Anywire B2G78-E1 User manual

Anywire Corporation
AnyWireASLINK System
Ethernet Gateway
B2G78-E1
User's Manual
Version 1.4 September 14, 2017
AnyWireASLINK System
PMA-12813F

i
Improper handling may cause a dangerous situation and can result in
death or serious injury.
Improper handling may cause a dangerous situation and can result in
moderate injury or minor injury or is assumed to result in property
damage only.
Precautions
Precautions related to this manual
1. This manual describes the overall concepts of the AnyWireASLINK system.
Make sure to read each individual "Products Guide" for handling of the respective products.
2. Reproduction or duplication of part or all of this Manual without permission is prohibited.
3. Contents of this Manual may be subject to future changes without prior notice.
Safety precautions (Make sure to read before use)
When using this product, please carefully read this Manual and the related Manuals introduced in this
Manual, and pay sufficient attention to safety in order to handle this product properly.
The precautions in this Manual describe only matters related to this product. Refer to the User's Manual
of the CPU unit for safety precautions as a sequencer system.
The "Safety precautions" rank safety precaution items into " WARNING" and " CAUTION"
categories.
[Precautions for design]
The AnyWireASLINK system has high noise resistance, however, keep transmission lines and
input/output cables 100mm or more (as a guide) away from high-voltage cables or power lines.
Failure to do so may result in a malfunction.
Incorporate an emergency stop circuit and an interlock circuit for safety into an external circuit other
than the AnyWireASLINK system.
[Precautions for installation]
Use the sequencer in an environment described in the general specifications in the User's Manual of
the CPU unit.
Use in any environment out of the range of the general specifications may result in electric shock, fire,
malfunction, damage or deterioration of the product.
Improper mounting of the unit may result in malfunction, failure or the unit falling down.
During installation and removal of the unit, make sure to shut off all phases of the external power
supply used in the system.
Unless all phases are shut off, the product may be damaged.
Do not directly touch the conductive sections and electronic components of the unit. This may result in
malfunction or failure of the unit.
CAUTION
WARNING
CAUTION
CAUTION

ii
[Precautions for wiring]
Tighten the terminal screws within the specified torque range. Loose tightening of the terminal screws
may result in a short-circuit, fire or malfunction. Excessive tightening of the terminal screws may
cause damage to the screws or unit, resulting in the unit falling down, short-circuit or malfunction.
Be careful to prevent foreign matter such as cutting chips and wiring offcuts from entering into the
unit.
Failure to do so may result in fire, failure or malfunction.
[Precautions for wiring]
An entry prevention label is attached at the upper part of the unit in order to prevent foreign matter
such as wiring scraps from entering into the unit when wiring. Do not remove this label during wiring
work.
Make sure to remove this label to discharge heat when operating the system.
Miswiring may damage the equipment. Be careful with regard to the label length and layout so that
connectors and electric wires are not disconnected.
When connecting wires with terminal blocks, do not use solder. Doing so may result in a contact
failure.
If wiring for the power line is too long, the voltage of the power supply to the remote slave unit may
become insufficient due to the voltage drop. Therefore, please connect an external power source to
ensure the specified voltage.
Do not turn on the 24V DC power source before completing wiring and connections throughout the
whole AnyWireASLINK system.
Use a 24V DC stabilized power supply for all AnyWireASLINK system devices.
Do not bind control wires or communication cables along with the main circuit or power line, and
ensure that they are not held close together.
Excess noise generated may result in malfunction.
Make sure to insert electric wires and cables to be connected to the unit into ducts or fix them with
clamps. Failure to put cables into ducts or fix them with clamps may cause drift, movement, or
careless tensioning which can lead to damage to the unit or cable, or a cable connection failure which
can lead to malfunction.
When removing cables connected to the unit, do not hold the cable and pull them out by hand.
Remove cables equipped with a connector by gripping the connector part of the unit.
To remove cables connected to the terminal blocks, first loosen the terminal screws on the terminal
block. If cables are pulled on while they are connected to the unit, it may result in malfunction or
damage of the unit or cable.
CAUTION
CAUTION

iii
[Precautions for startup and maintenance]
Do not touch the terminals while the power is on. Doing so may result in electric shock or malfunction.
When cleaning or re-tightening the screws on the terminal block and the unit mounting screws, make
sure to shut off all phases of the external supply power used in the system. Failure to shut off all
phases may result in electric shock. Insufficient tightening of the screws may result in short-circuit or
malfunction. Excessive tightening of the screws may cause damage to the screws or unit, resulting in
it falling down, a short-circuit, or malfunction.
Do not disassemble or modify each unit. Doing so may result in failure, malfunction, injury, or fire.
During installation and removal of the unit, make sure to shut off all phases of the external power
supply used in the system.
Failure to shut off all phases may result in failure or malfunction of the unit.
Before touching the unit, make sure you first touch grounded metal to discharge any static charge
present in your body. Failure to discharge static electricity may result in failure or malfunction of the
unit.
[Precautions for disposal]
When disposing of this product, always treat it as industrial waste.
CAUTION
CAUTION
WARNING

iv
Contents
1. Overview ·············································································································· 1-1
2. Specifications ········································································································ 2-1
2.1 General specifications ························································································· 2-1
2.2 Performance specifications ··················································································· 2-1
2.3 Outside dimensions····························································································· 2-2
2.4 Name of each part ······························································································ 2-3
2.5 Attaching to/detaching from DIN rail········································································ 2-4
3. Switch settings······································································································· 3-1
3.1 SET switch ········································································································ 3-1
3.2 RESET switch ···································································································· 3-1
4. LED display··········································································································· 4-1
5. Connections ·········································································································· 5-1
5.1 Connectors········································································································ 5-1
5.1.1. LAN connector ···························································································· 5-1
5.1.2. Connector terminal block··············································································· 5-1
5.1.3. Monitor connector························································································ 5-2
6. AnyWireASLINK····································································································· 6-1
6.1 System configuration ··························································································· 6-1
6.2 Slave units ········································································································ 6-2
6.3 Transmission line (DP-DN) ··················································································· 6-3
6.4 Connection mode································································································ 6-3
6.5 Transmission distance ························································································· 6-6
6.6 Transmission cable type and precautions ································································ 6-7
6.7 Transmission line supply current value ···································································· 6-8
6.8 Terminator········································································································· 6-9
6.9 AnyWire filter ····································································································6-10
6.10 Address setting (reference) ················································································6-12
7. Software functions ·································································································· 7-1
7.1 Modbus/TCP······································································································ 7-1
7.1.1. Input memory map······················································································· 7-1
7.1.1.1 Input memory map details·········································································· 7-2
7.1.1.2 Calendar clock ························································································ 7-3
7.1.1.3 Error status····························································································· 7-3
7.1.1.4 Check setting for number of transmission points············································· 7-4
7.1.1.5 Flag for ASLINK communication ································································· 7-4
7.1.1.6 Error history ···························································································· 7-5
7.1.1.7 MAC address ·························································································· 7-6
7.1.1.8 Latest error code/Latest error occurrence ID·················································· 7-6
7.1.1.9 Redundant address (ID) ············································································ 7-8
7.1.1.10 Error/alarm history·················································································· 7-9
7.1.1.11 R/O parameter storage area (30x128) ·······················································7-10
7.1.1.12 Registration ID······················································································7-12
7.1.2. Output memory map ···················································································7-13
7.1.2.1 Output area ···························································································7-13
7.1.2.2 Calendar clock settings ············································································7-14
7.1.2.3 Error clear ·····························································································7-14
7.1.2.4 Control command····················································································7-15
7.1.2.5 Parameter access method/Parameter access target ID···································7-16
7.1.2.6 Parameter storage area (20x128)·······························································7-17
7.2 SLMP (MC protocol) ···························································································7-17
7.3 EtherNet/IP·······································································································7-17

v
7.4 Web functions ···································································································7-18
7.4.1. Network settings·························································································7-19
7.4.2. Own station information ···············································································7-19
7.4.3. Connection destination information·································································7-20
7.4.4. AnyWire settings ························································································7-22
7.4.5. Time settings ·····························································································7-22
7.4.6. Process settings·························································································7-23
7.4.7. Off delay settings························································································7-23
7.4.8. Reboot ·····································································································7-24
7.4.9. Default setting····························································································7-24
8. Monitoring function ································································································· 8-1
8.1 Overview··········································································································· 8-1
8.2 Automatic address recognition··············································································· 8-1
8.3 Monitoring operation···························································································· 8-1
9. Required transmission time ······················································································ 9-1
9.1 Input ················································································································ 9-1
9.2 Output ·············································································································· 9-1
10. Device profile······································································································10-1
11. Troubleshooting ··································································································11-1
11.1 Visual check····································································································11-1
11.2 Check using input/output data·············································································11-2
11.3 LED state of the gateway···················································································11-3
11.4 LED state of the slave unit ·················································································11-4
12. Warranty············································································································12-1
13. RoHS Directive for the Chinese version····································································13-1
14. Change history····································································································14-1

Overview
1-1
1. Overview
The B2G78-E1 operates as a gateway unit for the Ethernet and AnyWireASLINK. The AnyWireASLINK
system can be connected to the Ethernet by using this gateway.
The AnyWireASLINK system is a "Sho-Haisen" (wiring saving) system consisting of compact and
fewer-point/multiple-distribution units suitable for wire saving on the sensor level.
This system covers bundling of a minimum 1 point to 16 points in a compact unit, therefore, it can bundle even
in a narrow device in which a BOX is not placed.
In addition, this system also proposes "Digital Link Sensors" that incorporate the AnyWireASLINK sensing
function and wiring saving function.
This is a sensor able to be directly connected to the transmission line, and offers excellent wiring saving
without using a remote terminal.
In addition to ON/OFF information, information such as sensing level and disconnections are also transmitted
to the controller side.
It is possible to monitor the operating state, prevent momentary stoppages, and significantly reduce cause
investigation time during a failure.

Specifications
2-1
2. Specifications
2.1 General specifications
Items Specifications
Ambient temperature for use 0 to +55°C
Storage temperature -20 to +75°C
Ambient humidity for use 10 to 90%RH (No condensation)
Atmosphere No corrosive or flammable gas
2.2 Performance specifications
Items Specifications
Transmission clock 27kHz (37μs)
Transmission
distance/supply current
Wire
diameter
Transmission distance DP-DN allowable
supply current
1.25mm
2
Shorter than 50m Less than 2A
Exceeding 50m, shorter than 100m Less than 1A
Exceeding 100m, shorter than 200m Less than 0.5A
0.75mm
2
Shorter than 50m Less than 1.2A
Exceeding 50m, shorter than 100m Less than 0.6A
Exceeding 100m, shorter than 200m Less than 0.3A
Number of units
connected
Up to 128 units
Transmission method DC power supply superimposed total frame/cyclic method
Connection mode T-branch method, multi-drop method, star-branch method, tree-branch
method
Transmission protocol AnyWireASLINK protocol
Error control Double check, checksum
Connection I/O points Up to 512 points (Input 256 points/output 256 points)
RAS function Transmission line disconnection detection function, transmission line
short-circuit detection function, transmission circuit drive power voltage
drop detection function, ID (address) redundancy/not set detection
function
Electric wire used General-purpose two-wire/four-wire cable (VCTF, VCT 0.75 to
1.25mm2, rated temperature 70°C)
General-purpose electric wire (0.75 to 1.25mm2, rated temperature
70ºC)
Dedicated flat cable (0.75mm2, 1.25mm2, rated temperature 90ºC)
Power supply Voltage 24[V] DC +15 to -10% (21.6 to 27.6[V] DC) Ripple 0.5[V]p-p max.
Current 150[mA] (when 128 slave units are connected, load current is not
included)
Transmission I/O point
number setting
Input 32 points
Output 32 points
Input 64
points
Output 64
points
Input 128
points
Output 128
points
Input 256 points
Output 256 points
Transmission cycle
time
2.4ms 3.6ms 6.0ms 10.7ms
Rated voltage 24V DC (21.6V to 27.6V)
Communication power
supply
Superimposed on transmission line
Load power supply Local power supply or collective power supply
Vibration resistance Conform to JIS C 0040
Withstand voltage 1,000V between external terminal and outer box for one minute
Noise resistance 1,000 Vp-p, pulse width 1μs

Specifications
2-2
2.3 Outside dimensions
Unit: mm
Board guide
Board guide
DIN hook
105,8

Specifications
2-3
2.4 Name of each part
LED display
RESET switch
SET switch
Monitor connector
AnyWireASLINK
connector terminal block
Ethernet connector
terminal block
LINK.E LED
ACT LED

Specifications
2-4
2.5 Attaching to/detaching from DIN rail
Please install this device to the DIN rail before use.
Vertical installation
1. DIN rail attachment procedure
Hook spring pin A on the center of the back face onto the DIN rail.
Fit C into the DIN rail while pressing this device upward from underneath.
2. DIN rail detachment procedure
When the knob B is pulled downward with a flat-blade screwdriver, C is removed, and then this system
can be detached.
Do not install in the reverse direction (with A on the bottom side).
This device may become detached from the DIN rail due to vibration, etc.
CAUTION
!
B
A
DIN rail
B
DIN rail
C
C
A
DIN rail
DIN rail
C

Switch settings
3-1
3. Switch settings
3.1 SET switch
This is a switch for carrying out automatic address recognition for the AnyWireASLINK slave unit.
Pressing the SET switch for approximately two seconds or more lights up the "SET" LED to start automatic
address recognition.
In addition, when the B2G78-E1 is turned on (or reset) while the SET switch is being held down, the system
starts up in the default setting mode. P7-19
3.2 RESET switch
Resets the main unit.

LED display
4-1
4. LED display
LED
symbol
Color Name : Lit/flashing : Unlit
RUN Green B2G78-E1
status
Lit Normally operating Hardware error or watchdog
timer error has occurred
LINK Green Transmission
active
Flashing Normally operating
SET Green Automatic
address
recognition
operating
Lit Automatic address
recognition operating
Normally operating
RDY Green B2G78-E1
status
Lit Normally operating
ERR Red Master unit
alarm status
Lit DP, DN disconnection
No slave unit response
Normally operating
Slow flashing
(every second)
Short-circuit between
DP-DN
Quick flashing
(every 0.2 seconds)
24V DC is not supplied
or voltage is low.
ALM Orange Slave unit
status
Lit I/O disconnection, I/O
short-circuit, address
redundancy, sensing
level drop etc., are
detected
Normally operating
LINK.E Orange Ethernet link
status
Lit LAN cable is correctly
connected
ACT Green Ethernet BUS
status
Flashing Packet detection
RDY LED
LINK.E LED
ACT LED
ERR LED
ALM LED
RUN LED
LINK LED
SET LED

Connections
5-1
5. Connections
5.1 Connectors
5.1.1. LAN connector
This is an RJ45 connector for connecting a 10BASET/100BASETX cable.
Ethernet port
5.1.2. Connector terminal block
This is a connector terminal block for connecting a 24V DC power supply and AnyWireASLINK transmission
lines (DP, DN).
The following shows the terminal arrangement.
Signal
name
Dedicated flat
cable wire color Link connector
0.75sq 1.25sq Pin
number
Type
24V
0V
DP
DN
LG
Green
White
Red
Black
--
Brown
White
Red
Black
--
4
3
2
1
0.75sq:
LP2-BK-10P (For two-wire)
LP4-BK-10P (For four-wire)
LP4-WH-10P (For four-wire, pin
protector type)
1.25sq:
LP2-BR-10P (For two-wire)
LP4-WR-10P (For four-wire)
Connector type: MC1, 5/5-STF-3,81 (manufactured by Phoenix Contact)
Pin Signal
1 TxD+
2 TxD-
3 RxD+
4 Termination
5 Termination
6 RxD-
7 Termination
8 Termination

Connections
5-2
5.1.3. Monitor connector
This is a connector for connecting a debugging monitor. Signals are RS232 compatible.
5
4
3
2
1
SG
RXD
TXD
MRXD
MTXD
5
4
3
2
1
SG
RXD
TXD
9
8
7
6
-
-
-
-
-
-
* Connect the above extension cable and the personal computer with a cross cable.
Connector: Manufactured by JST
Housing: XHP-5
Contact: BXH-001T-P0.6
D-sub 9-pin
Male
When making an
extension cable

AnyWireASLINK
6-1
6. AnyWireASLINK
6.1 System configuration
The AnyWireASLINK system consists of a master unit, slave units and their peripheral devices.
For
out
p
ut
For
in
p
ut
For
in
p
ut
For
out
p
ut
Terminator
Slave unit
Gateway

AnyWireASLINK
6-2
6.2 Slave units
Types of slave units
This product uses slave units for the AnyWireASLINK system.
The following types of slave units can be used.
Name Example of devices to be connected
Input/output unit General-purpose switches, sensors, LEDs, solenoid valves, relays, etc.
Relay output terminal AC drive load, etc.
Manifold driver Dedicated manifold
Digital link sensor Integrated transmission/sensing functions
General-purpose input head
Dedicated function
device ASLINK POKAYOKE terminals, ASLINK mapping terminals
Confirm the model name and type of the slave unit by using the separate AnyWireASLINK system
catalog.
Number of slave units connected
The maximum number of slave units that can be connected to one line of the AnyWireASLINK system
is 128 units.
(It is necessary that both the total number of points occupied by slave units and the total consumption
current of the transmission line do not exceed the maximum number of transmission points and the
allowable supply current.)
Connection of slave units
There are roughly two types of methods for the connection of AnyWireASLINK slave units.
One is the "two-wire (non-isolated) type" method and the other is the "four-wire (isolated) type" method.
Classification Operation
Two-wire (non-isolated)
type
Slave units and connection loads are driven with just two transmission lines.
Four-wire (isolated) type
Two transmission lines are used to drive the transceivers. Slave units and
connection loads are driven by two external power supply lines.
This is selected when the allowable supply current via two transmission lines
is insufficient, or when you wish to separate the power supply to the load.
Any configuration consisting of the two-wire type only, the four-wire type only, or a mixture of two-wire
and four-wire types can be used.
The choice whether to use a two-wire type or a four-wire type depends on the slave unit.

AnyWireASLINK
6-3
6.3 Transmission line (DP-DN)
The "AnyWireASLINK Protocol" is a low speed transmission clock that can also achieve effective
high-speed transmission making it compatible with a wide range of cable characteristics, and therefore
allows for various transmission cables and general-purpose electric wires to be used as transmission
channels.
6.4 Connection mode
The AnyWireASLINK system allows for various connections such as T-branching, multi-drop, tree-branching,
and star-branching.
T-branching method
The T-branching method is a connection method to branch off a cable from an insulation displacement
connector or terminal block and connect to the slave unit.
The actual wiring is shown below.
When an insulation displacement connector is used
A flat cable is branched using an insulation
displacement connector as described below.
Branch
line
T-branching Multi-drop
Tree-branching

AnyWireASLINK
6-4
When a terminal block is used
A cable can be branched as follows using a commercially available terminal block (a terminal block
in which terminals that face each other are internally connected).
Branching between cabtyre cables
Conversion to a dedicated flat cable
Multi-drop method
The multi-drop method is a way to connect slave units directly to cables.
Use of this method eliminates the need for new cables or other connecting devices other than cables.
In the actual wiring, as shown in the image above, the signal lines of transmission cables from one side
and those of transmission cables from the other side are integrated and connected to the slave unit.

AnyWireASLINK
6-5
Tree-branching method
The tree-branching method is a way to re-connect a T-branched branch line using the T-branching
method or multi-drop method.
Actual wiring is the same as the T-branching method and the multi-drop method.
Star-branching method
The star-branching method is a way to connect the master unit and lay
cable radially from a certain branching point to connect the slave unit.
This method makes it easy to bundle transmission channels.
However, it also tends to easily cause reflection.
Although the AnyWireASLINK is not susceptible to reflection by a
transmission method with a low-speed transmission clock, lay cables at
the shortest distance with the minimum number of branches possible.
Table of contents
Other Anywire Gateway manuals
Popular Gateway manuals by other brands
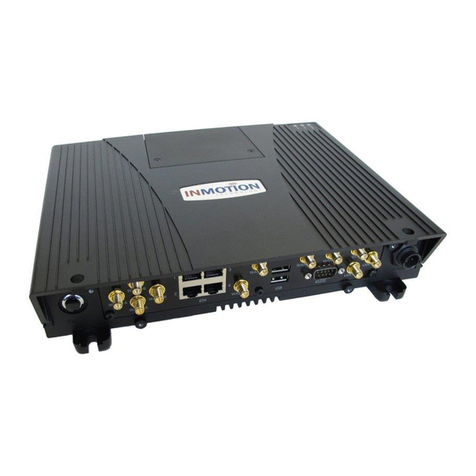
Sierra Wireless
Sierra Wireless oMG 2000 Quick setup guide

Juniper
Juniper SRX4200 Hardware guide
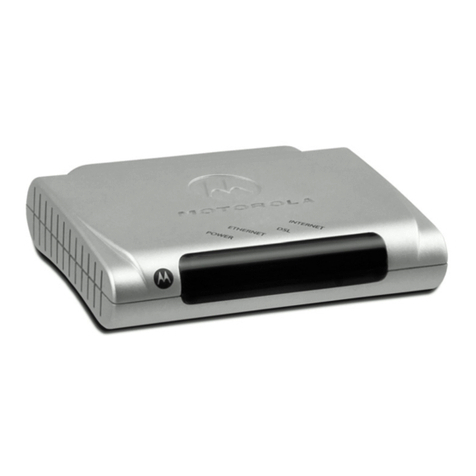
Motorola
Motorola NETOPIA 2210-02 ADSL2-RESIDENTIAL GATEWAY -... user manual
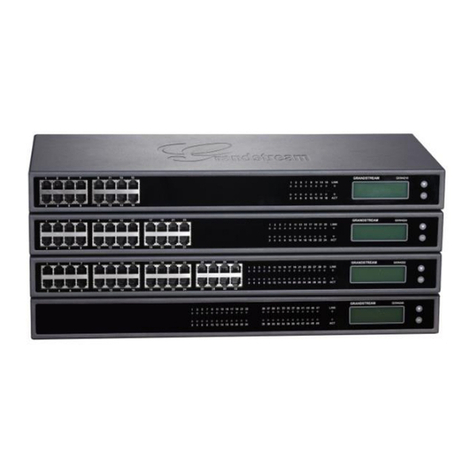
Grandstream Networks
Grandstream Networks GXW42XX series user manual
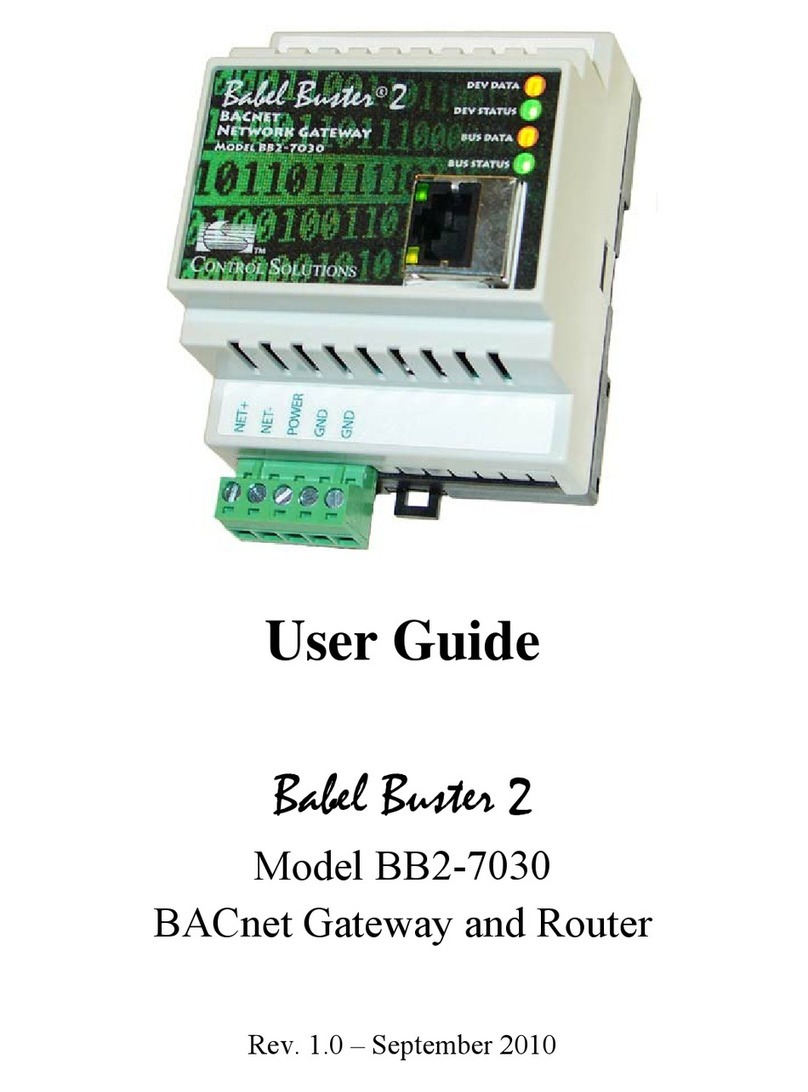
CONTROL SOLUTIONS
CONTROL SOLUTIONS BB2-7030 user guide
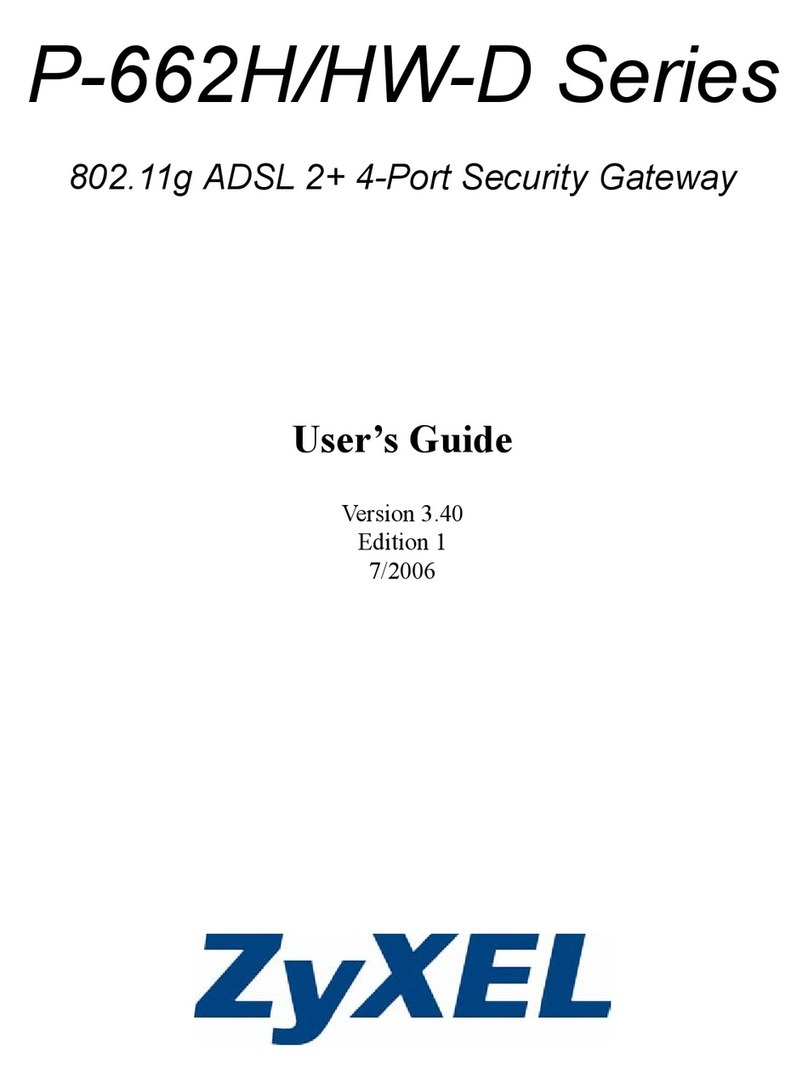
ZyXEL Communications
ZyXEL Communications 802.11g ADSL 2+ 4-Port Security Gateway HW-D... user guide