Yale MSW030-F Guide

Maintenance
MASTER DRIVE UNIT
MSW020/025-E [A895];
MSW025/030-F [B895];
MPB040-E [B827];
MPW045-E [B802];
MPW050-E [C802]
PART NO. 524154891 630 YRM 1003

SAFETY PRECAUTIONS
MAINTENANCE AND REPAIR
•When lifting parts or assemblies, make sure all slings, chains, or cables are correctly fastened, and
that the load being lifted is balanced. Make sure the crane, cables, and chains have the capacity to
support the weight of the load.
•Do not lift heavy parts by hand, use a lifting mechanism.
•Wear safety glasses.
•DISCONNECT THE BATTERY CONNECTOR before doing any maintenance or repair on electric lift
trucks. Disconnect the battery ground cable on internal combustion lift trucks.
•Always use correct blocks to prevent the unit from rolling or falling. See HOW TO PUT THE LIFT
TRUCK ON BLOCKS in the Operating Manual or the Periodic Maintenance section.
•Keep the unit clean and the working area clean and orderly.
•Use the correct tools for the job.
•Keep the tools clean and in good condition.
•Always use YALE APPROVED parts when making repairs. Replacement parts must meet or exceed
the specifications of the original equipment manufacturer.
•Make sure all nuts, bolts, snap rings, and other fastening devices are removed before using force to
remove parts.
•Always fasten a DO NOT OPERATE tag to the controls of the unit when making repairs, or if the unit
needs repairs.
•Be sure to follow the WARNING and CAUTION notes in the instructions.
•Gasoline, Liquid Petroleum Gas (LPG), Compressed Natural Gas (CNG), and Diesel fuel are
flammable. Be sure to follow the necessary safety precautions when handling these fuels and when
working on these fuel systems.
•Batteries generate flammable gas when they are being charged. Keep fire and sparks away from the
area. Make sure the area is well ventilated.
NOTE: The following symbols and words indicate safety information in this manual:
WARNING
Indicates a hazardous situation which, if not avoided, could result in death or
serious injury.
CAUTION
Indicates a hazardous situation which, if not avoided, could result in minor
or moderate injury and property damage.
On the lift truck, the WARNING symbol and word are on orange background.
The CAUTION symbol and word are on yellow background.

Master Drive Unit Table of Contents
TABLE OF CONTENTS
General................................................................................................................................................................ 1
Description .......................................................................................................................................................... 1
Special Precautions............................................................................................................................................. 1
Master Drive Unit Repair ..................................................................................................................................... 3
Remove........................................................................................................................................................... 3
Disassemble.................................................................................................................................................... 5
Repair.............................................................................................................................................................. 6
Assemble ........................................................................................................................................................ 6
Install............................................................................................................................................................... 6
Troubleshooting ................................................................................................................................................... 7
This section is for the following models:
MSW020/025-E [A895];
MSW025/030-F [B895];
MPB040-E [B827];
MPW045-E [B802];
MPW050-E [C802]
©2008 Yale Materials Handling Corp. i


630 YRM 1003 Special Precautions
General
This section has the description and repair procedures
for the master drive unit (MDU). The traction motor,
steering, and brake repair procedures are in separate
sections. The main parts of the drive unit are the hous-
ing, pinion (motor), first intermediate gear set, second
intermediate gear set, drive gear, bearings, axle, wheel,
and spindle. The spindle is bolted to the top of the drive
unit has tapered bearings installed for the mounting of
the MDU to the frame. The steering control handle fas-
tens to the MDU. The traction motor fastens to the drive
unit. The drive unit and the traction motor turn as a unit
for steering.
In some instances, it may only be necessary to remove
the drive motor and brake assembly to work on the
MDU, while in other cases, the MDU must be com-
pletely removed. Determine the extent of disassembly
required before proceeding with any repairs.
See the section Steering Mechanism 1600 YRM 1004
for troubleshooting and repairs on the steering compo-
nents.
See the section Electrical System 2200 YRM 1007
and DC Motor Maintenance 620 YRM 294 for trou-
bleshooting and repairs on the electrical components
of the MDU.
See the section Brakes 1800 YRM 1005 for trou-
bleshooting and repairs of the brake components.
See the section Periodic Maintenance 8000 YRM
1048, Periodic Maintenance 8000 YRM 1379, or Pe-
riodic Maintenance 8000 YRM 1009 for instructions
on checking and changing the drive unit gear oil.
Description
TheMDUisatriplereductiondriveunit.Thethreesets
of gears do not need adjustment for wear. All the parts
that rotate have ball bearings or tapered roller bearings.
The ball bearings are lubed by gear oil and the tapered
roller bearings are packed with multipurpose #2 grease
with 2% to 4% molybdenum disulfide. A pinion gear on
the motor armature drives the first of the three reduction
gears. The second intermediate gear engages the drive
gear. The drive gear is mounted on the drive axle. The
drive axle is the mount for the final drive gear and the
wheel.
A spring applied/electrically released friction brake is
mounted to the drive motor between the motor and the
MDU. See the section Brakes 1800 YRM 1005 for ad-
ditional information on the electrical brake.
Special Precautions
WARNING
Block each side of the truck under the drive unit
frame. Position blocks on both sides of the load
wheels to prevent the truck from falling.
WARNING
The capacitor in the transistor controller can hold
an electrical charge after the battery is discon-
nected. Discharge the capacitor before inspecting
or repairing any component in the MDU compart-
ment to prevent personal injury and damage to
the electrical system. Make certain the battery has
been disconnected. DO NOT use a screwdriver
to make a short circuit across the B+ and B
terminals of the transistor controller. Always wear
safety glasses.
WARNING
Perform the following steps before performing any
troubleshooting or adjustments, and before con-
necting or disconnecting a handset or personal
computer to avoid personal injury and prevent
electrical shock.
1. Verify that the key switch is in the OFF position and
the battery connector is completely disconnected.
1

Special Precautions 630 YRM 1003
WARNING
To avoid controller damage, always disconnect
the battery, discharge the capacitor, and never put
power to the controller with any power wire dis-
connected. Never short any controller terminal or
motor terminal to battery. Make sure to use proper
procedure when servicing the controller.
2. Discharge capacitors. Carefully connect a 200-
ohm, 2-watt resistor between B+ and B on con-
troller using insulated jumper wires and hold for 5
seconds. Remove the 200-ohm, 2-watt resistor be-
fore reconnecting the battery. See Figure 1 or Fig-
ure 2
Figure 1. Discharging Controller - MPB040-E
Legend for Figure 1
1. POSITIVE CONNECTION
2. NEGATIVE CONNECTION
3. INSULATED JUMPER WIRES
4. 200-OHM, 2-WATT RESISTOR
1. NEGATIVE CONNECTION
2. POSITIVE CONNECTION
3. 200-OHM, 2-WATT RESISTOR
4. INSULATED JUMPER WIRES
Figure 2. Discharging Controller - MSW020-E,
MSW025-E, MSW025-F, MSW030-F, MPW045-E, and
MPW050-E
2

630 YRM 1003 Master Drive Unit Repair
Master Drive Unit Repair
REMOVE
Separate parts of the MDU can be removed without re-
moving the complete MDU. It is not necessary to per-
form each step of the entire procedure to remove some
parts of the MDU. This procedure has steps to remove
the complete MDU. Read the entire procedure first and
do only the steps necessary to make the required re-
pairs.
WARNING
Block each side of the truck under the drive unit
frame. Position blocks on both sides of the load
wheels to prevent the truck from falling.
WARNING
Keep the MDU supported at all times using a sling
and an overhead hoist to avoid personal injury
when removing the MDU from the lift truck.
WARNING
Always disconnect the battery connector so that
the connector is completely free before performing
repairs. If the connector is not completely free, it
can reconnect the battery. Tag the connector - DO
NOT CONNECT.
1. Block lift truck. Raise drive wheel off floor. Refer to
the proper section for your lift truck: Periodic Main-
tenance 8000 YRM 1009, Periodic Maintenance
8000 YRM 1379, or Periodic Maintenance 8000
YRM 1048 - How to Put a Lift Truck on Blocks.
2. Turn key switch to OFF position and disconnect bat-
tery.
3. Remove the upper drive unit compartment cover.
4. Use the following procedure that applies to your lift
truck:
a. Remove the lower drive unit compartment
cover.
b. Remove the two screws securing the lower
drive unit compartment cover to the frame. Re-
move the lower drive unit compartment cover.
5. Remove the four Allen-head screws from the two
piece shield over the MDU and remove the shield.
WARNING
The capacitor in the transistor controller can hold
an electrical charge after the battery is discon-
nected. Discharge the capacitor before inspecting
or repairing any component in the MDU compart-
ment to prevent personal injury and damage to the
electrical system. Always wear safety glasses.
6. Discharge capacitors. Refer to Special Precau-
tions.
7. Remove control handle. Refer to the section Steer-
ing Mechanism 1600 YRM 1004.
8. Removedrivewheelandtireassemblybyremoving
capscrews (23) and washers (22).
CAUTION
Be careful not to damage the wiring when discon-
necting from the motor and the brake or when re-
moving the motor and the brake from the housing.
9. Remove drive motor and brake assembly and pull
the wires out of the top of the spindle (12). See the
section Brakes 1800 YRM 1005.
10. Support drive unit with sling ran through the center
of the spindle and a hoist or overhead crane.
11. Loosen bearing lockwasher by bending tab and
then remove lock nut.
12. Lower MDUfromframe.
3

Master Drive Unit Repair 630 YRM 1003
Figure 3. Drive Unit and Brake Assembly
4

630 YRM 1003 Master Drive Unit Repair
Legend for Figure 3
1. WIRE HARNESS
2. SLEEVE
3. NUT
4. LOCKWASHER
5. FLAT WASHER
6. BEARING CONE AND CUP
ASSEMBLY
7. BEARING CONE
8. BEARING CUP
9. BEARING CUP
10. BEARING CONE
11. ALLEN-HEAD SCREW
12. SPINDLE
13. O-RING
14. BALL BEARING
15. SPACER
16. BRAKE ASSEMBLY
17. BRAKE HUB
18. KEY
19. KEY
20. DRIVE MOTOR
21. PIVOT BUSHING
22. WASHER
23. CAPSCREW
24. DRIVE TIRE AND WHEEL
25. MDU
26. DRIVE AXLE
27. BEARING CONE AND SEAL
ASSEMBLY
28. BEARING CUP
29. PIN
30. DRIVE GEAR
31. NUT
32. BALL BEARING
33. GEAR AND PINION ASSEMBLY
34. GEAR AND PINION ASSEMBLY
35. NUT
36. GEAR
37. OIL SLINGER
38. CASTING
39. LOCKWASHER
40. CAPSCREW
41. FILL PLUG
42. ALLEN-HEAD SCREW
43. LOCKWASHER
44. COVER
45. ALLEN-HEAD SCREW
46. LOCKWASHER
DISASSEMBLE
Refer to Figure 3 for the following instructions.
NOTE: Total d isassembly may not be necessary to re-
pairtheMDU.Doo
nly the steps necessary to complete
repairs.
TheMDUcanberem
oved from the lift truck to be com-
pletely disassembled. See Remove. However, certain
components may be removed with the MDU installed
in the truck. The drive motor, brake, drive wheel and
tire assembly, and pivot bushing (21) may be removed
with the MDU installed on the truck. The gear oil may
also be changed with the MDU installed. Where partial
disassembly of the MDU while installed is possible, as-
sembly, cleaning, and inspection of the MDU is much
easier when completely removed. The following steps
refer to the disassembly of an MDU which has been re-
moved from the drive unit compartment. See Figure 3.
1. Remove MDU from lift truck. Refer to Remove.
2. Place the MDU on a clean workbench.
3. Detach steering spindle by removing Allen-head
screws (11) if necessary.
4. Remove pivot bushings (21) if necessary.
CAUTION
Disposal of lubricants and fluids must meet local
environmental regulations.
5. Remove cover and drain oil:
a. Remove eight capscrews (40) and lockwashers
(39).
b. Remove two Allen-head screws (42) and wash-
ers (43).
c. Using the slots provided, gently pry the top and
bottom sides of cover alternately from the MDU.
d. Remove cover and place on a clean work-
bench.
e. Remove two pins (29) from MDU housing if
necessary.
CAUTION
Use a hammer and a soft punch when removing
bearings to avoid damage to bearings and/or cast-
ing.
6. Remove drive axle and bearings:
a. Remove nut (31) and gear (30).
b. Remove drive axle.
c. Remove bearing cone and seal assembly (27).
7. Remove gear and pinion assemblies and bearings:
a. Remove gear and pinion assemblies (33, 34)
by hand.
b. Remove bearings (32) from casting and cover.
5

Master Drive Unit Repair 630 YRM 1003
REPAIR
WARNING
Cleaning solvents can be flammable and toxic and
can cause skin irritation. Wear protection when
handling solvents and always follow the recom-
mendations of the manufacturer.
Clean all of the parts of the MDU assembly thoroughly
with solvent. Inspect each part for damage and replace
any damaged or excessively worn parts. Bearings
should fit snug where they ride on the shaft. If there is
excessive play, replace the bearing and/or shaft. Check
the bearings for smooth operation. If a clean bearing
does not roll smoothly, it must be replaced. Check the
teeth on the gears and on the gear and pinion assem-
blies; see Figure 3, above. If the teeth are chipped or
show wear, they must be replaced. Inspect keys and
keyway grooves for damage. Never reuse a damaged
key. Always check the used gear oil for metallic chips
and shavings. If there are chips or shavings in the oil,
there is wear or damage in the MDU.
ASSEMBLE
Assembly of the MDU is basically the opposite of disas-
sembly. The major difference is installation of the bear-
ing assemblies. Use a bearing driver and hammer to
drive the bearings into place. Be careful not to damage
the casting with the bearing driver and make sure the
bearing is completely seated. The following instructions
refer to the assembly of new or undamaged parts in a
clean work environment.
CAUTION
Useaham
mer and proper size driver when in-
stalling bearings to avoid damage to bearings
and/or casting.
1. Install drive axle and bearings:
a. Clean and inspect the tapered roller bearings
for wear or damage. Replace as needed.
b. Grease the tapered roller bearings, using a
standard bearing packing device, with multipur-
pose #2 grease with 2% to 4% molybdenum
disulfide.
c. Install bearing cone and seal assembly (27)
into casting and properly position seals.
d. Install drive axle.
e. Install gear (30) with the flat side facing out
toward the cover. Install nut (31) and torque to
175 N•m (129 lbf ft).
2. Install gear and pinion assemblies and cover:
a. Clean and inspect the ball bearings for wear or
damage. Replace as needed.
b. Lubricate the ball bearings with gear oil.
c. Install bearings (32) into casting and cover.
d. Install gear and pinion assemblies (33, 34) by
hand.
e. Install gear case cover:
(1) Clean mounting surface of cover and
housing thoroughly to remove oil, old
sealant, and dirt.
(2) Apply Loctite 510™ around mounting
flange of cover.
(3) Install cover to housing using eight cap-
screws (40) and washers (39).
(4) Torque capscrews to 23 N•m (17 lbf ft).
3. Install steering spindle to MDU using the
Allen-head screws (11). Apply Loctite 242™ to
the Allen-head screws and torque to 23 N•m
(17 lbf ft).
INSTALL
The following steps refer to the installation of clean parts
that are new or that have been inspected and meet
specifications.
1. Support MDU with sling and hoist or overhead
crane and raise to a vertical position.
2. Clean and inspect the steer bearings for wear or
damage. Replace as needed.
3. Grease the steer bearings, using a standard bear-
ing packing device, with multipurpose #2 grease
with 2% to 4% molybdenum disulfide.
4. Install lower steer bearing on spindle.
6

630 YRM 1003 Troubleshooting
5. Raise MDU slowly and insert steer shaft through
drive frame.
6. Install upper steer bearing, flat washer, lockwasher,
lock nut, and wire guard sleeve.
7. Torque steer bearing lock nut to 54 N•m (40 lbf ft).
Loosen nut and retorque to 34 N•m (25 lbf ft).
8. Bend locking tab into slot on bearing lockwasher.
9. Feed main wire harness through the spindle.
CAUTION
Be careful not to damage the wiring when installing
the drive motor and brake assembly to the MDU.
10. Install drive motor and brake assembly to MDU. See
the section Brakes 1800 YRM 1005.
11. Mount drive wheel on axle shaft; install washers,
and wheel bolts. Torque wheel bolts to 115 N•m
(85 lbf ft).
12. Install control handle. Refer to the section Steering
Mechanism 1600 YRM 1004.
13. Remove fill plug (41) and fill MDU to correct level
with gear oil. Install fill plug and torque to 40 N•m
(30 lbf ft).
14. Install two piece shield on the MDU using the four
Allen-head screws to secure.
15. Use the following procedure that applies to your lift
truck:
a. Install the lower drive unit compartment cover.
b. Install the lower drive unit compartment cover
and install the two screws to secure the cover
to the frame.
16. Install the upper drive unit compartment cover.
17. Lower truck and connect battery. Check for proper
operation before returning to service.
Troubleshooting
PROBLEM POSSIBLE CAUSE PROCEDURE OR ACTION
Lift truck will not move. Battery not properly connected. Check electrical connections.
Battery is dead. Recharge or replace battery.
Motor not operating. Check wiring or repair motor.
Damaged gears or bearings. Replace gears or bearings.
MDU makes noise. The wrong lubricant is used. Drain incorrect lubricant and refill with
correct gear oil. Refer to Periodic
Maintenance 8000 YRM 1009, Peri-
odic Maintenance 8000 YRM 1379,
or Periodic Maintenance 8000 YRM
1048.
There is not enough lubricant. Fill with gear oil to proper level.
Dry or damaged bearings. Replace bearings.
Worn or damaged gears. Replace gears.
7

Troubleshooting 630 YRM 1003
PROBLEM POSSIBLE CAUSE PROCEDURE OR ACTION
Oil leaks. Loose case cover. Tighten case cover.
Loose fill plug.Tighten fill plug.
Worn or damagedaxleoilseal. Replace bearing cone and seal assem-
bly.
8


Yale Materials Handling Corp.
1400 Sullivan Dr., Greenville, NC 27834-2011
630 YRM 1003 3/08 (8/05)(5/03)(1/02) Printed in U.S.A.
This manual suits for next models
11
Table of contents
Popular DC Drive manuals by other brands

GFA
GFA ELEKTROMAT SE 9.20 WS-25,40 ER installation instructions
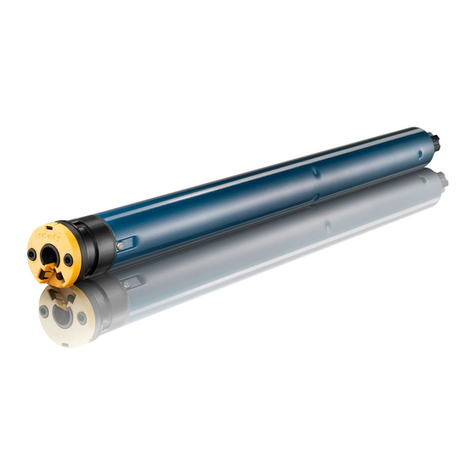
SOMFY
SOMFY Sunea 40 RTS DC instructions
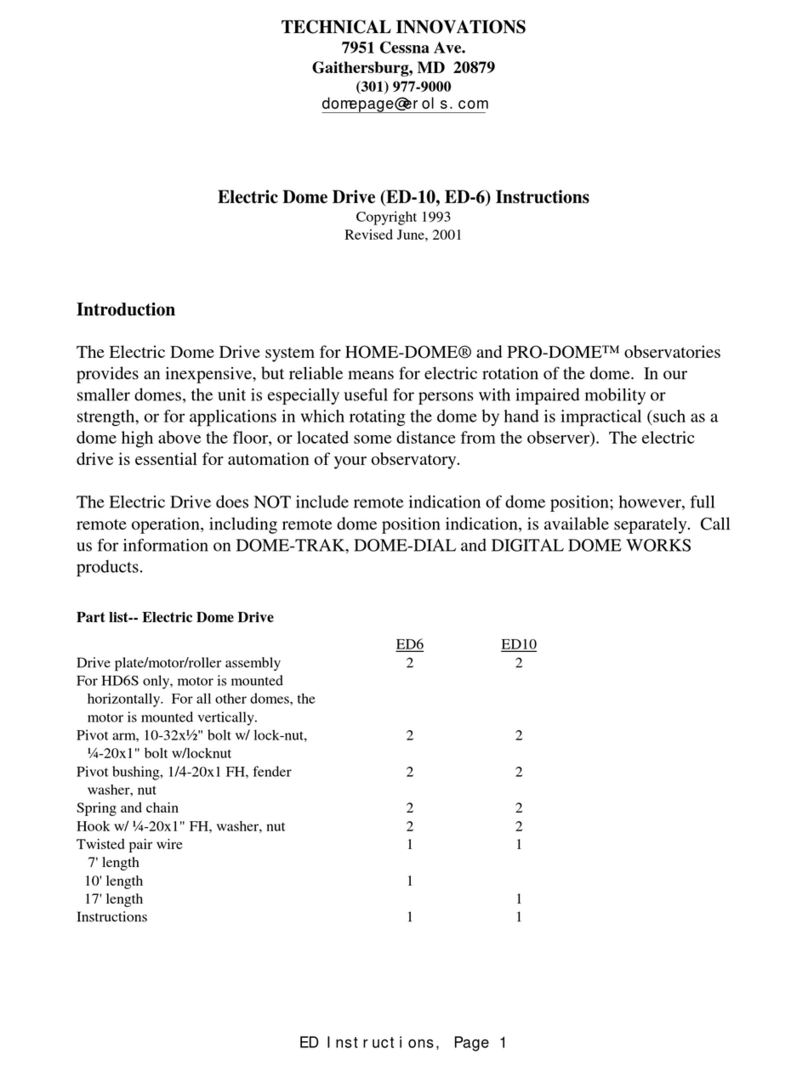
TECHNICAL INNOVATIONS
TECHNICAL INNOVATIONS ED-10 instructions

Allen-Bradley
Allen-Bradley PowerFlex 6000T Hardware Service Manual
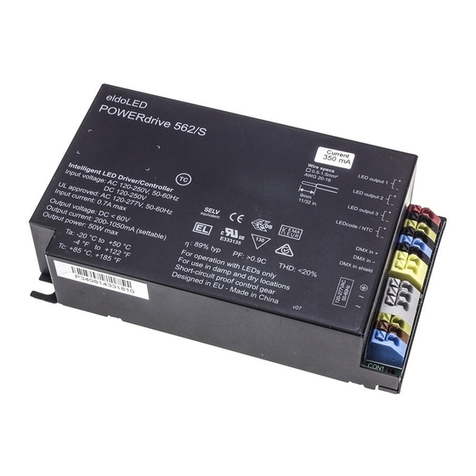
eldoLED
eldoLED POWERdrive 562/S manual

SEW-Eurodrive
SEW-Eurodrive MOVITRAC LTP-B operating instructions

RADEMACHER
RADEMACHER RolloTron Pro Star Series Installation and operation manual
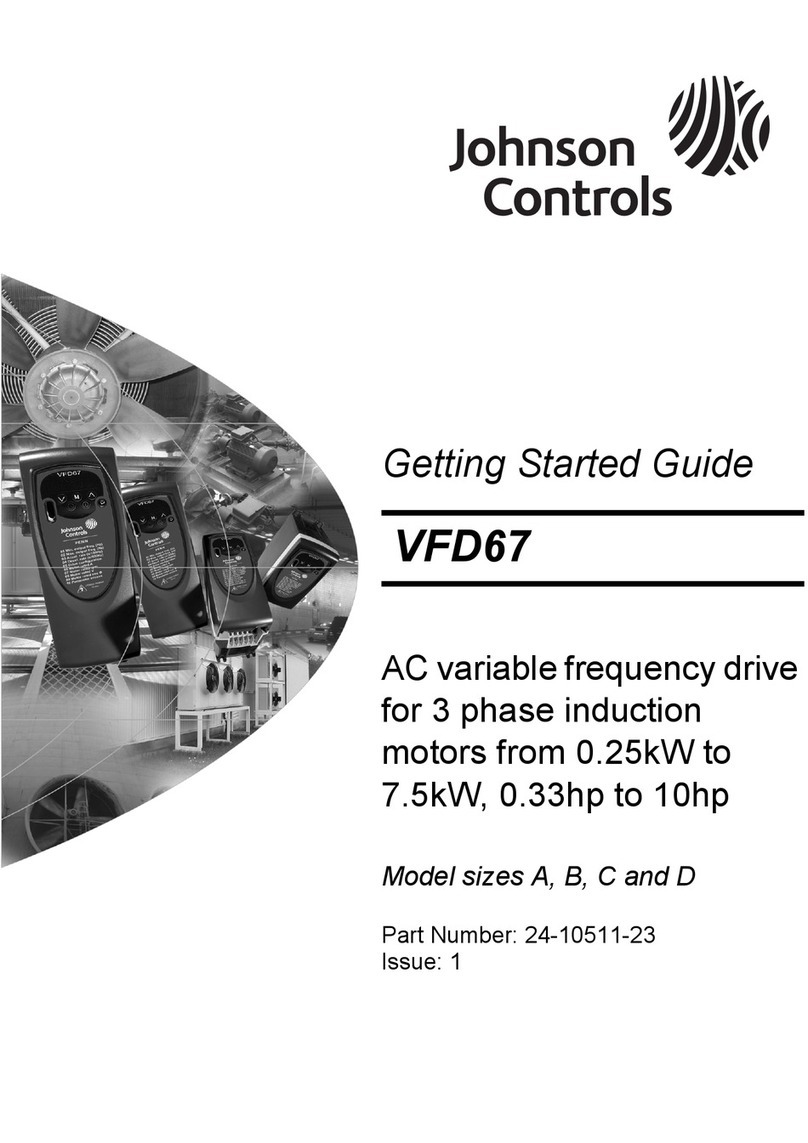
Johnson Controls
Johnson Controls VFD67 Series Getting started guide
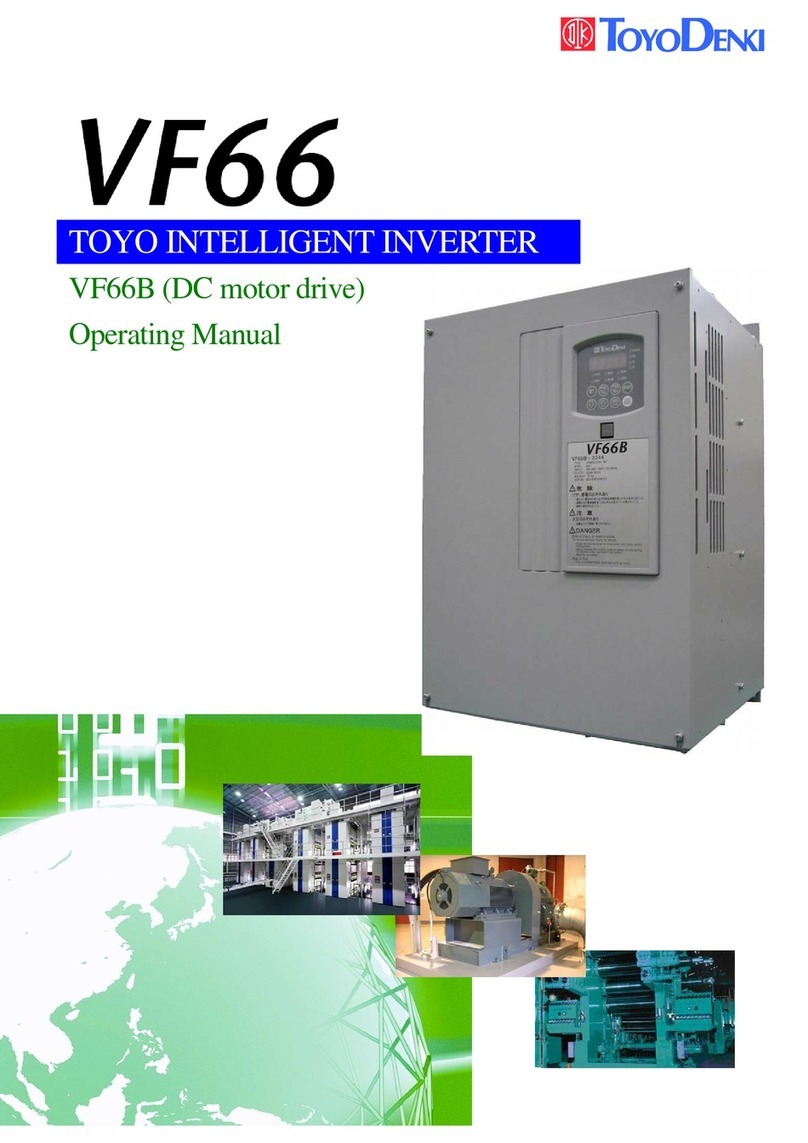
TOYODenki
TOYODenki VF66 operating manual

GFA
GFA ELEKTROMAT SI 40.15-40,00 Ex installation instructions
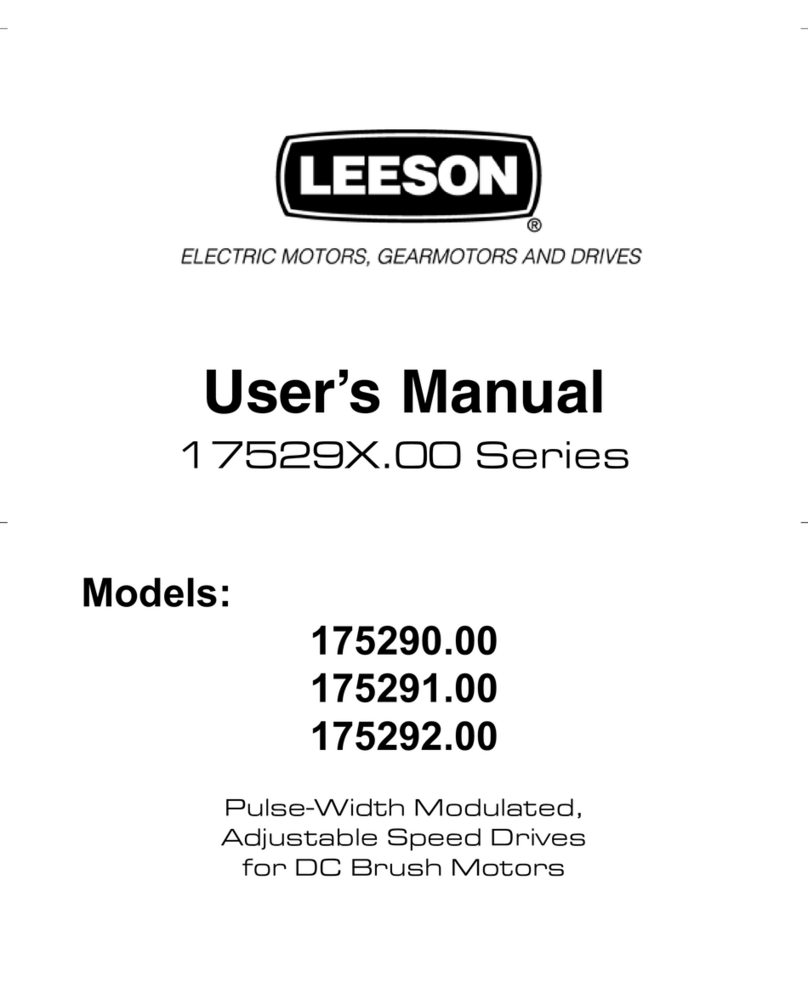
Leeson
Leeson 175290.00 user manual
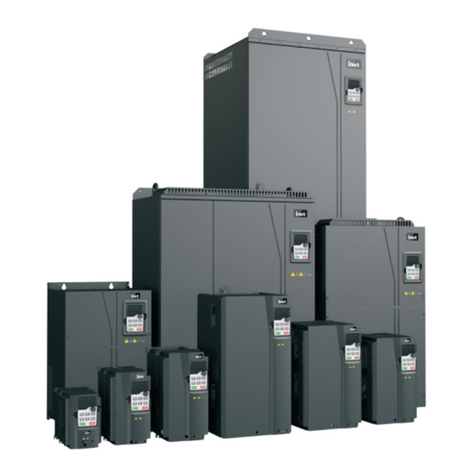
INVT
INVT Goodrive350-19 Series Operation manual