AB Quality GuardPLC 1600 User manual

Publication 1753-IN001B-EN-P - March 2004
Installation Instructions
GuardPLC™ 1600 Controllers
(Catalog Numbers 1753-L28BBB-M and 1753-L28BBB-P)
Inside…............................................................................................page
Related Documentation ............................................................................3
Description................................................................................................4
European Communities (EC) Directive Compliance ..................................4
General Safety ..........................................................................................5
Mounting...................................................................................................5
Connecting the GuardPLC 1600 ................................................................6
Reset Pushbutton......................................................................................7
Wiring the GuardPLC 1600 .......................................................................8
Controller Tests.......................................................................................15
Troubleshooting with LED Indicators......................................................16
Specifications .........................................................................................18

2GuardPLC™ 1600 Controllers
Publication 1753-IN001B-EN-P - March 2004
Important User Information
Solid state equipment has operational characteristics differing from those of electromechanical equipment.
Safety Guidelines for the Application, Installation and Maintenance of Solid State Controls (Publication
SGI-1.1 available from your local Rockwell Automation sales office or online at
http://www.ab.com/manuals/gi) describes some important differences between solid state equipment and
hard-wired electromechanical devices. Because of this difference, and also because of the wide variety of
uses for solid state equipment, all persons responsible for applying this equipment must satisfy themselves
that each intended application of this equipment is acceptable.
In no event will Rockwell Automation, Inc. be responsible or liable for indirect or consequential damages
resulting from the use or application of this equipment.
The examples and diagrams in this manual are included solely for illustrative purposes. Because of the many
variables and requirements associated with any particular installation, Rockwell Automation, Inc. cannot
assume responsibility or liability for actual use based on the examples and diagrams.
No patent liability is assumed by Rockwell Automation, Inc. with respect to use of information, circuits,
equipment, or software described in this manual.
Reproduction of the contents of this manual, in whole or in part, without written permission of Rockwell
Automation, Inc. is prohibited.
Throughout this manual we use notes to make you aware of safety considerations.
WARNING Identifies information about practices or circumstances that can cause an explosion in a
hazardous environment, which may lead to personal injury or death, property damage,
or economic loss.
IMPORTANT Identifies information that is critical for successful application and understanding of the
product.
ATTENTION Identifies information about practices or circumstances that can lead to personal injury
or death, property damage, or economic loss. Attentions help you:
•identify a hazard
•avoid a hazard
•recognize the consequence

GuardPLC™ 1600 Controllers 3
Publication 1753-IN001B-EN-P - March 2004
Related Documentation
The table below provides a listing of publications that contain important
information about GuardPLC systems.
If you would like a manual, you can:
•download a free electronic version from the internet at
www.theautomationbookstore.com
•purchase a printed manual by:
–contacting your local distributor or Rockwell Automation representative
–visiting www.theautomationbookstore.com and placing your order
–calling 1.800.963.9548 (USA/Canada) or 001.330.725.1574 (Outside
USA/Canada)
For Read this document Publication
number
Detailed information regarding the safety certification
of the GuardPLC System.
GuardPLC Systems Safety
Reference Manual
1755-RM001
Detailed information on installing, wiring, configuring,
operating, maintaining, and troubleshooting GuardPLC
systems.
GuardPLC Systems User Manual 1753-UM001
Information on installing GuardPLC 1800 controllers GuardPLC 1800 Controller
Installation Instructions
1753-IN002
Information on installing GuardPLC 1753-IB20XOB8
Digital I/O Module
GuardPLC Digital I/O Module
Installation Instructions
1753-IN003
Information on installing GuardPLC 1753-IB16 Digital
Input Module
GuardPLC Digital Input Module
Installation Instructions
1753-IN004
Information on installing GuardPLC 1753-OB16 Digital
Output Module
GuardPLC Digital Output Module
Installation Instructions
1753-IN005
IMPORTANT For planning information, see the Industrial Automation Wiring
and Grounding Guidelines, publication 1770-4.1.

4GuardPLC™ 1600 Controllers
Publication 1753-IN001B-EN-P - March 2004
Description
The GuardPLC 1600 is a Programmable Electronic System featuring 20 digital inputs
and 8 digital outputs and 4 connections for GuardPLC Ethernet communications, as
shown below.
European Communities (EC) Directive Compliance
If this product has the CE mark it is approved for installation within the European
Union and EEA regions. It has been designed and tested to meet the following
directives.
EMC Directive
This product is tested to meet the Council Directive 89/336/EEC Electromagnetic
Compatibility (EMC) by applying the following standards, in whole or in part:
•EN 50081-2 EMC — Generic Emission Standard, Part 2 — Industrial
Environment
•EN 50082-2 EMC — Generic Immunity Standard, Part 2 — Industrial
Environment
•EN 61131-2 — Programmable Controllers, Part 2 — Equipment
Requirements and Tests
•EN 61000-6-2 EMC — Part 6-2, Generic Standards — Immunity for Industrial
Environments
This product is intended for use in an industrial environment.
Digital Outputs
Digital Inputs
Voltage Supply
Connection
Ethernet Ports (on top of controller)
Ethernet Ports (on bottom of controller)

GuardPLC™ 1600 Controllers 5
Publication 1753-IN001B-EN-P - March 2004
Low Voltage Directive
The power supply of the GuardPLC controller must meet Council Directive
73/23/EEC Low Voltage, by applying the requirements of EN 61131-2
Programmable Controllers, Part 2 - Equipment Requirements and Tests, as well as
either of the following:
•EN 60950 - SELV (Safety Extra Low Voltage)
•EN 60204 - PELV (Protective Extra Low Voltage)
General Safety
Open-style devices must be provided with environmental and safety protection by
proper mounting in enclosures designed for specific application conditions. See
NEMA standards publication 250 and IEC publication 60529, as applicable, for
explanations of the degrees of protection provided by different types of enclosures.
Mounting
The GuardPLC 1600 cannot be panel-mounted. Mount the GuardPLC 1600
controller to a DIN rail by following the four steps below.
1. Hook the top slot over the DIN rail.
2. Insert a flathead screwdriver into the
gap between the housing and the latch
and pull the latch downward.
3. Hold the latch down as you push the
housing back onto the DIN rail.
IMPORTANT For effective cooling:
•Mount the controller horizontally.
•Provide a gap of at least 100 mm (3.94 in.) above and below
the controller.
•Select a location where air flows freely or use an additional
fan.
•Do not mount the controller over a heating device.
DIN Rail
(1) Top Slot
Latch
(3)
(2)

6GuardPLC™ 1600 Controllers
Publication 1753-IN001B-EN-P - March 2004
4. Release the latch to lock the device onto the rail.
Connecting the GuardPLC 1600
Connections for Safety-Related Communications
The controller has four 10/100BaseT, RJ-45 connectors to provide communications
via GuardPLC Ethernet to distributed I/O and other GuardPLC controllers, OLE for
Process Control (OPC) servers, and with the programming software. Connectors 1
and 2 are located on the bottom side on the left. Connectors 3 and 4 are located on
the top side on the left. All four connectors and the GuardPLC processor are
connected together by an internal Ethernet switch. The switches are auto-detect.
Either cross-over or straight-through Ethernet cabling can be used.
Star or line configurations are available. Make sure that a network loop is not
generated. Data packets must only be able to reach a node via a single path.
OPC Server
The GuardPLC 1600 is an OPC client. An OPC server, catalog number 1753-OPC, is
available from Rockwell Automation and allows PC applications to read and write
data to and from the GuardPLC.
MAC Address
The Media Access Control (MAC) Address of the controller can be found on the
label positioned over both lower RJ-45 connections.
Connections for Non-Safety-Related Communications
Three 9-pin D-shell connectors are located on the front of the controller, providing
the following communications:
TIP To remove the controller from the DIN rail, insert a flathead
screwdriver into the gap between the housing and the latch
and pull the latch downward as you lift the controller off of
the rail.
Designation Function
COMM1 (RS-485) Modbus Slave (1753-L28BBB-M)
Profibus-DP-Slave (1753-L28BBB-P)
COMM2 Not Used
COMM3 (RS-485) GuardPLC ASCII Protocol

GuardPLC™ 1600 Controllers 7
Publication 1753-IN001B-EN-P - March 2004
Pin Assignments of D-shell Connector
The pin assignments of the D-shell connector are as follows:
IP Address and System ID (SRS)
A transparent label provided with the controller can be used to note the IP Address
and system ID (SRS). The default value for the IP Address is 192.168.0.99. The
default SRS is 60000. Do not cover the ventilation slots when attaching the label to
the controller housing.
Reset Pushbutton
The controller is equipped with a reset pushbutton. Reset via the pushbutton is
necessary if you forget the password for the programming software. The
pushbutton is accessible through a small round hole at the top of the housing,
approximately 4 to 5 cm (1.6 to 2.0 in.) from the left rim and recessed
approximately 9.5 mm (0.375 in.).
To reset, press and hold the pushbutton for 20 seconds while rebooting the
controller by cycling power. Pressing the Reset pushbutton during operation has no
affect.
During reset:
•all accounts are deleted, except the default “Administrator” account
•IP address and system ID (SRS) are set to their default values
Connection Signal Function
1——
2 RP 5V, decoupled with diodes
3 RxD/TxD-A Receive/Transmit data A
4 CNTR-A Control signal A
5 DGND Data reference potential
6 VP 5V, positive pole of supply voltage
7——
8 RxD/TxD-B Receive/Transmit data B
9 CNTR-B Control signal B
IMPORTANT Activate the reset pushbutton using an insulated pin to prevent
short-circuits.

8GuardPLC™ 1600 Controllers
Publication 1753-IN001B-EN-P - March 2004
Wiring the GuardPLC 1600
Preventing Electrostatic Discharge
Grounding
The controller is grounded through its DIN rail connection and through a separate
grounding screw, located on the upper left of the housing and marked with the
grounding symbol . To improve EMC conditions, ground the housing. Keep
connection to earth ground as short as possible.
You must also provide an acceptable grounding path for each device in your
application. For more information on proper grounding guidelines, refer to the
Industrial Automation Wiring and Grounding Guidelines, publication number
1770-4.1.
Connecting the Voltage Supply
The 24V dc voltage supply must feature galvanic isolation (in accordance with
EN 60950 or UL 1950) since inputs and outputs are not electrically isolated from the
processor. It must also meet the requirements of the Safety Extra Low Voltage
(SELV – EN 60950) and Protective Extra Low Voltage (PELV – EN 60204) guidelines.
ATTENTION Electrostatic discharge can damage integrated circuits or
semiconductors. Follow these guidelines when you handle the
module:
•Touch a grounded object to discharge static potential.
•Wear an approved wrist-strap grounding device.
•If available, use a static-safe workstation.
•When not in use, keep the GuardPLC controller in its
static-shield box.
IMPORTANT Protect the controller with a slow-blowing fuse.
IMPORTANT The GuardPLC 1600 can draw up to 8A. 0.5A is needed to operate
the controllers. Up to 7.5A can be used to source voltage power
for inputs and outputs connected to the 1600.

GuardPLC™ 1600 Controllers 9
Publication 1753-IN001B-EN-P - March 2004
The supply voltage is connected via a 4-pin connector which accommodates wire
sizes up to 2.5 mm2(14 AWG). You only need to connect one wire to L+ and one
wire to L-. Both L+ and L- terminals are internally connected, so you can
daisy-chain 24V dc power from the GuardPLC to other devices in the panel using
the remaining terminal.
Safety-Related Digital Inputs
The controller has 20 digital inputs whose status is indicated via LEDs when the
controller is in RUN mode.
LS+ is a voltage source that provides 24V dc for a group of four dry contact inputs.
There are five groups on the GuardPLC 1600.
ATTENTION Do not reverse the L+ and L- terminals or damage to the controller
will result. There is no reverse polarity protection.
123456
1234
1L-
L-L- L+ L+ L-DO 2 (2A)
34
1LS+- LS+ LS+ LS+ LS+L-
D1 234
56
13 14 15 16 17 18
5L-
D1 678
19 20 21 22 23 24
9L-
D1 10 11 12
25 26 27 28 29 30
13 L-
D1 14 15 16
31 32 33 34 35 36
17 L-
D1 18 19 20
37 38 39 40 41 42
19 20 21 22 23 2413 14 15 16 23 24 25 26 27 28 29 30 31 32 33 34 35 36 37 38 39 40 41 42
789101112
78910
5L- L-DO 6 (2A)
7 8
11 12
COMM1
MODBUS
RS-485
24V DC
COMM2 COMM3 RUN
24 V DC
GuardPLC Ethernet
10/100 BaseT
PROG
ERROR
FAULT
FORCE
BL
OSL
PROFIBUS
3(—) 4
(—)
3(—) 4
(—)
1753-L28BBBM
20 DC Inputs
8 DC Outputs
1LS+- L-
D1 234
13 14 15 16 17 18
13 14 15 16 23 24
L-L- L+ L+
24V DC
24V dc
Power
Supply
COM
+
Connection of Voltage Supply to
Input Device

10 GuardPLC™ 1600 Controllers
Publication 1753-IN001B-EN-P - March 2004
If devices require 24V dc to operate and use the same power source as the
GuardPLC, then wire the outputs of the device directly to inputs on the GuardPLC.
Devices with their own dedicated power supply can also be connected. Connect
the reference pole of the external power supply to the L- reference pole of the
input.
The safe state of an input is indicated by a 0 signal being passed to the user
program logic. If the test routines detect a fault in the digital inputs, a 0-signal is
processed in the user program for the defective channel. When a fault occurs, the
inputs are switched off (0).
123456
1234
1L-
L-L- L+ L+ L-DO 2 (2A)
34
1LS+- LS+ LS+ LS+ LS+L-
D1 234
56
13 14 15 16 17 18
5L-
D1 678
19 20 21 22 23 24
9L-
D1 10 11 12
25 26 27 28 29 30
13 L-
D1 14 15 16
31 32 33 34 35 36
17 L-
D1 18 19 20
37 38 39 40 41 42
19 20 21 22 23 2413 14 15 16 23 24 25 26 27 28 29 30 31 32 33 34 35 36 37 38 39 40 41 42
789101112
78910
5L- L-DO 6 (2A)
7 8
11 12
COMM1
MODBUS
RS-485
24V DC
COMM2 COMM3 RUN
24 V DC
GuardPLC Ethernet
10/100 BaseT
PROG
ERROR
FAULT
FORCE
BL
OSL
PROFIBUS
3(—) 4
(—)
3(—) 4
(—)
1753-L28BBBM
20 DC Inputs
8 DC Outputs
1LS+- L-
D1 234
13 14 15 16 17 18
13 14 15 16 23 24
L-L- L+ L+
24V DC
COM
24V dc
Power
Supply
COM
+
+
Light Curtain
(or any Safety Input)
Connection of Voltage Supply to
Input Device
123456
1234
1L-
L-L- L+ L+ L-DO 2 (2A)
34
1LS+- LS+ LS+ LS+ LS+L-
D1 234
56
13 14 15 16 17 18
5L-
D1 678
19 20 21 22 23 24
9L-
D1 10 11 12
25 26 27 28 29 30
13 L-
D1 14 15 16
31 32 33 34 35 36
17 L-
D1 18 19 20
37 38 39 40 41 42
19 20 21 22 23 2413 14 15 16 23 24 25 26 27 28 29 30 31 32 33 34 35 36 37 38 39 40 41 42
789101112
78910
5L- L-DO 6 (2A)
7 8
11 12
COMM1
MODBUS
RS-485
24V DC
COMM2 COMM3 RUN
24 V DC
GuardPLC Ethernet
10/100 BaseT
PROG
ERROR
FAULT
FORCE
BL
OSL
PROFIBUS
3(—) 4
(—)
3(—) 4
(—)
1753-L28BBBM
20 DC Inputs
8 DC Outputs
1LS+- L-
D1 234
13 14 15 16 17 18
13 14 15 16 23 24
L-L- L+ L+
24V DC
24V dc
Power
Supply
COMCOM
+
24V dc
Power
Supply
COM
+
+
Light Curtain
(or any Safety Input)
Connection of Devices with Dedicated Power Supplies

GuardPLC™ 1600 Controllers 11
Publication 1753-IN001B-EN-P - March 2004
Follow the closed-circuit principle for external wiring when connecting sensors. To
create a safe state in the event of a fault, the input signals revert to the de-energized
state (0). The “FAULT” LED activates.
Digital Input Terminals
Terminals accommodate wires up to 1.5 mm2(16 AWG). Digital inputs are
connected to the following terminals:
TIP For more information on input wiring, see the GuardPLC™
System User Manual, publication number 1753-UM001.
Terminal Number Designation Function
13 LS+ Sensor supply for inputs 1 to 4
14 1 Digital input 1
15 2 Digital input 2
16 3 Digital input 3
17 4 Digital input 4
18 L- Reference pole
19 LS+ Sensor supply for inputs 5 to 8
20 5 Digital input 5
21 6 Digital input 6
22 7 Digital input 7
23 8 Digital input 8
24 L- Reference pole
25 LS+ Sensor supply for inputs 9 to 12
26 9 Digital input 9
27 10 Digital input 10
28 11 Digital input 11
29 12 Digital input 12
30 L- Reference pole
1LS+- LS+ LS+ LS+ LS+L-
DI
234
13 14 15 16 17 18
5L-
DI
678
19 20 21 22 23 24
9L-
DI
10 11 12
25 26 27 28 29 30
13 L-
DI
14 15 16
31 32 33 34 35 36
17 L-
DI
18 19 20
37 38 39 40 41 42
19 20 21 22 23 2413 14 15 16 17 18 25 26 27 28 29 30 31 32 33 34 35 36 37 38 39 40 41 42

12 GuardPLC™ 1600 Controllers
Publication 1753-IN001B-EN-P - March 2004
LS+, not L+, should be used for short-circuit protection. Each LS+ features individual
short-circuit and EMC protection that make it important to use LS+ for only it’s four
related inputs.
Line Control
Line control is a short-circuit and line break monitoring system (e.g., E-Stop inputs)
which can be configured for the GuardPLC system. Up to 8 digital outputs (DO1 to
DO8) can be configured as pulsed outputs. The example below shows 2 pulse
outputs connected to the digital inputs (DI) of the same system. As a result, the
connections to the digital inputs (DI) are monitored.
31 LS+ Sensor supply for inputs 13 to 16
32 13 Digital input13
33 14 Digital input 14
34 15 Digital input 15
35 16 Digital input 16
36 L- Reference pole
37 LS+ Sensor supply for inputs 17 to 20
38 17 Digital input 17
39 18 Digital input 18
40 19 Digital input 19
41 20 Digital input 20
42 L- Reference pole
Terminal Number Designation Function
Emergency OFF 1 Emergency OFF 2
DO 1 2
DI 1 2 DI 3 4

GuardPLC™ 1600 Controllers 13
Publication 1753-IN001B-EN-P - March 2004
When the following occurs, inputs are set to 0, a fault code is generated, and the
FAULT LED is on.
•short-circuit between two parallel connections
•reversal of two connections
•earth fault on one of the lines (only with earthed reference pole)
•line break or opening of the contacts (e.g., when one of the E-stop off
switches is pressed in the example above), the FAULT LED is on and the
fault code is generated.
Safety-Related Digital Outputs
The controller has 8 digital outputs (DO1 to DO8) whose status is indicated via
LEDs.
An output is in a safe state when it is de-energized. When a fault occurs, all outputs
are switched off.
Outputs 1 to 3 and 5 to 7 can have a load of 0.5A at an ambient temperature of
60°C (140°F). Outputs 4 and 8 can each have a load of 1A or up to 2A at an
ambient temperature of 50°C (122°F).
With an overload, one or all of the outputs are turned off. When the overload is
eliminated, the outputs are activated again according to the specified value.
Although the external line of an output is not monitored, a short-circuit will be
indicated.
IMPORTANT For information on how to configure inputs and outputs for line
control, see the GuardPLC™ System User Manual, publication
number 1753-UM001.

14 GuardPLC™ 1600 Controllers
Publication 1753-IN001B-EN-P - March 2004
Digital Output Terminals
Terminals accommodate wires up to 1.5 mm2(16 AWG). Digital outputs are
connected to the following terminals:
For connection of a load, the reference pole L- of the concerned channel group
must be used (2-pole connection). Although L- at terminals 1 and 6 and at 7 and 12
is connected internally to L- on the power supply input, it is strictly recommended
to use 1 and 6 for outputs 1 through 4 only and 7 and 12 for outputs 5 through 8
only. EMC testing was performed in this manner.
Terminal Number Designation Function Current
1 L- Reference pole —
2 1 Digital output 1 0.5 A
3 2 Digital output 2 0.5 A
4 3 Digital output 3 0.5 A
5 4 Digital output 4 (for increased load) 2.0 A
6 L- Reference pole —
7 L- Reference pole —
8 5 Digital output 5 0.5 A
9 6 Digital output 6 0.5 A
10 7 Digital output 7 0.5 A
11 8 Digital output 8 (for increased load) 2.0 A
12 L- Reference pole —
123456
1234
1L- L-DO 2 (2A)
34
56
789101112
78910
5L- L-DO 6 (2A)
7 8
11 12

GuardPLC™ 1600 Controllers 15
Publication 1753-IN001B-EN-P - March 2004
Example: Connecting Actuators to the Outputs
The digital outputs can be pulsed with the safety-related digital inputs of the same
device. This enables short-circuit or line break monitoring to be carried out (e.g.
EMERGENCY STOP buttons to conform to Cat. 4 in EN954-1).
Controller Tests
In addition to the tests for safety, the controller tests the supply voltage and
controller temperature.
Supply Voltage Tests
The supply voltage (24V dc) is monitored and the alarm and system shutdown are
controlled according to the voltage levels listed below.
TIP Inductive loads can be connected without a protection diode on
the load. However, Rockwell Automation strongly recommends
that a protection diode be fitted directly to the load to suppress
any interference voltage. A 1N4004 diode is recommended.
ATTENTION Pulse outputs may not be used as safety related outputs.
TIP For more information on output wiring, see the GuardPLC™
System User Manual, publication number 1753-UM001.
Voltage Level System Condition
19.3 to 28.8V Normal
< 19.3V alarm state 1 (internal variables are written)
< 15.4V alarm state 2 (prepares for shutdown)
< 13.0V switched off
DO 1
DO 2
DO 3
DO 4
L-
L-

16 GuardPLC™ 1600 Controllers
Publication 1753-IN001B-EN-P - March 2004
Temperature Tests
The temperature of the controller is automatically and continuously monitored. The
alarm is triggered by the temperature conditions described in the table below.
Troubleshooting with LED Indicators
Operating Temperature Alarm
< 60°C (140°F) None (normal)
60° C to 70°C (140°F to 158°F) Warning ON
> 70°C (158°F) Main Alarm ON
return to 64°C to 54°C (147.2°F to 129.2°F) Main Alarm OFF, Warning ON
return to < 54°C (129.2°F) None (return to normal)
Indicator State Condition
24V dc On 24V dc operating voltage present.
Off No operating voltage.
RUN On This is the normal status of the controller.
A routine, which has been loaded into the controller, is executed.
The controller processes input and output signals, carries out communication and
performs hardware and software tests.
Flashing The controller is in STOP mode and is not executing a routine.
All system outputs are reset.
STOP mode can be triggered by setting the Emergency stop system variable to TRUE
in the routine, or by direct command from the programming software.
Off The controller is in ERROR_STOP (see ERROR).
ERROR On •A hardware error has been detected by the controller. The controller goes to
ERROR_STOP and the execution of the routine is halted. Hardware errors are
errors in the controller, errors in one or more of the digital input and output
modules, or errors in the counters.
•A software error in the operating system has been detected by the controller.
•The watchdog has reported an error due to exceeded cycle time.
All system outputs will be reset and the controller ceases all hardware and software
tests. The controller can only be restarted by a command from the programming
software.
Off No errors are detected.
PROGress On The upload of a new controller configuration is in progress.
Flashing The upload of a new operating system into the Flash ROM is in progress.
Off No upload of controller configuration or operating system in progress.
FORCE On The controller is executing a routine (RUN) and FORCE mode is activated by the user.
Flashing The controller is in STOP, but Forcing has been initiated and will be activated when
the controller is started.
Off Forcing is OFF.

GuardPLC™ 1600 Controllers 17
Publication 1753-IN001B-EN-P - March 2004
Communication Display
Communication via GuardPLC Ethernet is indicated by two small LEDs integrated
into all connecting sockets.
Additional non-safety related communication occurs on the field buses and is
indicated by the LEDs.
FAULT On •The routine (logic) has caused an error.
•The controller configuration is faulty.
•The upload of a new operating system was not successful and the operating
system is corrupted.
Flashing An error has occurred during a Flash ROM write cycle.
One or more I/O errors have occurred.
Off None of the above errors has occurred.
OSL Flashing Emergency Operating System Loader is active.
BL Flashing Boot Loader unable to load operating system or unable to start COMM operating
system loader.
Controller status can be interrogated through the programming software. For more information, refer to the
GuardPLC™ System User Manual (1753-UM001).
LED Status Condition
Green On Full-duplex operation
Flashing Collision
Off Half-duplex operation, no collision
Yellow On Connection established
Flashing Interface activity
LED Connection Condition
Green COMM 1 RS485 interface, field bus active
COMM 2 Unassigned
COMM 3 Unassigned
Indicator State Condition

18 GuardPLC™ 1600 Controllers
Publication 1753-IN001B-EN-P - March 2004
Specifications
Controller
User Memory max. 250 KB user program memory
max. 250 KB application data memory
Minimum Watchdog 10 ms
Minimum Safety Time 20 ms
Current Consumption max. 8 A (with max. load)
0.5 A idle current
Operating Voltage 24V dc, -15% to +20%, wss ≤15% (from a power supply with protective
separation conforming to IEC 61131-2 requirements)
Protection IP20
Digital Inputs
No. of Inputs 20 (not electrically isolated)
On-state Voltage: 15V to 30V dc
Current Consumption: ≥ 2 mA @ 15V
7.5 mA @ 30V
Off-state Voltage: max. 5V dc
Current Consumption: max 1.5 mA (1 mA @ 5V)
Switching Point typically 7.5V
Supply 5 x 20V / 100 mA @ 24V short-circuit proof
Digital Outputs
No. of Outputs 8 (not electrically isolated)
Output Voltage Range 18.4V to 26.8V
Output Current Channels 1 to 3 and 5 to 7: 0.5 A @ 60°C (140°F)
Channels 4 and 8: 1 A @ 60°C (140°F); 2 A @ 50°C (122°C)
Surge Current per Channel 1A for 10ms @ 1Hz (Channels 1 to 3 and 5 to 7)
4A for 10ms @ 1Hz (Channels 4 and 8)
Minimum Current Load 2 mA per Channel
On-State Voltage Drop max. 2.0V dc @ 2 A
Off-State Leakage Current max. 1 mA @ 2V
Environmental Conditions
Storage Temperature : -40°C to +85°C (-40°F to +185°F)
Operating Temperature: 0°C to +60°C (+32°F to 140°F)

GuardPLC™ 1600 Controllers 19
Publication 1753-IN001B-EN-P - March 2004
Specifications (continued)
Mechanical Dimensions
Width 257 mm (10.1 in.) including housing screws
Height 114 mm (4.49 in.) including latch
Depth 66 mm (2.60 in.) including grounding bolt
Weight 1.2 kg (2.64 lbs.)
Agency Certifications
(when product is marked)
N223
Functional Safety 1oo2D (AK 1 to 6, SIL 1 to 3,
according to DIN V 19250 and IEC 61508 respectively)
Category 1 to 4, according to EN954-1
Marked for all applicable directives
Marked for all applicable acts
C-UL Listed Industrial Control Equipment

Publication 1753-IN001B-EN-P - March 2004 PN 40071-162-01(2)
Supersedes Publication 1753-IN001A-EN-P - January 2004 Copyright © 2004 Rockwell Automation, Inc. All rights reserved. Printed in the U.S.A.
Allen-Bradley is a registered trademark of Rockwell Automation, Inc.
GuardPLC is a trademark of Rockwell Automation, Inc.
C-UL is a registered trademark of Underwriters Laboratories, Inc.
This manual suits for next models
1
Table of contents
Other AB Quality Controllers manuals

AB Quality
AB Quality 1760-L18AWA-EX User manual

AB Quality
AB Quality SD3000 PLUS User manual
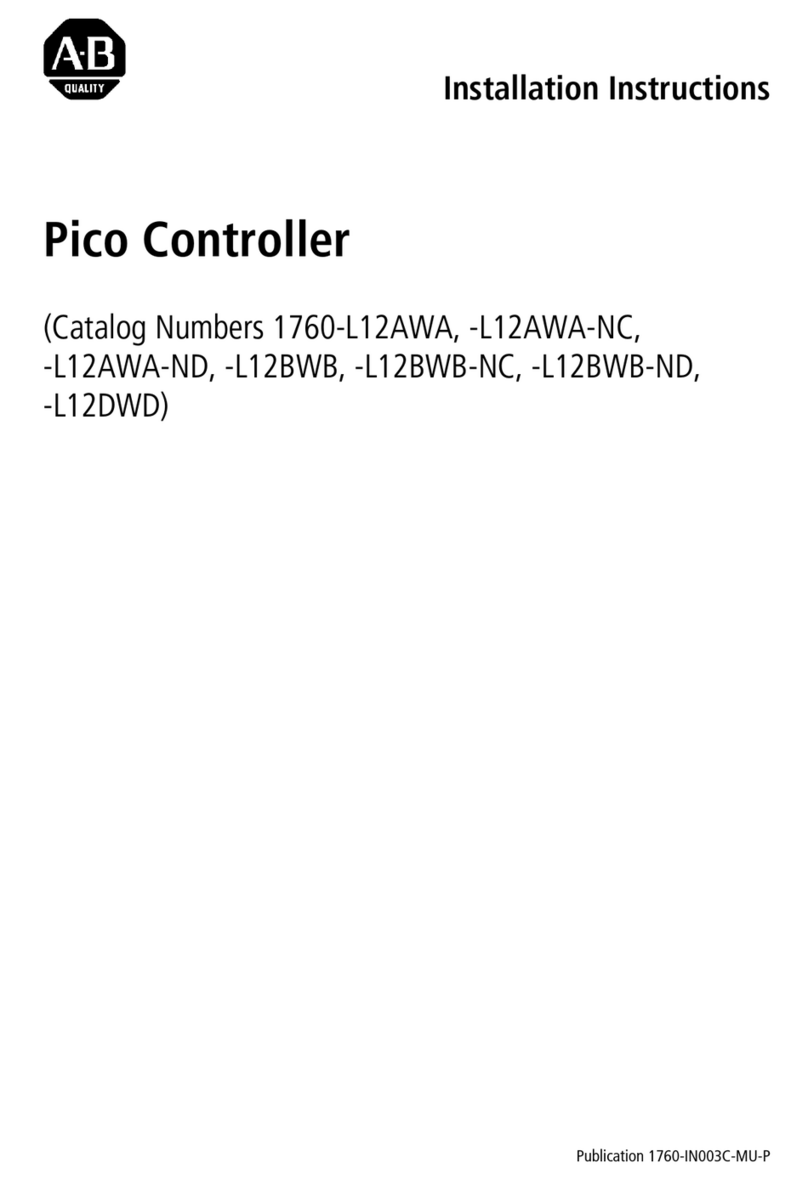
AB Quality
AB Quality 1760-L12AWA User manual
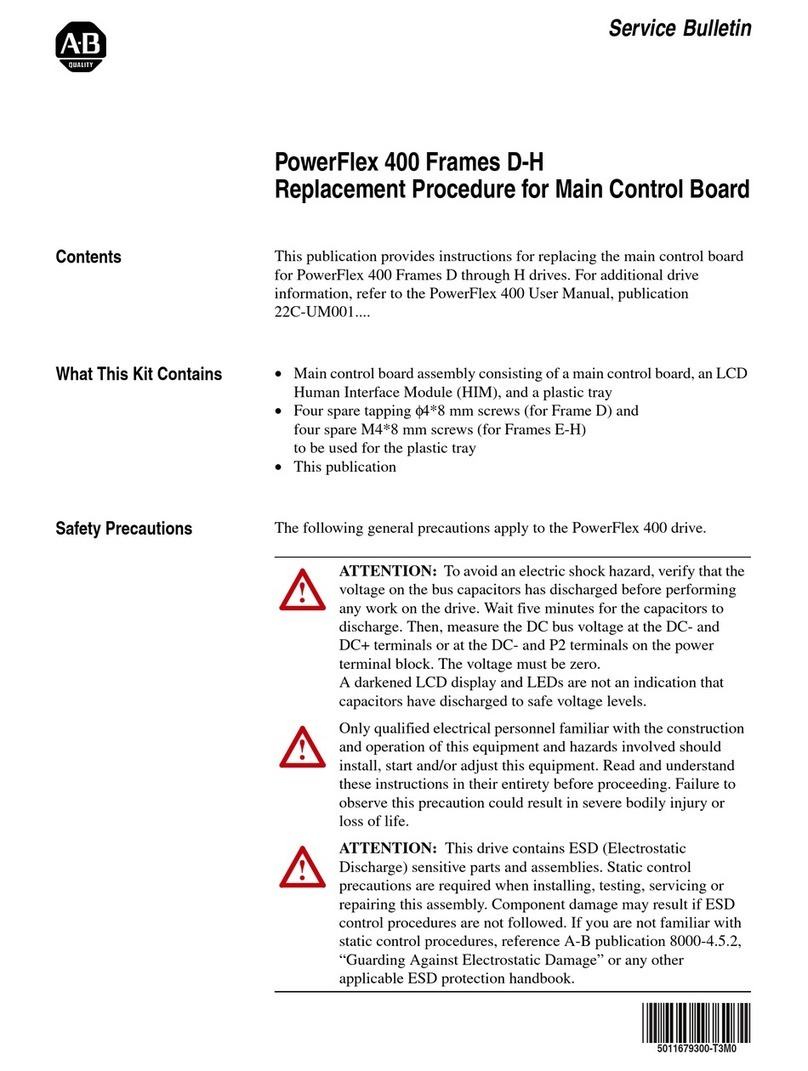
AB Quality
AB Quality PowerFlex 400 Frames D-H Reference manual
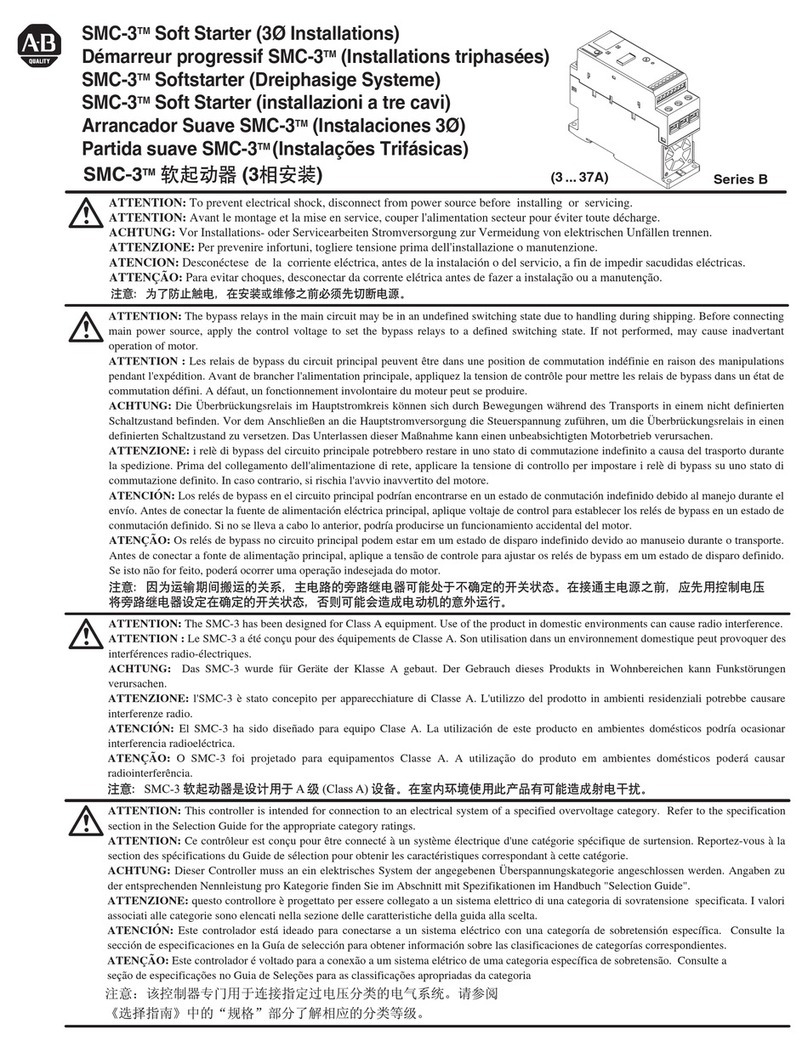
AB Quality
AB Quality SMC-3 150-C30NBD User manual
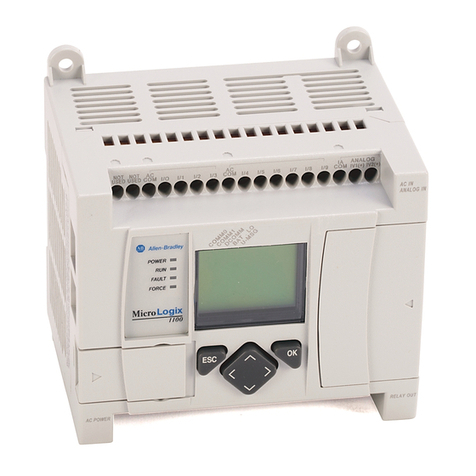
AB Quality
AB Quality MicroLogix 1100 User manual
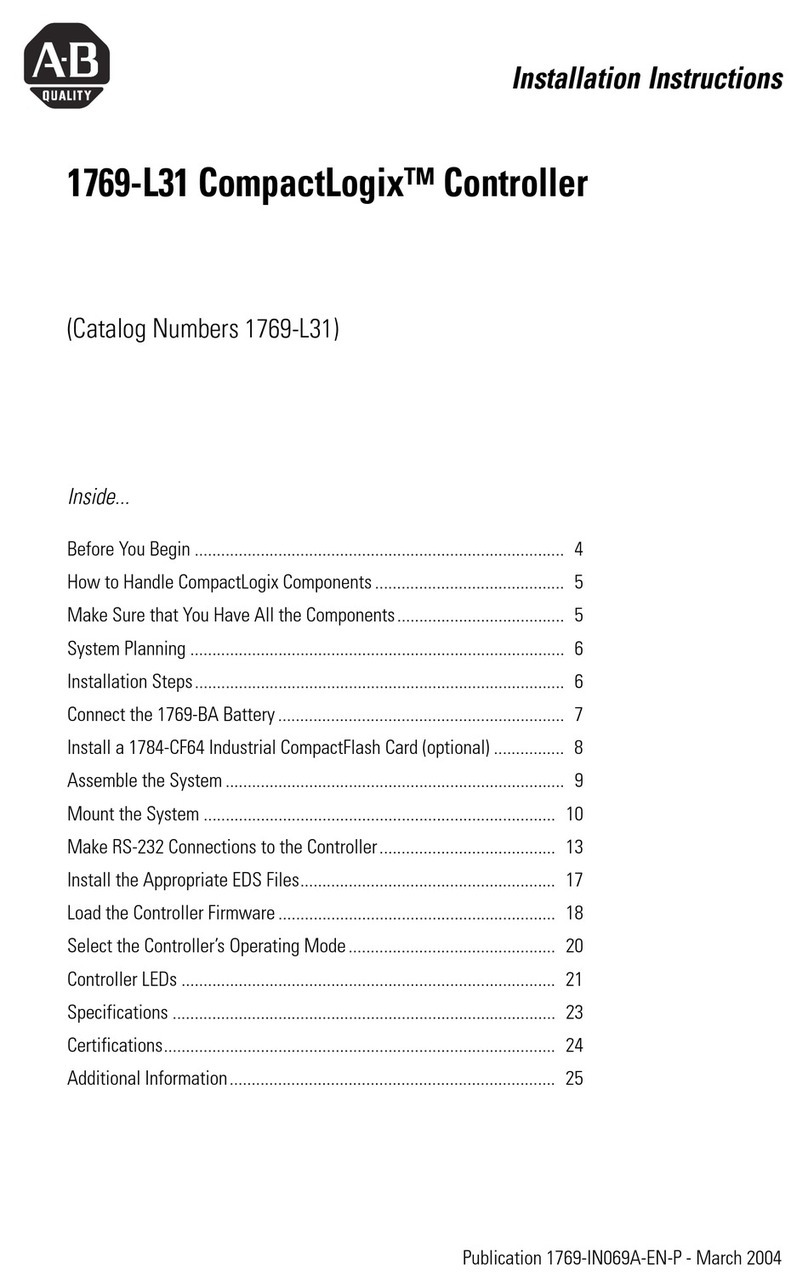
AB Quality
AB Quality 1769-L31 CompactLogix User manual