Wenglor SS2-00VA000R3 User manual

SS2-00VA000R3
Individual Safety Light Barrier Control Unit
Operating instructions
Available as PDF only
Status: 02.05.2016
www.wenglor.com
EN

2
EN
Table of contents
1 General 5
1.1 Function and Use for Intended Purpose 5
1.2 Features 5
1.3 Applications Examples 5
1.3.1 Single Barrier Protection 6
1.3.2 Multiple Barrier Protection 6
1.3.3 Muting Function 6
1.4 Brief Explanation 7
1.5 Explanation of Utilized Symbols 7
2 Important Notes Concerning Use 7
2.1 General Comments 7
2.2 Securing the Danger Zone 8
2.3 Safety Clearance per EN ISO 13855 8
2.3.1 Perpendicular Approach to the Safety Field 9
2.3.2 Parallel Approach to the Safety Field 10
2.4 Minimum Clearance to Reflective Surfaces 10
2.5 Mutual interference of the Light Barriers 11
3 Connection and Installation to the Machine 11
3.1 General 11
3.2 Notes Regarding Connector Cables 12
3.3 Terminal Assignments and LED Display 12
3.4 Connecting the light Barriers 13
3.4.1 Connecting One Light Barrier 14
3.4.2 Connecting Two Light Barriers 15
3.4.3 Connecting Three Light Barriers 16
3.4.4 Connecting Four Light Barriers 17
4 Inputs 18
4.1 Test Input 18
4.2 Acknowledgement Input 18
4.2.1 Selecting the Mode of Operation 18
4.2.2 Automatic Restart 18
4.2.3 Restart Inhibit 19
4.3 Contactor Monitoring 20

3
5 Outputs 22
5.1 Safety Outputs 22
5.2 Signal Control 22
5.3 Muting Signal Output 22
6 Muting 22
6.1 Basics 22
6.2 Connecting the Muting Sensors and the Muting Indicator 23
6.2.1 Muting Sensors 23
6.2.2 Muting Indicator 23
6.3 Selecting a Muting Duration 24
6.4 Mode of Operation 24
6.4.1 Muting Procedure 25
6.4.2 Muting Time Sequence 26
7 Override 26
7.1 Basics 26
7.2 Settings 26
7.2.1 Selecting the Mode of Operation 26
7.2.2 Override with Continuous Command 27
7.2.3 Override with Command Pulse 27
8 Functions and Operation 28
8.1 Use of One Channel 28
8.2 Use of Two Channel 28
8.3 Muting Modul 28
9 Diagnosis Information 29
10 Inspection Instructions 30
10.1 Inspection Prior to Initial Start-Up 30
10.2 Daily Inspection and Maintenance 30
10.3 Yearly Inspection and Maintenance 30
11 Environmentally Sound Disposal 31
12 Dimensional Drawings 31
13 Accessories and Order Designation 32

4
EN
Due to the fact that they describe the operation of a safety device, these operating instructions are of a binding
nature.
14 Technical Data 32
14.1 Safety Light Barriers 32
14.2 Individual Light Barrier Control Unit 33
15 Checklist 35
16 Certification 35
17 EC Declaration of Conformity 36
17.1 Declaration of conformity for Individual Safety Light Barrier Control Units SS2 36
17.2 Declaration of conformity for Safety Through Beam Sensor SL2 37

5
1 General
The SS2-00VA000R3 Individual Light Barrier Control Unit is part of a design-approved, contactless safety device in
accordance with EN 61496-1 for electro-sensitive protective equipment (ESPE).
It’s a type 2 safety device in per EN 61496-1.
The ESPE consists of an Individual Light Barrier Control Unit to which as many as four sensors can be connected.
Use of the Individual Light Barrier Control Unit is only permitted with wenglor SL2-00 Light Barriers (see section 13
for order designations). Safety category 2 and Performance Level c is otherwise not assured.
For this reason, use with SL2-00 Light Barriers is described in these operating instructions.
• It is absolutely essential to observe all of the instructions included herein in order to assure safe use of the ESPE.
• Non-observance of the instructions included herein may place the operator of the system into great danger.
1.1 Function and Use for Intended Purpose
The Individual Light Barrier Control Unit monitors the safety field between the light barriers. If the safety field is
penetrated by an object, a switching command is triggered. This switching command may prevent initialization
of a hazardous machine motion, or may stop an action which has already been started.
Use of the Individual Light Barrier Control Unit in combination with SL2-00NE000H2/SL2-00NS000H2 oder
SL2-00TE000H1/SL2-00TS000H2 Light Barriers is only permissible if:
• The hazardous motion can be stopped electrically by the safety output of the Individual Light Barrier Control Unit
• The use of a type 2 safety device is permissible in accordance with the risk analysis
After completion of every new installation or change of the configuration, the entire safety system must be tested for
correct functioning (i.e. Individual Light Barrier Control Unit, Safety Light Barriers and the machine). In particular if the
restart inhibit mode was originally activated, it must be assured that the unit is once again configured for this mode
of operation. In order to check the safety field a testing stick (see section 8) can be used.
1.2 Features
• Safety device per EN 61496-1, type 2
• TÜV certification
• Long working range with SL2-00TS000H2 and SL2-00TE000H1 (transmitter/receiver)
• Easy to use
• Floating safety relay outputs (normally open contacts)
• Either restart inhibit or automatic restart
• Monitoring of external safety relays
• For connection of up to 4 light barriers
• One PNP output for displaying system status
• Periodic self-testing of the connected safety light barriers (every 20 seconds)
• Integrated muting function
• One muting enable input
• One PNP output for connecting a muting indicator
• Muting duration of either 30 seconds or unlimited
• Integrated override function
1.3 Applications Examples
A risk analysis is decisive regarding use of the Individual Light Barrier Control Unit.
Use is conceivable with the following types of machines:
• Palletizers
• Textile machinery
• Transfer and assembly lines
• Automatic insertion equipment
• Packaging machines
• Rotary indexing machines
• Woodworking machines
• Warehouse technology

6
EN
1.3.1 Single Barrier Protection
Use for securing robots
1.3.2 Multiple Barrier Protection
Use for access monitoring
1.3.3 Muting Function
Safety Light Barrier
Receiver
Muting Sensor
Receiver 1
Muting Sensor
Receiver 2
Safety Light Barrier
Transmitter
Muting Sensor
Transmitter 2
Muting Sensor
Transmitter 1

7
1.4 Brief Explanation
Contactor Monitoring
An operating mode for which switching performance of the contacts at an external relay is dynamically monitored.
The contacts must close fully within a specified period of time.
Muting Mode
Objects can be fed through the safety field without switching the safety output in this operating mode.
OSSD (Output Signal Switching Device)
The output of the contactless safety device which is connected to the machine controls. The safety output is deac-
tivated when the safety field is interrupted.
Override
This function enables to switch the outputs ON if the protection zone is interrupted. If there is for example after an
error during the Muting Operation Mode still material within the protection zone, this material can be removed with
the help of the Override function.
Restart Inhibit
A function which prevents a machine from starting up automatically after it has been switched on. The machine can
only be enabled by activating an acknowledgement key.
Safety Operating Mode
In this operating mode, the switching outputs are disabled when the safety field is penetrated. The switching outputs
are automatically enabled after penetration of the safety field is ended.
Signal Output
The signal output is used to connect a watchdog for the floating blanking, auto floating blanking and reduced reso-
lution function types.
1.5 Explanation of Utilized Symbols
Makes reference to a measure for the prevention of a concrete danger.
Illustrates suggestions and instructions, which make use of the controller easier.
2 Important Notes Concerning Use
2.1 General Comments
The use of electro-sensitive protective equipment (ESPE) is regulated by official directives. National and
international regulations apply to the safe utilization of ESPE, in particular:
• EN standards
• Accident prevention regulations
Contactless safety devices may only be used at power operated machinery whose controls can be electrically influ-
enced such that hazardous motion can be stopped immediately during all operating phases.
A risk analysis in accordance with ISO 14121 must be conducted before use, in order to determine whether or not
the use of a safety device Performance Level c per EN ISO 13849-1 is permissible.
If other light beams occur in an application (e.g. use of infrared controls, radiation of welding processes,
stroboscope lights) additional measures could be necessary to assure that the ESPE doesn’t fail dangerously.
Powerful fluorescent lamps must not be pointed directly towards the receiver’s lens. The receiver
might otherwise fail in a hazardous manner.
Testing must be performed by an expert prior to initial start-up of electro-sensitive protective equipment.
Testing must establish flawless interaction of the electro-sensitive protective equipment together with the
controls of the power operated machinery, and correct installation in accordance with these safety precau-
tions.

8
EN
2.2 Securing the Danger Zone
The danger zone must be secured by means of the light barriers alone, or by means of the light barriers in
combination with additional mechanical safety devices. Reaching around, over and/or under the safety field must
be prevented in any case. It must be impossible to approach the point of danger without passing through the light
barriers. The safety field is located between the beam emission of the sender and the beam entry at the receiver. The
beam diameter is smaller than 30 mm.
The Light Barriers are only allowed to be used to secure access according to EN ISO 13855. The use for
finger and hand protection is not allowed.
2.3 Safety Clearance per EN ISO 13855
Safety clearance S is calculated with the following formula in accordance with EN ISO 13855: S = K × T +C
A gripping speed of 1,6 meters per second is assumed.
Example:
Danger Zone
Standstill Standstill
Stop Signal
S = Minimum safety clearance in mm, measured from the danger zone to the point of detection, to the line of
detection or to the safety field.
K = Approach speed constant in mm per sec. = 1600 mm per sec.
T = Total response time (t1 + t2) in seconds
t1 = Response time of the Individual Light Barrier Control Unit in seconds
t2 = Machine or process over-travel time in seconds
C = Additional clearance in mm (margin), which is based upon penetration into the danger zone before the safety
device is triggered
Obstruction of the safety field during hazardous motion results in immediate shutdown. The distance between
the safety field and the point of danger must be large enough to assure that the point of danger cannot be
reached until hazardous motion has come to a standstill. This safety clearance depends upon total over-travel time,
as well as the person’s maximum gripping or walking speed.
Total over-travel time is the sum of maximum response time of the ESPE and maximum over-travel time of the
hazardous motion. Machine over-travel time must be determined by means of repeated measurement prior to
initial start-up, and each time the machine is retooled or set up.
In order to secure the danger zones, the safety heights set forth in EN ISO 13855 are determined by means of a risk
analysis in accordance with EN ISO 13849-1.

9
2.3.1 Perpendicular Approach to the Safety Field
Direction of
Approach
Installation Height 750 mm
A minimum installation height of 750 mm
from the reference level is required for the
use of a light barrier
C = Margin for penetration into the dan-
ger zone before the safety device is
tripped (never < 0) = 1200 mm
K = 1600 mm per second
S = K×(t1+t2)+C(1200 mm)
Direction of
Approach
If more than one light barrier is used, the
table included below applies.
C = Margin for penetration into the dan-
ger zone before the safety device is
tripped (never < 0) = 850 mm
K = 1600 mm per second
S = K×(t1+t2)+C(850 mm)
The number of utilized light barriers is based upon EN ISO 13855 in consideration of the relevant level C
standard.
Number of
Light Barriers
Installation Height in mm Above the Reference Level
Barrier 1 Barrier 2 Barrier 3 Barrier 4
1 750
2 400 900
3 300 700 1100
4 300 600 900 1200

10
EN
2.3.2 Parallel Approach to the Safety Field
If this safety concept is used, the height of the safety field (H) may not be any greater than 1000 mm. If H is
greater than 300 mm (or 200 mm for non-industrial applications, e.g. if children are present), one runs the
risk of inadvertent, undetected access from underneath the safety field. This must be taken into consider-
ation during risk analysis.
H = Height of the safety field above the reference level
C = Margin for penetration into the danger zone before the safety device is tripped (never < 850) = 1200 mm -
0.4×H
K = 1600 mm per second
S = K×(t1+t2)+C(1200 mm - 0,4×H)
Direction of
Approach
S = Minimum safety clearance
H = Height of the safety field
2.4 Minimum Clearance to Reflective Surfaces
If reflective surfaces are located within the aperture angle between the transmitter and the receiver, reflection may
result which could cause an obstruction to go undetected. For this reason, a minimum clearance (m) between
reflective objects and the optical axis must be maintained.
Beam angles are taken from the IEC 61496-2 standard. They represent worst case values. Actual values are lower.
Danger Zone
Reflective
Object
Central Beam
Transmitter Receiver
Light Beam
Obstructed m = tan a× (distance from transmitter to receiver
a= Opening Angle of Emitter and Receiver Optic
a= ±5°

11
Max. distance m in m
Distance in Meters
2.5 Mutual interference of the Light Barriers
In order to inhibit a mutual interference of the Light Barriers, to following points have to be adhered to:
• Within the opening angle of the receiver (transmitter) should only be the transmitter (receiver).
• In case of Multiple Barrier Protection an arrangement of the Light Barriers according to the following picture has
to be preferred:
Emitter
Receiver
Emitter
Receiver
Emitter
Receiver
3 Connection and Installation to the Machine
3.1 General
The Individual Light Barrier Control Unit must be integrated into the system such that at least IP 54 protection
is assured (e.g. installation to a control cabinet).
After the light barriers have been mechanically mounted (see operating instructions for SL2-00), the
SS2-00VA000R3 control unit is linked to the machine’s controller.
The OSSD outputs must be connected to the machine’s safety circuit such that safety category 2 is still
complied with. The safety precautions for the respective machine, and for connection to the machine’s
controller, must also be observed.

12
EN
If several control units are mounted next to each other, a minimum clearance of 2 cm must be maintained
between the units in order to avoid overheating.
The control unit must be provided with 24 V DC ± 20% supply power.
External power supply must comply with EN 60204-1.
It is absolutely essential that terminals 17 and 18 are not short-circuited during installation.
Additional measures for the prevention of electrostatic discharge should be implemented during installation,
troubleshooting and adjustment.
It is advisable to furnish the connector cables with wire end ferrules before installing the light barriers.
3.2 Notes Regarding Connector Cables
• Cables with a cross-section of greater than 1 square mm must be used for connections between safety light bar-
riers and the control with lengths of more than 50 meters.
• Supply power for the control unit should be isolated from other electrical equipment (electrical motors, inverters,
frequency variators), as well as any other sources of interference.
• The connector cables between the control unit and the sensors, connector cables to the test command generator
and to the feedback contacts connected to terminal 20 must be laid separately from power conducting cables.
3.3 Terminal Assignments and LED Display
M1
M2
MUT
123
CH1
CH2/
Failure
OSSD/
DIAG
456
789
10 11 12
13 15
16 17 18
19 20 21
22 23 24
Terminal Designation Input/
Output
Further
Information
1 Muting input 1 I p. 23, section
6.2
2 Muting input 2 I p. 23, section
6.2
3 24 V DC – –
4 Muting duration 1 I p. 24, section
6.3
5 Muting duration 2 I p. 24, section
6.3
6 Restart inhibit I p. 19, section
4.2.3
7 Override 1 I p. 26, section 7
8 Override 2 I p. 26, section 7
9 S1 test O –
10 Muting signal O p. 22, section
5.3
11 Muting enable I –
12 OSSD B contact 1 O –
13 0 V – –
14 PE (ground) – –
15 Acknowledgement input Ip. 18, section
4.2
16 contact I p. 18, section
4.1
17 S1 contact I –
18 S2 contact I –
19 S2 test O –
20 Contactor monitoring I p. 20, section
4.3
21 Signal control O –
22 OSSD B contact 2 O –
23 OSSD A contact 1 O –
24 OSSD A contact 2 O –

13
LED Color Status Operating State
M1 Yellow Off Muting sensor 1 unobstructed
On Muting sensor 1 obstructed
M2 Yellow Off Muting sensor 2 unobstructed
On Muting sensor 2 obstructed
MUT Yellow
Off Normal operation
On Muting active
Blinking • Override request
• Muting failure (only with CH/Failure on) *
CH1 Green On Channel 1 unobstructed
Off Channel 1 obstructed
CH2
Failure
Green,
Red
Red Failure detected *
Green Channel 2 unobstructed
Off Channel 2 unobstructed or unused
OSSD
DIAG
Green,
Red,
Yellow
Red Output relay open
Red
blinking
The number of pulses indicates the type of
failure (only when CH2/Failure is on) *
Green Output replay closed
Yellow Channel unobstructed – relay open
(only with restart inhibit)
* See error codes on page 29 in section 9
3.4 Connecting the light Barriers
The following wiring diagrams demonstrate connection of the light barriers to the control unit using the automatic
restart setting, and without contact monitoring.
It must be assured that a muting indicator is always connected, in order to assure correct functioning
of the controller.

14
EN
3.4.1 Connecting One Light Barrier
**
24 V DC 24 V DC
0 V
1
2
3
4
5
6
7
8
9
10
11
12
13
14
15
16
17
18
19
20
21
22
23
24
*
Transmitter 1
SL2-00
Receiver 1
SL2-00
Muting Sensor 1
Muting Sensor 2
* See page 23 in section 6.2.1
** See page 23 in section 6.2.2
Terminal Designation Input/
Output
Further
Information
1 Muting input 1 I p. 23, section 6.2
2 Muting input 2 I p. 23, section 6.2
3 24 V DC – –
4 Muting duration 1 I p. 24, section 6.3
5 Muting duration 2 I p. 24, section 6.3
6 Restart inhibit I p. 19, section 4.2.3
7 Override 1 I p. 26, section 7
8 Override 2 I p. 26, section 7
9 S1 test O –
10 Muting signal O p. 22, section 5.3
11 Muting enable I –
12 OSSD B contact 1 O –
13 0 V – –
14 PE (ground) – –
15 Acknowledgement input I p. 18, section 4.2
16 contact I p. 18, section 4.1
17 S1 contact I –
18 S2 contact I –
19 S2 test O –
20 Contactor monitoring I p. 20, section 4.3
21 Signal control O –
22 OSSD B contact 2 O –
23 OSSD A contact 1 O –
24 OSSD A contact 2 O –

15
3.4.2 Connecting Two Light Barriers
**
24 V DC
24 V DC
0 V
1
2
3
4
5
6
7
8
9
10
11
12
13
14
15
16
17
18
19
20
21
22
23
24
*
24 V DC
Receiver 1
SL2-00
Receiver 2
SL2-00
Transmitter 1
SL2-00
Transmitter 2
SL2-00
Muting Sensor 1
Muting Sensor 2
* See page 23 in section 6.2.1
** See page 23 in section 6.2.2.
Terminal Designation Input/
Output
Further
Information Terminal Designation Input/
Output
Further
Information
1 Muting input 1 I p. 23, section 6.2 13 0 V – –
2 Muting input 2 I p. 23, section 6.2 14 PE (ground) – –
3 24 V DC – – 15 Acknowledgement input I p. 18, section 4.2
4 Muting duration 1 I p. 24, section 6.3 16 Test input I p. 18, section 4.1
5 Muting duration 2 I p. 24, section 6.3 17 S1 NO contact I –
6 Restart inhibit I p. 19, section
4.2.3 18 S2 NO contact I –
7 Override 1 I p. 26, section 7 19 S2 test O –
8 Override 2 I p. 26, section 7 20 Contactor monitoring I p. 20, section 4.3
9 S1 test O – 21 Signal control O –
10 Muting signal O p. 22, section 5.3 22 OSSD B contact 2 O –
11 Muting enable I – 23 OSSD A contact 1 O –
12 OSSD B contact 1 O – 24 OSSD A contact 2 O –

16
EN
3.4.3 Connecting Three Light Barriers
**
24 V DC 0 V
1
2
3
4
5
6
7
8
9
10
11
12
13
14
15
16
17
18
19
20
21
22
23
24
*
24 V DC
24 V DC
24 V DC
Muting Sensor 2
Muting Sensor 1
Transmitter 3
SL2-00
Transmitter 1
SL2-00
Transmitter 2
SL2-00
Receiver 2
SL2-00
Receiver 3
SL2-00
Receiver 1
SL2-00
* See page 23 in section 6.2.1
** See page 23 in section 6.2.2
Terminal Designation Input/
Output
Further
Information Terminal Designation Input/
Output
Further
Information
1 Muting input 1 I p. 23, section 6.2 13 0 V – –
2 Muting input 2 I p. 23, section 6.2 14 PE (ground) – –
3 24 V DC – – 15 Acknowledgement input I p. 18, section 4.2
4 Muting duration 1 I p. 24, section 6.3 16 Test input I p. 18, section 4.1
5 Muting duration 2 I p. 24, section 6.3 17 S1 NO contact I –
6 Restart inhibit I p. 19, section
4.2.3 18 S2 NO contact I –
7 Override 1 I p. 26, section 7 19 S2 test O –
8 Override 2 I p. 26, section 7 20 Contactor monitoring I p. 20, section 4.3
9 S1 test O – 21 Signal control O –
10 Muting signal O p. 22, section 5.3 22 OSSD B contact 2 O –
11 Muting enable I – 23 OSSD A contact 1 O –
12 OSSD B contact 1 O – 24 OSSD A contact 2 O –

17
3.4.4 Connecting Four Light Barriers
**
24 V DC 0 V
1
2
3
4
5
6
7
8
9
10
11
12
13
14
15
16
17
18
19
20
21
22
23
24
*
24 V DC
24 V DC
24 V DC
24 V DC
Transmitter 1
SL2-00
Transmitter 3
SL2-00
Transmitter 4
SL2-00
Transmitter 2
SL2-00
Receiver 1
SL2-00
Receiver 3
SL2-00
Receiver 4
SL2-00
Receiver 2
SL2-00
Muting Sensor 1
Muting Sensor 2
* See page 23 in section 6.2.1
** See page 23 in section 6.2.2.
Terminal Designation Input/
Output
Further
Information Terminal Designation Input/
Output
Further
Information
1 Muting input 1 I p. 23, section 6.2 13 0 V – –
2 Muting input 2 I p. 23, section 6.2 14 PE (ground) – –
3 24 V DC – – 15 Acknowledgement input I p. 18, section 4.2
4 Muting duration 1 I p. 24, section 6.3 16 Test input I p. 18, section 4.1
5 Muting duration 2 I p. 24, section 6.3 17 S1 NO contact I –
6 Restart inhibit I p. 19, section
4.2.3 18 S2 NO contact I –
7 Override 1 I p. 26, section 7 19 S2 test O –
8 Override 2 I p. 26, section 7 20 Contactor monitoring I p. 20, section 4.3
9 S1 test O – 21 Signal control O –
10 Muting signal O p. 22, section 5.3 22 OSSD B contact 2 O –
11 Muting enable I – 23 OSSD A contact 1 O –
12 OSSD B contact 1 O – 24 OSSD A contact 2 O –

18
EN
4 Inputs
4.1 Test Input
A self-test is started at the control unit by applying 24 V DC to the test input (terminal 16). When the control
unit’s safety inputs are activated, the control unit indicates that testing is being executed by shutting down the
transmitters at the connected safety light barriers, and thus simulating penetration of the protected area. The
operator must then check the effectiveness of the shut down. The transmitters are shut down for as long
as 24 V DC is applied to the input.
The externally triggered test has no significance with regard to testing the control unit, because it is self-testing.
The test pulse has a minimum duration of 40 ms. Test frequency is based upon the risk analysis (safety
regulations).
4.2 Acknowledgement Input
The control unit can be setup with either restart inhibit of automatic restart.
The use of restart inhibit (start and restart disabled) is required if the safety device is used to secure a passageway
to the danger zone, and if it is possible for a person to be present in the danger zone without being detected after
traversing the passageway.
4.2.1 Selecting the Mode of Operation
The following table depicts configuration of the operating modes.
Selecting the Mode of Operation
Terminal 6 Terminal 15 Mode of Operation
0 V not connected 24 V DC Automatic restart
24 V DC 0 V not connected Restart inhibit
0 V not connected 0 V not connected Impermissible operation
24 V DC 24 V DC
4.2.2 Automatic Restart
In this operating mode, the control unit’s outputs correspond to the status of the light barriers:
• If the safety zone is unobstructed (light barrier outputs active), the relay outputs are activated.
• If the safety zone is obstructed (light barrier outputs inactive), the relay outputs are deactivated.

19
Terminal Designation Input/
Output
Further
Information Terminal Designation Input/
Output
Further
Information
1 Muting input 1 I p. 23, section 6.2 13 0 V – –
2 Muting input 2 I p. 23, section 6.2 14 PE (ground) – –
3 24 V DC – – 15 Acknowledgement input I p. 18, section 4.2
4 Muting duration 1 I p. 24, section 6.3 16 Test input I p. 18, section 4.1
5 Muting duration 2 I p. 24, section 6.3 17 S1 NO contact I –
6 Restart inhibit I p. 19, section
4.2.3 18 S2 NO contact I –
7 Override 1 I p. 26, section 7 19 S2 test O –
8 Override 2 I p. 26, section 7 20 Contactor monitoring I p. 20, section 4.3
9 S1 test O – 21 Signal control O –
10 Muting signal O p. 22, section 5.3 22 OSSD B contact 2 O –
11 Muting enable I – 23 OSSD A contact 1 O –
12 OSSD B contact 1 O – 24 OSSD A contact 2 O –
4.2.3 Restart Inhibit
In this operating mode, the control unit’s outputs are only activated if the safety field is unobstructed and the cor-
responding signal has been received at the unit’s acknowledgement input (terminal 15) from a pushbutton, or by
means of an appropriate command, for example from a PLC. After penetration into the protected area, the relay
outputs are deactivated, and can only be reactivated by means of the above described procedure.
A slope from 0 V to 24 V DC at the acknowledgment input serves as the acknowledgement signal.
The 24 V DC signal must be applied for at least 100 ms. The maximum current value is 20 mA.
These values are of special importance if transmission of the acknowledgement input signal will be managed auto-
matically, for example by a PLC. An external NO pushbutton can be used to manually generate the acknowledge-
ment input signal.
The system’s power-up delay time results from the sum of the power-up delay times of the control unit (150 ms) and
any K1/K2 auxiliary contact elements which might be used.
Acknowledgement must originate from outside of the protected area, from a location at which the protected area
and all of the effected working area can be clearly observed.
The button for the acknowledgement input may not be accessible from inside the protected area.
Restart

20
EN
Terminal Designation Input/
Output
Further
Information Terminal Designation Input/
Output
Further
Information
1 Muting input 1 I p. 23, section 6.2 13 0 V – –
2 Muting input 2 I p. 23, section 6.2 14 PE (ground) – –
3 24 V DC – – 15 Acknowledgement input I p. 18, section 4.2
4 Muting duration 1 I p. 24, section 6.3 16 Test input I p. 18, section 4.1
5 Muting duration 2 I p. 24, section 6.3 17 S1 NO contact I –
6 Restart inhibit I p. 19, section
4.2.3 18 S2 NO contact I –
7 Override 1 I p. 26, section 7 19 S2 test O –
8 Override 2 I p. 26, section 7 20 Contactor monitoring I p. 20, section 4.3
9 S1 test O – 21 Signal control O –
10 Muting signal O p. 22, section 5.3 22 OSSD B contact 2 O –
11 Muting enable I – 23 OSSD A contact 1 O –
12 OSSD B contact 1 O – 24 OSSD A contact 2 O –
4.3 Contactor Monitoring
Contactor monitoring is used to determine whether or not external contactors or auxiliary contact elements func-
tion properly. External contactors may only be connected if they are equipped with positively driven, normally
closed contacts. The contactors are monitored statically and dynamically for correct timing performance of the
contacts. Switching time may not exceed 300 ms. 24 V DC is returned to the input via an available NC contact
at the external contactor.
Input for Contactor Monitoring
If external relays or K1 and K2 auxiliary contact elements with positively driven contacts are used, 24 V DC must be
connected in series to the contactor monitoring input (terminal 20) via control contacts K1-1 and K2-1 (NC, block B
in the graphic). Monitoring for correct switching of K1 and K2 is delayed 300 ms after the effective command.
If no K1 and K2 auxiliary contact elements are used, terminals 20 (contact monitoring) and 21 (signal monitoring)
must be connected to each other.
Table of contents
Other Wenglor Control Unit manuals
Popular Control Unit manuals by other brands
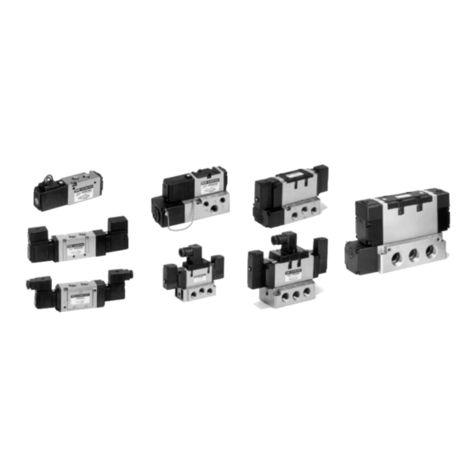
SMC Networks
SMC Networks VFS1000 instruction manual
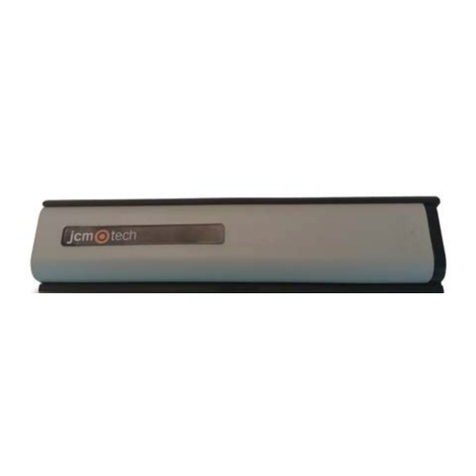
jcm-tech
jcm-tech RB3 TGL868 user manual
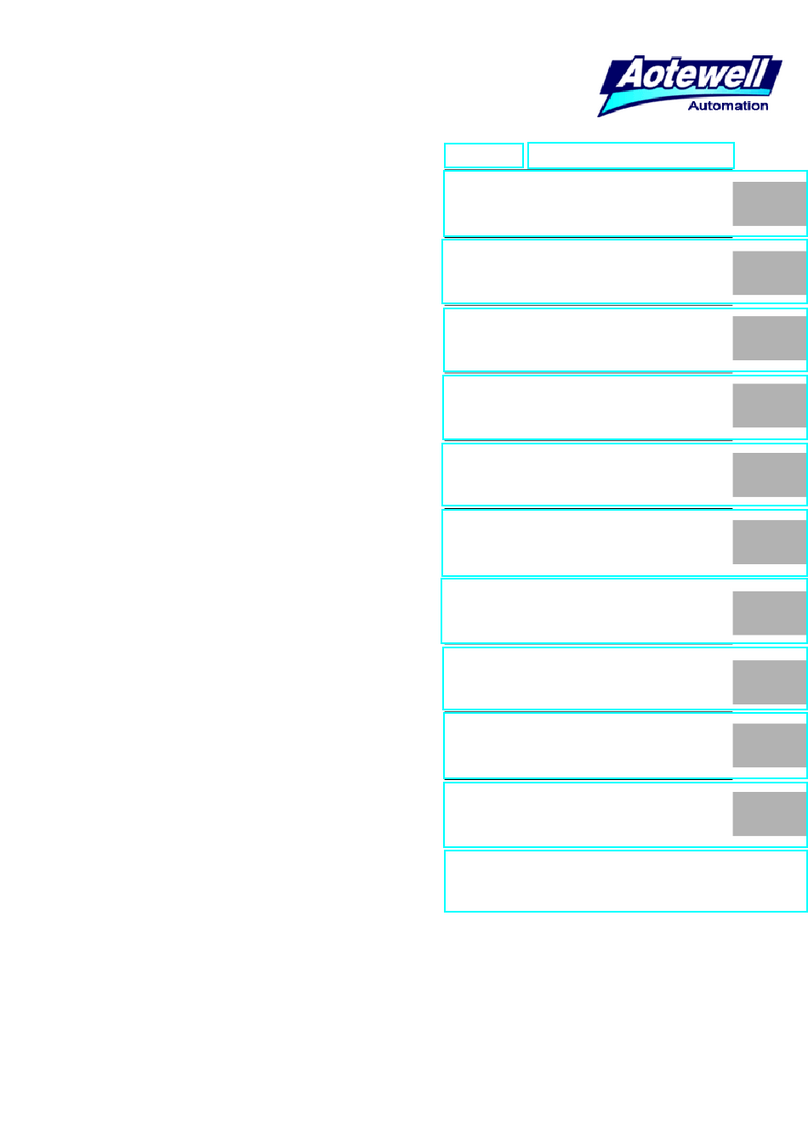
Siemens
Siemens SIMADYN D Hardware manual
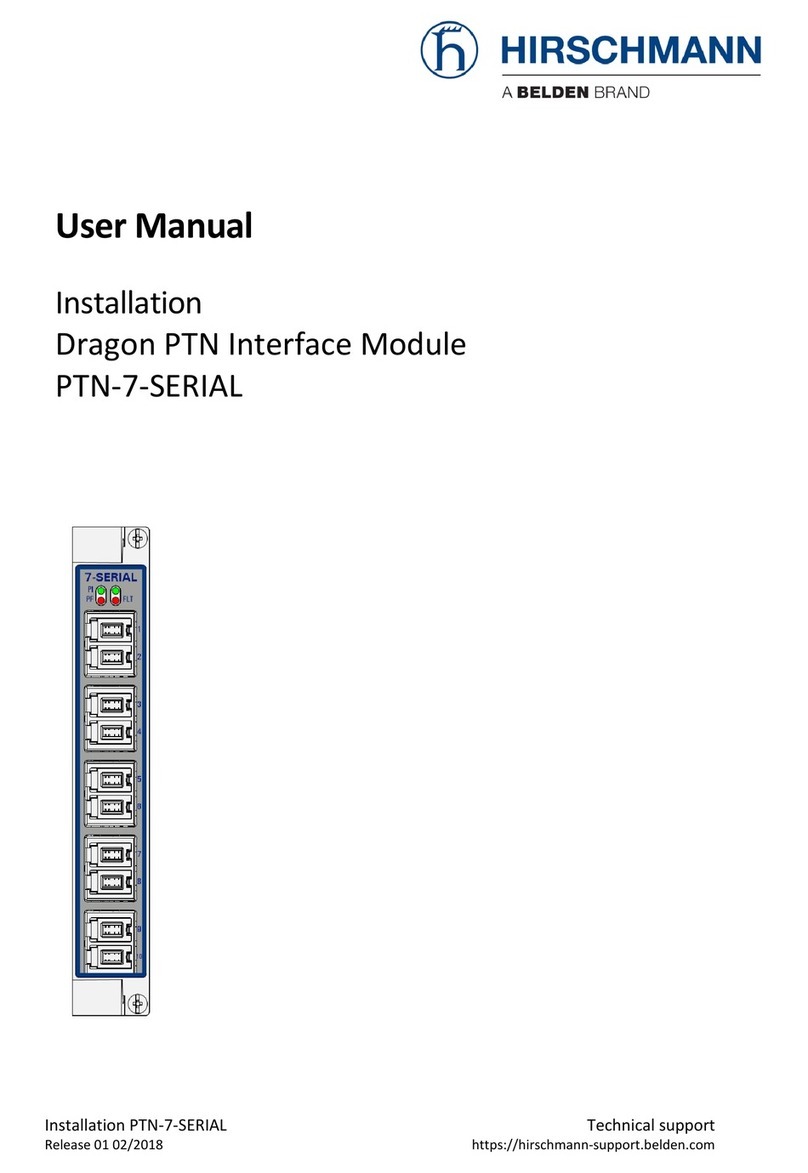
Hirschmann
Hirschmann PTN-7-SERIAL user manual

Pacific Recorders & Engineering Corporation
Pacific Recorders & Engineering Corporation LSM-10 Technical manual
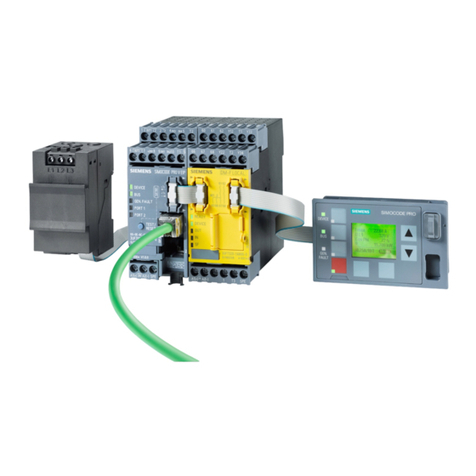
Siemens
Siemens SIMOCODE pro manual