amiad ICS-TCP Series Manual

AmiadUSA Ltd.
Tel: 704.662.3133
E-mail: info@amiadusa.com
120-J Talbert Road
Fax: 704.662.3155
Web: www.amiadusa.com
Mooresville, NC 28117
AMIAD WATER SYSTEMS
ICS-TCP Series
Installation, Operation
and Maintenance
Instructions
Disclaimer:
This document and the information enclosed within it contain restricted and/or privileged information that are intended only for
usage by authorized Amiad technicians. If you are not a qualified Amiad technician you must not take any action in reliance on this
document, unless permitted by Amiad.
None of the procedures provided in this file may be used in any form or by any means without permission from Amiad.
If you received this file in error please notify Amiad immediately.
The confidential nature of and/or privilege in the file enclosed is not waived or lost as a result of a mistake or error in this file.
Amiad accepts no liability whatsoever, whether it was caused by:
1. Accessing or other related actions to this file.
2. Any links, procedures or materials provided/attached to this file.
Amiad assumes that all users understand risks involved within this file and/or its attached materials.
All the procedures, drawings, pictures and/or any other information provided in this document are presented as general
information only; they can be altered, removed or changed without any further notice by Amiad.
This document does not replace any certified drawing, procedure or information provided by Amiad in reference to a specific
customer, site or project.
All rights reserved.
1 of 34

AmiadUSA Ltd.
Tel: 704.662.3133
E-mail: info@amiadusa.com
120-J Talbert Road
Fax: 704.662.3155
Web: www.amiadusa.com
Mooresville, NC 28117
Table of Contents
2 of 34
Table of Contents (page 2)
Introduction (page 3)
General Description (page 3)
Pre Assembly & Start-up Checks (page 3)
Startup and Operation (page 4)
Maintenance (page 5)
Trouble Shooting (page 7)
Pump Data and Curve (page 9)
Pump manual (page 11)
Electrical Manual (page 22)
Warranty (Page 33)

AmiadUSA Ltd.
Tel: 704.662.3133
E-mail: info@amiadusa.com
120-J Talbert Road
Fax: 704.662.3155
Web: www.amiadusa.com
Mooresville, NC 28117
Introduction:
Amiad filtration equipment has been designed to give long, trouble-free service when properly
installed, operated and maintained. This manual contains important installation procedures and
should be read prior to installing. This manual is also a guide for proper filter operation
maintenance and winterizing. It is important that maintenance personnel review this manual
carefully, including the Safety Precautions and Warnings before performing any maintenance on this
sand media water filter.
Note that the recommendations on the frequency service are minimums, and where operating
conditions are severe, the service should be performed more often. For each required service,
follow the procedures outlined under the Maintenance Procedures section in this manual. If
additional information beyond the scope of this manual is required, contact your local Amiad
Representative or the factory.
General Description:
The ICS-TCP basin cleaning system and side stream system are compact filter packages for the
removal of grit, airborne particles and scale from the cooling tower water in order to avoid
system failing.
The system use the ICS Separator with centrifugal-action performance, Amiad quality,
reliability, to control buildup of solid with in a heat transfer system. The system reduces
maintenance of the system, while increasing cost effectiveness as reduced blowdown and
reduced chemicals provide additional savings.
Basin sweeping ICS-TCP Systems provide circulation and agitation of the cooling tower
basin. Directing the flow to the filter the system can reduce buildup of solids in the tower.
The condenser water ICS-TCP is a side stream after the main circulation pumps and returns
back into the condenser water line, providing removal troublesome particulates that cause
maintenance issues.
Pre Assembly & Start-up Checks:
Only licensed or trained electricians and pipe fitters should install ICS-TCP systems.
Pad should be level and structurally sound for the application and equipment.
Proper anchor bolts should be sized correctly for the application to secure unit.
All piping to the and from the filter is to be supported.
Suction line is to be sized for 5ft/sec with pipe length not to exceed 30’. Long runs with
elbows and fittings should be calculated for head loss to make sure pump receives proper
NPSH.
Proper gaskets and treaded sealants are required for proper sealing of the system. If you
need recommendations please contact Amiad.
Only tighten fittings, nuts & bolts, threads as required to prevent leaks.
Power should be supplied to the unit with proper conductor size and voltage. The wiring
will need to be arranged for proper pump rotation for three phase systems. It is
recommended that this is performed by a trained electrician. Motor name plate provides
necessary information required for electrical.
3 of 34

AmiadUSA Ltd.
Tel: 704.662.3133
E-mail: info@amiadusa.com
120-J Talbert Road
Fax: 704.662.3155
Web: www.amiadusa.com
Mooresville, NC 28117
Once fitted and wired allow water to flow into the pump, only bump the motor for rotation
at this time. Caution….bumping a dry motor will damage the seals and is not a
warranty event. Reverse terminal leads as required.
Start-up and Operation:
1. The pump suction strainer needs to be filled with water before starting the Pump (Tower
Clean Systems only). Partially close (approximately 25%) the discharge valve and make
sure that the suction valve is fully open. Start the pump and observe the pressure gauge
which reads the discharge pressure of the pump at the inlet of the separator. The needle of
the gauges might flicker for a few seconds and will then settle, indicating that any air in the
system is being bled off naturally. If it continuously flickers and if the pump cavitates for
more than a minute, bleed-off air from the system.
Once pressure has reached 20 psi or more (Tower Clean System) or 15 psi (Side Stream
System), slowly open the discharge valve to ensure proper pump operation. If the valve
cannot be fully opened without the pump cavitating, be sure there are the correct number
of sweeper jets installed downstream of the Tower Clean System. In a Side Stream System
application the valve may need to be adjusted to ensure proper backpressure on the pump.
This is normal.
NOTE:
Make sure that all suction valves (from the source of water to the pump intake) are fully
opened when the pump is running. Operating the system with a partially closed suction
valve can damage the pump and/or affect the system's performance. Each model requires
a minimum liquid submergence level (above the pump intake) to meet the pump's Net
Positive Suction Head Required (NPSHR) to avoid air intrusion or cavitation (vortexing at
point of source). See appropriate pump curve included with your submittal. This is also very
important when Amiad sweeper jets are in use.
Entrapped air will always seek the highest elevation in the system. A valve in the system
outlet will be at the highest elevation. When partially opened during start-up, it will relieve
air from the system.
The Solids Recovery System, if installed with your system, must also be primed and
vented at the solids collection vessel (BGFS). Please see BGFS operating procedure
in this manual.
DO NOT DRY-RUN THE PUMP.All pumps require a flooded suction before
starting, using water as a lubricant for their seals. John Crane-type seals (e.g.,
Silicon Carbide Seals) can wear out in 20 seconds of dry operation. It only takes a
small amount of water to lubricate the seal, and it vaporizes during pump
operation. Also, when replacing the seals, avoid touching the Silicon Carbide faces;
oils, moisture and dirt from your fingers escalate seal wear.
4 of 34

AmiadUSA Ltd.
Tel: 704.662.3133
E-mail: info@amiadusa.com
120-J Talbert Road
Fax: 704.662.3155
Web: www.amiadusa.com
Mooresville, NC 28117
2. Negative Lift Applications
If the water level of the sump is lower than the centerline of the pump inlet, the use of
a self-priming pump might be necessary. Follow priming procedures every time the
pump is started.
Consult the factory for systems requiring suction lift.
3. Winterizing
In areas subject to freezing winter temperatures, protect the pump when not in
use by removing both drain plugs (from the pump volute and from the suction
strainer). Use a compressed air hose to remove any water trapped in the pump
casing or flush the system with antifreeze. Do not replace the plugs. Store them
in the strainer basket for the winter.
Alternatively, remove the pump and motor from the plumbing entirely. Store
them indoors in a warm and dry place.
The ICS Separator and the purge line should also be drained of liquid to
prevent damage from freezing. To remove trapped water from the separator,
use a compressed air. Alternatively, flush system with antifreeze is
recommended.
Heat tracing or pipe insulation may be used. Please contact your local supplier
of these products to ensure proper usage.
Maintenance:
1. ICS-TCP System start information is important, arecord of all readings (inlet and outlet
pressures, motor amperage draw and liquid flow rate) during start-up as reference.
Please record the required information and keep a copy for your records.
2. Record and compare these readings whenever periodic check-up and maintenance is
required. These records would be helpful in troubleshooting the system when a
problem occurs during the operational life of the system.
A. Suction Strainer Basket
The suction strainer basket is sized to allow a maximum pressure drop of 2 psi at the
specified flow rate. It will protect the pump, separator, flow control valves and other
equipment from becoming plugged by dirt and debris 1/4" in size and greater. The
strainer basket is easy to clean. Isolate the strainer by closing the isolation valves
5 of 34

AmiadUSA Ltd.
Tel: 704.662.3133
E-mail: info@amiadusa.com
120-J Talbert Road
Fax: 704.662.3155
Web: www.amiadusa.com
Mooresville, NC 28117
installed before the pump and after the separator outlet. These are not provided as a
standard option by Amiad, but are available if a valve kit is ordered. Loosen the nuts
or threaded stud and remove the lid. Remove the basket and clean. Inspect the '0'
ring or gasket and, if damaged, replace. Replace the lid and tighten the nuts.
B. Pump and Motor
Make sure that there are no leaks in the pump housing. If leaks occur at the back of
the volute casing, you may have a damaged the seal (pump seals are not covered
under warranty) and/or loose bolts. Replace and/or tighten as necessary.
Whenever maintenance or repair is needed for the pump, SHUT-OFF and LOCK-OUT
power into the panel feeding the pump; close the suction and discharge valves, open
drain plug/valve, making sure no air or hydraulic pressure is in the system before
unhooking the pump. Refer to Pump Manual.
Outside air is very important to cool the motor. The TEFC motor has a fan in the back.
Ensure that the fan is rotating when motor is energized. Zerk fittings were installed in
the front and back of the pump shaft/bearing housing. A small amount of grease might
be needed periodically to replenish the old grease in the housing. Whenever new
grease is injected, the old grease will ooze out on the opposite side and wipe clean.
Please see pump and motor manufactures IOM for additional details.
C. Control Panel
See control panel IOM in this manual for details.
D. Periodically check pressure gauges for proper readings. Verify operation by opening
and closing servicing valve installed prior to gauge. Stuck needles or damaged gauges
will need to be replaced.
E. BGFS (Solids Recovery)
These bag filters are in place to recover separated solids from the system from the
purge outlet of the ICS Separator.
Collected solids will need to be periodically removed from the BGFS. The bags can be
used over if clean up to 4-5 times before discarded. The change out of the bags can
be performed without disruption to the filtering process of the system.
The BGFS uses a differential pressure gauge/switch or gauges. The DP gauge will
have a red zone when need to change, gauges will indicate that the filter meets a 12
PSI differential and bag needs to be changed. The electrical contact with the DP
switch gives the ability for remote indication.
Steps for changing/maintenance/operation:
1. Close the manual valve on the purge line from the ICS Separator.
2. Close the valve on the line from the BGFS to pump suction. It is important to only
close this valve after pressure is released.
3. Open the lid on the vessel.
4. Remove the bag retainer from the vessel with the bag filter.
6 of 34

AmiadUSA Ltd.
Tel: 704.662.3133
E-mail: info@amiadusa.com
120-J Talbert Road
Fax: 704.662.3155
Web: www.amiadusa.com
Mooresville, NC 28117
5. Clean and or replace the bag in the retainer basket.
6. Inspect all seals or O-rings (replace as necessary).
7. Replace the basket and bag into the unit and secure the lid.
8. Open the from the purge line to the BGFS.
9. When the auto vent or manual vet indicated vessel is full open the valve from
BGFS to pump suction.
F. Purge valves
Purge valves typically do not require periodic maintenance. With ball valve or failsafe valve
it should be checked once a week for proper operation through a test purge. Also look for
leakage from the seals. Replace or repair as necessary. For flush setting please review the
electrical portion of this manual.
Trouble shooting:
Pump will not prime:
Make sure the strainer basket is not clogged (if applicable).
Make sure the strainer basket is positioned correctly (if applicable).
Tighten the strainer lid down completely (if applicable).
Make sure the strainer is full of water (if applicable).
Tighten all the fittings and seal all the joints on the suction side.
Open all the valves on the return and suction lines.
Remove and replace the pump seal if needed.
Check the compatibility of the pump and motor.
Check pump rotation. Reverse motor wire terminals if necessary.
Motor Runs Hot:
Motors will run warm to the touch. The motor starter thermal and
overload module will function to tum off the motor if there is an
overload current problem.
Factors which will increase the operating temperature:
The pump is installed in the direct sun.
Poor ventilation in the area the pump is located.
Low voltage is available to the pump.
The wiring is the incorrect size for the load.
The solids loading requires more than the pump's motor horsepower
rating.
The pump is operated above the full load Amp rating of the motor.
Motor is experiencing imbalance load (in case of 3 phase; it is doing a
single phase.)
Fan is broken/missing.
Motor does not start:
There is a safety/shock hazard. Have a qualified electrician perform
the testing. Opening the motor starter box does not shut off power
into the box; it only disconnects the starter module and control
transformer. Follow electro-mechanical safety lock-out procedure.
If the system does not start, open the motor control box and check for
power and/or blown control transformer fuses. If the motor overload
trips, check the overload amp setting. Adjust the overload module to
7 of 34

AmiadUSA Ltd.
Tel: 704.662.3133
E-mail: info@amiadusa.com
120-J Talbert Road
Fax: 704.662.3155
Web: www.amiadusa.com
Mooresville, NC 28117
the motor's full load amp rating. Replace the overload with the correct
overload module going from 460 to 230 system and re-wire the control
transformer and motor terminals inside the motor junction box. Do
not set or adjust to above full load amp rating.
Deadhead pressure cannot be met:
First determine if the pump motor is rotating in the correct direction.
Jog-start the motor control box hand switch off and on while observing
the motor shaft rotation.
If the pump is not rotating correctly, shut off the power and switch two
of the motor lead wires.
If the pump is rotating correctly, check for shut valves on the suction
line, a clogged suction line at inlet, a clogged strainer basket, or a
clogged pump.
Adjust the separator outlet valve to the required pressure drop across the
separator for the desired flow. If the flow rate cannot be obtained, check for
closed valves downstream of the separator, or restricted outlet piping.
Systems with Amiad Sweeper Jets, you can use the Sweeper Jets to act as a
control valve.
No solids in BGFS:
Purge valve to the inlet of the SRV is closed.
Air-locked in the system, bleed BGFS of trapped air. Follow BGFS
maintenance procedure.
Purge line is blocked. Isolate the system from pressure by closing the
purge line and liquid recovery line valves. Remove piping and clean
out the blockage or replace the appropriate components.
8 of 34

AmiadUSA Ltd.
Tel: 704.662.3133
E-mail: info@amiadusa.com
120-J Talbert Road
Fax: 704.662.3155
Web: www.amiadusa.com
Mooresville, NC 28117
Pump Data and Spare parts:
Amiad Pump Part No. 720401-000215
Amiad Pump Seal Kit Part No. 720401-000303
9 of 34

Pump Data Sheet - Scot Division of Ardox Corp.
Company: Amiad Filtration Systems
Name: ICS-TCP-900gpm-HH
Date: 12/3/2015
Pump:
Size: 096-10-6.0x5.0
Type: Endsuct-Encl Speed: 1750 rpm
Synch speed: 1800 rpm Dia: 9.25 in
Curve: 40.000.322 Impeller:
Specific Speeds: Ns: ---
Nss: ---
Dimensions: Suction: 6 in
Discharge: 5 in
Pump Limits:
Temperature: 300 °F Power: ---
Pressure: 175 psi g Eye area: ---
Sphere size: 1.25 in
Search Criteria:
Flow: 900 US gpm Head: 70 ft
Near miss: 5 % of Head
Fluid:
Water Temperature: 60 °F
SG: 1 Vapor pressure: 0.2563 psi a
Viscosity: 1.105 cP Atm pressure: 14.7 psi a
NPSHa: 10 ft
Motor: Size: 25 hp
Speed: 1800
Frame: 284T
Standard: NEMA
Enclosure: TEFC
Sizing criteria: Max Power on Design Curve
Selected from catalog: Scot.60 Vers: 10.1
---- Data Point ----
Flow: 900 US gpm
Head: 72 ft
Eff: 77%
Power: 21.4 hp
NPSHr: 10 ft
---- Design Curve ----
Shutoff head: 80.4 ft
Shutoff dP: 34.8 psi
Min flow: ---
BEP: 81% @ 1200 US gpm
NOL power:
23.1 hp @1263 US gpm
-- Max Curve --
Max power:
31.5 hp @1350 US gpm
US gpm
NPSHr - ft
18001600140012001000800600400
0200
10
20
Head - ft
% - Efficiency
0
10
20
30
40
50
60
70
80
90
1800
016001400
20
1200
40
1000
60
800600
80
400
100
200
81.3
9.25 in
10.25 in
7.8 in
10 hp
15 hp
20 hp
25 hp
30 hp
40 hp
Performance Evaluation:
Flow Speed Head Efficiency Power NPSHr
US gpm rpm ft % hp ft
1080 1750 66 79 22.4 11.2
900 1750 72 77 21.4 10
720 1750 75.2 68 19.8 9.4
540 1750 77.8 57 18.4 9
360 1750 79.2 41 17.2 9
10 of 34

11 of 34

12 of 34

13 of 34

14 of 34

15 of 34

16 of 34

17 of 34

18 of 34

19 of 34

INSTALLATION INSTRUCTIONS
TYPE 21 SHAFT SEAL
The seal assembly consists of these components:
ASPRING
BROTARY SEAL HEAD
CSTATIONARY SEAT - May
have an O-ring groove in seat (C)
or a rubber cup seat (CC).
CAUTION: This seal is a precision product and should
be handled accordingly. Be especically careful of the
lapped sealing surface of the rotary washer and
stationary seat.
THE SEAL IS SUPPLIED WITH
A PACKET OF LUBRICANT.
LAPPED RUNNING FACES
The lapped running surfaces of the rotary seal head
and stationary seat must be treated with care. KEEP
CLEAN. DO NOT SCRATCH. Use a clean, soft cloth
during installation. Protect the faces. Install both the
seat and rotary square to the shaft. Check the
stationary seat installation from behind the seal cavity
for squareness.
STATIONARY SEAT INSTALLATION (C)
Clean the seal seat cavity of the adapter and lubricate.
Lubricate the seat O-ring or cup and press the
stationary seat in seal cavity of the adapter squarely
and evenly using an arbor press and the cardboard disc
supplied with the seal. Be careful not to scratch or
touch the lapped surface of stationary seat.
Inspect the face of the stationary seat to be certain
there is no dirt on face. If there is any dirt or fingerprints
on the face, wipe it off carefully with a soft cloth.
ROTARY SEAL HEAD INSTALLATION (B)
Clean, polish and lubricate the shaft (or shaft sleeve).
Check lapped faces on the stationary seat and rotary
seal head. Be certain no dirt is on either face.
Lubricate lightly.
Slide the rotary seal head on the shaft with the carbon
rotating ring facing the stationary seat. Press the drive
band until the head seats firmly against the seat. Install
spring (and spring retainer washer if used). Install
impeller which will compress the spring to proper length
assuring correct pressure on the lapped faces.
CAUTION: Never operate the lapped running faces
dry. The liquid being handled ensures proper
lubrication.
In some cases a short period of operation is required
to clear up slight leakage.
NOTE: The lubricant supplied with the seal is the
only approved lubricant. DO NOT USE OTHER
LUBRICATING LIQUIDS!
61.000.172B
JANUARY 2000
SCOT
HOME OFFICE
• Cedarburg, WI 53012 • P.O. Box 286 • 262-377-7000 • FAX 262-377-7330
FACTORY BRANCHES
• Irvine, CA 92614 • 1881 Kettering • 949-756-8076 • FAX 949-756-9480
• Ft. Lauderdale, FL 33315 • 77 SW 20th Street • 954-524-6776 • FAX 954-764-3361
SCOT
DIVISION OF
ARDOX CORP.
Replaces March 1990
20 of 34
Table of contents
Other amiad Water System manuals
Popular Water System manuals by other brands
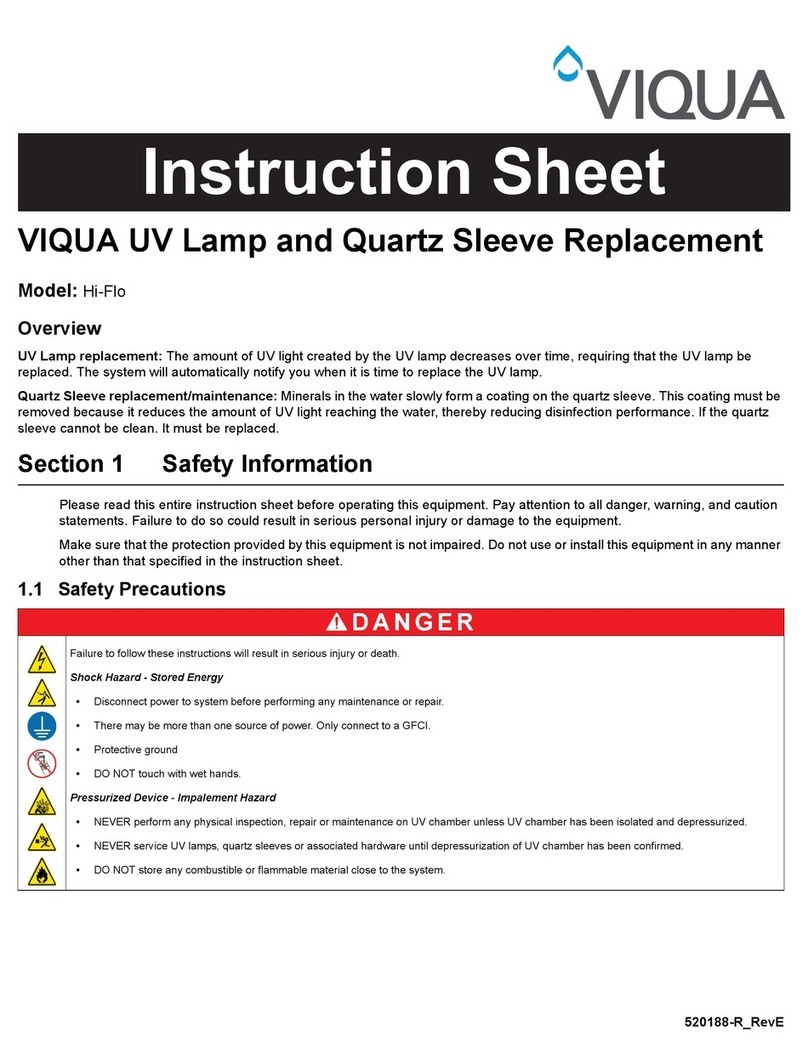
Viqua
Viqua Hi-Flo instruction sheet
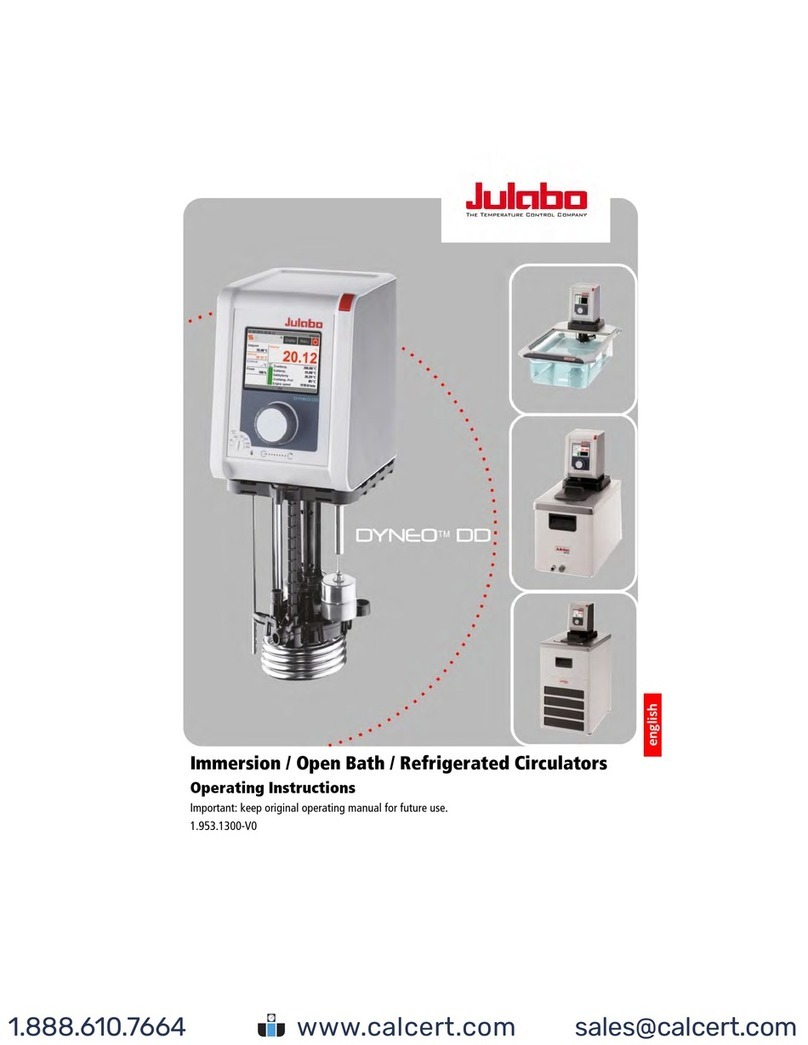
Julabo
Julabo DYNEO DD BT19 operating instructions
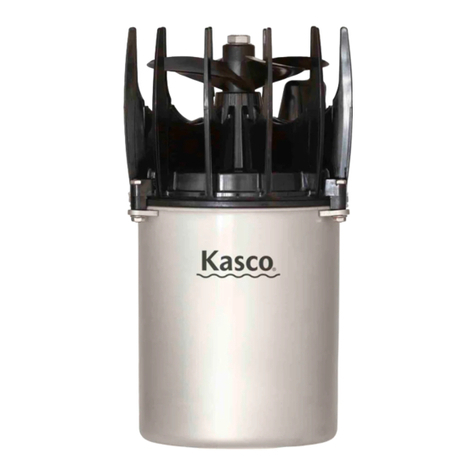
Kasco
Kasco AquatiClear 2400EC Operation & maintenance manual
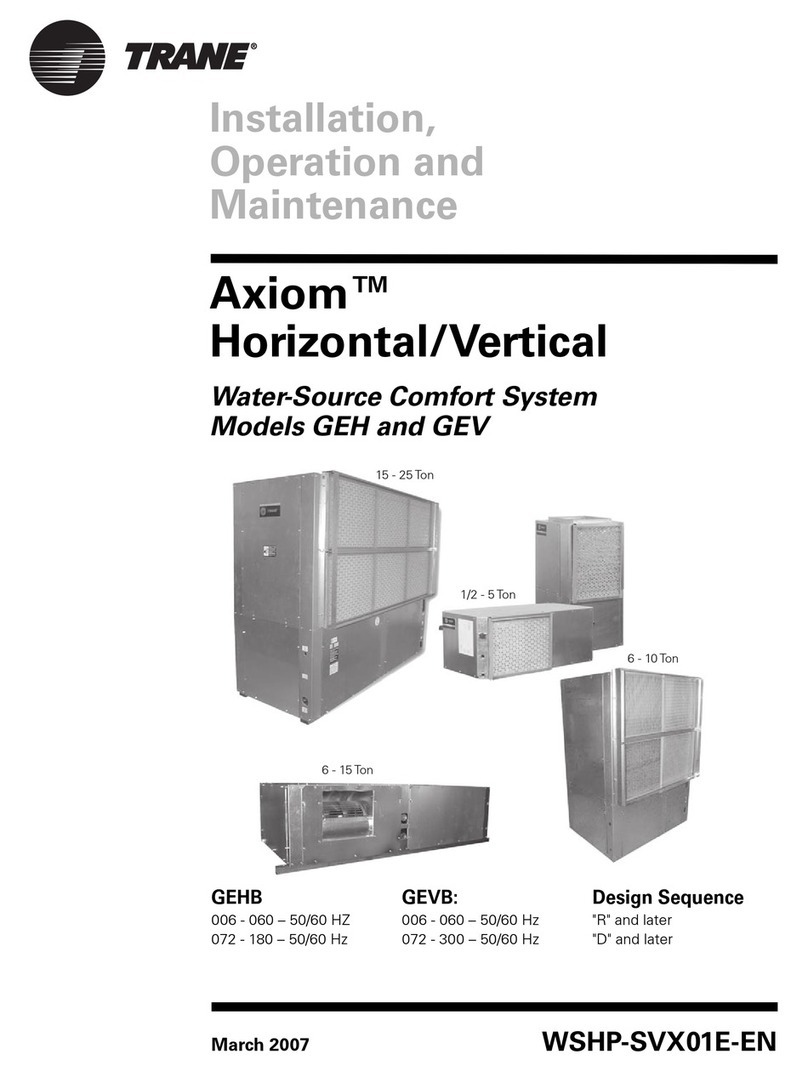
Trane
Trane Axiom GEHB 006 Installation, operation and maintenance
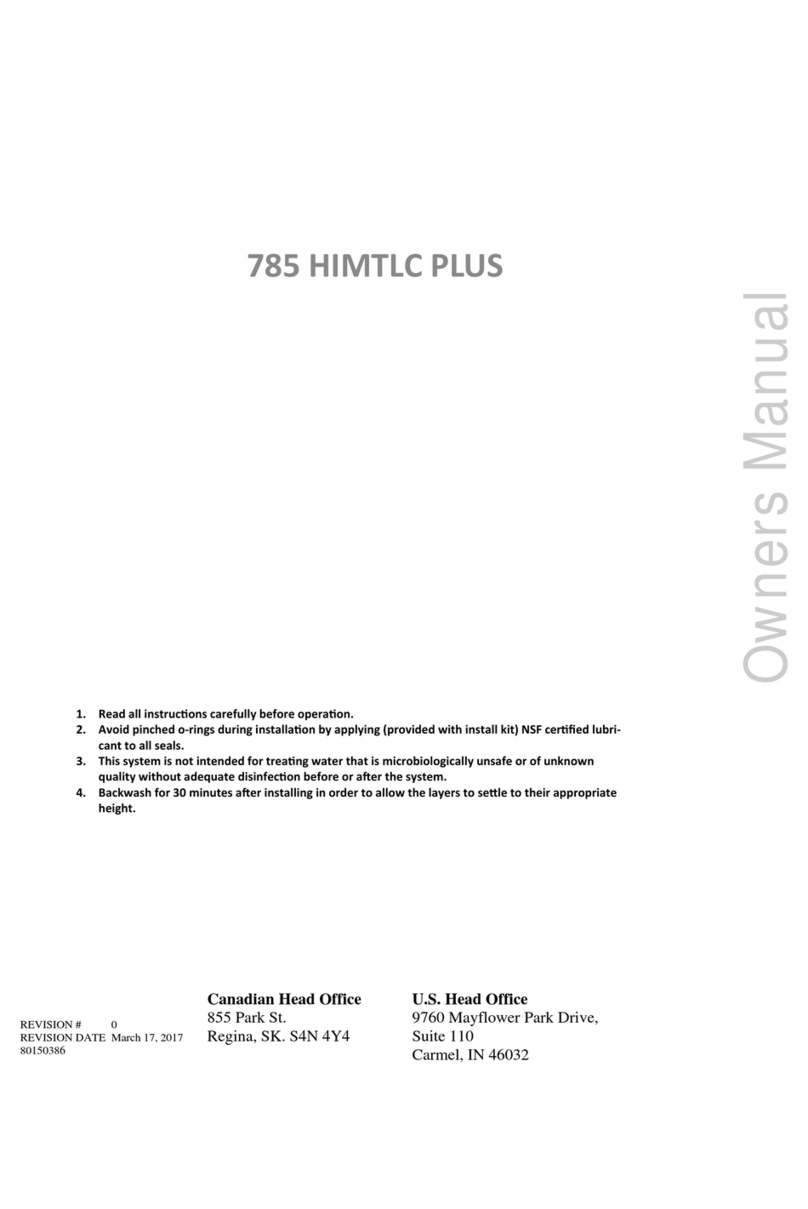
Canature
Canature 785 HIMTLC PLUS Series owner's manual

First Sales
First Sales XTS30 Installation instructions and owner's manual
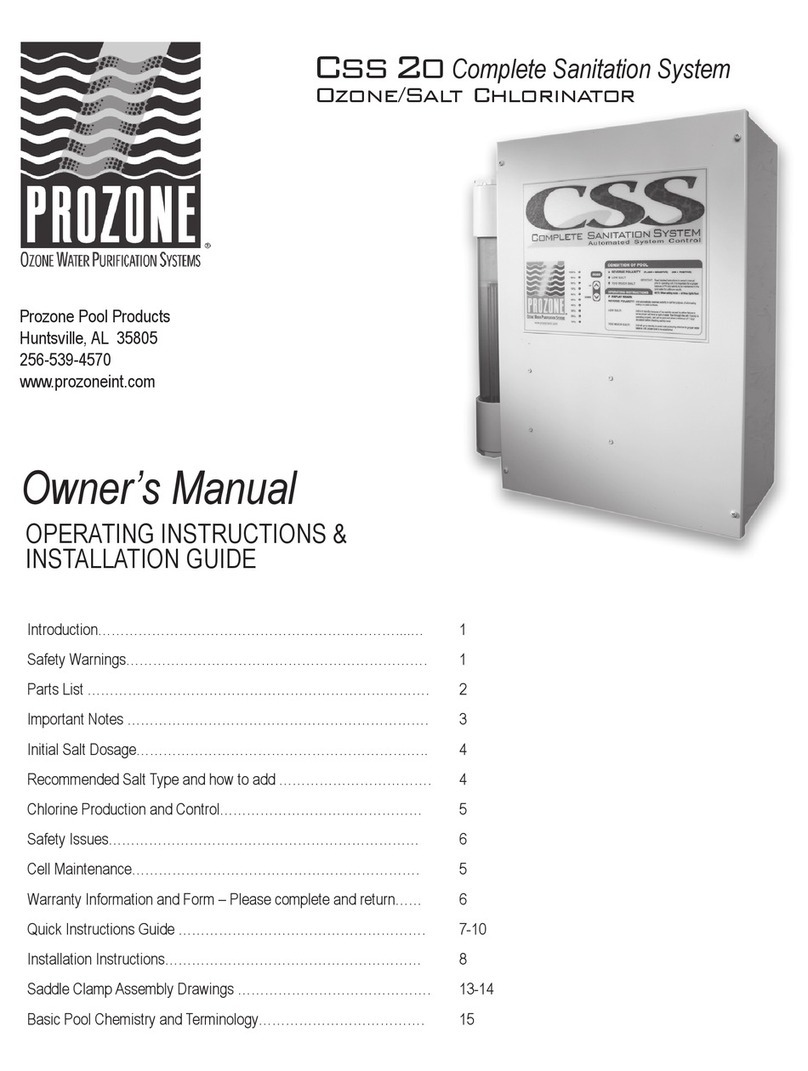
Prozone
Prozone CSS20 owner's manual
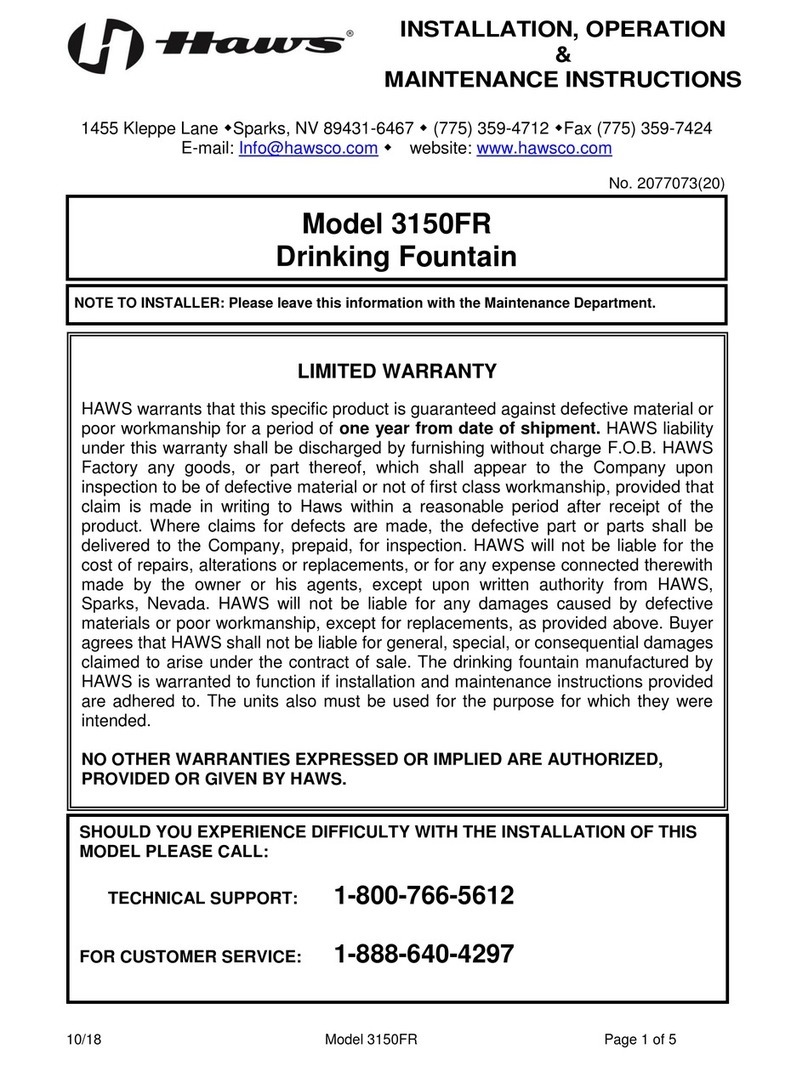
Haws
Haws 3150FR Installation, operation & maintenance instructions
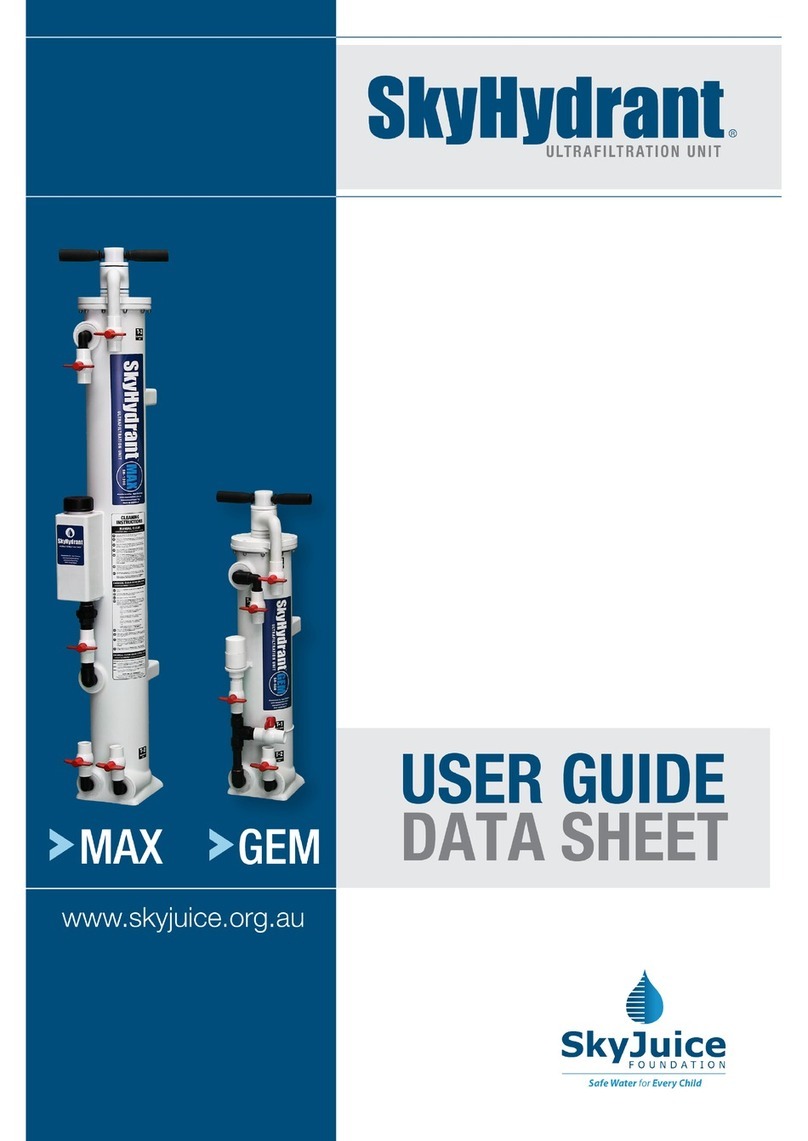
SkyJuice
SkyJuice SkyHydrant-GEM user guide

Armstrong
Armstrong E.2 Series Installation and operating instructions
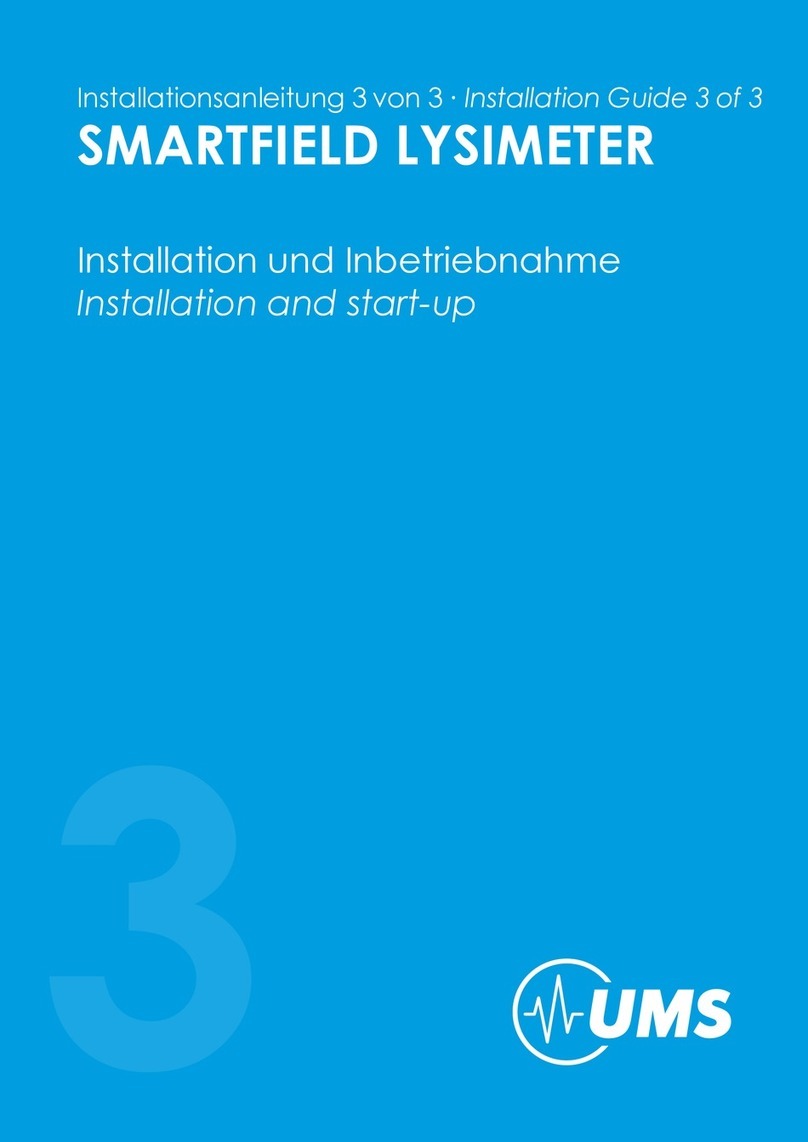
UMS
UMS SMARTFIELD LYSIMETER installation guide

Armstrong
Armstrong ASTRO Installation and operating instructions