing “ ” key for 3 sec to enter the
parameter menu viewing mode, press “ ” key to switch the display channel, the
channel number is displayed in the CH indication window, parameters displayed on
the panel correspond to the displayed channel numbe.
b. In menu viewing mode, press “ ” or “ ” key to check the common menu
parameters circularly.
c. In menu viewing mode, press “ ” key to flash the viewed menu parameter value to
enter the parameter modification mode, and each press of the key can move one bit
to the left in cycle.
d. In parameter modification mode, press “ ” or “ ” key once to increase or
decrease the flashing data bit by one.
e. In parameter modification mode, after the parameter is modified, press “ ” key to
save the modified value, and keep pressing it for 3 sec to exit to the menu viewing
mode.
f. In normal measurement control mode, keep pressing “ ” key for 3 sec to enter the
PID auto-tuning state.
h.In normal measurement control mode, keep pressing “ ” key for 3 sec to enter/exit
the running mode or stop mode; in stop mode, the SV window displays “STOP”.
Note: SSM menu should be set as 1 to enable the operation function.
3
2
4
SET
SET
SET
VII. Panel illustration
4
26
23
21
22 25
PV
SV
CH
IX. Menu illustration
: No mater what model,what control mode it is,these parameters will be displayed always.
: According to different model and control mode, these parameters will be hidden.
1. Common menu illustration
1
2
3
4
5
7
8
6
PV
Measured value, it will flash or display LLLL/
HHHH when the value overflow measure range.
Unit: ℃/℉or no unit.
Refer to
measured
signal table
No
CH
SV
Target temperature set value,unit:
℃/℉
or no unit.
Channel number display window
SLL~SLH
1~99
LCK
Lock function;
0001:SV value cannot be changed;
0010: menu set value can be read only;
0033: advanced menu can be accessed;
0123: menu restore factory setting
0
~
9999 0
200
ADD Communication address for this meter 1~247 1
BAD
RS485 communication baud rate
0:1200;1:2400 2:4800;3:9600;
4:19200;5:38400;6:57600;7:115200;
0~7 3
PRTY Communication parity check setting,
0:NO 1:ODD 2:EVEN 0~2 0
0
DATC
Communication data transport sequence 000;
1st bit function reserved; 2nd bit is byte
sequence exchange; 3rd bit function reserved.
Refer to
communication
protocol
VIII. Operation process and menu illustration
1. Operation process
Measurement display interface
Auto-tuning
AT
Output stop
StoP
(Currently displayed channel)
Normal control
When SSM=1
press 3 sec
Press 3 sec
Power On
SET
SET
SET
SET
SET
SET
SET
SET
PV
SV
CH
PV
SV
CH
PV
SV
CH
Advanced
menu
Common
menu
Press SET key>3 sec
Press SET key
>3 sec
Press SET key
>3 sec
PV
SV
CH
PV
SV
CH
PV
SV
CH
PV
SV
CH
PV
SV
CH
When LCK=33
press SET key
When LCK=33
press SET key
1. Wiring marker
VI. Wiring diagram
A B
134
OUT
6
571 2 34567 8
TC INPUT
TC INPUT
G
CECCCCE
COM1 COM2
COM4COM3
E
CC C C E E +- + - + - + -
+- + -
+-
+-
2
8NC
+ - C E
10
C C
11
C C
12
E E
OUT
14
13 15
CC C C EE+- + - + - + -
+- + -
+-
+-
9 10 11 12 13 14 15 16
9 16 NC
POWER
RS485
AU2
AU1
2. Wiring example
+
TC
TC input
-
C
C OUT 2
OUT 3
OUT 4
C
C
COM1
COM1
OUT 1
E
E
Transistor
output
-
+
+
DV 24V
Temperature
control module
Temperature
control module
SSR output
SSR
C
E
DV 24V
Relay output
Relay
C
E
+
V. Dimension and installation (unit:mm)
Panel Side Installation
Wire connection
端子顶视图 端子正视图
端子螺帽尺寸Φ3
扭力 0.2N.m
Input Type Measurement
range
Symbol
Resolution
Accuracy
Input impedance/
Auxiliary current
Comm.
code
N
B250~1800 1℃1%F.S±2℃>500kΩ
>500kΩ
>500kΩ
>500kΩ
>500kΩ
>500kΩ
4
1℃1%F.S±2℃
1℃1%F.S±2℃
1℃0.5%F.S±1℃
0.2℃0.5%F.S±1℃
12bit 0.5%F.S±3digits
5
6
7
20
12
R
S
N1
N2
0~50mV
-10~1700
-10~1600
-50~1200
-50.0~999.9
-1999~9999
41.00
147.50
57.80
8.80 20.50
28.50
45.50 131.60
3.00
35.00
6.50 4.00
3. Isolation diagram:
RS485 port
AU1 OUT CH1-CH4 transistor output
OUT CH5-CH8 transistor output
AU2 OUT CH9-CH12 transistor output
OUT CH13-CH16 transistor output
TC CH1-CH16 TC input
Power
supply
:Functional isolation AC 1000V
:Functional isolation AC 500V
153.00
Wire
5
6
AL2
Alarm 2#
indicator (red)
COM indicator (red)
AT
COM
2nd alarm indicator, alarm on when the light is on,
alarm off when the light is off.
Communication status indicator, after receiving data,
the light is on, after sending data, the light is off.
AT indicator (red) Auto-tuning indicator, during the auto-tuning
process, the light is on.
PV display (red)
Set value or parameter set value; when it displays
“STOP” , control stop.
Channel number
Measured value or parameter menu symbol
No.
Symbol
Name Function description
1
2
3
4
AL1
Alarm 1#
indicator (red)
PV
SV display (green)SV
1st alarm indicator, alarm on when the light is on,
alarm off when the light is off.
CH
Channel display (red)
Menu key/ confirm key, press it to enter/exit
parameter modification mode, saving modified
value, and switch between channels.
Add key/ R/S
Decrease key
Add key/menu up key; in measurement control mode,
keep pressing it to switch between RUN & STOP mode.
Decrease key/ menu down key
Control output indicator of each channel, output on
when the light is on, output off when the light is off.
Activation key/shift key/AT auto-tuning key, in
measurement control mode, keep pressing it to
enter/exit auto-tuning.
Shift/AT key
SET keySET
OUT CH 1-16
control output

5
CP 1 ~ 200
5.0
-199.9 ~
999.9
0
K1
DB
INP
2. Advanced menu illustration
9
11
12
13
14
15
17
16
AL1
AD1
(1)
AL2
HY2
AD2
(1)
FL ~FH
10 HY1 0 ~1000
0 ~12
10
FL ~FH
5
1
0 ~1000
1
0 ~6
4
3
30
5
1
I
0~9999 120
18
19
20
21
22
23
24
D
OVS
0~9999
0~9999
OT Control Mode,0:ON/OFF Heating control;1:PID
heating;2:ON/OFF Cooling control;3:Reserved;
4:Over temperature cooling output;5:PID Cooling
0
~
5 1
P 0~9999 30
A-M AUTO~AM AUTO
PS
-1999 ~ 9999
0
0
25
Control Mode,0 ~1:SSR Output or Transistor output
ACT 0
~
1
0
26 AE1
(2) 0~5
0
27 AE2
(2) 0~5
1.0
0~3DP28
(0~20)
DTR 0.0 ~ 2.0
0
29
SSM Press the key on the panel to switch the RUN/STOP
operation switch, 0: prohibited, 1: OPEN 0 ~1
0
30
SLL
SLH
Low limit of target setting value range
High limit of target setting value range
FL~FH
FL~FH
33 FL
34 FH
OLL
OLH
35
FT 0 ~ 255 10
0
-5.0 ~ 100.0
0.0 ~ 105.0
0.0
100.0
36
37
38
39
40
41
42
43
Temperature unit setting ℃: Celsius ℉: Fahrenheit,
note: this unit setting is only for temperature
measurement signals,“_”: No unit display
PT
PDC
UNIT
0 ~ 9999
FUZ/STD
(25)℃
(26)℉
FUZ
(25)℃
31
32
PRS EEP/RAM EEP
RSS
LPH
EEP/RAM EEP
0.0~999.9 0.0
The actual power of each channel load, used for the
total power limit; Unit: KW.When set to 0, this channel
don't participate in power limitation
No.
Name
Symbol
Illustration Setting range
Factory
setting
1st alarm value, note: the minus is dealed as absolute
value when it is as a deviation value.
1st alarm hystersis
1st alarm mode,note: when AD1=0, close alarm
function . When AD1>6, 2nd alarm function is invalid.
2nd alarm value, note: the minus is dealed as
absolute value when it is as a deviation value.
2nd alarm hystersis
2nd alarm mode
Overshoot limit, during PID control process, when PV(measured
value) > SV(set value) + OVS(overshoot limit), force to close output.
The smaller this value is, the smaller the PID adjustment range is,
the worse the control stability is. Please set the appropriate value
according to the actual situation.This function is unavailable when it is
set to 0
Differential time:The system oscillation can be
prevented by reducing the differential action to a
suitable value. The larger the value is, the stronger
the differential action is. Unit: s
Integral time, the smaller the value is, the stronger the integral action is,
otherwise, it is weeker. and the more it tends to eliminate the deviation
from the set value. The deviation may not be eliminated if the integral
effect is too weak. Unit: s
Proportional band: the smaller the setting value is, the faster the system
responds; otherwise, it is slower.Increasing the proportional band can
reduce the oscillation, but it will increase the control deviation. Decrease
the proportional band can reduce the control deviation, but it will cause
oscillation. Unit: corresponding measured value
Auto-manual control switch, AUTO(0): auto control
only; MAN(1): manual control only;
OUT1 control cycle, 1: SSR control output,
4-200: relay control output. Unit: s
Position control hystersis(Negative return differential
control),or cooling control and compressor refrigeration
control dead zone.after change the INP setting, please
change this parameter according to the decimal point
position.
Optional input signal. see the corresponding table of
input signal parameters for details,Note: other
relevant parameters to be modified
Amend value, display value= actual measured value
+ amend value
refer to input
signal para-
meters table
(page 2)
No.
Name
Symbol
Illustration
Setting range
Factory
setting
1st alarm extensions function,refer to alarm extension
function table
2nd alarm extensions function,refer to alarm
extension function table
Decimal point setting is effective under the linear
signal input
PV fuzzy tracking value,properly set this value on some
occasions, it can get a more stable control display value,
this value is unrelated with actual measured value. Note:
after setting this value,when alarm setting value is equal
to SV setting value, alarm output operation is subject to
actual measured value. Set as 0 to close this function.
The temperature input unit: Fahrenheit or Celsius.The
linear signal input unit: Engineering Digits
Measure range low limit,the setting value
must be less than measure range high limit
Measure range high limit,the setting value
must be more than measure range low limit.
Refer to
measured signal
parameter table
Refer to
measured signal
parameter table
Output low limit, limit the output low limit current amplitude.
Setting value must be less than high limit setting
Output high limit,limit the output high limit current amplitude.
Setting value must be greater than low limit setting
PV digital filter coefficient, the value larger,the
stronger of the filtering effect
Compressor start delay time, unit: s
PID algorithm option:0(FUZ): Advanced fuzzy PID
arithmetic; 1(STD): normal PID arithmetic
Setting parameter reserve position: 0 (EEP):EEPROM
with power failure protection; 1(RAM): RAM without power
failure protection. Description of setting parameter storage
location: EEP and RAM. EEP means that the setting
parameters are written into EEPROM and can be
permanently saved after power failure.It is generally used
for factory setting parameters of equipment. Because
EEPROM has the limit of writing times, too many and too
frequent writes will be damaged;RAM: it means that the
parameters are stored in RAM without writing limit and will
not be damaged due to frequent writing. The parameters
set after the equipment is powered off will not be saved.
After power on, they will be restored to the parameters
saved in EEPROM by the equipment manufacturer.It is
usually used for frequent parameters writing when
communicating with the upper computer PLC.
The method of using this parameter is to set this parameter
to EEP first. After the equipment factory has finished debugging
the equipment and set the parameters, the parameters
are saved in EEPROM, and then PRS is modified to RAM,
and the equipment is delivered to the user for use, so as to
prevent erroneous modification or long-term communication
writing data from damaging the EEPROM.
RUN/STOP reserve position: 0 (EEP):EEPROM with power
failure protection;1(RAM): RAM without power failure protection.
this parameter method: if the instrument is required to be in stop
mode every time when it is powered on, first set RSS to EEP,
and then set "start stop operation" = STOP. This setting parameter
will be saved for a long time; Then set RSS to RAM. When using,
the upper computer starts/stops the instrument, which is stored in
RAM. After power on again, the instrument still enters STOP mode.
6
(3)Auxiliary output function table
X. Key function operation
Continued
44
47
48
49
50
SLPL
DN
DNS
DNT
VER
0.0~999.9
1~16 16
1~84
0~99
—— ——
1
4
45
46
AU1P
(3)
AU2P
(3)
0~32 1
0~32 17
Auxiliary output 1 programming, use for programming
AU2 output function
Auxiliary output 2 programming, use for programming
AU2 output function
0.0
Total power limit, limits the power distribution of each
participating channel when the total power of channel output
controls exceeds the total power limit value; Unit: kW; Set to 0,
no power limit function
1. Monitoring mode operation(RUN/STOP)
1)SSM is set in open meter operation; Otherwise, the settings only be modified during communication.
2)Under the measure mode, long press “ ” key to enter the STOP mode, SV window will display
“STOP”, main control output will stop or keep the minimum output.
3)Under STOP mode, long press “ ” key to exit STOP mode, press “ ” key to modify SV value.
4)Under STOP mode, alarm output and analog output work normally.
2. PID auto-tune operation:
1)Before auto-tune procedure, please switch off the control output load power, or set the meter as STOP
mode.
2)Before auto-tune procedure, PV value should meet below condition: when it is PID heating control, PV
needs to be much smaller than SV; when it is PID cooling control, PV needs to be much larger than SV.
3)Before auto-tune procedure, please set a proper alarm value or eliminate the alarm condition, in
order to prevent the auto-tune procedure from being affected by alarm output.
4)Set PID type and SV value; the factory default setting is fuzzy PID.
5)Set as PID control, if there is OLL & OLH output limiting, please set the output to a proper range;
factory default setting is OLL=0%, OLH=100%.
6)Exit STOP mode, or switch on the load Power, immediately long press “ ” key to enter auto-tune
mode, then the AT indicator light is on.。
7)The auto-tune procedure will take some time, in order not to affect auto-tune result,please don`t modify
the parameters or power-off.
8)When AT light goes out, it automatically exits auto-tune mode, PID parameters will be updated
automatically, and then the meter will control automatically and exactly.
9) During the auto-tune procedure, below actions will cause the termination of the precess, long press
“ ” key, measure beyond the scope, abnormal display, switch to STOP mode, power-off, etc.
10)Note: In the occasions with output limiting operation, sometimes, even if the auto-tune is carried out,
the best PID parameters still cannot be obtained.
11)Experienced users can set a proper PID parameter according to their experience.
0
1
2
3
4
5
6
7
8
9
10
11
12
13
14
15
16
17
18
19
20
21
22
23
24
25
26
27
28
29
30
31
32
Code Function
NO
CH1-AL1
CH2-AL1
CH3-AL1
CH4-AL1
CH5-AL1
CH6-AL1
CH7-AL1
CH10-AL1
CH9-AL1
CH11-AL1
CH12-AL1
CH13-AL1
CH14-AL1
CH15-AL1
CH16-AL1
CH1-AL2
CH2-AL2
CH3-AL2
CH4-AL2
CH5-AL2
CH6-AL2
CH7-AL2
CH8-AL2
CH9-AL2
CH10-AL2
CH11-AL2
CH12-AL2
CH13-AL2
CH14-AL2
CH15-AL2
CH16-AL2
CH8-AL1
Code Function Code Function Code Function
No.
Name
Symbol
Illustration Setting range
Factory
setting
Display the number of channels, indicating the number
of measurement channels actually used by the instrument
Display the starting channel number, which is used to indicate
number of channel 1 in multi-machine application. For example:
when DNS=3, CH3~CH18 represent 1~16 channels respectively
Channel cycle display time, 0 means cancel automatic cycle display
Software version.
7
8
9
10
11
12
High and low limit absolute
value interval alarm
※High and low limit deviation
value interval alarm
High/low limit absolute value
alarm
High/low limit deviation value
alarm
※High limit absolute value
and low limit deviation value
interval alarm
※High limit deviation value
and low limit absolute value
interval alarm
SV
SV
SV
SV
SV
SVSV-AL1
SV-AL1
SV-AL1
SV+AL2
SV+AL2
SV+AL2
AL2
AL2
AL2
AL1
AL1
AL1
(1) Alarm parameters and output logic diagram:
Symbol description: “☆” means HY, “▲” means alarm value, “ ” means SV value
Alarm
code Alarm mode
Alarm
code Alarm mode
Alarm output(AL1 & AL2 are independent from each)
Image:the hatched section means the alarm action
The below two alarm parameters(AL1,AL2) are used in
combination, AL1 alarm output, AD2 must be set as 0
PV
PV
PV
PV
PV
PV
☆
☆
☆
☆
☆
☆
☆
☆
☆
☆
☆
☆
▲▲
△
△
▲▲
△
▲▲
△
▲▲
△
▲
▲
▲
▲
△
△
High limit absolute value
alarm
1
2
3
4
5
6
※High limit deviation
value alarm
※Low limit deviation value
alarm
※High/low limit deviation
value alarm
※High/low limit interval
value alarm
Low limit absolute value
alarm
SV+AL
SV+AL
SV-AL
SV-AL SV
SV SV+ALSV-AL
AL
SV
SV
SV
SV
PV
PV
PV
PV
PV
PV
AL
☆
☆
☆
☆☆
☆
☆
▲
▲ ▲
▲ ▲
▲
△
△
△
☆
▲
△
△
△
▲
※When the alarm value with deviation alarm is set as a negative number, it will be dealed as an
absolute value.
(2)Alarm extension function table
AE1/AE2
value
0
1
2
3
4
5
Alarm handling method when
it displays HHHH/LLLL Power on, alarm inhibition
Power on, no alarm inhibition
(As long as the alarm condition is met, alarm
output immediately.)
Power on, alarm inhibition
(After power on and before the PV value reaches
the SV for the first time, the alarm is forced to
close, After that alarm work normally)
Alarm status remains the same
Forced alarm output
Forced alarm close
Alarm status remains the same
Forced alarm output
Forced alarm close

7 8
Continued from the front chart
XII. Protocol
Instrument parameter address mapping table
0x2000~0x200F(48193~48208)
0x2010~0x201F(48209~48223)
0x2100~0x210F(48449~48464)
0x2110~0x211F(48465~48481)
0x2120~0x212F(48481~48496)
0x2130~0x213F(48497~48512)
0x2140~0x214F(48513~48528)
0x2150~0x215F(48529~48544)
0x2200~0x220F(48705~48720)
0x2210~0x221F(48721~48736)
0x2220~0x222F(48737~48752)
0x2230~0x223F(48753~48768)
0x2300~0x230F(48961~48976)
0x2310~0x231F(48977~48992)
0x2320~0x232F(48993~49008)
0x2330~0x233F(49009~49024)
0x2340~0x234F(49025~49040)
0x2400~0x240F(49217~49232)
0x2410~0x241F(49233~49248)
0x2420~0x242F(49249~49264)
0x2430~0x243F(49265~49280)
0x2440~0x244F(49281~49296)
0x2500(49473)
0x2501(49474)
0x2502(49475)
0x2503(49476)
0x2504(49477)
1
2
3
4
5
6
7
8
9
10
11
12
13
14
15
16
17
18
19
20
21
22
23
24
25
26
27
PV1~PV16
STA1~STA16
MV1~MV16
SV1~SV16
RSA1~RSA16
SSM1~SSM16
SLL1~SLL16
SLH1~SLH16
INP1~INP16
FL1~FL16
FH1~FH16
DP1~DP16
PS1~PS16
FT1~FT16
DTR1~DTR16
BRL1~BRL16
BRH1~BRH16
OLL1~OLL16
OLH1~OLH16
PRS1~PRS16
RSS1~RSS16
DN
DNS
DNT
AU1P
AU2P
UNIT1~UNIT16
Upper range limit
Lower range limit
Demical point
Display correction value
Display filter coefficients
Show trace values
Output lower limt
Output upper limt
Transmission output lower limit
Transmission output upper limit
Measurement display unit
Set parameter save location
Display channel quantity
Display the starting channel number
Channel cycle display time
Auxiliary output 1 program
Auxiliary output 2 program
RUN/STOP
Save Location
Unlisted address reserved
Unlisted address reserved
Unlisted address reserved
Unlisted address reserved
Unlisted address reserved
Unlisted address reserved
Unlisted address reserved
Unlisted address reserved
Unlisted address reserved
Unlisted address reserved
Unlisted address reserved
Measured value
Status value
PID control output
Setting value
Switch
Panel R/S enable
switch
Limit setpoint
lower limit
Limit setpoint
upper limit
Input type
No. Address (register number ①)Read
Write
Qty Remark
R
R
1
1
R/W
R/W
1
R/W1
R/W1
R/W1
R/W1
R/W1
R/W1
R/W1
R/W1
R/W1
1
R/W1
R/W1
R/W1
R/W1
R/W1
R/W1
R/W1
R/W1
R/W1
R/W1
R/W1
R/W
Reserved
Reserved
Reserved
Reserved
0:ROM
1:RAM
1
R/W1
R/W1
R/W1
R/W1
R/W1
R/W1
R/W1
R/W1
R/W1
R/W1
R/W1
0:RUN
1:STOP
0:Banned
1:ON
R:Read only;R/W:Read/Write
Note ③: DTC communication data transmission sequence description
Reserved
Byte transfer order: When 0, 1, 2, when 1, 2, 1
Reserved
□ □ □
DTC:
※16-bit CRC check code to obtain C program
unsigned int Get_CRC(uchar *pBuf, uchar num)
{
unsigned i,j;
unsigned int wCrc = 0xFFFF;
for(i=0; i<num; i++)
{
wCrc ^= (unsigned int)(pBuf[i]);
for(j=0; j<8; j++)
{
if(wCrc & 1){wCrc >>= 1; wCrc ^= 0xA001; }
else
wCrc >>= 1;
}
}
return wCrc;
}
D9 D8 D7 D6 D5 D4 D3 D2 D1 D0
____ AT HHHH LLLL ℃F AL2 AL1 ____ OUT1
Note ①: The register number is formed by converting the address into decimal and adding 1, and
then adding the register identification code 4 in front; for example: the register number of the data
address 0x2000 is 8192+1=8193 and then adding 4 in front, that is, the register number 48193;
Related applications can be seen such as Siemens S7-200 PLC.
Note ②: Channel status indication, when the data bit is 1, it means executing, and when it is 0,
it means not executing.
28
29
30
31
32
33
34
35
36
37
38
39
40
41
42
43
44
45
46
47
48
49
50
51
52
53
54
55
56
0x2800
~
0x280F(410241
~
410256)
0x2810
~
0x281F(410257
~
410272)
0x2820
~
0x282F(410273
~
410288)
0x2830
~
0x283F(410289
~
410304)
0x2840
~
0x284F(410305
~
410320)
AL21
~
AL216
AD21
~
AD216
HY21
~
HY216
AE21
~
AE216
OT1
~
OT16
P1
~
P16
I1
~
I16
D1
~
D16
OVS1
~
OVS16
R/W1
R/W1
R/W1
R/W1
0x2600
~
0x260F(49729
~
49744)
0x2610
~
0x261F(49745
~
49760)
0x2620
~
0x262F(49761
~
49776)
0x2630
~
0x263F(49777
~
49792)
AL11
~
AL116
AD11
~
AD116
HY11
~
HY116
AE11
~
AE116
Alarm value
Alarm method
Alarm hysteresis
Alarm expansion mode
Alarm value
Alarm method
Alarm hysteresis
Alarm expansion mode
R/W
0x2F00(412033)
0x2F01(412034)
0x2F02(412035)
0x2F03(412036)
0x2F04(412037)
0x2F05(412038)
ADD
BAD
PRTY
DATC
LCK
NAME
Communication address
Communication baud rate
Check Digit Selection
Data sending order
Password lock function
Instrument name
R/W
Control execution way
Compressor cooling start delay
PID type
Actual load power (KW)
Total Load Power Limit (KW)
1
R/W1
R/W1
R/W1
R/W1
1
R1
R1
R1
R1
R1
0x2A00
~
0x2A0F(410753
~
410768)
0x2A10
~
0x2A1F(410769
~
410784)
0x2A20
~
0x2A2F(410785
~
410800)
0x2A30
~
0x2A3F(410801
~
410816)
0x2A40(410817)
ACT1
~
ACT16
PT1
~
PT16
PDC1
~
PDC16
LPH1
~
LPH16
SLPL
R/W1
R/W1
R/W1
R/W1
R/W1
0x2900
~
0x290F(410497
~
410512)
0x2910
~
0x291F(410513
~
410528)
0x2920
~
0x292F(410529
~
410544)
0x2930
~
0x293F(410545
~
410560)
0x2940
~
0x294F(410561
~
410576)
CP1
~
CP16
DB1
~
DB16
AM1
~
AM16
CP11
~
CP116
PC1
~
PC16
Main control cycle
Bit control hysteresis
Automatic hand switch
Cooling control cycle
Cooling scaling factor
Control method
Proportional band
Integration time
Differential time
Overshoot limit
NO. Address (register number ①) Parameter Parameter
Description
Parameter Parameter
Description
Read
Write
Qty
Remark
0x2700~0x270F(49985~410000)
0x2710~0x271F(410001~410016)
0x2720~0x272F(410017~410032)
0x2730~0x273F(410033~410048)
It uses Modbus RTU communication protocol, read 04 area to keep the register function number
be 0x03, write function number 0x10 or 0x06, adopts 16-bit CRC check, it does not return the
check error. The data type is a 16-bit signed or unsigned integer.
Data frame format:
1. Read register
Example: The host reads PV1 value (PV1=200)
The register address of PV1 is 0x2000 ("0x" stands for hexadecimal), because the data type
of SV is a 16-bit integer (2 bytes), 1 register. The decimal integer 200 is converted to hexadecimal
as 0x00C8. Note: When reading data, you should first determine the decimal point position and
convert the read data to get the actual value.
Start bit
Data bit
81
1None/Odd/Even
Stop bit Check bit
Device
address
Function
code
Start
ADD
High bit
Start
ADD
Low bit
Data
Length
high bit
Data
Length
low bit
CRC
code
CRC
code
Host request
Slave responds normally 0x01
0x01
0x01
0x03
0x83
0x03
0x02
0x20
0x02 Error code
0x00
0x00 0xC8
0xC0
0xB9 0xD2
0xCA0x8F0x01
0xF1
0x00
Slave abnormal response
2. Write multiple registers
Example: The host writes multiple registers (using function code 10) write SV1 value (SV1=150)
The register address of SV1 is 0x2110, because the data type of SV1 is 16-bit integer (2 bytes), 1
register. The decimal integer 150 is converted to hexadecimal as 0x0096. Before writing data, convert
the data to the corresponding magnification and then write the data to the meter.
0x01 0x10 0x21 0x10 0x00 0x01 0x02 0x00 0x96
Host request (write multiple registers)
Meter
add
Meter
add
Start
ADD
High bit
Start
ADD
Low bit
Start
ADD
High bit
Start
ADD
Low bit
Data
low bit
Data
high bit
Data
length
low bit
Data
length
high bit
Data
length
low bit
Data
length
high bit
Data
byte
length
Function
code
Function
code
CRC
code
CRC
code
0x15 0xAC
Slave responds normally (write multiple registers)
※CRC code
high bit
※CRC code
low bit
0x300x0A0x010x000x100x210x100x01
CRCCRC
Slave normal
responds
Meter
add
Function
code
0x000x100x210x060x01
Host request
Write single register
Add
high bit Add
low bit
Data
high bit
Data
low bit
0x5d0x020x96
0x5d0x020x96
0x000x100x210x060x01
0xA10x01 0x86 function code 0x02 erro code 0xC3
Slave abnormal
response
Host write single register (06 function code) write SV value (SV=150)
no.of bytes
Example: host request add is 0x2011
Read multiple registers
Communication abnormal handling:
In the case of abnormal response, the highest bit of the function number is set to 1.
For example, if the function number requested by the master is 0x03, the corresponding item of the
function number returned by the slave is 0x83.
0x01---Illegal function: The instrument with the function number sent by the host does not support it.
0x02---The address is illegal: the register address specified by the host exceeds the allowable
range of the instrument parameter address.
0x03---Illegal value: The write data value sent by the host exceeds the allowable range of the
instrument.
Display
LLLL/HHHH
No display after
power on
Check whether the voltage is normal; whether the contact is poor; whether the
internal protection of grid harmonics is too high.
Check whether the wiring is correct; whether the contact is bad;
whether the ACT/OT menu setting is wrong;
No output
No
communication
Troubleshoot hardware connection, instrument settings,software read settings;
binary conversion errors; address errors; data errors
How to troubleshoot
Check whether the input is disconnected; check the FH value and FL value;
whether the work temperature is normal & the input signal selection is correct.
XI. Simple troubleshooting method
3. Single channel power limit:
1) OLL and OLH are used to limit the mini to maximum range of the single channel output control
amount, which is 0 to 100% by default.
2) The OLL setting value must be less than the OLH setting value.
3) If the OLH setting value is too small, the control efficiency and speed will be affected, and the target
value may not be reached.
4) The single-channel power limit cannot realize the total power limit function.
4. Total power limit function:
1) When the actual power LPH setting value of each channel is greater than 0, that is, this channel
participates in the function of total power limit SLPL and power even distribution.
2) If the total power limit value SLPL is set too small, it will affect the control response speed of each
limit channel, or even fail to reach the target value. Therefore, it should be set appropriately according
to the actual situation.
3) After setting the LPH and SLPL values, the controller will automatically stagger and distribute the
load power evenly to avoid the impact of the simultaneous full power output of each channel on the
grid.
4) The channel that is performing auto-tuning will temporarily exit the total power limit, and will
automatically recover after the auto-tuning is completed.
This manual suits for next models
2
Other Toky Temperature Controllers manuals
Popular Temperature Controllers manuals by other brands
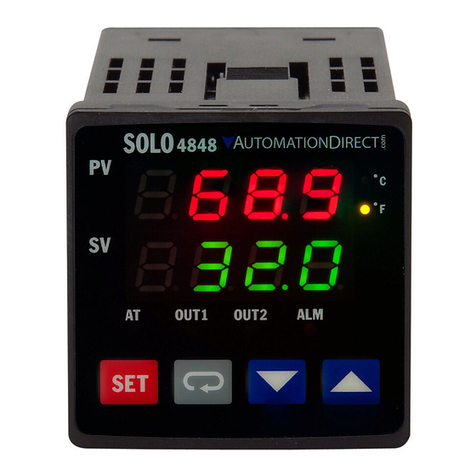
Solo
Solo SL4848-RR quick start guide
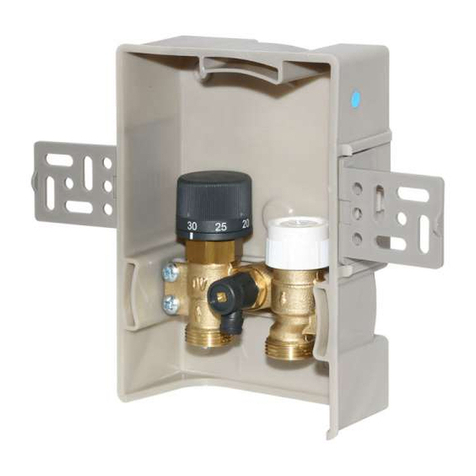
oventrop
oventrop Unibox E BV vario operating instructions
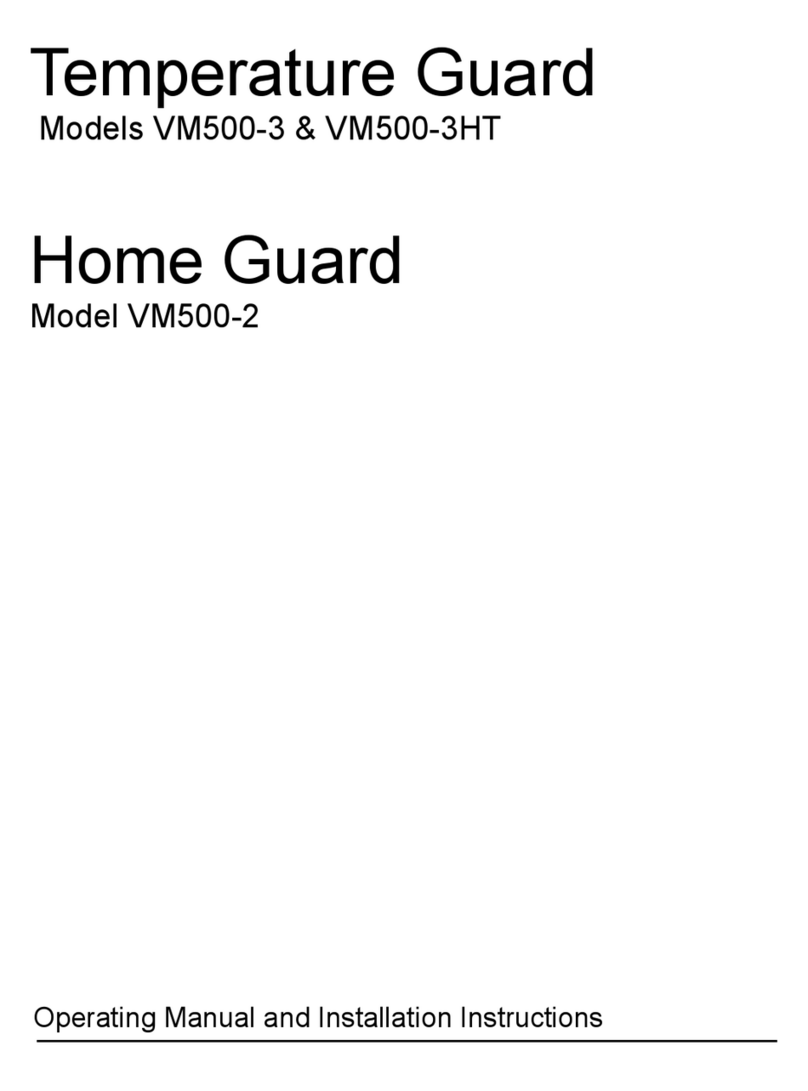
Temperature Guard
Temperature Guard VM500-2 Operating Manual and Installation Instructions
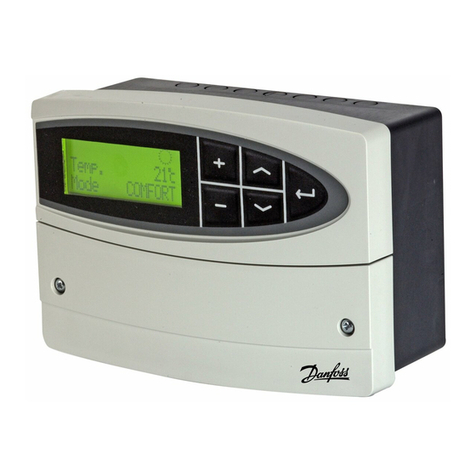
Danfoss
Danfoss ECL Comfort 110 operating guide
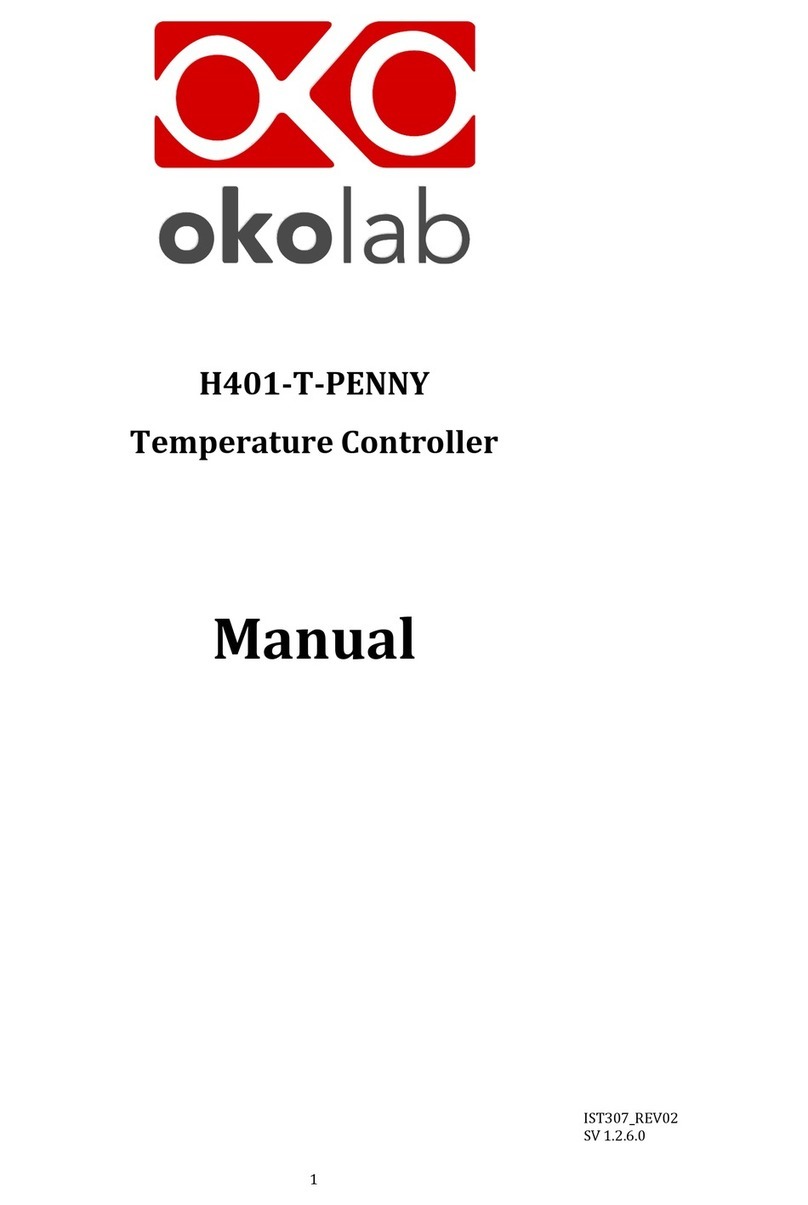
Okolab
Okolab H401-T-PENNY manual
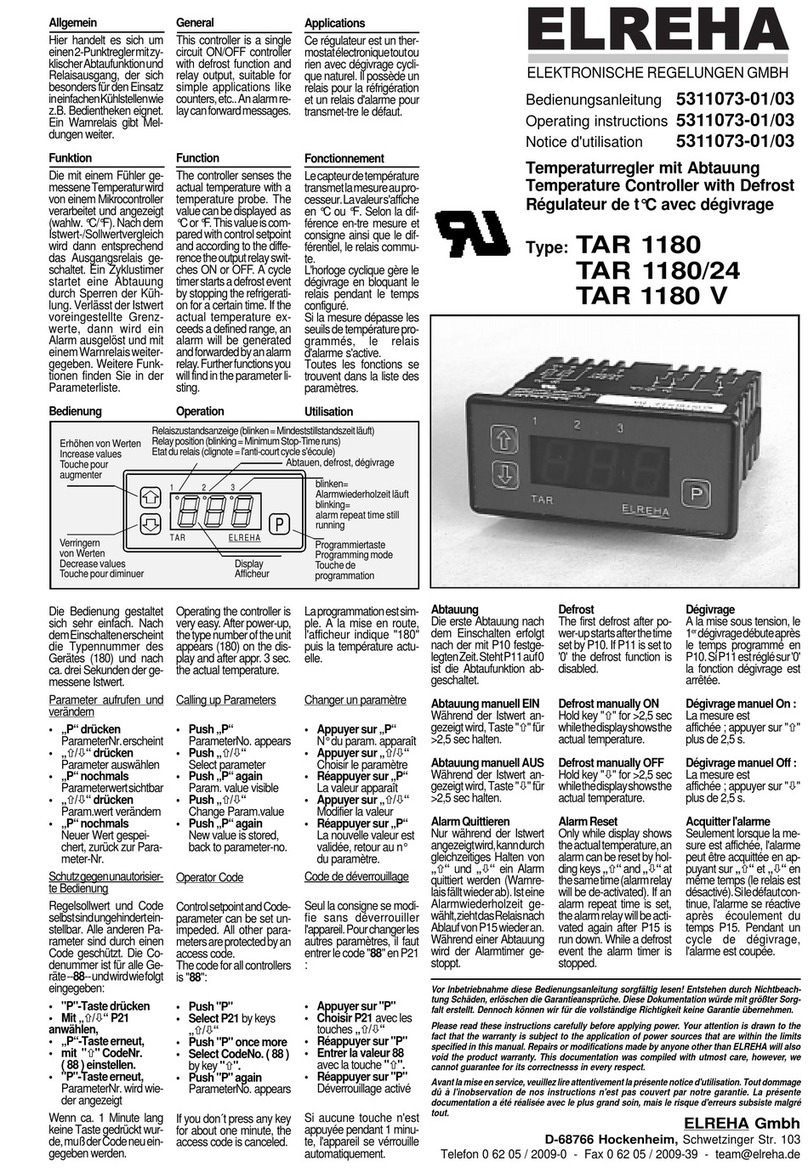
ELREHA
ELREHA TAR 1180/24 operating instructions