AIRTEQ 9600 Series User manual

9600 SERIES LOCK


9600 SERIES LOCK
PARTS LIST
ITEM QTY PART NUMBER DESCRIPTION
1 1 216-9600-070 LOCK BODY FRAME
2 1 216-9400-022 SPRING, TORSION
3 1 216-9400-026 SPACER, LATCHBOLT
4 1 146-9600-035 ASSY, LATCHBOLT, RH (SHOWN)
4 1 146-9600-034 (OR) ASSY, LATCHBOLT, LH
5 1 316-0000-059 ROLL PIN, 1/8 X 1/2
6 1 146-9600-005 ASSY, AIR CYLINDER
7 3 330-0000-133 FITTING, 90 BARB, 10-32 X .078
8 1 216-9600-084 SLIDE
9 1 316-0000-063 DOWEL PIN, 5/16 X 1 1/4
10 1 313-0000-093 WASHER, .317 ID X 505 OD X .030
11 1 146-9600-008 ASSY, DEADLATCH ROLLER BOLT
12 1 216-9600-115 DEADLOCK ARM
13 2 310-0832-010 SCREW, SHCS 8-32 X 1/4
14 2 310-1032-020 SCREW, SHCS., 10-32 X 2 1/2
15 1 160-9600-004ASSY, LOCK STATUS SWITCH (3WIRE)
16 1 315-0000-040 SPRING, DEADLATCH
17 1 216-9600-072 RACK (SHOWN)
17 1 216-9600-111 (OR) RACK, ELHB
18 1 216-9600-123 MOUNTING PLATE
19 1* 216-9600-075 MOGUL CYLINDER PLATE, RH
20 1* 216-9600-074 MOGUL CYLINDER PLATE, LH
21 12 310-0632-007 SCREW, FH SOC., 6-32 X 5/16
22 2 310-0000-034 SCREW, BH SOC., 6-32 X 3/16
23 1 331-0000-053 SOLENOID
24 2** 160-9600-000 ASSY, KEY SWITCH
25 4** 319-0000-052 SPACER, KEY SWITCH
26 1 146-9600-010 ASSY, GEAR
27 3*** 319-0000-045 SPACER, GEAR
28 3 310-0632-021 SCREW, SHCS, 6-32 X 7/8
29 2 216-9600-081 GEAR SUPPORT PLATE
30 5 310-1032-019 SCREW FH SOC., 10-32 X 5/8
31 1 330-1206-000 TUBING, 1/8 OD X 1/16 ID, POLYURETHANE, 22"
32 1 330-1206-000 TUBING, 1/8 OD X 1/16 ID, POLYURETHANE, 3 1/2"
33 2 310-0832-021 SET SCREW, 8-32 X 3/4
34 8 310-0000-009 SCREW, FH SOC., 10-32 X 1/2
35 2**** 310-0632-023 SCREW, Set, 6-32 X 3/8
36 2** 310-0632-022 SCREW, SHCS, 6-32 X 1/2
37 1 216-9600-082 BACK PLATE
38 1 216-9600-087 RIGHT SIDE COVER
39 1 216-9600-088 LEFT SIDE COVER
40 1 216-9600-094 SLIDE COVER
41 1 216-9600-078 HOUSING COVER
ITEM QTY PART NUMBER DESCRIPTION
42 1 216-9600-108 WIRE COVER
43 1 315-0000-018 SPRING, SLIDE RETURN
44 1***** 146-9600-028 ASSY, HOLDBACK LATCH, KBS (SHOWN)
44 1***** 216-9600-091 (OR) HOLDBACK LATCH, RH
44 1***** 216-9600-090 (OR) HOLDBACK LATCH, LH
45 1 216-9600-086 MOTOR MOUNT PLATE
46 2** 315-0000-041 SPRING, KEY SWITCH
47 2** 216-9600-083 KEY SWITCH ACTUATOR
48 1***** 315-0000-053 SPRING, HOLDBACK LATCH
49 1***** 216-9600-104 RLB LATCH
50 1 340-0000-205 SPLIT LOOM, 5"
51 1 330-0000-414 TUBING COUPLING HALF
52 2 310-0000-014 SCREW, SHCS, 2-56 X 3/8
53 6****** 310-0256-002 SCREW, SHCS, 2-56 X 9/16
54 1 216-9500-025 INSULATOR PAD
55 1******* 330-0000-415 TUBING COUPLING HALF (FIELD SIDE)
56 1 SEE WIRING DIAGRAM ASSY, 6 PIN MOLEX CONNECTOR
57 1 SEE WIRING DIAGRAM ASSY, 3 PIN MOLEX CONNECTOR
58 3******* 340-0000-204 WIRE TIE
59 2***** 313-0000-092 FLAT WASHER, #6, TYPE A
60 2***** 319-0000-064 SPACER, KEY SWITCH ACTUATOR
61 2***** 310-0632-024 SCREW, BH SOC., 6-32 X 1/4
62 2 313-0000-072 WASHER, PLASTIC
63 2 310-0632-006 SCREW, SHCS., 6-32 X 1/4
64 1 310-1032-027 SCREW, SHCS., 10-32 X 3/16
* KEYED ONE SIDE MODELS USE P/N 216-9600-076, MOGUL CLYINDER PLATE,
BLANK ON SIDE NOT KEYED.
.
** DIVIDE QTY BY 2 FOR KEYED ONE SIDE MODELS. PART NOT PRESENT ON
ALL MODELS.
*** QTY VARIES. KEYED ONE SIDE MODELS WITH MOGUL CYLINDER PLATE, LH
USE QTY OF 6.
**** KEYED ONE SIDE MODELS USE P/N 310-0632-006, SCREW, SHCS, 6-32 X 1/4. QTY (1)
PART NOT PRESENT ON ALL MODELS.
***** PART NOT PRESENT ON ALL MODELS.
****** QTY VARIES. MODELS WITH KEY SWITCH ONE SIDE USE QTY OF 4. MODELS
WITHOUT KEY SWITCH USE QTY OF 2.
*******PARTNOTSHOWN.
9600 Parts List -7-2007
9600 Assy 5-1-99.eps

R H
9600 SERIES LOCK
23
45
7
8
10
11
12
13
16
17
19
20
21
21
21
21
61
22
26
27
27
28
29
29
34
34
38
40
41
42
43
44
48
36
47
49
24 24
46
1
21
21
21
37
39
6
7
14
23
32
45
50
55
56
57
15
25
46
25 53
18
30
34
9
60 59 60
9600 Assy 5-1-99.eps
9600 Parts List 5-1-99.pm6
30
31
54
33
22
A
A
B
B
62
62
53
63
52
64 21
35

9600 SERIES LOCK
RECOMMENDED SPARE PARTS LIST
PART NUMBER DESCRIPTION
400-9600-000 9600 Air Cylinder, Repair Kit
160-9600-004 Assembly, Lock Status Switch
160-9600-000* Assembly, Key Switch
315-0000-041 Spring, Key Switch
315-0000-040 Spring, Deadlatch
315-0000-018 Spring, Slide Return
315-0000-053* Spring, Holdback Latch
340-0000-209 Terminal, Male
* NOT USED ON ALL MODELS
Updated 8/6/2007

LOCK MAINTENANCE INFORMATION

PNEUMATIC LOCKING DEVICES
A. Lubrication and cleaning
1. Each Airlock is well lubricated at the time of assembly. However,
all lubricants deteriorate eventually and need replacing on a
regularly scheduled basis in order to prevent equipment failure.
Airteq Systems recommends cleaning and lubricating each type
of lock according to the following instructions approximately
every (2) years. (Yearly for locks in high use areas).
9400 SERIES LOCK:
Remove the side cover plate and lubricate the angled ramp surface
on the sideplate that the deadlatch bolt dowel pin rides against.
Lubricate the stop side of the deadlatch bolt (back side). When
replacing the side cover, be sure the lever of the lock status switch
is not trapped under the retainer plate or actuator. The lower lock
mechanism should be checked and cleaned once a year
(or more often if special conditions exist) for accumulated dirt
and other debris that would interfere with proper operation.
Lubrication of upper lock mechanism is not necessary nor
recommended.
9600 SERIES LOCK:
Remove the slide cover. Remove the housing cover. Remove the slide
assembly . Clean and re-lubricate the slide with a thin coating of
recommended lubricant on the following surfaces:
a.) The 45º angled surface that contacts the deadbolt.
b.) The flat "shelf" that lifts the back of the latchbolt.
c.) The two small areas where the slide contacts the back wall
of the slide cavity.
d.) The edges of the two "rails" which contact the side of the
right side cover.
e.) The front and rear faces of the slide which contact the slide
cavity walls.
When replacing the slide assembly, hold the latchbolt retracted into
the lock housing while inserting the slide assembly near the top
of the cavity so that it drops in above the lock status switch lever arm
and not on top of it. Replace the housing cover and slide cover and
fasten securely.
Lubrication of the upper lock mechanism is not necessary nor
recommended.

PNEUMATIC LOCKING DEVICES
9700 SERIES LOCK:
Remove one side cover plate and lubricate the deadbolt shaft and
cam surface. Lubricate the latchbolt shaft and the stop sides of both
bolts.
9700P SERIES LOCK: (PARACENTRIC KEYING)
Remove one side cover plate and lubricate the deadbolt shaft and
cam surface. Lubricate the latchbolt shaft and the stop sides of both bolts.
KEYS AND LEVER TUMBLERS:
1) Key wear can cause improper operation of the lock and may damage
the lock's lever tumblers. Keys in constant use should be periodically
compared to a similar new key. When grooves due to wear are noted in
the steps on the key bit, the old key should be replaced.
2) When rekeying is performed, new tumbler stacks should be purchased
as a set including a new key. This enables Airteq to maintain complete
keying records.
WARNING:
1) Never use WD40 or similar silicone based lubricants.
2) Never use graphite powder as a lubricant.
3) Never lubricate the lever tumblers.
ALL LOCKS:
2. RECOMMENDED LUBRICANTS:
Multipurpose teflon based grease: Lubricate internal moving parts with
SYNCO SUPER LUBE WITH TEFLON or equivalent.
Stick lubricant: Lubricate the beveled surfaces of all latch bolts and strikes
with stick lubricant as required. Use PANEF WHITE STICK LUBRICANT
WITH SILICONE or equivalent.
B. Electrical:
1. The electrical system of this lock is operated on regulated 24VDC
current. Any other voltage or current condition is not acceptable
and will result in failure of the solenoid.
9000 Series Lock Maint 1-7-2000.pm6

TROUBLESHOOTING
9400, 9500 AND 9700 LOCKS
If the lock is not working properly, the following chart may be
used as a guide to locate and correct the problem.
Because the lock receives its signal from the electronic control
system, a thorough check of the control system should be con-
ducted. Using a volt/ohm meter known to be accurate, verify the
correct power signal input at the appropriate connector pin. If the
proper electronic signal is not evident, begin checking “ up-
stream “ from the connector. If the electronic signal input is
correct, the problem is within the locking device, use the follow-
ing chart to locate and correct the problem.
The recommended air pressure at the lock is 80 P.S.I.. If the cor-
rect air pressure is not evident, begin checking “upstream” from
the lock. If the air pressure is correct, the problem is within the
locking device, use the following chart to locate and correct the
problem.

PROBLEM CHECK
LATCHBOLT WILL NOT RETRACT *AIR SUPPLY TO LOCK
*MECHANICAL INTERFERENCE
*POWER INPUT TO UNLOCK SOLENOID
(POWER SHOULD BE PRESENT
DURING LOCK OPEN CYCLE)
*BROKEN OR LOOSE WIRING
*FAULTY OR CONTAMINATED
SOLENOID VALVE
LATCHBOLT WILL NOT EXTEND *MECHANICAL INTERFERENCE
*BROKEN OR LOOSE WIRING (SHORT
TO GROUND)
*POWER INPUT TO UNLOCK SOLENOID
(POWER SHOULD NOT BE PRESENT
DURING LOCK SECURE CYCLE)
*FAULTY KEYSWITCH
LOCK RETRACTS/EXTENDS SLOWLY *AIR PRESSURE TO LOCK
*MECHANICAL INTERFERENCE
*FAULTY OR CONTAMINATED SOLE-
NOID
VALVE
*MECHANICAL INTERFERENCE
*PROPER ENGAGEMENT OF KEY
CYLINDER CAM IN LOCK
*BROKEN OR LOOSE WIRING
(SEE WIRING DIAGRAM)
*BROKEN OR LOOSE WIRING
(SEE WIRING DIAGRAM)
MANUAL OVERRIDE NOT WORKING
PROPERLY
DOOR POSITION SIGNAL NOT GIVEN
LATCHBOLT POSITION SIGNAL NOT
GIVEN
This manual suits for next models
4
Table of contents
Other AIRTEQ Lock manuals
Popular Lock manuals by other brands
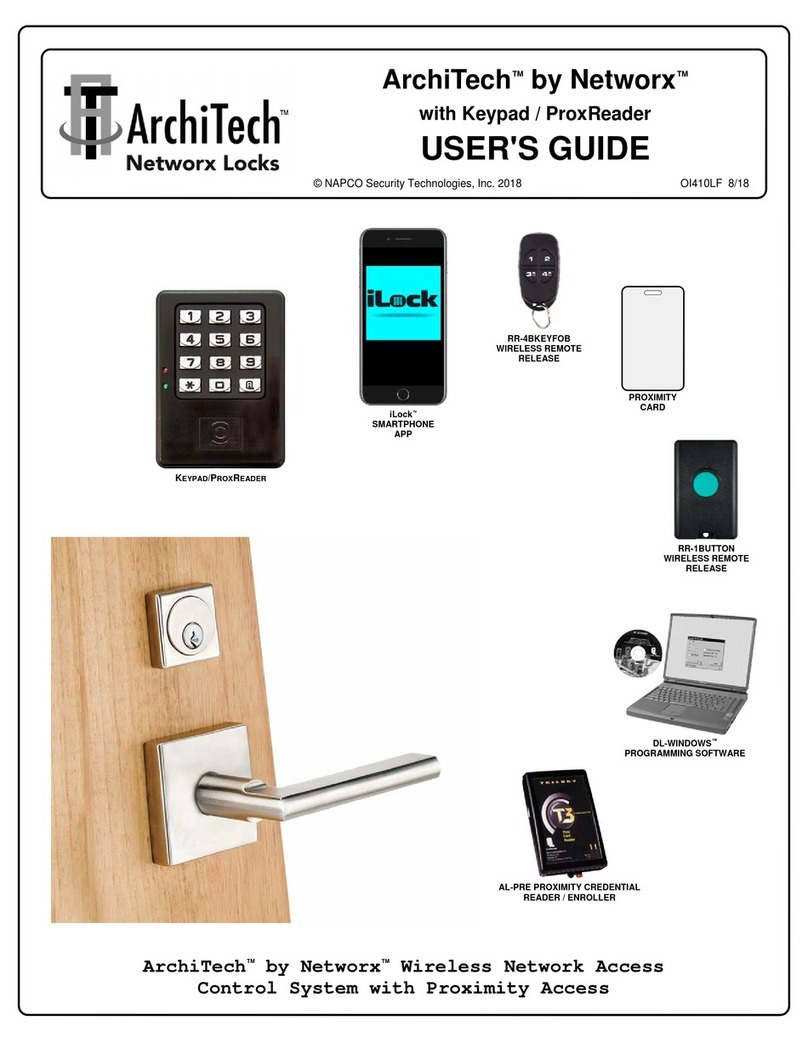
NAPCO
NAPCO Networx ArchiTech user guide
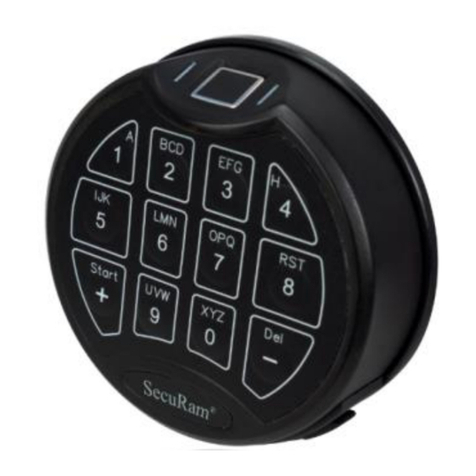
Securam
Securam ScanLogic Optical Programming Instruction
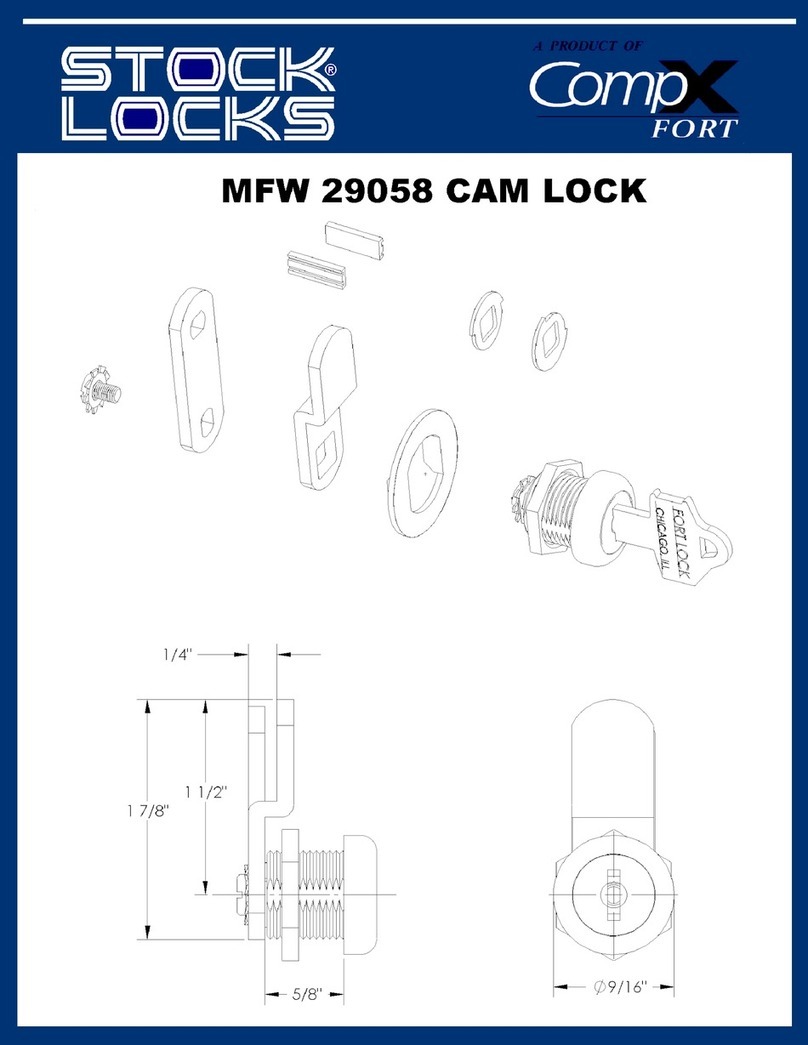
COMPX
COMPX MFW 29058 Dimensional drawing
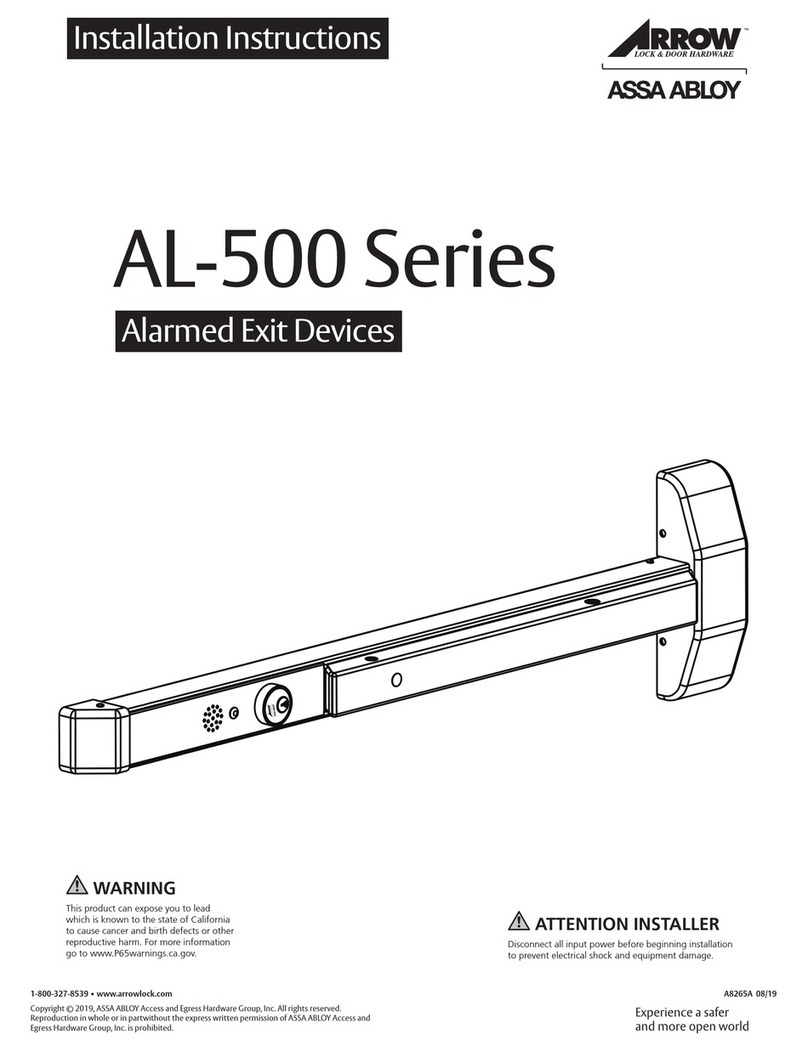
Assa Abloy
Assa Abloy Arrow AL-500 Series installation instructions

Kaba
Kaba Simplex 6200 Series installation instructions
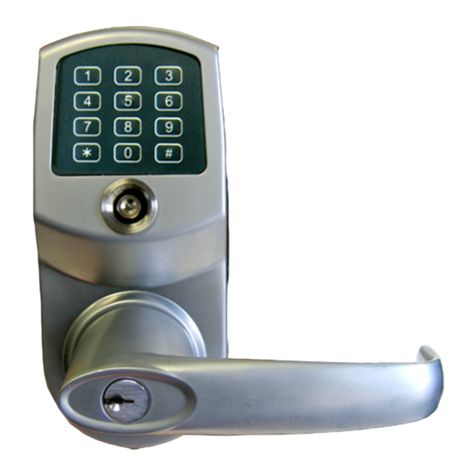
TimePilot
TimePilot CrossOver X45 Installation