Universal Analyzers 270SF User manual

MAN.270SF.REVB.102018
Instruction Manual
Model 270SF
Extractive Gas Sample Probe
5200 Convair Drive • Carson City, NV 89706 • Ph: 775.883.2500 • Fax: 775.883.6388 • www.universalanalyzers.com

MAN.270SF.REVB.102018 Page 2 of 18
TABLE OF CONTENTS
1.0Receiving and Storage .......................................................................................... 3
2.0Definition of Symbols ............................................................................................. 4
3.0Product Identification ............................................................................................. 5
4.0Specifications ........................................................................................................ 7
5.0Description and Principle of Operation .................................................................. 8
6.0Installation ............................................................................................................. 9
7.0Start-Up ............................................................................................................... 10
8.0Shutdown ............................................................................................................ 11
9.0Maintenance ........................................................................................................ 12
10.0Troubleshooting ................................................................................................... 13
11.0Spare Parts ......................................................................................................... 14
12.0Drawings 270SF .................................................................................................. 15
13.0Limited Warranty ................................................................................................. 16

MAN.270SF.REVB.102018 Page 3 of 18
1.0 Receiving and Storage
The Universal Analyzers 270SF Extractive Gas Sample Probe are completely pre-assembled. No assembly is
necessary when received on-site.
Carefully inspect the product and any special accessories included with it immediately on arrival by removing them
from the packing and checking for missing articles against the packing list.
Check the items for any damage in transit and, if required, inform the shipping insurance company immediately of
any damage found.
Storage Location should be protected from the elements. Although all components provided are designed to resist
corrosion, additional protection from heat (>140°F/ 60°C) and humidity is recommended.

MAN.270SF.REVB.102018 Page 4 of 18
2.0 Definition of Symbols
CAUTION, RISK OF DANGER SYMBOL INDICATES INJURY MAY OCCUR IF MANUFACTURER’S
INSTRUCTIONS ARE NOT ADHERED TO.
PLEASE READ MANUAL CAREFULLY WHEN SYMBOL IS DISPLAYED
CAUTION, HOT SURFACE SYMBOL INDICATES EXPOSED SURFACE TEMPERATURE CAN
CAUSE BURNS OR PERSONAL INJURY. CARE SHOULD BE TAKEN WHEN CONTACT IS
REQUIRED.
CAUTION, RISK OF ELECTRICAL SHOCK SYMBOL INDICATES ELECTRICAL SHOCK MAY
OCCUR. CAUTION SHOULD BE TAKEN BEFORE DISCONNECTING OR CONTACTING ANY
ELECTRICAL CONNECTIONS.
PROTECTIVE CONDUCTOR TERMINAL SYMBOL INDICATES THE TERMINAL LOCATION FOR
THE PROTECTIVE CONDUCTOR. FAILURE TO CONNECT TO THE PROTECTIVE CONDUCTOR
TERMINAL MAY RESULT IN A SHOCK HAZARD.

MAN.270SF.REVB.102018 Page 5 of 18
3.0 Product Identification
270SF (subflange design) Gas Sample Probe for General Purpose & Hazardous Areas
Additional Options Shown on Next Page
270SF Model Extraction Sample Probe (Items marked with ** are not available on FM and ++ for ATEX hazardous area probes
All
Sample Probes are Configured and Sold WITHOUT probe tubes (Stinger, Quill, Straw)
Chamber Material (Part Number Configurator: 270)
SF
316 Stainless Steel <400˚F (204˚C) (Standard) -Sub-Flange Mount
CF
Hastelloy C-276 < 400˚F (204˚C) -Sub-Flange Mount
TF
316 Stainless Steel w/TFE Coating < 400˚F (204˚C) -Sub-Flange Mount (no chamber isolation valve option)
NF
316 Stainless Steel w/ SilcoNert™ 2000 Coating < 400˚F (204˚C) -Sub-Flange Mount
SHF
316SS Hi Temp w/Kalrez® < 550˚F (288˚C) -Sub-Flange Mount
CHF
Hastelloy C-276 Hi Temp w/Kalrez® < 550˚F (288˚C) -Sub-Flange Mount
NHF
316 Stainless Steel w/ SilcoNert™ 2000 Coating Hi Temp w/ Kalrez® < 550˚F (288˚C) -Sub-Flange Mount
xxxU
xxxV
For Chamber Isolation Valve, add a 'U' to the End of the Chamber Material Selection for Unheated
For Chamber Isolation Valve, add a 'V' to the End of the Chamber Material Selection for Heated **++
Unheated - 316SS Valve, Monel (used with Hast. C-276 chamber), 316SS SilcoNert™ 2000
Low Temp (heated to 270 °F) - 316SS Valve, Monel (used with Hast. C-276 chamber), 316SS SilcoNert™ 2000
High Temp (heated to 550 °F) - 316SS Valve, Monel (used with Hast. C-276 chamber), 316SS SilcoNert™ 2000
Flange Size (Other Sizes Available, Consult the Factory)
F1
1.5" Flange
F2
2" Flange
F3
3" Flange
F4
4" Flange
F6
6" Flange
F1T
1.5" Flange - Top Dead Center
F2T
2" Flange - Top Dead Center
F3T
3" Flange - Top Dead Center
F4T
4" Flange - Top Dead Center
F6T
6" Flange - Top Dead Center
Chamber Heat Control
340
340°F (171°C) Temp Switch (Standard) - Mandatory for FM/ ATEX Approved Units (Standard)
375
375
°F
(190
°C
) Temp Switch**++
550
550
°F
(288
°C
) Temp Switch**++ (use high temp chamber in Chamber Material)
R
RTD Only**++ (includes 550 °F safety switch)
K
T/C Only, Type K**++ (includes 550°F safety switch)
J
T/C Only, Type J**++ (includes 550°F safety switch)
Blowback Type
BB
Blowback (Standard)
BT
Blowback w/ Smart Timer (Same as system voltage, 115 or 230 VAC. BB valve must match)**++
HB
Heated Blowback**++
HT
Heated Blowback w/Smart Timer (Same as system voltage, 115 or 230. BB valve must match)**++
N
No Blowback
Blowback Port
S
Standard Blowback
P
Blowback Probe Tip Filter Only -
No Chamber Blowback
N
No Blowback
Blowback Valve
24
24 VDC Actuator
1
115 VAC Actuator
2
230 VAC Actuator
A
Pneumatic Actuator
N
No Blowback
Enclosure (If Heatshrink Boot is other than 3", identify size after enclosure designator)
2 = 0.75" - 1.6" (19.05mm - 40.64mm) Dia.
3 (Standard) = 1.38" - 2.75" (35.05mm - 69.85mm) Dia.
4 = 1.43" - 4.47" (36.32mm - 113.54mm) Dia.
FG
Fiberglass Enclosure (Standard), 3" Boot
FI
Fiberglass Enclosure, Insulated, 3" Boot
SS
Stainless Steel Enclosure, 3" Boot
SI
Stainless Steel Enclosure, Insulated, 3" Boot
Enclosure Heat Control (Heating requires Insulated Enclosure)
N
No Enclosure Heat (Standard)
T
225
°F
(107
°C
) Temp Switch** (ATEX Enclosure uses a 150
°F
(65
°C
) T-Stat)
K
T/C Only, Type K**++
J
T/C Only, Type J**++
R
RTD Only**++
Power/Classification
1
115 VAC General Purpose
2
230 VAC General Purpose
1FM
115 VAC Approved for Class I, DIV. II, Grp. B, C, D (FM/ CSA)
2FM
230 VAC Approved for Class I, DIV. II, Grp. B, C, D (FM/ CSA)
1EX
115 VAC ATEX Approved for Zone IIC (TUV)
2EX
230 VAC ATEX Approved for Zone IIC (TUV)
Filter
2
2μm Ceramic (standard)
1
1μm Ceramic
C
0.1μm Ceramic coated
S
2μm Sintered 316SS

MAN.270SF.REVB.102018 Page 6 of 18
Temperature/Alarm (do not choose R/K/J option if used above)
F
Failsafe (Open on Alarm)
C
Closed on Alarm
R
100 Ohm RTD (Includes Failsafe Alarm Contact)
K
Type K ThermoCouple (Includes Failsafe Alarm Contact)
J
Type J ThermoCouple (Includes Failsafe Alarm Contact)
N
None
Ammonia Converter (General Purpose area only)
A
Integrated on the Right Side of the 270**++
N
None
Extended Length Probe Tube Support (not with HPA)
N
Std PTS
2C
Extended Length Probe Tube Support
x = Length in Ft (2,3,4,5)
y=Material of Construction
S = 316SS (up to 1100˚F (593˚C))
T = 310SS (up to 1600˚F (871˚C))
C = Hast C-276 (up to 1900˚F (1038˚C))
2S
2T
3C
3S
3T
4C
4S
4T
5C
5S
5T
Heated Probe Adapte
r
(adds Terminal Blocks to 270)
N
None
K
Type K T/C Terminal Blocks
J
Type J T/C Terminal Blocks
R
RTD Terminal Blocks
Z-Purge Panel
N
None
H
Mounted on Top of 270**++
V
Mounted on Side of 270**++
270 -SF -F1 -340 -BB -S -24 -SS -N -1 -2 -R -N -N -N -N

MAN.270SF.REVB.102018 Page 7 of 18
4.0 Specifications
OPERATING SPECIFICATIONS
Sample Flow Rate 0 to 20 l/m
Calibration Gas Requirement Sample flow rate plus 10%
Operating Pressure Drop at 10 l/m 12” water column
Maximum Stack Temperature 700°F (370°C)
Oven Temperature 340°F (171°C)
Enclosure Dimensions:
Fiberglass H 18” x W 16” x D 10” (H 458mm x W 407mm x D 255mm) f
SS H 16” x W 14” x D 8” (H 407mm x W 356mm x D 203mm)
Weight 25 lbs (12kg) (plus probe)
Input Voltage Requirement 115/230VAC 50/60 Hz
Input Power Requirement 150 watts
With Optional Heated Enclosure 350 watts
**External fuse required of 20 A or less**
Electrical Classification General purpose
Ambient Temperature, Operating 200°F maximum (93°C)
Blowback Tank Volume 0.7 scf (19.8 l) when at 100 psig (7.4 barg)
Blowback Duration 0.5 sec. to empty accumulator
Enclosure Nema 4x fiberglass (standard)
Stainless steel (optional)
Sample Line Connection 3” Heat shrink boot (standard)
4” Heat shrink boot (optional)
2” Heat shrink boot (optional)
Heater Type Rod heaters in aluminum block, controlled w/ thermal switch
Available Filter 2 µm ceramic (standard)
316SS (optional)
Chamber Materials 316SS (standard)
316SS, SilcoNert™ coated Hastelloy C-276

MAN.270SF.REVB.102018 Page 8 of 18
5.0 Description and Principle of Operation
APPLICATION
The Universal Analyzers Model 270SF Extractive Gas Sample Probe Assembly is designed to be installed on
sample stacks containing non-hazardous gases. The 270 may be installed in an unclassified location. Filter
changes can be made in less than one minute.
The 270SF filter will mount by means of a pipe flange to a mating flange on the stack. The size of the flange
can be specified by the user and can include 2”, 3”, 4”, 6” or DIN type. A 1/2” NPT female threaded
connection is provided for the sample probe to mount inside the mounting flange. Stack temperatures and
corrosive gases will determine the material and design of the probe to be used.
Sample flow rates of up to 20 liters per minute can be extracted and filtered through the Model 270 with a
minimal amount of pressure drop.
GENERAL DESCRIPTION, HEATED FILTER SECTION
The Model 270SF is a Extractive Gas Sample Probe Assembly consisting of the filter body mounted in a
NEMA 4X Fiberglass Enclosure or Stainless Steel Enclosure. An optional blowback system is provided to
allow the blowback to occur on command from a computer, data logger, PLC, UAI timer card or external
switch mounted in a safe area.
Two 63 watt heaters are mounted in an aluminum sleeve around the filter cavity. The heater holds the
temperature of the filter at 340°F (171°C). A hermetically sealed bi-metallic thermal switch mounted to the
filter body keeps the temperature from exceeding 350°F (177°C) by opening the circuit at that temperature.
An optional independent temperature sensor can be provided as a means to measure and transmit or record
the temperature of the filter. A second thermal switch, set at 225°F (107°C) is provided to be used as an
alarm contact, if the temperature drops below the switch temperature. In colder climates, an additional heater
can be supplied for the enclosure. This heater will maintain 150°F (65°C) inside the enclosure.
Several types of filter elements can be supplied with the Model 270. The 2μm ceramic filter is supplied as an
economical general-purpose filter. A similar ceramic filter with an internal 0.1μm coating is available for finer
filtration or to provide a surface to enhance the blowback capability where the particulates have a tendency to
fill the pores of the 2μm element. A 2μm, 316SS Filter can be inserted for those applications where the
ceramic filter is determined to be unsuitable. Additional filtration materials and pore sizes are available on
request.
Blowback air is used to clean the filter element. Compressed air supplied to the blowback assembly needs to
be clean and dry (-40°F/°C recommended). Instrument quality air is preferred. The pressure should be as
high as possible, up to 125psig (8.8barg). High pressure air fills the accumulator (a 7” (178mm) diameter SS
sphere) and provides a substantial blast when the high flow solenoid valve opens. This loosens the particles
on the filter surface and forces them back through the sample probe into the sample point. The period of time
between blowback cycles should be set to occur before the pressure drop across the filter begins to increase
beyond acceptable limits. By installing and monitoring a vacuum gauge ahead of the sample pump, a
maintenance interval can be established. This can be as often as every fifteen minutes but no less frequently
than once per day. The time period between blowback cycles can be based on a calculation to estimate the
amount of sample required to deposit from three to five grams of solids in the filter element.
Instrument air usage is minimal and smoothed by the fact that the air accumulator is charged over a period of
time through a 1/4” instrument airline. The recharge time could be extended with a restriction in the air line if it
were desired to reduce the pressure pulses on the instrument air supply and to consume instrument air more
slowly.
The calibration gas is injected into the chamber ahead of the filter. This is close to the sample source, as is
required by many EPA officers. A back-pressure check valve (set at 3 psig (0.2 barg) is provided in the cal
gas injection path to ensure that calibration gas does not leak into the sample while the sample is being
drawn through the filter.

MAN.270SF.REVB.102018 Page 9 of 18
6.0 Installation
The probe tube (stinger) should be screwed into the 1/2” NPT fitting on the inside of the mounting flange. To
prevent galling, coat the threads with an anti-seize compound. Remove and anti-seize compound from the
inner wall of the probe tube before attaching it to the probe. The length of the probe should be selected to
extend into the center third of the stack; or if the stack diameter is greater than 12’, at least 6’ into that stack.
The studs on the mounting flange should be joined to the sampling nozzle on the stack and the assembly
bolted into place.
A heated sample line should be supported close to the Model 270. The heated sample line should be fed
through the heat shrink boot on the bottom of the enclosure. Connect the sample tube to the center tubing
fitting (3/8”) on the filter. The unheated portion of the sample line should be kept short and insulated to avoid
condensation. Connect the calibration gas line to 1/4” tubing fitting located on the left side of the chamber and
is connected to the chamber via a check valve. If the compressed air line is part of the heated sample line, it
can be connected to the 1/4” fitting adjacent to the blowback accumulator. If an external airline is to be used
for blowback, bring the air into the enclosure through a bulkhead fitting (supplied by others) to be installed in
the wall of the enclosure, typically the mounting location is in the bottom of the enclosure, and connect the air
to the same 1/4” fitting.
Provide power to the terminal block(s) within the stack filter enclosure in the Model 270. 150 watts (without
heated enclosure) or 350 watts with heated enclosure, at 115/230VAC is required.
NOTE: The supply power circuit MUST include an overprotection device with a maximum
rating of 20A. A disconnect switch must be located in close proximity to the probe.
A thermal switch mounted in the aluminum heater will control the temperature to 340°F (171°C).
Insure the power supplied to the heater matches the heater voltage requirement shown on the
serial number tag. The voltage requirement can be changed by changing the jumpers on the
terminal strips (reference terminal strip label or drawings for details). An independent ground
wire should be run to the grounding terminal on the terminal strip.
If an independent measurement and display of the oven temperature is desired, a temperature sensor can be
slipped into a 1/8” diameter thermowell supplied on the heater tube assembly.
The final installation step is to ensure that the sample line is insulated completely. Close the cover of the
enclosure and secure the latches. After securing the heated sample line, use a heat gun to shrink the entry
boot onto the sample line. The goal is to keep the temperature of the gas sample at a temperature above the
dew point of the gas all the way from the stack to the sample cooler/dehydrator.

MAN.270SF.REVB.102018 Page 10 of 18
7.0 Start-Up
Apply power to the Model 270. Allow fifteen to twenty minutes for the filter to come to temperature. This
warm-up period is extremely important to avoid the condensation within the Model 270 filter which would
cement the particulates to the filter surface.
Start the sample pump and determine that the proper amount of sample is being supplied to the
instrumentation.
Perform a calibration cycle to ensure that the calibration lines are properly installed and sealed. A flow meter
should be installed in the calibration gas supply line to ensure that there is at least 10 percent more calibration
gas being supplied to the Model 270 than is being withdrawn as sample. This will ensure that the filter and
probe are being properly flooded with calibration gas. The excess calibration gas will pass through the probe
tube into the stack.
Open the instrument air valve to charge the blowback accumulator. Exercise the blowback solenoid valve to
insure it is properly wired. After a blowback cycle, the presence of a slight pulse on the sample tubing in the
analyzer shelter and the momentary dilution of the sample with instrument air is normal and signifies that a
blowback cycle has occurred.
The optimum time between blowback cycles is to be determined by experience, once a day is sufficient in
relatively clean applications. The requirement could be as frequent as every fifteen minutes where the dust
and soot levels are severe. It is better to blowback too often than not often enough. A vacuum gauge in the
sample line can be helpful to indicate if the particulate loading of the filter has started to restrict the flow of
sample. The blowback cycle should be initiated before unacceptable pressure drop occurs.

MAN.270SF.REVB.102018 Page 11 of 18
8.0 Shutdown
Before removing power from the unit, ensure filter chamber has been purged of any potentially hazardous
components.
To purge the chamber, perform the following:
1. If equipped, perform a manual blowback operation.
2. Close the filter stack isolation valve(s).
3. Ensure no sample is being drawn though the filter chamber. If the sample is being drawn using a sample
pump, turn off the power to the pump or disconnect the sample line.
4. If not already done, disconnect the sample line.
5. Use instrument air or other inert gas, flow ~10 l/m for 15-30 minutes through the filter chamber.
Note: Inert gas can be routed through the chamber via the calibration gas line.
6. After purging is complete, follow the maintenance procedure to change the filter.
7. Cap the sample outlet tube connection and disconnect power from the unit.
Note: If electrical wires are to be disconnected, follow applicable ‘Lock Out/ Tag Out’ requirements.

MAN.270SF.REVB.102018 Page 12 of 18
9.0 Maintenance
CHANGING THE FILTER
CAUTION: THIS PROCEDURE CAN CAUSE SEVERE BURNS. USE PROPER
PROTECTION.
Changing the filter in the Model 270 Heated Filter Assembly is extremely easy. Using gloves to protect the
hand, grasp the cap on the end of the filter body opposite the probe and turn it counterclockwise. The cover
may be hot to the touch and may cause burns to the hand if not protected. Removing the cover exposes the
filter. The cover is secured to the assembly with a retainer chain. Reach into the heated oven with pliers to
pull out the old filter.
Inspect the O-Rings which are at each end of the filter to ensure they are still elastic and will seal the filter.
Replace O-Rings if they are charred or deformed.
Replace the filter with a new one, again handling it with pliers. Ensure that the filter is pushed in the center of
the oven so that it is in contact with the O-Ring on the far end of the filter. Screw the cap back on the filter
body. The filter replacement procedure is complete.

MAN.270SF.REVB.102018 Page 13 of 18
10.0 Troubleshooting
The following table should give an overview of possible errors and an instruction to check and to repair them
(is not valid for the starting-up period of cooler).
Error Possible reason Check/Repair
No sample gas flow Filter element plugged
Filter chamber exit port plugged
Check/ replace filter element
Remove filter element and
inspect exit port. Exit port will be
located at 0° or 180° depending
on confi
g
uration
Low temperature alarm Insufficient warm-up time
Power disconnected
Control switch defective
Ensure power has been applied
to the unit for a minimum of 15
minutes
Ensure power is supplied to the
unit. Check by measuring for AC
voltage on TB1-1 & 2
Verify by measuring for a closed
circuit between TB1-1 & 4
High oxygen readings/ low
pollutant readings
Leak Leaking past the filter element O-
Rings. Remove filter element and
inspect O-Rings. There are two
O-Rings, one located at the base
of the filter element and the other
in the cap. Ensure both are
pliable and seated in their
respective grooves
Leaking blowback solenoid valve.
Block or disconnect the blowback
supply
Loose connection Verify all
fittin
g
s are leak free
Low readings during calibration Insufficient calibration gas flow Ensure calibration flow is at least
110% of the sample
g
as flow

MAN.270SF.REVB.102018 Page 14 of 18
11.0 Spare Parts
Consumable Spare Parts
Part P/N
O-Ring, Viton 2-208, Filter Element 4904-0015
O-Ring, Viton 2-217, Knob Assembly 4904-0016
Heater Element Paste 8010-0001
Filter Element Ceramic Alumina, 2 µm (Standard) 4980-0007
Filter Element Ceramic Coalesc.1µm Coated 4980-0018
Filter Element Sintered 316SS, 2 µm 4980-0023
Filter Element Ceramic Alumina, 1 µm 4980-0127
Spare Parts
Part P/N
Temp. Switch Heater Control, Normally Closed Below 340°F (171°C) 3103-0014
Knob Assembly 5209-0083
Low Temp. Switch, Normally Closed Below 225°F 3103-0013
Low Temp. Switch, Normally Open Below 225°F (107°C) “Fail Safe” 3103-0012
Valve Check 1/4” Tube X 1/4” Tube 316SS Set At 3 PSI 4955-0148
Optional Parts
Part P/N
Heater Tube Assembly (Incl. Alum Oven, Heater Elements, Temp. Switch’s & 3014-0002
Heater Tube Assembly (Incl. Alum Oven, Heater Elements, Temp. Switch’s &
Insulation Blanket) – “Fail Safe”
3014-0026
Solenoid Valve Blowback, 2-Way 24VDC 4955-0010
Solenoid Valve Blowback, 2-Way 120VAC 4955-0002
Solenoid Valve Blowback, 2-Way 240VAC 4955-0005
Check Valve Calib. Gas, Adjustable Pressure 5150-0014
Accumulator Sphere Blowback, Unheated 4956-0001
Acid Blocker Assembly, Blowback 5110-0015
Gasket Ring For 4” 150# Flange Garlock 9850 1/16” Thk 4903-0001
* Commissioning Spare Part

MAN.270SF.REVB.102018 Page 15 of 18
12.0 Drawings 270SF
For the current revision of all Model 270SF Probe drawings, visit the Universal Analyzers website.
https://www.universalanalyzers.com/
Navigate to: Products -> Gas Sample Probes -> Model 270SF
Links to all current drawings for standard probe configurations are provided at the bottom of the page.

MAN.270SF.REVB.102018 Page 16 of 18
13.0 Standard Terms & Conditions of Sale and Warranty
THE FOLLOWING TERMS/CONDITIONS, TOGETHER WITH ANY OTHER TERMS/CONDITIONS
SPECIFICALLY AGREED TO IN WRITING BY SELLER, SHALL APPLY TO ALL ORDERS (“Order(s)”) FROM,
AND SALES OF PRODUCTS (“Products”) OR SERVICES (“Services”) TO BUYER. ANY ACCEPTANCE OF
ANY ORDER OF BUYER IS CONDITIONED UPON THESE TERMS/CONDITIONS. ANY ADDITIONAL OR
DIFFERENT TERMS/CONDITIONS PROPOSED BY BUYER IN ANY DOCUMENT ARE OBJECTED TO AND
SHALL NOT BE BINDING UPON SELLER.
No salesperson is authorized to bind Seller to any promise or understanding not expressed herein.
I. PRICES
All prices are subject to change without notice in the
event of any changes in cost of materials or labor,
specifications, quantities, delivery schedules, customs
duties, other factors beyond Seller’s control, or in the
event of delays caused by instructions of the Buyer, or
failure of the Buyer to give Seller adequate information.
Further, prices payable by the Buyer shall be subject to
immediate increase, should the Seller as a result of
governmental action or regulation including, without
limitation, those contemplated by an investigation under
Section 232 of the Trade Expansion Act of 1962 (19
U.S.C.§1862), incur additional duties, tariffs or
restrictions on products sold hereunder, or on the raw
materials that are used in making such products. In no
event shall prices include any amounts imposed on the
Buyer in connection with Buyer’s purchases from Seller,
such as taxes, including but not limited to Value Added
Tax (VAT) or excise taxes, duties, tariffs, or any other
costs assessed against the Buyer by a governmental
authority.
II. DELIVERY
Delivery dates are approximate and are dependent on
prompt receipt by Seller of all necessary information.
Seller may deliver all or any part of Products/ Services as
early as 30 days in advance of agreed schedule. The
point of delivery shall be "Exworks" Seller’s premises,
unless otherwise specified by Seller. Upon delivery, title
to Products and all risk of loss or damage thereto shall
pass to Buyer. Where Buyer notifies Seller that it cannot
take timely delivery of the Products, Seller may place
such Products in storage, at the risk of Buyer, and Buyer
shall reimburse Seller for all expenses incurred in
connection with such storage. Buyer shall dispose of the
packing materials for Products at its own expense, and
shall defend, indemnify and hold harmless Seller from
any legal obligations in connection with such packing
waste.
III. PAYMENT
A. The term of payment shall be net 30 days from date of
Seller's invoice, unless otherwise specified. Payments
shall be made by Buyer without any deduction or set-off.
Unless otherwise agreed, payment shall be made in U.S.
dollars. Seller may charge late payment fees at the rate
of 1.5% per month, or the highest rate permitted by law,
whichever is less, accruing daily.
B. If the financial condition of Buyer is unsatisfactory to
Seller, Seller may require full or partial payment in
advance, or satisfactory security, in the form of a letter of
credit or otherwise. In the event of bankruptcy or
insolvency of Buyer, Seller may immediately cancel any
Order then outstanding.
C. Buyer grants Seller a purchase money security
interest in Products located in the United States, or
Services, as well as any proceeds, for the purpose of
securing the obligations of Buyer hereunder. Buyer
authorizes Seller to execute on Buyer’s behalf and file
such financing statements as Seller deems appropriate
to perfect and notify Buyer’s creditors of Seller’s security
interest.
IV. VARIATIONS IN QUANTITY; CHANGES.
Buyer shall accept delivery of quantities greater or
smaller than the quantity specified in Order(s), provided
that any such variation shall not exceed 5% of the
quantity originally specified, or 2 units, whichever is
greater. Seller shall not be required to give notice of any
such variations other than in the applicable shipping
notice and invoice. Seller reserves the option to make
changes to Products or Services which do not affect form,
fit, or function, and shall deliver Products to the latest
configuration part number at the time of delivery.
V. EXPORT CONTROLS; FCPA; ANTI-BOYCOTT
A. Buyer shall not make any disposition of the Products,
by way of transshipment, re-export, diversion or
otherwise, except as applicable U.S. export laws and
regulations may expressly permit, and other than in and
to the ultimate country of destination specified on
Order(s) or declared as the country of ultimate
destination on Seller's invoices or in the End Use
Statement that Buyer supplies Seller. Seller shall not be
named as shipper or exporter of record or U.S. principal
partyin- interest (USPPI) unless specifically agreed to in
writing by Seller in which case, Buyer shall provide Seller
with a copy of the documents filed by Buyer for Export
clearance purposes. At Seller’s request, Buyer shall
supply end-use and end-user information to determine
export license applicability. Failure of Buyer to comply

MAN.270SF.REVB.102018 Page 17 of 18
with this section shall constitute a material default
allowing Seller to cancel related Order(s) without liability.
B. Buyer warrants that it shall not violate or cause the
Seller to violate the U.S. Foreign Corrupt Practices act of
1977 (FCPA), as amended, the United Kingdom Bribery
Act (UKBA) of 2010, as amended, or their respective
implementing regulations in connection with Buyer’s sale
or distribution of the Products and/or Services, and that
Buyer does not know or have reason to believe that any
consultant, agent, representative or other person
retained by Buyer in connection with the sale and/or
distribution of Products/Services has violated, nor caused
Seller to violate the FPCA and/or the UKBA. Where Buyer
learns of or has reason to know of any violation of FCPA
and/or or UKBA in connection with the sale or distribution
of Products/Services, Buyer shall immediately advise
Seller.
C. Buyer further warrants that Buyer shall not violate or
cause Seller to violate the U.S. Antiboycott Provisions of
the U.S. Export Administration Regulations issued
pursuant to the U.S. Export Administration Act of 1979,
as amended, in connection with Buyer’s purchase of
Products/Services and that Buyer shall not request or
require Seller to make statements or certifications against
countries that are not subject to boycott by the U.S.
VI. WARRANTIES
A. Seller warrants that Products manufactured by Seller,
when delivered, shall be free from defects in
material/workmanship. Seller warrants that Services shall
be performed in accordance with generally accepted
industry practice. Seller's obligations under this warranty
shall be limited exclusively to repairing or replacing, at
Seller's option, any part of Products which, if properly
installed, used and maintained, proved to have been
defective in material or workmanship within 1 year from
the date of shipment or re-performing the Services. Seller
warrants for a period of 1 year from the date of shipment
that software or firmware, when used with Products, shall
perform in accordance with Seller’s published
specifications. Seller makes no warranty, express or
implied, that the operations of the software or firmware
shall be uninterrupted or error-free, or that functions
contained therein shall meet or satisfy the Buyer’s
intended use/requirements. Buyer shall notify Seller of
any defect in the quality or condition of Products
(including software/firmware) or Services within 7 days of
the date of delivery or performance, unless the defect
was not apparent on reasonable inspection, in which
case, within 7 days after discovery of the defect. If Buyer
does not provide such timely notification, it shall not be
entitled to reject Products (including software/firmware)
or Services, and Seller shall have no liability for such
defect.
B. Seller's warranty obligations shall not apply to
Products which (1) have been altered or repaired by
someone other than Seller, or (2) have been subjected to
misuse, neglect, or improper use or application, or (3) are
normally consumed in operation, or (4) have a normal life
inherently shorter than the warranty period stated therein.
C. No Products may be returned unless authorized in
advance by Seller, and then only upon such conditions to
which Seller may agree. Buyer must obtain a Return
Material Authorization (RMA) number from Seller prior to
any return shipment, and such RMA number must appear
on the shipping label and packing slip. Buyer shall be
responsible for returned Products until such time as
Seller receives the same at its facility, and for all charges
for packing, inspection, shipping, transportation or
insurance associated with returned Products.
D. This section VI sets forth the exclusive remedies and
obligations for claims based upon defects in or
nonconformity of Products/Services, whether the claim is
in contract, warranty, tort (including negligence of any
degree or strict liability) or otherwise. THE FOREGOING
WARRANTIES ARE IN LIEU OF ALL OTHER
WARRANTIES, WHETHER ORAL, WRITTEN,
EXPRESS, IMPLIED OR STATUTORY. NO IMPLIED
OR STATUTORY WARRANTIES OF
MERCHANTABILITY OR FITNESS FOR PARTICULAR
PURPOSE SHALL APPLY.
VII. PATENTS/INDEMNITY
If Buyer receives a claim that Products, or part thereof
manufactured by Seller infringes a patent, Buyer shall
notify Seller promptly in writing and give Seller
information, assistance and exclusive authority to
evaluate, defend and settle such claim. Where Buyer has
furnished specifications/designs for the manufacture of
the allegedly infringing Products, Buyer shall defend,
indemnify and hold harmless Seller against third-party
claims for infringement arising out of Seller’s use of such
specifications/designs.
VIII. LIMITATION OF LIABILITY
The total liability of Seller on any claim, whether in
contract, tort (including negligence of any degree and
strict liability) or otherwise arising out of, connected with,
or resulting from the manufacture, sale, delivery, resale,
repair, replacement or use of any Products/Services,
shall not exceed the price allocable to the
Products/Services or part thereof which gives rise to the
claim. IN NO EVENT, WHETHER AS A RESULT OF
BREACH OF CONTRACT, WARRANTY, TORT,
(INCLUDING NEGLIGENCE OF ANY DEGREE, STRICT
LIABILITY OR PATENT INFRINGEMENT) OR
OTHERWISE, SHALL SELLER, ITS AFFILIATES,
SUBCONTRACTORS, OR SUPPLIERS BE LIABLE
FOR ANY LOSS OF PROFIT OR REVENUES, LOSS OF
USE OF THE PRODUCTS OR SERVICES, OR ANY
ASSOCIATED EQUIPMENT, COST OF CAPITAL,
COST OF SUBSTITUTE GOODS, FACILITIES,
SERVICES OR REPLACEMENT POWER, DOWNTIME
COSTS OR CLAIMS OF BUYER'S CUSTOMERS FOR
DAMAGES OR FOR ANY SPECIAL, PROXIMATE,
CONSEQUENTIAL, INCIDENTAL, INDIRECT OR
EXEMPLARY DAMAGES. If Buyer transfers title to, or
leases Products sold hereunder to, or otherwise permits
or suffers use by, any third party, Buyer shall obtain from
such third party a provision affording Seller and its
subcontractors/suppliers the protection of the preceding
sentence. Any action against Seller must be brought
within 18 months after cause of action accrues.
IX. EXCUSABLE DELAYS
A. Seller shall not be liable for delays in delivery or failure
to perform due directly or indirectly to causes beyond
Seller's reasonable control including but not limited to:

MAN.270SF.REVB.102018 Page 18 of 18
acts of God; war; terrorism; civil commotion; riots;
embargoes; government regulations, orders, instructions
or priorities; port congestion; acts of or failure to act on
the part of Buyer or its agents/employees; fires; floods;
sabotage; nuclear incidents; earthquakes; storms;
epidemics; strikes; lockouts or other labor difficulties;
shortages of or inability to timely obtain proper labor,
materials, components, shipping space or transportation,
fuel, supplies or power at current prices; or due to
limitations imposed by the extent of availability of Seller’s
normal manufacturing facilities.
B. If a delay excused per the above extends for more than
90 days and the parties have not agreed upon a revised
basis for continuing providing Products/Services at the
end of the delay, including adjustment of the price, then
either party (except where delay is caused by Buyer, in
which event only Seller) upon thirty (30) days’ notice may
terminate the Order with respect to the unexecuted
portion of the Products/Services, whereupon Buyer shall
promptly pay Seller its reasonable termination charges
upon submission of Seller's invoices thereof.
X. SOFTWARE/TECHNICAL/PROPRIETARY
INFORMATION
A. Buyer shall not acquire any rights to any software
which may be delivered with Products, except as granted
in Seller’s standard software license. Any software
license granted in connection with Products shall be an
interim license, which may be withdrawn, pending
payment for Products in full.
B. The purchase of Products shall not include any right to
supply of technical information such as drawings or
specifications.
C. Proprietary information, including drawings,
documents, technical data, reports, software, designs,
inventions and other technical information supplied by
Seller in connection herewith (hereinafter called "Data"),
shall remain Seller's sole property and shall be held in
confidence by Buyer. Data shall not be reproduced, used
or disclosed to others by Buyer without Seller’s prior
written consent. Upon completion of Order, Buyer shall
promptly return all Data to Seller together with all copies
or reprints thereof then in Buyer's possession or control,
and Buyer shall thereafter make no future use, either
directly or indirectly, of any Data or any information
derived therefrom without Seller's prior written consent.
The foregoing shall in no way obligate Seller to provide
or supply Data.
XI. DIES, TOOLS, PATTERNS
Seller’s charges for dies, molds, patterns and the like
represent the Buyer’s proportionate cost thereof, it being
expressly understood that they remain the property of
Seller. Modifications made to dies, molds, patterns and
the like in order to manufacture Products shall be at the
discretion of Seller.
XII. GENERAL
A. The rights and obligations of the Buyer and Seller
hereunder shall be governed in all respects by the law of
the Commonwealth of Pennsylvania, U.S.A. The
exclusive forum for adjudication of any disputes shall be
the federal or state courts of the Commonwealth of
Pennsylvania, and Buyer/Seller hereby consent to
personal jurisdiction and venue in such courts in any
proceeding. The United Nations Convention on the
International Sale of Goods shall not apply.
B. These Terms and Conditions of Sale together with any
other terms specifically agreed to in writing by Seller
constitute the entire agreement between Buyer and
Seller and supersede any prior or contemporaneous
representations, agreements, proposals, warranties, or
understandings, oral or written, express or implied. No
waiver, modification, amendment, rescission or other
change to these Terms and Conditions of Sale shall be
binding unless specifically agreed to in writing by an
authorized representative of Seller.
C. The invalidity, of any part hereof shall not affect the
validity of the remainder. The failure of Seller to assert
any right at any time hereunder shall not prevent Seller's
subsequent assertion of the same or different rights.
D. Buyer may not assign this contract without the prior
written approval of the Seller.
XIII. PROHIBITION FOR HAZARDOUS USE
Products sold hereunder are not intended for application
in, and shall not be used by Buyer in construction or
application of a nuclear installation or in connection with
use or handling of nuclear material or for any hazardous
activity or critical application, where failure of a single
component could cause substantial harm to persons or
property, unless Products have been specifically
approved for such activity or application. Seller disclaims
all liability for loss or damage resulting from such
unauthorized use and Buyer shall defend, hold harmless
and indemnify Seller against any such liability, whether
arising under breach of contract, warranty, tort
(regardless of the degree of fault or negligence), strict
liability or otherwise. Where Seller approves the
application of the Products in a nuclear facility, the Buyer
shall, before such use or provision, arrange for insurance
or governmental indemnity protecting the Seller against
liability and hereby releases and agrees to indemnify the
Seller and its suppliers for any nuclear damage, including
loss of use, in any manner arising out of a nuclear
incident, whether alleged to be due, in whole or in part to
the negligence or otherwise of the Seller or its suppliers.
XIV. STATUTORY REQUIREMENTS
Seller reserves the right to make any changes in the
general specifications of the Products which are required
for the Products to conform to any statutory requirement.
XV. GOVERNMENT CONTRACTS
Only Federal Acquisition Regulation (“FAR”) supplement
clauses expressly accepted in writing by Seller shall be
included or incorporated by reference herein. Seller shall
not be bound by and makes no representation of
compliance with any FAR or FAR supplement clauses
that Seller shall not have expressly accepted in writing
Table of contents
Other Universal Analyzers Measuring Instrument manuals
Popular Measuring Instrument manuals by other brands

ChoiceMMed
ChoiceMMed MD300W11 instruction manual

Endress+Hauser
Endress+Hauser RID14 operating instructions
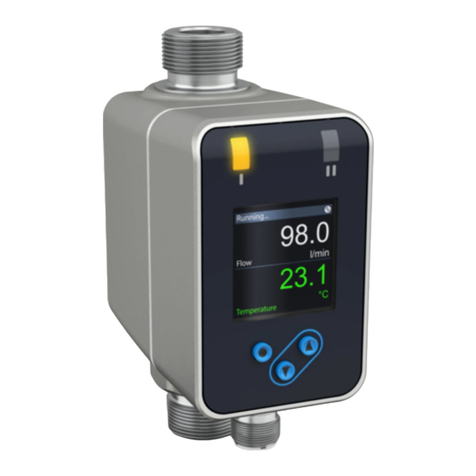
KROHNE
KROHNE AF-E 400 Handbook
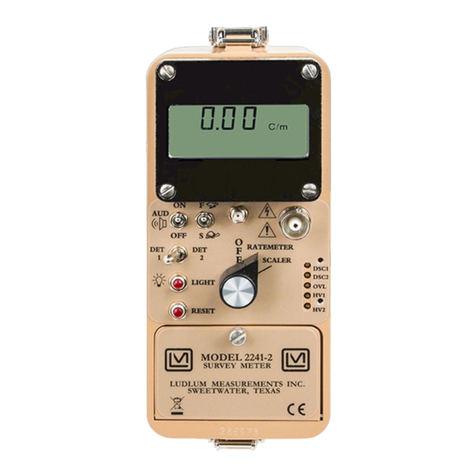
Ludlum Measurements
Ludlum Measurements 2241-2RK manual

Magnetrol
Magnetrol THERMATEL TG1 Installation and operating manual
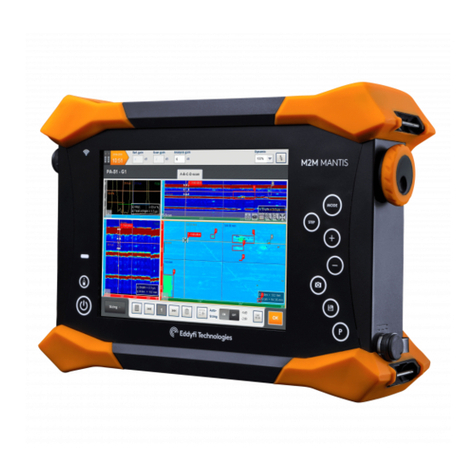
Eddyfi Technologies
Eddyfi Technologies M2M MANTIS Technical documentation