Amana A/GPG14M Series Manual

INSTALLATION & OPERATING
INSTRUCTIONS for
A/GPG14M SERIES W/ R410A
SINGLE PACKAGE GAS-ELECTRIC
HEATING & COOLING UNIT
RECOGNIZE THIS SYMBOL AS A SAFETY
PRECAUTION.
O
NLY
PERSONNEL
THAT
HAVE
BEEN
TRAINED
TO
INSTALL
,
ADJUST
,
SERVICE
OR
REPAIR
(
HEREINAFTER
, “
SERVICE
”)
THE
EQUIPMENT
SPECIFIED
IN
THIS
MANUAL
SHOULD
SERVICE
THE
EQUIPMENT
. T
HE
MANUFACTURER
WILL
NOT
BE
RESPONSIBLE
FOR
ANY
INJURY
OR
PROPERTY
DAMAGE
ARISING
FROM
IMPROPER
SERVICE
OR
SERVICE
PROCEDURES
. I
F
YOU
SERVICE
THIS
UNIT
,
YOU
ASSUME
RESPONSIBILITY
FOR
ANY
INJURY
OR
PROPERTY
DAMAGE
WHICH
MAY
RESULT
. I
N
ADDITION
,
IN
JURISDICTIONS
THAT
REQUIRE
ONE
OR
MORE
LICENSES
TO
SERVICE
THE
EQUIPMENT
SPECIFIED
IN
THIS
MANUAL
,
ONLY
LICENSED
PERSONNEL
SHOULD
SERVICE
THE
EQUIPMENT
. I
MPROPER
INSTALLATION
,
ADJUSTMENT
,
SERVICING
OR
REPAIR
OF
THE
EQUIPMENT
SPECIFIED
IN
THIS
MANUAL
,
OR
ATTEMPTING
TO
INSTALL
,
ADJUST
,
SERVICE
OR
REPAIR
THE
EQUIPMENT
SPECIFIED
IN
THIS
MANUAL
WITHOUT
PROPER
TRAINING
MAY
RESULT
IN
PRODUCT
DAMAGE
,
PROPERTY
DAMAGE
,
PERSONAL
INJURY
OR
DEATH
.
This Forced Air Central Unit Design Complies With
Requirements Embodied In The American National
Standard / National Standard of Canada Shown Below.
ANSI Z21.47•CSA-2.3 Central Furnaces.
Goodman Company, L.P.
19001 Kermier Rd., Waller, TX 77484
www.goodmanmfg.com - or - www.amana-hac.com
© 2014-2019, 2021 Goodman Company, L.P.
IOG-3008K
05/2021 is a registered trademark of Maytag Corporation or its related companies and is used
under license. All rights reserved.
These installation instructions cover the outdoor installa-
tion of self contained package air conditioners and heating
model for information regarding accessories.
*NOTE: Please contact your distributor or our website
manual.

2
INDEX
REPLACEMENT PARTS.................................................2
..........................................................2
SAFETY INSTRUCTIONS ..............................................2
.........................................................2
GENERAL INFORMATION .............................................5
...........................................5
UNIT LOCATION..............................................................6
.......................................................6
...........................6
....................................6
................................7
RIGGING DETAILS .........................................................7
GAS PIPING.....................................................................7
....7
...........................................................................8
....................................................8
PROPANE GAS INSTALLATIONS .................................9
........................................................9
ELECTRICAL WIRING ..................................................10
..............................................10
.......................................10
CIRCULATING AIR AND FILTERS............................... 11
................................................ 11
.................................................................. 11
....................................................................... 11
VENTING........................................................................ 11
...........................................12
CONDENSATE DRAIN..................................................12
..............................12
NORMAL SEQUENCES OF OPERATION ..................12
.....................................................................12
.....................................................................12
...................................................................13
STARTUP, ADJUSTMENTS, AND CHECKS ...............13
......................................................13
.....................14
....................................................15
...............................................15
........................................16
..........................16
......................................................17
TROUBLESHOOTING ..................................................18
SUPERHEAT...................................................................18
.................................................18
...............................................18
...............................18
19
............................20
MAINTENANCE.............................................................20
..........................20
...................................20
...20
......................................................20
.............21
............21
......................................................21
....21
....................................................21
ACCESSORIES AND FUNCTIONAL PARTS..............22
......................................22
.....................................................22
...............................................22
APPENDIX ......................................................................29
UNIT DIMENSIONS.......................................................29
WIRING DIAGRAMS .....................................................30
MINIMUM CLEARANCES.............................................36
RECOMMENDED FILTER SIZES ................................36
START-UP CHECKLIST................................................38
REPLACEMENT PARTS
When reporting shortages or damages, or ordering repair
parts, give the complete unit model and serial numbers as
stamped on the unit’s nameplate.
Replacement parts for this appliance are available through
your contractor or local distributor. For the location of your
nearest distributor, consult the white business pages, the
yellow page section of the local telephone book or contact:
HOMEOWNER SUPPORT
GOODMAN MANUFACTURING COMPANY, L.P.
19001 KERMIER ROAD
WALLER, TX 77484
SAFETY INSTRUCTIONS
Before installing this unit, please read this manual to famil-
to, including maximum external static pressure to unit, air
temperature rise, minimum or maximum CFM and motor
speed connections.
Keep this literature in a safe place for future reference.
WARNING
DO NOT CONNECT TO OR USE ANY DEVICE THAT IS NOT DESIGN CERTIFIED
BY GOODMAN FOR USE WITH THIS UNIT. SERIOUS PROPERTY DAMAGE,
PERSONAL INJURY, REDUCED UNIT PERFORMANCE AND/OR HAZARDOUS
CONDITIONS MAY RESULT FROM THE USE OF SUCH NON-APPROVED DEVICES.
WARNING
SHOULD OVERHEATING OCCUR OR THE GAS SUPPLY FAIL TO SHUT OFF, TURN
OFF THE MANUAL GAS SHUTOFF VALVE EXTERNAL TO THE FURNACE BEFORE
TURNING OFF THE ELECTRICAL SUPPLY.

3
WARNING
THIS PRODUCT CONTAINS OR PRODUCES A CHEMICAL OR CHEMICALS WHICH
MAY CAUSE SERIOUS ILLNESS OR DEATH AND WHICH ARE KNOWN TO THE
STATE OF CALIFORNIA TO CAUSE CANCER, BIRTH DEFECTS OR OTHER
REPRODUCTIVE HARM.
WARNING
TO AVOID PROPERTY DAMAGE, PERSONAL INJURY OR DEATH, DO NOT USE
THIS UNIT IF ANY PART HAS BEEN UNDER WATER. IMMEDIATELY CALL A
QUALIFIED SERVICE TECHNICIAN TO INSPECT THE FURNACE AND TO REPLACE
ANY PART OF THE CONTROL SYSTEM AND ANY GAS CONTROL HAVING BEEN
UNDER WATER.
CARBON MONOXIDE POISONING HAZARD
Failure to follow the steps outlined below for each
appliance connected to the venting system being placed
into operation could result in carbon monoxide poisoning
or death.
The following steps shall be followed with each appliance
connected to the venting system placed in operation,
while any other appliances connected to the venting
system are not in operation:
1. Seal any unused openings in the venting system.
2. Inspect the venting system for proper size and
horizontal pitch, as required by the National Fuel Gas
Code, ANSI Z223.1 or the Natural Gas and Propane
Installation Code, CSA B149.1-15 and these
instructions. Determine that there is no blockage or
restriction, leakage, corrosion and other deficiencies
which could cause an unsafe condition.
3. As far as practical, close all building doors and
windows and all doors between the space in which
the appliance(s) connected to the venting system are
located and other spaces of the building.
4. Close fireplace dampers.
5. Turn on clothes dryers and any appliance not
connected to the venting system. Turn on any
exhaust fans, such as range hoods and bathroom
exhausts, so they shall operate at maximum speed.
Do not operate a summer exhaust fan.
6. Follow the lighting instructions. Place the appliance
being inspected in operation. Adjust thermostat so
appliance shall operate continuously.
7. Test for spillage from draft hood appliances at the
draft hood relief opening after 5 minutes of main
burner operation. Use the flame of a match or
candle.
8. If improper venting is observed during any of the
above tests, the venting system must be corrected in
accordance with the National Fuel Gas Code ANSI
Z223.1/NFPA 54 and/or National Gas and Propane
Installation Code CSA B149.1-15.
9. After it has been determined that each appliance
connected to the venting system properly vents
when tested as outlined above, return doors,
windows, exhaust fans, fireplace dampers and any
other gas burning appliance to their previous
conditions of use.

4
AVERTISSEMENT
RISQUE D'INTOXICATION AU MONOXYDE DE CARBONE
Si les étapes décrites ci-dessous ne sont pas suivies pour
chacun des appareils raccordés au système de ventilation
au moment de sa mise en marche, cela peut entraîner une
intoxication au monoxyde de carbone ou la mort. Les
étapes suivantes doivent être suivies pour chacun des
appareils raccordés au système de ventilation au moment
de sa mise en marche, alors que tous les autres appareils
raccordés au système de ventilation ne sont pas en marche:
1) Sceller toutes les ouvertures inutilisées du système
de ventilation.
2) Inspecter le système de ventilation afin de vérifier si la
taille et l'inclinaison par rapport à l'horizontale sont
conformes aux exigences du National Fuel Gas Code,
ANSI Z223.1/NFPA 54 ou du Code d'installation du gaz
naturel et du propane, CSA B149.1 et à ces instructions.
Vérifier qu'il n'y a pas d'obstruction ou de restriction, de
fuite, de corrosion et d'autres problèmes qui pourraient
entraîner une situation dangereuse.
3) Si possible, fermer toutes les portes et fenêtres du
bâtiment ainsi que toutes les portes séparant l'endroit
où se trouvent les appareils raccordés au système de
ventilation et les autres zones du bâtiment.
4) Fermer le registre des foyers.
5) Mettre les sécheuses en marche ainsi que tous les
autres appareils qui ne sont pas raccordés au système de
ventilation. Mettre en marche tous les ventilateurs de
tirage, comme celui des hottes de cuisine et des salles de
bains, et les régler à la puissance maximale. Ne pas
mettre en marche les ventilateurs d'été.
6) Suivre les instructions d'allumage. Mettre en marche
l'appareil soumis à l'inspection. Régler le thermostat
de manière à ce que l'appareil fonctionne en continu.
7) Vérifier la présence de fuite au niveau de l'ouverture
du coupe-tirage des appareils qui en sont dotés après 5
minutes de fonctionnement du brûleur principal. Utiliser
la flamme d'une allumette ou d'une bougie.
8) Si un problème de ventilation est observé pendant
l'un des essais décrits ci-dessus, des correctifs doivent
être apportés au système de ventilation conformément
au National Fuel Gas Code, ANSI Z223.1/NFPA 54 et (ou)
au Code d'installation du gaz naturel et du propane, CSA
B149.1.
9) Une fois qu'il a été déterminé que chaque appareil
raccordé au système de ventilation fonctionne
correctement au moyen des essais décrits ci-dessus,
les portes, les fenêtres, les ventilateurs, les registres
de foyer et tous les autres appareils de combustion
alimentés au gaz doivent être remis dans leur état
initial.
FIRE OR EXPLOSION HAZARD
Failure to follow the safety warnings exactly could result in
serious injury, death or property damage.
Never test for gas leaks with an open flame.
Use a commercially available soap solution made specifically
for the detection of leaks to check all connections. A fire or
explosion may result causing property damage, personal
injury or loss of life.
AVERTISSEMENT
RISQUE D'INCENDIE OU D'EXPLOSION
Si les consignes de sécurité ne sont pas suivies à la lettre,
cela peut entraîner la mort, de graves blessures ou des
dommages matériels.
Ne jamais vérifier la présence de fuites de gaz au moyen
d'une flamme nue. Vérifier tous les raccords en utilisant
une solution savonneuse commerciale conçue
spécialement pour la détection de fuites. Un incendie ou
une explosion risque de se produire, ce qui peut entraîner
la mort, des blessures ou des dommages matériels.
CARBON MONOXIDE POISONING HAZARD
Failure to follow instructions could result in severe personal
injury or death due to carbon-monoxide poisoning, if
combustion products infiltrate into the building. Check that
all openings in the outside wall around the vent (and air
intake) pipe(s) are sealed to prevent infiltration of
combustion products into the building. Check that furnace
vent (and air intake) terminal(s) are not obstructed in any
way during all seasons.
AVERTISSEMENT
R
Si ces directives ne sont pas suivies, cela peut entraîner des
blessures graves ou une intoxication au monoxyde de
carbone pouvant causer la mort, si des produits de
combustion s'infiltrent dans le bâtiment. Vérifier que toutes
les ouvertures pratiquées dans le mur extérieur autour du ou
des tuyaux d'évent (et de la prise d'air) sont scellées de
manière à empêcher l'infiltration de produits de combustion
dans le bâtiment. Veiller à ce que la ou les sorties de l'évent
de l'appareil de chauffage (et la prise d'air) ne soient, en
aucune façon, obstruées, quelle que soit la saison.
ISQUE D'INTOXICATION AU MONOXYDE DE CARBONE

5
B10259-216
CO can cause serious illness including permanent brain
damage or death.
Advertencia especial para la instalación de calentadores ó manejadoras
de aire en áreas cerradas como estacionamientos ó cuartos de servicio.
B10259-216
El monóxido de carbono puede causar enfermedades severas
como daño cerebral permanente ó muerte.
Las emisiones de monóxido de carbono pueden circular a través
del aparato cuando se opera en cualquier modo.
B10259-216
RISQUE D'EMPOISONNEMENT AU MONOXYDE DE CARBONE
Le monoxyde de
des
carbone peut causer des maladies graves telles que
dommages permanents au cerveau et meme la mort.
Cette ventilation est nécessaire pour éviter le danger d'intoxication
au CO pouvant survenir si un appareil produisant du monoxyde
de carbone continue de fonctionner au sein de la zone confinée.
GENERAL INFORMATION
WARNING
T
O PREVENT PROPERTY DAMAGE, PERSONAL INJURY OR DEATH, DUE TO FIRE,
EXPLOSIONS, SMOKE, SOOT, CONDENSATION, ELECTRIC SHOCK OR CARBON
MONOXIDE, THIS UNIT MUST BE PROPERLY INSTALLED, REPAIRED, OPERATED,
AND MAINTAINED.
This unit is approved for outdoor installation ONLY.
Rated performance is achieved after 20 hours of operation.
-
www.
goodmanmfg.com for Goodman® brand products or www.
amana-hac.com for Amana® brand products. Within either
website, please select the residential or commercial prod-
ucts menu and then select the submenu for the type of prod-
uct to be installed, such as air conditioners or heat pumps, to
access a list of product pages that each contain links to that
must be installed, operated, and maintained in accordance
with these installation and operating instructions, all local
building codes and ordinances, or in their absence, with the
latest edition of the National Fuel Gas Code NFPA54/ANSI
Z223.1 and National Standard of Canada CAN/CSA B149
Installation Codes.
The heating and cooling capacities of the unit should be
greater than or equal to the design heating and cooling
loads of the area to be conditioned. The loads should be
calculated by an approved method or in accordance with
A.S.H.R.A.E. Guide or Manual J - Load Calculations pub-
lished by the Air Conditioning Contractors of America.
Obtain from:
American National Standards Institute
25 West 43rd Street, 4th Floor
New York, NY 10036
Check the carton upon arrival for external damage. If dam-
age is found, a request for inspection by carrier agent should
be made in writing immediately.
Carefully inspect the unit for damage including damage to
the cabinetry. Any bolts or screws which may have loosened
in transit must be re-tightened. In the event of damage, the
receiver should:
1. Make notation on delivery receipt of any visible dam-
age to shipment or container.
2. Notify carrier promptly and request an inspection.
3. In case of concealed damage, carrier should be noti-
4. File the claim with the following supporting documents:
a.
bond.
b. Original paid freight bill or indemnity in lieu thereof.
c.
trade and other discounts or reductions.
d. Copy of the inspection report issued by carrier rep-
resentative at the time damage is reported to the
carrier. The carrier is responsible for making prompt
inspection of damage and for a thorough investiga-
tion of each claim. The distributor or manufacturer
will not accept claims from dealers for transportation
damage.
NOTE: When inspecting the unit for transportation damage,
remove all packaging materials. Recycle or dispose of the
packaging material according to local codes.

6
UNIT LOCATION
WARNING
T
O PREVENT POSSIBLE EQUIPMENT DAMAGE, PROPERTY DAMAGE, PERSONAL
INJURY OR DEATH, THE FOLLOWING BULLET POINTS MUST BE OBSERVED
WHEN INSTALLING THE UNIT.
•
proper condensate drainage, the unit must be mounted
level.
•
building, and at least three feet above any forced air
inlet located within ten feet. The economizer/manual
fresh air intake/motorized fresh air intake and combus-
restriction.
• To avoid possible corrosion of the heat exchanger, do
-
Common sources of such compounds include swim-
ming pool chemicals and chlorine bleaches, paint
stripper, adhesives, paints, varnishes, sealers, wax-
construction and remodeling. Various commercial and
industrial processes may also be sources of chlorine/
• To avoid possible illness or death of the building occu-
-
omizer, manual fresh air intake, motorized fresh air
-
required, consult local codes.
•
maintained.
•
unit must never be obstructed. If used, do not allow the
economizer/manual fresh air damper/ motorized fresh
air damper to become blocked by snow or debris. In
some climates or locations, it may be necessary to ele-
vate the unit to avoid these problems.
• Damper must be on open position when appliance
• Le registre doit être ouvert lorsque tout brûleur princi-
pal de l’appareil est en état de fonctionnement.
• When the unit is heating, the temperature of the return
air entering the unit must be between 50° F and 100° F.
• Units manufactured on or after May 1, 2017 are not
permitted to be used in Canada for heating of buildings
or structures under construction.
• When the unit is installed on the ground adjacent to
-
ommended. Prepare a base that is 3” larger than the
package unit footprint and a minimum of 3” thick.
•
water from higher ground can collect in the unit.
• The top of the unit should be completely unobstruct-
ed. If units are to be located under an overhang, there
should be a minimum of 48” clearance and provisions
overhang.
Outside Slab Installation
NOTE: To ensure proper condensate drainage, unit must be
installed in a level position.
• To avoid possible property damage or personal injury,
required by local codes. Consult a structural engineer
to determine the weight capabilities of the roof.
Rooftop Installation
•
Class A, Class B, or Class C roof covering material.
•
service personnel should be provided.

7
•
to locating and mounting the curb and package unit.
• Ductwork must be constructed using industry guide-
lines. The duct work must be placed into the roof curb
before mounting the package unit.
• -
ing material are furnished by the contractor.
Roof Curb Installation
RIGGING DETAILS
WARNING
T
O PREVENT PROPERTY DAMAGE, THE UNIT SHOULD REMAIN IN AN UPRIGHT
POSITION DURING ALL RIGGING AND MOVING OPERATIONS.
T
O FACILITATE
LIFTING AND MOVING WHEN A CRANE IS USED, PLACE THE UNIT IN AN
ADEQUATE CABLE SLING.
Important: If using bottom discharge with roof curb,
ductwork should be attached to the curb prior to installing
the unit. Ductwork dimensions are shown in roof curb instal-
lation instructions.
Refer to the Roof Curb Installation Instructions for proper
curb installation. Curbing must be installed in compliance
Lower unit carefully onto roof mounting curb. While rigging
unit, center of gravity will cause condenser end to be lower
than supply air end.
Rigging
GAS PIPING
IMPORTANT NOTE: This unit is factory set to operate on
natural gas at the altitudes shown on the rating plate.
WARNING
T
O AVOID PROPERTY DAMAGE, PERSONAL INJURY OR DEATH WHEN EITHER
USING PROPANE GAS ALONE OR AT HIGHER ALTITUDES, OBTAIN AND INSTALL
THE PROPER CONVERSION KIT(S).
F
AILURE TO DO SO CAN RESULT IN
UNSATISFACTORY OPERATION AND/OR EQUIPMENT DAMAGE.
H
IGH ALTITUDE
KITS ARE FOR
U
.
S
. INSTALLATIONS ONLY AND ARE NOT APPROVED FOR USE
IN
C
ANADA.
The rating plate is stamped with the model number, type of
gas and gas input rating. Make sure the unit is equipped to
operate on the type of gas available. Conversion to LP gas
is permitted with the use of the factory authorized conver-
sion kit LPM-07, for use with single stage models, or LPM-
08, for use with two-stage models. See table below.
LP Conversion Kit Model
LPM-07 Single Stage Heating Models
LPM-08 Two-Stage Heating Models
Inlet Gas Pressure
Natural Min. 5.0" W.C., Max. 10.0" W.C.
Propane
Min. 11.0" W.C., Max. 13.0" W.C.
Inlet Gas Pressure must be within the minimum and maxi-
mum value shown in table above.
The minimum supply pressure should not vary from that
shown in the table above because this could prevent the
unit from having dependable ignition. In addition, gas input
to the burners must not exceed the rated input shown on the
heat exchanger failure.
IMPORTANT NOTE: The gas/electric units naturally derate
can cause poor combustion and equipment failure. At all

8
altitudes, the manifold pressure must be within 0.3 inches
W.C. of that listed on the nameplate for the fuel used. At all
altitudes and with either fuel, the air temperature rise must
be within the range listed on the unit nameplate.
Refer to the Installation Manual provided with the LP kit
for conversion from natural gas to propane gas and for alti-
tude adjustments. NOTE: Up to 2,000 feet, no changes are
required; above 2,000 feet, please refer to the gas/electric
Installation of the gas/electric unit at altitudes above 2000
Altitude Conversion Kit available for this gas/electric unit.
Installation de l’unité gaz/électrique à des altitude
à la Haute Altitude Kit de Conversion disponible pour cette
unité gaz/électrique.
IMPORTANT NOTE: To avoid possible unsatisfactory opera-
do not undersize the natural/propane gas piping from the
meter/tank to the unit. When sizing a trunk line, include all
appliances on that line that could be operated simultaneously.
The rating plate is stamped with the model number, type of
gas and gas input rating. Make sure the unit is equipped to
operate on the type of gas available. The gas line installa-
tion must comply with local codes, or in the absence of local
codes, with the latest edition of the National Fuel Gas Code
NFPA 54/ANSI Z223.1.
Natural Gas Connection
Length of
Pipe in Feet 1/2 3/4 11 1/4 1 1/2
10 132 278 520 1050 1600
20 92 190 350 730 1100
30 73 152 285 590 980
40 63 130 245 500 760
50 56 115 215 440 670
60 50 105 195 400 610
70 46 96 180 370 560
80 43 90 170 350 530
90 40 84 160 320 490
100 38 79 150 305 460
Natural Gas Capacity of Pipe
in Cubic Feet of Gas Per Hour (CFH)
Nominal Black Pipe Size (inches)
BTUH Furnace Input
Heating Value of Gas (BTU/Cubic Foot)
CFH =
Refer to the Proper Piping Practice drawing for the general
layout at the unit. The following rules apply:
1.
-
mitted as long as it is in agreement with local codes.
2. Use pipe joint compound on male threads only. Pipe
joint compound must be resistant to the action of the
fuel used.
3. Use ground joint unions.
4. Install a drip leg to trap dirt and moisture before it can
enter the gas valve. The drip leg must be a minimum of
three inches long.
5. Use two pipe wrenches when making connection to the
gas valve to keep it from turning.
6.
7. Tighten all joints securely.
8. The unit must be connected to the building piping by
one of the following methods:
•
• -
• Listed gas appliance connectors used in accordance
with the terms of their listing that are completely in the
same room as the equipment
• In the prior two methods above the connector or tubing
must be protected from physical and thermal damage.
Aluminum alloy tubing and connectors must be coated
to protect against external corrosion when in contact
with masonry, plaster or insulation or are subject to re-
-
Proper Piping Practice
NOTE: The unit gas supply entrance is factory sealed with
plugs. Keep plugs in place until gas supply is ready to be
installed. Once ready, replace the plugs with the supplied
grommets and install gas supply line.
CAUTION
T
O PREVENT PROPERTY DAMAGE OR PERSONAL INJURY DUE TO FIRE, THE
FOLLOWING INSTRUCTIONS MUST BE PERFORMED REGARDING GAS
CONNECTIONS AND PRESSURE TESTING:
•
T
HE UNIT AND ITS GAS CONNECTIONS MUST BE LEAK TESTED BEFORE
PLACING IN OPERATION.
B
ECAUSE OF THE DANGER OF EXPLOSION OR
FIRE, NEVER USE A MATCH OR OPEN FLAME TO TEST FOR LEAKS.
N
EVER
EXCEED SPECIFIED PRESSURES FOR TESTING.
H
IGHER PRESSURE MAY
DAMAGE GAS VALVE AND CAUSE OVERFIRING WHICH MAY RESULT IN
PREMATURE HEAT EXCHANGE FAILURE.
•
T
HIS UNIT AND ITS SHUT-OFF VALVE MUST BE DISCONNECTED FROM
THE GAS SUPPLY DURING ANY PRESSURE TESTING OF THAT SYSTEM AT
TEST PRESSURES IN EXCESS OF 1/2
PSIG
(3.48 K
P
A).
•
T
HIS UNIT MUST BE ISOLATED FROM THE GAS SUPPLY SYSTEM BY
CLOSING ITS MANUAL SHUT-OFF VALVE DURING ANY PRESSURE
TESTING OF THE GAS SUPPLY PIPING SYSTEM AT TEST PRESSURES
EQUAL TO OR LESS THAN 1/2
PSIG
(3.48 K
P
A).

9
• There will be air in the gas supply line after testing for
leaks on a new installation. Therefore, the air must be
bled from the line by loosening the ground joint union
minutes until all gas has been dissipated in the air. Be
bleeding procedure. The unit is placed in operation by
closing the main electrical disconnect switch for the unit.
WARNING
TO AVOID PROPERTY DAMAGE OR PERSONAL INJURY, BE SURE THERE IS
NO OPEN FLAME IN THE VICINITY DURING AIR BLEEDING.
PROPANE GAS INSTALLATIONS
WARNING
T
O AVOID PROPERTY DAMAGE, PERSONAL INJURY OR DEATH DUE TO FIRE
OR EXPLOSION CAUSED BY A PROPANE GAS LEAK, INSTALL A GAS
DETECTING WARNING DEVICE.
S
INCE RUST CAN REDUCE THE LEVEL
OF ODORANT IN PROPANE GAS, A GAS DETECTING WARNING DEVICE
IS THE ONLY RELIABLE WAY TO DETECT A PROPANE GAS LEAK.
C
ONTACT A LOCAL PROPANE GAS SUPPLIER ABOUT INSTALLING A
GAS DETECTING WARNING DEVICE.
IMPORTANT NOTE: Propane gas conversion kits must be
installed to convert units to propane gas.
All propane gas equipment must conform to the safety stan-
For satisfactory operation, propane gas supply pressure
must be within 9.7 - 10.3 inches W.C. at the manifold with all
gas appliances in operation. Maintaining proper gas pres-
sure depends on three main factors:
1.
or containers.
2. Proper pressure regulation.
3. Pressure drop in lines between regulators, and be-
tween second stage regulator and the appliance. Pipe
size required will depend on length of pipe run and total
load of all appliances.
Complete information regarding tank sizing for vaporization,
recommended regulator settings and pipe sizing is available
from most regulator manufacturers and propane gas suppliers.
Since propane gas will quickly dissolve white lead or most
standard commercial compounds, special pipe dope must
be used. Shellac base compounds resistant to the actions
Clyde’s® or John Crane® are satisfactory.
See below for typical propane gas piping.
200 PSIG
Maximum
5 to 15 PSIG
(20 PSIG Max.) Continuous
11" W.C.
Second Stage
Regulator
First Stage
Regulator
Typical Propane Gas Piping
Sizing Between First and Second Stage Regulator
Maximum Propane Capacities listed are based on 1 PSIG Pressure Drop at 10
PSIG Setting. Capacities in 1,000 BTU/HR
3/8" 1/2" 5/8" 3/4" 7/8" 1/2" 3/4"
30 309 700 1,303 2,205 3,394 1,843 3,854
40 265 599 1,115 1,887 2,904 1,577 3,298
50 235 531 988 1,672 2,574 1,398 2,923
60 213 481 896 1,515 2,332 1,267 2,649
70 196 446 824 1,394 2,146 1,165 2,437
80 182 412 767 1,297 1,996 1,084 2,267
90 171 386 719 1,217 1,873 1,017 2,127
100 161 365 679 1,149 1,769 961 2,009
150 130 293 546 923 1,421 772 1,613
200 111 251 467 790 1,216 660 1,381
250 90 222 414 700 1,078 585 1,224
300 89 201 378 634 976 530 1,109
350 82 185 345 584 898 488 1,020
400 76 172 321 543 836 454 949
To convert to Capacities at 15 PSIG Settings -- Multiply by 1.130
To convert to Capacities at 5 PSIG Settings -- Multiply by 0.879
PIPE OR
TUBING
LENGTH,
FEET
NOMINAL PIPE SIZE,
SCHEDULE 40
TUBING SIZE, O.D., TYPE L
Sizing Between Single or Second Stage Regulator and Appliance*
Maximum Propane Capacities Listed are Based on 1/2" W.C. Pressure Drop at
11" W.C. Setting. Capacities in 1,000 BTU/HR
3/8" 1/2" 5/8" 3/4" 7/8" 1/2"
3/4" 1" 1-1/4" 1-1/2"
10 49 110 206 348 539 291 608 1,146 2,353 3,525
20 34 76 141 239 368 200 418 788 1,617 2,423
30 27 61 114 192 296 161 336 632 1,299 1,946
40 23 52 97 164 253 137 284 541 1,111 1,665
50 20 46 86 146 224 122 255 480 985 1,476
60 19 42 78 132 203 110 231 436 892 1,337
80 16 36 67 113 174 94 198 372 764 1,144
100 14 32 59 100 154 84 175 330 677 1,014
125 12 28 52 89 137 74 155 292 600 899
150 11 26 48 80 124 67 141 265 544 815
200 10 22 41 69 106 58 120 227 465 697
250 919 36 61 94 51 107 201 412 618
300 818 33 55 85 46 97 182 374 560
350 716 30 51 78 43 89 167 344 515
400 715 28 47 73 40 83 156 320 479
*DATA IN ACCORDANCE WITH NFPA PAMPHLET NO. 54
NOMINAL PIPE SIZE,
SCHEDULE 40
TUBING SIZE, O.D., TYPE L
PIPE OR
TUBING
LENGTH,
FEET
Table 3 - Propane Gas Pipe Sizing
WARNING
TO PREVENT PROPERTY DAMAGE OR SERIOUS PERSONAL INJURY DUE TO
FIRE OR EXPLOSION CAUSED BY A PROPANE GAS LEAK, INSTALL A GAS
DETECTING WARNING DEVICE.
IF THE PROPANE GAS UNIT IS INSTALLED IN AN EXCAVATED AREA OR A
CONFINED SPACE, A WARNING DEVICE IS REQUIRED DUE TO:
• PROPANE GAS IS HEAVIER THAN AIR AND ANY LEAKING GAS CAN
SETTLE IN ANY LOW AREAS OR CONFINED SPACES.
• PROPANE GAS ODORANT MAY FADE, MAKING THE GAS UNDETECTABLE
EXCEPT WITH A WARNING DEVICE.

10
ELECTRICAL WIRING
has good air circulation.
Movement of air must not be obstructed by furniture, door,
draperies, etc. The thermostat must not be mounted where
television, etc. Consult the Instruction Sheet packaged with
thermostat for mounting instructions.
Five ton models have two stages of heating and two stages
of mechanical cooling. Units which have economizers may
use thermostats with two or three stages of cooling.
All other units have one stage of heating and one stage of
mechanical cooling. Units which have economizers may use
thermostats with one or two stages of cooling.
The units are designed for operation on 60 hertz current
and at voltages as shown on the rating plate. All internal
wiring in the unit is complete. It is necessary to bring in the
power supply to the contactor as shown on the unit wiring
diagram which is supplied with each unit. 24 volt wiring must
be connected between the unit control panel and the room
thermostat.
Thermostat Wiring - Single Stage Models
From
Unit
Single Stage Heating & Cooling Thermostat Diagram
Thermostat Wiring - Two Stage Models
R C W1W2 GY1 Y2
RY2
CY1
W1 G
W2
Furnace Integrated
Control Module
Thermostat
Two-Stage Heating
with
Two-Stage Cooling
Two-Stage Heating with Two-Stage Cooling
Thermostat Diagram
To use a single stage thermostat, move jumper located to the
left of the terminal strip labeled “Stage Delay” from NONE to
“5” or “10” minutes. This selection will cause the control to
shift to HIGH STAGE. This option controls both cooling and
heating modes. If the jumper is not moved, only low-stage
cool and low-stage heat will operate.
5 MINUTE DELAY
PERIOD WITH
JUMPER IN THIS
POSITION
10 MINUTE DELAY
PERIOD WITH
JUMPER IN THIS
POSITION
Two-Stage Heating (timed) and Two-Stage Cooling (timed)
with Single Stage Thermostat Diagram
Refer to the unit wiring diagram for electrical connections.
When installed, the unit must be electrically grounded in ac-
cordance with local codes or in the absence of local codes,
with the National Electrical Code, ANSI/NFPA No. 70, and/
or the CSA C22.1 Electrical Code. Ensure low voltage con-
nections are waterproof.
WARNING
TO AVOID THE RISK OF ELECTRICAL SHOCK, WIRING TO THE UNIT MUST BE
POLARIZED AND GROUNDED.
CAUTION
T
O AVOID PROPERTY DAMAGE OR PERSONAL INJURY DUE TO FIRE, USE
ONLY COPPER CONDUCTORS.
CAUTION
TO PREVENT IMPROPER AND DANGEROUS OPERATION DUE TO WIRING ERRORS,
LABEL ALL WIRES PRIOR TO DISCONNECTION WHEN SERVICING CONTROLS.
VERIFY PROPER OPERATION AFTER SERVICING.

11
For unit protection, use a time delay fuse or hacr circuit
breaker that is in excess of the circuit ampacity, but less than
or equal to the maximum overcurrent protection device. DO
NOT EXCEED THE MAXIMUM OVERCURRENT DEVICE
SIZE SHOWN ON UNIT DATA PLATE.
All line voltage connections must be made through weath-
must be in approved weatherproof conduit. Low voltage wir-
ing from the unit control panel to the thermostat requires
coded cable. See below for ground level and rooftop wiring.
CIRCULATING AIR AND FILTERS
Units can easily be converted from horizontal to down-dis-
-
stallations, the installer should measure the total external
static and review the blower performance charts before per-
forming the installation. In some installations it will be neces-
Horizontal Air Flow
Duct Cover Installation
Cut insulation around bottom openings and remove panels
from the bottom of the unit, saving the screws holding the
panels in place.
NOTE: Single phase models require installation of hori-
section for chassis sizes.
Duct systems and register sizes must be properly designed
for the C.F.M. and external static pressure rating of the unit.
Ductwork should be designed in accordance with the recom-
mended methods of Air Conditioning Contractors of Ameri-
ductwork exposed to the outdoors must include a weather-
proof barrier and adequate insulation.
A duct system should be installed in accordance with Stan-
dards of the National Board of Fire Underwriters for the In-
stallation of Air Conditioning, Warm Air Heating and Ventilat-
ing Systems. Pamphlets No. 90A and 90B.
The supply duct from the unit through a wall may be installed
without clearance. However, minimum unit clearances as
shown in the appendix must be maintained. The supply duct
should be provided with an access panel large enough to
inspect the air chamber downstream of the heat exchanger.
A cover should be tightly attached to prevent air leaks.
-
mension illustration in the appendix.
For down-discharge applications, the ductwork should be
attached to the roof curb prior to installing the unit. Ductwork
dimensions are shown in the roof curb installation manual.
If desired, supply and return duct connections to the unit
unit operating sound transmission.
CAUTION
T
O PREVENT PROPERTY DAMAGE DUE TO FIRE AND LOSS OF
EQUIPMENT EFFICIENCY OR EQUIPMENT DAMAGE DUE TO DUST AND LINT
BUILD UP ON INTERNAL PARTS, NEVER OPERATE UNIT WITHOUT AN AIR
FILTER INSTALLED IN THE RETURN AIR SYSTEM.
information.
Filters installed external to the unit should be sized in accor-
dance with their manufacturer recommendations. A throw-
feet per minute.
Filter Installation
VENTING
NOTE: Venting is self-contained. Do not modify or block.
prior to operation of the unit.

12
-
cated in the blower compartment.
Flue Hood and Bug Screen Installation
CONDENSATE DRAIN
A 3/4” NPT drain connection is supplied for condensate pip-
ing. An external trap must be installed for proper condensate
drainage. NOTE: Maximum torque is 10 in-lbs.
DRAIN
CONNECTION
UNIT 2" MINIMUM
FLEXIBLE
TUBING-HOSE
OR PIPE
3" MINIMUM
A POSITIVE LIQUID
SEAL IS REQUIRED
Drain Connection
NORMAL SEQUENCES OF OPERATION
This unit is equipped with an ignition control that automat-
ically lights the main burner. DO NOT attempt to light the
main burners by any other method.
Single-Stage Models:
NOTE: Ignition control begins timing the HEAT FAN OFF
delay. There is an adjustable HEAT FAN OFF delay of ap-
the HEAT FAN OFF delay time has elapsed, the blower will
de-energize. This allows any additional heat in the heat ex-
changer to be transferred to the conditioned space.
1. Thermostat calls for heat.
2. The induced draft blower energizes for a 15-second
pre-purge.
3. The spark igniter and gas valve energizes for 7 sec-
onds. NOTE: The igniter produces a very intense elec-
trical spark that ignites the gas.
4. Main burners light and control detects presence of
5. The 30-second HEAT FAN ON delay time begins after
the main burners light.
6. The unit delivers heat to the conditioned space until the
7. The gas valve de-energizes. The induced draft blower
continues operation for a 29-second post-purge.
Two-Stage Models:
If the call is for low stage heat, the induced draft blower
switches to low speed and the high stage gas valve closes 5
seconds after the main burners light. If call is for high stage
heat, induced draft blower remains at high speed and high
stage gas valve remains open.
NOTE: If a single stage thermostat is used, the control will
step to low stage after the main burners light and remain at
low stage for 5 or 10 minutes, depending on jumper position.
If the call for HEAT remains after the transition delay time ex-
pires, the control will transition from low stage to high stage.
post purge.
Two-Stage Models:
There is an adjustable HEAT FAN OFF delay of approxi-
unit is operating at high stage when the call for heat is re-
moved, the blower will operate for 30 seconds at high heat
speed then switch to low heat speed for the remainder of the
selected HEAT FAN OFF delay.
1. Thermostat calls for cooling. The compressor and out-
door fan are energized.
Two-Stage Models:
If the thermostat call is for low stage cooling, the compressor
and outdoor fan are energized at low stage. If the thermostat
call is for high stage cooling, the compressor and outdoor
fan are energized at high stage.
2. Approximately seven seconds later, the indoor fan starts.
3. The unit will deliver cooling to the conditioned space
4. The compressor and outdoor fan will be de-energized
when the thermostat opens.
5. The indoor fan continues to run for approximately 60

13
Two-Stage Models:
allows additional cooling from the indoor coil to be trans-
ferred to the conditioned space. Then, the indoor fan stops.
NOTE: A 180-second anti-short cycle is integral to the con-
trol and prevents recycling of the compressor.
1. Thermostat calls for FAN ONLY by energizing “G”.
2. Approximately seven seconds later, the indoor fan
starts.
Two-Stage Models:
Indoor fan is energized at low heat speed.
3. The indoor fan continues to run for approximately 60
seconds after “G” is de-energized.
Two-Stage Models:
The indoor fan is immediately de-energized once the ther-
mostat “G” is de-energized.
STARTUP, ADJUSTMENTS, AND CHECKS
This unit is equipped with an electronic ignition device to
automatically light the main burners. It also has a power vent
blower to exhaust combustion products.
On new installations, or if a major component has been re-
placed, the operation of the unit must be checked.
Check unit operation as outlined in the following instructions.
If any sparking, odors, or unusual sounds are encountered,
obstructions in or near the blower motors. Duct covers must
be removed before operating unit.
Rollout Protection Control
The rollout protection device opens, cutting power to the gas
into the heat exchanger. The rollout protection device is lo-
cated on the burner bracket. The reason for elevated tem-
peratures at the control should be determined and repaired
prior to resetting this manual reset control.
WARNING
T
O AVOID PROPERTY DAMAGE, PERSONAL INJURY OR DEATH DUE TO FIRE
OR EXPLOSION, A QUALIFIED SERVICER MUST INVESTIGATE THE REASON FOR
THE ROLLOUT PROTECTION DEVICE TO OPEN BEFORE MANUALLY RESETTING
THE ROLLOUT PROTECTION DEVICE.
Rollout Protection
Rollout Protection on Burner Bracket
Secondary Limit Control
The secondary limit control is located on the top of the blower
scroll assembly. This control opens when elevated tempera-
tures are sensed. Elevated temperatures at the control are
normally caused by blower failure. The reason for the opening
should be determined and repaired prior to resetting.
If the power to the unit is interrupted during the heating cy-
cle, it may cause the secondary limit to trip. Once the blower
compartment temperature drops below the limit reset tem-
perature, the limit will automatically reset.
Secondary
Control Limit
Back of Unit
Secondary Limit Control
Pre-Operation Checks
1. Close the manual gas valve external to the unit.
2.
3. Set the room thermostat to its lowest possible setting.
4. Remove the heat exchanger door on the side of the
unit by removing screws.
5. This unit is equipped with an ignition device which au-
tomatically lights the main burner. DO NOT try to light
burner by any other method.
6. Move the gas control valve switch to the OFF position.
Do not force.
7.
8. Smell for gas, including near the ground. This is im-
portant because some types of gas are heavier than
gas, immediately follow the warnings on page 3 of this
smell is noted, move the gas control valve switch to the
ON position.
9. Replace the heat exchanger door on the side of the
unit.

14
10. Open the manual gas valve external to the unit.
11. Turn on the electrical power supply to the unit.
12. Set the thermostat to desired setting.
Gas Valve
On/Off
Selector
Switch
INLET OUTLET
White-Rodgers 36G22 (Single Stage)
Inlet
Pressure Boss
Low Fire
Regulator Adjust
High Fire Regulator
Adjust Regulator
Vent
Outlet
Pressure Boss
White-Rodgers Model 36G54 (Two Stage)
Gas Supply And Manifold Check
Gas supply pressure and manifold pressure with the burners
NOTE: Use adapter kit #0151K00000S to measure gas
pressure on White-Rodgers 36G22 and 36G54 gas valves.
T
O
PREVENT
UNRELIABLE
OPERATION
OR
EQUIPMENT
DAMAGE
,
THE
I
NLET
GAS
SUPPLY
PRESSURE
MUST
BE
AS
SPECIFIED
ON
THE
UNIT
RATING
PLATE
WITH
ALL
OTHER
HOUSEHOLD
GAS
FIRED
APPLIANCES
OPERATING
.
CAUTION
The line pressure supplied to the gas valve must be within the
supply pressure can be measured at the gas valve inlet pres-
The supply pressure must be measured with the unit OFF. To
measure inlet pressure, use the following procedure.
Pressure Regulator
Adjustment
Gas Valve
On/Off
Selector
Switch
INLET
OUTLET
Inlet Pressure
Tap
Outlet Pressure
Tap
White-Rodgers Model 36G22 (Single Stage)
Inlet
Pressure Boss
Low Fire
Regulator Adjust
High Fire Regulator
Adjust Regulator
Vent
Outlet
Pressure Boss
White-Rodgers Model 36G54 (Two Stage)
1.
valve external to the furnace.
2. Turn OFF all electrical power to the system.
3. Inlet pressure tap connections:
White-Rodgers 36G22 or 36G54 valve:
4. Attach a hose and manometer to the inlet pressure
5. Turn ON the gas supply.
6. Turn On power and close thermostat “R” and “W” con-
tacts, or “R” and “W1” + “W2” for two-stage models, to
provide a call for heat.
7. Using a leak detection solution or soap suds, check for
leaks at t-
GAS AND REPAIR ALL LEAKS IMMEDIATELY!

15
8.
Adjust supply pressure using the Inlet Gas Supply
Pressure table shown below. If supply pressure read-
to pressure regulator, gas piping size, etc., and/or con-
sult with local gas utility.
Propane Gas
Natural Gas
Inlet Gas Supply Pressure
Minimum:5.0" W.C. Maximum :10.0" W.C.
Minimum:11.0" W.C. Maximum :13.0" W.C.
9. Turn OFF all electrical power and gas supply to the
system.
10. Remove the manometer hose from the inlet pressure boss.
White-Rodgers 36G22 or 36G54 valve:
Turn inlet pressure test screw in to seal pressure
12. Retest for leaks. If bubbles form, shut down gas and
repair leaks immediately.
13. Turn ON electrical power and gas supply to the system.
14. Turn valve switch ON.
T
O
PREVENT
UNRELIABLE
OPERATION
OR
EQUIPMENT
DAMAGE
,
THE
I
NLET
GAS
SUPPLY
PRESSURE
MUST
BE
AS
SPECIFIED
ON
THE
UNIT
RATING
PLATE
WITH
ALL
OTHER
HOUSEHOLD
GAS
FIRED
APPLIANCES
OPERATING
.
CAUTION
This valve is shipped from the factory with the regulator pre-
Consult the appliance rating plate to ensure burner man-
required, follow these steps.
1.
external to the unit.
2. Turn OFF all electrical power to the system.
3. Outlet pressure tap connections:
White-Rodgers 36G22 or 36G54 valve:
4. Attach a hose and manometer to the outlet pressure
5. Turn ON the gas supply.
6. Turn ON power and place unit into a heating cycle.
Single Stage Models:
Close thermostat “R” and “W” contacts.
Two-Stage Models
thermostat contacts “R” and “W1” contacts for low heat
stage heating ONLY; do not energize high stage heat.
7. Using a leak detection solution or soap suds, check for
-
OFF GAS AND REPAIR ALL LEAKS IMMEDIATELY!
8.
Adjust manifold pressure using the Manifold Gas Pres-
sure table shown below.
9. Regulator adjustment:
Single Stage Models -
move regulator cover screw from the outlet pressure regula-
tor and turn screw clockwise to increase pressure or coun-
terclockwise to decrease pressure. Replace regulator cover
screw.
Two-Stage Models
regulator adjust tower and turn screw clockwise to increase
pressure, or counterclockwise to decrease pressure.
Energize the “R”, “W1”, and “W2” contacts for high stage
heat. Remove regulator cover screw from the HI outlet pres-
sure regulator adjust tower and turn screw clockwise to in-
crease pressure or counterclockwise to decrease pressure.
Range Nominal
Low Stage 1.6 - 2.2" w.c. 2.0" w.c.
High or Single Stage 3.2 - 3.8" w.c. 3.5" w.c.
Low Stage 5.7 - 6.3" w.c. 6.0" w.c.
High or Single Stage 9.7 - 10.3" w.c. 10.0" w.c.
Manifold Gas Pressure
Gas
Natural
LP
10. Turn OFF all electrical power and gas supply to the
system.
11. Remove the manometer hose from the outlet pressure
tap.
12. Replace outlet pressure tap:
White-Rodgers 36G22 or 36G54 valve: Turn outlet
-
13. Turn ON electrical power and gas supply to the system.
14. Close thermostat contacts to provide a call for heat.
15. Retest for leaks. If bubbles form, SHUT OFF GAS AND
REPAIR ALL LEAKS IMMEDIATELY!
To measure the gas input use a gas meter and proceed as
follows:
1.
unit.
2. With the unit operating, time the smallest dial on the
meter for one complete revolution. If this is a 2 cubic
foot dial, divide the seconds by 2; if it is a 1 cubic foot
dial, use the seconds as is. This gives the seconds per
cubic foot of gas being delivered to the unit.
3. INPUT=GAS HTG VALUE x 3600 / SEC. PER CUBIC
FOOT

16
Example: Natural gas with a heating value of 1000 BTU per
cubic foot and 34 seconds per cubic foot as determined by
Step 2, then:
Input = 1000 x 3600 / 34 = 106,000 BTU per Hour.
NOTE: BTU content of the gas should be obtained from the
gas supplier. This measured input must not be greater than
shown on the unit rating plate.
4.
all pilot burners are operating.
Main Burner Flame Check
-
Check the temperature rise through the unit by placing ther-
mometers in supply and return air registers as close to the
unit as possible. Thermometers must not be able to sample
temperature directly from the unit heat exchangers, or false
readings could be obtained.
Checking Temperature Rise
1. All registers must be open; all duct dampers must be in
operated for 15 minutes before taking readings.
2. The temperature rise must be within the range speci-
NOTE:
between supply and return air.
With a properly designed system, the proper amount of tem-
perature rise will normally be obtained when the unit is op-
erated at rated input with the recommended blower speed.
If the correct amount of temperature rise is not obtained,
it may be necessary to change the blower speed. A higher
blower speed will lower the temperature rise. A slower blow-
er speed will increase the temperature rise.
NOTE: Blower speed MUST be set to give the correct air
temperature rise through the unit as marked on the rating
plate.
The total external static pressure must be checked on this
Total External Static Testing
1. Using a digital manometer measure the static pressure of
Total External Static
2. -
3. Add the two readings together.
NOTE: Both readings may be taken simultaneously and
read directly on the manometer if so desired.
4. Consult proper table for quantity of air.
If the external static pressure exceeds the minimum or max-
-
ters, undersized or poorly laid out ductwork.
Blower Speed Adjustments
Refer to the wiring diagram in the appendix to verify speed
tap settings.
All models are equipped with EEM motors. EEM motors are
constant torque motors with very low power consumption.
This motor is energized by 24V. Adjust the CFM for the unit
by changing the 24V low voltage leads to the speed terminal
block on the motor.
Single Stage Models:
Heating-White Lead Cooling-Yellow Lead
T1 - Low Speed T4 - Low Speed
T2 - Medium Speed T5 - High Speed
T3 - High Speed

17
Two-Stage Models:
Speed
Tap
Definition
Lead
Color
Speed
Tap
Definition
Lead
Color
T1
Low
Speed Heat
White T3
Low Speed
Cool
Purple
T2
High
Speed Heat
Brown T4
High Speed
Cool
Yellow
T5
High Speed
Cool Hi-Static
HEATING
COOLING
NOTE: -
perature rise shown on rating plate.
Limit Check
Check limit control operation after 15 minutes of operation
1. After several minutes the main burners must go OFF.
Blower will continue to run.
2. Remove air restrictions and main burners will relight
after a cool down period of a few minutes.
Adjust the thermostat setting below room temperature.
1. Main burners must go OFF.
2. Circulating Air Blower will continue to run for 120, 135
setting.
123
10
11
12
9
6
2 3
6
5
89
11 12
L2
L2L2
L2
D1 L1 L1 UNUSED HEAT COOL
FS
K2
K1
R8
R10
R3
K4
K3
R31
LED
1068-83-400A
C27
D3
R38
D9
D10
R34
R35
R4
R11
R42 D12
R36
D11
D14
C20
Z1
R29
R22
C13
R25
D5
D7
Control Board (Single Stage)
L OCOOL
HI C OO L
L OHE AT
HIHEAT
U6
U7
U4
U5
U3
K2
K1
P1
ECON
STAGE
DELAY
SPEEDUP
S W1
F AU L T
RECA L L
BLOWER
OFFDELAY
F1
R C W1 W2 GY1 Y2
Control Board (Two-Stage)
NOTE: If necessary, adjust fan OFF delay settings to obtain
satisfactory comfort level.
Unit Shutdown
1. Set the thermostat to lowest setting.
2.
3. Remove the heat exchanger door on the side of the
unit by removing screws.
4. Move the gas control valve switch to the OFF position.
Do not force.
5.
6. Replace the heat exchanger door on the unit.
7. If cooling and/or air circulation will be desired, turn ON
the electrical power.
NOTE: The outdoor temperature must be 60°F or higher be-
fore making adjustments to charge.
Compressor Protection Devices
The compressor includes components which are designed to
protect the compressor against abnormal operating conditions.
WARNING
T
O PREVENT PERSONAL INJURY OR DEATH, ALWAYS DISCONNECT ELECTRICAL
POWER BEFORE INSPECTING OR SERVICING THE UNIT.
A
LL COMPRESSOR
PROTECTION DEVICES RESET AUTOMATICALLY, ENERGIZING THE CONTACTOR
AND OUTDOOR FAN.
Refrigerant Charge Check
unit’s refrigerant charge must be checked. The unit comes
factory charged, but this charge is based on 325 CFM per
than above, the refrigerant charge must be adjusted to the
are charged using the super heat method at the compressor
suction line.
After superheat is adjusted it is recommended to check unit
sub-cooling at the condenser coil liquid line out. For charge
adjustments, see superheat chart below.

18
SUPERHEAT
Refrigerant gas is considered superheated whenever its
temperature is higher than the saturation temperature cor-
responding to its pressure. The degree of superheat equals
the degrees of temperature increase above the saturation
temperature at existing pressure.
1. Run system at least 10 minutes to allow pressure to
stabilize.
2.
near compressor with adequate contact and insulate
for best possible reading.
3. Refer to the superheat table provided for proper sys-
tem superheat. Add charge to lower superheat or re-
cover charge to raise superheat.
Superheat Formula = Suct. Line Temp. - Sat. Suct. Temp.
Refrigerant liquid is considered subcooled when its tem-
perature is lower than the saturation temperature corre-
sponding to its pressure. The degree of subcooling equals
the degrees of temperature decrease below the saturation
temperature at the existing pressure.
1. Attach an accurate thermometer or preferably a ther-
mocouple type temperature tester to the liquid line
close to the pressure switch.
2. Install a high side pressure gauge on the liquid access-
3. Record the gauge pressure and the temperature of the
line.
4.
pressure to temperature conversion is the amount of
subcooling.
Subcooling Formula = Sat. Liquid Temp. - Liquid Line
Temp.
EXAMPLE:
a. Liquid Line Pressure = 417
b. Corresponding Temp. °F. = 120°
c. Thermometer on Liquid line = 109°F.
To obtain the amount of subcooling, subtract 109°F from
-
tion sheet or technical information manual for the design
subcooling range for your unit.
Cooling Refrigerant Charging (5-Ton Models)
The 5-Ton models has a thermostatic expansion valve me-
tering device. To ensure the unit is properly charged for the
intended application, check the unit refrigerant sub-cooling
at the condenser. The refrigerant sub-cooling is a function of
outdoor ambient temperature and return air temperature of
the conditioned space. It is the installing contractors respon-
sibility to ensure the proper refrigerant sub-cooling at the
condenser is adjusted for each application. As the outdoor
ambient temperature rises the sub-cooling decreases and
as the outdoor ambient temperature lowers, the sub-cooling
increases. NOTE: Proper sub-cooling adjustment optimiz-
es cooling performance. Models equipped with thermostatic
expansion valve, charge the system to sub-cooling, range
shown on chart, when necessary, adjust expansion valve
stem for superheat setting.
Superheat Adjustment (5-Ton Models)
To adjust superheat, unscrew the cover from the expansion
superheat. Replace adjustment cap. Wait a minimum of 10
minutes between adjustments to allow time for the TXV and
pressures to stabilize.
NOTE: The expansion valve will not need adjustment for
most applications. Ensure system superheat is set within
range listed on chart.
Cooling Operation
NOTE: Mechanical cooling cannot be reliably provided at
ambient temperatures below 50° F.
1. Turn on the electrical power supply to the unit.
2. Place the room thermostat selector switch in the COOL
-
3. Set the room thermostat to the desired temperature.
TROUBLESHOOTING
The following presents probable causes of questionable unit
operation. Refer to Diagnostic Indicator Chart for an inter-
pretation of the signal and to this section for an explanation.
Remove the control box access panel and note the num-
Chart for an interpretation of the signal and to this section
for an explanation.
Fault Recall (Two-Stage Models ONLY)
The ignition control is equipped with a momentary push-but-
ton switch that can be used to display on the diagnostic LED
-
ture. Depress the push-button switch for approximately 2
seconds. NOTE: Do not hold for longer than 4 seconds.
Holding the button for 4 seconds or higher will erase the
-
the most recent fault to the least recent fault.

19
Internal Control Failure
If the integrated ignition control in this unit encounters an
diagnostic LED. If diagnostic LED indicates an internal fault,
check power supply to unit for proper voltage, check all fus-
es, circuit breakers and wiring. Disconnect electric power
replace control.
External Lockout
An external lockout occurs if the integrated ignition control
determines that a measurable combustion cannot be estab-
-
tion, the gas valve is de-energized, 15 second inter-purge
cycle is completed, and ignition is reattempted. The control
will repeat this routine three times if a measurable combus-
-
duced draft blower and go into a lockout state.
circulator blower at the heat speed and then begin a new
-
-
will automatically reset after one hour, or it can be reset by
removing the thermostat signal or disconnecting the electri-
indicates an external lockout, perform the following checks:
faulty limit, or a failed circulator blower can cause this limit
and limit. An interruption in electrical power during a heating
cycle may also cause the auxiliary limit to open. The auto-
matic reset secondary limit is located on top of the circulator
blower assembly.
blocked or cracked heat exchanger, a failed induced draft
device is a manual reset limit located on the burner bracket.
-
rected before resetting the limit.
coating on the sensor. Remove the sensor and carefully
clean with steel wool.
Check wiring for opens/shorts and miswiring.
Important: If you have to frequently reset your gas/electric
package unit, it means that a problem exists that should be
Pressure Switch Stuck Open
A pressure switch stuck open can be caused by a faulty
pressure switch, faulty wiring, a disconnected or damaged
blower.
If the control senses an open pressure switch during the pre-
purge cycle, the induced draft blower only will be energized.
If the pressure switch opens after ignition has begun the gas
begins, and the induced draft blower remains on. The diag-
Pressure Switch Stuck Closed
A stuck closed pressure switch can be caused by a faulty
pressure switch or faulty wiring. If the control encounters a
pressure switch stuck closed, the induced draft blower re-
Open Thermal Protection Device
If the primary limit switch opens, the gas valve is immediate-
ly de-energized, the induced draft and air circulating blowers
are energized. The induced draft and air circulator blowers
remain energized until the limit switch recloses. The diag-
A primary limit will open due to excessive supply air tem-
total external duct static, blower motor, blower motor speed
-
cally reset once the temperature falls below a preset level.
Primary Limit
A primary limit will open due to excessive supply air tem-
total external duct static, blower motor, blower motor speed
-
cally reset once the temperature falls below a preset level.
Auxiliary/Secondary Limit
faulty limit, or a failed circulator blower can cause this limit
and limit. An interruption in electrical power during a heating
cycle may also cause the auxiliary limit to open. The auto-
matic reset secondary limit is located on top of the circulator
blower assembly.

20
Rollout Limit
blocked or cracked heat exchanger, a failed induced draft
device is a manual reset limit located on the burner bracket.
-
rected before resetting the limit.
Flame Detected with Gas Valve Closed
combustion and air circulator blowers are energized. The di-
control can be reset by removing the power supply to the
unit or it will automatically reset after one hour. Miswiring is
the probable cause for this fault.
Low Flame Signal (Two-Stage Models ONLY)
Under some conditions, the fuel or air supply can create a
diagnostic LED. The unit will continue to operate until the
The automatic ignition control has a built-in feature that pre-
vents damage to the compressor in short cycling situations.
In the event of intermittent power losses or intermittent ther-
mostat operation, the ignition control will delay output to the
compressor contactor for three minutes from the time power
-
pressor contactor output is being delayed.
NOTE: Some electronic thermostats also have a built-in
compressor short cycle timer that may be longer than the
three minute delay given above. If you are using an elec-
tronic thermostat and the compressor has not started after
thermostat to complete its short cycle delay time.
High Pressure Switch/Low Pressure Switch
Some models include a high pressure cutout switch and/
or a loss of charge cutout switch. The high pressure cutout
switch protects the refrigeration system from excessive op-
erating pressures. The loss of charge cutout switch protects
the refrigeration system from very low operating pressures
due to a loss of refrigerant. Compressor operation will be
disabled if either of these devices opens. If either device
that a refrigeration system pressure switch is open.
MAINTENANCE
Have the gas heating section of the unit checked at least
once a year before the heating season begins, to be sure
blocked by debris, which would prevent adequate combus-
tion air and a properly operating vent system.
-
-
ing or cooling performance. Filter inspection should be made
at least every two months; more often if necessary because
of local conditions and usage.
last several years. However, should one become torn or un-
cleanable, it should be replaced.
important in installations with extended periods of direct
sunlight.
-
ed annually and cleaned as frequently as necessary to keep
Bearings on the air circulating blower motor, condenser mo-
tor and the combustion fan motor are permanently lubricat-
ed. No additional oiling is required.
-
fuel or combustion air supply, can be removed by carefully
Table of contents
Other Amana Fan manuals
Popular Fan manuals by other brands
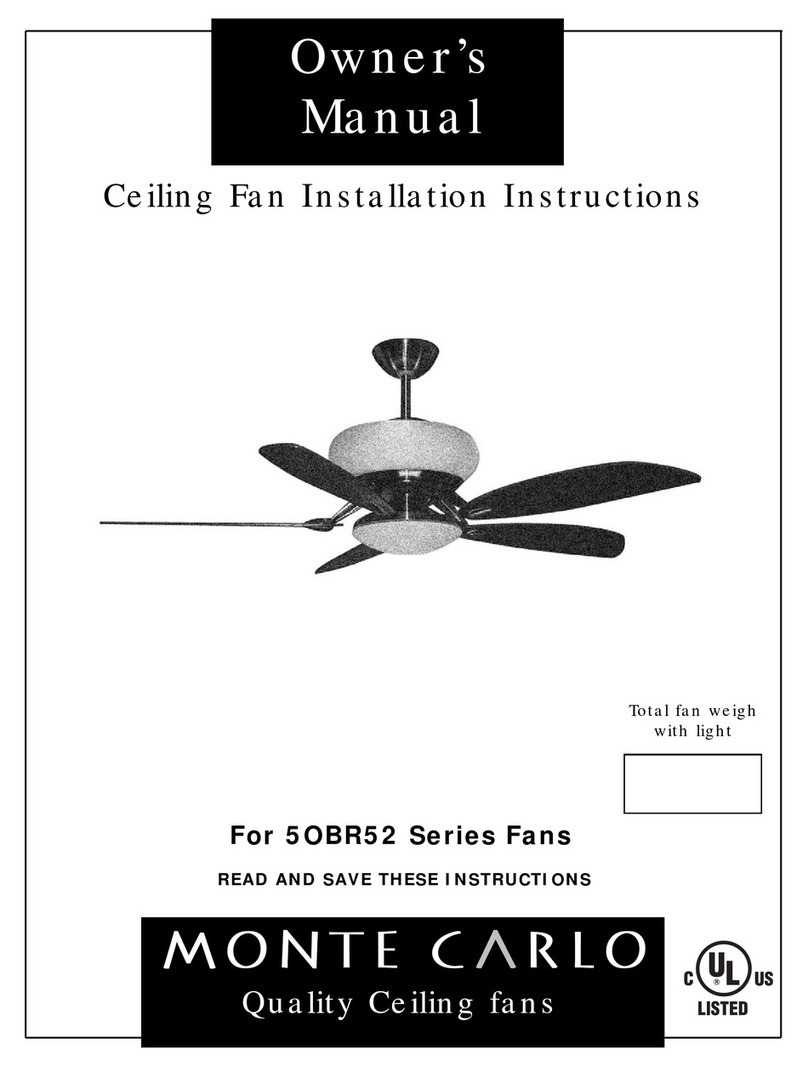
Monte Carlo Fan Company
Monte Carlo Fan Company 5OBR52 Series owner's manual

Modine Manufacturing
Modine Manufacturing Atherion ERM Installation and service manual

BLAUBERG Ventilatoren
BLAUBERG Ventilatoren BLABDUCTO Series user manual
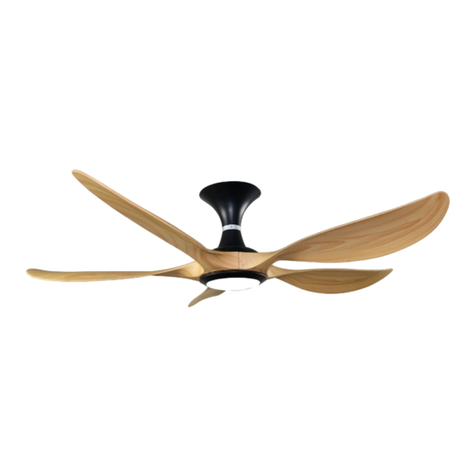
Rubine
Rubine Raffica 56-5BL user manual
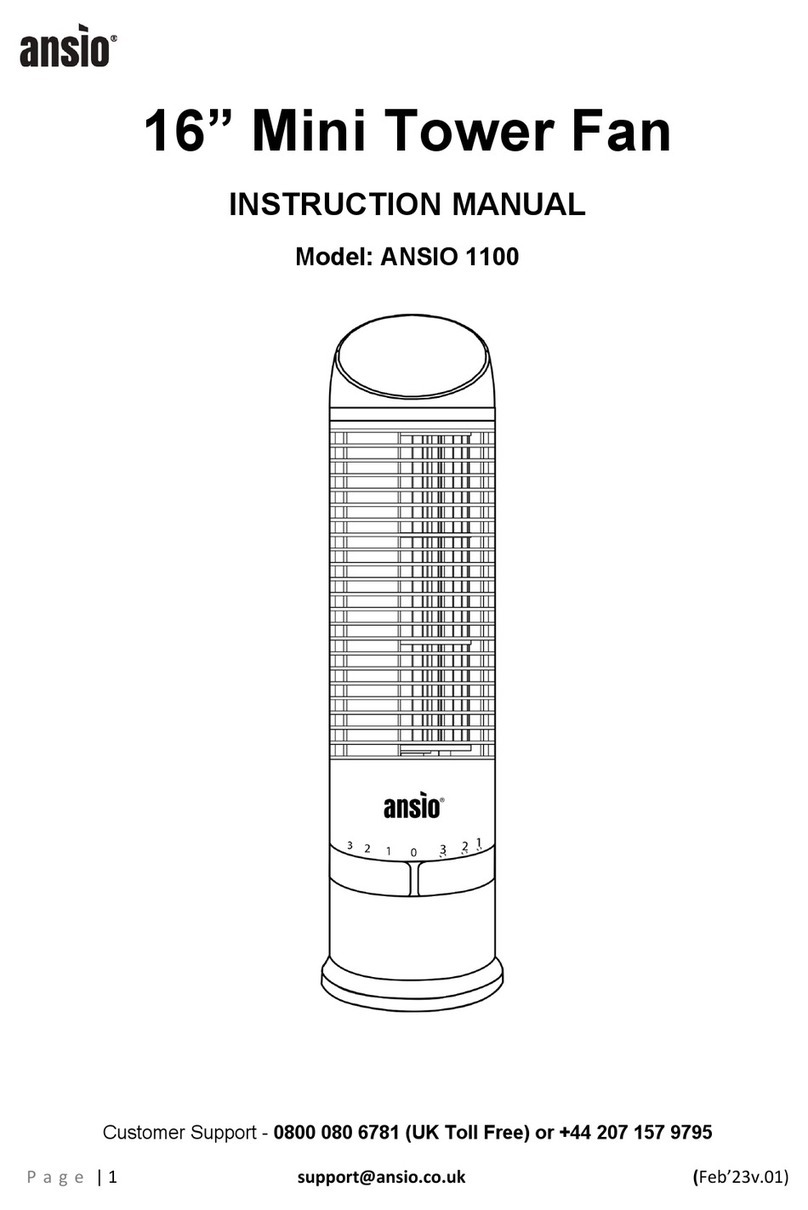
ansio
ansio 1100 instruction manual
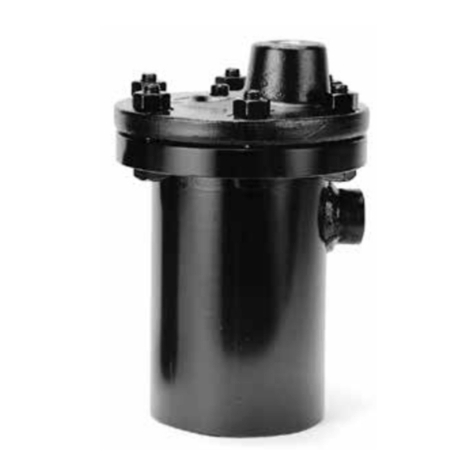
Armstrong
Armstrong HLAR Series instructions
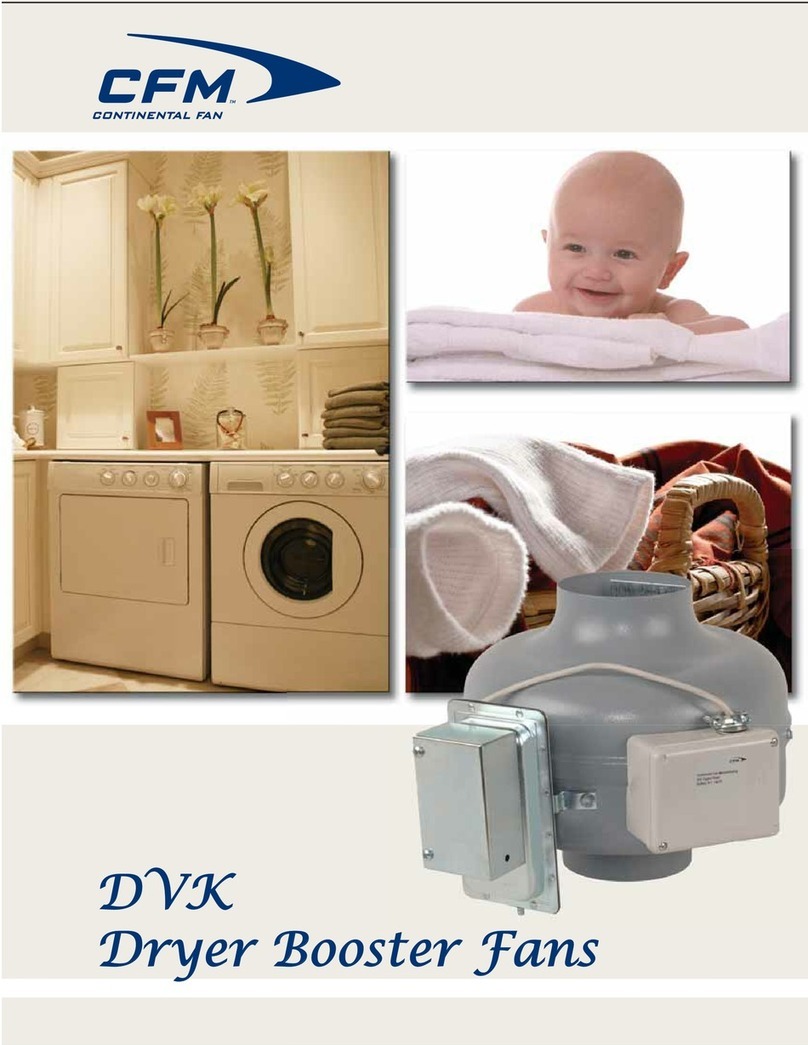
CFM
CFM DVK-0910 brochure
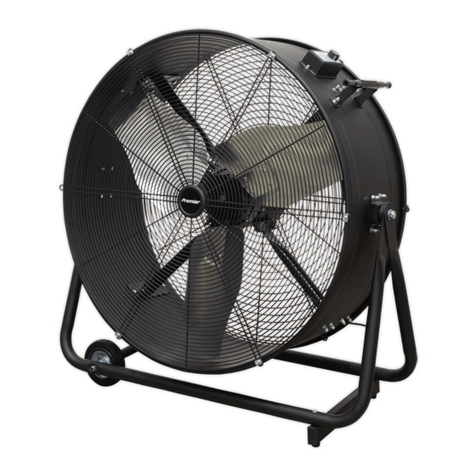
Sealey
Sealey HVD24P instructions
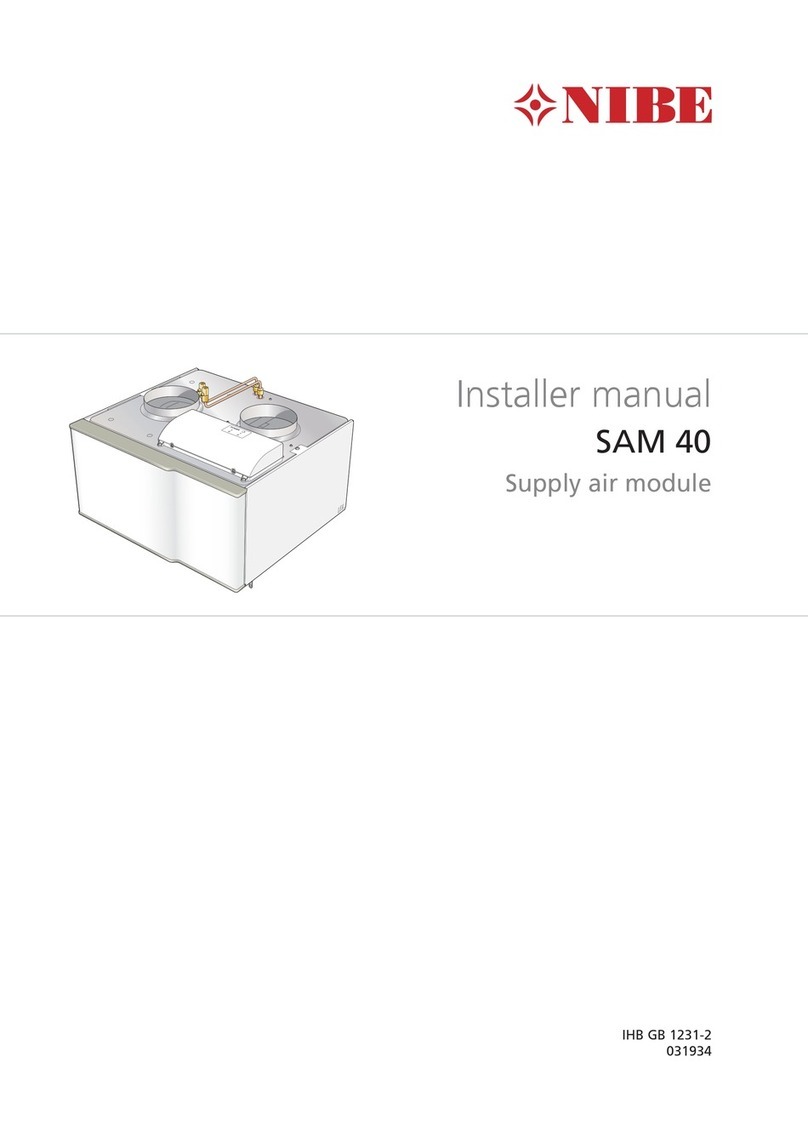
Nibe
Nibe SAM 40 Installer manual

iLiving
iLiving ILG8SF10V-ST owner's manual

Kooltronic
Kooltronic Guardian Series installation instructions

LUCCI Air
LUCCI Air AIRFUSION AIRLIE II ECO Series Installation, operation, maintenance & warranty information