Aceinna IMU383 Series User manual

IMU383 Series User’s Manual
Doc# 7430-1398-01
Page iii
Revision History
Date
Document
Revision
Firmware
Applicability
Description
Author(s)
Aug 22,
2019
Rev. A
v1.1.x
Draft release of IMU383
manual
Joseph Motyka
Dec. 9,
2019
Rev. B
v1.1.3
Updates to manual to
describe fault detection and
settings
Joseph Motyka
Dec. 18,
2019
Rev. C
v1.1.4
Fixed links to and
formatting of tables and
figures.
Joseph Motyka
Downloaded From Oneyac.com

IMU383 Series User’s Manual
Page iv
Doc# 7430-1398-01
Table of Contents
1Introduction ..............................................................................................................................1
Manual Overview..............................................................................................................1
Overview of the IMU383 Series Inertial Measurement Unit ............................................2
2Interface....................................................................................................................................3
Electrical Interface ............................................................................................................3
2.1.1 Connector and Mating Connector..............................................................................3
2.1.2 Power Input and Power Input Ground........................................................................4
2.1.3 Serial Data Interface...................................................................................................4
2.1.4 Reserved –Factory Use Only.....................................................................................5
Mechanical Interface.........................................................................................................5
3Theory of Operation .................................................................................................................6
IMU383 Series Default Coordinate System......................................................................8
3.1.1 Advanced Settings......................................................................................................8
IMU383 Theory of Operation ...........................................................................................9
3.2.1 Sensor Fault Detection:..............................................................................................9
3.2.2 IMU383 Advanced Settings.....................................................................................11
3.2.3 IMU383 Built-In Test ..............................................................................................11
4IMU383 SPI Port Interface Definition ...................................................................................13
IMU383 Register Map.....................................................................................................13
IMU383 SPI Register Read Methodology ......................................................................14
4.2.1 IMU383 SPI Port Polled-Mode Read.......................................................................15
4.2.2 IMU383 SPI Port Burst-Mode Read........................................................................15
Output Data Scaling ........................................................................................................18
System Registers .............................................................................................................19
Diagnostic Status Register...............................................................................................19
Sensors status registers....................................................................................................20
IMU383 SPI Register Write Methodology......................................................................20
Configuration Registers...................................................................................................21
4.8.1 Data-Ready...............................................................................................................21
4.8.2 Output Data Rate......................................................................................................21
4.8.3 Rate-Sensor Scaling and Low-Pass Filter................................................................22
4.8.4 Axis Orientation Settings.........................................................................................24
4.8.5 Saving the Configuration to EEPROM....................................................................24
Downloaded From Oneyac.com

IMU383 Series User’s Manual
Doc# 7430-1398-01
Page v
4.8.6 Hardware and Software Version..............................................................................25
4.8.7 Sensor Control registers...........................................................................................25
4.8.8 Fault detection Control registers..............................................................................26
Suggested Operation........................................................................................................26
4.9.1 Startup Timing .........................................................................................................26
4.9.2 SPI Timing...............................................................................................................27
Signal Synchronization....................................................................................................28
Bootloader.......................................................................................................................29
5IMU383 UART Port Interface Definition ..............................................................................30
General Settings ..............................................................................................................30
Number Formats..............................................................................................................30
Packet Format..................................................................................................................31
5.3.1 Packet Header...........................................................................................................31
5.3.2 Packet Type..............................................................................................................31
5.3.3 Payload Length.........................................................................................................32
5.3.4 Payload.....................................................................................................................32
5.3.5 16-bit CRC-CCITT ..................................................................................................32
5.3.6 Messaging Overview................................................................................................32
6IMU383 Standard UART Port Commands and Messages .....................................................34
Link Test..........................................................................................................................34
6.1.1 Ping Command.........................................................................................................34
6.1.2 Ping Response..........................................................................................................34
6.1.3 Echo Command........................................................................................................34
6.1.4 Echo Response.........................................................................................................34
Interactive Commands.....................................................................................................34
6.2.1 Get Packet Request ..................................................................................................35
6.2.9 Error Response.........................................................................................................35
Output Packets (Polled)...................................................................................................35
6.3.1 Identification Data Packet........................................................................................35
6.3.2 Version Data Packet.................................................................................................36
6.3.3 Test 0 (Detailed BIT and Status) Packet..................................................................36
Output Packets (Polled or Continuous)...........................................................................37
6.4.1 Scaled Sensor Data Packet 0....................................................................................37
6.4.2 Scaled Sensor Data Packet 1 (Default IMU Data)...................................................38
Downloaded From Oneyac.com

IMU383 Series User’s Manual
Page vi
Doc# 7430-1398-01
7IMU383 Advanced UART Port Commands...........................................................................40
Configuration Fields........................................................................................................40
Continuous Packet Type Field.........................................................................................41
Digital Filter Settings ......................................................................................................41
Orientation Field..............................................................................................................41
Fault-Detection Fault-Causation Fields...........................................................................42
Fault-Detection Enable/Disable.......................................................................................43
Commands to Program Configuration.............................................................................43
7.7.1 Write Fields Command............................................................................................43
7.7.2 Set Fields Command................................................................................................44
Read Fields Command ....................................................................................................45
Read Fields Response......................................................................................................45
Get Fields Command.......................................................................................................46
Get Fields Response........................................................................................................46
8IMU383 Advanced UART Port BIT ......................................................................................48
Built In Test (BIT) and Status Fields ..............................................................................48
Master BIT and Status (BITstatus) Field.........................................................................49
hardwareBIT Field ..........................................................................................................49
softwareDataBIT Field....................................................................................................50
hardwareStatus Field.......................................................................................................50
sensorStatus Field............................................................................................................50
9IMU383 BOOTLOADER ......................................................................................................51
Updating firmware over UART Interface .......................................................................51
9.1.1 Jump to BootLoader Command ...............................................................................51
9.1.2 Write APP Command...............................................................................................51
9.1.3 Jump to Application command ................................................................................52
Updating firmware using the SPI Interface.....................................................................52
9.2.1 Boot Mode Registers................................................................................................52
9.2.2 Boot Mode Status Register (0x78)...........................................................................53
9.2.3 Boot Command Register (0x7A)..............................................................................54
9.2.4 Boot Data Register (0x7C).......................................................................................55
9.2.5 Boot Loading Sequence ...........................................................................................56
10 Warranty and Support Information.....................................................................................57
10.3.1 Authorization............................................................................................................57
Downloaded From Oneyac.com

IMU383 Series User’s Manual
Doc# 7430-1398-01
Page vii
10.3.2 Identification and Protection....................................................................................57
10.3.3 Sealing the Container...............................................................................................58
10.3.4 Marking....................................................................................................................58
Appendix A: Installation and Operation of NAV-VIEW ..............................................................59
NAV-VIEW Computer Requirements .......................................................................................59
Install NAV-VIEW.................................................................................................................59
Setting up NAV-VIEW..............................................................................................................59
Data Recording...........................................................................................................................60
Data Playback.............................................................................................................................61
Raw Data Console......................................................................................................................61
Packet Statistics View................................................................................................................62
Unit Configuration .....................................................................................................................63
Advanced Configuration............................................................................................................64
Bit Configuration........................................................................................................................65
Read Unit Configuration............................................................................................................66
Appendix B: Sample Packet-Parser Code......................................................................................70
Overview....................................................................................................................................70
Code listing ................................................................................................................................71
Appendix C: Sample Packet Decoding..........................................................................................78
Downloaded From Oneyac.com

IMU383 Series User’s Manual
Page viii
Doc# 7430-1398-01
About this Manual
The following symbols are used to provide additional information.
NOTE
Note provides additional information about the topic.
EXAMPLE
This symbol indicates an example that will help the reader understand the terminology.
IMPORTANT
This symbol defines items that have significant meaning to the user
WARNING
The user should pay particular attention to this symbol. It means there is a chance that physical
harm could happen to either the person or the equipment.
This manual uses the following paragraph heading formats:
1 Heading 1
1.1 Heading 2
1.1.1 Heading 3
1.1.1.1 Heading 4
Normal
Downloaded From Oneyac.com

IMU383ZA Series User’s Manual
________________________________________________________________________
Doc# 7430-1398-01 Page 1
1Introduction
Manual Overview
This manual describes ACEINNA’s IMU383 IMU Inertial Measurement Unit. The IMU383 will
be referred to as “the unit” frequently in this document.
For users wishing to get started quickly, please refer to the two-page quick start guide included
with each evaluation kit shipment. Table 1 highlights the content in each section and suggests
how to use this manual.
Table 1 Manual Content
Manual Section
Who Should Read?
Section 1:
Manual Overview
All customers should read sections 1.1 and 1.2.
Section 2:
Interface
Customers designing the electrical and mechanical interface to the IMU383
series products should read Section 2.
Section 3:
Theory of Operation
All customers should read Section 3.
Section 4:
SPI Port Interface
Customers designing the software interface to the IMU383 series products
SPI Port should review Section 4.
Section 5-8:
UART Port Interface
Customers designing the software interface to the IMU383 series products
UART Port should review Sections 5-8.
Section 9:
IMU383 Bootloader
Customers that intend to update Aceinna firmware in the unit should read
Section 9.
Section 10:
Warranty and Support Information
All customers should read Section 10.
Appendix A:
Installation and Operation of NAV-VIEW
All customers should read Appendix A.
Appendix B:
Sample Packet-Parser Code
All customers that intend to create scripts to interface with serial messages
should read Appendix B
Appendix C:
Sample Packet Decoding
All customers that intend to create scripts to interface with serial messages
should read Appendix C
Downloaded From Oneyac.com

IMU383 Series User’s Manual
________________________________________________________________________
Doc# 7430-1398-01 Page 2
Overview of the IMU383 Series Inertial Measurement Unit
This manual describes the use of ACEINNA’s IMU383 and is intended to be used as a detailed
technical reference and operating guide. ACEINNA’s IMU383 Series products combine the latest
in high-performance commercial MEMS (Micro-electromechanical Systems) sensors and digital
signal processing techniques to provide a small, cost-effective alternative to existing IMU
systems.
The IMU383 Series is ACEINNA’s fifth generation of MEMS-based Inertial Systems, building
on over a decade of field experience, and encompassing thousands of deployed units and millions
of operational hours in a wide range of land, marine, airborne, and instrumentation applications.
It is designed for OEM applications.
At the core of the IMU383 Series is a trio of rugged 6-DOF (Degrees of Freedom) MEMS inertial
sensor clusters. Each 6-DOF MEMS inertial sensor cluster includes three axes of MEMS angular
rate sensing and three axes of MEMS linear acceleration sensing. These sensors are based on
rugged, field proven silicon bulk micromachining technology. Each sensor within the cluster is
individually factory calibrated for temperature and non-linearity effects during ACEINNA’s
manufacturing and test process using automated thermal chambers and rate tables.
The differentiating feature of the IMU383 Series is the trio of redundant 6-DOF MEMS sensor
clusters. This redundancy has two direct benefits:
1) Combining multiple sensor reading improves the noise characteristics of the output signal
2) Using more than one sensor enables the unit to operate through a single sensor-chip
failure by detecting and voting out the failed part. Failures include stuck or railed
readings as well as sustained inconsistency between the three sensor sets.
Another unique feature of the IMU383 Series is the extensive field configurability of the units.
This field configurability allows the IMU383 Series of Inertial Systems to satisfy a wide range of
applications and performance requirements with a single mass produced hardware platform. The
basic configurability includes parameters such as baud rate (UART), clock speed (SPI), packet
type, and update rate, and the advanced configurability includes the defining of custom axes.
The IMU383 Series module is packaged in a lightweight, rugged, unsealed metal enclosure that is
designed for cost-sensitive commercial and OEM applications. The unit can be configured to
output data over a SPI Port or a low level UART serial port. The port choice is user controlled by
grounding the appropriate pin on the connector. ACEINNA’s NAV-VIEW 3.X Windows
application supports using the unit low level UART data port NAV-VIEW 3.X is a powerful
Windows-based operating tool that provides complete field configuration, diagnostics, charting of
sensor performance, and data logging with playback.
Downloaded From Oneyac.com

IMU383ZA Series User’s Manual
________________________________________________________________________
Doc# 7430-1398-01 Page 3
2Interface
Electrical Interface
2.1.1 Connector and Mating Connector
The unit main connector is a SAMTEC FTM-110-02-F-DV-P defined in Figure 1. The SAMTEC
CLM-110-02 mating connector is compatible with the IMU383unit main connector.
Figure 1 IMU383 Interface Connector
Table 2 Interface Connector Pin Definition IMU383
Pin
Pin Description (IMU383)
1
Inertial-Sensor Sampling Indicator (sampling
upon falling edge)
2
Synchronization Input (1 kHz Pulse used to
synchronize SPI Comm). If used, this clock
should be 1kHz +/- 0.1%
3
SPI Clock (SCLK) / UART TX
4
SPI Data Output (MISO) / UART RX
5
SPI Data Input (MOSI)
6
SPI Chip Select (SS)
7
Data Ready (SPI Communication Data Ready) /
SPI-UART Port Select
Downloaded From Oneyac.com

IMU383 Series User’s Manual
________________________________________________________________________
Doc# 7430-1398-01 Page 4
8
External Reset (NRST)
9
Reserved –factory use only
10
Power VIN (3-5 VDC)
11
Power VIN (3-5 VDC)
12
Power VIN (3-5 VDC)
13
Power GND
14
Power GND
15
Power GND
16
Reserved –factory use only
17
Reserved
18
Reserved –factory use only
19
Reserved
20
Reserved –factory use only
2.1.2 Power Input and Power Input Ground
Power is applied to the unit on pins 10 through 15. Pins 13-15 are ground; Pins 10-12 accepts 3
to 5 VDC unregulated input. Note that these are redundant power ground input pairs.
WARNING
Do not reverse the power leads or damage may occur. Do not add greater than 5.5 volts on the
power pins or damage may occur. This system has no reverse voltage or over-voltage protection.
2.1.3 Serial Data Interface
The user can select the serial interface used with the unit by controlling the logic level on
connector pin 7 at system startup. If pin 7 is left floating then the unit is configured for SPI
communications on pins 3-6. Pin 7 is set as an output and used as the DATA READY discrete
for SPI communications. Additionally, the user can synchronize the output data on the SPI port
by providing a 1 kHz input pulse on Pin 2. For the complete SPI interface definition, please refer
to Section 4.
If the connector pin 7 is grounded then the unit is configured for low-level UART output on pins
3 and 4. This is a standard UART asynchronous output data port. For the complete UART
interface definition, please refer to Sections 5-8. Note that the two output port interface methods
are controlled independently from each other. The UART port output controls apply only to data
being output over the UART port, and the SPI output controls apply only to data being output
over the SPI port.
Downloaded From Oneyac.com

IMU383ZA Series User’s Manual
________________________________________________________________________
Doc# 7430-1398-01 Page 5
2.1.3.1 SPI Com Synchronization Input
Pin 2 can be used as a sync pulse to force synchronization of sensor data collection to a 1 kHz
rising-edge signal for output over the SPI port. See Section 4.10 for a more complete description.
2.1.4 Reserved –Factory Use Only
During normal operation of the unit no connection is made to the Reserved –factory use only
pins. These pins have internal pull-up mechanisms and must have no connections for the unit to
operate properly.
Mechanical Interface
The IMU383 mechanical interface is defined by the outline drawing in Figure 2.
Figure 2 IMU383 Outline Drawing
NOTES UNLESS OTHERWISE STATED:
1) MATING CONNECTOR SAMTEC CLM-110-02
2) DIMENSION TO CENTROID OF PIN ONE
Downloaded From Oneyac.com

IMU383 Series User’s Manual
________________________________________________________________________
Doc# 7430-1398-01 Page 6
3Theory of Operation
This section of the manual covers detailed theory of operation for the IMU383
Figure 3 shows the IMU383 Series hardware block diagram. At the core of the IMU383 Series is
a rugged 6-DOF (Degrees of Freedom) MEMS inertial sensor cluster. The 6-DOF MEMS inertial
sensor cluster includes three axes of MEMS angular rate sensing and three axes of MEMS linear
acceleration sensing. These sensors are based on rugged, field proven silicon bulk
micromachining technology.
Each sensor within the cluster is individually factory calibrated using ACEINNA’s automated
manufacturing process. Sensor errors are compensated for temperature bias, scale factor, non-
linearity and misalignment effects using a proprietary algorithm from data collected during
manufacturing. Accelerometer and rate gyro sensor bias shifts over temperature (-40 0C to +71
0C) are compensated and verified using calibrated thermal chambers and rate tables.
The 6-DOF inertial sensor cluster data is fed into a high speed signal processing chain, which
provides the sensor compensation, digital filtering, and sensor fault detection. Measurement data
packets are available at fixed continuous output rates or on a polled basis from the SPI port or the
UART port. The SPI port outputs data via registers, and the user can perform polled reads of
each register, or a block burst read of a set of predefined registers. Output data over the SPI port
can be synchronized to an external 1 kHz pulse. The complete SPI interface is defined in Section
4. The UART port outputs data packets are asynchronous and defined in Sections 5-8.
Sensors
High-Speed
Sampling
+
Sensor
Compensation, Calibration
and Filtering
X/Y/Z
Gyros
X/Y/Z
Accelerometers
Temperature
Sensor
UART1
SPI SPI Register Read/Write
· X/Y/Z Acceleration
· X/Y/Z Angular Rate
ACEINNA Serial Protocol
· X/Y/Z Acceleration
· X/Y/Z Angular Rate
1KHz Pulse
(+/- 0.01Hz)
Processor
Figure 3 IMU383 Series Hardware Block Diagram
Figure 4 shows the software block diagram. The 6-DOF inertial sensor cluster data is fed into a
high speed 200Hz signal processing chain. These 6-DOF signals pass through one or more of the
processing blocks and these signals are converted into output measurement data as shown.
Measurement data packets are available at fixed continuous output rates or on a polled basis.
As shown in the software block diagram, the IMU383 Series has a unit setting and profile block
which configures the algorithm to user and application specific needs. This feature is one of the
Downloaded From Oneyac.com

IMU383ZA Series User’s Manual
________________________________________________________________________
Doc# 7430-1398-01 Page 7
more powerful features in the IMU383 Series architecture as it allows the IMU383 Series to work
in a wide range of commercial applications by settings different modes of operation for the
IMU383 Series.
6-DOF Sensor Cluster
X/Y/Z Body
Angular Rates
Unit Settings & Profile
· Communication Settings
· Axes Orientation
· Low Pass Filter
· Programmable BIT Alerts
X/Y/Z Body
Accelerations
Measurement Data
Available to User
(Fixed Rate or Polled)
IMU Scaled Packets
(S0, S1)
200Hz
Sensor Processing Sensor
Filtering
User Outputs
User Inputs
Sensor Inputs
Processing
Built-In Test &
Status Data
Status
Packet
(T0)
Sensor
Calibration
Axes Rotation
Figure 4 IMU383 Series Software Block Diagram
Downloaded From Oneyac.com

IMU383 Series User’s Manual
________________________________________________________________________
Doc# 7430-1398-01 Page 8
IMU383 Series Default Coordinate System
The IMU383 Series Inertial System default coordinate systems are shown in Figure 5. As with
many elements of the IMU383 Series, the coordinate system is configurable with either NAV-
VIEW or by sending the appropriate serial commands over the UART port. These configurable
elements are known as Advanced Settings. This section of the manual describes the default
coordinate system settings of the IMU383 Series when it leaves the factory.
Figure 5 IMU383 Default Coordinate Frame
The axes form an orthogonal SAE right-handed coordinate system. Acceleration is positive when
it is oriented towards the positive side of the coordinate axis. For example, with a IMU383 Series
product sitting on a level table, it will measure zero g along the x- and y-axes and -1 g along the
z-axis. Normal Force acceleration is directed upward, and thus will be defined as negative for the
IMU383 Series z-axis.
The angular rate sensors are aligned with these same axes. The rate sensors measure angular
rotation rate around a given axis. The rate measurements are labeled by the appropriate axis. The
direction of a positive rotation is defined by the right-hand rule. With the thumb of your right
hand pointing along the axis in a positive direction, your fingers curl around in the positive
rotation direction. For example, if the IMU383 Series product is sitting on a level surface and you
rotate it clockwise on that surface, this will be a positive rotation around the z-axis. The x- and y-
axis rate sensors would measure zero angular rates, and the z-axis sensor would measure a
positive angular rate.
3.1.1 Advanced Settings
The IMU383 Series Inertial Navigation Units have a number of advanced settings that can be
changed. All units support baud rate
1
, power-up output packet type, output rate, sensor low pass
1
Note: certain combinations of baud-rate, packet-type, and output data rate are invalid because the time to transmit the data exceeds a
limit on the permissible message length. The IMU383 limits the output packet width to 80% of the time between data packets. For
instance, if the packet is output every 10 milliseconds (100 Hz) then the packet width must be less than 8 milliseconds or the
combination is not allowed. This prevents messages from overlapping and causing communication problems. For this reason, 57.6
kbps and higher baud-rates are suggested.
Downloaded From Oneyac.com

IMU383ZA Series User’s Manual
________________________________________________________________________
Doc# 7430-1398-01 Page 9
filtering, and custom axes configuration. The units can be configured using NAV-VIEW, as
described in Appendix A, or directly with serial commands as described in Sections 5-8.
IMU383 Theory of Operation
The unit provides inertial rate and acceleration data in 6-DOF (six degrees of freedom). The unit
signal processing chain consists of the 6-DOF sensor cluster, programmable low-pass filters, and
a signal processing component for sensor error compensation. The unit has a UART input/output
port and a SPI input/output port.
After passing through a digitally controlled programmable low-pass filter, the rate and
acceleration sensor signals are obtained at 200 Hz. The factory calibration data, stored in
EEPROM, is used by the processor to remove temperature bias, misalignment, scale factor errors,
and non-linearities from the sensor data. Additionally any advanced user settings such as axes
rotation are applied to the IMU data. Finally, sensor fault detection is performed on the sensor
signals and the individual sensor signals are combined to form a signal with reduced noise
characteristics.
The 200Hz IMU data is continuously maintained inside the unit, and is available at 200Hz on the
SPI output port registers. Digital IMU data is output over the UART port at a selectable fixed rate
(100, 50, 25, 20, 10, 5 or 2 Hz) or on as-requested basis using the GP, ‘Get Packet’ command.
The digital IMU data is available in several measurement packet formats including Scaled Sensor
Data (‘S1’ Packet). In the Scaled Sensor Data (‘S1’ Packet), data is output in scaled engineering
units. See Section 6 of the manual for full packet descriptions.
3.2.1 Sensor Fault Detection:
New for the IMU383 is the incorporation of triple-redundant accelerometer and gyro sensors,
which enables sensor fault detection. The fault detection routine incorporated into the firmware
continually monitors the output of the three sensor chips. If an outlier is detected in the output,
the routine continues to monitor the sensors until the part is deemed failed. The Fault Tolerant
Time Interval (FTTI) for such a failure is set to 300 msec, however the actual detection time
could be changed if needed. Contact the factory for more information.
Configuration Field Settings for Sensor Enable and Sensor Select:
The same mechanism that enables the firmware to vote out a failed or underperforming sensor
also enables the user to turn on or off a sensor chip or exclude an enabled sensor from the output,
if desired (Section 7.1). When communicating with the device using UART, field 0x42 controls
the sensor enable function while field 0x43 controls which sensors are included in the combined
sensor output (SPI communication protocol uses SPI registers 0x1A, 0x1B, and 0x1C to define
which sensors are active, as described in Sections 4.1 and 4.8.7). . Nominally both fields are set
to 0x7, representing the bit pattern 111 (a one indicates enabled while a zero indicates disabled).
In this bit pattern, the least-significant bit (the bit on the far right) controls sensor chip 1, the
most-significant bit (on the far left) controls sensor chip 3, and the middle bit controls sensor 2.
Both fields tells the firmware which sensors to include in the combined sensor output. The
combination is done by averaging the readings from the selected sensors.
Field 0x42 and 0x43 are set via the set-field (SF) or write-field (WF) commands (described in
sections 7.7). In the case of the Sensor Enable Setting, the write-field command must be used as
the part must be reset (either via power-cycling the unit of issuing a software-reset command) in
order for the setting to take effect.
Downloaded From Oneyac.com

IMU383 Series User’s Manual
________________________________________________________________________
Doc# 7430-1398-01 Page 10
When a fault is detected, the system BIT (Section 8.5) will indicate that a fault related to the
sensor fault detection has occurred. This field will not indicate which sensor was removed from
the triad; Fields 0x42 and 0x43 must be read to determine which of the three sensors was
removed from the combination.
Field 0x42: Sensor Enable Setting
Value
Sensor Enable Flag
Description
Sensor #3
Sensor #2
Sensor #1
0x0
0
0
0
All sensors disabled
0x1
0
0
1
Only sensor #1 enabled
0x2
0
1
0
Only sensor #2 enabled
0x3
0
1
1
Sensors #1 and #2 enabled
0x4
1
0
0
Only sensor #3 enabled
0x5
1
0
1
Sensors #1 and #3 enabled
0x6
1
1
0
Sensors #2 and #3 enabled
0x7
1
1
1
All sensors enabled
Field 0x43: Sensor Included in Output
Value
Sensor Inclusion Flag
Description
Sensor #3
Sensor #2
Sensor #1
0x0
0
0
0
No sensors included (output 0.0)
0x1
0
0
1
Only sensor #1 included
0x2
0
1
0
Only sensor #2 included
0x3
0
1
1
Sensors #1 and #2 included
0x4
1
0
0
Only sensor #3 included
0x5
1
0
1
Sensors #1 and #3 included
0x6
1
1
0
Sensors #2 and #3 included
0x7
1
1
1
All sensors included in output
User Settings:
Selecting which sensors are included in the output can be accomplished using either the write-
field or set-field command (WF or SF) over UART. Using the SF command will cause the
setting to take effect immediately; the WF command will require a unit-reset before the output is
modified. Several example commands follow:
To get the values for fields 0x42 and 0x43 stored in RAM, use the Get-Field (GF) command:
5555 4746 05 02 0042 0043 a0d0
To set the value for field 0x43 stored in RAM to 0x1 (output sensor #1 only), use the Set-Field
(SF) command:
5555 5346 05 01 0043 0001 236d
To change the value for field 0x42 in EEPROM to 0x1 (enable sensor #1 only), use the Write-
Field (WF) command:
Downloaded From Oneyac.com

IMU383ZA Series User’s Manual
________________________________________________________________________
Doc# 7430-1398-01 Page 11
5555 5746 05 01 0042 0001 1b30
Section 4 describes how to set these fields via the SPI interface.
3.2.2 IMU383 Advanced Settings
The unit advanced settings are described in Table 3. All of the advanced settings are accessible
through NAV-VIEW under the Configuration Menu, Unit Configuration settings. For a full
definition of the SPI port please see section 4.
Table 3 IMU383 Advanced Settings
Setting
Default
Comments
Baud Rate
38,400 baud
57600, 115200, and 230400 also available
Packet Type
S0
S1 also available
Packet Rate
100Hz
This setting sets the rate at which selected Packet Type, packets are output. If
polled mode is desired, then select Quiet. If Quiet is selected, the unit will only
send measurement packets in response to GP commands.
Orientation
See Figure 5
To configure the axis orientation, select the desired measurement for each
axis: NAV-VIEW will show the corresponding image of the unit, so it easy to
visualize the mode of operation. Refer to Section 7.4 Orientation Field settings
for the twenty four possible orientation settings.
Filter Settings
(unfiltered, 2, 5,
10, 20, 25, 40 50
Hz).
20 Hz
The low pass filters are set to a default of 20 Hz for the accelerometers, and 20
Hz for the angular rate sensors. There is one filter setting for all three angular
rate sensors. There is one filter setting for all three accelerometers. Setting
either to zero disables the low-pass filter.
BIT
See section 8.1
NOTE on Filter Settings
Generally, there is no reason to change the low-pass filter settings on the unit or other IMU383
Series Inertial Systems. However, when an IMU383 Series product is installed in an environment
with a lot of vibration, it can be helpful to reduce the vibration-based signal energy and noise
prior to further processing on the signal. Installing the unit in the target environment and
reviewing the data with NAV-VIEW can be helpful to determine if changing the filter settings
would be helpful. Although the filter settings can be helpful in reducing vibration based noise in
the signal, low filter settings (e.g., 5Hz) also reduce the bandwidth of the signal, which can wash
out the signals containing the dynamics of a target. Therefore, caution should be used when
changing the filter settings.
3.2.3 IMU383 Built-In Test
The unit Built-In Test capability allows users of the unit to monitor health, diagnostic, and system
status information of the unit in real-time. The Built-In Test information consists of a BIT word
(2 bytes) transmitted in every measurement packet. In addition, there is a diagnostic packet ‘T0’
that can be requested via the Get Packet ‘GP’ command which contains a complete set of status
for each hardware and software subsystem in the unit. See Sections 5-8 for details on the ‘T0’
packet.
The BIT word, which is contained within each measurement packet, is detailed below. The LSB
(Least Significant Bit) is the Error byte, and the MSB (Most Significant Bit) is a Status byte with
Downloaded From Oneyac.com

IMU383 Series User’s Manual
________________________________________________________________________
Doc# 7430-1398-01 Page 12
programmable alerts. Internal health and status are monitored and communicated in both
hardware and software. The ultimate indication of a fatal problem is the masterFail flag.
The masterStatus flag is a configurable indication that can be modified by the user. This flag is
asserted as a result of any asserted alert signals which have been enabled. See Advanced BIT
(Section 8) for details regarding the configuration of the masterStatus flags. Table 4 shows the
BIT definition and default settings for BIT programmable alerts in the unit.
Table 4 IMU383 Default BIT Status Definition
BITstatus Field
Bits
Meaning
Category
masterFail
0
0 = normal, 1 = fatal error has occurred
BIT
HardwareError
1
0 = normal, 1= internal hardware error
BIT
comError
2
0 = normal, 1 = communication error
BIT
softwareError
3
0 = normal, 1 = internal software error
BIT
Reserved
4:7
N/A
N/A
masterStatus
8
0 = nominal, 1 = Alert, Sensor Over Range
Status
hardwareStatus
9
Disabled
Status
comStatus
10
Disabled
Status
softwareStatus
11
Disabled
Status
sensorStatus
12
0 = nominal, 1 = Sensor Over Range
Status
Reserved
13:15
N/A
N/A
The unit also allows a user to configure the Status byte within the BIT message. To configure the
word, select the BIT Configuration tab from the Unit Configuration menu. The dialog box allows
selection of which status types to enable (hardware, software, sensor, and comm). In the case of
the unit, which has fewer features and options than other Acienna measurement products, the only
meaningful parameter is sensor over-range. It is recommended that users leave the default
configuration, which is sensorStatus enabled and flag on sensor over-range. The over-range only
applies to the rotational rate sensors. Because instantaneous acceleration levels due to vibration
can exceed the accelerometer sensor range in many applications, none of the IMU383 Series
products trigger over-range on accelerometer readings.
Downloaded From Oneyac.com
Other manuals for IMU383 Series
1
This manual suits for next models
2
Table of contents
Popular Control Unit manuals by other brands

Schippers
Schippers MS TagMatic Evo manual

VAT
VAT 25740-QE99-0001 TRANSLATION OF INSTALLATION AND OPERATING INSTRUCTIONS
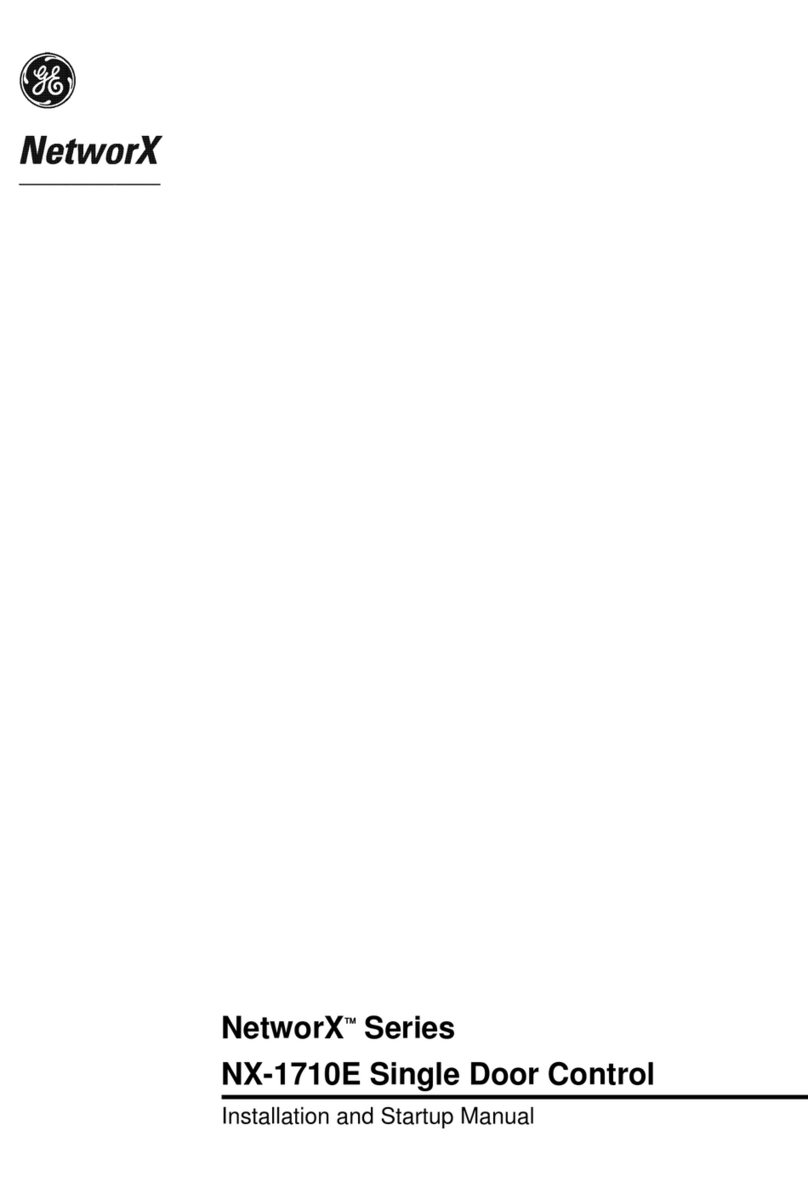
GE
GE NX-1710E - Single Door Control Module Installation and start-up manual
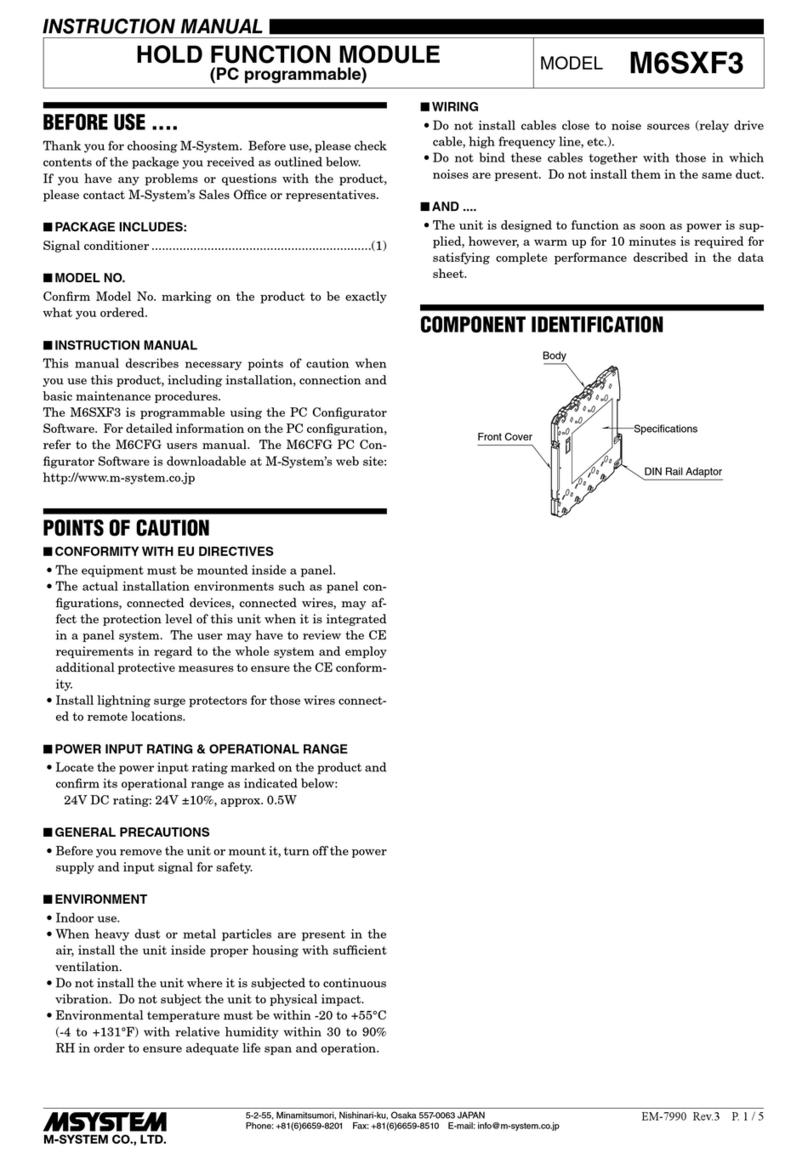
M-system
M-system M6SXF3 instruction manual

Nordmann Engineering
Nordmann Engineering SBC operating instructions
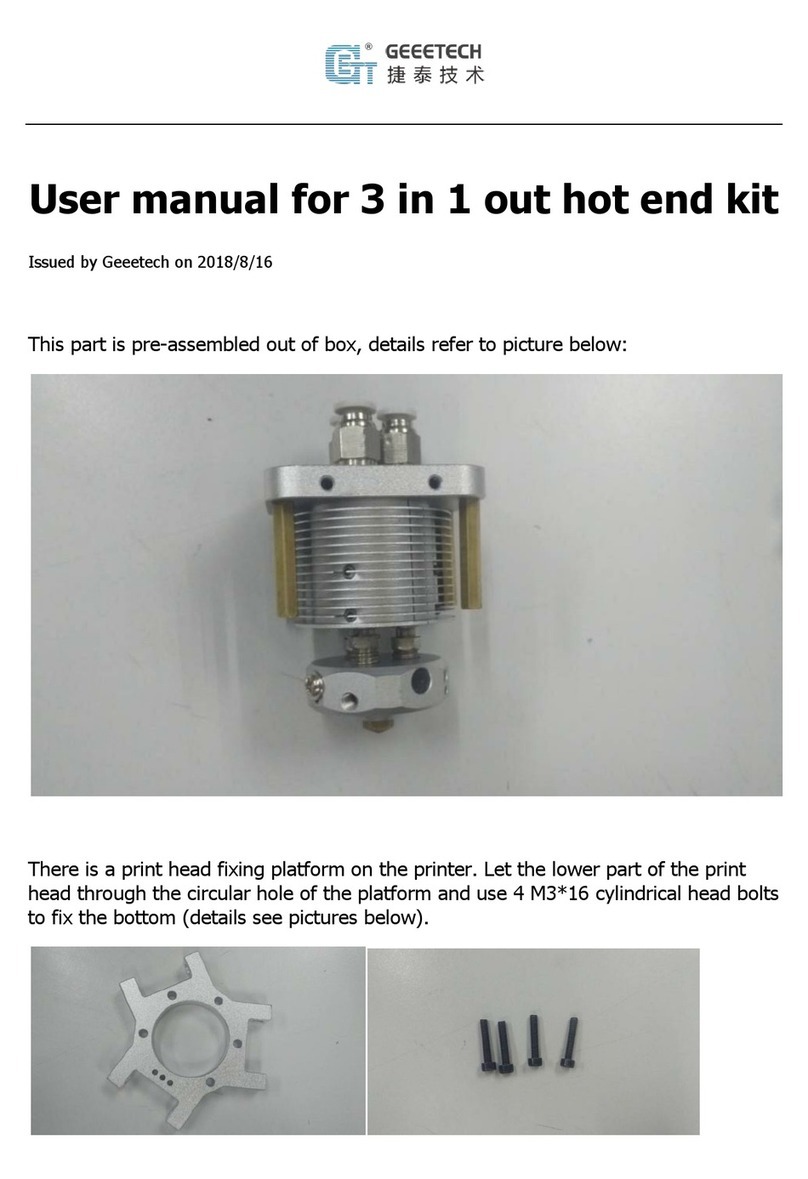
Geeetech
Geeetech 800-001-0554 user manual