WEST VENTMISER CMSM User manual

1
West Energy Saving Technologies Ltd
76 Cow Lane, Bramcote
Nottingham NG9 3BB
Tel: 00 44(0)115 9222940
Fax: 00 44(0)115 9250222
www.westenergy.co.uk
Ventmiser and Cookermiser are patented devices.
TWIN & MULTI-INPUT AUTOMATIC FAN CONTROLLER
Automatic Fan Controllers with
Current and Temperature Sensing Options
for Kitchen & Bathroom Appliances
Installation Instructions

2
Automatic Fan Controllers with Current
and Temperature Sensing Options for
Kitchen & Bathroom Appliances
Installation Instructions
85 mm
159 mm
45 mm
Front view
Top view
Side view
Description
VENTMISER CMSM twin and multi-input automatic fan
controllers comprise of a main controller with the optional
choice of either or both current and temperature sensors which
detects when a cooker, shower or other moisture producing
appliances are in use.
Twin-input unit - normally used to control local extract fans.
Multi-input unit is ideal for controlling MEV and MVHR.
At the dictates of the input signal/signals the onboard microprocessor
will automatically turn on an extract system or boost a central
ventilation system such as a MEV or MVHR.
Multi-input automatic fan controllers incorporate a load
potentiometer and time potentiometer for each group of three
current and each group of three temperature sensors.
Both variants - the twin and multi-input units incorporate a manual
override input which can receive a signal from one or several push
buttons.
For electric showers and cookers a current sensor is used to
detect the flow of current.
For conventional showers (fed from a hot water system) a
temperature sensor is used to detect the presence of hot water
in the hot water pipe to the shower mixer.
Both current and temperature sensors are normally supplied with a
cable lengths as follows:
Twin-input unit: 4, 6 and 12 metre lengths.
Multi-input unit: 4, 6 and 12 metre lengths.
VENTMISER CMSM Twin and multi-input automatic fan
controllers are robust, with the main printed circuit board (PCB)
mounted in a stylish white, fire retardant (V0 rated) ABS enclosure.
Controllers are suitable for 230V single phase 50 Hz extractor fans
up to 2 amps or 500 watts. The control unit has a change over relay
rated at 10amps (resistive load).
Dimensions
Installation
Installation must be carried out by a qualified electrician
conforming to all statutory and governing regulations.
Safety
1. Isolate the feed to the electric cooker/shower at the distribution
board by turning off the breaker or removing the fuse.
2. Isolate the fused spur serving the extractor fan at the
distribution board by turning off the breaker orremoving the
fuse.
3. Test electrical tester in a live socket to prove functionality, then
test both the electric shower feed and the fused spur serving
the fan to ensure they are at zero voltage and safe to work on.
Once items 1 – 3 have been carried out, proceed as follows:
4. Establish a suitable position for the main control unit, and secure
to wall, or timber. N.B the control unit must be sited well
away from the shower or bath as prescribed in the current
IEE regulations. Remember the enclosure is not water proof.
5. Wire live neutral and earth from fused spur into the controller as
indicated in figure 4 and 5. (i.e. “LIVE IN”, “NEUTRAL IN” &
EARTH).
6. Wire live neutral and earth from the controller to the fan as
indicated in figure 4 and 5. (i.e. “N.O./LIVE OUT”, “NEUTRAL
OUT” & EARTH.
Current Sensing (For Cookers)
7a. Remove the cooker switch by removing the screws (check that
there is still no voltage, using tester).
Carefully pull the switch away from the back box and decide
upon the best possible position within the backbox to mount
the sensor. Disconnect the live conductor from the switch and
carefully thread the sensor over same. Slide the sensor over the
conductor to a position where it will not be trapped.
Reconnect the live conductor back into the terminal from where
it was removed.
Current Sensing (For Showers)
7b. Where used for current sensing to an electric shower, find a
suitable position to fit the current sensor, this could be in a local
isolator, at the distribution board or inside the shower unit.
Once the position has been determined, (check that there is still
no voltage using tester). Disconnect the live conductor from
the switch or shower and carefully thread the sensor over same.
Slide the sensor over the conductor to a position where it will
not be trapped.
Reconnect the live conductor back into the terminal from where
it was removed.
8. From wherever the sensor is fitted, find a suitable route to run
the sensor control wiring to the main controller. If fitted in a
shower unit ensure that you do not damage the waterproof
integrity in any way.
At all times ensure the wire does not get damaged by trapping
of the cable when re instating casings or covers to isolators.
9. Wire the cable into the terminals as indicated in the wiring
diagrams.
10. Test out all wiring, ensure that fan has a good earth by carrying
out a continuity test between the fused spur and the fan.
TWIN & MULTI-INPUT AUTOMATIC FAN CONTROLLER
Fig 1. Dimensions for twin and multi-input controllers.

3
Fig 2:Typical twin controller current sensor installation.
11. Turn on the breaker and switch to the fused spur, the healthy
LED should flash/blink.
12. Turn down the Load Pot to the mid position and Time Pot to
minimum.
13. Turn on the breaker and the cooker/shower isolating switch.
14. Turn on the cooker/shower to low power and the current load
LED should light up. After approximately five seconds the run
LED should light up and the fan should run.
15. Adjust the load pot if necessary. Anti-clockwise to increase the
sensitivity and clockwise to decrease the sensitivity.
16. Now set the time pot by turning it clockwise. It has a range of
1 to 25 minutes for optimum performance and energy
conservation, a 20 minute overrun time is probably the best
starting point. N.B. the overrun time serves two functions:
the first to ensure the fan does not cycle with the cooker/
shower thermostat. Second to clear residual steam and
condensation following and after showering has finished.
17. Turn off the fused spur and fit the front cover plate to complete
the installation.
Temperature Sensing
18. Where used for temperature sensing to a normal shower, the
sensor must be fitted to the hot water dead leg. Find a position,
on the pipework which must be uninsulated copper. Remove
any paint or corrosion from the pipe, apply thermal grease to the
flat part of the sensor then firmly secure the sensor to the pipe
using the clip provided. It is most important that good thermal
conductivity is obtained. (see fig. 3 below).
19. From wherever the sensor is fitted, find a suitable route to run
the sensor control wiring to the main controller. At all times
ensure the wire does not get damaged by trapping of the cable.
20. Wire the cable into the terminals as indicated in the diagrams.
21. Test out all wiring, ensure that fan has a good earth by carrying
out a continuity test between the fused spur and the fan. Either
wire the fan for high speed operation or turn the fan on to high
speed and fix the setting.
22. Turn on the breaker and switch to the fused spur, the healthy
LED should flash/blink.
23. Turn down the load pot to the mid position and time pot to
minimum.
24. Turn on the shower wait 30 seconds after the hot water is being
delivered, if the load LED does not light up, then turn the load
pot very slightly in an anticlockwise direction, do not turn the pot
below the 50% position as this will allow the fan to run when
not required. If a lower setting is needed first check that the
temperature of the hot water is above 60oC as it should be to kill
off legionella, if it is at this temperature then the integrity of the
conduction of heat from the pipe to the sensor should be care
fully checked.
25. Now set the time pot by turning it clockwise. It has a range of
1 to 25 minutes for optimum performance and energy
conservation, a 20 minute overrun time is probably the best
starting point. N.B. the overrun time should be set to ensure
the fan clears all residual steam and condensation after
showering has finished.
26. Turn off the fused spur and fit the front cover plate to complete
the installation.
Installing a manual fan push switch (momentary)
e.g. MK - Reference: K4878P-WHI
27. Turn off the fused spur to the control unit and remove the front
cover.
28. Wire the cable into the terminals as indicated in the wiring
diagram figure 4 (i.e. OVERRIDE).
29. Run the cable to suitable location for the override switch and fix
securely.
30. Test the operation of the switch. Push and hold until the fan
starts running, this will give an override time of approximately
25 minutes. Push and hold the switch until the fan turns off, this
will disable the override during the 25 minute period.
31. Turn off the fused spur and fit the front cover to complete the
installation.
Special Notes regarding Temperature Sensing
a) There will be an inevitable delay between hot water being
delivered at point of use and the controller sensing the
temperature, this is due to the time taken by the conduction of
heat from the water through to the outside of the pipe and then
to the clamp on sensor. This time delay will vary with ambient
conditions, hot water temperature and pipe wall thickness. it is
most important therefore that great care is taken when fixing
the sensor to maximise the heat conduction process.
Please pay particular attention to cleaning the pipe, applying the
thermal grease and clamping the sensor.
b) Similarly there will be a delay in the unit turning off the fan as it
will take time for the dead leg to loose heat, again this will vary
with ambient conditions, hot water temperature and pipe wall
thickness.
The time of this natural cooling process should be taken account
of when setting the run on timer. As a guide, at an ambient
temperature of 21oC and a hot water temperature of 50oC. the
cooling down process will be 5 – 10 minutes and this should be
taken into account when setting the overrun timer.
c) The temperature sensor must be fitted to the copper pipe. With
plastic plumbing systems a section of copper tube must there-
fore be installed to receive the sensor.
L
Blue S1
Negative (-)
Red S1
Positive (+)
Mains Supply
Current Sensor
Shower
Cooker
Isolator
+ - + - + -
S1 S2 Override
Control Terminals
for twin unit
N
HOT
COLD
Cold water
pipe
Hot water
pipe
Water to
shower
head
Blue
Negative (-)
Red Positive (+)
Temperature
Sensor
Plastic
Clamp
Fig 3:Typical
temperature sensor
installation.
Safety:Take care not to touch the mains terminals
whilst the controller front cover is not in place when
adjusting the time and load pots.

4
Twin input controller wiring diagram and
further information
Multi input controller wiring diagram and
further information
Trouble shooting
Problem Action to determine
the fault
1.The healthy LED does Check that there is
not blink. 240 volts between
Live and Neutral
2.The load LED does
not illuminate. Momentarily short down live to
neutral on S1 or S2 for twin input
unit or S1 - S6 for multi unit. The
load LED should illuminate
N.B. Prolonged shorting down
of these terminals will damage
the PCB.
Electrical Wiring
Ventmiser can be used for a variety of applications, please contact us
for further information and advice.
West Energy Saving Technologies Ltd
76 Cow Lane, Bramcote
Nottingham NG9 3BB
Tel: 00 44(0)115 9222940
Fax: 00 44(0)115 9250222
www.westenergy.co.uk
Ventmiser and Cookermiser are patented devices.
Rel ay
Transform er
Load
Pot
Time Pot
1 −25mins
Fan r u n
LED
Load
LED
Healthy
LED
Fuse
+ −+ −+ −
S1 S2 Override
L
N
L
N
Live in
Neutral in
Live to relay
Neutral out
Ear t h
L
L
L
N.O. Live out to fan
Com m o n
N.C. Live out
Fig 4: Internal layout of Ventmiser twin input control.
Where a current sensor is being used with a temperature sensor
the current being sensed must exceed 2.5 amps. An additional
controller is required for sensing current values less than 2.5 amps,
alternatively the multi sensor unit should be used.
In applications where the controller is being used to switch
only, do not directly power the fan from the controller, whether
240, 24 or 12V, the link wire must be removed between Live
and the common terminals.
In these circumstances the common should be used as Live in
& N.O. Live out should be used to turn on the fan.
Additional sensor
An additional sensor may be installed into S2.
Additional push buttons
Additional push buttons may be installed. These must be wired in
parallel and connected into the O/R terminal.
Fig 5: Internal layout of Ventmiser multi input control.
In applications where the controller is being used to switch
only, do not directly power the fan from the controller, whether
240, 24 or 12V, the link wire must be removed between Live
and the common terminals.
In these circumstances the common should be used as Live in
& N.O. Live out should be used to turn on the fan or take a fan
to boost.
Where used for boosting MEV & MVHR the N.C. terminal is
generally used to provide low/trickle speed and the N.O. to provide
boost.
Sensors
Current sensors should be installed into S1, S2 & S3.
Temperature sensors should be installed into S4, S5 & S6.
Additional push buttons
Two push buttons may be installed. These must be wired in parallel
and connected into the O/R terminal. If further inputs are required
we suggest these are wired in parallel to a larger terminal block
outside the enclosure.
L
N
L
N
Live in
Neutral in
Live to relay
Neutral out
Earth
L
L
L
N.O. Live out to fan
Common
N.C. Live out
Relay
Transformer
Fan run
Load Temp
Load Current
Fuse
+ - + - + -
S1 S2
Current
+ - + - + -
S4 S5
Temperature
S3 S6
Healthy
Load
Current
Load
Tem p
Time
Current
Time
Tem p
N.B. Time Pot ranges
are 1 - 25 minutes
+ -
O/R
P/B
Other WEST Controllers manuals
Popular Controllers manuals by other brands

Mitsubishi Electric
Mitsubishi Electric MELSEC FX2N-232-BD user guide
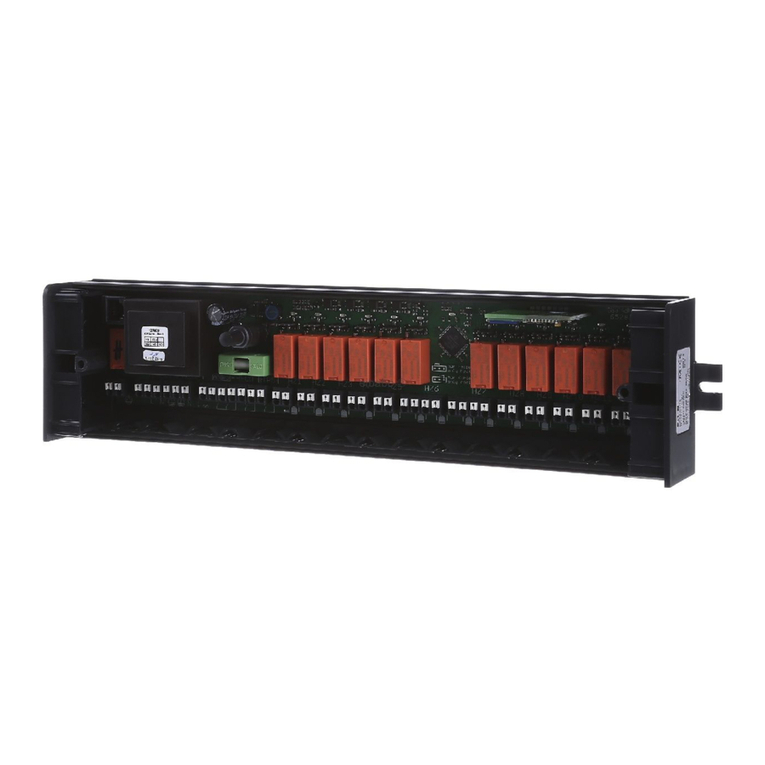
Eaton
Eaton xComfort CHAZ-01/12 Assembly instructions
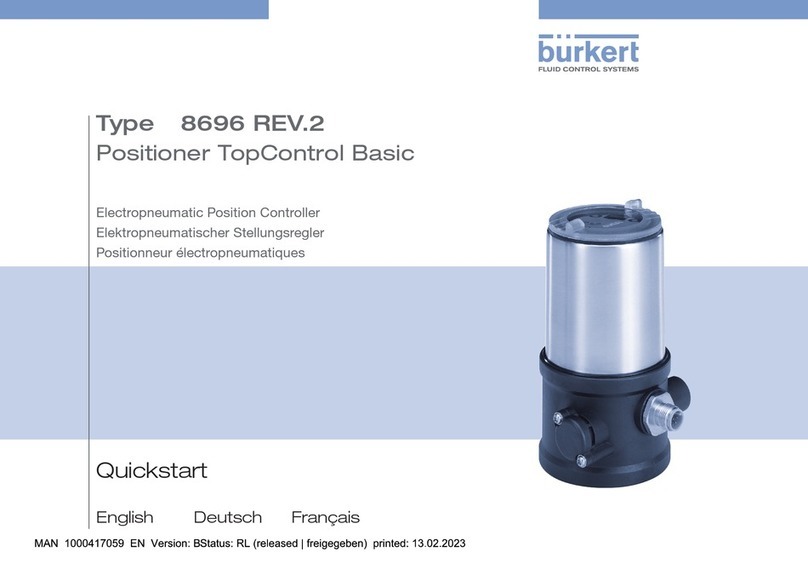
Burkert
Burkert 326445 quick start
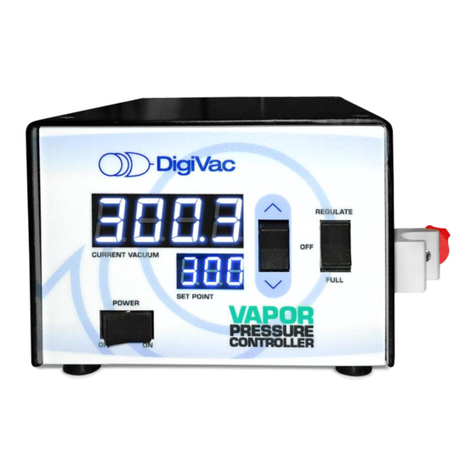
DigiVac
DigiVac VAPOR Operation manual
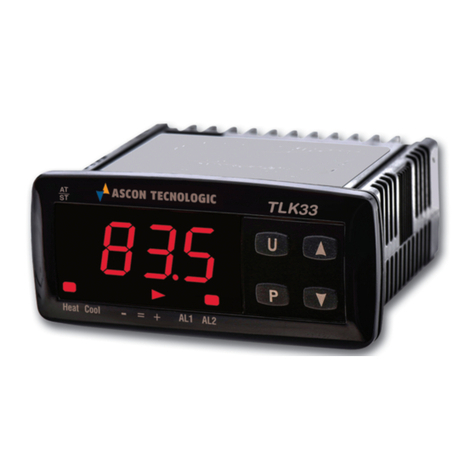
Ascon tecnologic
Ascon tecnologic TLK 33 operating instructions
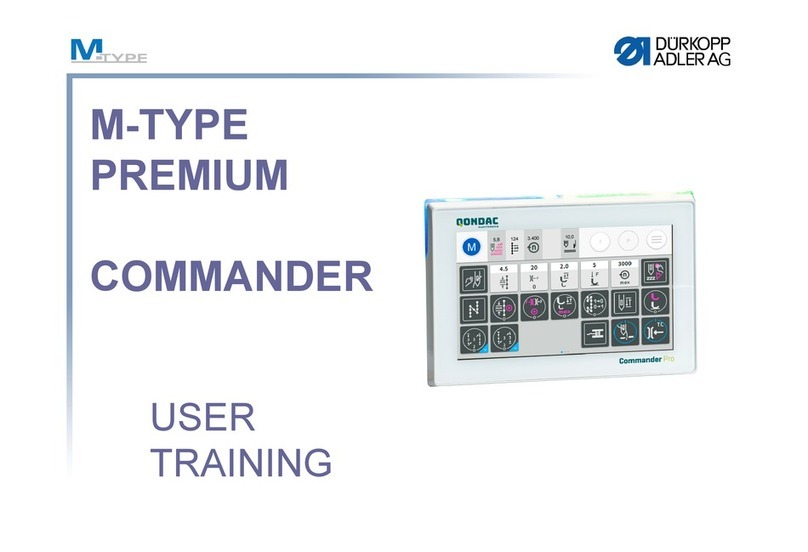
DURKOPP ADLER
DURKOPP ADLER M-TYPE PREMIUM COMMANDER User training guide