VDH MC2-FC User manual

Description:
MC2
-
FC
mode
MC
(software 181030 v3.00)
Pages:
58
Doc. no.
200061
Type:
Manual
By:
BVDB
Version:
1.3
File:
Do200063 MC2-FC mode MC V13 EN.docx
Initials:
Date:
28
-
02
-
2020
VDH Products BV
Manual
MC2-FC mode MC

MC2-FC mode MC Document no.:200063 Version: 1.3
Page 2of 58
Table of Contents
1Functional specification..............................................................................................................................4
1.1 Introduction...........................................................................................................................................4
1.2 Commissioning.....................................................................................................................................5
1.3 Phases and cooling..............................................................................................................................5
1.4 Heating...................................................................................................................................................6
1.5 Defrost....................................................................................................................................................7
1.6 Ventilation functions...........................................................................................................................9
1.7 Humidification................................................................................................................................... 10
1.8 Day/night mode................................................................................................................................. 10
1.9 Setpoint link....................................................................................................................................... 10
1.10 External temperature set point...................................................................................................... 10
1.11 Blocking............................................................................................................................................... 11
1.12 Lighting............................................................................................................................................... 11
1.13 Water measurement......................................................................................................................... 11
1.14 Hotgas heating.................................................................................................................................. 11
1.15 Alarms ................................................................................................................................................. 12
1.16 Counters.............................................................................................................................................. 12
1.17 Sensor offsets.................................................................................................................................... 12
1.18 Storage cycle order........................................................................................................................... 13
2Control ......................................................................................................................................................... 14
2.1 Cell name ............................................................................................................................................ 14
2.2 Touchscreen....................................................................................................................................... 15
2.2.1 Power-up page.......................................................................................................................... 16
2.2.2 Cell page 1.................................................................................................................................. 17
2.2.3 Cell page 2.................................................................................................................................. 17
2.2.4 Status pages ............................................................................................................................. 18
2.2.5 Settings page 1......................................................................................................................... 19
2.2.6 Settings page 2......................................................................................................................... 20
2.2.7 Parameter page........................................................................................................................ 20
2.2.8 Access code page..................................................................................................................... 21

MC2-FC mode MC Document no.:200063 Version: 1.3
Page 3of 58
2.2.9 Temperature set point page................................................................................................... 21
2.2.10 Day counters 1 page................................................................................................................ 22
2.2.11 Day counters 2 page................................................................................................................ 22
2.2.12 Free-running Counters page.................................................................................................. 23
2.2.13 Alarm pages............................................................................................................................... 23
3Input and output functions...................................................................................................................... 24
3.1 Pt1000 Temperature sensor input functions.............................................................................. 24
3.2 Digital input functions...................................................................................................................... 24
3.3 Relay output functions..................................................................................................................... 25
4Parameters................................................................................................................................................. 26
4.1 Cell parameters................................................................................................................................. 26
4.2 Network parameters......................................................................................................................... 37
5Alarms.......................................................................................................................................................... 39
6Ethernet....................................................................................................................................................... 40
6.1 Define IP address.............................................................................................................................. 40
6.2 Define mode....................................................................................................................................... 42
6.3 Defining the name and inputs and outputs................................................................................. 43
6.4 Displaying status inputs and outputs........................................................................................... 45
6.5 Parameter web page ........................................................................................................................ 46
7Connections................................................................................................................................................ 47
7.1 Controller............................................................................................................................................ 47
7.1.1 Wall-mount version.................................................................................................................. 48
7.1.2 Panel-mount version............................................................................................................... 49
7.1.3 RS485 connections.................................................................................................................. 50
7.2 Extension module 907.100054 MC3-EM [1Do12,1Rth16]....................................................... 51
8Dimensions................................................................................................................................................. 53
8.1 Controller wall-mount version........................................................................................................ 53
8.2 Controller panel-mount version..................................................................................................... 54
8.3 Extension module 907.100054 MC3-EM [1Do12,1Rth16]....................................................... 55
9Timing diagram hotgas defrost.............................................................................................................. 56
10 Aantekeningen........................................................................................................................................... 57

MC2-FC mode MC Document no.:200063 Version: 1.3
Page 4of 58
1Functional specification
1.1 Introduction
The MC2-FC is a controller that can control, monitor and register the temperature, humidity and
ventilation of cooling and storage cells. The controller is very suitable for the control of fruit storage
cells, but it can also be used for many other control applications. There are 2 versions: a wall-mount
version and a panel-mount version, see sections 7.1 and 8.
The controller has Pt1000 temperature sensor inputs, digital inputs and relay outputs that are freely
configurable. The inputs are used to supply the controller with the measurements and external data
required for the control processes. The controller uses these inputs in combination with the control
settings (set points, parameters, etc.) to calculate the control values. The control values are
transmitted by means of relays to the processes to be controlled.
Multiple controllers can be connected to each other through a network (RS485 or Ethernet,
depending on the mode) so that they can exchange technical control data. In this way, they canbe
combined to create an integrated control system with mutually coordinated control actions, while
retaining their autonomous operation in the event of network malfunctions.
The controller supports two modes: the mode FC (standard) and the mode MC. In the mode MC, the
controller can work together with MC3-FRUIT and MC3-COOL controllers through the Ethernet. In the
mode FC, the controller functions in the same way as the FC785-PC controllers and in that way can
work together through the RS485 network. This mode is described in another manual. It is possible
to switch between the two modes through an internal web page (see section 6.2).
The controller can be operated using the touchscreen. It can also be operated (also by remote
control) using a computer on which the VDH Alfa Server Program (VASP) has been installed. VASP
provides access to the advanced control functions such as registrations, alarm handling settings,
etc.
The controller has 5 temperature sensor inputs (which can also be used as digital inputs) and 5
relays. If more inputs or relays are necessary, the controller can be expanded with an optional
907.100054 MC3-EM [1Do12,1Rth16] extension module. That adds 16 temperature sensor inputs
and 12 relays to the controller.

MC2-FC mode MC Document no.:200063 Version: 1.3
Page 5of 58
1.2 Commissioning
The following must be taken into account before the controller is commissioned:
·When the Ethernet connection is used, the IP address must be checked/defined (see section
6.1).
·The correct mode (FC or MC) must be selected (see section6.2)
·The desired controller name and input and output functions must be defined (see section6.3).
·If the controller must work together with other controllers, the controllers must be linked to
each other through the Ethernet. Then a unique cell number with a parameter (P01001) must
be defined on every controller.
·The parameters must be checked/defined (see section 0).
The software version number of the controller can be retrieved using parameter P7000. To
ensure that multiple controllers can work together in a single network, it is recommended that
controllers with similar software versions are used. Controllers with different software versions
do not always work well together.
In addition, we strongly recommend that after a controller has been commissioned you
carefully note down the defined parameters and store them in a safe place. Then, if a controller
needs to be exchanged, that can be done much faster and more easily.
The functional operation of the controller is described in the following sections.
1.3 Phases and cooling
The controller functions in 3 phases. These phases mainly relate to the control of the mechanical
cooling (fluid valve and, where relevant, suction valve).
Cool phase: In this phase the cell starts mechanical cooling if the control temperature exceeds the
actual temperature set point + temperature differential. The cooling stops if the temperature set
point is reached. For the cool phase, each cell is placed in a cool group. Cool groups can be formed
by setting a cool group number for each cell (P0310). A maximum cooling capacity can be set for
each cool group (P2100 and other parameters). The cooling is only started if that does not cause
exceeding the maximum cooling capacity in the cool group. For that purpose the cooling capacity of
each cell applicable for the cool phase must be programmed (P0300). Due to this maximization cells
sometimes have to wait until cooling capacity becomes available. The cool group of a cell also applies
to the standby phase.
1In this manual, parameters are indicated with P<x>, where x = the parameter number.

MC2-FC mode MC Document no.:200063 Version: 1.3
Page 6of 58
Store phase: For the store phase, each cell is placed in a store group. Store groups can be formed
by setting a store group number for each cell (P0320). Within each store group, each cell
mechanically cools only once in a store cycle time interval until the control temperature reaches the
temperature set point. The time between two consecutive cycles of a store group can be configured
(P2201 and other parameters). The store cycles of the different store groups are not synchronized.
By default, the cells are cooled in order of ascending cell number (P0100). As many cells with cool
demand will be started as the maximum cooling capacity of the store group allows. Thus, the
maximum cooling capacity of each store group (P2200 and other parameters) and the cooling
capacity of each cell must be programmed in the store phase (P0301). If a cell cannot be started
because it is defrosting or because the remaining cooling capacity in the store group is insufficient
for that cell, then a somewhat different order is used. If, however, the next cell can be started, it is
started to avoid loss of cooling capacity. Instead of the default order, other cooling orders can be
configured (P2202 and other parameters). These are further described in section 1.18. The store
phase is very suitable to operate multiple cells with limited compressor capacity and limited
compressor starts. This phase can be enabled or disabled (P0110).
Standby phase: In this phase the cell only (mechanically) cools if that is required to deliver hotgas
to another cell which is waiting for a hotgas defrost action. The other functions of this cell (defrost,
heating, humidify and automatic ventilation) are disabled. This phase can be enabled and disabled
(P0111).
1.4 Heating
The cell heating (Heating relay function) is switched on when the control temperature drops below
the current temperature set point + heating set point offset – heating differential (P0400 and
P0401). The heating stops when the current temperature set point + heating set point offset is
reached.
Heating with hotgas from mechanically cooling cells is also possible. That is described in section 0.

MC2-FC mode MC Document no.:200063 Version: 1.3
Page 7of 58
1.5 Defrost
The controller support 3 defrost methods, which are described in further detail below: A separate
defrost group can be configured for each defrost method on the cell controllers (P0800..P0802).
Different settings can be made for each defrost group (P2400..P2406 and other parameters), for
example, the maximum number of cells that defrost at the same time, the number of cooling cells
which are required for hotgas defrost.
A defrost action can be started manually, on clock time intervals, effective cooling time intervals or
on real-time intervals (P0810..P0843). A defrost action only startswhen the defrosting temperature
is lower than the defrost release temperature (P0850).
Offcycle defrost: During the defrost time, the cooling ventilation of the evaporators is switch on and
the cooling is blocked. Defrost will automatically stop if the maximum defrost time (P0851) has
passed. Automatic stop at the reaching of the end of defrost temperature (P0852) can also be set
(P0805). In case of multiple evaporators, the evaporators are defrosted simultaneously.
The offcycle defrost method can also be selected automatically when electrical or hotgas defrost is
programmed. Automatic selection is based on the control temperature. When the control
temperature rises above an adjustable value (P0803), then offcycle defrost is used instead of the
defrost method programmed.
Electrical defrost: During defrost the cooling ventilation of the evaporators stays off. Defrost will
automatically stop if the end of defrost temperature (P0852) is reached or the maximum defrost
time (P0851) has passed. After defrost a dripoff is performed. The ventilation after electrical defrost
can be released on time, defrost temperature or on a combination of both (P0872..P0874). In case
of multiple evaporators, the evaporators can be configured (P0804) to defrost simultaneously or
after one another.
Hotgas defrost: This defrost method requires one or more cells (within the same defrost group)
which are cooling to deliver hotgas. The number of cooling cells which are required for hotgas
defrosting can be programmed (P2402 and other parameters). The maximum time a cell must wait
for hotgas can also be programmed. If this maximum time is exceeded or there are too many cells
waiting for hotgas (P2401), then other cells are forced to start cooling to deliver hotgas. If required,
forced cell cooling and order of cooling can be programmed (P2406). We distinguish the following
categories of cells:

MC2-FC mode MC Document no.:200063 Version: 1.3
Page 8of 58
"Preference cells": These are cells that are identified as preference cell using parameter P0120.
"Highest cool demand" cells: These are cells that are not cooling (yet), but that have a cool demand.
These cells are forced to start cooling in sequence of decreasing cool demand.
"Standby cells": These are cells that have been defined in the standby phase.
As many cells as required will be forced to start cooling, according to the defined sequence, until the
required number of cooling cells has been reached.
During defrost the cooling ventilation of the evaporators stays off. Defrost will automatically stop if
the end of defrost temperature (P0852) is reached or the maximum defrost time (P0851) has
passed. Defrost will also stop if no hotgas is available anymore. After defrost a dripoff, pressure
equalizing B and a pumpdown are performed. The ventilation after hotgas defrost can be released
on time, defrost temperature or on a combination of both (P0872..P0874). In case of multiple
evaporators, the evaporators can be programmed to defrost simultaneously or one after the other
(P0804).
Section 9 includes a timing diagram in which the various times and functions of hotgas defrosting
are displayed.

MC2-FC mode MC Document no.:200063 Version: 1.3
Page 9of 58
1.6 Ventilation functions
The controller supports 3 separate ventilation functions:
Cooling ventilation: This ventilation function is coupled to an evaporator and used during cooling
and offcycle defrost. The function can be switch on and off automatically, but it can also be switched
on continuously by manual control. This selection can be made using the cooling ventilation mode
(see section Fout! Verwijzingsbron niet gevonden.). The function can also be continuously
switched on using a digital input (Continuous cooling function).
An additional relay function is coupled to this ventilation function: High RPM ventilation. This relay
function is active (only during cooling) if the control temperature exceeds the temperature set point
+ High RPM ventilation set point offset (P0360) + High RPM ventilation differential (P0361). The
function stops if the control temperature reaches the temperature set point + High RPM ventilation
set point offset.
Heating ventilation: This ventilation function is active during heating.
Automatic ventilation: This ventilation function is not coupled to cooling. It can be switched on at
real-time periods, on pulse/pause basis or pulse/pause basis synchronized with cooling or
combinations of these options (P0700..P0739). Pulse/pause synchronized with cooling means: After
a cool action and the ventilation switch-off delay the automatic ventilation starts with a pause time.
Five sets of pulse/pause times can be programmed for the pulse/pause basis. One of the sets can
be selected at the control panel using the automatic ventilation pulse/pause mode (see section
Fout! Verwijzingsbron niet gevonden.).
Parameters (P0411, P0701) can be set that the relays with function "Cooling ventilation" are also
activated for the functions "Heatingventilation" and/or "Automatic ventilation". This can simplify the
configuration of the ventilation relay functions.
The relays with function "Cooling ventilation" are also activated during offcycle defrost.

MC2-FC mode MC Document no.:200063 Version: 1.3
Page 10 of 58
1.7 Humidification
The controller supports 3 humidification modes:
Off: The humidification control is continuously disabled.
Continuous: The humidification control is continuously active.
Automatic: The humidification control is activated on the basis of the advanced automatic
humidification timing settings that include pulse/pause timing and synchronisation with cooling and
ventilation (P0600..P0631).
An overruling limitation provision can be used to limit the total humidification time in a time period:
A maximum humidification time in a blocking time can be defined (P0630..P0631).
1.8 Day/night mode
The day/night mode is used to determine the temperature and RH set points. It can be switched
manually, automatically (P0160..P0163) or by a digital input. An automatic coupling or a coupling via
a digital input can be changed manually.
The night mode can also be completely blocked (P0164). The cell controller is then always in day
mode and the day-night indications/buttons and night set points are not displayed on the
touchscreen.
1.9 Setpoint link
The temperature set point can be linked to another cell (P0130]. The controller then uses the same
temperature set point as the cell to which it is linked. In the same way, switching on/off can be linked
to another cell (P0101).
1.10 External temperature set point
The normal day and night temperature set point can be changed by an external digital input, such as
a switch. The digital input can be used to start, restart and stop an alternative temperature set point
or an offset on the normal set point. Different timing and activation options are available
(P0170..P0173). A minimum pulse time of 5 seconds is required to ensure proper starting and
stopping through the digital input.

MC2-FC mode MC Document no.:200063 Version: 1.3
Page 11 of 58
1.11 Blocking
If blocking is activated, all the control functions are stopped. Blocking can be activated during real-
time periods (P1000..P1035) or with adigitalinput. Ifrequired, blockingcanbe ignored for automatic
ventilation (P1040). The detection of temperature alarms during blocking can be switched off
(P1042).
1.12 Lighting
If a relay function Light is configured, then a light button is displayed on the cell pages of the touch
screen control panel with which the lighting can be switched. With a parameter (P0152) it can be set
that the lighting also couples on the door contact. The lighting can also be switched with an external
pulse switch, if it is configured as a "Light switch" on a digital input. A minimum pulse time of 5 s
applies for this digital pulse input.
1.13 Water measurement
The controller supports measurement of water quantity. It can, for example, measure the defrost
water from the evaporators. A water counter pulse can be sent through a digital input. The minimum
pulse time required is 5 seconds. The number of litres of water corresponding to a pulse can be
defined with a parameter (P1100). A free-running counter and day counter are used to keep track of
the amount of water from the evaporators.
It is possible to open a water valve after a settable number of liters for a settable period of time
(P1101..P1102). This can then be used, for example, to empty out a collection vessel.
Note: The water measurement function and water valve control are also active when the controller
is switched off.
1.14 Hotgas heating
With the relay function Hotgas heating you can heat with hotgas that is supplied by other
mechanically cooling cells. For this purpose, a hotgas defrosting group must be set (P0420) which
indicates from which mechanically cooling cells hotgas can be received.
The hotgas heating is switched on if the control temperature drops below the current temperature
set point + hotgas heating set point offset (P0421) - hotgas heating differential (P0422). Additional
release conditions are that there are cooling cells within the set defrosting group (P0420) and that
no hotgasdefrost is active. The hotgas defrosting thereforehas a higher priority within thedefrosting
group than hotgas heating.
The hotgas heating is stopped when the current temperature set point + hotgas heating set point
offset is reached and the release conditions are no longer fulfilled.

MC2-FC mode MC Document no.:200063 Version: 1.3
Page 12 of 58
1.15 Alarms
The controller has 2 adjustable temperature alarms. Parameters (P0900..P0966) can be used to
configure how the alarms operate: in which phase, on which sensor(s), against which reference, at
which alarm delay and with which actions.
Note: For the temperature alarms, an alarm can be generated when the (absolute) difference
between two temperature sensors becomes too high. This can be used, for example, to issue a
warning when a product temperature difference reaches a critical point.
External alarms on the controller can also be generated with digital inputs: Three non-fatal alarms
and three fatal alarms. Separate alarm delays can be defined for these alarms (P0931..P0936).
1.16 Counters
The controller has the following free-running counters. These counters can be read and manually
reset from the control. A time to automatically reset the free-running counters can be defined with
parameters (P0165..P0166).
·Cooling actions/pulses
·Cooling time
·Measured litres of water
The controller has the following daycounters. These counters can be read through VASP and are
automatically reset at midnight.
·Cooling actions/pulses
·Cooling time
·Ventilation time ("Cooling ventilation" or "Automatic ventilation" active)
·Cooling ventilation time (function "Cooling ventilation" active)
·Automatic ventilation time ("Automatic ventilation" function active)
·Humidification time
·Measured litres of water
·Heating time
1.17 Sensor offsets
The controller has a sensor offset parameter (P0200..P0234) for every sensor. This can be used to
correct the measurement value indication due to the inaccuracy of the sensor and (partly) the
measurement circuit of the controller. If the controller indicates too much for a temperature sensor
– for example, 2˚C – the offset parameter of that sensor must be lowered by 2 K.

MC2-FC mode MC Document no.:200063 Version: 1.3
Page 13 of 58
1.18 Storage cycle order
In addition to the default store cycle order, the cell controllers also support the orders below. The
order can be set per store group (P2202 and other parameters)
"Rotating" order: This order is equal to the default order, however, the cell number which starts the
cycle rotates: The first cycle starts, for example, with cell number 1, the second cycle with cell
number 2 and so on.
"Store start number" order: The cells (in this storegroup) with cool demand are cooled in ascending
store start number order (P0321 and other parameters), where as many cells are started as the
maximum cooling capacity of the store group allows. If a cell cannot be started because it is
defrosting or because the remaining cooling capacity in the store group is insufficient for that cell,
then a somewhat different order is used. If,however,thenext cellcan be started, it is startedto avoid
loss of cooling capacity.
"Per store start number" order: This order is equal to the "Store start number" order, however, a
cell will only be started when there are no more cooling cells with a lower store start number. Thus,
there are no simultaneously cooling cells with different store start numbers within the store group.
This order can be used, for example, to prevent a series of cells requiring different suction pressures
from cooling simultaneously.
"With store subgroups" order: With this order, the store group is further divided into store
subgroups (P0322 and other parameters). A cycle is run for each store subgroup. The cycles in the
store subgroups (in the same store group) start at the same time, but are no longer linked to each
other. In a store subgroup, only one cell with cool demand is set to cooling in ascending store start
number order. The set maximum cooling capacity per store group does not apply to this order.

MC2-FC mode MC Document no.:200063 Version: 1.3
Page 14 of 58
2Control
The controllercan be operated usingthe touchscreen. The languagecanbe defined with aparameter
(P6300). In the following sections, the indications and buttons of the touchscreen are described
using screenshots. If a function of the controller is not used (not defined), the relevant indications
and buttons are not displayed on the pages. For example: If no heating has been configured, no
heating indication is displayed.
2.1 Cell name
The cell name that is displayed on the cell pages can be entered on an internal web page. If no name
is entered, the standard name "Cell x" is used, where x = the cell number (P0100).

MC2-FC mode MC Document no.:200063 Version: 1.3
Page 15 of 58
2.2 Touchscreen
On the touchscreen, the symbols in the following table are used to display the status and the button
functions.
Symbol Meaning Button function
Cooling active
Blinking = cell is waiting for the release conditions
so that it can start cooling
Heating active
Defrost active
Blinking = cell is waiting for the release conditions
to be met so that it can start defrosting
Start or stop defrosting manually
Drip-off after defrosting enabled
Humidification active
Blocking enabled (blocking contact/time, control
delay or door open)
"Automatic" cooling ventilation mode enabled Change cooling ventilation mode
"Continuous" cooling ventilation mode enabled Change cooling ventilation mode
Automatic ventilation pulse/pause mode
Number of lines = mode number (1 to 5)
Number = corresponding pulse/pause ventilation
percentage
Change automatic ventilation
pulse/pause mode
Ventilation functions enabled
Green = Controller switched on
Grey = Controller switched off
Switch the controller on and off
The button must be pressed for
3 seconds
Daytime mode active Change day/night mode
The button must be pressed for
3 seconds
Night-time mode active Change day/night mode
The button must be pressed for
3 seconds
Blinking red = unconfirmed alarms
Continuous red = active confirmed alarms
Grey = no active alarms
Go to alarm pages
Lighting switched on
Switching lighting on and off

MC2-FC mode MC Document no.:200063 Version: 1.3
Page 16 of 58
Symbol Meaning Button function
Go to previous page
Increase setting,
Go to next subpage
Decrease setting,
Go to previous subpage
Go to previous parameter group
Go to next parameter group
Go to Status pages
Go to Settings pages
Go to parameter page
2.2.1 Power-up page
This page is displayed during power-up. The software version of the touchscreen (not of the
controller) is displayed.

MC2-FC mode MC Document no.:200063 Version: 1.3
Page 17 of 58
2.2.2 Cell page 1
After power-up, cell page 1 main page (P0137 = 0) is automatically displayed.
The cell number (P0100) and the cell name are displayed at the top left. The background colour of
the cell number shows which phase the cell is in: dark blue = Cool, light blue = Store, green = Standby.
The status of the cell is displayed using symbols. The yellow area displays the current control
temperature. The green area displays the day set point on the left and the night set point on the right.
The text of an active set point is written in blue. In the grey area, the Tcold and Twarm temperatures
(if present, seeP0135, P0136). Onthefar right, the free-running cooling counters (hours and pulses)
and water counters are displayed.
A set point is displayed in red for a set point link and an active external temperature set point (see
sections 1.9 and 1.10). For a linked set point, the text ">x" displays the cell number (x) to which it is
linked. For an active external temperature set point, the remaining time (where applicable) is
displayed in minutes.
2.2.3 Cell page 2
This page is the same as cell page 1 except that the control temperature is displayed in a large font
with a yellow background. This page can be defined as standard (P0137 = 2). In that case, pressing
the control temperature displays cell page 1. Cellpage 1 can be used toview and adapt the set points
and counters.

MC2-FC mode MC Document no.:200063 Version: 1.3
Page 18 of 58
2.2.4 Status pages
These pages are displayed when you press the status button on a cell page. There are several
pages for displaying the current status (sensor measurements). You can use the arrow keys to
browse through the pages.

MC2-FC mode MC Document no.:200063 Version: 1.3
Page 19 of 58
2.2.5 Settings page 1
This page is displayed when you pressthe Settings key on a cell page. You can use the displayed
buttons to select the phase, defrost method and humidification mode. You can use the arrow keys
to scroll to the other Settings pages.

MC2-FC mode MC Document no.:200063 Version: 1.3
Page 20 of 58
2.2.6 Settings page 2
The date and time can be adapted on this page.
2.2.7 Parameter page
This page is displayed when you press the Parameter key on a cell page. The parameters can
be selected and adjustedusing the arrowkeys. You can use the left and right arrows to switch quickly
between the parameter groups.
The values (number or parameter value) can also be entered numerically. To do this, you must click
the appropriate field. A blue border is then displayed around the field. You can use the "Del" button
and the number keys to change the value. Press the "OK" button to confirm the input. Incorrect or
invalid input values are displayed in red.
Other manuals for MC2-FC
1
Table of contents
Other VDH Controllers manuals
Popular Controllers manuals by other brands
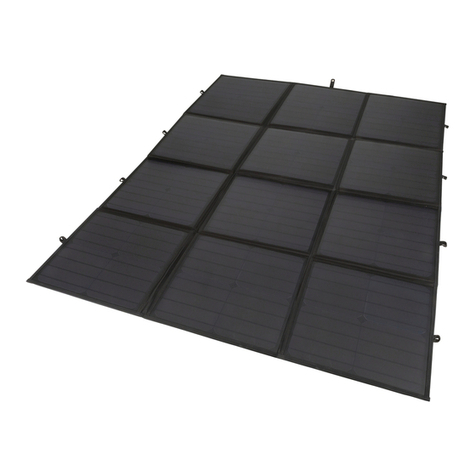
PowerTech
PowerTech ZM9126 instruction manual
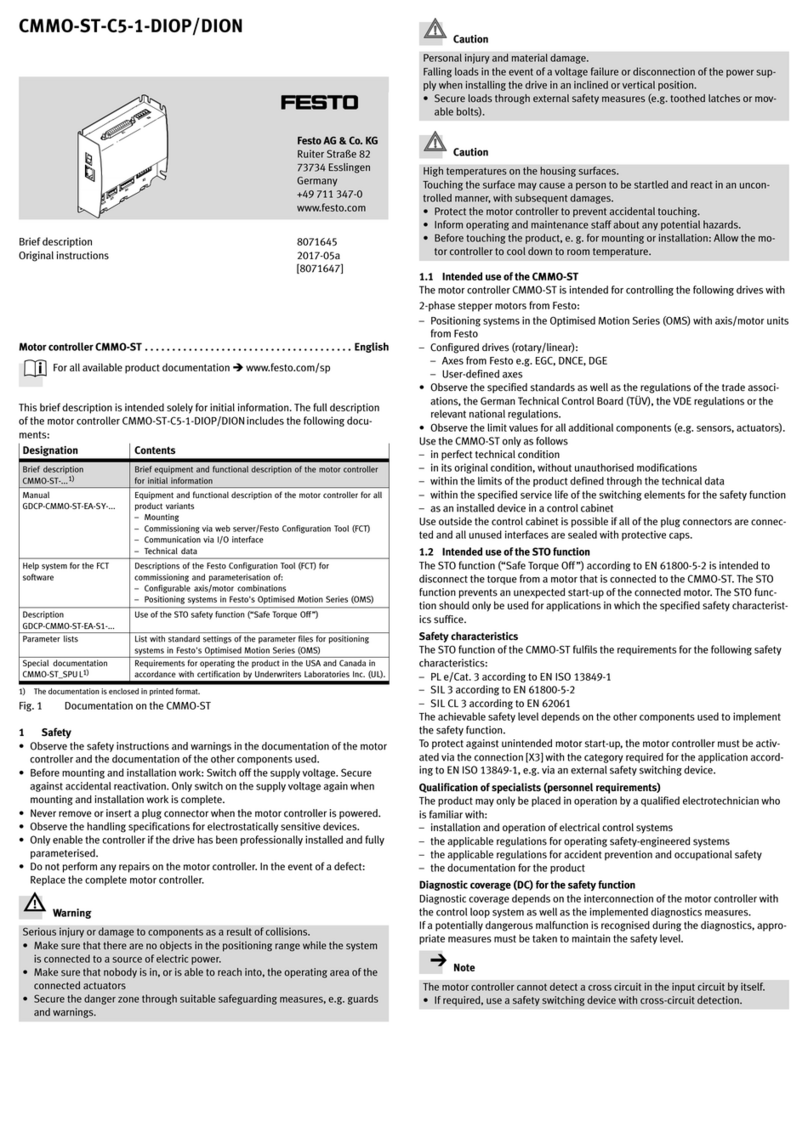
Festo
Festo CMMO-ST-C5-1-DIOP Original instructions

Doms
Doms PSS 5000 installation guide
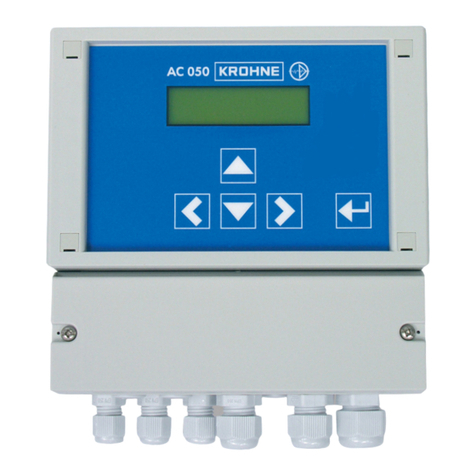
KROHNE
KROHNE OPTISENS AAC 050 Series Installation and operating instructions
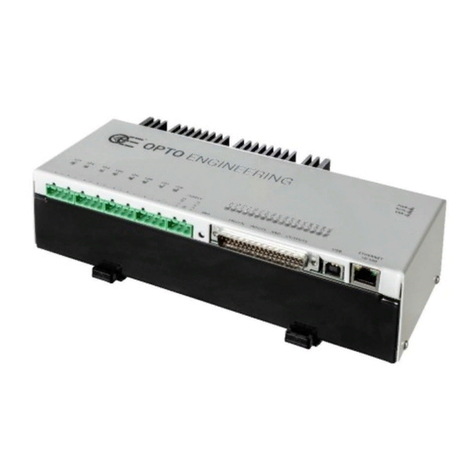
opto engineering
opto engineering LTDVE8CH-20 instruction manual
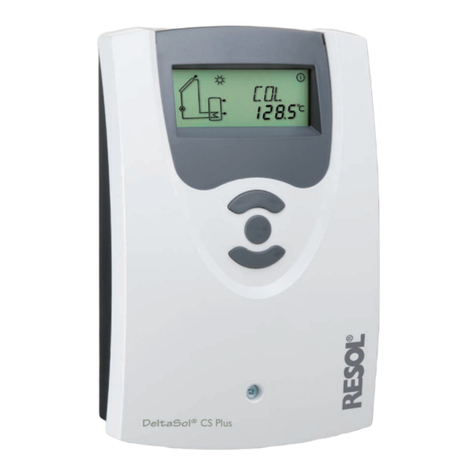
Resol
Resol DeltaSol CS Plus manual