Absolute Measurement CLT User manual

Transducer Instruction
Manual
Range: Ultra
Type: CLT
Revision: V1.0

_____________________________________________________________________________________________________________________
Absolute Measurement Ltd. (T/A CMC Controls)
t: (0) 1732 763278 | e: sales@absolutemeasurement.co.uk | w: absolutemeasurement.co.uk
Unit 19 | Silver Birches Business Park | Aston Road | Bromsgrove | B60 3EU
1
Transducer Instruction Manual
Range: Ultra
Type: CLT
Revision: V1.0
Contents
Contents........................................................................................................................................................1
1. Principle of Transducer Operation........................................................................................................2
2. Installation ............................................................................................................................................2
2.1 Selection of Transducer Mounting Location.................................................................................2
2.2 Installation Precautions ................................................................................................................3
2.3 Mounting Surface Preparation .....................................................................................................3
2.4 CLT-SCM Installation .....................................................................................................................3
2.5 CLT-FLCM Installation ...................................................................................................................4
2.6 CLT-PBCM Installation...................................................................................................................4
2.7 CLT-BRCM Installation...................................................................................................................4
2.8 Sensing Roller Installation.............................................................................................................5
2.9 Temperature Compensation and Shaft Expansion .......................................................................6
2.10 Hazardous Area Installation - Intrinsic Safety...............................................................................6
2.11 Single Transducer Operation ........................................................................................................6
3. Transducer Force (MWF) Calculation ...................................................................................................6
4. Troubleshooting....................................................................................................................................7
4.1 High Output Signal With No Tension ............................................................................................7
4.2 Low Output Signal With Maximum Tension .................................................................................7
4.3 Wrong Polarity of Output Signal...................................................................................................7
4.4 Output Signal Not Linear, Zero Shifts During Operation...............................................................8
4.5 Transducer Strain Gauge Resistance.............................................................................................8

_____________________________________________________________________________________________________________________
Absolute Measurement Ltd. (T/A CMC Controls)
t: (0) 1732 763278 | e: sales@absolutemeasurement.co.uk | w: absolutemeasurement.co.uk
Unit 19 | Silver Birches Business Park | Aston Road | Bromsgrove | B60 3EU
2
Transducer Instruction Manual
Range: Ultra
Type: CLT
Revision: V1.0
1. Principle of Transducer Operation
Cleveland Kidder web tension transducers utilise a sensing beam to which semi-conductor strain gauges
are bonded and are used for non-rotating shaft applications. Normally a pair of transducers would be
used, supporting the ends of the sensing roller shaft. The tension force applied to the sensing roller must
pass freely through to the transducers, which convert this force into an electrical signal.
This signal is a combination of tension force and sensing roller dead weight. The dead weight of the roller
is zeroed out electrically in the indicator or controller leaving the tension force signal only to be amplified
to give a true display of measured tension.
2. Installation
2.1 Selection of Transducer Mounting Location
The transducer must be mounted in a clean, dry location, see below for hazardous area installation.
When selecting a transducer mounting location, please remember that the tension sensing roller must
NOT be mounted where the web wrap angle can vary. Any change in the wrap angle will be sensed by
the transducer as a change in tension, and indicated as such on the tension meter or display.
A - Bored
C
D
E
H
I
K
L
M
N
O
P
Q
R
S
U
W
Size 1
17, 20, 25, 30
63.5
M12
60.3
54
70
54
79
10
82.5
12.7
102
50.8
44.2
137
41.3
45
Size 2
20, 25, 30, 35
70
M16
66.7
57
77
59
93
12
89.0
15.7
115
63.5
47.5
156
49.3
48

_____________________________________________________________________________________________________________________
Absolute Measurement Ltd. (T/A CMC Controls)
t: (0) 1732 763278 | e: sales@absolutemeasurement.co.uk | w: absolutemeasurement.co.uk
Unit 19 | Silver Birches Business Park | Aston Road | Bromsgrove | B60 3EU
3
Transducer Instruction Manual
Range: Ultra
Type: CLT
Revision: V1.0
2.2 Installation Precautions
To ensure proper installation and operation of the tension system, the following steps should be
performed in sequence - always install, orientate and firmly bolt down the transducer BEFORE installing
the tension sensing roller.
Welding. Unplug the cable connector from the transducer before any electric welding is undertaken on
the machine.
Transport. It is recommended that the tension sensing roller is removed from the transducer before the
machine is transported to prevent excessive shock being transmitted through to the transducer.
Failure to carry out these precautions could seriously damage the transducer and invalidate the warranty.
2.3 Mounting Surface Preparation
The mounting surface for the transducer should be rigid, flat and clean. Prepare the machine frame or
mounting surface by removing any loose paint, rust, scale, burrs etc.
2.4 CLT-SCM Installation
Rotate the transducer so that the tension resultant force is in line with the "LOAD LINE" label as shown
alongside, then SECURELY tighten the mounting bolt. The cable connector should bisect the web wrap
angle.
The mounting bolt must not bottom in the transducer, the depth of the mounting hole in the CLT-SCM
transducer is 14mm. Check that there is clearance between the mounting bolt and the bottom of the
transducer mounting hole. Fixings are available from CMC Controls if they have not been supplied with
the order, request Part Number 0594 or 0595.

_____________________________________________________________________________________________________________________
Absolute Measurement Ltd. (T/A CMC Controls)
t: (0) 1732 763278 | e: sales@absolutemeasurement.co.uk | w: absolutemeasurement.co.uk
Unit 19 | Silver Birches Business Park | Aston Road | Bromsgrove | B60 3EU
4
Transducer Instruction Manual
Range: Ultra
Type: CLT
Revision: V1.0
2.5 CLT-FLCM Installation
Four mounting holes should be drilled in the machine frame to accept the split flange. Loosen, but do not
remove the two clamping bolts for the split flange. Rotate the transducer in the split flange so that the
tension resultant force is in line with the "LOAD LINE" label as shown, then tighten the two clamping
bolts for the split flange. The cable connector should bisect the web wrap angle.
Secure the transducer firmly to the machine frame with four mounting bolts.
2.6 CLT-PBCM Installation
Mount the transducer and fix firmly to the machine frame with two fixing bolts. Loosen, but do not remove,
the four socket head screws retaining the lockplate on to the rear of the transducer. Rotate the transducer
body so that the tension resultant force is in line with the "LOAD LINE" label as shown, then tighten the
lockplate retaining screws.
2.7 CLT-BRCM Installation
Remove the four socket head retaining screws and the lockplate on the rear of the transducer. Insert the
transducer into the hole bored in the machine frame. Rotate the transducer in the machine frame so that
the tension resultant force is in line with the "LOAD LINE" label as shown, then secure the transducer
firmly in the machine frame using the lockplate. A spacer over the transducer body may be used if
required.

_____________________________________________________________________________________________________________________
Absolute Measurement Ltd. (T/A CMC Controls)
t: (0) 1732 763278 | e: sales@absolutemeasurement.co.uk | w: absolutemeasurement.co.uk
Unit 19 | Silver Birches Business Park | Aston Road | Bromsgrove | B60 3EU
5
Transducer Instruction Manual
Range: Ultra
Type: CLT
Revision: V1.0
2.8 Sensing Roller Installation
The transducer has a choice of adaptors with bores of 17, 20, 25, 30 and 35mm diameter, to accept a
shaft to which a tension sensing roller or guide pulley can be mounted as shown below. Two set screws
at 90 degrees are used to hold the shaft in place. The tension sensing roller or guide pulley should be
dynamically balanced when the roller speed exceeds 300 RPM as excessive vibration can damage the
transducer. Any out of balance force should not exceed 10% of the maximum working force (MWF) of the
transducer.
The recommended maximum roller length is 450mm to avoid an excessive bending moment being
applied to the transducer and roller deflection.

_____________________________________________________________________________________________________________________
Absolute Measurement Ltd. (T/A CMC Controls)
t: (0) 1732 763278 | e: sales@absolutemeasurement.co.uk | w: absolutemeasurement.co.uk
Unit 19 | Silver Birches Business Park | Aston Road | Bromsgrove | B60 3EU
6
Transducer Instruction Manual
Range: Ultra
Type: CLT
Revision: V1.0
2.9 Temperature Compensation and Shaft Expansion
The transducer is supplied with a temperature compensation network which is in series with Pin A, the
output signal lead. The compensation circuit will operate correctly only when used with a tension indicator
or controller supplied by CMC Controls. The transducer can accommodate sensing roller shaft expansion
due to normal temperature changes. The transducer, sensing roller and machine structure should all
therefore be at normal room temperature during installation.
2.10 Hazardous Area Installation - Intrinsic Safety
CMC Controls tension transducers can be located in a hazardous area to provide an Intrinsically Safe
installation to EN 50039 when a proprietary Zener Barrier module, Part Number 4503, is used. Tension
transducers are passive components and are classified as simple apparatus by EN 50014. Strain gauge
transducers (load cells) will be damaged if subjected to the 500 volt insulation test required by EN 50020.
To comply with Intrinsic Safety regulations the body of the transducer must be bonded to the IS earth
using 4 square millimetre green/yellow insulated cable. Consult CMC Controls for more information.
NOTE It is the responsibility of the user to ensure that all relevant safety regulations are complied with.
The integrity of all connections particularly the earth should form part of any maintenance procedure.
2.11 Single Transducer Operation
Most web tension installations require two transducers, each supporting one end of the sensing roller
shaft and the transducer output signals are summed to give a measurement of Total tension. For those
installations where only one transducer is required a Dummy Transducer, Part Number 4431, may be
needed to complete the full Wheatstone bridge. For single transducer installations the MWF calculation,
see below, should be derated by a factor of 1.5, consult CMC Controls for more information.
3. Transducer Force (MWF) Calculation
The formula for calculation of the transducer maximum working force (MWF) or force rating allows a
100% overload for tension transients or a tight edge to the web.
Remember to use the correct units.

_____________________________________________________________________________________________________________________
Absolute Measurement Ltd. (T/A CMC Controls)
t: (0) 1732 763278 | e: sales@absolutemeasurement.co.uk | w: absolutemeasurement.co.uk
Unit 19 | Silver Birches Business Park | Aston Road | Bromsgrove | B60 3EU
7
Transducer Instruction Manual
Range: Ultra
Type: CLT
Revision: V1.0
To convert W in Kg to Newtons - N multiply by 10, the exact factor is 9.81
MWF = 2 Tmax Sin(A/2) + (W/2) Sin(B) MWF = 2 Tmax Sin(A/2) - (W/2) Sin(B)
MWF MUST BE GREATER THAN SENSING ROLLER WEIGHT W
ANGLE 'A' IS 30 DEGREES MINIMUM
4. Troubleshooting
There are no user replaceable or serviceable parts in the transducer. Tampering or damage caused
during installation will invalidate the warranty.
The signal output from the transducer with the recommended 5.6V DC excitation is 200mV (nominal)
when the transducer is loaded to its maximum working force - MWF.
The transducer has built in mechanical overload stops which operate at approximately 125% of the MWF.
Forces above 150% of MWF particularly transients or tension snatches may cause permanent damage.
The ultimate overload capability before breakage is 300%, bearing damage may occur before this.
4.1 High Output Signal With No Tension
[1] Check for correct wiring to the transducer.
[2] Check cables and connectors for good continuity with an ohm meter, do NOT use a 'megger'.
[3] The transducer may have too low a MWF, replace with a higher MWF transducer or reduce the
web wrap angle.
[4] The transducer excitation voltage may be too high - this will cause permanent damage and may
invalidate the warranty.
[5] The sensing roller weight may be too heavy, this should not exceed the MWF of the transducer.
4.2 Low Output Signal With Maximum Tension
[1] Check for correct wiring to the transducer.
[2] Check cables and connectors for good continuity with an ohm meter, do NOT use a 'megger'.
[3] The transducer may have too high a MWF, replace with a lower MWF transducer or increase the
web wrap angle.
[4] The transducer excitation voltage may be too low.
4.3 Wrong Polarity of Output Signal
[1] Check that the web path is correct.
[2] The transducer may be incorrectly orientated, rotate 180to correct this. If rotation is not possible,
interchange the transducer excitation supply or output signal leads at the indicator or controller
terminals.

_____________________________________________________________________________________________________________________
Absolute Measurement Ltd. (T/A CMC Controls)
t: (0) 1732 763278 | e: sales@absolutemeasurement.co.uk | w: absolutemeasurement.co.uk
Unit 19 | Silver Birches Business Park | Aston Road | Bromsgrove | B60 3EU
8
Transducer Instruction Manual
Range: Ultra
Type: CLT
Revision: V1.0
4.4 Output Signal Not Linear, Zero Shifts During Operation
[1] Check that there is no dirt or foreign matter interfering with the transducer mounting.
[2] Check that the shaft clamp and transducer mounting bolts are secure.
4.5 Transducer Strain Gauge Resistance
The transducer has semiconductor strain gauges in a full bridge configuration.
The gauge resistances, measured at room temperature with no load, are shown in the table below.
Measurements taken
between the following
wires:
Corresponding
M12 Connector
Pins:
Target Resistance
Aluminium Beam
Target Resistance Steel Beam
GN/RD
2 - 1
88 Ω
88 Ω
YL/RD
4 - 1
88 Ω
88 Ω
GN/YL
2 - 4
118 Ω
118 Ω
GN/BU
2 - 3
104 Ω
112 Ω
(Varies slightly based on load cell
temperature)
YL/BU
4 - 3
104 Ω
112 Ω
(Varies slightly based on load cell
temperature)
RD/BU
1 - 3
133 Ω
141 Ω
(Varies slightly based on load cell
temperature)
Table of contents
Popular Transducer manuals by other brands
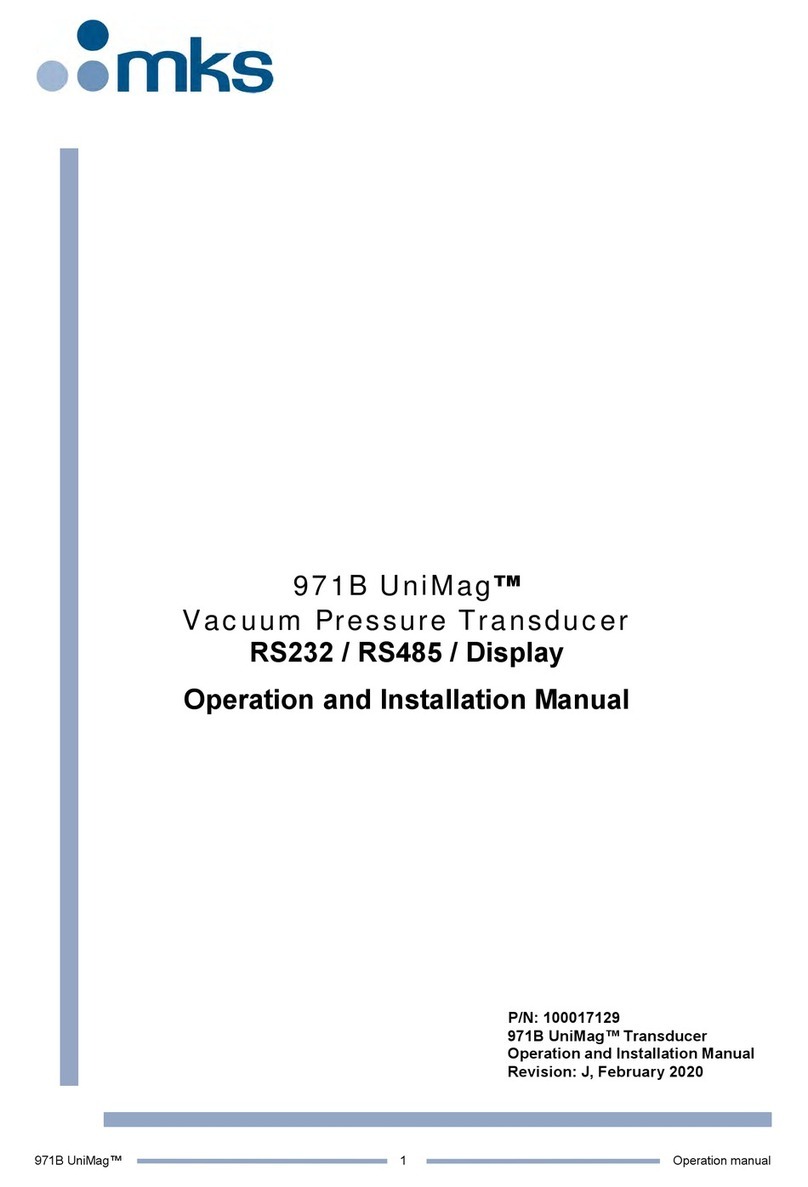
MKS
MKS UniMag 971B Operation and installation manual
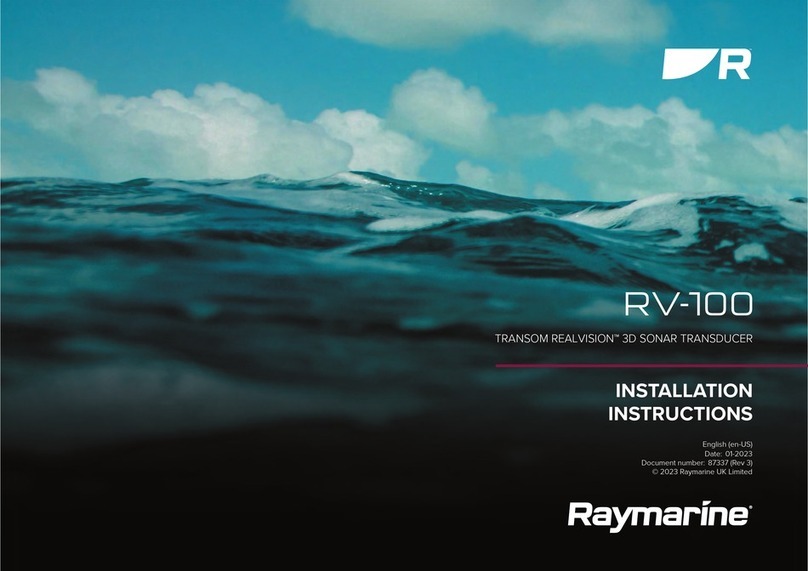
Raymarine
Raymarine RV-100 RealVision 3D installation instructions
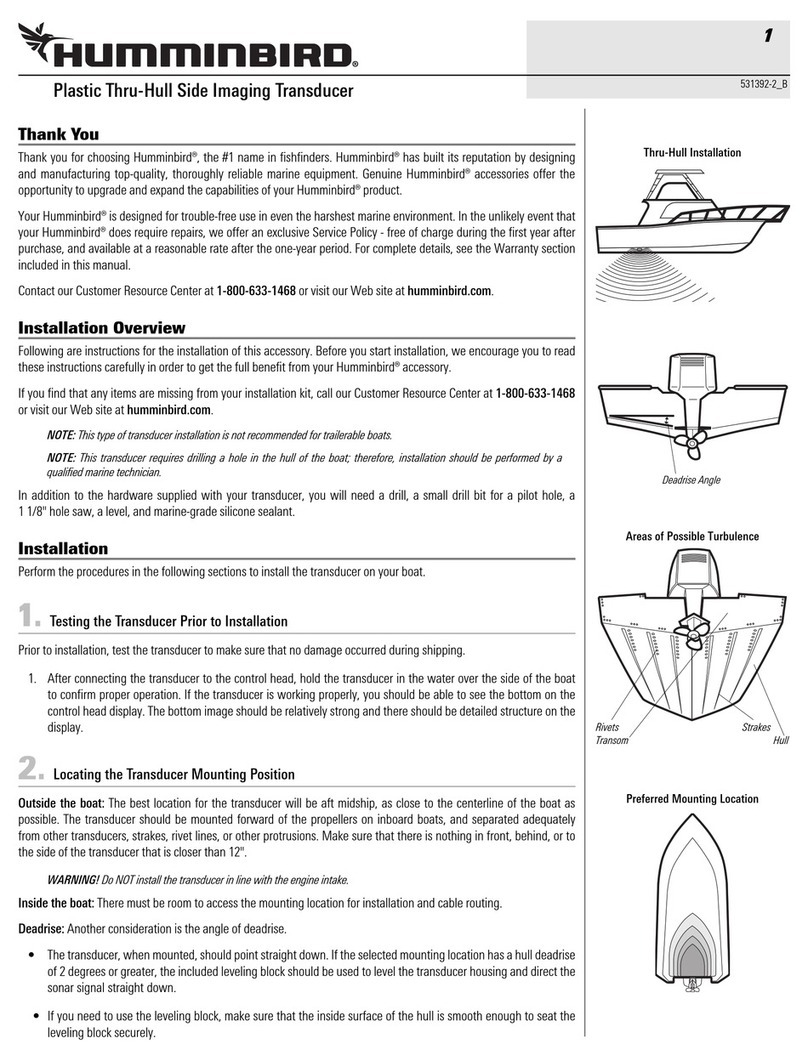
Humminbird
Humminbird 531392-2_B Quick manual
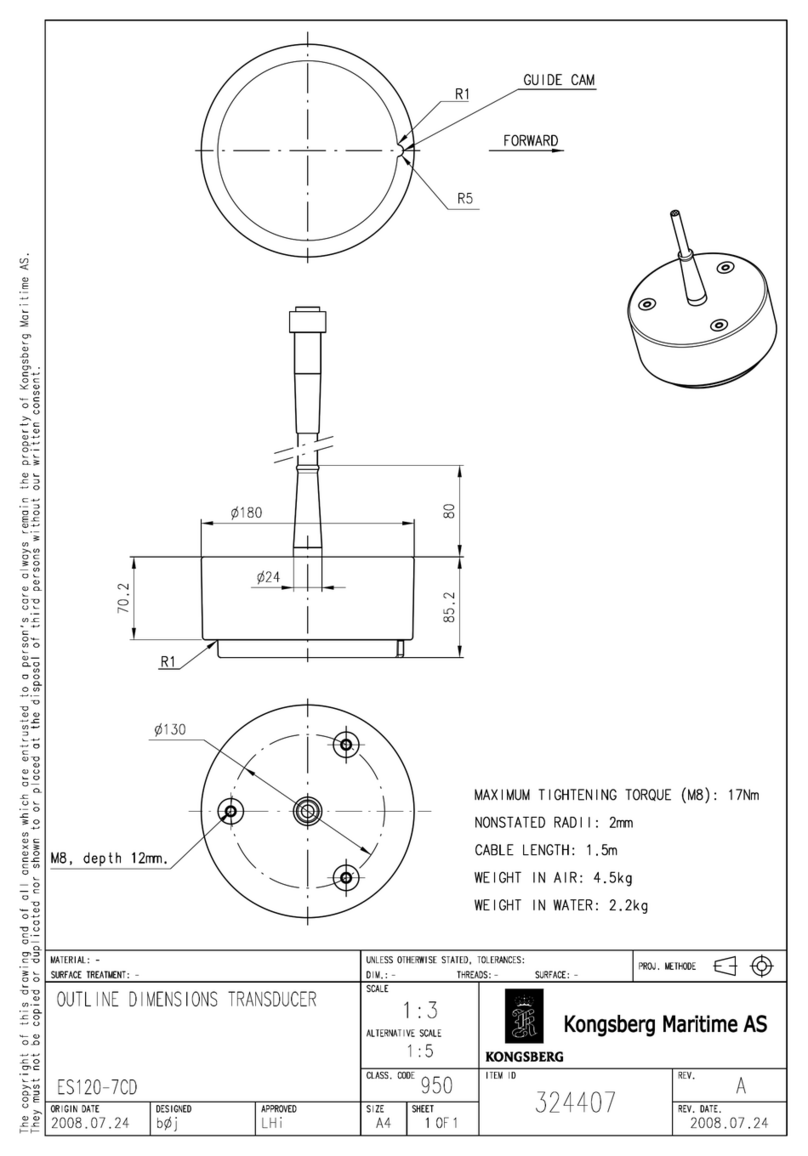
Simrad
Simrad ES120-7CD - REV A Dimensions
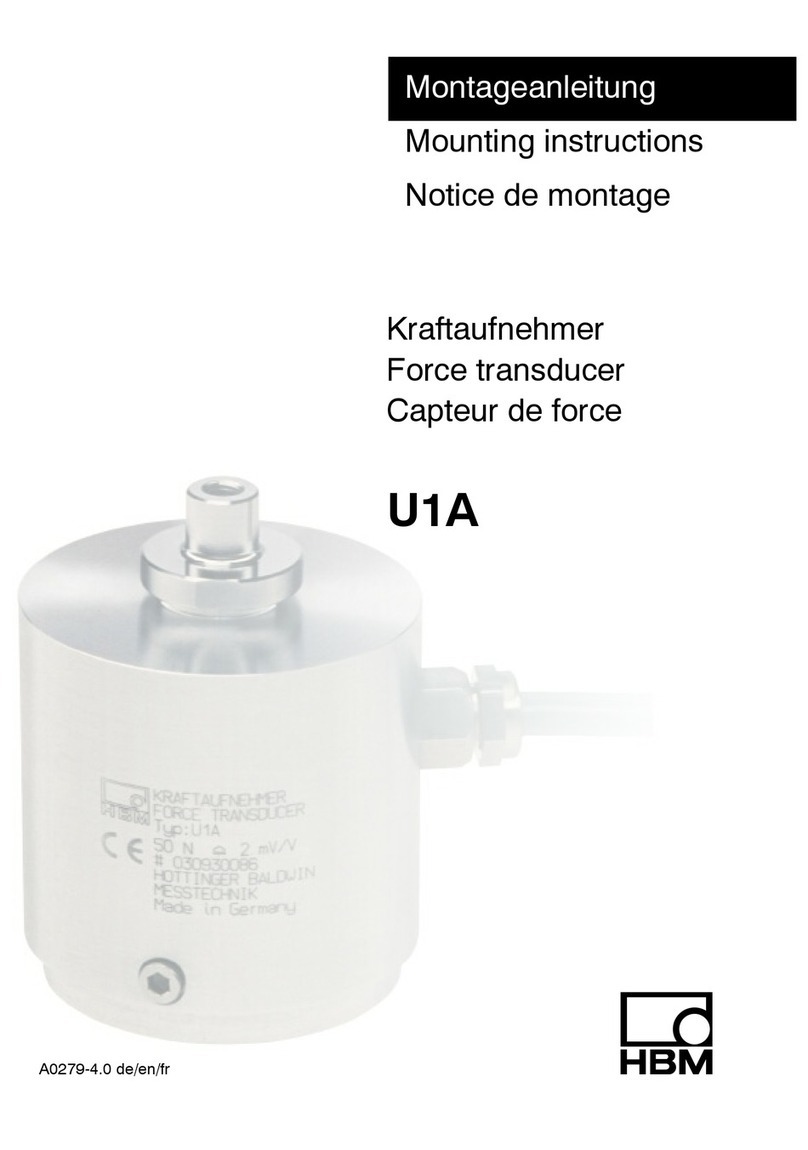
HBM
HBM U1A Mounting instructions
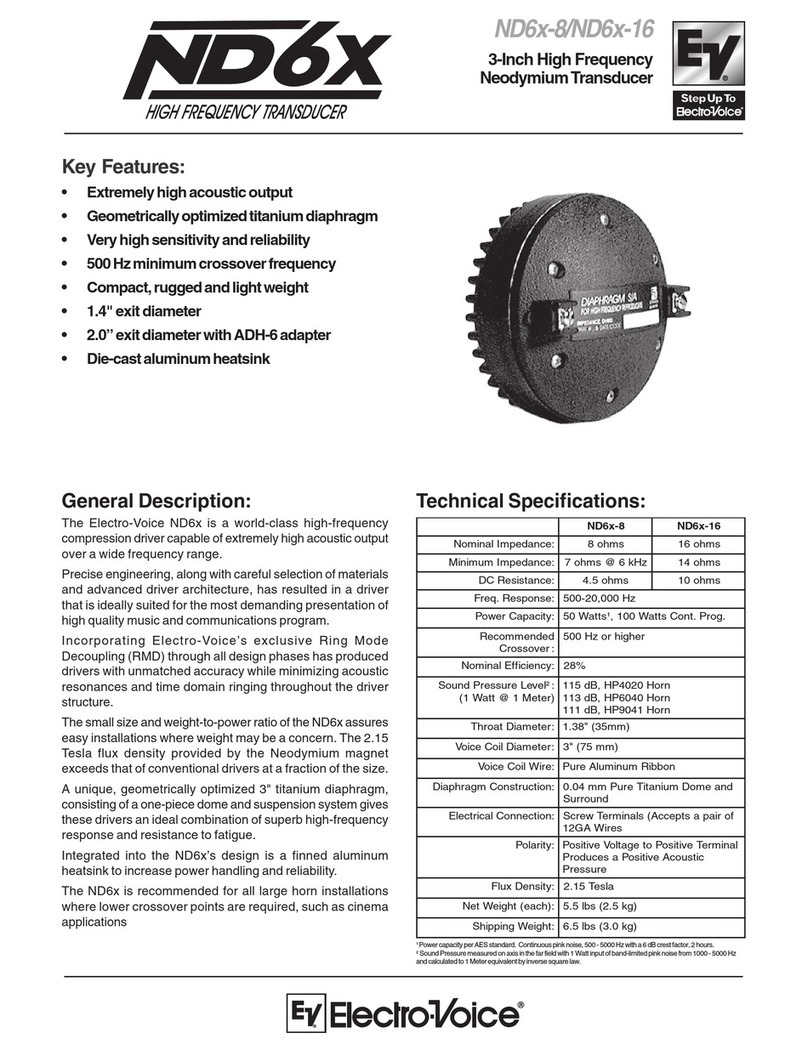
Electro-Voice
Electro-Voice 3-Inch High Frequency Neodymium Transducer... Technical specifications