Anywire ASLINK B2G78-PB1 User manual

PMA-18204AA
PMA-10725AG-EN
AnyWireASLINK System
PROFIBUS Gateway
B2G78-PB1
User’s Manual
Version 1.5 August 6, 2019
Anywire Corporation
AnyWireASLINK System

i
Precautions
Precautions related to this user’s manual
1. The customer is kindly requested to see to it that this user’s manual reaches the end user.
2. Read this user’s manual thoroughly and understand the descriptions, and then operate this product.
3. This user’s manual is intended to describe the details of the functions provided in this product and not to
guarantee that this product serves the specific purposes the customer aims at.
4. Reproduction or duplication of part or all of this user’s manual without permission is prohibited.
5. Contents of this user’s manual may be subject to future changes without prior notice.
Safety precautions (Make sure to read before use)
When using this product, please carefully read this Manual and the related Manuals introduced in this Manual
and pay sufficient attention to safety in order to handle this product properly.
The precautions in this Manual describe only matters related to this product.
For safety precautions as a system, refer to User’s Manuals for controllers, such as the CPU unit.
“Safety precautions”ranks the safety precaution items into “WARNING”and “CAUTION.”
In addition,
Matters described in CAUTION may lead to serious consequences depending on the situation.
All describe important contents, therefore, make sure to observe the cautions and warnings.
Carefully store this Manual so as to access it whenever necessary, and deliver this Manual to the end user.
[Application of the product]
Application of the AnyWire system is limited to areas in which any failure and/or problem of the product
shall not result in serious consequences and in systems with fail-safe and backup functions are
provided externally.
The AnyWire system is designed for applications in general industrial purposes and does not come
with control features designed for mission critical purposes.
Therefore, the product is not applicable in areas like medical equipment, nuclear power plants, railroad,
aviation, safety devices, in which extreme safety is the priority.
WARNING
Improper handling may cause a dangerous situation and can result in
death or serious injury.
Improper handling may cause a dangerous situation and can result in
moderate injury or minor injury or is assumed to result in property
damage only.
WARNING
CAUTION

ii
[Precautions for design]
The AnyWire system has high noise resistance, however, keep transmission lines and input/output
cables 100 mm or more (as a guide) away from high-voltage cables or power lines. A malfunction may
result.
Incorporate an emergency stop circuit and an interlock circuit for safety into an external circuit other
than the AnyWire system.
[Precautions for installation]
AnyWire products should be used in environments that meet the general specifications presented in
the User’s Manual.
Using them in environments outside the general specifications may result in injuries due to electric
shock, fire, malfunctions and/or damage to or degradation of the products.
Install respective products properly. Improper installations may cause malfunctions, failures and/or
falls.
If they are to be installed on a DIN rail, ensure to orient the products so that the fixed hooks would be
on top.
Holding them with the movable hooks on top may cause devices to fall due to vibrations or the weight
of cables.
It is strongly recommended to use DIN rail stoppers for secure installation.
If screws were used to install them, fasten screws within the torque specified for respective screws.
Loose screws or screws fastened too tight may cause damage, dropout and/or malfunction of the
devices.
To install and remove the devices, always ensure that all phases of external power supplies used in the
system are shut down.
Failing to do so may result in damages and/or malfunctions due to sneak current.
Do not touch energized parts and electronic components with a bare hand. Doing so may cause
malfunctions and/or failures.
CAUTION
WARNING

iii
[Precautions for wiring]
Tighten the terminal screws within the specified torque range. Loose tightening of the terminal screws
may result in short-circuit, fire or malfunction. Excessive tightening of the terminal screws may cause
damage to the screws or unit, resulting in dropping, short-circuit or malfunction.
Be careful to prevent foreign matter such as cutting chips and wiring offcuts from entering into the unit.
Fire, failure or malfunction may result.
On the upper part of the units, protective labels are provided to prevent foreign matter, such as chips of
wires and shields, entering inside the units during the wiring operation. Do not remove those labels
until the wiring is complete.
To ensure proper heat radiation, confirm that those labels are removed prior to operating the system.
Incorrect wiring may damage the equipment. Be careful with regard to the label length and layout so
that connectors and electric wires are not disconnected.
When connecting wires with terminal blocks, do not solder. A contact failure may result.
If wiring for the power line is long, power voltage for the remote slave unit may become insufficient due
to voltage drop. Therefore, connect an external power source to ensure the specified voltage.
Do not turn on the 24 V DC power source before completing wiring and connections of the whole
Anywire system.
Use a 24 V DC direct current stabilized power supply for Anywire system devices.
Do not bind the control wire and communication cable with the main circuit or power line, or do not
bring them close to each other. Noise may result in malfunction.
Make sure to put electric wires and cables to be connected to the unit into ducts or fix them with
clamps. Unless cables are put into ducts or fixed with clamps, drift, movement or careless tensioning of
a cable may result in damage to the unit or cable, and a connection failure of a cable may result in
malfunction.
When removing cables connected to the unit, do not hold the cable section by hand when pulling.
Remove the cable equipped with a connector by holding the connector on the connection part of the
unit.
To remove cables connected to the terminal blocks, loosen the terminal screws on the terminal block.
When cables are pulled while they are connected to the unit, malfunction or damage of the unit or cable
may result.
CAUTION

iv
[Precautions for startup and maintenance]
Do not touch the terminals while the power is on. Electric shock or malfunction may result.
To clean or to re-tighten the screws on the terminal block and the unit mounting screws, make sure to
shut off all phases of the external supply power used in the system. Unless all phases are shut off,
electric shock may result. Loose tightening of the screws may result in short-circuit or malfunction.
Excessive tightening of the screws may cause damage to the screws or unit, resulting in dropping,
short-circuit or malfunction.
Do not disassemble or remodel each unit. Failure, malfunction, injury or fire may result.
Make sure to shut off all phases of the external supply power source used in the system for installation
and removal of the unit.
Unless all phases are shut off, failure or malfunction of the unit may result.
Before touching the unit, make sure to touch grounded metal to discharge static electricity charged to
the human body. Unless static electricity is discharged, failure or malfunction of the unit may result.
[Precautions for disposal]
Dispose of this product as industrial waste.
WARNING
CAUTION
CAUTION

v
Contents
1. Overview·············································································································1-1
2. Specifications·······································································································2-1
2.1 General specifications ························································································2-1
2.2 Performance specifications··················································································2-2
2.3 Outside dimensions ···························································································2-3
2.4 Name of each part·····························································································2-4
2.5 Attaching to/detaching from DIN rail·······································································2-5
3. Switch settings ·····································································································3-1
3.1 Address setting switch························································································3-1
3.2 Communication speed setting ··············································································3-1
3.3 Transmission point number setting switch ·······························································3-1
3.4 Registration of slave module················································································3-2
3.5 SET switch·······································································································3-3
4. AnyWireASLINK ···································································································4-1
4.1 System configuration··························································································4-1
4.2 Slave units·······································································································4-2
4.3 Transmission line (DP-DN) ··················································································4-3
4.4 Connection mode ······························································································4-3
4.5 Transmission distance························································································4-6
4.6 Transmission cable type and precautions································································4-7
4.7 Transmission line supply current value ···································································4-8
4.8 Terminator ·······································································································4-9
4.9 AnyWire filter·································································································· 4-10
4.10 Address setting (reference)·············································································· 4-12
5. Input/output data···································································································5-1
5.1 Input memory map·····························································································5-1
5.2 Output memory map···························································································5-2
5.3 Latest error code/Latest error occurrence ID····························································5-3
5.4 Status details····································································································5-6
5.5 Status details/sensing level access method·····························································5-7
5.6 Error clear········································································································5-7
6. Monitoring function································································································6-1
6.1 Overview·········································································································6-1
6.2 Automatic address recognition··············································································6-1
6.3 Monitoring operation ··························································································6-1
7. LED display ·········································································································7-1
8. Connections·········································································································8-1
8.1 Connectors ······································································································8-1
8.1.1. PROFIBUS connector.................................................................................................8-1
8.1.2. AnyWireASLINK connector terminal block...................................................................8-1
8.1.3. Monitor connector........................................................................................................8-2
9. Required transmission time ·····················································································9-1
9.1 Double check····································································································9-1
9.2 Maximum transmission delay time·········································································9-2
10. Device profile ··································································································· 10-1
11. Troubleshooting ································································································ 11-1
11.1 Visual check ································································································· 11-1
11.2 Check using input/output data··········································································· 11-2
11.3 LED state of the gateway················································································· 11-3
11.4 LED state of the slave unit ··············································································· 11-4

vi
12. Warranty ········································································································· 12-1
13. RoHS Directive for the Chinese version·································································· 13-1
14. Change history ································································································· 14-1

Overview
1-1
1. Overview
The B2G78-PB1 operates as a gateway unit for the PROFIBUS and AnyWireASLINK. The AnyWireASLINK
system can be connected to the PROFIBUS by using this gateway.
The AnyWireASLINK system is a “Sho-Haisen”(wiring saving) system consisting of compact and
fewer-point/multiple-distribution units suitable for wire saving on the sensor level.
This system covers bundling of a minimum 1 point to 16 points in a compact unit, therefore, it can bundle even
in a narrow device in which a BOX is not placed.
In addition, this system also proposes “Digital Link Sensors”that incorporate the AnyWireASLINK sensing
function and wiring saving function.
This is a sensor able to be directly connected to the transmission line, and offers excellent wiring saving
without using a remote terminal.
In addition to ON/OFF information, information such as sensing level and disconnections are also transmitted
to the controller side.
It is possible to monitor the operating state, prevent momentary stoppages, and significantly reduce cause
investigation time during a failure.

Specifications
2-1
2. Specifications
2.1 General specifications
Items
Specifications
Operating ambient temperature/humidity
0–+55C, 10%–90% RH, without condensation
Storage ambient temperature/humidity
-20–+75C, 10%–90% RH, without condensation
Resistance to vibration
Based on JIS B 3502 and IEC 61131-2
Resistance to shock
Based on JIS B 3502 and IEC 61131-2
Atmosphere
No corrosive gas
Rated altitude*1
0–2000 m
Pollution degree*2
2 or less
*1 Do not use or store the AnyWire ASLINK equipment in an environment pressurized more than the atmospheric
pressure at 0 m altitude. Failure to observe this instruction causes malfunction of the equipment.
*2 Index indicating a degree of conductive substance generation under the equipment operating environment.
“Pollution degree 2” indicates generation of nonconductive substance only. However, temporary conduction may
occur in the environment due to accidental coagulation.

Specifications
2-2
2.2 Performance specifications
Items
Specifications
Transmission clock
27 kHz (37 μs)
Transmission method
DC power supply superimposed total frame, cyclic method
Synchronization
Frame/bit synchronization
Transmission protocol
AnyWire ASLINK protocol
Maximum number of bits
512 points (256 inputs, 256 outputs)
Number of connectable units
128 units max.
Transmission distance /
Supply current
Cable diameter
Transmission distance
DP-DN allowable
supply current
1.25 mm2
50 m or less
MAX 2A
Over 50 m, 100 m or less
MAX 1A
Over 100 m, 200 m or less
MAX 0.5A
0.75 mm2
50 m or less
MAX 1.2A
Over 50 m, 100 m or less
MAX 0.6A
Over 100 m, 200 m or less
MAX 0.3A
0.5 mm2
50 m or less
MAX 0.8A
Over 50 m, 100 m or less
MAX 0.4A
Over 100 m, 200 m or less
MAX 0.2A
Error correction
Double check, chuck sum
RAS functions
Transmission cable disconnection detecting function, Transmission cable
short-circuit detecting function, Transmission circuit drive power supply
voltage drop detecting function, ID (address) duplication/no setting
detecting function
Applicable cable
General-purpose, 2-core/4-core cable (VCTF, VCT 0.75 to 1.25 mm2,
Rated temperature: 70C)
General-purpose cable (0.75 to 1.25 mm2, Rated temperature: 70C)
Dedicated flat cable (0.75 mm2 / 1.25 mm2, Rated temperature: 90C)
Connection method
T-branching, multi-drop, star-branching, Tree-branching
Power supply
Voltage: 21.6 to 27.6 V DC (24 V DC -10 to +15%) Ripple: 0.5 V p-p or less
Recommended voltage: 26.4 V DC (24 V DC +10%)
To comply with the UL standard, be sure to use a 24 V DC stabilized power
supply for NEC Class 2 output.
Bit transmission cycle time
32 inputs
32 outputs
64 inputs
64 outputs
128 inputs
128 outputs
256 inputs
256 outputs
2.4 ms
3.6 ms
6.0 ms
10.7 ms
Power consumption
150 mA (not including the load)
Weight
200 g

Specifications
2-3
2.3 Outside dimensions
Unit: mm

Specifications
2-4
2.4 Name of each part
LED display
Node address
setting switch
SET switch
Monitor connector
Transmission point number
setting switch
AnyWireASLINK
connector terminal block
PROFIBUS connector
terminal block

Specifications
2-5
2.5 Attaching to/detaching from DIN rail
Please install this device to the DIN rail before use.
Vertical installation
1. How to attach to the DIN rail
Hang the fixed hook on the upper part of the bottom surface on the DIN rail.
Snap in the machine by pressing it against the DIN rail.
2. How to detach from the DIN rail
Using a screwdriver or similar tool, loosen the DIN hook on the lower part of the bottom surface by
pulling it downward.
Remove the machine from the DIN rail.
Do not install this machine upside-down (with the fixed hook down).
This machine may be detached from the DIN rail due to vibration, etc.
CAUTION
!

Switch settings
3-1
3. Switch settings
3.1 Address setting switch
Set the address by using the address setting switch.
Do not change the address while the unit is in operation.
Address
Address setting switch
x10
x1
0
0
0
1
0
1
2
0
2
:
:
:
99
9
9
3.2 Communication speed setting
The communication speed on the PROFIBUS side is not set because it is according to the automatic follow
function.
The communication speed on the AnyWireASLINK side is fixed.
3.3 Transmission point number setting switch
Set the number of transmission points for the AnyWireASLINK.
This setting also changes the number of bytes occupied by the PROFIBUS.
SW
Number of transmission points
Number of bytes occupied by
the PROFIBUS
1
2
Input
Output
Total
Input
Output
ON
ON
32 points
32 points
64 points
16
16
OFF
ON
64 points
64 points
128 points
20
20
ON
OFF
128 points
128 points
256 points
28
28
OFF
OFF
256 points
256 points
512 points
44
44
* Always turn off the power before changing the DIP switch settings.

Switch settings
3-2
3.4 Registration of slave module
Register the slave module of this unit according to the number of transmission points on the
AnyWireASLINK side.
Total number of
transmission points
Module (registration order)
64 points
Status input 4 words
Status input 2 words
Command output 4 words
Command output 2 words
Input 2 words
Output 2 words
128 points
Status input 4 words
Status input 2 words
Command output 4 words
Command output 2 words
Input 4 words
Output 4 words
256 points
Status input 4 words
Status input 2 words
Command output 4 words
Command output 2 words
Input 4 words
Input 4 words
Output 4 words
Output 4 words
512 points
Status input 4 words
Status input 2 words
Command output 4 words
Command output 2 words
Input 4 words
Input 4 words
Input 4 words
Input 4 words
Output 4 words
Output 4 words
Output 4 words
Output 4 words

Switch settings
3-3
Module registration example for a total of 512 transmission points
3.5 SET switch
This switch is for performing error flag clear, and automatic address recognition for the AnyWireASLINK
slave unit.
(1) Error flag clear
Pressing the SET switch clears the error flag.
This is the same operation as clearing the error flag of the output memory. P5-7
(2) Automatic address recognition
Pressing the SET switch for approximately two seconds or more lights up the “SET”LED to start
automatic address recognition. P6-1

AnyWireASLINK
4-1
4. AnyWireASLINK
4.1 System configuration
The AnyWireASLINK system consists of a master unit, slave units and their peripheral devices.
For
output
For
input
For
input
For
output
Terminator
Slave unit
Gateway

AnyWireASLINK
4-2
4.2 Slave units
Types of slave units
This product uses slave units for the AnyWireASLINK system.
The following types of slave units can be used.
Unit type
Slave
I/O terminal
ASLINK terminals and the like
Analog terminal
Analog input unit and the like
Sensor/amplifier
ASLINK sensor and the like
Other hardware
Small display unit and the like
Confirm the model name and type of the slave unit by using the separate AnyWireASLINK system
catalog.
Number of slave units connected
The maximum number of slave units that can be connected to one line of the AnyWireASLINK system
is 128 units.
(It is necessary that both the total number of points occupied by slave units and the total consumption
current of the transmission line do not exceed the maximum number of transmission points and the
allowable supply current.)
Connection of slave units
There are roughly two types of methods for the connection of AnyWireASLINK slave units.
One is the “two-wire (non-isolated) type”method and the other is the “four-wire (isolated) type”method.
Classification
Operation
Two-wire (non-isolated)
type
Slave units and connection loads are driven with just two transmission lines.
Four-wire (isolated) type
Two transmission lines are used to drive the transceivers. Slave units and
connection loads are driven by two external power supply lines.
This is selected when the allowable supply current via two transmission lines
is insufficient, or when you wish to separate the power supply to the load.
Any configuration consisting of the two-wire type only, the four-wire type only, or a mixture of two-wire and
four-wire types can be used.
The choice whether to use a two-wire type or a four-wire type depends on the slave unit.

AnyWireASLINK
4-3
4.3 Transmission line (DP-DN)
The “AnyWireASLINK Protocol”is a low speed transmission clock that can also achieve effective
high-speed transmission making it compatible with a wide range of cable characteristics, and therefore
allows for various transmission cables and general-purpose electric wires to be used as transmission
channels.
4.4 Connection mode
The AnyWireASLINK system allows for various connections such as T-branching, multi-drop, tree-branching,
and star-branching.
T-branching method
The T-branching method is a connection method to branch off a cable from an insulation displacement
connector or terminal block and connect to the slave unit.
The actual wiring is shown below.
When an insulation displacement connector is used
A flat cable is branched using an insulation
displacement connector as described below.
Branch
line
T-branching
Multi-drop
Tree-branching

AnyWireASLINK
4-4
When a terminal block is used
A cable can be branched as follows using a commercially available terminal block (a terminal block
in which terminals that face each other are internally connected).
Branching between cabtyre cables
Conversion to a dedicated flat cable
Multi-drop method
The multi-drop method is a way to connect slave units directly to cables.
Use of this method eliminates the need for new cables or other connecting devices other than cables.
In the actual wiring, as shown in the image above, the signal lines of transmission cables from one side
and those of transmission cables from the other side are integrated and connected to the slave unit.
Table of contents
Other Anywire Gateway manuals
Popular Gateway manuals by other brands
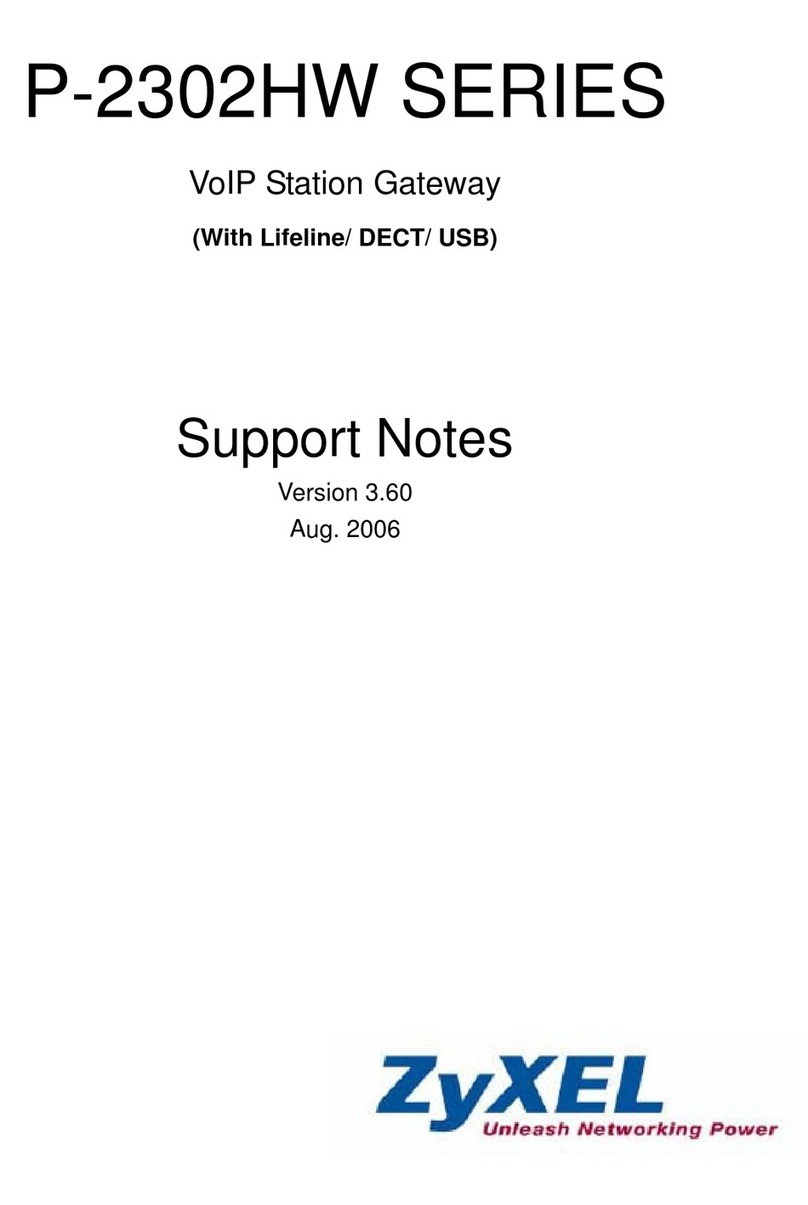
ZyXEL Communications
ZyXEL Communications P-2302HWDL-P1 Support notes
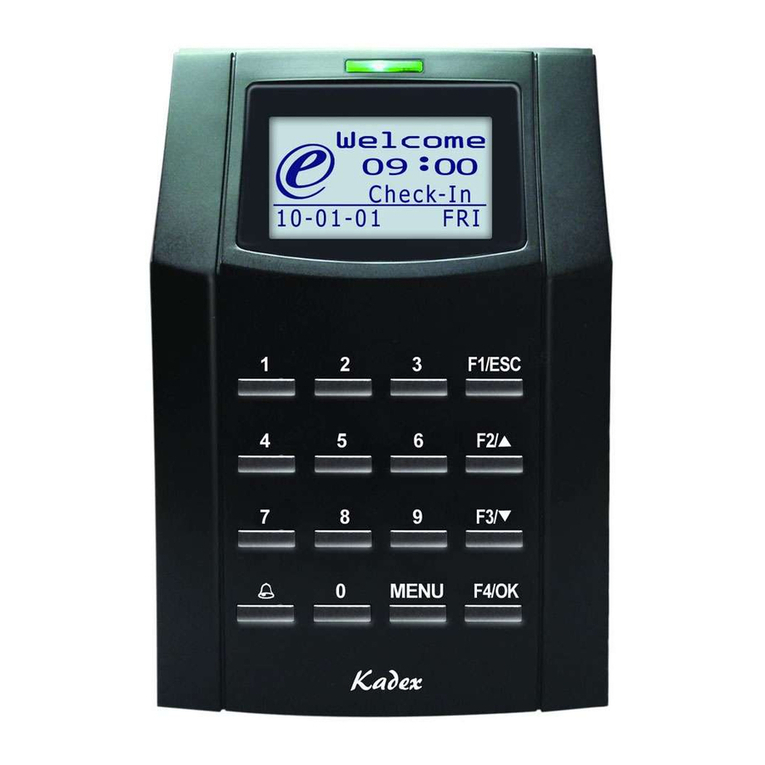
FingerTec
FingerTec Kadex user guide
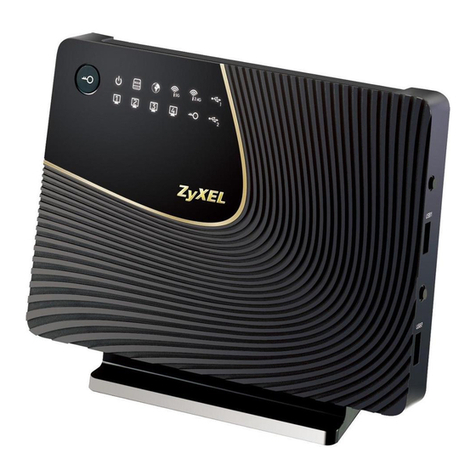
Videotron
Videotron EMG2926-Q10A user guide
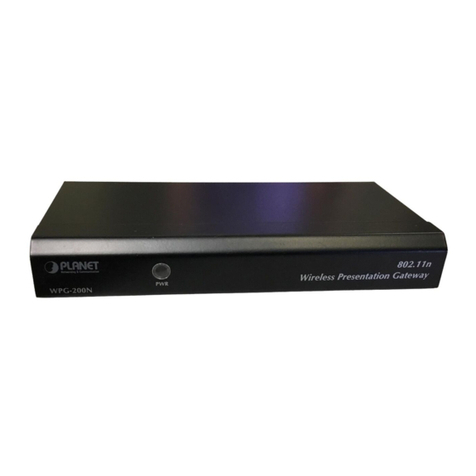
Planet Networking & Communication
Planet Networking & Communication WPG-200N Quick installation guide
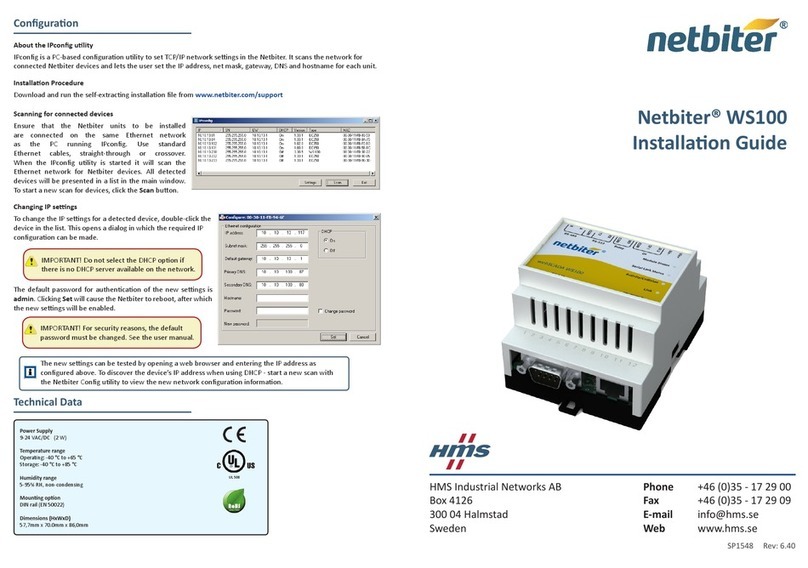
Netbiter
Netbiter WS100 installation guide
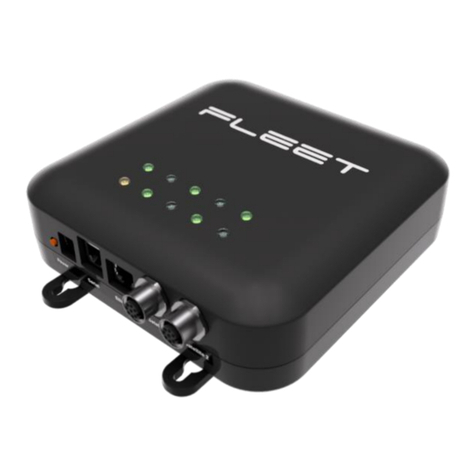
FLEET
FLEET Gen 2 Portal FSPOR0201-2 user manual