Watts Aerco ProtoNode FPC-N34 User manual

AERCO ProtoNode FPC-N34 & FPC-N35 User Manual
User Manual
OMM-0107_0B AERCO International, Inc. •100 Oritani Dr. •Blauvelt, NY 10913 Page 1of 108
GF-150 Ph.: 800-526-0288 03/07/2017
OMM-0107
GF-150
AERCO ProtoNode FPC-N34 and FPC-N35 User Manual
AERCO Serial
ProtoNode FPC-N34
Part Number 64129
AERCO LonWorks
ProtoNode FPC-N35
Part Number 64130
For interfacing with the following AERCO products:
•AM Series
•C-More
•Modulex
•ECS/SmartPlate
•BMS/BMSII/ACS
For interfacing with the following Building Automation Systems:
•BACnet MS/TP
•BACnet/IP
•Modbus TCP/IP
•Modbus RTU
•Metasys N2
•LonWorks
Latest Revision: March 07, 2017
This user manual applies
only
to ProtoNode Models
FPC-N34 (P/N 64129) and FPC-N35 (P/N 64130)
For ProtoNode RER (P/N 64084) and LER (P/N 64085) see
user manual OMM-0080, GF-129

AERCO ProtoNode FPC-N34 & FPC-N35 User Manual
User Manual
Page 2of 108 AERCO International, Inc. •100 Oritani Dr. •Blauvelt, NY 10913 OMM-0107_0B
03/07/2017Ph.: 800-526-0288 GF-150
OMM-0107
GF-150
Technical Support
(Mon-Fri, 8am-5pm EST)
1-800-526-0288
Website: www.aerco.com
Certifications
BTL MARK – BACNET TESTING LABORATORY
LONMARK CERTIFICATION
Thank you for purchasing the ProtoNode for AERCO products.
Please call AERCO for Technical support of the ProtoNode product.
SMC does not provide direct support. If AERCO needs to escalate the concern, they will contact
Sierra Monitor Corporation for assistance.
DISCLAIMER
The information contained in this manual is subject to change without notice from AERCO
International, Inc. AERCO makes no warranty of any kind with respect to this material, including, but
not limited to, implied warranties of merchantability and fitness for a particular application. AERCO
International is not liable for errors appearing in this manual, nor for incidental or consequential
damages occurring in connection with the furnishing, performance, or use of these materials.
The BTL Mark on ProtoNode FPC-N34 is a symbol that indicates that a
product has passed a series of rigorous tests conducted by an
independent laboratory which verifies that the product correctly
implements the BACnet features claimed in the listing. The mark is a
symbol of a high-quality BACnet product.
Go to http://www.BACnetInternational.net/btl/
for more information
about the BACnet Testing Laboratory. Click here for
BACnet PIC
Statement
LonMark International is the recognized authority for certification,
education, and promotion of interoperability standards for the benefit of
manufacturers, integrators and end users. LonMark International has
developed extensive product certification standards and tests to
provide the integrator and user with confidence that products from
multiple manufacturers utilizing LonMark devices work together. Sierra
Monitor has more LonMark Certified gateways than any other gateway
manufacturer, including the ProtoCessor, ProtoCarrier and ProtoNode
for OEM applications and the full featured, configurable gateways.

AERCO ProtoNode FPC-N34 & FPC-N35 User Manual
User Manual
OMM-0107_0B AERCO International, Inc. •100 Oritani Dr. •Blauvelt, NY 10913 Page 3of 108
GF-150 Ph.: 800-526-0288 03/07/2017
OMM-0107
GF-150
TABLE OF CONTENTS
Quick Start Guide......................................................................................................................................................... 6
CHAPTER 1. Introduction.................................................................................................................................7
1.1 ProtoNode Gateway.................................................................................................................7
CHAPTER 2. BACnet/LonWorks Setup for ProtoNode FPC-N34/FPC-N35.............................. 11
2.1 Record Identification Data......................................................................................................11
2.2 Point Count Capacity and Registers per Device.....................................................................11
2.3 Configuring Device Communications......................................................................................12
2.3.1 Set Modbus COM setting on all of the Devices connected to the ProtoNode.................................. 12
2.3.2 Set Modbus RTU Node-ID for each of the Devices attached to the ProtoNode ............................... 12
2.4 Selecting the Desired Field Protocol and Enabling Auto-Discovery........................................12
2.4.1 Selecting Desired Field Protocol........................................................................................................ 12
2.4.2 Enabling Auto-Discovery (Not used on BST or WHM)....................................................................... 13
2.4.3 Manually Selecting Your Equipment ................................................................................................. 14
2.5 BAS Network Settings: MAC Address, Device Instance and Baud Rate.................................14
2.5.1 BACnet MS/TP (FPC-N34): Setting the MAC Address for BAS Network............................................ 14
2.5.2 BACnet MS/TP and BACnet/IP (FPC-N34): Setting the Device Instance............................................ 15
2.5.3 Metasys N2 or Modbus TCP/IP (FPC-N34): Setting the Node-ID ...................................................... 16
2.5.4 BACnet MS/TP or Modbus RTU (FPC-N34): Setting the Baud Rate for BAS Network....................... 16
CHAPTER 3. Interfacing ProtoNode to Devices................................................................................... 17
3.1 ProtoNode FPC-N34 and FPC-N35 Showing Connection Ports.............................................17
3.2 Device Connections to ProtoNode .........................................................................................18
3.2.1 Biasing the Modbus RS-485 Device Network .................................................................................... 19
3.2.2 End of Line Termination Switch for the Modbus RS-485 Device Network........................................ 20
3.3 BACnet MS/TP, Modbus RTU or Metasys N2 (FPC-N34): Wiring Field Port to RS-485 BAS
Network 21
3.4 LonWorks (FPC-N35): Wiring Field Port to LonWorks Network..............................................21
3.5 ACS/BMS II Wiring Connections to ProtoNode FPC-N34 and FPC-N35................................22
3.5.1 Modulex BCM Connections............................................................................................................... 23
3.5.2 ECS Connections................................................................................................................................ 23
3.5.3 C-MORE Connections ........................................................................................................................ 24
3.5.4 AM Series Connections...................................................................................................................... 24
3.6 Power-Up ProtoNode.............................................................................................................25
3.6.1 Auto-Discovery: After Completion – Turn Off to Save Configuration ............................................... 26
CHAPTER 4. BACnet/IP or Modbus TCP/IP: Change the ProtoNode IP Address................. 27
4.1 Connect the PC to ProtoNode via the Ethernet Port...............................................................27
4.2 BACnet/IP and Modbus TCP/IP: Setting IP Address for Field Network...................................29
CHAPTER 5. BACnet MS/TP and BACnet/IP: Setting Node_Offset to Assign Specific
Device Instances..................................................................................................................................................... 31
CHAPTER 6. How to Start the Installation Over: Clearing Profiles............................................. 33
CHAPTER 7. LonWorks (FPC-N35): Commissioning ProtoNode on a LonWorks Network35
7.1 Commissioning ProtoNode FPC-N35 on a LonWorks Network ..............................................35
7.1.1 Instructions for Downloading XIF File from ProtoNode FPC-N35 Using Browser............................. 35

AERCO ProtoNode FPC-N34 & FPC-N35 User Manual
User Manual
Page 4of 108 AERCO International, Inc. •100 Oritani Dr. •Blauvelt, NY 10913 OMM-0107_0B
03/07/2017Ph.: 800-526-0288 GF-150
OMM-0107
GF-150
CHAPTER 8. CAS BACnet Explorer for Validating ProtoNode in the Field............................. 37
8.1 Downloading the CAS Explorer and Requesting an Activation Key........................................37
8.2 CAS BACnet Setup................................................................................................................38
8.2.1 CAS BACnet MS/TP Setup.................................................................................................................. 38
8.2.2 CAS BACnet BACnet/IP Setup............................................................................................................ 39
Appendix A: “A” Bank DIP Switch Settings.......................................................................................... 41
Appendix B: AERCO Equipment Monitor and Control Point Definitions...................................... 45
Appendix B-2: AERCO Electronic Control System (ECS) Point Definitions..................................48
Appendix B-3: AERCO (Modulex) BCM Point Definitions............................................................48
Appendix B-4: Water Heater Management System (WHM) and On-Board Boiler Sequencing
Technology (BST) Point Definitions..............................................................................................50
Appendix B-5: AM Series Point Definitions..................................................................................53
Appendix C: AERCO Equipment Point Mappings.............................................................................. 57
Appendix C-1: AM Mngr Modbus RTU Mappings to BACnet MS/TP, BACnet/IP, Metasys N2,
Modbus TCP/IP and LonWorks...................................................................................................57
Appendix C-2: AM Dep Modbus RTU Mappings to BACnet MS/TP, BACnet/IP, Metasys N2,
Modbus TCP/IP and LonWorks....................................................................................................61
Appendix C-3: C-More Modbus RTU Mappings to BACnet MS/TP, BACnet/IP, Metasys N2,
Modbus TCP/IP and LonWorks....................................................................................................63
Appendix C-4: Modulex Modbus RTU Mappings to BACnet MS/TP, BACnet/IP, Metasys N2,
Modbus TCP/IP and LonWorks....................................................................................................63
Appendix C-5: ECS Modbus RTU Mappings to BACnet MS/TP, BACnet/IP, Metasys N2, Modbus
TCP/IP and LonWorks .................................................................................................................64
Appendix C-6: ACS/BMSII/BMS Modbus RTU Mappings to BACnet MS/TP, BACnet/IP, Metasys
N2, Modbus TCP/IP and LonWorks .............................................................................................65
Appendix D: Eight C-More Boilers/Heaters and BST/WHM Master............................................... 67
Appendix E: Troubleshooting..................................................................................................................... 77
Appendix E-1: Viewing Diagnostic Information............................................................................77
Appendix E-2: Check Wiring and Settings...................................................................................78
Appendix E-3: Diagnostic Capture with the FieldServer Utilities..................................................79
Appendix E-4: BACnet: Setting Network_Number for more than one ProtoNode on Subnet.......82
Appendix E-5: LED Diagnostics for Modbus RTU Communications Between ProtoNode and
Devices 83
Appendix E-6: Passwords..........................................................................................................84
Appendix F: C-More Status And Fault Messages ................................................................................... 85
Appendix G: Conversion Equations For Temperature Variables.................................................... 91
Appendix H: BCM and BMM Fault Codes For Modulex E8 Controller............................................. 93
Appendix H-1: BCM and BMM Fault Code Conversion Table .....................................................93
Appendix H-2: BMM Fault Code Table........................................................................................94
Appendix H-3: BCM Fault Code Table ........................................................................................96
Appendix I: AM Error, State and Status Tables..................................................................................... 98
Appendix I-1: AM Lockout Error Codes Table ..............................................................................98
Appendix I-2: AM Blocking Error Codes Table .............................................................................99
Appendix I-3: AM State Parameters Table.................................................................................100

AERCO ProtoNode FPC-N34 & FPC-N35 User Manual
User Manual
OMM-0107_0B AERCO International, Inc. •100 Oritani Dr. •Blauvelt, NY 10913 Page 5of 108
GF-150 Ph.: 800-526-0288 03/07/2017
OMM-0107
GF-150
Appendix I-4: AM Status Parameters Table ...............................................................................100
Appendix I-5: Cascade Connection of AM Boiler with ProtoNode...............................................101
Appendix J: Reference................................................................................................................................104
Appendix J-1: Specifications.....................................................................................................104
Appendix J-2: Compliance with UL Regulations........................................................................104
Appendix K: Limited 2 Year Warranty....................................................................................................107

AERCO ProtoNode FPC-N34 & FPC-N35 User Manual
User Manual
Page 6of 108 AERCO International, Inc. •100 Oritani Dr. •Blauvelt, NY 10913 OMM-0107_0B
03/07/2017Ph.: 800-526-0288 GF-150
OMM-0107
GF-150
Quick Start Guide
•Auto-Discovery connection points are limited by available memory in the device.
•Auto-Discovery is not available in SSD mode required for BST (Boiler Sequencing
Technology) and WHM (Water Heater Management).
•BST and WHM are limited to eight (8) C-More connections.
•BST and WHM require a ProtoNode with all protocols, including Modbus.
INSTRUCTION SECTION
1. Record the information about the unit. 2.1
2. Set the device’s Modbus RTU serial settings (i.e. baud rate, parity, stop bits)
and Modbus Node-
ID for each of the devices that will be connected to
ProtoNode FPC-N34 or FPC-N35.
2.3
3. ProtoNode FPC-N34 units: Select
the Field Protocol (BACnet MS/TP,
BACnet/IP, Modbus TCP/IP or Metasys N2) on the S Bank Dip Switches. 2.4.1
4. Enable the ProtoNode “Auto Discovery” mode on Dip Switch Bank S. 2.4.2
5. BACnet MS/TP (FPC-N34): Set the MAC Address on DIP Switch Bank A. 2.5.1
6. BACnet MS/TP or BACnet IP (FPC-N34): Set the BACnet Device Instance 2.5.2
7. Metasys N2, Modbus RTU, or Modbus TCP/IP (FPC-N34): Set the Node-ID. 2.5.3
8. BACnet MS/TP or Modbus RTU (FPC-N34): Set the BAUD rate of the Field
Protocol on DIP Switch Bank B. 2.5.4
9. Connect ProtoNode’s 6 pin RS-485 connector to the Modbus RS-485 network
that is connected to each of the devices. 3.2
10.
Connect ProtoNode FPC-N34’s
3 pin RS-485 port to the Field Protocol
cabling,
or
Connect ProtoNode FPC-N35’s 2 pin LonWorks port to the Field Protocol
cabling.
3.3
3.4
11. Connect Power to ProtoNode’s 6 pin connector. 3.5
12. When power is applied it will take about 10 minutes for all the devices to be
discovered and the configuration file to be built. Once Auto-
Discovery is
complete, turn OFF the S3 DIP Switch to save the configuration settings.
3.6
13. BACnet/IP or Modbus TCP/IP (FPC-N34): Use the ProtoNode’s embedded
tool which is accessed with a browser, referred to in this manual as the Web
Configurator, to change the IP Address. No changes to the configuration file
are necessary.
CHAPTER
4
14. LonWorks (FPC-N35
): The ProtoNode must be commissioned on the
LonWorks Network. This needs to be done by the Lon
Works administrator
using a LonWorks Commissioning tool.
CHAPTER
7

AERCO ProtoNode FPC-N34 & FPC-N35 User Manual
CHAPTER 1 – Introduction
OMM-0107_0B AERCO International, Inc. •100 Oritani Dr. •Blauvelt, NY 10913 Page 7of 108
GF-150 Ph.: 800-526-0288 03/07/2017
CHAPTER 1. Introduction
1.1 ProtoNode Gateway
ProtoNode is an external, high performance Building Automation multi-protocol gateway
that is preconfigured to Auto-Discover any AERCO products (hereafter called a “device”)
connected to the ProtoNode and automatically configure them for BACnet®1MS/TP, BACnet/IP,
Metasys®2N2 by JCI, Modbus RTU, Modbus TCP/IP, or LonWorks®3.
It is not necessary to download any configuration files to support the required applications. The
ProtoNode is pre-loaded with tested Profiles/Configurations for the supported devices.
Figure 1-1: ProtoNode Connections to Devices
1BACnet is a registered trademark of ASHRAE
2Metasys is a registered trademark of Johnson Controls Inc.
3 LonWorks is a registered trademark of Echelon Corporation
Controller A
Controller B
Controller C
Controller D
Controller E
Controller F
Controller G
Auto-Discovered
RS-485 Field Protocol
One or multiple
Ethernet Field Protocols

AERCO ProtoNode FPC-N34 & FPC-N35 User Manual
CHAPTER 1 – Introduction
Page 8of 108 AERCO International, Inc. •100 Oritani Dr. •Blauvelt, NY 10913 OMM-0107_0B
03/07/2017Ph.: 800-526-0288 GF-150
AERCO’s multi-protocol communications gateway supports integration of AERCO devices with
customers’ building control and energy management systems. The plug-n-play package
supports integration with BACnet/IP, BACnet MS/TP, LonWorks, and Johnson Controls Metasys
N2 systems. AERCO’s Communications Gateway is available for all AERCO boilers, water
heaters, and electronically controlled indirect systems.
• Built-in translation for BACnet/IP, BACnet MS/ TP, LonWorks, Metasys N2 and Modbus
TCP Protocols
• Supports individual units and systems including AERCO’s WHM and BST.
• Select protocol and baud rate in the field using simple DIP switch selection
• Captures alarm and trend history for faster troubleshooting
• Non-volatile memory retains point mappings and programs in the event of power loss.
• Approvals: BACnet Testing Labs (BTL) B-ASC on ProtoNode FPC-N34, CE Mark,
LonMark 3.4 Certified on ProtoNode FPC-N35, TUV approved to UL 916
Serial ProtoNode FPC-N34
P/N 64129
LonWorks ProtoNode FPC-N35
P/N 64130
Figure 1-2: ProtoNode Dimensions
4.52
[114.91]
4.52
[114.91]
3.25 [82.55]
3.62 [91.98]
3.25 [82.55]
3.62 [91.98]
2.91 [73.91]
2.91 [73.91]
1.60
[40.6]

AERCO ProtoNode FPC-N34 & FPC-N35 User Manual
CHAPTER 1 – Introduction
OMM-0107_0B AERCO International, Inc. •100 Oritani Dr. •Blauvelt, NY 10913 Page 9of 108
GF-150 Ph.: 800-526-0288 03/07/2017
AERCO’s Communications Gateway (ProtoNode) is an external, high performance, Building
Automation multi-protocol gateway that has been preprogrammed for AERCO’s equipment
to support BACnet®4MS/TP, BACnet/IP, Metasys®5N2 by JCI, Modbus TCP, and LonWorks®6.
All the different AERCO configurations for the various protocols are stored within the ProtoNode
and are selectable via DIP switches for fast and easy installation. There is no need to download
any configuration files to support the required applications.
AERCO’s Communications Gateway Supports WHM and BST
AERCO has co-developed the ProtoNode to communicate between systems of AERCO units
(for example: multiple water heaters running Onboard Water Heater Management (WHM) or
multiple AERCO Boilers running Boiler Sequencing Technology (BST). The AERCO ProtoNode
in SSD mode eliminates multiple master issues and is included with all AERCO’s
Communications Gateway ProtoNodes. Use SSD mode to enable a Building Automation
System Modbus master to bi-directionally communicate to BST and WHM Modbus masters.
The AERCO SSD device is unique because it enables two Modbus masters to bi-directionally
communicate over RS-485. The AERCO SSD device is also specifically designed to support the
BST/WHM Automatic failover Feature. While the BST/WHM role can be transferred to another
unit (with a different Modbus address) the SSD device operates at a fixed and constant Modbus
address. The fixed SSD address is propagated to each unit and allows the BST/WHM master to
resume communications after a failover without BAS changes.
This manual provides the necessary information to assist the Installers of the boilers/heaters
with the installation of the ProtoNode FPC-N34 on BACnet MS/TP, BACnet/IP, Modbus TCP
and Metasys N2 by JCI networks and installation of the ProtoNode FPC-N35 on a LonWorks
network.
BACnet International BTL certification is the highest level of BACnet conformance tests that a
product can be subjected to.
•The ProtoNode FPC-N34 is BACnet Certified by the BACnet Testing Laboratory (BTL).
•The ProtoNode FPC-N35 is LonMark Certified by LonMark International.
The ProtoNode units feature a small form factor, as indicated in Figure 1.1
4BACnet is a registered trademark of ASHRAE
5Metasys is a registered trademark of Johnson Controls Inc.
3LonMark is a registered trademark of LonMark International
4 LonWorks is a registered trademark of Echelon Corporation

AERCO ProtoNode FPC-N34 & FPC-N35 User Manual
CHAPTER 1 – Introduction
Page 10 of 108 AERCO International, Inc. •100 Oritani Dr. •Blauvelt, NY 10913 OMM-0107_0B
03/07/2017Ph.: 800-526-0288 GF-150
(This Page Left Intentionally Blank)

AERCO ProtoNode FPC-N34 & FPC-N35 User Manual
CHAPTER 2 – BACnet/LonWorks Setup
OMM-0107_0B AERCO International, Inc. •100 Oritani Dr. •Blauvelt, NY 10913 Page 11 of 108
GF-150 Ph.: 800-526-0288 03/07/2017
CHAPTER 2. BACnet/LonWorks Setup for ProtoNode
FPC-N34/FPC-N35
2.1 Record Identification Data
Each ProtoNode has a unique part number located on the side or the back of the unit. This
number should be recorded, as it may be required for technical support. The numbers are as
follows:
AERCO ProtoNode
Model AERCO Part Number
Serial ProtoNode N34 64129
LonWorks ProtoNode N35 64130
Figure 2-1: ProtoNode Part Numbers
•ProtoNode FPC-N34 units have the following 3 ports: RS-485,Ethernet,RS-485
•ProtoNode FPC-N35 units have the following 3 ports: LonWorks,Ethernet,RS-485
2.2 Point Count Capacity and Registers per Device
The total number of Modbus Registers presented by all of the devices attached to the ProtoNode
cannot exceed:
Part number Total Registers
FPC-N34-0645 1,500
FPC-N35-1051 1,500
Figure 2-2: Supported Point Count Capacity
Devices Registers Per Device Unit Address Range
AM Managing Boiler/Heater 95 Addr 1 to 16
AM Dependent Boiler/Heater 49 Addr 1 to 16
C-More BMK/INN 12 Addr 1 to 16
Modulex & Modulex EXT 10 Addr 1 to 8
ECS * IND/SP/DW 7 Addr 17 to 32
BMS/BMSII/ACS 51 Addr 128 to 228
BST/WHM 186 (for 1 up to 8 devices) Addr 1 to 8 on C-More (SSD address = 247)
* Does not apply to Pneumatic or self-contained controls
Figure 2-3: Modbus Registers per Device

AERCO ProtoNode FPC-N34 & FPC-N35 User Manual
CHAPTER 2 – BACnet/LonWorks Setup
Page 12 of 108 AERCO International, Inc. •100 Oritani Dr. •Blauvelt, NY 10913 OMM-0107_0B
03/07/2017Ph.: 800-526-0288 GF-150
2.3 Configuring Device Communications
2.3.1 Set Modbus COM setting on all of the Devices connected to the ProtoNode
•All of the Serial devices connected to ProtoNode MUST have the same Baud Rate,
Data Bits, Stop Bits, and Parity settings.
•The Figure below specifies the device serial port settings required to communicate with
the ProtoNode.
Serial Port Setting Device
Protocol
Modbus RTU
Baud Rate
9600
Parity
None
Data Bits
8
Stop Bits
1
Figure 2-4: Modbus RTU COM Settings
2.3.2 Set Modbus RTU Node-ID for each of the Devices attached to the ProtoNode
•Set Modbus Node-ID for each of the devices attached to ProtoNode. The Modbus
Node-ID’s need to be uniquely assigned between 1 and 255.
oThe Modbus Node-ID that is assigned for each device needs to be
documented.
The Modbus Node-ID’s assigned are used for designating the Device
Instance for BACnet/IP and BACnet MS/TP (Section 2.5.2 )
•The Metasys N2 and Modbus TCP/IP Node-ID will be set to same value as the Node-ID
of the Modbus RTU device.
2.4 Selecting the Desired Field Protocol and Enabling Auto-Discovery
2.4.1 Selecting Desired Field Protocol
•ProtoNode FPC-N34 units use the “S” bank of DIP switches (S0 – S2) to select the
Field Protocol.
oSee the table in the Figure below for the switch settings to select BACnet MS/TP,
BACnet/IP, Modbus TCP/IP, or Metasys N2.
oThe OFF position is when the DIP switches are set closest to the outside of the
box.

AERCO ProtoNode FPC-N34 & FPC-N35 User Manual
CHAPTER 2 – BACnet/LonWorks Setup
OMM-0107_0B AERCO International, Inc. •100 Oritani Dr. •Blauvelt, NY 10913 Page 13 of 108
GF-150 Ph.: 800-526-0288 03/07/2017
ProtoNode FPC-N34 S Bank DIP Switches
Profile S0 S1 S2 S3
BACnet/IP
Off
Off
Off
Off
BACnet MS/TP
ON
Off
Off
Off
Metasys N2
Off
ON
Off
Off
Modbus TCP/IP or Modbus RTU
ON
ON
Off
Off
*Modbus to 8 WHM/BST Units
Off
Off
ON
Off
*BACnet to 8 WHM/BST Units
ON
Off
ON
Off
*Metasys N2 to 8 WHM/BST Units
Off
ON
ON
Off
ProtoNode FPC-N35
LonWorks
Off
Off
Off
Off
*Lon to 8 WHM/BST Units
ON
Off
Off
Off
Figure 2-5: S Bank DIP Switches
*NOTE: For WHM or BST systems auto-discovery cannot be done. Be sure that the
S Bank DIP Switches are set properly.
2.4.2 Enabling Auto-Discovery (Not used on BST or WHM)
The S3 DIP switch is used to both enable Auto-Discovery of known devices attached to the
ProtoNode, and to save the recently discovered configuration.
•See the table in Figure below for the switch setting to enable Auto-Discovery.
•If the ProtoNode is being installed for the first time, set S3 to the ON position to enable
Auto-Discovery.
•Cycle the power to the ProtoNode to start Auto-Discovery
•The ON position is when the DIP switches are set closest to the inside of the box.
NOTE: Allow 10 minutes for the Auto-Discovery process to complete.
•After Auto-Discovery is complete, turn off S3 to save the configuration.
S3 DIP Switch Auto-Discovery Mode S3
Auto-Discovery ON – Build New Configuration
ON
Auto-Discover OFF – Save Current Configuration
Off
Figure 2-6: S3 DIP Switch setting for Auto Discovering Devices
S0 S1 S2 S3
S0 – S3 DIP
Switches
S Bank DIP Switch Location
S0 S1 S2 S3

AERCO ProtoNode FPC-N34 & FPC-N35 User Manual
CHAPTER 2 – BACnet/LonWorks Setup
Page 14 of 108 AERCO International, Inc. •100 Oritani Dr. •Blauvelt, NY 10913 OMM-0107_0B
03/07/2017Ph.: 800-526-0288 GF-150
2.4.3 Manually Selecting Your Equipment
A laptop or PC is required to do this. This cannot be done for BST or WHM
The ProtoNode’s device port can be pre-configured for your equipment. Leave the S3 dip switch
in the OFF position and follow the instructions below:
1. Be sure the ProtoNode is already configured as outlined in Section 2.3.
2. Select the desired field protocol as outlined in Section 2.4.1.
3. Follow Section 4.1 to connect your PC or laptop to the Ethernet port.
4. Open a web browser on your PC
5. Enter the IP Address of the ProtoNode – the default address is: 192.168.1.24. The
“Configuration Parameters” page appears.
6. Go to the bottom of the page and find the “Active Profiles” section. This is where you can
add equipment profiles. Be sure the desired field protocol is already selected, as in Step 2;
if the field protocol is changed after the equipment profiles are selected, they become
invalid and must be cleared and re-selected again.
7. If any profiles are present and not desired, select them and click Remove.
8. Select your desired profiles and click Add.
9. Enter the Node ID or equipment address.
10. Select the “Current Profile” of the equipment from the drop-down box.
11. Once your information is correct, click on Submit, or click Cancel and enter your
information again.
12. Repeat steps 8 to 11 to add more equipment profiles, as needed.
13. After selecting all your equipment profiles, click the System Restart tab on the bottom to
update the ProtoNode.
2.5 BAS Network Settings: MAC Address, Device Instance and Baud Rate
2.5.1 BACnet MS/TP (FPC-N34): Setting the MAC Address for BAS Network
•Only 1 MAC address is set for ProtoNode regardless of how many devices are
connected to ProtoNode.
•Set the BACnet MS/TP MAC addresses of the ProtoNode to a value between 1 to 127
(MAC Master Addresses); this is so that the BMS Front End can find the ProtoNode
via BACnet auto discovery.
•Note: Never set a BACnet MS/TP MAC Address from 128 to 255. Addresses from
128 to 255 are Slave Addresses and cannot be discovered by BAS Front Ends that
support auto discovery of BACnet MS/TP devices.
•Set “A” bank DIP switches A0 – A7 to assign a MAC Address to the ProtoNode for
BACnet MS/TP.
•Please refer to Appendix A for the complete range of MAC Addresses and DIP switch
settings.

AERCO ProtoNode FPC-N34 & FPC-N35 User Manual
CHAPTER 2 – BACnet/LonWorks Setup
OMM-0107_0B AERCO International, Inc. •100 Oritani Dr. •Blauvelt, NY 10913 Page 15 of 108
GF-150 Ph.: 800-526-0288 03/07/2017
Figure 2-7: MAC Address DIP Switches
NOTE: When setting DIP Switches, please ensure that power to the board is OFF.
NOTE
A MAC address greater than 127 will cause the ERR LED to light and will
disable the ProtoNode from being discovered by the BAS. Either set the
MAC address to 127 or lower, or change the “MAX MAC” on the
Configuration page.
2.5.2 BACnet MS/TP and BACnet/IP (FPC-N34): Setting the Device Instance
•The BACnet Device Instances will be calculated by adding the Node_Offset (default
value is 50,000) to the device’s Modbus Node ID (that was assigned in Section 2.3.2).
•The BACnet Device Instance can range from 1 to 4,194,303.
For example:
Node_Offset value (default) = 50,000
oDevice 1 has a Modbus Node-ID of 1
oDevice 2 has a Modbus Node-ID of 2
oDevice 3 has a Modbus Node-ID of 3
oGiven that: Device Instance = Node_Offset + Modbus Node_ID
oDevice Instance, Device 1 = 50,000 + 1 = 50,001
oDevice Instance, Device 2 = 50,000 + 2 = 50,002
oDevice Instance, Device 3 = 50,000 + 3 = 50,003
2.5.2.1 BACnet MS/TP or BACnet/IP: Assigning Specific Device Instances
With the default Node_Offset value of 50,000 the Device Instances values generated will be
within the range of 50,001 to 50,127.
•The values allowed for a BACnet Device Instance can range from 1 to 4,194,303.
•To assign a specific Device Instance (or range), change the Node_Offset value.
•Methods for changing the Node_Offset value are provided in Chapter 5
oThis step cannot be performed until after the unit is connected and powered.

AERCO ProtoNode FPC-N34 & FPC-N35 User Manual
CHAPTER 2 – BACnet/LonWorks Setup
Page 16 of 108 AERCO International, Inc. •100 Oritani Dr. •Blauvelt, NY 10913 OMM-0107_0B
03/07/2017Ph.: 800-526-0288 GF-150
2.5.3 Metasys N2 or Modbus TCP/IP (FPC-N34): Setting the Node-ID
•The Modbus RTU Node-ID’s assigned to the devices attached to the ProtoNode in
Section 2.3.2 will be the Metasy N2 or Modbus TCP/IP Node_ID’s to the field
protocols.
•Metasys N2 and Modbus TCP/IP Node-ID Addressing: Metasys N2 and Modbus
TCP/IP Node-ID’s range from 1-255.
2.5.4 BACnet MS/TP or Modbus RTU (FPC-N34): Setting the Baud Rate for BAS Network
•“B” bank DIP switches B0 – B3 can be used to set the Field baud rate of the
ProtoNode to match the baud rate required by the Building Management System for
BACnet MS/TP or Modbus RTU.
•The baud rate on ProtoNode for Metasys N2 is set for 9600. “B” bank DIP switches
B0 – B3 are disabled for Metasys N2 on ProtoNode FPC-N34.
•“B” bank DIP switches B0 – B3 are disabled on ProtoNode FPC-N35 (FPC-N35
LonWorks).
B0 B1 B2 B3
Figure 2-8: BMS Baud Rate DIP Switches
2.5.4.1 Baud Rate DIP Switch Selection
Baud B0 B1 B2 B3
9600
On
On
On
Off
19200
Off
Off
Off
On
38400 *
On
On
Off
On
57600
Off
Off
On
On
76800
On
Off
On
On
* Factory default setting = 38,400
Figure 2-9: BMS Baud Rate

AERCO ProtoNode FPC-N34 & FPC-N35 User Manual
CHAPTER 3 – Interfacing ProtoNode to Devices
OMM-0107_0B AERCO International, Inc. •100 Oritani Dr. •Blauvelt, NY 10913 Page 17 of 108
GF-150 Ph.: 800-526-0288 03/07/2017
CHAPTER 3. Interfacing ProtoNode to Devices
3.1 ProtoNode FPC-N34 and FPC-N35 Showing Connection Ports
Figure 3-1a: Serial ProtoNode BACnet FPC-N34 (P/N 64129)
Figure 3-1b: LonWorks ProtoNode FPC-N35 (P/N 64130)

AERCO ProtoNode FPC-N34 & FPC-N35 User Manual
CHAPTER 3 – Interfacing ProtoNode to Devices
Page 18 of 108 AERCO International, Inc. •100 Oritani Dr. •Blauvelt, NY 10913 OMM-0107_0B
03/07/2017Ph.: 800-526-0288 GF-150
3.2 Device Connections to ProtoNode
ProtoNode 6 Pin Phoenix connector for RS-485 Devices
•The 6 pin Phoenix connector is the same for ProtoNode FPC-N34 and FPC-N35.
•Pins 1 through 3 are for Modbus RS-485 devices.
oThe RS-485 GND (Pin 3) is not typically connected.
•Pins 4 through 6 are for power. Do not connect power (wait until Section 3.6).
Figure 3-2: Power and RS-485 Connections
Device Pins ProtoNode
Pin # Pin
Assignment
Pin RS-485 +
Pin 1
RS-485 +
Pin RS-485 -
Pin 2
RS-485 -
Pin GND
Pin 3
RS-485 GND
Power In (+)
Pin 4
V +
Power In (-)
Pin 5
V -
Frame Ground
Pin 6
FRAME GND

AERCO ProtoNode FPC-N34 & FPC-N35 User Manual
CHAPTER 3 – Interfacing ProtoNode to Devices
OMM-0107_0B AERCO International, Inc. •100 Oritani Dr. •Blauvelt, NY 10913 Page 19 of 108
GF-150 Ph.: 800-526-0288 03/07/2017
3.2.1 Biasing the Modbus RS-485 Device Network
•An RS-485 network with more than one device needs to have biasing to ensure proper
communication. The biasing only needs to be done on one device.
•The ProtoNode has 510 Ohm resistors that can be used to set the biasing. The
ProtoNode’s default positions from the factory for the Biasing jumpers are OFF.
•The OFF position is when the 2 RED biasing jumpers straddle the 4 pins closest to the
outside of the board of the ProtoNode (see Figure 3).
•Only turn biasing ON:
oIF the BAS cannot see more than one device connected to the ProtoNode
oAND you have checked all the settings (Modbus COM settings, wiring, and
DIP switches).
•To turn biasing ON, move the 2 RED biasing jumpers to straddle the 4 pins closest to
the inside of the board of the ProtoNode.
ProtoNode FPC-N34 ProtoNode FPC-N35
Figure 3-3: Modbus RS-485 Biasing Switch
RS-485 Bias
Switch

AERCO ProtoNode FPC-N34 & FPC-N35 User Manual
CHAPTER 3 – Interfacing ProtoNode to Devices
Page 20 of 108 AERCO International, Inc. •100 Oritani Dr. •Blauvelt, NY 10913 OMM-0107_0B
03/07/2017Ph.: 800-526-0288 GF-150
3.2.2 End of Line Termination Switch for the Modbus RS-485 Device Network
•On long RS-485 cabling runs, the RS-485 trunk must be properly terminated at each
end.
•The ProtoNode has an End Of Line (EOL) blue jumper. The default setting for this
Blue EOL jumper is OFF with the jumper straddling the pins closest to the inside of the
board of the ProtoNode.
oOn short cabling runs the EOL jumper may not need to be turned ON.
•If the ProtoNode is placed at one of the ends of the trunk, set the blue EOL
jumper to the ON position straddling the pins closest to the outside of the board
of the ProtoNode.
•Always leave the single Red Jumper on the right in the A position (default
factory setting).
ProtoNode FPC-N34 ProtoNode FPC-N35
Figure 3-4: Modbus RS-485 End-Of-Line Termination Switch
Modbus
RS-485
EOL Switch
Leave in A Position
Other manuals for Aerco ProtoNode FPC-N34
1
This manual suits for next models
3
Table of contents
Other Watts Gateway manuals
Popular Gateway manuals by other brands
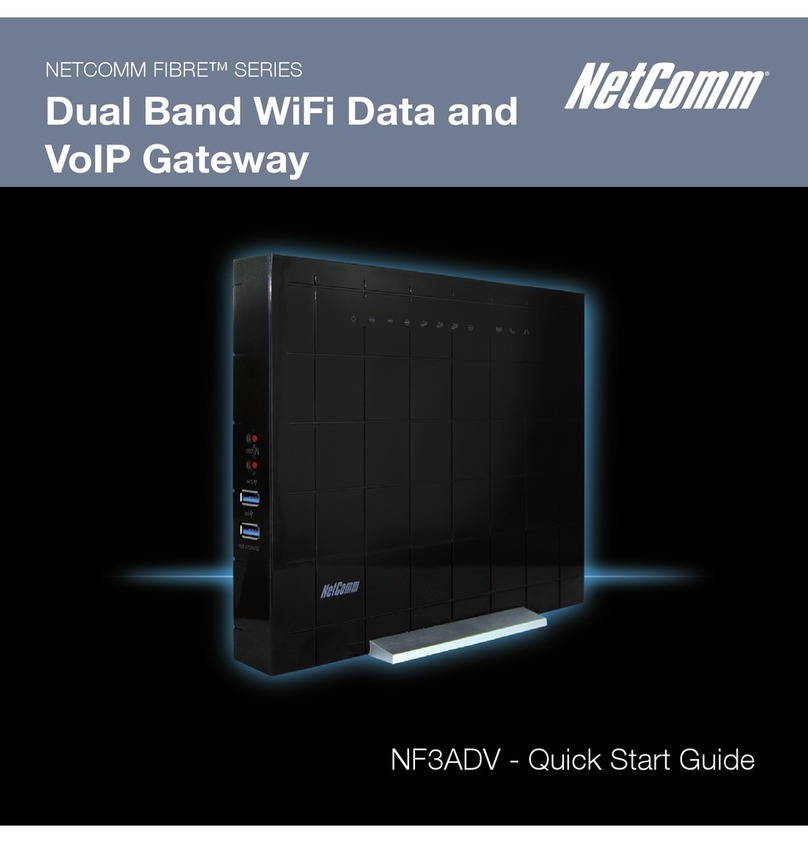
NetComm
NetComm FIBRE NF3ADV quick start guide
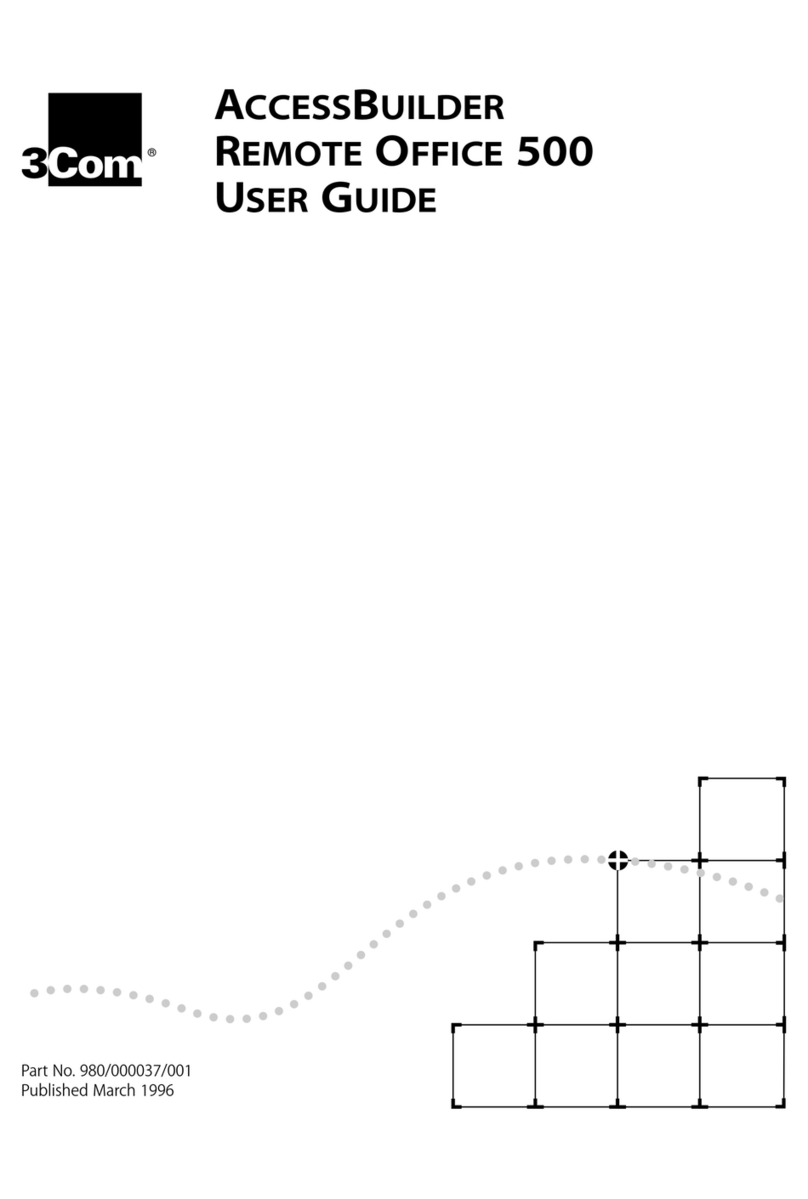
3Com
3Com AccessBuilder 500 user guide

Grandstream Networks
Grandstream Networks BroadWorks BroadSoft GXW-400X Quick installation guide
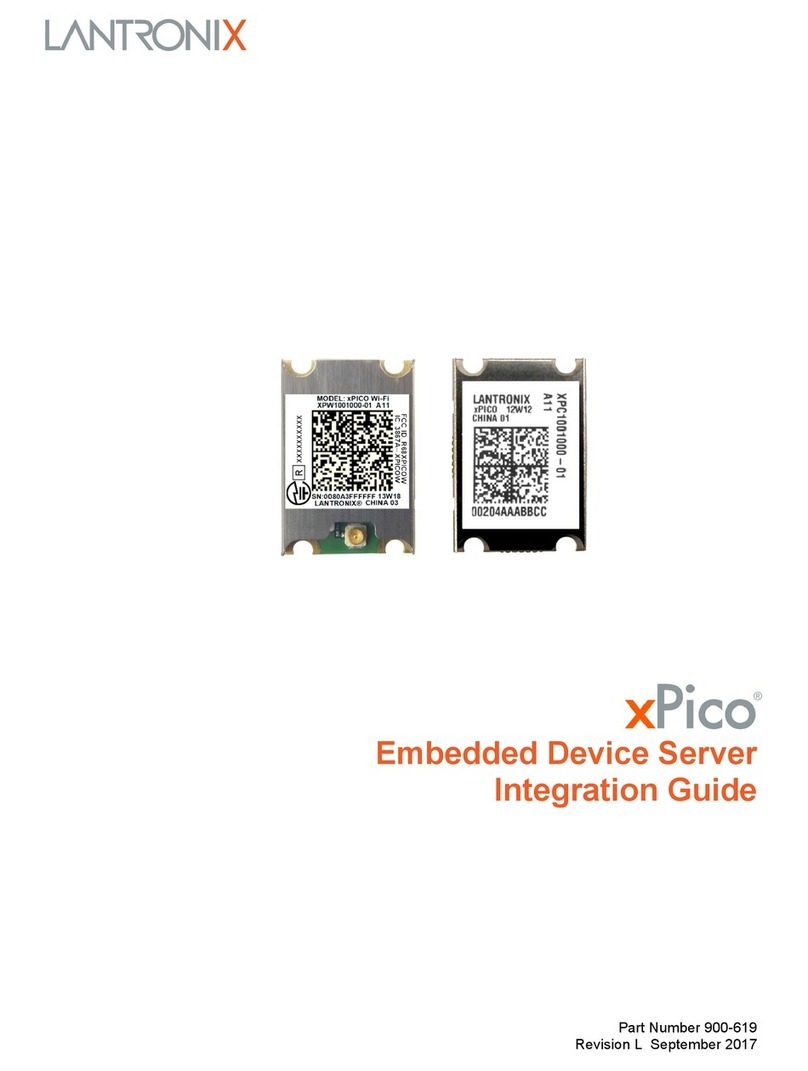
Lantronix
Lantronix xPico 900-619 Integration guide
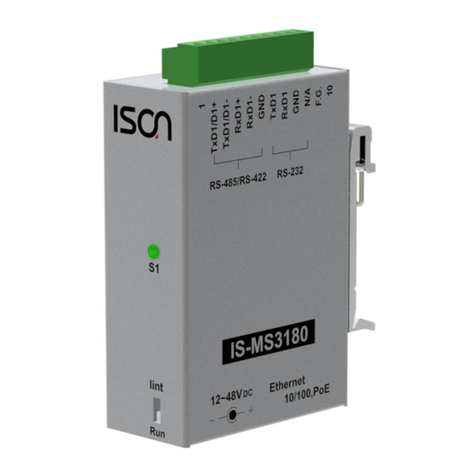
ISON
ISON IS-MS3180 Series user manual
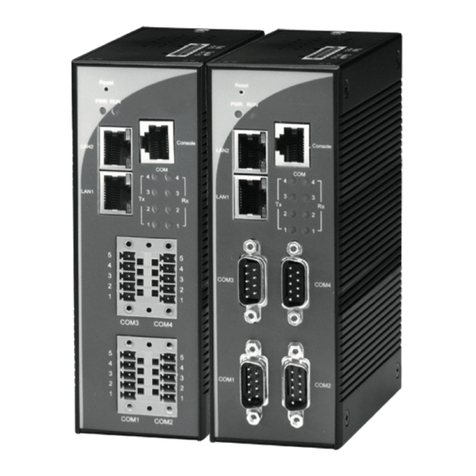
Atop
Atop MB5404D-X Series Hardware installation guide