Alico YP5000 Series User manual

YP5000 SERIES SOFT STARTER
User Manual

Preface
Thanks for choosing Our company the soft starter YP5000. The starter used to
control the rattrap type three-phase asynchronous motor start and stop. Before
using it, please read this manual carefully so as to guarantee correct operation.
Caution
Ø
Ø
Ø
Ø
Ø
Ø
Ø
Ø
Please read the manual carefully before installating of the product in
order to ensure correct installation and operation. The soft starter
parameters must be changed by professional personnel;
Only professional and technical personnel is allowed to install of YP5000
series soft starter;
Must guarantee power match between the motor and YP5000 series soft
starter, please be sure to operate according to the user manual;
Do not connect capacitor to the soft starter output, or it will cause damage
of the soft starter;
Please wrap the input and the output of the copper wire with insulating
tape after installation;
Must lock the keyboard when using remote control;
Soft starter housing must be fixed to the ground;
Please cut off the line power when maintaining.
Although this manual is edited and proofread very carefully, there may still be
small mistakes. The features and operation may be different from the actual
product due to possible modification of product design, and this may not be
considered in the contract. Thank you very much for your understanding.
YP5000 Soft Starter User Manual
V1.0
-1-

YP5000 Soft Starter User Manual
V1.0
Contents
1 Notes...................................................................................................................4
1.1 Inspection.....................................................................................................4
1.2 Nameplate....................................................................................................4
1.3 Soft Starter Model.........................................................................................4
1.4 Product Apperance........................................................................................5
2 Installation and Connection...........................................................................5
2.1 Environment..................................................................................................5
2.2 Installation Requirments................................................................................6
2.3 Wiring...........................................................................................................6
2.4 Main Circuit and Terminal..............................................................................8
2.5 Main Circuit Wiring Diagram........................................................................10
2.6 Control Terminal Connection.......................................................................11
2.7 Terminal Configuration Diagram..................................................................12
2.8 Wiring Diagram...........................................................................................13
2.9 Relay and Remote Control Wiring Diagram..................................................14
3 Operation.........................................................................................................14
3.1 Inspection and Preparation before Operation...............................................14
3.2 Operating Method........................................................................................15
4 Keyboard Panel..............................................................................................16
4.1 Appearance................................................................................................16
4.2 Key Function...............................................................................................16
5 Code Setting Functions................................................................................18
6 Function Specification..................................................................................19
6.1 Code FE Used to Program Running Output Relay Action Time......................19
6.2 Code FC Parameter Allowed Modification....................................................20
6.3 Code FU Set Underload Protection Function................................................20
-2-

7 Revise Setting Parameter.............................................................................21
8 Useful information.........................................................................................22
9 Protection Function.......................................................................................22
9.1 Protection Function Specification.................................................................22
9.2 Protection Function Setting..........................................................................23
9.3 Protection and Tripping Curves....................................................................25
10 Protection......................................................................................................26
11 Troubleshooting...........................................................................................27
12 Starting Mode...............................................................................................28
12.1 Current Limit Starting Mode.......................................................................28
12.2 Voltage Ramp Start Model.........................................................................29
12.3 Kickstart Mode..........................................................................................29
12.4 Current Ramp Start Mode..........................................................................30
12.5 Voltage Limiting Double Loop Start Mode...................................................30
12.6 Soft Stop Mode..........................................................................................31
12.7 Free Stop Mode.........................................................................................31
13 Dimension......................................................................................................32
13.1 YP5000-4T0110L~YP5000-4T0750M........................................................32
13.2 YP5000-4T0750L~YP5000-4T2000L ........................................................32
13.3 YP5000-4T2500L~YP5000-4T3200L.........................................................33
13.4 YP5000-4000L..........................................................................................33
14 Application....................................................................................................34
15 Rs485 Communication................................................................................34
15.1 MODBUS Communication Protocol............................................................35
16 External Parts list.........................................................................................40
YP5000 Soft Starter User Manual
V1.0
-3-

1.1 Inspection
Please carry out checks on the products after they arrive, if the product is found
defective or not a correct model, please contact your vendor.
1 Notes
Ø
Ø
Ø
Ø
Check on the nameplate, confirm the specifications of your order
Check if there is any damage on the appearance during transport, such as the
bending of the shell and fuselage and the damage or loss of the components;
In addition to soft starter, there are also a user manual and a product inspec-
tion certificate ;
Must lift the body of the soft starter in handling. It can not promote the circuit
board control box, or it may cause damage or personal injury.
;
1.2 Nameplate
MODEL: YP5000-4T0370L
INPUT: AC380V 50Hz
POWER: 37KW/75A
ALMO132
SOFT STARTER
4 3 6 5 3 5 3 6
1.3 Soft Starter Model
YP5000
1
0370
4
L
5
4
2
T
3
No. Content
YP5000
Key
Abbreviation
Voltage level
Power adapter
Load type
Input voltage
1
2
3
4
5
2:220V 4 380V:
5.5KW~500KW
L Heavy load type M Light load type: :
S Single T Three phase: :
YP5000 Soft Starter User Manual
V1.0
-4-

1.4 Product Apperance
2.1 Environment
2 Installation and Connection
Contents
Conforming to :GB14048.6-98( )
380V±15%
50Hz
Squirrel cage three-phase asynchronous motor
Depending on the load, it is recommended that no
more than 20 times per hour.
IP40(Negotiable)
15G11MS
Altitude above 3000M, vibration force device 0.5G below.
-10℃ to +40℃ w/o derating ( between 40℃-60℃,
rasing each 1℃ will cause 1.2% current derating)
-25℃~70℃
90% RH in Max. (no dewing)
1000 m without derating (above this, derate the
current by 0.5% for each additional 100 m)
Natural air cooling
No requirement
Items
Standard
Three-phase
supply voltage VAC( )
Applicable motor
Start frequency
The protective level
Shock resistance
Vibration resistance
Ambient temperature
Storage temperature
Ambient humidity
Maximum operating
altitude
Cooling
Maximum installation angle
Frequency
YP5000 Soft Starter User Manual
V1.0
-5-
The bypass contactor
(L21、L22、L23)
Power supply
terminal
( )R、S、T
Circuit board
control box
Communication
interface
Frame
Keyboard panel
,Motor connecting
terminal
(U、V、W)
Control circuit
terminal

2.2 Installation Requirments
Ø
Ø
The soft starter should be installed vertically, do not flip, ramp or horizontal
installation. Use screws to secure the structure.
For vertical installation of soft starter, adequate cooling room should be left,
so as to ensure effective cooling, see following drawing for details.
YP5000 Soft Starter User Manual
V1.0
ENT
确认
SET
设置
RUN
启动
STOP\/RS
停止/复位
DIGITYAL PANEL
>100mm
>
(mm)
50
>100mm
>
(mm)
50
Air inlet
Air outlet
>
(mm)
50
SOFT STARTE R
PIC 2-2-1
2.3 Wiring
Ø
Ø
Ø
Ø
Please note the following instructions when wiring. Fig. 2-3-1 is the basic
wiring diagram.
The power supply should be connected to the main circuit, power supply
terminals R, S, T require no phase sequence. If the power supply is connected
incorrectly, the soft starter will be damaged;
Ground terminal must be well grounded, can prevent electric shock or fire
accident and reduce noise;
Both ends of the wire must be pressed to ensure high reliability of connection.
-6-

Fig. 2-3-1
FU
Ue=
100%
KM
A1 A2
N
or
L3
K3
01
02
7
8
9
10
11
03
04
05
06
K2
K1
1 2
3 4
7 6
R
S
T
U
V
W
The main circuit
With bypass electromagnetic contactor
(KM)
Distribution
circuit breaker
Three phase
power supply
M
Motor
Ground
Ins tant aneous stop
Stop
Start
Common ends
Analog output
(DC4~20mA)
12
Control circuit
RS485 communi cation
Total pressure
output
Delay out
(programmable)
The fault output
+DC12V
YP5000 Soft Starter User Manual
V1.0
-7-

YP5000 Soft Starter User Manual
V1.0
2.4 Main Circuit and Terminal
Table 2-4-1 Main circuit and terminal wiring
Terminal Name
AC Main Circuit Power Input
Terminal Symbol
R. S. T
L21. L22. L23
U. V. W
Description
Connected with three-phase
AC Power Supply
Soft Starter Output Terminal Connected with three-phase
asynchronous electric machine
External Bypass Contactor
Terminal
Connected with bypass
contactor
Grounding Terminal Grounding
G
Main circuit power input terminals(R. S. T)
1. Main circuit power input terminals R, S, T are connected to the three-phase
AC power supply by line protection circuit breakers or circuit breakers with
leakage protection regardless of the connected phase sequence.
2. Don’t use the main circuit power ON / OFF method to control the soft start
operation and stop. After the soft starter is energized, select the control terminal
on the soft starter or the RUN and STOP keys on the keyboard panel to control.
3. Do not connect with single power supply.
Soft starter output terminals(U. V. W)
1. The soft starter output terminals are connected to the three - phase motor in
the correct phase sequence. If the direction of rotation of the motor is not
correct, you can exchange any two phases wiring of U, V, W.
2. The soft starter output side can not be connected to the phase-in capacitor
and the energizing absorber.
3. When the line between the soft starter and the motor is long, the distributed
capacitance between the wires will produce a large high frequency current,
which may cause the soft start overcurrent trip, the leakage current increases,
and the current display accuracy is poor. Therefore, it is recommended that the
motor connection should not exceed 50 meters.
-8-

YP5000 Soft Starter User Manual
V1.0
Bypass connection(L21. L22. L23)
Bypass connection terminals L21, L22, L23, be sure to connect the electromag-
netic bypass contactor, otherwise it will burn the soft starter. Soft starter start is
completed, the main circuit power device (SCR) exit, while bypassing the
electromagnetic contactor work, then the motor into normal operation, phase
sequence can not be wrong.
Soft starter ground terminal(G)
For safety and noise reduction, the ground terminal G of the soft starter must
be well grounded.
Danger
Ø
Ø
Ø
Ø
Confirm the input phase number of the soft starter, the rated input voltage
and the phase number of the AC power, voltage value is the same;
Don’t connect AC power supply to the output terminals(U. V. W);
Bypass electromagnetic contactor must be connected to the phase
sequence connection;
Otherwise it may damage the accident.
-9-

YP5000 Soft Starter User Manual
V1.0
2.5 Main Circuit Wiring Diagram
-10-
YP
soft starter
5000
Three-phase asynchronous motor
M
Bypass
contactor(KM)
2 4 6
RT
S
L21
L22
L23
Circuit breaker or leakage
circuit breaker
Three phase power input
1 3 5

YP5000 Soft Starter User Manual
V1.0
2.6 Control Terminal Connection
Control circuit terminal function Table 2-6-1, according to the different function
settings, control terminal function and connection is also different.
Table2-6-1 Control circuit terminal function table
Bypass
output
Terminal 1. 2 is bypass output which is used to
control bypass contactor
Contact
output
01. 02 01
02
FU
A1 A2
L1
L3 or N
KW
Run output
(D)elay
Terminal 3. 4 is programmable relay output,
delay time set by the code F4, output function time
set by the code FE. This terminal is normally
open passsive pot. Capacity is AC250V 5A./
03. 04
Fault
output
Terminal 5. 6 is error output:
which will clsse when soft starter error or power lose,
Capacity is AC250V/5A.
05. 06
Transient
stop input
The motor will stop immediately when 07 and 10 turned
off (or in series with other protector closed point).
07
Contact
input
Soft stop
input
Start input
Common
terminal
The motor will slow down and soft stop when 08
and 10 turned off (or stop by itself)
The motor will start to run when 09 and 10 closed.
Common terminal of contact input signal.
08
09
10
Analog
output
Terminal 11. 12 is 0~20mA DC analog output.
Which is used to inspect the motor current. The
max 20mA indicates motor current is 4 times of
soft starter rated current. Which can be viewed by
extra 0-20mA current meter. The max resistor of
output load is 300Ω.
11. 12
Analog
output
RS485
communi-
cation
input/output
Classi-
fication
Terminal
name Description
Terminal
mark
Rs485 communication input/output terminal, can be
used for multiple soft starters connection.
DB
Communi-
cation
-11-

YP5000 Soft Starter User Manual
V1.0
Contact input terminal
1. When controlling the soft starter start and stop functions with an external
terminal, set the code FB to external control.
2. For remote control requirements, it is recommended to use (two wire) control.
3. The contact signal input terminals and common terminals are generally
closed/disconnected( ), soft starter, motor and wiring will produce
interference, so the line as short as possible (under 20 meters ), the cable
please use the shielding line.
4. The wiring of the control terminal must be kept away from the wiring of the
main circuit as much as possible, otherwise it may cause erroneous operation
due to interference.
ON/OFF
2.7.1 Main Circuit Terminal Drawing
2.7 Terminal Configuration Diagram
2.7.2 Control Circuit Terminal Drawing
01 02 03 04 05 06
bypass output fault output
delay output
07 08 09 10 11 12
instantaneous
stop
analog output
stop start-up
common terminal
-12-
power
incoming line
(R、S、T)
connect by-pass
contactor
(L21. L22. L23)
YP5000 series 11KW~75KW
G
connect
electrical
mechine
(U. V. W)
connect by-pass
contactor
(L21. L22. L23)
power
incoming
line(R. S. T)
connect
electrical
machine
(U. V. W)G
YP5000 75KW~800KWseries

YP5000 Soft Starter User Manual
V1.0
07
three lines for controlling
instantaneous stop
stop
start-up
common terminal
08
09
10
controlling terminal wire0.75-1.25mm2
07
two lines for controlling
instantaneous stop
stop
start-up
common terminal
08
09
10
K
K closed means start-up, K broke means stop
2.7.3 Controlling Circuit Terminal Wiring
2.8 Wiring Diagram
QF
L1 L2 L3
L21
1 3 5
2 4 6
M
A
R S T
UV W
01 02
07 08 09 10 11 12
L22
L23
03 0504 06
+-
N or L1
A1
A2
FU
KM
Fault
output
Delay
output
Output
bypass
Analog
output
(DC4~20mA)
Com Start Stop Instantaneous
stop
With bypass
electromagnetic
(KM)
-13-

YP5000 Soft Starter User Manual
V1.0
2.9 Relay and Remote Control Wiring Diagram
07
relay controlling method
instantaneous stop
stop
start-up
common terminal
08
09
10
KA
K
LKA
KA
NLN
KA
KS
K is the normally closed point (eg. thermal protector) connected to other protector,
the factory default setting is short-circuit.
07
relay controlling method
instantaneous stop
stop
start-up
common terminal
08
09
10
KA
K
3.1 Inspection and Preparation before Operation
3 Operation
Check and preparation before start are necessary:
Check if the wiring is correct. In particular, the output terminal can not be
connected to the power supply, bypass contactor is connected, and confirm
that the ground terminal is well grounded;
Make sure there is no short circuit or short circuit to ground between terminals
or exposed live parts.
Ø
Ø
-14-

YP5000 Soft Starter User Manual
V1.0
3.2 Operating Method
Ø
Ø
Ø
Ø
Ø
Ø
Ø
Ø
Ø
When power on and show <Ready> state, press start button;
Enter the setting item FP by the rated current value on the motor plate;
Check the motor after the start if the direction of rotation is correct, the
operation is normal, if abnormal, you can press the stop button or cut off the
power if necessary;
If the motor starting condition is not ideal, please refer to page P19 soft
starter start mode and application section selection appropriate;
When the starting voltage code F0 (voltage mode) or the current limit value
code F5 (current mode), the motor starting torque is increased;
After the soft starter is energized, do not open the cover to avoid electric
shock;
In the process of power test run, if found the abnormal phenomena, such as
abnormal sound, smoke, or smell, etc., should quickly cut off the power and
find out the reason;
If the fault is displayed after power-up or on startup, and ErrXX is displayed,
check the cause according to the displayed fault code;
Press the stop button or the external control stop button to reset the fault
condition.
Note:
When the environment temperature is less than -10 ℃, should preheat more than 30
minutes before start up.
-15-

YP5000 Soft Starter User Manual
V1.0
4.1 Appearance
4 Keyboard Panel
The keyboard panel has lots of operating functions such as keyboard panel
operation, stop function data validation and change, and various status confirm-
ation function.
4.2 Key Function
Button Main function
Display 【Ready】 status. Press this key to start the start, and
display the start state, motor current - A
Start
1. the normal operation shows the motor current - A (current value),
press this button to stop, soft stop display (soft stop);
2. the state motor current - A this key to reset the fault status of the
function.
Stop
Display READY state, press this button to enter the menu settings,
display F0:30% or F0:40%,press this button again, the colon
flashing, then modify the parameters according to the up/down key.
Set
1. When the parameters are modified, press this button to save,
show GOOD data to read-in and ring two twice, it means data
stored, then press this button or stop button again to exit;
Confirm
-16-
data function
start
stop/reset
set
up/ down
confirm

YP5000 Soft Starter User Manual
V1.0
Button Main function
2. Press this button and display input power supply voltage has
been input already;
3. Press confirm button to power on, to set parameters to restore
the factory value.
Confirm
1. Enter the menu settings, to press this button to modify paramet-
ers (the colon is not flashing, press xx: XXX button to modify
function code. The colon is flashing, press this button to modify
data).
2. Press this button can be observed A current, P power, H over-
load heat balance display in the operation.
Up/Down
Table 4-2-1 Button function specification
When digits number > 999 three-digit number, the last decimal light up, means
the mantissa zero padding.
There is prompt sound happened in soft starter when press the button, otherwise
this button is invalid;
remove the keyboard panel, (put it to the outside of the cabinet) lead distance < 3
meters.
-17-

YP5000 Soft Starter User Manual
V1.0
Parameter setting code as following table
5 Code Setting Functions
Specifications
50-500%
50-200%
100-140%
startup effective voltage ramp mode; current
mode starting voltage is 40%.
current limit mode invalid
set 0 as free parking, set 0 when 1 connect
two wires
use the countdown time to delay, set 0 as not
delay
used for programmable relay output
current limit mode is valid, the max voltage
ramp mode current limit is 400%
motor rated current percentage
lower than setting value protection
value higher than setting value protection
0 limit current,1 voltage,2kick +voltage,
4current slope,5 double closed-loop
30%
16S
0S
0S
0S
30-80%
2-60S
0-60S
0-999S
0-999S
Setting
range
Default
Setting
280%
100%
80%
120%
1
40-90%
0-5
Startup
voltage
Startup time
Stop time
Startup
interval delay
Program
delay
Name
Starting limit
current
Max working
current
Over-voltage
protection
Startup mode
Under-voltage
protection
F0
F1
F2
F3
F4
Code
F5
F6
F7
F8
F9
4
0-4
Protection
level
FA
0 keyboard,1 keyboard+control 2 external
control, 3 external control +communication,4
keyboard+ external control +communication
1
0-6
Operating
control
method
FB
0 primary, 1 underload, 2 stantard, 3 overload,
4 senior
specs please refer to P12
1
0-2
Parameters
modification
is allowed
FC
0
0-63
Communication
address
FD used for many soft starter communicate with
upper computers
7
0-19
Program
output
FE current running relay output (03. 04
terminal )setting
80%20-100%
Soft stop limit
current
FF specs refer to P21
Rated
value
---
Motor rated
current
FP used for inputting rated current
-18-

YP5000 Soft Starter User Manual
V1.0
---
---
Underload
Protection
FU
0=close the protection for both the voltage
imbalance and lack -phase
1=close the protection of voltage imbalance,
start the protection of lack-phase.
2=open the protection of voltage imbalance,
close the protection of the lack-phase
3= the protection for both the voltage
imbalance and lack-phase
open
30-3
lack-phase
protection
FL
specs refer to P13
Specifications
Setting
range
Default
Setting
Name
Code
Note:
Øset the term F6 maximum work is taken to allow the motor to determine the
number of FP based on the calculation of the maximum running current,
beyond this value will do inverse time thermal protection;
Øset the state if more than 2 minutes without key operation, will automatically
exit the set state;
Ø in the soft and soft stop process can not set the parameters, other states can
be set parameters;
Øif the press key to power on, you can set the parameters (except FE) to
return to the factory value.
6.1 Code FE Used to Program Running Output Relay Action Time
6 Function Specification
Programmable relay output function has two modes, that is, programmable timing
output mode and programmable state output mode.
When the setting item FE is 0-4 (10-14), the programmable output operates in the
timing output mode, and sets the starting time of the output.
The following table:
Table 6-1-1
Programme
output moment
Issue startup
command
Start to
kick-in
Bypass
operating
Issue stop
order
Stop
complete
FE Setting Value 0(10) 1(11) 2(12) 3(13) 4(14)
ØThis mode of operation includes a 999 second timer, set by setting item F4. If
F4 is not 0, the start time set by the setting item FE starts counting;
-19-
This manual suits for next models
7
Table of contents
Popular Controllers manuals by other brands

Johnson Controls
Johnson Controls FEC26 Series installation instructions
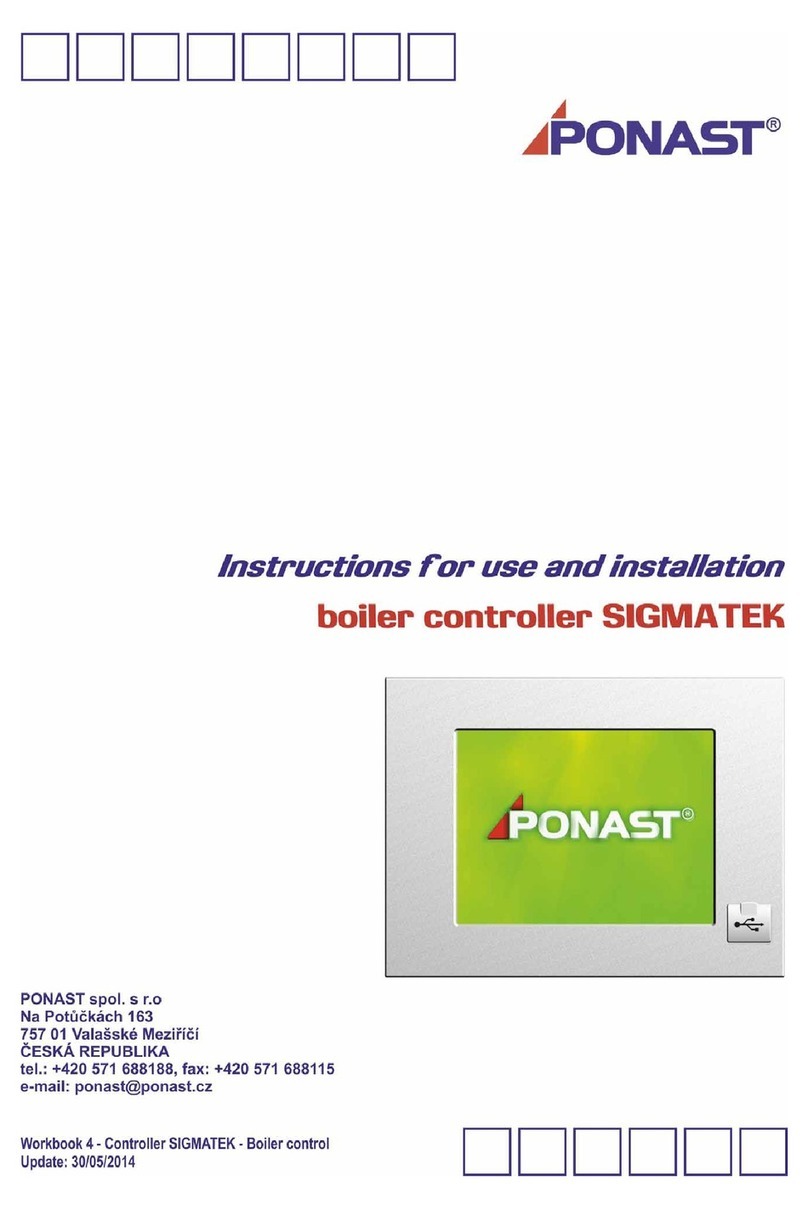
Ponast
Ponast Sigmatek Instructions for use and installation
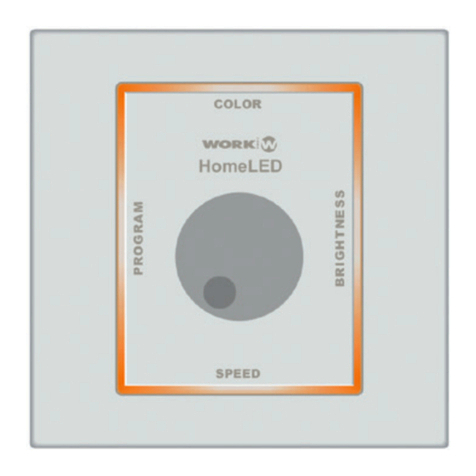
AUTLED
AUTLED LC-006-001 user manual

Nidec
Nidec LEROY-SOMER R251 Installation and Maintenance
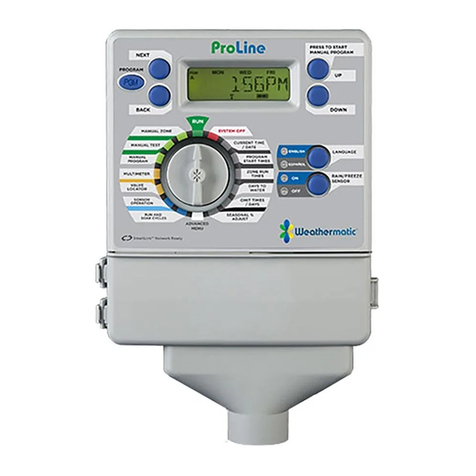
Weathermatic
Weathermatic ProLine 800 Series owner's manual
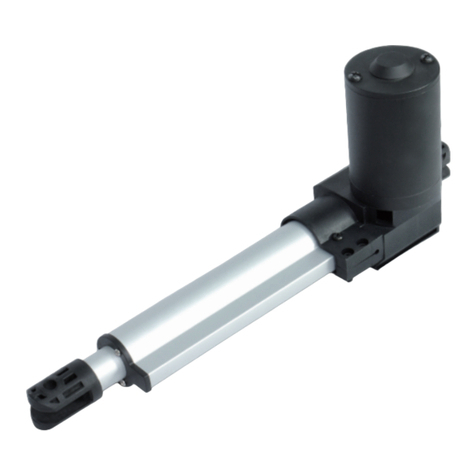
MOTECK
MOTECK FD60 user guide
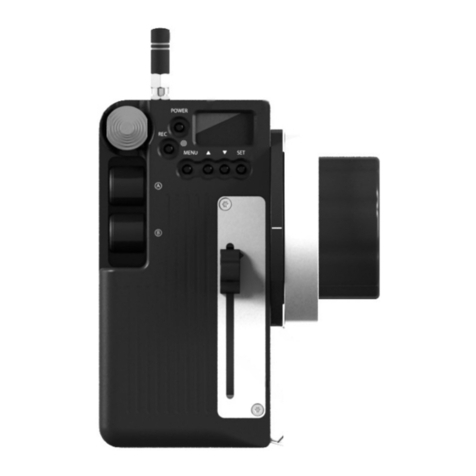
RTMOTION
RTMOTION MK3 user guide
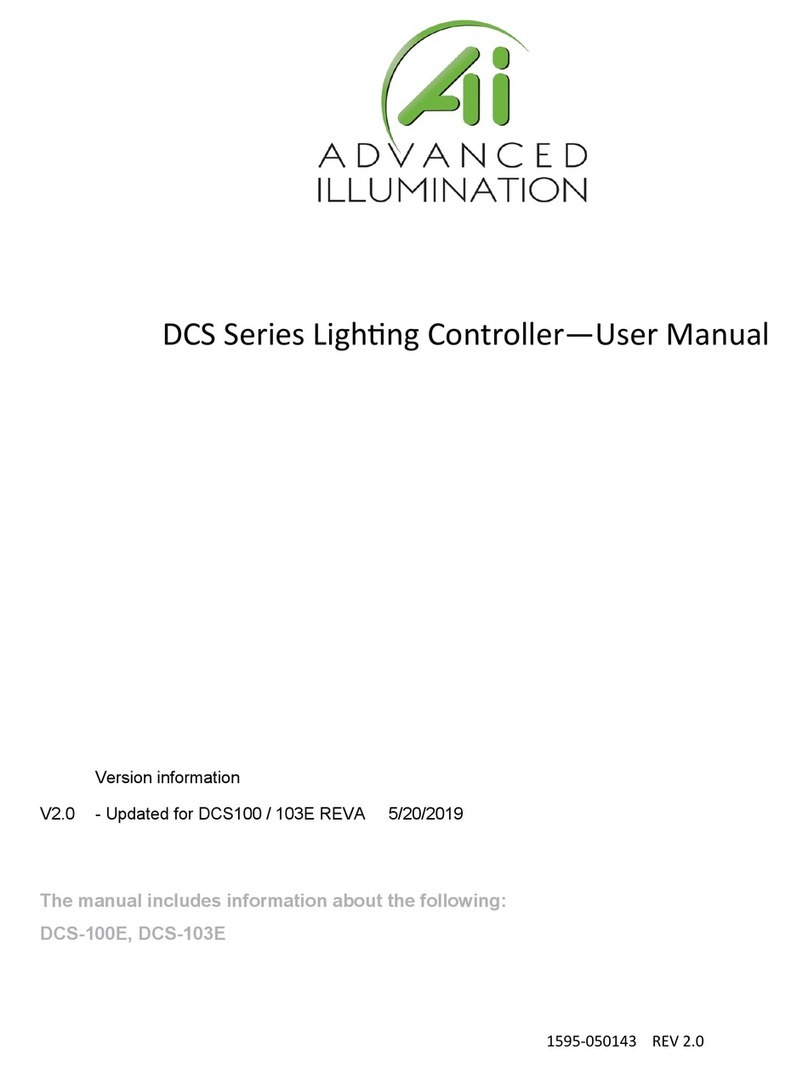
Advanced Illumination
Advanced Illumination DCS Series user manual
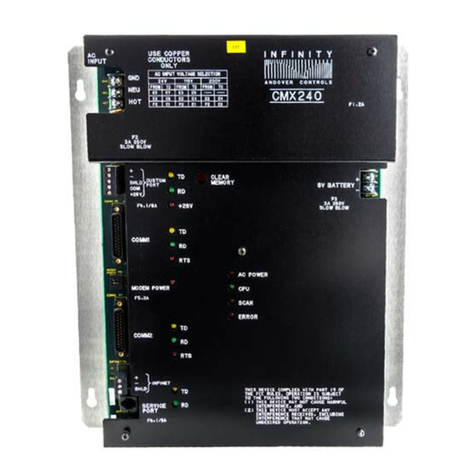
Andover Controls
Andover Controls CMX 240 Series installation guide
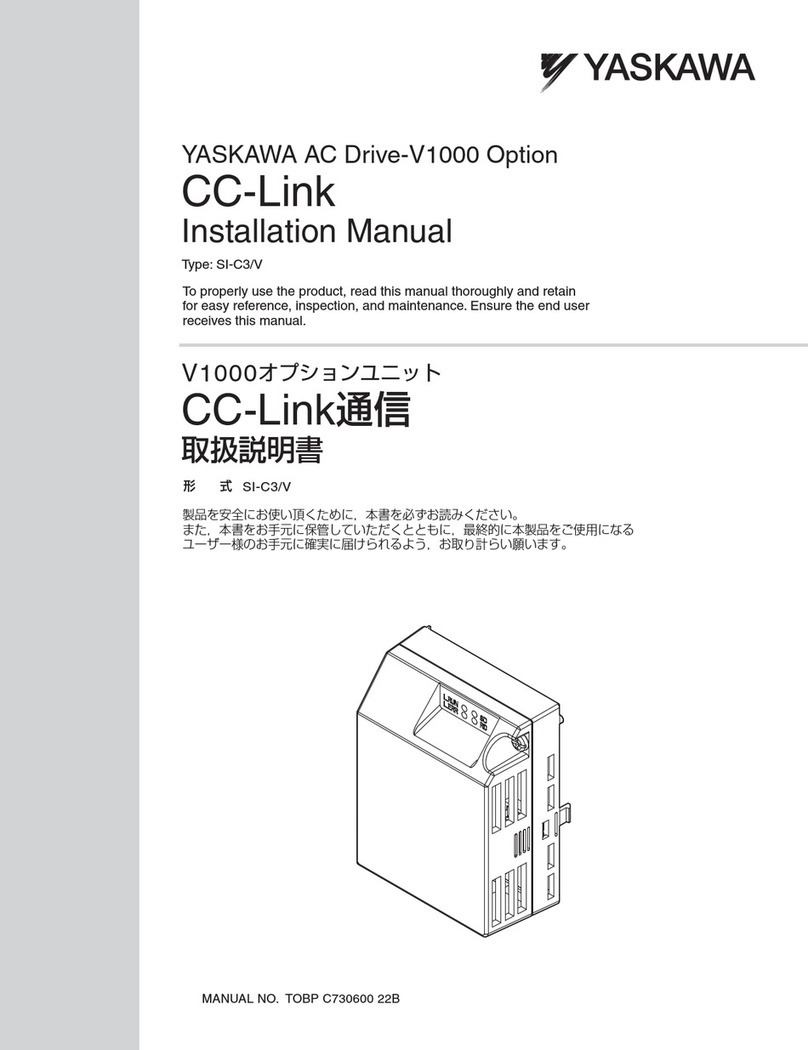
YASKAWA
YASKAWA PROFINET V1000 installation manual
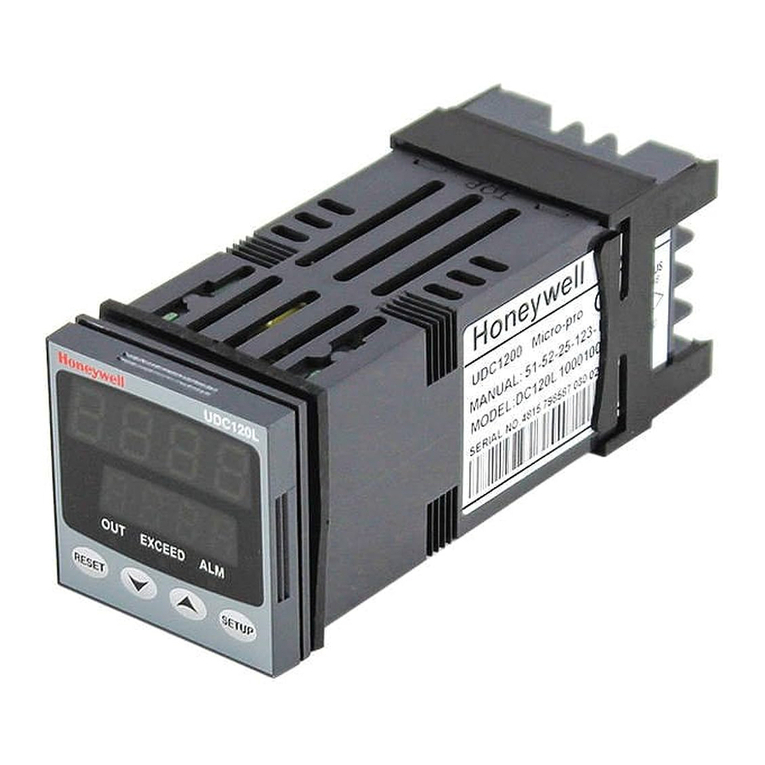
Honeywell
Honeywell UDC120L user manual
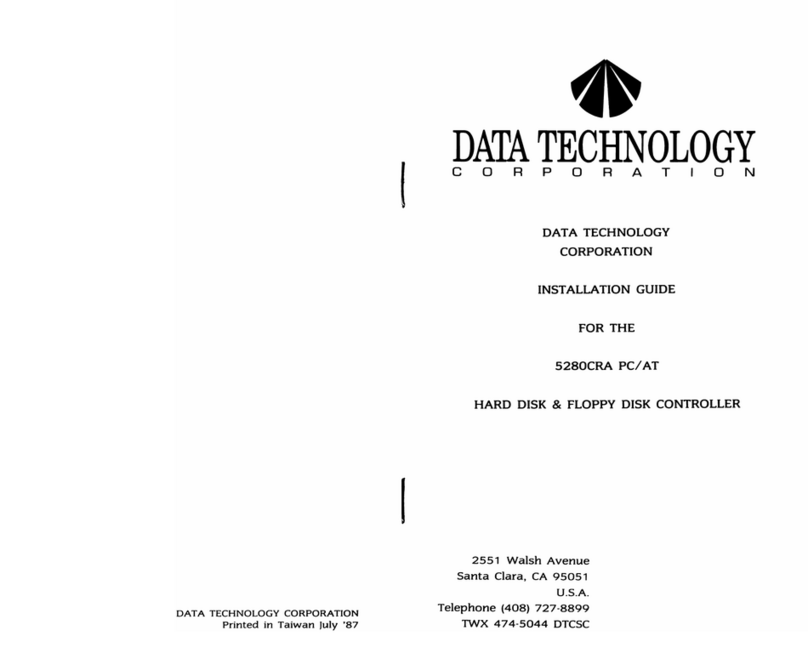
Data Technology
Data Technology 5280CRA installation guide