Amkus Super Simo 240SS User manual

©Copyright AMKUS Rescue Systems, Inc. 2018 LAP-012 July 16, 2018 Rev01
Instructions for safe operation, installation, and maintenance.
DANGER Understand manual before use. Operating AMKUS Rescue Systems without understanding
the manual, receiving proper training, and using appropriate personal protective equipment
is a misuse of AMKUS equipment. This manual does not fully address safety. Additional
safety information is published in AMKUS Safety Manual LAA-001. Obtain manual at
amkus.com/resources/information.
Manual: 240SS
Super Simo Power Unit
AMKUS RESCUE SYSTEMS
amkus.com
4201 Montdale Drive, Valparaiso, IN 46383-4098 USA
800-592-6587 • 219-548-5000 • Fax 219-476-1669
Electrically driven, truck mounted, 10,500 PSI (720 bar) twin pump
hydraulic power unit for simultaneous operation of two rescue tools.
©Copyright Amkus Rescue Systems, Inc. 2016 LAA-001 April 15, 2016 Rev00
DANGER Understand manual before use. Operating AMKUS Rescue Systems without understanding the
manual, receiving proper training, and using appropriate personal protective equipment is a
misuse of AMKUS equipment. Obtain safety information at www.amkus.com/
This Safety Manual is intended to familiarize rescue workers and maintenance personnel with the safety messages of AMKUS
Rescue Systems, including powered rescue tools (rams, cutters, spreaders, combination tools), power units (electric or gasoline
driven), and powered rescue tool components (cable assemblies, hose assemblies, hose reels, etc.). The safety messages in this
publication supersede safety information appearing in AMKUS publications prior to April 2016.
This manual is intended for use with manuals published by manufacturers of prime movers (engines, electric motors, and pumps)
used in AMKUS power units.
This manual does NOT address operation or servicing of AMKUS Rescue Systems. Only competent rescue tool repair technicians
are quali¿ ed to repair AMKUS equipment. This manual should be available to all personnel involved with AMKUS equipment.
SAFETY MANUAL for AMKUS
RESCUE SYSTEMS
AMKUS RESCUE SYSTEMS
www.amkus.com
4201 Montdale Drive, Valparaiso, IN 46383-4098 USA
800-592-6587 • 219-548-5000 • Fax 219-476-1669
©Copyright Amkus Rescue Systems, Inc. 2014-2016 LAA-004 December 8, 2016 Rev04
SAFETY DATA SHEET
According to OSHA Hazard Communication
Standard, 29 CFR 1910.1200
AMKUS RESCUE SYSTEMS
MADE IN USA • www.amkus.com
4201 Montdale Drive, Valparaiso, IN 46383-4098 USA
800-592-6587 • 219-548-5000 • Fax 219-476-1669
SECTION 1. IDENTIFICATION
DIULF CILUARDYH 1VM SUKMAemaN tcudorP
Manufacturers of suppliers details
AMKUS RESCUE SYSTEMS, INC.
4201 Montdale Drive
Valparaiso, IN 46383-4098 USA
0005-845-912tseuqeR SDS
Customer Service
Emergency telephone number
CERTMEHC 0039-424-008noitamrofnI
llipS
Health Information
Recommend use of the chemical and restrictions on use
lio ciluardyHesU dednemmoceR
SECTION 2. HAZARDS IDENTIFICATION
GHS Classi¿ cation
Not a hazardous substance or mixture
GHS Label element
deriuqer lobmys drazah oNsmargotcip drazaH
drow langis oNdrow langiS
:SDRAZAH LACISYHPstnemetatS drazaH
Not classi¿ ed as a physical hazard under GHS criteria.
HEALTH HAZARDS:
Not classi¿ ed as a health hazard under GHS criteria.
ENVIRONMENTAL HAZARDS:
Not classi¿ ed as an environmental hazard under GHS criteria.
Precautionary statements
Prevention: No precautionary phrases.
Response: No precautionary phrases.
Storage: No precautionary phrases.
Disposal: No precautionary phrases.
Other hazards which do not result in classi¿ cation
Prolonged or repeated skin contact without proper cleaning can clog the pores of the skin resulting in disorders
such as oil acne/folliculitis.
Used oil may contain harmful impurities.
High-pressure injection under the skin may cause serious damage including local necrosis.
Not classi¿ ed as À ammable but will burn.
The classi¿ cation of this material is based on OSHA HCS 2012 criteria.
Under normal conditions of use or in a foreseeable emergency, this product does not meet the de¿ nition of
a hazardous chemical when evaluated according to the OSHA Hazard Communication Standard, 29 CFR
1910.1200.
LAA-001
SAFETY MANUAL
FOR AMKUS RESCUE SYSTEMS
LAA-004
SAFETY DATA SHEET
AMKUS MV1 HYDRAULIC FLUID
This manual is intended for use with manuals published by manufacturers of the prime movers
(motor and pump) used in this power unit.

©Copyright AMKUS Rescue Systems, Inc. 2018 LAP-012 July 16, 2018 Rev01
2
DANGER
PERSONAL RESPONSIBILITY CODE
The member companies of FEMSA that provide emergency response
equipment and services want responders to know and understand the
following:
1. Firefi ghting and Emergency Response are inherently dangerous activities
requiring proper training in their hazards and the use of extreme caution
at all times.
2. It is your responsibility to read and understand any user’s instructions,
including purpose and limitations, provided with any piece of equipment
you may be called upon to use.
3. It is your responsibility to know that you have been properly trained in
Firefi ghting and /or Emergency Response and in the use, precautions, and
care of any equipment you may be called upon to use.
4. It is your responsibility to be in proper physical condition and to maintain
the personal skill level required to operate any equipment you may be
called upon to use.
5. It is your responsibility to know that your equipment is in operable
condition and has been maintained in accordance with the manufacturer’s
instructions.
6. Failure to follow these guidelines may result in death, burns or other
severe injury.
FEM S A
Fire and Emergency Manufacturers and Service Association
P.O. Box 147, Lynnfi eld, MA 01940 • www.FEMSA.org
TABLE OF CONTENTS
1.0 MEANING OF SAFETY SIGNAL WORDS................................................................................................................................. 3
1.1 GENERAL WARNINGS ....................................................................................................................................................... 3
2.0 SPECIFICATIONS...................................................................................................................................................................... 4
2.1 GENERAL............................................................................................................................................................................ 4
2.2 OVERALL DIMENSIONS..................................................................................................................................................... 5
2.3 PART IDENTIFICATION....................................................................................................................................................... 6
2.4 SCREEN IDENTIFICATION................................................................................................................................................. 7
2.5 WIRING IDENTIFICATION .................................................................................................................................................. 8
3.0 PROTECTIVE CLOTHING......................................................................................................................................................... 9
4.0 TRAINING .................................................................................................................................................................................. 9
5.0 INSTALLATION .......................................................................................................................................................................... 9
5.1 SITE SELECTION ............................................................................................................................................................... 9
6.0 GETTING STARTED ................................................................................................................................................................ 12
6.1 INITIAL START-UP............................................................................................................................................................. 12
7.0 OPERATING INSTRUCTIONS................................................................................................................................................. 15
7.1 GENERAL.......................................................................................................................................................................... 15
7.2 OPTIONAL WIRELESS REMOTE CONTROL OPERATING INSTRUCTIONS................................................................. 15
8.0 TROUBLESHOOTING GUIDE ................................................................................................................................................. 15
9.0 ROUTINE MAINTENANCE ...................................................................................................................................................... 16
9.1 ROUTINE MAINTENANCE FOR HYDRAULIC PUMP...................................................................................................... 16
9.2 ROUTINE MAINTENANCE FOR HOSES.......................................................................................................................... 16
9.3 ROUTINE MAINTENANCE FOR COUPLINGS................................................................................................................. 16
9.4 MAINTENANCE RECORDS.............................................................................................................................................. 16
10.0 PARTS, SERVICE AND TECHNICAL INFORMATION........................................................................................................... 16
11.0 DECOMMISIONING ............................................................................................................................................................... 16
12.0 INSPECTION, CLEANING, DECONTAMINATION, AND STORAGE..................................................................................... 16

©Copyright AMKUS Rescue Systems, Inc. 2018 LAP-012 July 16, 2018 Rev01
3
1.0 MEANING OF SAFETY SIGNAL WORDS
A safety related message is identifi ed by a safety alert symbol and a signal word to indicate the level of risk involved with a particular
hazard. Per ANSI standard Z535.6-2011, the defi nitions of the four signal words are as follows:
DANGER DANGER indicates a hazardous situation which, if not avoided, will result in death or serious
injury.
WARNING WARNING indicates a hazardous situation which, if not avoided, could result in death or serious
injury.
CAUTION CAUTION indicates a potentially hazardous situation which, if not avoided, could result in minor
or moderate injury.
NOTICE NOTICE is used to address practices not related to physical injury.
1.1 GENERAL WARNINGS
WARNING Servicing tools creates injury risk not found during normal product use;
• Guards removed for service create pinch points. Avoid injury during service by keeping hands
and fi ngers away from movable mechanisms when cycling the tool under pressure. Replace
guards before returning tools to service.
• Pressure stored within a hydraulic cylinder against an end stop can be suddenly released
during service by disassembly of hydraulic components. Release pressure by moving
cylinder slightly from the end stop before service.
• Energizing electrical connections and wiring exposed during service creates ignition and
shock hazards.
• Always wear safety glasses when servicing, or testing Amkus rescue equipment.
Obtain Level 3 service technician training before servicing Amkus rescue equipment.
WARNING Do not touch electrical connections before you fi rst ensure that power has been disconnected.
Electrical shock can cause serious or fatal injury. Only qualifi ed personnel should attempt the
installation, operation and maintenance of this equipment.
WARNING Be sure the system is properly grounded before applying power. Do not apply AC power before
you ensure that all grounding instructions have been followed. Electrical shock can cause serious
or fatal injury.
WARNING Use proper care and procedures that are safe during handling, lifting, installing, operating and
maintaining operations. Improper methods may cause muscle strain or other harm.
WARNING When using electric motorized equipment, basic safety precautions should always be followed to
reduce the risk of fi re, electric shock, injury, or death.
WARNING When using electric motorized equipment, basic safety precautions should always be followed
to reduce the risk of fi re, electric shock, injury, or death. The following are some basic safety
precautions:
Electric motor and controls are ignition sources. Flammable vapors heavier than air can accumulate
in low spots. Avoid selecting these locations when setting up the equipment. Use detectors to verify safe
site selection.
Electric motor and wiring are not waterproof. Don’t submerge or douse electric motors or their
controls. Refer to manuals from motor manufacturer for specifi c details.
Installation by qualifi ed person – Power componentry properly, sized and installed, to run the equipment
are the responsibility of the purchaser. Qualifi ed electricians should install the equipment per applicable
regulations (NEC, NFPA, OSHA, etc.) before the equipment can be used.
Circuit breakers matched to the motor capacity are required. Don’t operate electric motors without
circuit breaker protection.
Type of power cord - cord type should be rated for outdoor use, such as SW, SOW, STW, STOW, SJW,
SJOW, SJTW, or SJTOW. (W service rating = outdoor and wet location)
Use of power cords - Always use a cord heavy enough to carry the current the tool will draw. Use of an
undersized cord will cause a drop in line voltage resulting in loss of power and overheating.
Don’t abuse the cord – Make sure the power cord is in good condition before use. Never lift or pull
the equipment by the cord or yank it to disconnect from receptacle. Keep cord from heat, oil, crushing,
and sharp edges. Inspect cords for damage after each use. Replace damaged cords before placing
equipment in service.
Disconnect power –Disconnect the equipment from the power supply when not in use, before cleaning,
inspecting, or servicing electric motors and controls.
Keep covers and guards in place and in working order

©Copyright AMKUS Rescue Systems, Inc. 2018 LAP-012 July 16, 2018 Rev01
4
2.0 SPECIFICATIONS
AMKUS 240SS Specifi cations
Length 33 in 838 mm
Width 10.25 in 260 mm
Height 21 in 533 mm
Weight 217 lbs (wet) 98.4 kg
177 lbs (dry) 80.3 kg
Motor Input Voltage 208/240 | VAC Single Phase
Current Draw Amps (maximum) 70 Amps at 208VAC (Input)
Number of Pumps 2
Rated Flow Of The Pump per Port, First Stage 1 gpm 3.9 l/min
Rated Output Pressure, First Stage 6450 psi 445 bar
Rated Flow Of The Pump per Port, Second Stage 0.68 gpm 2.6 l/min
Rated Output Pressure, Second Stage 10,500 psi 724 bar
Fluid Type: AMKUS MV1 Mineral Base Hydraulic Fluid
Safety Data Sheet (SDS) for AMKUS MV1 Hydraulic Fluid is available at
AMKUS.com and CHEMTREC.com
(For equipment stored and operated in environments below 32 deg. F (0 deg C)
contact Amkus Rescue Systems for recommendation.
Hydraulic Fluid Reservoir Capacity: 7 gals. US 26.5 liters
Hydraulic Filter AMKUS Part # KSS010
2.1 GENERAL
For two-tool simultaneous operations, the 240SS Super Simo is a true “on board” 2 circuit hydraulic rescue tool power unit. This
high performance unit provides the power and tool speed needed to be used with longer length hoses such as 100, 150, and even
200 foot length hoses. The performance of the 240SS virtually eliminates long tool reaction times created by the expansion of long
lengths of hydraulic hoses.
AMKUS uses another industry fi rst Variable Frequency Drives to regulate electrical requirements. This infi nitely customizable control
system is set up to require only 5 amps of current at start up. Unlike other electric power units, the 240SS increases electrical power
as the pressure increases through the use of a Programmable Logic Controller (PLC). Maximum electrical requirement of less than
15kW is only needed when both circuits reach 10,500 psi simultaneously.
The Programmable Logic Control Module puts the controls in one location providing master on/off switch, circuit controls, low oil,
high temperature indicator lights. The Human Machine Interface (HMI) display provides system operational information as well as
input and output indicators to quickly troubleshoot the system. An Ethernet interface provides a programming and troubleshooting
connection for factory assistance should the need occur to interface to the power unit.

©Copyright AMKUS Rescue Systems, Inc. 2018 LAP-012 July 16, 2018 Rev01
5
2.2 OVERALL DIMENSIONS

©Copyright AMKUS Rescue Systems, Inc. 2018 LAP-012 July 16, 2018 Rev01
6
2.3 PART IDENTIFICATION
Power Unit
Wireless Remote Control
Receiver
Reel ReturnReel Pressure
Reel Return Reel Pressure
Sight Gauge
Drain Plug
Vent Cap Reservoir Fill Cap
Oil Filter
Heat Exchanger Inlet
Power Plug
Heat Exchanger Outlet

©Copyright AMKUS Rescue Systems, Inc. 2018 LAP-012 July 16, 2018 Rev01
7
2.4 SCREEN IDENTIFICATION
Main Screen
The main touch screen is used to operate the unit . Using the
touchscreen or the button switches below, the user may:
Start the system
Operate either pump motor
Open or close the pump valves
See section 6.0 for detailed operating instructions.
I/O Screen
The I/O screen shows the states of each input and output in real
time. This screen is most helpful for troubleshooting a system.
Runtime Screen
The runtime screen shows total hours of use on each motor.

©Copyright AMKUS Rescue Systems, Inc. 2018 LAP-012 July 16, 2018 Rev01
8
2.5 WIRING IDENTIFICATION
Connection Callouts
1 - Radio (TR)
2 - HMI Ethernet (C5)
3 - HMI POWER/CONTROL (HMI)
4 - OIL/TEMP SENSORS (LVTEMP)
5 - 12VDC IN (12 IN)
6 - 12VDC OUT (12 OUT)
7 - MOTOR 1 (M1)
8 - MOTOR 2 (M2)
9 - 208/240VAC IN (POWER)
1
2
3
4
5
6
7
8
9

©Copyright AMKUS Rescue Systems, Inc. 2018 LAP-012 July 16, 2018 Rev01
9
3.0 PROTECTIVE CLOTHING
It is the responsibility of the user to ensure that appropriate protective clothing are worn and equipment are used to provide
protection from those hazards to which personnel are exposed or could be exposed while working with this product.
4.0 TRAINING
This product is designed to be used by emergency services personnel to facilitate the extrication of victims from entrapment. Its
use should be limited to trained personnel only. All personnel using this equipment are assumed to have completed a course of
instruction that is acknowledged as being educationally sound by the local authority having jurisdiction over such training. This
document contains basic operating and maintenance instructions only.
Normally, AMKUS equipment is prepared and serviced by your dealer prior to delivery. If, however, you have decided to place the
equipment into service yourself, please review the following instructions carefully.
1. Remove equipment from the packing cartons and carefully inspect for damage. Damage that occurs during shipment should be
reported immediately to the carrier.
2. There are 4 major components included in the 240SS Super Simo Power Unit and an optional remote control system.
a. VFD (Variable Frequency Drive) Panel
b. Control Panel
c. Heat Exchanger
d. Power Unit
Optional
Wireless Receiver
VFD Panel
Control Panel
Heat Exchanger
Power Unit
5.0 INSTALLATION
5.1 SITE SELECTION
When selecting a location to mount the 240SS system it is important to install it inside a compartment away from the elements. For
more information contact your local AMKUS dealer.
AMKUS equipment is manufactured with superior craftsmanship and quality that is backed by the standard warranty which is
published on the AMKUS website.
NOTICE Only use AMKUS tools with AMKUS equipment. Mixing AMKUS tools with another manufacturer’s
equipment may cause operational problems, equipment failure, or denial of warranty claims.
NOTICE Only use AMKUS mineral-base hydraulic fluid in AMKUS equipment. Using another manufacturer’s
hydraulic fluid in AMKUS equipment may cause operational problems, equipment failure, or
denial of warranty claims.

©Copyright AMKUS Rescue Systems, Inc. 2018 LAP-012 July 16, 2018 Rev01
10
Remove Bolt
Remove Bolt
Sight Gauge
1. Remove the black cover from the power unit by removing
the bolts on either end of the unit.
2. Determine the location for the power unit. To allow for
easier service, make sure the black cover can be removed
and the sight gauge is visible.
3. The power unit has been shipped with the kinetic bushings
and mounting brackets installed.
Vent Cap Reservoir Fill Cap
4. Install and tighten the 4 mounting bolts. 5. Remove the black vent cap with a 12mm Hex Key. Unscrew
the red reservoir fi ll cap and fi ll the hydraulic fl uid reservoir
until the sight gauge is completely full. Replace the black
vent cap and the red reservoir fi ll cap.

©Copyright AMKUS Rescue Systems, Inc. 2018 LAP-012 July 16, 2018 Rev01
11
Return PortPressure Port
Return Port Pressure Port
Pump 2
Pump 1
6. Connect the pressure and return hose
If AMKUS standard couplers are being used, be sure the
pressure line has a male coupler at the end of the reel. The
return line will have a female coupler at the end of the reel.
If AMKUS Mono Couplers are being used, be sure the
pressure line is connected to the pressure port (P) of the
female Mono Coupler and the return line is connected to
the tank port (T) of the female Mono Coupler.
7. The heat exchanger supply utilizes a check valve. The fl ow
direction can be determined by the arrow stamped on the
check valve. Connect this hose to an installer provided #8
SAE 100 R2 hose and connect the other end to the inlet
side of the heat exchanger. The inlet side is the port closest
to the power plug.
Heat Exchanger Inlet
Power Plug
Heat Exchanger Outlet
8. The heat exchanger should be mounted in a location that
allows the intake of fresh air. Caution should be taken to
prevent recirculation of the heated air. The air intake side
of the heat exchanger should have a minimum of 3 inches
from any obstruction. The exhaust (fan) side of the heat
exchanger should exhaust into free air (no back pressure).
9. The 240SS Control Panel (shown above) houses a display
and 5 buttons used to operate the unit. The green button
is used to start/stop the entire system. Each reel circuit
has a motor button and valve control button. Refer to the
operating section of this manual for further explanation of
button functions.

©Copyright AMKUS Rescue Systems, Inc. 2018 LAP-012 July 16, 2018 Rev01
12
10. Mount the 240SS Control Panel in a compartment
accessible to tool operators.
11. Mount the 240SS VFD Panel in a compartment. Ensure
the VFD can be accessed and the cover can be easily
removed by maintenance technicians.
Receiver
Wireless Remote Controls
12. Mount the optional wireless receiver using the supplied
bolt.
NOTICE This unit should be installed in a compartment out of the elements. Plug the receiver cable into
the matching plug from the VDF panel.
6.0 GETTING STARTED
6.1 INITIAL START-UP
1. Connect the hose reel hoses together before starting the
system.
2. Using a hex-key wrench, remove 4 corner screws
Remove the VFD cover.

©Copyright AMKUS Rescue Systems, Inc. 2018 LAP-012 July 16, 2018 Rev01
13
3. The VFD is shipped with the circuit breakers in the OFF
position.
4. Place the VFD circuit breakers in the ON position fl ipping
each black switch up.
ON
5. The upper section of the Control Panel houses the touch
screen display and the touch display. The green button is
used to enable/disable the entire unit. Press the physical
or digital green button to start the system. The screen
should indicate the system has started.
6. Press the physical or digital blue M1 button to start Motor
No. 1. The screen should indicate Motor No .1 is running
ON ON
7. Press the physical or digital red M2 button to start Motor
No. 2. The screen should indicate Motor No. 2 is running.
8. Press the physical or digital blue V1 button to activate
Valve No. 1. The screen should indicate Valve No. 1 is open.

©Copyright AMKUS Rescue Systems, Inc. 2018 LAP-012 July 16, 2018 Rev01
14
ON
FULL
LOW
9. Press the physical or digital blue V2 button to activate
Valve No. 2. The screen should indicate Valve No. 2 is open.
10. With both motors running and valves open, allow the
power unit to fl ow through the reels for several minutes
while monitoring the fl uid sight gauge level. If the fl uid level
continues to drop after several minutes check for fl uid leaks.
When fi nished, shut the power unit off . Replenish hydraulic
fl uid until the sight gauge is completely full.
Pressure
Line
Fluid Flowing
From The
Pressure Line
Return
Line
Verify Hose Connections
Male CouplingFemale Coupling
1. To verify which hose is the pressure hose, remove both
couplings from the end of the hoses and place the hose
ends in a bucket. Charge the appropriate valve. Fluid will
fl ow from the pressure line. Turn off the valve once the
pressure line is identifi ed.
2. If AMKUS standard couplers are being used, place the
male coupler on the pressure line and the female coupler
on the return line. Repeat for the other reel.
If AMKUS Mono Couplers are being used, be sure the
pressure line is connected to the pressure port (P) of the
female Mono Coupler and the return line is connected to
the tank port (T) of the female Mono Coupler.
3. Check the sight gauge and add fl uid until the sight gauge
is completely full again.
4. Put the black cover back in place and tighten the bolts on
both ends to 25 in-lb (2.8 NM).

©Copyright AMKUS Rescue Systems, Inc. 2018 LAP-012 July 16, 2018 Rev01
15
7.0 OPERATING INSTRUCTIONS
7.1 GENERAL
The 240SS is a simultaneous operation power unit. Two tools can be connected to a single power unit and operated either
independently or simultaneously. To operate the 240SS. Ensure there is power to the unit. Begin operation by pressing the system
start button. Then, press the motor button to begin building pressure. Once pressure builds, press the corresponding valve button to
charge the rescue tool for operation.
After completing operations, pressing the green start button turns the entire system off .
Please note that the minimum safe bend radius of the hoses is 4 inches (101.6 mm).
7.2 OPTIONAL WIRELESS REMOTE CONTROL OPERATING INSTRUCTIONS
Wireless Remote Control Remote Control Operation
1
5
6
2
3
4
• Rotate the Emergency Stop (1) (Red) thumb wheel clockwise and release
to be sure the remote is in the operation mode.
• Press and hold both start buttons at the bottom of the remote. While
holding the start buttons the remote is linking up to the receiver mounted
in the apparatus so it is best to the hold the start buttons pressed fi rmly
to ensure a good signal.
• Push the M1 and/or M2 motor buttons (The motors are programmed to
reach full operating speed in 5 seconds).
• Push the V1 and/or V2 valve button(s) to activate the appropriate reel
circuits.
• To shut off a circuit, push the appropriate valve (5) and/or (6) button.
• To quickly shut down the entire system including the power, motors and
reel circuits, push the Emergency Stop. To re-activate the system, repeat
these instructions starting at number 1.
Remote Control Features
1. Emergency Stop (Red) – Closes both valves and powers down both motors. Press to active Emergency Stop. Rotate thumb
wheel clockwise to resume normal operation.
2. Start Buttons (Green)- Synchronizes the remote to the receiver and activates the system..
3. M1 Motor Switch – Depress to activate motor for M1 circuit. Depress again to turn motor off .
4. M2 Motor Switch – Press to activate motor for M2 circuit. Press again to turn motor off .
5. V1 Valve 1 Switch – Press to activate control valve for V1 circuit. Press again to turn control valve off .
6. V2 Valve 2 Switch – Press to activate control valve for V2 circuit. Press again to turn control valve off .
8.0 TROUBLESHOOTING GUIDE
Any problem not resolved by the following suggestions may require you to contact your local dealer or AMKUS Rescue Systems for
further guidance.
Problem Solution
Tool lacks power or speed Check hydraulic fl uid level in power unit reservoir.
Fluid leaks at fi ttings or hoses Check tightness of hose fi ttings.
Replace damaged hoses.
Tools do not operate Check to see that the power unit is running.
Check to see that the line is charged.
Check hydraulic fl uid level in power unit reservoir.

©Copyright AMKUS Rescue Systems, Inc. 2018 LAP-012 July 16, 2018 Rev01
9.2 ROUTINE MAINTENANCE FOR HOSES
After each use, hoses should be wiped clean with a light cleaner such as Simple Green®. Inspect hoses for damage to the rubber
outer cover. Damage which exposes the wire braided reinforcement subjects the wire to corrosion and may weaken the hose.
9.3 ROUTINE MAINTENANCE FOR COUPLINGS
Use care when making hydraulic connections by avoiding dirt, sand, and water puddles at the scene. Even with care, residual oils
on the moving parts will gradually accumulate dirt and grit making connections difficult. Couplings and dust caps can be periodically
cleaned using an automotive type aerosol solvent de-greaser. Avoid water-based cleaning products. Apply a light spray lube
(automotive, lock, or gun type) to keep the collars moving easily. Avoid covering a clean coupling with a dirty dust cap.
9.4 MAINTENANCE RECORDS
It is the responsibility of the user to keep maintenance records for each component of the rescue system. Maintenance shall be
performed by qualified service technicians in accordance with the recommendations as outlined in this manual.
9.0 ROUTINE MAINTENANCE
Obtain appropriate level service technician training before servicing AMKUS Rescue Systems equipment. For more information
contact your local AMKUS Rescue Systems dealer about service levels and training courses .
9.1 ROUTINE MAINTENANCE FOR HYDRAULIC PUMP
Normally, you will have a maintenance agreement for your system with your local dealer. However, if you have decided to service
the equipment yourself, please review the following instructions carefully.
Check the hydraulic fluid level sight gage after every use. Fluid should be “clear-gold”. Cloudy, milky, brownish, or smelly fluid
indicates contamination. Contact your local dealer or AMKUS Rescue Systems. A noticeable drop in fluid level indicates fluid loss.
Investigate and correct the cause of loss, add MV1 hydraulic fluid as needed. Change oil filter after every 100 hours of pump
operation. Change hydraulic fluid after every 300 hours of pump operation.
OIL CHANGE PROCEDURE; remove the fill plug/vent cap. Place a drain pan under the drain plug. Unscrew the drain plug being
careful not to lose it. Allow the hydraulic fluid to drain completely. Clean and reinstall the drain plug. Replace the filter. Fill the
hydraulic fluid reservoir with new AMKUS MV1 fluid. Reinstall the fill plug/vent cap. Cycle rescue tools several times to purge air
from the hydraulic hoses.
The next step is to purge air from the hydraulic hoses.
The rated hydraulic pressure at maximum output is 10,500 psi +- 500 psi (724 bar+-34 bar). Verify performance by periodic testing
using a pressure gauge. If performance falls outside of this range, contact your local dealer or AMKUS Rescue Systems.
WARNING DO NOT ATTEMPT TO ADJUST THE INTERNAL PRESSURE RELIEF SETTING! Pressure relief
valves are NOT user serviceable. User adjustment is a misuse of this equipment.
AMKUS RESCUE SYSTEMS
amkus.com
4201 Montdale Drive, Valparaiso, IN 46383-4098 USA
800-592-6587 • 219-548-5000 • Fax 219-476-1669
12.0 INSPECTION, CLEANING, DECONTAMINATION, AND STORAGE
BEFORE BEING PLACED BACK IN SERVICE, power units must be inspected to this checklist;
1. Check to see that all markings are legible. Contact your local dealer or AMKUS Rescue Systems for replacement labels.
2. Wipe tool, hoses, fittings and couplings clean (see routine maintenance for hoses and couplings).
3. Inspect the power unit, hoses, fittings and couplings after each use for damage, leakage and excessive wear.
4. If the power unit becomes contaminated, determine the nature of the contamination. IE: biological, chemical, radioactive. The
authority having jurisdiction may follow internal decontamination guidelines or request technical advice from AMKUS.
5. Check the hydraulic fluid levels after each use. Replenish as necessary with AMKUS MV1 mineral based hydraulic fluid.
WARNING Any power unit failing any part of the checklist is unsafe for use and must have the problem
corrected before use or being placed back into service. Operating a power unit that has failed the
checklist is a misuse of this equipment.
10.0 PARTS, SERVICE AND TECHNICAL INFORMATION
Parts, service and technical information may be obtained from your local AMKUS dealer, or by contacting AMKUS Rescue Systems.
11.0 DECOMMISIONING
When decommissioning any AMKUS Recue Systems Tool or power supply local regulations shall be followed. For proper disposal
information contact your local AMKUS Recue Systems dealer.
Other manuals for Super Simo 240SS
1
Table of contents
Other Amkus Portable Generator manuals
Popular Portable Generator manuals by other brands
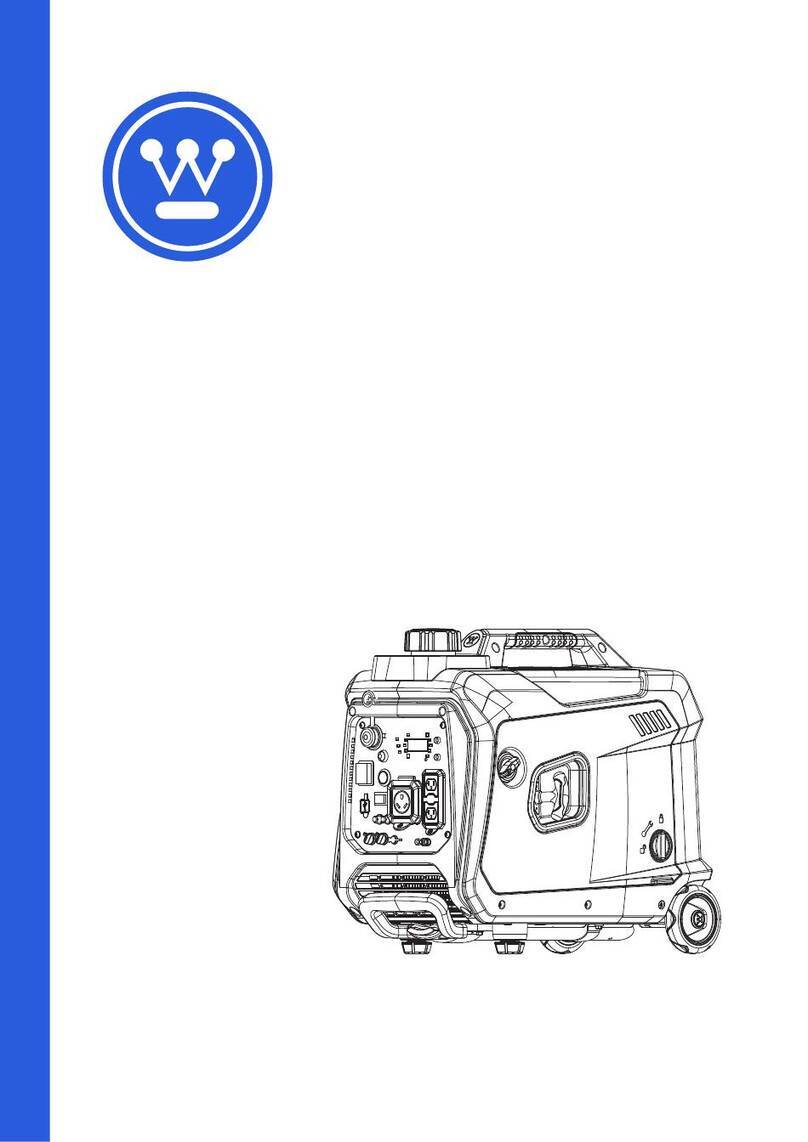
Westinghouse
Westinghouse iGen4000DFc user manual
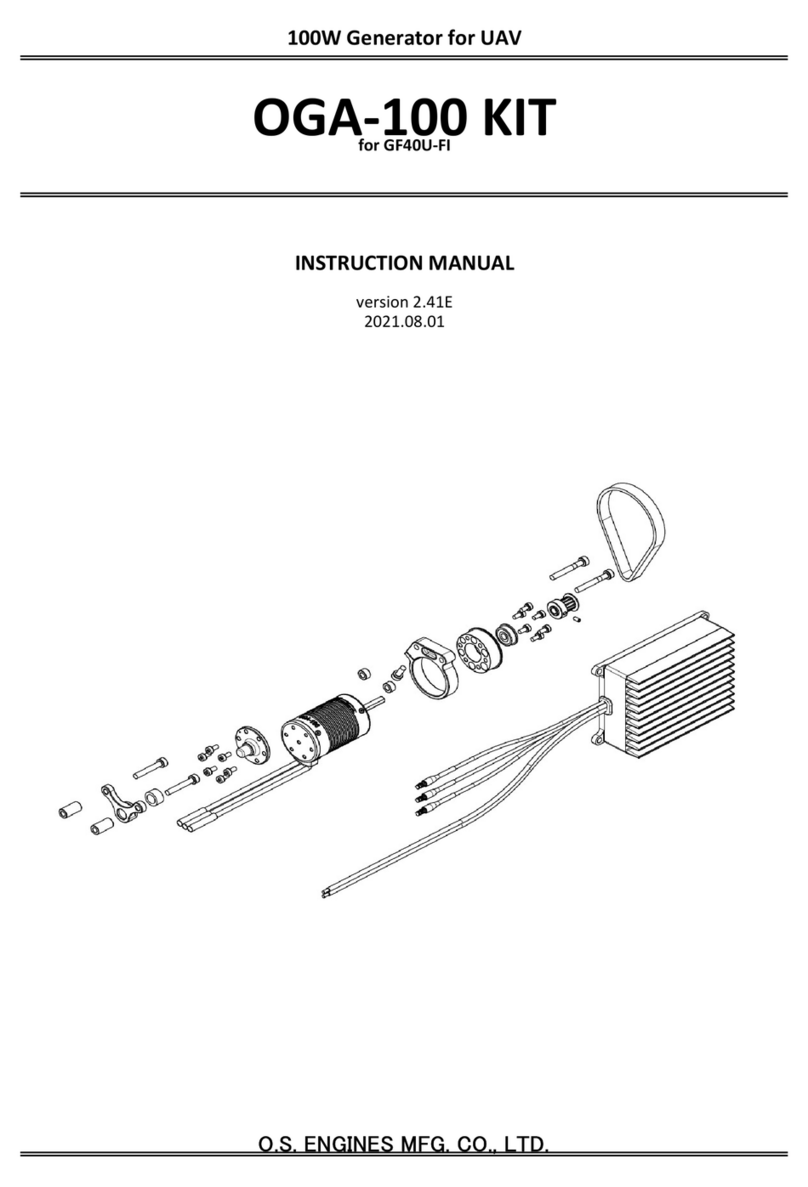
O.S. engine
O.S. engine OGA-100 KIT instruction manual

Anker
Anker SOLIX F1200 user manual
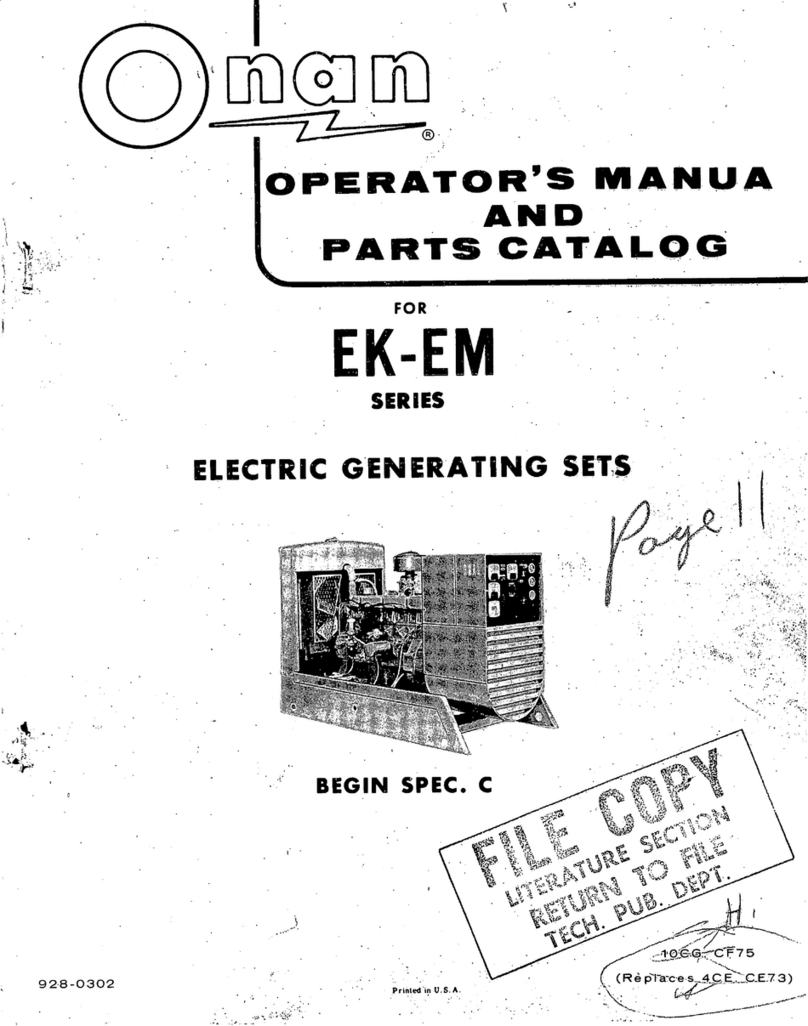
Onan
Onan EM Series Operator's manual and parts catalog
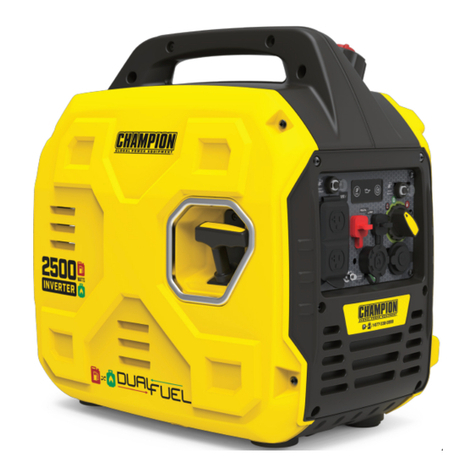
Champion Global Power Equipment
Champion Global Power Equipment 200961 quick start guide
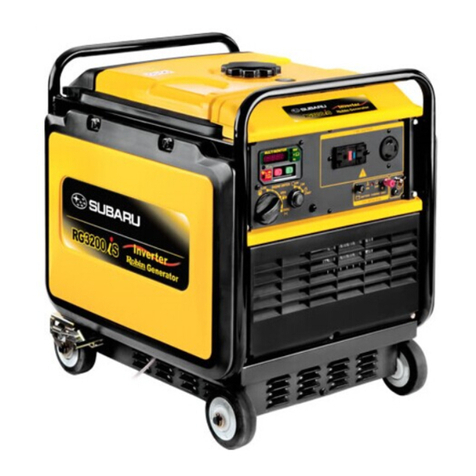
Robin
Robin RG2800is Instructions for use