AI-Tek Instruments TACHTROL 3 User manual

TACHTROL®3

152 Knotter Drive
P.O.
Box 748
Cheshire, CT USA 06410-0748
www.aitekinstruments.com
Phone: 1-800-643-0643
7/04
Printed in U.S.A.
AI-TEK INSTRUMENTS, LLC
13010-D 7/04
Printed in U.S.A.

TABLE OF CONTENTS
1.0 FOREWORD . . . . . . . . . . . . . . . . . . . . . . . . . . . . . . . . . . . . . . . . . . . . . . . . . . . . . . . . . . . . . . 1
2.0 INTRODUCTION . . . . . . . . . . . . . . . . . . . . . . . . . . . . . . . . . . . . . . . . . . . . . . . . . . . . . . . . . . . . . 1
2.1 MATHEMATICAL FUNCTIONS . . . . . . . . . . . . . . . . . . . . . . . . . . . . . . . . . . . . . . . . . . . . . . . 1
2.1.1 Single Channel Operation . . . . . . . . . . . . . . . . . . . . . . . . . . . . . . . . . . . . . . . . 1
2.1.2 Dual Channel Operation . . . . . . . . . . . . . . . . . . . . . . . . . . . . . . . . . . . . . . . . . 1
2.1.3 Bi-Dlrectlonal Operation . . . . . . . . . . . . . . . . . . . . . . . . . . . . . . . . . . . . . . . . . . 1
2.2 OUTPUTS . . . . . . . . . . . . . . . . . . . . . . . . . . . . . . . . . . . . . . . . . . . . . . . . . . . . . . . . . . . . . . . . . . 2
3.0 THEORY OF OPERATION . . . . . . . . . . . . . . . . . . . . . . . . . . . . . . . . . . . . . . . . . . . . . . . . . . . . . . 2
4.0 HOW TO OPERATE THE TACHTROL®3 TACHOMETER . . . . . . . . . . . . . . . . . . . . . . . . . . . . . . . . . . 4
4.1 FINDING THE SCALING FACTORS . . . . . . . . . . . . . . . . . . . . . . . . . . . . . . . . . . . . . . . . . . . 4
4.1.1 Finding the Scaling Factor For Common Applications . . . . . . . . . . . . . . . . . . 4
Single Channel and Bi-Dlrectlonal . . . . . . . . . . . . . . . . . . . . . . . . . . . . . . . 4
Dual Channel . . . . . . . . . . . . . . . . . . . . . . . . . . . . . . . . . . . . . . . . . . . . . . . 6
4.1.2 Finding The Scaling Factor For Other Applications . . . . . . . . . . . . . . . . . . . . . 6
4.2 SELECTING THE MATHEMATICAL FUNCTIONS . . . . . . . . . . . . . . . . . . . . . . . . . . . . . . . . . . . 6
4.3 DEFINING THE BEHAVIOR OF THE OUTPUTS . . . . . . . . . . . . . . . . . . . . . . . . . . . . . . . . . . . . 7
4.3.1 Display . . . . . . . . . . . . . . . . . . . . . . . . . . . . . . . . . . . . . . . . . . . . . . . . . . . . . . . 7
Autoranglng . . . . . . . . . . . . . . . . . . . . . . . . . . . . . . . . . . . . . . . . . . . . . . . . 7
4.3.2 Analog Output . . . . . . . . . . . . . . . . . . . . . . . . . . . . . . . . . . . . . . . . . . . . . . . . 7
Zero Scale . . . . . . . . . . . . . . . . . . . . . . . . . . . . . . . . . . . . . . . . . . . . . . . . . 7
FullScole . . . . . . . . . . . . . . . . . . . . . . . . . . . . . . . . . . . . . . . . . . . . . . . . . . . 8
4.3.3 Setpolnts . . . . . . . . . . . . . . . . . . . . . . . . . . . . . . . . . . . . . . . . . . . . . . . . . . . . . 8
Setpoint Types . . . . . . . . . . . . . . . . . . . . . . . . . . . . . . . . . . . . . . . . . . . . . . 8
Setpoint Behavior . . . . . . . . . . . . . . . . . . . . . . . . . . . . . . . . . . . . . . . . . . . . 8
Latchlng/Auto Reset . . . . . . . . . . . . . . . . . . . . . . . . . . . . . . . . . . . . . . . . . 9
4.3.4 Sample Set-Ups . . . . . . . . . . . . . . . . . . . . . . . . . . . . . . . . . . . . . . . . . . . . . . . 10
Single Channel Operations . . . . . . . . . . . . . . . . . . . . . . . . . . . . . . . . . . . . 10
Dual Channel Operation . . . . . . . . . . . . . . . . . . . . . . . . . . . . . . . . . . . . . 11
4.4 ENTERING THE CONSTANTS . . . . . . . . . . . . . . . . . . . . . . . . . . . . . . . . . . . . . . . . . . . . . . . 13
4.4.1 Control Features . . . . . . . . . . . . . . . . . . . . . . . . . . . . . . . . . . . . . . . . . . . . . . 13
4.4.2 Turning On The Power . . . . . . . . . . . . . . . . . . . . . . . . . . . . . . . . . . . . . . . . . . 14
4.4.3 Entering The Scaling Factors . . . . . . . . . . . . . . . . . . . . . . . . . . . . . . . . . . . . . 14
4.4.4 Entering The Function Constant . . . . . . . . . . . . . . . . . . . . . . . . . . . . . . . . . . 15
4.4.5 Entering Constants Which Define Output Behavior . . . . . . . . . . . . . . . . . . . 15
Display Output . . . . . . . . . . . . . . . . . . . . . . . . . . . . . . . . . . . . . . . . . . . . . 15
Analog Output . . . . . . . . . . . . . . . . . . . . . . . . . . . . . . . . . . . . . . . . . . . . . 16
Setpoint 1 Output . . . . . . . . . . . . . . . . . . . . . . . . . . . . . . . . . . . . . . . . . . . 16
Setpoint 2 Output . . . . . . . . . . . . . . . . . . . . . . . . . . . . . . . . . . . . . . . . . . . 17
4.5 STORING THE CONSTANTS . . . . . . . . . . . . . . . . . . . . . . . . . . . . . . . . . . . . . . . . . . . . . . . 18
4.6 SELECTING THE INPUT OPTIONS . . . . . . . . . . . . . . . . . . . . . . . . . . . . . . . . . . . . . . . . . . . . 18

5.0 HOW TO INSTALL THE TACHTROL®3 TACHOMETER . . . . . . . . . . . . . . . . . . . . . . . . . . . . . . . . . . 18
5.1 MOUNTING THE INSTRUMENT . . . . . . . . . . . . . . . . . . . . . . . . . . . . . . . . . . . . . . . . . . . . . 18
5.2 PANEL MOUNTING DIMENSIONS . . . . . . . . . . . . . . . . . . . . . . . . . . . . . . . . . . . . . . . . . . . 18
6.0 HOW TO INSTALL THE SPEED SENSOR (S) . . . . . . . . . . . . . . . . . . . . . . . . . . . . . . . . . . . . . . . . . 20
6.1 MOUNTING THE SPEED SENSOR (S) . . . . . . . . . . . . . . . . . . . . . . . . . . . . . . . . . . . . . . . . . 20
6.2 SETTING THE CLEARANCE . . . . . . . . . . . . . . . . . . . . . . . . . . . . . . . . . . . . . . . . . . . . . . . . 20
6.3 TYPICAL WIRING CONNECTIONS FOR AI-TEK SENSORS . . . . . . . . . . . . . . . . . . . . . . . . . 20
6.3.1 Passive Sensors . . . . . . . . . . . . . . . . . . . . . . . . . . . . . . . . . . . . . . . . . . . . . . . . 21
6.3.2 Active Sensors . . . . . . . . . . . . . . . . . . . . . . . . . . . . . . . . . . . . . . . . . . . . . . . . . 22
6.3.3 BI-Directlonal Sensors . . . . . . . . . . . . . . . . . . . . . . . . . . . . . . . . . . . . . . . . . . . 22
7.0 APPENDIX: TIME MODE OPERATION . . . . . . . . . . . . . . . . . . . . . . . . . . . . . . . . . . . . . . . . . . . . 23
SPECIFICATIONS . . . . . . . . . . . . . . . . . . . . . . . . . . . . . . . . . . . . . . . . . . . . . . . . . . . . . . . . . . . 23
INSTALLATION AND WIRING PRACTICES
FOR ELECTRONIC INSTRUMENTATION & CONTROL . . . . . . . . . . . . . . . . . . . . . . . . . . . . . . . . . . . . . . . 25
WARRANTY . . . . . . . . . . . . . . . . . . . . . . . . . . . . . . . . . . . . . . . . . . . . . . . . . . . . . . . . . . . 27

1.0 FOREWORD
The following manual is written for users of the TACHTROL®3 tachometer manufactured by AI-Tek
Instruments. The manual provides easy to follow, step by step instructions for setting up and installing
the instrument. Some knowledge of algebra is helpful but not necessary.
2.0 INTRODUCTION
The TACHTROL®3 tachometer is an applications oriented, single or dual channel computing tach-
ometer which uses the period mode of frequency measurement (time per event).
Used as a single channel tachometer, the TACHTROL®3 tachometer measures the rate of industrial
events, such as the rate at which liquid is passing through a pump, or the rate at which bottles are
passing along a conveyor belt. The tachometer displays these rates in engineering units such as FPS
(feet per second), GPH (gallons per hour), RPM (revolutions per minute), and other rates.*
Used as a dual channel tachometer, the TACHTROL®3 tachometer can read two unrelated speeds
or can compute six mathematical functions from the input signal frequencies of two related speeds.
In addition, the TACHTROL®3 tachometer may be used as a bi-directional tachometer to measure
speed with direction indication (from an AI-Tek bi-directional sensor).
2.1 MATHEMATICAL FUNCTIONS
2.1.1 Single Channel Operation. Used as a single channel instrument, the TACHTROL®3
tachometer can compute Speed A or Speed B.
2.1.2 Dual Channel Operation. Used as a dual channel instrument, the TACHTROL®3
tachometer can compute unrelated Speed A and Speed B. When Speed A
and Speed B are related, the TACHTROL®3 can compute the following math-
ematical functions.
A - B (Difference) A-B x 100 (% Slip)
A
A/B (Ratio)
B/A (Inverse Ratio) B-A x 100 (% Elongation)
A
A + B (Average)
2
2.1.3 Bi-Directional Operation. Used as a bi-directional instrument, the TACHTROL®3
tachometer can compute +A, -A (opposite direction).
*Note: Like most conventional tachometers, the TACHTROL®3 tachometer comes
from the factory ready to read RPM from a single, 60 pulse per revolution gear.
2.2 OUTPUTS
Any of the mathematical functions may be assigned independently to:
• An L.E.D. Display which updates every 0.5 seconds.
• An optional output (a current source): either 4 to 20mA or 0 to 20mA.
• 1 or 2 optional Relay Setpoints (2 form C contacts) whlch can be used to trlgger external
events such as alarms. All forms of relay logic can be selected and adjusted In the field.
1

3.0 THEORY OF OPERATION
Speed sensors (transducers such as AI-Tek series 70085, H or BH) are placed near ferrous metal tar-
gets such as gears. The sensors generate repeating electrical pulses (input signal frequencies) whose
repetition rates are proportional to the rates of the event. The TACHTROL®3 tachometer measures
these rates in the number of pulses per second. The tachometer’s microcomputer allows you to scale
the input signal frequencies to appropriate display values, select and route the mathematical
functions to the outputs, and define the behavior of each output. Figure 1 illustrates the flow of data
in the TACHTROL®3 tachometer.
Figure 1, Data Flow Diagram
2
C5 - ADDITIONAL
SCALING FACTOR
C12-DIGIT 1
DECIMAL LOCATION
C6-ZERO SCALE
C7-FULL SCALE
C12-DIGIT 5
0-20 / 4-20 mA
C8-SETPOINT
C10-DIGITS 1 & 2
% HYSTERESIS
C12-DIGIT 2
RELAY LOGIC
C9-SETPOINT
C10-DIGITS 3 & 4
% HYSTERESIS
C12-DIGIT 3
RELAY LOGIC
FUNC. K1 S.P.
= DEVIATION
FUNC. K2 S.P.
= DEVIATION
C12-DIGIT 4
SER. OUTPUT INFO
DIGIT 1
FUNCTION C11 DIGIT 2
0=OFF
1 = A
2 = B
3 = A-B
4 = +/- A
5 = A/B
6 = B/A
7 = (A+B) / 2 DIGIT 3
8 = (A+B) / Ax100 DIGIT 4
9 = (B-A) / Ax100
C1
XC2
F
A
F
BC3
XC4
ANALOG
DISPLAY
SET-
POINT 1
SET-
POINT 2
SERIAL
OUTPUT
A RESULT
B RESULT

Once you have selected a function for and determined the behavior of each output, you set up
the instrument by entering twelve 4 1/2 digit, signed numbers (called constants) on the thumbwheel
and pushbutton switches on the control panel located behind the Door. These constants are held in
the TACHTROL®3 tachometer’s electrically alterable, read only memory (EAROM) and can be indi-
vidually displayed and altered by a method similar to the setting of a digital watch. You then mount
the instrument, install the speed sensor(s), connect the sensor(s) and the power wiring, and you are
ready to operate. The following chart describes the purpose of each constant (C1thru C12) and lists
the standard constants which are preset in the instrument.
Constant Purpose Std. Constants
C1and C2scale (normalize) the input signal 1.000
frequency from channel A.
C3and C4scale (normalize) the input signal 1.000
frequency from channel B.
C5provides an additional method of scaling. When C5is 1.000
set to standard constant. Display shows the computed
function of channel A or channel B. However, C5can
be altered to convert one engineering unit to another
for Display purposes only. For example, C5can be used
to configure the instrument so that RPM is being com-
puted and FPS Is being displayed. This Is Illustrated by the
following equation.
Arpm x C5= Dfpm
where A = scaled Input signal frequency
D = display value
C6sets the Analog Output Zero Scale by determining at 0.000
which value of the analog function (C11) the analog
output delivers 0 or 4mA to the load.
C7sets the Analog Output Full Scale by determining at 2000
which value of the analog function (C11) the analog
output delivers 20mA to the load.
Note: You can make the Zero Scale larger than the Full Scale to compute Inverse functions.
C8determines at which value of the selected function (C11) 1000
setpoint one relay K1 changes to the alarm state.
C9determines at which value of the selected function (C11) 1000
setpoint two relay K2 changes to the alarm state.
C10 determines the independent reset point for both relays. 0505
(Hysteresis The Hysteresis (dead band) may be specified in 1%
Constant) steps from 00 to 99% of the setpoint value.
C10
SP2 SP1
3

C11 determines which functions are sent to the four outputs. 1121
(Function The calculated values of A and B (such as difference,
Constant) ratio, and average) may be assigned independently
to any of the four outputs.
C11
Display Function
Analog Function
Setpoint I Function
Setpoint 2 Function
Note: Any unused outputs should be set to zero (OFF) for faster response.
C12 determines the specific properties of the four outputs, 14017
(Output such as analog zero scale current, reporting method,
Constant) display decimal location (autoranging). and relay logic.
C12
Decimal Location
Setpoint 1 Relay Logic
Setpoint 2 Relay Logic
Serial Output (Special Option)
Analog Output
4.0 HOW TO OPERATE THE TACHTROL®3 TACHOMETER
This section provides you with instructions for:
1. Finding the Scaling Factors.
2. Selecting the Mathematical Functions
3. Defining the Behavior of the Outputs
4. Entering the Constants
5. Storing the Constants
6. Selecting the Input Options
4.1 FINDING THE SCALING FACTORS (C1THRU C4)
If you are using the TACHTROL®3 tachometer as a single channel Instrument to measure RPM
and are using a 60 tooth gear. skip this section and proceed to section 4.2 Selecting The
Mathematical Functions.
4.1.1 Finding the Scaling Factor for Common Applications:
This section provides you with formulas and examples for finding the scaling factor for
revolutions per minute (RPM). gallons per minute (GPM), feet per minute (FPM). Inches
per minute (IPM). yards per minute (YPM). Inches per second (IPS) and feet per second
(FPS). For other applications, see Section B.
1. Single Channel and BI-Directional:
A. Find the number of pulses per revolution (ppr) produced by the gear or target
being monitored by the speed sensor.
B. Calculate the scaling factor by applying the number of ppr to the appropriate
formula for the engineering units you are displaying.
4

For RPM the formula for finding the scaling factor Is:
60
PPR = Scaling Factor
Suppose you have a 72 ppr gear. The formula reads:
Scaling Factor = 60 = 5
72 6
For GPM the formula for finding the scaling factor is:
60
PPG = Scaling Factor
where PPG = Pulses Per Gallon
Suppose you have a gear operating at 140 PPG. The formula reads:
Scaling Factor = 60 = 3
140 7
For FPM the formula for finding the scaling factor Is:
60 x π x D’
PPR = Scaling Factor
Suppose you are monitoring the speed of a moving conveyor belt. To calculate the scaling factor,
you would need to know the diameter (In feet) of the roller to which the gear is attached and the
thickness of the belt (multiplied by 2). If the diameter of the roller is 1 ft. 10 Inches and the thickness
of the belt Is 1inch (x2). and the gear is 48 ppr. then the formula reads:
Sealing Factor = 60 x 3.1416* x 2’ = 7.8512
48 1
* π always = 3.1416
You can improve the accuracy of the scaling factor by manipulating the fraction in a way that uses
the full 4 1/2 digits that can be entered on the Display. In this example the two 4 1/2 digit scaling
factors are used to scale the channel with 5 digits of accuracy.
7.8512 = 7.8512 x 10000 = 78512 ÷4= 19628
1 1 10000 10000 4 2500
For IPM; YPM; IPS; and FPS the formulas for finding the scaling factor are:
IPM: 60 x πx D” = SF YPM: 60 x πx D’ = SF
PPR PPR x 3
IPS: π x D” = SF FPS: π x D’ = SF
PPR PPR
Where
D’ = diameter in feet
D” = diameter in inches
SF = scaling factor
Note: In some applications the shaft’s speed you want to read may not be accessible. You may
need to mount the gear and sensor on a shaft whose speed is proportional to but not the same as
the one you want to read. In such cases, you will need to determine the ratio of speeds. For
example, if the shaft to which you have mounted the gear and sensor makes three rotations for
every single rotation of the shaft you want to read, then you must divide the scaling factor by 3.
5

2. Dual Channel
A. Find the number of pulses per revolution (PPR) produced by the gears or targets
being monitored by the speed sensors.
B. Calculate the scaling factors by applying the number of PPR’s to the appropriate for-
mula for the engineering units you are displaying.
For RPM the formula for finding the scaling factor is:
60
PPR = Scaling Factor
Suppose you are using Channel A to measure RPM from a 48 tooth gear and Channel
B to measure RPM from a 90 tooth gear. The formulas read:
60 = 5
Channel A: Scaling Factor = 48 = 4
60 = 6
Channel A: Scaling Factor = 90 = 9
The formulas for GPM; FPM; IPM; IPS; and FPS are given in the previous section for single
channel instruments. Please be sure to read the note at the end of that section.
4.1.2 Other Applications for Scaling to Other Engineering Units
The general formula is:
DISPLAYVALUE
SCALING FACTOR = INPUT SIGNAL FREQUENCY
To solve this problem:
1. Pick a display value within the range of your operation.
2. Calculate the Input signal frequency produced by the speed sensor at the display value
you’ve picked.
Frequency is simply the number of electrical “pulses” produced by the sensor in one second.
All AI-Tek sensors produce 1 pulse each time a gear or target tooth passes in front of the sen-
sor. You wilI need to calculate how many pulses per second are created by the sensor when
your machinery is operating at the display value you’ve picked.
3. Divide the display value by the input signal frequency.
4.2 SELECTING THE MATHEMATICAL FUNCTIONS (C11)
Select the mathematical functions from the menu below. You select and route a mathematical
function to an output by placing the number to the left of the function in a digit of the Function
Constant (C11). For a complete explanation of how to enter the functions see Section 4.4.
6

MENU
Function C11
0 = OFF
1 = A
2 = B
3 = A-B
4 = ±A
5 = A/B
6 = B/A
7 = A+B
2
8 = A-B x 100
A
9 = B-A x 100
A
The mathematical functions which can be computed in each mode of operation are listed
in Section 2.1.
Note: A + B can be computed by using a negative scaling factor for the B channel.
Note: With bi-directional operation, when a bidirectional sensor is connected to the instru-
ment, Speed A can be computed from one frequency input (TTL input A) and direction can
be computed from TTL input B. High (+5V) indicates a positive direction. Only single speed
functions (Speed A) are useful when connected in this operation mode. In addition, channel
B can be connected to any type of limit switches when using Function 4 (±A).
Note: With dual channel operation, when ratio and elongation functions are selected
(Functions 5, 6 and 9), the ratio of zero over zero, by definition is unity (1).
4.3 DEFINING THE BEHAVIOR OF THE OUTPUTS
4.3.1 Display
You can program the Display to show the computed function of channel A and/or channel
B, and you can configure the instrument to compute in one unit of measurement and to
display another by altering constant C5. (See page 3.)
Autoranging
Autoranging refers to the movement of the decimal among the 4 1/2 digits on the Display.
You can limit the movement of the decimal point, and thereby determine the smallest value
the Display will show.
4.3.2 Analog Output
Zero Scale
You can determine at which value of the analog function the analog output delivers 0 or 4
milllamps to the load.
7

Full Scale
You can determine at which value of the analog function the analog output delivers 20
milllamps to the load.
Note: The 0-20mA can be converted to a 0 to 5vdc or 0 to 10vdc signal by placing a resistor
across the input of the receiving instrument whose parallel combination with the input resist-
ance of the receiver is 250 ohms or 500 ohms respectively.
4.3.3 Setpoints
Relay setpolnts are used to trigger events. In some applications, they are used to trigger the
adding of ingredients at specified stages of a process. In other applications, they are used to
trigger alarm conditions. For Instance, they are used to trigger an alarm condition when the
speed of a machine drops below or rises above its normal range of operation. The following dis-
cussion will focus on the latter type of application.
Setpoint Types
There are two types of setpoints: underspeed and overspeed. Underspeed relays trigger events
when frequency drops below the setpolnt.
FIGURE 2. UNDERSPEED SETPOINT
Overspeed relays trigger events when the frequency rises above the setpolnt.
FIGURE 3. OVERSPEED SETPOINT
Setpoint Behavior
Relay setpoints may be configured to either energize or de-energize above and below the set-
point value. Thus, for each relay setpoint you must decide what type you want and how you
want the relay to behave. Overspeed relays which energize above the setpoint and under-
speed relays which energize below the setpoint are called Non-Failsafe. Ovespeed relays which
de-energize above the setpoint and underspeed relays which de-energize below the setpoint
are called Failsafe. Failsafe provides you with a warning in the event that a power failure occurs
which the machine is operating within the Non-Alarm (Safe) area of operation.
8

Latchlng/Auto Reset
You can configure the relays as either Latching or Auto Reset. Latching relays remain in an
alarm condition and must be reset manually by using the pushbutton located behind the
instrument’s Display door*. Failsafe Auto Reset relays automatically energize when the
machine returns to its Non-Alarm state of operation. You can program the relay to automat-
ically reset at setpoint or you can program it to reset with a Hysteresis (a dead band). That
is, you can program it to reset within a specified range of the setpoint. Hysteresis prevents
“chatter” (the clicking on and off of the relay) as frequency hovers around the setpoint
value. Hysteresis is specified as a percentage of the setpoint value. The position of hysteresis
above or below the setpoint is determined by the relay type. Overspeed relays have
hysteresis below the setpoint. Underspeed relays have hysteresis above the setpoint.
Figure 4 shows an overspeed relay with hysteresis below setpolnt.
*Loss of instrument power will cause a latching relay to reset in the absence of an alarm
condition.
FIGURE 4. OVERSPEED RELAY WITH HYSTERESIS BELOW SETPOINT
Figure 5 illustrates the behavior of the setpoint relays.
FIGURE 5. SETPOINT RELAY BEHAVIOR
En = energize RP = resetpoint > = above
DE - EN = de-energize HYS. = hysteresis < = below
9

Use Table 1 to select the behavior and type of relay setpoint. The numbers in the table denote
the numbers placed in the second digit of Constant C12 for setpoint 1 and the third digit of
Constant C12 for setpoint 2.
SETPOINT TYPE
TABLE 1. RELAY SETPOINT BEHAVIOR AND TYPE
4.3.4 Sample Set-ups
Single Channel Operation
Suppose you are measuring the rate at which paper is passing along a bed roll, the diameter
of the roller plus twice the thickness of the conveyor belt is equal to 36 inches. The sensor is read-
ing from a 24 tooth gear.
You want the tachometer to;
1. Compute Speed A in RPM
SF = C1= 60 = 60 = 10
C2, PPR 24 4
C1= 10.000
(C3and C4are not adjusted)
C2= 4.000
(C3and C4are not adjusted)
2. Send Computed Function (Speed A) to All Outputs
Speed A = 1 on Function Chart
C11 = X 1 1 1 1 x - denotes unused digit
3. Have Display Show FPM with Autoranging to Two Decimals, right only
A x C5= Display value: RPM x FPR = FPM
10
Overspeed
hysteresis below
setpoint
de-energize above
setpoint
0
energize above
setpoint
2
de-energize above
setpoint
4
energize above
ssetpoint
6
Underspeed
hysteresis above
setpoint
de-energize below
setpoint
1
energize below
setpoint
3
de-energize below
setpoint
5
energize below
setpoint
7
Auto Reset
Failsafe
Auto Reset
Non-Failsafe
Latching
Failsafe
Latching
Non-Failsafe
S
E
T
P
O
I
N
T
B
E
H
A
V
I
O
R

FPR = Diameter x π= 36 x 3.1416 = l l3.0973 in. Converted to Feet = 9.425 where FPR = feet
per revolution
C5= 9.425
C12 = X 6
4. Have the Analog Output Drive an Auxiliary 0-20mA meter with a range of 600 to lOOOrpm.
20mA
0mA
0 600 rpm 1000 rpm
C6= 600
C7= 1000
C12 = 1 X 6
5. Go to an Alarm Condition when the speed drops below 600rpm and automatically come out of
Alarm when it returns to 660rpm (Underspeed Failsafe)
6. Go to an Alarm condition when the speed rises above lOOOrpm and automatically come out of
Alarm when it returns to 950rpm (Overspeed Failsafe)
C8= 600
C9= 1000
C10 = X 0 5 1 0
C12 = 1 X 0 1 6
autoranging to two decimals, right only
underspeed failsafe
overspeed failsafe
analog output is 0 - 20 mA
Dual Channel Operation
Suppose you are using the tachometer as an elongation monitor in a paper mill. Elongation is the
change in length of the paper at the outgoing roller. The diameter of the roller plus twice the thick-
ness of the belt at each end of the process is 36 inches. The sensors are reading from 48 tooth gears.
11

The shaft driving the incoming roller is turning at 1000 rpm, and the shaft driving the outgoing roller
is turning at 1250 rpm.
You want the tachometer to:
1. Compute Speed A (Incoming roller) and Speed B (out-going roller) in FPM.
SF fpm = 60 x πx D’ = 60 x 3.1416 x 3’ = 565.4880
PPR 48 48
C1= 565.5
C2= 48.00
C3= 565.5
C4= 48.00
2. Send the percentage of elongation to Display, ratio to Setpoints I and 2, and Speed B only to
Analog Output.
C11 = x 5 5 2 9
3. Have Display show FPM with autoranging fixed to one decimal place.
C5=1000
C12 = 1
4. Have the Analog Output drive an auxiliary 4 - 20mA recorded which has a range of 0 to 5000fpm.
20mA
4mA 0 fpm 5000
C6= 0000 C12 = 1
C7= 5000 blank
5. Use the setpoints for web break detection, with Setpoint 1 going to alarm if the ratio is less than
0.5, and Setpoint 2 going to alarm if the ratio is less than 1.0. Relays are latching.
C8= 0.500
C9= 1.000
C10 = x 0 0 0 0 (no hysteresis)
C12 = x 5 5 1
autoranging fixed to one decimal place
latching relay
latching relay
analog output is 4 - 20mA
12

4.4 ENTERING THE CONSTANTS
The Control Panel Is located behind the door of the Display. To gain access to the panel, slide the
latch on the Display door to the left.
4.4.1 Control Features
Constant Thumbwheel (CTW): When the CTW is set to “0”, the instrument runs at its configured mode.
When it is set to a number other than “0”, the instrument stops operating as a rate monitor, all out-
puts freeze at their current values, and the Display shows the constant selected by the CTW. For
example, to look at the value for setpoint one, set CTW to 8. Constant 8 (C8) will appear on the
Display. In like manner all constants may be viewed. After reviewing the constants, return CTW and
DTW to zero. The Display will show Pb”. This means “push the button Pb.” By pushing the button, you
instruct the instrument to return to normal operation.
Digit Thumbwheel (DTW): The constant being displayed can be altered by using the DTW and the Pb.
When the DTW is set to “O”, pushing and holding the Pb locates the decimal. When the DTW is set
to a Display digit, pushing and holding the Pb changes the number in the digit.
Push Button (Pb): TTL/MAG Dipswitches: Four possible settings program the instrument for the type of
sensor being used.
A.O. Full Scale R31 is factory set and normally will not require calibration. It may be adjusted by
inputting signals to the instrument that force the output beyond the analog output full scale and by
adjusting R31 to 20 milllamps using an accurate current meter.
Display: The Display has 4 1/2 digits. The digit to the far left is referred to as a 1/2 digit because only
a blank (zero) or a one (1) can be entered on it. Any two channel calculation may result in a
negative quantity. Any value too large for the Display will cause the Display to flash its largest value
(19999).
13
FUNCTION INDICATORS
DISPLAY
DIGIT THUMBWHEEL
CONSTANT THUMBWHEEL
TTL/MAG DIPSWITCH
A O FULL SCALE R31
PUSH BUTTON (Pb)
A
B

Alternate Display Mode: While in the run mode (CTW and DTW = 0), you may use the DTW to vlew quan-
tities A and B. To view A. set DTW to 1. To view B. set DTW to 2. To view the quantity originally selected for
the Display, set DTW to zero. This does not affect the operation of the instrument. The values displayed
under A and B using this feature will always be full autoranging regardless of the setting of digit 1 of the
constant C12.
Function Indicators: These indicator lamps show the channel displayed.
4.4.2 Turning On The Power
1. Place the tachometer on the flat surface.
2. Attach the AC power cord to rear terminal lead 9,10, and 11.
3. Plug the unit into an AC outlet.
4.4.3 Entering The Scaling Factors For Frequency A and B (C1thru C4)
Note: If you have a 60 tooth gear. then frequency is equal to RPM and the constants are equal to 1 (the
standard constant).
1. Use two 4 1/2 digit numbers in the form of a fraction to enter each of the scaling factors.
2. For Frequency A, enter the numerator in C1and the denominator in C2. For Frequency B, enter the
numerator in C3and the denominator in C4. If you are using the TACHTROL®3 tachometer as a single
channel instrument, do not adjust the settings for C3and C4.
SAMPLE SCALING FACTOR
C1= 19628,
C22500
To enter C1:
1. Turn CTW to 1
2. DTW is already set at 0. Push and hold the Pb until the decimal disappears.
3. Turn DTW to 1. Push and hold Pb until 8 appears on Display Digit 1.
4. Turn DTW to 2. Push and hold Pb until 2 appears on Display Digit 2.
5. Turn DTW to 3. Push and hold Pb until 6 appears on Display Digit 3.
6. Turn DTW to 4. Push and hold Pb until 9 appears on Display Digit 4.
7. Turn DTW to 5. Push and hold Pb until a 1 appears on Display Digit 5.
14

To enter C2:
1. Turn CTW to 2 and then use DTW and Pb to enter the decimal and the number for each
digit in the same manner as you did for C1.
4.4.4 Entering The Function Constant (C11)
1. Turn CTW to 11.
2. Turn DTW to 1 and enter the number of the function you have selected to send to Display
by pushing and holding the Pb until the number appears in the first Display digit.
3. Turn DTW to 2 and enter the number of the function you have selected to send to analog
output by pushing and holding the Pb until the number appears in the second Display digit.
4. Turn DTW to 3 enter the number of the function you have selected to send to setpoint 1
by pushing and holding the Pb until the number appears in the third Display digit.
5. Turn DTW to 4 enter the number of the function you have selected to send to setpoint 2
by pushing and holding the Pb until the number appears in the fourth Display digit.
Select the number of the function from the
table on the left for each output.
Note: Set any unused output to “0” (off) for faster response.
4.4.5 Entering The Constants Which Define The Behavior Of The Outputs(C12)
Display Output
1. Constant
A. Turn CTW to 5.
B. Enter the constant by using the DTW and Pb in the same manner as you did for C1
thru C4
2. Autoranging
A. Turn CTW to 12.
B. Turn DTW to 1.
15
C11

C. Use chart below to select the location of the decimal.
D. Push and hold Pb until the number from the chart appears in the first Display digit.
DECIMAL LOCATOR IS:
0= No decimal
1= 1888.8 = 5
Fixed 2 = 188.88 = 6 Auto Range
Decimal 3 = 18.888 = 7 (right only)
C12
Analog Output
1. Zero Scale Constant
A. Turn CTW to 6.
B. Enter the constant by using DTW and Pb in the same manner as you did for C1thru C5.
2. Full Scale Constant
A. Turn CTW to 7.
B. Enter constant by using the DTW and Pb in the same manner as you did for C1thru C6.
3. Zero Scale Current
A. Turn CTW to 12.
B. Turn DTW to 5.
C. Select the zero scale current from chart (0 or 4ma).
D. Push and hold Pb until the number representing the zero you’ve selected appears in the
fifth Display digit.
ANALOG OUTPUT IS: . . . . . 4 - 20ma = blank C12
OR . . . . . 0 - 20ma = 1
Setpoint 1 Output
1. Setpoint Constant
A. Turn CTW to 8.
B. Enter constant by using DTW and Pb in the same manner as you did for C1thru C7.
2. Hysteresis For Setpoint 1
A. Turn CTW to 10.
B. Enter the value of the hysteresis (given in percents) as a two digit number. (i.e. 5% as 05).
16
Table of contents
Other AI-Tek Instruments Measuring Instrument manuals
Popular Measuring Instrument manuals by other brands

Rotronic
Rotronic HygroClip Digital quick start guide
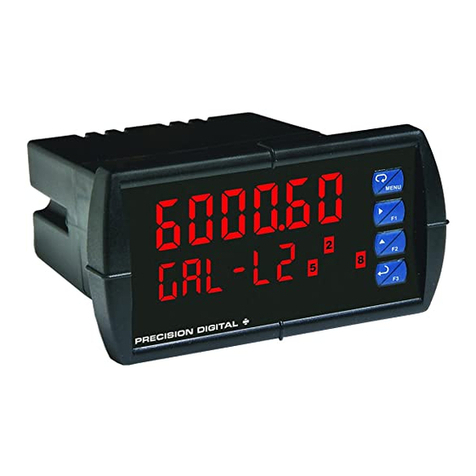
Precision Digital Corporation
Precision Digital Corporation PROVU Series instruction manual
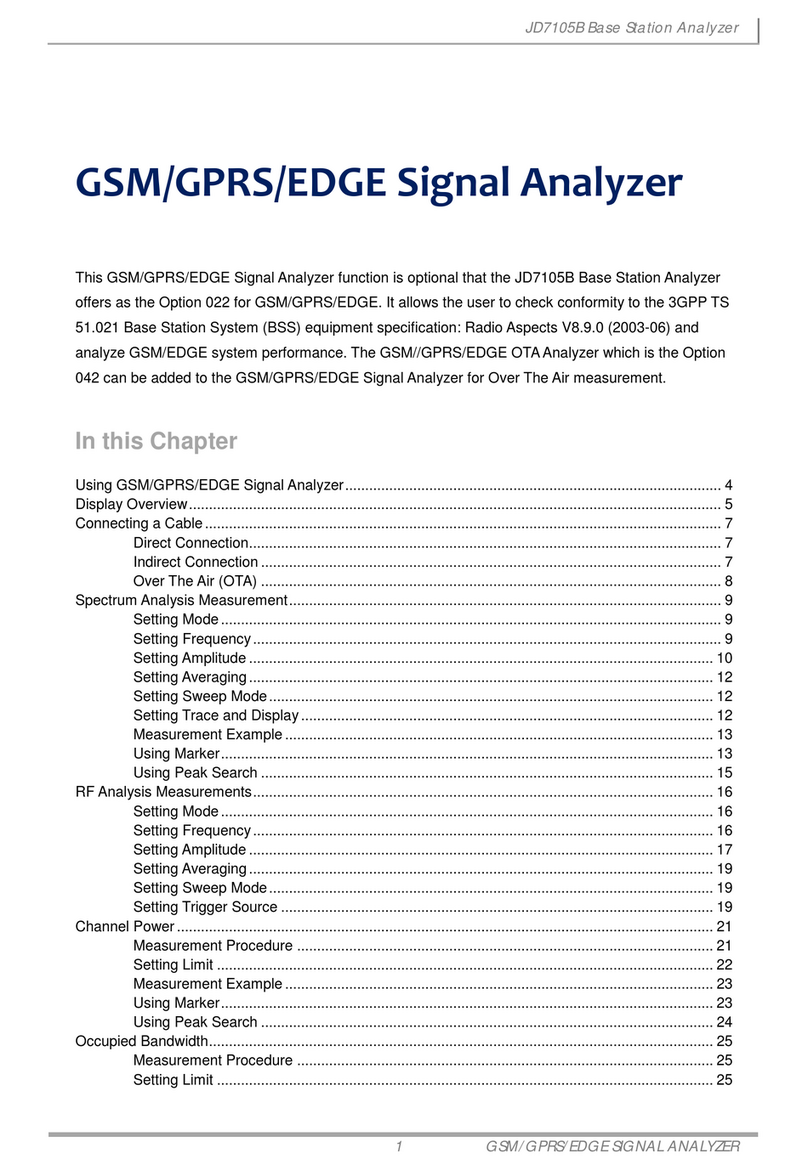
JDS Uniphase
JDS Uniphase JD7105B manual
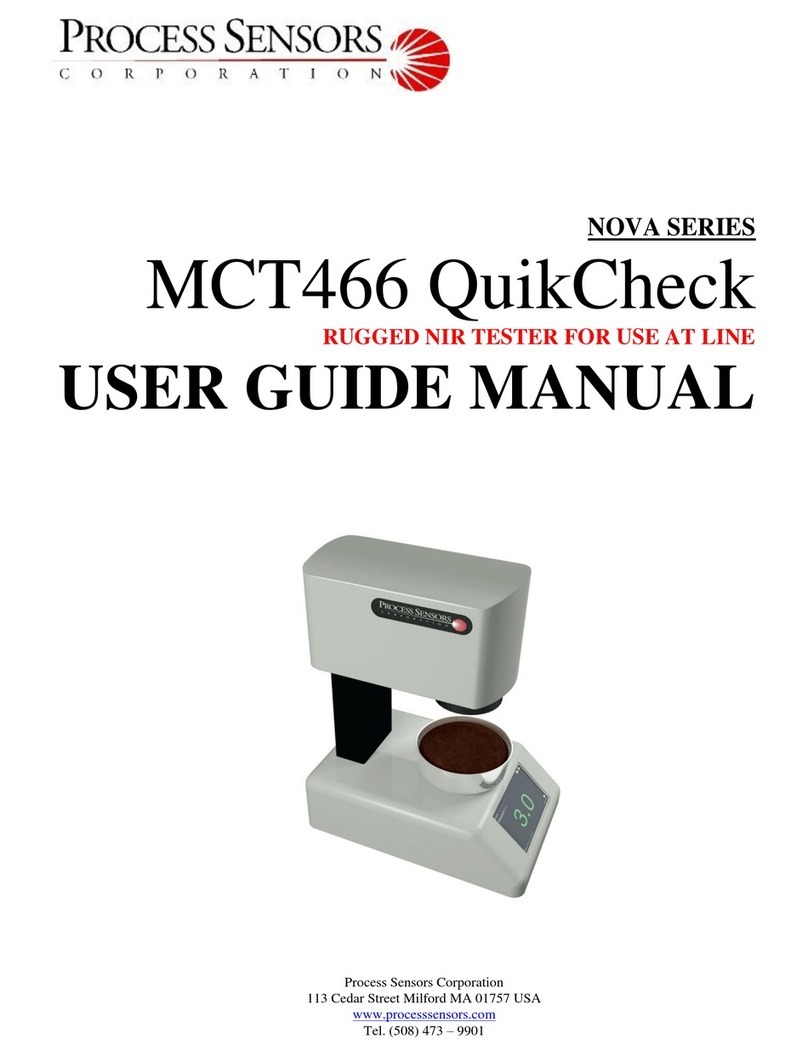
Process Sensors
Process Sensors MCT466-QC User guide manual
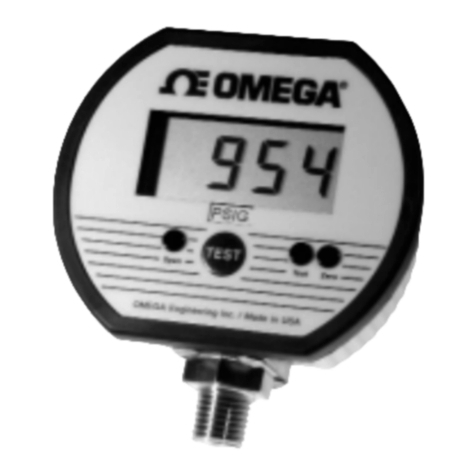
Omega
Omega DPG1000L Series instruction sheet
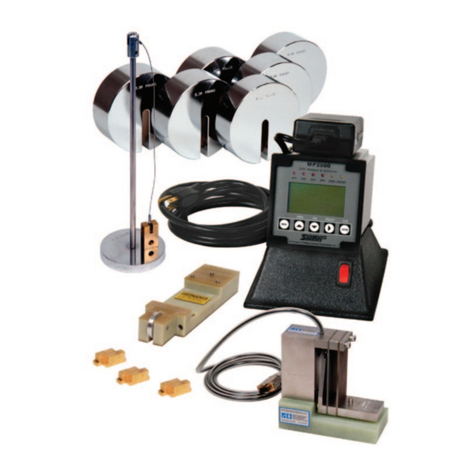
Humboldt
Humboldt FD-4A product manual

Energometrika
Energometrika EnergoM 400 user manual
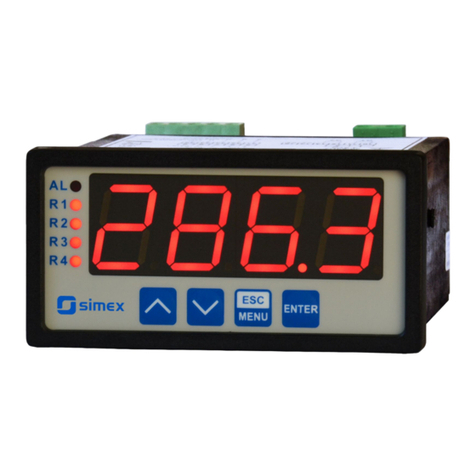
Simex
Simex SRT-94-XA user manual
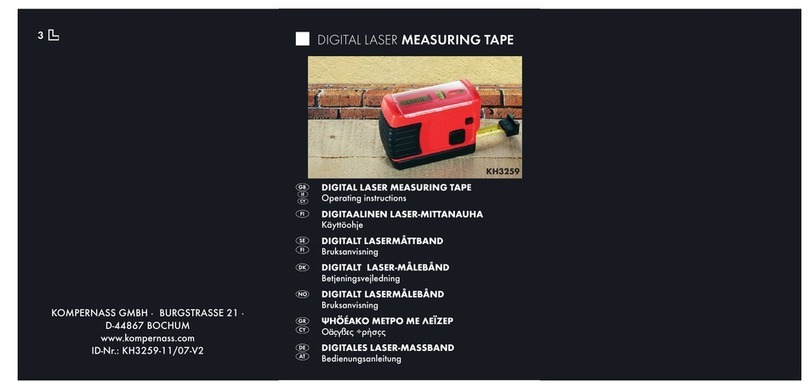
Kompernass
Kompernass KH 3259 operating instructions
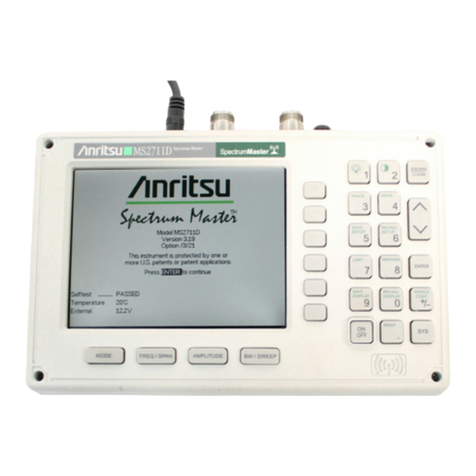
Anritsu
Anritsu Spectrum Master MS2711D Maintenance manual
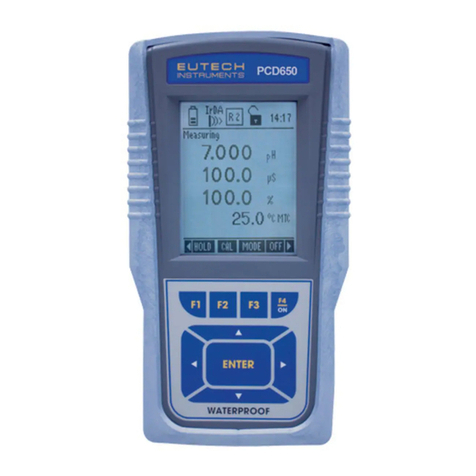
EUTECH INSTRUMENTS
EUTECH INSTRUMENTS CyberScan PCD 650 quick guide
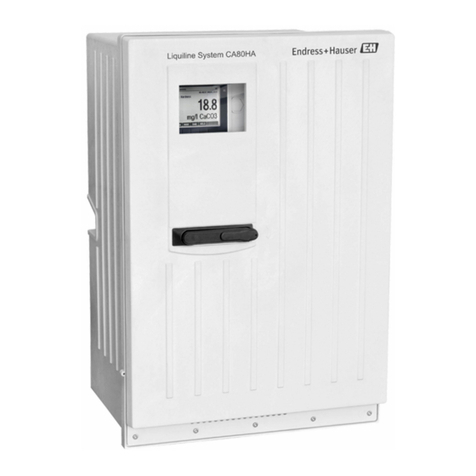
Endress+Hauser
Endress+Hauser Liquiline System CA80HA operating instructions