Tyco NG-1 1150 User manual

Model NG-1 1150, NG-1 1500, NG-1 2000,
and NG-1 3000 Stand-Alone Nitrogen Generator
Page 1 of 8 FEBRUARY 2021 TFP1253
Worldwide
Contacts
www.tyco-fire.com
IMPORTANT
Refer to Technical Data Sheet
TFP2300 for warnings pertaining to
regulatory and health information.
General
Description
The TYCO NG-1 1150, NG-1 1500, NG-1
2000, and NG-1 3000 Stand-Alone
Nitrogen Generators are designed to
facilitate the Dry Pipe Nitrogen Inerting
(DPNI) process for controlling oxygen
corrosion in dry and preaction fire
sprinkler systems, and provide super-
visory maintenance gas. Designed for
plug and play performance in a typical
dry or preaction fire sprinkler system,
the nitrogen generator utilizes mem-
brane separation technology that
produces 98%+ nitrogen on demand
without the need for nitrogen storage.
The Nitrogen Generator is an on-site
nitrogen generation system that
is designed to be installed in-line
between the compressed air supply
and the sprinkler system riser(s). The
system provides DPNI for single or mul-
tiple zones depending on:
• the number of systems
• the volume of the largest system
• the cumulative volume of all systems
being supplied
The generator includes an external
bypass valve for maintenance or for fast
fill needs to meet the NATIONAL FIRE
PROTECTION AGENCY (NFPA) stan-
dard NFPA 13 30-minute fill require-
ment for dry pipe and preaction fire
protection systems.
The Nitrogen Generator is designed
to nitrogen inert all of the zones being
served within 14 days. Thereafter, it
will continue to automatically provide
supervisory nitrogen gas sufficient for
pressure maintenance of the fire sprin-
kler system(s).
The Nitrogen Generator facilitates
the patented fill and purge breathing
process in the fire sprinkler system
when paired with an oxygen removal
vent installed on the sprinkler riser such
as the TYCO Manual Air Vent (TAV-D)
or the TYCO Dry SMART Vent (TSV-D).
Refer to TFP1262 for more information
on TYCO Dry Air Vent (TAV-D), and to
TFP1263 for more information on TYCO
SMART Air Vent (TSV-D).
System Assembly
The TYCO Nitrogen Generator unit
includes the following components:
• Steel enclosure cabinet with mem-
brane type nitrogen generator (no
nitrogen gas storage) and manual
bypass
• Power supply:
120 VAC/Single phase/60Hz
(230 VAC/Single phase/50Hz)
• Single point nitrogen/air discharge –
1/2 in. NPT
• Hour Run Meter
• Cycle Counter
System Status
The TYCO Nitrogen Generator includes
the following system status indicators:
• Bypass Mode Alarm Indicator -
Nitrogen generator is in the By-Pass
mode (flashing indicator). See Fig-
ure 4.
• Leak Monitoring Alarm - Nitrogen
generator is running excessively
(audible signal).
System Input/Output
Signals
The TYCO Nitrogen Generator includes
the following monitoring outputs:
Digital Outputs
• Power On/Off
• Bypass Mode Alarm
• Nitrogen Generator Running
• Leak Monitoring
Analog Outputs
• Nitrogen Supply Line Pressure
Support Equipment
The Nitrogen Generator is designed to
be used in conjunction with the TYCO
AMD-1 Air Maintenance Device, the
TYCO Handheld Gas Analyzer (THGA),
and the Riser-mounted TYCO Dry Air
Vent (TAV-D), or TYCO Dry SMART
Vent (TSV-D), as part of the com-
plete Dry Pipe Nitrogen Inerting (DPNI)
system. Refer to TFP1267 for more
information on the TYCO Handheld
Gas Analyzer.
The TYCO Nitrogen Generator can
be used with the following optional
equipment:
• TYCO Model TSGA SMART Gas
Analyzer - one for each nitrogen
generator is recommended. Refer to
TFP1270 Model TSGA SMART Gas
Analyzer for more information.
• TYCO Model TILD In-Line Corro-
sion Detector - monitoring at least
one for each sprinkler system is rec-
ommended. Refer to Technical Data
Sheet TFP1261 TYCO Model TILD
In-Line Corrosion Detector for more
information.
TYCO NG1
Compressors
The TYCO NG1 Compressors are
paired with the TYCO NG-1 1150,
NG-1 1500, NG-1 2000, and NG-1
3000 Nitrogen Generator in facilitating
the Dry Pipe Nitrogen Inerting (DPNI)
process in dry and preaction fire sprin-
kler systems as well as Wet Pipe Nitro-
gen Inerting (WPNI) process in wet pipe

TFP1253
Page 2 of 8
NITROGEN/AIR
SUPPLY LINES
AIR
COMPRESSOR1, 2
DRY/PREACTION
SPRINKLER RISERS
AIR VENT,
DRY
NITROGEN
GENERATOR
TABLE B
MODEL NG-1 1150, NG-1 1500, NG-1 2000, AND NG-1 3000 STAND-ALONE NITROGEN GENERATOR
OPERATING PERFORMANCE
Notes:
1. The Americas compressor vertical tank arrangement is shown. The EMEA and APAC compressor tank is a horizontal arrangement.
2. See Table C for compressor dimensions for your region.
Model
Number Min. Supply Air
SCFM (L/min) Total System Capacity
Gal. (L)
Single System
Capacitya
at 40 psig (2,8 bar)
Gal. (L)
Single System
Capacitya
at 20 psig (1,4 bar)
Gal. (L)
NG-1 1150 14.3 (405) 6500 (24605) 1150 (4 353) 2300 (8706)
NG-1 1500 24.3 (688) 11000 (41640) 1440 (5451) 2880 (10902)
NG-1 2000 24 (688) 18500 (70030) 2025 (7666) 4050 (15331)
NG-1 3000 35 (992) 22500 (85172) 2900 (10978) 5800 (21955)
Notes:
a. Capacity based on NFPA 13 30-minute ll requirement of largest single system
Model
Number
Cabinet Without Bypass Cabinet With Bypass Weight
Lbs
(kg)
Width
Inches
(mm)
Height
Inches
(mm)
Depth
Inches
(mm)
Width
Inches
(mm)
Height
Inches
(mm)
Depth
Inches
(mm)
NG-1 1150
NG-1 1500
24.5
(622)
52.5
(1334)
8.5
(216)
32.5
(826)
52.5
(1334)
8.5
(216)
152
(69)
NG-1 2000
NG-1 3000
24.5
(622)
76
(1930)
12.5
(318)
32
(813)
76
(1930)
12.5
(318)
300
(136)
FIGURE 1
MODEL NG-1 1150, NG-1 1500, NG-1 2000, AND NG-1 3000 STAND-ALONE NITROGEN GENERATOR
INSTALLATION SCHEMATIC
TABLE A
MODEL NG-1 1150, NG-1 1500, NG-1 2000, AND NG-1 3000 STAND-ALONE NITROGEN GENERATOR
DIMENSIONS AND WEIGHT

TFP1253
Page 3 of 8
sprinkler systems. The air compressors
work in conjunction with the NG-1 1150,
NG-1 1500, NG-1 2000, and NG-1 3000
Nitrogen Generators in a typical dry or
preaction fire sprinkler system. It is also
a plant nitrogen source for wet pipe fire
sprinkler systems used with the NG-1
1500, NG-1 2000, and NG-1 3000
Nitrogen Generators.
The NG1 Air Compressors consists of
the following features:
TNGC-1150
• 5 hp
• Used with Model NG-1 1150
• Air receiver tank:
—Americas: 60 gal (227 L); vertical
—EMEA, APAC: 71 gal (270 L);
horizontal
TNGC-1500/2000
• 7.5 hp
• Used with Model NG-1 1500 or NG-1
2000
• Air Receiver Tank:
—Americas: 80 gal (303 L); with
after cooler; vertical
—EMEA, APAC: 71 gal (270 L);
horizontal
TNGC-3000
• 10 hp
• Used with Model NG-1 3000
• Air Receiver Tank
—Americas: 120 gal (488 L); with
after cooler; vertical
—EMEA, APAC: 71 gal (270 L);
horizontal
NOTICE
The TYCO Model NG-1 1150, NG-1
1500, NG-1 2000, and NG-1 3000
Stand-Alone Nitrogen Generator
described herein must be installed
and maintained in compliance with this
document, as well as with the applica-
ble standards of the NATIONAL FIRE
PROTECTION ASSOCIATION, in addi-
tion to the standards of any authorities
having jurisdiction, such as FM Global.
Failure to do so may impair the perfor-
mance of these devices.
The owner is responsible for main-
taining their fire protection system
and devices in proper operating con-
dition. Contact the installing contrac-
tor or product manufacturer with any
questions.
In all cases, the appropriate NFPA or
FM Global installation standard, or
other applicable standard, must be
referenced to ensure applicability and
to obtain complete installation guide-
lines. The general guidelines in this
data sheet are not intended to provide
complete installation criteria.
Technical
Data
NG-1 Nitrogen Generators
Approvals
FM Approved
Compliance with CE Pressure Equipment
UL508A Listed Industrial Control Panel
Cabinet Dimensions
See Table A
Weight
See Table A
Operating Performance
See Table B
Temperature Range
40°F (5°C) to 105°F (40°C)
Power Supply
120 VAC/Single 1 phase/60Hz (dedicated
circuit)
230 VAC/Single phase/50Hz (dedicated
circuit)
Power Consumption
2 amps
Gas Connection
Air Inlet - 1/2 in. NPT Female
Nitrogen Outlet - 1/2 in. NPT Female
Drain Connection
1/4 in. NPT Connection
Nitrogen Quality
N2Purity at Discharge: 98% or greater
(maximum of 2.0% oxygen)
N2 Pressure at Discharge: Minimum of
15 psig (1 bar); Max of feed air pressure
minus 15 psig (1 bar)
N2 Water Dew Point: Typically less than
-70°F (-57°C)
Note: When connecting a TYCO Stand-
Alone Nitrogen Generator to an existing
dry pipe/preaction fire sprinkler system,
the existing fire sprinkler system(s) must be
limited to a maximum leak rate of less than
6 psig (0.4 bar) within a 24 hour period, per
system.
NG1 Compressors
Air Compressor Dimensions
See Table C
Weight
See Table C
Operating Performance
See Table B
Temperature Range
40°F (5°C) to 105°F (40°C)
Power Supply
Americas:
• 460 VAC/Three phase/60 Hz (Standard)
• 208 VAC/Three phase/60 Hz (Optional)
EMEA and APAC:
• 400 VAC/Single phase/50Hz (Standard)
Note: Other configurations are available.
Contact Johnson Controls Technical Ser-
vices for more information.
Auto Drain
• 120 VAC/Single phase/60Hz
• 220 VAC/1 phase/50Hz
Note: The auto drain can be connected
to the Nitrogen Generator cabinet power
supply.
Power Consumption
Americas:
TNGC-1150 7.6 Amps @ 460 VAC
17.5 Amps @ 208 VAC
TNGC-1500/2000 11 Amps @ 460 VAC
25.3 Amps @ 208 VAC
TNGC-3000 14 Amps @ 460 VAC
32.2 Amps @ 208 VAC
Model
Number
Width
Inches (mm) Length
Inches (mm) Height
Inches (mm) Weight
Lbs (kg)
Americas RoW Americas RoW Americas RoW Americas RoW
TNGC-1150 20 (508) 23.9 (606) 32 (813) 62.4 (1584) 70 (1778) 43.7 (1111) 435 (197) 295.4 (134)
TNGC-1500/2000 23.6 (599) 23.3 (592) 38 .1 (9 68) 60.6 (1540) 70.1 (1781) 47.2 (1200) 573 (260) 416.7 (189)
TNGC-3000 43.2(1097) 23.9 (606) 30 (762) 60.6 (1540) 76.6 (1946) 47.2 (1200) 800 (362) 443.2 (201)
NOTES
• RoW = Rest of World - the EMEA and APAC regions.
TABLE C
MODEL NG1 COMPRESSOR DIMENSIONS AND WEIGHT -
AMERICAS AND REST OF WORLD REGIONS

TFP1253
Page 4 of 8
EMEA and APAC:
TNGC-1150 13 Amps @ 400 VAC
TNGC-1500/2000 17 Amps @ 400 VAC
TNGC-3000 22 Amps @ 400 VAC
Air Connection
Americas:
TNGC-1150 1/2 in. NPT Female
TNGC-1500/2000 1/2 in. NPT Female
TNGC-3000 1 in. Female
EMEA and APAC:
TNGC-1150 1/2 in. BSPP Female
TNGC-1500/2000 1/2 in. BSPP Female
TNGC-3000 1/2 in. BSPP Female
Drain Connection
Americas:
TNGC-1150 1/4 in. NPT Female
TNGC-1500/2000 1/2 in. NPT Female
TNGC-3000 1/2 in. NPT Female
EMEA and APAC:
TNGC-1150 1/2 in. BSPP Female
TNGC-1500/2000 1/2 in. BSPP Female
TNGC-3000 1/2 in. BSPP Female
Installation
The TYCO NG-1 1150, NG-1 1500, NG-1
2000, and NG-1 3000 Stand-Alone
Nitrogen Generators must be installed
in accordance with this section.
WARNING
Do not operate the TYCO Nitrogen
Generator if damaged during ship-
ment, handling or use. Failure to do so
may result in personal injury or prop-
erty damage.
Operation of the nitrogen membrane
above the rated design pressure could
be hazardous. Do not connect the
nitrogen generation equipment to com-
pressed air sources that can exceed
the maximum rated pressure without
installing pressure controls and safety
relief devices in the compressed air
supply line.
Specific procedures must be devel-
oped for maintenance and servicing
of the equipment where the nitrogen
membrane is located. Appropriate
labels must be continuously displayed
in all areas where personnel might be
exposed to a nitrogen atmosphere
under normal and abnormal conditions.
Nitrogen is nontoxic and largely inert.
Rapid release of nitrogen gas into an
enclosed space displaces the oxygen
and can cause an asphyxiation hazard.
CAUTION
Do not install the TYCO Nitrogen Gen-
erator or Air Compressor Package in
an area where ammonia, sulfur dioxide,
hydrogen sulfide, mercaptans, chlo-
rides, chlorine, oxides of nitrogen, acid
fumes, solvent vent vapors, and ozone
vapors or similar contaminates exist.
The equipment can be damaged by
ammonia and other vapors shortening
membrane life.
NG-1 Nitrogen Generators
Step 1: Mounting the Stand-Alone
Nitrogen Generator
The TYCO Stand-Alone Nitrogen Gen-
erator is designed to be mounted
directly to the floor and/or the wall at
the installation location. Several factors
should be considered in choosing the
proper mounting location for the nitro-
gen generator:
• Access to the power supply (dedi-
cated circuit)
• Access to the air source supplied to
the nitrogen generator
• Access to the sprinkler riser being
supplied from the nitrogen generator
• Access to drain for the condensate
discharge line
• Clearance at the front of the unit to
open cabinet door
• Clearance around ventilation vents
on side and bottom for proper cabi-
net ventilation
• When floor mounting the cabinet,
ensure floor is flat and level
• If wall mounting the cabinet, ensure
the wall is capable of supporting the
weight of the generator cabinet
The cabinet includes pre-punched
holes in the feet for floor mounting and
holes in the back panel for wall mount-
ing using standard anchors.
Step 2: Power Supply
The Nitrogen Generator requires a ded-
icated power supply that connects to
the terminal blocks in the nitrogen gen-
erator cabinet. See Figure 2A or 2B as
applicable.
Step 3. Plumb the Nitrogen/Air
Supply Line
The nitrogen/air discharge plumb-
ing from the nitrogen generator is to
be connected directly to the sprinkler
system valve trim using a minimum
of 1/2 in. to 1 in. black steel, galva-
nized steel or copper piping. The size
of the nitrogen/air supply line is to be
based on the length of pipe between
the nitrogen generator and the fire
sprinkler systems along with the total
volume of the fire sprinkler systems
being supplied. The nitrogen genera-
tor requires an in-line Air Maintenance
Device (AMD) that is equipped with an
on-board field adjustable pressure reg-
ulator for each zone being served. The
preferred AMD is the TYCO AMD-1.
Refer to technical datasheet TFP1221.
Note: When both dry pipe and preaction
fire sprinkler systems are connected to
one nitrogen generator, additional equip-
ment may be required if the fire sprinkler
systems operate at different supervisory gas
pressures.
Step 4: Plumb the Condensate Drain
Line
The Stand-Alone Nitrogen Genera-
tor will occasionally discharge a small
amount of condensate water from the
coalescing filters inside the cabinet. It
is recommended that the 1/4 in. drain
connection be plumbed to a floor drain
or building exterior. When plumbing to
a drain is not feasible an evaporative
collection chamber can be used.
Step 5: System Signals and Monitor-
ing (where used)
The nitrogen generator cabinet has
two system signals and five outputs
that can be monitored by the facility’s
BMS or fire alarm system as shown in
Figure 2A or 2B as applicable.
• Bypass Alarm - The nitrogen gener-
ator is operating in the bypass mode
which is activated when the bypass
valve is in the fast fill position to fast
fill the fire sprinkler system and the
air supplied directly from the air com-
pressor has reached a pressure of 20
psig (1,4 bar). (Flashing amber light)
• Leak Monitor - The nitrogen gener-
ator is equipped with a leak moni-
tor audible signal which is activated
when the nitrogen generator runs
excessively. (Audible signal)
The nitrogen generator cabinet includes
system monitoring signals which can
be monitored through a building moni-
toring system, if desired:
• Nitrogen Generator Running - Form
C contacts
• Bypass Mode Alarm - Form C
contacts
• Nitrogen Generator Power Monitor-
ing - Form C contacts
• Leak Monitoring - Form C contacts
• Nitrogen System Supply Line Pres-
sure - Analog Signal
NG1 Compressors
Step 1. Mounting the Air Compressor
The simplex air compressors are
designed to be mounted directly to
the floor in the fire sprinkler riser room.
Several factors should be considered in
choosing the proper mounting location
for the air compressors:
• Access to the appropriate power
supply (see Step 2 for power circuit
requirements per compressor sizes)
• Access to the nitrogen generator
inlet 1/2 in. supply line
• Access to a drain for the condensate
discharge line
• Clearance to access air compressor
for servicing

TFP1253
Page 5 of 8
GG
L1 N N N
NITROGEN GENERATOR
RUNNING OUTPUT
BYPASS MODE ALARM
OUTPUT LEAK MONITORING OUTPUT
POWER ON/OFF OUTPUT
NITROGEN SUPPLY
LINE PRESSURE
OUTPUT
230 VAC/
SINGLE PHASE/
50 HZ
CONNECTIONS
PRESSURE
SWITCH
INCOMING
POWER
FUSE
BOX
BUILDING
MANAGEMENT
SYSTEM
MONITORING
POINTS
POWER
SUPPLY
POWER
DISTRIBUTION
120 VAC/
SINGLE PHASE
60 HZ
CONNECTIONS
NITROGEN GENERATOR
RUNNING OUTPUT
BYPASS MODE ALARM
OUTPUT LEAK MONITORING OUTPUT
POWER ON/OFF OUTPUT
NITROGEN SUPPLY
LINE PRESSURE
OUTPUT L1 N G
PRESSURE
SWITCH
INCOMING
POWER
FUSE
BOX
BUILDING
MANAGEMENT
SYSTEM
MONITORING
POINTS
POWER
SUPPLY
POWER
DISTRIBUTION
L1 G
N N N G
FIGURE 2A
MODEL NG-1 1150, NG-1 1500, NG-1 2000, AND NG-1 3000 STAND-ALONE NITROGEN GENERATOR
AMERICAS SYSTEM SIGNAL MONITOR AND POWER SUPPLY CONNECTION
L1 N G
FIGURE 2B
MODEL NG-1 1150, NG-1 1500, NG-1 2000, AND NG-1 3000 STAND-ALONE NITROGEN GENERATOR
EMEA AND APAC SYSTEM SIGNAL MONITOR AND POWER SUPPLY CONNECTION

TFP1253
Page 6 of 8
460 VAC/3 PHASE/60 HZ OR
208 VAC/3 PHASE 60 HZ CONNECTIONS
LANDING POINTS
LABELED L1, L2, L3
The air compressors come with pre-
punched holes in the feet for easy
mounting to the floor using standard
anchors.
Note: Vibration pads (supplied) must be
installed under the feet of the air compressor
to ensure warranty of the air compressor.
Step 2. Power Supply
NOTICE
It is recommended that a service dis-
connect be provided adjacent to the air
compressor.
The air compressors require a dedi-
cated power supply that is terminated
in the power supply box on the air com-
pressor as shown in Figure 3A, 3B, or
3C as applicable. Verify the voltage
of the power supply available for the
air compressor is compatible with
the voltage requirements of the air
compressor.
NOTICE
With the TNGC-1500/2000 and the
TNGC-3000, verify that the compres-
sor and motor starter are configured
for operating at 208 VAC/3 phase
when providing 208 VAC/3 phase to
the control box.
Step 3: Plumb the Air Supply Line
For compressors in the Americas, the
air discharge plumbing from the air
compressor is to be connected to the
inlet of the nitrogen generator using
1/2 in. black steel, galvanized steel or
copper lines. For compressors in EMEA
and APAC, the air discharge plumb-
ing should first be connected to the
WSD-25 water separator which then is
to be connected to the inlet of the nitro-
gen generator.
Step 4: Plumb the Condensate
Drain Line
The TYCO oil-less air compressor will
discharge condensate water from the
air receiver tank. It is recommended
that the 1/4 in. drain connection be
plumbed to a floor drain or building
exterior. When plumbing to a drain is
not feasible an evaporative collection
chamber can be used.
Note: Ensure that the receiver tank auto-
drain is connected to an un-switched power
source: 120 VAC for Americas, 230 VAC for
EMEA and APAC.
Note: The Low Oil Level Sensor on the air
compressor automatically shuts down air
compressor until the proper oil level has
been restored. Care and
Maintenance
Nitrogen Generators
The TYCO NG-1 1150, NG-1 1500, NG-1
2000, and NG-1 3000 Stand-Alone
Nitrogen Generators, the TNGC-1150
Air Compressor, and TNGC-1500/2000
and 3000 Air Compressors must be
maintained and serviced in accordance
with this section.
Before closing a fire protection system
main control valve for maintenance
work on the fire protection system that
460 VAC/THREE PHASE/60 HZ OR
208 VAC/THREE PHASE/60 HZ
CONNECTIONS
LABELED L1, L2, L3
FIGURE 3A
MODEL TNGC-1150 AIR COMPRESSOR
AMERICAS POWER SUPPLY CONNECTIONS
FIGURE 3B
MODEL TNGC-1500/2000/3000 AIR COMPRESSOR
AMERICAS POWER SUPPLY CONNECTIONS

TFP1253
Page 7 of 8
DELTA
CONTACTOR
ON/OFF
SWITCH
FUSE
LINE CONTACTOR
WITH INTEGRATED
Y-D TIMER
OVERLOAD
REL AY
STAR
CONTACTOR
TERMINAL
BOARD
HOURMETER
RUNNING HOURS
it controls, permission to shut down
the affected fire protection systems
must first be obtained from the proper
authorities. All personnel who may
be affected by this decision must be
notified.
Inspection, testing, and maintenance
must be performed in accordance
with the requirements of the NFPA, and
any impairment must be immediately
corrected.
The owner is responsible for the inspec-
tion, testing, and maintenance of their
fire protection system and devices in
compliance with this document, as well
as with the applicable standards of any
authorities having jurisdiction. Contact
the installing contractor or product
manufacturer with any questions.
Automatic sprinkler systems are rec-
ommended to be inspected, tested,
and maintained by a qualified Inspec-
tion Service in accordance with local
requirements and/or national codes.
Maintenance of the Nitrogen
Generator
The nitrogen generator cabinet con-
tains three separate cartridge filters.
It is recommended that each of the
filter cartridges be replaced as part of
an annual preventative maintenance
program. In some environments it may
be necessary to replace filters more
frequently. When maintained properly
the nitrogen separation membrane will
provide up to 20 years of service life.
Filter Replacement Procedure
With reference to Figure 4, perform
the following steps when replacing the
cartridge filters located in the Filter
Housing.
Step 1. Turn the power supply to the
unit off.
Step 2. Close the Inlet and Outlet Ball
Valves, and open the Bypass Ball Valve.
Step 3. Depressurize the nitrogen gen-
erator internal inlet piping by slowly
opening the Depressurization Ball
Valve in the cabinet to the left of the
filter housing.
Step 4. Remove the filter housing by
pulling down on the blue housing lock
and turning the filter housing count-
er-clock wise.
Step 5. Once the filter housing has
been removed, the filter cartridge
inside is removed by first unscrewing
the black retaining disc at the base of
the cartridge and then pulling down on
the cartridge. Discard the old filter car-
tridge and replace it with the appropri-
ately marked filter cartridge from the
filter replacement kit by pushing up
so that it fits snugly onto the receiving
cylinder in the upper part of the filter
housing. Hand tighten the black retain-
ing disc back onto the central metal
threaded rod.
Step 6. Replace the filter housing by
pushing up into position and turning the
housing clockwise until blue housing
lock locks into place.
Step 7. Repeat Step 4 through Step 6
for each additional filter.
Note: Filters 2 & 3 do not have a black retain-
ing disc, filters screw directly into housing.
FIGURE 3C
MODEL TNGC-1150/1500/2000/3000 AIR COMPRESSOR
EMEA AND APAC POWER SUPPLY CONNECTIONS

TFP1253
Page 8 of 8
NATIONAL FIRE PROTECTION ASSOCIATION and NFPA are registered trademarks of National Fire Protection Association
1400 Pennbrook Parkway, Lansdale, PA 19446 | Telephone +1-215-362-0700
© 2021 Johnson Controls. All rights reserved. All specifications and other information shown were current as of document revision date and are subject to change without notice.
FILTER HOUSING WITH
LOWER HOUSING REMOVED
FILTER
CARTRIDGE
BLACK
DISC
WATER
SEPARATOR
FILTER
HOUSING
INLET BALL
VALVE
OUTLET BALL
VALVE
BYPASS BALL
VALVE
DEPRESSURIZATION
BALL VALVE
POWER ON/OFF
SWITCH
BYPASS
MODE
ALARM
INDICATOR
FIGURE 4
MODEL NG-1 1150, NG-1 1500, NG-1 2000, AND NG-1 3000 STAND-ALONE
NITROGEN GENERATOR FILTER CARTRIDGE REPLACEMENT
Step 8. Remove the Water Separator
housing by pulling down on the blue
housing lock and turning the housing
counter-clockwise. Inspect the Water
Separator and clean as necessary.
Step 9. Replace the Water Separator
housing by pushing up into position
and turning the housing clockwise until
blue housing lock locks into place.
Step 10. Close the depressurization
ball valve. The Nitrogen Generator can
now be placed back into service.
Step 11. Turn the power supply to the
unit ON.
Step 12. Close the Bypass Ball Valve.
Step 13. Open the Inlet and Outlet Ball
Valves.
Compressors
Maintenance of the Compressor
For compressor maintenance, please
refer to the manufacturer’s recom-
mended maintenance plan in the
owner’s manual for the compressor.
Limited
Warranty
For warranty terms and conditions, visit
www.tyco-fire.com.
Ordering
Procedure
TYCO will supply a list of required part
numbers to order through regular sales
channels. Contact your local business
manager or sales person and specify
the following:
Sizing of Nitrogen Generator
• Total cumulative size of all dry/pre-
action sprinkler systems
• Size of the largest single dry/preac-
tion sprinkler system
• Total number of dry/preaction sprin-
kler systems
• Supervisory pressure of all dry/pre-
action sprinkler systems
• Required voltage needed for dry/pre-
action sprinkler system
Filter Replacement Kit
Filter Replacement Kit . . . . . . . . . . . . . TNGFLTS
Optional Monitoring Equipment
Model THGA Handheld Gas Analyzer..THGA01
Model TSGA SMART Gas Analyzer....TSGA01
Model TILD In-Line Corrosion Detector
Refer to Technical Data Sheet TFP1261 for
ordering instructions.
This manual suits for next models
3
Table of contents
Other Tyco Portable Generator manuals
Popular Portable Generator manuals by other brands
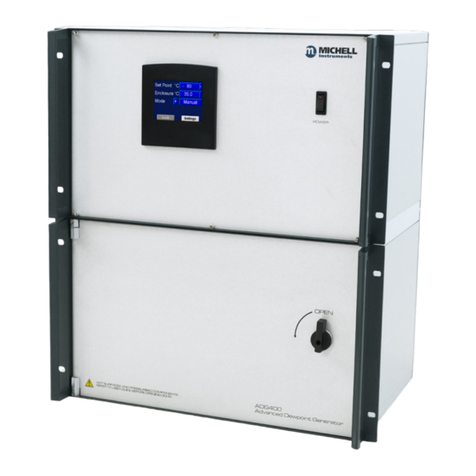
PST
PST MICHELL Instruments ADG400 user manual

Buffalo
Buffalo Sportsman GEN10K instruction manual

Champion Power Equipment
Champion Power Equipment 73001I-DF Owner's manual & operating instructions

Pasco Scientific
Pasco Scientific SE-8763 Instruction manual and experiment guide

GenConnex
GenConnex GXK LPNG-EU7000is-Kit-EC5.0 owner's manual
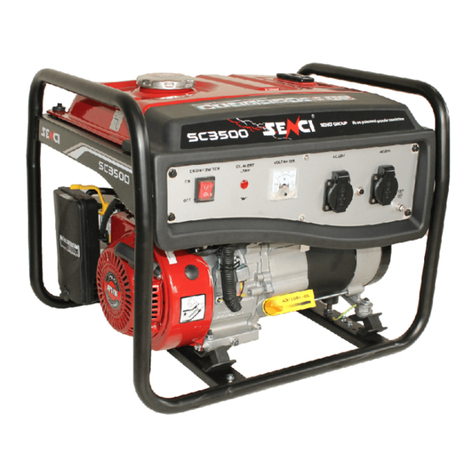
Senci
Senci SC-3500 LITE user guide