Allied Systems Long Reach PTC Series Manual

145-074, REV. 5/18
Installation, Maintenance
and Service Manual
PTC
Pipe Clamp

245-074, REV. 5/18
TABLE OF CONTENTS
SECTION 1 NAMEPLATE LOCATION ..............3
SECTION 2 MODEL NUMBER DESCRIPTION 4
SECTION 3 SAFETY SUMMARY......................5
3.1 Safety Information ....................................5
3.2 Safety Regulations ...................................5
3.3 Safety Symbols ........................................5
3.4 Labeling....................................................6
3.5 Training.....................................................6
3.6 Personnel Safety ......................................6
3.7 Pre-start Checks ......................................7
3.8 Operation Warnings .................................7
3.9 Hydraulic Hazards ...................................7
3.10 Electrical Hazards ..................................7
3.11 Maintenance Warnings...........................8
3.12 Load Handling........................................8
3.13 Load Positioning.....................................9
3.14 Operator’s Controls ...............................9
3.15 Industry Standards...............................10
3.16 Clamp Open Control ............................10
SECTION 4 INSTALLATION PROCEDURE....12
4.1 Truck Requirements ...............................12
4.2 Attachment Installation...........................12
4.3 Hydraulic Connections ...........................13
SECTION 5 SERVICE PROCEDURE..............14
5.1 Attachment Removal..............................14
5.2 Pinion/Ring Gear And Bearing...............14
5.3 Bearing Seal Replacement ....................15
5.4 Gearbox Lubrication...............................15
5.5 Gearbox Disassembly ............................16
5.6 Gearbox Assembly.................................21
5.7 Motor Disassembly.................................21
5.8 Motor Assembly .....................................24
5.9 Cylinder Removal...................................28
5.10 Cylinder Installation..............................28
5.11 Cylinder Disassembly...........................28
5.12 Cylinder Inspection...............................29
5.13 Cylinder Assembly ...............................30
5.14 Swivel Assembly Removal ...................30
5.16 Swivel Assembly Installation ................31
SECTION 6 MAINTENANCE ...........................32
6.1 Schedule ................................................32
6.2 Torque Specifications .............................33

345-074, REV. 5/18
- -
Date Received:
SECTION 1 NAMEPLATE LOCATION
When you receive your attachment,
locate the Long Reach nameplate (upper
left corner on the body). Record the
information from the nameplate, along
with the date received, at the bottom of
this page. If the nameplate is missing,
look for the serial number stamped
directly into the metal at the nameplate
location and consult the factory for
details.
APPROX.
S/N PLATE
LOCATION

445-074, REV. 5/18
SECTION 2 MODEL NUMBER DESCRIPTION
Each clamp is identified by a model number and a serial number located on the name plate attached to the unit prior
to shipment. Long Reach’s model numbers are designed to describe how an attachment is equipped. The guide
below illustrates the information that is represented in its model number. Always include model and serial number
when ordering parts or requesting service information.
Series Model Number:
PT C 1 2 2 4 P 3
SERIES
PTC = Pipe Clamp
CAPACITY
12 = 12,000 lb
STD = Standard
P3J = Pin mounting to fit CAT truck
model DP115. Approximate pivot/
sideshift - 22"
Polyurethane covered swivel pads,
360° rotation
J
24 = Designed to handle
9" - 24" diamter pipe

545-074, REV. 5/18
SECTION 3 SAFETY SUMMARY
3.1 Safety Information
Safety is Everyone’s Responsibility
Whether you are new on the job or a seasoned veteran,
these safety tips may prevent injury to you, to others, or
to the materials you are handling. Always be alert, watch
out for others, and follow these suggestions:
Attachments handle material, not people.
Safety starts with common sense, good
judgement, properly maintained equipment,
careful operation, and properly trained
operators.
The safety instructions and warnings, as documented
in this manual and shipped with the machine, provide
the most reliable procedures for the safe operation and
maintenance of your Long Reach attachment. It’s your
responsibility to see that they are carried out.
3.2 Safety Regulations
Know your company’s safety rules. Some companies
have site-specific directions and procedures. The meth-
ods outlined in your operator’s manual provide a basis for
safe operation of the machine. Because of special condi-
tions, your company’s material handling procedures may
be somewhat different from those shown in this manual.
3.3 Safety Symbols
The following terms define the various precautions and
notices:
DANGER
Indicates a hazardous situation which, if
not avoided, will result in death or serious
injury. Carefully read the message that
follows to prevent serious injury or death.
WARNING
Indicates a hazardous situation which,
if not avoided, could result in death or
serious injury. Carefully read the message
that follows to prevent serious injury or
death.
CAUTION
Indicates a hazardous situation which,
if not avoided, could result in minor or
moderate injury, or equipment damage or
void the machine warranty. Carefully read
the message that follows to prevent minor
or moderate injury.
NOTICE
Describes information that is useful but not
safety related.
WARNING
Multiple hazards.
Ignoring safety warnings may cause
equipment damage, personal injury or
death.
All possible safety hazards cannot be
foreseen and included in this manual. The
operator must always be alert to possible
hazards that could endanger personnel or
damage the equipment.

645-074, REV. 5/18
3.4 Labeling
• Change capacity, operation, and maintenance instruc-
tion plates, tags, or decals when a forklift truck is
equipped with an attachment. If the truck is equipped
with front-end attachments other than factory installed
attachments, truck must be marked to identify the
attachments and show the approximate weight of
the truck and attachment combination at maximum
elevation with load laterally centered.
3.5 Training
• Make sure all operators are trained in the fork and
attachment adaptation, operation, and use limitations.
Retrain an operator if a new attachment is added to
the forklift. Consult the operator’s manual for instruc-
tions on how to use the new equipment.
• Know the mechanical limitations of your forklift.
• Modifications or additions that affect capacity or safe
operation must have prior written approval from the
forklift truck manufacturer. Capacity, operation, and
maintenance instruction plates, tags, or decals shall
be changed accordingly.
• Never use free rigging for a below-the-forks lift. It could
affect the capacity and safe operation of a lift truck.
3.6 Personnel Safety
• When removing or installing dismountable at-
tachments always keep hands and feet free from
dangerous positions or pinch points. Never leave a
dismounted attachment in a dangerous position.
• Keep hands, feet, long hair and clothing away from
power-driven parts. Do not wear loose fitting clothing
or jewelry while performing maintenance and lubrica-
tion in these areas.
• Never jump on or off the machine.
• Never stand on top of material being raised, lowered,
or transported. (Figure 3-1)
Figure 3-1
Figure 3-2
Figure 3-3
• Never use the attachment or its load to support a
man-carrying device.
• Never allow anyone under a load or under the car-
riage. (Figure 3-2)
• Never stand in front of or beside an attachment that
is being operated. Never allow another person to ap-
proach an attachment that is being operated. (Figure
3-3)
• Never leave an attachment or load in an elevated
position.
• Never reach through the mast of the truck. Keep all
parts of the body within the driver’s compartment.
• Always operate an attachment from the operator’s
seat, never while standing next to the lift truck.
• Do not allow riders on the truck at any time.
• Always use reverse when carrying a load that impedes
full vision. Watch for pedestrians when transporting.
• Always use personal protective equipment (PPE)
appropriate to the situation.

745-074, REV. 5/18
3.7 Pre-start Checks
• Check your equipment before you operate it. If any-
thing looks wrong, unusual or different, report it before
using the attachment.
• Do not operate this machine if you know of malfunc-
tions, missing parts, and/or mis-adjustments. These
situations can cause or contribute to an accident or
damage to the machine. Stop the machine immedi-
ately if problems arise after starting.
• Check to make sure the attachment on your truck is
the same as on the truck capacity plate.
• Check for hydraulic leaks and cracked hoses or fit-
tings. Check the hydraulic oil level in the lift truck
hydraulic reservoir.
• All electrical cables and connectors must be in good
condition. Use caution in wet weather to avoid danger
from electrical shock.
• Always check the attachment for proper fit and en-
gagement of the truck carriage.
3.8 Operation Warnings
• You must be trained to operate this equipment prior to
operation. Be extremely careful if you do not normally
operate this machine. Reorient yourself to the machine
before starting, then proceed slowly.
• Always operate an attachment from the driver’s seat.
• Always lower the attachment if you need to leave the
lift truck. A lift truck supporting a load requires your
full attention.
3.9 Hydraulic Hazards
DANGER
Injection hazard.
Infection and gangrene will result
when hydraulic oil penetrates the
skin. See a doctor immediately to
prevent loss of limb or death.
Use a piece of cardboard to check for
hydraulic leaks.
• Wear personal protective equipment, such as gloves
and safety glasses, whenever servicing or checking
a hydraulic system.
• Assume that all hydraulic hoses and components are
pressurized. Relieve all hydraulic pressure before
disconnecting any hydraulic line.
• Never try to stop or check for a hydraulic leak with any
part of your body; use a piece of cardboard to check
for hydraulic leaks.
3.10 Electrical Hazards
WARNING
Electrocution hazard.
Contact with energized equipment may
result in injury or death and will damage
equipment.
Remain at least 25 feet from high voltage
electrical wires.
• All electrical cables and connectors must be in good
condition (free of corrosion, damage, etc). Use cau-
tion in wet weather to avoid danger from electrical
shock. Never attempt electrical testing or repair while
standing in water.
• Do not wear electrically conductive jewelry, clothing,
or other items while working on the electrical system.
3.11 Maintenance Warnings
Maintenance, lubrication and repair of this machine can
be dangerous unless performed properly.You must have
the necessary skills and information, proper tools and
equipment. Work in a method that is safe, correct, and
meets your company’s requirements.
• Do not attempt to make adjustments, or perform
maintenance or service unless you are authorized
and qualified to do so.
• Include attachments in a scheduled maintenance
and inspection program. Tailor inspection steps to
the attachment.
• Unless specified in service procedures, never attempt
maintenance or lubrication procedures while the ma-
chine is moving or the engine is running.

845-074, REV. 5/18
• Always perform all maintenance and lubrication pro-
cedures with the machine on level ground, parked
away from traffic lanes.
NOTICE
Local laws and regulations may require
that additional safety measures be taken.
• Never rely on the hydraulic system to support any
part of the machine during maintenance or lubrication.
Never stand under a component that is supported
only by the hydraulics. Make sure it is resting on its
mechanical stops or appropriate safety stands.
• Use caution when working around hot fluids. Always
allow lubricating and hydraulic oils to cool before
draining. Burns can be severe.
• Use extreme caution when using compressed air to
blow parts dry. The pressure should not exceed 30
psi (208 kPa) at the nozzle. Never use compressed
air on yourself. Air pressure penetrating your skin
can be fatal.
WARNING
Suffocation hazard.
Engine exhaust fumes can cause death.
Remove the exhaust fumes from the area
with an exhaust pipe extension, or use
ventilation fans and open shop doors to
provide adequate ventilation.
• Before disconnecting hydraulic lines, be sure to lower
all loads and relieve all hydraulic pressure. The load
could fall on you, or escaping hydraulic oil could cause
severe personal injury.
• Prevent personal injury or equipment damage by us-
ing a lifting device with a lifting capacity greater than
twice the weight of any equipment to be lifted.
3.12 Load Handling
• Treat an unloaded forklift with an attachment as par-
tially loaded.
Equipment overload hazard.
Injury or equipment damage may result if
the capacity of the truck and attachment
combined are less than the attachment
capacity.
Consult truck nameplate for truck
capacity with an attachment installed.
• Never overload the attachment. Refer to the attach-
ment nameplate for the rated capacity of the attach-
ment. Refer to the truck nameplate for the maximum
net working capacity of the truck/attachment combi-
nation. Never use a load to support or move another
object. Doing so can easily exceed the holding capac-
ity of the attachment.
• Always check loads to be handled. Correct loads that
are broken, unbalanced, loose, or too heavy.
• Never lift, lower, side shift, pivot, rotate, or tilt loads
while traveling. Repositioning loads while traveling af-
fects the stability of the truck and may impede vision
or clearances.
• Do not use an attachment to open or close boxcar
doors. Doing so can severely damage the attachment
and cause loss of warranty. Damage to clamp arms
may result in product damage.
• Do not carry loose items or unsupported loads on top
of a clamped load.
• Never use chains, cables, or other devices in conjunc-
tion with an attachment for load handling.
• Never clamp loads other than what the attachment
was designed to handle.
• Always carry cylindrically shaped loads in the vertical
position, not the horizontal.
• Always clamp loads with the contact pads, if appli-
cable, not the arm or arm base.
• Never rotate a load that is off center to the centerline
of rotation. Severe damage to the rotator could result.
• Always ensure that the load is the same width as the
pallet and neatly stacked when using a carton clamp.

945-074, REV. 5/18
3.13 Load Positioning
• Be accurate in load placement. It’s important to know
what the load will do when it’s released.
• Always carry loads as close to the floor as possible,
consistent with the surface being traversed. Scraping
or bumping the floor surface with the load or the at-
tachment can severely damage the attachment and
cause product damage. The mast should be tilted
back.
• Always keep the load positioned as close as possible
to the horizontal center of the lift truck.
• Always back down ramps or inclines. Driving forward
down a ramp or incline with a clamped load will lessen
the stability of the truck. (Figure 3-4)
Figure 3-4
• Do not cross dock boards or dock levelers with the
attachment or carriage fully lowered. Ramming the
front or rear of the attachment against a dock board
can cause severe damage.
• Limit lift truck movement to a minimum when high
stacking. Limit sideshift movement to a minimum
when high stacking.
• Always be observant when high stacking. Look for
poorly stacked loads, overhead obstacles, broken
cartons, or damaged products in the stack.
• Travel slowly around corners. Sound horn on blind
corners. Be careful of tail swing and overhead clear-
ances. Watch in all directions. Avoid sudden stops.
3.14 Operator’s Controls
Some lift trucks are equipped with a single lever to control
both hoist and tilt functions, others have separate levers
for each function. Refer to your lift truck manual for more
information.
For clarity, the direction of arm movement is shown on the
control handle.To move the arms in the direction shown,
pull the handle towards the operator. To move the arms
in the opposite direction, the push the handle away from
the operator. (Figure 3-5)
Clamp Fork position
Push/pull Rotate Sideshift
Figure 3-5 Operator controls
Lifting speed is controlled by the speed of the engine
and the position of the control lever. Engine speed has
no effect on lowering speed.
Before going on the job, shift the truck control levers one
way and then the other to determine which direction the
attachment moves when the levers are shifted. Make sure
the attachment moves smoothly throughout its travel,
without binding or pinching hoses.
Equipment damage hazard.
Injury or equipment damage may result if
the attachment does NOT operate smoothly.
Do not take malfunctioning equipment on
the job. Check with your supervisor about
needed repairs.

10 45-074, REV. 5/18
3.15 Industry Standards
ANSI/ITSDF B56.1-2016 is the published sequence and
direction standard for lever- and hand-type controls.
The chart on the following page shows
industry standards. Your equipment may
be different. If you do not routinely operate
this equipment, refresher training is
recommended. You must reacquaint
yourself with this manual and the equipment
before starting, and then proceed slowly.
Special controls such as automatic devices should be
identified, preferably according to the recommendations
in Figure 3-6.
When a function is controlled by a pair of push buttons,
they should operate in the same sense as the lever con-
trols. For example, pushing a button located to the rear
(relative to the operator’s position) should serve the same
function as moving a control lever to the rear.
3.16 Clamp Open Control
Effective October 7, 2010, safety standard ANSI/ITSDF
B56.1, Section 7.25.7 covers all lift trucks with a load
bearing clamp (paper roll clamp, carton clamp, etc.),
and requires the driver to make two distinct motions
before opening or releasing the clamp. For example,
you must press a switch and then move a lever to
unclamp the load. This requirement applies to new
and used attachments being mounted on trucks which
shipped from the factory after October 7, 2010, and is a
recommended feature to be installed on dealer orders
and existing applications.

1145-074, REV. 5/18
Function Direction of motion
Load Operator's hand on control handle, facing the load*
Hoist
Up
Down
Rearward or up
Forward or down
Reach Retract
Extend
Rearward or up**
Forward or down
Tilt Rearward
Forward
Rearward or up**
Forward or down
Sideshift Right
Left
Rearward or up
Forward or down
Push-pull Rearward
Forward
Rearward or up**
Forward or down
Rotate, lateral Clockwise
Counterclockwise
Rearward or up
Forward or down
Rotate, longitude Rearward
Forward
Rearward or up
Forward or down
Load stabilizer Down
Up
Rearward or up
Forward or down
Swing Right
Left
Rearward or up
Forward or down
Slope Clockwise
Counterclockwise
Rearward or up
Forward or down
Fork position Together
Apart
Rearward or up
Forward or down
Tr i p Engage
Release
Rearward or up
Forward or down
Grip Engage
Release
Rearward or up
Forward or down
Truck stabilizer Raise
Lower
Rearward or up
Forward or down
Clamp Clamp
Release
Rearward or up
Forward or down
Figure 3-6 ANSI/ITSDF Sequence of location and direction of motion for lever- or hand-type controls
* For high lift order picker trucks and center control pallet trucks, predominant motion of the operator’s hand when actuating the control handle
while facing away from the load.
** The sense of rotation of the control handle is intended to be in the same direction as the desired motion of the mast or load.

12 45-074, REV. 5/18
SECTION 4 INSTALLATION PROCEDURE
4.1 Truck Requirements
Long Reach attachments have been designed to oper-
ate within specific limits. Operating pressures above the
recommended maximum may cause damage to the at-
tachment and may void the warranty. Operating pressure
specifications for your attachment can be found on the
attachment nameplate. (Section 1)
Hydraulic flow less than the recommended rates, or the use
of small I.D. hoses may reduce operating speed. Higher flow
can result in excessive heat buildup, erratic operation and
damage to the truck/attachment hydraulic system. Hydraulic
flow specifications for your attachment can be found on
the attachment nameplate. (Section 1)
The dealer and/or the user must provide
and install the valving required to meet
the recommended hydraulic pressures
and flow, or must arrange installation of
the required valving at the truck factory.
The attachment model description, found
on your shipped invoice, will state the
following truck requirements: flow (gpm),
psi, and minimum truck carriage width.
1. The truck carriage must conform to the American
National Standard (ANSI) dimensions shown in ANSI/
ITSDF B56.11.4-2013.
2. Make sure the truck carriage is clean, conforms to
ANSI recommendations, and the notches are not
damaged.
3. The truck hydraulic system must supply the attach-
ment hydraulic oil that meets the specifications
required to operate the attachment properly.
3. The truck hydraulic system must supply to the attach-
ment with hydraulic oil that meets the specifications
required to operate the attachment properly. Find
specifications for your attachment on the attachment
nameplate. (Section 1)
4.2 Attachment Installation
1. Prior to connecting the truck hydraulic system to the
attachment, the system must be purged through the fil-
tration system.This will eliminate any contamination that
might exist in the auxiliary hydraulic system of the truck.
WARNING
Equipment overload hazard.
Overloading the truck may cause equipment
damage.
Consult truck nameplate to determine
the capacity of the truck and attachment
combination, as it may be less than the
capacity shown on the attachment alone.
2. Purging can be accomplished by installing a jumper
line and operating each hydraulic function (clamp,
rotate and side shift if equipped) in each direc-
tion for a minimum of 30 seconds. (Figure 4-1)
Hoses should be 2300 psi working pressure rated for
all attachment functions.
To Truck
To Clamp
Figure 4-1, Jumper Line

1345-074, REV. 5/18
3. Install the pin-mount attachment to truck carriage.
Using the attachment as a template, weld on the
bracket lugs, supplied with the attachment, to lower
bar on the truck carriage. (Figure 4-2)
Truck Carriage
Mounting Lug
Capscrew
70,000 PSI
min. yield
strength typ.
.38
Washer
Figure 4-2, Pin-Mount Lug
4. Weld the bracket lugs with 7018 welding rod, or equiva-
lent, on each side of the truck carriage. Use provided
capscrews to secure attachment to truck carriage.
(Figure 4-3)
Equipment damage hazard.
Equipment damage, performance
reduction, personal injury and/or loss of
warranty could result if any alterations are
made to the original attachment.
Consult with factory before altering original
equipment.
4.3 Hydraulic Connections
1. Install the lines from the truck’s hydraulics to the
hydraulics of the attachment.
2. Inspect installation to ensure hoses are not kinked or
pinched between the truck carriage and attachment.
3. Operate the attachment continuously for several min-
utes to determine that all hydraulic connections are
secure with no leaks.
4. With the mast in the vertical position, rotate the attach-
ment fully 360°. After this procedure, check that the
truck’s hydraulic reservoir oil level is at the recom-
mended level.
5. Before placing the attachment in operation inspect
all hoses and fittings for leaks and routing clearance.
Be sure to include clearance of jumper hoses to the
mast.
6. After completing the installation, operate the attach-
ment without a load for several cycles to remove any
air in the hydraulic system.Test the attachment with a
load to make sure the attachment operates correctly.

14 45-074, REV. 5/18
SECTION 5 SERVICE PROCEDURE
5.1 Attachment Removal
Not all procedures require that the attachment be re-
moved from the truck. Review each procedure before
beginning. Make sure any lifting equipment used is rated
for the load being lifted.
1. Position the attachment arms to the width of the unit’s
body.Turn off lift truck.Relieve pressure in the hydrau-
lic circuit to the attachment by cycling the lever back
and forth several times.
WARNING
Crush hazard.
Serious injury could result if residual
hydraulic pressure causes equipment to
drift during service procedures.
Cycle the hydraulic circuit as described
above to relieve all system pressure.
2. Slightly raise the truck carriage to allow the removal
of the bottom mounting lug bolts.
3. Position the attachment on the edge of a pallet.Lower
the attachment so that the lower carriage bar misses
the pallet when lowered. Remove any necessary
components from the truck carriage to allow access
to fork pin. Drive pin out to allow safe disengagement
of attachment from truck.
4. To reinstall, follow the installation procedure in this
manual.
NOTICE
Equipment damage hazard.
Equipment damage and loss of performance
could result if air is trapped in the hydraulic
system.
Activate the hydraulic functions several
times after hydraulic service has been
performed, to bleed trapped air out of the
system before returning attachment to
service.
5.2 Pinion/Ring Gear And Bearing
1. Grease the pinion/ring gear every 40 hours.Grease the
ring gear bearings every 100 hours.(See Section 6)
Equipment damage hazard.
Gears may wear out prematurely if not
properly greased. Worn gears may affect
performance or safety and result in loss
of warranty.
Grease gears with recommended lubricant
as described.
2. Grease the pinion/ring gear with Mobil lubricating
grease NLGI grade 2 ISO 220 or equivalent.
3. Gease the ring gear bearings with Aeroshell 22 grease
or equivalent.
4. To ensure proper greasing of gears and bearings,
slowly rotate the ring gear 360° while greasing, this
will allow grease to completely coat the gear. Gears
must be fully greased. (Figure 5-3)
Pinion/Ring
Gear Grease
Fitting
Ring Gear
Bearing Grease
Fitting
Figure 5-1, Grease Fitting Locations

1545-074, REV. 5/18
5.3 Bearing Seal Replacement
Equipment damage hazard.
Foreign matter in the bearing could cause
bearing failure.
Prevent any foreign matter from falling into
the bearing during the seal replacement
procedure.
1. Remove all traces of the former seal and glue from
the seal groove by mechanically scraping the groove.
2. Clean the groove with a no-residue commercial sol-
vent (trichloroethane) to remove any trace of oil or
grease.
3. Wipe the seal with the same solvent to insure
cleanliness.
4. Apply a bead of adhesive to the back of the seal groove.
Use enough adhesive to cause some extrusion to coat
the seal on all three surfaces contacting the groove.
Equipment damage hazard.
Foreign matter in the bearing could cause
bearing failure.
Keep adhesive from being extruded into
the bearing SEPARATION LINE as the seal
is installed.
Separation
Line
Seal
Seal Separation
Line
Figure 5-2, Bearing Seal
5. Insert the seal into the groove with firm steady pres-
sure, but avoid stretching the seal.
6. The length of the seal provided is longer than required.
Before gluing the last six inches, insert the seal into the
groove to determine the exact length required.Trim
the excess with a sharp knife so it smoothly meets
the adjoining end.
7. Place a drop of super-glue on the end already in the
bearing so that the two ends will be joined.
8. Allow ten minutes for the glue to cure.
9. Re-grease the bearing until grease exudes from under
the seal to remove any foreign matter that might have
become lodged in the bearing separation line.
5.4 Gearbox Lubrication
Part Number: YGC-29, YGC-32, YGC-43 And YGC-
43-LH
1. Remove the top plug and the oil level plug from the
Gearbox. (Figure 5-3)
Plug
Oil Level Plug
Figure 5-3, Gearbox Oil Plugs
2. Use Mobil HD 85W140 or equivalent oil.For tempera-
tures below -20° F, use Mobil SHC 634 or equivalent
synthetic oil.

16 45-074, REV. 5/18
Equipment damage hazard.
Overfilling the gearbox may damage the
gearbox, causing a leak.
Do not overfill gearbox with oil.
3. Fill the gearbox to the oil level plug location.
4. The oil level should be checked occasionally at the
oil level plug. If the oil level has dropped, a leak may
have occurred.The leak should be corrected and the
oil should be leveled off to the oil level plug location.
5. Reinstall plugs.
Part Number: YGC-48, YGC-49, YGC-49-LH, YGC-50
And YGC-50-LH
1. The grease in the gearbox will not need to be filled or
changed unless the Gearbox itself has been serviced.
2. Remove the top and back plugs from the gearbox and
completely fill with Movilux EPO or equivalent grease.
(Figure 5-6)
Top Plug
Back Plug
Figure 5-6, Gearbox Grease Plugs
3. Lay the gearbox with the pinion gear down and fill the
gearbox from the top plug hole, allowing traped air
to escape through the back plug hole, until grease is
present in the back plug hole.
4. To fill gearbox mounted to back plate, fill gearbox
from the back plug hole, allowing traped air to escape
through the top plug hole, until grease is present in
the top plug hole.
5. Reinstall the plugs.
5.5 Gearbox Disassembly
Part Number: YGC-29, YGC-32, YGC-43 And YGC-
43-LH
1. Remove the attachment from truck. (See Section 5.1)
2. Before removing the gearbox from the back plate,
place a support overhead or under the gearbox.
Remove the mounting capscrews from the gearbox.
(Figure 5-7)
3. Place the gearbox on a flat surface and remove the
Motor mounting capscrews. Note:Coupling fits loose
and may slide out. (Figure 5-8)
4. Remove the Pinion Gear and Key from the Output
Shaft. Use a screwdriver to knock loose the key.
Gearbox
Capscrew Motor
Back Plate
Figure 5-7, Gearbox Removal
3. Place the gearbox on a flat surface and remove the
motor mounting capscrews. Note:Coupling fits loose
and may slide out. (Figure 5-8)

1745-074, REV. 5/18
Gearbox
Capscrew
Motor
Capscrew
Housing Cover
Figure 5-8, Motor Removal
4. Remove the pinion gear and key from the output shaft.
Use a screwdriver to knock loose the key.
Equipment damage hazard.
Impact wrenches could damage screws
or sockets if screws have been secured
with Loctite.
Use care when working with the gear
assembly. Do not use a impact wrench on
the screws that have been secured with
Loctite.
CAUTION
Oil leak hazard.
Removing the adapter plate without
draining the oil can result in a large oil spill.
Drain oil from the gearbox before removing
the adapter plate.
5. Remove the capscrews from the adapter plate. The
adapter plate capscrews are installed with Loctite, use
a long handle wrench to them break loose.Lightly tap
the back of the adapter plate with a rubber mallet to
remove. (Figure 5-9)
Key
Screwdriver
Pinion Gear
Capscrew
Capscrew
Adapter
Plate
Figure 5-9, Adapter Plate Removal
6. The output shaft seals may now be serviced. (Figure
5-10)
O-Ring
Seal
Adapter Plate
Figure 5-10, Output Shaft Seals

18 45-074, REV. 5/18
7. Remove the output shaft assembly. (Figure 5-11)
Bearing
Bearing
Snap Ring
Output Shaft
Worm Gear
Shim
Spacer
Figure 5-11, Output Shaft
8. The output shaft fits tightly, so you may need to remove
the cap on the back of the gearbox and lightly tap the
end of the output shaft with a rubber mallet to remove
it. (Figure 5-12)
Cap
Figure 5-12, Output Shaft Cap
9. Remove the end cap and motor adapter. Make note
of any installed shims. Capscrews are installed with
Loctite, so use a long handle wrench to break them
loose. (Figure 5-13)
Capscrew
Capscrew
O-Ring
O-Ring
Motor Adapter
End Cap
Shim
Shim
Shim
Coupling
Figure 5-13, End Cap / Motor Adapter
10. Remove the input shaft assembly.The assembly fits
tightly, so use a rubber mallet or press on the extend-
ed shaft to remove it. Remove the exposed key with a
screwdriver, allowing the bearing and worm to slide
off of the shaft. (Figure 5-14)
Screwdriver
Key
Bearing
Snap Ring
Key Worm
Bearing
Figure 5-14, Input Shaft
11. Reassemble in reverse order.Use Loctite (Blue) on all
capscrews.(See Section 6 for Torque Specifications)
NOTICE
It is important to get oil to the worm and
worm bearings. Before reinstalling, dip the
worm and worm bearings in oil for proper
lubrication. (See Section 5.3)

1945-074, REV. 5/18
Part Number: YGC-48, YGC-49, YGC-49-LH, YGC-50
And YGC-50-LH
1. Remove the attachment from truck.(See Section 5.1)
2. Before removing the gearbox from the back plate,
place a support overhead or under the gearbox.
Remove the mounting capscrews from the gearbox.
(Figure 5-15)
Motor
Gearbox
Backplate
Capscrew
Figure 5-15, Gearbox Removal
3. Place the gearbox on a flat surface and remove the
Motor mounting capscrews. (Figure 5-16)
Gearbox
Capscrew
Motor
Capscrew
Housing Cover
Figure 5-16, Motor/Gear Cap Removal
4. Remove the capscrews from the gear cap.The gear
cap capscrews are installed with Loctite, so use a long
handle wrench to break them loose. Using a large
screwdriver and hammer, separate the gear cap from
the housing. (Figure 5-16)
Equipment damage hazard.
Impact wrenches could damage screws
or sockets if screws have been secured
with Loctite.
Use care when working with the gear
assembly. Do not use a impact wrench on
the screws that have been secured with
Loctite.
Equipment damage hazard.
The equipment could fail if machined
surfaces of the gear cap and housing are
damaged during disassembly.
Use care when working with the gear
assembly.
5. Remove the pinion shaft assembly. (Figure 5-17)
6. Remove the snap ring from the end of the pinion shaft.
(Figure 5-17)
Housing Cover
Shims
Large Bearing
Worm Gear
Small Bearing
Pinion Shaft
Snap Ring
Figure 5-17, Pinion Shaft
7. Place the assembly in a press supporting the gear cap,
not the pinion shaft.Press the pinion shaft through the
small bearing and the worm gear. At this point the small
bearing, worm gear and large bearing are loose and can
be lifted out of the housing. (Figure 5-17)

20 45-074, REV. 5/18
Equipment damage hazard.
A chipped pinion shaft will affect machine
performance.
Do not drop the pinion shaft onto a hard
surface or it may chip.
NOTICE
The small bearing cup in the housing and
the large bearing cup in the gear cap will
need to be removed with a bearing puller.
8. Wipe as much grease out of the housing as possible
with a rag and inspect for any foreign particles.
9. The oil seals may now be serviced. Note the orienta-
tion of the seals. (Figure 5-18)
Seals
Housing Cover
Figure 5-18, Pinion Shaft Seals
10. Remove the worm cap and motor adapter.Make note
of any installed shims. Capscrews are installed with
Loctite, so use a long-handled wrench to break them
loose. Use a large screwdriver and hammer to sepa-
rate the worm cap from the housing.Note any installed
shims. (Figure 5-19)
Capscrew
Capscrew
O-Ring
O-Ring
Motor Adapter
End Cap
Shim
Shim
Shim
Coupling
Figure 5-19, Worm Cap/Motor Adapter
Equipment damage hazard.
Damage to the worm cap or housing could
reduce machine performance or void the
warranty.
Do not damage the machined surfaces of
the worm cap and housing.
11. The seal in the motor adapter can now be replaced.
(Figure 5-20)
Seal
Motor Adapter
Figure 5-20, Motor Adapter Seal
12. Using a rubber mallet, lightly tap on the extended end
of the worm gear shaft and remove it through the
housing.
Table of contents
Other Allied Systems Lifting System manuals
Popular Lifting System manuals by other brands
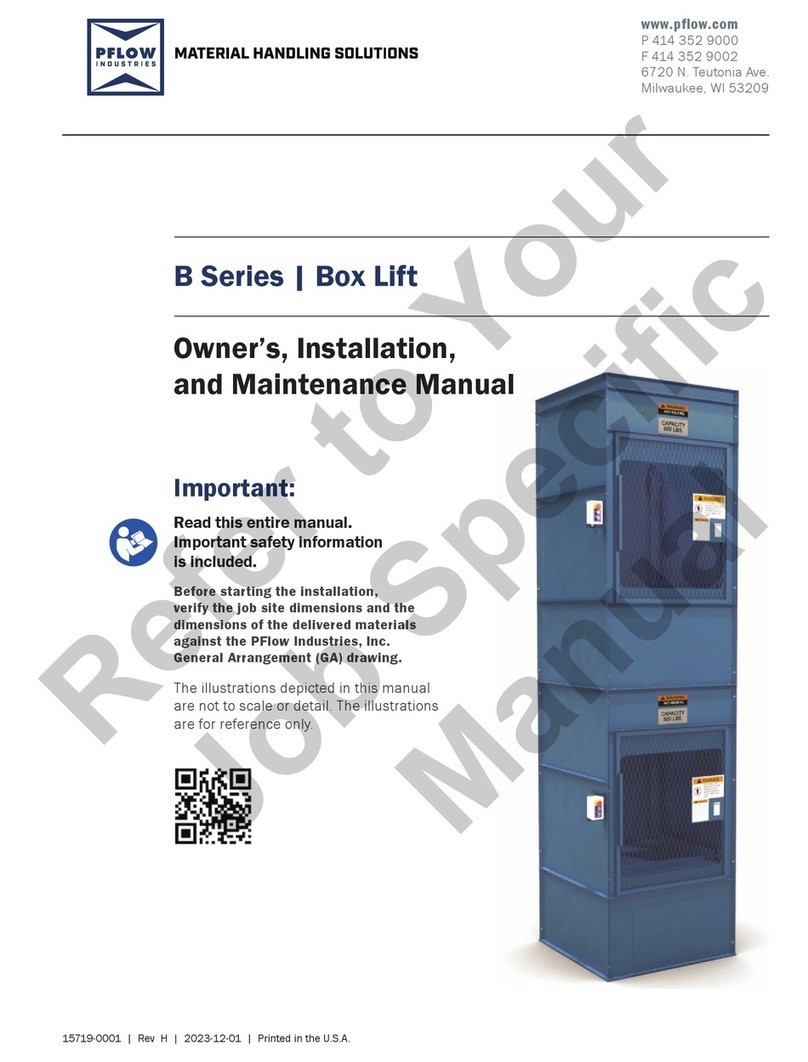
PFlow Industries
PFlow Industries B Series Owner's, Installation and Maintenance Manual
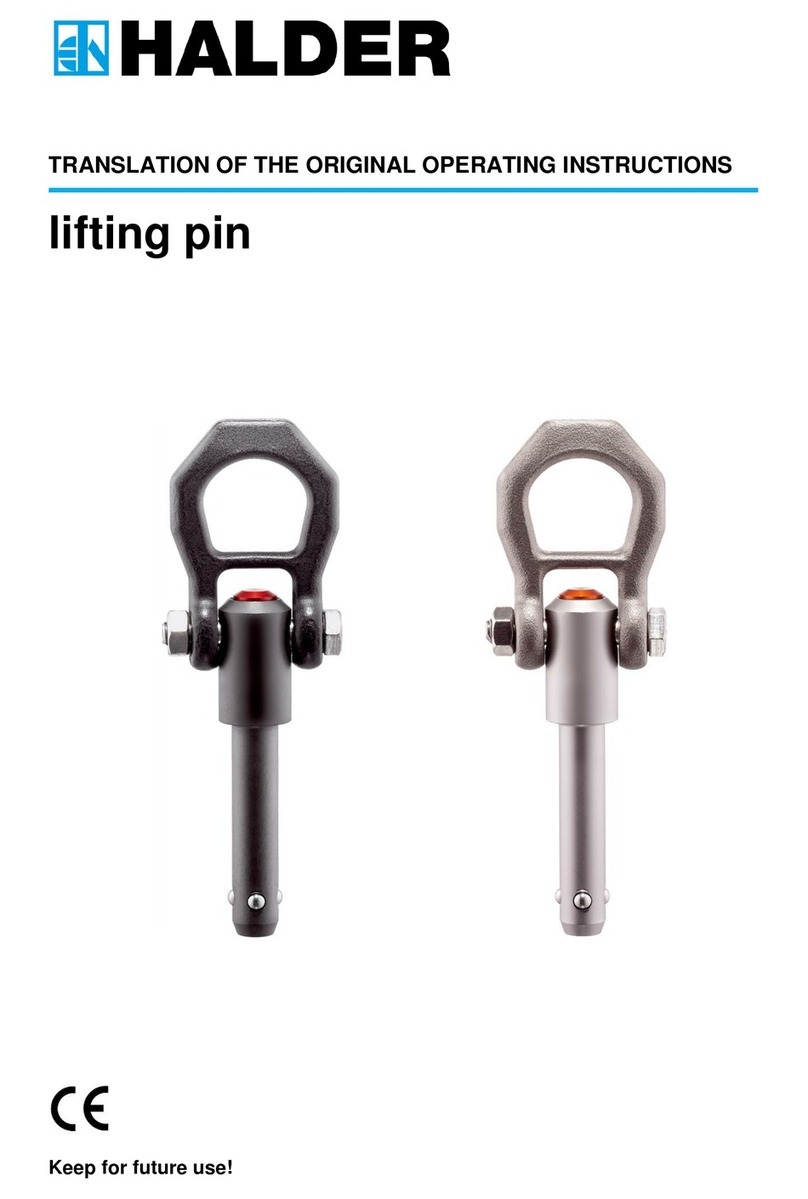
HALDER
HALDER EH 22350 operating instructions

ixtur
ixtur LI-120 user manual
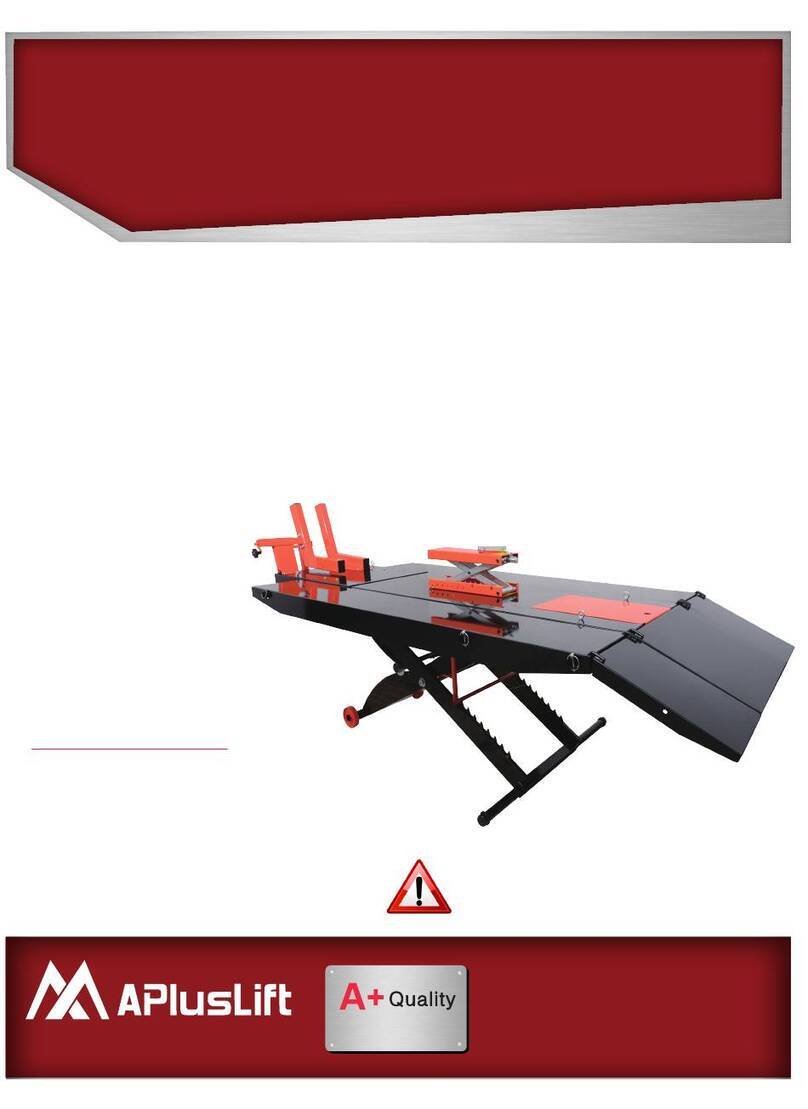
APlusLift
APlusLift MT1500 Installation manual & operation instructions
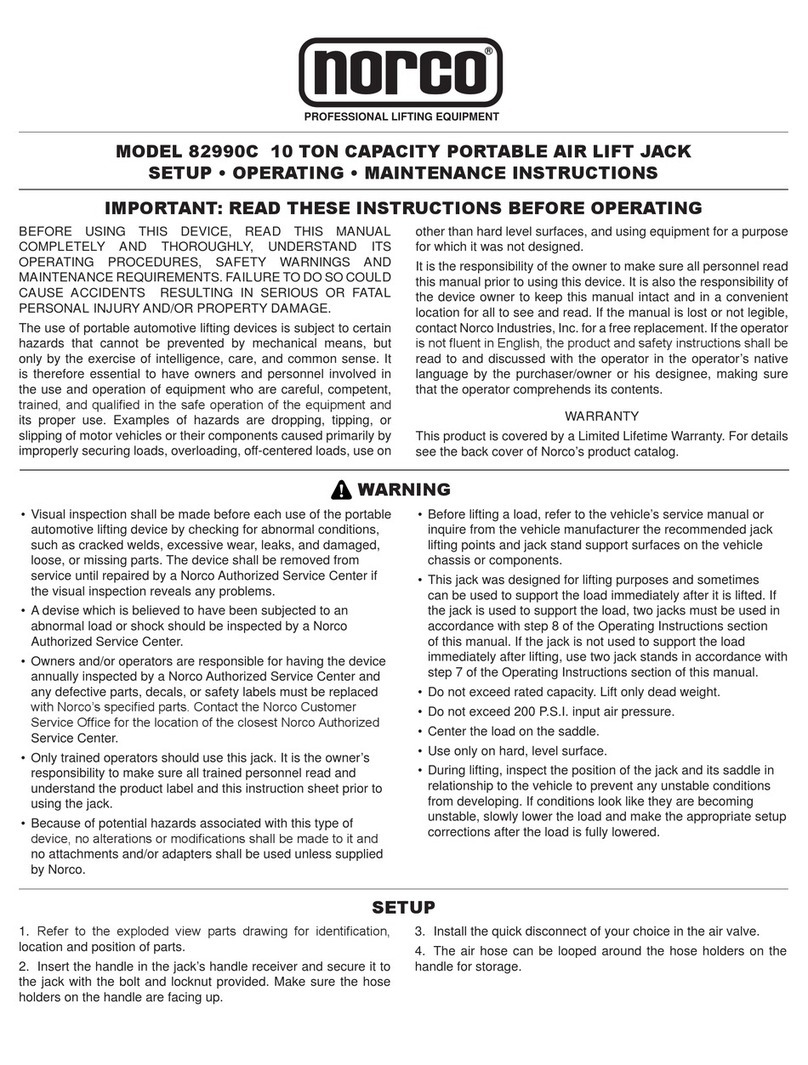
Norco
Norco 82990C Setup, operating, maintenance instructions
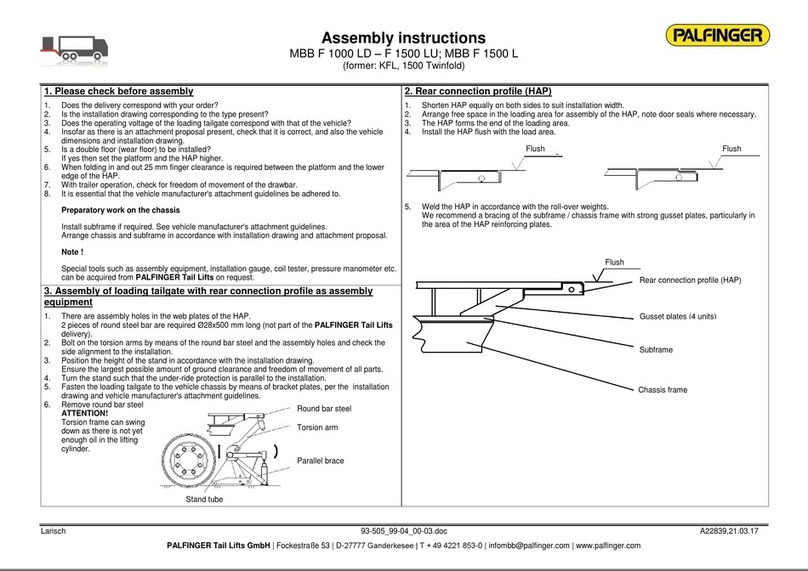
Palfinger
Palfinger MBB F 1000 LD Assembly instructions
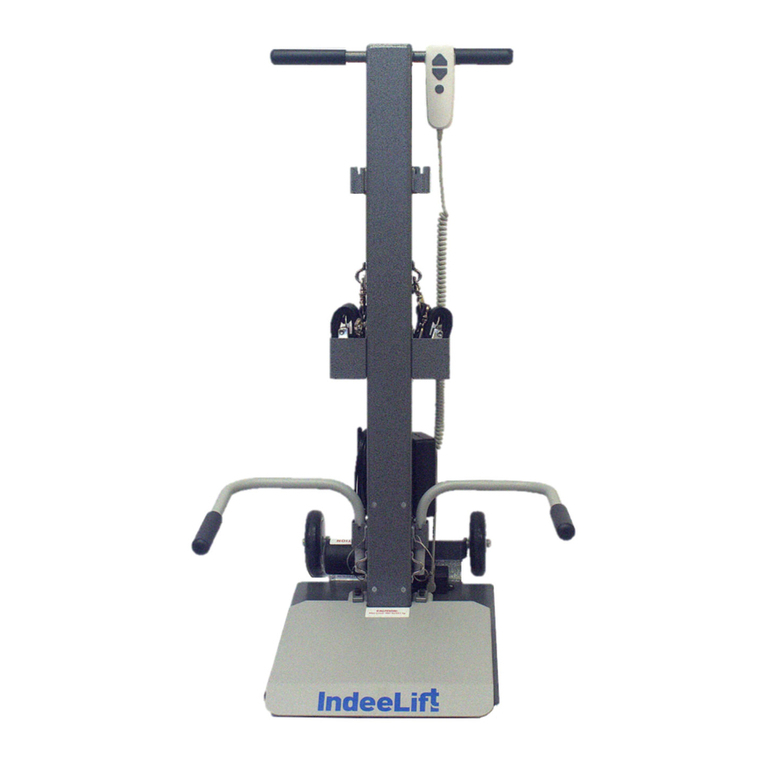
IndeeLift
IndeeLift HFL-400-FTS user manual
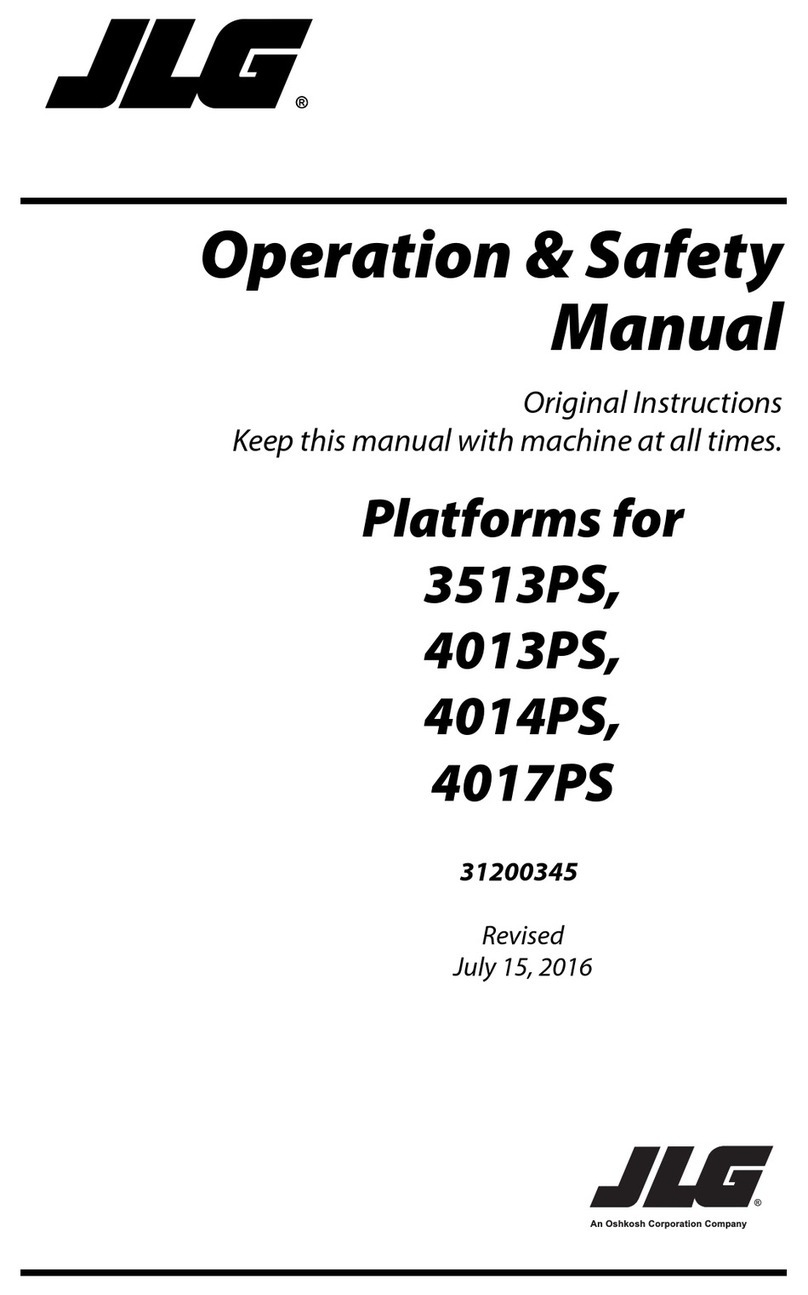
JLG
JLG 3513PS Operation & safety manual
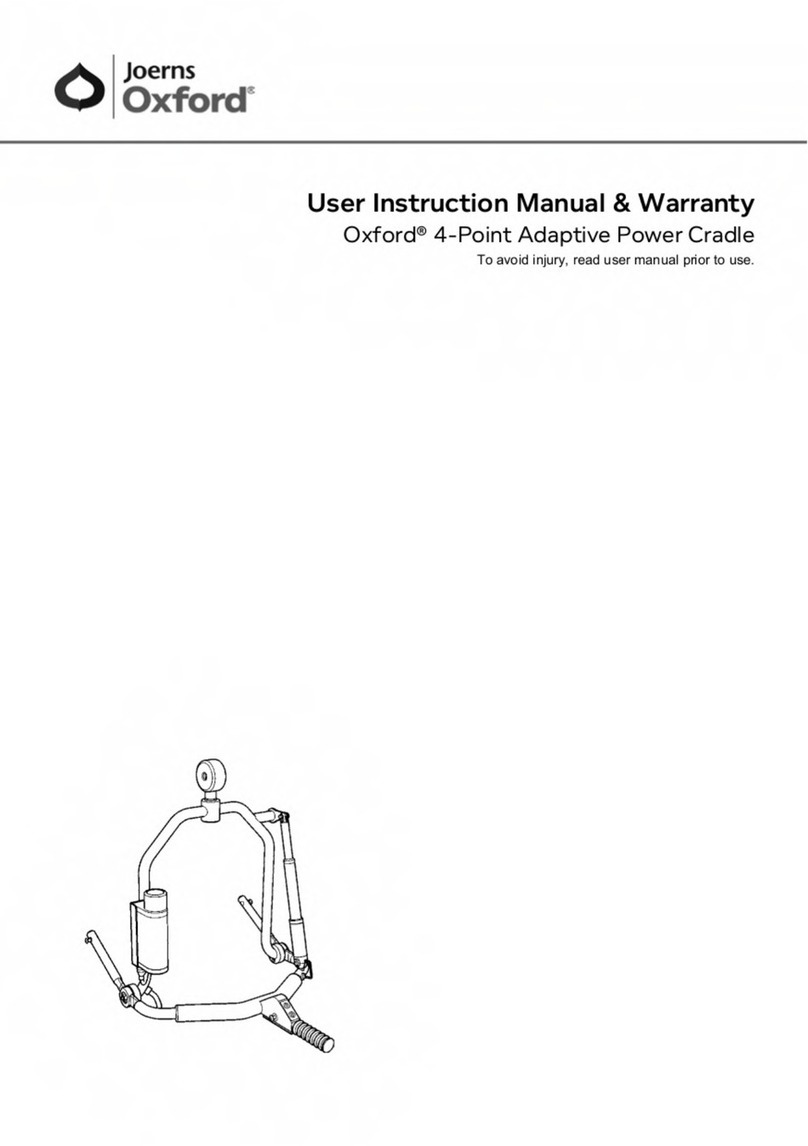
Joerns
Joerns Oxford Adaptive Power Cradle User instruction manual & warranty
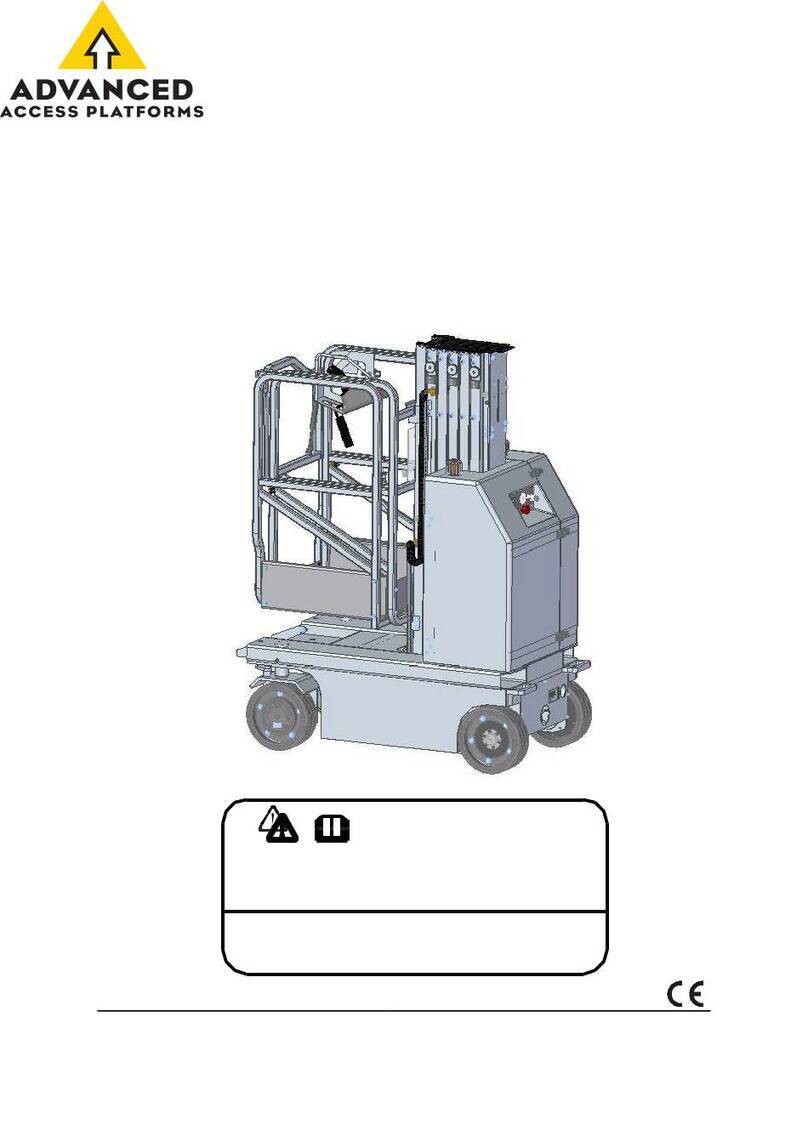
DINGLI
DINGLI AMWP8-1200 operators manual with maintenance information
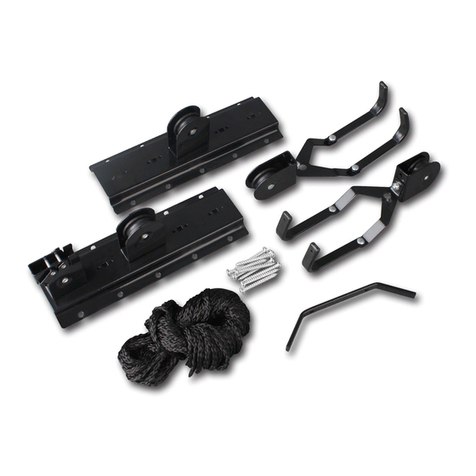
Fieldmann
Fieldmann FDAD 6201 instruction manual
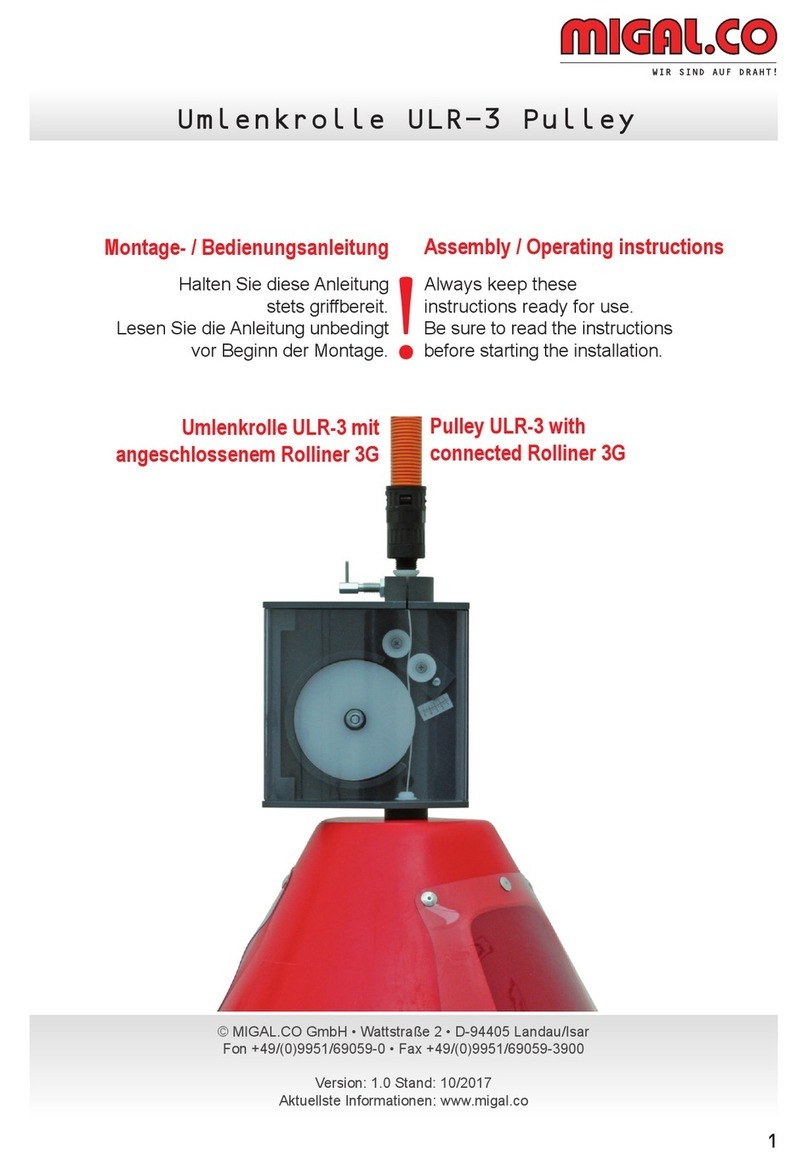
MIGAL.CO
MIGAL.CO ULR-3 operating manual