ALTER SM 1180 Series Specification sheet

SM1180 & TM060
SWITCHING POWER GENERATOR
FOR 6 KW MAGNETRON
SM1180 D for line 3 x 208V
SM1180 T for line 3 x 400V
SM1180 U for line 3 x 480V
TM060: generator (head)
TECHNICAL NOTE
(issue December 2007)

File: SM1180_r9eng - December 2007 - Technical note: SM 1180 & TM 060 page 1 of 35
SM1180 & TM060
CE Declaration of Conformity
Dichiarazione di Conformità CE
Nome del Costruttore: ALTER s.r.l
Manufacturer’s Name:
Indirizzo del Costruttore: Via Curie, 8 - 42100 Reggio Emilia - Italy
Manufacturer’s Address:
Dichiara che il Prodotto:
Declare that the product:
nome del prodotto: SM1180 (alimentatore elettrico) e TM060 (generatore a distanza)
product name: SM1180 (power supply) and TM060 (microwave generator head)
modello: SM1180D.xxx4/54, SM1180T.xxx4/54, SM1180U.xxx4/54,
model: TM060.xxx0, TM060.xxx2
Al quale questa dichiarazione si riferisce è conforme alle seguenti norme:
complies with the following norms:
EN 61010-1: 2001; EN55011: 1999; EN55011/A1: 2000; EN55011/A2: 2003
The “D” version complies also the following EMC (Electromagnetic Compatibility) norms:
IEC 61000-4-34 (voltage dips, short interruptions and voltage variations)*
IEC 61000-4-4 (burst); IEC 61000-4-5 (surge)
I Prodotti sopra descritti sono conformi ai requisiti dela Direttiva di Bassa Tensione 73/23 CEE.
The products listed above comply with the requirements of the Low Voltage Directive 73/23/EEC.
Reggio Emilia, December 2007. Marco Garuti
Presidente C.d.A.
* Note: the conformity to this norm makes it also compliant with the american SEMI F47-0200 (voltage sag) related to equip-
ments for the semiconductor technology.

page 2 of 35 File: SM1180_r9eng - December 2007 - Technical note: SM1180 & TM 060
SM1180 & TM060
File: SM1180_r9eng - December 2007 - Technical note: SM 1180 & TM 060 page 3 of 35
SM1180 & TM060
Rev. Revision note Date File
0 First emission March 1997 SM1180_r0
1 SM1180 version 0, 2 & 3 December 1999 SM1180T3_r1
2 TM060 version 2 & 3 June 2002 SM1180T3_r2eng
3 Deleted TM060 version 3 May 2004 SM1180T3_r3eng
4 Upgraded with SM1180U data October 2004 SM1180_r4eng
5 Upgraded with RD8400 data September 2005 SM1180_r5eng
6 Upgraded with SM1180D data December 2005 SM1180_r6eng
7 IEC 61000 conformity ver. “D” & RoHS conformity June 2006 SM1180_r7eng
8 New version 4 & 54 with separate AUX voltage November 2007 SM1180_r8eng
9 New version 5 & 55 December 2007 SM1180_r9eng

page 2 of 35 File: SM1180_r9eng - December 2007 - Technical note: SM1180 & TM 060
SM1180 & TM060
File: SM1180_r9eng - December 2007 - Technical note: SM 1180 & TM 060 page 3 of 35
SM1180 & TM060
Alter’ policy about Reduction on Hazardous Substances (RoHS) and Waste
Electrical and Electronic Equipment (WEEE)
Law Reference
• Directive 2002/96/EC of European Parliament (WEEE)
• Directive 2002/95/EC of European Parliament (RoHS)
• Decreto Legislativo D.L. n. 151 – 25/07/2005 (WEEE and RoHS)
Starting from September 2005 Alter has set the rule to accept only RoHS compliant components from its Suppliers.
At the present date of 15 May 2006, 90% of components in our stock is RoHS compliant.
The components still not compliant were hold in stock and still used for two reasons:
• there is not the same or equivalent product RoHS compliant, or
• the product is a spare part for equipment produced and put on market before 1st July 2006.
Alter Risk Assessment on RoHS
Of the six substances forbidden from electronic equipment (Lead (Pb), Mercury (Hg), Cadmium (Cd), Hexavalent
Cromium (Cr-VI), Polybrominated biphenyls (PBB), Polybrominated diphenyl ethers (PBDE)) only two are used in
Alter’s current manufacturing process, Pb and Cr-VI, of whose lead is the more important.
Mercury: not present, never used
Cadmium: was present as part of alloy on relay contact. We are using relay RoHS compliant now.
Never used as anti-corrosion coating on metal parts.
Pbb & Pbde: may be present in some cables and insulating material in the past.
We are using only RoHS compliant suppliers and products now.
Cr-VI: is used as anticorrosion layer on aluminium part. We are evaluating alternative coating. It is still
present within the limit of 0,1% in weight as set by Directive.
Lead: it is largely used as an alloy for welding of electronic parts. We are already using alternative alloys
lead-free, but as we still have components that cannot be soldered without lead, we have to use some
lead-alloy for welding. At present there are still general concerns about reliability over the time of a
soldered electronic joint done without traditional Sn/Pb alloy. We are putting any effort on reducing
lead weight within 0,1% of products as set by Directive.
Important information to User about disposal, recycling, reuse of this electronic
equipment at the end of its useful life (WEEE Directive).
According to Annex IA and IB of EC Directive 200/96/EC this equipment is not included on the list of categories/
products covered by the Directive (as a matter of fact it does not perform a function alone, must be included into a
larger process equipment and it’s for stationary use).
Nevertheless we invite the User to respect the following Directive rules:
• this WEEE is not a municipal waste and should be collected separately according to rules of your country
• the symbol means that this WEEE cannot be disposal in the same place and in the same way like
municipal waste
• this WEEE may present risk for environment as well as for person in case of disposal in unauthorized
place, due to content of hazardous substances
• for disposal of this WEEE in unauthorized area the User may be charged with a ne or prosecuted by
law.

page 4 of 35 File: SM1180_r9eng - December 2007 - Technical note: SM1180 & TM 060
SM1180 & TM060
File: SM1180_r9eng - December 2007 - Technical note: SM 1180 & TM 060 page 5 of 35
SM1180 & TM060
Contents
CE Declaration of Conformity 1
General Informations 4
How to order 33
Technical assistance 33
Warnings 4
SM 1180
Alarm codes table 28
Components lists 17, 18
Connectors and fuses specications 9
Control and IGBT driver board M216 27
Environmental conditions 8
Equipment installation 8
Equipment maintenance
Cleaning 16
Fuses replacement 16
Equipment operation
Alarms coding 12
Alarms table 12
Buttons meaning & programm. procedures (Master CPU) 12
Buttons meaning & programm. procedures (Slave CPU) 13
Display and LED meaning 11
Functions table (Master CPU) 14
Functions table (Slave CPU) 15
Power-up procedure 10
Operating controls 10
Visualization mode of the lower display (Slave CPU) 11
Visualization mode of the upper display (Master CPU) 11
Equipment Ratings 7
General Description 5
Handling instructions 9
Handling Warnings 5
Physical characteristics 8
Pin out of Connector #1 SM1180D v.4/5 20
Pin out of Connector #1 SM1180T/U v.4/5 21
Pin out of Connector #1 & #7 SM1180D v.54/55 22
Pin out of Connector #1 & #7 SM1180T/U v.54/55 23
Pin out of Connector #2 24
Pin out of Connectors #3 & #5 25
Pin out of Connectors #4 using RD8400Ax 26
RoHS conformity 3
Wiring example 31
Wiring instructions 9
TM 060
Assembling example with circulator 32
General description 29
Physical specications 29
Wiring example 31
Appendix
POWER SENSOR RD8400A
General Informations
This equipment satisfy the European Standard EN 61010-
1 (=CEI 66-5) (=IEC 1010-1) approved by CENELEC on
9/3/1993.
With reference to EN 61010-1 standard, note:
this appliance must be installed and serviced only by qualied
personnel.
The appliance must only be used by persons acquainted with
the regulations covering the application.
Note about EMC regulation: the generic emission standard
EN50081-2 (title: Electromagnetic compatibility - Generic
emission standard - Part 2: Industrial environment) sets that
“Where a relevant dedicated product or product-family EMC
emission standard exists, it shall take precedence over all
aspects of this generic standard”.
The equipments described in this manual have been classied
as industrial, scientic and medical (ISM) radio-frequency
equipments and the related standard for the emission is the
EN55011 (=CEI110-6) (title: Limits and methods of measure-
ment of radio disturbance characteristics of ISM equipment.)
With reference to EN55011 standard, this equipment is inclu-
ded into Group 2 (Microwave generators, Thyristor command
equipment, Welding equipment, Induction heating equipment
or machine, Microwave industrial oven, etc.), Class A (indu-
strial environment): for this reason this equipment shall not
be used in the residential, commercial and light-industrial
environment.
The SM1180 complies with the limits of radio disturbance
characteristic of a Group2, Class A equipments as stated by
EN55011.
Copy of the tests performed may be sent on request. Be aware
those tests cannot be used as a conformity certicate of the
user’s nal equipment.
WARNINGS
The SM1180 is powered by AC main line and has high
voltage output: read carefully this manual before using. Be
sure of correct connections and use.
Failure to comply with the instructions enclosed in this
manual may involve considerable risks for the staff respon-
sible for checking and using the equipment, as well as the
risk of general malfunctions of the equipment itself.

page 4 of 35 File: SM1180_r9eng - December 2007 - Technical note: SM1180 & TM 060
SM1180 & TM060
File: SM1180_r9eng - December 2007 - Technical note: SM 1180 & TM 060 page 5 of 35
SM1180 & TM060
Handling Warnings
The SM1180 has two handles on the front panel to help
unpacking and handling operations: never use only the
handles to lift the equipment but support the weight with
an appropriate base on bottom!
The handles do not withstand the off-center weight of the
equipment
(SM1180T: 36.5 kg = 80 lbs, SM1180D/U: 40 kg = 87 lbs).
General Description
The SM1180 is able to supply the power required by a magne-
tron with power up to 6 kW (which correspond to 1100 mA
of anodic current), meeting the specications set by the tube
manufacturer.
This manual describes the features of the following:
- version 4: standard version for YJ1600 magnetron
- version 5: standard version for H3881 magnetron
- version 54: special version with separate aux voltage and
magnetron YJ1600
- version 55: special version with separate aux voltage and
magnetron H3881
The description apply to any versions unless specied diffe-
rently.
The power output can be regulated continuously using an
external analogue signal or the panel potentiometer where
provided.
The power supply is built in a self-ventilated 19” wide rack,
7HE high, with a front panel comprising:
-a 4 digit display (upper) showing a working parameter, i.e. the
output power, or the alarms codes
-a 4 digit display (lower) showing the reverse power (if the
necessary external accessories are provided)
-several signalling LED for working conditions
- inlet air lter
The power supply is designed to guarantee stable, correct and
safe operation, and offers the following special features:
a) all the versions has the option to be driven with a reference
signal 0-10 V (or 0-5 V or 0-20 mA), while into versions 2
and 3 may be used also the front potentiometer.
b) it is equipped with a circuit capable of detecting the over-
voltage on the magnetron (“moding”, detecting operation
at frequencies other than the normal operating frequency or
damage or end of the magnetron life).
The circuit accepts a short period of overvoltage (about 2
seconds) in the switch-on phase, this is normal, especially if
the magnetron reaches the end of its life or the lament power
supply voltage is low.
The circuit also ensures that the power supply is switched
off if the high voltage cable is disconnected, or if the heating
lament fails.
c) it has a circuit capable of detecting an earth current on the
anode circuit, super imposing the normal current circulating in
the magnetron (which returns to earth).
The circuit can pick up current from a resistance of 5 Kohm,
in parallel to the magnetron, irrespective of the current circu-
lating.
The circuit also intervenes in case the high voltage short cir-
cuits to earth, or there is a reduction in the working voltage of
the magnetron.

page 6 of 35 File: SM1180_r9eng - December 2007 - Technical note: SM1180 & TM 060
SM1180 & TM060
File: SM1180_r9eng - December 2007 - Technical note: SM 1180 & TM 060 page 7 of 35
SM1180 & TM060
The SM1180 has been developed to power and monitor our
remotable microwave head type TM060.
The SM1180 power supply may be used also to power
microwave generators (heads) developed by others manufactu-
rers under condition that they are electrically compatible. See
the electrical specications of the unit on the next pages.
The reduced height of the rack (only 7HE, corresponding to
310 mm) allows to use small boards, even in big plant: i.e. in a
standard board with an height of 2 meters, arranged to receive
19” racks, up to 5 SM1180 units may be housed.
The user must provide a proper cooling ow: the cooling air
enter into the unit from the front panel, it passes through the
internal circuits and components, then it goes out from the
rear panel.
The intake air ow is approx. 200 m³/h.
The rear panel comprises the following:
- a 7 pins socket for main supply (Conn. #1)
- the fuses holders
- a 14 pins socket for the signals (Conn. #2)
- a 7 pins socket to power the remote microwave head (Conn. #3)
- a 9 pins socket for the signals coming from the remote
microwave head (Conn. #4)
- a 4 pins socket for the high voltage output (Conn. #5)
- a 2 pins terminal to allow remote head “INTERLOCK” func-
tion (Conn. #6);
if you don’t use this feature then let the jumper between the 2 pins
unchanged (= connected)
- a 2 position key switch to enable the panel potentiometer;
pos. 0 = potentiometer disabled; pos. 1 = potentiometer enabled
- a “READY” contact (closed when the unit is ready to gene-
rate anodic current).
- the outlet of the cooling air.
The rear panel of the version 54 and 55 comprises also the
following:
- a 3 pins socket to power the auxiliary section (Conn. #7)
vers. 4/5
vers. 54/55

page 6 of 35 File: SM1180_r9eng - December 2007 - Technical note: SM1180 & TM 060
SM1180 & TM060
File: SM1180_r9eng - December 2007 - Technical note: SM 1180 & TM 060 page 7 of 35
SM1180 & TM060
Equipment Ratings
any versions
SM1180T SM1180U SM1180D
Main supply (50/60 Hz): 3x400 V 3x480 V 3x208 V
Minimum main voltage: 3x360 V 3x435 V 3x187 V
Maximum main voltage: 3x440 V 3x525 V 3x229 V
Form factor: 1.22 1.22 1.08
Intake current (nominal): 18,5 Arms/phase 14,5 Arms/phase 30 Arms/phase
Max anodic output current: 1100 mA @ 7800 V for all models (at the max ambient temperature of 40°C)
Output power: 8600 W for all models
Efciency: 91% for all models
Specs of version 54 and 55 only:
The connector #7 has been added, on version 54/55 only, to
power the control section of the psu, in order to have the latter
separated from main line power (provided through Conn #1)
The Conn #7 powers the remote head (fan, lament transfor-
mer, lamp) and the internal fan of the psu.
The user must provide an external switch to power/unpower
the control section of the SM1180 vers. 54/55.
Two 6A fuses (F1 and F2) are provided to protect the 230V
(nominal) circuit.
A max current of 1.4 Arms (@ 230V) must be provided in
normal operation, while 3.2 Arms is the max surge inrush
current, due to initial cold lament heating, every time the
lament is switched off (i.e. by removing the power input, or
by interlock chain opening).
The main line voltage can still be switched ON and OFF
through the front panel breaker.
WARNING: to avoid alarms it must be adopted the correct
sequence of switch-on
Enable signal ON
OFF
Power section ON
OFF
Control section ON
OFF
Correct sequence:
1) Enable signal: OFF
2) Control section: POWER-ON
3) Preheating time: 30 seconds
4) Power section: POWER-ON
5) Enable signal: ON
No problem arises if the Power section is switched Off (or
ON) while the Enable signal is OFF, but powering down the
Power section while Enable is ONleads to A_4 alarm, after
10 seconds, as the system doesn’t sense the power anode
current.
Also powering ON together the Power section and the
Enable can cause an A_2 alarm
30 sec 2 sec
Timing sequence for vers. 54/55 only

page 8 of 35 File: SM1180_r9eng - December 2007 - Technical note: SM1180 & TM 060
SM1180 & TM060
File: SM1180_r9eng - December 2007 - Technical note: SM 1180 & TM 060 page 9 of 35
SM1180 & TM060
Reference signal to adjust power:
a) 0-5 Vdc (Z=20 Kohm)
b)0-10 Vdc (Z=10 Kohm)
(standard)
c)0-20 mA (Z=250 ohm)
Filament preheating time: 12 seconds
Monitoring signal of the anodic current: 1V = 200 mA
(Z=250 ohm)
Management of alarm situations: a) by internal alarm relay,
contact load: max 130 V 0.5A.
b) by numeric code of the
alarm displayed on upper
display (see the table “Display
functions” on next pages).
Working mode of the alarm relay contact:
a) when the unit is “OFF”:
the contact is open
b) when the unit is “ON” and
no alarm conditions:
the contact is closed
c) when the unit is “ON” and
an alarm condition is present:
the contact is open.
Working mode of the READY relay:
a) when the unit is “OFF”:
the contact is open;
b) when the unit is “ON” and
the lament is not ready or
there is an alarm condition:the
contact is open;
c) when the unit is “ON”, the
lament is ready and there isn’t
alarm: the contact is closed.
Ripple on output current: 3% under any conditions.
Automatic shut-off in case of: a) shortcircuit to hearth
b)H.V. connection opened
c) lament cold or broken
d)internal overtempera-
ture of the SM1180
Delay of reference signal vs output power: 40 msec when
increasing, 10 msec when
decreasing.
Environmental conditions
Use: indoor use only
Altitude: tested up to 2,000 m (approx
6,000 feet)
Temperature: 5°C to 40°C (41°F to 104°F)
Relative Humidity: 80% for temperature up
31°C(88°F), decreasing
linearly to 50%
RH at 40°C (104°F)
Pollution degree: 2, according IEC664
Physical characteristics
Standard dimensions: 19” x 7HE (482x311 mm)
Rack total width: 450 mm
Rack total height: 305 mm
Rack depth (without handles + plugs):540 mm
Housing board depth (minimum): 600 mm
Total weight: SM1180T= 36.5 kg (80 lbs),
SM1180D/U= 40 kg (87 lbs)
Intake air ow: approx 200 m³/h
Cleaning of air lter: at least every 200 hours in a normal
industrial environment or more frequently for dusty envi-
ronment. Before removing the lter switch-off the unit!To
remove the lter simply raise the front grid with a tool and
pull.
Equipment installation
The SM1180 cannot operate on a bench: it must be installed
into a proper cabinet like a commercial 19” standard enclo-
sure.
The equipment cannot operate cantilevered, it must be safely
xed inside a cabinet by means of screws on the front panel
(which is provided with 4 holes) and supported by means of a
proper frame on the bottom.
Usually two “L” shaped supports on each side of the equip-
ment are suitable for that purpose.
The rear side of the equipment must be protected by a xed
panel which can be removed only by means of tools or by a
door with security micro-switch: when the door is opened the
micro-switch must shut-off at least the enabling signal of the
equipment or the main line. This safety precautions must be
taken to avoid operations on rear fuses or on connectors while
the unit is still powered.
Special attention must be taken on designing the cooling air
ow in case of stacking several units into the same cabinet.

page 8 of 35 File: SM1180_r9eng - December 2007 - Technical note: SM1180 & TM 060
SM1180 & TM060
File: SM1180_r9eng - December 2007 - Technical note: SM 1180 & TM 060 page 9 of 35
SM1180 & TM060
Note that each equipment has its own fan which intake approx
200 m³/h: the outlet of the exhaust air is on rear side of the
equipment.
When designing a board to house several units we recommend
to adopt the following design criteria:
1. use a standard 19” wide enclosure with a minimum depth of
600 mm (24”);
2. allow free intake of the cooling air from the front of the
cabinet;
3. in case of ambient air with high degree of dust and moisture,
you need a deeper cabinet (at least 32”) to assemble the units in
the middle of cabinet and install a closed door. In this way you are
providing two vertical ducts (inside cabinet) with exit from top or
bottom; the front one is for air inlet, the rear one for exhaust air;
4. provide a separation between the air intake duct and the air
outlets, in order to avoid air-recyrculating;
Consider a ow rate of 200 m³/h for each power supply.
Connectors and fuses specications
The following specications refer to panel connectors and
installed fuses. Please note that all the connector plugs must be
ordered separately with the p/n 44/SET1180 or 44/SET1180D.
The set includes also the single pins and spare fuses.
Handling instructions
The equipment weight is 36.5 kg (80 lbs) for SM1180T and
40 kg (87 lbs) for SM1180D/U. Always lift from the bottom
and use an adeguate rugged support to avoid personal injury
and damage to equipment itself.
In case of shipping package with wooden case and a proper
ller: movement of the equipment inside the package must be
avoided.
Warning for handling: use handles only for helping during
installation. Never use handles to lift the rack: the handles
don’t withstand the off-center weight of the rack!
To lift always lean the rack over a proper supporting base.
Wiring instructions
The SM1180 must be installed and serviced only by quali-
ed personnel acquainted with the regulations covering the
application. For safety operations the following rules must be
adopted:
I) the equipment must be grounded through the connector #1
using pin 4 (see the wiring diagrams at page 20, 21, 22, 23);
Panel
connector #1
Panel
connector #2
Panel
connector
#3
Panel
connector #4
Panel
connector #5
Panel
connector #6
Panel
connector #7
Function Main line input Signals Main power to
head
Signals from
head
H.V. output Interlock Power Control
section
Funzione
Type 7 pins 14 pins 7 pins 9 pins 4 pins female 2 pins 3 pins Tipo
Model AMP CPC3 AMP CPC1 AMP CPC1 AMP CPC1 AMP LGH PHOENIX AMP CPC3 Modello
Socket P/N 206137-1 206043-1 211398-1 206705-1 863017-3 MSTB-2,5/2-
STF-5,08
206036-2 P/N Spina
Contact P/N 66261-4
or 193991-4
163088-1 163088-1 163088-1 DKF-MSTB-2,5/
2-GF5,08
066261-4 P/N Contatto
Fuses specs Aux fuses
(2x)
Fusibili
Type Fast Tipo
Model Ceramic Modello
Dimensions 10x38mm
6 A Dimensioni

page 10 of 35 File: SM1180_r9eng - December 2007 - Technical note: SM1180 & TM 060
SM1180 & TM060
File: SM1180_r9eng - December 2007 - Technical note: SM 1180 & TM 060 page 11 of 35
SM1180 & TM060
II) connect the ground screw on panel rear (indicated by
“ground” symbol) directly to the remote microwave head by a
separate yellow/green wire gauge 6 mm²;
III) the three phases main supply, type phase/phase/phase
/ground, must be provided through connector #1: connect
phases to pin 2, 3 and 7, ground to pin 4:
the connector’s pins can house wires with gauge up to 4 mm²
(vers. T & U), 10 mm² (vers. D); the wires lenght shall be
according to current capability of the wires section;
IV) the connector #2 brings the input/output signals to the
equipment. Refer to wiring diagram at page 24;
V) the connector #3 provides the power supply for the la-
ment transformer (usually located near the magnetron) and the
magnetron fan. Refer to wiring diagram at page 25;
VI) the connector #5 is the high voltage output and must be
connected to magnetron’s cathode. The voltage value is near
7.8 kV .Use a proper insulated cable with working voltage >10
kVdc and minimum gauge of 0.25 mm²; protect the wire with
sheating (armoured if appropriate) with ext diam. 13 mm max.
Assemble the wire into plug according to AMP’s instructions:
a resin epoxy lling is required. Alter may supply the HV
cable with lenght on request.
VII) the connector #6 allows the use of the remote “INTER-
LOCK” function: if not requested connect togheter the 2
terminals. Look diagram at page 26.
VIII) the connector #7, available only on version 54/55, provi-
des the power for control section.
See the relevant chapter “Specs of version 54/55” at page 22,
23.
IX) the user must provide external circuit breaker . We also
suggest to install a thermal cut-off device, to protect the
SM1180 from short-citcuit and thermal runaway with breaking
capacity > 50 kA: note the unit has a magnetic circuit breaker
with a breaking capacity of 15 kA;
X) these external protection devices must allow to switch-off
the main line for maintenance operations;
XI) the external circuit breaker must be a three poles breaker
and must comply the norm EN61010-1;
XII) the external circuit breaker must be in close proximity to
the SM1180 and within easy reach of the operator;
XIII) the external circuit breaker must be marked as the
disconnecting device for the SM1180;
XIV) the connector #1 must never be used as a switch-off
device.
Failure to comply with these instructions may involve con-
siderable risks for the staff responsible for checking and
using the equipment, as well as the risk of general malfunc-
tions of the equipment itself.
Equipment operation
Power-up procedure
To power-up the equipment set the front panel breaker in
“ON” position. In case the breaker trigs to OFF then wait at
least ten seconds before setting it ON again.
This rule must be valid even in case the power is given
by an external contactor (and the panel breaker is always
left in ON state): the OFF state, between two con-
secutive ON state, must last ten seconds minimum.
At power on the unit starts the lament preheating cycle, :
during preheating the “MAGNETRON ON” led ashes twice
per second. At the end of preheating the unit is ready to start
microwave emission on command as described in the next
paragraph: the “MAGNETRON ON” led ashes 5 times per
second and the “READY” contact is closed.
Operating control
The SM1180 operation is controlled by an external command
at +24 Vdc (nominal): the voltage range may vary from 8 to 30
Vdc, common to ground, Z=2.5 kOhm.
The command signal must be wired to pin 3 of the connector
#2: if the user doesn’t have a suitable voltage generator for this
signal, then the equipment’s internal voltage generator can be
used: a voltage signal is available at pin 4 of connector #2. In
this case the user must provide an external contact closing the
circuit between pin 4 and pin 3 to enable the equipment opera-
tion. Refer to wiring diagram at page 24.
When the command is ON and the followings condition are
satised:
-the SM1180 has been properly connected to a remote
microwave head,
- there are not alarms conditions,
- the “interlock” loop is closed,
- the lament preheating has been completed, then
the SM1180 reaches the preset value of anodic current and
power-up the remote microwave head.

page 10 of 35 File: SM1180_r9eng - December 2007 - Technical note: SM1180 & TM 060
SM1180 & TM060
File: SM1180_r9eng - December 2007 - Technical note: SM 1180 & TM 060 page 11 of 35
SM1180 & TM060
Display and LED meaning.
On the front panel there are 2 digital displays, one upon the
other, and on one side there are the status leds. The upper
display and leds are controlled by the main CPU (or “master”
CPU), the lower display is controlled by the secondary CPU
(or “slave” CPU).
The panel potentiometer must be enabled by means of the key
switch located on the rear of the unit: the switch avoid the
presence of both signals at the same time.
Led meaning:
POWER ON: ON when main breaker is ON and
main line present
MAGNETRON ON: FLASH twice per second during la-
ment preheating.
FLASH 5 times per second: the la-
ment is preheated, the unit is ready
ON with Ia> 50 mA.
OVERTEMP.: OFF with no overtemperature alarm.
FLASHING in case of overtemp.
inside the rack.
ON in case of magnetron overtempe-
rature.
WATCH DOG: OFF with no alarms
FLASHING in case of arc detection
(an electrical arc occured inside the
waveguide launcher and has been
detected by the arc detector)
ON : shortcircuit present.
OVERVOLTAGE: OFF with no alarms
ON : magnetron overvoltage (moding)
POWER ON (slave): ON when main line is present
MAX REVERSE: ON when the signal of the reverse
power exceeds its threshold .
Visualization modes of the upper display
(CPUMaster)
This display usually shows one of the followings (see the
function table): - anodic current (in mA), or
- anodic voltage (in Vx10), or
- magnetron power (in Wx10)
with the following exceptions:
- when you switch on: all the segments are shortly
lighted up, then appear the
word “mast” for a short time.
- during an alarm condition:
shows an alarm code (A...)
(see the alarms code table)
Visualization mode of the lower display
(CPU Slave)
This display shows the reected r.f. power (in Wx10) with the
following exception:
- when you switch on: all the segments are shortly
lighted up, then appear the
word “slav” for a short time.

page 12 of 35 File: SM1180_r9eng - December 2007 - Technical note: SM1180 & TM 060
SM1180 & TM060
File: SM1180_r9eng - December 2007 - Technical note: SM 1180 & TM 060 page 13 of 35
SM1180 & TM060
Alarms coding
A--1: magnetron overtemperature
A--2: rack overtemperature
A--3: arc detection
A--4: overcurrent/undercurrent
A--5: overvoltage
A--6: head sensors (water switch or air switch or
cover sw.)
A--7: reverse power exceeding the threshold
Warning: in case of alarm the unit shuts-off the output. To
restart the user must remove the alarm condition and must
execute the reset procedure which starts a lament preheating
cycle again.
Reset procedure after alarm condition:
I) with the unit powered but not enabled to generate
microwave (the “enabling command” was OFF): hold down
for 1 second both the “+” and “-” buttons of the upper display
(master CPU). To do a remote reset procedure set ON and
then OFF: keep OFF the enabling command for at least 2
seconds;
II) the unit was generating microwave: keep OFF the enabling
command at least 2 seconds.
When the alarm condition is removed the alarm code is hold
on display till the reset procedure is executed, then the display
shows the current parameters.
The code of the alarms are present also on the signal connector
#2 as a 3 bit binary numbers as shown in the “alarms table”.
ALARMS TABLE
The 3 bit binary code is wired as follow:
- bit n° 1 (LSB): pin n°11 of the connector #2
- bit n° 2: pin n°12 “ “ “
- bit n° 3 (MSB): pin n°13 “ “ “
Buttons meaning and programming procedures
(Master CPU):
During normal operation the display shows a user dened
parameter. In addition the on-board software allows the access
to several internal parameters, such as alarm threshold and
linearization parameters, already set in factory during nal
tests.
These parameters are recorded into 28 functions, shown on the
display with the format Fnn: nn is the function number from 0
to 27.
I.e. the function F_0 allows to select which type of value is
displayed during normal operation (anodic current, or anodic
voltage or magnetron power).
For all these datas the CPU does an analog reading and then
use a calculated value with respect to a line dened during
calibration on factory.
As known to dene a line it needs two points, the rst at low
value, the last at higher value.
The “X” co-ordinates, which refer to analog reading, are self-
stored by means of a simple command, while the “Y” co-ordi-
nates, which refer to the value you want to display, must be
stored by User.
For more informations pls ask detailed informations about
“Calibration procedure of the SM1180”.
Code
displayed Meanings Pin n° 13 (MSB) Pin n° 12 Pin n°11 (LSB)
000 Ok 0 0 0
A__1 Magnetron
overtemperature
0 0 1
A__2 Internal overtemperature 0 1 0
A__3 Arc detector 0 1 1
A__4 Overcurrent/Undercurrent 1 0 0
A__5 Overvoltage 1 0 1
A__6 Head sensors 1 1 0
A__7 Reverse power limit 1 1 1
Codice allarme Signicato Pin n° 13 (MSB) Pin n° 12 Pin n°11 (LSB)

page 12 of 35 File: SM1180_r9eng - December 2007 - Technical note: SM1180 & TM 060
SM1180 & TM060
File: SM1180_r9eng - December 2007 - Technical note: SM 1180 & TM 060 page 13 of 35
SM1180 & TM060
On the right side of the display are located the 3 push-buttons:
“F” to enter into programming or select a function or
conrm/exit;
“+” to increase the displayed value;
“-” to decrease the displayed value.
Note: in the next paragraph the words:
“current page” means the usual parameter and / or infor-
mation displayed during working mode;
“F_nn” means the function # nn displayed with that
format.
Viewing and modifying parameters:
(From current page of working mode)
I) Press F and hold for 2 seconds: you enter in programming
mode; the display will show F_nn.
II) Press + o - to increase or decrease nn and choose the func-
tion F_1.
III) Press again F to see the value of the parameter which is
set to 0: press + to set the value to 1.
From this point it is enabled the programming mode.
IV) Press again F to go back one step and the display will
show F__1: you are now into programming mode. Press + or
- to modify nn (function selection).
V) Press F to see the value of the function: now using + and
- you may modify this value.
VI) Press again F to go back one step: the display will show
F_nn (you are now at step “II”).
VII) Press F and hold for 2 second to exit from the program-
ming mode and to go to current page. You may exit at any
time: if none value has been modied, the previous values are
actual, otherwise the new ones are stored.
VIII) It is provided a timeout to exit from any situation: after
10 seconds without modications you exit from programming
mode and come back to current page.
Every time you go back to current page you also leave the
programming mode: F__1 is automatically set to 0.
Buttons meaning and programming procedures
(Slave CPU):
To modify the internal parameters follow the same procedure
described for the Master CPU.
Main parameters of the Slave CPU:
The value in F 7 shows the alarm threshold of the Reverse
Power (value: Watt x 10).
It is possible to x this threshold to the preferred value, also
over the value of the max forward power: in this case the alarm
will not enter in function.
The value in F 19 shows the level of the Reverse Power with a
10Vdc input signal (value: Watt x 10).
If the value of the maximum Reverse Power is measured with
an output signal different from 10V it is possible to change
with this value (F 19) the Slave CPU visualization.
Default values:
F7 (Reverse Power alarm threshold) = 300 means 3000W
F19 (max power with 10Vdc input) = 600 means 6000W

page 14 of 35 File: SM1180_r9eng - December 2007 - Technical note: SM1180 & TM 060
SM1180 & TM060
File: SM1180_r9eng - December 2007 - Technical note: SM 1180 & TM 060 page 15 of 35
SM1180 & TM060
Functions table of Master CPU
F_nn Default
Value Parameter Comment
F_00
0 Anodic current (mA) Values >9999 =values/10 (format:
nnn-)
1 Anodic voltage (V) Value showed=value/10
2 Magnetron power (W), calculated value “
3 Working hours counter Values >9999 displayed as hours
* 100, with last digit equal to _
F_01
0 Set display mode Standard
1 Set programming mode Access to function F>1
F_02 50 Anodic undercurrent threshold (mA) It affects led “MAGNETRON ON”
F_03 till
F_12 -- Not used
F_13 -- Internal use, don’t modify
F_14 -- Internal use, don’t modify
F_15 -- Not used
F_16 X1 Coordinate for linearization of “la” It affects the “la”
value displayed
F_17 Y1 Coordinate for linearization of “la” “
F_18 X2 Coordinate for linearization of “la” “
F_19 Y2 Coordinate for linearization of “la” “
F_20 X1 Coordinate for linearization of “Va” It affects the “Va” value displayed
F_21 Y1 Coordinate for linearization of “Va” “
F_22 X2 Coordinate for linearization of “Va” “
F_23 Y2 Coordinate for linearization of “Va” “
F_24 X1 Coordinate for linearization of “Pa” It affects the “Pa” value displayed
F_25 Y1 Coordinate for linearization of “Pa” “
F_26 X2 Coordinate for linearization of “Pa” “
F_27 Y2 Coordinate for linearization of “Pa” “

page 14 of 35 File: SM1180_r9eng - December 2007 - Technical note: SM1180 & TM 060
SM1180 & TM060
File: SM1180_r9eng - December 2007 - Technical note: SM 1180 & TM 060 page 15 of 35
SM1180 & TM060
F_nn Default
Value
Parameter Comment
F_00 0 Not used
F_01 0 Display mode set
1 Programming mode set
F_02 50 Not used
F_03 8000 Not used
F_04 80 Not used
F_05 8000 Not used
F_06 80 Not used
F_07 600 (=6000W) Reverse Power alarm threshold
F_8 80 Not used
F_9 8000 Not used
F_10 1 Not used
F_11 0 Not used
F_12 0 Working hours counter
F_13 0 EEPROM initialization value #1
F_14 0 EEPROM initialization value #2
F_15 0 Not used
F_16 1 X1 Coordinate for linearization “Pr” unit = bit
F_17 0 Y1 Coordinate for linearization “Pr” unit = W x 10
F_18 2626 X2 Coordinate for linearization “Pr” unit = bit
F_19 300 Y2 Coordinate for linearization “Pr” unit = W x 10
Functions table of Slave CPU

page 16 of 35 File: SM1180_r9eng - December 2007 - Technical note: SM1180 & TM 060
SM1180 & TM060
File: SM1180_r9eng - December 2007 - Technical note: SM 1180 & TM 060 page 17 of 35
SM1180 & TM060
Equipment maintenance
Cleaning
Once a week inspect the inlet air lter as well as the outlet
window.
The inlet lter, on the front panel, may be taken off by means
of a screwdriver or similar tool doing raise between the lter
and the panel: before doing any operation switch off the
external circuit breaker provided to remove the main from the
equipment.
In case the equipment needs internal cleaning then proceed as
follow:
- switch off the external circuit breaker or whatever device
provided to remove the main from the equiment;
-remove the main connector #1 by rotating counter-clockwise
the external ring then pull it;
- remove cover
- remove dust with dry air
- reinstall cover: tighten all the screws
- plug the connector #1: push the plug into the socket, rotate
clockwise the ring.
Fuses replacement
To replace the fuses on rear panel proceed as follow:
- switch off the external circuit breaker or whatever device is
provided by customer to remove main from the equipment;
- remove the main connector #1 by rotating counter-clockwise
the external ring then pull it;
- unscrew fuseholder cap;
- replace the fuse with a new one with same electrical cha
racteristics;
- inspect also the fuseholder: if it is oxidated or it presents
burned points then replace it;
- install the fuseholder cap and screw tight;
- plug the connector #1: push the plug into the socket, rotate
clockwise the ring.
- For the fuses value see page 9.
Failure to comply with these instructions may involve con-
siderable risks for the staff responsible for checking and
using the equipment, as well as the risk of malfunctions of
the equipment itself.

page 16 of 35 File: SM1180_r9eng - December 2007 - Technical note: SM1180 & TM 060
SM1180 & TM060
File: SM1180_r9eng - December 2007 - Technical note: SM 1180 & TM 060 page 17 of 35
SM1180 & TM060
Pos. Q.ty Description P/N D T U
1
1 Main breaker (Magnetic breaker) C60L-MA26369 c g c
1 Main breaker (Magnetic breaker) IA3RV13214DC10 c c g
1 Main breaker (Magnetic breaker) IAC60H25135 g c c
2 1 Potentiometer RS-33P010K g g g
3 1 7 pins Socket, AMP/CPC Conn.# 1 CPC07/2061371 g g g
4 7 Male pin, size XII CPCX/0662614 c g g
4 Male pin, size XII 60A CPCX/1939914 g c c
5 1 7 pins Plug, AMP/CPC CPC07/2061361 g g g
6 7 Female pin, size XII CPCX/0667402 c g g
4 Female pin, size XII 60 A CPCX/1939902 g c c
7 2 Fuseholder for 10x38 mm fuse FUP1891 g g g
8 2 Fuse 10x38 mm, 6A, 500V, ceramic, quick FU3NW6001/1 g g g
9 1 14 pins Socket, AMP/CPC (206043-1) Conn.# 2 CPC14/1826411 g g g
10 14 Female pin, size III CPCX/1630881 g g g
11 1 14 pins Plug, AMP/CPC CPC14/1826491 g g g
12 14 Male pin, size III CPCX/1630861 g g g
13 3 7 pins Socket, AMP/CPC Conn.# 3 CPC07/2113981 g g g
14 5 Female pin, size III CPCX/1630881 g g g
15 1 7 pins Plug, AMP/CPC CPC07/2114001 g g g
16 5 Male pin, size III CPCX/1630861 g g g
17 1 9 pins Socket, AMP/CPC Conn.# 4 CPC09/2067051 g g g
18 9 Female pin, size III CPCX/1630881 g g g
19 1 9 pins Plug, AMP/CPC CPC09/1826451 g g g
20 9 Male pin, size III CPCX/1630861 g g g
21 1 Driver board M216 800000216 g g g
22 1 Display board (slave) 800000177S g g g
23 1 Display board (master) 800000177M g g g
24 1 Capacitor for motor fan - 2µF 450V CR/202A450 g g g
25 1 Autotransformer 42/ATT230/002 c g g
1 Autotransformer 42ATT230/008 g c c
26 1 Fan VE2GRE120/6221 g g g
27 1 Snubber Capacitor 1µF 500V CR/102A500MKP g g g
28 1 Filter board M207 800000207 g g g
29 2 IGBT transistors TT/SKM100GB123D c g g
2 IGBT transistors TT/SKM195GB066D g c c
30 1 Capacitor board M230 800000230 c g g
1 Filter capacitor 66uF 800V CPVFFVE6B66/KJE g c c
31 1 Bridge rectier DD/SKD6212 g g g
1 Main line lter, Corcom FL/20AY01 c g c
32 1 Main line lter, Corcom FL16FCD10 c c g
1 Main line lter, Corcom FL50FCD10 g c c
33 1 H.V. rectier assembly AS1180 800AS1180 g g g
Components list (see drawing at page 19)

page 18 of 35 File: SM1180_r9eng - December 2007 - Technical note: SM1180 & TM 060
SM1180 & TM060
File: SM1180_r9eng - December 2007 - Technical note: SM 1180 & TM 060 page 19 of 35
SM1180 & TM060
Components list (see drawing at page 19)
Pos. Q.ty Description P/N D T U
34 1 Capacitor pack board M209 800000209 cgg
1 Capacitor pack board M201 800000209 gcc
35 1 4 pins, H.V. Socket AMP/LGH Kit MO/…8630173 ggg
36 4 Female pin (included on kit) ggg
37 1 4 pins, H.V. Plug AMP/LGH (included on kit) ggg
38 4 Male pin (included on kit) ggg
39 1 L.V. Main Choke 42/FI1180A/BT cgg
40 1 H.V. Choke 42/FI1180A/AT cgg
41
1 H.V. Transformer 42/FT1180A cgc
1 H.V. Transformer 42/FT1180U ccg
1 H.V. Transformer 42/FT1180DA gcc
42 1 2 Pins socket, PHOENIX MSTB2,5/2STF5,08 ccg
43 1 2 Pins plug, PHOENIX DKFMSTB2,5/2GF5,08 ggg
44 1 Key switch S3SB20004LB01 ggg
45 1 Contact holder S3SB2908-0AA ggg
46 1 N.O. Contact S3SB2404-0B ggg
47 1 N.C. Contact S3SB2404-0C ggg
1 L.V. Main Choke 42/FI1180DABTF gcc
1 Choke L-C 42/FI1180DABTR gcc
48 1 Relay board M222 4000222 ggg
49 1 3 pins Socket, AMP/CPC Conn.# 7 CPC03/2060362 * ggg
50 1 3 pins Plug, AMP/CPC CPC03/2060372 * ggg
* Note: on version 54 only

page 18 of 35 File: SM1180_r9eng - December 2007 - Technical note: SM1180 & TM 060
SM1180 & TM060
File: SM1180_r9eng - December 2007 - Technical note: SM 1180 & TM 060 page 19 of 35
SM1180 & TM060
Components layout
This manual suits for next models
4
Table of contents
Other ALTER Portable Generator manuals
Popular Portable Generator manuals by other brands

global thermoelectric
global thermoelectric 8550 operating manual

Rigol
Rigol DG1000 Series user guide
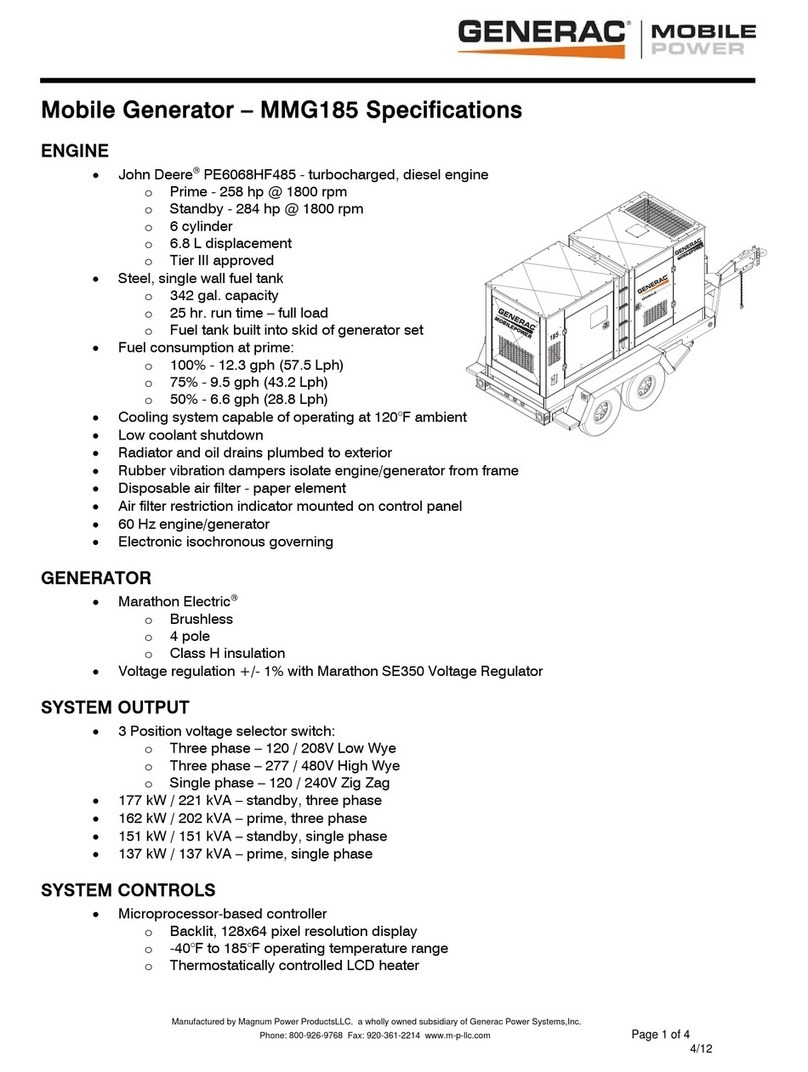
Generac Power Systems
Generac Power Systems Mobile Power MMG185 Specifications
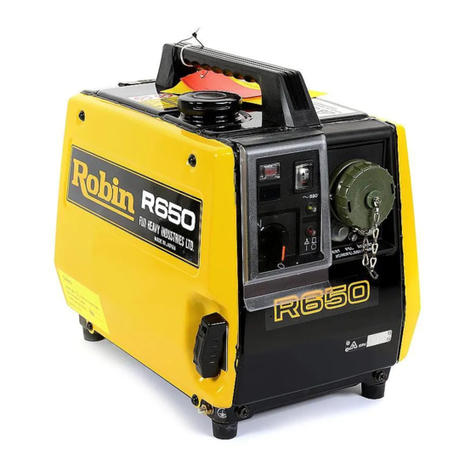
Robin
Robin R650 Service manual

Northern Lights
Northern Lights M944WF3 Operator's manual
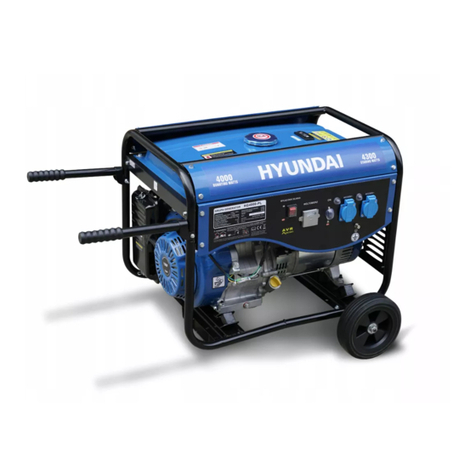
Hyundai power products
Hyundai power products HG4000-A Original instructions