Amphenol Temposonics Level Plus LLH User manual

Magnetostrictive Liquid Level Transmitters with Temposonics®Technology
Level Plus®– LLH
Operation Manual
Compact Sanitary Level Measurement
Inherent Accuracy +/-0.5 mm
No Scheduled Maintenance or Recalibration

Table of contents
1. Contact information.......................................................................................................................................... 3
2. Terms and definitions........................................................................................................................................ 4
3. Introduction ................................................................................................................................................... 5
3.1 Purpose and use of this manual ................................................................................................................................................................ 5
3.2 Used symbols and warnings ..................................................................................................................................................................... 5
4. Safety instructions ........................................................................................................................................... 5
4.1 Intended use.............................................................................................................................................................................................. 5
4.2 Foreseeable misuse................................................................................................................................................................................... 5
4.3 Installation, commissioning and operation................................................................................................................................................ 6
5. Product overview............................................................................................................................................. 7
5.1 Components.............................................................................................................................................................................................. 7
5.2 Accuracy.................................................................................................................................................................................................... 7
5.3 Warranty.................................................................................................................................................................................................... 7
5.4 Storage...................................................................................................................................................................................................... 8
5.5 Model number identification...................................................................................................................................................................... 9
5.6 Technical data.......................................................................................................................................................................................... 11
5.7 Technical drawing.................................................................................................................................................................................... 12
6. Installation and mounting .................................................................................................................................13
6.1 Training ................................................................................................................................................................................................... 13
6.2 Stilling wells and guide poles .................................................................................................................................................................. 13
6.3 Tools........................................................................................................................................................................................................ 13
6.4 Installation steps ..................................................................................................................................................................................... 13
6.5 Mounting................................................................................................................................................................................................. 14
7. Electrical connections ......................................................................................................................................15
7.1 Basic information .................................................................................................................................................................................... 15
7.2. Safety recommendations........................................................................................................................................................................ 15
7.3 Grounding ............................................................................................................................................................................................... 16
7.4 Wiring connection ................................................................................................................................................................................... 16
8. Maintenance .................................................................................................................................................18
8.1 Training ................................................................................................................................................................................................... 18
8.2 Tools........................................................................................................................................................................................................ 18
8.3 Inspection................................................................................................................................................................................................ 18
8.4 Preventative maintenance........................................................................................................................................................................ 18
9. Repair.........................................................................................................................................................19
9.1 RMA policy.............................................................................................................................................................................................. 19
9.2 Training ................................................................................................................................................................................................... 19
9.3 Troubleshooting....................................................................................................................................................................................... 19
10. Spare Parts...................................................................................................................................................20
11. Interface .......................................................................................................................................................20
11.1 Analog Output ....................................................................................................................................................................................... 20
11.2 IO-Link Output....................................................................................................................................................................................... 20
11.3 SSI Output............................................................................................................................................................................................. 20
11.4 CANopen Output.................................................................................................................................................................................... 20
11.5 Profinet RT & IRT.................................................................................................................................................................................. 20
11.6 EtherNet/IP............................................................................................................................................................................................ 21
11.7 POWERLINK.......................................................................................................................................................................................... 21
11.8 EtherCAT................................................................................................................................................................................................ 21

Level Plus® LLH
Operation Manual
I3 I
1. Contact information
United States
General
Tel: +1-919-677-0100
Fax: +1-919-677-2343
E-mail: [email protected]
http://www.temposonics.com
Mailing and shipping address
Temposonics LLC
3001 Sheldon Drive
Cary, North Carolina, 27513, USA
Customer service
Tel: +1-800-633-7609
Fax: +1-800-498-4442
Technical support and applications
24 Hour Emergency Technical Support
Tel: +1-800-633-7609
E-mail: [email protected]
Germany
General
Tel: +49-2351-9587-0
Fax: +49-2351-56491
E-mail: [email protected]
http://www.temposonics.com
Mailing and shipping address
Temposonics GmbH & Co. KG
Auf dem Schüffel 9
58513 Lüdenscheid, Germany
Technical support and applications
Tel: +49-2351-9587-0
E-mail: [email protected]
http://www.temposonics.com

Level Plus® LLH
Operation Manual
I4 I
2. Terms and definitions
A
Analog Output
For a sensor with analog output, the measured value is output as an
analog voltage signal or current signal.
D
Differential
For differential measurement, the distance between the two position-
magnets is output as a value.
I
Interface
Noun; The measurement of the level of one liquid when that liquid is
below another liquid.
Interface
Adj.; The Software Graphical User Interface (GUI) that allows the user
to access software protocols (HART®, DDA, MODBUS).
N
NPT
U.S. standard defining tapered pipe threads used to join pipes and
fittings.
S
Specific Gravity
The density ratio of a liquid to the density of water at the same
conditions.
R
Resolution
The sensor precisely measures time to provide the position
measurement. For the analog output the measured time value is
converted into an analog voltage signal or current signal using a high-
performance Digital to Analog Converter (DAC) having 16 bits of
resolution.

Level Plus® LLH
Operation Manual
I5 I
3. Introduction
3.1 Purpose and use of this manual
Important:
Before starting the operation of the equipment read this
documentation thoroughly and follow the safety information.
The content of this technical documentation and of its various annexes
is intended to provide information on mounting, installation and
commissioning by qualified automation personnel or instructed service
technicians who are familiar with the project planning and dealing with
the Level Plus liquid level transmitters.
3.2 Used symbols and warnings
Warnings are intended for your personal safety and for avoidance
of damage to the described product or connected devices. In this
documentation, safety information and warnings to avoid dangers that
might affect the life and health of personnel or cause material damage
are highlighted by the preceding pictogram, which is defined below.
Symbol Meaning
NOTICE
This symbol is used to point to situations
that may lead to material damage and/or
personal injury.
4. Safety instructions
4.1 Intended use
The liquid level transmitter is intended to be used to measure the level
of liquid(s) contained by a structure. The product may only be used for
the applications defined under item 1 to item 3 and only in conjunction
with third-party devices and components recommended or approved
by Temposonics. As a prerequisite of proper and safe operation, the
product requires correct transport, storage, mounting and commissio-
ning and must be operated with utmost care.
1. Application does not exceed product’s performance specification in
chapter 5.5.
2. The liquid(s) being measured are compatible with the selected
wetted parts of the product.
3. Temposonics floats should be used for proper functionality and
safety approval.
Forseeable misuse Consequence
Wrong sensor connection Possible damage to electronics
See chapter 7 for Electrical
Connections
Improper Installation Physical damage to packaging
See chapter 6 for Installation
Process Temperature out of range Signal Degradation, Possible
Damage to Sensor
See chapter 5.6 for Specications
Power Supply out of range No Communication, Possible
Damage to Sensor
See chapter 5.6 for Specications
Process Pressure out of range Possible Damage to Sensor,
See chapter 5.6 for Specications
Improper Chemical Compatibility Possible Damage to Sensor,
Customer Must Select Wetted
Material that is compatible with
liquid(s) in tank
Modifying Sensor Warranty Void, Hazardous
Approval Void Customer should
contact factory for custom unit
Improper Grounding Possible Damage to Sensor, Full
Protection Compromised,
See chapter 7.3 for Grounding
Use of oat not sold by
Temposonics
Unit may not function correctly or
may have erradic output
Fig. 1: Foreseeable misuse
4.2 Foreseeable misuse

Level Plus® LLH
Operation Manual
I6 I
4.3 Installation, commissioning and operation
The liquid level transmitter should be used only in technically safe
conditions. To maintain this condition and to ensure safe operation,
installation, connection and service, work may be performed only by
qualified technical personnel.
If danger of injury to persons or of damage to operating equipment
could be caused by sensor failure or malfunction, additional safety
measures should be included in the overall automation solution. In
the event of trouble, shut down the sensor and protect it against
accidental operation.
1. Wear proper personal protection equipment such as hard hat,
safety shoes, safety glasses, gloves, and hearing protection.
2. Do not open or dismantle the sensor.
3. Follow the specifications given in the technical documentation.
4. Two (2) individuals are recommended to conduct proper
installation, commissioning, and repair of the level transmitter.
5. Protect the sensor against mechanical damage during installation
and operation.
6. Do not use damaged products and secure them against
unintentional use. Mark damaged products as being defective.
7. Connect the sensor very carefully and pay attention to the
polarity of connections. Temposonics recommends to not make
connections while power is live.
8. Before turning on power, ensure that nobody’s safety is
jeopardized by starting level transmitter and/or process.
9. Regularly follow preventative maintenance to prevent safety risks
10. Make sure that no wire strands are loose or sticking out of
the terminal block connection which could short and cause a
problem.

Level Plus® LLH
Operation Manual
I7 I
5. Product overview
The Level Plus LLH satisfies the demand for an accurate and robust
liquid level transmitter for sanitary/hygienic applications. The LLH can
provide product level and/or interface level in a compact mechanical
design. There is no requirement for scheduled maintenance or
recalibration for the expected 10 year life of the sensor. Set it and
Forget it.
The LLH liquid level transmitter can be mounted on most tanks
offering NPT and Tri-clamp connections from 3/4 to 6 inches. The LLH
also offers a variety of outputs including Analog, CANbus, SSI, IO-
Link, Powerlink, ProfiNet, Ethernet IP, and EtherCat. Included in the
model number is the selection of float(s) and cable. The single model
number offers everything needed for level measurement in a variety of
applications.
Applications
• Sanitary Finish Ra 25 uin (0.64 um)
• Product Level
• No scheduled maintenance or recalibration
• Inherent Accuracy +/- 0.5 mm
• IP69K
• 100 g Shock/15 g Vibration
Features
• Bottle Filling Machines
• CIP Tanks
• Skids
• Balance Tanks
• Fermentation Tanks
• Dispensing
5.1 Components
The Level Plus®LLH liquid level transmitter consists of three main
components; a base model, float, and process connection. Varying the
components of the transmitter allows the transmitter to be customized
to almost any application.
Base Model
The base model of the LLH consist of the housing, M18 threads, M12
connector, 10 mm inner pipe, 5/8” OD outer pipe, and pipe connection
fitting. The drawing of the base model is shown in section 5.7
Technical Drawing.
Floats
LLH transmitters offer numerous floats for different applications
such as stainless steel for product level. For detailed information
about floats, refer to the ‘Accessories Catalog’, (Temposonics Part #
551103).
For assistance with selecting a specific float for your application,
please contact Technical Support with the following information:
• Specific gravity of liquid(s) being measured
• Process temperature
• Process opening size
• Vessel pressure
Process Connection
The LLH is available with multiple connection types and sizes to allow
for mounting on the tank. The options include a 3/4" NPT fitting or a
Tri-clamp available from 1.5 to 6”.
Accessories
Temposonics also offers a series of displays, housings, converters,
and other accessories, please refer to the ‘Accessories Catalog’,
(Part#551103).
5.2 Accuracy
For magnetostrictive transmitters inherent accuracy is measured
in terms of non-linearity. Non-linearity is a measurement of any
imperfections in the waveguide that are reflected in the linearity of
the transmitter’s output. Temposonics tolerances reflect a maximum
non-linearity of +/- 0.5 mm Temposonics is able to achieve such
strict tolerances by manufacturing all of its own waveguide from a
proprietary alloy and testing 100% of all transmitters before shipping.
5.3 Warranty
Important:
Contact Technical Support or Customer Service for assistance if
you suspect that the transmitter is not working correctly. Technical
support can assist you with troubleshooting, part replacement, and
Returned Material Authorization (RMA) information if required.
All Level Plus®transmitters come with a two year limited warranty
from the factory shipment date. An additional extended warranty can
be purchased. A Return Materials Authorization (RMA) number is
required and must accompany any transmitter returns. Any unit that
was used in a process must be properly cleaned in accordance with
OSHA standards, before it is returned to the factory. A Material Safety
Data Sheet (MSDS) must also accompany the transmitter that was
used in any process.
The Temposonics obligation is limited to repair or replacement of any
defective part of the unit. No warranty can be provided for defects
that are due to improper use or above average stress of the product,
as well as for wear parts. Under no circumstances will Temposonics
accept liability in the event of offense against the warranty rules, no
matter if these have been assured or expected, even in case of fault or
negligence of the company.
Temposonics explicitly excludes any further warranties. Neither
the company’s representatives, agents, dealers nor employees are
authorized to increase or change the scope of warranty.

Level Plus® LLH
Operation Manual
I8 I
5.4 Storage
If storage is required prior to installation, store indoors in a dry
environment at ambient temperature range not to exceed −40…+71°C
(−40…+160°F).

Level Plus® LLH
Operation Manual
I9 I
5.5 Model Number Indentification
e Process Connection Type
1NPT **
4Welded Tri-Clamp
5Adjustabel Tri-Clamp
ZCustom Flange
b Sensors pipe
CSanitary, T-bar, TB
DSanitary, drain-in-place, DP
ESanitary, clean-in-place, CP
FSanitary, drain-in-place, no hole, DN
L L H
a b c d e f g h i
a Sensor model
LL H E-Series/R-Series
c Order length
X X X X M 0156…2646 mm
X X X X U 006.2…104.2 in.
.
1 2 3 4 5 6 7 8 9 10 11 12 13 14 15 16
d Output
S 1 B 0 SSI, 25 bit, Binary, 0.1 mm resolution*
S 1 G 0 SSI, 25 bit, Gray, 0.1 mm resolution*
S 2 B 0 SSI, 24 bit, Binary, 0.1 mm resolution*
S 2 G 0 SSI, 24 bit, Gray, 0.1 mm resolution
C 3 1 1 CANopen, 1000 kBit/s, 20 um, 1 magnet
C 3 2 1 CANopen, 500 kBit/s, 20 um, 1 magnet
C 3 3 1 CANopen, 250 kBit/s, 20 um, 1 magnet
C 3 4 1 CANopen, 125 kBit/s, 20 um, 1 magnet
C 4 1 1 CANopen (bus terminator), 1000 kBit/s, 20 um,
1 magnet
C 4 2 1 CANopen (bus terminator), 500 kBit/s, 20 um,
1 magnet
C 4 3 1 CANopen (bus terminator), 250 kBit/s, 20 um,
1 magnet
C 4 4 1 CANopen (bus terminator), 125 kBit/s, 20 um,
1 magnet
V 1 0 1 10…0 Vdc RH-V
A 1 0 1 20…4 mA RH-V
d Output
Voltage
V 1 1 0 10…0 Vdc (1 output channel with 1
position magnet)
Current
A 1 1 0 20…4 mA (1 output channel with 1
position magnet)
U 4 0 1 Profinet RT & IRT
U 4 0 2 Profinet RT & IRT
U 2 0 1 EtherNet/IP
U 3 0 1 POWERLINK
U 1 0 1 EtherCAT
L 0 0 0 IO-Link
17 18 19 20
See next page
f
*/ Measurement direction is set to measure away from housing towards tip.
**/ Only available with Sensor Pipe options E and F

Level Plus® LLH
Operation Manual
I10 I
***/ Only available with Sensor Pipe Options E and F and NPT Process Connection Type
****/ Make sure to order the sensor with a process connection large enough to fit the float
when ordering Sensor Pipe options E or F.
f Process Connection Size
A3/4" ***
B1" ***
C1½"
D2"
F2½"
G3"
H4"
J6"
XNone
ZCustom Flange
gFloat 1 ****
X X None
S 1 401513-2
S 5 200931-6
S 7 251234-2
S 8 252228-2
S 9 403374
S A 560564-2
h Float 2
X X None
f Options
C5 m cable
XNone
Manuals, Software & 3D models available at:
www.temposonics.com

Level Plus® LLH
Operation Manual
I11 I
5.6 Technical data
Output Options
Voltage 0…10 VDC or 10…0 VDC, 0…10 VDC and 10…0 VDC (controller input resistance RL > 5 kΩ)
Current 4…20 mA or 20…4 mA (minimum / maximum load: 0 / 500 Ω)
SSI (Synchronous Serial Interface) Binary or Gray, 24 or 25 bit
CANbus CANopen: CIA standard DS 301 V3.0 / encoder profile DS 406 V3.1, CAN System ISO-11898
IO-Link V1.1, 32 bit signed, COM3 (230.4 kBaud)
EtherCAT 100 Base-Tx, Fast Etherner, 100 MBits/s max
POWERLINK Ethernet POWERLINK V2
EtherNet/IP Encoder CIP device profile with CIP Sync and DLR capabilities, 100 MBits/s max
Profinet Profinet RT, Profinet IRT version 2.3, MTS Profile and Encoder Profile 4.1, 100 MBits/s max
Measured value Product Level and/or Interface Level
Measurement parameters
Resolution 0.1 mm or greater
Inherent accuracy +/-0.5 mm
Repeatability ≤ ±0.005 % F.S. (minimum ±20 μm)
Operating conditions
Operating temperature −40…+75 °C (−40…+167 °F)
Humidity 90 % relative humidity, no condensation
Ingress protection 1IP67 / IP69K (select outputs only, see manual 552103) (correctly fitted)
Shock test 100 g (single shock) IEC standard 60068-2-27
Vibration test 15 g / 10…2000 Hz IEC standard 60068-2-6 (resonance frequencies excluded)
EMC test Electromagnetic emission according to EN 61000-6-3
Electromagnetic immunity according to EN 61000-6-2
The sensor meets the requirements of the EU directives and is marked with
Design/Material
Sensor electronics housing/Flange Stainless steel 1.4305 (AISI 303); option: Stainless steel 1.4404 (AISI 316L)
Wetted parts Stainless steel 1.4404 (AISI 316L) Ra 25 uin. (Ra 0.625um)
Order Length 127 to 2525 mm (5.0 to 99.4 in)
Operating pressure 5/8" O.D. 69 bar (1000 psi)
Mounting
Rigid Pipe NPT (3/4", 1", 1.5", 2", 2.5", 3", 4"), ANSI RF Flange (2", 3", 4", 5", 6") (150#, 300#, 600#)
Electrical connection
Connection type M12 male connector (for pin see page 5 and page 6)
Operating voltage +24 VDC (−15 / +20 %); UL recognition requires an approved power supply with energy
limitation (UL 61010-1), or Class 2 rating according to the National Electrical Code (USA) /
Canadian Electrical Code
Ripple ≤ 0.28 VPP
Current consumption Analog: 50…140 mA, SSI, CANbus & IO-Link: 60 mA
Dielectric strength 500 VDC (DC ground to machine ground)
Polarity protection Up to −30 VDC
Overvoltage protection Up to 36 VDC
1/ The IP rating is not part of the UL recognition

Level Plus® LLH
Operation Manual
I12 I
5.7 Technical drawing
Controlling design dimensions are in millimeters and measurements in ( ) are in inches
LLH - E-Series
48
(1.9)
Sensor
electronics
housing
85
(3.4)
44
(1.7)
34
(1.3)
13
(0.5)
Product float Sensor rod
16 (0.625) OD
M12 Connector
Process connection
Sanitary Tri-Clamp
76.2
(3.0)
Inactive zone
127…2525
(5.0…99.4)
Order length
LLH - R-Series
68
(2.7)
Sensor
electronics
housing
93
(3.7)
55
(2.2)
27
(1.9)
17
(0.7)
Product float Sensor rod
16 (0.625) OD
M12 Connector
Process connection
Sanitary Tri-Clamp
76.2
(3.0)
Inactive zone
127…2525
(5.0…99.4)
Order length
End plug options
Fig. 2: Technical drawing LLH and End plug options

Level Plus® LLH
Operation Manual
I13 I
6. Installation and mounting
6.1 Training
Installation should only be conducted by qualified service person-
nel according to local regulations or Temposonics trained service
technicians. Temposonics offers web based and in person training for
installation, commissioning, maintenance, and repair. Temposonics
also offers factory direct services for these same functions. Contact
Temposonics to discuss training or factory direct services before
starting.
6.2 Stilling wells and guide poles
Level Plus®transmitters can be mounted in slotted or unslotted stilling
wells but a slotted stilling well is always preferred. Using a unslotted
stilling well will negatively affect performance of any level device as
the level in the stilling well can differ from the level in the tank. The
Level Plus®transmitter can also be installed to one side of the stilling
well to also allow for sampling and manual gauging from the same
opening as the automatic tank gauging. Contact technical support for
details.
Level Plus®transmitters do not require a stilling well for installation.
Our transmitters are installed in numerous tanks without stilling wells
with no loss in performance due to our patented flexible waveguide
and hose. A stilling well is highly recommended for agitated, turbulent,
and/or fast filling tanks.
6.3 Tools
• Adjustable pliers
• Large pipe wrench
• Common head screwdriver, slotted screwdriver
6.4 Installation steps
Caution:
It is recommended that assembly and mounting of this transmitter
should not be done alone. To ensure proper and safe assembly
of the level transmitter, a minimum of two (2) individuals are
recommended. Gloves are also recommended. PPE may be required
for work areas such as safety shoes, safety glasses, and hard hat.
1. Consult chapter 4.3 before starting.
2. Perform steps 1-10 in chapter 8.4.1
3. For pipe options C with T-bar end plug and D with DP end plug
the floats are captive and cannot be removed.
4. For pipe options E with Clean-in-Place end plug and F with DN
end plug the floats can be removed.
5. The pipe options E and F can be ordered with the 3/4" NPT fitting.
For this combination, remove the float and add adapter. Slide
adapter up the pipe and do not scratch the pipe. Place float on
pipe at the bottom.Do not drop float or allow it to free fall along
the rigid pipe as damage may result.
6. Insert the rigid pipe and floats through the tank opening and
lower the transmitter/ float assembly into the tank.
7. For Tri-clamp process connections, lower until the Tri-clamp rest
on the mating connection of the tank. Install Tri-clamp.
8. For NPT connections, connect the adapter to the tank. Position
level transmitter at desired height and tighten NPT fitting.
9. Connect cable to connector.
10. Terminate the pigtail cable noting proper wire orientation. Wiring
diagram is shown in Section 7.
Consult Section 5.7 Technical Drawing to reference what the finished
installation should look like.

Level Plus® LLH
Operation Manual
I14 I
6.5 Mounting
The method of mounting the transmitter is dependent on the vessel
or tank in which it is being used, and what type of transmitter is being
mounted. For model LLH there is a NPT thread mount or Tri-clamp
mount.
NPT Threaded mounting
In some applications, the model LLH transmitter can be mounted
directly to the tank or flange via a NPT threaded fitting,assuming
there is a proper threaded connection available. If the float will not fit
through the flange opening when the flange is removed, there must
be some alternative means to mount the float on the transmitter from
inside the vessel; this may require an access port nearby the entry
point of the transmitter as shown in Fig. 3.
Tri-Clamp mounting
The model LLH can also be mounted to a Tri-Clamp as shown in Fig. 4.
Depending on the end plug the float may come on the level transmitter.
If not, install the float on the level transmitter. To complete the
installation, mount the transmitter, Tri-clamp and float as a unit into
the tank.
Riser
NPT or BSPP fitting
Tank flange
(customer supplied
or ordered separately)
Float access
port
Tip of transmitter
Tri-Clamp®Cap size
Inactive Zone
(See important note below)
Sanitary
Tri-Clamp®Cap
Sanitary
Tri-Clamp®Fitting
34 mm
(1.3 in.)
13mm
(0.5 in.)
48 mm
(1.9 in.)
85 mm
(3.4 in.)
305 mm (12 in.) to
7620 mm (300 in.)
Fig. 3: NPT Threaded mounting
Fig. 4: Tri-Clamp mounting

Level Plus® LLH
Operation Manual
I15 I
7. Electrical connections
7.1 Basic information
Placement of installation and cabling have decisive influence on
the sensor‘s electromagnetic compatibility (EMC). Hence correct
installation of this active electronic system and the EMC of the entire
system must be ensured by using suitable metal connectors, shielded
cables and grounding. Overvoltages or faulty connections can damage
its electronics despite protection against wrong polarity.
7.2 Safety recommendations
Be sure to:
1. Always follow applicable local and national electrical codes and
observe polarity when making electrical connections.
2. Never make electrical connections to the level transmitter with
power turned on.
3. Use low-resistant twisted pair and shielded cables. Connect the
shield to ground externally via the controller equipment.
4. Keep control and sign leads separate from power cables and
sufficiently far away from motor cables, frequency inverters, valve
lines, relays, etc.
5. Use only connectors with metal housing and connect the
shielding to the connector housing.
6. Keep the connection surface at both shielding ends as large as
possible. Connect the cable clamps to function as a ground.
7. Keep all non-shielded leads as short as possible.
8. Keep the earth connection as short as possible with a large cross
section. Avoid ground loops.
9. With potential differences between machine and electronics
earth connections, no compensating currents are allowed to flow
across the cable shielding. Recommendation: Install potential
compensating leads with large cross section or use cables with
separate double shielding, and connect only one end of the shield.
10. Use only stabilized power supplies in compliance with the
specified connecting values
NOTICE
1. Do not mount the sensors in the area of strong magnetic or
electric noise fields.
2.Never connect / disconnect the sensor when voltage is applied.

Level Plus® LLH
Operation Manual
I16 I
7.3 Grounding
Earth/Machine Ground
The LLH is earth grounded through the process connection to the
tank with the assumption that the tank is grounded. If the tank is not
grounded then a ground will need to be connected to the housing of
the LLH. Without correct grounding the overvoltage protection will be
compromised.
Shield Ground
Immunity performance of the sensor from external sources of surge,
burst, RF, radiated emissions and other noise is dependent on a proper
ground for the shield of the communications cable. The communica-
tions cable shield should be of a braided type and connected to the
internals.
.
7.4 Wiring Connections
D34 Analog
Signal + power supply
M12 male connector
(A-coded) Pin Function
1
2
3
4
5
View on sensor
1+24 VDC (−15 / +20 %)
2 Output 1
3 DC Ground (0 V)
4 Output 2
5 DC Ground
D34 CAN
Signal + power supply
M12 male connector
(A-coded) Pin Function
1
2
3
4
5
View on sensor
1 Shield
2+24 VDC (−15 / +20 %)
3 DC Ground (0 V)
4 CAN_H
5 CAN_L
D44 IO-Link
Signal + power supply
M12 A-coded Pin Function
2
1
4
31 +24 VDC (±25 %)
2DI / DQ
3 DC Ground (0 V)
4C / Q
Fig. 5: D34 Analog
Fig. 6: D34 SSI
Fig. 7: D44 IO-Link
D56
Port 1 – Signal
M12 female connector
(D-coded) Pin Function
View on sensor
1 Tx (+)
2 Rx (+)
3Tx (−)
4Rx (−)
Port 2 – Signal
M12 female connector
(D-coded) Pin Function
View on sensor
1 Tx (+)
2 Rx (+)
3Tx (−)
4Rx (−)
Power supply
M8 male connector Pin Function
2
4
1
3
View on sensor
1 +12…30 VDC (±20 %)
2 Not connected
3 DC Ground (0 V)
4 Not connected
Fig. 8: D56
D84 SSI
Signal + power supply
M12 male connector
(A-coded) Pin Function
1
4
2
6
3
5
7
View on sensor
1 Clock (+)
2Clock (−)
3 Data (+)
4Data (−)
5 Not connected
6 Not connected
7+24 VDC (−15 / +20 %)
8 DC Ground (0 V)
Fig. 9: D84 CAN

Level Plus® LLH
Operation Manual
I17 I
D58
Port 1 – Signal
M12 female connector
(D-coded) Pin Function
View on sensor
1 Tx (+)
2 Rx (+)
3Tx (−)
4Rx (−)
Port 2 – Signal
M12 female connector
(D-coded) Pin Function
View on sensor
1 Tx (+)
2 Rx (+)
3Tx (−)
4Rx (−)
Power supply
M12 male connector
(A-coded) Pin Function
View on sensor
1 +12…30 VDC (±20 %)
2 Not connected
3 DC Ground (0 V)
4 Not connected
Fig. 10: D58

Level Plus® LLH
Operation Manual
I18 I
8.4.2 Severe Service Applications
8.4.2.1
Perform Inspection suggested in chapter 8.3.
8.4.2.2
Disconnect Power.
8.4.2.3
Disconnect process connection from tank. Remove level transmitter
from tank.
8.4.2.4
When the bottom of the pipe is reached inspect the float(s).
8.4.2.4.1
If the floats are highly contaminated then remove the assembly from
the tank and remove the floats from the pipe.
8.4.2.4.2
If the floats are slightly contaminated then clean the floats without
removing the floats from the pipe.
8.4.2.5
Add anti-seize or similar lubricant to connection to prevent daamge to
threads. Replace rigid pipe and floats in tank.
8.4.2.6
Connect process connection to tank.
8.4.2.7
Connect Power.
8.4.2.8
The process should be carried out regularly until a consistent pattern
has been established as to how long the intervals between cleanings
should be.
8. Maintaince
8.1 Training
Installation should only be conducted by qualified service personnel
according to local regulations or Temposonics trained service
technicians. Temposonics offers web based and in person training for
installation, commissioning, maintenance, and repair. Temposonics
also offers factory direct services for these same functions. Contact
Temposonics to discuss training or factory direct services before
starting.
8.2 Tools
• Adjustable wrench
• Anti-seize
8.3 Inspection
Below are some standard items that should be inspected on a
regular basis to make sure that the level transmitter and surrounding
environment are in operating condition.
• There are no visible unauthorized modifications
• Electrical connections are tight
• No obvious damage to cable
• Housing is not damaged or cracked
• No corrosion on visible parts
8.4 Preventative maintenance
The level transmitters do not typically require preventative
maintenance but may require preventative maintenance dependent
on the application. For general purpose applications where there is
no potential for buildup on the pipe and/or float there is no need for
preventative maintenance but routine inspection is still suggested.
For severe service applications where there is potential for buildup on
the pipe and/or float then preventative maintenance is
8.4.1 General purpose applications
8.4.1.1
Perform Inspection suggested in chapter 8.3.
8.4.1.2
It is suggested to disconnect the process connection between the tank
and the level transmitter and anti-seize or similar lubricant to prevent
damage to threads.
8.4.1.3
No additional preventative maintenance is necessary. Preventative
maintenance suggested for Severe Service Applications may be
performed.
NOTE
It is best to clean the pipe as it is removed from the tank to minimize
the amount of product that is removed from the tank. The user
should take caution and abide by all regulations so that product is
not spilled and the environment is not contaminated.

Level Plus® LLH
Operation Manual
I19 I
9. Repair
9.1 RMA policy
Important:
Contact Technical Support or Customer Service for assistance if
you suspect that the transmitter is not working correctly. Technical
support can assist you with troubleshooting, part replacement, and
Returned Material Authorization (RMA) information if required.
All Level Plus®transmitters come with a two year limited warranty
from the factory shipment date. A Return Materials Authorization
(RMA) number is required and must accompany any transmitter
returns. Any unit that was used in a process must be properly cleaned
in accordance with OSHA standards, before it is returned to the
factory. A Material Safety Data Sheet (MSDS) must also accompany
the transmitter that was used in any process.
9.2 Training
Repair should only be conducted by qualified service personnel
according to local regulations or Temposonics trained service
technicians. Temposonics offers web based and in person training for
installation, commissioning, maintenance, and repair. Temposonics
also offers factory direct services for these same functions. Contact
Temposonics to discuss training or factory direct services before
starting.
9.3 Troubleshooting
Symptom Possible cause Action
No
communication
with transmitter
No power Check voltage at
transmitter
Wiring incorrect Reference installation
drawing chapter 7.4
Wrong protocol Conrm software and
transmitter are same
protocol
Fig. 11: Troubleshooting reference

Level Plus® LLH
Operation Manual
I20 I
Fig. 12: Spare parts
10. Spare Parts
Below are the spare parts list for the LP-Series shown as the display,
electronic module, sensing element, and flexible hose. Please contact
Temposonics Technical Support with any questions.
11. Interface
11.1 Analog output
The analog output for LLH is a single output The output codes
starting with V are voltage outputs and the codes starting with A are
current outputs. The first digit is the voltage or current closest to the
head and the second is closet to the tip. For example, A010 4..20mA
has the 4mA set point closest to the head and 20 mA closest to the tip.
The analog output cannot be adjusted.
11.2 IO-Link output
IO-Link is an open standard according to IEC 61131-9. It is a serial,
bi-directional point-to-point connection for signal transmission and
energy supply. The bi-directional communication enables consistent
communication between sensors and the controller as well as
consistent diagnostic information down to the sensor level. For
additional details on setup please consult the EH IO Link manual
551485 section 5.
The measurement direction of IO Link can be programmed by the
customer. The Parameter Measuring Direction, Index 0x73, can be set
to False to measure from the housing to the tip of the pipe or True to
measure from the tip of the pipe to the housing.
Cable Part number
Analog 370675
IO-Link 370675
CANopen 370675
SSI 370676
Ethernet Power 530066
Ethernet Communication 530065
Process Connection Part number
1 “ NPT 562349-1
1,5 “ NPT 562349-2
2 “ NPT 562349-3
2,5 " NPT 562349-4
3 " NPT 562349-5
4 " NPT 562349-3
11.3 SSI output
The SSI output is available as either 24 or 25 bit, Binary or Gray code,
and 0.1 mm resolution. The measurement direction is set to measure
up from the tip of the pipe.
11.4 CANopen output
CANbus (Controller Area Network) is designed for high-speed data
exchange at machine level. CAN is a vendor independent open
fieldbus system, based on standard ISO 11898. CAN specifies the
functional and technical parameters with which the intelligent digital
automation devices can be networked via a master-slave serial link
by using a communication profile. Protocol architecture of functional
and applications data is oriented to the OSI reference model (ISO
7498). Bus technology is administrated and developed by the user
organisation CiA (CAN in Automation)
The CANOpen output of the LLH is avaialbe with or without integral
termination, selectable Baud rate of 1000, 500, 250, or 125 kBit/s.
The resolution is set at 0.02 mm and the output can be configured for
1 or 2 floats. The measurement direction is set to measure away from
the electronic housing and towards the tip of the pipe
11.5 Profinet RT & IRT
The model LLH is are available with PROFINET RT (Real Time)
and IRT (Isochronous Real Time). PROFINET IRT offers a
synchronized communication with a minimum cycle time of 250 µs.
For time-critical applications, linear extrapolation enables synchronized
controller communication for any stroke length of the sensor.
In addition to the measured position value via the PROFINET protocol
further data about the current sensor status, such like the total
distance travelled, the internal temperature and the total
operating hours, can be displayed for diagnostic purposes
For details on the Profinet RT & IRT output consult operation manual
551973 sections 5 and 6. The measurement direction by default is set
to measure away from the housing. The direction can be changed to
Reverse to allow for measuring away from the tip of the pipe
11.6 Ethernet/IP
The EtherNet/IP™ output supports CIP Sync™ (Common Industrial
Protocol) and DLR (Device Level Ring) capabilities. CIP Sync™ offers
synchronization between devices in an EtherNet/IP™ network, allowing
for increased control coordination in time-critical applications. DLR
capability provides a fault-tolerant network so that the sensor can be
used in ring connection topologies when reliable continuous system
operation is required.
Table of contents
Other Amphenol Measuring Instrument manuals

Amphenol
Amphenol Protimeter ReachMaster Pro User manual

Amphenol
Amphenol Protimeter Hygromaster2 User manual
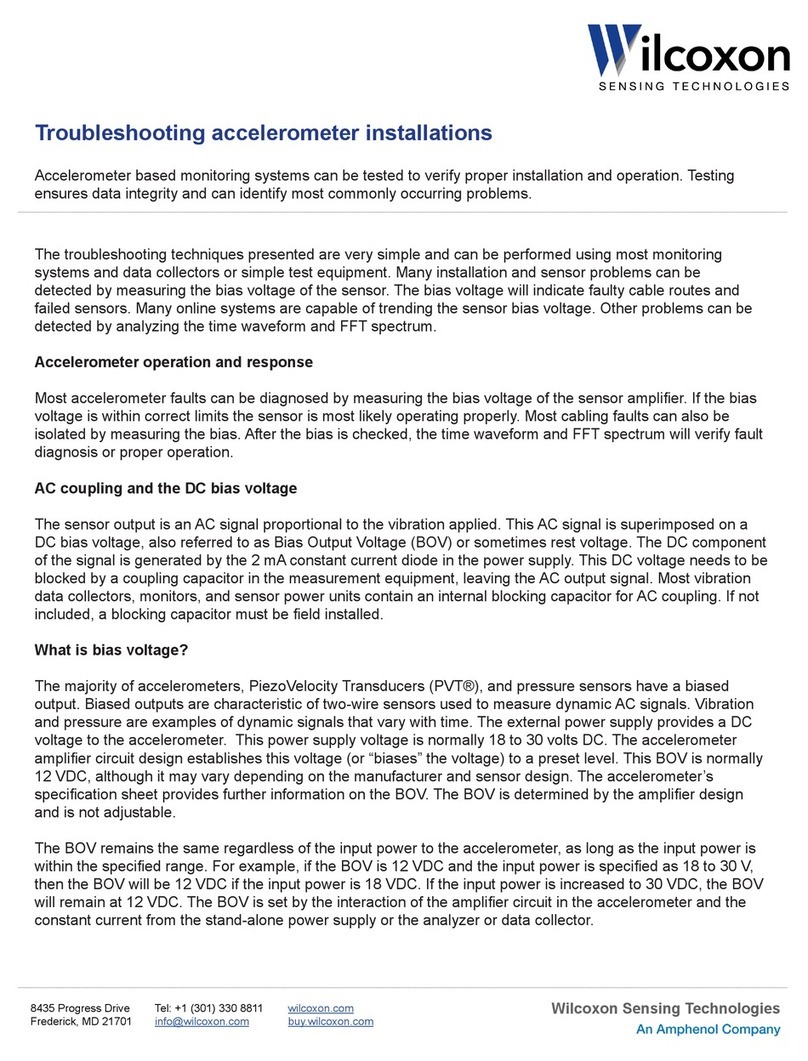
Amphenol
Amphenol Wilcoxon TN14 User manual

Amphenol
Amphenol PROTIMETER HygroMaster-L BLD7750L User manual

Amphenol
Amphenol THE MODAL SHOP 831 User manual
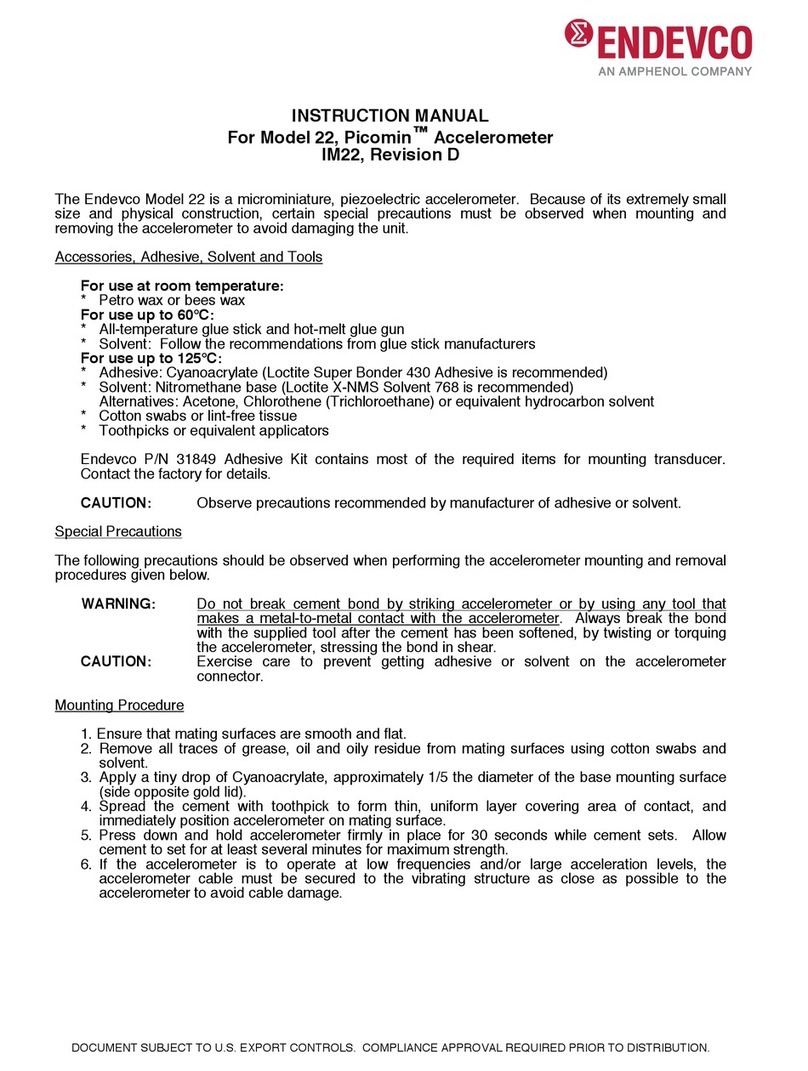
Amphenol
Amphenol ENDEVCO Picomin 22 User manual

Amphenol
Amphenol 240GT54 User manual
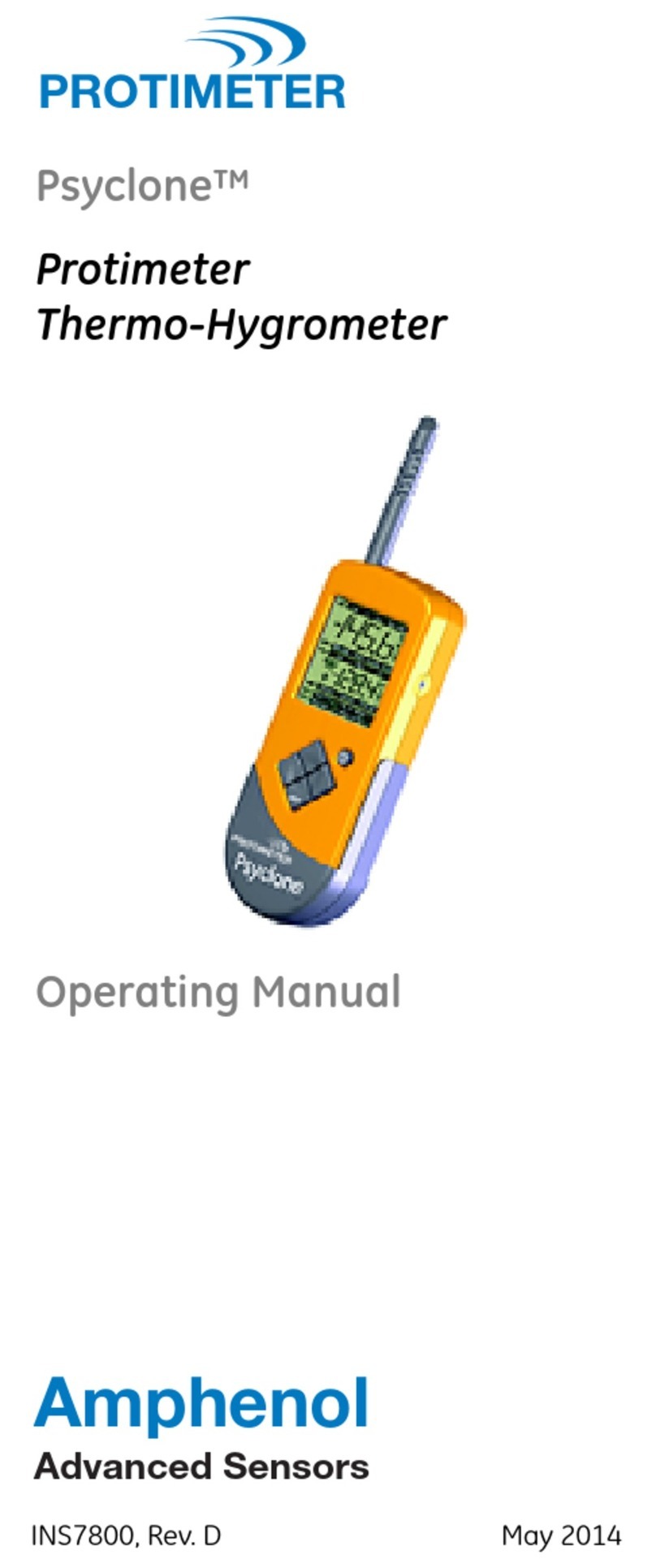
Amphenol
Amphenol PROTOMETER Psyclone User manual