AirBench FPW Installation guide

© Copyright AirBench Ltd 2019 Page 2 of 18
Cautions 3
Introduction 4
OVERVIEW 4
ABOUT AIRBENCH 4
ABOUT THIS DOCUMENT 4
Installation 5
GENERAL 5
ELECTRICAL 5
DUCTED UNITS 5
ASSEMBLY OF ACCESSORIES 5
Commissioning 7
GENERAL 7
IN HOUSE COMMISSIONING 7
FUME EXTRACTION UNITS 7
Operation 8
PRIOR TO USE 8
GENERAL USE 8
Maintenance 10
FILTER CARE 10
SPARES 13
OTHER ROUTINE MAINTENANCE 14
Accessories 15
FILTER PRESSURE GAUGES 15
HOURS RUN METER 15
WHEELS 15
COMPRESSED AIR INTERLINK 15
Thorough Examination and Testing 16
Technical 17
ARRANGEMENT 17
TECHNICAL DATA 17
Declaration of Conformity 18
AIRBENCH LTD

© Copyright AirBench Ltd 2019 Page 3 of 18
CAUTIONS
Use the AirBench only for the designed duty –consult the manufacturer on any change of
use.
Each unit is marked with its design application, which is also shown on the commissioning
certificate.
The filters are not self-cleaning.
They must be maintained / cleaned / replaced as described within.
Do not mix incompatible materials e.g. steel and aluminium.
It is the users’ responsibility to comply with this legal requirement.
This unit is not ATEX rated.
It is your responsibility under ATEX regulations to ensure the AirBench is located in an
area rated suitable for the specification of the AirBench.
Do not work coated or galvanised materials on this unit. Use only for mild steel.

© Copyright AirBench Ltd 2019 Page 4 of 18
INTRODUCTION
Overview
Thank you for choosing AirBench as your fume or dust control system. Please read this document before
installation and use.
This document details maintenance activities which are essential to the safe use of your AirBench. We
recommend that the Responsible Person reads this manual fully prior to installation and operation of the
AirBench.
This document refers to the AirBench FPW type. Models of this type are available with a range of filter
configurations. The filter configuration in use is detailed on the system Commissioning Certificate and is used
within this document to provide filter-specific maintenance information.
About AirBench
AirBench is a self-contained down draught extraction bench which utilises a fan and filter combination selected
for your specific application, to extract and filter dust/fumes and return filtered air to the work place.
Some models vary in filtration and filtered air delivery point.
It is used by running the fan at either fixed speed or variable speed (if speed controller fitted) to draw the
pollutant down and through the filters, allowing the process to proceed on the surface.
About this Document
This document provides general maintenance and operation instructions for the AirBench FPW range. It should
be read in conjunction with the Commissioning Certificate supplied with the unit. If you have any concerns or
doubts about maintenance or operation of this unit, contact the manufacturer.

© Copyright AirBench Ltd 2019 Page 5 of 18
INSTALLATION
General
Unpack the unit and check for damage, if not already completed.
The AirBench must be installed on a flat and level floor capable of carrying the weight of the unit. For nominal
unit weights, see Specifications section at rear of manual. When determining an installation location, be aware
that the air exhaust must discharge somewhere. Do not position the unit so all outlets are blocked.
These models are designed to be moved into place using a forklift or pallet truck, taking care not to damage
fittings on the base of the unit.
Please note installation may be required when using certain accessories, external fansets, or ducting (see
below).
After shipment, filters may be dislodged. Always check prefilters (in main body of bench) and final
filter (in side table) prior to first use.
Electrical
WIRING
AirBench is supplied as standard with an internal fan or fans. These are pre-wired to a switch or speed
controller and fitted with a lead and plug for your convenience. Standard electrical supply is 240V/1Ph/50Hz.
Certain models can be supplied with 110V/1Ph/50Hz internal fans if specified in advance; this is noted on the
front left of each unit where applicable.
BS7671 requires that the lead is appropriate for the working environment and you must satisfy yourself that the
pre fitted lead is satisfactory.
FUSES
Switched units: A fuse is provided on the switch front plate.
Speed controlled units: An additional fuse is provided within the speed control panel. To check this fuse,
remove the service panel; the speed control panel is mounted on the rear of the service panel.
PAT TESTING
FPW Model AirBenches use EC (electrically commutated) fans. EC fans may give misleading readings when
PAT Testing, particularly if using a battery powered tester. These units should be tested by a qualified
electrician using a mains-fed PAT Testing device.
Ducted Units
This unit is not suitable for connection to ducting.
Assembly of Accessories

© Copyright AirBench Ltd 2019 Page 6 of 18
These items apply only when they have been ordered with the AirBench.
ENCLOSURE
Enclosures are supplied fully assembled where possible. Where shipping does not permit assembly prior to
dispatch, enclosures should be assembled as follows using bolts supplied:
- Loosely fit left and right panels to left and right frame of bench.
- Loosely fit rear panel with assistance if required.
- Lay top panel (if supplied) on top of enclosure and bolt into position.
- Tighten all bolts.

© Copyright AirBench Ltd 2019 Page 7 of 18
COMMISSIONING
General
The initial commissioning and testing of your AirBench has been performed prior to delivery. However, as part
of in-house commissioning we recommend that you complete the following tasks and record the results as
appropriate in the system logbook.
In House Commissioning
The following tasks should be completed by a responsible person; for example, the Health and Safety Officer,
or Director, responsible for this process.
-Review the commissioning certificate for this unit, in particular any notes made by our engineer in relation to
use.
-Ensure all operators are trained to use this machine and are aware of the effective capture zone in which
they should aim to work.
-Ensure all operators are aware of the filter maintenance routine required for this machine.
Once complete, you should note this on the commissioning certificate and retain the certificate for future
reference.
As operating conditions vary, each installation will vary in maintenance needs and this is best established by
empirical means, regularly checking filter condition in the first weeks of operation to establish a procedure.
Reduced airflow is a key indication of filter condition. If the filter pressure gauge on the front of the unit is
showing in the red zone, this indicates low airflow and filters should be checked and cleaned or changed
promptly, according to the instructions contained within this manual.
We recommend keeping the commissioning certificate, Quick Start guide, and logbook with the machine at all
times for operator access.
If in doubt please contact the manufacturer quoting the machine serial number.
Fume Extraction Units
The effectiveness of carbon filtration improves as airspeed is lowered allowing fumes to spend longer passing
through the filters. A speed controller is supplied with carbon filtered units to allow airflow to be adjusted to the
optimum level.
We therefore recommend adjusting the speed controller provided to the lowest level at which extraction is still
effective and marking this operation point on the speed controller. Ongoing adjustment may be required as
filters become blocked with use.

© Copyright AirBench Ltd 2019 Page 8 of 18
OPERATION
This page contains the same information as the Quick Start guide provided with your AirBench.
Prior to use
Check the system logbook to ensure no routine maintenance is required.
General use
To use AirBench, ensure it is plugged in to a mains socket and the socket is switched on. Turn on the switch on
the front of the bench.
If a speed controller is fitted, turn it to full power before switching on, then adjust it to an appropriate level. Our
recommended settings are shown below:
Fume: 50-75%
Light dusts, 50-100%
Heavy dusts, 75-100%
During commissioning, an optimum setting may have been determined and this should be noted in the system
logbook.
Check the filter pressure gauge on the front of the bench. If the needle on the gauge is showing within the RED
zone, check the filter condition –they may require cleaning or replacement.
Your AirBench has a zone above the surface in which capture is most effective, in a straight line upwards from
the ventilated area. The extent of this zone is detailed in the commissioning certificate supplied with the unit.
This zone forms a box in which you should aim to do the majority of your work. Working outside this zone may
reduce the effectiveness of the extraction.
Work as normal, aiming to work within the extraction zone described above. On completion of work, switch the
AirBench off using the switch on the front. Record any maintenance you have undertaken, or any that is
required, in the logbook.
To avoid fan overload, do not block more than 95% of the work surface or the air
outlet.

© Copyright AirBench Ltd 2019 Page 9 of 18

© Copyright AirBench Ltd 2019 Page 10 of 18
MAINTENANCE
Filter care
The filters are not self-cleaning and must be maintained / cleaned / replaced as described below. Proper filter
care is essential for the effective operation of your AirBench. If in doubt, contact the manufacturer for advice.
When changing filters, the seals on which the filters sit should be checked for damage and replaced if
necessary.
All filters should be regularly checked for wear, damage, or by-passing.
When completing filter maintenance activities these should be recorded in the accompanying log sheet.
Take precautions and wear appropriate PPE when handing filters.
They may contain hazardous dusts.
i
If using a vacuum cleaner to empty filters, excessive cleaning will reduce filter life.
Remove excess dust only.
FILTER ACCESS
Prefilters are accessed by removing the top surface, taking care as the surface may have sharp edges. Once
the surface is removed, a retaining plate is exposed which holds the prefilters vertically in place. This can be
lifted out and filters rotated forwards for access as per the following diagram.

© Copyright AirBench Ltd 2019 Page 11 of 18
The main filter is accessed via the door on the filter housing (to the left of the main unit). This can be opened by
rotating the quarter turn latch and swinging the door forward. Once the door is open, a clamp bar is exposed
which holds the filter in position against soft rubber seals. The clamp bar can be loosened, allowing the main
filter to rotate forwards and be removed as per the following diagram.

© Copyright AirBench Ltd 2019 Page 12 of 18
Surfaces can be heavy and have sharp edges.
Wear appropriate hand protection.
LABYRINTH FILTERS
Labyrinth filters consist of a series of metal channels, in a metal frame.
These filters can be emptied regularly using a vacuum cleaner by lifting the
surface of the AirBench. They can also be removed and emptied.
In general labyrinth filters do not require replacement except when
damaged.
DISPOSABLE MEDIA PADS
Media pads are green and white fibreglass pads, held in a metal frame.
These filters are not cleanable. When replacing, the frame and clip which hold the
pad can be reused. Always replace with white side downwards.
Replace on a monthly basis, or more regularly if required.
WELDING / FETTLING PLEATS
Welding / fettling pleats consist of large, 300mm deep arrays of fine paper pleats,
in a plastic case.
This filter is not cleanable.
Replace the filter when it is stained on the clean (outlet) side or damaged.

© Copyright AirBench Ltd 2019 Page 13 of 18
Do not clean filters using compressed air.
This will damage media and spread dust.
Spares
See the specific list for your machine shown on the commissioning certificate.
When ordering, please contact the manufacturer quoting the serial number of this machine.

© Copyright AirBench Ltd 2019 Page 14 of 18
Other routine maintenance
We recommend the following tasks be performed on a regular basis. Suggested intervals are shown and these
should be reviewed dependent on level of use. Actual completion of these operations and any variation to these
recommended maintenance intervals should be recorded in the system logbook.
If completion of routine maintenance tasks suggests additional issues, contact the manufacturer for advice.
FILTER SEALS
These sit behind the filters and prevent dust passing into the body of the bench and the exhaust airstream. It is
important the seals are in good order. Check the condition of the filter seals every time filters are changed or
removed.
SURFACE
At least monthly, or as routine, check the surface condition. Clear any blocked holes.
FAN CHAMBER
At least every 6 months, check the fan chamber. Remove any debris and clean.
FAN
At least annually, check and tighten fan fixings, impeller fixings, and electrical connections.

© Copyright AirBench Ltd 2019 Page 15 of 18
ACCESSORIES
Some accessories are only supplied if specified with purchase.
Filter Pressure Gauges
A filter pressure gauge is fitted as standard to the front of each AirBench. This indicates performance of the unit
as a whole, and filter condition. Certain models show a red zone on the filter gauge; when the gauge indicates
within this zone, filters may be blocked or require cleaning. Turn the AirBench off and inspect the filters.
Where no red zone is shown, a filter inspection pressure drop will be recorded on the Commissioning
Certificate. When pressure loss is greater than that shown on the Commissioning Certificate, follow the above
procedure.
A high pressure reading may also indicate a blocked surface. Inspect the surface for blockages and clean if
required. Do not operate AirBench continuously with more than 75% of the surface blocked.
Hours Run Meter
The meter is not resettable and operates at all times when the speed control or switch is powered.
Wheels
Standard industrial rubber wheeled swivel castors are used. The two front wheels are lockable. Lock by
pressing on the lever and trip by flicking (models and operation vary slightly). Do not attempt to move while
brakes are on.
Compressed Air Interlink
This option ensures the safety of operators by preventing the use of air tools without extraction being
operational; and reduces energy use by switching off the fan after 5 minutes of non-use.
4 off series 19 airline connectors are provided to the front or side of the unit and an internal timer fitted, pre-set
to an agreed value –usually 5 minutes. The control panel is supplied with an additional Red / Green push-
button.
System control will be as follows:
Switch main on/off switch to On –system is energized. Airline is switched to operational.
Press green button –fan starts and runs for 5 minutes.
Use airline or press green button again –timer is reset for a further 5 minutes.
Press red button –fan stops, airline stops.
The timer can be re-set to a different interval; contact the manufacturer for details.

© Copyright AirBench Ltd 2019 Page 16 of 18
THOROUGH EXAMINATION AND TESTING
If AirBench is used as an LEV system it must be tested at regular (normally 12 month) intervals and certificated
under the COSHH regulations. This service is available from us, or our approved testers.
Thorough examination and test should include:
-Ensuring the prescribed maintenance routines are being completed and recorded within the system logbook.
-Condition check of fan, filters, electrics.
-Performance testing according to recommended face velocities.
-Visual check that operators are working within effective area.
-Visual check of effectiveness using, for example, smoke tubes.
Recommended face velocities are as follows:
Fume control: Minimum 0.5m/s
Light dust control: Minimum 1.0 m/s
Heavy dust control: 1.2 –1.5m/s
Completion of Thorough Examination and Testing should be recorded within the system logbook.

© Copyright AirBench Ltd 2019 Page 17 of 18
TECHNICAL
Arrangement
Technical Data
Model
Width
Depth
Height
Weight
Fan Power
Max Current
(mm)
(mm)
(mm)
(kg)
(kw)
(a)
FPW209084
1950
960
840
160
0.86
4.4
FPT209084
1950
960
840
160
0.86
4.4
Data shown is for standard models. Check the Commissioning Certificate for details specific to your unit.

© Copyright AirBench Ltd 2019 Page 18 of 18
DECLARATION OF CONFORMITY
Manufactured by:
AirBench Ltd.
6b Commerce Way,
Colchester,
Essex.
CO2 8HR
Responsible Person:
Simon Cook
Description:
Ventilated work bench known as “AirBench”
DECLARATION OF CONFORMITY
BY AIRBENCH LIMITED
RELEVANT DIRECTIVES
EMC Directive 2014/30/EU (when connected to standard mains sinusoidal supply).
Machinery Directive 2006/42/EC
Low voltage Directive 2014/35/EU
- EN-60204–1:2018 (Safety of machinery, electrical equipment of machines, general requirements).
- EN-60335-2-80 (Safety requirements for electric fans and regulators).
We; AIRBENCH Limited, declare that “AirBenches” when supplied as self contained equipment comply with the
directives detailed above and therefore comply with requirements of the Low Voltage Directive.
Simon Cook / Managing Director / 5th March 2021
Data shown is for standard models. Check the Commissioning Certificate for details specific to your unit.
This manual suits for next models
3
Table of contents
Other AirBench Control System manuals
Popular Control System manuals by other brands
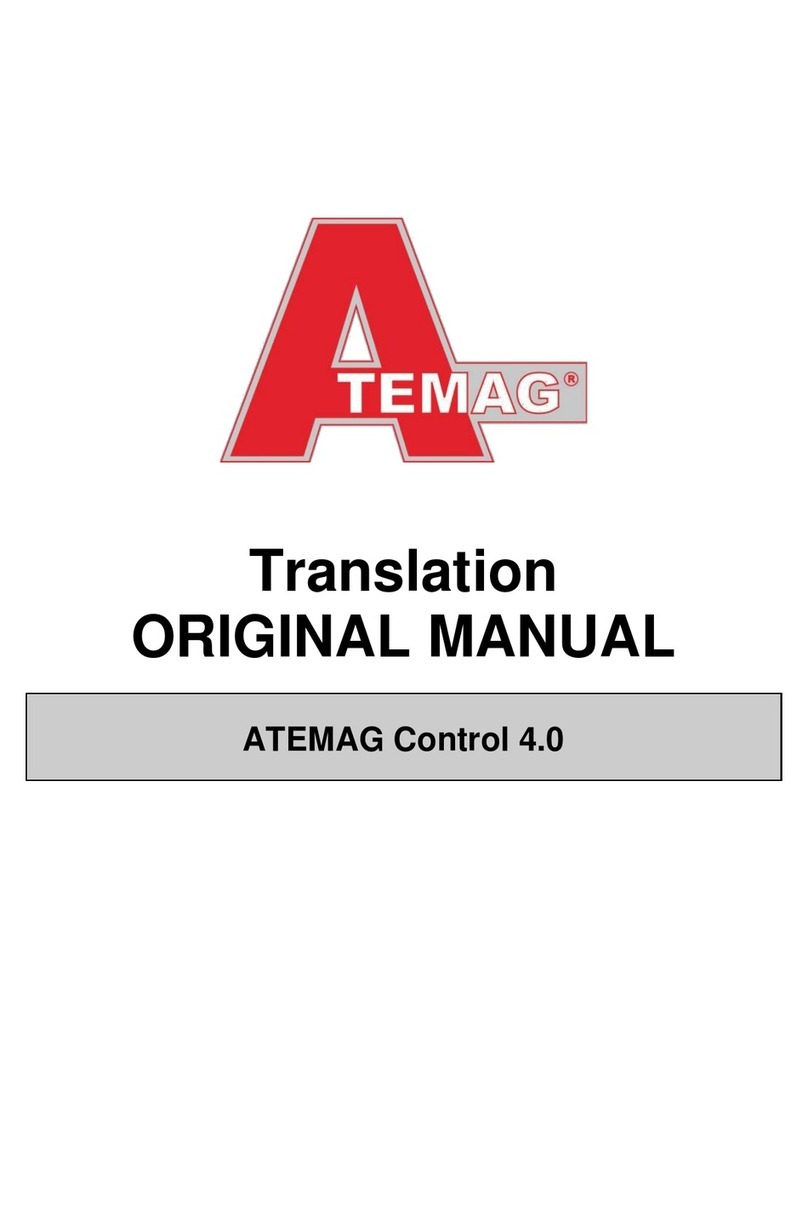
ATEMAG
ATEMAG Control 4.0 Translation original manual

Sutter Instrument
Sutter Instrument MPC-385 Series Operation manual
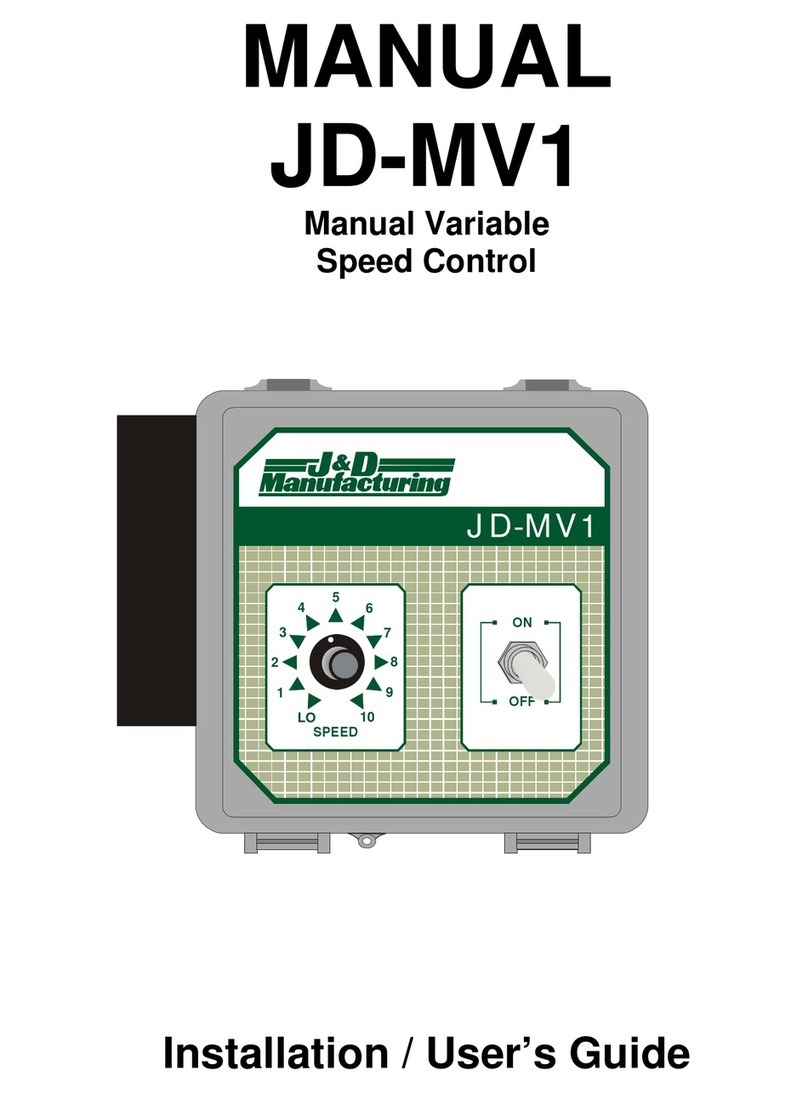
J&D MAnufacturing
J&D MAnufacturing JD-MV1 Installation & user guide
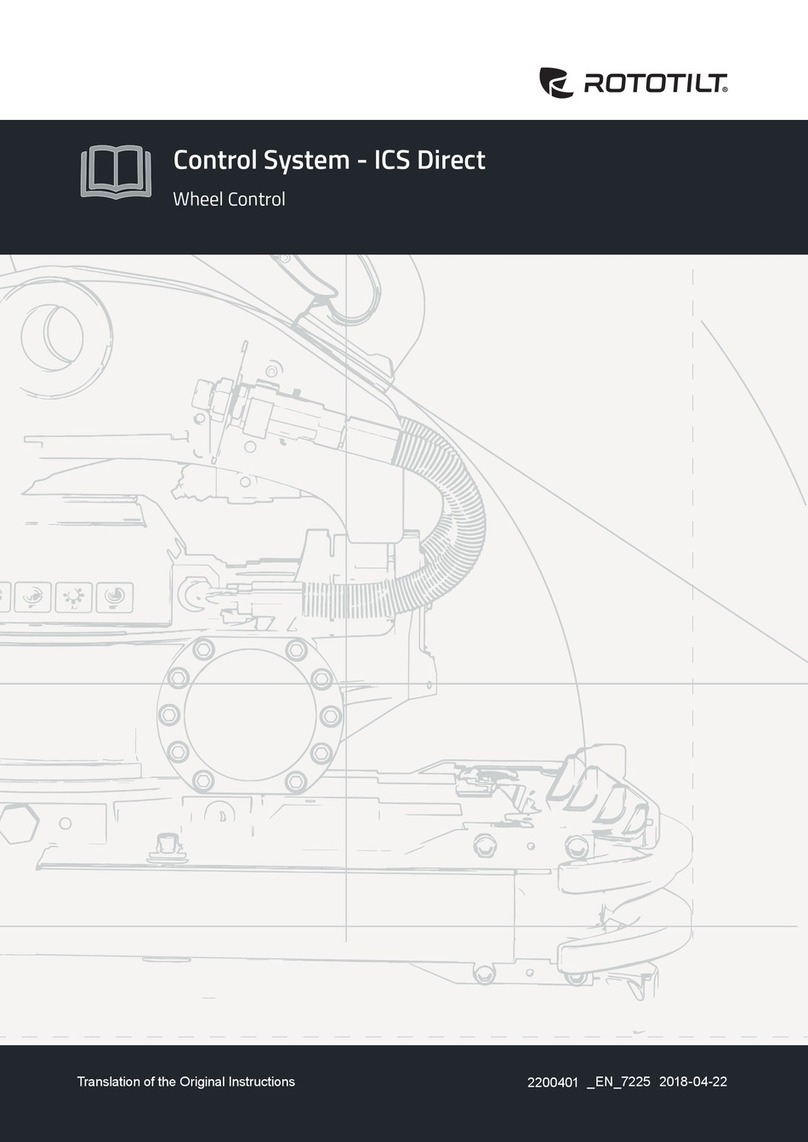
ROTOTILT
ROTOTILT ICS Direct manual
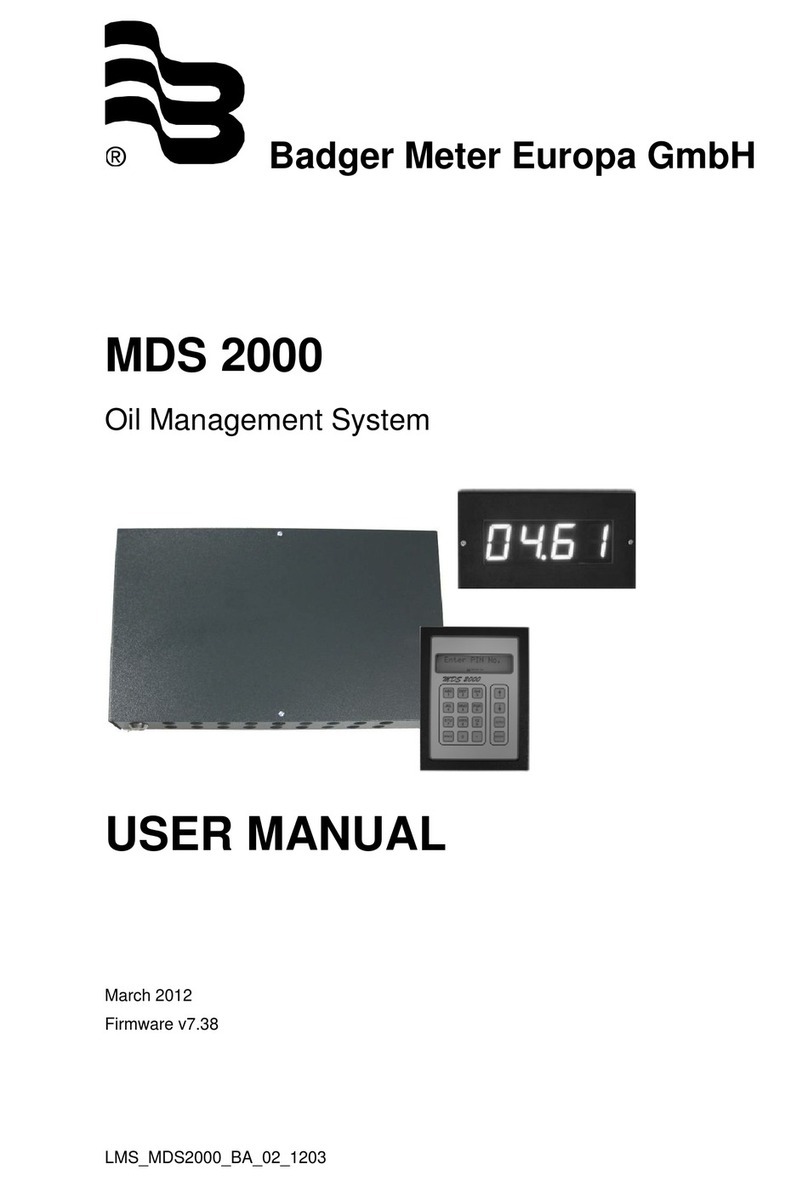
Badger Meter
Badger Meter MDS 2000 user manual
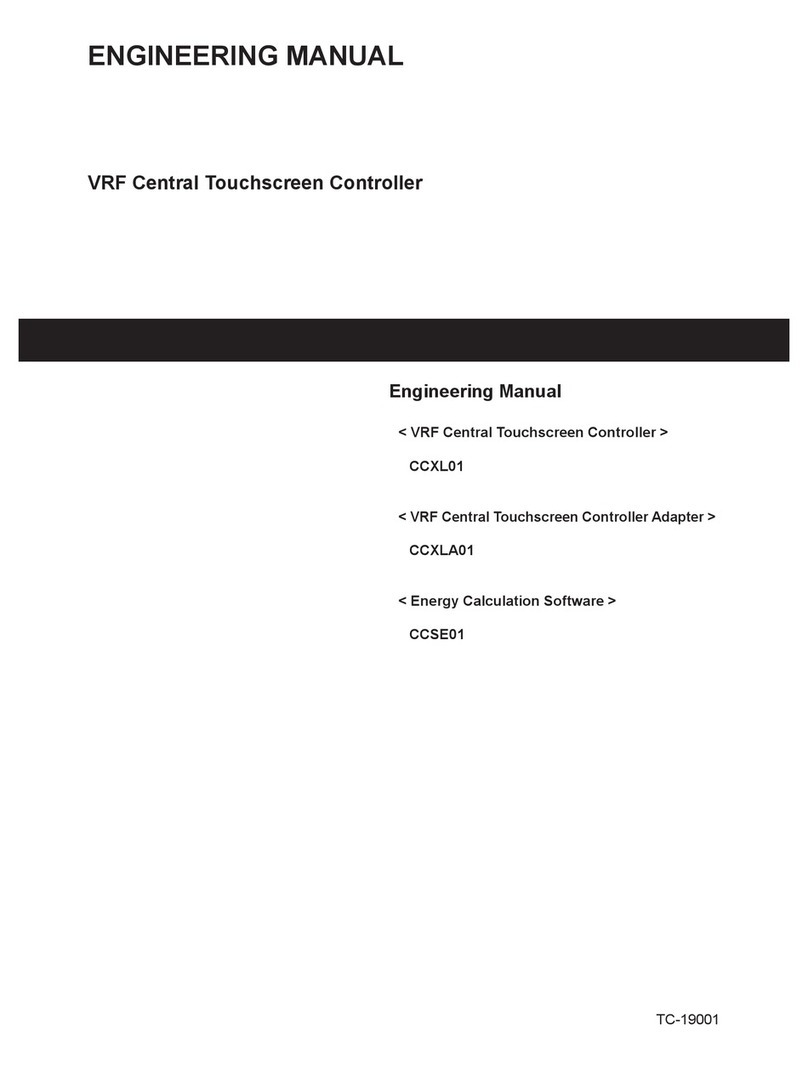
Johnson Controls
Johnson Controls CCXL01 Engineering manual