XYZ Machine Tools ProtoTRAK RMX User manual

XYZ Machine Tools Ltd.
Woodlands Business Park
Burlescombe, Tiverton, Devon EX16 7LL
T: 01823 674200 F: 01823 674201
www.xyzmachinetools.com
Copyright 2019, XYZ Machine Tools Ltd. All rights are reserved. No part of this publication may be reproduced,
stored in a retrieval system, or transmitted, in any form or by any means, mechanical, photocopying, recording or
otherwise, without the prior written permission of XYZ Machine Tools Ltd.
While every effort has been made to include all the information required for the purposes of this guide, XYZ Machine
Tools Ltd. assumes no responsibility for inaccuracies or omission and accepts no liability for damages resulting from
the use of the information contained in this guide.
All brand names and products are trademarks or registered trademarks of their respective holders.
XYZ Machine Tools
ProtoTRAK®RX CNC
Safety and Quick Start Guide
Part Number: 17639
Version: 230519
Covers all XYZ RMX and RLX Models

1
XYZ Machine Tools
ProtoTRAK RX CNC control, Safety and Quick Start Guide
Introduction
This guide provides important safety Information and a very brief description of the operation of the
CNC control.
Full safety and operating information is provided in the ProtoTRAK RMX or RLX CNC Safety,
Programming, Operating, and Care Manual. Please take time to read and understand these manuals
before using the machine. These manuals can be downloaded from the support pages of our website
https://www.xyzmachinetools.com/customer-support/downloads-manuals/
Safety
This machine is designed for the machining of cold metal within the stated capacity of the machine
with axes movement occurring by manual use of handwheels or CNC control.
This machine must not be used for machining flammable materials (e.g. magnesium) without
undertaking a risk assessment and incorporating any additional safety measures identified.
It is designed to be used in a standard workshop environment only.
It is the responsibility of the employer, machine owner or machine controller to ensure that this
machine is installed, operated and maintained in accordance with the Provision and Use of Work
Equipment Regulations (1998) or equivalent local regulations.
In particular, the responsible person must:
1. Undertake a Risk Assessment on the use of this machine, paying particular attention to the
unique characteristics of the Prototrak control system (for example, operating mode selection
and access to the work zone)
2. Generate and apply Safe Operating Procedures for the use of the Prototrak machine
3. Provide any additional training, safeguarding and PPE identified by the risk assessment.
This machine must only be operated by trained and experienced operators.
The following Safety Features must be checked on a regular basis (e.g. at the start of every shift):
1. E-stop
a. Press the E-stop button and ensure that the control flags up faults 261 (E-stop active)
and 0055 (machine disabled) and that the axes and spindle cannot be started. For
lathes, check that the spindle is held on the emergency stop brake.
b. For lathes with sliding front guards: press each of the safety edge strips and check the
machine goes into the E-stop condition each time.
2. Guard Interlocks
a. Table Guards (RMX Mills): Start the spindle at maximum speed and then open each door
guard in turn. Check that the spindle stops quickly (around 1 second) and cannot be re-
started and that the maximum feedrate is limited to 2m/min (78 ipm)
b. Chuck Guard (RLX lathes): Start the spindle at maximum speed and then open the chuck
guard. Check that the spindle stops quickly (around 3 to 8 secs depending on model)
and cannot be re-started.
c. Belt door guard (RLX lathes): Repeat the above for the belt door guard. WARNING:
Only open the door enough to trigger the interlock –stay well clear of the drive belts!
d. Main Door (RLX lathes): open the main door guard in DRO mode. Check that the door
open message appears on the screen and that maximum feedrate is limited to 2m/min
(78 ipm).
3. Safety Speed Monitoring –Close the table guards(mills) or main door guard (lathes) and
whilst jogging at max feedrate, open the guards. Check for a fault 247, 248 or 249,
depending on which axes was jogging (max permissible feedrate exceeded).
4. Guards: Inspect the guards for signs of damage (especially the transparent panels). Replace
if any part of the guard is damaged. Replace the transparent panels in accordance with the
stated schedule, regardless of their apparent condition (see the FAQ on our website for why

2
XYZ Machine Tools
ProtoTRAK RX CNC control, Safety and Quick Start Guide
this is important). For mills, do not forget to use the retractable guard at the back of the
table. For lathes, always close the front door when cutting, regardless of mode.
Notes on the E-stop and Guard critical safety functions:
•E-stop:
•This is provided by a safety rated, hard-wired E-stop system controlled by the E-stop
button on the pendant or table guard/apron panel. When the machine is E-stopped, the
axes are disabled and the spindle is put into a Safe Torque Off mode.
•Releasing the E-stop button and pressing the Reset button, will always take the machine
out of the hardware E-stop condition (unless there is a fault with the safety circuits).
However, the machine may still be disabled because of the current machine mode, or on
the results of software safety checks undertaken by the control (fault 0055). This an
“NC Not ready” state; and should not be confused with the hardware E-stop condition.
•If you wish to leave the machine in a hardware E-stop condition, for example, when
leaving the machine unattended, always press in, and leave pressed in, one of the E-
stop buttons. Do not twist to release the E-stop button until you are ready to make the
machine live again.
•Spindle Guards (table guards for mills or chuck/belt door guards for lathes):
•When the spindle guards are opened, the spindle control system actively drives the
spindle to a stop very quickly, but the spindle remains powered. After a short delay, the
spindle is put into a Safe Torque Off mode, where the spindle is now completely safe.
On mills, this time delay coincides with the spindle air brake being applied.
•Therefore, DO NOT touch the spindle until the spindle is in the Safe Torque Off Mode,
i.e. the mill air brake has engaged (which occurs approximately 3 seconds after the door
guards are opened) or a few seconds after the lathe chuck has come to a stop.
•Note, if the spindle guards are closed again at about the same time as the delay expires,
due to small differences in each of the dual channel safety circuits, it is possible for the
safety circuit to lock out and then the spindle cannot be run. In this case, simply open
the guards again and wait about 10 seconds before closing.
When operating this machine, always observe the following safety precautions
•Do not operate this machine without knowing the function of every control key, button, knob,
or handle.
•Always wear the appropriate personal protective equipment, including safety glasses and
safety shoes.
•Do not wear loose fitting gloves whilst operating this machine as they could easily get caught
in moving parts.
•Never wear rings, watches, long sleeves, neckties, jewelry, or other loose items when
operating the machine.
•Keep your hair away from moving parts. Wear adequate safety head gear.
•Never operate any machine tool after consuming alcoholic beverages, or taking strong
medications, or while using non-prescription drugs.
•Carry out a COSHH risk assessment and use the correct protection equipment, e.g. barrier
cream/latex gloves, to prevent harm from items such as cutting fluid, lubrication oil and other
substances used on the machine.
•Do not use compressed air to remove swarf or clean the machine. This can damage the
slideway seals and create coolant mist which can be harmful. XYZ recommend the use of
BioConcept cutting fluids which do not present a risk to the respiratory tract.
•Always ensure the appropriate guarding is in place for the machinery operation being
undertaken. Never reach around a guard to gain access to the part, tool, or fixture.
•Observe and understand the warning and safety information labels affixed to this machine.
•Do not attempt to tamper with or override any guarding/safety device fitted to the machine.
•Stop the machine spindle, open the table/ or chuck guards and take the CNC control out of
an active mode (DRO, RUN, TOOL SETUP):
oBefore changing tools.
oBefore changing parts.

3
XYZ Machine Tools
ProtoTRAK RX CNC control, Safety and Quick Start Guide
oBefore you clear away the Swarf, oil or coolant. Always use a chip scraper or brush.
oBefore you make an adjustment to the part, vice, coolant nozzle or take measurements.
•Do not rotate the spindle by hand unless the table guard or chuck guard is open.
•Keep the working area clear and remove all tools (spanners, chuck keys etc.) from the
machine before you start the machine running. Loose items can become dangerous flying
projectiles.
•Keep work area well lit. Ask for additional light if needed.
•Be aware that the machine can move unexpectedly so do not lean on the machine while it is
running.
•To prevent slippage and personal injury, keep the working area around the machine dry and
clean. Ensure there is no swarf, oil, coolant and obstacles of any kind around the machine.
•Avoid getting pinched in places where the spindle, table or guards create "pinch points" whilst
the machine is in motion.
•Securely clamp and properly locate the workpiece in the vice, fixture or chuck. Use proper
tool holding equipment.
•For Mills:
oDo not raise the cutting tool above the table guards without additional guarding
measures such as a cutter guard.
oManual handwheels: to prevent injury during powered axes movement, keep the handle
folded inside the hand wheel at all times except when required to hand crank the table.
•For Lathes
oThe safe RPM for the chuck, faceplate or job set up must never be exceeded. The
maximum safe RPM value must always be entered into the control before the spindle is
started.
oLong workpieces must not be machined without suitable supports from the tailstock
and/or steadies. The maximum, unsupported workpiece length MUST NOT EXCEED
300mm.
oMaterial extending out the back of the headstock can present a whipping hazard. Ensure
the workpiece is supported with the correct equipment prior to starting the spindle.
•Use the correct tooling for the process being undertaken. Never use damaged or worn tools
and ensure the correct cutting parameters (speed, feed, and depth of cut) are used in order
to prevent tool breakage.
•Prevent damage to the workpiece or the cutting tool. Never start the machine (including the
rotation of the spindle) if the tool is in contact with the part.
•Avoid large overhangs on cutting tools when not necessary.
•To prevent fires, keep flammable materials and fluids away from the machine, hot swarf and
workpieces.
•Never change gears when the spindle is rotating
•Stop and disconnect the power to the machine before undertaking any cleaning or
maintenance

4
XYZ Machine Tools
ProtoTRAK RX CNC control, Safety and Quick Start Guide
Operating Controls
Keyboard Hard Keys
X, Y, Z: selects axis for subsequent commands
INC SET: loads incremental dimensions and general data
ABS SET: loads absolute dimensions and general data
0-9, +/-, . : inputs numeric data with floating point format. Data is automatically + unless +/-key
is pressed. All input data is automatically rounded to the system's resolution
RESTORE: clears an entry, aborts a keying procedure
BACK: Moves back within the screen or the DIL when there isn’t a better way to do it.
* KEY –Not used at this time.
** KEY –Not used at this time.
Feed Keys:
GO: initiates motion in Run. The green LED on the GO key will be lit when the servomotors are
moving the machine or when the program run has been initiated by the GO key.
STOP: halts motion during Run. The red LED on the STOP key will be lit when the servos motors
are not moving the machine.
Spindle Keys:
REV: runs the spindle in reverse at programmed speed with any override.
OFF: Turns spindle off.
FWD: runs spindle in the forward direction at programmed spindle speed with any override.
EHW FINE/COURSE:
Selects the resolution for the Electronic Handwheels (if fitted).
ACCESSORY: When the switch is in the On position, the flood coolant pump will come on and stay
on during machining operations. It will not turn off during tool changes.
POWER / RESET: the LED on indicates the servo system (axes and spindle) is ready. This button
will need to be pressed at first power up and any time the control gets into a critical fault condition.
For example, if the user presses the Emergency Stop button.
Keyboard Soft Keys
The soft keys are enabled and operated by the touchscreen.

5
XYZ Machine Tools
ProtoTRAK RX CNC control, Safety and Quick Start Guide
Fly Out Windows
Touching one of the INFO Soft Keys initiates another window to open (or “fly out”). When one of
these windows is active, the associated INFO Soft Key will be yellow. In order to put the window
away, or switch to another Fly Out Window, press the INFO Soft Key again.
Warnings are also presented in a Fly Out Window. When a Warning appears, you must press the
Clear soft key to dismiss the warning.
The lower ethernet port is used for communication with the computer module in the electrical cabinet
–do not remove this cable.
A USB Option Key is plugged into the USB port above the lower Ethernet port. This key must be
plugged in to allow certain standard software features to work and also to allow optional software
features to work.
Please note a number of control features designed to maximise the productivity of the machine:
The Touch Screen Interface enables you to interact with your programs and set ups with more
certainty and control than ever before.
Defaults allow you to customize the ProtoTRAK RX for how
you
make parts; they are easy to set and
easy to change.
The large LCD screen and fly out windows allow you work with everything you need at the same
time without flipping between screens.
Enhanced ProtoTRAK Assistance (EPA) is always available for you to quickly look up the
information you need for what you are doing at the time.
Powering Up the System
To turn on the machine, rotate the power switch on the Electrical Cabinet to the On position.
The control will go through its boot up sequence. When it is finished, the following screen will
appear.

6
XYZ Machine Tools
ProtoTRAK RX CNC control, Safety and Quick Start Guide
Tap the CHECK SYSTEM soft key and, for lathes, enter the maximum (safe) spindle speed based on
chuck rating and/or job setup and press ABS SET
The machine will always power up in an Estop condition, Press the POWER Reset hard key and hold it
for a few seconds, until the white LED comes on, when you are ready to start moving the machine.
Shutting down the ProtoTRAK RX CNC
Important: The system must be turned off properly or you may lose unsaved data such as
programs or certain machine configurations. The SHUT DOWN soft key will initiate the
process of shutting down safely. When the screen goes blank, turn the power switch at the
back of the electrical cabinet to the Off position.
First close any Fly Out Windows that are open. We also recommend that you complete any prompted
activity, such as programming an Event. Press the BACK hard key repeatedly until you get to the
screen shown above.
The ProtoTRAK control should be shut off at a minimum every few days. Failure to reboot may cause
the control to run slowly. Use the SAVE TEMP feature prior to shut down to save your current
positions, tool information and program.
If the screen does not go blank after the RX software closes, use the on-screen keyboard or an
external keyboard to shut down Windows in the normal way (do not switch off power if Windows is
still running).
Please refer to the Operating Manual for full operating instructions.
Maintenance
Please refer to the maintenance schedule on the machine or in the service manual for important
maintenance activity.

7
XYZ Machine Tools
ProtoTRAK RX CNC control, Safety and Quick Start Guide
XYZ Machine Tools Ltd.
ProtoTRAK UK Warranty Policy
ProtoTRAK products are warranted to the original purchaser to be free from defects in workmanship
and materials for the following periods:
Product
Warranty Period
New ProtoTRAK Controlled Machine
12 Months
Any Exchange Unit or Spare Part
6 Months
The warranty period starts on the date of the invoice to the original purchaser from XYZ Machine
Tools Ltd (XYZ) or their authorised distributor. If a unit under warranty fails, it will be repaired or
exchanged at our option for a properly functioning unit in similar or better condition. Such repairs or
exchanges will be made carriage paid within the UK mainland.
Disclaimers of Warranties This warranty is expressly in lieu of any other warranties, express or
implied, including any implied warranty of merchantability or fitness for a particular purpose, and of
any other obligations or liability on the part of XYZ (or any producing entity, if different). Warranty
repairs/exchanges do not cover incidental costs such as installation, labour, etc.
•XYZ is not responsible for consequential damages from use or misuse of any of its products.
•ProtoTRAK products are precision mechanical/electromechanical measurement systems and
must be given the reasonable care that these types of instruments require.
•Replacement of slideway wipers and covers is the responsibility of the customer.
Consequently, the warranty does not apply if swarf or coolant have been allowed to enter the
mechanism.
•This machine is designed to cut common, metallic engineering materials (such as steel and
aluminium). DO NOT use to cut special materials (such as composites or abrasives) without
agreement from XYZ Machine Tools. Any damage caused to the machine by processing such
materials will not be covered by the warranty.
•Accidental damage, beyond the control of XYZ, is not covered by the warranty. Thus, the
warranty does not apply if an instrument has been abused, dropped, hit, disassembled or
opened.
•Improper installation by or at the direction of the customer in such a way that the product
consequently fails, is considered to be beyond the control of the manufacturer and outside
the scope of the warranty.
This manual suits for next models
1
Table of contents
Popular Control Panel manuals by other brands
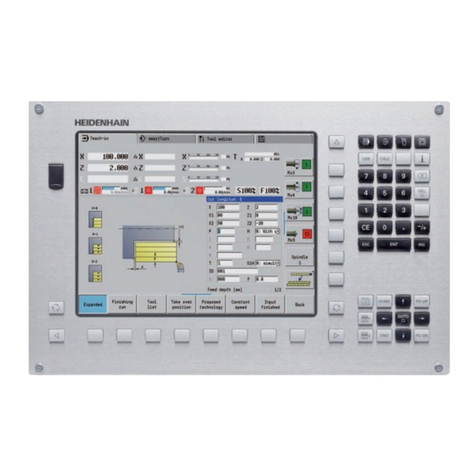
HEIDENHAIN
HEIDENHAIN MANUALPLUS 620 manual
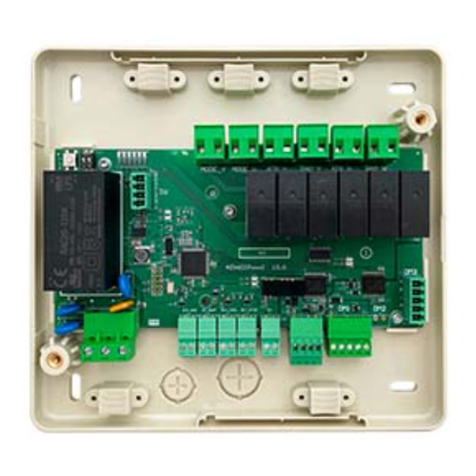
Airzone
Airzone AZX6CCPGAWI Quick installation guide
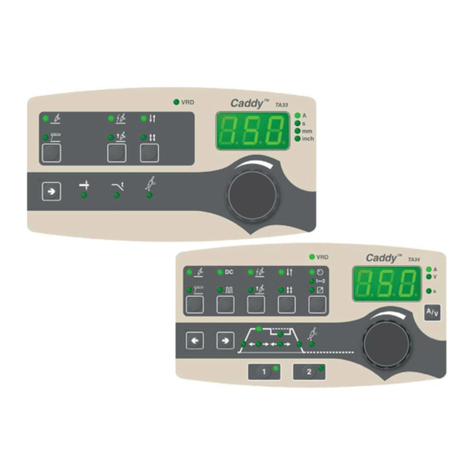
ESAB
ESAB Caddy TA33 instruction manual
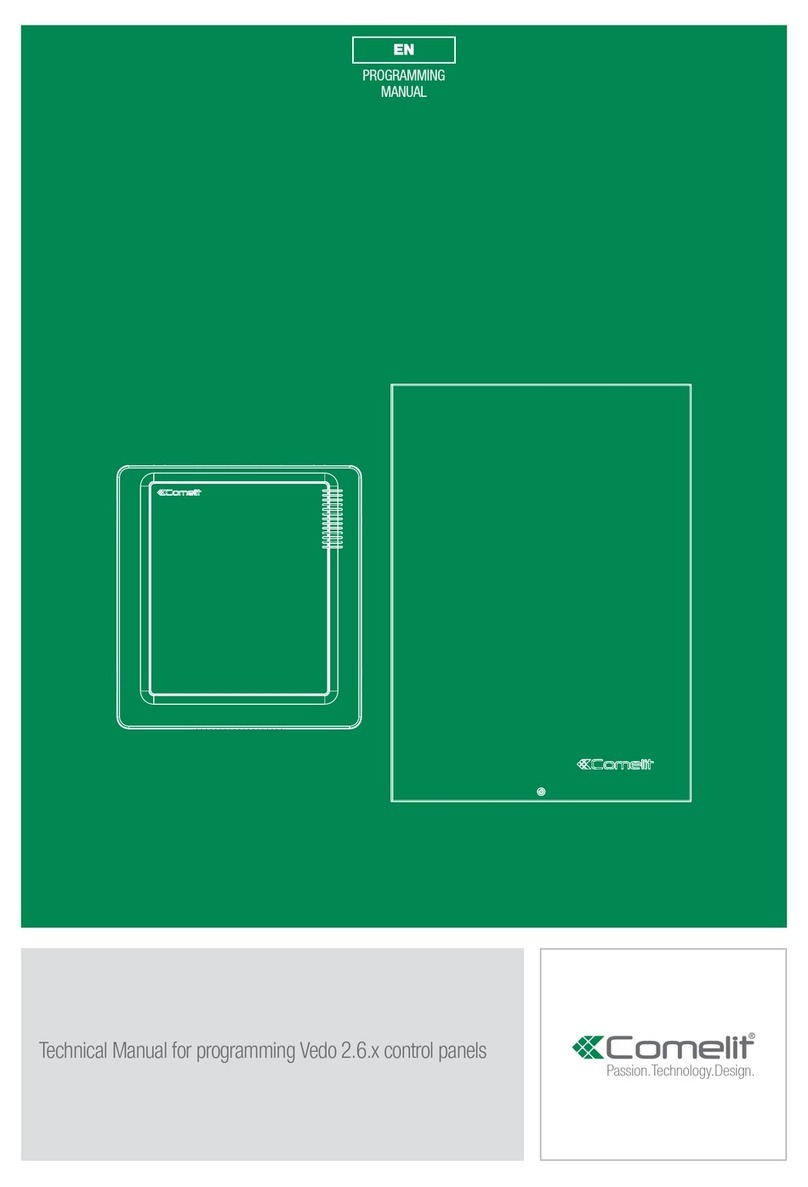
Comelit
Comelit VEDO 2.6 Series Programming manual

BFT
BFT RIGEL 5 quick reference
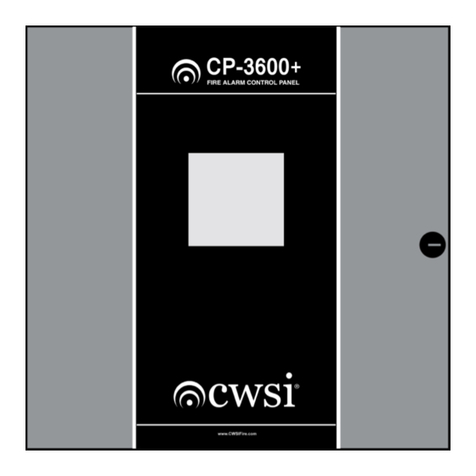
Tyco Fire & Security
Tyco Fire & Security CWSI CP-3600 Operating and installation instruction manual

Zonefirst
Zonefirst H32 Uni-Zone Installation and operating information

American Standard
American Standard ACONT900AC43UA owner's guide
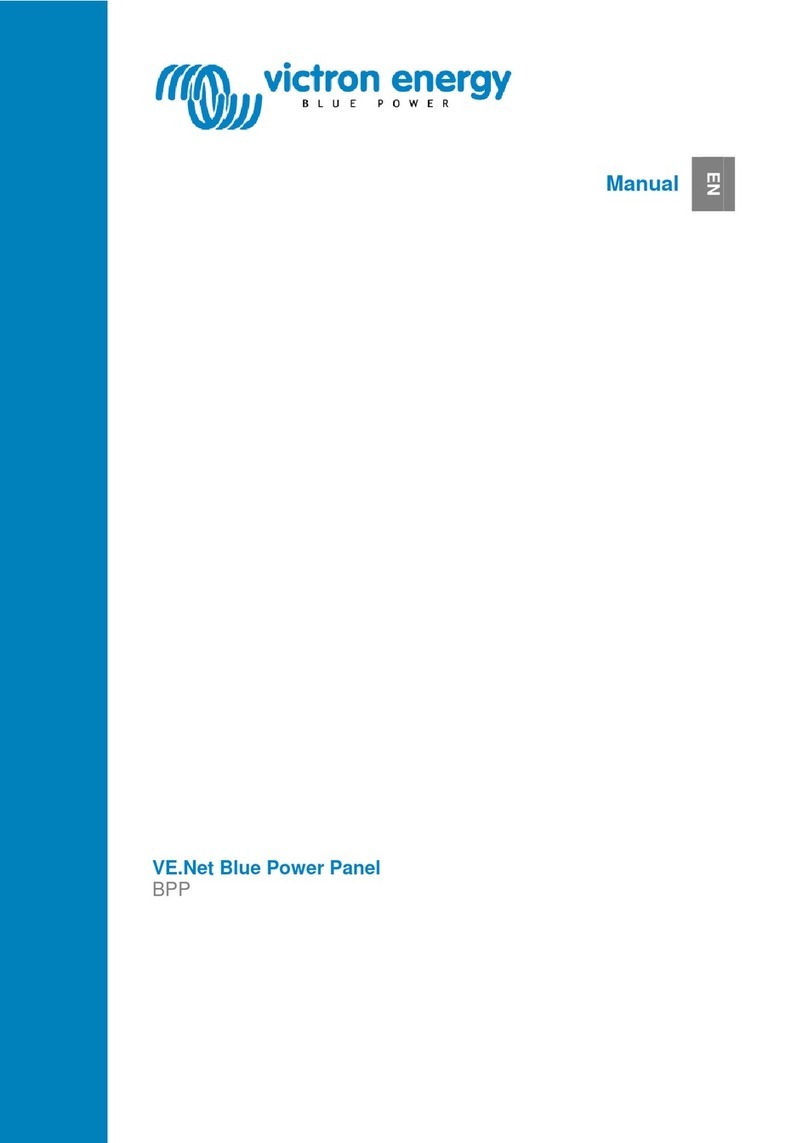
Victron energy
Victron energy VE.Net Blue Power Panel manual

Sleipner
Sleipner 8950G user manual
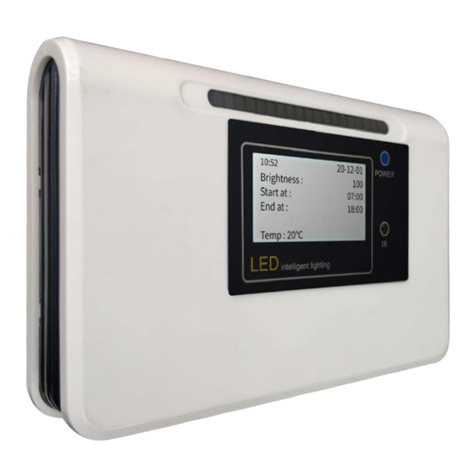
IndoorLED
IndoorLED ILCP01 instruction manual
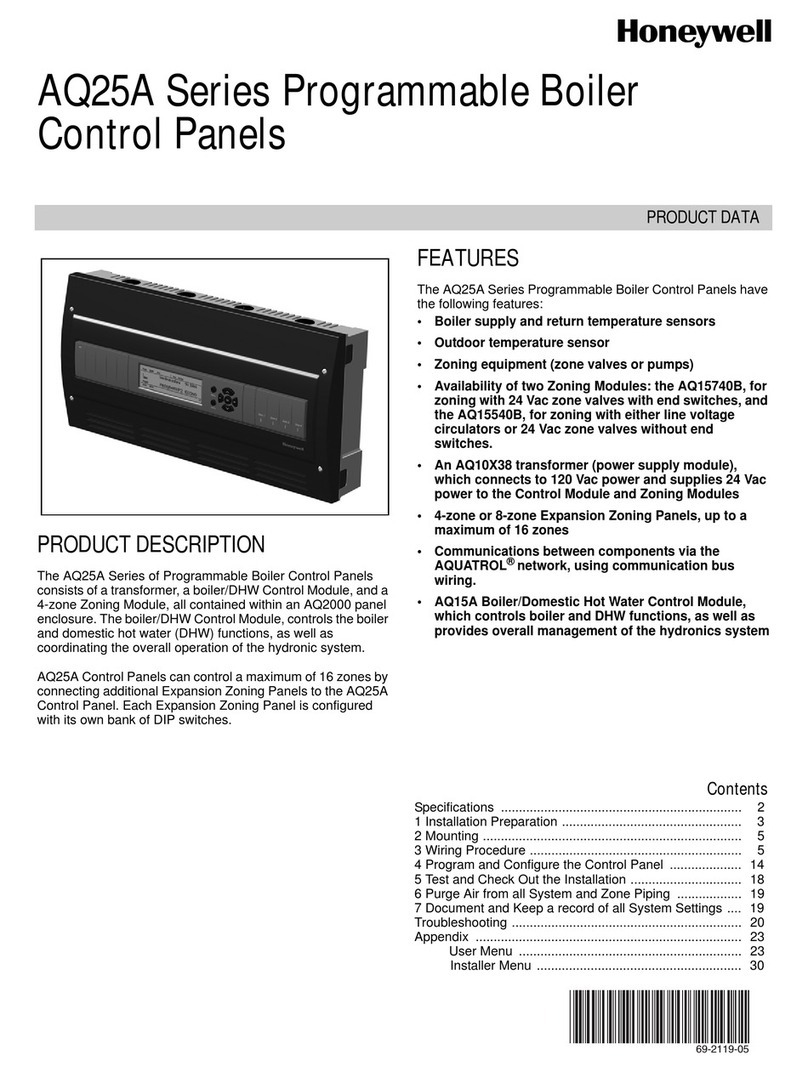
Honeywell
Honeywell AQ25A Series instruction manual