Variobot variAnt User manual

Version 230825

Safety instructions
Before building and using the robot, it is important
to read the following precautions. Please follow
them!
●Read through these instructions before you
begin, and keep them on hand while building.
●This robot kit is not a toy! Keep it out of the
reach of children! t is only for ages 14 and up.
●Do not use where small animals are loose.
●For safety reasons, never leave the robot
unattended.
●Since variAnt doesn’t have a cover, be extra
careful to keep metal objects and tools from
causing a short circuit.
●Caution: Do not touch inside the power unit!
●Caution: Due to variAnt’s open structure, there
are sharp edges and corners.
●variAnt may only be used indoors. Do not use
this robot in traffic areas!
●Do not use variAnt on tables and other
surfaces from which it could fall.
●Only use the robot in dry, clean spaces. Dirt,
dust, foreign objects, and dampness destroy
the mechanics and electronics.
●Caution: Do not hook up devices to the robot,
especially not ones with mains voltage!
●f you hook up a device to the robot, we are
not liable for lost data.
●The robot is designed exclusively for learners,
teachers, and experimental purposes. Any and
all liability is excluded in the case that it is
used for any other purpose.

General Battery nformation
●Rechargeable batteries (RBs) should be kept
out of the reach of children!
●Do not charge conventional batteries. Doing so
is both a fire and explosion hazard.
Conventional batteries are not recommended
for this kit.
●Avoid short circuiting the RB; it can result in
the wires and/or the RB overheating.
●Do not disassemble, burn, or damage the RB.
●Charge the RB approximately every 3 months.
Otherwise, it can come to an over-discharged
or dead RB, which can make the battery
unusable.
●Defect RBs are to be disposed of in accordance
with the environmental rules and regulations
of your state and/or country. Most typically
they need to be entirely discharged, have non-
conductive tape placed over the terminals or
be placed separately into sealed plastic bags.
Do not put them in the trash or municipal
recycling bins!
Although the constructions and circuits introduced
in this instruction manual were designed and tested
with as much accuracy and detail as possible, errors
cannot be entirely excluded.
The intended use of this kit is described in this
instruction manual. f you deviate from the
instructions, the guarantee and liability will be
forfeited and the use of the robot is at your own
risk!
This product was produced in accordance with the
currently effective European Union directives and,
therefore, has the CE symbol.
The symbol of the garbage can/rubbish bin with an
X through it means that this product may not be put
into household garbage bins; it should be brought
to a recycling center and added to the electronic
scrap. Please take the time to find where you can
best recycle your electronic scrap!

ntroduction
Thank you for buying our variAnt robot kit. We did
our very best to make it as much like a real ant as
possible.
Thanks to its innovative and compact running
mechanism that’s powered by two high quality
micro-gear-motors, variAnt walks and acts almost
exactly like its biological counterpart.
This autonomous robot ant explores its
surroundings with up to 12 analog sensors.
These allow it to be aware of obstacles, movement,
floor markings or light with even the slightest
difference in brightness.
The control unit with its Nano-control-board in the
abdomen (rear part) and the breadboard,
integrated in the head, make multiple options for
connectivity and extensions possible.
Once the fun of putting variAnt together is over,
the pre-made and expandable code modules
ensure a quick and easy introduction to Arduino
programming. Your first experiments with A can
begin!
Content
●Section A (Construction) of this manual uses
numerous images to show you how to build
your robotic ant step-by-step.
●Section B (Startup Procedure) uses a
programming tutorial to explain how you can
use the custom-made variAnt Library to help
you write your first programs and then
gradually expand upon them.
●Section C (Appendix) currently has an
overview of the robot parts and circuit
diagrams. We will be adding more soon.
We wish you lots of fun building, programming, and
experimenting with variAnt!
You will also need:
●wire cutter & flat nose pliers
●utility knife & permanent marker
●PC or tablet with internet connection
●micro USB cable & USB-C cable

Table of Contents
A) Construction
1) Mounting the Spacers
2) Mounting the Motors
3) Prepping the Cables
4) Mounting the Boards
5) nstalling the Long Cables
6) Connecting the Short Cables
7) Prepping the Top Body Component
8) Connecting the Body Components
9) Prepping the Drive Shafts
10) Putting on the Gears
11) nstalling the Drive Shafts
12) Securing the Bushings and the Ball Joints
13) Assembling the Legs
14) Attaching the Legs
15) Defining the Step Sequence
16) Attaching the Sensors
17) Attaching the Mandibles
18) Attaching the Antennae
19) nstalling the Battery
20) Mounting the Electronics
B) Startup Procedure
1) Charging the Battery
2) Configuring the Arduino- DE
3) nstalling variAnt’s Library
4) Creating a Test Program
5) Testing the Walking Movement
6) mplementing Outputs
7) Checking the Sensors
8) Avoiding Obstacles
9) Notes on the Testing Environment
10) Additional Features of the variAnt Class
C) Appendix
1) Overview of the Components
2) Schematic Diagram of the variAnt Boards
We will continue to optimize and expand
sections B) and C) as well as the variAnt library.
We welcome your feedback so that we can
incorporate it into future updates if necessary.

List of Abbreviations
Connections on the variAnt board (front)
DL0 Digital- /O Left 0
DL1 Digital- /O Left 1
DL2 Digital- /O Left 2
DL3 Digital- /O Left 3
DR0 Digital- /O Right 0
DR1 Digital- /O Right 1
DR2 Digital- /O Right 2
DR3 Digital- /O Right 3
RSL Reed Switch Left
RSR Reed Switch Right
MLA Motor Left Ahead
MLB Motor Left Back
MRA Motor Right Ahead
MRB Motor Right Back
PWR Power
Buttons
LEDs LEDs on/off
PWR Power (battery on/off)
Connections on the variAnt board (rear)
AL0 Analog- nput Left 0
AL1 Analog- nput Left 1
AL2 Analog- nput Left 2
AL3 Analog- nput Left 3
AR0 Analog- nput Right 0
AR1 Analog- nput Right 1
AR2 Analog- nput Right 2
AR3 Analog- nput Right 3
GND Ground (0 Volt)
REF Analog Reference
RST Reset
3V3 3,3 Volt output
5V 5 Volt output (Arduino)
6V 6 Volt output (motors)
9V 9 Volt output (battery)

A) Construction
1 bottom body component
short screw (4 mm) medium screw (6 mm) long screw (8 mm)
short spacer brass ball (5 mm) long spacer
Overview of the most common combinations of small parts
Fragile! Handle with care!
When handling the acrylic parts, be careful
not to bend them too much until they
are connected to their counterpart.
Before you begin, remove the acrylic parts from
their individual transparent plastic film.
Begin with the bottom body component.

1) Mounting the Spacers
9 long spacers (plastic)
15 long screws (8 mm)
10 short spacers (brass)
10 short screws (4 mm)
The temporary feet will make mounting the
motors and gears easier.
Mount the 9 black hexagonal spacers with the 9
long screws (8 mm) and an Allen key at the
indicated positions on the top side of the acrylic
plate, which is smooth.
Then, on the same side of the plate, mount 4 of the
short brass spacers with 4 of the 4 mm screws.
Now attach 6 brass spacers with 4 mm screws onto
the bottom of the plate where variAnt’s legs will be
mounted.
Once you’ve done that, screw a long 8 mm screw
into each of the spacers. Use the Allen Key to
tighten them from the top and the bottom.

2) Mounting the Motors
Bend the connectors of each of the black twin
cables apart. Assure the indentations (1) are
facing in the same direction.
Push them through the small square openings in
the acrylic plate at the height of the indentations
(2).
After that, bend the motor cables by 180° so that
they lie flat against the side of the motor housing.
Now, ensuring you use little
pressure, slant the motors
and set them into the
corresponding openings.
The motors’ cables should run through
the small openings (4) next to the motors
and the black cable connectors should now
be stabilized.
2 black twin cables
2 gear motors with cables
1
Press the motors’ red cables right next to
the black caps of the motor housings (3).
This will prevent them from bumping into
the gears while using variAnt. 3
4
2

3) Prepping the Cables
4 cm
4 cm 7 cm9 cm
1 rainbow flat ribbon cable, 10 cm (10 pin)
2 rainbow flat ribbon cables, 20 cm (10 pin)
Carefully use a utility knife (held almost
horizontally) to split the 10 cm long flat
ribbon cable into 4 two-colored twin
cables.
Keep the leftover cable in case you
decide to do some additional wiring.
From one of the 20 cm long flat ribbon cables, sepa-
rate the outer four pole strands. Now split the three
long cables according to the specified dimensions.

4) Mounting the Boards
1 breadboard
1 control board
4 short screws
Plug the connectors of the split 10-pin flat ribbon
cable onto the back pin header of the control board
(brown » +5 V, . . . , black » GND).
Bend the cable 180°, so that it runs under the
control board. Then use the 4 short screws to
mount the board onto the brass spacers.
Now place the breadboard into the 2
large openings on variAnt’s head,
just far enough that it sits firmly.
Push the cable’s 10 pins into the 4th row of the
breadboard. Leave position number 5 vacant.
To finish the job, bend down the cable on the left
and on the right of the 2 spacers in the middle (1),
pressing them close to the breadboard (2).
Nr. 5
11
2

5) nstalling the Long Cables
Tie a knot in the 4-pin cable (brown, ..., yellow) as
shown, and then thread the 2-pin branches from
the center through the 5-pin cable strand
(brown, ..., green).
nsert the 4 connectors directly in front of the
cables of the same color into the breadboard.
Place the brown-red cable between the motors
and slide the knot onto the middle spacer.
Proceed in the same manner with the cable
(violet, ..., black) on the left side.

6) Connecting the Short Cables
Make sure the cables located near the motors
do not go too far above the black spacers.
nsert the orange-red and white-gray cables (each
10 cm long) directly in front of the cables of the
same color on the breadboard. Then, bend them
backward and guide them to the front between the
breadboard and the spacers.
Now, plug the two black twin cables into the outer
contacts RSR and RSL on the front pin header of the
control board.
Knot the left motor cable. Then, connect both
motor cables to the contacts MR and ML on the
control board, ensuring that the red cable is
positioned on the right side for each connection.

7) Prepping the Top Body Component
1 top body component
6 short screws (4 mm)
6 short spacers
1 battery clip cable
Attach 6 short spacers to the top body component
using short screws.
Then slide the clip cable for the battery through the
small rectangular opening (1) and connect it to the
available contacts in the middle of the control
board (BAT, red » +, black » ).‒
Using the included sandpaper, roughen up
both sides of the two spacers on the head
before attaching them. Then, be sure to
screw them on tightly.
1

8) Connecting the Body Components
5 long screws (8 mm)
2 medium screws (6 mm)
2 perforated brass balls (5 mm)
Now, press the diagonally positioned motors apart
at the top, and push the cables that are in between
downwards. Then, position the top acrylic compo-
nent in a way that all the components (cables etc.)
protrude through their respective openings.
For now, secure the upper component only to the
head and the abdomen using 5 long screws.
Then, attach 2 balls with 6 mm screws to the short
spacers in the head area.
Ensure that these screws are firmly tightened.
Check if the top acrylic component can be
easily pressed against the black spacers
without pinching any cables.
Also ensure the push buttons of the control
board do not stick on the acrylic when pushed.

deally, the bending angles of the 6 drive shafts
should be exactly 10°. However, they may have
some manufacturing tolerances.
To check the bending angles, use the angle
references below. f a shaft is bent slightly more
than 10°, gently press it together at the bending
point using flat pliers.
f it is less than 9°, hold the shaft with the pliers
precisely at the side of the bend and carefully
adjust it.
9) Prepping the Drive Shafts
6 bent shafts (80 mm)
6 small shaft collars
The bending angles of the shafts determine
the range of motion for the legs. f a shaft is
bent too much, the legs may collide with
each other while walking.
10°
9°
When variAnt runs into an obstacle, the impact
upon the gears is very high. To prevent the
gears from slipping on the shafts during such
situations, it’s necessary to roughen those
areas beforehand.
5 mm
Slide a shaft collar onto each of the long sides of
the 6 shafts; they’ll be 5 mm away from the end of
the shaft (the width of a small gear).
Now, using the sandpaper, roughen the ends in a
longitudinal direction (1) all the way around.
When finished, remove the shaft collars.
1

10) Putting on the Gears
8 brass bushings (26 mm)
8 small gears (2 mm hole)
2 medium shafts (35 mm)
Start by sliding one brass bushing over
the roughened ends of each of the 6
bent shafts.
Hold the shafts upright on a surface and
press one small gear onto each of these
ends.
Now, place the shafts on a smooth surface
as shown below, with 4 of the bent ends
pointing upward as much as possible and 2
pointing downward.
f the alignment of the bending angles
doesn’t match precisely for some of the
shafts, the corresponding gears need to be
adjusted as follows.
Use pliers to hold the shaft near the bend and a
piece of cloth to slide the gear off the shaft. Then,
press the gear back on again.
Now, mark the 6 upward-facing teeth of each gear
with a marker, and using the provided lubricant,
lubricate the shafts between the gears and the
bushings (1).
Lastly, for the two 35 mm long shafts,
press a small gear onto each one,
lubricate them, and slide a brass
bushing onto each of them as well.
Keep in mind that the 15 teeth of the gear
correspond to one step cycle (360°).
So, if a gear is, for example, half a tooth
misaligned when attached, it results in a
deviation of 360°/30 = 12°.
1

11) nstalling the Drive Shafts
2 cube magnets (2 mm)
8 little shaft collars
By adjusting the height of the gears, you can
also adjust their distance from each other.
Please note that the red-brown cable should
run between two shafts, while the other three
cables should run either in front of or behind
the shafts.
Start by rotating the D-shaped motor shafts so that
the flattened sides are facing directly outward (1).
Then, place the two small cube-shaped magnets
approximately in the middle of each shaft (2).
Carefully slide the two shafts, whose gears
you marked in the opposite direction of
their bending, through the middle oval
holes (3).
f the brass bushing gets stuck in the second hole,
gently push the end of the shaft towards the center
while inserting it. Ensure the gears protrude the
same distance as the motor shafts.
Next, insert the 2 shorter shafts into the openings
opposite the motors (4).
Lastly, slide the remaining 4 long shafts
through the outer oval openings.
The alignment of the gears to
each other does not need to
be considered at this stage.
Now, secure each of the 8 shafts with a shaft collar.
Place variAnt on its feet, and adjust the height of
the brass bushings so that the gears just barely
rotate without touching the ground.
1
2
34

12) Securing the Bushings and Attaching the Ball Joints
6 medium-length screws (6 mm)
6 brass balls with holes (5 mm)
Begin by disassembling the six temporary feet and
placing the whole thing on its gears.
While applying slight pressure to the center of the body
(to keep the brass bushings from slipping out of place),
carefully tighten the acrylic pieces at the remaining
positions using 4 long 8 mm screws.
Then temporarily remove the two short shafts.
Now, attach 6 short brass spacers to
the 6 leg mounts using short 4 mm
screws.
Lastly, mount 6 brass balls on
top of them using medium-
length screws.
Ensure the 6 mm screws
are positioned exactly at
the center of the balls.
At this point, ensure all the gears are still at the
correct height.

13) Assembling the Legs
6 right leg elements
6 left leg elements
48 short screws
24 short spacers
6 short shafts (8 mm)
6 small shaft collars
So that the legs can be easily attached to the
body in the next step, the two screws at
positions 3 and 4 should not be tightened yet.
On a smooth surface, check if the shaft collars
at the end of the legs roll smoothly.
They compensate for lateral leg movements
and even increase variAnt’s speed.
4
2
3
1
Attach 4 short spacers using 4 short screws to each of the
unengraved sides of the right leg elements.
Slide one shaft collar up to the middle of each of
the 6 short shafts (8 mm) and insert one of these
into the hole at the end of each right leg element.
Place a left leg element on top of each right leg element,
and secure each with 2 short screws at positions 1 and 2.
Screw the other two screws loosely into the spacers
at positions 3 and 4 (about halfway in).
Carefully remove any rough edges on these shaft
collars using a utility knife.
Other Variobot Robotics manuals
Popular Robotics manuals by other brands
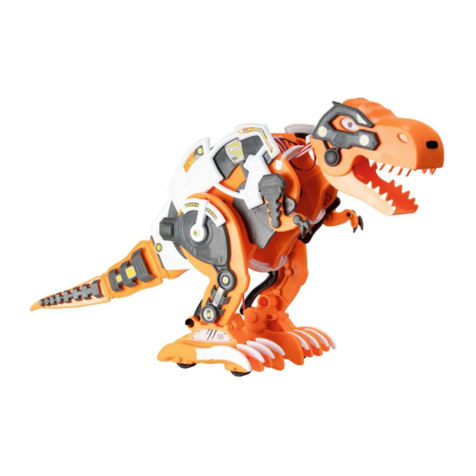
Xtrem Bots
Xtrem Bots REX THE DINOBOT instruction manual
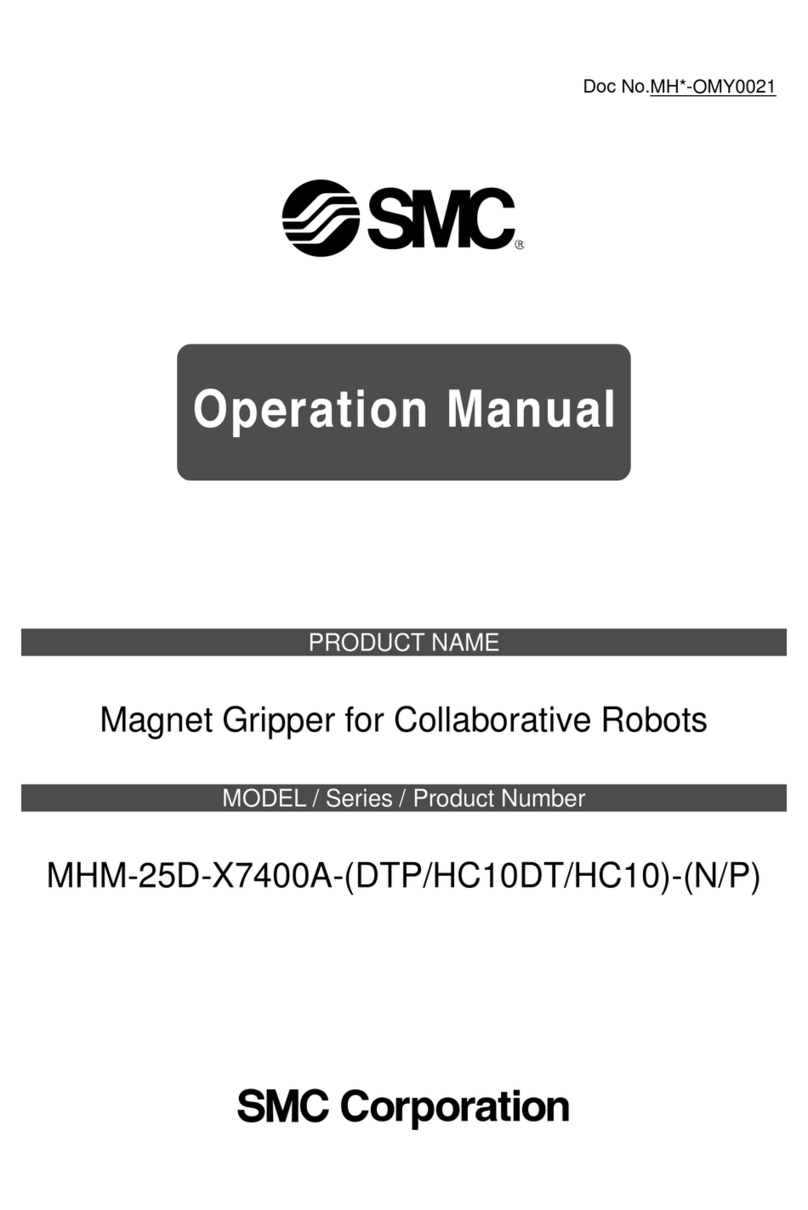
SMC Networks
SMC Networks MHM-25D-X7400A-DTP-N Operation manual
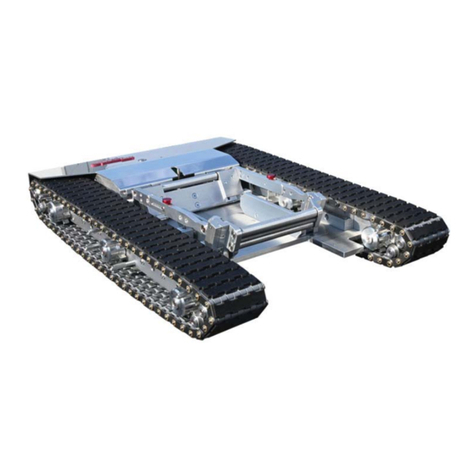
AC Air Technology
AC Air Technology AC TRACKTECH T1X2 instruction manual
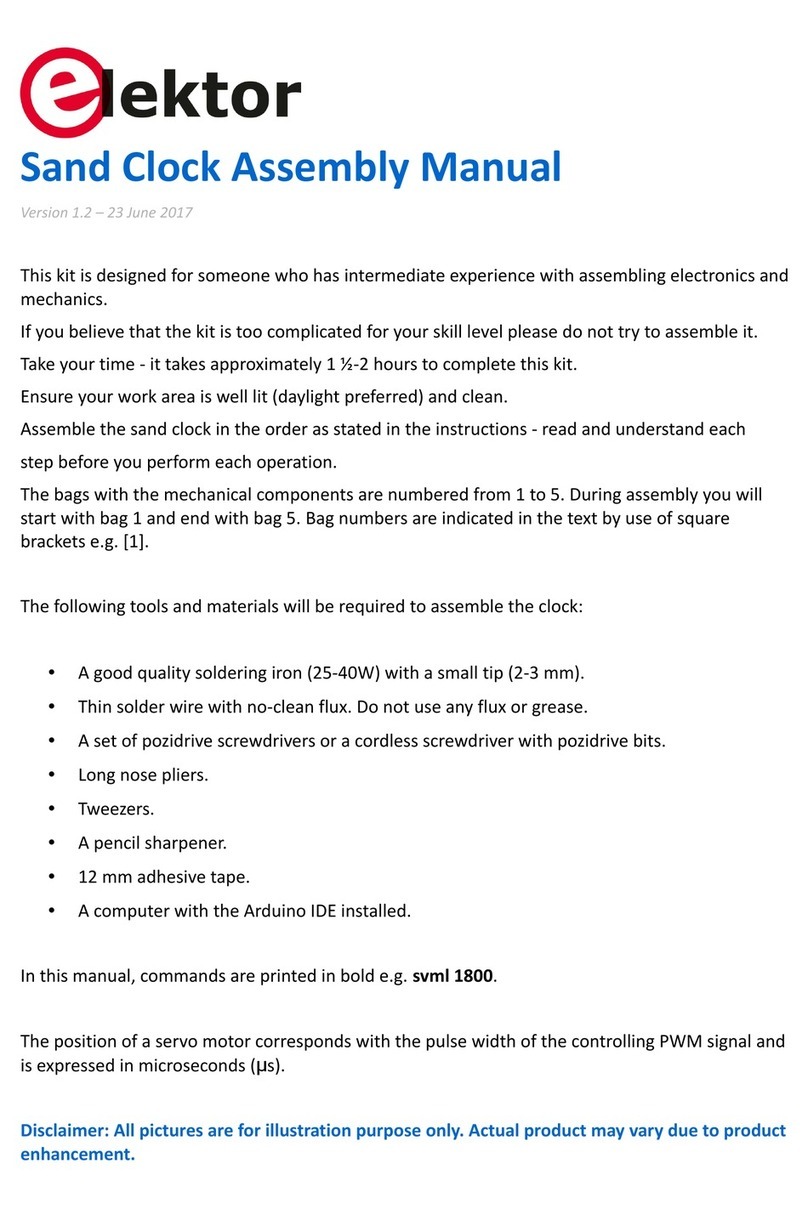
Elektor
Elektor SAND CLOCK Assembly manual

EFORT
EFORT ER180-4-3200 Quick operation manual
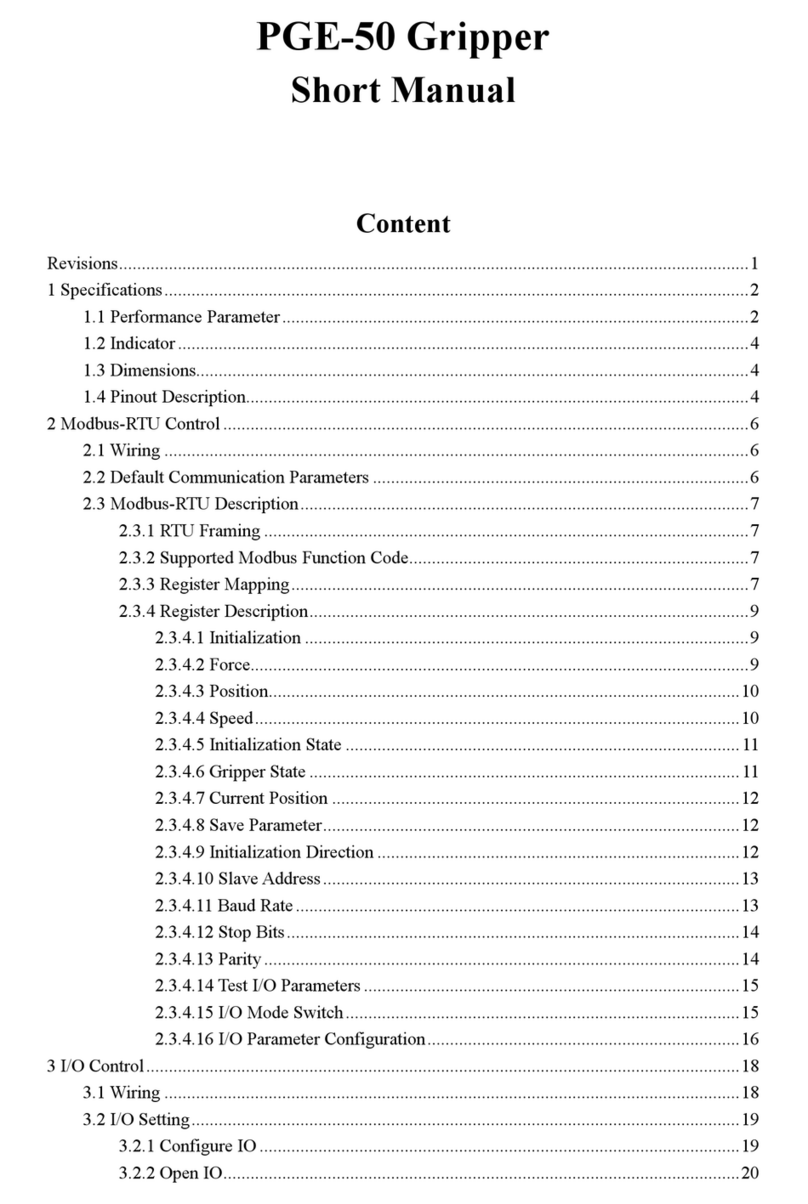
DH Robotics Technology
DH Robotics Technology PGE-50 manual
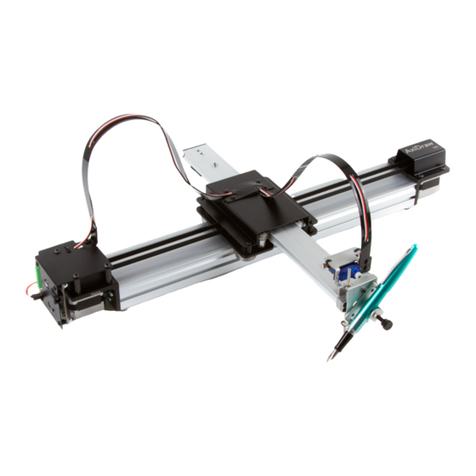
Evil Mad Scientist
Evil Mad Scientist AxiDraw V3 user guide
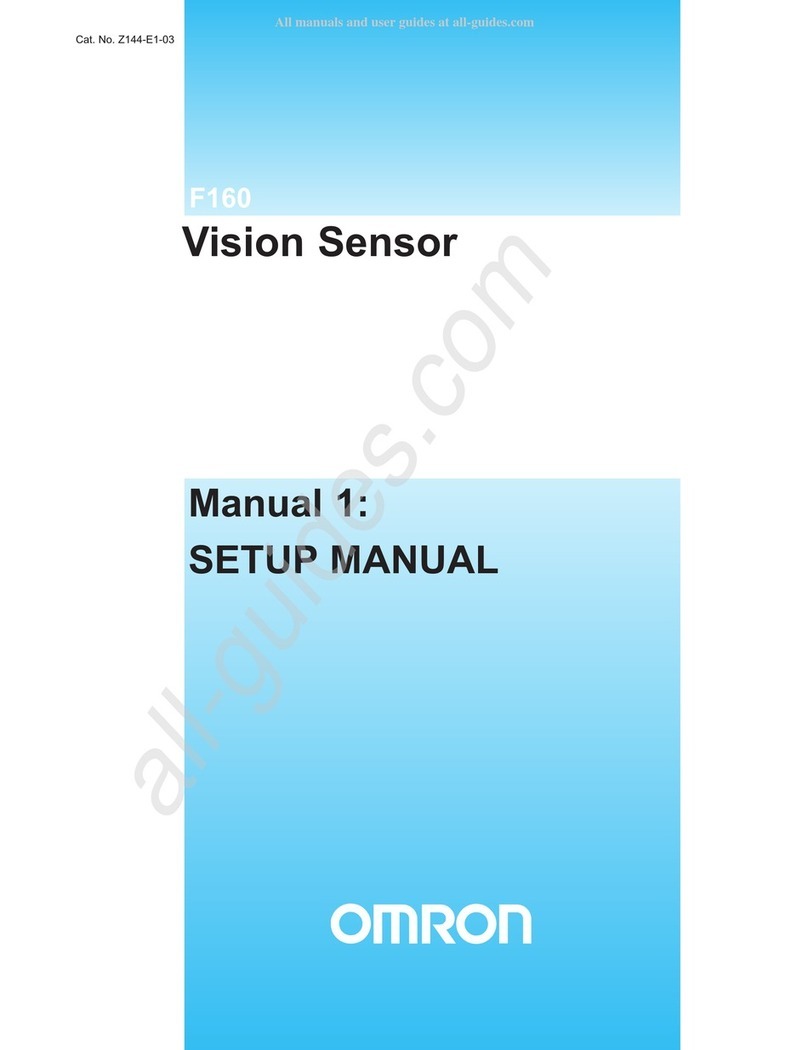
Omron
Omron F160 Vision Sensor Setup manual
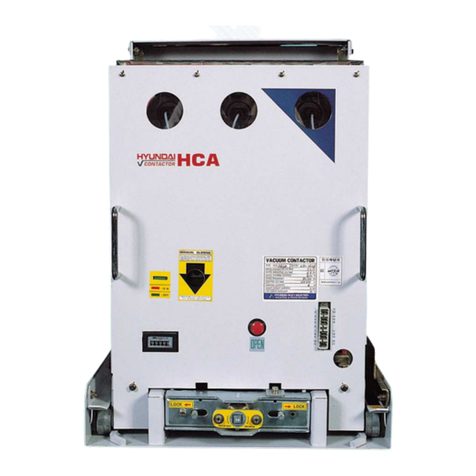
Hyundai Heavy Industries
Hyundai Heavy Industries HCA Series instruction manual
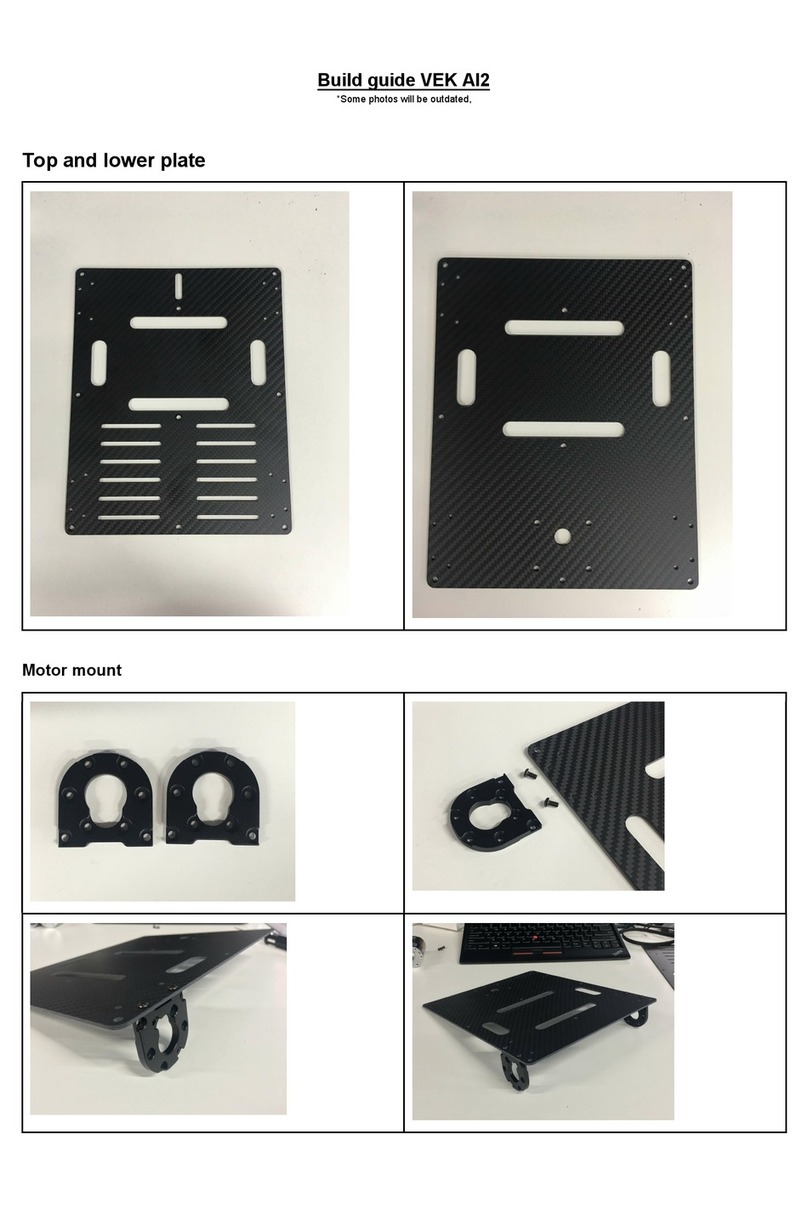
LAB
LAB VEK AI2 Build guide
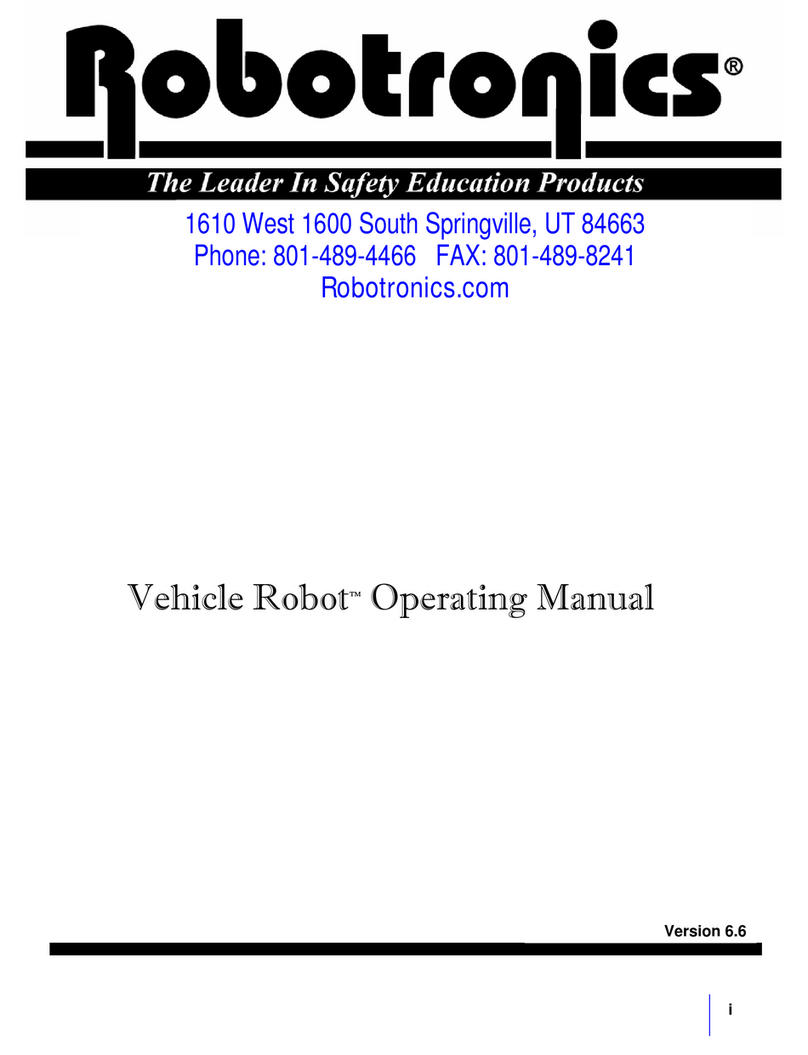
Robotronics
Robotronics Vehicle Robot operating manual
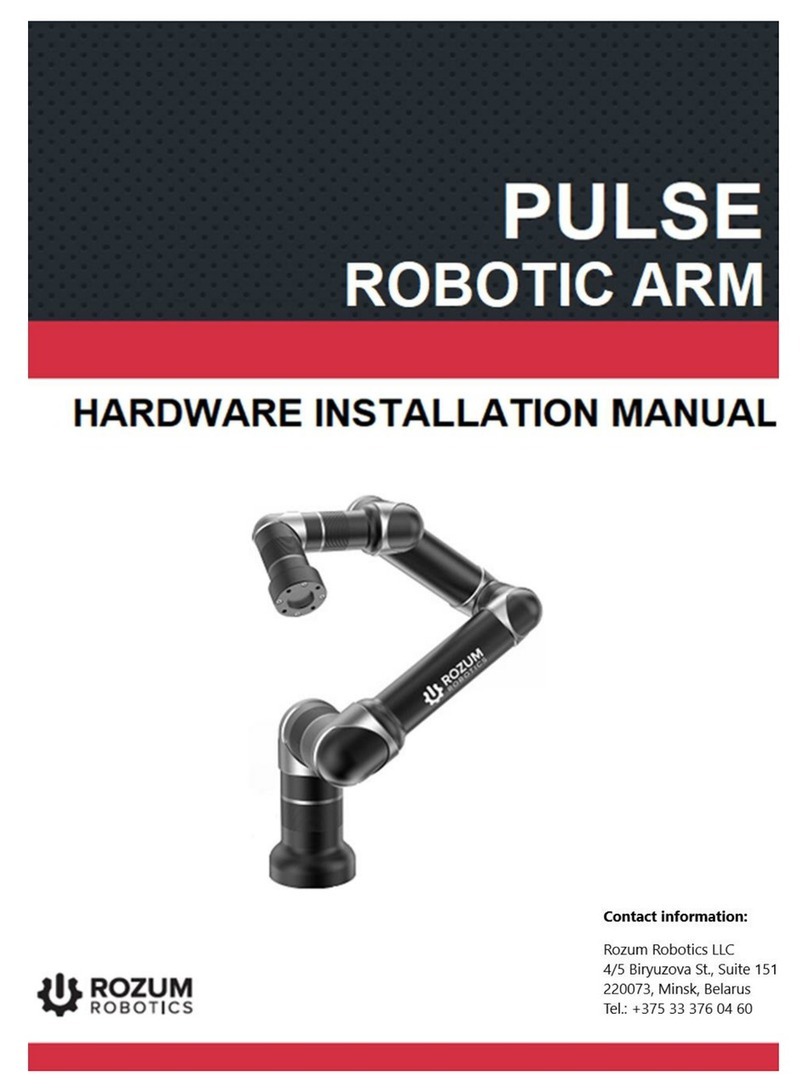
rozum robotics
rozum robotics PULSE 75 Hardware installation manual