WoodMaxx WM-8M User manual


www.WoodMaxx.com
1
All content in this manual; pictures, and text are the sole property of
WoodMaxx™Power Equipment Ltd. © 2013-19. No unauthorized reproduction.
TABLE OF CONTENTSTABLE OF CONTENTS
Introduction ........................................ 2
Safety Information ................................... 2
Driveline Safety ..................................... 7
Assembly Instructions ............................... 10
PTO Shaft Sizing Instructions .......................... 20
General Operation .................................. 24
Lubrication ....................................... 26
Knife Changing / Adjusting............................ 27
Flywheel Knife Sharpening............................ 30
Flywheel Knife Care ................................. 31
Clearing Flywheel Housing............................ 32
Infeed Drive Axle Power Belt .......................... 33
Changing / Adjusting Drive Belt ........................ 34
Maintain Infeed Drive Axle ............................ 35
Maintenance / Storage............................... 36
Torque Specications................................ 37
Safety Labels...................................... 38
Troubleshooting .................................... 40
Parts & Diagrams................................... 41
Warranty ......................................... 56

www.WoodMaxx.com
2
INTRODUCTIONINTRODUCTION
SAFETY INFORMATIONSAFETY INFORMATION
Safe Operation Tips
Thoroughly read and understand the instructions given in this manual before operation. Refer to
the safety decals in the back of this manual. Read all instructions noted on them.
Do not allow anyone to operate this equipment who has not fully read and comprehended this
manual and who has not been properly trained in the safe operation of the equipment.
• Operator should be familiar with all functions of the unit.
• Make sure all guards and shields are in place and secured before operating the equipment.
• Dismounting from a moving tractor could cause serious injury or death.
• Do not stand between the tractor and the implement during hitching.
CONGRATULATIONS! You have just purchased a WoodMaxx
™
WM-Series Wood
Chipper, the strongest, safest and the most compact PTO Wood Chipper available.
We have compiled this owner’s manual to help you understand and appreciate your
chipper. By taking a few minutes to read this manual and understand the maintenance
instructions, it will give you better performance and extend the life of your chipper.
You must read this manual before operating the chipper.
Using This Manual
This Operator’s Manual is designed to help familiarize you with safety, assembly,
operation, adjustments, troubleshooting, and maintenance. Read this manual and follow
the recommendations to help ensure safe and efcient operation.
The information contained within this manual was current at the time of printing.
Some parts may change slightly to assure you of the best performance.To check for
updates refer to our website at www.WoodMaxx.com or call 1-855-966-3629
to speak to one of our representatives.
Owner Assistance
If customer service or repair parts are required please contact WoodMaxx at
1-855-966-3629. WoodMaxx has trained personnel, repair parts and equipment
needed to service this machine. The parts on your machine have been specially
designed and should only be replaced with genuine WoodMaxx parts. Please
reference your order number or serial number when calling.

www.WoodMaxx.com
3
SAFETY INFORMATIONSAFETY INFORMATION
• Watch out for wires, trees, etc., when raising and moving implement. Make sure all persons
are clear of working area.
• Turning tractor too tight may cause implement to ride up on wheels. This could result in injury
or equipment damage.
• Visually inspect the infeed bin and the ywheel before applying power to ensure that the
chipper head is clear, all the bolts are clear, and the ywheel knives clear the ywheel housing
and the bed knife.
• Bystanders must be at a safe distance from chipper during operation.
• Children should NEVER operate, or be near the chipper during operation.
• Make sure the PTO shaft does not come apart or bottom out during the normal lifting range.
Damage resulting from an improperly sized PTO shaft is not covered under warranty.
• Check the chip pile to see if the knives need to be serviced. Long slivers in the chip pile are
one of the best indicators of dull knives.
• It is NOT recommended to operate the chipper in temperatures below freezing. Hardened
steel (as used on knives) can become brittle in temperatures below freezing and may result in
breakage.
•
Always keep the guards and chip deector installed properly while operating the chipper.
• Never leave the chipper running unattended.
• Do not attempt alterations, repairs, or adjustments while the ywheel is turning. Always
disconnect the PTO, stop the tractor’s motor, and put the keys in your pocket prior to
attempting any alterations, repairs or adjustments.
• Keep hands, feet, clothing and other extremities out of and away from the hopper (infeed
bin) and any power driven parts. Wear snug tting clothing to avoid entanglement with
moving parts.
• No loose clothing should be worn around the chipper. Personal injury can occur if someone
or something turns the ywheel over when the knives are being checked or the cutter bar is
being adjusted. The ywheel has enough residual energy to easily remove ngers.
• Point the discharge chute away from doorways, sidewalks, or any other area where your view
is obstructed. The chute should be pointed downwind when possible. This will keep the chips
from blowing back in the operator’s direction.
A Note to All Users
List of warnings and cautions cannot be all-inclusive. If situations occur that are
not covered by this manual, the operator must apply common sense and operate
this Wood Chipper in a safe manner. If you have any questions, please contact
WoodMaxx at (855) 966-3629.

www.WoodMaxx.com
4
SAFETY INFORMATIONSAFETY INFORMATION
DANGER
This symbol indicates an imminently hazardous situation which, if not avoided,
will result in death or serious injury. This signal word is limited to the most
extreme situations, typically for machine components that, for functional
purpose, cannot be guarded.
WARNING
This symbol indicates a potentially hazardous situation which, if not avoided,
could result in death or serious injury, and includes hazards that are exposed
when guards are removed. It may also be used to alert against unsafe practices.
CAUTION
This symbol indicates a potentially hazardous situation which, if not avoided,
may result in minor or moderate injury. It may also be used to alert against
unsafe practices.
Safety Alert Symbols
The SAFETY ALERT SYMBOL indicates there is a potential hazard to personal safety
involved and extra safety precaution must be taken. When you see this symbol,
be alert and carefully read the message that follows it. In addition to design and
conguration of equipment, hazard control and accident prevention are dependent
upon the awareness, concern, prudence and proper training of personnel involved in
the operation, transport, maintenance and storage of equipment.

www.WoodMaxx.com
5
Use Safety Lights and Devices
•
Slow moving tractors, self-propelled equipment, and towed implements can create a
hazard when driven on public roads. They are difcult to see, especially at night.
• Flashing warning lights and turn signals are recommended whenever driving
on public roads. Use lights and devices provided with implement.
Transport Machinery Safely
• Comply with state and local laws.
• Maximum transport speed for any WoodMaxx implement is 20 mph on paved
surface and 10 mph maximum on unpaved surface. Do not exceed. Never travel at
a speed which does not allow adequate control of steering and stopping. Rough
terrain requires a slower speed. Traveling at excessive speed on rough terrain that
causes violent shaking or bouncing of the implement will damage the attachment
point on the implement and/or the tractor. This type of damage is not covered
under warranty.
• Use the following maximum speed - for paved surfaces only:
• 20 mph when weight is less than or equal to the weight of tractor.
• 10 mph when weight is more than the weight of the tractor.
Keep Riders Off Machinery
• Riders obstruct the operator’s view, they could be struck by foreign objects or
thrown from the machine.
• Never allow children to operate equipment.
Practice Safe Maintenance
• Understand procedure before doing work. Use proper tools and equipment.
Refer to Operator’s Manual for additional information.
• Work in a clean dry area.
• Lower the implement to the ground, put tractor in park, turn off engine, and remove
key before performing maintenance.
• Allow implement to cool completely.
• Do not grease or oil implement while it is in operation.
SAFETY INFORMATIONSAFETY INFORMATION

www.WoodMaxx.com
6
Prepare For Emergencies
• Be prepared if a re starts.
• Keep a rst aid kit and re extinguisher handy.
• Keep emergency numbers for doctor, ambulance, hospital and re
department near phone.
Avoid High Pressure Fluids Hazard
• Escaping uid under pressure can penetrate the skin causing serious injury.
• Avoid the hazard by relieving pressure before disconnecting hydraulic lines.
• Use a piece of paper or cardboard, not body parts, to check for suspected
leaks. Wear protective gloves and safety glasses or goggles when working
with hydraulic systems.
• If an accident occurs, see a doctor immediately. Any uid injected into the skin must
be treated within a few hours or gangrene may result.
Wear Protective Equipment
• Protective clothing and equipment should be worn.
• Wear clothing and equipment appropriate for the job. Avoid loose
tting clothing.
• Prolonged exposure to loud noise can cause hearing impairment or hearing loss.
Wear suitable hearing protection such as
earmuffs or earplugs.
• Operating equipment safely requires
the full attention of the operator.
Avoid wearing radio headphones while
operating machinery.
SAFETY INFORMATIONSAFETY INFORMATION
Protective Gear Required:
• Wrap around safety glasses
• Ear plugs
• Leather gloves
• Steel-toe work boots
• Heavy pants
• Long sleeved shirt

www.WoodMaxx.com
7
DRIVELINE SAFETYDRIVELINE SAFETY
DRIVELINE SAFETY CHECKLISTDRIVELINE SAFETY CHECKLIST
Agriculture and forestry are recognized as one of the most hazardous of occupations.
Today’s farmer spends long hours in close proximity to increasingly complex and
powerful machinery.
To avoid accidents, everyone from the component supplier and the company who
manufacturers and assembles the machinery, to the dealers and ultimately the
actual user, must keep safety in mind. The checklist below relates to the drive line of
agricultural implements, general safety literature, and the standards published by the
American Society of Agricultural Engineers.
Driveline Specications – The rst step towards safe applications is to specify and
test the driveline so that it operates properly under expected eld conditions.
✔Specify and test the proper size joints and telescoping members based upon
the power required by the implement, speed of rotation, joints angles, shock
loads, and expected life.
✔Test the hitch geometry to prevent the drive line from:
• Extending beyond the recommended maximum length.
• Bottoming out.
• Reaching a position that allows universal joints to lock.
• Exceeding the maximum allowable angle for constant velocity of
the universal joints.
Information concerning these parameters may be found in all driveline
manufacturer’s catalogs.
✔Specify and test telescoping members to allow the lowest possible thrust loads,
considering the expected working conditions.
✔Specify and test torque limiters to control excessive shock loads.
✔Where necessary, specify and test overrunning clutches to prevent inertial loads
from overpowering the tractor.

www.WoodMaxx.com
8
Hazard Reduction – The second step in specifying a safe driveline application is to
strive to eliminate as many hazards as possible
✔On driveline with torque limiting or overrunning devices, specify that
the device be positioned to the end of the driveline by the implement.
✔For implement connections which require bolts or set screws, select
and/or supply hardware which minimizes protrusions. Information concerning
these parameters may be found in all driveline manufacturer’s catalogs.
✔For tractors PTO shaft connections, specify a safety type yoke (twist or
slide collar) to minimize protrusions.
✔Provide a proper clearance zone for the operation of the driveline, to
avoid damaging the shielding components.
Some common areas of interference are:
•
Three point linkage.
• Extended or eye loop hitch pins.
• Hydraulic hoses.
Guarding – For hazards which cannot be eliminated effectively, guarding must be
provided whenever feasible.
The PTO master shield, integral driveline shield, and implement input connection
shield should provide an interactive guarding system.
✔Provide instructions by labels or manuals. The implement should be used only
with the tractor’s PTO master shield in place.
✔Specify and test an integral driveline shield with end cones which overlap, but
not interfere with the PTO master shield or implement input connection shield.
✔Provide an implement input connection shield to interact with the integral
driveline shield to provide guarding of the shaft coupling and any torque
limiting devices installed on the driveline.
✔Check that all routine maintenance of the driveline can be done without
removal of the shields.
DRIVELINE SAFETY CHECKLISTDRIVELINE SAFETY CHECKLIST

www.WoodMaxx.com
9
DRIVELINE SAFETY CHECKLISTDRIVELINE SAFETY CHECKLIST
Warnings and Instructions – Provide warnings and instructions for hazards associated
with the machine. Provide instructions for proper maintenance and repair.
✔Provide labels on the unit to advise the user of proper hitch dimensions and
maximum safe operating speed.
✔Check that proper danger labels are supplied with the driveline concerning
these parameters may be found in all driveline manufacturer’s catalogs.
✔Provide easy-to-understand instructions for proper driveline operation,
maintenance, and repair in the operator’s manual.
✔Advise against the use of PTO adapters which may defeat the purpose of the
tractor’s master shield and adversely affect the performance of the driveline.
✔Advise the user of locations of genuine original equipment spare parts.
Further information about driveline specications and safety may be obtained from
your driveline supplier and the following ASME standards and engineering practices:
S203 – Rear power take-off for agricultural tractors
S205 – Power take-off denitions and terminology for agricultural tractor
S207 – Operating requirements for tractors and power take-off driven
equipment implements
S318 – Safety for agricultural equipment
S331 – Implement power take-off driveline specications
S333 – Agricultural tractor auxiliary power take-off drives
S350 – Safety alert symbol for agricultural equipment
S441 – Safety signs
S493 – Guarding for agricultural equipment
EP363 – Technical publications for agricultural equipment
Other standards may apply for particular types of implements. All driveline
manufacturers strive to produce a safe product. Drivelines, like most other
components must be used properly, including the use of proper tractor master shields
and implement input connection shields. Please contact us if you have any questions
about your driveline applications.

www.WoodMaxx.com
10
• Your chipper will need to be set up prior to installation. It arrives in a steel crate that can
be dismantled in minutes.
• The infeed bin and discharge chute are shipped with the unit and are located in the
bottom of the steel crate.
• Visually inspect the infeed bin, and the y wheel before attaching to tractor, and applying
power to ensure that nothing is in the chipper head. If the chip deector or any of the
guards have been removed for shipping, be sure to replace them properly before use.
• The PTO (Driveline) is also shipped with the unit and is located in the bottom of the steel
crate.
• When mounting, keep the chipper as close to the tractor as possible.
• IMPORTANT - Make sure that the PTO shaft is sized properly. See PTO Shaft Sizing
Instructions on page 20 of this manual.
• While in use, keep the PTO shaft as straight as possible. Your PTO shaft will be more
efcient and will have a longer life if it is as close to level as possible.
No more than 25° degrees from level is acceptable.
• Do not operate the chipper without the chip deectors, and or drive belt cover properly in
place.
• Read and understand all assembly instructions prior to assembly.
ASSEMBLY INSTRUCTIONSASSEMBLY INSTRUCTIONS

www.WoodMaxx.com
11
Infeed bin left
side panel
Infeed roller
assist lever
Hardware box
& accessories
(See below for contents)
Support leg
Infeed bin right
side panel
Infeed bin
bottom panel
Infeed bin
top panel
Adjustable
base legs
Discharge
chute
Assembly Instructions (continued)
ASSEMBLY INSTRUCTIONSASSEMBLY INSTRUCTIONS
(36) 10mm
washers
(8) Fender Washers
(4) M10x15
bolts
(4) Lock
Washers
(18) M10x25mm
bolts
(4) 2-Hole
Straps
(18) M10
Lock Nuts
PTO Shield
& Hardware
Skid Shoes Safety Bar Spring
Removal Tool

www.WoodMaxx.com
12
ASSEMBLY INSTRUCTIONSASSEMBLY INSTRUCTIONS
Tools you will need:
• 13mm Wrench (same as 1/2")
• 16mm Wrench (same as 5/8")
• Adjustable Wrench
Assembly Time - Approximately 2.5 Hours
• Remove the plastic wrapping and/
or the cardboard from the crate and
inspect the chipper for any obvious
shipping damage.
• Remove and unwrap all the chipper
components that are packaged in the
crate.
• Remove the cardboard box from the
in-feed bin. This box contains the
user’s manual, hardware packet, extra
shear bolts, and any additional item
that you may have purchased such as
extra chipper knives.
• 3/16 Allen Wrench
• 6mm Allen Wrench
• Open the hardware packet and
organize the enclosed fasteners into
separate piles. There is a picture
of the hardware on page 11 of this
manual that you can use as a guide
to ensure that you use the correct
hardware in the upcoming steps.
• Remove the four bolts that secure the
top of the crate frame. Remove the
top of the crate, and set it aside.
• Located on the bottom of the crate is
a cross bar that secures the chipper to
the frame. Loosen the two bolts that
hold this bar in place, and drive the
bar forward with a dead blow hammer.
STEP 1 STEP 2

www.WoodMaxx.com
13
25°
Assembly Instructions (continued)
ASSEMBLY INSTRUCTIONSASSEMBLY INSTRUCTIONS
•
Locate the lift point on the top of the
chipper. This is the balance point, and the
only point the chipper should be lifted from.
• Using a chain or strap that is rated strong
enough to lift the weight of the chipper,
and the lift pin (not provided) lift the
chipper out of the crate.
• If you do not have a front end loader,
attach the three point hitch of your
tractor to the chipper to lift the chipper
out of the crate.
STEP 3 STEP 4
STEP 5
• Measure the distance from the PTO spline
of your tractor to the ground. Write down
this measurement here ________. You will
need it for the next step.
• While the chipper is raised in the air,
attach the four adjustable base legs so
that when the chipper is on the ground,
the spline of the chipper is slightly lower
than the spline of your tractor.
• The shaft does not need to be perfectly
horizontal, but it is recommended that
the slope of the PTO shaft is no more
than 25° degrees.
• Attach the skid shoe base plates as
shown using the included carriage bolts
and nuts. At this time, carefully lower the
chipper to the ground, and remove the
chain or strap.
STEP 6

www.WoodMaxx.com
14
Assembly Instructions (continued)
ASSEMBLY INSTRUCTIONSASSEMBLY INSTRUCTIONS
Inside mount
(washer, lock nut)
Outside mount (bolt,
fender washer)
View of proper assembly of in-feed bin
using 2 hole straps. All other bolts are
typically assembled as follows; bolt-
washer-panel-washer-lock-nut
Use Fender
Washers Here
• Attach the left panel of the in-feed bin
using two of the 2-hole straps and two
M10x25mm bolts. Straps will bend when
tightened down. This panel can be
identied by the two small holes on the
bottom of the panel where the fasteners
for the support leg attach.
• Attach the right side panel in the same
manor.
• Attach the bottom panel of the in-feed
bin, by rst inserting the two M10x25
bolts through the side panels in the two
holes closest to the feed roller. Do not
tighten these bolts yet, and allow the
panel to hang vertically.
STEP 7 STEP 8
STEP 9

www.WoodMaxx.com
15
ASSEMBLY INSTRUCTIONSASSEMBLY INSTRUCTIONS
Assembly Instructions (continued)
• Raise the bottom panel in place and
insert the two M10x25 bolts the side
panel in the two holes closest to the end
of the panel.
•
Install the remaining four M10x25 bolts in
the remaining four holes in the lower panel.
STEP 10 STEP 11
STEP 12
• Before tightening the bolts, ensure that
the lower panel is slightly higher than
the in-feed bin. This will prevent material
from hanging up where the two pieces
join together.
• Attach the top panel of the in-feed bin
by installing the four M10x25mm bolts in
the two forward holes of the panel. Afx
the safety bar stop to the top left of the
in-feed bin.
NOTE
Although we choose to
install the hardware with
the bolts pointing into the
infeed bin, it is acceptable to
point them outward to avoid
the possibility of branches
catching on the bolts.

www.WoodMaxx.com
16
ASSEMBLY INSTRUCTIONSASSEMBLY INSTRUCTIONS
Assembly Instructions (continued)
• Attach the upper feed roller assist lever
using four M10x25mm bolts.
• Fasten the chain from the upper feed
roller assembly to the feed roller assist
lever. The hardware for this is found
located on the end of the chain.
• Connect the safety bar to the top side
of the in-feed bin. First remove the bolt
and nut on right arm of the safety bar.
Hold the safety bar in place, so that you
can read the word STOP, and the arrows
point downward. Hook the bolt on the
left arm of the safety bar through the
hole on the top of the edge of the left in-
feed panel.
STEP 14
STEP 15
STEP 16
STEP 13
• Attach the support leg with two M10x25
bolts. Remember, the support leg should
be in the down position during storage
only. When the chipper is attached to the
tractor, the support leg should be in the
up position at all times.

www.WoodMaxx.com
17
ASSEMBLY INSTRUCTIONSASSEMBLY INSTRUCTIONSASSEMBLY INSTRUCTIONSASSEMBLY INSTRUCTIONS
Assembly Instructions (continued)
•
Align the hole on the right arm of the safety
bar with the hole in the top edge of the right
side panel, and reinstall the bolt and nut that
you removed in the previous step.
•
Adjust the clutch cable length so that it
is tight but not so tight that it starts to
disengage the clutch. Attach the end of
the clutch cable to the safety bar.
STEP 17 STEP 18
• Thread a M10 locknut onto the bolt on
either side, but do not tighten these nuts.
This is a hinge point and the bar must
move freely.
STEP 19 STEP 20
• Afx the discharge chute to the chipper
using four M10x15mm bolts along with
the four 10mm lock washers that were
included in the hardware packet.
Please check to make sure all nuts and bolts on machine are tightened after you complete the
assembly, and before using the chipper for the rst time. Although every effort has been made
to ensure that all hardware has been tightened, it is a good idea for you to double check.

www.WoodMaxx.com
18
ASSEMBLY INSTRUCTIONSASSEMBLY INSTRUCTIONS
STEP 21
• Connect the chipper to the 3-point hitch of your tractor [left], or if you have one, using your
category I quick hitch [right].
3-Point Hitch Category 1 Quick Hitch
Assembly Instructions (continued)
STEP 22 - See PTO Shaft Sizing Instructions on page 20 to size your
PTO shaft to t your tractor. Failure to properly size your PTO shaft
will result in damage to your chipper or tractor.
Damage resulting from improperly sized PTO shaft is not covered under warranty.
• By extending the lower hitch brackets,
you increase the distance between the
tractor and the chipper, which lessens
how much shaft you're required to cut.
• Now the shaft must be sized according
to this measurement. Refer to the “PTO
shaft cutting instructions” starting on
page 20 of this manual to determine if
you must size the shaft .
To adjust the MSED: Remove pin and
move draw arm in or out.

www.WoodMaxx.com
19
• Attach the PTO shaft from the tractor to the chipper. Notice that one end of the shaft has a
shear bolt, this end should be attached to the chipper.
Prior to shipping the chipper to you, the following service has been done in
our warehouse: the drive belts have been adjusted and tightened, the bearings
on the chipper have been greased, USA made knives have been installed,
adjusted, and the bolts were torqued to 40 ft. lbs.
SHEAR BOLT
CHIPPER
END
TRACTOR
END
SHEAR BOLT
CHIPPER
END
TRACTOR
END
STANDARD PTO SHAFT PREMIUM PTO SHAFT
ASSEMBLY INSTRUCTIONSASSEMBLY INSTRUCTIONS
STEP 24
Assembly Instructions (continued)
Setup is now complete. You must read and understand
all operation instructions before using the chipper.
• After properly sizing the shaft, locate
the three grease ttings on the shafts
U-joints, and pump several shots of high
quality grease into the ttings.
NOTE: Check to ensure that the zerk
(grease) ttings are screwed in tight.
Occasionally, dried paint may cover
the end of the zerk tting on the PTO
shaft. Remove this by scraping the paint
off with a knife prior to attempting to
pump grease into these ttings.
STEP 23
Table of contents
Other WoodMaxx Chipper manuals
Popular Chipper manuals by other brands
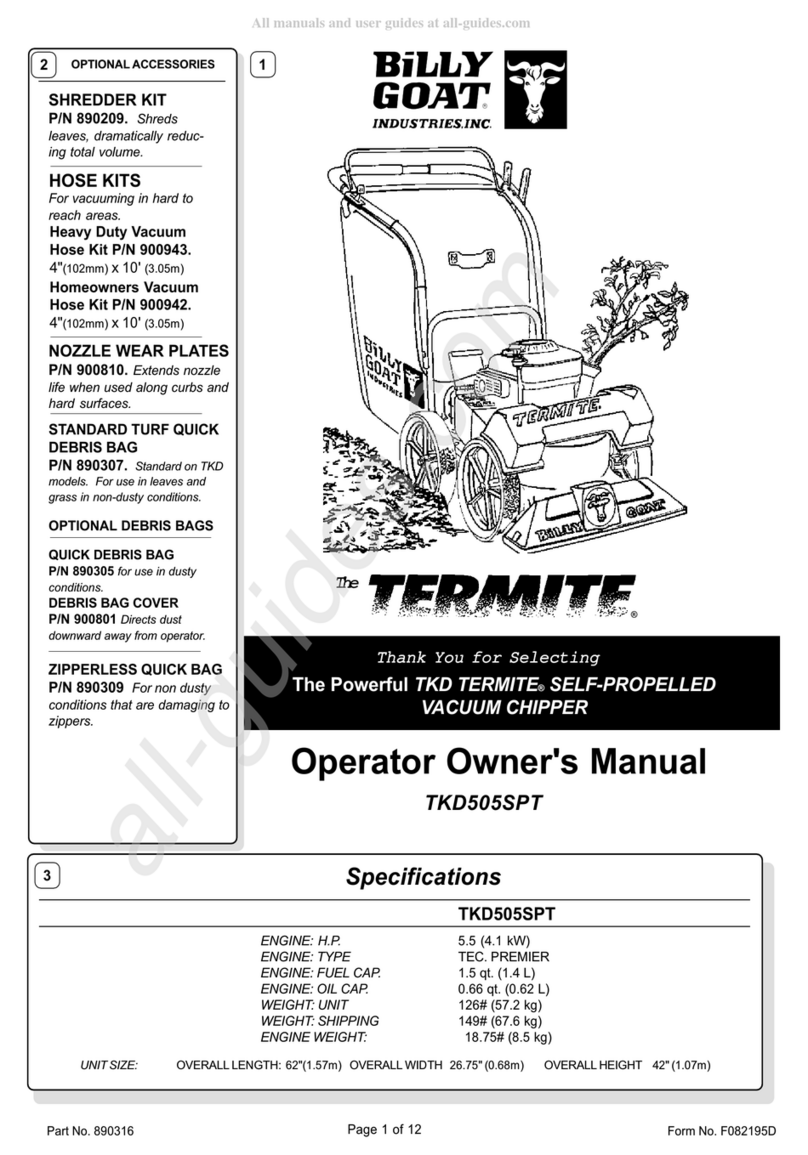
Billy Goat
Billy Goat 890209 Operator owner's manual

Giant-Vac
Giant-Vac 20hp Series Assembly instructions operator's manual parts list
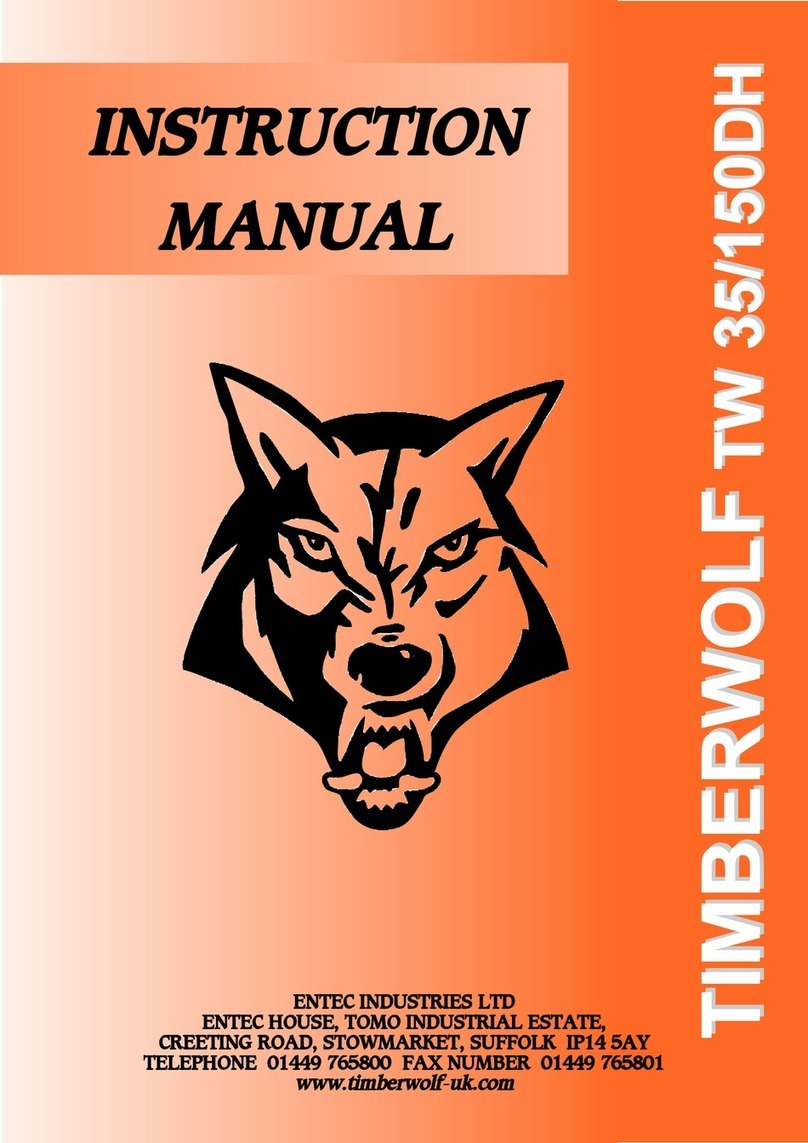
Entec
Entec Timberwolf TW 35DH instruction manual
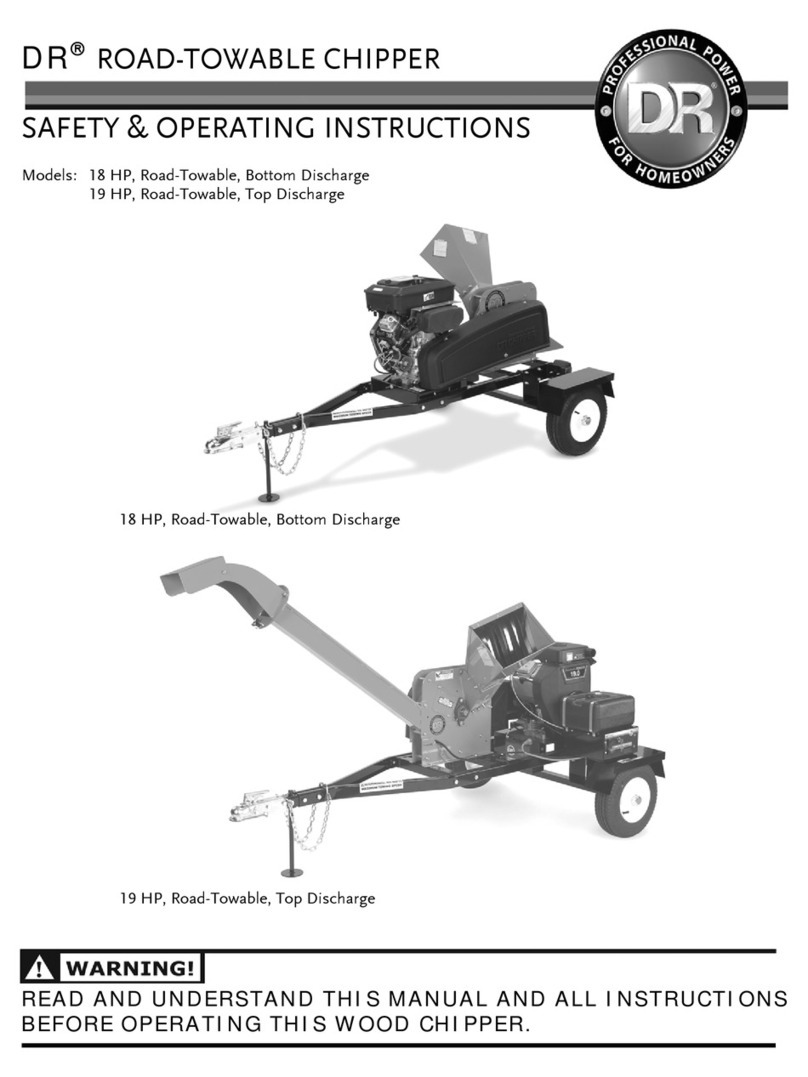
DR
DR 18 HP Safety & Operating Instructions

Victory
Victory BX42S Operator's manual

Vermeer
Vermeer BC160XL Operating and safety instructions