Voltdrive ShiftGuard User manual

VOLTDRIVE s.r.o.,
Háj 365 (MICOS TELCOM premises), 798 12 Kralice na Hané, Czech Republic
Tel.: +420 582 307 603, Fax: +420 582 307 688
1
ShiftGuard
USER MANUAL
BASIC PURPOSE
The ShiftGuard PLC (Power Line Communication)
modules are communication components for
electric vehicle charging infrastructure. These PLC
modems can also be used for transmission of binary
signals in a wide range of applications. For example,
they are used instead of conventional power cables
to transmit information on the current tariffs of
electricity meters. When installed in the VoltDrive
charging infrastructure system, the ShiftGuard PLC
modems are used to transmit information from the
HomeGuard residual capacity meter of the electrical
connection to the electric vehicle charging station.
It enables the PortGuard charging control unit to
set the charging current exactly according to the
current available at the point of supply (at the
distribution meter). The communication between
the HomeGuard Residual Capacity Meter and the
PortGuard charging control unit can also be done
by means of RS485 twisted pair bus, however,
such a cable is usually not installed between the
input of the power supply point and the charging
station. In case the installation uses the ShiftGuard PLC modems, the charging station can be placed anywhere
after the distribution meter. When used in the tariff control system, a pair of the ShiftGuard PLC modems replaces
the communication cable carrying information on the current tariff. PLC communication enables the distribution of
information on the current tariff to any home appliance in a flat or a house.
MAIN FEATURES
¬PLC modems for the VoltGuard system and the binary replicator
¬Internal power supply of 230V AC, 50Hz
¬PLC_IN – a pair of digital inputs 230V AC
¬PLC_OUT – a pair of bistable relays 16A/230V AC
¬Combined input and output installation
¬Possibility of setting Master and Slave nodes
¬RS485 communication line for setting and data input
¬Variable system of node addressing
¬Possibility of data transfer through 230V Ac power network within one distribution transformer
¬Robust S-FSK modulation within the CENELEC D-band
¬LED status indication
¬Compact DIN rail box dimensions – 5 modules

VOLTDRIVE s.r.o.,
Háj 365 (MICOS TELCOM premises), 798 12 Kralice na Hané, Czech Republic
Tel.: +420 582 307 603, Fax: +420 582 307 688
2
BLOCK DIAGRAM
DESCRIPTION
The PLC_IN and PLC_OUT modems are primarily used for transmitting the signal within the VoltGuard electric vehicle
charging infrastructure system. They can also be used as the replicators of digital signals in a wide range of applica-
tions. For example, they are used to transmit the tariff signal to the appliances switched on only at the particular tariff
period. This solution can replace the cabling that is difficult to install, for example, in historical houses or new large
buildings.
VOLTGUARD SYSTEM
The VoltGuard system is used for optimization of electric vehicle charging in areas with limited charging current values.
A typical example is a detached house with its own consumption that needs to charge an electric vehicle. In this case
you can set a very low available current capacity, so that the usual activities of the residents were not limited and the
electric vehicle charging was not significantly delayed. Or you can install the VoltGuard system that always sets the
maximum residual current value on the charging station (residual current = total input breaker capacity – immediate
home consumption) and regulates it dynamically according to household operations. The communication between the
HomeGuard residual capacity meter and the PortGuard charging control unit can be done by means of a twisted pair or
the PLC communication using the ShiftGuard modules.
The communication between the HomeGuard and the PortGuard modules is done by means of RS485 twisted pair.
Before it is connected, you have to set the modem connected to the HomeGuard module as the Master modem and the
modem connected to the PortGuard module as the Slave modem. The modems communicate with sufficient frequency
to ensure reliable dynamic switching of the residual current value in the PortGuard module.
2 x 230V AV
input
2 x 16A relay
output
DIP switch
domain/address
Control
microprocessor PLC modem
LED indication RS485 AC/DC
power supply

VOLTDRIVE s.r.o.,
Háj 365 (MICOS TELCOM premises), 798 12 Kralice na Hané, Czech Republic
Tel.: +420 582 307 603, Fax: +420 582 307 688
3
STATE REPLICATOR (RIO)
The Master modem is fitted with a pair of digital inputs replicated through PLC communication to the selected digital
outputs (bistable relay) of the Slave modem. Using a serial parameterization terminal, you can set which input will
be replicated on which output, or you can define that an input will be negated on a particular output. Once the power
supply is on, the relay remains in the same state as without power and when communication is established the relay
switches to the state corresponding to the particular input within few seconds. When communication is interrupted, the
output relay switches to the state defined as the emergency state. Once communication is re-established, the output
relay switches to the state corresponding to the particular input again.
CONNECTION DIAGRAM AND LED INDICATION
Connection diagram:
RIO system LED indication
LEDLED MasterMaster SlaveSlave
1 - Yellow Input voltage available Input voltage available
2 - Green Voltage available after stabilizer Voltage available after stabilizer
3 - Red True value read at IN2 input True value on DIGIOUT2.
LED indicator on, the device receives information on Log1 from
the counterparty (the state corresponds to the relay state: ON/
OFF)
4 - Red True value read at IN1 input True value on DIGIOUT1.
The LED indicator is on, the device receives information on Log1
from the counterparty (the state corresponds to the relay state:
ON/OFF)
5 - Blue The internal system of status machine interruptions and timing running in the device. The LED indicator blinks, changes its state
every 1 s.
6 - Blue The device has sent the packet (the state change indicates
sending)
The device has received the packet (the state change upon
receiving the packet).
7 - Red In case the LED indicator is on or blinks, the device has initiated the peripheries and the processor started communicating with
the modem
∫The LED indicator is on: DIO sends status information about the digital inputs and rewrites the Switch data on the output – the
DIO device receives the data through the RS485 input line, encodes the data into the packet sent by PLC communication and
writes the Switch data on the RS485 output.
∫The LED indicator blinks: a console running in the DIO device – the PLC packets transfer only status information about the digital
inputs.
8 - Blue OFF – the device is used as the Master digital input ON – the device is used as the Slave digital output

VOLTDRIVE s.r.o.,
Háj 365 (MICOS TELCOM premises), 798 12 Kralice na Hané, Czech Republic
Tel.: +420 582 307 603, Fax: +420 582 307 688
4
CONFIGURATION
SERIAL PARAMETERIZATION TERMINAL
RS485 is used for transmitting information through the serial link in the VoltGuard system or for setting the RIO system
parameters. The RIO system settings require a built-in serial terminal on the RS485 line.
Connection
RS485 connection parameters: ....................................................................... 9600, 8n1
The control terminal uses the RS485 interface in the semi-duplex mode. Once the power supply is on, the module
automatically sends the basic menu. In case the terminal is connected after the power supply on the modules is on, the
menu is sent immediately after ENTER is pressed again.
Basic menu
The basic menu enables the selection of four options. The selection is done by entering a number in square brackets
and pressing ENTER. In case you select a wrong option, the menu is automatically displayed again. You can use this fea-
ture when the display terminal is not ready after the power supply is on, i.e. after pressing ENTER the menu is displayed
again. The basic menu is displayed as follows:
----- DIO Terminal -----
[1] List digital inputs
[2] Slave settings list
[3] Change slave setting
[4] Save settings
Selection :
Option: [1] List digital inputs
The first option displays the way the processor interprets the digital inputs DIG_IN1 and DIG_IN2. In case the number 1
is displayed, 230V/50Hz voltage is connected on the DIG_IN input. Once the values are listed, the basic menu is auto-
matically displayed. The option “List digital inputs” is displayed as follows:
Selection :1
> Digital input 1 state : 0
> Digital input 2 state : 1
----- DIO Terminal -----
[1] List digital inputs
[2] Slave settings list
[3] Change slave setting
[4] Save settings
Selection :
Option: [2] Slave settings list
The master module is planned to enable controlling several slave devices. The current implementation enables trans-
ferring the setting only for slave 0 through PLC communication. The communication protocol for PLC is prepared for
slave type multi-node connections for future use. The option lists the setting for each slave and each input. This is
displayed in two lines. The setting is then interpreted by the slave. The input settings are described in next chapter. The
final list is displayed as follows:
Selection :2
> Slave 0, master input 1 controls : disabled and normal
> Slave 0, master input 2 controls : both and normal
> Slave 1, master input 1 controls : direct and normal
> Slave 1, master input 2 controls : direct and normal
> Slave 2, master input 1 controls : direct and normal
> Slave 2, master input 2 controls : direct and normal
> Slave 3, master input 1 controls : direct and normal
> Slave 3, master input 2 controls : direct and normal
> Slave 4, master input 1 controls : direct and normal
> Slave 4, master input 2 controls : direct and normal
> Slave 5, master input 1 controls : direct and normal

VOLTDRIVE s.r.o.,
Háj 365 (MICOS TELCOM premises), 798 12 Kralice na Hané, Czech Republic
Tel.: +420 582 307 603, Fax: +420 582 307 688
5
> Slave 5, master input 2 controls : direct and normal
> Slave 6, master input 1 controls : direct and normal
> Slave 6, master input 2 controls : direct and normal
> Slave 7, master input 1 controls : direct and normal
> Slave 7, master input 2 controls : direct and normal
> Slave 8, master input 1 controls : direct and normal
> Slave 8, master input 2 controls : direct and normal
> Slave 9, master input 1 controls : direct and normal
> Slave 9, master input 2 controls : direct and normal
> Slave 10, master input 1 controls : direct and normal
> Slave 10, master input 2 controls : direct and normal
> Slave 11, master input 1 controls : direct and normal
> Slave 11, master input 2 controls : direct and normal
> Slave 12, master input 1 controls : direct and normal
> Slave 12, master input 2 controls : direct and normal
> Slave 13, master input 1 controls : direct and normal
> Slave 13, master input 2 controls : direct and normal
> Slave 14, master input 1 controls : direct and normal
> Slave 14, master input 2 controls : direct and normal
> Slave 15, master input 1 controls : direct and normal
> Slave 15, master input 2 controls : direct and normal
----- DIO Terminal -----
[1] List digital inputs
[2] Slave settings list
[3] Change slave setting
[4] Save settings
Selection :
Option: [3] Change slave setting
This item in the menu enables setting the properties of logical 0 and logical 1 interpretation on the DIG_IN input and the
way it is transferred to the output. Once the option “Change slave setting” is selected, you must enter the number of
the slave device for which the setting is to be changed, i.e. in the following list, it is the line “Enter slave (e = exit):” with
entered option 0 and then you are asked to select Input 1 or 2. The list is displayed as follows:
Selection :3
Enter slave (e = exit) :˙0
> Slave 0. Select input:
[1] Input 1
[2] Input 2
[e] Exit
Selection :
Once you select the channel for which you want to change the setting, the first part lists the device and the input you
change the setting on, see:
> Slave 0, master input 2
Next the current setting of both inputs is listed, see:
> Slave 0, master input 1 controls : disabled and normal
> Slave 0, master input 2 controls : both and normal
The list for both channels is displayed because the setting of one channel can affect the setting of the other channel.
The final list of the setting options for a particular input is displayed as follows:
Selection :2
> Slave 0, master input 2
> Slave 0, master input 1 controls : disabled and normal
> Slave 0, master input 2 controls : both and normal
[0] None/disabled
[1] Direct output
[2] Opposite output
[3] Both outputs
[4] Normal
[5] Reversed
[e] Exit
Selection :

VOLTDRIVE s.r.o.,
Háj 365 (MICOS TELCOM premises), 798 12 Kralice na Hané, Czech Republic
Tel.: +420 582 307 603, Fax: +420 582 307 688
6
The setting options are:
¬None/disabled: The input value is not transferred.
¬Direct output: The input value is directly linked to the output, i.e. Input 1 to Output 1 or Input 2 to Output 2.
¬Opposite output: The input value is linked to the opposite output, i.e. Input 1 to Output 2 or Input 2 to Output 1.
¬Both outputs: The selected input controls both outputs.
¬Normal: It sets the input behaviour. In case of Normal, log 1 on the input means switching on the output.
¬Reversed: It sets the input behaviour. In case of Reversed, log 1 on the input means switching off the output.
The changes in the setting are reflected immediately in the transferred data and the internal states of both modules,
i.e. the setting can be tested on the running modules.
Option: [4] Save settings
The last option enables saving the master module setting to the internal memory. This setting is then loaded once the
power supply is on. The result of the option is either ok or fail. The result fail means the processor internal memory
error, i.e. the written data do not match the read data.
Selection :˙4
> saving ....
> ok.
----- DIO Terminal -----
[1] List digital inputs
[2] Slave settings list
[3] Change slave setting
[4] Save settings
Selection :
SWITCH SETTING
The DIP switch on the ShiftGuard motherboard is used for setting the basic modem properties. The DIP switch enables
setting three types of parameters.
- Selecting Master/Slave or Transmitter/Receiver
- Selecting the function on the RS485 serial interface between the parameterization console and forwarding the data
communication part
- Setting the Slave unit address. Setting the Master unit address makes no sense as the Master unit transmits only for
the selected Slave addresses
DIP switch position
1 2 3 4 5 6
Select Master (0)
Or Slave (1)
Select forwarding of data communication part (0)
or configuration console (1) Address
The position of a logical 0/logical 1 on the DIP switch. The switch on the DIP switch is switched on in logical 1 position.

VOLTDRIVE s.r.o.,
Háj 365 (MICOS TELCOM premises), 798 12 Kralice na Hané, Czech Republic
Tel.: +420 582 307 603, Fax: +420 582 307 688
7
TYPE DESIGNATION AND ORDER CODE
For a specific order code depending on the device features, contact the supplier or directly the manufacturer.
ShiftGuard SG xx yy. zz
HW modification
FW modification
Internal setting
INSTALLATION AND SOLVING OPERATIONAL PROBLEMS
MASTER AND SLAVE SETTING
The selection if the unit is the Master or the Slave is done by the first switch on the DIP switch on the motherboard. The
DIP switch can be accessed after the upper cover of the terminal block is removed. This setting should be done only by a
trained installation technician.
Address setting
The setting of the address makes sense only with the Slave unit. The setting is done by the last 4 switches on the DIP
switch. In case the node is switched to the Slave mode, the setting console does not work.
Example:
Master, setting console: 01 00 00
Slave, communication, address 0: 10 00 00
DIN rail installation
The unit is mounted vertically onto the DIN rail in the switchboard. The device can be installed within the array of
modular devices on the DIN rail like breakers and contactors. It is advisable to install the Master unit right next to the
HomeGuard module and connect both units with a communication cable. The cables with a suitable cross-section are
connected according to the diagram in the chapter “Connection diagram and LED indication”.
Connection of RS485 line with HomeGuard (Master) and PortGuard (Slave)
The ShiftGuard communication modules in the VoltGuard system are used for transmitting information on residual
capacity, or for transmitting the status signals, typically information on the tariff. The connection is done through the
RS485 line. The line is connected using a usual twisted pair; a suitable cable is, for example, Lam Flexo Twin communi-
cation cable or Lam Flexo FTP. With a cable length of hundreds of meters, it is advisable to consider terminating the bus
by a termination resistor, usually up to 1000 ohms. However, it is not necessary in most cases as the bus communica-
tion speed is very low.
Switching on and checking LED status indication
Switching on the device does not require any special procedure. It is enough to connect the device to the power supply.
Once the device is switched on, it is advisory to check the LED status indication, see the chapter “Connection diagram
and LED indication”. In case the device does not work, check if PLC_IN and PLC_OUT are on the same phase. The con-
nection to a different phase may work thanks to inductive coupling between the supply conductors. However, such a
connection is unreliable. In case you cannot connect both nodes to the same phase, use the interfacial couplers (con-
tact the manufacturer) to establish the communication connection between the particular phases.

VOLTDRIVE s.r.o.,
Háj 365 (MICOS TELCOM premises), 798 12 Kralice na Hané, Czech Republic
Tel.: +420 582 307 603, Fax: +420 582 307 688
8
TECHNICAL SPECIFICATIONS
Napájení
¬Rated supply voltage Un: ..............................................................................230 V AC
¬Specified supply voltage range: .....................................................................0.9 – 1.1 Un
¬Rated frequency: ....................................................................................... 50 Hz
¬Typical receiving power: ..................................................................................1.5 W
¬Typical transmitting power: .....................................................................2.5W (peak 6W)
Digital inputs
¬Number/type: ..........................................................................2 x galvanically isolated
¬Input voltage: ........................................................................................230 V AC
¬Decision voltage logical 0: ........................................................................... 0 – 0.2 Un
¬Decision voltage logical 1: .........................................................................0.7 – 1.15 Un
Digital outputs
¬Number: ..........................................................................................2 x bistable
¬Contact working voltage: .....................................................................230 V AC, 30 V DC
¬Maximum load current:....................................................................................16 A
PLC communication
¬PLC band: ...........................................................................................Cenelec D
¬Modulation: ............................................................................................S-FSK
¬Communication frequency: ..............................................................f1=140kHz, f2=148kHz
¬Output reaction time for input change: ..................................................................max 2 s
RS485 communication
¬Type: .........................................................................RS485 twisted pair physical layer
¬Communication line parameters:................................................................9600 baud, 8n1
¬RS485 serial line power supply: .........................................................................internal
¬RS485 twisted pair replacement options: ....................................... Voltdrive ShiftGuard PLC modems
¬Communication protocol:....................... VoltGuard system proprietary protocol, see product documentation
Technical parameters
¬Rated voltage: ......................................................................................... 230 V~
¬Specified supply voltage range: .....................................................................0.9 – 1.1 Un
¬Rated frequency: ....................................................................................... 50 Hz
¬Typical receiving input power: .............................................................................1.5 W
¬Typical transmitting input power:...............................................................2.6 W (peak 6 W)
Construction parameters
¬Dimensions:..........................................................................88 x 91 x58 mm (WxHxD)
¬Weight: ................................................................................................ 200 g
¬Operating temperature: .............................................................. between -30°C and +50°C
¬Storage temperature: ................................................................ between -40°C and +70°C
¬Installation: ...........................................................................................DIN rail
¬IP Code ..................................................................................................IP20
Insulation parameters according to the CSN EN 60664-1/CSN EN 60664-3 standards
¬Overvoltage category: .......................................................................................III
¬Pollution degree: ............................................................................................3
¬Altitude: .............................................................................................<2000m
Type tests
¬Safety:.....................................................assessed according to the CSN EN 61010-1 standard
¬Protection class:.............................................................................................2

VOLTDRIVE s.r.o.,
Háj 365 (MICOS TELCOM premises), 798 12 Kralice na Hané, Czech Republic
Tel.: +420 582 307 603, Fax: +420 582 307 688
9
SAFETY INSTRUCTIONS
The product is capable of safe operation. The manufacturer warns of the risk of possible danger resulting from incor-
rect handling or incorrect use of the product:
¬The installation and maintenance must be carried out by a competent person with relevant electrical qualifications,
who informs the operator about the conditions for safe operation.
¬The product must not be used for other than its intended purpose.
¬The product must not be modified compared to its standard design.
¬The product must not be operated with other voltage, current or frequency than it was produce or professionally mod-
ified for.
¬The product must be placed and secured, so that it is difficult to access or inaccessible for the people without any
electrical qualification, especially children.
¬Before every re-commissioning, for example, after any reparation or maintenance, the protection and all safety meas-
ures must be completely restored to ensure safe operation.
¬The product must not be used in conditions and environments that do not guarantee safe operation (for example,
installed on a flammable surface, its cover made of flammable materials, insufficient protection against foreign body
intrusion or water and other liquid ingress).
In case the user does not comply with any of the above instructions and if this noncompliance results in any defect, the
manufacturer disclaims any liability for the defect.
Table of contents
Popular Modem manuals by other brands
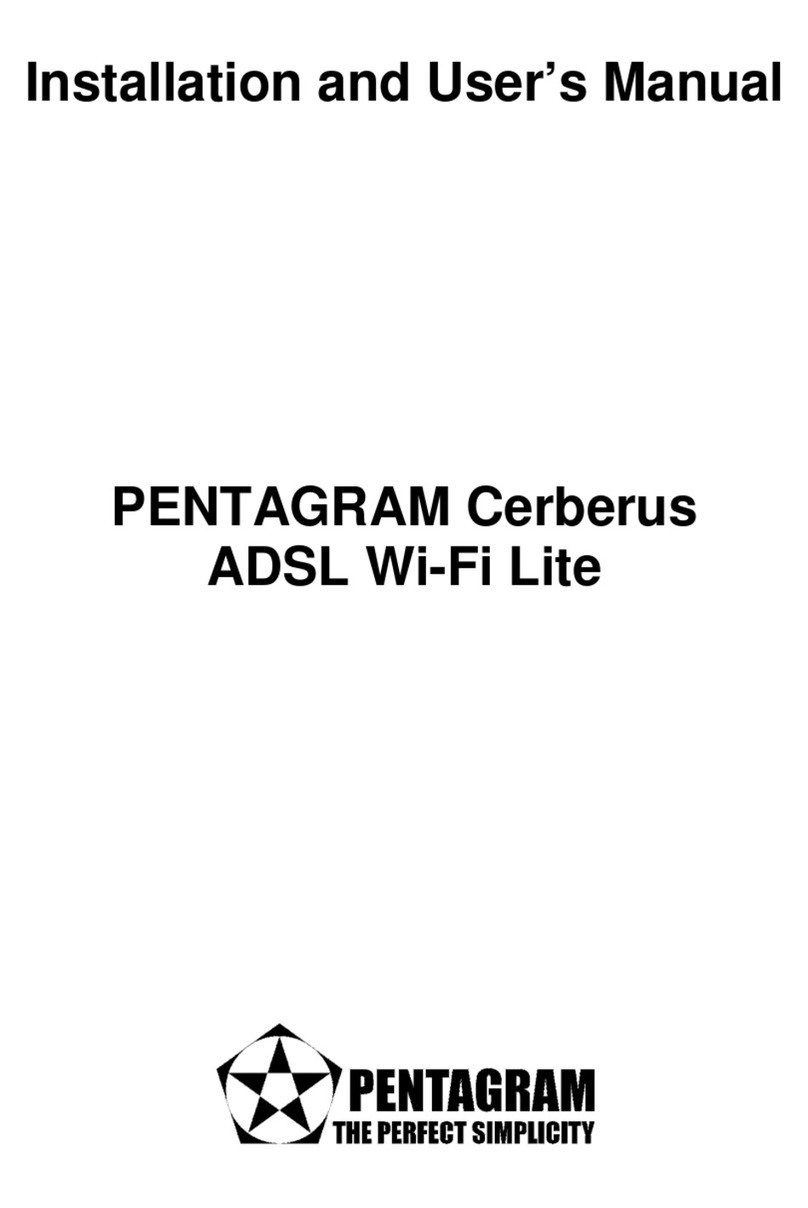
Pentagram
Pentagram Cerberus Wi-Fi Lite Installation and user manual
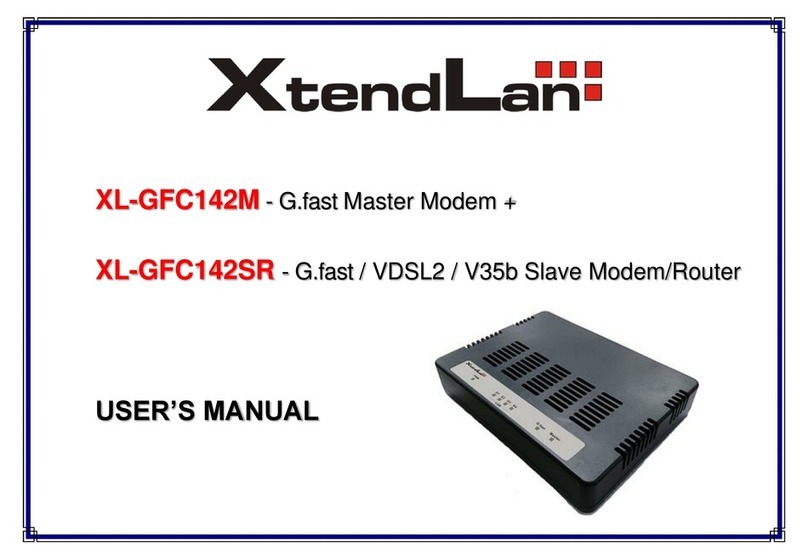
XtendLan
XtendLan XL-GFC142M user manual
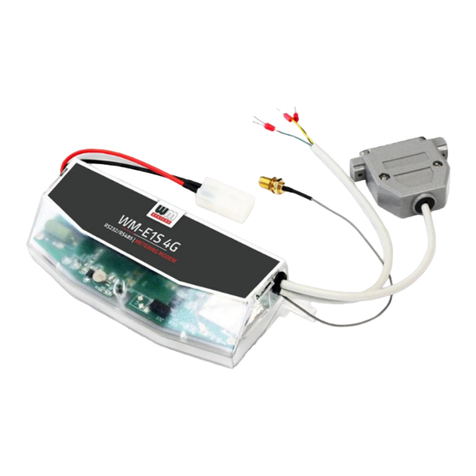
WM Systems
WM Systems WM-E1S Datasheet and User Manual
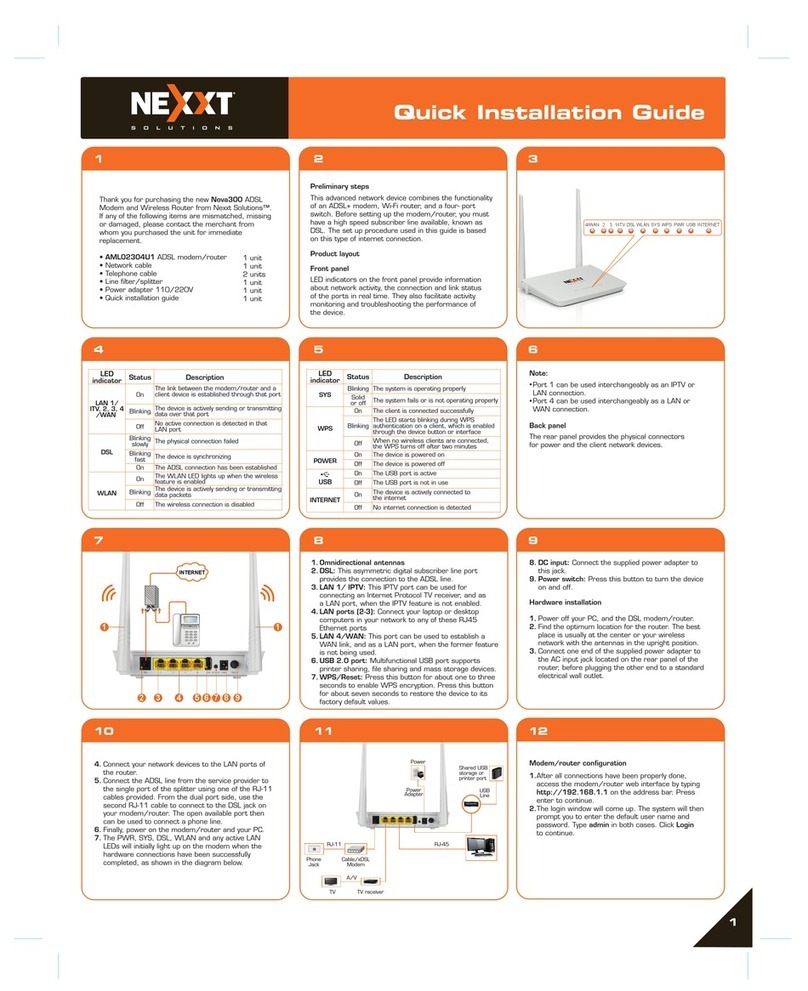
Nexxt Solutions
Nexxt Solutions Nova300 Quick installation guide

Garnet
Garnet GAE-3020 user guide
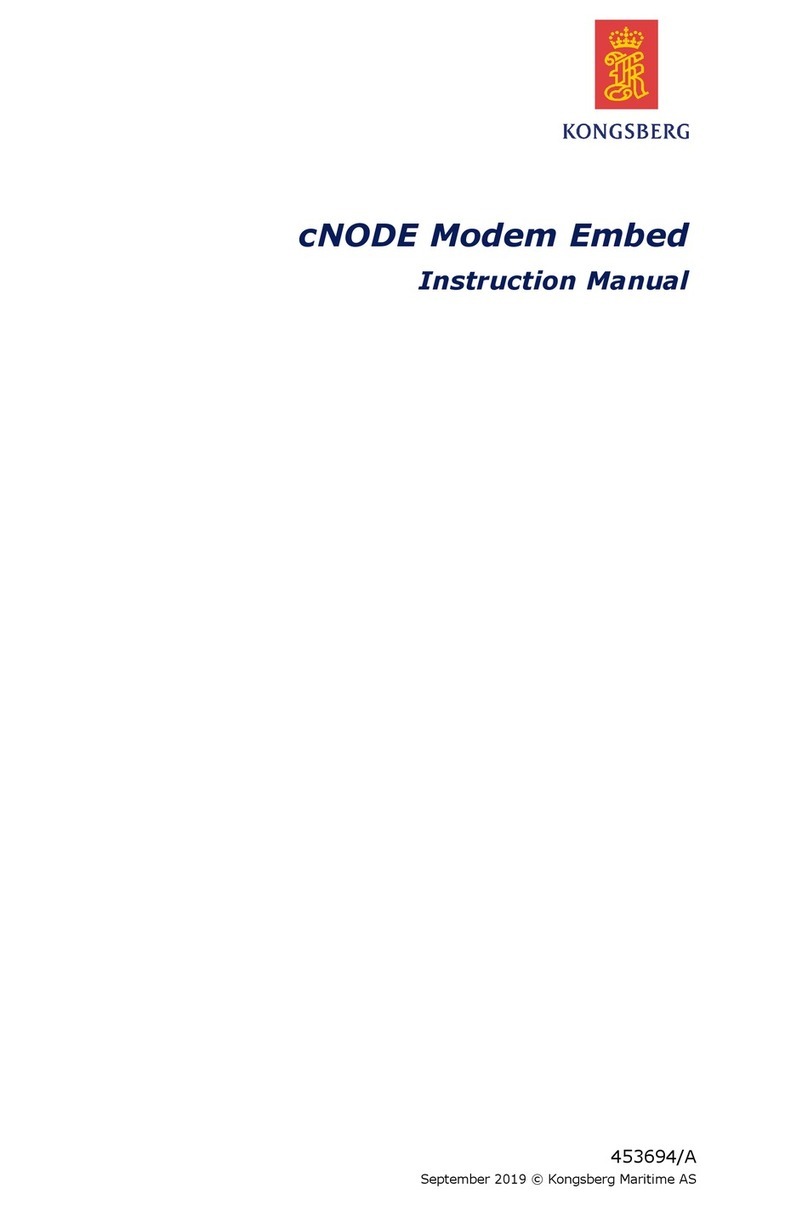
Kongsberg
Kongsberg cNODE Embed instruction manual