Work Smart JE Series User manual

Instruction Manual
ELECTRIC HIGH LIFT TRUCK
Note: Owner/Operator must read and understand this instruction
manual before using the electric high lift truck.

1
THANK YOU VERY MUCH FOR SELECTING OUR ELECTRIC HIGH
LIFT TRUCK. THIS INSTRUCTION MANUAL DESCRIBES THE
CORRECT OPERATING METHOD TO ENSURE PROLONGED
SERVICE LIFE. PLEASE READ AND COMPLETELY UNDERSTAND
THIS MANUAL BEFORE OPERATING THE LIFT TABLE. ALWAYS
KEEP THIS MANUAL AT AN APPROPRIATE PLACE. IF THE
MANUAL OR WARNING DECAL IS MISSING, PLEASE CONTACT
OUR DEALER.
Brief Introduction
JE series electric high lift trucks (short for JE series hereafter) are
designed on the basis of a hand-operated high lift pallet truck (short for
JL hereafter). It is equipped with a battery powered Pump Station,
high-pressure hose and electrical control device.
This lift truck features automatic up and down pumping. It greatly
reduces labor and maintains high working efficiency. Meanwhile, it has
retained JL features, such as the application of material lifting and
transporting when the fork is in its lowest position, and the use as a
working table when the fork is in its highest position.
Those features make the JL series a most popular tool in workshops
and warehouses whether it is used as a working table, or for loading
and unloading.
The mechanical part of the JE series consists mainly of a fork, lifting
yoke, lifting bar, cylinder, handle, etc.
Its power part mainly includes a battery, mini-pump station,
high-pressure hose, fuse, control switch, etc.
It is easy to operate by pushing a button (Part No.197) on the top of
Handle (102) to pump the goods up and down. It can be stopped at
any position desired.

2
Specifications
Assembly and Adjustment
1. Remove the packing materials carefully. Be careful not to damage
the pallet truck while unpacking.
2. Insert handle (102) into the socket of cylinder (160); lock it with a pin
(108) and two screws (109). Raise the handle up and down to see if
it moves freely. Finally, attach the spring (105).
3. Open the electrical control case by removing the cover (255). Insert
switch wire and plug (184) hanging down from handle (102) into
socket (221) in the case. Insert one fuse of 5 Amp (277) into two
sockets of F2.
4. Check the electrical device and elements to ensure they are not
loose or broken.
5. Check oil pipes in the hydraulic system to confirm they are securely
tightened. Open cover (217) to see if oil is sufficient.
Model
WS-MH-LFTB
1-114
WS-MH-LFTB
1-116
WS-MH-LFTB
1-115
WS-MH-LFTB
1-117
Rated Capacity (lb) 2200 3300
Max. Lifting Height
(in)
31.5
Min. Fork Height
(in)
3.3
Fork Length
(in)
44.9
43.3
Fork Overall Width (in)20.5 26.7 20.5 26.7
Dia. of Front Wheel (in) Φ2.95×1.97
Dia. of Rear Wheel (in) Φ5.9×1.57
Motor Working Voltage 12V
Battery 66Ah/12V
Charger 8A/12V
Net Weight (lb) 309 324 328 346

3
6. Push the Up-button (197) on the top of the handle (102)
intermittently to lift the fork, while observing the electrical device and
elements to confirm there are no abnormal phenomenons. If none
are observed, continue to push the Up-button to lift the fork to its
highest position. Then push the Down-Button (197) to release the
fork to its lowest position gradually.
7. Repeat the above procedure 3 to 4 times to its fullest extent in order
to release any possible air in the hydraulic system and to ensure
there are no other problems.
8. Close the case with cover (255) and tighten the screw securely
(256).
Operation
1. JE truck lift series are designed for working on flat and even ground.
2. The handle (102) should only be used for pulling and steering.
3. When the fork is lifted to its highest position, the JE series lift truck
should not be moved.
4. When the Push Up-button is activated, the fork goes up. Upon
release of the Push Up-button, the fork will stop at that position and
will no longer raise up or lower.
5. When the Push Down-button is activated, the fork will lower. Upon
release of the Push Down-button, the fork will stop at that position
and will no longer lower or raise up.
6. With a safety valve set in the pump station, when the JE series truck
lifts elevates a load(its full capacity), only the mid-cylinder (413) will
extend out fully, while the piston rod (406) will not extract out which
prevents overload.
7. Recharge Battery (254): when the indicator of the electric meter
rests on the red line, operation is strictly prohibited. Recharge the
battery immediately. Plug the recharger (271) into a power socket.

4
Make sure your local power matches the recharger. Then connect
the recharger to the Socket (225) in the electrical control case. The
battery will be automatically recharged. Details are located in the
manual.
Precautions
1. Read the manual completely before operation. Complete each step
as required in the manual.
2. Raise the fork to its full range 1 to 2 times before use to release the
air in the hydraulic system.
3. JE series truck lifts are prohibited to lift or pull personnel. The JE
series truck lifts are prohibited from operation on a sloped surface.
4. Do not put your hand or foot under the fork or on the moving surface
of piston rod (406) and mid-cylinder (413).
5. Always place the load on the center of the forks. Unbalanced loading
is strictly prohibited.
6. The safety valve in the pump station will automatically open when it
is overloaded. Under such a circumstance, do not push the
up-button. Otherwise the lifetime of the pump station will be reduced.
7. To replace or fill hydraulic oil, the forks should be placed to the
lowest position. The oil to be used should be clean. The oil
condensation point should be ≤- 68ºF. The motion viscosity: 20-30
cst (centistokes).
Easily worn Parts
Series No.
Part No.
Description
Quantity
1
277
5A
1

5
Problems and Maintenance
N0.
Symptom
Cause
Remedy
1
Fork does not
ascend when
activating the
up-button
1.Switch is out of order
2.Fuse is broken
3.
Magnetic switch is out
of order
4.Not enough oil
1. Check switch (197)
2. Replace fuse (277)
3.
Check magnetic
switch (224)
4. Fill oil
2 Fork does not
descend when
activating the
down-button
1.Switch is out of order
2.Fuse broken
3.
Magnetic switch is out
of order
4.Object blocking path
1.Check switch (197)
2.Replace fuse (277)
3.
Check magnetic
switch
4.Check and remove the
object
3
Fork does not
ascend to the
highest position
1.Not enough oil
1.Fill oil
4 Motor does not
work
1.Motor broken
2.
Terminals and inserters
are loose
3.Battery worn out
1.Check motor brush
2.
Check terminals and
inserters
3.Recharge at once
5 Battery has not
enough power
1.Recharging time needs
to be extended
2.Battery is out of order
1.Recharge for a longer
time
2.Fill battery liquid or
replace battery
6
Oil leakage from
Piston Rod &
Mid-cylinder
1.Oil seals broken
1.Replace oil seals
7
Unsteady when
JE
is on its
highest position
1.The ground is not flat or
even
2.Centrifugal axle is off
the ground
1. Work on flat and even
ground
2.Adjusting centrifugal
axle (7)
to touch the
ground

6
HYDRAULIC CIRCUIT / ELECTRIC WIRING
DIAGRAM
M
M

7
EXPANDED FIGURE & PARTS LIST
Item No.
Description
QTY
1 Fork 1
2 Screw 1
3 Nut 1
4 Power Unit 1
5 Hold Yoke 1
6 Wheel Yoke 1

8
7 Centrifugal Axle 2
8 Spacer 2
9 Steering Wheel 2
10 Snap Ring 8
11 Pin 2
12 Snap Ring 12
13 Bush 2
14 Leg 2
15 Leg 1
16 Bush 2
17 Pin 2
18 Washer 2
19 Nut 2
20 washer 8
21 Ball bearing 8
22 Front wheel 2
23 Wheel axle 2
24 Roller 4
25 Bush 2
26 Washer 4
27 Spring washer 2
28 Lock Nut 2
29 Screw 1
30
Steering wheel assembly
(incls.6,9,10,21)
1
31 Screw 1
32 Nut 1
33 Ball 51
34 Snap ring 1
35 Bush 1
36 quill bearing 1

9
EXPANDED FIGURE & PARTS LIST
FOR ELECTRIC CONTROL ASSEMBLY

10
Item No.
Description
QTY
4 Power Unit 1
202 Battery Terminal (+) 1
203 Battery Terminal (-) 1
204 Terminal 2
205 Washer 3
206 Screw 2
207 Electric Control Case 1
208 Spacer 2
209 Spring Washer 1
210 Screw 1
211 Fuse Base 1
212 Relay 1
213 Relay Base 1
214 Screw 1
215 Relay 1
216 Control Valve 1
217 Cap 1
218 Oil Tank 1
219 Control Valve 1
220 Pump Station Assembly 1
221 Switch Socket 1
222 Fuse Box 1
223 Magnet 1
224 Magnet 1
225 Recharger Socket 1
226 Nut 1
227 Screw 1
228 Valve Body 1
229 Switch 1
230 Switch Base 1

11
231 Screw 1
232 Moving Plate 1
233 Cover 1
234 Switch 1
235 Volt Meter 1
251 Washer 7
254 Battery ,12V/80Ah 1
255 Cover 1
256 Screw 2
271 Recharger, 12V/10A 1
273 Screw 2
277 Fuse,5A 1
279 Fixing Screw for Battery 1
281 Nut 2
282 High Pressure Oil Pipe 1
284 Washer 2
285 Washer 2
286 Screw 2

12
EXPANDED FIGURE & PARTS LIST
FOR PUMP ASSEMBLY

13
Item No.
Description
Remark
97 Handle 1
98 Cover 1
99 Screw 4
100 Pin 6
101 Spacer 2
102 Handle tube 1
103 Washer 2
105 Tension spring 1
108 Pin 1
109 Screw 2
110 Adjusting screw 1
111 Snap ring 4
112 Sleeve 2
113 Pin 1
114 Pin 1
136 Scraper ring 1
137 O-ring 1
138 Y-ring 1
153 O-ring 1
160 Pump housing 1
161 Thrust bearing 1
162 Ball 1
163 Snap ring 1
164 Washer 1
176 Rubber sleeve 1
184 Switch wire & plug 1
190 Copper piston 1
191 Snap ring 1
192 Snap ring 1
195 Washer 1

14
197 Up-down switch 1
198 O-ring 2
199 Bushing 1
200 Cylinder 1
201 Back-Up ring 1
400 Bronze Bushing 1
401 Back-Up Ring 1
402 Y-Ring 1
403 Bushing 1
404 Snap Ring 1
405 Bushing 1
406 Piston Rod 1
407 O-Ring 1
408 Piston 1
409 Washer 1
410 Washer 1
411 Screw 1
412 Cylinder Head 1
413 Cylinder 1
414 Snap Ring 1
50 Handle assembly 1
300 Pump Unit 1
*
Seal Kits:
136#、137#、138#、201#、153#、
198#
、
401#
、
402#
、
407#
1
This manual suits for next models
4
Table of contents
Popular Lifting System manuals by other brands
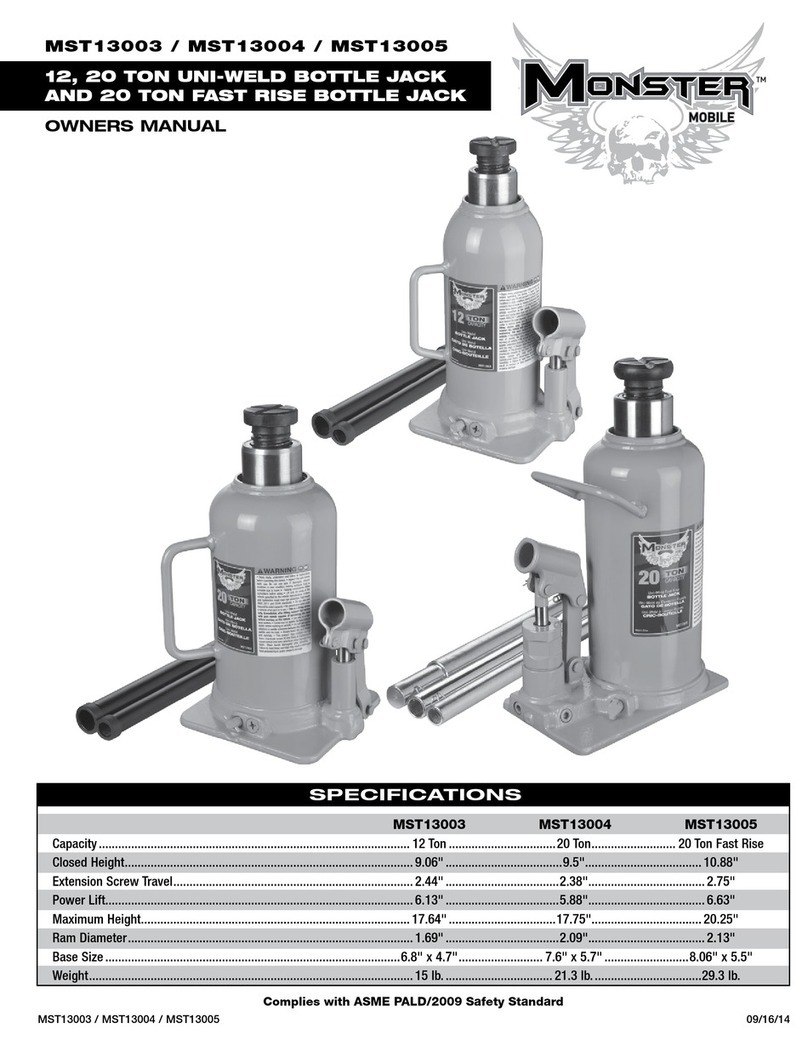
MONSTER MOBILE
MONSTER MOBILE MST13003 owner's manual
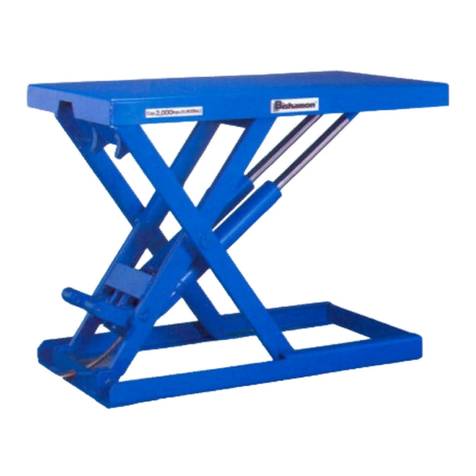
Bishamon
Bishamon LX25SA Operation and service manual

Bohle
Bohle BO 600.1G operating instructions
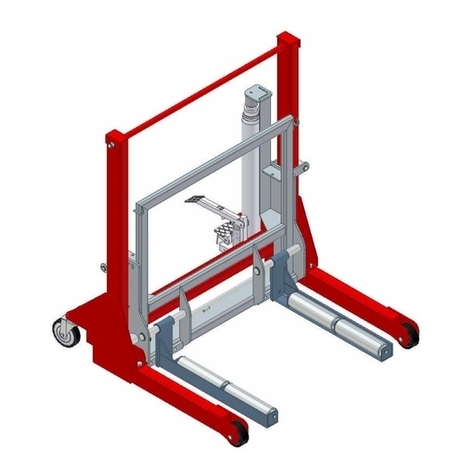
MELCHOR GABILONDO
MELCHOR GABILONDO MEGA SR 700 Operation and maintenance instructions

Mec
Mec 60-J Diesel Service & parts manual

Avanti
Avanti OCTOPUS L95 Original instructions