Alke Global-5 Series Manual

Version: September 2017 1 manual number: 0009 0440EN
User, Service and Installation Manual
Global-5, Global-10
Series
Atmospheric stainless-steel gas infrared heaters for use in well ventilated areas
Country of destination:
GB, IE, MT
General international manual
Global-5 Global-10
Global-5-(T)(2F)(2FT)(S)(2FS)
Global-10-(T)(2F)(2FT)(S)(2FS)
Global-5-(Ei)(2FEi)(SEi)(2FSEi)
Global-10-(Ei)(2FEi)(SEi)(2FSEi)
Alke BV
Industrielaan 11a
3925 BD Scherpenzeel
The Netherlands
Tel: +31 33-277 3824
Fax: +31 33-277 3080
www.alke.nl

Version: Sept 2017 2 manual number: 0009 0440EN
Warnings
Do:
•Read this manual carefully before installation and use and keep it for future reference. Make sure
that all daily users know the content of this manual.
•Install these heaters only in according with all applicable local and/or national regulations for
installation and ventilation of gas heaters.
•Improper installation, adjustment, alteration, service or maintenance can cause injury, damage or
death. For assistance or additional information consult your dealer, gas supplier or installer.
•Use these heaters only in well ventilated environment.
•Before installation and use make sure that the required type of electricity, gas and gas pressure, as
mentioned on the data plate, is in accordance with the local situation.
•Store gas cylinders always in accordance with national and local regulations.
•Use only gas cylinders with a gas isolation valve or gas lines with a main gas valve at the beginning.
In case more than one heater is connected to a gas system, place also a gas tap directly before the
heaters. Close these taps when the heaters are not in use.
•Installation, maintenance and conversion to other gases shall only be done by competent, qualified
and experienced installers.
•Make sure that during service, maintenance, cleaning and other work on the heaters, gas lines and
electricity are closed and the heaters are cooled down
•These heaters are intended for heating of animals, poultry, barns, workshops, local outside heating
projects and other similar heating purposes in agricultural environment.
•When gas is smelled or a leak is detected, directly close the gas supply and immediately take care
for good ventilation. Do not touch any electrical switch or do not create sparks in another way. Do
not use the system before the leaks are solved and the system is safe again. Consult an installer.
•If a heater is not safe to use anymore, remove it so that nobody accidentally operates the heater.
Store the heater in a safe place, mark that it cannot be used, and contact a service agent or gas
installer to solve the problem.
•This heater has an open flame. Make sure and take action that small children, mentally disabled
persons or elderly people never can touch the appliance or are in the vicinity without supervision.
Do not:
•These heaters are not intended for domestic use or for use in habitable parts of buildings and
houses.
•Never use LPG heaters below ground level or in cellars or basements.
•Never use these heaters in small rooms or insufficient ventilated areas. This can be dangerous and
is forbidden.
•Do not use these heaters for other purposes than room heating. Other use is not foreseen or
evaluated and maybe will be dangerous.
•Do not use another electricity voltage or type, gas or gas pressure than what is written on the data
plate.
•Never use these heaters in rooms or areas where combustible liquids or vapours are used or stored
or where there is a danger for dust explosions. These heaters are not ATEX approved.
•Never cover these heaters with cloths or other materials for drying purposes.
•Make sure that never gas lines, gas hoses, electric lines, etc. are mounted directly above the heaters
or are heated by these.
•Take care that gas hoses are not heated above 40 degrees Celsius.
•Never modify heaters. The manufacturer does not take any responsibility for modified heaters.
•Bad installation, wrong adjustment or incorrect maintenance can cause damage, accidents or even
personal injury or death.
•Do not touch, move, handle or service the heater when it is burning or in operation.
NOTE: Sometimes in the text numbers between brackets are used. These numbers correspond with the
numbers of the exploded view and parts list in the back of the manual.
General information
Model identification
The main identification of the different models is Global-5 and Global-10. These are independent
atmospheric stainless-steel infrared heaters. Suffixes are used behind these model names to add
additional type information about the models (e.g. Global-5-2FT).
2F: equipped with a dual dust filter
Di: equipped with a dual injection system

Version: Sept 2017 3 manual number: 0009 0440EN
T: equipped with an independent manual thermostat with remote sensor (Ti = integrated sensor)
S: equipped with an individual solenoid valve
Ei: equipped with an electronic ignition device (EID2G)
Ha: adjusted for high altitude installation (>1400 meter)
Packaging
Normally (depending model and order quantity) the heaters are packed per 1, 2 or 4 in a box. Always
check the heaters for transport damage directly after receiving them. Note that the heaters will be a bit
discoloured by temperature due to a 5 minutes quality check after manufacturing.
The heaters are pre-assembled. In some cases, if there is a risk for damaging during transport, the
thermocouple sensor is separated from the gas safety device. Re-assembly can be simply done by
screwing the M8 nut of the thermocouple sensor (64-68) back on the safety device nut (55) or on EID2G
(59) for the Ei models. Do not tighten too strong.
In most cases the reflector is delivered separately from the burner part to save on transport costs.
Reassembly is easy: move the burner tube through the hole in the reflector. Slide the reflector over the
tube till it rests on the upper plate of the burner. Secure the reflector with 4 nuts M4 (17) and washers
(16).
The thermostat knob is always delivered separated from the thermostat valve.
1) Remove the plastic protection cover from the thermostat valve (sometimes already removed before).
2) Turn the knob on maximum temperature and push the knob on the valve.
3) Fix the knob by turning the large metal screw ring till it stops (at least 2 turns, hand tight).
For thermostats with a remote sensor only: bend the sensor line carefully (no sharp bends) to the
thermostat valve and secure the sensor line with a ty-rap around the red protection lining and the
thermocouple safety device (see picture). Note that the tubing is hollow, a sharp bend will close the
tubing and makes the sensor worthless. The chance of breaking the line at the entrance of the
thermostat knob is largely limited now.
Installation
Before installation, check that the local distribution conditions, nature of gas and pressure, and
adjustment of the appliance are compatible. Make sure that the gas is clean. Install a gas filter and
condensate trap before the heaters in case the gas is dirty or wet/oily. No guarantee can be given on
heaters operating on gas that is not clean.
Dimensions
Physical dimensions of the appliances (rounded values)
Model
Length (cm)
Width (cm)
Height (cm)
Weight (kg)
Global-5 / Global-10
59 / 69
42 / 61
25 / 25
2,0 / 3,3
Global-5-T / Global-10-T
64 / 74
42 / 61
31 / 31
2,4 / 3,7
Global-5-2F / Global-10-2F
59 / 69
42 / 61
25 / 25
2,2 / 3,5
Global-5-2FT / Global-10-2FT
64 / 74
42 / 61
31 / 31
2,5 / 3,8
Global-5-S / Global-10-S
67 / 77
42 / 61
26 / 26
2,4 / 3,7
Global-5-2FS / Global-10-2FS
67 / 77
42 / 61
26 / 26
2,5 / 3,8
Global-5-Ei / Global-10-Ei
60 / 70
42 / 61
31 / 31
2,7 / 4,0
Global-5-2FEi / Global-10-2FEi
60 / 70
42 / 61
31 / 31
2,8 / 4,1
Global-5-SEi / Global-10-SEi
65 / 75
42 / 61
31 / 31
2,9 / 4,2
Global-5-2FSEi / Global-10-2FSEi
65 / 75
42 / 61
31 / 31
3,1 / 4,4
Global-5-2FDi
57
42
25
2,3

Version: Sept 2017 4 manual number: 0009 0440EN
Place of installation
The heaters are intended for use in well ventilated areas only. Do not install the heaters in situations
that are not well ventilated. See also below for more ventilation information. Check also your local
regulations for the ventilation and room size requirements. The number of heaters per building is
depending the type of building, the animals, the insulation, the climate and local wind conditions. Check
with your installer or distributor for a heat transmission calculation to determine the number of heaters
needed.
Make sure that the place of installation is free of draft (less than 1 m/s). Too much draft will make the
flames unstable and will result in a lower infrared heat efficiency. It is advisable to install an alarm system
that reacts on temperature in case a temperature drop will cause damage. Find in the table below a
rough guideline for the installation height to start with. Adjust afterwards on to the height based on your
personal preference and experience.
Operational Distances
Global-5
Global-10
To the ground
1,4 –1,7 m
1,6 –2,0 m
Safety distance to combustible materials
The heaters produce heat by radiation and by combustion gases. It is important to take the following
distances in account from the heaters to combustible materials. This is to avoid fire or overheating. Do
not use the heaters in situations where the distances to combustibles are smaller. Never store gases or
inflammable liquids or easy combustible materials in close vicinity of the heaters.
Safety Distances
Global-5
Global-10
to the ceiling (A)
>65 cm
>70 cm
to the ground. (B)
>135 cm
>130 cm
in front of heater (C)
>50 cm
>60 cm
to the back (D)
>50 cm
>60 cm
to side walls (E)
>50 cm
>60 cm
The minimum distance to non-combustible materials depends on the specific local situation. Keep in
mind that there must be sufficient free space left to vent the combustion gases away. Otherwise, they
will influence the combustion and proper function of the heater. On locations where the combustion
gases can vent away easily, a minimum of 25 cm to the ceiling is advisable. Note: Be aware that some
non-combustible materials can be subject to discolouring when they become too hot.
Warning: be careful with the use of heaters in places with storage of manure. Manure can contain large
amounts of methane and other inflammable gases.
Ventilation
These models of appliances are of the so-called type A1. That means that there is no independent air
supply connection and no flue connection. The flue gasses are vented away by the ventilation of the
space.
A proper ventilation is extreme important for safe and convenient operation. Lack of ventilation can cause
production of carbon monoxide (very poisonous). Sufficient ventilation shall be guaranteed by a
monitored fan or by permanent, non-adjustable, ventilation openings. Consult EN13410:2001 for more
details.
Beside other important requirements this standard states in short that a 1,5 times room air replacement
per hour is sufficient in most situations. Also, a maximum of 5W heat input per m3 room content is
considered to be safe. If this is not the case make sure that a minimum of 10m3/h air replacement per
1 kW heat input is guaranteed by means of fans or ventilation openings.
In case local requirements ask for more stringent ventilation, or when animals ask for more ventilation,
always follow the most stringent requirements. In case there are no requirements or standards for

Version: Sept 2017 5 manual number: 0009 0440EN
ventilation in the country of installation, we advise to keep a minimum ventilation of 20m3/h per kW heat
input. Check regularly if fans are working properly and ventilation openings are not closed.
Installation
The heaters are intended for suspension only. Use only a chain and S-hooks that are galvanised or
made of stainless steel. Do not use the gas line, gas hose or electric lines for suspension purposes.
Never use rope or plastic mounting materials. Close all S-hooks after the heater is in correct position.
•Mount a screw eye or screw hook at a rigid part of the ceiling construction at the proper location of
the building.
•Attach a chain of sufficient length with an S-hook to the screw eye or screw hook.
•Attach the suspension clamp of the heater with an S-hook or carabiner hook at the other end of the
chain at the proper height.
•Move the suspension clamp in such a position on the tube of the heater that the heater (including the
gas hose and electric lines) has an angle of 15 degrees with the horizontal level and with the gas
safety device at the lower end.
•Secure the suspension clamp in the proper location by the eyebolt and close the S-hooks.
•Never hang the heater horizontally while in that case the flue gases will influence a proper
combustion.
The gas safety device and electric components can handle a maximum temperature of 60 degrees
Celsius. Be sure that the heater is not mounted in such a way that this temperature will be reached (e.g.
by other heaters in close vicinity). Take into account the safety distances mentioned on page 4. After
installation always check if the gas type and gas pressure complies with the technical table and data
plate information. Remove the black end cap from the safety device (hose pillar and 1/8” thread version
only).
The gas hose shall be hanging free and have a minimal distance of 1,3 meters from the ground. This to
make sure animals will not damage the hose. Connect the hose via an individual gas tap to the central
gas supply.
A guideline for placement of the sensor of the temperature regulation is 60 cm above the ground and
minimal 40 cm away from a heater. Use sensors with a black surface in case the regulation is based on
measuring the infrared temperature.
Electric connection
All electrical connections/installations shall be made in accordance with the national and/or local
regulations that are in force in the country of destination where the heater will be installed. Before doing
maintenance or installation work always disconnect the electricity to all the lines by removing or
disconnecting the fuses from the electrical system to the heaters.
A proper earth connection MUST be made to the heaters with an electronic ignition device and/or with
a solenoid valve. First for safety reasons and secondly also while the electric ignition device (EID2G)
will not operate correctly and will give failures or will shut down. The EID2G device is not phase sensitive.
In case of an electrical fault directly after installation concentrate first on earth continuity and resistance
to earth. These are the main reasons for failures while all heaters are operated before leaving the factory.
Thermostats, fuses and switches are not supplied with the heater. The electric installation shall have a
separate fuse for the protection of the heaters only. The operation switches in front of the heaters shall
be preferably of a double pole type with minimum contact separation of 3 mm. Make sure that always
the live wire (or hot wire) of the electric supply is used to switch the heaters on and off.

Version: Sept 2017 6 manual number: 0009 0440EN
Ei
S (Ceme)
S (Asco)
Electrical supply:
230VAC
50/60Hz, IP65
230VAC 50/60Hz, IP65
24 VAC 50/60Hz, IP65
230VAC 50Hz, IP65
24VAC 50Hz, IP65
Power:
Max 30VA
17VA
6,3W
Current rating:
Max 0,2A
0,1A/0,9A
0,05A/0,3A
Waiting time T(w)
7 seconds
X
X
Safety time T(s)
30 seconds
X
X
Schematic diagram electronic ignition device
Timing diagram electronic ignition device
The operating or control box, which is not delivered by the manufacturer but by the installer, can be installed
on any desired place and height, provided this is within reach of the user. The temperature sensor shall have
a free view to a heater and placed on a position representative for the average temperature needed in the
whole space. Protect the sensor for draught, direct sunlight or cold walls. Avoid ramping up of the thermostat
by adding a too small temperature differential. It is far more efficient and comfortable not to ignite the
appliance more than 3 times per hour. Try to modulate as much as possible between high and low. To avoid
locking-out, the EID2G control needs to operate at least 3 minutes after each ignition. The drawings below
give a typical lay-out for the position of a switch box or thermostat in the electric lines. The drawing is
applicable for the S, 2FS, Ei, 2FEi, SEi and 2FSEi models
1
To control box
2
To additional zones
TH1
Thermostat on/off
TH2
Thermostat high/low
BR
Brown
BL
Blue
YE
Yellow/Green = Earth
Ei
Electronic Ignition
Device
S
Solenoid for high/low
NB: dotted line is optional on
the Ei model (as SEi model)
or only applicable for the S
model (as S or 2FS)
Gas line supply
In case a main gas line supplies the gas to the heaters, make sure that an authorised company in your
country, in accordance with the local rules and requirements, install the system. To avoid problems, use
galvanised or copper tubing for the gas line. First make a calculation to determine the capacity of the
whole system and the diameters of the piping in each section. Use the common available calculation
methods as written in most gas installation standards. Contact an installer or the distributor in case this
calculation method is not available in your area. For data needed to calculate the dimensions of the gas
line, see the technical table on the last page.
The most common way to install a gas line is in the centre of the barn (at least 2-meter-high) with every
3 to 5 meter a “T” or “cross” connection for gas supply to the heaters. Always mount a (easy reachable)
gas tap at the beginning of the gas hose to the heaters. This gas tap is needed to close the gas supply
to the burners to extinguish the flames. In addition, it makes it possible to remove the heaters after use
or to service the heaters safely. The gas inlet at the heater side is standard an 8-mm hose nipple
(optional a smooth hose nipple or a G1/8” right handed thread. Other connections are possible after
consultation). Always use approved gas sealant to close the gas connections.

Version: Sept 2017 7 manual number: 0009 0440EN
Gas cylinder supply
The gas can also be supplied from LPG gas cylinders. The minimum size is a 11-kg cylinder or larger.
Before buying a cylinder make sure that the connections of the gas regulator and the gas valve of the
cylinder are of the same type. Check with your gas supplier for the correct size of gas regulator. Check
the technical table for the maximum gas consumption and gas pressure.
Store the gas cylinders always on ground level in a well-ventilated place, preferably outside the room
where the heater is. In case the gas cylinder is placed in a cylinder housing, or cover, make sure that
there is enough ventilation as requested by the applicable regulations or standards. Never obstruct these
ventilation holes. Make sure that the gas cylinders are used in upright position only and are secured
again tipping over during use. Gas cylinders laying on their side will give liquid gas. This is very
dangerous and will give a fire ball when it reaches the heaters.
In case the gas cylinder is placed in the same room as the heater is, keep it at a safe distance from the
heater so it will not be over heated. Advisable is at least 2 meters. Make sure that the gas cylinder valve
can easily be reached to close the gas supply in an emergency. Pay special attention how to change
the gas cylinders in a safe way.
For the Global-5 a minimum of 1,5 gas cylinder (11 kg or larger) per heater is needed. For the Global-
10 a minimum of 2 gas cylinders (11 kg or larger) per heater are needed for a guaranteed gas supply.
For a 45-kg gas cylinder a maximum of two Global-5 heaters is recommended. Having more heaters on
the gas cylinders as recommended above will give gas capacity problems, especially when it becomes
colder, due to limited vaporisation of the gas.
Biogas
While biogas can be corrosive under certain conditions it is important that the biogas is clean before
entrance to the appliances. The gas shall be dry and free from dust, oily and greasy particles to avoid
internal blockage of the appliances. Also, halogens, chlorides, H2S and NH3 shall be removed to avoid
corrosion. The tolerance on biogas composition with CH4=60% is +/- 4% CH4.
Gas hose
In most installations, the heaters are not connected directly to the gas system but a gas hose is used.
Keep the hoses always as short as possible, especially for natural gas and low-pressure LPG. For high-
pressure LPG, the maximum length (concerning capacity issues) is 5 meters.
The gas hoses must be inspected frequently and must be changed within the prescribed intervals. Check
the hose at least every 6 weeks. Avoid twisting or stress of the gas hose. Twisting or stress will shorten
the live time of the gas hose. During inspection, check the hose for damage, splitting, ageing and
cracking. Pay special attention to the connections. If a defect is seen directly change the gas hose by a
new one of the same type. Keep the hoses clean from dirt, moisture and dust.
Some countries have regulations that gas hoses must be replaced every 2 or 3 years. Please check with
your gas supplier. Always use official approved gas hoses, suitable for the pressure concerning. Replace
a gas hose always by a type of the same length, internal diameter and equivalent quality. For safety
reasons: never use air hoses or water hoses, these are very dangerous for gas transportation and
will leak soon!

Version: Sept 2017 8 manual number: 0009 0440EN
The gas hose shall always be connected to the heater with the help of hose clips. Not using hose clips
at both ends of the gas hose is very dangerous. Make sure that the gas hose never is heated above 40
degrees Celsius.
Changing gas cylinders
In case gas cylinders are used, changing or connecting gas cylinders must be done preferably outside,
or in a well-ventilated area, in a flame-free environment and away from other people.
- Check if there are no other operating heaters, other gas heaters, burning candles or people smoking
cigarettes in the area.
- Be sure that the valve on the gas cylinder is closed, electricity to the heaters is disconnected and
the burner of the heater is extinguished.
- Unscrew the nut by which the gas regulator is connected to the gas cylinder valve. (Note that most
connections are with left-handed threads. They open in clockwise direction).
- Before connecting the (new) gas cylinder, first check if the rubber seals on the cylinder valve or on
the regulator connecting nut are fitted properly and able to fulfil its function and are not damaged or
worn. If the last case is true, do not use it and replace the seals first.
- After connecting the regulator firmly, open the cylinder valve and check with soapy water if the
connection is leak tight. If bubbles appear, the connection leaks. Do not use the heater unless the
system is sound.
Soundness check
Before using a new built gas system, first make sure that the installer made a careful and extensive
check for gas leakage. After executing a pressure drop test to determine that there are not large leaks,
check every connection with soapy water or gas detection liquid with all gas valves open and with
maximum gas pressure. Pay special attention to the hose connections. Maintain maximum air ventilation
during the test. Repeat this check at least every year. This soundness check shall be done by a
competent installer only.
Gas leakage
When a gas leak is detected, immediately close the gas
supply and disconnect electricity. Keep flames away.
Do not use the heater anymore. Contact an authorised
gas technician, gas installer or gas service agent to
determine if the gas leakage can be repaired. Never try
to do gas repairs by yourself. Do not use the heater
anymore until the problem is solved.
Operation
New heaters
New heaters need a cleaning period before they are ready for operation. Turn the ventilation to maximum
position or place the heaters outside in the open air. Fire the heaters for at least two hours on full capacity
to burn-off oily and greasy remnants of the production. Make sure that after two hours all smoke and
smell is disappeared. The smoke and smell can be unhealthy, so keep animals and human beings away
till the heaters and the environment air is clean.
Ignition of the heater
Warning: after a manual operated heater is extinguished (intentionally or unintentionally) wait always for
3 minutes before (re)ignition. This is a worldwide safety rule and intended to ventilate unburned gases
away and to leave enough time for the thermocouple device to close.
Ignition shall always be done in high fire. So, the gas pressure shall be adjusted at maximum pressure,
solenoid valves shall be in open position, thermostats shall be on maximum setting. In case the heaters
are operated by a barn computer, this computer shall be programmed in such a way that during ignition
the heaters are operated for at least 30 seconds in high fire.

Version: Sept 2017 9 manual number: 0009 0440EN
Manual operated heaters
Global-(5, 10), -T, -2F, -2FT, -S, -2FS and -2FDi versions:
1) Open all gas taps and turn the thermostat (T) or gas pressure
regulator on maximum pressure, open the solenoid valve (S)
by electricity.
2) Keep a flame of a BBQ lighter (or long match) in the ignition
hole of the burner globe.
3) Press the knob of the gas safety device and wait for 10-25
seconds after ignition before releasing the knob.
4) The burner will stay on now.
5) Repeat al steps again in case the burner directly extinguishes.
Electric operated heaters
Global-(5, 10)-Ei, -2FEi, -SEi and -2FSEi versions:
1) Open all gas taps, be assured that the burner gas pressure does not exceed the maximum pressure
indicated on the data plate during ignition.
2) Set the thermostat to call for heat after adjustment of the gas pressure regulator to maximum pressure
and opening of the solenoid valve (S) by electricity.
3) After a safety time of 7 seconds the ignitor sparks for 30 seconds and ignites the heater.
4) After 30 seconds, the thermocouple safety device will take over the safety function and supervises
the flame.
5) When ignition is completed the gas pressure can be adjusted to the desired pressure (see also the
dataplate).
6) If ignition fails, turn the thermostat (or power) to off for 1 second to reset the system.
7) After ending the ignition time the burner will stay on as long as there is 230V supply on the electric
ignition device (Ei).
Note: A proper electric earth connection is needed for a reliable ignition. Poor earthing will give nuisance
lockouts.
Note: If 10 ignition attempts are made in sequence within a short interval (<120 seconds per ignition
attempt) the EID2G will fall into a safety lockout and needs a reset (cool down period) for 20 minutes.
During the reset, leave the power on to feed the internal reset timer.
Heat regulation of the heater
Global-(5, 10), -2F, -2FDi, -Ei, -2FEi versions:
The heat input of this heater can only be changed by adjusting the pressure of the gas supply. Check
the gas supply pressure information on the data plate of the heater for the minimum and maximum
values. If only one pressure is mentioned on the data plate, adjustment is not possible and only
continuous operation or on-off operation is allowed.
Global-(5, 10)-S, -2FS, -SEi, -2FSEi versions:
Make sure that the gas supply pressure remains constant at the value indicated on the data plate. Adjust
the heat input between high and low by opening or closing the solenoid valve (S).
Global-(5, 10)-T, -2FT versions:
Make sure that the gas supply pressure remains constant at the value
indicated on the data plate. Adjust the heat input by setting the
thermostat knob at the desired value. Note that the temperature on the
ground will be several degrees higher than at the sensor. So, use the
setting on the thermostat knob as a rough guideline and always check
the real temperature on the ground.
Extinguishing the heater
Global-(5, 10), -T, -2F, 2FT, -S, -2FS, -2FDi versions:
Close the gas tap or the central gas supply. The burner will extinguish now. The thermocouple safety
valve will close after 60 seconds.
Global-(5, 10)-Ei, -2FEi, -SEi, -2FSEi versions:
Switch-off the electric power supply to the electronic ignition device. This will close immediately the gas
supply by the gas safety device
Approx. Temperature (T)
Δ = 15 °C
* = 20 °C
1 = 22 °C
2 = 28 °C
3 = 33 °C
4 = 36 °C
5 = 38 °C

Version: Sept 2017 10 manual number: 0009 0440EN
Visual examination of the flame
Check after every ignition (and also during regular barn inspection) if a heater still burns correctly. The
flame shall remain always inside the outer burner globe. The burner globe shall be equal red/orange in
high firing position and having a blue flame. Some types will have in high fire position a dark ring on the
globe. This will not give a problem and is created by cooling air around the flame. A little bit yellow tipping
or yellow glow in low fire is allowed.
A burner does not operate well in case there is a (green)-blue cloud inside the reflector and/or (green)
blue flame tongues are coming out the exhaust holes in the reflector. Soot deposit on the reflector and
yellow flames are also a sign of bad functioning and are not allowed. Cleaning will solve these problems
in most cases. When gas is used with a lot of butane instead of propane the centre of the outer globe
will become overheated. The centre will be white-yellow hot coloured; small flames of a few mm will
come through the perforation of the globe. The globe will burn through after some time. Take action
when this is noted.
In high fire operation, the flame makes a soft roaring noise. In case the burner makes a loud roaring
noise and the burner globe does not become equal red/orange, the inner burner globe is damaged and
the flame is burning inside the venturi tube (back firing). The venturi tube becomes very hot now behind
the venturi. Directly extinguish the heater and replace the damaged unit by a new one.
Emergency operation (Only models: Ei, 2FEi)
The Global heater has the option to be converted to
full manual operation without the need of electricity
anymore. This can be an emergency solution in case
a long-term power breakage occurs in the barn or the
electronic sparking unit breaks without having a spare
one on stock. The conversion to manual operation
takes 2 minutes per brooder. See figure at the right
side (situation shown after conversion). The numbers
between brackets refer to this drawing.
[1] Unscrew the thermocouple nut (1) from the black
electronic ignition device.
[2] Unscrew the nut of the extension wire (3) from the
gas safety valve, leaving this one unconnected.
[3] Screw the thermocouple nut (1) on the gas safety valve. (replacing the nut of the extension wire).
Now the EID2G is completely overruled, electric power is not needed anymore.
[4] Push the knob (2) of the gas safety valve and light the burner with a hand ignitor (long tip BBQ lighter)
at the location of the 8-mm hole in the burner globe.
[5] After ignition of the burner keep the knob (2) pushed for 20 seconds. The thermocouple of the gas
safety valve will take over the operation and the burner will stay alight.
[6] To extinguish the burner, close the manual valve in the gas supply line before the brooder. After 60
seconds cooling down the safety valve will close also.
Game rearing
Global heaters are used a lot for game rearing. Especially for game rearing, due to the small cages and
active birds, pay a lot of attention to cleaning and ventilation. While the cages are small, the effect of
lack of ventilation and not cleaning will be directly causing the death of birds in a short time. While
normally one heater is used for one cage, we advise to add an independent temperature alarm system
for those situations where a temperature drop due to a (gas supply) failure will result in bird loss.
Service and maintenance
General
The frequency of maintenance is strongly depending on the quality of the combustion air and the
intensity of use. When used in poultry houses, maintenance is advised every 6 weeks or by changing
the animals. By use in clean environment conditions, the maintenance period can be extended but not
longer than 6 months. In case heaters are not used for a long period, always do maintenance first before
using them again. Wear safety goggles during cleaning with compressed air.
Parts that are broken, or are not functioning well, must be replaced directly by identical ones of same
brand and type. Consult the dealer or manufacturer in case of doubt.

Version: Sept 2017 11 manual number: 0009 0440EN
WARNING: always switch off the heater and isolate the gas and electricity before carrying out any
service or maintenance operation.
Order of maintenance
•First clean the heater and filters as described below by daily maintenance. Take the venturi (22) out
during cleaning to remove dust directly behind it.
•Clean the reflector and other parts with water and mild detergent and a cloth or soft brush.
•Carefully inspect the outer and inner burner globes on damage, cracks and holes. Replace when
needed.
•Check the gas injector for obstructions. Remove obstructions by brushing them away and by using
a pin or drill to clean the injector hole. Make sure that the injector hole does not become wider by
using a pin or drill that is larger than the size stamped on the side of the injector.
•Pay special attention to the dual injection model Di. (See parts list for numbers). Clean the holes in
injector (32) very carefully. Gas soundness is achieved by a metal to metal connection with part (34).
So, keep clean and inspect for damage and avoid making scratches on the contact surfaces of both
parts. Make sure that the small o-ring (33) (4 mm) is still in place in the seat behind the injector and
does not get lost during cleaning.
•Clean the inside of the gas safety device and injector with compressed air. Make sure that the
pressure of the compressed air is not larger than the 1,5x the pressure mentioned on the data plate
(300 till 1400 mbar). Otherwise the rubber seals inside the safety device will become damaged.
•Check the condition of the thermocouple sensor. Replace in case the tip is burnt-in already to avoid
unnecessary shut down later on. The end of the thermocouple shall be 25 or 22 mm above the upper
plate of the burner (see picture next page).
•Check the condition of the spark plug; no cracks of the ceramic and a spark gap of 3-4 mm. Check
if the metal spark wire and earthing wire still makes a 90 degrees angle directly above the ceramics
and are not bending away to larger angles.
•Clean the EID2G and check the connection of the ignition wire for proper contact and watertightness.
Check if the ignition wire is not damaged and has no cracks.
•Check all gas carrying parts and connections for gas tightness with leak detection liquid or soapy
water according the procedure in the standards applicable at the local installation situation. Never
use a flame for soundness checks!
•In case a gas hose is used, check this carefully for cracks, wear and other signs of damage or
alteration. Replace it also when the maximum lifetime printed on the hose, or the maximum allowed
by local requirements, has been passed.
•Commission the heater after maintenance and check it carefully during first ignition, firing and
extinguishing.
In case the heaters need to be stored for a long time, make sure that no dust, spiders, etc. can enter the
heater. Use the carton packaging box to store the heater, or a plastic bag if the box is not available
anymore, and close this carefully.
Daily maintenance
In dusty or dirty environments check and clean a heater every day. In case a heater is not cleaned
internally the heat efficiency will drop and the lifetime of the inner and outer burner globe will become
shorter or they will be destroyed. Also, there is a possibility that carbon monoxide (poisonous) will be
produced and soot deposit will occur. It is very important to keep the heater internally and externally free
of dust. Inspect and clean also every day the combustion air openings into the building and the proper
functioning of exhaust fans.
Dust filter 2F (if applicable)
Dust filters must be check
every day and cleaned in case
needed. Remove a filter before
cleaning. Dry dust can be
removed by tapping the filter
softly against a solid surface
like the sole of a shoe. The
dust will fall off easy now. In
case the filter is still not clean, brush the surface gently with a brush or clean it with compressed air from
inside to the outside. In case the dust is greasy, clean the filter in warm water with a bit detergent. Make
sure that filters are dry before placing them back. Even with the use of a filter still check the heater
regularly inside while very fine dust still will pass the filter and pollute the heater internally.

Version: Sept 2017 12 manual number: 0009 0440EN
Advice: Lots of farmers use a second set of dust filters. They replace the dusty ones directly with the
clean ones and clean the filters outside the barn to avoid unneeded disturbance of the animals.
Internal cleaning
The internal part of a heater can be cleaned with compressed air and with a tube brush. If needed do
this every day. First clean the outside of the burner globe. Then the inside of the venturi and burner
tube via the dust filter connection. Repeat this 3 times to be sure that all the dust is removed.
Water
Never wash the heater with water when it is
operating or still hot. Do not clean the heater
with steam or chemicals or high-pressure jets.
The lifetime of the burner globes will go down
in those cases. It is allowed to wash the inside
of the venturi and burner globes with low
pressure (warm)water from a normal hose (so
not pressurized) to remove greasy dust. Be
sure that the burner is completely dry before
using it again. Also make sure that the gas
safety device and injector remains dry all the
time.
High fire
The lifetime of infrared heaters in a dusty environment will be extended in case these heaters are
operated on high fire every 12 to 24 hours for minimal 15 minutes. This burns off dust in the burner that
accumulates during low-fire operation. This is only needed in case heaters operate on lower setting for
a longer period. When a barn computer is used for heating and ventilation, it will be easy to modify the
program to add a 15 minutes high fire operation every day. In case a mechanical thermostat (T) is used
a solution can be to put the sensor for 15 minutes in a bucket with cold water during daily inspection of
the barn.
Consumable parts
Thermocouples (64-68) and the magnet unit (56) inside the gas safety device are the most important
parts that maybe requires replacement during normal operational life. See the Parts List for more
information.
Replacement thermocouple and magnet unit
- Remove the thermocouple (64-68) by unscrewing the nut M8 at
the gas safety device.
- Unscrew the nut (55) at the gas safety device (51-54).
- Remove the broken magnet unit (56) and replace by a new one.
- Replace the nut (55) and close carefully (firmly but not excessive)
to avoid gas leakage.
- Loosen nut M8x1 (70) one turn, bend the thermocouple straight
again and turn it out of the top plate (8, 9)
- Screw nut M8x1 (70) on the new thermocouple and turn
thermocouple (still straight) in the top plate (8, 9) until the depth as indicated in the drawing (Global
5 = 25 mm, Global 10 = 22 mm). Tighten nut M8x1 (70) to secure the thermocouple in place.
- Bend the new thermocouple in the identical shape as the old one the and screw the thermocouple
nut M8 in nut (55) of the gas safety device (51-54). Hand-tight first and then an additional 1/6 turn.
- Carefully check the gas safety device for gas leakage before taking back into operation.
Conversion instructions
Conversion shall be done by a qualified installer only. To convert a heater from one gas or gas pressure
to another gas or gas pressure, take the following actions.
- Consult the technical table on the last page and contact the manufacturer or dealer for the parts
needed. (new injector (31, 32) new venturi (22), new thermostat body (46) or solenoid body (41, 42)
and a new dataplate).
- Replace the parts by new ones. Use a proper gas sealant to avoid gas leakage and seal the new
parts.

Version: Sept 2017 13 manual number: 0009 0440EN
- Consult the technical table for the proper ring (38) distance. (Rings are counted from the gas safety
device).
- Check the gas supply for the proper gas pressure and gas type and do a leakage test first.
- Take the heater into operation and do a visual examination of the flame as explained above.
End-of life disposal
The infrared heaters are made up of valuable recyclable materials. Therefore, deliver your heater at the
end of its life in a recycling company.
Fault finding table
Trouble
Action
Burner does not light.
•Check if gas valve of the gas cylinder or gas line is open
•Check if gas cylinder is empty
•Purge air out of the new gas lines
•First ignition will take up to 60 or more seconds before gas is available
•Check if the injector is blocked
•Check if the gas pressure/gas quality is identical to the pressure
indicated on the data plate
•Check if the burner is on high fire setting
Burner does not light.
Spark is available
•Check if during sparking ignition is possible manually with a BBQ
lighter
•Location of the ignitor tip to the inner burner is incorrect.
•Check if the gas safety device opens. Click can be heard when
opening. If not, coil EID2G is broken
Burner does not light.
No spark available
•Check if there is 230 Volt available at the EID2G
•Spark electrode not connected to the EID2G
•Spark electrode gap incorrect. Shall be between 3-4 mm
•Spark jumps off to other metal parts before the spark electrode. Check
wire, connectors and ignitor ceramics. Check if parts are dry
•Ignition loop is not complete. Check the ignition and earthing wire
•Ignitor EID2G is broken. Replace
•EID2G in recovery phase. Leave the EID2G connected to 230V for 20
minutes to reset and try again
Burner extinguishes after
lighting
•Keep button safety device pressed for a longer period (up till 25
seconds)
•Check the position of the thermocouple (see above)
•Check if the thermocouple nut is connected properly to the gas safety
device and to the EID2G unit and that the nuts are not loose
•Check if the thermocouple has the proper depth in the burner,
measured on the top plate (Global 5 = 25mm, Global 10 = 22 mm)
•Thermocouple switch in EID2G is broken. Check (after switching 230V
to the EID2G) by multimeter if resistance of the internal switch is <25
mΩ
•Thermocouple or magnetic coil of the safety device is broken.
•Gas pressure lower than minimum requested
•Heater not suspended at 15 degrees angle
Flames leave the
- confines of the burner
- or are sooting
- or a blue cloud is under
the reflector
•Gas pressure is too high. Check the gas pressure with the data plate
•Check if the gas pressure regulator is broken.
•Wrong gas is used. Check data plate for the correct gas supply
•Venturi/air inlet is blocked/dirty
•Valve dual injection model (Di) is leaking
•Check the size of the venturi and injector with the table
•Not enough fresh air available due to mounting situation
•Air filter is dirty
•Heater not suspended at 15 degrees angle
•Small o-ring (33) (Di) is missing or leaking

Version: Sept 2017 14 manual number: 0009 0440EN
The burner is only partly
glowing
•Wrong gas or pressure is used. Check data plate with the gas supply
•Check if the injector or venturi are blocked or dirty
•Check the injector and venture size with the table
•Check if pipe sizes or gas hoses have sufficient capacity
•Check the setting of the thermostat
•Valve (35) dual injection model (Di) is blocked
The burner makes a lot
of noise after ignition or
after several minutes
•Wrong gas is used. Check data plate with the gas supply
•Check if the inner globe is broken or damaged so the flame burns
inside the venturi tube
•A zoom noise of the EID2G is created by magnetic fields and lasts only
30 seconds. Not harmful. Temperature dependent. Turn the EID2G in
another position
The burner do not work
at minimum position
•Gas pressure is not correct. Check the gas pressure with the data plate
•Wrong gas is used. Check data plate for the correct gas supply
•Check the size of the venturi and injector with the table
•Sensor or wire thermostat (T) is broken
•Thermostat (T) valve adjusting mechanism is blocked
•By-pass hole thermostat (T) or solenoid valve (S) is blocked
•Injector (partly) blocked
•Centre hole dual injector (Di) is blocked
•Check if the thermocouple has the proper depth in the burner,
measured on the top plate (Global 5 = 25mm, Global 10 = 22 mm)
Heater will not attain the
desired temperature
•There is insufficient heat in the building for heat loss (i.e., not enough
brooders).
•The thermostat (T) sensing bulb is incorrectly placed
•The thermostat (T) is out of calibration or broken
•The solenoid valve (S) is not functioning
•One of the two holes of the dual injector (Di) is blocked
•Injector partly blocked
Declaration of conformity
We, Alke B.V., located in Scherpenzeel, The Netherlands, hereby declare that the Global series, marked
on their dataplates with CE and with CE approval/production supervision by Kiwa (number 0063) are in
compliance with the following EU legislation:
- Directive on appliances burning gaseous fuels (GAD) 2009/142/EC (ex 90/396/EEC)
- Regulation on appliances burning gaseous fuels (GAR) 2016/426/EU
- Low Voltage Directive (LVD) 2014/35/EU (models with electric components)
- EMC Directive (EMC) 2014/30/EU (models with electric components)
Scherpenzeel, 01-09-2017
Adri van Alphen
President

Version: Sept 2017 15 manual number: 0009 0440EN
Parts list
The parts list below is a combination list of both Global 5 and 10 models. Most parts of both models are
identical. Parts that differ are specified with the Global model identification. Consult the data plate to
determine the model you have before using this list.
12005000
Burner replacement kit Global 5 (set of parts: 3, 5, 6, 7, 8, 10, 11, 12, 14, 15, 18)
12006000
Burner replacement kit Global 10 (set of parts: 4, 5, 6, 7, 9, 10, 11, 13, 14, 15, 18)

Version: Sept 2017 16 manual number: 0009 0440EN
Nr
Art / Drawing Nr
Description
Amount
t
1
02354000
Reflector Global 5
1
2
02355000
Reflector Global 10
1
3
02525000
Burner Globe Global 5
1
4
02527000
Burner Globe Global 10
1
5
07734000
Hexagonal bolt M5x30
6
6
02224000
Mounting Ring SS
1
7
02524000
Burner Globe Small
1
8
02222000
Bottom Plate Global 5
1
9
02225000
Bottom Plate Global 10
1
10
08892000
Distance tubes SS
6
11
07426010
Hexagonal nut M5
12
12
02223000
Top Plate Global 5
1
13
02226000
Top Plate Global 10
1
14
07065000
Rifbolt M4
4
15
07781000
Toothed lockwasher 5,3mm
6
16
07800000
Washer 4,3mm
4
17
07401000
Hexagonal nut M4
4
18
08896000
Venturi Tube
1
19
03879900
Tube Clamp 30mm
1
20
07850015
Eyebolt M6
1
21
99107020
Clamp 30 mm
2
22
01307999
Venturi Global 30x75
1
23
01811000
Connection piece 4x17mm
1
24
01813000
Connection piece Global 10
1
25
01803000
Double Filter Connection Piece
1
26
01812020
Connection piece GL5 Dual Injector
1
27
07086010
Wingbolt M5x15
1
28
07135005
Metal Screw M5x12
1 (3)
29
02530000
Dust Filter Universal
2
30
02533000
Dust Filter High Model
2
31
0115x000
Gas Injector M8x0,75 (top 0,5/1,0)
1
32
0128601x
Gas Injector 1/8G Dual Injector
1
33
81113017
O-ring 2,0x1,0mm
1
34
01812021
Insert Gl5 Dual Injector
1
35
01368010
Valve Assembly Dual Injector
1
36
81113013
O-ring 7,5x1,5mm
1
37
01301000
Gas Injector Holder M8x0,75
1
38
07001000
Circlip E Type 9mm
1
39
01405000
Reducing Bush 3/8Mx1/8F
1
40
01400000
Reducing Bush 1/4Mx1/8F
1
41
00611000
Solenoid valve 1/4Fx1/4F 230V 50/60Hz
1
42
00612000
Solenoid valve 1/4Fx1/4F 24V 50/60Hz
1
43
00698000
Coil 230V 50/60Hz
1
44
00698010
Coil 24V 50/60Hz
1
45
03028000
Electric connector
1
46
00925010
Thermostat valve 3/8F
1
47
00923070
Thermostat with internal sensor
1
48
00924130-V
Thermostat with sensor 1,25m
1
49
01429000
Reducing Nipple 3/8Mx1/8M
1
50
01421000
Reducing Nipple 1/4Mx1/8M
1
51
00106000
Gas safety Device 1/8Fx8mm hose pilar T10
1
52
00101010
Gas safety Device 1/8Fx1/8M T10
1
53
00110010
Gas safety Device 1/8Fx1/8M EID2G+PTP (300mbar) T10
1
54
00110011
Gas safety Device 1/8Fx1/8M EID2G+PTP (1400mbar) T10
1
55
00158000
Nut Gas Safety Device M8x1 T10
1
56
00161000
Magnet Unit #53 T10
1
57
01327000
Hose nipple 1/8Fx8mmM
1
58
01328000
Hose nipple 1/8Fx8mmM smooth
1
59
00185003
Electronic Ignition Device EID2G 230V-50/60Hz
1
60
03895000-V
Yoke EID2G
1
61
10053003
Nut M12x1
1
62
03025000
Electric connector
1
63
01360000
Reducing Nipple 1/8Mx1/8M
1
64
00202030
Thermocouple M8x1x560 Alu tip
1
65
00202015
Thermocouple M8x1x520 Alu tip
1
66
00204000
Thermocouple M8x1x600 Alu tip
1
67
00202000
Thermocouple M8x1x450 Alu tip
1
68
00202040
Thermocouple + fuse 115 M8x1x570 Alu tip
1
69
00198010
Thermocouple extension M8xM8 L=300mm
1
70
01381001
Hexagonal nut M8x1
2
71
03000010
Bougie EID2G-Global
1
72
03000020
Cooling Ring EID2G Ignitor
1
73
03010010
Ignition Cable
1
74
07250020
Self tapping screw3,5x16mm
1

Technical table
Category
Gas
Maximum
Supply
pressure
Minimum
Supply
pressure **
Maximum
Heat Input
Minimum
Heat Input
Gas
consumption
Main
Injector
(1x)
By-pass
hole T,
Ti, S **
Venturi
Ring
Injector
Holder
NOx
Class
Remarks
(-) (-)*
(mbar)
(mbar) (kW Hs)
(kW Hs)
(g/h or m3/h)
(mm)
(mm)
(mm)
(-)
(-)
(-)
Global-5 series
I2H, I2E
G20
300
10
5,2
0,87
0,50 m3/h
0,77
-
13
0
I2H, I2E
G20
300
20
4,8
0,63
0,46 m3/h
0,60/0,59
0,31
12
-
(Di)
I3B/P
G30
1000
10
5,1
0,50
370 g/h
0,47
-
11
4
I3P
G31
350/300
20
5,0/4,6
0,60
360/330 g/h
0,50/0,47
0,24
18
-
(Di)
I3P
G31
1000
20
5,7
0,80
410 g/h
0,52
0,25
10
4
I3P
G31
1400
20
5,5
0,65(T=1,2)
400 g/h
0,47
0,22
10
4
4
0063CS3936
I3P
G31
1400
20
5,5
0,65(T=1,2)
400 g/h
0,47
0,22
12
4
5
0063CS3936 (2F)
I3P
G31
1400
20
4,6
0,55
330 g/h
0,45
0,25
11
4
(Ha >1400 m)
Biogas
BG
100
5
5,1
0,90
0,74 m3/h
1,55
0,75
10,5
4
Global-10 series
I2H, I2E
G20
300
50
8,8
3,6
0,84 m3/h
1,05
-
15
6
I2H, I2E
G20
1400
20
8,5
1,0
0,81 m3/h
0,70
-
10
4
(air=4x17mm)
I3P
G31
300
100
8,0
4,6
570 g/h
0,83
-
16
7
I3P
G31
1400
20
9,5
1,15(T=1,9)
680 g/h
0,62
0,28
13
6
4
0063CS3936
I3P
G31
1400
20
8,6
1,0(T=1,9)
615 g/h
0,59
0,28
13
6
4, (T=3)
0063CS3936 (2F)
I3P
G31
1400
20
7,5
0,9 (T=1,7)
620 g/h
0,58
0,28
14
6
(Ha >1400 m)
I3P
G31
2000
20
8,8
0,8(T=1,4)
630 g/h
0,53
0,22
12
6
I3P
G31
2000
20
8,8
0,8(T=1,4)
630 g/h
0,53
0,22
13
6
(2F)
* G31 = propane, G20 = natural gas (100% methane), G25 = natural gas (86% methane); Biogas = 60% methane + 40% carbon dioxide
** In case the heater is equipped with a bypass hole (thermostat T, Ti and solenoid S version) the heater shall be operated on maximum supply pressure only.
See also the pressure information on the data plate.
Conversion calculation from gross heat input kW(Hs) to nett heat input kW(Hi):
Propane: divide gross heat input kW(Hs) by factor 1,09 (example: 1,20 kW(Hs) / 1,09 = 1,10 kW(Hi)
Natural gas: divide gross heat input kW(Hs) by factor 1,11 (example: 1,20 kW(Hs) / 1,11 = 1,08 kW(Hi)
This manual suits for next models
19
Table of contents
Other Alke Heater manuals
Popular Heater manuals by other brands
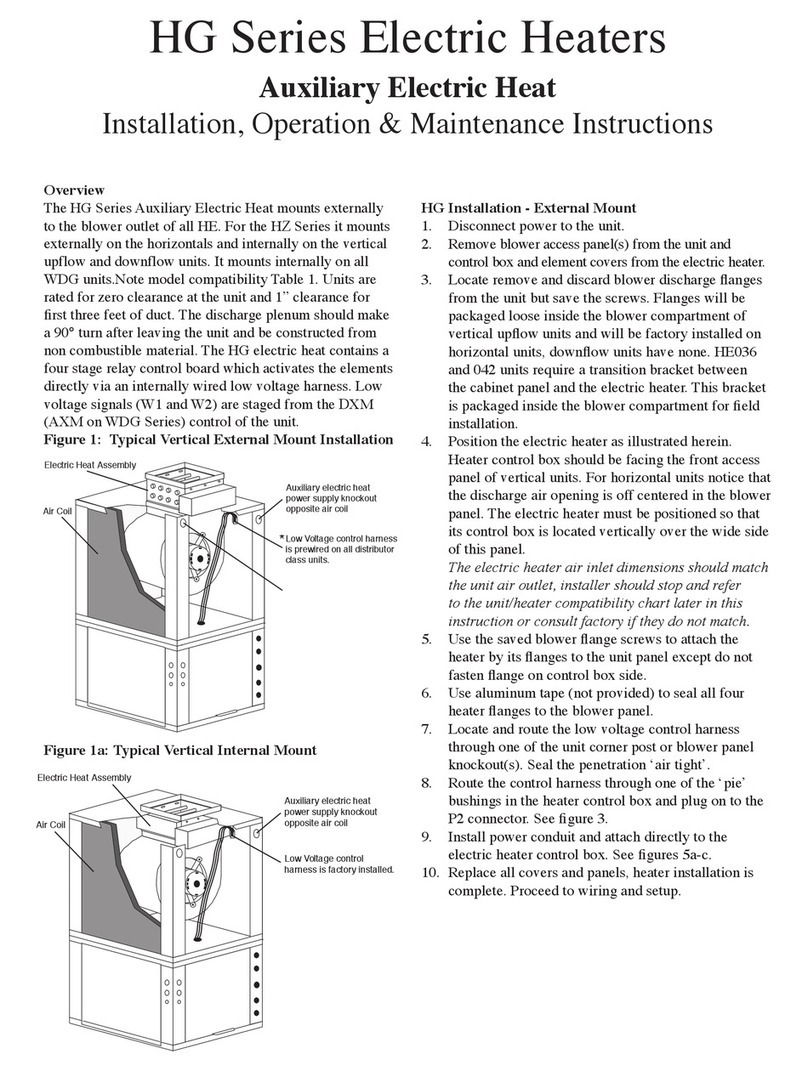
Mars
Mars Comfort-Aire Century HG Series Installation, operation & maintenance instructions
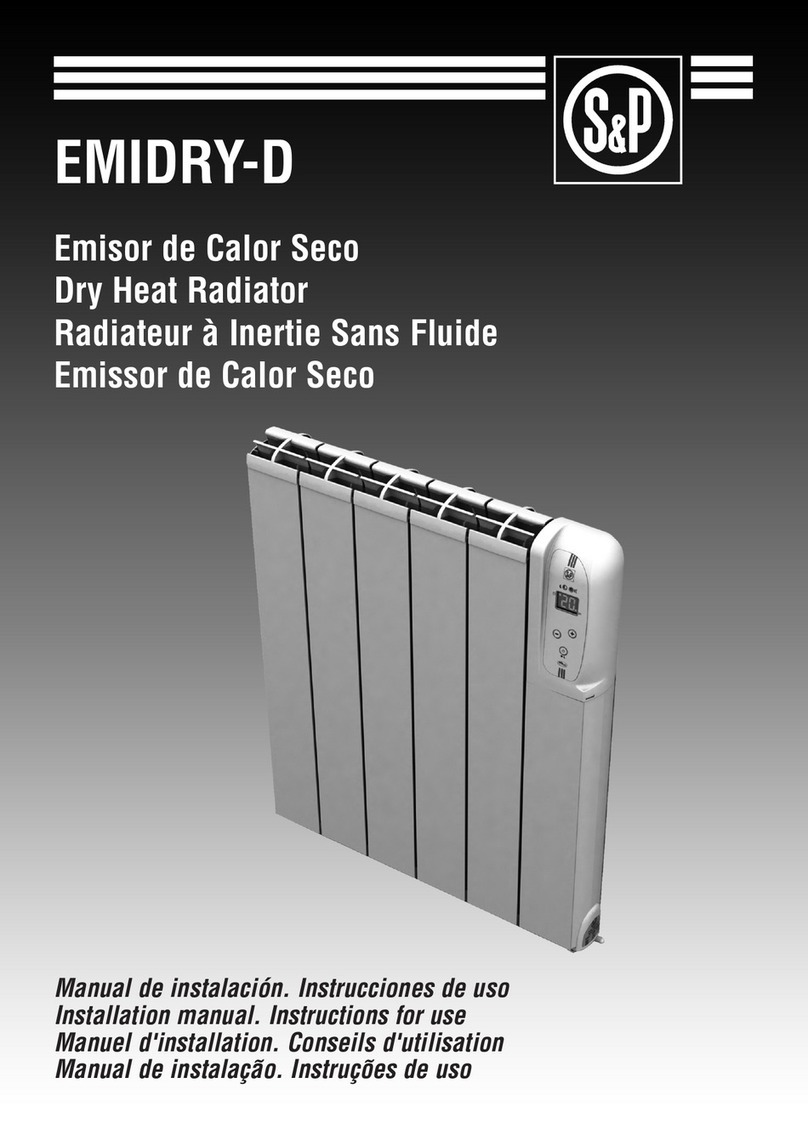
S&P
S&P EMIDRY-D Installation manual and instructions for use

Frico
Frico PA2510E05 Original instructions
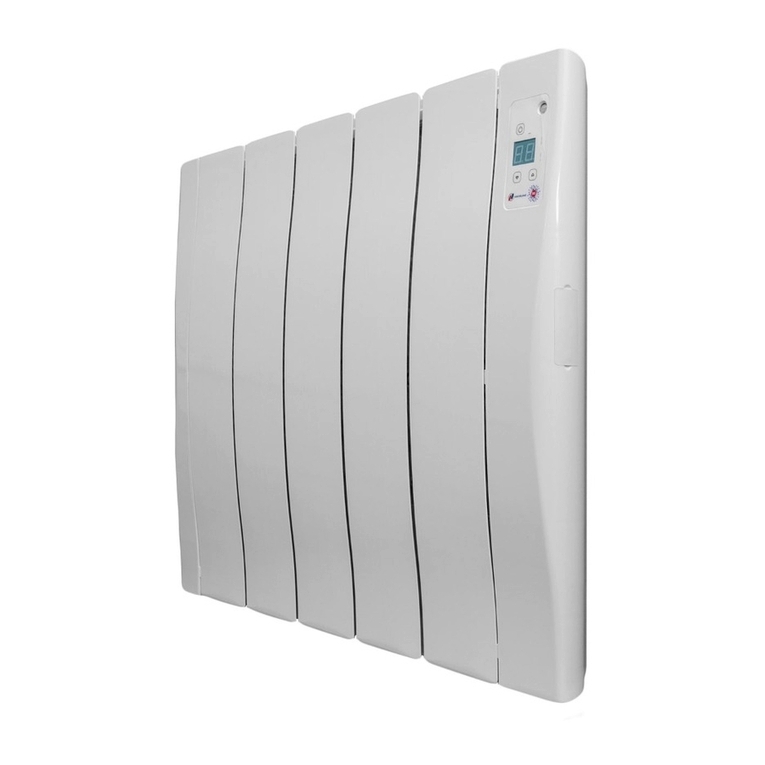
Haverland
Haverland Wi SmartWave Series Instruction and installation manual
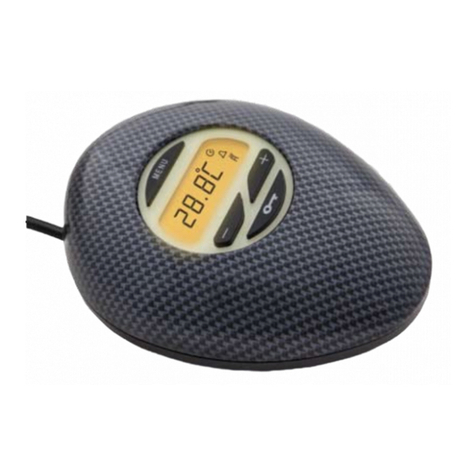
Carbon Heater
Carbon Heater CHD 230V 100-300W operating instructions
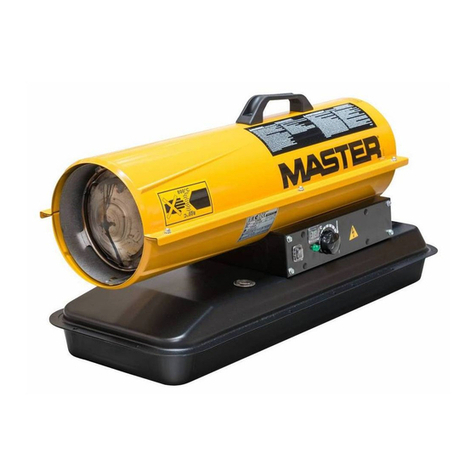
Master
Master B 65 CEL owner's manual