Witt LEAK-MASTER EASY User manual

Copyright WITT-GASETECHNIK GmbH & Co KG, 2017, all rights reserved
Instruction Manual for
WITT LEAK-MASTER®EASY
Caution!
Filling the LEAK-MASTER®EASY with water warmer than ambient temperatures may cause thermal
expansion of the plastic and the tank may crack. This is not covered under warranty.
Issue: 24.04.2017
This issue is not subject to change management

Page 2 of 16
WITT-GASETECHNIK GmbH & Co KG
Salinger Feld 4-8
: +49 (0)2302 89010
www.wittgas.com
Gas Safety- & Control Equipment
D-58454 Witten
Fax: +49 (0)2302 89013
witt@wittgas.com
1 Table of contents
1Table of contents......................................................................................................... 2
2Notes on these operating instructions...................................................................... 3
2.1 Introduction..........................................................................................................................................3
2.2 What does this manual contain?.........................................................................................................3
2.3 Rights to this manual...........................................................................................................................3
2.4 What symbols are used?.....................................................................................................................4
3Safety instructions and precautionary measures .................................................... 5
3.1 General safety guidelines....................................................................................................................5
3.2 Liability for proper function or damage................................................................................................5
4Commissioning and operation................................................................................... 6
4.1 The device at a glance ........................................................................................................................6
4.2 Preparations........................................................................................................................................7
4.3 Performing measurements..................................................................................................................8
4.3.1 Time duration for evacuation....................................................................................................9
5General test method.................................................................................................. 10
6Alternative Testing Methods .................................................................................... 10
6.1 Dry chamber testing ..........................................................................................................................10
6.2 Empty bag test method .....................................................................................................................10
6.3 Rigid tray, tub, or cup test method ....................................................................................................10
6.4 Altitude simulation test method .........................................................................................................11
6.5 LEAK-MASTER®EASY vacuum set test method for vacuum packed products...............................12
7Suggestions for setting test parameters................................................................. 13
8Maintenance .............................................................................................................. 14
8.1 Cleaning ............................................................................................................................................14
8.1.1 Prolongation of service life of the water filling........................................................................14
8.1.2 Let off the water......................................................................................................................15
8.2 Hinge adjustment...............................................................................................................................15
8.3 Setting support effect of the gas pressure spring..............................................................................15
8.4 Replacement of lid gasket.................................................................................................................16
8.4.1 Devices with transparent or blue gasket installation..............................................................16

Page 3 of 16
WITT-GASETECHNIK GmbH & Co KG
Salinger Feld 4-8
: +49 (0)2302 89010
www.wittgas.com
Gas Safety- & Control Equipment
D-58454 Witten
Fax: +49 (0)2302 89013
witt@wittgas.com
2 Notes on these operating instructions
2.1 Introduction
How do you guarantee to your customers that your packaging system is dependable once it leaves
your facility? That’s a complex question. Issues such as packaging material compatibility, sealing
machine set-up, and seal reliability in high altitude trucking and airfreight (see Section 6.4) are just
some of the production variables that need to be taken into account. The manufacturing considera-
tions are countless. Fortunately, the LEAK-MASTER®EASY Detector is a simple answer. A sys-
tematic package testing system that incorporates the LEAK-MASTER®EASY Leak Detector will al-
low you to quickly and reliably set-up packaging lines. The result: less downtime for machinery ad-
justments. Additionally, continual process monitoring with the LEAK-MASTER®EASY Leak Detec-
tor will detect sealing problems before they snowball, thus improving production yield. Above all,
the LEAK-MASTER®EASY Leak Detector will catch defects before they get to your customers.
2.2 What does this manual contain?
This document provides all instructions necessary for operation and maintenance of the device.
Observation of the instructions given herein helps to maintain safe operating conditions, minimise
downtime through incorrect equipment operation and to ensure the service life and reliability of the
device.
A legible copy of these operating instructions shall be maintained at operating locations. Employ-
ees designated to operate the device shall be familiar with operating this equipment or shall have
been properly instructed to operate such equipment.
If unexpected malfunctions occur that you cannot rectify even with the assistance of these operat-
ing instructions, please contact your local service agent, or call WITT-GASETECHNIK at the tele-
phone number given below to receive additional instruction on operation. Please state the serial
number of the device and give a short problem description.
Please make sure that you advise of your company’s name and telephone number.
Our address is:
WITT-GASETECHNIK GmbH & Co KG
Salinger Feld 4-8
D-58454 Witten
Germany
Tel.: +49 (0)2302 89010
Fax: +49 (0)2302 89013
Alternatively you can also contact us via e-mail (service@wittgas.com) or visit our homepage at
http://www.wittgas.com.
In the case of modification to the device these operating instructions cease to be applicable!
2.3 Rights to this manual
This manual is the copyright of WITT-GASETECHNIK GmbH & Co KG.
Without the prior written agreement of WITT-GASETECHNIK GmbH & Co KG these operating in-
structions are not permitted to be duplicated in whole or in part or be used in a manner contrary to
the company’s due interests.
It is only permitted to pass these operating instructions on to third parties in conjunction with the
device.

Page 4 of 16
WITT-GASETECHNIK GmbH & Co KG
Salinger Feld 4-8
: +49 (0)2302 89010
www.wittgas.com
Gas Safety- & Control Equipment
D-58454 Witten
Fax: +49 (0)2302 89013
witt@wittgas.com
2.4 What symbols are used?
The warning symbol indicated hazards for personnel or the equipment.
It is imperative that these instructions are observed and followed.
The word “Warning” is placed in front of information indicating risk of personal injury or po-
tentially fatal hazards.
The word “Caution” is placed in front of information indication potential equipment damage.
Note!
The pointing had marks general notes that explain operating procedures.
The “dot” marks actions to be performed.
The “square” is used to identify a list.
This symbol indicates that you should turn the page.

Page 5 of 16
WITT-GASETECHNIK GmbH & Co KG
Salinger Feld 4-8
: +49 (0)2302 89010
www.wittgas.com
Gas Safety- & Control Equipment
D-58454 Witten
Fax: +49 (0)2302 89013
witt@wittgas.com
3 Safety instructions and precautionary measures
It is imperative to follow and observe the following safety instructions and precautionary measures.
They are intended to prevent hazards which might occur if the device is not operated properly. In
addition, all applicable national health and safety regulations and standards must be observed. For
example, on usage in Germany the “Unfallverhütungsvorschriften (UVV)” and the safety regulations
issued by the “Berufsgenossenschaften” shall be observed, e.g.:
Unfallverhütungsvorschriften der gewerblichen Berufsgenossenschaften (safety regulations
issued by the german tradel associations)
DGUV Vorschrift 1 Grundsätze der Prävention (principles of prevention)
BGR 500 Sec. 2.33 Gase (Gases)
No claim is made to the completeness of this list!
When handling the equipment the following shall be observed:
The operating instructions.
All health and safety regulations and standards applicable in the country and the place of use.
All engineering rules and guidelines for safety and good workmanship.
The owner or user of the equipment should ensure that the device is operated by authorised per-
sonnel only. All employees designated to handle the device shall be properly instructed and ad-
vised of the applicable safety and health precautions. The device has been designed and built ac-
cording to the state of the art. It shall only be used for its intended purpose. Any operation not con-
forming to the intended use or operation by inadequately trained personnel may result in hazardous
operating conditions.
3.1 General safety guidelines
Warning !
The equipment is only permitted to be operated by personnel who has properly instructed
to operate such equipment and who has read and understood these operating instructions.
Please ensure that all applicable national health and safety regulations and standards for the
safe handling of gases are observed (e.g. UVV’s (Unfallverhütungsvorschriften) = German
health and safety regulations).
For safety reasons all unauthorised modifications, or addition or removal of parts onto the
product are not permitted.
Any malfunction occurring during the operating of the device shall be corrected adequately
trained and qualified personnel only.
All maintenance and repair of the equipment shall be performed by adequately trained and
qualified personnel only.
During all maintenance and repair it must be ensured that the equipment is un-pressurised.
All gas supply lines to the device must be suitable for the maximum allowable inlet pressures.
If that proves to be impracticable, suitable pressure regulators or safety relief devices should
be installed in the gas supply lines to make sure that the maximum allowable gas inlet pres-
sures cannot be exceeded.
The material of piping, tubing, fittings, gaskets, and gasket and thread sealants, as well as the ma-
terial of all valves, gauges, regulators, and other accessories installed in the gas lines to the device
shall be suitable for service of the particular gas at the pressures and temperatures involved.
The maximum allowable inlet pressure (see type plate) must not be exceeded. If necessary,
safety relief devices should be installed in the gas supply line.
Check the compressed air supply respective the connection cable at regular intervals for nicks
/ damages.
3.2 Liability for proper function or damage
The liability for the proper function of the instrument is irrevocably transferred to the owner or operating
organisation to the extent the instrument has been serviced or repaired by personnel not employed or
authorised by WITT-Service or when the instrument was used in a manner not conforming to its intend-
ed use, or if the operation did not follow the applicable national health and safety regulations.
WITT-Gasetechnik GmbH & Co KG cannot be held responsible for damages arising from failure to
observe these operating instructions.

Page 6 of 16
WITT-GASETECHNIK GmbH & Co KG
Salinger Feld 4-8
: +49 (0)2302 89010
www.wittgas.com
Gas Safety- & Control Equipment
D-58454 Witten
Fax: +49 (0)2302 89013
witt@wittgas.com
1
2
3
4
5
6
7
9
10
11
8
12
13
4 Commissioning and operation
Caution!
Filling the LEAK-MASTER®EASY with water warmer than ambient temperatures may cause
thermal expansion of the plastic and the tank may crack. This is not covered under warran-
ty.
Caution!
Take care that the time the chamber is under vacuum don´t exceeds 2 minutes.
4.1 The device at a glance
1 Vacuum gauge (Pvac) of the chamber
2 Handle of the lid
3 Handle for unlocking the lock of the lid
4 Operating pressure gauge (P1) of the compressed air
5 Pressure regulator for setting the operation pressure (P1) of the compressed air
Caution: max. allowed P1is 6 bar
6 Ball valve for opening / closing the compressed air
7 Compressed air connection
8 Let off with ball valve for the water
9 Vacuum suction nozzle
10 Base frame
11 Measurement chamber
12 Vacuum hose
13 Vacuum limiter- Vacuum is limited to -0.8 bar / 200 mbar abs.

Page 7 of 16
WITT-GASETECHNIK GmbH & Co KG
Salinger Feld 4-8
: +49 (0)2302 89010
www.wittgas.com
Gas Safety- & Control Equipment
D-58454 Witten
Fax: +49 (0)2302 89013
witt@wittgas.com
4.2 Preparations
Warning !
The LEAK-MASTER®EASY is extremely heavy when filled with water. Be sure the table or
cart is stable and rated for the appropriate weight.
Caution !
After filled with water check the tightness of the water let off at the bottom the LEAK-
MASTER®EASY.
Caution !
Do not over tighten any fittings or you may damage the tank. Hand tightening is usually suf-
ficient. Some fittings may require gentle use of a wrench.
The LEAK-MASTER®EASY is very easy to assemble and operate. If you received your LEAK-
MASTER®EASY already attached to the base,
Connect the compressed air supply (min. 6 barg, max. 8 barg, capacity of the compressed air
supply: min. 300 l/min) to the compressed air connection located at the back side of the base
frame.
If necessary the following installation work might be necessary:
Install vacuum gauge (1) with suitable sealing material to left rear port on the lid.
Install the handle of the lid (2) to the intended place at the front side of the lid.
Install the water let off (8) with suitable sealing material.
Handle of the ball valve should be oriented for ease of operation. A hose is supplied for drain-
ing.
Install the vacuum hose (12) to the right rear connection on the lid.

Page 8 of 16
WITT-GASETECHNIK GmbH & Co KG
Salinger Feld 4-8
: +49 (0)2302 89010
www.wittgas.com
Gas Safety- & Control Equipment
D-58454 Witten
Fax: +49 (0)2302 89013
witt@wittgas.com
-+
5
6
closed
open
4.3 Performing measurements
Caution!
Take care that the time the chamber is under vacuum don´t exceeds 2 minutes.
For all testing methods it is necessary to generate vacuum in the test chamber.
The general necessary operating steps are declared below:
Close ball valve (6).
Release / lower the set operating pressure at the op-
erating pressure regulator (5):
Unlock the pressure regulator by pulling the set-
ting knob.
Turn the setting knob anti clockwise as far as it
will go.
Then push the setting knob back to lock the setting.
Open the compressed air supply.
(min. 6 barg, max. 8 barg, capacity of the compressed air supply: min. 300 l/min).
Place product to be tested in the chamber and close the lid.
Open ball valve (6).
Unlock the operating pressure regulator (5) by pulling the setting knob. Then slowly turn the
setting knob clockwise to increase the operating pressure (P1, max. P1= 6 bar).
You can read the operating pressure (P1)
at pressure gauge (4) and the vacuum
(Pvac) in the test chamber at pressure
gauge (1). In the diagram right you can
read which vacuum a set operating pres-
sure will generate.
To ensure the stability of the test chamber
a vacuum limiter (13) is implemented to
the device. It limits the max. reachable
vacuum to -0.8 bar (0.2 bar abs.).
If the desired vacuum is reached (also
see Section 7) push the setting knob to
lock the operating pressure regulator.
Monitor the product to be tested accord-
ing to the description of the respective
test method.
Close ball valve (6).
The compressed air supply is interrupted
now and the test chamber will be vented
via the vacuum suction nozzle.
Open the lid and remove the product.
For further tests with the same vacuum only
the following steps are necessary:
Place product to be tested in the chamber and close the lid.
Open ball valve (6). Wait until the set vacuum is reached. Then perform the visual testing.
Close ball valve (6).
Open the lid and remove the product.
Vacuum (P
vac
) in dependence to the set operating pressure (P
1
)
P
vac
/ bar
P
1
/ bar
max.
100
0
200
300
400
500
600
700
0 1 2 3 4 5 6 7 8 9
Compressed air consumption (Q
n
) in dependence
to the set operating pre
ssure (P1)
Q
n
[l/min]
P1/ bar

Page 9 of 16
WITT-GASETECHNIK GmbH & Co KG
Salinger Feld 4-8
: +49 (0)2302 89010
www.wittgas.com
Gas Safety- & Control Equipment
D-58454 Witten
Fax: +49 (0)2302 89013
witt@wittgas.com
4.3.1 Time duration for evacuation
Vacuum in bar
-0.05 -0.1 -0.2 -0.3 -0.4 -0.5 -0.6 -0.7 -0.8
Time duration in s/l (per liter „remaining camber volume“)
0.03 0.04 0.07 0.09 0.14 0.2 0.28 0.42 0.99
Water filling: 0 %
Remaining
camber volume Time duration for evacuation in s
EASY 1 9.8 l 0.3 0.4 0.7 0.9 1.4 2.0 2.7 4.1 9.7
EASY 2 32.1 l 1.0 1.3 2.3 2.9 4.5 6.4 9.0 13.5 31.8
EASY 3 52.0 l 1.6 2.1 3.6 4.7 7.3 10.4 14.6 21.8 51.5
EASY 4 100 l 3.0 4.0 7.0 9.0 14.0 20.0 28.0 42.0 99.0
EASY 5 129 l 3.9 5.2 9.0 11.6 18.1 25.8 36.2 54.3 127.9
Water filling: 85 %
Remaining
camber volume Time duration for evacuation in s
EASY 1 1.5 l 0.04 0.06 0.10 0.13 0.2 0.3 0.4 0.6 1.5
EASY 2 4.8 l 0.1 0,2 0.3 0.4 0.7 1.0 1.4 2.0 4.8
EASY 3 7.8 l 0.2 0,3 0.6 0.7 1.1 1.6 2.2 3.3 7.7
EASY 4 15.0 l 0.5 0,6 1.1 1.4 2.1 3.0 4.2 6.3 14.9
EASY 5 19.4 l 0.6 0,8 1.4 1.7 2.7 3.9 5.4 8.1 19.2

Page 10 of 16
WITT-GASETECHNIK GmbH & Co KG
Salinger Feld 4-8
: +49 (0)2302 89010
www.wittgas.com
Gas Safety- & Control Equipment
D-58454 Witten
Fax: +49 (0)2302 89013
witt@wittgas.com
5 General test method
The most common way to use the LEAK-MASTER®EASY is the bubble emission test.
Note !
When testing a new package, always start with the lowest vacuum setting. Slowly raise vac-
uum level to prevent sudden bursting, see Section 7.
Fill unit with enough water to submerge package when expanded.
Water level will rise as package is expanded under vacuum.
Place product to be tested in the chamber and close the lid.
Generate vacuum as described in Section 4.3.
Monitor the product during the vacuum increases.
Bubbles will rise from a leak.
Close ball valve (6), open the lid and remove the product.
6 Alternative Testing Methods
6.1 Dry chamber testing
The unit can be used dry for simple burst strength and altitude testing. Also, a package containing
liquid with some headspace can be checked using the following method:
Place the product on a paper towel in the dry chamber.
Close lid and start the vacuum.
Increase vacuum to fully expand package and put pressure on the seals.
When finished, examine for leakage on the package or paper towel.
6.2 Empty bag test method
Empty bags should be sealed with some air in them to test properly. It is recommended that a block
of foam be placed in the bag to give a consistent volume for testing. This insures that all operators
will achieve the same results.
6.3 Rigid tray, tub, or cup test method
Rigid packaging sealed with lid film can be tested with the lid film down if there is no product. It is
recommended that the test is performed with the lid film up if there is product. This allows the gas
in the headspace to escape if there are any leaks. Gases are much more easily seen than liquid
product.
Some products can be tested with lid film down using the dry chamber method, looking for product
see section 6.1.

Page 11 of 16
WITT-GASETECHNIK GmbH & Co KG
Salinger Feld 4-8
: +49 (0)2302 89010
www.wittgas.com
Gas Safety- & Control Equipment
D-58454 Witten
Fax: +49 (0)2302 89013
witt@wittgas.com
6.4 Altitude simulation test method
Many shipping methods subject packaging to stress from changes in altitude. High altitude truck
routes can cause package expansion and failures. Air cargo holds are typically pressurized to only
2,743 meters (9,000 feet). The LEAK-MASTER®EASY can reveal potential weaknesses in the
package before shipping.
Altitude simulation can be done wet or dry. Vacuum levels can converted to altitude with chart. Alti-
tude reading will be a differential from current altitude.
For absolute altitude, add the local altitude of the testing facility.
0

Page 12 of 16
WITT-GASETECHNIK GmbH & Co KG
Salinger Feld 4-8
: +49 (0)2302 89010
www.wittgas.com
Gas Safety- & Control Equipment
D-58454 Witten
Fax: +49 (0)2302 89013
witt@wittgas.com
6.5 LEAK-MASTER®EASY vacuum set test method for vacuum packed products
The LEAK-MASTER®EASY vacuum set is used for vacuum packed product or product with very
little head-space. Set up the test as follows:
Setup LEAK-MASTER®EASY vacuum set according to the
figure right. Don´t over tighten the vacuum set - hand-
screwed is usually sufficient.
Note !
The ball valve of LEAK-MASTER®EASY vacuum set must be
open.
Apply septa to clean dry portion of package.
If necessary, clean the surface of the package.
Insert needle through septa into package. Avoid clogging
needle with product.
Close lid and start the vacuum at a very low level. Package
expansion is slower with the LEAK-MASTER®EASY vacuum
set in use.

Page 13 of 16
WITT-GASETECHNIK GmbH & Co KG
Salinger Feld 4-8
: +49 (0)2302 89010
www.wittgas.com
Gas Safety- & Control Equipment
D-58454 Witten
Fax: +49 (0)2302 89013
witt@wittgas.com
7 Suggestions for setting test parameters
Testing parameters must be set for each size and type of package. Frequency of testing, vacuum
level, water level (if any), and length of test are all variables that must be researched. Parameters
can change due to variances in package headspace. In some cases, operators should have an un-
derstanding of the "look" of the expanded package more than trying to maintain a certain vacuum
level. With some research and training, the LEAK-MASTER®EASY will become an integral part of
your quality control program. General test parameters can be set up as follows:
Slowly apply vacuum pressure to package in a dry chamber (to prevent excessive clean up).
Raise vacuum level until the package fails, note vacuum level.
Repeat until a consistent failure point is found.
Vacuum level should be set at approximately 70% of the failure point for future testing on the
production line as long as this level meets shipping tests.
Note !
The consistency of any test is dependant on the consistency of the package being tested.
Note !
It may be found that the package cannot meet minimum requirements for integrity.
The LEAK-MASTER®EASY is useful for testing new materials, machinery, and products be-
fore they are released to production.

Page 14 of 16
WITT-GASETECHNIK GmbH & Co KG
Salinger Feld 4-8
: +49 (0)2302 89010
www.wittgas.com
Gas Safety- & Control Equipment
D-58454 Witten
Fax: +49 (0)2302 89013
witt@wittgas.com
8 Maintenance
The LEAK-MASTER®EASY requires little maintenance. The following guidelines will ensure years
of service from your LEAK-MASTER®EASY.
8.1 Cleaning
The LEAK-MASTER®EASY tank should be cleaned on a regular basis with mild soap and water to
remove mineral deposits before they degrade the clarity of the plastic.
Using water with lower mineral content will delay mineral build-up.
Important note to the lifetime of the test chamber:
On service and maintenance according to the specifications given in this Section, the life-
time of the test chamber is about 100,000 load cycles.
Caution!
Never use alcohol, alcohol-containing cleaning agents, solvents, strong acids or alkali.
These can damage the acryl glass so that the stability is reduced and the test chamber can
possibly implode.
If a stronger cleaning agent is needed due to strong pollution, the cleaning agent must ex-
plicit suitable for acryl glass.
Caution!
Never use a high pressure cleaner for cleaning.
On working with a high pressure cleaner near the device, take care that the water jet don’t
hit the device.
8.1.1 Prolongation of service life of the water filling
To reduce the change interval of the water in the test chamber, we recommend to use WITT Floc-
culant 50 tablets. WITT Flocculant 50 tablets remove organic impurities and all kinds of microor-
ganisms as e.g. algae, bacteria, viruses and fungi, so that the water remains longer in proper con-
dition.
Note !
WITT Flocculant 50 tablets don´t remove strong pollutions like they occur on defects of
tested food packagings.
Warning !
Observe the instructions for use delivered with the WITT Flocculant 50 tablets as well as the
safety data sheets.
As stated in the table below put the number of WITT Flocculant 50 tablets per application into
the water of the test chamber. Afterwards close the lid.
device
For prevention
every 2 – 4 days
maximum
every 24 hours
EASY 1
1 Tab
1 Tab
EASY 2
1 Tab
2 Tabs
EASY 3
1 Tab
2 Tabs
EASY 4
1 – 2 Tabs
2 Tabs
EASY 5
2 Tabs
2 Tabs
By performing measurements active ingredient will be removed from the water. Thus, we
recommend the application of the WITT Flocculant 50 tablets before longer measurement
breaks (e.g. at finishing time).

Page 15 of 16
WITT-GASETECHNIK GmbH & Co KG
Salinger Feld 4-8
: +49 (0)2302 89010
www.wittgas.com
Gas Safety- & Control Equipment
D-58454 Witten
Fax: +49 (0)2302 89013
witt@wittgas.com
8.1.2 Let off the water
At the bottom side of the LEAK-MASTER®EASY a let off with ball valve for the water is located.
Before letting the water off a hose must be connected to the connector to enable a directed let off
to a suitable basin or gully.
For let off the water the device must be pressureless.
8.2 Hinge adjustment
Periodically the hinges may need to be adjusted as follows:
Close lid and set vacuum level at approx. -0.3 bar.
Loosen all hinge screws.
Retighten while lid is under vacuum.
Release vacuum and return to normal use.
8.3 Setting support effect of the gas pressure spring
To lower the effort to open the lid the models EASY 4 and EASY 5 are equipped with gas pressure
springs.
The support effect should be set in that way that the test chamber is tight for vacuum generation on
closed lid without additional pushing by the operator.
If this is not the case the support effect can be altered as follows:
On closed lid loosen the four screws (S) of the mounting plate a
little bit.
Move the mounting plate.
- Moving the position of the mounting plate upwards decreases
the support effect.
- Moving the position of the mounting plate downwards in-
creases the support effect.
Carefully tighten the screws (max. 10 Nm).
The position of the mounting plates should be similar on both
sides.
S
S
S
S
decrease support
increase support

Page 16 of 16
WITT-GASETECHNIK GmbH & Co KG
Salinger Feld 4-8
: +49 (0)2302 89010
www.wittgas.com
Gas Safety- & Control Equipment
D-58454 Witten
Fax: +49 (0)2302 89013
witt@wittgas.com
8.4 Replacement of lid gasket
8.4.1 Devices with transparent or blue gasket installation
Remove the old gasket completely.
The lip of the gasket faces out!
Start at the back center and press the ends together into the groove.
Next, press each corner into the groove. Do not stretch the gasket.
Press the remaining portions of the gasket into the groove.
Close the lid. Loosen and retighten hinge screws to set lid height.
Table of contents
Popular Security Sensor manuals by other brands
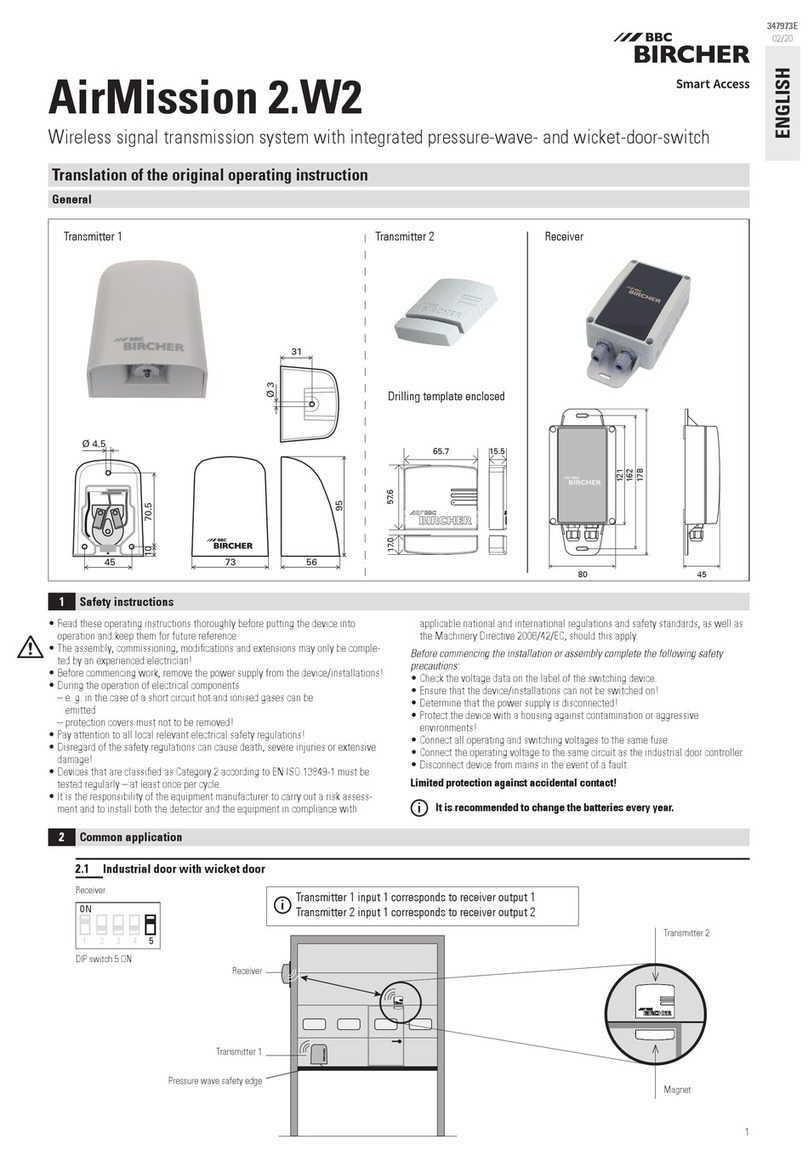
BBC Bircher
BBC Bircher AirMission 2.W2 Translation of the original operating instruction
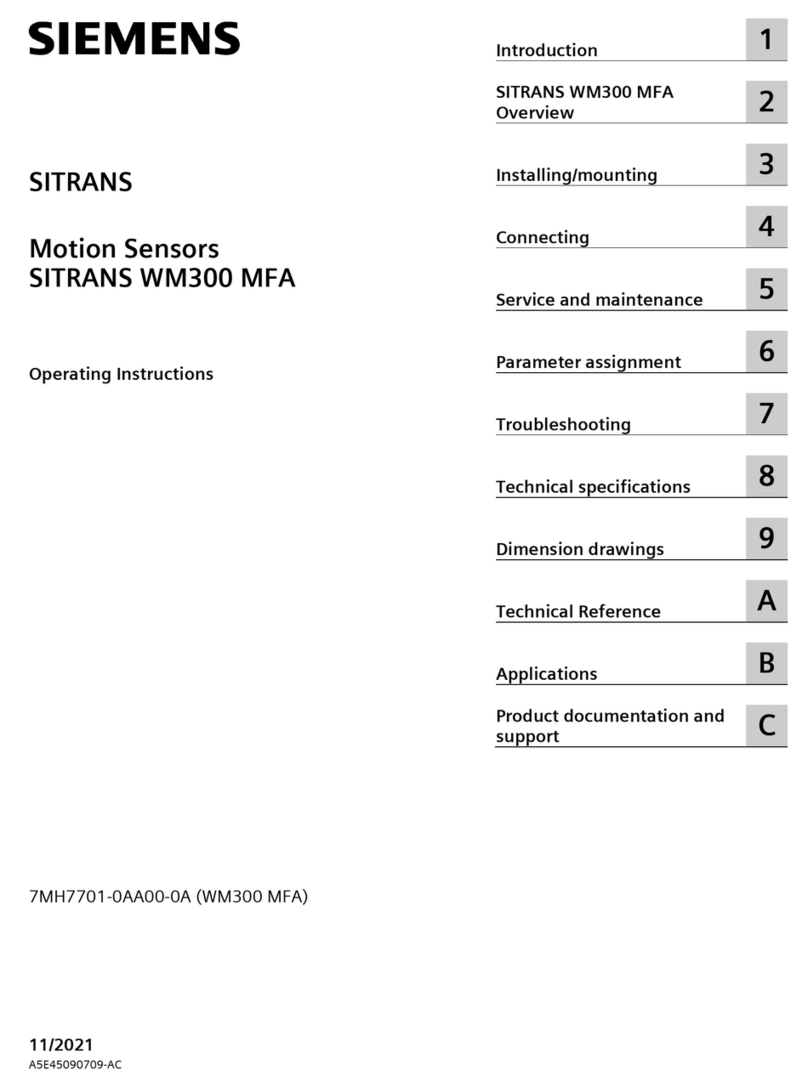
Siemens
Siemens 7MH7701-0AA00-0A operating instructions
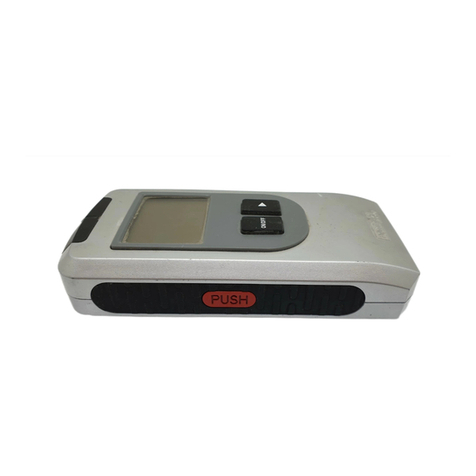
Powerfix Profi
Powerfix Profi 271367 Operation and safety notes
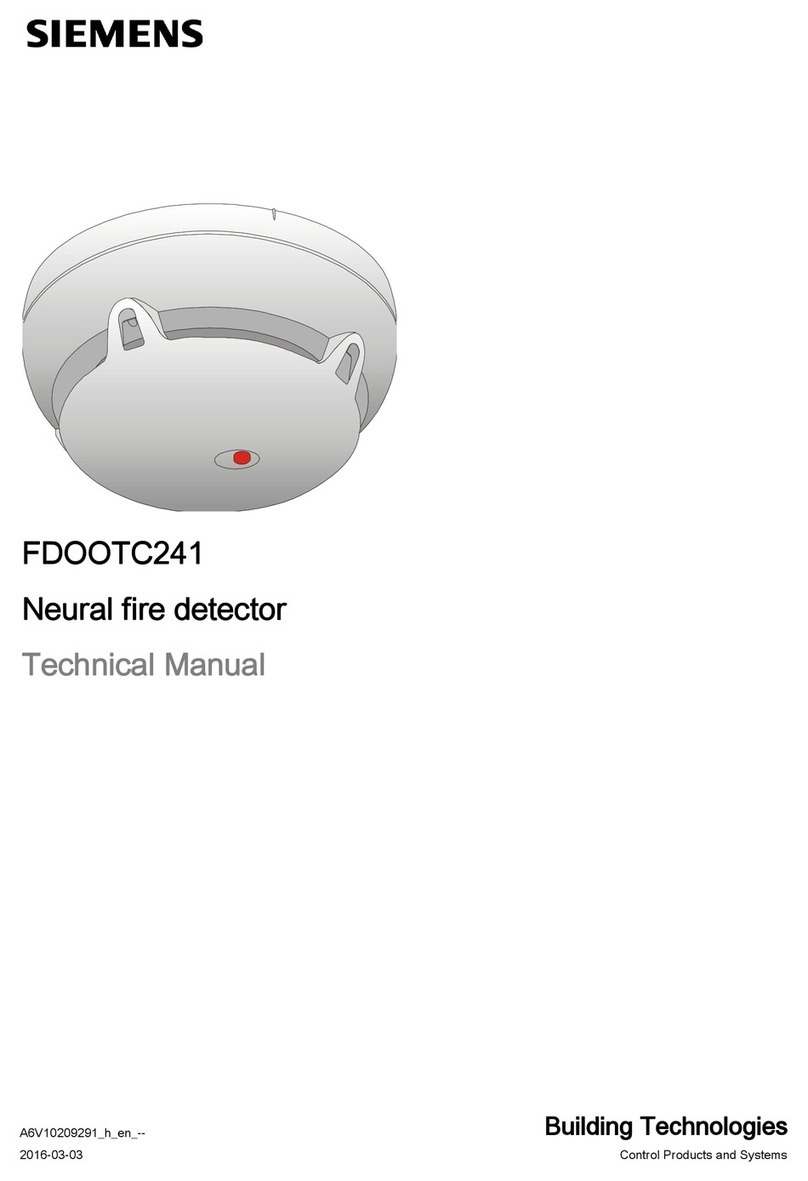
Siemens
Siemens FDOOTC241 Technical manual

Glasdon
Glasdon GLENWOOD 170 POST Installation and maintenance instructions
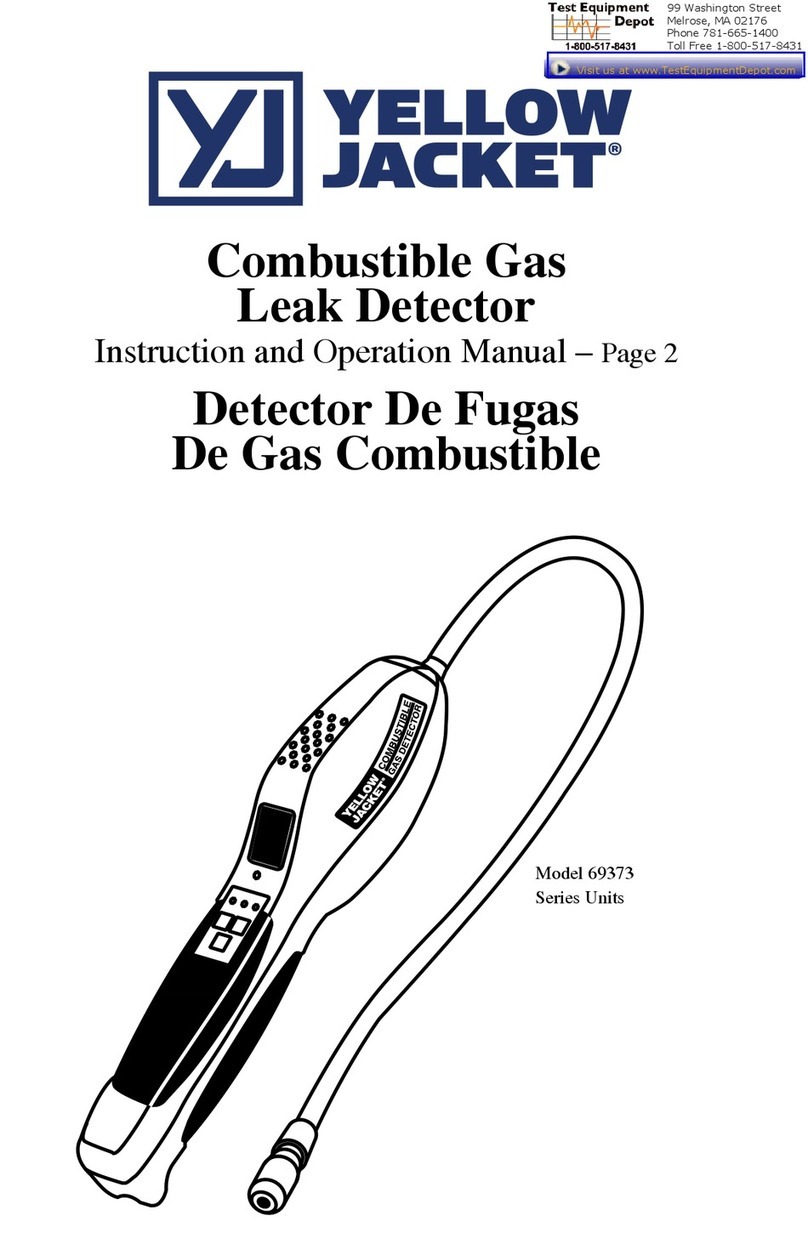
yellow jacket
yellow jacket 69373 Series Installation and operation manual