Uno International Stepper Control Board User manual

BOXER®PUMPS
uno.
Uno International Ltd.
20 Belsize Avenue
London NW3 4AU/England
Co Reg No 4694961
VAT No. 858 3837 74
Uno International Ltd.
Stepper Control Board Manual 1/21
Stepper Control Board
Manual
ISS 8
June 2013
USA
Clark Solutions
10 Brent Drive
Hudson, MA 01749
Tel: 978-568-3400

uno.
Uno International Ltd.
Stepper Control Board Manual 2/21
Table of contents
1. General description.....................................................................................................3
2. Required hardware.....................................................................................................3
3. Connection between motor and controll board ...........................................................3
4. Software installation....................................................................................................4
5. Hardware installation..................................................................................................4
6. Software explanation..................................................................................................5
7. Practical tips .............................................................................................................14
8. Daisy chaining pumps...............................................................................................15
9. Warranty...................................................................................................................21

uno.
Uno International Ltd.
Stepper Control Board Manual 3/21
1. General description
The Controlled Stepper Driver (CSD) a flexible and powerful controller for the accurate dispense. It is provided
as means to drive one or more of the following pump models:
Boxer 3500/3600, Boxer 9600 or Unoverse 6100/6500.
Each pump controlled using the CSD has to have it's own CSD board and a power supply.
2. Required hardware
Apart of the control board you will require the following hardware:
1. Power supply unit (PSU) 24V 2.5A+
2. USB cable A to B
3. PC with Windows XP, Vista or Windows 7 installed, .NET platform 2.0 minimum.
3. Connection between motor and control board
The CSD board requires three connections to run the pump:
1. Power in 24V 2.5A 2.1mm pin
2. USB cable A to B
3. 4 motor poles via Molex 0.1" terminal connector
4. 3 Opto poles(optional - only if homing is required) via Molex 0.1" terminal connector
Mains jack
24V 2.5A
+ @ centre
Daisy header
USB socket
Power LED
Motor header
Homing Opto header
Panic
button
socket
Motor address
DIP block
Fan header

uno.
Uno International Ltd.
Stepper Control Board Manual 4/21
Motor wires layout:
1 - Black - Phase A
2 - Green - Phase A-
3 - Red - Phase B
4 - Blue - Phase B-
Opto wires layout:
Red: LED A +
Black: LED K -
White: Transistor Collector
Green: Transistor Emitter
4. Software installation
Download and locate the folder called InsallCD. This folder contains a folder called Installer. In this folder you
will find the setup.exe file . Using this file install the BoxerPumps Controller application onto your computer.
Plug the PSU plug into the controller board and make sure mains power to the power supply in On.
5. Hardware installation
1. Connect the stepper motor to the control board.
2. Link the board with your PC using the A to B USB cable.
3. Power the board using a good quality 2.5A switch mode PSU. The yellow LED on the control board
should come on as soon as power is supplied to the board.
Motor connection
Homing Opto connection
5V output for cooling fan
DIP switches

uno.
Uno International Ltd.
Stepper Control Board Manual 5/21
Double click on the BoxerPumps Controller to launch the application.
The software will prompt you to open an existing controller program. Controller programs have the extension
*.bpj. If no such program exists your computer press "Cancel". A new dialogue box called New Project will
prompt you to save a a new project under your chosen name. Substitute "New Project" with a name and in a
place of your choice and press "Save".
6. Software explanation
Press the round Green Connect button to create a link between the PC and the control board.
There are 2 main interface boxes:
1. Motors (top) - for motor configuration
2. Project (bottom)- for run configuration
The STOP button is a panic button. Whenever you want to terminate a movement of a motor, press this
button. The PCB has also a socket for a panic stop actuator.
1. Motor configuration
1. Right click "Motors" and choose "Configure". A new dialogue box pops up.
2. Press "Add" to add a new motor
3. Choose a snappy description for the motor (e.g. "Reagent 1") and insert it in the Description of the
motor.
4. If you are about to calibrate a pump then choose Steps. Otherwise assign the type of motor - whether a
pump, linear drive or a rotary drive
5. Set drive current: Small motors such as the one used Boxer 9600 run better on much lower current than
the large steppers which will run better at full current. If you are running the controller for example from
a 1.5A power supply, there is little point in entering 2500mA in the drive current box as the motor can
get a max of 1500mA.
6. Stepping: Full Stepping or Half Stepping. Choose half stepping if you intend to run the motor in low
speeds i.e. below 1000 steps/sec (below 300rpm).
7. For accurate operation always apply a hold current. A hold current of 400mA

uno.
Uno International Ltd.
Stepper Control Board Manual 6/21
8. If you are operating more than one motor, run through the same procedure and configure motors for
other addresses on the board.
2. Gravimetric pump calibration procedure
1. Calibrate the pump using the media you are intending to use the pump for.
2. Use precision scales with tare function.
3. Initiate new chain by pressing the New Chain (Ctrl+N) on the project box.
4. Drag and drop the motor into the chain box.

uno.
Uno International Ltd.
Stepper Control Board Manual 7/21
5. Depends the side where you reservoir is choose either move forward or move backward.
6. Put the pump dispense side into a receiving vessel
7. Prime the pump: Put both tube sides - suction + dispense into the reagent reservoir. Right click your
chosen to prime and choose "Run Continuously". Press the stop button as soon as you see that the
tubes are primes throughout their entire length and void of any air bubbles.
8. Enter 2000 steps which represents 10 full motor revolutions

uno.
Uno International Ltd.
Stepper Control Board Manual 8/21
9. Set rate - a speed which is typical in your application. As any common stepper motor has 200 steps per
revolution, 1000 steps/second means 5 full revolutions per second or 300rpm (1000/200*60).
10. Choose the motor from the chain list and press the Green "Run" button. This will rotate the motor 10 full
revolution (=2000 steps).
11. Carry out 10 dispenses and calculate the mean value.
12. Go back to Motor Configuration of the motor you are calibrating and choose "Pump" as description of
the motor.
13. Enter the mean value you calculated as µl/revolution.
3. Changing the configuration of the motor
1. Now that the pump is calibrated you can reconfigure the motor from a motor counting steps to a pump
which dispenses in ml.
2. Highlight the motor to reconfigure from the Motors list and choose Motors/Configure from the drop down
menu.

uno.
Uno International Ltd.
Stepper Control Board Manual 9/21
3. Specify the type of motor whether Pump, Linear Drive or Rotary Drive. The parameters associated with
your chosen motor type will be updated automatically such as µl/revolution if you chose Pump.
4. Enter the value you established during the calibration process whether µl/revolution, mm/step or
steps/revolution and press OK.
5. From now on, whenever you wish to run the pump, you can enter the volume you would like to
dispense, the speed of dispense and the direction - whether forward or backward (dispense or
aspirate).
6. Save your settings.

uno.
Uno International Ltd.
Stepper Control Board Manual 10/21
4. Working with chains
1. You can run a single motor at any number of intervals, at any interval duration as many time as you
wish.
2. Right Click in the Chain box and choose "Add Repeat", "Add Delay" or "Add Backstep". Each time you
add one of these functions it will be added to the Chain box.
3. Drag the function you requested to the position you want and specify each function separately. You can
delete any of the functions by right-click and choosing Delete.
You can specify:
Repeat: Number of repeats
Delay: Period of delay between actions in seconds
Backstep: Volume of Backstep, it's speed and direction.
Backstep is a useful function in order to aspirate back into the dispense tip any partial droplets which might be
formed after a dispense.
You can drag the functions into any position in the chain tree, drag the motor from the motors box into the chain
box in order to achieve any motor variation you require.
An operation for a single motor function can look like this:

uno.
Uno International Ltd.
Stepper Control Board Manual 11/21
5. Adding repeat function to a particular set of commands
If you wish to repeat specific set commands do the following:
Right click in the chain pane and choose "Add Repeat"
Specify the number of repeats
drag the commands you wish to repeat onto the "Repeat" command
Example
You have written the following commands:
You would like to repeat 5 times the addition of die to the cell.
Right click and choose "Add Repeat".
Drag the "Add die to cell" line and the backstep onto the "Add Repeat"

uno.
Uno International Ltd.
Stepper Control Board Manual 12/21
Now drag the sub menu into a position in the protocol where you want these actions to take place.

uno.
Uno International Ltd.
Stepper Control Board Manual 13/21
6. Scheduling
You can choose to run any chain at any intervals - as long as the computer is on, the Boxer Pump Controller
program is running and the pump is powered up.
Right click on the New Project and choose Scheduling or from the File drop down menu choose Scheduling.
Choose the chain you would like to schedule.
Define the start time and the intervals in hours and minutes you would like the chain to run.
Press Add to add the chain to your scheduling.
7. Saving your settings
You can quickly generate many protocols from one master protocol by changing various functions, their order or
value, and save into any position on your hard drive. Use the "Save As" function to save the modified protocols.

uno.
Uno International Ltd.
Stepper Control Board Manual 14/21
7. Practical tips
Run any new tubing in. New tubing is very stiff and requires a lot of torque from the motor. Once the tubing has
been "softened" you will be able to run at much higher speeds without problems. We suggest 100 revolutions to
run a tube in.
Adjust the run current to the speed of rotor. If you want to run the pump very slowly, for example at the min
speed of 50 steps/sec, reduce the Run Current to 500mA. Too much current causes the motor to shudder and
the processor to overheat. In most applications you will not need a higher supply current than 1500mA. You can
set a different Run Current for each protocol you run.
When a stepper motor slips, a high pitch noise can be heard and the motor stalls. Any of the variants can cause
a motor to slip. The optimal settings of the acceleration, the initial speed and the final speed are all crucial for
the best motor run.
Setting a high speed with too high initial speed will cause the motor to slip.
In very short rotations, for example 100 steps, the motor might not reach the requested speed.

uno.
Uno International Ltd.
Stepper Control Board Manual 15/21
8. Daisy chaining pumps
You can daisy chain up to eight motors of various types and control them all from a single PC. Each pump must
have its own control board and a power supply. You can daisy chain the power supplies for all boards in an
assembly. You can run any number of different motor types sequentially. You can not run the motors
simultaneously.
8.1 Daisy chaining cable
In order to enable the software to talk to all pumps, you need a Daisy Chain Cable to run from each pump to the
next.
A daisy chain cable for connecting two pumps consists of 2 female Molex connectors and a cable and can look
like this:
A daisy chain cable for connecting many motors could look like this:
These cables are available from Uno International Ltd.
Part No. 6000.553
Uno Part No. 6000.554

uno.
Uno International Ltd.
Stepper Control Board Manual 16/21
8.2 Connecting the pumps
The first pump's PCB must be connected via the USB cable to the computer.
Each pump has to have a power supply.
A daisy cable must connect the pumps together.
Here is a typical installation of 2 daisy chained pumps:
USB cable to the PC
24V DC 2.5A Power supply
cable
24V DC 2.5A Power supply
cable
Daisy chain cable 6000.553
Motor connection
Opto connection
Motor connection
Opto connection
Remote STOP Panic Button

uno.
Uno International Ltd.
Stepper Control Board Manual 17/21
8.3 Addressing the pumps
In order for the computer software to address the motor you wish to communicate with, each of the boards has
to have a unique address.
The first motor which is connected to the PC via the USB cable must be set on the controller software as no. 1.
The DIP switch setting on this pump must be as per following picture. This is the master motor.
Picture shows setting for Master:
DIP switch address setting is as Binary code and is used to daisy chain boards:
1 –Master or Slave ON for Master, address must be 0
2 –USB or RS232 ON for USB control
3 –not used Leave OFF
4 –not used Leave OFF
5 –Address A Binary 1
6 –Address B Binary 2
7 –Address C Binary 4
8 –Address D Binary 8

uno.
Uno International Ltd.
Stepper Control Board Manual 18/21
8.4 Writing protocols for multiple pumps
The procedure of writing the protocols for multiple pumps is identical to writing the protocol for a single pump.
The only difference is that now as part of each protocol you have to specify which of the motors should carry out
the task.
Motor 1 = Master
Motor 2 = Slave
Motor 3= Slave 3
and so on….
1. Configure a new motor and set it's address to the desired position.
2. Go through the calibration procedure as described in section 6.2.
3. After calibration you can assign the new motor as a pump, linear drive or a rotary drive as you did in the
first motor setting.

uno.
Uno International Ltd.
Stepper Control Board Manual 19/21
A simple protocol made from 4 different motors could look like this:
You can add all the sub functions as done previously and a finished protocol for 4 motors could look like this:

uno.
Uno International Ltd.
Stepper Control Board Manual 20/21
Once this is done you can add many chains in series.
Protocol 1
Protocol 2
Protocol 4
Protocol 2
Protocol 7
Protocol 3
Protocol 2
Protocol 4
Protocol 7
Protocol 3
Protocol 2
Protocol 2
Protocol 4
Protocol 7
Protocol 3
Protocol 2
Protocol 1
Protocol 1
Table of contents
Popular Controllers manuals by other brands
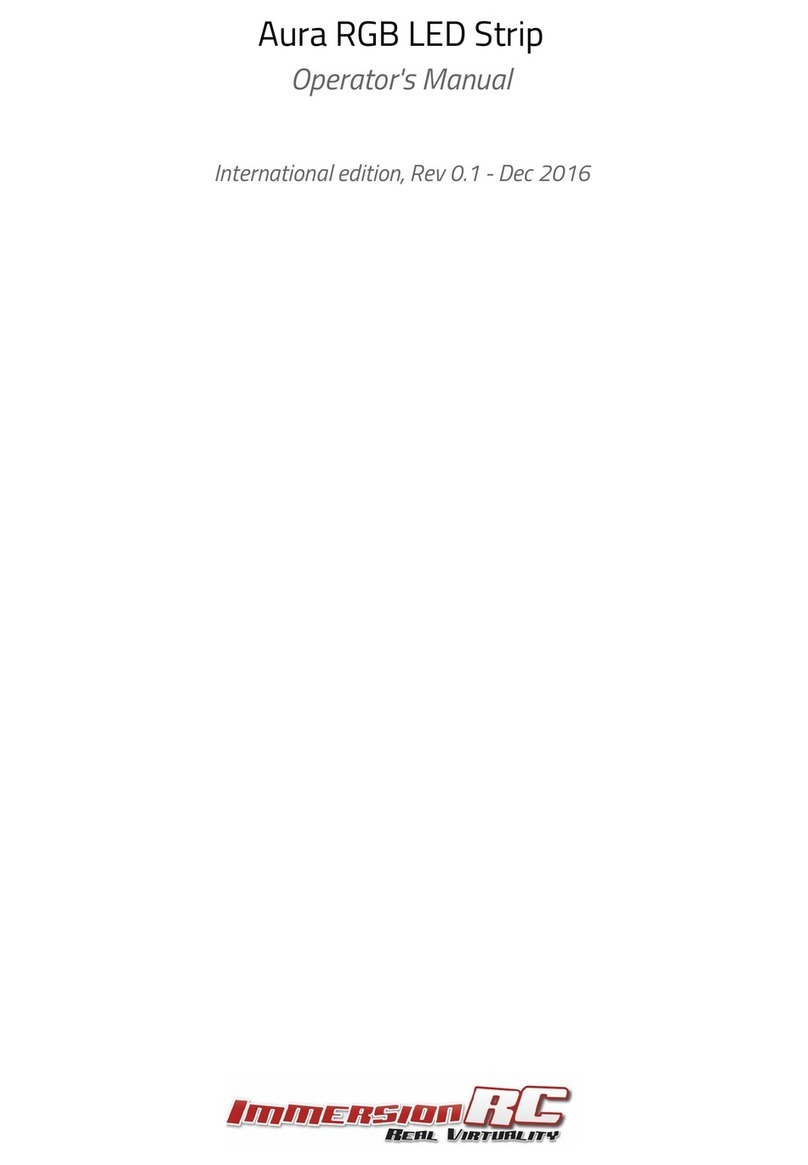
ImmersionRC
ImmersionRC Aura RGB LED Strip Operator's manual
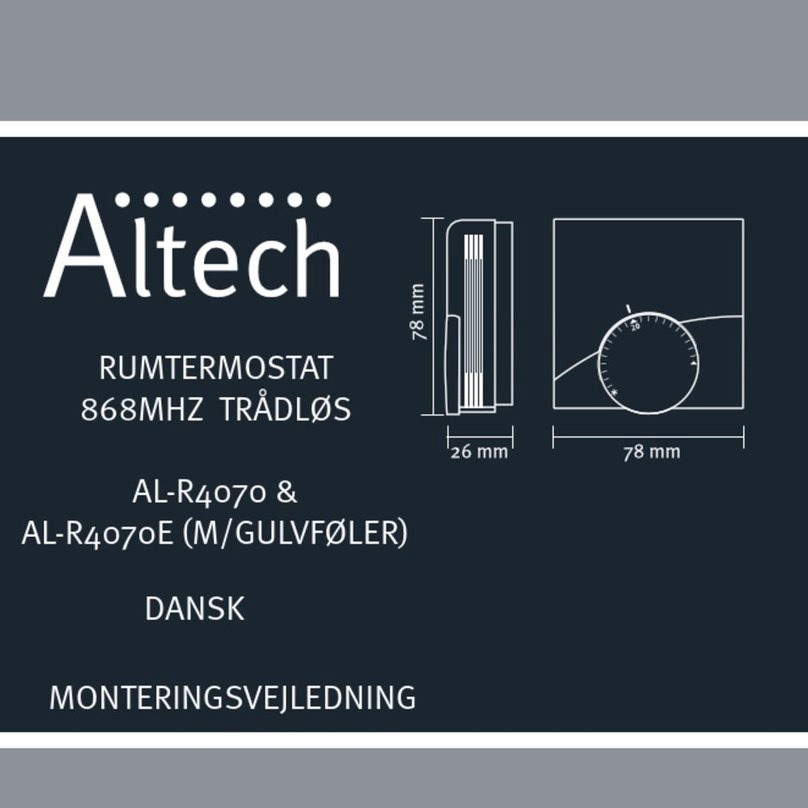
AL Tech
AL Tech AL-R4070 manual
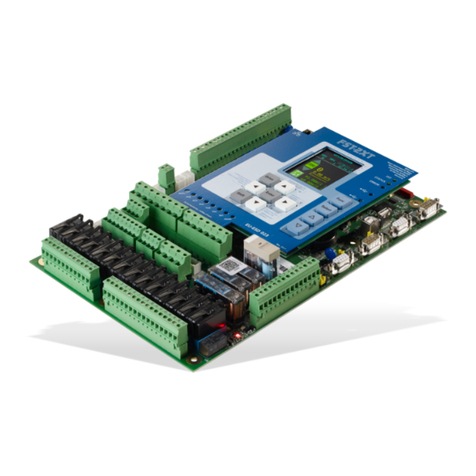
New lift
New lift FST-2XT MRL Installation & commissioning
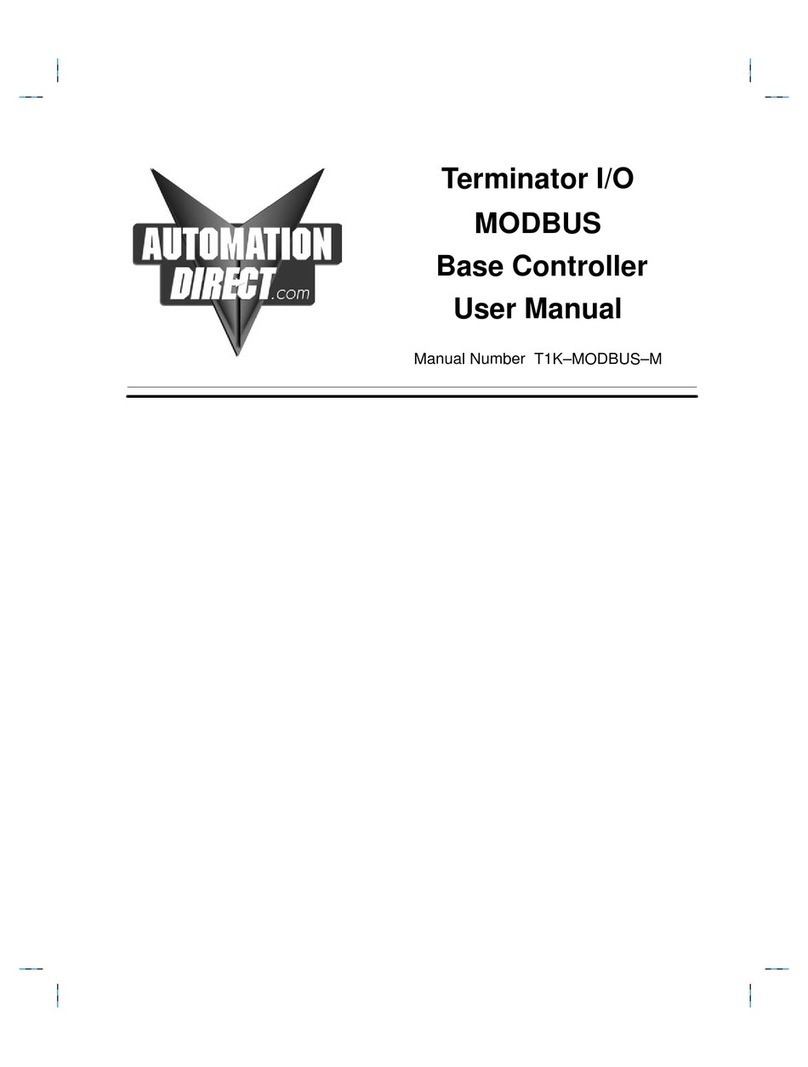
AutomationDirect
AutomationDirect T1K-MODBUS-M user manual
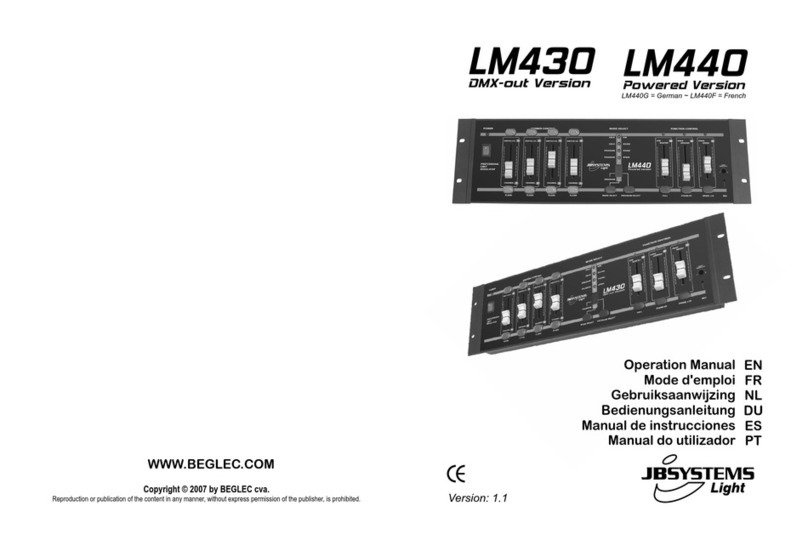
JB Systems Light
JB Systems Light LM430 Operation manual
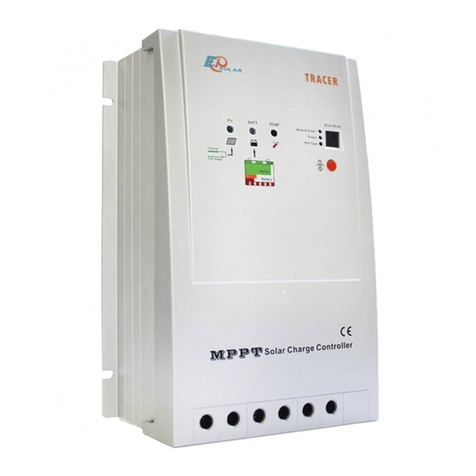
EP Solar
EP Solar Tracer-4210RN instruction manual