TT electronics AB Connectors ABCIRP Series User manual

AB Connectors Limited
Specification No. 528
ABCIRP Connector Series
Assembly and wiring Instructions
AB Connectors Limited Issue 9: July 2010
Page 1 of 41
ABCIRP Series
Circular Multi-pin Electrical
Connectors
Assembly and
Wiring Instructions

AB Connectors Limited
Specification No. 528
ABCIRP Connector Series
Assembly and wiring Instructions
AB Connectors Limited Issue 9: July 2010
Page 2 of 41
Table of contents
1 Product Introduction 4
1.1 General 4
1.2 Typical Connector 6
2 Connector Description and Terminology 7
2.1 ABCIRP Free Connector 7
2.2 ABCIRP Fixed Connector 8
3 Backshells and Accessories 9
4 Polarisation 10
4.1 Insert Orientation 10
4.2 Alignment Pin 11
5 Individual Wire Termination 12
5.2 Individual Wire Termination (Crimping Cables) 13
5.3 Individual Wire Termination (Contact insertion Method 1) 14
5.4 Individual Wire Termination (Contact insertion Method 2) 16
6 Contact Extraction 17
7 Screen termination system 19
7.2 Method: A: Termination Procedure For In-line Wire Bundles 20
7.3 Procedure for a Fixed Connector with (SCHSA) 20
7.4 Method B: RFI Grounding 23
7.5 Procedure Shown Of Free Connector With ECHSA Accessory 23
7.6 Method C: Electrical Termination 24
7.7 Method D: Electrical Termination (90 Degree Elbow) 27

AB Connectors Limited
Specification No. 528
ABCIRP Connector Series
Assembly and wiring Instructions
AB Connectors Limited Issue 9: July 2010
Page 3 of 41
Appendices
Appendix A: Tooling data. 28
Appendix B: Dimensional positions of contacts in fixed & free shells 33
Appendix C: Guidance for the use of 90°backshells 34
Appendix C: Steel Band Termination Assembly Process 35
Appendix D: Backshell Torque Values. 37
Appendix E: Trouble Shooting 39
Appendix F: Contact addresses 41

AB Connectors Limited
Specification No. 528
ABCIRP Connector Series
Assembly and wiring Instructions
AB Connectors Limited Issue 9: July 2010
Page 4 of 41
1 Product Introduction
1.1 General
1.1.1 The ABCIRP connector series is based on the MS Bayonet lock series of connectors
conforming to MIL-C-5015 specification. They are interchangeable with all
corresponding MS bayonet lock types and feature identical panel mounting
dimensions.
1.1.2 Designed to operate within a temperature range of -55°C to +125°C, the connector
also meets the mechanical and environmental ratings of BS9522 F0032, VG95234
and NF-F-61-030.
1.1.3 Unlike other MIL-C-5015 bayonet connectors, which utilise insulators bonded into the
shell and or bonded or rubber retained contacts, the ABCIRP connector series
incorporates a Circlip retained solid plastic insulator and metal clip retained contacts.
1.1.4 Stainless steel bayonet pins and rollers riding along the three cam tracks machined
into the receptacle shell achieve the connector coupling. Coupling integrity is
guaranteed by:
•Firstly having three stainless steel pins at the critical wear points of the receptacle
shell cam-tracks and secondly, by positive lock indicators in the form of
•An audible click when fully mated.
•Alignment of coloured dots when fully mated.
1.1.5 ABCIRP connectors are available in 7 sizes from shell size 18 to shell size 40 with
arrangements having 7 to 60 contacts.
1.1.6 Crimp contacts are available in sizes 16, 12 and 8 AWG.
1.1.7 Insulator angular orientation is available for occasions where like connectors are in
close proximity and cross mating has to be avoided. This is achieved by aligning pre-
determined keyways in the insulator with the master key of the plug and receptacle
shell. These angular positions are in accordance with the MIL-C-5015 specification
thereby ensuring compatibility with existing equipment.
1.1.8 The dynamic sealing ring at the base of the plug shell guarantees high reliability and
anti-vibration characteristics including the stainless steel pins at the cam track critical
wear points.
1.1.9 Environmental sealing of mated connectors to IP67 is achieved by compression of
the dynamic seal ring, while integrity at the rear is achieved by the use of an
individual wire seal grommet with membranes being penetrated only when a wire is
present.
1.1.10 Electrical continuity between connectors is achieved by ensuring compression of the
wavy and flat washer assembly at the base of the plug shell.

AB Connectors Limited
Specification No. 528
ABCIRP Connector Series
Assembly and wiring Instructions
AB Connectors Limited Issue 9: July 2010
Page 5 of 41
1.1.11 Screen termination is simplified by using one of a range of back shell/accessory
combinations.
1.1.12 In summary, the ABCIRP modular bayonet coupling connector offers several
advantages to the user.
•Metal clip retained removable crimp contacts.
•Positive lock location of contacts.
•Circlip retained removable insulator allowing for angular re-positioning.
•Rapid coupling and uncoupling. 120°rotation of th e coupling nut.
•Vibration resistant -loosening of the coupling nut under vibration or shock condition is
prevented.
•Inter-matable and interchangeable with other Mil-C-5015 bayonet types.

AB Connectors Limited
Specification No. 528
ABCIRP Connector Series
Assembly and wiring Instructions
AB Connectors Limited Issue 9: July 2010
Page 6 of 41
1.2 Typical Connector
Fixed
(Receptacle)
Free
(Plug)
Standard Data
1.2.1 Materials
Shell: Aluminium Alloy
Insulator: Hard Plastic, Low fire hazard
Grommet: Rubber, Low fire hazard
Contacts: Copper Alloy
Retaining Clip: Beryllium Copper
Accessory: Aluminium Alloy
1.2.2 Plating Finishes
Shell: Zinc Cobalt, Black Passivation
Contacts: Gold or Silver
Accessory: Zinc Cobalt, Black Passivation
1.2.3 Environmental Ratings
Shock: 75g
Vibration: 5 to 500Hz long endurance, 30 hour test at 10g
Acceleration: 50g
Mechanical Endurance: 500 mating cycles minimum
Stainless steel pins
Stainless steel pins
Alignment indicator

AB Connectors Limited
Specification No. 528
ABCIRP Connector Series
Assembly and wiring Instructions
AB Connectors Limited Issue 9: July 2010
Page 7 of 41
2 Connector Description and Terminology
2.1 ABCIRP Free Connector
Exploded View of ABCIRP Free Connector
2.1.1 Coupling Nut – Provides cam force when mating and unmating connectors.
2.1.2 Free Shell – Holds the insert and incorporates an alignment key to position the insert.
The free shell accommodates either the socket or pin insert to reverse gender.
2.1.3 Insert (Pin or Socket) – Removable, orientatable, retains the contacts and can be
used in either fixed or free shells.
2.1.4 Circlip – Retains the insert in the shell.
2.1.5 Contacts (Pin or Socket) – Crimped to the conductors.
2.1.6 Retaining clip – Retains the contacts in the insert.
2.1.7 Grommet – Resilient rubber seal for the individual wire terminations. It has a special
cut out feature to help position onto the rear of the insert. It also has a sealing web so
that when the connector is not fully populated, sealing still occurs. The grommet is ink
marked with the hole position identification.
Coupling nut
and Free shell
Socket insert
Circlip
Socket contacts
Grommet

AB Connectors Limited
Specification No. 528
ABCIRP Connector Series
Assembly and wiring Instructions
AB Connectors Limited Issue 9: July 2010
Page 8 of 41
2.2 ABCIRP Fixed Connector
Exploded view of ABCIRP Fixed Connector
2.2.1 Fixed Shell – The panel mounted half of the connector pair. Holds the insert and
incorporates an alignment key to position the insert. The shell accommodates either
the socket or pin insert to reverse gender. Coupling ramps provide cam action for
coupling and uncoupling. Stainless Steel pins at the top of the ramps ensure positive
locking and long service life.
2.2.2 Insert (Pin or Socket) – Removable, orientatable, retains the contacts and can be
used in either fixed or free shells.
2.2.3 Circlip – Retains the insert in the shell.
2.2.4 Contacts (Pin or Socket) – Crimped to the conductors.
2.2.5 Retaining clip – Retains the contacts in the insert.
2.2.6 Grommet – Resilient rubber seal for the individual wire terminations. It has a special
cut out feature to help position onto the rear of the insert. It also has a sealing web so
that when the connector is not fully populated, sealing still occurs. The grommet is ink
marked with the hole position identification.
Fixed shell
Pin insert
Pin contacts
Circlip
Grommet

AB Connectors Limited
Specification No. 528
ABCIRP Connector Series
Assembly and wiring Instructions
AB Connectors Limited Issue 9: July 2010
Page 9 of 41
3 Backshells and Accessories
3.1.1 A fully sealed connector is achieved by using a grommet in combination with an
accessory. When assembled on the back of the connector the accessory compresses
the grommet onto the individual wires and against the accessory body to obtain an
IP67 seal.
3.1.2 The accessory is assembled correctly when the teeth on the back of the connector
shell mesh with those of the accessory.
3.1.3 The spinning knurled locking nut prevents grommet twist when tightening.
3.1.4 Accessories are available to take heat shrink boots, screening systems and conduit.
Angled versions are also available, to guide cable routing. Please consult the
catalogue or ask the sales desk for more information on the type available.
Hint: When engaging the accessory onto the connector, linearly push the accessory onto
the fixed or free shell while rotating the accessory nut. This will ease the assembly by allowing
the threads to engage more naturally. Also continue to push the accessory inwards when
tightening to ease the torque required. The same applies during strip down; push forward on
the accessory to slacken thread.

AB Connectors Limited
Specification No. 528
ABCIRP Connector Series
Assembly and wiring Instructions
AB Connectors Limited Issue 9: July 2010
Page 10 of 41
4 Polarisation
4.1 Insert Orientation
4.1.1 Depending on end user needs, the pin and socket inserts may be supplied separately
to the fixed and free shells to allow the end user to specify the orientation of the
insulator within the connector.
Insert Orientation Components
4.1.2 Insulator orientation is used to prevent cross mating of like connectors, which are in
close proximity to each other. It is achieved by firstly having a location key cast into
the fixed and free shells, and secondly by the insulator having a number of location
keyways moulded into the outside shoulder for each desired orientation. Each
position is marked on the insulator and can also be seen on either the front face or
the location keyway.
4.1.3 Before the circlip is used, it is best practice to bend the circlip through 90°, so that a
spring washer effect is formed in the circlip. This will not only aid the assembly
process, but will take up any linear movement of the insulator within the shell.
4.1.4 Align the insulator orientation letter required with the key in the shell and press into
place. There may be a slight interference, but it can be pushed to a stop, exposing
the circlip groove in the fixed or free shell.
4.1.5 Insert one end of the circlip into the circlip groove, and prize around using a small
screwdriver until the circlip snaps into position. Attempt to push and twist the insulator
to ensure that the circlip is seated correctly.
4.1.6 The Insulator can also be easily removed to orientate it. Locate the chamfered end of
the circlip. Using a small screwdriver prise the circlip out of its groove and “ride” the
screwdriver under the circlip all the way around the shell and it will pop out. The

AB Connectors Limited
Specification No. 528
ABCIRP Connector Series
Assembly and wiring Instructions
AB Connectors Limited Issue 9: July 2010
Page 11 of 41
insulator can now be removed and repositioned or replaced as required.
4.2 Alignment Pin
4.2.1 For high density, symmetrical contact arrangements, where very few contacts are
being used, additional devices may be necessary to completely remove the
possibility of cross mating like connectors. These devices take the form of pins,
which occupy key contact positions in the insulator depending on the size and
complexity of the arrangement.
4.2.2 Note. The additional polarising device is inserted into the pin insulator only.
4.2.3 It is recommended that at least two of these pins be installed per connector. These
alignment pins should not be removed once installed.
Example of two 40-A35 Contact arrangements with X and Y orientations mated together. 25
out of the 35 available contacts can misalign.
Table showing optimum position for alignment pins.
Contact arrangement
Insulator Orientation
Alignment pin position
18-19 All Any one hole
20-15 All Any one apart from G
22-14 All Hole K & R
24-10 All Any one hole apart from G
28-21 All Holes E & e
32-A13 All Hole 10
36-A22 All Holes 14 & 17
40-A35 All Holes 1 & 24
40-A60 N Hole 3 & 51
W, X, Y & Z Holes 26 & 59

AB Connectors Limited
Specification No. 528
ABCIRP Connector Series
Assembly and wiring Instructions
AB Connectors Limited Issue 9: July 2010
Page 12 of 41
5 Individual Wire Termination
Cable preparation lengths
1.1.1 Cut cables to the desired length, which must include:
•The length of the grommet
•The strip length, as shown in the table below
•The assembly length of 40mm
•Apply cable idents and push back from approximately 70mm from the
end of the wire.
5.1.2
Contact Size AB Crimp Contact Part Number Dimension “L” mm
Strip Length
Pin Socket
16/22 ABCIRP1622KPK# ABCIRP1622KLK# 5-6mm
16/20 ABCIRP1620KPK# ABCIRP1620KLK# 5-6mm
16 ABCIRP16KPK# ABCIRP16KLK# 5-6mm
16/14 ABCIRP1614KPK# ABCIRP1614KLK# 5-6mm
12/40 ABCIRP1240KPKP80#
ABCIRP1240KLKP80#
7-8mm
12/20 ABCIRP1220KPKP80#
ABCIRP1220KLKP80#
7-8mm
12/16 ABCIRP1216KPKP80#
ABCIRP1216KLKP80#
7-8mm
12 ABCIRP12KPKP80# ABCIRP12KLKP80# 7-8mm
12/10 ABCIRP1210KPKP80#
ABCIRP1210KLKP80#
7-8mm
8/40 ABBP840KPKP80# ABBP840KSKP80# 12-13mm
8/16 ABBP816KPKP80# ABBP816KSKP80# 12-13mm
8/12 ABBP812KPKP80# ABBP812KSKP80# 12-13mm
100 ABBP100KPKP80# ABBP100KSKP80# 12-13mm
100/60 ABBP10060KPKP80# ABBP10060KSKP80# 12-13mm
Strip Lengths

AB Connectors Limited
Specification No. 528
ABCIRP Connector Series
Assembly and wiring Instructions
AB Connectors Limited Issue 9: July 2010
Page 13 of 41
1.2 Individual Wire Termination (Crimping Cables)
Size 16 contact
Single sided clip.
Size 12 contact
Single sided clip.
Size 8 contact with
Retaining collet.
Crimp Contacts Types
1.2.1 Inspect the conductor to ensure the insulator end is clean and square and the lay of
the strands is not disturbed.
Note: A damaged conductor or strand is not acceptable. Ensure the conductor is
clean before assembly into the contact.
1.2.2 Select the correct crimp tool and turret/locator for the contact to be crimped from the
table in Appendix A, and install the turret/locator onto the crimp tool.
1.2.3 Set the correct tool setting and tool position for the contact as shown in Appendix A.
1.2.4 Insert the stripped conductor into the contact crimp bucket. Ensure conductor is fully
pushed in and that insulation is tight to crimp bucket.
1.2.5 Check inspection hole to see if the conductor strands are visible. If they are not
visible, check the conductor strip length and check for foreign objects in the crimp
bucket.
1.2.6 Operate the empty crimp tool once to ensure the crimping dies are completely open
and there is no misalignment.
1.2.7 Insert the contact with the conductor installed into the contact-locating hole in the
crimp tool until it 'bottoms' in the locator/turret. Applicable to size 12 & 16 only.
Position the size 8 contact so that the crimp bucket rests on the bottom jaws of the
die set with the back of the contact protruding approximately 2mm over the back of
the die.
1.2.8 Activate the crimp tool through one complete cycle.
1.2.9 Note: When crimping Size 8 Contacts ensure that the flats of the Hexagonal Die Set
come together.
5.2.10 Remove the crimped assembly from the tool and inspect the joint for the correct crimp
location as below.

AB Connectors Limited
Specification No. 528
ABCIRP Connector Series
Assembly and wiring Instructions
AB Connectors Limited Issue 9: July 2010
Page 14 of 41
Completed crimp contact
5.2.11 Check that the conductor strands are visible through the inspection hole.
Important Note: Loose conductor strands or cracks in the crimp area are not
acceptable.
The crimp joint must be re-made if there is any sign of damage.
5.3 Contact Insertion – Method 1
5.3.1 Push the contacts through the grommet according to the wiring list / schedule and
push the grommet up to, but not beyond the idents. Lubricant such as Pronatur or
Isoproyl alcohol may be used. Important: Observe handling and operating safety
instructions as supplied by manufacture.
5.3.2 Locate the correct hole for the appropriate wire. Load the contact into the insert by
hand. Note: It is best practice to work from one side only, inserting from left to right or
top to bottom in an orderly fashion. Some arrangements have a radial pattern where
working from the centre and working outwards is best. Randomly inserting contacts is
more likely to result in wiring errors and difficulty inserting contacts.
5.3.3 Using the correct insertion tool for the contact as shown above, locate onto contact
bucket and push the contact forward until fully inserted, when a ‘click’ will be heard
and felt.
Hint: As each contact is inserted pull firmly on the cable to ensure that the contact has seated
correctly. Any contact not seated correctly will pull back. If this happens use the insertion tool
and reinsert the contact and repeat the pull test.
Inspection Hole

AB Connectors Limited
Specification No. 528
ABCIRP Connector Series
Assembly and wiring Instructions
AB Connectors Limited Issue 9: July 2010
Page 15 of 41
5.3.4 Checking the dimensions shown in Appendix B will verify that the contact is seated
correctly. As an extra final visual check, all contacts should be around the same
height with no visible differences in height from insert face.
5.3.5 Repeat steps 5.3.4 to 5.3.6 until all wires are located into their respective holes.
5.3.6 Slide the grommet down the cable and locate onto the insert. Lubricant such as
Pronatur or Isoproponyl alcohol may be used. Observe handling and operating safety
instructions as supplied by manufacturer.
5.3.7 Tuck the grommet in between the connector shell and the insert until the shoulder on
the grommet is pushed almost level with the top of the serrations on the shell. A
simple tool is available to help when tucking the grommet into position.
Hint: If you push forward on the back face of the grommet it should not buckle. If it does then
the grommet has not been tucked into position correctly. This can cause the grommet to tare
when the backshell is assembled and could affect sealing.
5.3.8 To ensure that the correct wire number has been inserted into the correct hole, check
that the lettering and step in the grommet align correctly.
5.3.9 Any grommet hole that has been pierced accidentally will need to be filled with a
grommet filler plug as shown. Unpierced holes can be left.
5.3.10 Slide cable idents up to the back of the grommet and leave a 5 to 15mm gap.
5.3.11 Assemble the accessory onto the connector and tighten to the recommended torque
values as stated in Appendix D.
Hint: When engaging the accessory to the connector, linearly push the accessory onto the
fixed or free shell while rotating the accessory nut. This will ease the assembly by allowing the
threads to engage more naturally. Also continue to push the accessory inwards when
tightening to ease the torque required. The same applies during strip down; push forward on
the accessory to slacken thread.

AB Connectors Limited
Specification No. 528
ABCIRP Connector Series
Assembly and wiring Instructions
AB Connectors Limited Issue 9: July 2010
Page 16 of 41
5.4 Contact insertion – Method 2
5.4.1 This alternative method involves assembling the grommet onto the connector before
inserting the contacts through the grommet and into the insert. The advantage of this
method is that the contacts can be crimped onto the wires before the connector and
accessories are touched, however:
5.4.2 This method is not preferred since it requires that the contact and insertion tools
penetrate the webs in the grommet. There is potential for the retaining clips on the
contacts to damage the grommet sealing holes and effect the performance of the
connector.
5.4.3 Extra care must therefore be taken when using this method and the grommet must be
inspected for damage after the contacts have been fitted.
5.4.4 Prepare the parts as follows:
•Strip and crimp the contacts as per sections 5.2 and 5.3
•Slide the accessories over the wires in the correct order.
5.4.5 Assemble the grommet onto the rear of the insulator, ensuring that the recess on the
grommet aligns with the corresponding raised section on the insert.
5.4.6 Tuck the grommet in between the connector shell and the insert until the shoulder on
the grommet is pushed almost level with the top of the serrations on the shell. A
simple tool is available to help when tucking the grommet into position.
Hint: If you push forward on the back face of the grommet it should not buckle. If it does then
the grommet has not been tucked into position correctly. This can cause the grommet to tare
when the backshell is assembled and could affect sealing.
5.4.7 Locate the required wire and feed it partially through the grommet. Note: It is best
practice to work from one side only, inserting from left to right or top to bottom in an
orderly fashion. Some arrangements have a radial pattern where working from the
centre and working outwards is best. Randomly inserting contacts is more likely to
result in wiring errors and difficulty inserting contacts.
5.4.8 Open the “Tweezers-type” insertion tool and close it around the crimp bucket of the
selected contact, ensuring that the wire does not pinch the wire as the tool closes.
Holding the tool as it close to the bucket as possible, apply a firm and even pressure,

AB Connectors Limited
Specification No. 528
ABCIRP Connector Series
Assembly and wiring Instructions
AB Connectors Limited Issue 9: July 2010
Page 17 of 41
inserting the contact into the insert until it clicks into place. When inserting a socket
contact it is good practice to place a socket guide pin in the front of the contact to
prevent any rubber from the grommet web entering the socket contact.
5.4.9 Slide the tool out and remove the tool from the wire.
Hint: When sliding the tool out lightly apply tweezers action to the open the tool. This
will help prevent chafing the wire insulation on the tool.
Hint: As each contact is inserted pull firmly on the cable to ensure that the contact has seated
correctly. Any contact not seated correctly will pull back. If this happens use the insertion tool
and reinsert the contact and repeat the pull test.
5.4.10 Repeat steps 5.5.8 to 5.5.9 for all wires.
5.4.11 Checking the dimensions shown in Appendix B will verify that the contact is seated
correctly. As an extra final visual check, all contacts should be around the same
height with no visible differences in height from insert face.
5.4.12 Assemble the rear backshells and accessories following steps 5.4.8 to 5.4.11.
2. Contact Extraction
2.1.1 The extraction tool can be utilised for both the size 16 and 12 contacts, by replacing
the probe with the appropriate size. These probes can become damaged over time
and therefore can be easily replaced. See Appendix A for details of the replacement
probe part numbers.
2.1.2 Loosen cable accessory and backshell. Slide these down the cable to allow easy
access to the rear of the connector. Slide the grommet and cable idents back
approximately 70mm.
2.1.3 Working from the front face of the connector, position the extraction tool over the pin
or socket contact. Carefully rotate the tool until the 3 slots in the tool align with the 3
ribs in the insert cavity. Push the tool firmly into the insert closing the clip with the
front collar.

AB Connectors Limited
Specification No. 528
ABCIRP Connector Series
Assembly and wiring Instructions
AB Connectors Limited Issue 9: July 2010
Page 18 of 41
2.1.4 Release the contact by pushing forward on the tool handle until a click can be heard.
The contact is now released.
2.1.5 Lightly pull on the cable to extract the contact from the insert cavity. Repeat steps
7.1.4 to 7.1 5 as required.
2.1.6 At this stage contacts can be cut off and replaced or pushed back through the
grommet to allow the contacts to be repositioned into a different hole. Important
Note To prevent damage to the grommet when pushing the contact through the
grommet hole, use the Grommet extraction tool.
2.1.7 Simply place the contact fully into the tool into the tool. Using the tool push the
contact through the grommet until the end of the tool in visible at the other end.
Remove the contact from the tool.
2.1.8 Repeat steps 6.1.3 to 6.1.7 as required. Re-insert the contacts into the connector
following steps 5.4.1 to 5.4.4 as required.
2.1.9 NOTE Contacts can be extracted 30 times with out degradation to performance.
Once 30 extractions have been performed it is recommended to change the contact.

AB Connectors Limited
Specification No. 528
ABCIRP Connector Series
Assembly and wiring Instructions
AB Connectors Limited Issue 9: July 2010
Page 19 of 41
3. Screen Termination system.
3.1.1 Termination of shielded cables is necessary to provide R.F.I. or E.M.I. shielding
protection. The ABCIR Connector series has various methods for attaching shield
braid to the connector backshell.
3.1.2 This section details assembly methods using four different backshell styles. They will
be described as Method -A, B, C & D.
3.1.3 The following items are required to complete the assemblies.
3.1.4
Braid Sock: Provides the overall screen and is secured to the connector backshell
and the interwoven knitted mesh at the opposite end.
Typical Braided Sock
Connector Shell Size Part Number Length/Diameter
Up to shell size 32 ABBMBS035015 150mm / 35mm
Shell sizes 36 & 40 ABBMBS05015 150mm / 50mm
Braided Sock Lengths
Note. Make certain the sock is expanded to the correct diameter before cutting to
length. To aide this operation, the use of an inner storage tube of the appropriate
diameter is recommended.
3.1.5
Knit Mesh: Interwoven between individual cable screens. Ensures all screens are
interconnected. Braid sock terminated to this component.
Knitmesh
3.1.6 Stainless Steel Locking Securing Band: Used to terminate outer overall screen to
backshell and interwoven knitted mesh.
Connector Shell Size Part Number
Up to shell size 32 ABB600052
Shell sizes 36 & 40 ABB600090
Shell Size with Securing Band

AB Connectors Limited
Specification No. 528
ABCIRP Connector Series
Assembly and wiring Instructions
AB Connectors Limited Issue 9: July 2010
Page 20 of 41
8.2 Method: A: Termination Procedure For In-line Wire Bundles
8.2.1 Method A uses two stainless steel securing bands that concentrically close to
mechanically grip and electrically terminate the overall shield to:-
. • The connector backshell, (RFI / Heat Shrink Adaptor)
. • The wire bundles or multi-core cables.
8.3 Procedure for a Fixed Connector with (SCHSA).
8.3.1 Cut the braid sock to the required length and remove inner storage tube. Fold one
end of the Braidsock back inside itself by approximately 15 to 20mm.
as shown right. This provides a clean edge without sharp sections.
8.3.2 Slide sock over threaded portion of RFI Adaptor.
8.3.3 Terminate braid sock to the RFI adaptor, using a securing band
shown in Appendix C.
Termination of Braid Sock To RFI Adaptor
8.3.4 Strip cable outer insulation exposing the screen for a length of 70mm, and trim off all
of this exposed screen.
8.3.5 Strip the cable outer insulation to a length of 170mm from the end of the cable, as
shown below; which then gives a braid length of 100/125mm.
SCHSA Insulation Strip Lengths
This manual suits for next models
34
Table of contents
Popular Cables And Connectors manuals by other brands

Pentair
Pentair Raychem H900 installation instructions
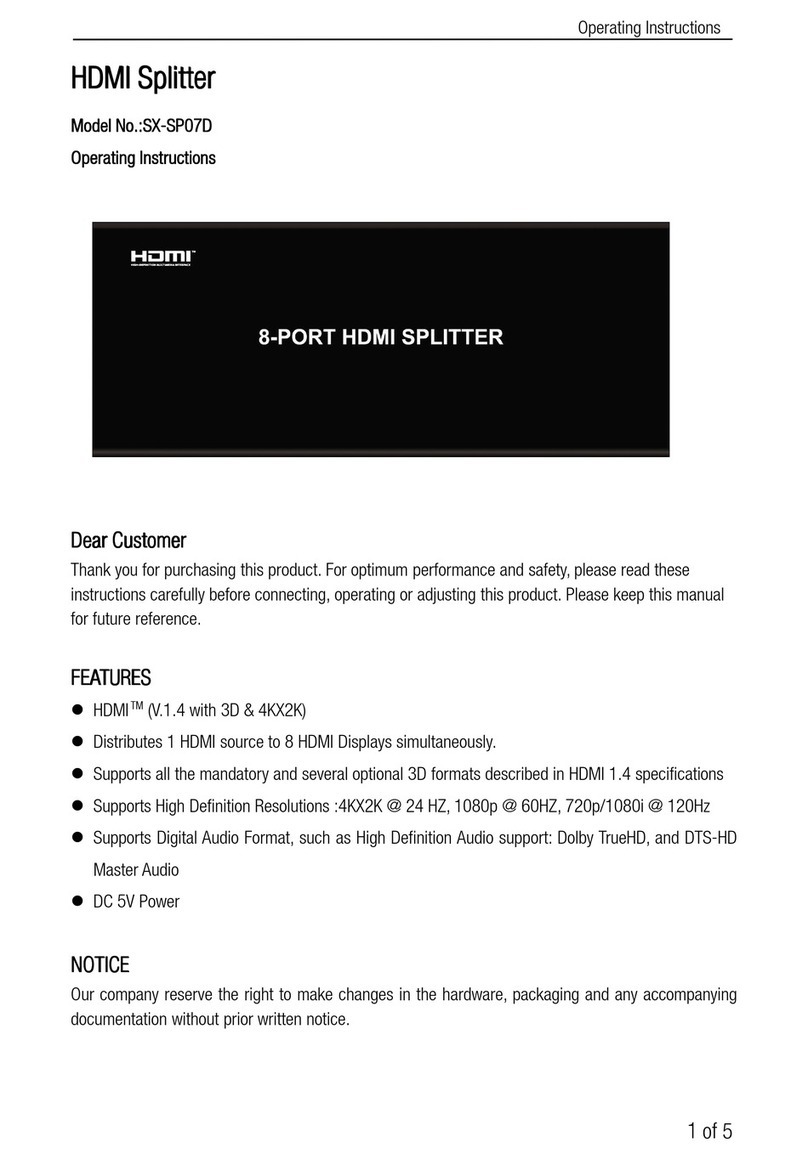
Foxun
Foxun SX-SP07D operating instructions

Gleason Reel
Gleason Reel Direct Drive Hazardous Duty Electric Cable Reels... Installation and maintenance instructions
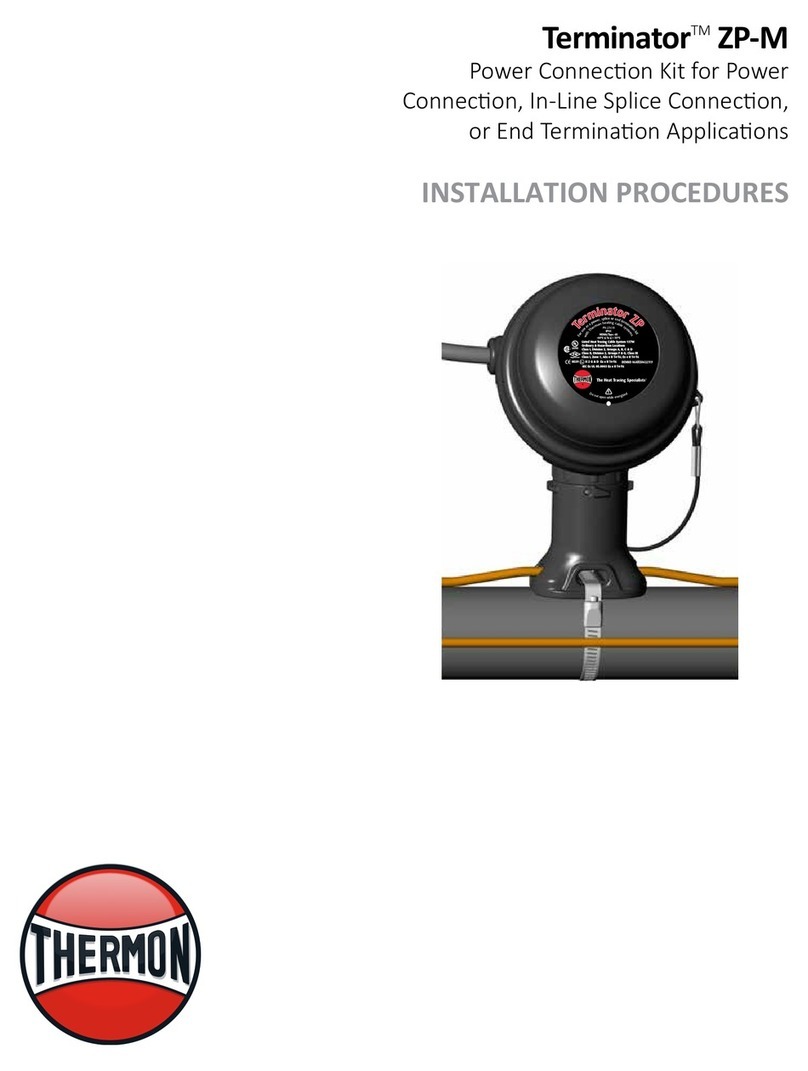
Thermon
Thermon Terminator ZP-M Installation procedures
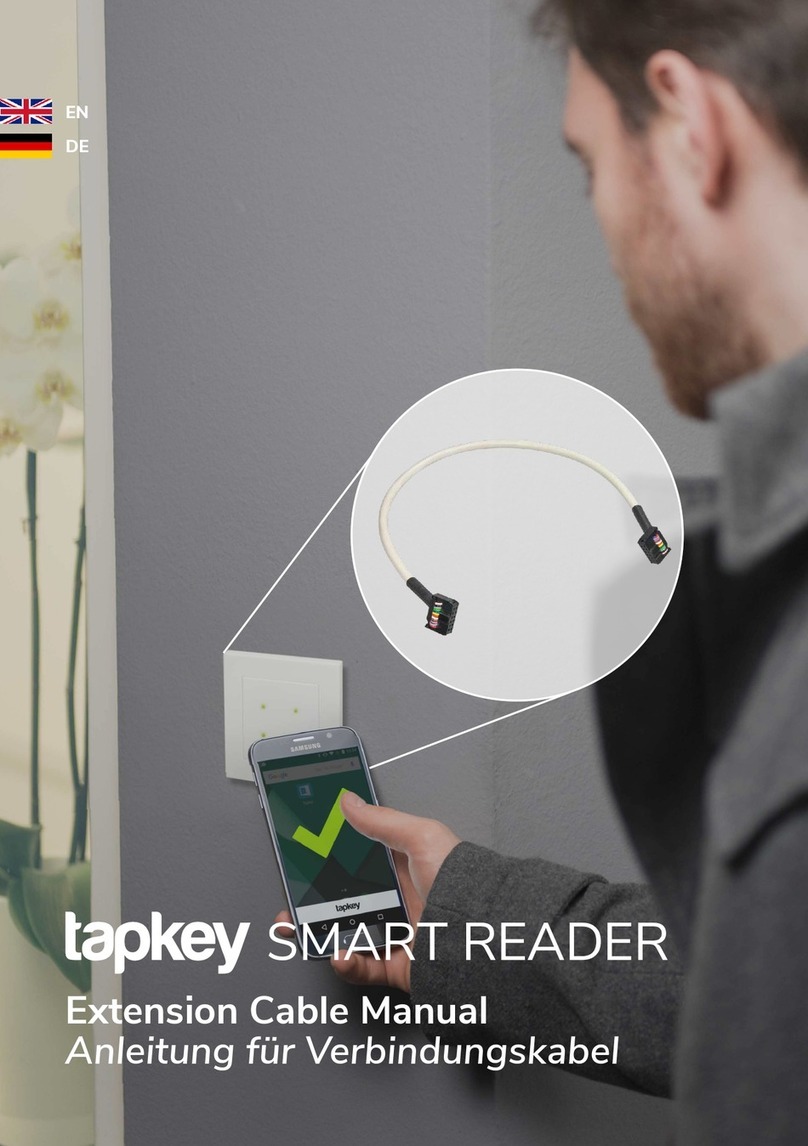
Tapkey
Tapkey Smart Reader manual
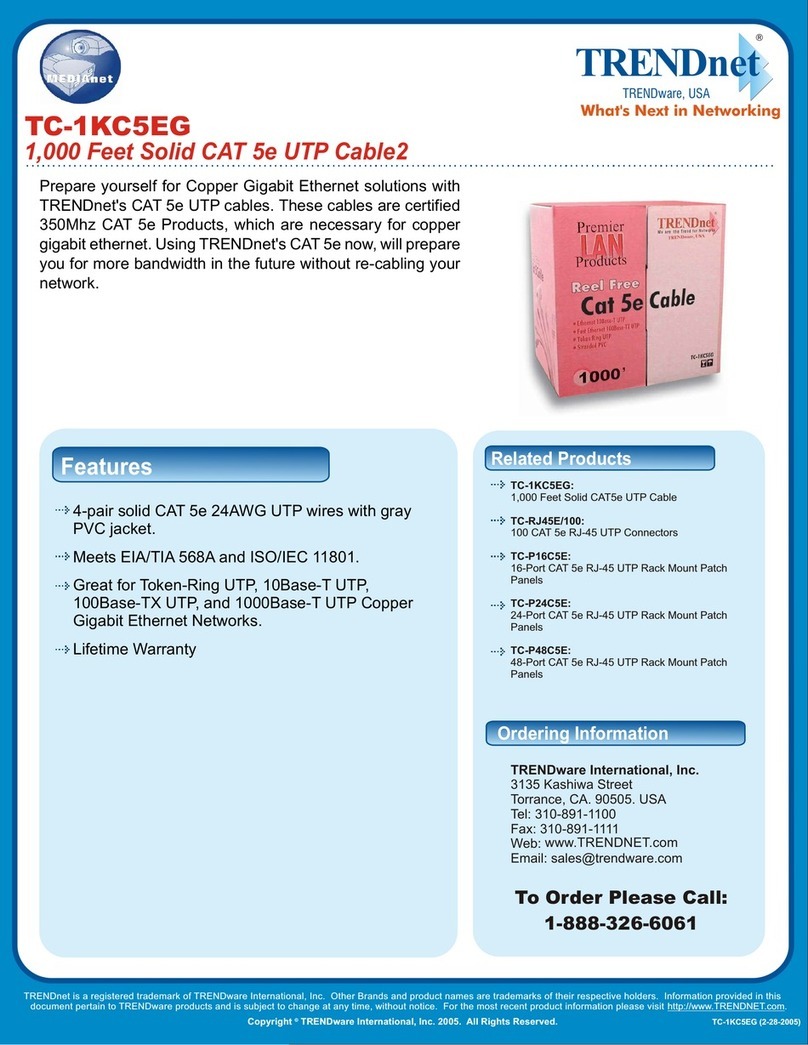
TRENDnet
TRENDnet TC-1KC5EG - DATA SHEETS datasheet
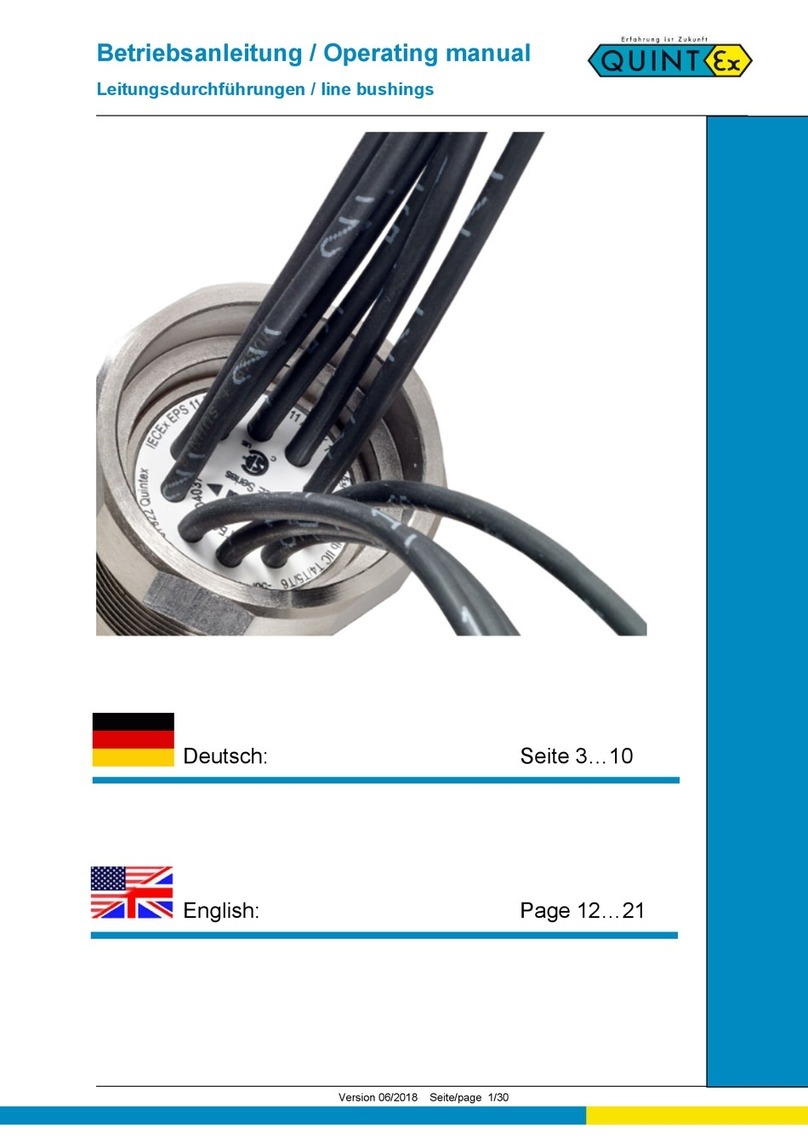
Quintex
Quintex LB Series operating manual

Roxtec
Roxtec R Series installation instructions
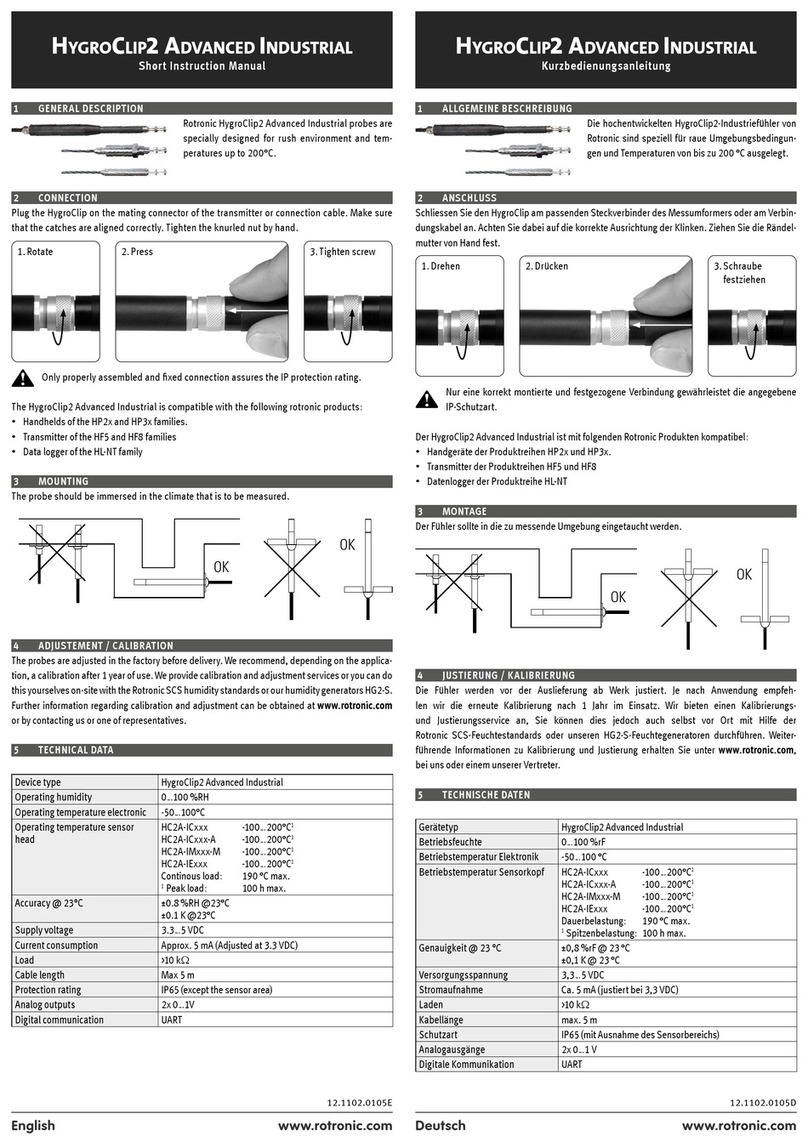
Rotronic
Rotronic HygroClip2 ADVANCED Short instruction manual
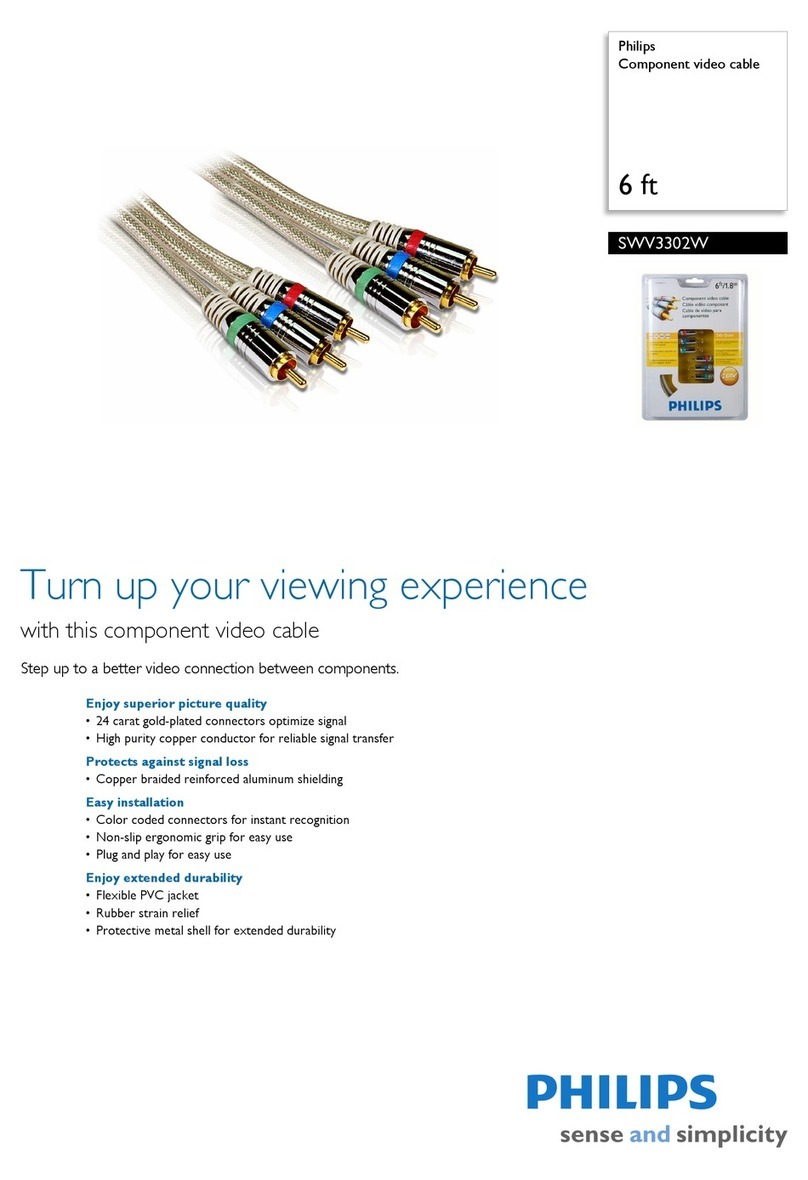
Philips
Philips SWV3302W Specifications
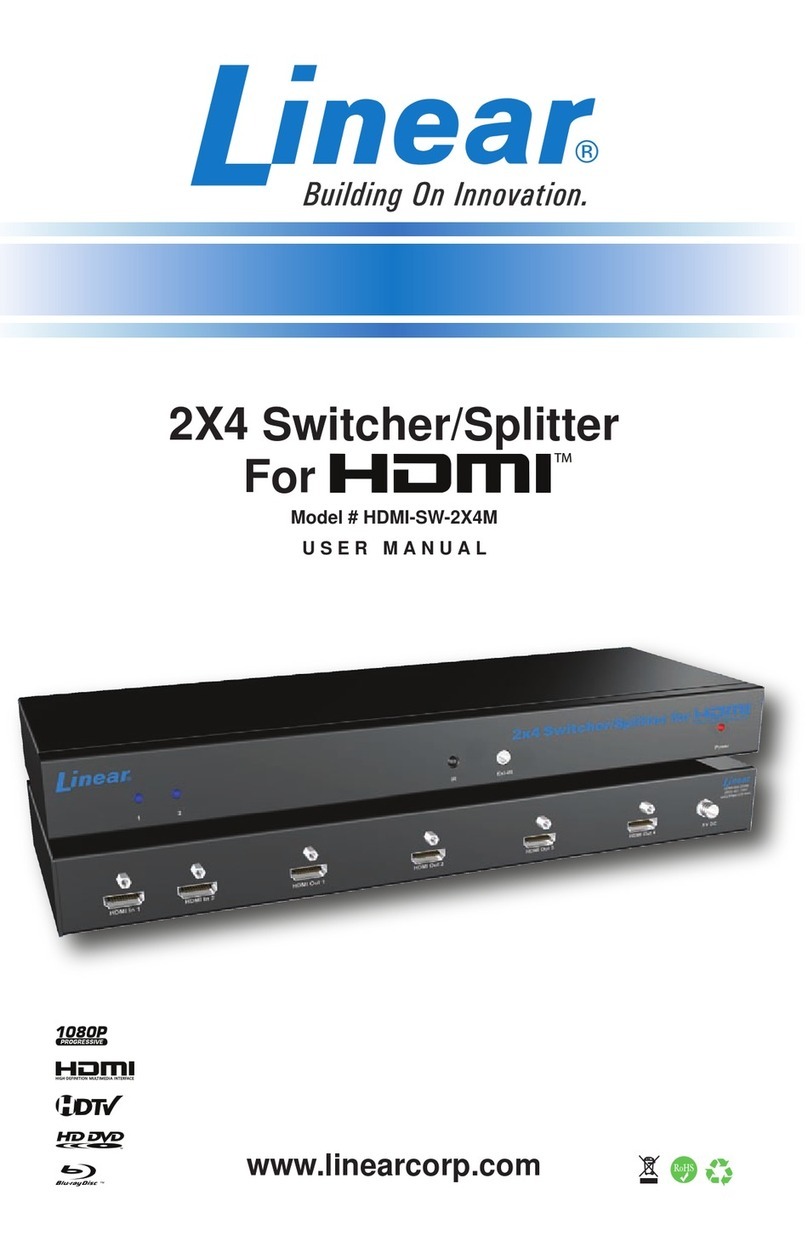
Linear
Linear HDMI-SW-2X4M user manual

Gleason Reel
Gleason Reel Gear Drive Electric Cable Reels MMD24 Installation and maintenance instructions