TRIATEK UVM-1000 User manual

1
UVM-1000
Universal Valve Module
LIT-12013155
September 2020
Installation Guide
This equipment has been tested and found to comply with the limits for a Class A digital device pursuant to Part 15 of the FCC
Rules. These limits are designed to provide reasonable protection against harmful interference when this equipment is operated in a
commercial environment. This equipment generates, uses, and can radiate radio frequency energy and, if not installed and used in
accordance with the instruction manual, may cause harmful interference to radio communications. Operation of this equipment in a
residential area may cause harmful interference, in which case users will be required to correct the interference at their own expense.
Canada
This Class (A) digital apparatus meets all the requirements of the Canadian Interference-Causing Equipment Regulations.
Cet appareil numérique de la Classe (A) respecte toutes les exigences du Règlement sur le matériel brouilleur du Canada.
IMPORTANT: The UVM-1000 Universal Valve Module must be wired to 24 VAC only. Wiring the unit to 110 VAC will cause serious
damange and void the warranty.
Risk of Property Damage.
Ensure that the power source conforms to the requirements of the equipment. Failure to use a correct power source may result in
permanent damage to the equipment.
Risque de dégâts matériels.
S’assurer que la source d’alimentation électrique est conforme aux spécications de l’équipement. L’utilisation d’une source
d’alimentation électrique inappropriée risque d’endommager irrémédiablement l’équipement.
North American Emissions Compliance
United States

UVM-1000
LIT-12013155
2
Setup Overview............................................................................................................................................................................ 3
Introduction / Overview of Operation ........................................................................................................................................ 4
Overview of Operation ................................................................................................................................................................ 6
Installation and Setup ............................................................................................................................................................... 11
UVM to FMS165X-S-0-1 Start Up .............................................................................................................................................. 17
Wiring ......................................................................................................................................................................................... 17
UVM Conguration Tool............................................................................................................................................................ 19
Before you begin .................................................................................................................................................................. 19
Overview of Lin Module Interface......................................................................................................................................... 19
Installation.................................................................................................................................................................................. 20
Misc Tab ..................................................................................................................................................................................... 22
User Settings Tab ...................................................................................................................................................................... 23
User Cong Settings ............................................................................................................................................................ 24
User Settings Tab and CFM Table Tab..................................................................................................................................... 27
CFM Table Tab ........................................................................................................................................................................... 28
CFM Table Tab and Dynamic Values Tab................................................................................................................................. 29
Dynamic Values Tab .................................................................................................................................................................. 30
Dynamic Values Tab and Factory Cong Settings Tab.......................................................................................................... 32
Factory Settings Tab ................................................................................................................................................................. 33
Factory Settings Tab and Calibration Import Tab................................................................................................................... 34
Table of contents

UVM-1000
LIT-12013155
3
Setup Overview
UVM Box and Venturi valve
1. Valve is calibrated at Triatek®.
2. The valve label indicates the calibration values at set positions.
3. Set controllers for a 0 V - 10 VDC, or 10 V - 0 VDC depending on the valve actuation type, Normal or Reverse acting.
4. Set the output airow scale based on your valve size.
5. Set your feedback signal voltage the same as the cfm scale.

UVM-1000
LIT-12013155
4
Introduction
Triatek’s Universal Valve Module (UVM) is designed to allow for
interoperability between Triatek Venturi valves and third party
controllers.
Each Triatek valve is individually calibrated and has its own
unique position to cubic feet per minute (cfm) curve. The UVM
enables you to create a linearization curve in each controller for
each associated valve. It also allows you to span, scale, and
linearize the feedback sensor to obtain useful information from it.
Overview of Operation
A diagram of the basic functionality of the UVM is shown in
Figure 1.
The UVM takes a 0 -10 V signal from the third party equipment,
and depending on the scaling setting, interprets this as a 0 –
xxxx cfm request signal. The UVM is pre-programmed with the
associated valve’s linearization curve, and will move the valve’s
actuator to the correct position for the requested cfm.
Each valve is tted with an electronic position sensor on the lever
arm at the point of entry into the valve body (see Figure 1). The
electronic position sensor is used to provide actual valve position
information to the controllers. This signal is non-linear, and has a
random 0 and 100% position voltages.
It converts the sensor signal to a position on the valve and then
translates that to a cfm value. The cfm value is in turn output
from the UVM as a 0 – 10 V signal at the same scaling as the
cfm request signal.
The 0 -10 V signal is processed by the valve’s calibration
settings as set by the factory. The user has the ability to access
and adjust this curve if so desired. The subsequent signal is
then converted to an equivalent cfm request value. This value
is dependent on settings provided by the factory as applicable
for the associated valve size. The user can modify this signal if
desired.
The factory default settings relative to valve size are:
8 in. valve 10 V = 800 cfm
10 in. valve 10 V = 1100 cfm
12 in. valve 10 V = 1600 cfm
14 in. valve 10 V = 2300 cfm
The equivalent cfm request value is applied to the calibration
curve as entered by the factory for the associated valve and a
corresponding valve position value is generated.
This position value is applied to the actuator output voltage
calibration section and output to the actuator. The consequent
result is that the actuator will move to the required position so
that the valve passes the requested cfm.
As the valve moves to position, the position feedback sensor
moves as well. The signal from this sensor is processed by a
sensor voltage to position calibration section. The output of this
section provides an accurate position value. The position value is
applied to the position to cfm mapping table and a corresponding
cfm value is output.
This cfm value is then passed through cfm to voltage scaling
factor and converted to a voltage value. This value is then
passed through the factory set output calibration section and
made available to the voltage output for use by the third party
equipment as the actual valve cfm.
In certain circumstances the feedback signal may not match the
requested cfm signal. If 0 cfm is requested (0V input), and the
valve is a partially closed valve, the valve has a minimum cfm
that it can attain. This value is not 0 and for a 12 in valve would
be around 90cfm. In this case the feedback signal would be the
equivalent of 90 cfm or 0.56V for a 10V = 1600 setting.
If a UVM for an 8 in. valve is set with an arbitrary scaling of 10V
= 1100 cfm (or 110 cfm / volt), and a request signal of 9 V (or 990
cfm) is input to the unit, then the actuator will end up driving to
100%, as the maximum the valve can do is 700 cfm. The voltage
feedback output signal will only be around 6.4 V as the actual
valve cfm would be around 700.
Introduction / Overview of Operation

UVM-1000
LIT-12013155
5
Triatek reserves the right to change product specications without notice.
Figure 1. Basic Functionality of the UVM
Electronic Position Sensor
Actuator
UVM Box
Venturi Valve

UVM-1000
LIT-12013155
6
Overview of Operation
Figure 2. UVM Use with DP Switch
Digital Input DP Switch
The UVM has the ability to accept a digital input DP switch. The
pneumatics of the DP switch are connected across the valve, and
the factory supplied switch is set to trip at 0.6 in. W.G.
Any pressure across the valve below this is to be interpreted as
the valve cfm is inaccurate or non-existent. The DP switch signal,
when enabled in the UVM, is used to provide a 0 cfm feedback
signal should the pressure across the valve drop below the 0.6
in. W.G. threshold.
The DP switch functionality can also be implemented by using
a pressure sensor with a 0-5 V output. The UVM can accept the
0-5 V signal and, via user gain and oset settings, convert it to an
internal pressure value.
Typically a 0-4 or 5 in. W.G. sensor would be used. When
enabled in the UVM, this value can be compared to a minimum
pressure value (typically 0.6 in. W.G.) as a threshold below
which, as like the DP switch, the cfm feedback signal goes to 0.

UVM-1000
LIT-12013155
7
Figure 3. UVM with Pressure Sensor

UVM-1000
LIT-12013155
8
Figure 4. UVM use as a VAV Interface
The UVM can also be made to operate with a variable air volume
(VAV) box instead of a Venturi valve. In this case, instead of
providing the UVM with a cfm request signal, the input will
be interpreted as an actuator position signal where 0-10 V
represents a 0 -100% position signal.
This signal only provides positioning information for the VAV
box. The feedback sensor signal is replaced by the VAV box
ow probe pressure signal. This voltage signal is scaled and
converted to an internal pressure value.
The pressure value is then square-rooted and multiplied by a K
factor to obtain an internal velocity value. The velocity value is
multiplied by a duct area value to obtain an internal cfm value.
This cfm value is then scaled to the appropriate voltage, passed
to the Vo feedback voltage signal for use by the third party
controller. The scaling, K factor, and area can be set by the user
with the UVM Conguration Tool.

UVM-1000
LIT-12013155
9
Figure 5. UVM Module DIP Switch Functions
Other than through the UVM Conguration Tool, the user does
not have access to any settings or operating modes of the UVM.
The exception is that the input and output signal modes and the
normal/reverse operation can be set via the DIP switches if that
functionality is enabled in the UVM.
The inputs and outputs can be set to be interpreted as a
Percentage (0 – 10 V = 0 – 100%) control or feedback signal, or
as a cfm ( 0 – 10 V = 0 – xxxx cfm ) control or feedback signal.
DIP switches 6 and 7 are used for this function. DIP switch 5 is
Normal Reverse Selection.
The UVM can communicate with the UVM Conguration Tool. To
this end, the UVM can reside at one of 16 hardware addresses.
These addresses are set via DIP switches 1, 2, 3, and 4. Via
the UVM Conguration Tool, the UVM is able to have up to an
additional 16 software addresses set for communications use.

UVM-1000
LIT-12013155
10
Due to continuous improvement, Triatek reserves the right to change product specications without notice.Triatek reserves the right to change product specications without notice.
Figure 6. UVM Controller Utilizing UVMNet to sum cfm values
The later version (S series revisions) is capable of being
congured to sum cfms over the RS485 network and output
the summed equivalent on the Vo of the unit designated to be
primary. The primary unit is the unit designated with hardware
address 15. Secondary (polled) units are units with address 16
on-wards. The primary unit species how many units to poll from
address 16 on-wards.

UVM-1000
LIT-12013155
11
Due to continuous improvement, Triatek reserves the right to change product specications without notice.
Installation and Setup
Triatek reserves the right to change product specications without notice.
The light blue area depicts the UVM housing, and the green
area the UVM board. The actuator and feedback sensor are
already wired as is the isolation transformer. Connect 24VAC to
the supplied power tails. This feeds both the actuator and the
isolation transformer.
The 24 VAC supply needs to be capable of providing at least
25 VA, with 20 for the actuator and 5 VA for the UVM. The
0 – 10 V cfm request signal is attached to the IN connection
on the UVM board, with the ground lead going to any of the
GND connections. The feedback signal is derived from the Vo
connection and any of the GND connections.
Figure 7. Universal Valve Module Wiring

UVM-1000
LIT-12013155
12
Due to continuous improvement, Triatek reserves the right to change product specications without notice.
Normal-Reverse Operation
The valve actuator can be set for normal/reverse operation.
This is to ensure that the various desired failsafe actions can be
achieved.
The failsafe modes include loss of power and loss of signal. The
UVM has a setting, either through the UVM Conguration Tool or
by DIP switch (if enabled) to select its Normal-Reverse Mode of
operation.
Set the Normal – Reverse acting DIP switch (if enabled), or
check/uncheck the reverse operation check box in the Misc Tab
of the UVM Conguration Tool to the desired mode of operation.
If the reverse setting is selected, then for revisions 0.75 and
upwards, the actuator needs to be set to reverse acting, and
the command signal from the third party controller needs to be
inverted (reverse operation).
In this case (reverse operation) the signal from the OEM
controller will be 10 – 0 V for 0 – xxxx cfm, and the actuator
output control signal from the UVM will be 20 – 4 mA for 0 –
100% positioning.
The feedback signal will always be 0 – 10 V for 0 – xxxx cfm,
it is never inverted.
For normal operation, typically used for supply valves, the
settings shown in Figure 8* are recommended.
For reverse operation, typically used for exhaust and hood
valves, the settings shown in Figure 9 are recommended for
UVM revisions 0.75 onwards. Earlier revisions do not invert the
UVM input signal.
*Figures 8 and 9 are on next the page.

UVM-1000
LIT-12013155
13
Due to continuous improvement, Triatek reserves the right to change product specications without notice.Triatek reserves the right to change product specications without notice.
Figure 8. Normal Operating Mode
Figure 9. Reverse Operating Mode
OFF
ON
ON
OFF
ON

UVM-1000
LIT-12013155
14
cfm / Percentage Selection
There is a DIP switch (when enabled) for each of the control
input and the feedback output. The individual DIP switch allows
the input or output voltage to be interpreted as cfm signal
or position signal. If the switch is set for cfm then the signal
represents what ever scaling the UVM is setup for cfms.
So if the cfm at 10 V is set to 1600, then an input voltage of 10 V
is a request for the valve to be at 1600 cfm, and a feedback out
of 10 V indicates the valve is doing 1600 cfm. If the DIP switch
is set to position, then 10 V is a request for the actuator to be
at 100%, and with the feedback Vo indicates the actuator is at
100%. There are separate switches for the input IN signal and
the output Vo signal.
Valve Flow Integrity (DP Switch)
If a DP switch is to be attached, it is done by connecting
voltage free NO or NC contacts between GND and DI. The
UVM has an internal 15K pull-up to the internal 3.3 V rail. This
input is protected to 15 V for application of over-voltages. NO
or NC operating mode can be set in the UVM via the UVM
Conguration Tool.
- Vin
Figure 10. DP Switch Connections

UVM-1000
LIT-12013155
15
DP Switch Connections
A pressure sensor can also be used to determine the pressure
across the valve and 0 the cfm feedback signal when the
pressure falls below a preset threshold. The UVM Conguration
Tool is used to scale the pressure sensor input, enable the
pressure sensor and dene the lower pressure threshold. The
pressure sensor is wired as shown below.
- Vin
Figure 11. Pressure Sensor Wiring

UVM-1000
LIT-12013155
16
Should the UVM be supplied without the valve and any pre-
wiring, then the following items are required to wired to the unit.
The device requires that Io be connected to an actuator capable
of accepting 4 – 20 mA. The connection is from Io and any GND
connector. The device also needs a 0 -5 signal from a valve
feed back sensor. This is connected to CN3 pins G, +Vfb and
FB. G is ground or common, +Vfb is the 5 V power to power the
position sensor, and feedback is the signal from the sensor that
represents its position.
The actuator and UVM need be isolated from each other by
means of a 24/24 isolation transformer.
In the case of dual and other multiple combination valves of the
same size, the following wiring is used. The feedback sensors
need to have a 1K ohm ¼ W 1% resistor placed in series with
the position signal output. Only one of the actuators should have
the 4-20 mA setting, the remaining actuators should be set for
2-10 V operation.
- Vin
Figure 12. Position Sensor / Actuator Wiring
- Vin
Figure 13. Dual Valve Operation

UVM-1000
LIT-12013155
17
This guide is specic to the installation of the FMS-1655 Room
Pressure Controller with the UVM. The information provided is
merely suggestive and does not supersede any data provided in
the Triatek Programming and Installation Guides.
1. The controller must be opened by rst loosening the four
screws in the sides. Then separate the FMS Controller from
the back plane.
2. Check Dip Switches in the FMS Controller.
Note: S1 has 8 switches. Switches 1 through 4 are to congure
Analog Inputs 1 through 4 as either voltage or current Input while
switches 5 through 8 set the signal range of Analog Inputs 1 to 4
as 0-5 VDC or 4-20 mA when selected OFF or 0-10 VDC when
selected ON. In other words, switch 5 sets the range for analog
input 1. Likewise, switch 6 sets the range for analog input 2. For
example, setting switch 1 ON and 5 OFF sets Analog Input_1
as signal type Current (mA) with a range of 4-20 mA. However,
setting switch 3 OFF and 7 ON sets Analog Input_3 as signal type
Voltage (V) with a range of 0-10 VDC.
3. Switch 1 of S1 should be ON for Current (mA) signal input
when using Triatek Digital sensors due to the Dierential
Pressure output type being 4-20 mA.
4. Please consider the additional devices such as UVM
feedback signals for type and range on designated inputs. For
Example: Supply UVM (Vo to Ground) feedback should be on
Analog Input 3. The input must be set as Voltage by setting
S1 switch 3 OFF with a 0-10 VDC range with switch 7 ON. If
the FMS is expected to control for volumetric oset, then the
Exhaust MUST be controlled by Analog Output 4 (0-10 VDC).
Therefore, the feedback of the Exhaust should be on Analog
Input 4. The input must be set as Voltage and 0-10 VDC by
setting S1 switch 4 OFF and switch 8 ON.
5. Analog Output should be set to determine the voltage range
preferred for the UVM Input signal. The UVM is designed
for a 0-10 VDC control Input signal. Therefore, dip switch
S4 should be set for 0-10 VDC for outputs controlling UVM
devices. Set all S4 switches to OFF for 0-10 VDC outputs of
analog outputs 1-4.
6. Next is the Protocol switch. S3 switch 5 should be OFF while
all other switches are ON for BACnet protocol and no network
termination required of FMS165X controller.
7. At this point, the FMS controller hardware settings have
been completed. However, the software congurations must
be completed for proper operation of controller. Also, the
wiring of the controller must be veried for correct device
terminations of inputs and outputs.
Wiring
Power
The FMS Controller is powered by (fused) 24 VAC.
IMPORTANT: Do not power both FMS Controller and valve
actuator with the same Triatek issued isolation transformer.
Analog Inputs
Most Common Conguration with Triatek devices for volumetric
oset control.
Analog Input 1 (AI_1): 3 Wire mA output sensor is wired to AI1.
Three wires are Sensor Power (DIGITAL SNS_PWR), Ground
(GND) and ANALOG_INput 1 (AI_1). The sensor should be wired
as follows from Controller to Sensor: DIGITAL SNS_PWR to +Vin;
GND to GND; AI_1 to Io.
GND and Io. Io is the 4-20 mA output to controller termination.
Note: A third party sensor can be used. However, the sensor
range must be entered correctly. Be sure to convert the sensor
pressure range from Pa to in. W.C. as the scale is in. W.C. by
default.
Analog Input 2 (AI_2): Temperature Sensor should be wired here
AI_2 to GRND.
Analog Input 3 (AI_3): 2 Wires from Supply UVM VO and ground
for a 0-10 VDC feedback signal to the FMS165x Analog Input_3
and ground. This connection is important for the display of Airow
Value on AI_3 for Supply.
Analog Input 4 (AI_4): 2 Wires from the Exhaust UVM VO and
ground for a 0-10 VDC feedback signal to the FMS165x Analog
Input_4 and ground. This connection is important for the display of
Airow Value on AI_4 for Exhaust.
Note: If volumetric oset control is preferred, then Analog Input_3
must be congured rst for Flow. Then congure Analog Input_4
for ow and the volumetric oset option will be made available.
The volumetric oset option is only made available in the menu of
analog input 4 if analog input 3 has been congured for ow.
Analog Outputs
The output wiring (control signal) goes from FMS back plane CN3
Analog Outputs 1-4 to UVM IN and Ground. Be sure to map the
correct input to output for expected control. I recommend mapping
analog output 4 to analog input 4. Also, analog output 3 should be
mapped to analog input 3. This mapping is accomplished in the
Main Menu >> System Setup >> Next >> Ai/Ao Mapping.
Analog Output 4: 2 Wires to the UVM Control Board IN and
Ground of valve being controlled to track for volumetric oset
control. Typical with BMS controlling Supply or Exhaust and the
FMS is expected to regulate Supply or Exhaust by tracking for
volumetric oset control.
Auxiliary Outputs
The auxiliary outputs are provided for the following voltages:
• 5 VDC
• 10 VDC
• +V = 32 VDC Typically used to power Occupancy Sensor
Network
BMS wiring goes on connector CN4 of backplane. It is polarity
sensitive. Uniformity of positive to positive and negative to
negative must be maintained throughout the network.
UVM to FMS165X-S-0-1 Start Up

UVM-1000
LIT-12013155
18
Software Settings
This is only a reference as programming the settings in most
cases isn’t sequence dependent with the exception of controllers
programmed for VOC (Volumetric Oset control). Enter Isolation
set point.
Note: it is recommended that the Room Isolation preference be
set before entering the settings for analog input 1.
Main Menu >> Unit Setup >> Room Setting >> Begransat lage >>
Select Primary, then select preferred Isolation Mode.
Go to Main Menu
1. System Setup >> Analog Inputs >> Analog Input 1
2. Sensor Input Settings >> Select Linearization Disabled and
Select Input Mode Normal (If the dierential pressure [DP]
sensor is installed backwards, then select Inverted Mode to
reverse the input as needed.)
3. Engineering Units >> Pascals Select Range 4-20 mA for
Triatek Sensor
4. AI-1 Sensor Range >> ± 0.25 in. W.C.
5. Enter ISO Set point.
Note: Be sure to indicate (-) for negative isolation set point.
Ex: -2.49
6. Enter Dead band and Select Finish
The same process will be required for all analog inputs. Please
note that feedback signals Vo and Ground from UVM supply and
exhaust should be on AI-3 (Supply) and AI-4 (Exhaust) of the
FMS165X controller. Therefore, FMS165x analog inputs 3 and
4 should be congured respectively. These are Flow Inputs with
Flow Sensor Type. The maximum Flow must be equal to the UVM
10 VDC ow Ex: 10 in. valve UVM is set for 1100 cfm at 10 VDC.
Therefore, the Maximum Flow is also 1100 cfm. Also, the range
in this analog input must be set for 0-10 VDC. Enter set point and
dead band as preferred.
Note: The Maximum Flow at 10 VDC is standardized based on
the Venturi Valve Size.
14 in. valve = 2300 cfm
12 in. valve = 1600 cfm
10 in. valve = 1100 cfm
8 in. valve = 800 cfm
UVM Board
The UVM Controller is precongured for the Venturi Valve it’s
associated with. Therefore, you should only need to do three
things:
1. Provide power 24 VAC to the factory supplied 24/24 Isolation
transformer
2. Connect wiring from the FMS Controller Analog Output to
UVM Controller IN-GRND for control signal
3. Connect wiring to the FMS Controller Analog Input from the
UVM Controller Vo-GRND
Dip Switch/Jumper Settings (Precongured at Factory)
SW1 on UVM Board is an 8 switch dip. Switch 5 (Actuator
Direction) will be set ON (Reverse) for Exhaust. Switch 5 will be
set OFF (Normal) for Supply. Switches 1-4 (Module Address)
should be OFF. Switches 6 and 7 (Operation Mode) will be set ON
for cfm. Switch 8 (Comms Termination) will be OFF.
Jumpers are preset at the factory
JP2-ON
JP-4 ON
JP-5 OFF
Wiring
As previously mentioned, you will only need to connect:
1. Power (24 VAC)
2. IN and Ground (Control Signal 0-10 VDC)
3. Vo and Ground (Feed Back 0-10 VDC)
Actuator (Neptronic Fast Acting)
IMPORTANT: The actuator must not be wired as a load with any
Triatek controllers. The 24 VAC required may be wired in parallel
with an isolation transformer Line side. The actuators consume 15
VA and 24 VA Peak of power.
The Neptronic Fast Acting actuator has a 4 switch dip switch. This
dip switch is precongured in the factory. However, please note
Switches 1 and 2 are typically o with switch 3 ON for Exhaust.
While switches 1,2 and 3 are ON for Supply.
We don’t use switch 4.
1. Switch 1 Rotation CW/CCW
2. Switch 2 Fail Safe at 0 or 90
3. Switch 3 Control Signal Voltage or Current.
The UVM control signal to the actuator is 4-20 mA.

UVM-1000
LIT-12013155
19
Before you begin
UVM Conguration Tool
Requirements to set up your Universal Valve Module (UVM) Conguration Software:
1. Link to UVM Conguration Tool le
2. jZip
3. Microsoft.Net
4. Internet connection (if you need to download Microsoft.Net)
5. USB-RS485
6. Visual Basic Power Pack 10
Overview of Lin Module Interface
Tabs
Ports
This manual will take you through the
initial UVM Conguration Tool installation
process, and then through each tab,
where you will enter in data specic to
your application.

UVM-1000
LIT-12013155
20
1. Open the UVM folder and run the Setup.exe program. The
program will rst try to install VB Powerpack 10. If this fails
to install, use the link below to manually install it (internet
connection is required):
http://go.microsoft.com/fwlink/?LinkID=145727&clcid=0x804
The software utilizes the Microsoft.Net architecture, and if it is
not installed on your computer, the setup program will instigate
a download of Microsoft.Net and install it (internet connection is
required).
2. When the Setup.exe program installation is complete the
Triatek Conguration Program will run.
3. To use the software, you will need a USB-RS485 adaptor
cable installed on the computer (Triatek part number 5-300102 or
commercially, USB-RS485-WE-1800-BT).
4. Take note of the CommsPort to which the RS485 cable is
installed. This can be done by going to Control Panel > Device
Manager > Comm Ports. Pull the USB plug out to see which
CommPort disappears, and then reappears when the USB is
plugged in again.
5. Run the Conguration Program, and if any of the port(s) are
not present, the associated port tab will be highlighted red (see
Figure 3).
6. To manually change the RS485 CommsPort settings or
the ProgrammerPort settings, click either the CommsPort,
ProgrammerPort, PowerSupplyPort, OEMProgPort, or MeterPort
option on the Main Menu. (see Figure 3).
7. Within the CommsPort dialogue box, select the
communications port that the RS485 is connected to and set the
Baud Rate to 9600. Click Set (see Figure 1).
Note: Optional if a re-ash is required. The ProgrammerPort
is for a USB connection to a MSP-GANG Programmer by
Elprotronics. This programmer and connection is used to ash
the MSP430 microprocessor with the UVM operating code. This
is already done by the factory, but certain circumstances may
require the module to be re-ashed to a later revision.
8. Select the appropriate CommsPort that the MSP-GANG
Programmer is connected to. Set the Baud Rate to 115200 (see
Figure 2). Click Set to use the selected settings, or Cancel to
ignore use of this port (most cases). The other CommsPorts are
relevant to factory calibration equipment and may be ignored.
Misc Tab
1. On the Misc Tab of the program (see Figure 3), set the
address of the UVM module that you will be interacting with.
Addresses 0 -15 are derived from the DIP switches on the unit
(see the UVM Installation Manual for DIP switch settings).
There may also be an already-set internal soft address (from 16
– 255) that the unit will respond to as well. The units will be set to
hardware address 0 when shipped from the factory.
2. Click the Get Revision button to conrm that Comms is
present. The revision number will appear in the Misc Tab Module
Revision box.
Ideally, click the Get All Settings From Device to retrieve what is
already set in the controller. This may take about 15 seconds to
complete.
Figure 1. Comms Port dialogue box
Figure 2. Comms Port for MSP-GANG Programmer
Installation
Table of contents
Popular Control Unit manuals by other brands
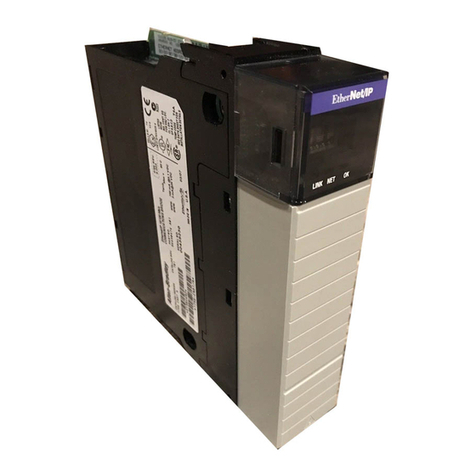
Allen-Bradley
Allen-Bradley ControlLogix 1756-ENBT user manual
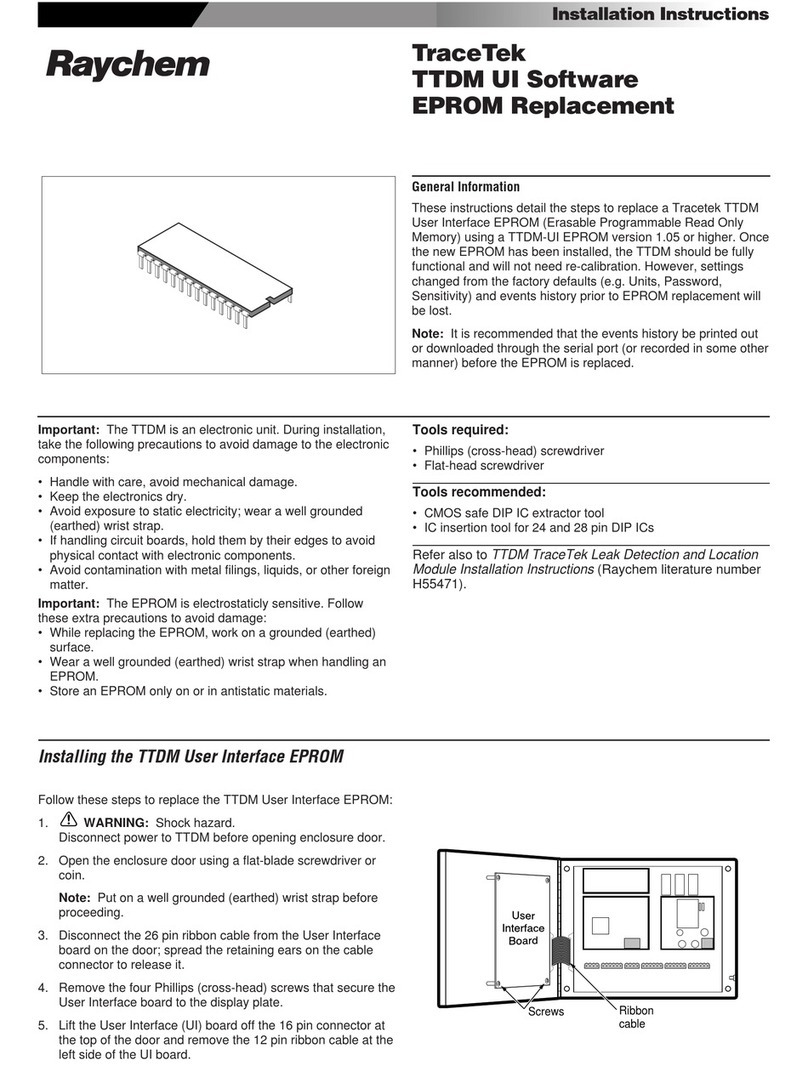
Raychem
Raychem TraceTek TTDM installation instructions
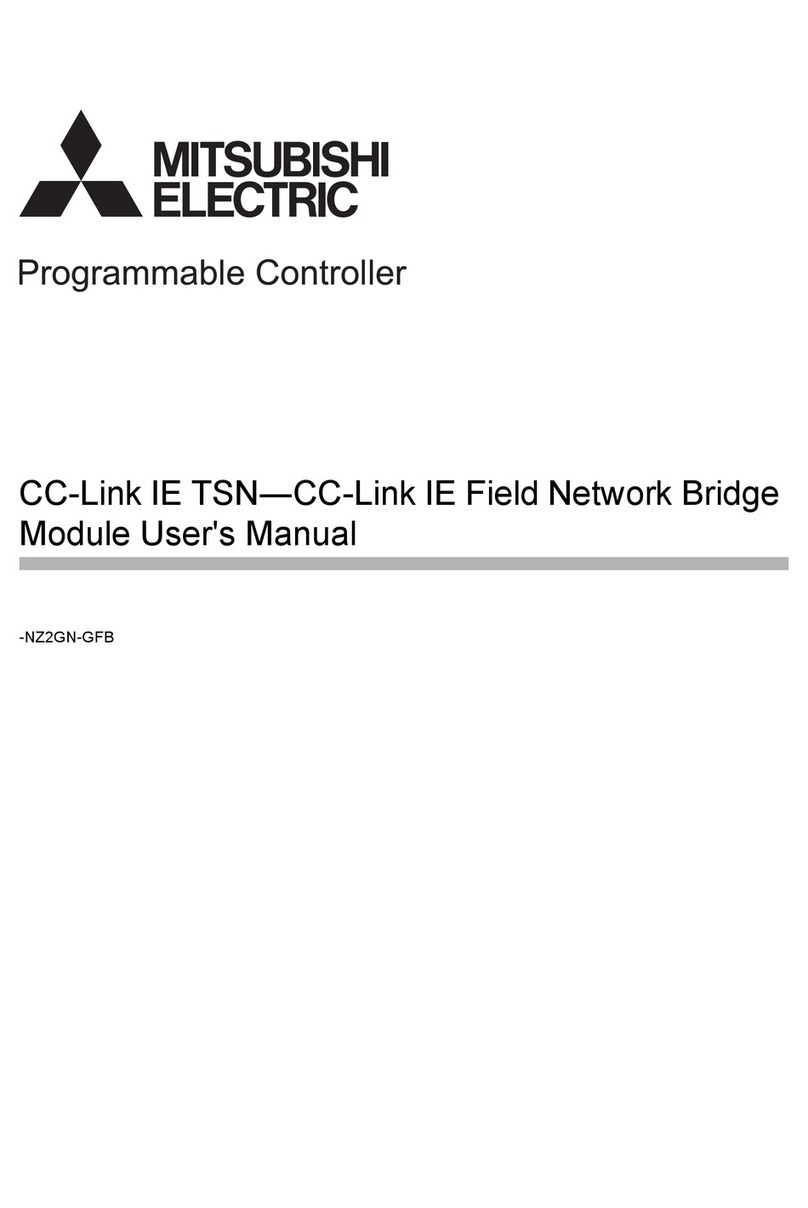
Mitsubishi Electric
Mitsubishi Electric CC-Link IE TSN user manual

Ametek
Ametek Z-tron IV Installation and operating instructions

Woodward
Woodward easYgen-300 Operation manual
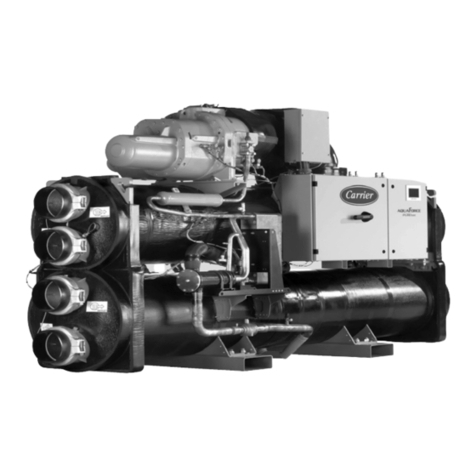
Carrier
Carrier Touch Pilot manual