ABB IRC5 Compact Instructions for use

ABB Robotics
Application manual
Robot Reference Interface

Trace back information:
Workspace R13-2 version a2
Checked in 2013-09-30
Skribenta version 4.0.378

Application manual
Robot Reference Interface
RobotWare 5.60
Document ID: 3HAC031973-001
Revision: F
© Copyright 2008-2009,2013 ABB. All rights reserved.

The information in this manual is subject to change without notice and should not
be construed as a commitment by ABB. ABB assumes no responsibility for any errors
that may appear in this manual.
Except as may be expressly stated anywhere in this manual, nothing herein shall be
construed as any kind of guarantee or warranty by ABB for losses, damages to
persons or property, fitness for a specific purpose or the like.
In no event shall ABB be liable for incidental or consequential damages arising from
use of this manual and products described herein.
This manual and parts thereof must not be reproduced or copied without ABB's
written permission.
Additional copies of this manual may be obtained from ABB.
The original language for this publication is English. Any other languages that are
supplied have been translated from English.
© Copyright 2008-2009,2013 ABB. All rights reserved.
ABB AB
Robotics Products
Se-721 68 Västerås
Sweden

Table of contents
7Overview of this manual ...................................................................................................................
9Product documentation, IRC5 ..........................................................................................................
11Safety ................................................................................................................................................
131 Introduction to Robot Reference Interface
152 Installation
152.1 Connecting the communication cable .................................................................... 162.2 Prerequisites .................................................................................................... 172.3 Data orchestration ............................................................................................. 182.4 Supported data types .........................................................................................
193 Configuration
193.1 Interface configuration ....................................................................................... 203.2 Interface settings .............................................................................................. 213.3 Device description ............................................................................................. 243.4 Device configuration ..........................................................................................
274 Configuration examples
274.1 RAPID programming .......................................................................................... 284.2 Example configuration .......................................................................................
335 RAPID reference information
335.1 RAPID instructions ............................................................................................ 335.1.1 SiConnect - Sensor Interface Connect ......................................................... 365.1.2 SiClose - Sensor Interface Close ................................................................ 385.1.3 SiGetCyclic - Sensor Interface Get Cyclic .................................................... 405.1.4 SiSetCyclic - Sensor Interface Set Cyclic ..................................................... 425.2 RAPID data types .............................................................................................. 425.2.1 sensor - External device descriptor ............................................................. 445.2.2 sensorstate - Communication state of the device ..........................................
45Index
3HAC031973-001 Revision: F 5
© Copyright 2008-2009,2013 ABB. All rights reserved.
Table of contents

This page is intentionally left blank

Overview of this manual
About this manual
This manual explains the basics of how and when to use the RobotWare option
Robot Reference Interface.
Usage
This manual can be used either as a reference to find out if an option is the right
choice for solving a problem, or as a description of how to use an option. Detailed
information regarding syntax for RAPID routines and configuration of system
parameters is not described here, but can be found in the respective reference
manual.
Who should read this manual?
This manual is mainly intended for robot programmers.
Prerequisites
The reader should be:
• Familiar with industrial robots and their terminology.
• Familiar with the RAPID programming language.
• Familiar with RobotStudio and how to work with system parameters.
References
Document IDReference
3HAC031045-001Operating manual - General safety information
3HAC16581-1Technical reference manual - RAPID Instructions, Functions and Data
types
3HAC032104-001Operating manual - RobotStudio
Sample code available on www.abb.com/robotics (ABB Library)
Revisions
DescriptionRevision
First edition-
Released with RobotWare 5.12. Minor corrections.A
SiConnect has a new switch \NoStop.
Updates in sensor.
SiTool and SiWobj are no longer needed for calculations. Current tool
and workobject are used instead.
Released with RobotWare 5.14.B
The following updates are made:
• The correct unit for robot joints is radians, see Example configura-
tion on page 28.
•Corrected code in examples, see Example configuration on page 28.
Correction of connections in Connecting the communication cable on
page 15.
C
Continues on next page
3HAC031973-001 Revision: F 7
© Copyright 2008-2009,2013 ABB. All rights reserved.
Overview of this manual

DescriptionRevision
Released with RobotWare 5.15.D
Clarifications added regarding the direction of data exchange in Introduc-
tion to Robot Reference Interface on page 13.
Released with RobotWare 5.15.01.
• All references to the protocol high-priority UDP (HP-UDP) are re-
moved throughout the manual. The protocol is not supported.
• The attribute Link is changed from optional to mandatory in
Properties on page 26.
• Minor corrections.
E
Released with RobotWare 5.60.
• Updated the graphic in the section Connecting the communication
cable on page 15.
• Updated information related to Network ports in the section Device
description on page 21.
F
8 3HAC031973-001 Revision: F
© Copyright 2008-2009,2013 ABB. All rights reserved.
Overview of this manual
Continued

Product documentation, IRC5
Categories for manipulator documentation
The manipulator documentation is divided into a number of categories. This listing
is based on the type of information in the documents, regardless of whether the
products are standard or optional.
All documents listed can be ordered from ABB on a DVD. The documents listed
are valid for IRC5 manipulator systems.
Product manuals
Manipulators, controllers, DressPack/SpotPack, and most other hardware will be
delivered with a Product manual that generally contains:
• Safety information.
• Installation and commissioning (descriptions of mechanical installation or
electrical connections).
•Maintenance (descriptions of all required preventive maintenance procedures
including intervals and expected life time of parts).
• Repair (descriptions of all recommended repair procedures including spare
parts).
• Calibration.
• Decommissioning.
•Reference information (safety standards, unit conversions, screw joints, lists
of tools ).
• Spare parts list with exploded views (or references to separate spare parts
lists).
• Circuit diagrams (or references to circuit diagrams).
Technical reference manuals
The technical reference manuals describe reference information for robotics
products.
•Technical reference manual - Lubrication in gearboxes: Description of types
and volumes of lubrication for the manipulator gearboxes.
•Technical reference manual - RAPID overview: An overview of the RAPID
programming language.
•Technical reference manual - RAPID Instructions, Functions and Data types:
Description and syntax for all RAPID instructions, functions, and data types.
•Technical reference manual - RAPID kernel: A formal description of the
RAPID programming language.
•Technical reference manual - System parameters: Description of system
parameters and configuration workflows.
Application manuals
Specific applications (for example software or hardware options) are described in
Application manuals. An application manual can describe one or several
applications.
Continues on next page
3HAC031973-001 Revision: F 9
© Copyright 2008-2009,2013 ABB. All rights reserved.
Product documentation, IRC5

An application manual generally contains information about:
• The purpose of the application (what it does and when it is useful).
•What is included (for example cables, I/O boards, RAPID instructions, system
parameters, DVD with PC software).
• How to install included or required hardware.
• How to use the application.
• Examples of how to use the application.
Operating manuals
The operating manuals describe hands-on handling of the products. The manuals
are aimed at those having first-hand operational contact with the product, that is
production cell operators, programmers, and trouble shooters.
The group of manuals includes (among others):
•Operating manual - Emergency safety information
•Operating manual - General safety information
•Operating manual - Getting started, IRC5 and RobotStudio
•Operating manual - Introduction to RAPID
•Operating manual - IRC5 with FlexPendant
•Operating manual - RobotStudio
•Operating manual - Trouble shooting IRC5, for the controller and manipulator.
10 3HAC031973-001 Revision: F
© Copyright 2008-2009,2013 ABB. All rights reserved.
Product documentation, IRC5
Continued

Safety
Safety of personnel
A robot is heavy and extremely powerful regardless of its speed. A pause or long
stop in movement can be followed by a fast hazardous movement. Even if a pattern
of movement is predicted, a change in operation can be triggered by an external
signal resulting in an unexpected movement.
Therefore, it is important that all safety regulations are followed when entering
safeguarded space.
Safety regulations
Before beginning work with the robot, make sure you are familiar with the safety
regulations described in the manual Operating manual - General safety information.
3HAC031973-001 Revision: F 11
© Copyright 2008-2009,2013 ABB. All rights reserved.
Safety

This page is intentionally left blank

1 Introduction to Robot Reference Interface
Introduction
Robot Reference Interface is an option, supporting data exchange on the cyclic
channel. It provides the possibility to periodically send planned and actual robot
position data from the robot controller, as well as the exchange of other RAPID
variables from and to the robot controller. The message contents are represented
in XML format and are configured using appropriate sensor configuration files.
Robot Reference Interface
The cyclic communication channel (TCP or UDP) can be executed in the high-priority
network environment of the IRC5 Controller which ensures a stable data exchange
up to 250Hz.
Robot Sensor
Rapid data
Motion data
RRI
Cyclic channel (TCP or UDP)
read/write Receive commands,
parameters and
robot data
Return parameters
and sensor data
read only
Cabinet status read only
xx0800000128
3HAC031973-001 Revision: F 13
© Copyright 2008-2009,2013 ABB. All rights reserved.
1 Introduction to Robot Reference Interface

This page is intentionally left blank

2 Installation
2.1 Connecting the communication cable
Overview
This section describes where to connect the communication cable on the controller.
For further instructions, see the corresponding product manual for your robot
system.
Location
A
B
xx1300000609
Service port on the computer unit (connected to the service port on the controller)A
WAN port on the computer unitB
NoteAction
Note
The service connection can only be
used if it is free.
Use one of these two connections (A or B).1
3HAC031973-001 Revision: F 15
© Copyright 2008-2009,2013 ABB. All rights reserved.
2 Installation
2.1 Connecting the communication cable

2.2 Prerequisites
Overview
This section describes the prerequisites for using Robot Reference Interface.
UDP/IP or TCP IP
Robot Reference Interface supports the communication over the standard IP
protocols UDP or TCP.
Recommendations
The delay in the overall communication mostly depends on the topology of the
employed network. In a switched network the transmission will be delayed due to
buffering of the messages in the switches. In a parallel network collisions with
multiple communication partners will lead to messages being resent.
Therefore we recommended using a dedicated Ethernet link between the external
system and the robot controller to provide the required performance for real-time
applications. Robot Reference Interface can be used to communicate with any
processor-based devices, that support IP via Ethernet and can serialize data into
XML format.
16 3HAC031973-001 Revision: F
© Copyright 2008-2009,2013 ABB. All rights reserved.
2 Installation
2.2 Prerequisites

2.3 Data orchestration
Overview
The outgoing message can be combined from any data from the RAPID level and
internal data from the cabinet and motion topic. The orchestration of the data is
defined in the device configuration by setting the Link attribute of internally linked
data to Intern.
Illustration
xx0800000178
Data from the Controller topic
CommentDescriptionTypeName
The mapping of the members for the Op-
Mode type can be defined in the configura-
tion file.
Operation mode
of the robot.
OpModeOperationMode
Data from the Motion topic
CommentDescriptionTypeName
There is a delay of approxim-
ately 8ms.
Time stamp for the robot posi-
tion from drive feedback.
TimeFeedbackTime
Current tool and workobject
are used for calculation.
Robot TCP calculated from
drive feedback.
FrameFeedbackPose
Robot joint values gathered
from drive feedback.
JointsFeedbackJoints
Prediction time from approxim-
ately 24ms to 60ms depending
on robot type.
Timestamp for planned robot
TCP position and joint values.
TimePredictedTime
Current tool and workobject
are used for calculation.
Planned robot TCP.FramePlannedPose
Planned robot joint values.JointsPlannedJoints
3HAC031973-001 Revision: F 17
© Copyright 2008-2009,2013 ABB. All rights reserved.
2 Installation
2.3 Data orchestration

2.4 Supported data types
Overview
This section contains a short description of the Robot Reference Interface supported
data types, for more detailed information about the supported data types see
References on page 7.
Data types
Robot Reference Interface supports the following simple data types:
RAPID type mappingDescriptionData type
boolBoolean value.bool
numSingle precision, floating point value.real
numTime in seconds expressed as floating point value.time
stringString with max length of 80 characters.string
poseCartesian position and orientation in Euler Angles
(Roll-Pitch-Jaw).
frame
robjointRobot joint values.joints
In addition, user-defined records can also be transferred from the external system
to the robot controller, which are composed from the supported simple data types.
User defined record types must be specified in the configuration file of the external
device. See Device configuration on page 24 for a description on how to create
user-defined record types.
18 3HAC031973-001 Revision: F
© Copyright 2008-2009,2013 ABB. All rights reserved.
2 Installation
2.4 Supported data types

3 Configuration
3.1 Interface configuration
Configuration files
The configuration and settings files for the interface must be located in the folder
HOME/GSI. This ensures that the configuration files are included in system backups.
xx0800000177
Related information
For more detailed information of the Settings.xml file see Interface settings on
page 20.
For more detailed information of the Description.xml file see Device description
on page 21.
For more detailed information of the Configuration.xml file see Device configuration
on page 24.
3HAC031973-001 Revision: F 19
© Copyright 2008-2009,2013 ABB. All rights reserved.
3 Configuration
3.1 Interface configuration

3.2 Interface settings
Overview
This section describes the use of the xml file Settings.xml.
Settings.xml
The settings file Settings.xml contains the general settings for the GSI interface.
It is located in the folder HOME/GSI. For the option Robot Reference Interface this
file refers to a list of all communication clients for external systems installed in the
controller. The Settings.xml file can be defined according to the XML schema
Settings.xsd.
Example
For each communication client installed on the controller, the file Settings.xml must
contain a Client entry in the Clients section. The Convention attribute identifies the
protocol convention used by the client, for the Robot Reference Interface option
only CDP is supported. The Name attribute identifies the name of the client and
also specifies the folder with the device related configuration files.
<?xml version="1.0" encoding="UTF-8"?>
<Settings>
<Clients>
<Client Convention="CDP" Name="MySensor" />
</Clients>
</Settings>
CDP stands for cyclic data protocol and is the internal name of the protocol, on
which Robot Reference Interface messages are transferred.
An internal client node of the interface module will be created, which is able to
connect to the external system MySensor that runs a data server application and
can communicate via Robot Reference Interface with the robot.
For each sensor system, a subdirectory named with the sensor system identifier,
for example MySensor, contains further settings.
20 3HAC031973-001 Revision: F
© Copyright 2008-2009,2013 ABB. All rights reserved.
3 Configuration
3.2 Interface settings
Other manuals for IRC5 Compact
17
Table of contents
Other ABB Controllers manuals
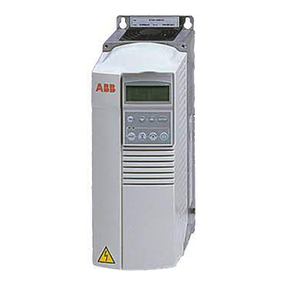
ABB
ABB ACS 400 User manual
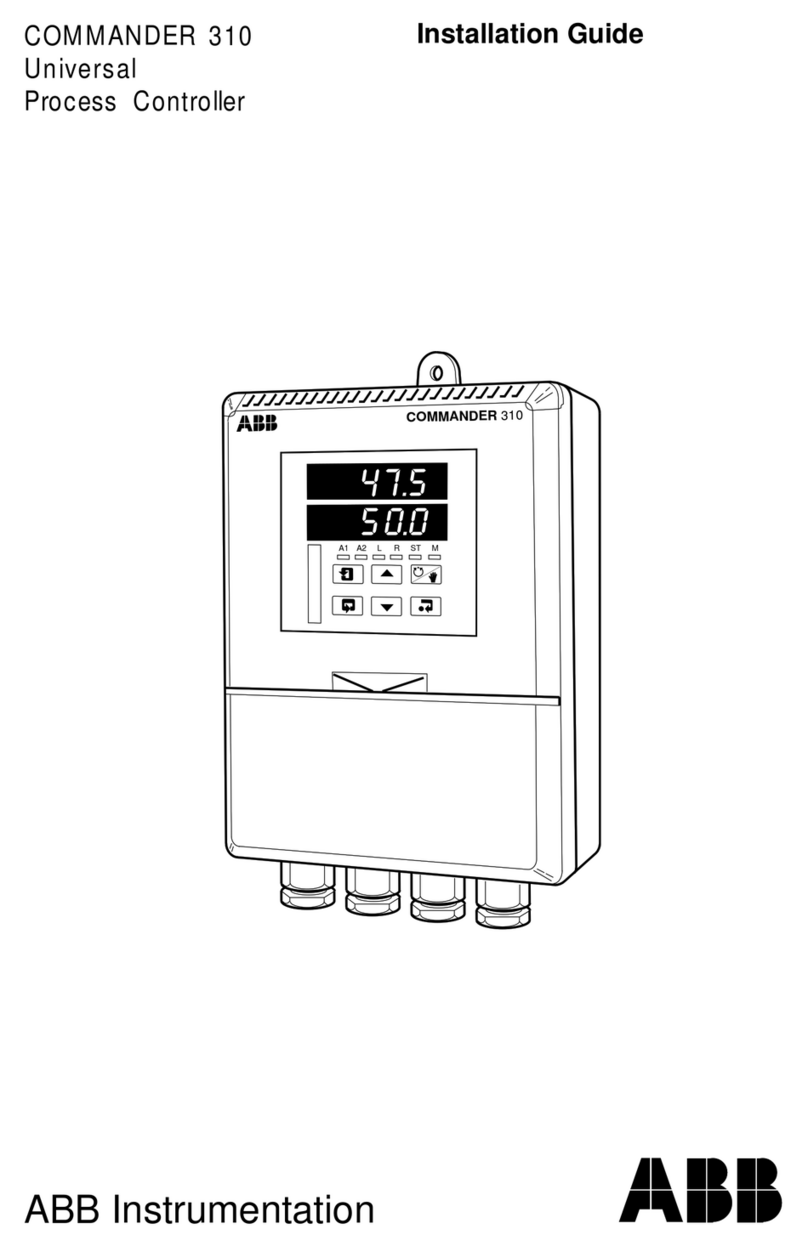
ABB
ABB COMMANDER 310 User manual
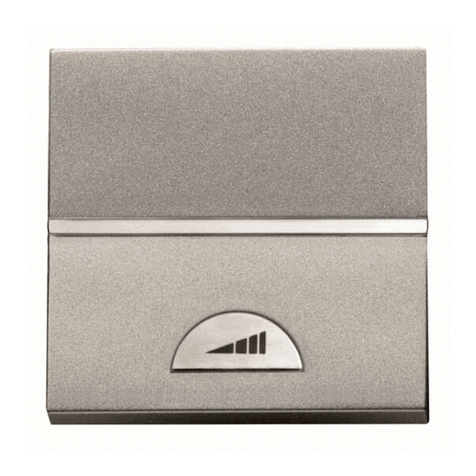
ABB
ABB NIESSEN 2260 Series User manual
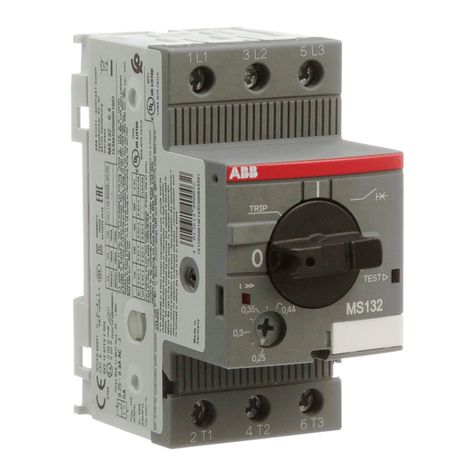
ABB
ABB MS116 User manual
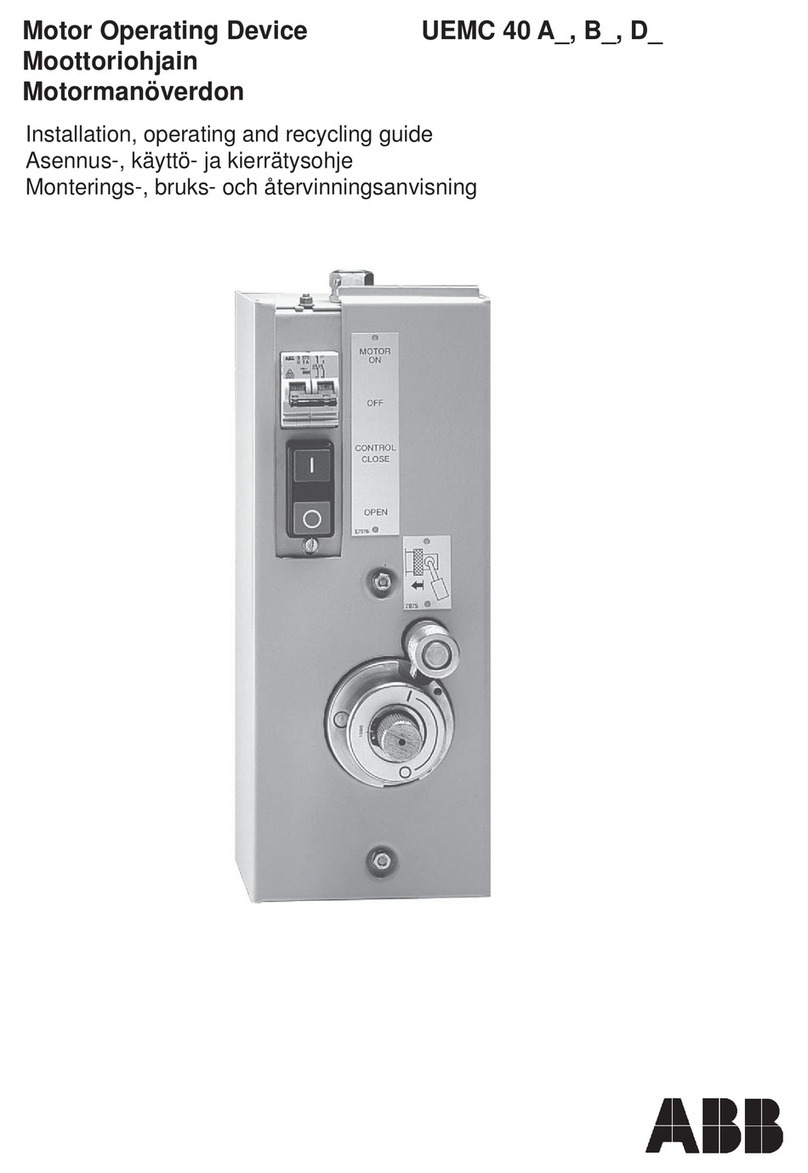
ABB
ABB UEMC 40 B Series Installation guide

ABB
ABB 6153 EB-500 User manual

ABB
ABB ACH550-PCR User manual
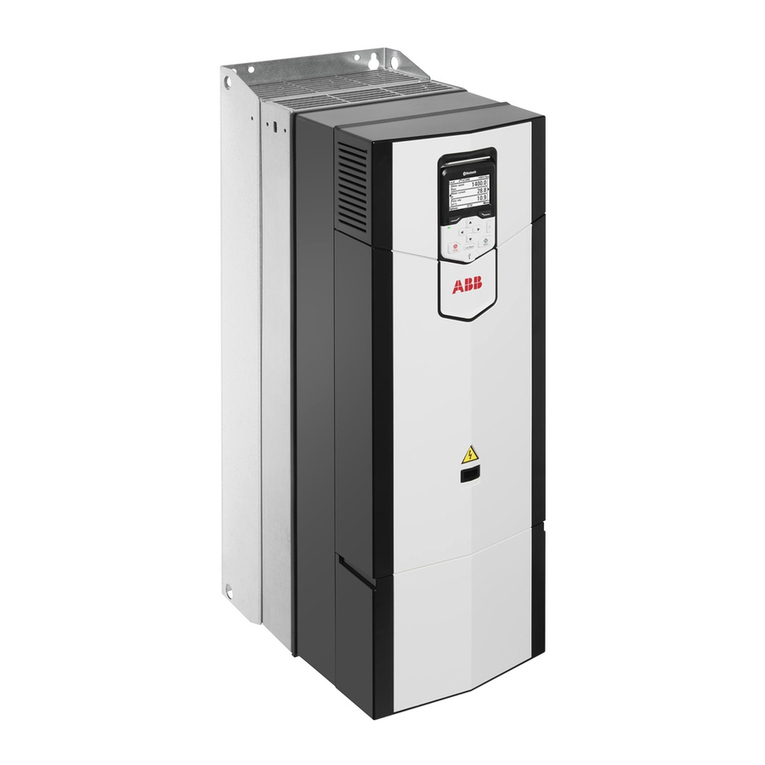
ABB
ABB ACS880-11 User manual
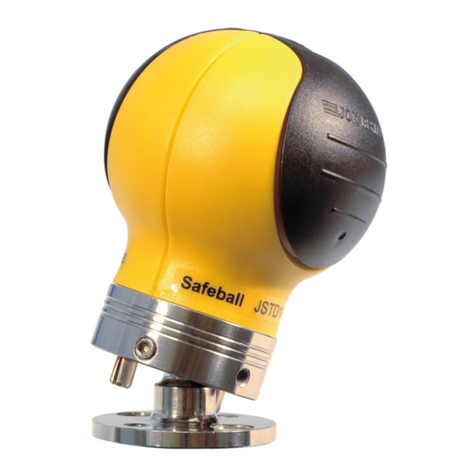
ABB
ABB Jokab Safety Safeball JSTD1 User manual
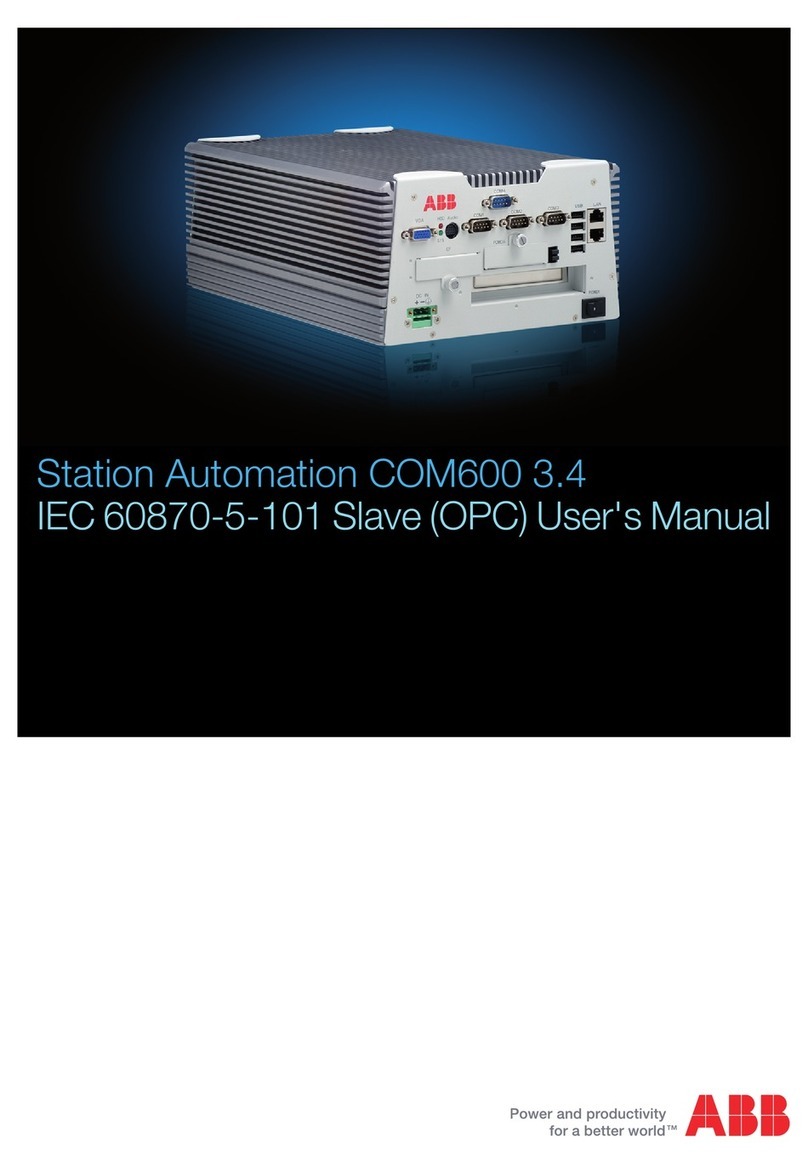
ABB
ABB COM600 3.4 User manual
Popular Controllers manuals by other brands
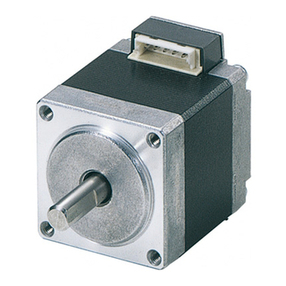
Oriental motor
Oriental motor CRK Series operating manual

ALLOYLED
ALLOYLED AL-60-03-0008 Specifications
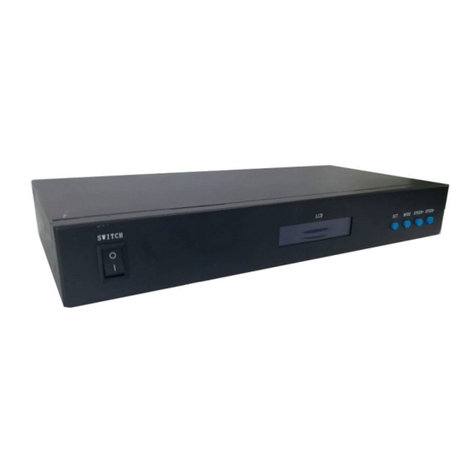
Sun-Tech
Sun-Tech T-780K Operation manual
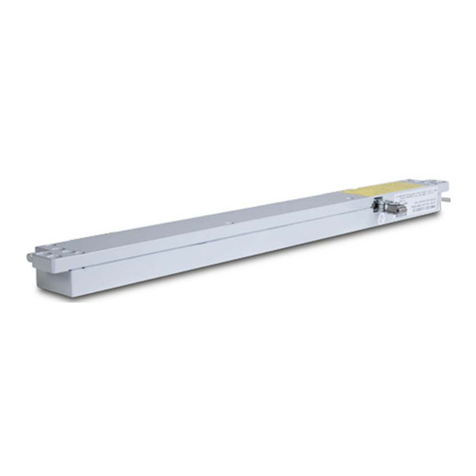
WindowMaster
WindowMaster WMX 523 Installation instructions manual
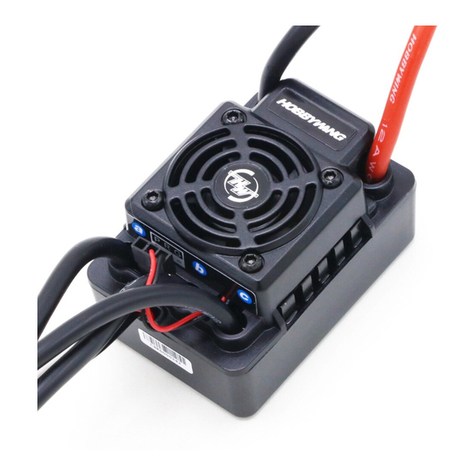
Hobby-Wing
Hobby-Wing EZRUN-WP-SC8 user manual

Global American Inc.
Global American Inc. 3307980 user manual