ANDERSON-NEGELE Load Stand II User manual

SENSORS FOR FOOD AND LIFE SCIENCES.
30044 / 1.0 / 2022-05-25 / MH / EU-NA
Installation and operating instructions
Weighing System Load Stand®II
Note
The contents of this document are the intellectual property
of Anderson-Negele. Any reproduction or translation without
written permission is prohibited.
Please read these installation and operating instructions
carefully. All instructions in this manual must be followed
exactly to ensure proper operation of the unit.
If you have any questions regarding the product, installa-
tion or commissioning, please contact Anderson-Negele
Support at support under:
America:
Phone 800-833-0081
techservice@anderson-negele.com
Other countries:
Phone +49-8333-9204720
support@anderson-negele.com
NEGELE MESSTECHNIK GMBH
87743 Egg an der Guenz, GERMANY
Phone +49 (0) 83 33 . 92 04 - 0
sales@anderson-negele.com
support@anderson-negele.com
Phone
techservice@anderson-negele.com
ANDERSON INSTRUMENT COMPANY
156 Auriesville Road
Fultonville, NY 12072, USA

2
Table of contents
Table of contents
Weighing System Load Stand®II...............................................................................1
· Welcome ....................................................................................................................................3
· Manual conventions................................................................................................................3
· Inspection and storage ..........................................................................................................3
Field of application / intended use ........................................................................4
· Description................................................................................................................................4
· Product features ......................................................................................................................4
Installation of the Load Stand®II.............................................................................6
· Vessel preparation ..................................................................................................................6
· Hardware ...................................................................................................................................6
Installation..................................................................................................................................7
· Leveling the vessel..................................................................................................................8
· Checking Output using Anderson-Negele-Testmeter ...................................................9
· Operation and Installation.................................................................................................13
· Notes........................................................................................................................................13
Electrical installation...................................................................................................14
· General Safety.......................................................................................................................14
· Disconnect requirements for permanently
installed equipment ............................................................................................................14
· Installation.............................................................................................................................14
· Guidelines ..............................................................................................................................14
Installation of the sun shield .................................................................................. 16
· Installation of a sun shield ................................................................................................ 16
Calibration ........................................................................................................................... 17
· Calibration methods............................................................................................................ 17
· Alternative methods for checking output...................................................................... 17
Troubleshooting Load Stand®II ......................................................................18–21
Dimensional drawings................................................................................................. 22

3Introduction
Welcome
In many applications, weighing systems for content mea-
category.
This manual describes the installation of the sensors and its
various hardware options. It includes procedures for adjust-
ing the vessel, and instructions for wiring the sensors to one
or several junction boxes and to the signal processor.
on wiring the junction boxes to the signal processor.
If you have any questions about the product, its installation or
commissioning please contact Anderson-Negele Support at:
America:
Phone 800-833-0081
techservice@anderson-negele.com
Other countries:
Phone +49-8333-9204720
support@anderson-negele.com
Authorized Personnel
All instructions described in this document must be per-
Before installation, please read these instructions and
familiarise yourself with the requirements and functions.
The required personal protective equipment must always be
worn when servicing the device.
Use
The device is solely intended for use as described in this
manual. Reliable operation is ensured only if the instrument
document. For safety and warranty reasons, use of accessory
equipment not recommended by the manufacturer or modi-
personnel only. This device should be mounted in locations
where it will not be subject to tampering by unauthorized
personnel.
Misuse
Improper use or installation of this device may cause
the following:
· Personal injury or harm
·
· Damage to the device or system
·
Inspection and storage
Inspect each package upon receipt for damage that may
have occurred due to mishandling during shipping. If the
unit is received damaged, notify the carrier or the factory for
instructions. Failure to do so may void your warranty.
If the device is not scheduled for immediate installation:
1. Following inspection, repackage the unit into its original
packaging.
2. Select a clean dry site, free of vibration, shock and
impact hazards.
3. If storage will be extended longer than 30 days, the unit
must be stored at temperatures between 0 to 40 °C
(32 to 104 ºF) in non-condensing atmosphere with
humidity less than 85 %.
Caution
Possible risk to the product. The sensor or other equip-
ment may be damaged if this information is ignored.
Note
Contains additional information about a step or feature
critical to the installation or operation of the sensors.
Manual Conventions
Two kinds of special explanations appear throughout the
manual: Caution and Note.
Caution
Do not store a non-powered unit outdoors for a
prolonged period.

4
Field of application / intended use
Field of application / intended use
Description
The Load Stand®II is a direct vessel-to-foundation structural
member designed to be your dependable and accurate con-
tinuous inventory monitoring and control solution. The Load
Stand®II system is ideal for vessels with loads of 45,000 kg
(100,000 lbs) or more and is available for loads of 11,000 to
453,000 kg ( 25,000 to 1,000,000 lbs) per support point.
The monolithic design becomes an integral part of the ves-
sel structure for maintenance free weight measurements.
the vessel out of service.
The mechanical design of the Load Stand®II lends to simpli-
Simple, rugged, and easy to match end-mounting plates
yield minimum design time and easy installations.
Product features
· Monolithic Design
· High Output
· Multiple Weight Ranges
· Solid State Strain Sensors
· Limited Down Time

5Specication
Specication Load Stand®II Weighing Cells
Technical Features Excitation Voltage - Operating Range
Maximum Current
Recommended Supply Voltage
Functional Integrity
Humidity
Protection Class
Materials
Sensor
Junction Box
12...30 V DC Half-Bridge
15.52 mA @ 12 VDC excitation
12 V DC
2 x rated load (compression)
100 % Non-condensing
Designed for outdoor applications
Pedestal: Carbon Steel 1.0044
(ASTM A53 GR)
Flanges: Carbon Steel 1.0459
(ASTM A36)
Finish: Polyester Powder Coating
4 x Microcell II
Plastic or Stainless Steel (ATEX),
included
Measurement Accuracy Non-Linearity/Hysteresis Combined
Repeatability
Rated Output
No Load Output
0.2 % of rated load
0.2 % of rated load
320 mV DC @ 12 V DC ±1 %
±50 mV
Temperature ranges Ambient Temperature Range
Operational Temperature Range
Storage Temperature Range
Standard: -18...38 °C (0...100 °F)
Mid: 10...66 °C (50...150 °F)
-34...66 °C (-30...150 °F) (outside this
range the accuracy may be reduced)
-34...66 °C (-30...150 °F)
Authorizations All models ATEX (option)

6
Installation of the Load Stand®II
Installation of the Load Stand®II
Vessel preparation
There are two aspects to successful use of Load Stands—
properly functioning Load Stands and appropriate vessel
support characteristics. Review the following list of error
sources, and make the recommended corrections before you
install Load Stands:
· An inadequate vessel foundation can allow excessive move-
ment. Ensure the foundation is concrete or steel. Refer to the
· Hidden load-bearing structures, such as discharge chutes
this problem.
· Cross-connecting structures, such as catwalks and mani-
folds, can transfer loads from adjacent vessels. Install slip
· Shock loads can damage the Load Stand. Install protective
barriers or stops to prevent vehicles from hitting the vessel
supports.
· Extra holes in the vessel gusset or vessel base plate which
bolts to the Load Stand, replace the gusset/ plate with the
correct number of holes for bolting to the Load Stand.
Hardware
1. Anderson-Negele provides rubber washer assemblies
for the Load Stand®top mounting hole connections.
2. All other hardware to attach the Load Stand®to the ves-
sel and to the foundation is customer-supplied.
3.
4. -
modate the thickness of the connecting parts and the
should not be so long that they interfere with other
parts of the installation.
· Anderson-Negele recommends the placement of a base
plate beneath the Load Stand. Refer to the installation
a load stand base.
· During installation, do not put the entire vessel load on
less than the correct number of Load Stands.
· If you need to raise the vessel or one vessel leg after instal-
lation: Loosen the bolts on all the Load Stands prior to
raising the vessel or leg to prevent overloading.
Caution
Remove power from the unit before installing, removing,
or making ajustments.
Caution
Stand®during installation, damaging the Load Stand®and
voiding the warranty.

7Installation of the Load Stand®II
1.
make sure the correct load stand will be installed.
2. Measure the No Load Output to ensure it’s ±50 mV.
3. Raise the vessel.
4. Inspect the bottom of the vessel mounting surface to
-
ment. Remove any debris from the mounting surface.
Depending on the foundation (concrete or beam mount-
5. Mount the Load Stands on the foundation.
a) Place the customer-supplied leveling nuts and hard-
ened washer on each anchor bolt on the load stand.
Check the angular alignment.
b) Carefully place the Load Stand®on the leveling
nuts/washers, aligning the mounting holes with
the foundation anchor bolts. The alignment should
allow the load stand to easily slide onto the anchor
bolts.
c) Place the customer-supplied hardened washer and
nut on each anchor bolt. Do not fully tighten the
nuts at this time. Leave a 6 mm (1/4") gap between
the nut and washer to allow for positioning the Load
Stand.
d) Repeat Steps A through D for each Load Stand.
e) Record the no load output by connecting the
electronics and following chapter “Shimming of the
Load Stand”.
6. Mount the vessel on the Load Stands:
Caution
Use proper supports to prevent the vessel from tipping
or falling.
Note
On 22,680 kg (50,000 lb) or larger Load Stands, a pry
bar may be used at the base of the Load Stand®to gently
move it into position.
Caution
If the vessel hole pattern does not match up with the
Load Stand®hole pattern, modify the mounting holes on
the vessel. Do not force the Load Stand®into position by
hammering or by tightening the mounting bolts.
Installation
a) Slowly lower the vessel until it is resting on the Load
Stand®assemblies. Alignment pins may be used to
help guide and position the vessel.
b) Center the Load Stand®top mounting holes with the
vessel mounting holes, using the clearance available
from the Load Stand®bottom mounting holes.
c) Place a rubber washer on each customer-provided
top bolt. Place the four top bolts through the vessel,
rubber pad, and Load Stand®mounting holes.
d) Place a rubber washer and customer provided nut on
Do not compress the rubber washers at this time.
7. Perform preliminary leveling shimming:
a) Inspect the installation for gaps between the vessel
mounting plate and the Load Stand.
b) Eliminate gaps by doing one or a combination of the
following:
· Turn the leveling nuts, only to raise the entire
load stand.
· Install one or more full shims above the Load
Stand®rubber pad. Two shims are provided by
Anderson-Negele with each Load Stand.
· Install one or more partial shims above the Load
Stand®rubber pad. Two shims are provided by
Anderson-Negele with each Load Stand. Using the
Load Stand®
shim shape on a thin piece of cardboard. Use this
as a template to cut the required shape from a
full shim.

8
Installation of the Load Stand®II
Caution
If installing shims, loosen the top bolts on all the Load
Stands before raising the vessel.
Shimming the load stands
Shimming the load stands distributes the weight evenly on
all Load Stands, increasing system accuracy and life. Perform
this procedure while the vessel is still empty:
1. Check if Leveling Needed
a) Remove the junction box cover.
b) Connect the red, white, and black wires of a 3-con-
ductor cable to the corresponding terminals on TB1
of the Load Stand®junction box. Connect the other
end of the cable to the corresponding terminals of
the Anderson-Negele Test Meter. Turn on the power
to the Test Meter and set the Simulate/Test switch
to the Test position.
c) Verify the dead weight voltage output of the Load
Stand®from step 3f.
d) Calculate the change in output, as shown in the
example. Output Change = installed output -
uninstalled output. The change in output must
be positive.
Note
If an Anderson-Negele Test Meter is not available, before
proceeding refer to Chapter Set-up - Alternative method
for checking output.
Rubber pad from
Anderson-Negele
Junction Box 6 mm (1/4")
Nut
Washer
Min. 50 mm (2")
for grout
Levelling nut
and washer
Vessel Leg and
Mounting Plate
Rubber washer
from Anderson-Negele
Bolt
Rubber pad from
Anderson-Negele
Center Load Stand top
mounting holes with
vessel mounting holes.
Center bolts in
mounting holes.
Rubber washer from
Anderson-Negele
Nut
Vessel Mounting Surface
Max. +-1° or
6 m (1/4")
Install grout
only after
Load Stand is
leveled

9Installation of the Load Stand®II
· Check the wiring polarity at the Test Meter.
Ensure the red, white, and black wires are con-
nected to the corresponding terminals.
· If the wiring is correct and you still observe a
negative output change, the vessel may be tilted.
Vessel tilting shifts the load onto some Load
Stands while putting other Load Stand(s) in a no
load or tension load condition.
This can occur in cases of extreme thermal defor-
mation or unequal vessel leg length. Proceed to
Step 2 to level the vessel.
e) Repeat Steps A through D for each Load Stand®for
this vessel.
f) Calculate the average output change for all Load
Stands for this vessel. The output increase for each
Load Stand®must be within ±25 % of the average
output increase. Load Stands 1, 2, and 4 meet this
requirement, while Load Stand®3 does not.
g) If the installation meets the criteria described
above (change in output is positive and is within
±25 % of the average output increase), the vessel is
·
the installation.
· -
scribed in Step 2. 8
Checking Output using Anderson-Negele-Testmeter
Example Recording and Analysis of Output for Level Check
Load Stand®
Nr.
Not installed output (no load)
(mV)
Installed dead weight
(mV)
Output change
(Installed - Not installed) (mV)
1+30 +90 +60
2-15 +50 +65
3+17 +30 +13
4-25 +30 +55
Average Output Change = (60 + 65 + 13 + 55) / 4 = 48.25
Allowable Range for Output Change max. ± 25 % = 48.25 ± (1/2 x 48.25) = 36.18 to 60.3
All Load Stands must meet the requirement that all output
changes must be positive (+). Load Stands 1, 2, and 4 meet
the requirement that the output change be within ±25 %
of the average output change. Load Stand®3 does not meet
the requirement, and its small output change indicates it is
carrying much less weight than the other supports. This load
stand must be adjust with the leveling nuts or by shimming
to carry additional weight. The vessel must be level to distri-
bute the weight evenly over all the supports.
B W R SHLD B W R
TB1 TB2
B W R B W R B W R B W R
SENSOR A SENSOR B SENSOR C SENSOR D
LOAD STAND STANDARDIZATION
TB3
Red White Black
ON
OFF
SENSOR
TEST
METER
ADJUST
SIMULATE TEST
+EX SIGNAL -EX
Junction Box
Anderson-Negele-Testmeter
Note: Wiring from sensors
to terminal TB3 not shown
for clarity.

10
Note
Adjusting leveling nuts and/or shimming on one Load
Stand®
Installation of the Load Stand®II
2. Shimming.
a) Raise the vessel legs for the low output load
stands.
b) Raise or lower the load stand with the leveling nuts
or add shim(s) above the rubber pad as required
adjusting the distribution of weight on the Load
Stands. Raising the leveling nuts and/or adding
shims increases the weight on the Load Stand.
Lowering the leveling nuts and removing shims
decreases the weight on the Load Stand.
Caution
Loosen the top bolts of all the Load Stands before raising
the vessel.
c) Slowly lower the vessel leg onto the Load Stand®
assembly.
d) Repeat Step 1, rechecking the output of all the Load
Stands and recalculating the Output Change (dead
weight output - no-load output).
e) Repeat Steps 2A through 2D until the installation
meets the criteria for weight distribution.
3. Complete Installation: Once the vessel is level, complete
the installation:
a) Tighten the nuts on the anchor bolts per the local
code.
b) Verify readings.
c) Tighten the nuts on the upper bolts 1/2 to 1 turns
washers and rubber pad.
d) Apply double nut, adhesive or spoil the upper bolts
and anchor bolts to prevent loosening of the nuts.
e) Pack grout or concrete under the Load Stand. Do not
grout above the bottom edge of the Load Stand®
assembly.
f) Replace the junction box cover if not ready to begin
wiring the junction boxes together and to the signal
processor, to ensure no moisture enters the box.
Tighten
1½ turns
past finger tight
Prevent
Loosening Tighten as
regulated
Install
grout

11
Figure 1
Load Stand®dimension chart (For any note references, see Figure 2 or 3)
Installation of the Load Stand®II
Note
Refer to installation notes on next pages:
Fig. 2 (concrete mounting)
Fig. 3 (beam mounting)
Fig. 4 (Wiring and Signal cable routing)
Legend
AOutside Dimension
BHole Dimension
DB Bolt Size
DH Hole Diameter
DW Washer Outside Diameter
HInstalled Height
PPipe Size
RCorner Radius
RT Recommended Thickness
TPlate Thickness
TP Pad Thickness
TW Washer Thickness
LOAD RATING PA
BDH RHTTPDW TW WEIGHTRTXX
LOAD STAND II DIMENSIONS
DB
COMPRESSIONTENSION SHEAR
LOAD STAND
MAXIMUM FRAME LOADSALLOWED PER AISC 14thEd.ULTIMATE FRAME LOADS
TENSIONCOMPRESSION SHEAR
LOAD RATING
REFERENCE
ONLY
( )
LOAD RATING
LOAD STAND
TENSION
COMPRESSION
SHEAR

12
Figure 2
Concrete Mounting
Notes
Bolts: ASTM A-325, bolt length determined by and
supplied by customer.
Pads: Supplied by Anderson-Negele
Install upper mounting bolts in oversized holes (DH) and
XX = Maximum thermal deformation allowed, computed
as shown here : X = DH - DB - 1.5 mm (1/16").
Use one of the following to prevent loosening Apply
double nut, adhesive or spoil bolt threads.
The loads listed are the maximum ASD loads for the
condition listed (Compression, Tension or Shear) and are
based on AISC 14th edition. All Load Stands must
Load combinations can be found in the applicable
building code.
-
ed) to maintain NEMA-4 rating and to de-couple conduit
run from the weighing system.
Operation and Installation
The Load Stand®II can compensate for thermally induced
expansion by slightly tilting the screws in oversized holes.
The mounting holes on the vessel should be of the same size
as the Load Stand®II („DH“) and their position should not be
more than ±1.5 mm (0.6") from their ideal position.
between the Load Stand®unit and the foundation. This is
mandatory to assure proper operation.
Customer provided loads and thermal expansion must be
must be taken into account so that applicable building codes
and and usage characteristics are met.
Load Stand®II has been designed in accordance with the
Uniform Builidng Code UBC, 1988 edition. Additional
information and test results can be obtained from Anderson-
Negele upon request.
Installation of the Load Stand®II
Microcell Sensor
Junction Box
View A-A
Kistler-Morse
RT
TP
T
TW
H
T
AA
DB
DW
Vessel support
bracket (customer)
4 x ASTM A-325 Upper
mounting bolts (customer)
8 x Washer sets
(Anderson-Negele)
Rubber pad
(Anderson-Negele)
Junction Box Plastic or
Stainless Steel (Anderson-Negele)
4 x Microcell Strain gauge sensor,
part of Load Stand II
Sun shield, installed by the customer,
mounts under the Junction Box and to
the bottom flange of the Load Stand.
Sun shield and sun shield mounting
hardware supplied with each Load Stand
8 x Hardened washers
4 x Nuts
(customer)
High strength grout,
5 cm (2") suggested (customer) Shim
4 x leveling nut and
hardened washer (customer
)
Anchor bolts according to
local code (customer)
Shim

13
Figure 3
Beam Mounting
Notes
Bolts: ASTM A-325, bolt length determined by and
supplied by customer.
Pads: Supplied by Anderson-Negele
Operation and Installation
The Load Stand®II can compensate for thermally induced
expansion by slightly tilting the screws in oversized holes.
The mounting holes on the vessel should be of the same size
as the Load Stand®II („DH“) and their position should not be
more than ±1.5 mm (0.6") from their ideal position.
between the Load Stand®unit and the foundation. This is
mandatory to assure proper operation.
Customer provided loads and thermal expansion must be
must be taken into account so that applicable building codes
and and usage characteristics are met.
Load Stand®II has been designed in accordance with the
Uniform Builidng Code UBC, 1988 edition. Additional
information and test results can be obtained from Anderson-
Negele upon request.
Install upper mounting bolts in oversized holes (DH) and
XX = Maximum thermal deformation allowed, computed
as shown here : X = DH - DB - 1.5 mm (1/16”).
Use one of the following to prevent loosening Apply
double nut, adhesive or spoil bolt threads.
The loads listed are the maximum ASD loads for the
condition listed (Compression, Tension or Shear) and are
based on AISC 14th edition. All Load Stands must
Load combinations can be found in the applicable
building code.
-
ed) to maintain NEMA-4 rating and to de-couple conduit
run from the weighing system.
We recommend to insure system performance and
-
face approximately twice dimension “A” long, the same
-
these requirements plate can be welded to the beam
a shown, however the plate should be a minimum one
half dimension “T” thick.
Installation of the Load Stand®II
4 x ASTM A-325 Upper
mounting bolts (customer)
Vessel support
bracket (customer)
8 x Washer sets
(Anderson-Negele)
Rubber pad and washer
(Anderson-Negele),
shim as required
Junction Box Plastic or
Stainless Steel (Anderson-Negele)
4 x Microcell Strain gauge sensor,
part of Load Stand II
Sun shield, installed by the customer,
mounts under the Junction Box and to
the bottom flange of the Load Stand.
Sun shield and sun shield mounting
hardware supplied with each Load Stand
8 x Hardened washers
4 x Nuts
(customer)
Mounting plate (customer provided),
welded to the vessel support
beam all around if required
Shim
Min. T/2 (if applicable)
≥
T
Vessel support
beam (customer)
4 x lower mounting bolts
(customer)

14
Electrical installation
General Safety
When using electrical equipment, you should always follow
basic safety precautions, including the following:
· The installation and wiring of this product must comply
with all national, federal, state, municipal, and local codes
that apply.
· Properly ground the enclosure to an adequate earth
ground.
· Do not modify any factory wiring. Connections should only
be made to the terminals described in this section.
· All connections to the unit must use conductors with an
insulation rating of 300 V minimum, rated for 105 ºC
of appropriate gauge for the voltage and current required
· Do not allow moisture to enter the electronics enclosure.
Conduit should slope downward from the unit housing.
Install drip loops and seal conduit with silicone rubber
product.
Disconnect requirements for permanently
installed equipment
A dedicated disconnecting device (circuit breaker) must be
provided for the proper installation of the unit. If inde-
pendent circuits are used for power input and main relay
outputs, individual disconnects are required.
Disconnects must meet the following requirements:
· Located in close proximity to the device
· Easily accessible to the operator
· Appropriately marked as the disconnect for the device and
associated circuit
· Sized appropriately to the requirements of the protected
Installation
There are two versions of the junction box enclosure. Both
versions have four small holes, which are used for factory-
wiring the sensors to the junction box. In addition, the junc-
tion box has one or two large holes for wiring the junction
box to other junction boxes and the signal processor:
· One large hole (conduit installation); the large hole accom-
· Two large holes (non-conduit installation); the two large
for non-conduit installations are required.
Electrical installation
Caution
Very high voltage is present. Remove power from the unit
before installing, removing or making adjustments.
Guidelines
· The procedure below assumes the conduit/cable tray has
been installed.
·
holes at conduit/cable tray lowest elevation(s) to allow
condensation to drain.
· Use Belden 3-conductor shielded interconnect cable or
equivalent to wire junction boxes together and to the
signal processor, for lengths up to 305 m (2,000').
· When wiring cable to junction box terminals, strip back 3"
(76 mm) of cable sheathing to expose the three conductor
wires and shield wire inside. Strip 1/4" (6 mm) of insula-
tion from the end of each of the conductor wires. Spread a
generous bead of sealant around the sides of the PG 13.5
1. See Figure 4: Route the 3-conductor cable through the
processor. Connect wires from the cable to the TB2
terminal in the junction box: black wire to B, white wire
to W, and red wire to R. Connect the cable shield wire to
the Shield terminal between TB1 and TB2.
2. Route the cable through conduit/cable tray to the next
junction box. Estimate the required length of cable to
the terminal strip, allowing a little extra for strain relief.
Cut the excess cable. Connect wires from the cable to
the TB1 terminal in the junction box: black wire to B,
white wire to W, and red wire to R. Connect the cable
shield wire to the Shield terminal between TB1
and TB2.
3.
this junction box, and attach wires to the TB2 terminal:
black wire to B, white wire to W, and red wire.
4. Repeat Steps 2 and 3 until all junction boxes for the ves-
sel are wired together.
5. Route the cable from the last junction box through
conduit to the signal processor. Refer to the signal pro-
cessor manual for wiring the junction box to the signal
processor. One vessel takes up one channel in the signal
processor—the channel shows the average value from
all the Load Stands supporting the vessel.
Caution
All wiring routed between Junction Boxes and Signal
Processor must be continuous (no splices)
Caution
or RTV 738. Other sealants may contain acetic acid, which
is harmful to sensors and electronics.

15 Electrical installation
Detail A
Preferred method with conduit installation
Typical cable and conduit routing
Typical Transducer / Junction Box Interconnect Diagram
Typical Sensor Wiring
Notes
1. All connection parts are customer provided (unless
otherwise noted).
2. Diagrams only examplary. Local electrical installation
requirements or code must be observed.
If the distance transducer - signal processor is max.
305 m (1000’), use 3-wire, shielded 18 AWG intercon-
nect cable for wiring junction boxes to each other and
to the signal processor. If the distance is between 305
and 610 m use 16 AWG cable.
4. Up to 4 Load Stand®sensor cables can be connected
in one junction box. Junction boxes can be intercon-
nected as required.
The conduit entry hole on this junction box is designed
for conduit with 0" NPS connector. Adapter plugs are
required for other connections and wiring to the signal
processor.
6. Junction boxes must always be securely closed and
all unused openings securely sealed with the plugs
provided.
Figure 4
Signal Cable Layout
To Indicator
Drip LoopDrip LoopDrip LoopDrip Loop
To signal processor (Conduit run)
Vessel leg Flexible conduit
From other Junction Box
Male flexible
conduit fitting
Male flexible conduit fitting
30–45 cm (12 - 18"
)
Vessel leg
flange
Conduit or Tee
Junction Box
(Cover removed for clarity)
Male flexible conduit fitting
Sensor cover
Flexible conduit
Sensor cable
(Factory wiring)
Load Stand II Transducer
Drip loop
3/4" Entry hole
1/2" min. clearance
to the ground
To sensor C
To sensor D
To sensor A
To sensor B
Factory wiring
up to 4 Microcel
l
sensors of
Load Stand II
To next TB1 of Junction Box
or to signal processor
From last TB2 of Junction Box
Note:
TB1 and TB2
are electrically
identical

16
Installation of the sun shield
Installation of the sun shield
The sun shield reduces sun-induced stresses in
the Load Stand®sensors and provides additional
protection for the sensors.
1.
the screws attaching the junction box to the
Load Stand.
2. Slightly loosen the horizontal screw(s) on the
3. Wrap the sun shield around the Load Stand,
slipping the cutout slots behind the loosened
screws.
4. Tighten the junction box screws and the horizon-
5. Replace the junction box cover.
Loosen Junction Box screws;
Re-thighten after sun shield
is installed
Slide sun shield behind junction
box and loosened screws.
Wrap sun shield around
Load Stand. Slide shield behind
Junction Box and loosened screws
on other end.
Screw not
on all models
Loosen bottom flange screw(s);
Re-thighten after sun shield
is installed.

17 Calibration
Alternative method for checking output
If you do not have an Anderson-Negele Test Meter, use a Dig-
ital Multimeter (DMM) and the Load Stand®II junction box to
monitor the voltage output of each Load Stand®before and
during installation. Set up the DMM as described below.
1. Disconnect the white wires from the W terminals on TB1
and TB2 in the junction box, see Figure below.
2. Connect the DMM (+) probe to the W terminal on either
TB1 or TB2 (See A).
3. Connect the DMM (-) probe to TP1 in the junction box
(See B).
Using DMM and Junction Box to Monitor Voltage Output
4. Set a voltage range on the DMM that will accommodate
a measured range of ±1 volt.
5. See Pre-Check Procedures, for details on checking the
voltage output before installation. See Leveling Vessel,
Hardware Installation, for details on monitoring the
voltage output to determine if the vessel weight is
evenly distributed among the Load Stands.
6.
the W Terminals on TB1 and TB2 in the junction box.
B W R SHLD B W R
TB1 TB2
B W R B W R B W R B W R
SENSOR A SENSOR B SENSOR C SENSOR D
LOAD STAND STANDARDIZATION
TB3
TP1
TP2
TP3
(B) Connect DMM
(-) probe to TP1
12 VDC Excitation Voltage from
Signal Processor connected on
Black and Red Terminals A) Connect DMM
(+) probe to either
W Terminal (TB1 or TB2)
Cable from Previous
Junction Box (if applicable) Cable to Next Junction
Box or Signal Processor
Calibration
Calibration methods
Before calibrating, you must install a signal processor.
There are two calibration methods:
· Live Load calibration: set lo span and hi span while mov-
ing material into or out of the vessel. This is the preferred
method.
· Manual calibration: set scale factor counts, scale factor
weight, and zero calibration value without moving materi-
al. This method is less accurate than Live Load calibration.
A Live Load calibration requires you to move a known
quantity of material into or out of the vessel while perform-
ing the procedure. The quantity of material moved must be
at least 25 % of the vessel’s total capacity to provide best
accuracy. Live Load calibration is also based on the material
weight currently in the vessel.
Manual calibration allows you to start using the system as
soon as sensors, junction boxes, and signal processor are
installed and wired, even if you cannot
move any (or enough) material now. Manual calibration
values are based on system parameters, including sensor
sensitivity, vessel stress, and signal processor A/D converter
sensitivity. These values are known, can be calculated, or
can be obtained from the signal processor. Manual calibra-
tion is also based on the material weight currently in the
vessel.
Note that manual calibration does not take into account
the actual response to changes in weight. Theoretically, a
change in weight results in a proportional change in digital
counts. However, the structure.s actual response to load and
interaction with piping, catwalks, a roof, discharge chutes,
etc. prevents the system from achieving theoretical values.
Manual calibration is a good start, but to obtain the highest
accuracy, perform a Live Load calibration when scheduling
permits you to move material into or out of the vessel.
Refer to the signal processor manual for the procedure to
input calibration parameters.

18
Problem Description Solution
Small Amplitude Changes
or Erratic Fluctuations in
Display Readings
Fluctuations can be caused by small
amplitude drift or oscillation, with
peak-to-peak disturbance of 0.1 % to
0.5 % of full scale, is normal.
Problem likely to be noticed shortly
after initial installation.
Reduce drift or oscillation by setting 'count by'
and 'averaging' appropriately on signal proces-
sor (refer to signal processor manual).
Fluctuations can be caused by mois-
ture in the cable conduit, junction
boxes, or PCBs.
Problem likely to be noticed on system
that previously functioned correctly.
Check conduit, junction boxes and PCBs for wa-
ter contamination. Find water entry source and
correct problem. Dry with a hair drier. Remove/
replace corroded parts and materials.
Caution: If using sealant to eliminate water
TM 1A polyurethane sealant,
Dow CorningTM RTV 739 or RTV 738. Other seal-
ants may contain acetic acid, which is harmful to
sensors and electronics.
Fluctuations can be caused by jammed
bolts or heat radiation/ conduction.
Problem likely to be noticed shortly
after initial installation or on system
that previously functioned correctly in
cool or overcast weather.
Loosen nuts on top bolts and inspect top bolts.
· Top bolts free to move in holes: If vessel is
heated, it may be radiating or conducting heat
®
sensors.
· To reduce head radiation/conduction:
a) Insulate vessel.
b) Contact Anderson-Negele to discuss adding
a high temperature insulating pad.
· Top bolts jammed: Jammed top bolts indicate
undersized bolt holes on vessel mounting
beyond limits of Load Stand®clearance
®
sensors.
· To reduce side loads:
a)
to provide additional clearance.
Fluctuations can be caused by dam-
aged Load Stand®sensor.
Problem likely to be noticed shortly
after initial installation or on system
that previously functioned correctly.
Using Digital Multimeter (DMM), check resis-
tance for individual Load Stands:
1. Set meter resistance scale to accommodate
2. At the suspect Load Stand®junction box,
remove wiring at TB1 and TB2, which
connects to other Load Stands and signal
processors.
Troubleshooting Load Stand®II
Troubleshooting Load Stand®II

19 Troubleshooting Load Stand®II
Problem Description Solution
Small Amplitude Changes
or Erratic Fluctuations in
Display Readings
Fluctuations can be caused by dam-
aged Load Stand®sensor.
Problem likely to be noticed shortly
after initial installation or on system
that previouslyfunctioned correctly.
3. Put one DMM lead on W and other lead on
R terminal on TB1 of Load Stand®junction
box. Record resistance, and verify it is 7,660
or more Load Stand®sensors are damaged
and must be replaced—go to Step 7 to
identify which sensor is damaged.
4. Put one DMM lead on W and other lead on
B terminal on TB1 of Load Stand®junction
box. Record resistance, and verify it is 7,660
or more Load Stand®sensors are damaged
and must be replaced—go to Step 7 to
identify which sensor is damaged.
5. Verify readings from Steps 3 and 4 are
more Load Stand®sensors are damaged and
must be replaced—go to Step 7 to identify
which sensor is damaged.
6. Repeat Steps 2 through 5 for each suspect
Load Stand, until Load Stand®with damaged
sensor is located.
7. Identify damaged sensor at Load Stand®
a) Remove one sensors‘s wires from junc-
tion box terminal TB3.
b) Put one DMM lead on sensor‘s white
wire and other lead on red wire. Record
resistance, and verify it is 1.45 K ±
range, sensor is damaged and must be
replaced.
c) Put one DMM lead on sensor‘s white
wire and other lead on black wire.
Record resistance, and verify it is 1.45K
range, sensor is damaged and must be
replaced.
d) Verify readings from Steps B and C are
-
sor is damaged and must be replaced.
e) Repeat Steps A through D for each sen-
sor, until damaged sensor is located and
replaced.

20
Troubleshooting Load Stand®II
Problem Description Solution
Small Amplitude Changes
or Erratic Fluctuations in
Display Readings
Fluctuations in readings can be caused
by short to ground.
Using a Digital Multimeter (DMM) or ohmmeter,
check for shorts to ground as follows:
1. Set meter resistance scale to accommodate
maximum measured range.
2. Disconnect junction box wires of suspect
vessel from signal processor.
3. With one lead to earth ground and other
lead to white wire, check resistance on
disconnected wires:
resistance), a short is indicated; proceed to
Step 4 to identify location.
If no short is indicated, investigate other
explanations for problem.
4. Starting with junction box closest to signal
processor in daisy chain, disconnect wires
connecting junction box to other junction
boxes. With one lead to earth ground and
other lead to white terminal on TB3, check
resistance on wires leading from junction
box:
is resistance), short is indicated; proceed
to Step 5 to identify location. If no short is
indicated, proceed to next junction box in
daisy chain, disconnecting wires connect-
ing it to other junction boxes and checking
resistance. Perform for each junction box
down chain until short is located; proceed
to Step 5 to identify location.
Note: Sun shield or junction box mounting
bolts are good locations for connecting
probe to ground.
5. Disconnect wires for one sensor from
lead to earth ground and other lead to white
wire, check resistance on disconnected
(i.e., there is resistance), short is indicated.
Replace shorted sensor. If no short is indi-
cated, disconnect next sensor’s wires from
junction box and check resistances. Repeat
for each sensor wired to junction box until
short is located. Replace shorted sensor.
Table of contents
Other ANDERSON-NEGELE Measuring Instrument manuals
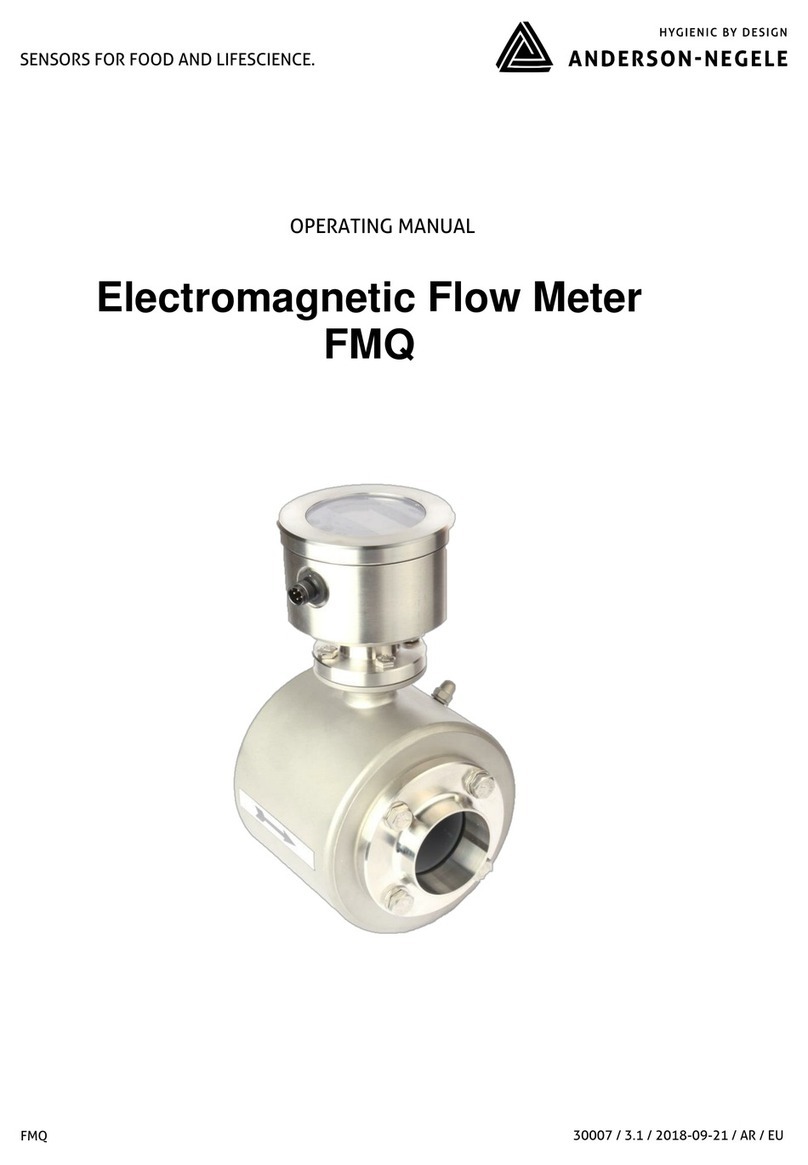
ANDERSON-NEGELE
ANDERSON-NEGELE FMQ User manual
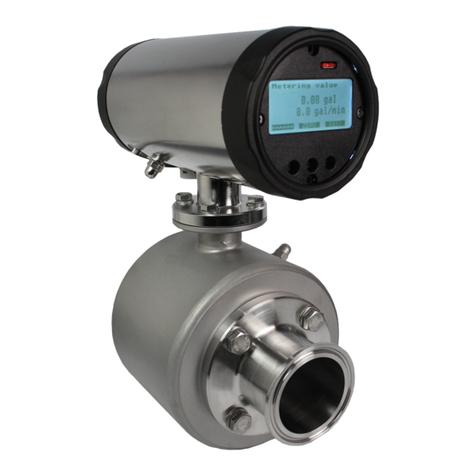
ANDERSON-NEGELE
ANDERSON-NEGELE IZMAG User manual

ANDERSON-NEGELE
ANDERSON-NEGELE IZMSA User manual
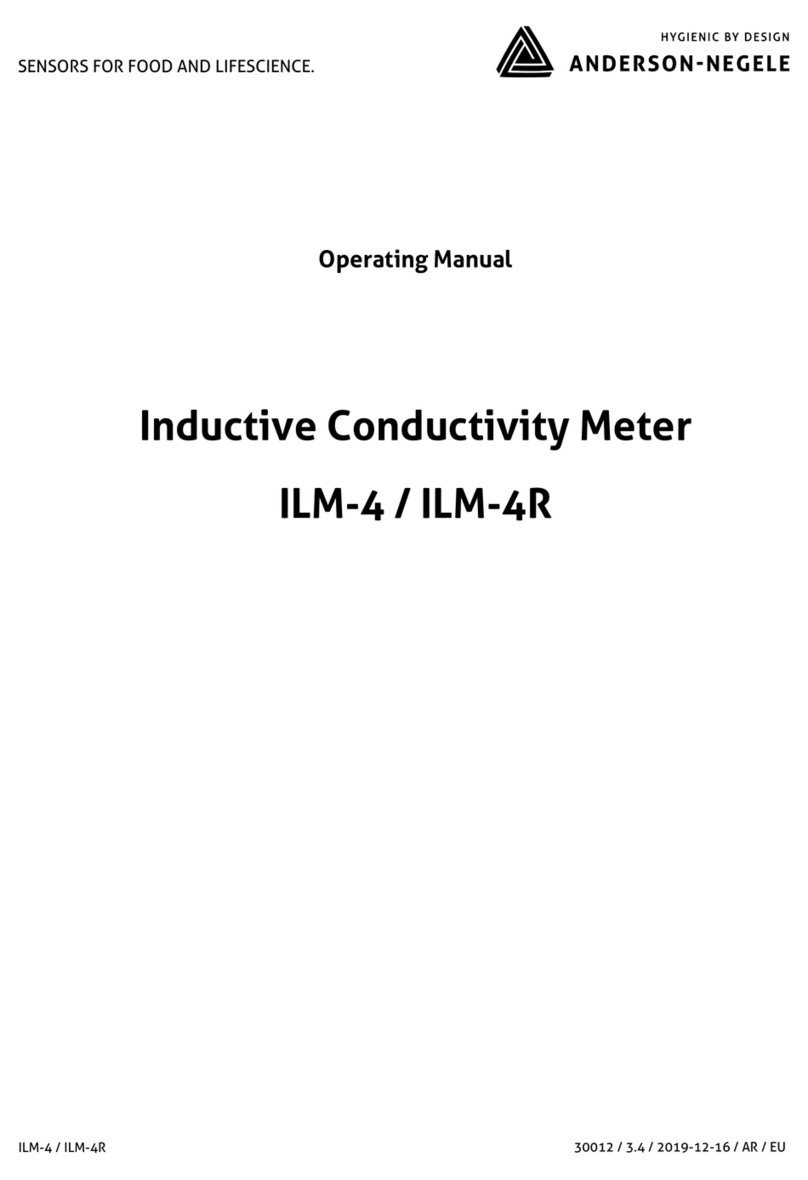
ANDERSON-NEGELE
ANDERSON-NEGELE ILM-4 User manual

ANDERSON-NEGELE
ANDERSON-NEGELE ILM-4R User manual
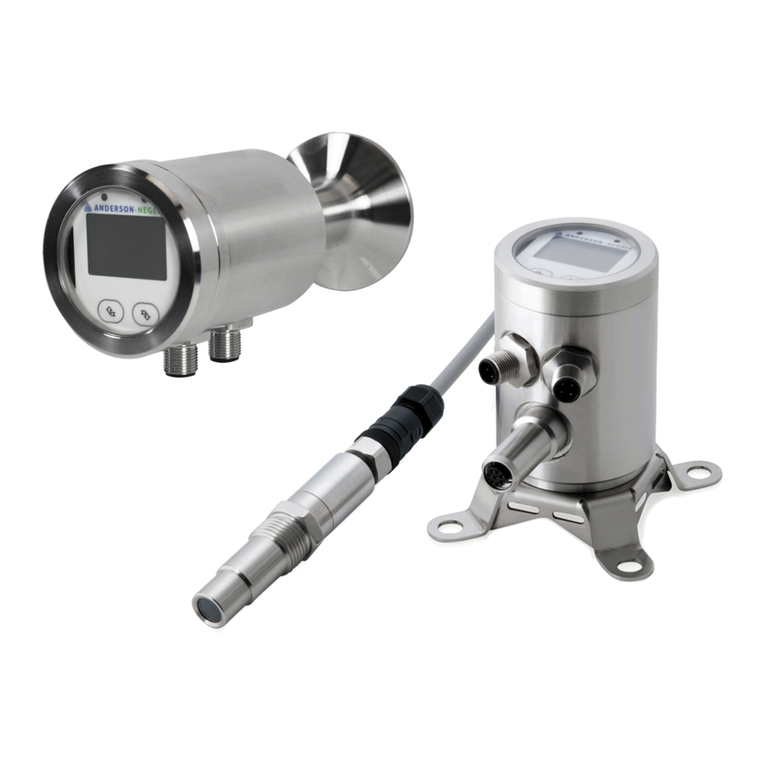
ANDERSON-NEGELE
ANDERSON-NEGELE ITM-51 User manual
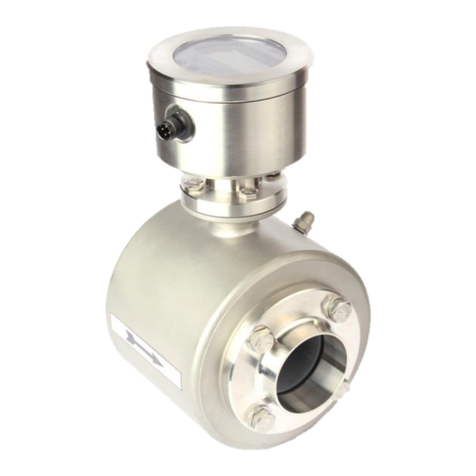
ANDERSON-NEGELE
ANDERSON-NEGELE FMQ User manual
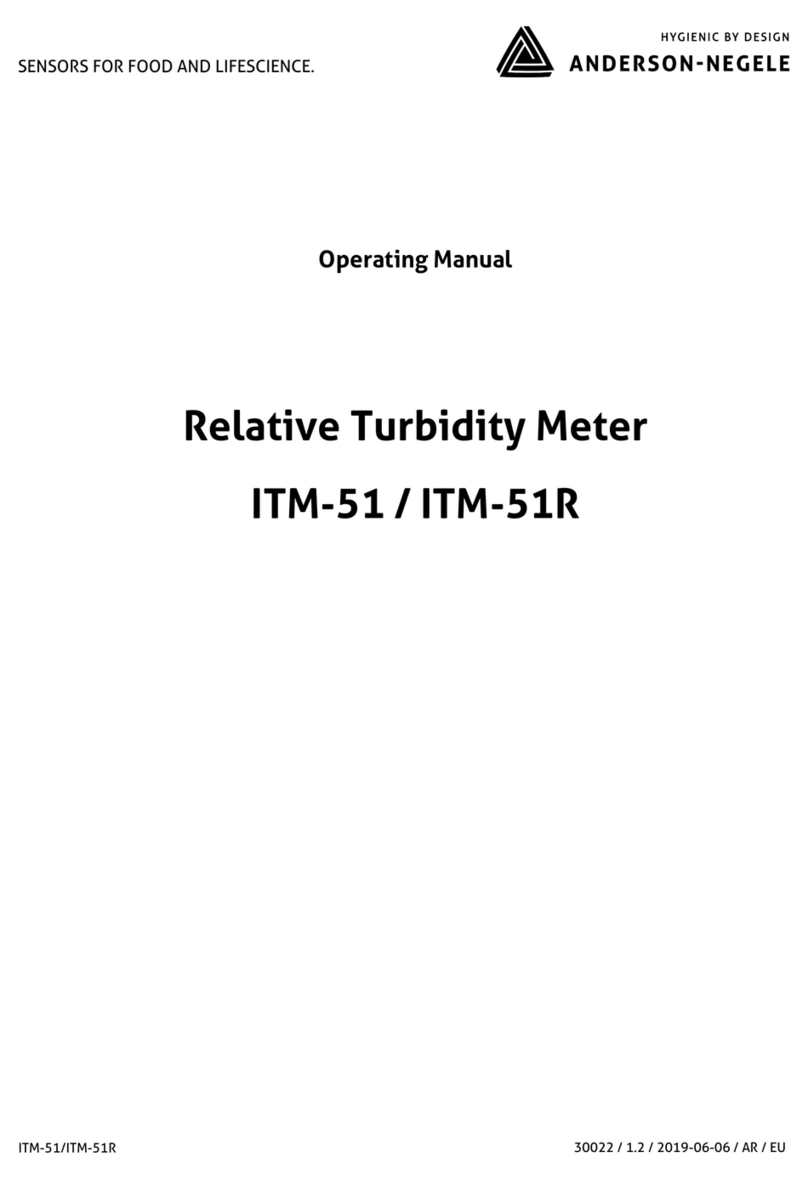
ANDERSON-NEGELE
ANDERSON-NEGELE ITM-51R User manual