Analyticon combi scan 500 User manual

User‘s Manual
Analyzer for
CombiScreen®11 SYS
urine test strips

1
Contents

1
Contents
Contents
1. Introduction .......................................................................................... 2
1.1. Methodology of the urine test ............................................................................... 2
1.2. The test strips........................................................................................................ 3
1.3. Intended use.......................................................................................................... 3
2. Description of the reader..................................................................... 4
2.1. Packing list ............................................................................................................ 6
3. Installation ............................................................................................ 7
4. Operation .............................................................................................. 9
4.1. Switching on/off..................................................................................................... 9
4.2. Overview of the menu system ............................................................................... 9
4.3. Worklist ................................................................................................................ 10
4.3.1. Add a worklist .............................................................................................. 10
4.3.2. Edit a worklist .............................................................................................. 10
4.4. Start ..................................................................................................................... 11
4.4.1. Mesurement ................................................................................................. 12
4.4.2. Result printout ............................................................................................. 13
4.5. Menu.................................................................................................................... 13
4.5.1. Setup menu.................................................................................................. 13
4.5.1.1. Output settings .................................................................................... 14
4.5.1.1.1. Printer settings ............................................................................ 14
4.5.1.1.2. Serial port settings ...................................................................... 14
4.5.1.1.3. Language settings....................................................................... 14
4.5.1.2. Strip options ........................................................................................ 15
4.5.1.2.1. Measurement units...................................................................... 15
4.5.1.2.2. Sensitivity adjustment ................................................................. 15
4.5.1.2.3. Pad sequence in printout ............................................................ 16
4.5.1.3. Clock and date settings....................................................................... 16
4.5.2. Service ......................................................................................................... 17
4.5.2.1. Cleaning............................................................................................... 17
4.5.2.2. Calibration settings.............................................................................. 18
4.5.3. Memory........................................................................................................ 18
4.5.3.1. Memory data transfer .......................................................................... 19
4.5.3.2. Clearing data from memory................................................................. 19
4.6. Data download .................................................................................................... 20
5. Care of the instrument....................................................................... 21
5.1. Cleaning of the waste bin .................................................................................... 21
5.2. Cleaning of the conveyor..................................................................................... 21
6. Warnings / Precautions ..................................................................... 22
7. Troubleshooting.................................................................................. 23
8. Technical data..................................................................................... 24
9. Symbols............................................................................................... 25
Appendix ................................................................................................. 26
V4.2.3 revised 3/2009

2
Introduction
3
Introduction
1. Introduction
1.1. Methodology of the urine test
The urinalysis is part of the medical diagnosis methods frequently used by medical doc-
tors in laboratories in order to reveal diseases. The most cost-effective device used to
screen urine is a reagent test strip. This microchemistry system has been available for
many years and allows qualitative or semi-quantitative analysis within one minute by sim-
ple but careful observation. The colour change occurring on each test pad of the strip is
compared to a colour chart to obtain the result. However, misreading or misinterpreting of
results, caused by individual handling habits of the user or different light conditions, may
happen. Urine analyzer (urine strip reader) equipment is designed specifically to improve
the accuracy and security of urine strip evaluation by using light and photometric reader
in order to detect the colour changes on the test strips. The CombiScan®500 supports
test data management and report generation by offering data storage and computerised
data processing features.
The CombiScan®500 is a urine analyzer for professional use. The reader is a semi-auto-
matic benchtop instrument designed to read the CombiScreen®11SYS reagent strips.
The operator needs only to feed the equipment by placing the moisturised strip on the
conveyor – the rest, as forwarding, reading, evaluating and disposal of the strips is done
automatically by the device. The timing (route-length and speed of the conveyor belt) is
adequate to the incubation time of the test strip.
The CombiScan®500 analyses the colour and intensity of the light reflected from the rea-
gent surface and reports the results in clinical meaningful units. No further calculation is
needed by the user. When a strip is moved into the measuring position under the optical
unit, the reflectance of each reagent pad is measured. The light reflected at specific wave-
lenghts from the test pad depends upon the degree of colour change of the pad, which
is related to the concentration of the particular parameter in urine. The intelligent image
analyzer software first detects, locates the strip and the pads, then, based on these colour
light-wave information the CombiScan®500 reads the reagent areas and the values are
calculated automatically. Results are stored, then printed out by the built-in printer and
can optionally be sent to host computer via serial connection.

2
Introduction
3
Introduction
1.2. The test strips
The base of the urine analysis is the good quality of the urine test strip. These strips have
separated pads for each parameter. The test pads contain reagents, which cause colour
changes according to the parameter concentration in the urine. The CombiScan®500 is
calibrated to CombiScreen®11SYS urine test strips and guarantees accurate results all
time. The CombiScreen®11SYS urine test strip contains reagents for testing:
Bilirubin
Urobilinogen
Ketones
Ascorbic Acid
Glucose
Protein
Blood
pH
Nitrite
Leukocytes
Specific Gravity
Besides the CombiScreen®11SYS, the CombiScreen®11SYS PLUS can also be used
with this instrument. To facilitate reading of the manual, the test strip is always named
CombiScreen®11SYS in this manual.
IMPORTANT! Before using the test strip read carefully the CombiScreen®
11 SYS packing insert! The meter can only be used with the CombiScreen®
11 SYS urine test strip!
1.3. Intended use
CombiScan®500 is an instrument for measurement of urine test strips CombiScreen®
11SYS for in-vitro determination of Ascorbic acid, Bilirubin, Blood, Glucose, Ketones,
Leukocytes, Nitrite, pH, Protein, Specific Gravity and Urobilinogen from urine. These
measurements are used in the evaluation of diabetes, liver diseases, haemolytic diseases,
urogenital and kidney disorders or metabolic abnormalities. For professional use, not for
self testing.

4
Description of the reader
5
Description of the reader
2. Description of the reader
The equipment is designed specifically for use in clinical laboratories. In its basic instal-
lation the housing is almost fully closed, its physical appearance including colour meets
the requirements raised by medical laboratories. Its throughput is about 500 test strip
evaluations/hour.
The optical system is designed espe-
cially for evaluation of urine test strips.
The test strip is illuminated by white
light and the reflected light from the
reagent strip is detected by a colour
CCD sensor. The signals are digitalized
and this digitalized image is evaluated
by the built-in program.
Due to the CCD-technology, the instru-
ment is able to distinguish between
colour changes caused by reaction of
the test pad chemistry and non-spe-
cific colour development, caused by
the sample.
Operation is very simple, and doesn’t
require any special knowledge or dif-
ficult practice. When measurement
starts, the front door opens and the
conveyor assembled onto a carriage
moves into the measuring position.
The strip needs to be placed on the
conveyor. Both the conveyor and the
carriage are driven by a DC motor.
Fig.1 Front view of the CombiScan®500 urine analyzer
LCD
Controll Keys
Numeric Keys
Function Keys
Front Waste-bin
Fig. 1
Carriage Strip Pumper
Front Shaft
Support
Rear Shaft Cylinder 1 Cylinder 2
Belts
Fig. 2 Description of the parts for installation
Fig. 2

4
Description of the reader
5
Description of the reader
The carriage has three positions:
Closed: The whole carriage is inside of the housing and the Frontdoor is closed. This is
the stand-by or off position.
Measurement: The front of the carriage is ejected of the reader housing in order to let
the operator place the strip onto the three-belt conveyor.
Maintenance: The carriage is fully ejected. In this position you can remove the belts and
cylinders for cleaning.
CAUTION! The carriage movement is controlled by the reader, never try to move
it manually, not even when the reader is in stand-by or turned-off position! If the
power shuts down when the carriage is ejected or an error occures, turn the
reader off and on. The carriage will find its normal position automatically.
The used strips are collected in a waste bin located under the conveyor inside the Com-
biScan®500 (capacity: about 150 strips). If the automatic strip-counter reaches 150 you
will get a warning message which asks you to empty the waste-bin. To remove the waste-
bin just push and release its front panel. It will be automatically ejected. Pull it out totally,
empty it and insert it back. Slip it gently till it is bumping (see section 5.1.).
On the top side of the CombiScan®500 you can find the built in printer. If you open the
printer cover by lifting it’s front side you will get access to the paper roll cave to load
printer paper. For loading the printer paper refer to section 3 (Installation).
The interface connectors are located on the back panel. The external barcode reader and/
or keyboard can be connected to the keyboard interface connector. The host computer
can be connected to the RS232 serial port.
DC connector Keyboard
Interface
RS232
Serial Port
Fig. 3 Rear view of the CombiScan®500 urine analyzer
Fig. 3
Slot
Firmware

6
Description of the reader
2.1. Packing list
CombiScan®500 instrument 1 pc
cylinder 1 1 pc
cylinder 2 (with gearwheel) 1 pc
belt 6 pcs
power adapter 1 pc
power cord 1 pc
serial cable 1 pc
users’ manual 1 pc
printer paper 1 roll
CD 1 pc (optional)

7
Installation
3. Installation
The CombiScan®500 is shipped in a carton box. Prior to unpacking, clear the area where
the instrument is to be operated, a surface of about 30x50 cm will be needed. While
handling the package, please be cautious of the shipping marks on the box. Open the
box. Cut the tape only, leaving the carton material intact. It is recommended to keep the
packing materials for a while as well, in case the instrument needs to be moved to another
location or must be shipped to have it been repaired in the manufacturers’ service. Check
the packing list, if the shipment is complete (see section 2.1.). If it is complete follow the
instruction below otherwise please contact your distributor immediately.
Place the CombiScan®500 to its working position.
Optional: Connect the CombiScan®500 to your computers’ serial port, by using the
serial cable, if necessary.
Optional: Connect your keyboard or barcode reader optional to the interface connec-
tor.
Connect the power adapter first to DC connector then to the mains.
Switch the reader on by pressing ENTER on the built-in keypad.
In a few seconds the actual software version appears for a short moment on the LCD.
„CLEAR MEMORY“ appears on the display.
Press QUIT. Now you reach the MAIN MENU.
Select MENU by pressing the control key below the MENU sign.
Select SERVICE by pressing the control key.
Select CLEAN by pressing the control key. Now the door opens automatically and the
conveyor section moves out until the cleaning position is reached.
Install the cylinder 2 (with the gear-
wheel) onto the rear shaft until the
built in magnet fixes it in the proper
position (see fig. 4).
Install the cylinder 1 onto the front
shaft until the built in magnet fixes
it in the proper position (see fig.4).
Front Shaft Rear Shaft
Strip
Bumper
Fig. 4 Installation of the cylinders
Fig. 4

8
Installation
Install all the three belts onto the
cylinders (see fig. 5).
Press the OK key. Now the convey-
or slips back and the door closes
automatically.
Open the printer cover.
Take the roll of printer paper and insert the roll into its cave. Load the free end of the
paper into the feeding slot in a way, that the outer side of the paper roll is facing down
while inserting it into the feeding slot (if the paper is inserted in the wrong way, there
will be no printout on the paper). The paper will be loaded automatically (see fig. 6). To
remove the paper, just pull out from top side.
Now, the CombiScan®500 is ready to work.
Note: Before the first measurement a calibration process should be done (see
section 4.5.2.2.)!
Fig. 5 Installation of the belts
Fig. 5
Printer Cover
Printer Paper
Printer
Fig. 6 Loading the printer paper
Fig. 6

9
Operation
4. Operation
4.1. Switching on/off
Connect the CombiScan®500 with the power adapter to a power socket. Press the EN-
TER button if the instrument is in standby mode. The name and software version of the
instrument is displayed on the LCD for a short time. Now, one of the following alternative
options will be executed depending on the stored “working history“ of the reader.
The strip counter is not equal to zero.
This means that measurements were done since the last waste bin emptying. If you empty
it now, press the „YES“ control key and the strip counter will be set to zero. If you do not
clear the waste bin from used strips now, select „Cancel“. In this case the strip counter
will not be reset.
If there are measurement results stored in the memory at the day’s first power-on, the
programm will offer an option of deleting the memory content.
CAUTION! If you select „OK“ all data stored in memory will be erased! Chose
this option only if data have been archived, printed out or you are sure you don‘t
need them any longer!
If the memory is free and the used strip counter is set to zero at the day’s first power on,
the MAIN MENU appears on LCD.
2004/08/09 19:19:26
>>004 Combi Scan 500
<<005 V.4.01.05
WORKLIST START MENU
If you want to switch off the reader, just press the QUIT button. Answer YES when the
reader asks for confirmation. Now the CombiScan®500 is in standby mode.
4.2. Overview of the Menu system
The equipment is controlled by a multilevel menu system. The bottom line of the four-row
LCD indicates the actual selectable menu items – max. 3 at the same time. These menu
points can be selected by pressing the control key right below. Without any selection you
will get back to the main menu by pressing the QUIT button.
2004/08/09 19:19:26
004 Combi Scan 500
005 V.4.01.05
WORKLIST START MENU
MANUAL CombiScan500
001
000
SKIP STOP
2004/08/09 19:19:26
MENU
SETUP SERVICE MEMORY
2004/08/09 19:19:26
MENU/WORKLIST
ITEM Nr: 0
EDIT/ADD CLEAR PRINT

10
Operation
11
Operation
4.3. Worklist
The worklist is a predefined sequence of samples. The worklist contains maximum 128
patients ID’s in the sequence of planned evaluation. A worklist can be generated through a
connected external keyboard or barcode reader. The patient ID is a maximum 13 charac-
ter long string containing either numeric or alphabetic characters. If the worklist is entered
through the internal keyboard, only numeric characters are possible. If you wish to delete
an ID from worklist it can be done in the MENU/WORKLIST/CLEAR submenu.
4.3.1. Add a worklist
The worklist can be entered by the internal keypad, an external keyboard or barcode
reader. Connect the keyboard or barcode reader to the keyboard interface connector of
the CombiScan®500 and press the left control key of the CombiScan®500 to get to the
worklist menu. In the EDIT/ADD worklist-submenu, a name or a patient ID of up to 13
characters can be typed or read in. If you have finalized one name or patient ID, press
enter to go to the next ID. When using a barcode reader, you automatically jump to next
ID after you have entered a new ID. To go back to the main menu press the QUIT button. If
you press the BACK control key you will come back to worklist menu, where you can print
out the worklist. If you wish to start the measurement of the first ID of the worklist quit the
worklist menu and start measurement from main menu.
4.3.2. Edit a worklist
A compiled worklist can be edited as well. You can edit the IDs, add new items or remove
single items or the whole worklist. Inserting a new item into an existing queue is not al-
lowed. To use the worklist features follow the flowchart shown above.
From MAIN MENU you can enter the worklist menue by selecting “WORKLIST”. If there
is no existing worklist the ADD text is displayed on the LCD left side, otherwise EDIT. By
selecting EDIT/ADD option you can modify the patient ID data and/or enter new items. In
the WORKLIST/CLEAR submenu single items or the whole worklist can be deleted, and in
WORKLIST/PRINT submenu the worklist can be printed out.
After pressing EDIT/ADD control key the worklist appears. Using the arrow keys you can
navigate through the worklist. If you want to modify a patient ID, use the DEL function key
2004/08/09 19:19:26
004 Combi Scan 500
005 V.4.01.05
WORKLIST START MENU
2004/08/09 19:19:26
MENU/WORKLIST
ITEM Nr:6
EDIT/ADD CLEAR PRINT
EDIT/ADD WORKLIST
LIST ITEM: 001 EDIT
ID: MILLER JOHN
BACK
2004/08/09 19:19:26
MENU/WORKLIST/CLEAR
ITEM ALL
CLEAR WORKLIST
ITEM: 001 Nr: 6
ID: MILLER JOHN
CLEAR

10
Operation
11
Operation
of the internal keypad to delete the last characters. To confirm the new entered ID press
ENTER. The next worklist item will appear.
Reaching the last item of the worklist ADD will appear on the display. Now you can enter
new items to the list. If the number of worklist elements reaches the limit the “FULL” text
will be displayed instead of the patient ID. To get back to MAIN MENU select BACK option
and than press the ENTER function key of the keypad.
To remove items from the worklist select CLEAR option. In the WORKLIST/CLEAR sub-
menu you can delete the whole worklist by selecting ALL, or just delete individual items
by pressing the ITEM control key. There you can select the desired item using the control
keys. Pressing OK the item will be deleted. To go back to MAIN MENU press QUIT
function key.
4.4. Start
The reader can evaluate only the CombiScreen®11SYS test strips. There is a calibration
card enclosed to the strips. Each calibration card has an individual code. This code au-
thorises the reader to read the strip. To read more about calibration see section 4.5.2.2.
Users should always follow the appropriate federal, state, and local guidelines concerning
the use of external quality control materials.
There is no further special operation needed to calibrate the instrument before starting the
daily routine urinalysis. It is recommended to use urine controls at least daily to check the
system.
It is possible to make measurements in sequence of samples or according to prepared
worklist. If a worklist is stored in the reader „WORKLIST“ is indicated in the START menu
on the left side of the first row of LCD (see below). Otherwise „MANUAL“ is displayed (see
below). To learn more about the worklist refer to section 4.3.
By selecting START the door will open and the conveyor will move out to be ready for
measuring the samples. To stop operation press the STOP control key. The conveyor will
stop running and slips back in “off” position and the door will close. The MAIN MENU will
be displayed again.
IMPORTANT! The reader will only stop operating if the conveyor is empty! The
STOP command will only be accepted if the last strip detection and evaluation
is over. If there is no strip detected for 5 minutes a STOP function will be ex-
ecuted automatically.
During operation the following informations are displayed on the LCD:
WORKLIST Combi Scan 500
001 MILLER, JOHN
000
SKIP STOP
MANUAL Combi Scan 500
001 12345678
000
SKIP STOP
or

12
Operation
13
Operation
4.4.1. Measurement
The day-to-day operation of the CombiScan®500 is easy, and will be guided by the fol-
lowing lines.
Have the urine test sample tubes prepared.
Press the START control key.
Insert an unused strip into the urine specimen, rinse it at the edge of the container,
briefly dap the edge of the test strip on a tissue paper and place it on the conveyor with
the test pads upside. Push the strip gently till it bumps against the strip-bumper. The
strips must be positioned at right angles to the conveyor (see Fig. 7a, 7b). However, the
system is able to compensate slight deviations. From this moment the testing process
is controlled automatically by the CombiScan®500.
If you are in „MANUAL“ mode, you can enter a alphanumeric, max. 13 digit patient ID to
be assigned to the next strip. You can enter the digits via the built-in numerical keypad
or by using a barcode reader or external keyboard. Using the WORKLIST mode the next
patient’s ID appears in the second row of the LCD.
When a strip has been evaluated, the results are sent to the serial port. If a computer
is connected to the reader, the data can be stored and displayed with the Analyti-
con CombiScanner Data Management software (see also section 4.6.). If the build-in
printer is turned on, the results are printed out, too.
After dipping the urine strips into the sample they can be placed on the conveyor. In a
minimum distance of approximately 3cm to the prior strip. This allows a throughput of
about 500 strips per hour.
If you would like to skip a patient ID from the worklist, just select the “SKIP” option and
the reader will delete the element and jump to the next item of the worklist or sequence
number in manual mode.
If during the work you reach the preprogrammed measurement counts (defined by the
calibration card), a warning message will be printed. In this case you are still allowed to
go on measuring an additional 1% of the named counts. Finish your work and perform
a calibration process with a new calibration card (see section 4.5.2.2.). If you do not
calibrate the instrument, it stops working until a new calibration is performed.
After having finished your daily routine press the “STOP” key. The conveyor will stop
running. Clean the instrument and emty the waste bin (see section 5.).
Fig. 7: Positioning of the reagent strip. Fig. 7a shows the right positioning. Fig. 7b shows
a wrong position.
Fig. 7a Fig. 7b

12
Operation
13
Operation
Note: The following error messages may appear during the measurement process.
„The waste bin is full!“ This message is accompanied by a short beep. It means that
the waste bin has not been emptied for 150 measurements. Interrupt the measurement
process and empty the waste bin, then continue working.
“The waste bin is out!“ This message is accompanied by a short beep. It means that
the waste bin is not in the right position. Maybe it wasn’t slipped back completely after
emptying, or it has been opened accidently.
Note: All instructions must be followed thoroughly to get accurate results!
4.4.2. Result printout
The printed/sent results contain the following data: device type, date and time, sequence
number of the test, patient identifier, result with analyte names, values, units, markings for
pathological values and an end line. Before each parameter name the pathological value is
marked with an asterisk (*). If one or more result classification limits (see section 4.5.1.2.2.
for changing sensitivity) have been changed, the bottom line of result starts and ends with
an asterisk (*----*). Each classification range has a name and a unit, corresponding to the
analyte.
Note: The printing on thermal paper may fade during storage, or if it is covered
with transparent tape.
4.5. Menu
The MENU offers the opportunity to adjust the instrument according to individual require-
ments, and to manage the data in memory. To carry out operations, select the MENU op-
tion in the main menu.
4.5.1. Setup menu
The SETUP menu is adapted to customize the CombiScan®500 according to your in-
dividual requirements or working methods. By selecting this menu, you can configure
the communication with your host computer, the built-in printer and the printout format
Date
Sequence Nr.
given by the reader
Patient ID
Values are displayed in conventional units
Pathological values are marked with an as-
terisk (*).
If one or more result classification limits
have been changed, the bottom line of re-
sult starts and ends with an asterisk (*----*).

14
Operation
15
Operation
including the result units, the sensitivity of different pads, etc. To get familiar with these
features please follow the flowchart below:
4.5.1.1. Output settings
In this submenu you can set the printer, the serial port and select the language. Select the
desired function by pressing the buttons below the displayed menu items.
4.5.1.1.1. Printer settings
In this submenu you can check and adjust the printer settings. By pressing the ON/OFF
key the status of the printer can be changed. In off-position the results will be stored in
memory and send to the serial port. In order to secure the permanent printout quality there
is a built-in option to adjust the contrast in a range of 0-3 by pressing the CONTRAST con-
trol key. In this way you can compensate varying paper quality. Pressing the CONTRAST
control key will change the contrast up by one degree. Reaching the highest contrast (+3)
the program will return to 0.
4.5.1.1.2. Serial port settings
Setting up the serial line is needed only if the CombiScan®500 is connected to a compu-
ter. Connect the serial cable to the computer only, if the reader is switched off. The follow-
ing protocols can be selected:
PC unidirectional for use of the CombiScan®500 with a host computer with the CombiS-
canner Data Management software installed.
All other protocols (Labureader, MT1, MT2, CL) are bidirectional protocols. They are need-
ed if the CombiScan®500 is used in a network environment. For more information about
using the CombiScan®500 in a network contact your distributor.
4.5.1.1.3. Language settings
Basically CombiScan®500 supports five languages: English, German, Hungarian, French,
and Spanish. Selecting this submenu use the keys to select the desired language.
Press the OK control key to confirm the selected language. In the printout, Chinese char-
acters can be selected instead of normal characters. If you want to print out the parameter
name in Chinese characters press the “1” numeric key of the keypad. In the same way you
can disable this function. The current setting is displayed on the LCD.
2004/08/09 19:19:26
004 Combi Scan 500
005 V.4.01.05
WORKLIST START MENU
2004/08/09 19:19:26
MENU
SETUP SERVICE MEMORY
2004/08/09 19:19:26
MENU/SETUP
OUTPUT STRIP CLOCK
2004/08/09 19:19:26
MENU/SETUP/STRIP
UNIT SENS. PADSEQ
2004/08/09 19:19:26
MENU/SETUP/OUTPUT
PRINTER SERIAL LANGUAGE
2004/08/09 19:19:26
MENU/SETUP/CLOCK
SET 12/24 SEQUENCE

14
Operation
15
Operation
4.5.1.2. Strip options
There are three possible options to be set: units, pad sensitivity and pad sequence on
printout.
4.5.1.2.1. Measurement units
Results can be displayed in different units. Use the control keys in MENU/SETUP/
STRIP/UNIT submenu to select the desired unit. The CombiScan®500 supports the fol-
lowing measuring units:
Conventional
SI
Arbitrary
Conventional + Arbitrary
SI + Arbitrary
4.5.1.2.2. Sensitivity adjustment
The CombiScan®500 provides semiquantitative results. In special cases, it may be nec-
essary to adjust the sensitivity of single parameters to special requirements of the user,
although it is not recommended by ANALYTICON. To adjust the sensitivity, enter MENU/
SETUP/STRIP/SENS submenu.
Pad measurement sensitivity can be set in two levels in both directions (+/-). The set val-
ues on the display are as follows:
– – 0 – 0 0 0 + 0 + +
2004/08/09 19:19:26
MENU/SETUP/STRIP
UNIT SENS. PADSEQ.
PAD SENSITIVITY
DEFAULT/USER DEFINE
DEFAULT SET QUIT
PAD SENSITIVITY
PAD NAME: BIL
SENSITIVITY: 0
NEXT
When SET option is selected the first PAD name with the actual setting is displayed. After
selecting the SET option the proper sensitivity of each test pad can be selected, using the
control keys. To enter the selected sensitivity of a parameter and to jump to the next
parameter, press the NEXT key. After having set the sensitivity, the program will automati-
cally return to the previous function menu. It is not possible to escape until all pad sensi-
tivities are set. To skip a pad without any modifications just select NEXT.
To get back to MAIN MENU without changing the actual settings, just press the QUIT
function key.
To reset the settings adjusted by the manufacturer for all pads select the DEFAULT option.
Going back to MAIN MENU without changing the actual settings, just press QUIT.

16
Operation
17
Operation
IMPORTANT! The adjustment of the pad sensitivity effects the results of the
measurement! When the reader is adjusted different from manufacturer setting
it will be indicated by asterisks in the footer of the printout!
4.5.1.2.3. Pad sequence in printout
By default, the reader prints out the result in the sequence of the pads physical position
but it is also possible to customize the layout.
2004/08/09 19:19:26
MENU/SETUP/STRIP
UNIT SENS. PADSEQ.
PAD PRINTING SEQUENCE
DEFAULT/USER DEFINE
DEFAULT SET QUIT
PAD PRINTING SEQUENCE
REPORT LINE: 01
PAD NAME: BIL
NEXT
This setup option effects only the printout and data transfer!
If the PADSEQ option is selected, you can restore either the default sequence or set up
your own sequence by selecting the SET option. Selecting SET you can choose pads in
a desired sequence of the printout lines. In the second row the line number is displayed
and the third line indicates the actual parameter name. Using the control keys you can
perform changes. Pressing the NEXT option will display the next printout line. If you select
“End rep.” only the previously selected parameters will be printed out. When the last line
is reached, the program returns to PADSEQ submenu.
NOTE: You can not define empty printout lines or the same parameter twice or
more times.
4.5.1.3. Clock and date settings
The built-in digital clock enables to store the date and time of the measurement. It is
working even if the reader is turned off or the power supply is not connected. The reader
supports different date and time formats.
2004/08/09 19:19:26
MENU/SETUP
OUTPUT STRIP CLOCK
2004/08/09 19:19:26
MENU/SETUP/CLOCK
SET 12/24 SEQUENCE
2004/08/09 19:19:26
ENTER NEW DATE & TIME
>>>

16
Operation
17
Operation
By selecting the MENU/SETUP/CLOCK submenu you can check the actual settings. By
pressing the 12/24 control key you can change between 12 and 24 hour time format. The
SEQUENCE option allows you to change the format of the date.
By selecting the SET option you can adjust the correct date and time. In this submenu use
the >>> control key function pad to move the cursor to the position you want to change.
Enter the correct numbers with the internal keypad or the control keys. Move the cursor
to the rightmost position to leave this submenu. If you press now the QUIT button, you will
get back to main menu.
4.5.2. Service
This submenu allows you to perform a new calibration and to clean the conveyor. Press
the SERVICE button and operate according to the flowchart. For calibration, there is a
calibration card enclosed to the test strips.
4.5.2.1. Cleaning
It is recommended to clean the conveyor regularly. The belts and the support shaft have to
be cleaned daily or even more often, in case of high number of measurements.
2004/08/09 19:19:26
MENU/SERVICE
CLEAN CALIBRATION
PLEASE WAIT...
CLEAN THE CONVEYOR BELT!
OK
For cleaning of the instrument refer to chapter 5.
NOTE: During the carriage movement „Please wait…“ is displayed.

18
Operation
19
Operation
4.5.2.2. Calibration settings
The calibration card is delivered with the reagent strips. Each calibration card has an in-
dividual barcode printed on it. This code contains test strip related data and the number
of measurements that can be carried out after calibration. If the number of measurement
exceeds the predefined number, the reader will stop measuring, and a new calibration has
to be carried out.
2004/08/09 19:19:26
MENU/SERVICE
CLEAN CALIBRATION
PLACE CALIBRATION CARD,
OR ENTER 1ST BARCODE!
MANUAL CANCEL
MANUAL CALIBRATION
Code:
CANCEL
If you select CALIBRATION, the conveyor will move to measurement position, but the con-
veyor will run faster than it does in the measuring modus. Place the calibration card with
the bar code upside on the conveyor. It must be placed at right angles to the conveyor in a
way, that the angle with the barcode is close to the meter. Place the card behind the strip
bumper close to the carriage. Before reaching the optical unit the conveyor will slow down
and the sensor reads the code. The conveyor starts to move in reverse direction delivering
back the calibration card. The stored calibration data will be printed out.
CAUTION! Don‘t throw the calibration card away before the package of strips is
completely consumed!
If the calibration wasn‘t successful or you want to do the calibration manually, select
MANUAL. The conveyor will move back into the housing. Now you can enter the 16 digit
number which is printed below the first barcode. As soon as all numbers are entered, the
code evaluation and calibration process takes place automatically. Details of stored cali-
bration data will be printed out.
To interrupt calibration select CANCEL or press the QUIT button.
4.5.3. Memory
The CombiScan®500 stores the last 999 results in memory. With the results, the se-
quence number, entered patient ID, time and date of measurement are stored as well. In
this MENU/MEMORY submenu you can clear results from memory or transfer stored data
to the built in printer or to a device connected to the serial port (i.e. host computer). To
achieve the functions mentioned above follow the flowchart below.
Table of contents
Other Analyticon Measuring Instrument manuals
Popular Measuring Instrument manuals by other brands

Bosch
Bosch GLL 5-50 X Professional Original instructions
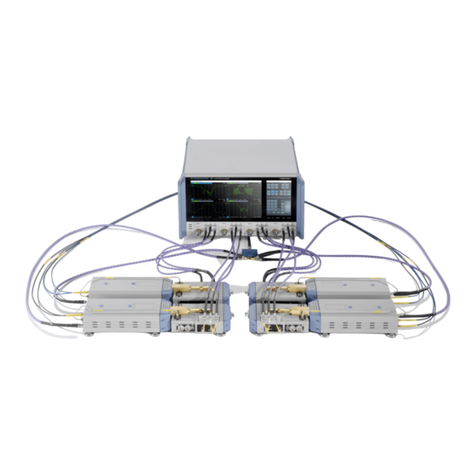
R&S
R&S ZNA67EXT Getting started
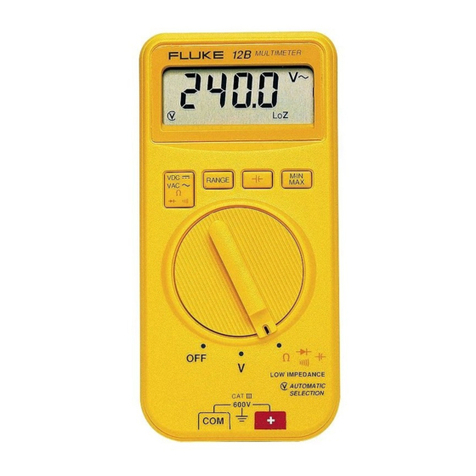
Fluke
Fluke 7 Series Service manual

Ripley
Ripley Miller UPM100 user guide
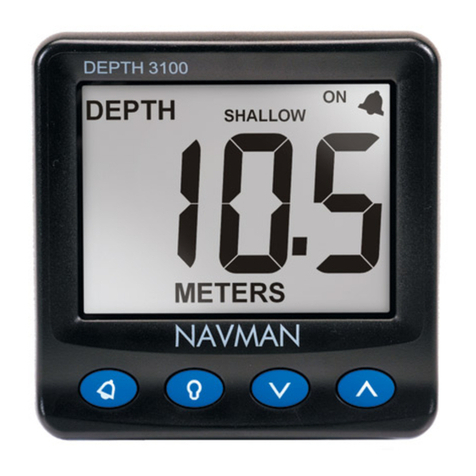
Navman
Navman Repeat 3100 Installation and operation manual
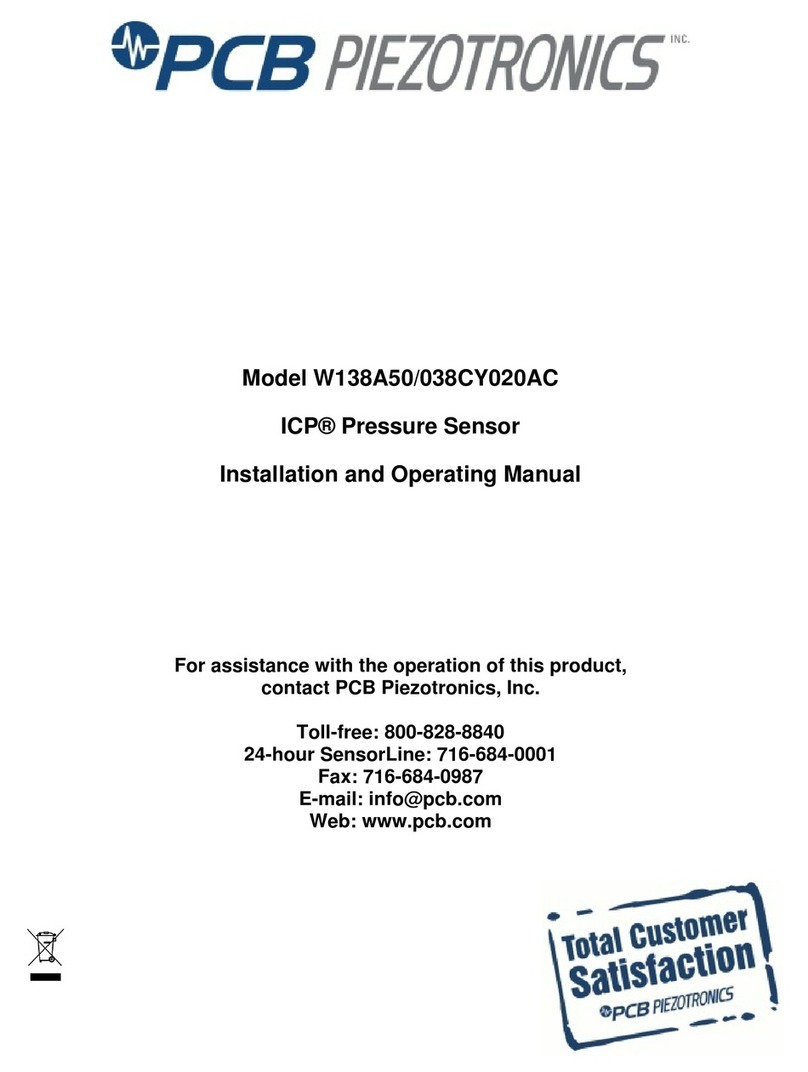
PCB Piezotronics
PCB Piezotronics W138A50/038CY020AC Installation and operating manual