ZLTECH ZLAC8015D User manual

Shenzhen ZhongLing Technology Co.,Ltd.
Add: 8th Floor, Building 3, Qiyu Industrial City, Gongle
Tiezai Rd., Xixiang St., Bao'an Dist, Shenzhen, China
Postcode: 518102
Tel: +86-0755-2979 9302
Fax: +86-0755-2912 4283
Email: sales@zlingkj.com
Web: www.zlingkj.com
ZLAC8015D
Servo Driver Manual (Special for
Hub Servo Motor)
【Pl e as e r ea d t h e ma n u a l in d et a i l b e fo r e us e , to a v o id d am a g e t o th e dr i v e r 】

ZLAC8015 Servo Driver Manual (Special for Hub Servo Motor) V2.00 ZLAC8015 Servo Driver Manual (Special for Hub Servo Motor) V2.00
1Shenzhen ZhongLing Technology Co.,Ltd. TEL: +86-0755-29799302 FAX:+86-0755-2912 4283 WEB: www.zlingkj.com Shenzhen ZhongLing Technology Co.,Ltd. TEL: +86-0755-29799302 FAX:+86-0755-2912 4283 WEB: www.zlingkj.com 2
CONTENTS
RELEASE NOTES....................................................................................................................2
PREFACE............................................................................................................................... 3
SAFETY PRECAUTIONS......................................................................................................... 3
1. PRODUCT INTRODUCTION.........................................................................................6
1.1. OUTLINE.................................................................................................................... 6
1.2. FEATURES.................................................................................................................. 6
1.3. APPLICATION............................................................................................................ 6
2. ELECTRICAL, ENVIRONMENTAL INDEX............................................................................7
2.1. ELECTRICAL INDEX.................................................................................................... 7
2.2. ENVIROMENTAL INDEX............................................................................................ 7
2.3. INSTALLATION DIMENSION......................................................................................
8
2.4. INSTALLATION........................................................................................................... 8
3.
DRIVER INTERFACE AND WIRING.................................................................................... 9
3.1. INTERFACE DEFINITION............................................................................................
9
3.2 CONTROL SIGNAL WIRING......................................................................................11
3.3. CANOPEN COMMUNICATION PORT DESCRIPTION............................................... 13
3.4. RS485 COMMUNICATION PORT DESCRIPTION..................................................... 13
3.5. STATUS INDICATOR LED.......................................................................................... 14
RELEASE NOTES
Version
Update Time
Update Content
Updater
V2.00 2021-02-21
First Edition
DHR, LHY

ZLAC8015 Servo Driver Manual (Special for Hub Servo Motor) V2.00 ZLAC8015 Servo Driver Manual (Special for Hub Servo Motor) V2.00
3Shenzhen ZhongLing Technology Co.,Ltd. TEL: +86-0755-29799302 FAX:+86-0755-2912 4283 WEB: www.zlingkj.com Shenzhen ZhongLing Technology Co.,Ltd. TEL: +86-0755-29799302 FAX:+86-0755-2912 4283 WEB: www.zlingkj.com 4
PREFACE
Thanks for choosing ZLAC8015D, the servo driver for hub servo motor.
This manual describes the installation, debugging, maintenance, operation and
other aspects of the servo driver ZLAC8015D. Please read this manual in detail
before use, and be familiar with the safety precautions.
This manual may be revised timely when product is improved, specification and
version are changed or for some other reasons, which will not be notified
particularly.
Any questions when using our products, please read the relevant manual or call our
technical service department, we will meet your requirements in the shortest
possible time.
Marks and warning signal:
Danger: Indicates that this operation error may endanger
personal safety!
Attention: Indicates that this operation error may result in
equipment damage!
SAFETY PRECAUTIONS
Open Box and Check
Do not install integrated step-servo motor which is damaged or with
missing parts.
Installation
Installed on a non-flammable metal frame, prevent the intrusion of
dust, corrosive gases, conductive objects, liquids and flammable materials, and
maintain good heat dissipation conditions.
During installation, be sure to tighten the mounting screws of the
integrated step-servo motor. It should be protected from vibration and shock.
Wiring
Please perform the wiring work by professional electrical engineer;
Before wiring, please confirm that the input power is off. Wiring and
inspection must be performed after the power is turned off and the integrated
step-servo motor indicator is off to prevent electric shock;
When plugging and unplugging the integrated step-servo motor
terminals, make sure that its indicator is off before proceeding;
Please set the emergent stop circuit outside the controller;
Please tighten the output terminal with a suitable torque.
Electrify
Please confirm whether the main circuit input power is consistent with
the rated working voltage of the integrated step-servo motor;
Do not test the integrated step-servo motor for high voltage and
insulation resistance at will;
Do not connect the electromagnetic contactor or electromagnetic
switch to the output circuit.
Operation
Do not directly touch the output terminals after the integrated
step-servo motor is powered on;
When the system is running, the integrated step-servo motor may

ZLAC8015 Servo Driver Manual (Special for Hub Servo Motor) V2.00 ZLAC8015 Servo Driver Manual (Special for Hub Servo Motor) V2.00
5Shenzhen ZhongLing Technology Co.,Ltd. TEL: +86-0755-29799302 FAX:+86-0755-2912 4283 WEB: www.zlingkj.com Shenzhen ZhongLing Technology Co.,Ltd. TEL: +86-0755-29799302 FAX:+86-0755-2912 4283 WEB: www.zlingkj.com 6
have a high temperature rise, do not touch it;
Please confirm the input and output signals to ensure safe operation;
The alarm can be reset only after the operation signal is cut off.
Alarm resetting in the running signal state will cause the integrated step-servo
motor to restart suddenly;
Do not change the parameter settings of the integrated step-servo
motor at will. The parameter modification needs to be performed under standby
condition.
Maintenance and Inspection
Do not touch the integrated step-servo motor terminals directly, and
some have high voltage, very dangerous;
Before powering up, be sure to install the cover; when removing the
cover, be sure to cut off the power supply first;
Before wiring, please confirm whether the input power is off;
After cutting off the main circuit input power and confirming the
integrated step-servo motor indicator light has completely extinguished, it
can be inspected and maintained;
Do the inspection and maintenance by professional electrical
engineer;
Do not do wiring, disassembling or other operation on the terminals
during power on.
There is an integrated circuit on the main control board of the servo
driver. Please pay full attention when checking to avoid damage caused by
static induction.
1. PRODUCT INTRODUCTION
1.1. OUTLINE
ZLAC8015D is a high-performance digital servo driver for hub servo motor. It has a
simple structure and high integration, and adds RS485 & CANOPEN bus
communication and single-axis controller function.
1.2. FEATURES
■Adopt CAN bus communication, support CiA301 and CiA402 sub-protocol of
CANopen protocol, could mount up to 127 devices. CAN bus communication baud rate
range 25-1000Kbps, default is 500Kbps.
■Adopt RS485 bus communication, support modbus-RTU protocol, could mount up
to 127 devices. RS485 bus communication baud rate range 9600-256000Bps, default is
115200bps.
■Support operation modes such as position control, velocity control and torque
control.
■User can control the start and stop of the motor through bus communication and
query the real-time status of the motor.
■Input voltage: 24V-48VDC.
■2 isolated signal input ports, programmable, implement the driver's functions such
as enable, start stop, emergency stop and limit.
■With protect function such as over-voltage, over-current.
1.3. APPLICATION
Suitable for AGV, delivery robot, service robot, automated handling machine, etc.

ZLAC8015 Servo Driver Manual (Special for Hub Servo Motor) V2.00 ZLAC8015 Servo Driver Manual (Special for Hub Servo Motor) V2.00
7Shenzhen ZhongLing Technology Co.,Ltd. TEL: +86-0755-29799302 FAX:+86-0755-2912 4283 WEB: www.zlingkj.com Shenzhen ZhongLing Technology Co.,Ltd. TEL: +86-0755-29799302 FAX:+86-0755-2912 4283 WEB: www.zlingkj.com 8
2. ELECTRICAL, ENVIRONMENTAL INDEX
2.1. ELECTRICIAL INDEX
Driver Parameter
Min value
Typical value
Max value
Unit
Input voltage
20 VDC
36VDC
48VDC
V
Output current(peak)
0
15
30
A
Control signal input
current
7
10
16
mA
Over-voltage
protection
-
75
-
VDC
Under-voltage
protection
-
16
-
VDC
Input signal voltage
-
5
-
VDC
Insulation resistance
100
MΩ
2.2. ENVIROMENTAL INDEX
Cooling Type
Natural cooling or forced cooling
Working
environment
Application occasion
Avoid dust, oil mist and corrosive gases
Working temperature
0~50℃
Max. ambient humidity
90% RH(no condensation)
Storage temperature
-10~70℃
Vibration
10~55Hz/0.15mm
Fig.1 Installation dimension diagram (unit: cm)
2.4. INSTALLATION
User can use the wide or narrow side of the driver cooled radiator for installation. If
installing with wide side, use M3 screws to install through the holes on four corners. If
installing with narrow side, use M3 screws to install through the holes on both sides. In
order to achieve good heat dissipation, it is recommended to use narrow-side
installation.
The power device of the driver will generate heat. If it works continuously under the
condition of high input voltage and high power, the effective heat dissipation area
should be enlarged or forced cooling. Do not use it in a place where there is no air
circulation or where the ambient temperature exceeds 60 ° C. Do not install the driver
in a humid or metal debris place.
2.3. INSTALLATION DIMENSION
150
2-
4.50
10.80
15.50
76.50
81
13.25
78.75
31
97
13.30

ZLAC8015 Servo Driver Manual (Special for Hub Servo Motor) V2.00 ZLAC8015 Servo Driver Manual (Special for Hub Servo Motor) V2.00
9Shenzhen ZhongLing Technology Co.,Ltd. TEL: +86-0755-29799302 FAX:+86-0755-2912 4283 WEB: www.zlingkj.com Shenzhen ZhongLing Technology Co.,Ltd. TEL: +86-0755-29799302 FAX:+86-0755-2912 4283 WEB: www.zlingkj.com 10
3.1.1 Power wire and power supply input port of left motor
Port Pin Mark Name Function
1 DC Power supply
interface
Power supply 24V-48V
2 GND
3UMotor power
interface
Wire connected to motor
4 V
5W
3.1.2 Power wire and power supply input port of right motor
Port Pin Mark Name Function
5 GND Power supply
interface
Power supply 24V-48V
4 DC
3WMotor power
interface
Wire connected to motor
2V
1U
3.1.3 Left/Right motor's incremental encoder and hall port J2/J6
Port Pin Mark Name Function
1 iA+
Encoder
2 iA-
3 iB+
4 iB-
5 RTC+ Temperature sensor
6 RTC-
7 V Hall sensor
8 W
9 U
10 GND Power ground
11 VCC Power positive Output to encoder and
HALL
12 GND Power ground
3. DRIVER INTERFACE AND WIRING
3.1. INTERFACE DEFINITION

ZLAC8015 Servo Driver Manual (Special for Hub Servo Motor) V2.00 ZLAC8015 Servo Driver Manual (Special for Hub Servo Motor) V2.00
11 Shenzhen ZhongLing Technology Co.,Ltd. TEL: +86-0755-29799302 FAX:+86-0755-2912 4283 WEB: www.zlingkj.com Shenzhen ZhongLing Technology Co.,Ltd. TEL: +86-0755-29799302 FAX:+86-0755-2912 4283 WEB: www.zlingkj.com 12
3.1.4 Motor control signal port J3
Port Pin Mark Name Function
1BGND-L
2-BR-L
3BDC-L
4BGND-R
5-BR-R
Left brake control
6BDC-R
7OUTPUT1 Could be configured via
CAN or 485
8OUTPUT2
Internal pull up 5V output
3.1.6 Communication port J5
Port Pin Mark Name Function
1 CANH CANOPEN
3 CANL
2 A RS485
4 B
5 CANH CANOPEN
7 CANL
6 A RS485
8 B
Left brake power-
Left brake-
Left brake power+/Left brake+
Right brake power-
Right brake-
Right brake power+/Right brake+
Right brake control
3.1.5 Motor control signal port J4
Port Pin Mark Name Function
1AOUT-L
2BOUT-L
3AOUT-R
4BOUT-R
5+5V
Left motor encoder
output signal
6GND
7INPUT1 Could be configured via
CAN or 485
8INPUT2
Input signal, internally
limited 5V input
Left motor encoder A
Encoder +5V power supply
+, <100mA External power output
Left motor encoder B
Right motor encoder A
Right motor encoder B
Right motor encoder
output signal
Encoder +5V power supply -

ZLAC8015 Servo Driver Manual (Special for Hub Servo Motor) V2.00 ZLAC8015 Servo Driver Manual (Special for Hub Servo Motor) V2.00
11 Shenzhen ZhongLing Technology Co.,Ltd. TEL: +86-0755-29799302 FAX:+86-0755-2912 4283 WEB: www.zlingkj.com Shenzhen ZhongLing Technology Co.,Ltd. TEL: +86-0755-29799302 FAX:+86-0755-2912 4283 WEB: www.zlingkj.com 12
3.2 CONTROL SIGNAL WIRING
ZLAC8015D series driver provides 2 photoelectric isolation programmable input
interfaces, compatible with NPN wiring and PNP wiring.
2-channel (IN1-IN2 of J4) programmable input signal is isolated from the external
control interface by an optocoupler. The driver is compatible with common cathode
and common anode connections, as shown in the following Figure 2. In order to ensure
the reliable conduction of the optocoupler inside the driver, the drive current provided
by the controller must be at least 10mA.
The level pulse width of IN1-IN2 input needs to be bigger than 10ms, otherwise the
driver may not respond normally. The IN1-IN2 timing diagram is shown in Figure 3.
Fig.2 Input interface circuit
Fig.3 Control signal interface wiring diagram
Note: The default input voltage of the control signal is 5V. For other voltages,
current limiting resistors must be added, for example: 12V, external 1K 1 / 2W resistor;
24V, external 2K 1 / 2W resistor.
After the driver is powered on, digital Inputs defaults to the unspecified state. At this
time, the input signal is invalid. User could configure input functions through
communication.
Signal output wiring, such as alarm, in place, etc., customer could internally pull up 5V
resistance to output, or externally pull up 3.3-24V resistance to output.
Fig.4 Output interface circuit

ZLAC8015 Servo Driver Manual (Special for Hub Servo Motor) V2.00 ZLAC8015 Servo Driver Manual (Special for Hub Servo Motor) V2.00
13 Shenzhen ZhongLing Technology Co.,Ltd. TEL: +86-0755-29799302 FAX:+86-0755-2912 4283 WEB: www.zlingkj.com Shenzhen ZhongLing Technology Co.,Ltd. TEL: +86-0755-29799302 FAX:+86-0755-2912 4283 WEB: www.zlingkj.com 14
There are 2brake circuits, the schematic diagram is shown in Figure 5.
Fig.5 Output interface circuit
3.3. CANOPEN COMMUNICATION PORT DESCRIPTION
ZLAC8015D series driver provides 4PIN communication port. For pin definition,
please refer to 3.1.6 Communication Port, which includes CANH, CANL, CANH and CANL.
Note: Please use shielded twisted-pair cables for communication cable and make
ground connection to ensure stable communication.
3.4. RS485 COMMUNICATION PORT DESCRIPTION
ZLAC8015D series driver provides 8PIN communication port. For pin definition,
please refer to 3.1.6 Communication Port.
Note: Please use shielded twisted-pair cables for communication cable and
make ground connection to ensure stable communication.
3.5. STATUS INDICATOR LED
The green LED is power indicator, which is always on when the driver is powered on;. It
is off when the driver is powered off. The red LED is fault indicator. When the driver fails,
the driver will stop and prompt the corresponding fault code. The fault can be cleared
when the user powers off and restarts the power. The status indicator LED represents
different operation and fault information, as shown in the following table:
Status Situation Status indicator LED
description
Over-Voltage The power supply voltage exceeds the
maximum rated voltage. 1 Red
Under-Voltage The power supply voltage is lower than
the minimum working voltage. 2 Red
Over-Current Phase current through the motor
exceeds short-circuit between phases 3 Red
Over-Load The phase current through the motor
exceeds the set overload current 4 Red
Current
out-of-tolerance
Control current and output current are
out of tolerance 5 Red
Position
out-of-tolerance
The given position is out of tolerance
with the output position 6 Red
Speed
out-of-tolerance
The given speed and output speed are
out of tolerance 7 Red
Internal reference
error Internal fault of the driver 8 Red
Parameter reading
error EEPROM parameters read error 9 Red
HALL fault The HALL cable is not plugged in or the
signal is incorrect 10 Red
High motor
temperature Motor temperature is too high 11 Red
Table of contents
Other ZLTECH Servo Drive manuals
Popular Servo Drive manuals by other brands
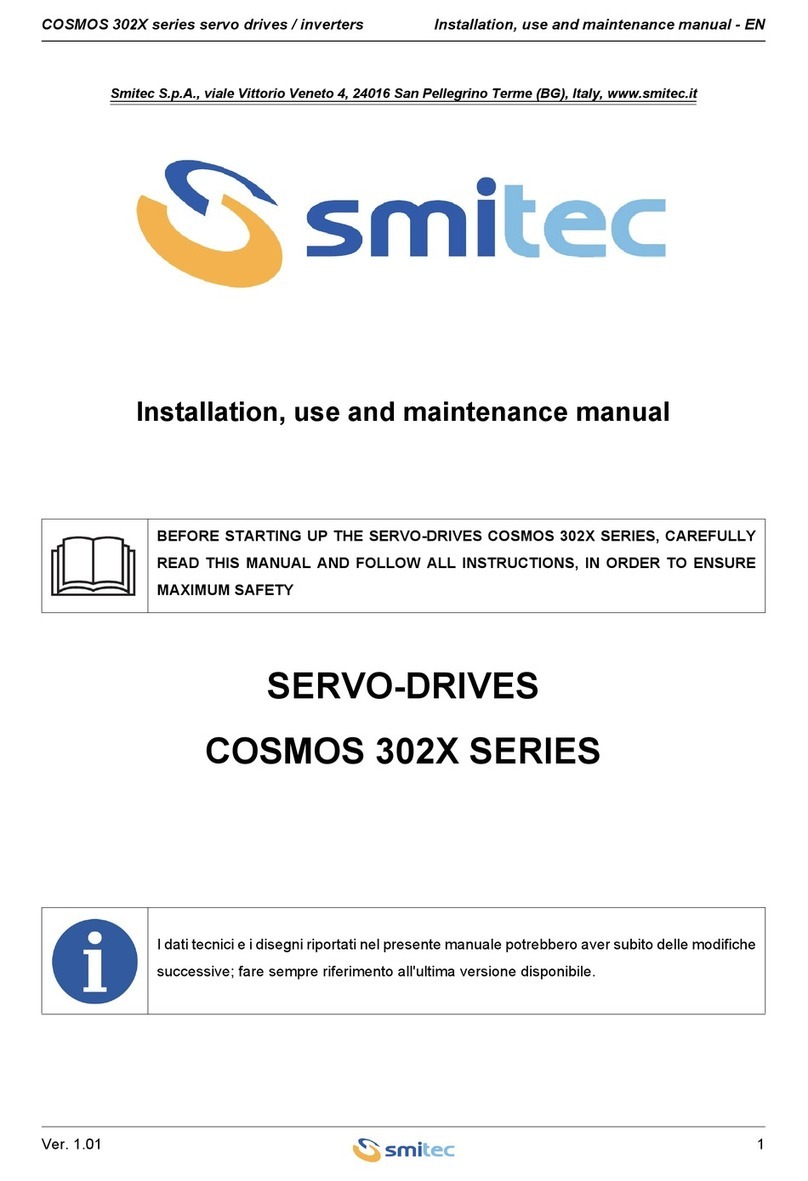
Smitec
Smitec COSMOS 302 Series Installation, use and maintenance manual
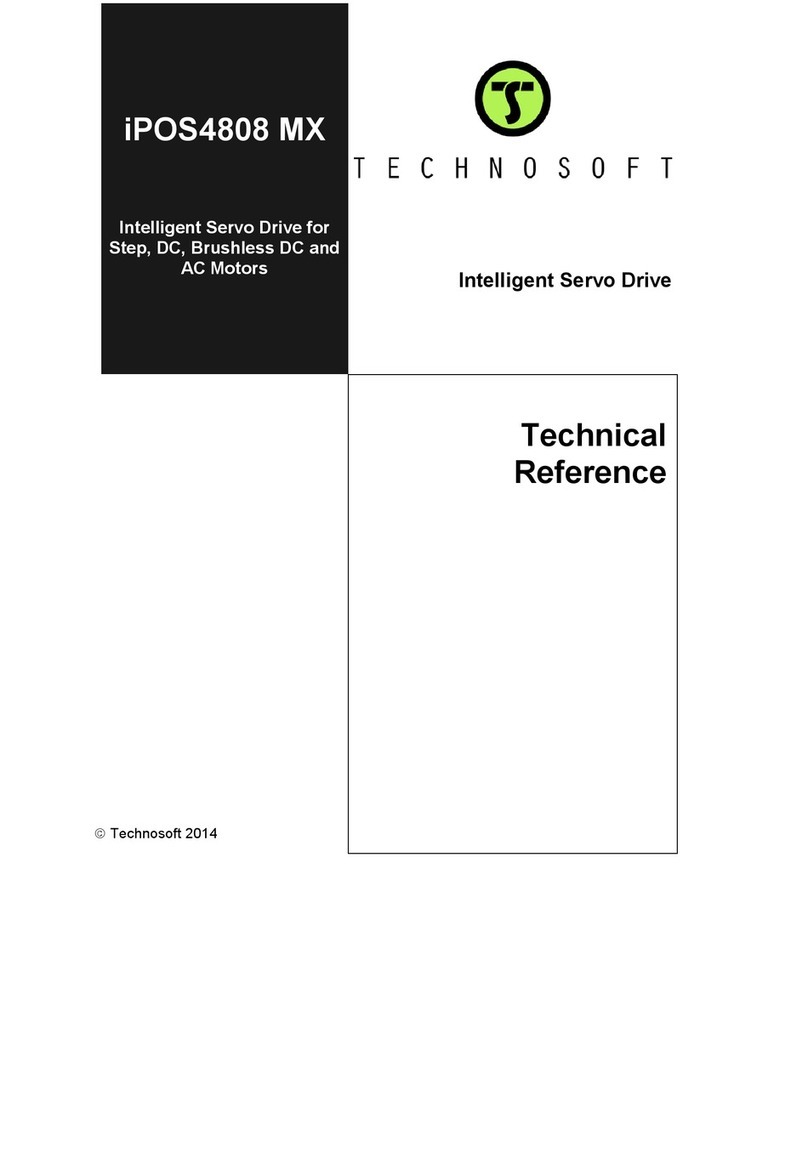
Technosoft
Technosoft iPOS4808 MX Series Technical reference
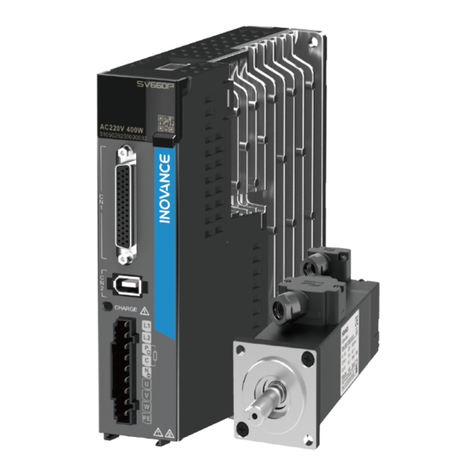
Inovance
Inovance SV660P Series Hardware guide
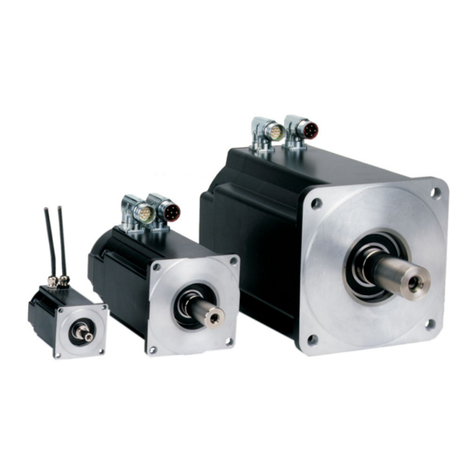
Beckhoff
Beckhoff AM3000 Series Technical description, Installation, Setup
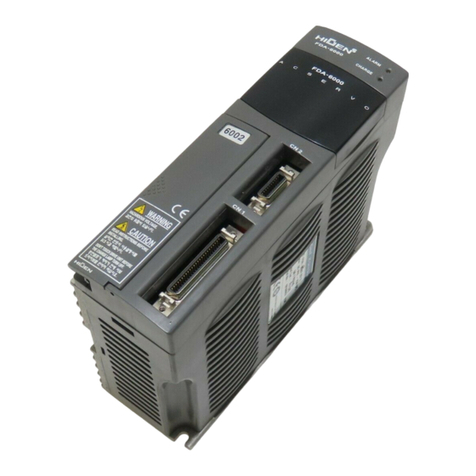
Higen
Higen FDA6000C Series user manual
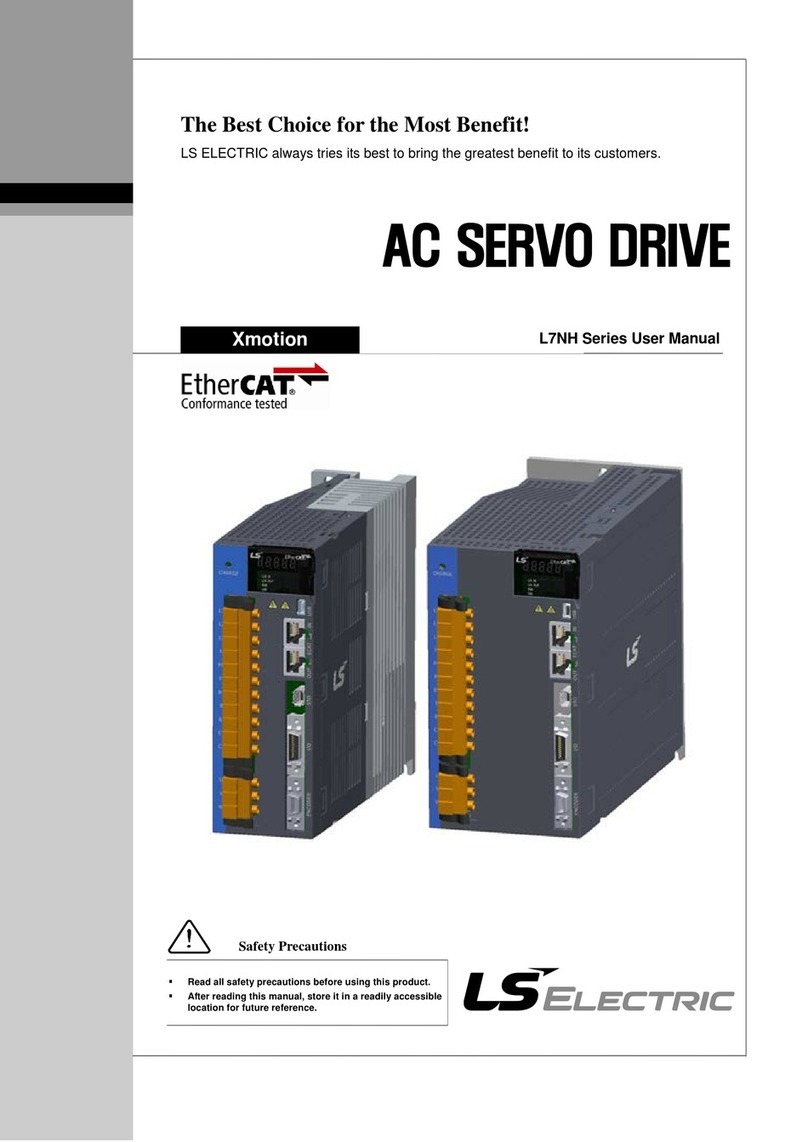
LS ELECTRIC
LS ELECTRIC L7NH Series user manual