Vogt VT Series User manual

VT-Series
Ice Maker
Model
VT40, VT60, VT100
Revision Date: 8/28/13

NOTICE
This manual is the property of the owner of this particular Vogt
Tube-Ice® machine.
Model #____________________ Serial #____________________.
It is to be left on the premises with this machine at all times. After
start-up, it should be stored in a safe place where it can be readily
available when needed for future reference in maintaining
troubleshooting or servicing.
Failure to comply with this notice will result in unnecessary
inconvenience and possible additional expenses.
This manual is intended as an informational tool for the installation,
operation, maintenance, troubleshooting, and servicing of this
equipment. If an existing situation calls for additional information
not found herein, we suggest that you contact your distributor first.
If further assistance or information is needed, please feel free to
contact the factory at 502-635-3000 or FAX at 502-635-3024.
IMPORTANT: The Warranty Registration/Start-Up Report found in
the front of this manual is to be completed and returned to the factory
promptly after the official start-up.
Please return to: VOGT ICE, LLC
1000 W. Ormsby Ave.
Louisville, KY 40210

FOREWORD
Vogt Ice
®
, LLC, strives to provide a quality product that is time-tested and will
provide years of dependable service to its customers.
Skilled craftsmen have carefully assembled your Vogt
®
VT Series ice maker using
material components and parts available from the leading vendors and producers of
the highest quality refrigeration equipment in our industry. You have invested in
quality equipment, and we pledge to support your needs and requirements after the
sale.
This manual is provided to aid the service technician and users in the installation,
operation, and maintenance of your equipment. Before attempting to install and
start the machine, the installer should read and understand each section of this
manual.
If, at any time, you encounter conditions that we have not addressed in this manual,
we welcome you to write or call Vogt
®
Ice, LLC and we will give your questions our
immediate attention and reply.
Vogt Ice®, LLC
1000 W. Ormsby Avenue
Suite 19
Louisville, KY 40210
(502) 635-3000
(502) 634-3024 Fax


TABLE OF CONTENTS
General Information - Section 1
History of Company............................................................................................. 1-1
Receipt of Your Ice Machine................................................................................ 1-2
Installation Information - Section 2
Important Safety Notice ....................................................................................... 2-1
Machine Dimension............................................................................................. 2-2
Machine Weights & Refrigerant Line Sizes.......................................................... 2-2
Ice Chute Cutout ................................................................................................. 2-3
Water Connections.............................................................................................. 2-4
Water Flow Rates / Water Tank Capacity ............................................................ 2-4
Electrical Connections ......................................................................................... 2-5
Air Cooled Condenser Electrical Connections .................................................... 2-6
Lowside Electrical Connections ..............................................................................2-6
Air Cooled Condenser Installation ....................................................................... 2-7
Air Cooled Condenser Wiring (Kramer) ............................................................... 2-9
Air Cooled Condenser Wiring (KeepRite) .......................................................... 2-10
Air Cooled Condenser Connections......................................................................2-12
Storing Ice – Bin Thermostat Mounting ............................................................. 2-14
Model Specifications and Wiring Diagrams - Section 3
Model Specifications............................................................................................ 3-1
Model Number Structure ..................................................................................... 3-2
Initial Startup - Section 4
Startup Procedure ............................................................................................... 4-1
Circuit Breakers & Lowside Control Panel Front .................................................. 4-2
Service Valve Locations ...................................................................................... 4-3
Adding Refrigerant............................................................................................... 4-4
Suction Line Access Port..................................................................................... 4-4
Removing Refrigerant.......................................................................................... 4-5
Electrical Controls - Section 5
Explanation of Controls........................................................................................ 5-1
Startup & Standby Mode ..................................................................................... 5-1
Freeze Mode ...................................................................................................... 5-1
PLC & Freezer Timer .......................................................................................... 5-1
Harvest Mode ...................................................................................................... 5-2
Harvest Hold Pressure Switch
(Increasing Harvest)
............................................... 5-2
Pumpdown Mode................................................................................................. 5-2
Clean Mode ......................................................................................................... 5-3
Fault Mode & Faults Designations ....................................................................... 5-3
PLC Input / Output Table ..................................................................................... 5-4
Electrical Schematic
(Standard - Air Cooled)
.......................................................... 5-5
Electrical Schematic
(CE - Water Cooled)
.............................................................. 5-6
Air Cooled Condenser Electrical Schematic (Kramer).......................................... 5-7
Air Cooled Condenser Electrical Schematic (KeepRite)..........................................5-8
Lowside Control Panel Layout .......................................................................... 5-10

Electrical Controls - Section 5 (Continued)
Condensing Unit Electrical Schematic
(Standard)
............................................... 5-11
Condensing Unit Control Panel Layout
(Standard)
.............................................. 5-12
Condensing Unit Electrical Schematic
(CE)
........................................................ 5-13
Condensing Unit Control Panel Layout
(CE)
...................................................... 5-14
Maintenance - Section 6
Preventive Maintenance ..................................................................................... 6-1
Preventive Maintenance Program ....................................................................... 6-2
Air Cooled Condenser Cleaning .......................................................................... 6-3
Compressor Oil ................................................................................................... 6-3
Chopper Gear Reducer Oil .................................................................................. 6-4
Water Distributor ................................................................................................. 6-4
Troubleshooting - Section 7
Machine Fault Light ............................................................................................ 7-1
Control Power Light ............................................................................................ 7-1
Machine Fault Table...............................................................................................7-1
PLC ..................................................................................................................... 7-2
Damaged Bin Control Sensor .............................................................................. 7-2
Machine Inoperative ............................................................................................ 7-3
Machine “Freeze-Up”........................................................................................... 7-4
Additional Troubleshooting ................................................................................. 7-5
Service Operations - Section 8
Principle Of Operation ........................................................................................ 8-1
Pressure Switches .............................................................................................. 8-2
CoreSense
(Copeland Compressor Protection
)........................................................ 8-3
Bin Control
(Electronic Temperature Control)
........................................................... 8-4
PLC
(Programmable Logic Controller)
...................................................................... 8-5
Compressor......................................................................................................... 8-6
TXV & Solenoid Valve ......................................................................................... 8-7
Adjusting TXV...................................................................................................... 8-8
Inlet Pressure Regulator...................................................................................... 8-9
Water Distributor / Tank Parts ........................................................................... 8-10
Chopper Assembly ........................................................................................... 8-11
Evaporator Housing Covers .............................................................................. 8-12
Freeze Cycle Piping Schematic
(No Hot Gas Loop)
............................................ 8-13
Harvest Cycle Piping Schematic
(No Hot Gas Loop)
........................................... 8-14
Freeze Cycle Piping Schematic
(With Hot Gas Loop)
.......................................... 8-15
Harvest Cycle Piping Schematic
(With Hot Gas Loop)
......................................... 8-16
Freeze Cycle Piping Schematic
(With Suction Stop Valve)
......................................8-17
Harvest Cycle Piping Schematic
(With Suction Stop Valve)
.....................................8-18
Replacement Parts List .................................................................................... 8-19
Options and Accessories - Section 9
Voltage Monitor
(Wagner Model DTP-3)
...................................................................9-1
Remote Switch
(Includes Ice/Off/Clean selector switch, start button & fault light)
...........9-3
Remote Switch Box Wiring Schematic....................................................................9-4

Vogt®VT Service Manual 1-1
General Information
1. General Information
H
ISTORY
OF
C
OMPANY
Henry Vogt Machine Co. was founded as a small machine shop in Louisville, Kentucky in
1880. In 1938, Vogt built the first Tube-Ice®machine and revolutionized the ice-making
industry. Our first “sized-ice” machine quickly replaced the old can-ice plants, which required
much hard labor and large amounts of floor space for freezing, cutting, and crushing ice by
hand.
Today, Vogt Ice
, LLC carries on the tradition as one of the world’s leading producers of ice-
making equipment.
Preview
Vogt
VT Series ice machines are built with the skill in engineering and fabrication
that we have learned in over a century of ice machine manufacturing.
Furnished with your machine is the “Certificate of Test”--the report of operating data that is a
record of the unit’s satisfactory operation on our factory test floor.
This manual is designed to assist you in the installation, start-up, and maintenance of your
unit. Your VT®machine will give you many years of service when you install it, maintain it,
and service it properly.
Please read your manual carefully before attempting installation, operation, or servicing of this
piece of equipment.
If you have additional questions, please call your distributor. Also, feel free to phone the
factory direct at (502) 635-3000 or 1-800-853-8648.

1-2 Vogt®VT Service Manual
General Information
Receipt Of Your Ice Machine
! CAUTION !
Only service personnel experienced in refrigeration and
qualified to work on high amperage electrical equipment should
be allowed to install or service this VT ice machine.
Eye protection should be worn by all personnel
working on or around the VT machine.
It is very important that you are familiar with and adhere to
all local, state, and federal, etc. ordinances and laws regarding
the handling, storing, and use of R404A.
! CAUTION !
Inspection.
As soon as you receive your machine, inspect it for any damage. If damage is suspected,
note it on the shipper’s papers (i.e., the trucker’s Bill of Lading). Immediately make a separate written
request for inspection by the freight line’s agent. Any repair work or alteration to the machine without the
permission of the Vogt Ice can void the machine’s warranty. You should also notify your Vogt distributor or
the factory.
Safety Tags and Labels.
Be sure to read and adhere to all special tags and labels attached to valves
or applied to various areas of the machine. They provide important information necessary for safe and
efficient operation of your equipment.

Vogt®VT Service Manual 2-1
Installation Instructions
2. Installation Information
Important Safety Notice.
This information is intended for use by individuals possessing adequate
backgrounds of electrical, refrigeration and mechanical experience. Any attempt to repair major equipment
may result in personal injury and property damage. The manufacturer or seller cannot be responsible for
the interpretation of this information, nor can it assume any liability in connection with its use.
Special Precautions To Be Observed When Charging Refrigeration Systems.
Only
technically-qualified persons, experienced and knowledgeable in the handling of refrigerant and operation
of refrigeration systems, should perform the operations described in this manual. All local, federal, and
EPA regulations must be strictly adhered to when handling refrigerants.
If a refrigeration system is being charged from refrigerant cylinders, disconnect each cylinder when empty
or when the system is fully charged. A gage should be installed in the charging line to indicate refrigerant
cylinder pressure. The cylinder may be considered empty of liquid R404A refrigerant when the gage
pressure is 25 pounds or less, and there is no frost on the cylinder. Close the refrigerant charging valve
and cylinder valve before disconnecting the cylinder. Loosen the union in the refrigerant charging line--
carefully to avoid unnecessary and illegal release of refrigerant into the atmosphere.
! CAUTION !
Immediately close system charging valve at commencement of defrost or thawing
cycle if refrigerant cylinder is connected. Never leave a refrigerant cylinder
connected to system except during charging operation. Failure to observe either
of these precautions can result in transferring refrigerant from the system to the
refrigerant cylinder, over-filling it, and possibly causing the cylinder to rupture
because of pressure from expansion of the liquid refrigerant brought on by an
increase in temperature.
! CAUTION !
Always store cylinders containing refrigerant in a cool place. They should never be exposed to
temperatures higher than 110°F and should be stored in a manner to prevent abnormal mechanical shocks.
Also, transferring refrigerant from a refrigeration system into a cylinder can be very dangerous and is not
recommended.
! CAUTION !
It is not recommended that refrigerant be transferred from a refrigeration system
directly into a cylinder. If such a transfer is made, the refrigerant cylinder must be
an approved, CLEAN cylinder--free of any contaminants or foreign materials--and
must be connected to an approved recovery mechanism with a safety shutoff
sensor to assure contents do not exceed net weight specified by cylinder
manufacturer or any applicable code requirements.
! CAUTION !

2-2 Vogt®VT Service Manual
Installation Instructions
FIGURE 2-1
Ice Machine Dimensions
Unit
"A"
"B"
"C"
"D"
"E"
"F"
VT40 72 5/8" 27" 24 3/8" 50 3/4" 44" 34"
VT60 89" 39 1/2" 30 1/2" 63 1/4" 57.5 68"
VT100 44 7/8" N/A N/A
TABLE 2-1
Ice Machine Dimensions
Remote Weights
Skid Mounted Weights
Model
Lowside
Condensing Unit
Model
Skid Mounted
VT40 520 lbs. 975 lbs. VT-40 1,525 lbs.
VT60 650 lbs. 1330 lbs. VT-60 2290 lbs.
VT100 1,850 lbs. 400 lbs. (condenser) VT-100 ----------
TABLE 2-2
Weight Of Machines
Suction
Hot Gas
Liquid
Remote Condenser
Model
Line
Line
Line
Discharge
Liquid Return
VT40 1 3/8 OD 7/8 OD 5/8 OD N/A N/A
VT60 1 1/8 OD 7/8 OD
VT100 1 5/8 OD 1 3/8 OD OD 7/8 OD
Note: Split systems will be supplied with Rota-lock adapters to connect the highside to the lowside
TABLE 2-3
Refrigerant Line Sizes
Machine Clearances:
A minimum three (3) feet of clearance is recommended around entire ice
machine. This will provide sufficient area for service and air flow.
Evaporator Installation:
Mount evaporator section (lowside) on storage area capable of sustaining its
weight and secure by thru bolting.
Note: Ambient at the lowside should remain between 50º
F
–105º
F. Makeup wa
ter temperature should
not drop below 40º
F. Machine may experience problems if operated outside of these ranges.
58" - VT40, VT60
71" - VT100
& VT80

Vogt®VT Service Manual 2-3
Installation Instructions
Piping Installation:
Use ACR refrigeration tubing and nitrogen purge during brazing to prevent formation
of copper oxide. For piping runs exceeding 25’, consult a reliable piping manual (Copeland, Heatcraft, or Vilter)
for proper pipe sizing. Heat sink all ball valves and remove Schrader valve core prior to brazing. Pressure test
piping for leaks. Evacuate lines to 500 microns prior to starting machine.
Chute Location:
Using drawing and table below, determine ice machine location so that it is centered on
bin. Place ice machine on ice storage unit and bolt in place. Machine must be level front to back and side
to side for proper operation.
FIGURE 2-2
Ice Chute Cutout Location
Split System
Skid Mounted
27” (VT40)
39 1/2” (VT60 & VT100)
27” (VT40)
39 1/2” (VT60 & VT100)

2-4 Vogt®VT Service Manual
Installation Instructions
FIGURE 2-3
VT Lowside Water and Electrical Connections – Rear View
Makeup Water Flow
VT40
VT60
VT100
Usage - Gallons /100 lbs of Ice 12 12 12
Flow rate – Gallons / minute 0.38 0.54 0.80
Flow rate – Gallons / hour 22.5 32.5 48.0
Water Tank Capacity – Gallons 6 7
Note: Water usage and flow rates base on 70°F water with no blowdown
TABLE 2-4
MakeUp Water Requirements / Flow Rates
Makeup water, water tank drain and water tank overflow are ½” FPT connections

Vogt®VT Service Manual 2-5
Installation Instructions
Wiring And Electrical Connection.
! WARNING !
Only service personnel experienced in refrigeration and qualified to work with high
voltage electrical equipment should be allowed to install or work on the Vogt
®
VT
Series Ice machine.
! WARNING !
Main Power:
Power for the entire ice machine will be supplied at the condensing unit.
Refer to the table below to properly size wiring connections. A fused disconnect switch must be provided
near the condensing unit of the ice machine. Connect 3 phase power to compressor contactor L1, L2, L3 for
operation of the VT ice machine and its controls. If one phase (leg) of the 3 phase power is higher or lower
(“Wild”), it should be connected to terminal #L2. Connect the “Ground” wire to the “Ground” terminal provided.
Electrical Data
VT40
VT60
VT100
Volts/ Phase/ Hertz
208/230-3-60 208/230-3-60 208/230-3-60 460-3-60
Kramer KeepRite Kramer KeepRite
Total F.L.A.
46.1 56.4 80.6 79.9 38.7 40.0
Minimum Circuit Ampacity
54.0 66.9 97.1 95.9 47 48
Maximum Fuse Size
85 110 165 80
TABLE 2-5
Electrical Requirements
FIGURE 2-4
Main Power Connection

2-6 Vogt®VT Service Manual
Installation Instructions
Air Cooled Condenser Wiring (VT100 with KeepRite Condenser) :
Run four #14 AWG wires
from the terminals A, B, T4 and T5 on the condensing unit control panel terminal block to the air cooled
condenser control panel.
FIGURE 2-5
Condensing Unit Terminal Blocks
Lowside Electrical Connections:
Run 11 #14 AWG or larger wires run from the Lowside control panel
terminal block to the condensing unit (highside) control panel terminal block.
TABLE 2-6
Lowside to Highside Wire
FIGURE 2-6
Lowside Unit Terminal Block
Note: Machine is supplied with a remote “on/off” connection on the lowside terminal block. If a remote
“On/Off” switch is used, remove jumper between #18 & #X1 and connect switch to these terminals.
Number of wires
Wire
Size
(AWG)
Wire #
5 16 (Red) 1, 2, 3, Y2, Y5
4 16 (Blue) X5, X6, X7, 12
2 14 (Black) 1A, 2A
1 14 (Green) GND
Standard Voltage Machine
200/230V or 400/460V, 3PH, 50/60HZ
REMOTE “ON/OFF” SWITCH TO LOWSIDE

Vogt®VT Service Manual 2-7
Installation Instructions
Power is supplied to the lowside through circuit breaker (CB1) located in the condensing unit control panel.
See diagram below.
FIGURE 2-7
Condensing Unit Circuit Breakers (200/230V)
Air Cooled Condenser Installation (VT100):
Ice making systems with remote condensers are
trapped internally. A trap leaving the compressor is not necessary. On vertical runs a short radius “P” trap
should be installed every 15’ to 20’ of vertical rise to facilitate oil flow. Horizontal runs should be sloped in
direction of refrigerant flow 1” for every 20’ of run. The condenser should be securely mounted in a place
capable of sustaining its weight.
FIGURE 2-8
Condenser Piping (VT100) and Recommended Traps
Condensing unit control panel
10A
15A
CB1 supplies power
to lowside unit

2-8 Vogt®VT Service Manual
Installation Instructions
Teflon Seal
12A2600T01 (for 1 1/4”-12 thread fitting)
12A2600T03 (for 1 3/4”-12 thread fitting)
FIGURE 2-10
VT100 Condenser Refrigerant Line Connections
Rota-lock Adapter
Note: Rota-lock adapters
supplied with machine
Note: Rota-lock male
adapter on ice machine
Must solder with 45% silver solder
Liquid return from
Air Cooled Condenser
(7/8” line)
Discharge gas to
Air Cooled Condenser
(1 3/8” line)
Female Rota-lock Adapters:
12A2396A0701 – for 1 ¼”-12 F x 7/8” Sweat (Solder)
(Return Line from condenser)
12A2396A0601 – for 1 ¾”-12 F x 1 3/8” Sweat (Solder)
(Discharge to condenser)

Vogt®VT Service Manual 2-9
Installation Instructions
Air Cooled Condenser:
The air cooled condenser will be wired to the condensing unit control panel.
Run two #14 AWG wires and a ground wire from the condensing unit control panel to the Air Cooled
condenser control panel.
208/230V
460V
FIGURE 2-11A
Kramer VT100 Remote Air Cooled Condenser Wiring
Note: Fan control pressure switch is located in air cooled condenser control panel on VT100’s with remote
condensers. On VT40’s and VT60’s, fan control pressure switch is location on condensing unit (highside).
To Ice Machines
condensing unit
control panel
To Ice
Machines
condensing unit
control panel

2-10 Vogt®VT Service Manual
Installation Instructions
FIGURE 2-11B
KeepRite VT100, 200/230V Remote Air Cooled Condenser Wiring
Note: Fan cycling switch, FCC2 (Danfoss) for fan motor #2, is not factory set.
Switch must be set in the field before startup. Cut Out = 210 psi, Diff = 25 psi.
Use an accurate gage to set, not the scale on the pressure switch.

Vogt®VT Service Manual 2-11
Installation Instructions
FIGURE 2-11C
KeepRite VT100, 400/460V Remote Air Cooled Condenser Wiring
Note: Fan cycling switch, FCC2 (Danfoss) for fan motor #2, is not factory set.
Switch must be set in the field before startup. Cut Out = 210 psi, Diff = 25 psi.
Use an accurate gage to set, not the scale on the pressure switch.

2-12 Vogt®VT Service Manual
Installation Instructions
Teflon Seal
12A2600T01 (for 1 1/4”-12 thread fitting)
12A2600T03 (for 1 3/4”-12 thread fitting)
FIGURE 2-12
VT Lowside Connections
Rota
-
lock Adapter
Teflon Seal
Where U
sed
Part # Description Part # VT40 VT60
12A2396A0501 1 1/8” IDS X 1 1/4”-12Thrd 12A2600T01 N/A Hot Gas Line
12A2396A0601 1 3/8” IDS X 1 3/4”-12Thrd 12A2600T03 Suction Line Suction Line
12A2396A0701 7/8” IDS X 1 1/4”-12Thrd 12A2600T01 Liquid & Hot Gas line Liquid Line
TABLE 2-5
Rota-lock Adapters
Note: See Refrigerant Line Size TABLE 2-3 for line sizes
Rota-lock Adapter
1 3/8” IDS X 1 3/4”-12 Threads
1 1/8” IDS X 1 1/4”-12 Threads
7/8” IDS X 1 1/4”-12 Threads
Note: Rota-lock fittings
supplied for both lowside
and highside
Must solder with 45% silver
Liquid Line
Suction Line
Hot Gas Line
Rota-lock Fitting
(on lowside & condensing unit)
This manual suits for next models
3
Other Vogt Ice Maker manuals

Vogt
Vogt TUBE-ICE P-118F User manual

Vogt
Vogt P-24AL User manual
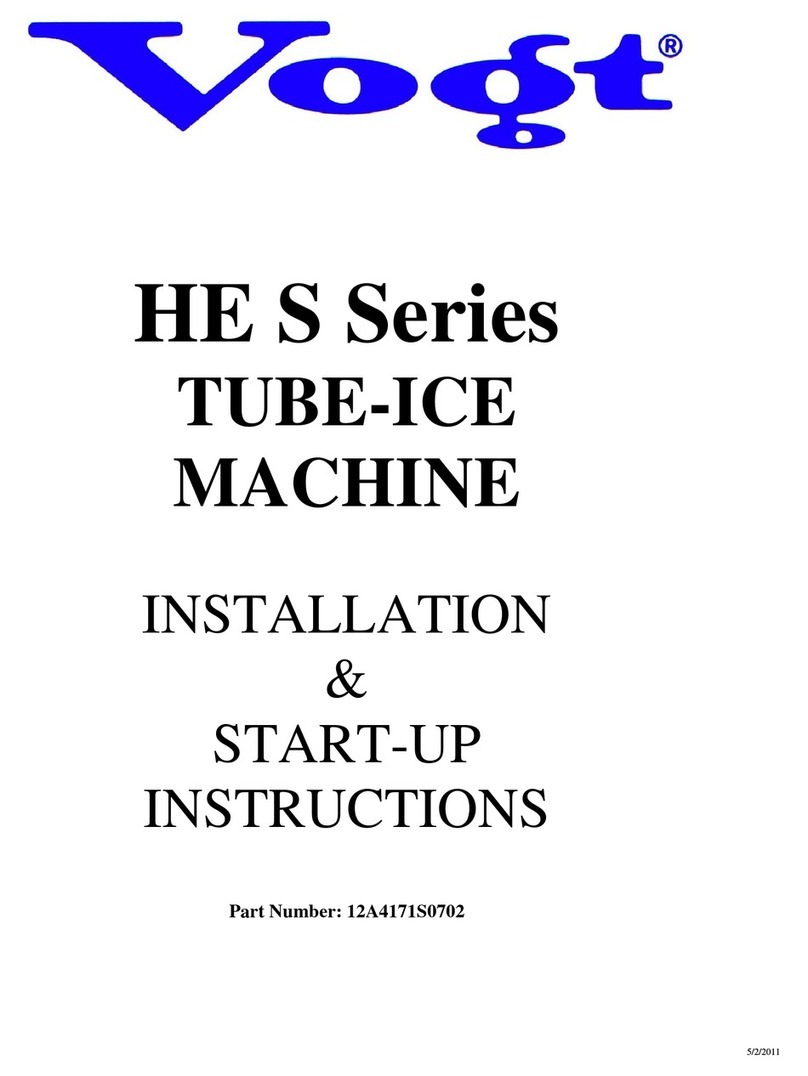
Vogt
Vogt HE S Series Installation manual
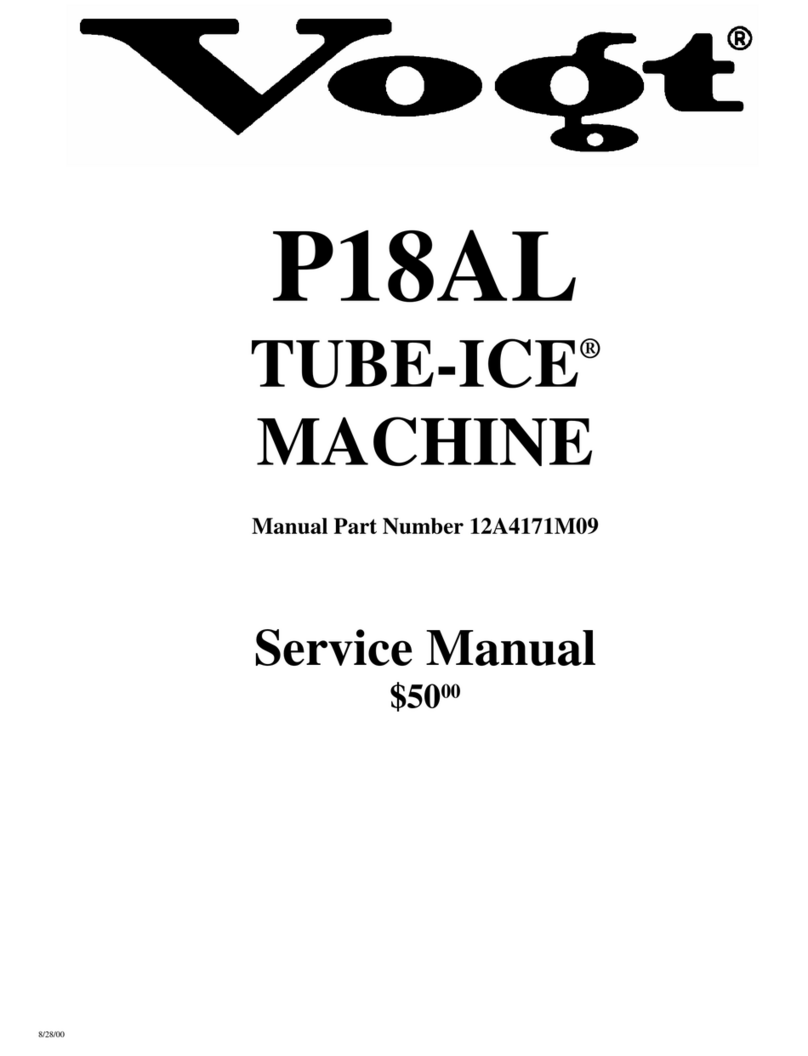
Vogt
Vogt P18AL TUBE-ICE User manual
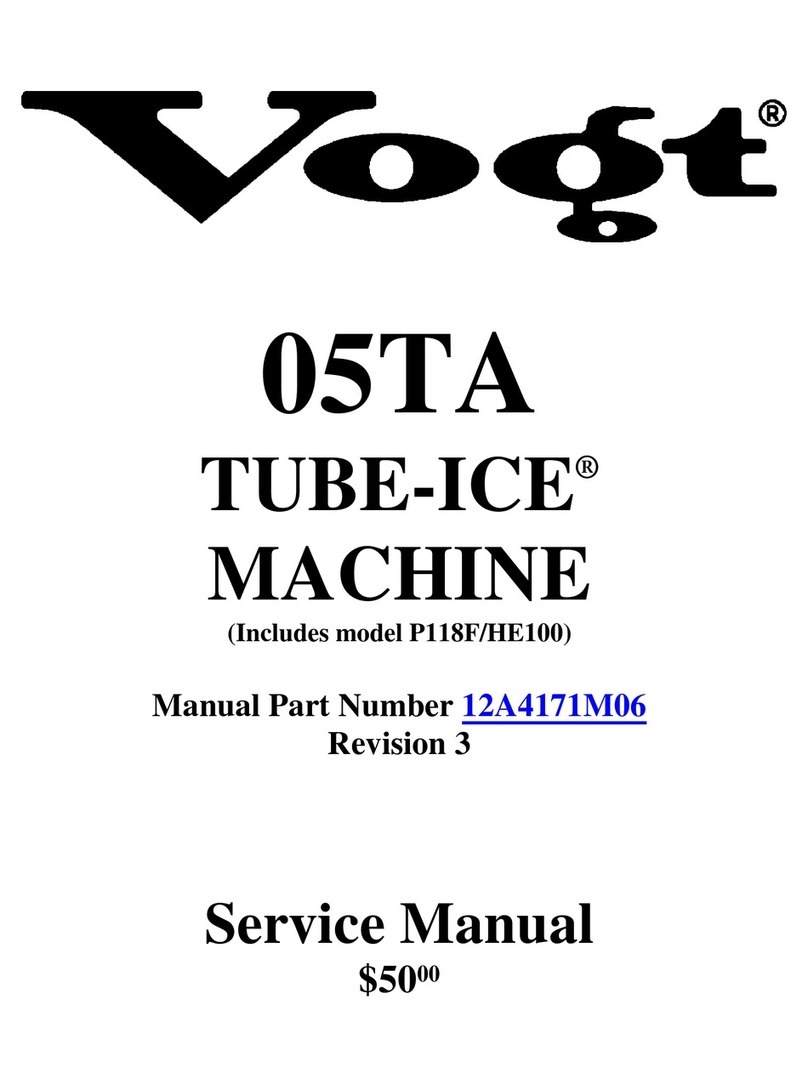
Vogt
Vogt TUBE-ICE 05TA User manual

Vogt
Vogt TUBE-ICE P34FXL User manual
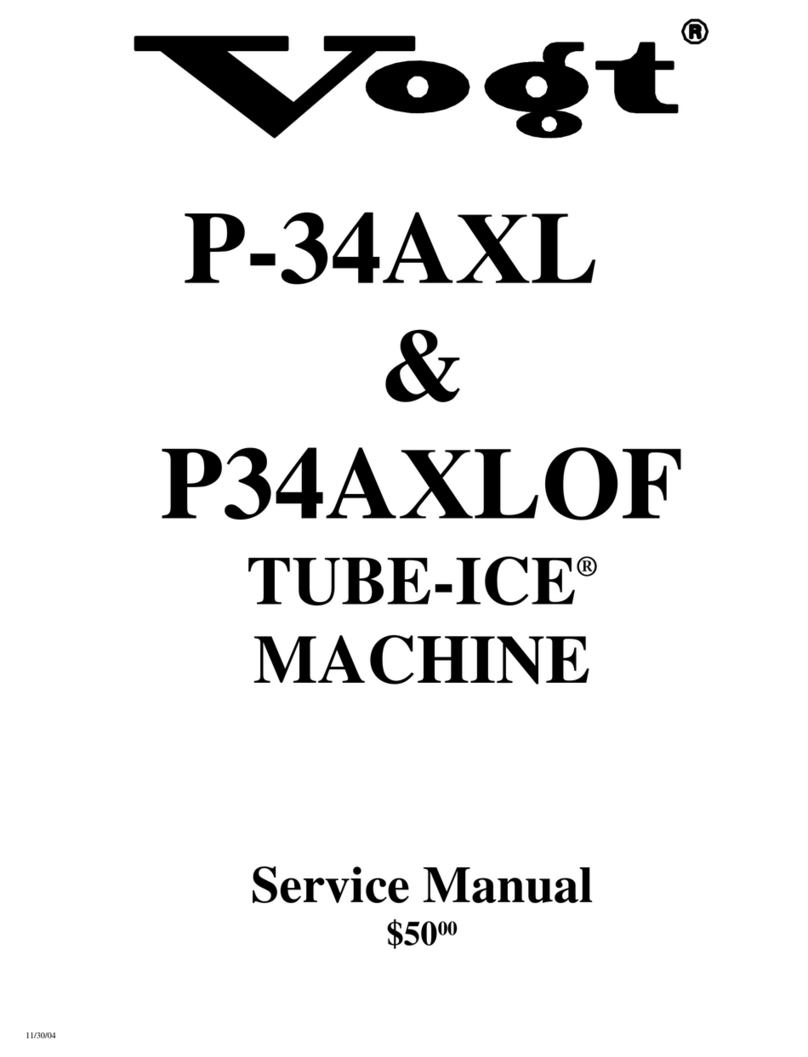
Vogt
Vogt TUBE-ICE P-34AXL User manual
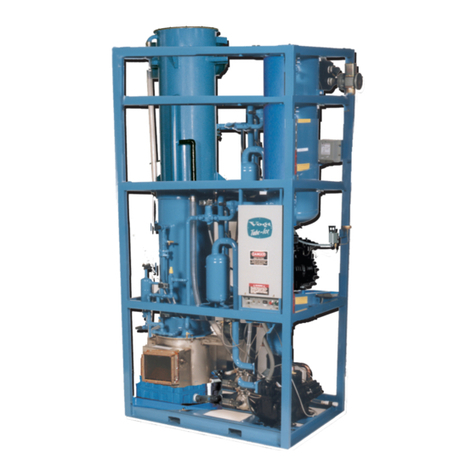
Vogt
Vogt TUBE-ICE 10TA User manual
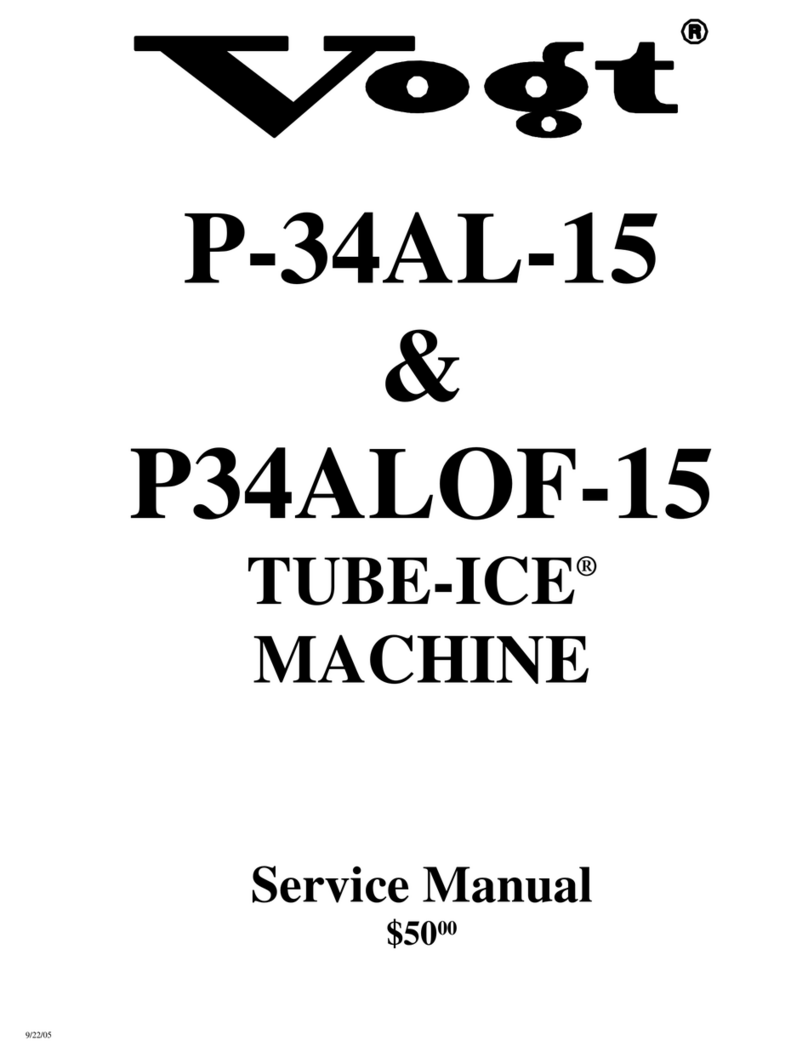
Vogt
Vogt P-34AL-15 User manual
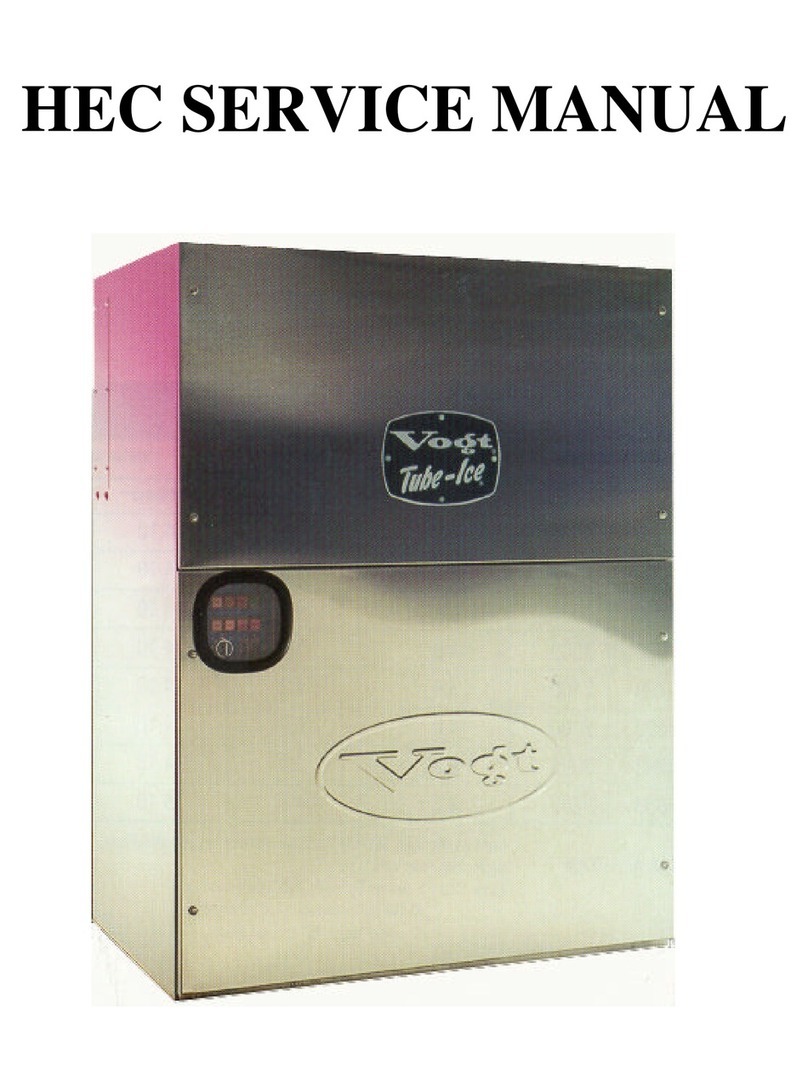
Vogt
Vogt HEC-10 User manual
Popular Ice Maker manuals by other brands
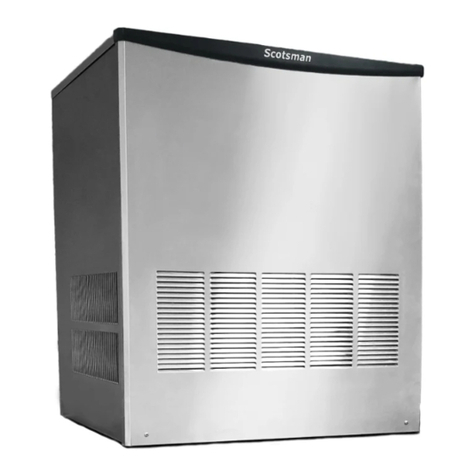
Scotsman
Scotsman BC0530 Service manual
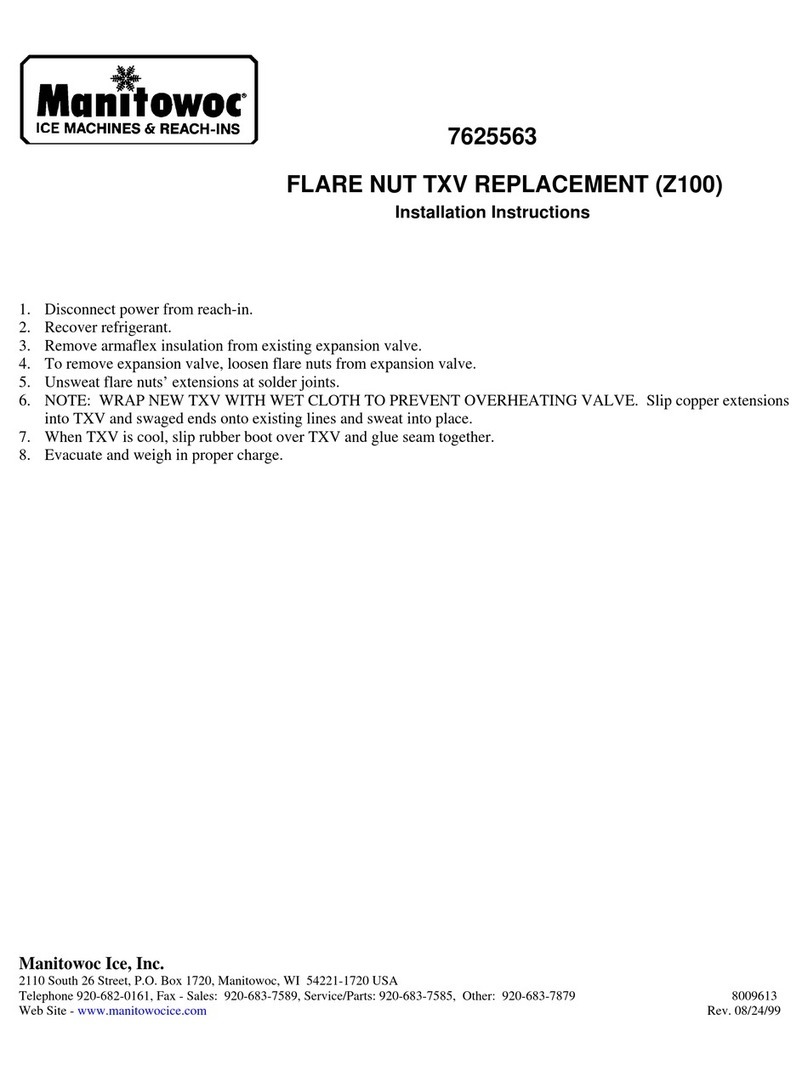
Manitowoc
Manitowoc FLARE NUT TXV REPLACEMENT (Z100) 7625563 installation instructions
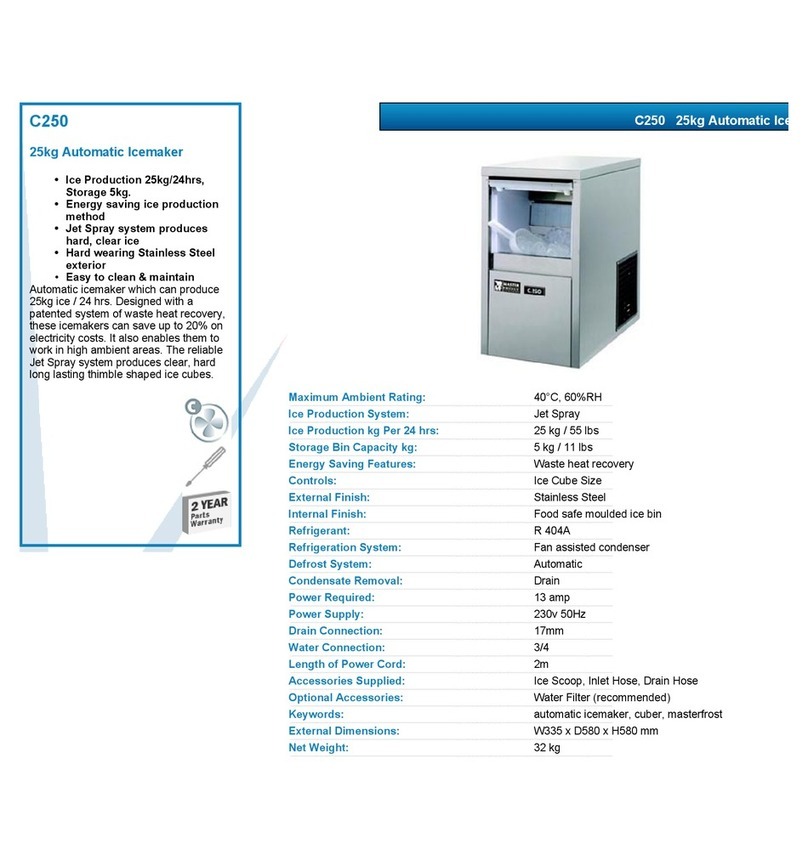
Master Frost
Master Frost C250 datasheet

Scotsman
Scotsman FME1200R Service manual

KitchenAid
KitchenAid KUIS18PNXB0 Use & care guide

Lacor
Lacor PRO 69320 Instructions for use and maintenance