Vaporless ARM-4073 User manual

Quality Petroleum Equipment
Solutions for Over 30 Years
ARM-4073
Automatic Repressure Module
Installation & Operation Manual
Rev. 05/08/2021

2
Vaporless Manufacturing, Inc.
8700 East Long Mesa Drive, Prescott Valley, Arizona 86314
800-367-0185 928-775-5191 Fax: 928-775-5309
Email: sales@vaporless.com Web Site: www.vaporless.com
SYSTEM CONCEPT:
When not transferring fuel, the pressure in the closed piping system of a fueling facility may fall
due to thermal contraction of the fuel within the line. This condition may create problems during
future dispensing operations. The ARM-4073 Automatic Repressure Module ensures line pressure
by periodically starting the turbine pump to repressurize the line.
Figure 1 illustrates the wiring diagram of the system’s control circuits. This diagram shows the
connection of the circuits but should not be interpreted as illustrating the relative size and location
of the components (See page 10).
OPERATION:
The ARM-4073 Automatic Repressure Module contains two timer circuits which operate in
sequence. The first determines the pump running time. The second determines the delay time ⎯
the amount of time between pump operations. The following statements outline the operation of
the ARM-4073.
1. With power applied, the module is active and performs its timing functions. The pump timer
is the first to operate following the application of power. Following the completion of the pump
cycle, the delay timer determines the elapsed time to the next pump cycle.
2. There is a small switch module located in the center of the circuit board. This module contains
five miniature switches which are used to program the timers. Refer to Table 1 for the switch
setting associated with the pump timer. Refer to Table 2 for the switch settings associated with
the delay timer (See page 9).
3. The timers operate asynchronously in relationship to dispensing authorization signals. That is,
the timing sequence does not monitor dispensing operations and therefore the module may
energize the pump contactor during a dispensing operation. This will not create a conflict with
dispensing.
CONTROLLER LABELING:
The following information is provided on the control unit’s label:
•Controller name, model number and serial number
•Voltage, current and load specifications
•Manufacturer’s name and telephone number
The installer should be familiar with the information presented on the product label.

3
Vaporless Manufacturing, Inc.
8700 East Long Mesa Drive, Prescott Valley, Arizona 86314
800-367-0185 928-775-5191 Fax: 928-775-5309
Email: sales@vaporless.com Web Site: www.vaporless.com
ENCLOSURE & MOUNTING:
The module is designed for operation in a non-hazardous, indoor environment such as an
equipment room. Holes are provided in the base for mounting the unit. Two holes are provided for
the connection of ½” conduit fittings. A hole plug is provided for closing an un-used conduit hole.
ELECTRICAL CONNECTIONS:
The best way to understand the operation of the ARM-4073 is to look at the device as though it
were an additional dispenser being installed at the site. All dispensers typically have a 120 VAC
power source being supplied to them. The ARM-4073 MUST be supplied with the same phase
power as the dispenser(s). After determining the 120 VAC power source of the dispensers, land
the 120 VAC (hot) on terminal L1 of the ARM-4073 and the (neutral) on terminal L2 of the ARM-
4073. Next, make a small jumper wire (minimum 16 AWG wire) that will land on terminals L1
and K1.
All dispensers have an authorization signal output that goes to some device that engages the turbine
pump. In some instances, this signal may go directly to the A1 terminal on the pump contactor
coil. That said, look at terminal K2 on the ARM-4073 as though it were another authorization
signal output from a dispenser and connect terminal K2 to where all the other authorization output
signal wires terminate. It makes no difference whether the turbine(s) at your site are single phase
or three phase. The ARM-4073 only controls the coil on the turbine contactor, just as any other
authorization signal would. The vast majority of installations for the ARM-4073 can be described
with Figure 1 located on page 10 of this manual. If you feel that your site is unique in some way,
please do not hesitate to consult with VMI for technical support.
1. Authorization signals are generally powered from a 120 VAC source. Because this signal is
derived from one of the phases of the main STP power source, there should be zero volts
between the signal side of the contactor’s coil when it is powered and one phase of the power
mains. Using a voltmeter, determine which phase exhibits this condition.
Though unlikely, please note that the source of the authorization control signal is not always
apparent. It could be derived from a source that does not exhibit the characteristics noted in the
previous paragraph. Note: It is the responsibility of the installer to determine the appropriate
signal (phase) supplied to the ARM-4073. Selecting the incorrect phase will likely cause
equipment damage and/or injury to the installer.
2. Connect terminal L1 on the ARM to 120 VAC dispenser power, and L2 terminal to neutral.
3. Connect terminal K2 on the ARM to the authorization signal side of the contactor’s coil or
other device that relays a signal to the turbine pump contactor (i.e., DHI, ATG, etc.).
4. Assuming you are powering the ARM-4073 with the same 120 VAC phase as the authorization
signal, place a jumper wire between terminals L1 & K1 (16 AWG minimum wire size). Please
see Figure 1 (wiring diagram) on page 10 of this document.

4
Vaporless Manufacturing, Inc.
8700 East Long Mesa Drive, Prescott Valley, Arizona 86314
800-367-0185 928-775-5191 Fax: 928-775-5309
Email: sales@vaporless.com Web Site: www.vaporless.com
EMERGENCY SHUT-OFF:
When installing new equipment, it is important to maintain the integrity of the emergency shut-off
system. It is the responsibility of the installer to develop an installation that provides for proper
emergency shut-off function.
•If the shut-off system breaks power at the mains, voltage will be removed from both the pump
and the ARM-4073. This type of system will not be affected by installation of the module as
shown in Figure 1.
•If the shut-off only breaks the authorization signal, voltage will not be removed from either the
pump or the ARM-4073. The repressure sequence will not be interrupted. This will result in
unexpected pump operation. To provide a proper shut-off function, the voltage to terminals
L1/K1 on the ARM-4073 must be from a source which is interrupted by the emergency shut-
off system.
POWER ON-OFF SWITCH:
At certain times of the year when the thermal contraction of fuel is not interfering with proper
operation of the distribution system it may be appropriate to disable the repressure module. A
power toggle switch is provided for this purpose. The switch is located next to the L1-L2 terminal
block on the module’s circuit board.
With the lever positioned toward the terminal block, power is applied to the module (on position).
With the lever positioned away from the terminal block, power is removed from the module (off
position). Care should be exercised when operating the switch as voltage may be present on the
L1-L2 terminals.
MEASURING SYSTEM BLEED-BACK:
When under pressure all closed piping systems exhibit an elastic response that will force fuel from
the line if an opening is provided. The volume of fuel forced from the line is dependent on several
factors and must be measured for each installation. The selection of a delay time from Table 2
(page 9) is dependent upon this volume.
The following statements outline a procedure for measuring the expelled volume which is referred
to as bleed-back. This procedure assumes the use of the Vaporless Model LDT-890 Leak Detector
Tester to perform this task.
The following procedure assumes no knowledge of the operation of the LDT-890 and therefore
details each step of the process. The operation manual supplied with the LDT-890 provides ad-
ditional information and should be consulted by the technician.
1. Power Off
Turn off the circuit breaker providing power to the product under test. This is done to prevent
the accidental starting of the turbine while the line is open in the following steps.
Turn off the power switch on the ARM-4073. The location and operation of this switch is
described under Power On-Off Switch. The unit is turned off to prevent unexpected starting of
the turbine while the following procedure is being conducted.

5
Vaporless Manufacturing, Inc.
8700 East Long Mesa Drive, Prescott Valley, Arizona 86314
800-367-0185 928-775-5191 Fax: 928-775-5309
Email: sales@vaporless.com Web Site: www.vaporless.com
2. Install LDT-890 Test Unit
Select the dispenser at the highest point of the delivery system. If there is no elevation
difference, select the dispenser farthest from the turbine.
Caution: Eye protection required during the calibration process.
3. Carefully remove the plug from the test port on the impact valve. There should still be pressure
in the line.
4. Install the 18” whip hose supplied with the test unit. The application of thread sealing
compound is recommended.
5. Connect the quick disconnect coupler on the hose from the test unit to the whip hose.
6. Set the test unit selector to the PRESSURE STEP TEST position.
7. Power On
Turn on the circuit breaker for the product under test.
8. System Purge
Authorize the dispenser. The turbine should start running. On the right-hand pressure gauge of
the LDT-890, watch for the turbine to achieve operating pressure.
9. Check all connections for leaks. Correct any fault conditions.
10. With the large beaker (1000 ml) under the LDT-890 discharge hose, set the selector to the
DISPENSER NOZZLE position. Purge the tester of air by allowing 800 to 1000 ml of fuel to flow
into the beaker. After purging the LDT-890, set the selector to the PRESSURE STEP TEST position.
11. Purge the dispenser line by running several gallons of fuel into an approved safety container.
12. Bleed-Back Measurement
Remove the dispenser authorization. The turbine should stop running. Unless there are fault
conditions such as a leak or significant thermal contraction, the line pressure should stabilize
at 20 –30 PSI for fractional horsepower turbines, or 20 –40 PSI for high-capacity or high-
pressure turbines.
13. With the large beaker under the LDT-890 discharge hose, carefully move the selector to the
DISPENSER NOZZLE position. Fuel will begin to flow into the beaker. When fuel stops flowing,
return the selector to the PRESSURE STEP TESTposition.
14. Note the volume of fuel collected. This volume is referred to as the bleed-back measurement.
Repeat the collection process several times to confirm the bleed-back volume.
Depending on the measured volume, the use of the small (250 ml) beaker may provide more
accurate measurements. The averaging of several consecutive samples is necessary to accurately
determine the bleed-back volume. It is recommended that a record be made of these values and
stored in a convenient location for future reference.

6
Vaporless Manufacturing, Inc.
8700 East Long Mesa Drive, Prescott Valley, Arizona 86314
800-367-0185 928-775-5191 Fax: 928-775-5309
Email: sales@vaporless.com Web Site: www.vaporless.com
15. Delay Timer Programming
Referring to Table 2, select the volume in the left-hand column which first exceeds the
measured bleed-back. The next four columns indicate the required switch settings. The right-
most column indicates the approximate time delay between pump cycles.
16. The Time Delays shown in Table 2 are the minimum values needed to allow the leak detector
to reset to its leak sense position. Longer delay times are acceptable, however, these longer
delay times will increase the frequency of false alarms due to thermal contraction.
17. Pump Timer Programming
Referring to Table 1, select the value in the right-hand column (30 or 70 seconds) which
provides enough time for the turbine to repressurize the line from a zero pressure condition.
The column to the left indicates the required switch setting for the selected operating time.
Under normal conditions 30 second setting should be selected. If the line exhibits excessive
bleed-back or extreme thermal contraction, then the 70 second setting may be selected.
18. Perform Leak Detector 3 GPH Test
This completes the bleed-back measurement procedure and set-up of the ARM Repressure
Module. A 3 GPH test should now be completed.
LEAK DETECTOR TEST AT 3 GPH:
Whether a new installation or the retrofit of an existing installation using VMI Leak Detectors, a
leak test should be performed. This is done to ensure that the VMI Leak Detector is operating
normally and that the selected ARM delay time is long enough for the VMI Leak Detector to return
to its reset position.
The following statements outline a procedure for testing the operation of the VMI Leak Detector.
This procedure assumes the use of the Vaporless Model LDT-890 Leak Detector Tester to perform
this task.
The following procedure assumes no knowledge of the operation of the LDT-890 and therefore
details each step of the process. The operation manual supplied with the LDT-890 provides ad-
ditional information and should be consulted by the technician.
1. Install LDT-890 Test Unit
If the LDT-890 has not been installed, follow steps 1 through 11 in the procedure outlined
under Measuring System Bleed-Back.
2. Leak Calibration
With the large beaker (1000 ml) under the LDT-890 discharge hose, set the selector to the
CALIBRATE GPH position. Fuel will begin to flow into the beaker.
3. The object of the next step is to calibrate the fuel flow from the test unit to the rate of 3 gallons
per hour at 10 psi pressure at the discharge. This specification meets the requirements of the
EPA regarding leak rate testing.

7
Vaporless Manufacturing, Inc.
8700 East Long Mesa Drive, Prescott Valley, Arizona 86314
800-367-0185 928-775-5191 Fax: 928-775-5309
Email: sales@vaporless.com Web Site: www.vaporless.com
4. The procedure is as follows: Adjust the fuel flow using the left-hand knob labeled CALIBRATE
ORIFICE. Adjust the pressure on the left-hand pressure gauge to 10 psi using the right-hand
knob labeled CALIBRATE PRESSURE.
Turn the ORIFICE knob counterclockwise to increase flow and clockwise to decrease flow.
Turn the PRESSURE knob counterclockwise to reduce pressure and clockwise to increase
pressure.
First adjust the flow using the ORIFICE knob and then adjust the gauge pressure using the
PRESSURE knob. It is important to perform the procedure in this order.
5. Using the small beaker (250 ml) collect a sample of fuel over a 30 second interval. The flow
is properly adjusted when 95 ml are collected in 30 seconds. This volume is equivalent to a
rate of 3 gallons per hour at 10 psi. Repeat the procedure outlined in step 4 until the correct
volume of fuel is collected in the specified time.
6. Set the selector to the PRESSURE STEP TEST position and remove the dispenser authorization.
7. Reduce Line Pressure to Zero
With the large beaker under the LDT-890 discharge hose, set the selector to the DISPENSER
NOZZLE position. Fuel will begin to flow into the beaker. After the reading on the right-hand
pressure gauge falls to zero, set the selector to the PRESSURE STEP TEST position.
8. Read Operating Pressure
Authorize the dispenser. The turbine will start running. Watch for the turbine to achieve
operating pressure as seen on the right-hand pressure gauge. Note this pressure reading and
then remove the authorization from the dispenser.
9. Reduce Line Pressure to Zero
With the large beaker under the discharge hose, set the test unit’s selector to the DISPENSER
NOZZLE position. Fuel will begin to flow into the beaker. After the reading on the right hand
pressure gauge falls to zero, set the test unit’s selector to the GPH TEST position and authorize
the dispenser.
10. 3 GPH Leak Test
With the dispenser authorized, the turbine will start running. With the selector in the GPH TEST
position a 3 GPH leak has been introduced to the system. On the right-hand pressure gauge
watch for the turbine to build pressure. If the mechanical leak detector is properly calibrated
this pressure should not reach the normal operating pressure previously observed. Note this
lower pressure value. Remove the authorization from the dispenser.
11. Reduce Line Pressure to Zero
Set the test unit’s selector to the DISPENSER NOZZLE position. Fuel will continue to flow into the
beaker. After the reading on the right-hand pressure gauge falls to zero, set the selector to the
GPH TEST position and again authorize the dispenser.

8
Vaporless Manufacturing, Inc.
8700 East Long Mesa Drive, Prescott Valley, Arizona 86314
800-367-0185 928-775-5191 Fax: 928-775-5309
Email: sales@vaporless.com Web Site: www.vaporless.com
12. Leak Test Confirmation
With the dispenser authorized, the turbine will start running. Again, note that with the selector
in the GPH TEST position a 3 GPH leak has been introduced to the system. Watch the right-hand
pressure gauge as the turbine builds pressure. The pressure should build to the value noted in
Step 10.
TECHNICAL NOTE —If the pressure indicated on the right-hand pressure gauge does not
stabilize at the lower pressure, but rather steps through to the higher normal operating value,
the leak detector has failed the leak test. Contact the factory for calibration information.
Turn the selector to the PRESSURE STEP TEST position. Following a short delay, the pressure should
step up to the value noted in Step 8. This is the indication that the mechanical leak detector has
properly transferred from its leak test position to its full flow position.
13. Auto-Repressure Test
Remove the dispenser authorization. With the large beaker under the discharge hose, set the
selector to the DISPENSER NOZZLE position. Fuel will flow into the beaker. After the reading on
the right-hand pressure gauge falls to zero, set the selector to the PRESSURE STEP TEST position.
14. Set the ARM-4073 power switch to the ONposition (refer to Power On-Off Switch). The
turbine will start running. Immediately return to the dispenser. On the right-hand pressure
gauge of the LDT-890, verify that normal operating has been achieved. Set the selector on the
LDT-890 to the GPH TEST position. This will introduce a 3 GPH leak to the system. Because
the leak detector has already stepped through to its fully open position, nothing will
change. This leak must be introduced to the system before the 30 second (or 70 second) pump
timer has completed its timing cycle.
15. At the end of the pump timing cycle, the ARM-4073 will automatically turn off the turbine.
On the right-hand pressure gauge of the LDT-890, verify that the pressure falls due to the 3
GPH leak. If the proper delay timer has been selected from Table 2, the pressure should fall to
zero before the next automatic pump cycle is started.
16. At the end of the delay timing cycle, the ARM-4073 will automatically turn on the turbine.
Pressure will begin to build but will stop at the value observed in Step 10 indicating that the
leak detector has found the 3 GPH leak. This successfully completes the ARM-4073 test.
17. Disconnect LDT-890 Test Unit
Turn off the appropriate power breaker. Turn off the ARM-4073 power switch.
18. With the large beaker under the LDT-890 discharge hose, set the selector to the DISPENSER
NOZZLE position and bleed off fuel until the reading on the right-hand pressure gauge is zero.
19. Disconnect the quick disconnect coupler attaching the test unit to the whip hose.
20. Remove the whip hose from the test port and install the original plug. The application of thread
sealing compound to the plug is recommended.

9
Vaporless Manufacturing, Inc.
8700 East Long Mesa Drive, Prescott Valley, Arizona 86314
800-367-0185 928-775-5191 Fax: 928-775-5309
Email: sales@vaporless.com Web Site: www.vaporless.com
21. Full System Operation
Turn on the power switch on the ARM-4073. Turn on the power breaker. This completes the
test procedure. The system including the ARM-4073 Automatic Repressure Module is now
fully functional and actively working to eliminate slow-flow issues.
TIMER SWITCH SETTINGS:
Table 1 ⎯Pump Timer Switch Setting
Switch Number
Pump Time
1
OFF
30 seconds
ON
70 seconds
Table 2 ⎯Delay Timer Switch Settings
Bleed-
Back
(ml)
Switch Number
Delay
Time
(minutes)
2
3
4
5
150
OFF
OFF
OFF
OFF
2 . 0
350
ON
OFF
OFF
OFF
4 .5
550
OFF
ON
OFF
OFF
7 .0
700
ON
ON
OFF
OFF
9 .5
900
OFF
OFF
ON
OFF
12 .0
1100
ON
OFF
ON
OFF
14 .5
1300
OFF
ON
ON
OFF
17 . 0
1500
ON
ON
ON
OFF
19 .5
1750
OFF
OFF
OFF
ON
22 . 0
2000
ON
OFF
OFF
ON
24 .5

10
Vaporless Manufacturing, Inc.
8700 East Long Mesa Drive, Prescott Valley, Arizona 86314
800-367-0185 928-775-5191 Fax: 928-775-5309
Email: sales@vaporless.com Web Site: www.vaporless.com
•If you have any questions or concerns after reading this manual, please contact VMI. We
are committed to customer service and the safety and satisfaction of our customers.
Manufactured by:
Vaporless Manufacturing, Inc.
Electronics Division
8700 East Long Mesa Drive
Prescott Valley, Arizona 86314
Phone: 928-775-5191
Website: www.vaporless.com
Table of contents
Popular Control Unit manuals by other brands
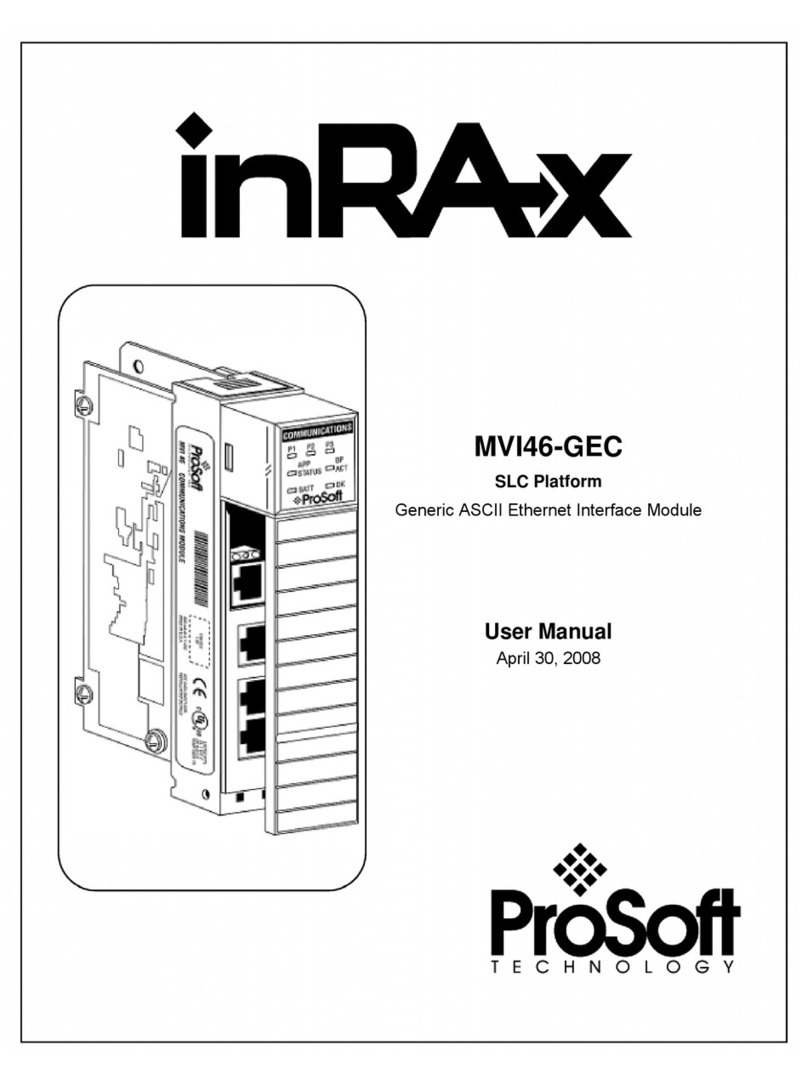
ProSoft Technology
ProSoft Technology inRAx MVI46-GEC user manual

Schmalz
Schmalz 10.02.02.02795 operating instructions
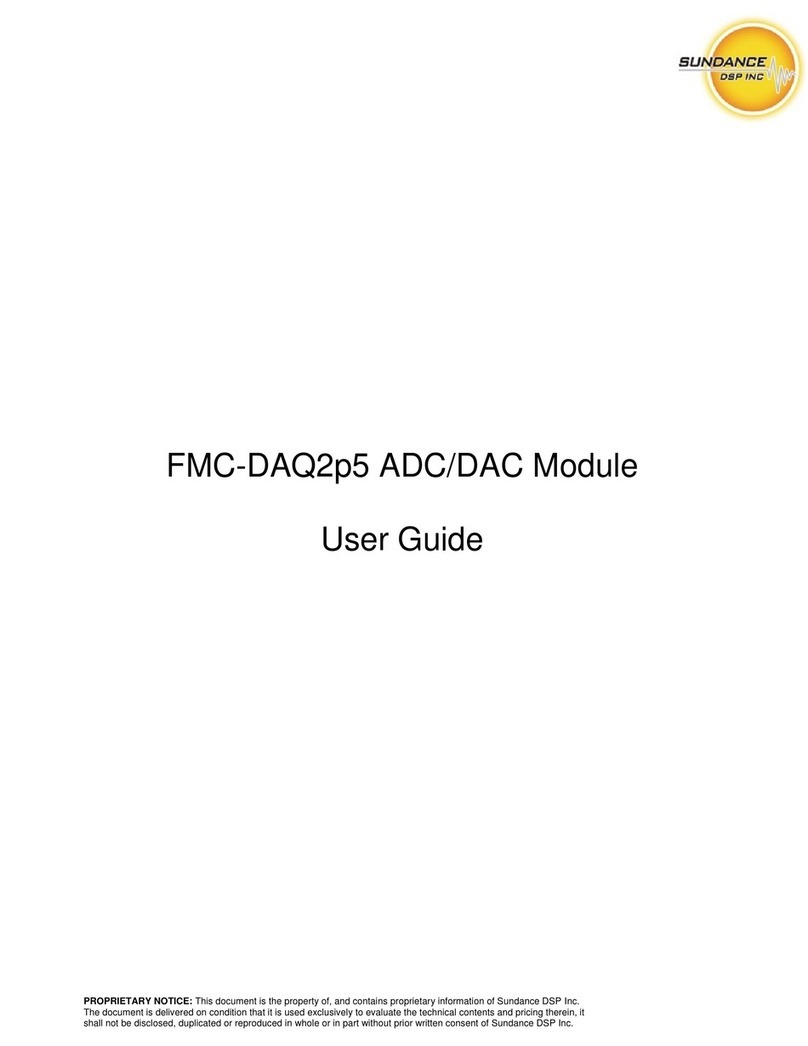
Sundance Spas
Sundance Spas FMC-DAQ2p5 user guide

Wouter Witzel
Wouter Witzel ECV user manual
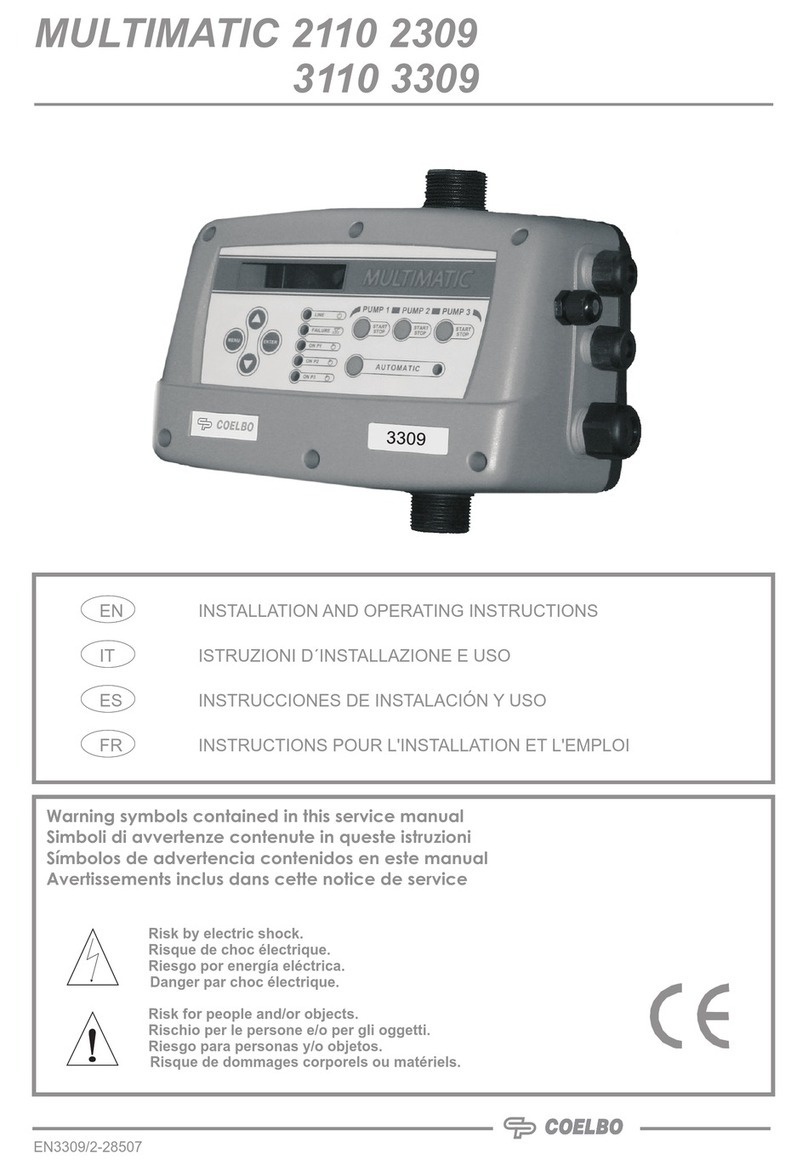
Coelbo
Coelbo MULTIMATIC 2110 Installation and operating instructions
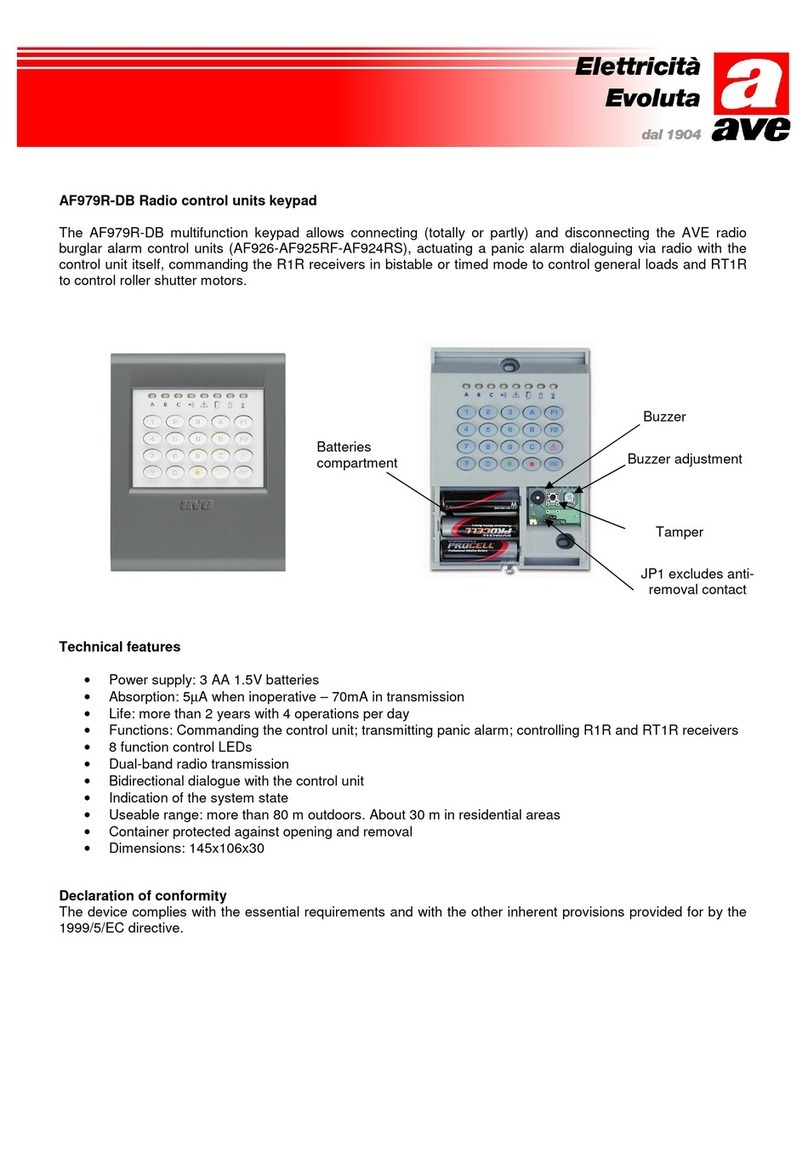
AVE
AVE AF979R-DB quick start guide