Ametek Crystal Pressure APM CPF Series User manual

APM CPF Series Operation Manual
for Advanced Pressure Module

Contents
Overview ............................................................. 1
Introduction ............................................................1
Operation ............................................................ 2
Advanced Pressure Module (APM) Instructions............................2
Specifications ....................................................... 3
Communications ................................................... 6
Interface Description ....................................................6
Setting up the Serial Port for Remote Control .............................6
Using Commands .......................................................6
Remote Commands and Error Codes .....................................8
Entering Commands ...................................................10
APMCAL ............................................................. 11
Calibration Software ...................................................11
Support .............................................................. 12
Contact Us.............................................................12
Warranty ..............................................................12

Overview 1
APM CPF Series Operation Manual
Overview
INTRODUCTION
The Crystal APM CPF series of pressure modules allow you to add pressure measurement capability to your JOFRA process calibrator. The APM uses the same
reliable, high accuracy, digital temperature compensated technology found in the nVision, housed in a new rugged enclosure with an integrated cable to con-
nect to your JOFRA calibrator. In addition, you can connect the APM to a hand-held pressure calibrator to increase the range of that calibrator.
Supported JOFRA Calibrators
The Crystal APM has been engineered to work seamlessly with many of the most popular JOFRA calibrators. Below is a list of compatible JOFRA calibrators.
• AMC910
• ASC300
• ASC301
• ASC321
• ASC- 400
• ASC- 400 BARO
• HPC500
• HPC502
• HPC600
Note: This manual includes information on the APM CPF modules only. For details on the operation of JOFRA calibrators, please refer to their User Manuals.
What's Included
Each unit includes an APM CPF pressure module, a tting of your choice (NPT, BSP, or M20), NIST traceable calibration certicate, and AMETEK product CD.
Crystal Engineering calibration facilities are A2LA accredited, (#2601.01) which is internationally recognized by ILAC.
Note: A CPF adaptor tting is not included with 15 000 psi /1000 bar /100MPa APM models. The module connector is compatible with 1/4 medium pressure
tube system, HIP LM4 and LF4 Series, Autoclave Engr SF250CX Male and Female Series. See our CPF Data Sheet for additional adapter ttings.

Operation 2
APM CPF Series Operation Manual
Operation
ADVANCED PRESSURE MODULE APM INSTRUCTIONS
Pressure Connection
Crystal CPFSystem: Medium Pressure Female (MPF) (1/4” medium pressure tube system with 7/16-20 threads). See our CPF Brochure for further information.
U.S. Patent No. 8,794,677
CPF o-ring size and material: AS568A-012, Viton 80 durometer (P/N 3981).
For most applications CPF Fittings can be hand tightened for use up to 10 000 psi / 700 bar / 70 MPa (no tools required). Wrench tightening is recommended
(to achieve a metal to metal cone seal) for applications where chemical compatibility of the process uid and the o-ring are a concern, or for pressures above
10 000 psi / 700 bar / 70 MPa. We recommend a tightening torque of 120 in-lbs ±20 in-lbs. Please note this is only a fraction of the typical torque required to
seal a 1/4” NPT tting. If a torque wrench isn’t practical to use, the ttings can be assembled as follows: Hand tighten tting fully until the cone has bottomed
out. Tighten an additional 20º using a wrench. Apply a small amount of media-compatible lubricant to the gland threads and male cone to increase tting life,
reduce the likelihood of galling, and promote sealing.
! CAUTION: To achieve CPF maximum allowable working pressures no o-ring substitutions are allowed. See our CPF brochure and CES-003 CPF Safety
Guide available from the website at ametekcalibration.com for further detail.
! WARNING: Pressurized hoses and associated equipment are potentially dangerous. Slowly bleed o pressure from the system being pressurized prior
to connecting or disconnecting the Crystal APM.
Measuring Vacuum
All ranges of the APM can be used to measure moderate vacuum. Ranges 300 psi / 30 bar / 3 MPa and below are calibrated for vacuum use.
When measuring pressure less than ambient barometric conditions, a minus sign (-) will appear.
! CAUTION: The APM is not recommended for continuous use at high vacuum.
Overpressure Conditions
The APM will read pressure up to approximately 110% of the rated pressure range. All JOFRA indicators will display overpressure warnings. For example,
above 110% of the range, “OL” will display in red on an ASC- 400, indicating an Overload Alarm. The zero function does not aect when the “OL”is displayed to
indicate overpressure. So depending on the zero value, it is possible that the display will indicate “OL”without the maximum pressure being displayed.
For instance, if a 100 psi APM is zeroed when 30 psi is being applied, it will indicate that the overpressure condition has been reached at 80 psi.
(i.e., 110% x 100 psi – 30 psi = 80 psi).
Overpressure can aect accuracy, but the eect is only temporary unless the sensor has been damaged. See Specications for maximum allowable overpres-
sure ratings.

Specications 3
APM CPF Series Operation Manual
Specifications
Modules
Module
Range
0 - 30%
Gauge Full Scale
30 - 110%
Gauge Full Scale
psi ± (% Full Scale) ± (% of Reading)
psi
30 0.0075% 0.025%
100 0.0075% 0.025%
300 0.0075% 0.025%
1000 0.015% 0.05%
3000 0.015% 0.05%
10000 0.015% 0.05%
15000 0.015% 0.05%
bar ± (% Full Scale) ± (% of Reading)
bar
30.0075% 0.025%
10 0.0075% 0.025%
30 0.0075% 0.025%
100 0.015% 0.05%
300 0.015% 0.05%
700 0.015% 0.05%
1000 0.015% 0.05%
kPa / MPa ± (% Full Scale) ± (% of Reading)
kPa /
MPa
300 kPa 0.0075% 0.025%
10.0075% 0.025%
30.0075% 0.025%
10 0.015% 0.05%
30 0.015% 0.05%
70 0.015% 0.05%
100 0.015% 0.05%
Accuracy (Gauge)
0 to 30% of Full Scale . . . . . . . . . . . .± (0.0075% of Full Scale) or ± (0.015% of Full Scale)
30 to 110% of Full Scale . . . . . . . . . . ± (0.025% of Reading) or ± (0.05% of Reading)
Vacuum . . . . . . . . . . . . . . . . . . . . . . . . . For 100 psi /10 bar /1 MPa and lower:
± (0.06% of Full Scale*)
For 300 psi /30 bar /3 MPa:
± (0.06% of Full Scale*) ±1 LSD
*Full Scale = -14.5 psi / -1.0 bar / -100.0 kPa.
Accuracy specications include all eects of linearity, hysteresis, repeatability, temperature, and stability for one year.
Note: Exposure to environmental extremes of temperature, shock, and/or vibration may warrant a more frequent
recertication period.
APM modules must be exercised and re-zeroed whenever exposed to signicant changes in environmental conditions to achieve
these specications. To exercise a module, cycle the module between zero (ambient barometric pressure) and the pressure of inter-
est.
A properly exercised module will return to a zero reading (or return to the same ambient barometric reading).
! CAUTION: Advanced Pressure Modules (APM) are not recommended for continuous use at high vacuum.
Operating and Storage Temperature
Operating Temperature Range . . . -20 to 50° C (-4 to 122° F)
Storage Temperature Range. . . . . . -40 to 75° C (-40 to 167° F)

Specications 4
APM CPF Series Operation Manual
Accuracies, Ranges, and Resolutions
psi bar kPa/MPa Overpressure psi kg/cm2 inHg inH20 mmHg mmH20 kPa bar mbar MPa
30PSI 3.0 x 0.001 0.0001 0.001 0.01 0.01 10.01 0.0001 0.1
3BAR 3.0 x 0.001 0.0001 0.001 0.01 0.01 10.01 0.0001 0.1
300KPA 3.0 x 0.01 0.0001 0.1
100PSI 2.0 x 0.001 0.0001 0.01 0.1 0.1 10.01 0.0001 0.1 0.00001
10BAR 2.0 x 0.001 0.0001 0.01 0.1 0.1 10.01 0.0001 0.1 0.00001
1MPA 2.0 x 0.01 0.0001 0.1 0.00001
300PSI 2.0 x 0.01 0.001 0.01 0.1 0.1 0.1 0.001 10.0001
30BAR 2.0 x 0.01 0.001 0.01 0.1 0.1 0.1 0.001 10.0001
3MPA 2.0 x 0.1 0.001 10.0001
1KPSI 2.0 x 0.1 0.001 0.1 0.1 0.001 0.0001
100BAR 2.0 x 0.1 0.001 0.1 0.1 0.001 0.0001
10MPA 2.0 x 0.1 0.001 0.0001
3KPSI 1.5 x 0.1 0.01 0.1 10.01 0.001
300BAR 1.5 x 0.1 0.01 0.1 1 0.01 0.001
30MPA 1.5 x 10.01 0.001
10KPSI 1.5 x 10.01 10.01 0.001
700BAR 1.5 x 10.01 1 0.01 0.001
70MPA 1.5 x 10.01 0.001
15KPSI* 1.3 x 10.01 10.01 0.001
1000BAR*1.3 x 10.01 1 0.01 0.001
100MPA*1.3 x 10.01 0.001
XOrdering Information
Model P/N
Fitting
APM –
NPT........omit
G 1/4 B.....-BSP
M20x1.5 ...-M20
0.025%
of Reading
modules
0.05%
of Reading
modules
Resolutions shown are the maximum resolutions available. The resolution of your JOFRA device may be dierent.
* CPF adaptor tting is not included. CPF female connection is compatible with 1/4” medium pressure tube system, HIP LM4 and LF4 Series,
Autoclave Engr SF250CX Male and Female Series. See our CPF data sheet for additional adapter ttings.
SAMPLE PART NUMBERS
APM30PSI ..............30 psi APM with a 1/4”NPT pressure tting.
APM700BAR-BSP .....700 bar APM with a 1/4”BSP pressure tting.
APM10MPA-M20 ......10 MPa APM with an M20x1.5 pressure tting.

Specications 5
APM CPF Series Operation Manual
Pressure Conversions
Pressure conversion factors will vary, and be dependent on the JOFRA device connected to the APM. Refer to the documentation for your particular JOFRA
device for its specications.
Media Compatibility
Liquids and gases compatible with sensor and CPF tting system.
Wrench-tight . . . . . . . . . . . . . . . . . . . .316 Stainless Steel
Finger-tight. . . . . . . . . . . . . . . . . . . . . .316 Stainless Steel and Viton (internal CPF o-ring)
CE Statement
We declare that the APM is in accordance with the Electromagnetic Compatibility Directive, and the Pressure Equipment Directive per our declaration(s).

Communications 6
APM CPF Series Operation Manual
Communications
The APM interface uses a command – query – response protocol. Using this protocol the user can access the pressure measured by the module, as well as
control and monitor the status of all the essential functions of the module.
INTERFACE DESCRIPTION
The APM can be remotely controlled using a PC terminal or computer program running the module in an automated system. A USB-based serial port con-
nection is required for remote operation. The serial port connection also powers the module. Once connected, a user can write programs with Windows-based
languages like Visual Basic.
SETTING UP THE SERIAL PORT FOR REMOTE CONTROL
A USB to serial cable (available with part number APMCAL KIT) is used for serial communications from the APM to a computer. To connect the module to a
computer, attach it to a USB-to-serial cable, connected and installed on a PC. Connecting the module to the cable will automatically power it on.
Note: Be sure to set the appropriate COM port in your communications software: 9600 Baud; No parity; 8 Data bits; 1 Stop bit; No hardware ow control;
Software ow control (XON/XOFF) recommended.
To verify the module has connected successfully, enter *IDN? within the communications program. This command will return information from the module.
USING COMMANDS
Command Types
The APM may be controlled using commands and queries. All commands may be entered using upper or lower case. Refer to Remote Commands and Error
Codes for all available commands.
The commands are divided into the following types:
XModule Commands
Module Commands are used only by the module. For example, VAL? asks for the values displayed on the module display.
XCommon Commands
Common Commands are standard commands used by most devices. These commands always begin with “*”. For example, *IDN? tells the module to return
its identication.
XQuery Commands
Query Commands ask for Information, and always end with“?”. For example, VAL? returns the current pressure reading of the module.

Communications 7
APM CPF Series Operation Manual
Command Processing
The data entered into the module is processed as follows:
• Data is taken as 7-bit ASCII.
• Characters are discarded if their decimal equivalent is less than 32 (space), except 10 (LF) and 13 (CR).
• The most signicant data bit is ignored.
• Upper or lower case is acceptable.
• More than one command (Compound Commands) may be entered on one line. Commands are separated by semi-colons. For example,
PRES_UNIT KPA;FAULT?
Response Data Types
The data returned by the module can be divided into four types:
XInteger
For most computers and controllers, integers are decimal numbers ranging from -32768 to 32768. For example, FAULT? could return an integer of 117. Refer
to the Error Codes table for more information on error codes.
XFloating
Floating numbers have up to 5 signicant gures and exponents. For example, VAL? might return 25.345 PSI.
XCharacter Response Data (CRD)
Character Response Data is data returned as keywords. For example, PRES_UNIT? might return PSI.
XIndenite ASCII (IAD)
Indenite ASCII are any characters followed by a terminator. For example, *IDN might return CRYSTAL, APM003C, 678123, R130000.31/R08009.13.
Module Status
XError Queue
If an error occurs due to invalid input or buer overow, its error code is sent to a 15 entry error queue. An error code is read from the queue with the FAULT?
command. When the error queue is empty, FAULT? returns 0. The error queue is cleared when power is reset or when the clear command *CLS is entered.
XInput Buer
The module stores all received data in a 128 character input buer, which accommodates varying character input speeds.. If the input command/symbol
stream is too fast, the module will send the XOFF command when the input buer is full. When the module is able to continue to receive commands, it will
generate the XON command. The module can receive up to eight more characters after the XOFF command has been sent. If more characters are received, it
will stop receiving, clear the input buers, interrupt command execution, and ag the error 120 (Input Buer overow).

Communications 8
APM CPF Series Operation Manual
In order to avoid interruptions in the command execution process:
• Turn on software (XON / XOFF) ow control on the PC side.
• Avoid long command lines (lines more than 96 characters).
• Send the *CLR command before starting the communication procedure.
• Check the error buer sending the FAULT? command after the communication procedure is nished.
REMOTE COMMANDS AND ERROR CODES
The following tables list all the commands, and their descriptions, accepted by the APM.
Common Commands
Command Description
*CLS (Clear Status) Clears the error queue.
*IDN? (Identication Query) Returns the manufacturer, model number, and rmware revision of the module.
*RST Resets the module to the power up state.
Module Commands
Command Description
DAMP Turns Damp on or o.
DAMP? Returns if Damp is on or o.
FAULT? Returns the most recent error code.
PRES_UNIT Sets the pressure unit for the indicated display.
PRES_UNIT? Returns the pressure unit from the indicated display.
VAL? Returns the measured values.
ZERO_MEAS Zeros the pressure module.
ZERO_MEAS? Returns the zero oset of the pressure module.
CAL_STORE This command must be sent anytime a parameter has changed.

Communications 9
APM CPF Series Operation Manual
Parameter Units
Units Meaning
PSI Pressure in pounds per square inch.
KG/CM2 or KGCM2
Pressure in kilograms per square centimeter.
INHG Pressure in inches of mercury at 0°C.
INH2O4C Pressure in inches of water at 4°C.
INH2O20C Pressure in inches of water at 20°C.
INH2O60F Pressure in inches of water at 60°F.
INH2O68F Pressure in inches of water at 68°F.
MMHG Pressure in millimeters of mercury at 0°C.
MMH2O4C Pressure in millimeters of water at 4°C.
MMH2O20C Pressure in millimeters of water at 20°C.
CMH2O4C Pressure in centimeters of water at 4°C.
CMH2O20C Pressure in centimeters of water at 20°C.
MH2O4C Pressure in meters of water at 4°C.
MH2O20C Pressure in meters of water at 20°C.
MSW Pressure in meters of sea water.
FTH2O4C Pressure in feet of water at 4°C.
FTH2O20C Pressure in feet of water at 20°C.
FTH2O60F Pressure in feet of water at 60°F.
FTSW Pressure in feet of sea water.
BAR Pressure in bar.
MBAR Pressure in millibar.
KPA or KPAL Pressure in kiloPascal.
MPA or MPAL Pressure in MegaPascal.
TORR Pressure in Torr.
Error Codes
Error Number Error Description
117 Unknown command.
118 Bad parameter value.
120 Input Buer overow.
122 Output Buer overow.
200 Invalid index.

Communications 10
APM CPF Series Operation Manual
ENTERING COMMANDS
Commands for the APM may be entered in upper or lower case. At least one space must be entered between the command and parameter. All other spaces
are optional. Almost all commands for the APM are sequential, and any overlapped commands will be indicated as such. This section will briey explain each
of the commands and describe their general use. The descriptions will include any parameters that may be entered with the command, as well as the output
of the command.
Common Commands
X*CLS
Clears the error queue. Also terminates all pending operations. When writing programs, use before each procedure to avoid buer overow.
X*IDN?
Returns the manufacturer, model number, and rmware revision of the APM. For example, *IDN? will return AMETEK, APM 0, 1.00.
Module Commands
XDAMP
Enables a damping lter on the readings returned by the VAL? command. The lter is a rst-order smoothing lter with 90% damping percentage.
For example, DAMP ON, will turn the damping function on.
XDAMP?
Returns the current state of the damping function. For example, DAMP? will return ON if the damping function is on.
XFAULT?
Returns the error code number of an error that has occurred. The command may be entered when a previous command did not do what it was intended to
do. Refer to the Error Codes table for more information on error code numbers.
XPRES_UNIT
Used to set the pressure unit for the indicated display. For example, PRES_UNIT PSI will set the pressure unit to psi. Send CAL_STORE to save the new
parameters. Refer to the Parameter Units table for a complete list of available pressure units.
XPRES_UNIT?
Returns the current pressure unit being used.
XVAL?
Returns the value of the current measurement on the upper and lower display. For example, if the APM is measuring 5 psi, then VAL? will return 5.000000E+00, PSI.
XZERO_MEAS
Zeros the APM. Send CAL_STORE to save the new parameters.
XZERO_MEAS?
Returns the zero oset of the APM.

APMCAL 11
APM CPF Series Operation Manual
APMCAL
CALIBRATION SOFTWARE
APMCAL provides an easy way to calibrate your APM CPF Series Pressure Module. With a USB to serial cable, a computer running Windows, an APM module,
and the APMCAL software program, you can:
• Calibrate the APM with an easy-to-use Userspan Wizard.
• View and change the calibration date.
• View module details including model number, serial number, and rmware version.
• Update the rmware version of the APM.
Order part number APMCAL KIT to receive the program on CD, plus a USB to serial cable.

Support 12
APM CPF Series Operation Manual
Support
CONTACT US
USA
Crystal Engineering • California*
Tel +1 (800) 444 1850
Fax +1 (805) 595 5466
Manseld & Green • Florida
Tel +1 (800) 527 9999
United Kingdom
Tel +44 (0)1243 833 302
France
Tel +33 (0)1 30 68 89 40
general.lloy[email protected]
Germany
Tel +49 (0)2159 9136 510
info.mc[email protected]
Denmark
Tel +45 4816 8000
India
Tel +91 22 2836 4750
Singapore
Tel +65 6484 2388
China
Shanghai
Tel +86 21 5868 5111
Beijing
Tel +86 10 8526 2111
Guangzhou
Tel +86 20 8363 4768
*ISO 17025 accredited calibration lab, (A2LA #2601. 01).
If calling, have ready the model number, serial number, date of purchase, and reason for return. You will receive instructions for returning the device to us.
WARRANTY
Crystal Engineering Corporation warrants the APM (Advanced Pressure Module) to be free from defects in material and workmanship under normal use and
service for one (1) year from date of purchase to the original purchaser. It does not apply to batteries or when the product has been misused, altered or damaged
by accident or abnormal conditions of operation.
Crystal Engineering will, at our option, repair or replace the defective device free of charge and the device will be returned, transportation prepaid. However, if
we determine the failure was caused by misuse, alteration, accident or abnormal condition of operation, you will be billed for the repair.
CRYSTAL ENGINEERING CORPORATION MAKES NO WARRANTY OTHER THAN THE LIMITED WARRANTY STATED ABOVE. ALL WARRANTIES, INCLUDING IMPLIED
WARRANTIES OF MERCHANTABILITY OR FITNESS FOR ANY PARTICULAR PURPOSE, ARE LIMITED TO A PERIOD OF ONE (1) YEAR FROM THE DATE OF PURCHASE.
CRYSTAL ENGINEERING SHALL NOT BE LIABLE FOR ANY SPECIAL, INCIDENTAL OR CONSEQUENTIAL DAMAGES, WHETHER IN CONTRACT, TORT OR OTHERWISE.
Note: (USA only) Some states do not allow limitations of implied warranties or the exclusion of incidental or consequential damages, so the above limita-
tions or exclusions may not apply to you. This warranty gives you specic legal rights and you may have other rights which vary from state to state.

5274.E 1908
© 2019 Crystal Engineering Corporation
708 Fiero Lane, Suite 9, San Luis Obispo, California 93401-8701
Table of contents
Other Ametek Control Unit manuals
Popular Control Unit manuals by other brands
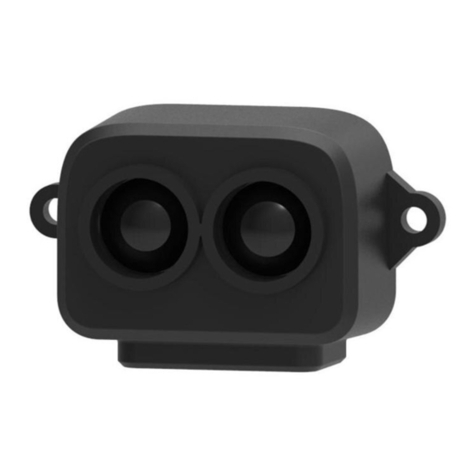
Benewake
Benewake TF-Luna product manual
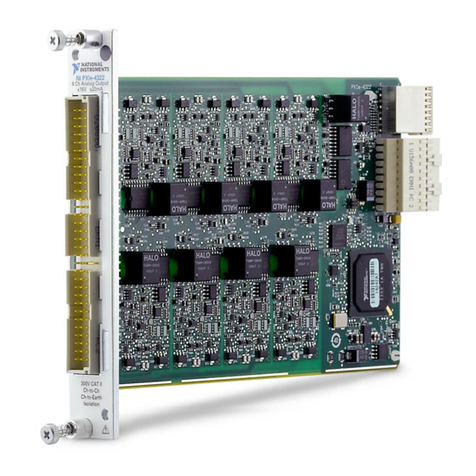
National Instruments
National Instruments PXIe-4322 installation guide
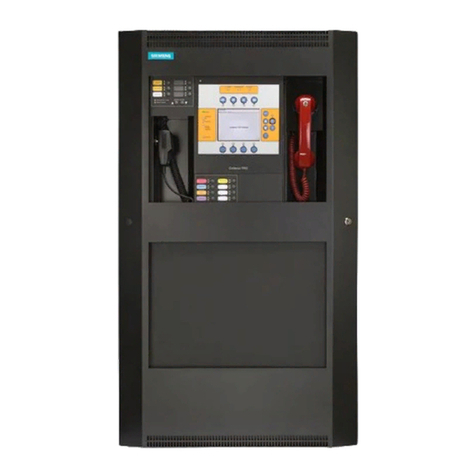
Siemens
Siemens FCM2041-U3 installation instructions
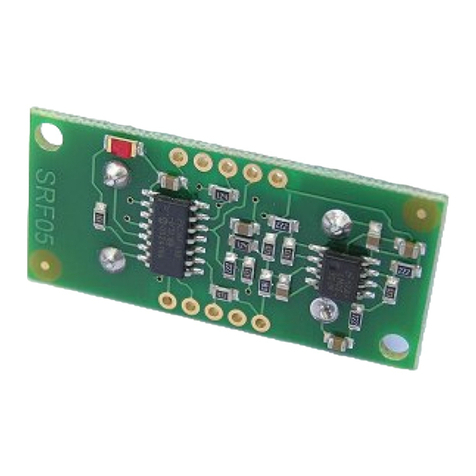
Futura
Futura SRF05 Technical specification

Viega
Viega 2275.2 Instructions for use

Zodiac
Zodiac Jandy Pro Series Installation and operation manual