APAR AR654 Installation instructions

USER INSTRUCTION
AR654
UNIVERSAL FOUR-CHANNEL
CONTROLLER WITH PROCESS RECORDING
AND A TIMER
Version 1 0 1
2017 03 24
APAR - SALES OFFICE
05-090 Raszyn, ul. Gałczyńs iego 6
Tel. +48 22 101-27-31, +48 22 853-49-30
E-mail: automaty a@apar.pl
Internet: www.apar.pl
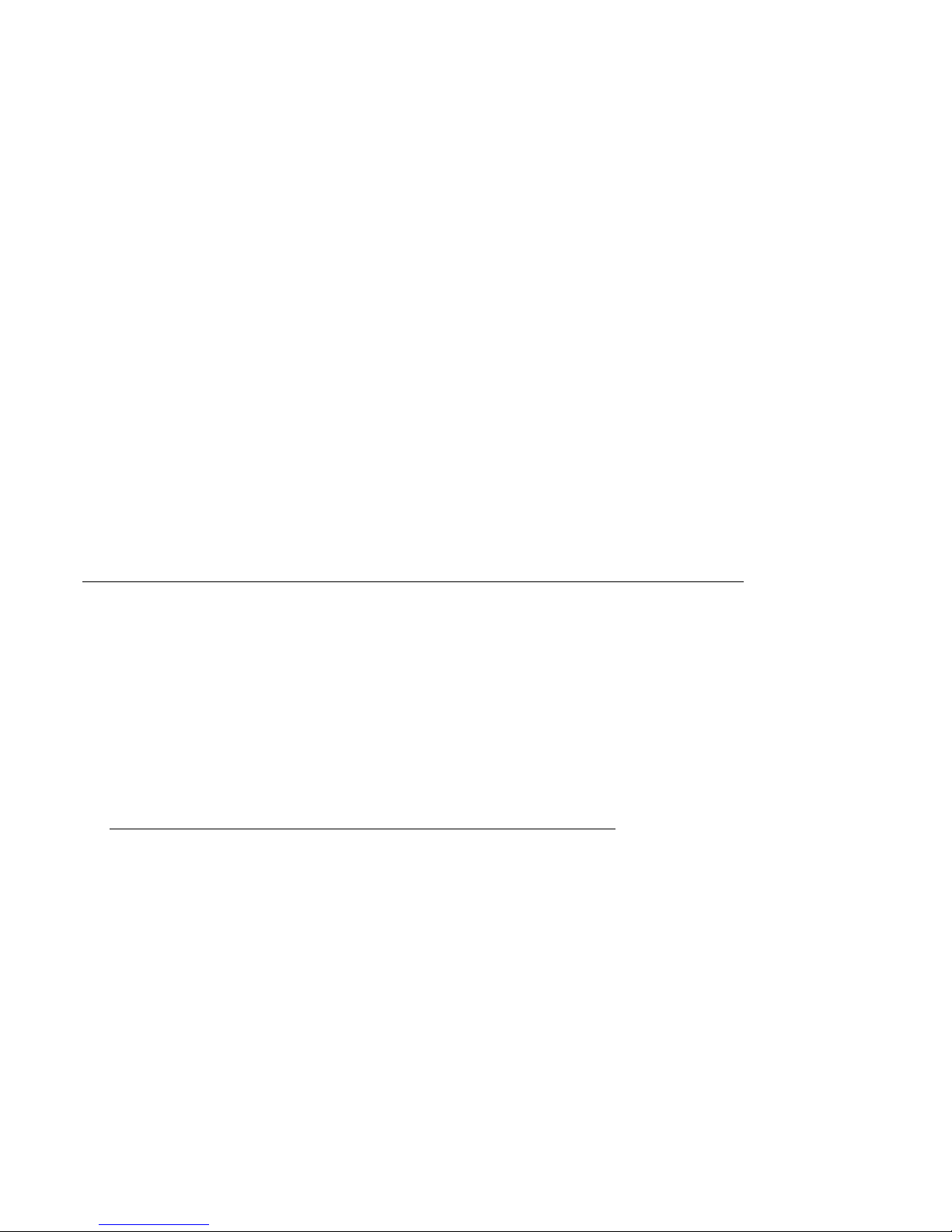
2
Thank you for choosing our product.
This instruction is intended to facilitate correct operation, safe use, and taking full advantage of
the controller's functionalities.
Before you start the device, please read and understand this instruction.
In the event of any additional questions, please contact our technical adviser.
CONTENT
1. AFETY RULE ........................................................................................................................................ 3
2. IN TALLATION GUIDELINE ................................................................................................................4
3. GENERAL CHARACTERI TIC OF THE CONTROLLER ..................................................................... 4
4. CONTENT OF THE PACKAGE ............................................................................................................. 6
5. TECHNICAL DATA .................................................................................................................................. 6
6. ENCLO URE DIMEN ION AND IN TALLATION DATA .................................................................. 7
7. DESCRIPTION OF TERMINAL STRIPS AND ELECTRICAL CONNECTIONS ........................ 8
8. CONNECTING TO A COMPUTER AND IN TALLATION OF U B DRIVER .................................... 9
9. IN TALLATION OF OFTWARE ........................................................................................................... 9
10. FUNCTION OF HARDWARE BUTTON AND ELEMENT OF THE TOUCH CREEN ............... 10
11. DESCRIPTION OF DATA SHOWN ON THE LCD DISPLAY ..................................................... 12
11.1. UPPER AND LOWER DEVICE TATU BAR ............................................................................ 12
11.2. VIEW OF A MEA UREMENT GROUP AND CONTROL PARAMETER (CONTROL)…..... 13
11.3. VIEW OF A MEA UREMENT GROUP (TEXT ONLY) .............................................................. 13
11.4. VIEW OF A MEA UREMENT GROUP (TEXT AND BAR GRAPH).......................................... 14
11.5. VIEW OF A MEA UREMENT GROUP (TEXT AND ANALOG INDICATOR) ......................... 14
11.6. INGLE MEA UREMENT (CHART) .......................................................................................... 14
11.7. QUICK CONTROL PARAMETER CONFIGURATION CREEN ............................................ 15
12. SETTING PARAMETERS AND OPERATIONS ON FILES (MAIN MENU)…………........ 15
12.1. MEANING OF ICON IN MENU ITEM ................................................................................... 16
12.2. CONFIGURATION OF MEA UREMENT CHANNEL OF THE DI PLAY.............................. 17
12.3. CONFIGURATION OF MEA UREMENT INPUT ................................................................... 18
12.4. CONTROL AND ALARM OPTION ........................................................................................ 19
12.4.1. OUTPUT (P/ R, mA/V) AND FUNCTION INPUT (BIN, F1) CONFIGURATION.... 19
12.4.1.1. ELECTION OF ETPOINT VALUE AND OPERATION MODE ,
AND TART OF CONTROL ................................................................................. 22
12.4.1.2.ANALOG OUTPUT (mA/V) .............................................................................. 22
12.4.1.3.MANUAL AND REMOTE CONTROL FUNCTION ............................................ 22
12.4.1.4.E-MAIL ALARM NOTIFICATION ......................................................................23

3
!
12.4.2. ET OF PID PARAMETER ............................................................................................ 23
12.4.2.1. PID CONTROL .....................................................................................................24
12.4.2.2. AUTOTUNING OF PID PARAMETER ............................................................. 25
12.4.2.3 PID PARAMETER CORRECTION ..................................................................... 26
12.4.3. ET OF PROGRAM CONTROL PARAMETER ........................................................... 26
12.4.3.1. CONFIGURATION OF AN EXAMPLE PROGRAM .......................................... 27
12.5. RECORDING ETTING ............................................................................................................ 28
12.6. MEMORY OPTION AND OPERATION ON FILE .............................................................. 28
12.7. DI PLAY ETTING ................................................................................................................... 30
12.8. ERIAL R 485, U B, AND ETHERNET COMMUNICATION ETTING .............................. 30
12.8.1. DYNAMIC ERVER DN (DDN ) CLIENT ................................................................. 31
12.9. ACCE AND OTHER ETTING .............................................................................................. 32
12.10. DATE AND TIME .......................................................................................................................33
12.11. DEVICE INFORMATION .......................................................................................................... 33
13. U E AND FUNCTION OF U B MEMORY (PENDRIVE) ................................................................ 33
14. VIEWING RECORDED MEA UREMENT AND EVENT ................................................................34
15. ME AGE AND ERROR IGNALING ................................................................................................. 34
16. IMPORTANT COMMENTS PERTAINING TO OPERATION..................................................... 35
17. R 485 COMMUNICATION INTERFACE (acc. to EIA R -485) ....................................................... 35
18. MODBU –RTU ERIAL TRAN MI ION PROTOCOL ( LAVE) .................................................... 36
19. MODBU –TCP ERIAL TRAN MI ION PROTOCOL .................................................................... 36
20. MAP OF DEVICE REGI TER FOR THE MODBU -RTU/TCP ......................................................... 37
21. U ER' NOTE ...................................................................................................................................... 40
Please pay particular attention to the text mar ed with this sign.
The manufacturer reserves the right to ma e changes to the design and the software (firmware) of the device
without any deterioration of the technical parameters (some functions may not be available in older versions).
Updating to the latest version of the firmware may require a repeated configuration of the device.
1 SAFETY PRINCIPLES
Before you start to use the device, become familiar with the present instructions.
a) in order to avoid electrocution or damage to the device, its mechanical and electrical installation must be
performed by qualified wor ers;
b) before switching on the power supply, ma e sure that all cables and wires are properly connected;
c) before ma ing any modifications to the wire and cable connections, switch off the voltage supplied to the device;
d) ensure proper operating conditions compliant with the technical specification of the device (chapter 5, power
supply voltage, humidity, temperature, etc.); do not expose the device to direct and intense heat.
!

4
!
2. INSTALLATION GUIDELINES
The device is designed so as to ensure an appropriate level of immunity to most interferences that may occur in
industrial and household environments. In environments of un nown level of interferences, it is recommended to
implement the following measures so as to prevent potential interference with the operation of the device:
a) do not supply the device from the same lines as high-power equipment without using appropriate power line filters;
b) use shielded supply, sensor, and signal cables, whereby the earthing of the shield should be single-point and
located as close to the device as possible;
c) avoid running measurement (signal) cables in the direct vicinity of and parallel to power and supply cables;
d) it is recommended to twist the signal wires in pairs or to use a finished twisted-pair cable;
e) in the case of sensing resistors in 3-wire connections, use identical wires;
f) avoid proximity of remotely controlled devices, electromagnetic meters, high power loads, loads with phase or
group power control, and other devices that cause high impulse disturbances;
g) ground or zero metal rails on which rail-mounted devices are installed.
Ma e sure to remove the protective film from the LCD display before the first use of the device.
3. GENERAL CHARACTERISTICS OF THE CONTROLLER
the device is intended for control, monitoring, and recording of temperature and other physical values
(humidity, pressure, level, flow rate, speed, etc.) processed into a standard electric signal (0/4÷20 mA, 0÷10 V,
0÷60 mV, 0÷850 Ω), with the possibility to present 1 to 4 measurement channels;
4 universal inputs (for thermoresistance and thermocouple sensors and for standard analogue signals, not
galvanically isolated) with the possibility to create inter-channel mathematical formulas such as difference,
average, sum, larger or smaller than, and ratio of measured values;
4 control/alarm outputs with independent adjustment algorithms:
ON-OFF with hysteresis, PID, autotuning PID, 12-section programmed control;
an optional module of 4 analogue outputs (0/4÷20 mA and 0/2V÷10V) and 5 functional binary inputs (BIN) to
change the operating modes of the associated outputs (control start/stop, selection of the day/night setpoint
value, manual/automatic mode for outputs); the analogue outputs are logically connected to the two-state
outputs (P/SSR) and are used for control or retransmission of measurements and setpoint values; the inputs
and the outputs are not insulated (common ground);
selection of setpoint values for outputs from among 2 defined for each output, the common value from the 1st
output (without and with offset for 3-way control), from the selected program or measurement from any input;
selection of independent PID sets (from the 8 available sets) for individual setpoint values (gain scheduling);
advanced automatic PID parameter selection function with fuzzy logic elements for each of the outputs;
4 programs with the possibility to define for each section such parameters as type (gradient/time/stop),
setpoint value, hysteresis, set of PID parameters, selection and status of auxiliary output, sound alarm, etc.;
time control/timer, options: continuous operation, periodic daily (hourly), or limited by date and time;
manual mode (open control loop) available for 2-state and analogue outputs with setting of the output signal
value in the range of 0÷100% (the impulse period or the entire range of variability for mA/V);
possibility to select the measured values to be displayed and, independently, the type of control signals for the
outputs (associated inputs or mathematic functions on the measurement signals, such as difference, average, etc.);
possibility to assign many outputs to one measurement channel and many inputs to one output;
available sound and visual signalling of the status of operation of outputs and email alarm notification;
programmable type of control/alarm: heating, cooling, in the band, outside of the band, manual mode;
recording of data in a standard text file located in the internal memory of the controller (4 GB) or an USB
memory in a FAT system, with possibility to edit in spreadsheet software, e.g. Microsoft Excel;
rich standard equipment with serial interfaces: USB (for wor with a computer and USB memories), RS485
(MODBUS-RTU), and Ethernet (100base-T, TCP/IP protocols: MODBUS-TCP, HTTP, SMTP, etc.);
a WWW server for wor with any web browser (Opera, IE, Firefox, etc.); the site contains information about active

5
measurement channels, control parameters and status, real time, status of the outputs, recording, etc., with the
possibility to show diagrams using the Google Chart API service (diagrams require constant Internet access);
the DDNS service, which enables easy access over the Internet to a controller connected to a networ that has
no fixed public IP address, through a friendly Internet address defined by the user; the service is available only
for registered users of popular DDNS services, such as DynDNS (www.dyndns.org), No-IP (www.no-ip.com), and
DNS-O-Matic (www.dnsomatic.com);
a colour LCD TFT graphic display 320x240 dots (QVGA), with a touch screen, brightness adjustment, and
programmable bac ground colour for individual measurement channels;
intuitive use, quic configuration, and clear signalling of device operating statuses and menu position;
a programmable language of the menu (Polish, English), which also covers the version of the site saved on the
WWW server;
graphic and text methods of presentation of the measured values (numerical values, bar graph, counter, graph);
grouping of measurement channels to be displayed, with automatic formatting of the screen (font size, etc.);
(programmable screen function buttons (F1) for each of the displayed control channels for quic selection of
one of the available functions (the same as for the binary inputs (BIN) of the optional module);
a programmable F button for quic selection of one of the available functions: start/stop of control for all
outputs, status of the device and of the Internet services, start/stop of recording, copying or moving archives
to a USB memory, bloc ing of sound alarms or the touch screen and the eypad;
a broad selection of recording start methods (continuous, limited by date and time, periodic daily, above or
below the permission threshold related to any measurement signal, only during control);
internal real time cloc with a battery bac up power supply (up to 8 years of continuous operation);
an integrated 24 V DC power supply supplying the field transducers (current output depending on the version);
compensation of line resistance for resistance sensors (automatic or permanent);
compensation of thermocouple cold tip temperature (automatic or permanent);
free software provided (for Windows 7/8/10) that enables presentation in a graphic or text form of the recorded
results (ARSOFT-LOG-WZ3) and configuration of parameters (ARSOFT-CFG-WZ1);
programmable display options, presented measured values and control signals for the outputs
(measurements, mathematic functions, etc.), types of measurement inputs, indication ranges, alphanumeric
description of measurement channels and groups, control/alarm, recording, communication, and access
options, and other configuration parameters;
two levels of access to the configuration parameters: full, protected with an administrator’s password, and limited,
to the quic configuration screen (for the basic control parameters), protected with the user’s password;
parameter configuration methods:
−from the film eypad and a touch screen located on the front panel of the device;
−through the USB, RS485, or Ethernet and free ARSOFT-CFG-WZ1 software or a user’s application,
communication protocol MODBUS-RTU and MODBUS-TCP;
−from configuration files saved in the USB memory or on a computer dis ;
available protection of saved measurement data against unauthorized modification (chec sum);
possibility to differentiate archives from many devices of the same or similar type by assigning individual
identification (ID) numbers;
clearly visible status of operation of control, recording, memory, USB port, alarms, file and dis operations,
serial transmission (USB, RS485, Ethernet), etc.;
recording of data until the memory is full (at least 2 years of continuous operation with recording of 4 channels
every 1 s);
possibility to transfer archive data and configuration data to a USB memory or using the USB port of a
computer, or via Ethernet;
simultaneous recording of data from all active measurement channels;
an enclosure for panel installation, lea -tightness from the front side IP65 or IP30 (depending on the version);
high accuracy and immunity to interferences;
possible user’s update of the controller’s software to the latest version from a USB memory;

6
available accessories: a USB memory (2 or 4 GB).
NOTE:
−Before you start working with the controller, make sure to become familiar with this operating
instruction and perform proper electrical and mechanical installation, as well as configuration of the
parameters in accordance with chapters 6, 7, and 12
−Do not use sharp-edged objects to work with the touch screen
−As a default, the controller is configured for presentation of temperature from the Pt100 sensors from
inputs 1-4 and for independent control of the ON-OF type with hysteresis for each of the P1/SSR1-
P4/SSR4 outputs (a description is provided in chapter 12).
4. CONTENTS OF THE SET
controller
a USB cable for connecting the device to a computer, 2 m long;
a CD with the drivers and the software (Windows XP/7/8/10);
a user instruction and a warranty card.
5. TECHNICAL DATA
Number of measurement inputs
4 universal, without galvanic separation (common earth)
Universal
inputs
(programmable, 16 types, 18-bit A/C processing), measurement ranges
-
Pt100 (RTD, 3
-
or 2
-
wire)
-
200 ÷ 850 °C
-
thermocouple R (TC, PtRh13
-
Pt
)
-
40 ÷ 1,600 °C
-
Ni100 (RTD, 3
-
or 2
-
wire)
-
50 ÷ 170 °C
-
thermocouple T (TC, Cu
-
CuNi)
-
25 ÷ 350 °C
-
Pt500 (RTD, 3
-
or 2
-
wire)
-
200 ÷ 620 °C
-
thermocouple E (TC, NiCr
-
CuNi)
-
25 ÷ 850 °C
-
Pt1000 (RTD, 3
-
or 2
-
wire)
-
200 ÷ 62
0 °C
-
thermocouple N (TC, NiCrSi
-
NiSi)
-
35 ÷ 1,300 °C
-
thermocouple J (TC, Fe
-
CuNi)
-
40 ÷ 800 °C
-
current (mA, R
in
= 100 Ω)
0/4 ÷ 20 mA
-
thermocouple K (TC, NiCr
-
NiAl)
-
40 ÷ 1,200 °C
-
voltage (V, R
in
= 180 Ω )
0 ÷ 10 V
-
thermocouple S (TC, PtRh10
-
Pt)
-
40 ÷ 1,600 °C
-
voltage (mV, R
in
> 2 M
Ω
)
0 ÷ 60 mV
-
thermocouple B (TC, PtRh30PtRh6)
300
÷ 1,800 °C
-
resistance (R, 3
-
p or 2
-
p)
0 ÷ 850
Ω
Response time for measurements
(10÷90%)
0.5 ÷ 2.5 s (programmable)
Resistance of leads
(RTD, R)
R
d
< 25 Ω (for each line), compensation of line
resistance
Resistance input current
(for RTD and R, multiplexed)
650
μ
A (Pt100, Ni100, 850
Ω
), 150
μ
A (Pt500, Pt1000)
Processing errors
(at ambient temperature of 25 °C):
-
basic
-
for RTD, mA, V, mV, R
≤0.1% of the measurement range ±1 digit
-
for thermocouples (TC)
≤0.2% of the measurement range ±1 d
igit
-
additional for thermocouples
≤2 °C (compensation of temperature of cold tips)
-
additional from ambient temperature changes
≤ 0.005% of the input range /°C
Indication range
(programmable)
total for measurement channel:
-
9999 ÷ 99999, for
analogue inputs: -9999 ÷ 19999 (resolution)
Resolution of indications/position of the decimal point
programmable, for thermometric inputs 0.1°C or 1 °C,
for other inputs 0 ÷ 0.000
2
-
state
outputs
(4 independent)
-
relay (P1÷P4, standard)
5A / 250VAC (for re
sistance loads), SPST
-
SSR (transistor, type NPN OC, optional)
24V, internal resistance 850 Ω, (SSR1
÷SSR4)
!

7
Analogue
outputs (optional,
4 current and
voltage, not
separated
galvanically) (1)
-
current 0/4 ÷ 20 mA (OUTPUT5 ÷
OUTPUT8, mA, common earth)
load capacity of the output Ro < 1,000 Ω, maximum
resolution 0.33 μA, 16 bit
-
voltage 0/2 ÷ 10 V (OUTPUT5 ÷ OUTPUT8,
V, common earth)
load capacity of the output Io < 3.7 mA (Ro > 2.7 Ω),
maximum resolution 0.17 mV, 16 bit
-
basic error of the output
< 0.1% of the output range
Digital inputs BIN
(quantity 5, contact or voltage < 24 V)
bistable, active level: short circuit or <0.8 V, optional
Power supply:
-
230 VAC (standard)
85 ÷ 260 VAC/ 10 VA
-
24 VAC/DC (option)
20 ÷ 50 VAC/ 10 VA, 22 ÷ 72 VDC/ 10 W
Power supply of field
transducers 24 VDC
(note 2)
for p
ower supply
230 V
AC
/24V
AC/DC
200/100 mA (without the optional module mA/V and
BIN)
for power supply 230 VAC +
module mA/V
150 mA
-
21 mA*N (N=number of active current outputs)
power supply 24 VAC/DC +
module mA/V
50 mA
-
21 mA*N (N=number of active curr
ent outputs)
Display
(graphical LCD TFT, 320x240 points - QVGA)
3.5" (diagonal), bac ground brightness adjustment
Touch screen
resistance, integrated with the LCD display
Communication
interfaces
(standard
equipment)
-
USB
(connection
type A4,
IP30 version
also accessible
from the front,
programmable mode
of operation)
-
slave mode
(device)
communication with a computer, drivers for the
Windows 2000/XP/Vista/7/8/10 system: exchangeable
dis (mass memory, readout speed approx. 335 B/s) +
virtual COM serial port (MODBUS-RTU protocol)
-
master mode
(host)
support of USB memory (pendrive) up to 4 GB, writing
speed approx. 135 B/s (depending on the type of the
memory)
-
RS485
(MODBUS-RTU protocol,
SLAVE)
speed 2.4÷115.2
bit/s, sign format 8N1, galvanic
separation
-
Ethernet
(type 100base-T, soc et RJ45,
data transfer up to 135 B/s - depending on
the networ )
web server, MODBUS
-
TCP, e
-
mail client (SMTP), DDNS
server client, TCP/IP protocols: DHCP (client, server),
SMTP, NetBIOS, ICMP, UDP, TCP
Real time clock
(
RTC
, lithium battery CR1220)
quartz, date, time, ta es leap years into account)
Data recording interval
programmable 1 s to 8 hours
(3)
Data storage memory
(non-volatile, recording of approx. 59 million measurements from 4 channels and 4 GB memory):
-
internal (micro SDHC card, industrial, MLC)
4 GB, FAT32 file system
-
external USB memory (pendrive, A4 type soc et)
FAT16, FAT32, maximum size 4 GB
Rated operating conditions
0 ÷ 50 °C, <100% RH (no condensat
ion)
Operating environment
air and neutral gases, no dust
Protection rating
IP65 or IP30 from the front, IP20 from the side of the
connections
Weight
approx. 420 g
Electromagnetic compatibility (EMC)
immunity: according to the PN
-
EN 61000
-
6
-
2 standar
d
emission: according to the PN
-
EN 61000
-
6
-
4 standard
Notes
: (1) - each of the outputs can wor in only one programmed standard: 0/4 ÷ 20 mA or 0/2 ÷ 10 V;
(2) - the output power depends on the equipment version (type of power supply, presence and number of
current outputs used); in the case of insufficient current efficiency, an external power supply and/or voltage
outputs instead of current outputs should be used;
(3) - for a recording interval equal to 1 s, uneven recording may ta e place during transfer of an archive via
Ethernet and also because of an excessive number of files, their sizes, and type and manufacturer of the USB
memory (pendrive) used.

8
6. ENCLOSURE DIMENSIONS AND INSTALLATION DATA
Enclosure type
panel, Incabox XT L57
Materi
al
self
-
extinguishing NORYL 94V
-
0,
polycarbonate
Enclosure dimensions
96 x 96 x 79 mm
Panel window
92 x 89 mm
Fixing methods
grips on the side of the enclosure
Conductor cross-sections
(separable connectors)
2.5 mm
2
(supply and alarm outputs),
1.5 mm
2
(others)
7. DESCRIPTION OF TERMINAL STRIPS AND ELECTRICAL CONNECTIONS
The numbering, location, and description of the connections on the bac panel and the method of connecting
sensors and electrical signals:
a) measurement connections (RTD, TC, mA, V, mV, R), INPUT1÷ INPUT4; the parameters configuration is described
in chapter 12.3
a 1) connection of the 2- and 3-wire transducer (Iou – output current, Uou – output voltage)
b) connections of the optional analogue output module (OUTPUT5÷OUTPUT8) and of functional binary inputs
(BIN1÷BIN5); the parameters configuration is described in chapter 12.4
Terminal clamps
(connections) Description
IN1
-
IN2
-
IN3
RTD and R (Pt100, Pt500, Pt1000, Ni100, 850Ω) inputs, in a 2
-
and 3
-
wire connection
IN1
-
IN2
thermocouple
input TC (J, K, S, B, R, T, E, N) and voltage input 0÷60 mV
IN1
-
GND
current input 0/4÷20 mA
IN2
-
GND
voltage input 0÷10 V
+24 V
output +24 V (in relation to the GND) of the integrated power supply of field transducers

9
!
c) other connections
NOTE:
In the IP30 version, a USB connection is
also available on the front panel.
DO NOT USE SIMULTANEOULY WITH
THE BACK CONNECTION!
8. CONNECTING TO A COMPUTER AND INSTALLATION OF US DRIVERS
Connecting the controller to a USB port of a computer may be useful in order to configure the names of channels,
groups, measurement units, and other parameters of the device, and to download files with recorded data. The
available support software is described further in the present instructions. Before connecting the cable to a USB
port of a computer, switch on the power supply of the controller and ma e sure that the US operation mode
parameter is set to Available for a computer (chapter 12.8, Communication settings menu). After you connect for
the first time, the Windows (XP/Vista/7/8/10) system detects the controller named "Apar Composite Device" and
demands installation of drivers of the virtual COM serial port (MODBUS-RTU protocol, also used by the ARSOFT-
CFG-WZ1 software). In the device manager or the new device wizard, manually indicate the location of the
drivers (a CD-ROM, a DRIVERS folder, or drivers downloaded from the www.apar.pl website).
In Windows 7/10 systems, one can use automatic downloading of the driver software from the Windows Update
website. In the Windows 7 system, from the Device Manager level, manual installation is performed in the
following manner:
1. Right-clic the item “Apar Composite Device” and select “Update the driver software”, and then “ rowse my
computer to find the driver software”.
2. Use the “ rowse...” button to indicate a location on the dis (the DRIVER folder) where the drivers are saved,
and then clic “Continue”.
3. The virtual COM port ”US Serial Port” is installed; press “Close”.
4. Additionally, in the “Disc drives” branch, the system detects and installs the “Microchip Mass Storage US Device”.
After the installation is completed, the controller is listed in the system as an exchangeable 4 GB dis with the label
Terminal
clamps
(connections)
Description
mA
-
GND
current output 0/4÷20 mA
each of OUTPUTS 5÷8 can wor in only one programmed
standard (mA or V), chapter 12.4
V
-
GND
voltage output 0/2÷10 V
BIN1÷4
-
GND
functional inputs related with control/alarm
outputs (chapter 12.4)
BIN5
-
GND
functional input Start/Stop for all control outputs (global, chapter 12.9)
Terminal
clamps
(connections)
Description
41÷44
RS485 serial interface (MODBUS
-
RTU transmission protocol)
45÷52
relay outputs P1÷P4 or SSR1÷SSR4 (transistor NPN OC), chapter 12.4
53
-
54
power supply input 230 VAC or 24 VAC/DC
ETHERNET
se
rial Ethernet interface (type 100base
-
T, RJ45 soc et, TCP/IP protocols)
USB
serial USB interface (programmable operation mode: device or host, chapter 12.8,
in the IP30 version, do not use two USB sockets at the same time)

10
!
AR654 and a virtual COMx serial port (x - port number: 1, 2, etc.). The serial port uses the MODBUS-RTU protocol.
In the internal memory two configuration text files are shown: AR654.cfg and AR654.txt (chapter 12).
Communication with the device can also be established using the Ethernet and the RS485 interfaces, which are a
part of the controller's standard equipment and do not require installation of additional drives. However, if an
RS485 converter for USB is used in the computer, it is necessary to install the serial port drivers provided by the
manufacturer.
NOTE:
- do not disconnect the device from the computer before completion of installation of the drivers
- connection of the controller to a USB port of a computer stops recording until the cable is disconnected and
bloc s the performance of file operations available from the menu level and transmission of files with
measurement data via Ethernet from the ARSOFT-LOG-WZ3 level.
9. INSTALLATION OF SOFTWARE
In the "SOFTWARE" folder of the CD-ROM that is provided with the device there is a free software installation set
for the controller. The installation set comprises the following applications (for Windows 2000/XP/Vista/7/8/10):
Name
Software description
ARSOFT-CFG-
WZ1
(for on-line
configuration)
-
display of current measurement data, as well as the date and the time,
- configuration of the real time cloc (RTC) and other parameters, such as types measurement
inputs, names of measurement channels, units, and groups, ranges of indications, recording,
alarm, display, communication, and access options etc. (chapter 12),
- creation on the dis of configuration files containing the current parameter settings for the
purpose of repeated use (bac up copy or multiplication of the configuration on other devices),
- the program requires communication with the recorder via the USB, RS485 or Ethernet port
ARSOFT-LOG-
WZ3
graphic or text presentation of recorded results with the possibility to print,
input data is ta en
from a csv text file created in the controller in the internal memory or the USB memory (chapter 14),
data can also be ta en via Ethernet
The latest versions of the aforementioned software are also available at the website (www.apar.pl, Download
oftware section). The detailed descriptions of the aforementioned applications can be found in the installation
folders.
10. FUNCTIONS OF HARDWARE UTTONS AND ELEMENTS OF THE TOUCHSCREEN
Fig 10 A description of the
front panel using the example
of the IP65 version (the IP30
version has an additional USB
soc et on the front)
LCD graphic display
with a touch panel screen buttons (touch)
hardware buttons
NOTE:
Do not use sharp-edged objects to work with the screen buttons and other screen objects
!

11
a) functions of buttons and elements of the touch panel in the measurement display mode (chapter 11)
Button or touch Description [and mar ing in the contents of the instruction]
[SET]
, hardware button:
- input in the parameter configuration and file operations menu. If the Password protection in the
Access and other options menu is switched on, then the password must be entered, chapter 12.9
- closes the message window appearing on the screen (chapter 15)
PV or SP
area of the
measu-
rement
channel
calling the Quick configuration screen for the main control parameters of the measurement
channel selected by touching (the area of the presented measured value PV or the setpoint value
SP, chapter 11). If the Password protection in the Access and other options menu is switched on
and the User password is other than zero, then the password must be entered, chapter 12.9
[UP]
or
[DOWN]
, screen buttons:
- change of the displayed measurement group or a single measurement channel in the CHART
type presentation mode
- change of the Quick configuration screen for the next associated control output
[LEFT] or [RIGHT], screen buttons: a change of the measurement data presentation method
(CONTROL, TEXT, BAR GRAPH, ANALOG INDICATOR, DIAGRAM, chapter 11)
[F], hardware button: activation of a function programmed with the F button function
parameter (chapter 12.9), active only in the measurement presentation mode, sub-item c
[ESC], hardware button: closing the message window appearing on the screen (chapter 15)
+
[F]
and
[ESC]
(simultaneously): calling the
Device status
screen (hardware information,
operation and Ethernet services parameters, current record number in the csv archive file, etc.);
the function is available also from the level of the [F] button (sub-item c and chapter 12.9)
b) functions of the buttons in the parameter configuration and file operations mode (Main Menu, chapter 12)
Button Description
-
selects the mar ed item in the menu (entering a lower menu level o
r edition of a parameter);
the action is also available from the touch screen level
- approves of the edited parameter value (saving in the non-volatile internal memory ta es
place after leaving the Main Menu or disconnecting the USB from the computer)
- closes the message window appearing on the screen (chapter 15)
[UP] or [DOWN] and the screen scroll bar:
- moves to the next or previous item in the menu
- changes the value of the edited parameter (also [LEFT] or [RIGHT])
-
returns to the previous menu (higher level)
- cancels the changes to the edited parameter
- exits the Main Menu and returns to the measurement presentation mode
- closes the message window appearing on the screen (chapter 15)
c) meaning of the function button [F] (active only in the measurement presentation mode)
Button
Description
(depending on the value of the
F button function
parameter in the
Access
and other options menu, chapter 12.9)
Status
signalling/icon
Device status
- device status screen (factory setting, function available also by
simultaneously pressing buttons [F] and [ESC], described in item a above) screen
Stop/Start of recording
- change of the
Type of recording
parameter to
O
ff
or
Continuous (chapter 12.5), after the power supply is switched on, the recording is always
on (continuous)
or none

12
Copy the archives to the US memory
(operation available also in the
Memory and files
options menu, chapter 12.6) messages
Move the archives to the US memory
- the files in the controller are deleted after they
have been copied messages
Disable/Enable sound alarm
- change of the
Alarm sound signal
parameter to
Disabled
or Enabled (chapter 12.4.1, Control and alarm options menu -> Output...); after the
power supply is switched on, the sound signalling of active alarms is always switched on
or none
Start/Stop of control for all outputs
- after the power supply is switched on, the control status
is exactly the same as at the time of switching off the power supply (no change), (chapter 12.4) or none
Touch panel lock – touch screen and eypad loc (except for [F]) or none
d) functions of the screen elements in the presentation mode of the Quick configuration screen of the control
channel (chapter 11.7)
Button or touch Description
or
[
SP c
hange]
or touching the area of the displayed measured value (
PV
) or setpoint value
(SP): change of the setpoint value selected with the Setpoint (SP) selection parameter
(chapter 12.4.1), limit of settings defined by parameters ottom and Top of the range for
graphics and SP (chapter 12.2)
[Start] or [Stop]: Start or Stop of control with the icon signalling the Control time mode
(continuous: or temporary: and ); after the power supply is switched on, the button
is set in accordance with the
State of control after power up
parameter, chapter 12.4.1
function button [F1] programmable with the F1 button and IN input function (select
P1/ P2, set Auto/Manu, None, etc.); a detailed description is given in chapter 12.4.1
11. DESCRIPTION OF DATA PRESENTATION ON THE LCD DISPLAY
The controller enables presentation of the measurement data in various modes in accordance with the following
diagram. The selection and methods of configuration of data for the displayed measurement channels are
described in chapter 12.2.
Fig 11 A bloc diagram of the available measurement data presentation modes (the detailed descriptions are
provided in successive chapters)

13
11.1. UPPER AND LOWER DEVICE STATUS AR
The status bars can be seen in the upper and lower part of the display only in the measurement presentation
modes. The meaning of the individual graphic elements is described below.
a) lower status bar
Fig 11 1 1 Lower status bar
Object
Description [
and mar ing in the contents of the instructions
]
6
no USB connection with the computer
the USB port is
accessible for the
computer (device)
signalling of the operation
mode and the status of the
USB port (chapter 12.8, Table
12.8, US operation mode
parameter)
the USB port is connected to the computer
no USB memory,
do not connect to the
computer! USB memory support
(host), chapter 13
USB memory (pendrive) was detected
7
measurement group name (up to 16 characters per group, ta en from the AR654.txt file, chapter 12.2)
8
view of a measurement group (control)
signalling of measurement
data presentation mode
(type of view) and of control
parameters
view of a measurement group (text only)
view of a measurement group (text and a bar graph)
view of a measurement group (text and an analogue indicator)
none
single measurement (chart)
Quic configuration screen (for main parameters of the control channel)
9
[Tx/Rx]
- signalling of presence of serial transmission (via the RS485, a USB port or the Ethernet)
10
signalling of the touch screen and eypad loc (one of the
[F]
button functions), chapter 12.9
b) upper status bar
Fig 11 1 2 Upper status bar
Object
Description [
and mar ing in the contents of the instructions
]
1
date (yyyy-mm-dd), day of the wee and time (hh:mm:ss) on the real time cloc (RTC, chapter 12.10)
2
status of control/alarm outputs, in the order from the 1st to the 4th, (configuration in the Control and
alarms options menu, chapter 12.4), grey colour - the output is off (the alarm is inactive), red colour (with
the numbers of the measurement inputs that activate the output) - the output is switched on
3
at least one of the output has the Alarm sound signal parameter is set to the Enabled value (chapter 12.4.1)
all the control/alarm outputs are bloc ed with the programmable [F] button (chapters 10 and 12.9)
4
[R/W]
- signalling of writing to or reading from the internal memory or the USB memory
5
signalling of ongoing recording in the internal memory or the USB memory (
)

14
11.2. VIEW OF A MEASUREMENT GROUP AND CONTROL PARAMETERS (CONTROL)
Fig 11 2 Appearance of the measurement group
screen in the CONTROL mode
11.3. VIEW OF A MEASUREMENT GROUP (TEXT ONLY)
Object
Description
1
status bars (chapter 11.1)
2
measurement panel: number, name (up to 16
characters) and unit (up to 4 characters) of the
measurement channel (name and unit ta en
from the AR654.txt file, chapter 12.2), measured
value (PV) with signalling of exceeded
measurement range (chapters 12.3
and 15)
Fig 11 3 Appearance of a measurement group screen in
the TEXT ONLY mode (an example of a group consisting of
two channels)
11.4. VIEW OF A MEASUREMENT GROUP (TEXT AND A AR GRAPH)
Fig 11 4 Appearance of the measurement group screen in
the TEXT AND BAR GRAPH mode
Object
Description
1
status bars (chapter 11.1)
2
measurement panel: number, name (up to 16
characters) and unit (up to 4 characters) of the
measurement channel (name and unit ta en from
the AR654.txt file, chapter 12.2), measured value
(PV) with signalling of exceeded measurement
range (chapters 12.3
and 15)
3 current setpoint value (
SP
) for the related
control/alarm output (chapter 12.4)
4
output signal value (
MV
) in the range of 0÷100%
(of the impulse period for the P/SSR output or the
full range of variability for the mA/V output)
5
control status: control mode (
ON
-
OFF
,
PID
,
ST
-
PID
-
autotuning, MANU - manual mode, STOP), the
number of the related output (control/alarm and
retransmission) and alternating information about
the status of the program control (PRG, if
activated); the details are given in chapter 12.4
Object
Description
1
status bars (chapter 11.1)
2
measurement panel: number, name, measured
value (PV), and unit of the measurement
channel (chapters 11.2 and 11.3), graphic
presentation of the measurement (bar graph)
wor s in the range set by the parameters
ottom of the range for graphs and Top of the
range for graphs (chapter 12.2)

15
11.5. VIEW OF A MEASUREMENT GROUP (ANALOG INDICATOR, COUNTER)
Fig 11 5 Appearance of the measurement group screen in
the ANALOG INDICATOR mode
11.6. SINGLE MEASUREMENT (DIAGRAM)
Fig 11 6 Appearance of a single measurement screen in the
DIAGRAM mode (possibility to present one channel)
11.7. QUICK CONTROL PARAMETERS CONFIGURATION SCREEN
Fig 11 7 Appearance of the Quick configuration
screen (possibility to present one control channel)
Entry into this display mode (a description is given in chapter 11) can be secured with a password screen when the
value of the Password protection parameter applies to manual configuration and the User’s password is other
than zero (Access and other options menu, chapter 12.9). As an alternative, the Administrator’s password can be
used.
Object
Description
1
status bars (chapter 11.1)
2
measurement panel: number, name, measured
value (PV), and unit of the measurement
channel (chapters 11.2 and 11.3), graphic
presentation of the measurement (analogue
indicator) wor s in the range set by the
parameters ottom of the range for graphs
and Top of the range for graphs (chapter 12.2)
Object
Description
1
status bars (chapter 11.1)
2
measurement panel: number, name, measured
value (PV), and unit of the measurement channel
(chapters 11.2 and 11.3), graphic presentation of
the measurement (diagram) wor s in the range
set by the parameters ottom of the range for
graphs, Top of the range for graphs (chapter
12.2), and Diagram time range (chapter 12.7)
Object
Description
1
status bars (chapter 11.1)
2
measurement panels (details are given in chapter 11.2)
3 current setpoint value (SP) for the related
control/alarm output (chapter 12.4)
4
output signal value (
MV
) in the range of 0÷100% (of
the impulse period for the P/SSR output or the full
range of variability for the mA/V output)
5
control status (the meaning is described in chapter
11.2)
6 the screen buttons are described in chapter 10, item d)

16
12. SETTING PARAMETERS AND OPERATIONS ON FILES (MAIN MENU)
All the configuration parameters and names of channels and groups, as well as measurement units of the
controller are stored in the non-volatile internal memory in two text files: AR654.cfg (numerical parameters) and
AR654.txt (names, units, groups, etc.) - changes can be implemented only using a computer in the ARSOFT-CFG-
WZ1 software via the USB port or the Ethernet, as well as in any text editor, e.g. Windows Noteboo ).
When the device is switched on for the first time, an error message may be shown in the display due to the lac of
a sensor or the fact that the sensor that is connected is not one that is factory-programmed. In such an event, the
proper sensor or analogue signal must be connected and the configuration must be programmed.
As a standard, the parameter configuration can be performed using one of the following three methods (do not
use them at the same time):
1
From the film eypad and a touch screen located on the front panel of the device:
- from the mode where the input measurements are displayed in the Main Menu ([SET] button). If Password
protection in the Access and other settings is on, the administrator’s password must be entered - the factory-set
value is 1111, see chapter 12.9.
Fig 12 Appearance of the password screen and the Main Menu
- use the [UP] or [DOWN] button, or the scroll bar to select an appropriate sub-menu or parameter to be
changed/viewed
- use the [SET] button or touch the selected item in the menu (also in order to edit the parameter)
- use the [UP], [DOWN], [LEFT], or [RIGHT] button, or the scroll bar to change the value of the edited parameter
- approve the changed value of the parameter by pressing the [SET] button or cancel it by pressing the [ESC] button
2
Use the USB or RS485 port, or the Ethernet and the ARSOFT-CFG-WZ1 software (
on
-
line configuration
) to:
- connect the recorder to a computer port and start and configure the ARSOFT-CFG-WZ1 application
- after the connection has been established, the current measured values and the internal time and date of the
controller are displayed; the [Tx/Rx] icon indicates the presence of transmission (lower status bar, chapter 11.1)
- setting and viewing of the device parameters is possible in the parameter configuration window
- new parameter values must be approved with the Approve changes button
- the software enables synchronization of the time and the date with the computer
- the current configuration can be saved in a file on the dis or set using values read from a file
- the recorder updates the configuration files and the displayed names after it is disconnected from the
computer's USB port
- online configuration via the USB port is possible only when the US operation mode parameter is set as
Available for computer (device), chapter 12.8.
NOTE:
!
- before disconnecting the device from a computer, press the Disconnect device button
- in the event of no response:
- in the Program options chec the configuration of the port and the MOD US Address of the device (in the
case of the RS485)

17
-
ma e sure that the serial port drivers have been installed correctly (chapter 8)
- disconnect for a few seconds and then reconnect the controller to the USB port
- restart the computer
3
From the configuration file created in the ARSOFT-CFG-WZ1 software or copied from another controller of the
same type to copy the configuration, off-line configuration:
- in ARSOFT-CFG-WZ1 set the required parameters (except for the RTC and the identification number ID)
- a current configuration can also be prepared by modifying the values read from the existing files
- save the created configuration in an AR654.cfg or AR654.txt file and save it in a USB memory
- in the Memory and file options of the controller, import the configuration from the USB memory, chapter 12.6.
- after the configuration has been completed, the memory can be disconnected from the USB soc et
As an alternative to the configuration methods described above, the user can prepare his own application using
the available serial interfaces and the MODBUS-RTU or MODBUS-TCP communication protocol.
In the event of differences between the indications and the actual value of the input signal, the zero and the
sensitivity of a sensor can be adjusted in the Measurement inputs configuration menu: the Offset calibration and
the Slope calibration (sensitivity) parameters, chapter 12.3.
In order to restore the factory settings, the Restore default file action can be used, which is described in chapter 12.6.
NOTE:
!
Do not shut down the power supply during the configuration performed using the eypad or on-line (via the
computer's USB port) because the changed parameter values are stored in the internal memory after the user exits
the Main Menu (by pressing the [ESC] button) or disconnects the device from the USB soc et.
12.1. MEANING OF ICONS IN THE MENU ITEMS
In order to improve the ease of use and configuration of the device, additional graphic descriptive elements were
added to the menu in the form of icons (pictograms).
The shared meaning of some icons described the type of menu item is the following:
12.2. CONFIGURATION OF MEASUREMENT CHANNELS OF THE DISPLAY
The controller has 4 measurement channels to present the measured values on the display. The measured values
can be directly the measurements from inputs 1÷4 or their mathematical formulas, such as difference, average,
sum, larger or smaller than, or ratio of the measurements. The measurement channels, together with the assigned
and switched on control and retransmission outputs, form control channels that are shown on the screen, for
which Quick configuration screens are also available (chapter 11.7) for the basic control/alarm parameters
(setpoint values SP, Start/Stop, etc.). If there are no related outputs, the message STOP, no output is displayed in
the control status and the message “------” is displayed in the field of the SP and MV values (if they are present in
the specific view, chapter 11). The method of assignment and configuration of the control and retransmission
outputs is described in detail in chapter 12.4.
Icon
Type of menu item (parameter)
parameter that can be modified using the buttons and the touch screen, saved in the internal memory
informative item, not modified directly using the buttons and the touch screen
file or dis action (operation) (chapter 12.6)

18
Table 12.2. Configuration parameters in the Display channel configuration menu for the selected channel (1÷4)
Parameter Range of variability of the parameter and description
Default
settings
Name, unit and group
edition of the name of the channel and the group (max. length 16 characters)
and of the measurement unit (4 characters) is possible on the computer (via the
USB port or the Ethernet and the ARSOFT-CFG-WZ1 software or by copying the
configuration - chapter 12.9). The format of a single section in the AR654.txt file is
the following: [Chan1] Name=Channel 1, Unit=°C, [Group1] Name=Group 1
Channel i (for
i=1÷4), °C,
Group j (for
j=1÷4)
Measured value to be
displayed
None
- the measurement channel is absent in the presentation and in the recording
Measurement
from the input
IN i (for
i=1÷4)
Measurement from the in
put
IN
1
Average (
IN
1+
IN
2+
IN
3)/3
Measurement from the input
IN
2
Average (
IN
1+
IN
2+
IN
3+
IN
4)
Measurement from the input IN3
The largest of the measurements
IN
1
and IN2
Measurement from the input IN4
The largest of the measurements
IN
3
and IN4
Diffe
rence between the
measurements IN1-IN2
The largest of the measurements
IN
1,
IN2, and IN3
Difference between the
measurements IN3-IN4
The largest of the measurements
IN
1,
IN2, IN3, and IN4
Difference between the
measurements IN1-IN2-IN3
The smallest o
f the measurements
IN1 and IN2
The difference IN1-IN2-IN3-IN4
The smallest of the measurements
IN3 and IN4
Sum of the measurements IN1+IN2
The smallest of the measurements
IN1, IN2, and IN3
Sum of the measurements
IN
3+
IN
4
The smallest of
IN
1,
IN
2,
I
N
3,
IN
4
Sum of the measurements
IN
1+
IN
2+
IN
3
(
IN
1+
IN
2)/2
-
(
IN
3+
IN
4)/2
Sum of
IN
1+
IN
2+
IN
3+
IN
4
The ratio of the measurements
IN
1/
IN
2
Average (
IN
1+
IN
2)/2
The ratio of the measurements
IN
3/
IN
4
Average of the measurements
(IN3+IN4)/2
Assigned and active
outputs
the numbers (
1
÷
4
or
None
) of the control/alarm outputs are displayed for
which the same type of control signal was assigned as the Measured value of
the current display channel, chapter 12.4.1, when None for the output is not
related or switched off (the parameter Control type = Off)
1÷4
ottom range for
graphics and SP
-
999.9
÷
9999.9°C
or
-
9999
÷
99999
units
(1)
– the lower value of the range of
variability for graphic elements (bar graph, counter, diagram) and for the
setpoint values SP of the related control outputs (1÷8)
-100.0 °C
Top range for graphics
and SP
-
999.9
÷
9999.9°C
or
-
9999
÷
99999
units
(1)
– the upper value of the range of
variability for graphic elements (bar graph, counter, diagram) and for the
setpoint values SP of the related control outputs (1÷8)
800.0 °C
Assignment of the
measurement group
channel elongs to all groups or only to one group in the range of 1 ÷ 4,
channel grouping is used in the measurement presentation modes
Group i (for
i=1÷4)
ackground colour
selection of the bac ground
colour
in the measurement presentation modes,
23 colours are available colour
Notes: (1) - applies to analogue inputs (mA, V, mV, Ω)

19
12.3. CONFIGURATION OF MEASUREMENT INPUTS
The controller has 4 universal measurement inputs for connecting temperature sensors and electrical signals.
Table 12.3. Configuration parameters in the Measurement inputs configuration menu for the selected input
(numbers 1÷4)
Parameter Range of variability of the parameter and description
Default
settings
Input type
Off
the measurement input is absent in the presentation and in
the recording
Pt100
thermoresistance sensor (RTD) Pt100 (-200 ÷ 850°C)
Pt100
Pt500
thermoresistance sensor (RTD) Pt500 (-200 ÷ 620°C)
Pt1000
thermoresistance sensor (RTD) Pt1000 (-200 ÷ 620°C)
Ni100
thermoresistance sensor (RTD) Ni100 (-50 ÷ 170°C)
J
(Fe-CuNi)
thermoelectric sensor (thermocouple) type J (-40 ÷ 800°C)
K
(NiCr-NiAl)
thermoelectric sensor (thermocouple) type K (-40 ÷ 1,200°C)
S
(PtRh 10-Pt) thermoelectric sensor (thermocouple) type S (-40 ÷ 1,600°C)
(PtRh30PtRh6)
thermoelectric sensor (thermocouple) type B (-300 ÷ 1,800°C)
R
(PtRh13-Pt)
thermoelectric sensor (thermocouple) type R (-40 ÷ 1,600°C)
T
(Cu-CuNi)
thermoelectric sensor (thermocouple) type T (-25 ÷ 350°C)
E
(NiCr-CuNi)
thermoelectric sensor (thermocouple) type E (-25 ÷ 850°C)
N
(NiCr i-Ni i)
thermoelectric sensor (thermocouple) type N (-35÷ 1,300°C)
4÷20 mA
current signal 4...20 mA
0÷20 mA
current signal 0...20 mA
0÷10 V
voltage signal 0...10 V
0÷60 mV
voltage signal 0...60 mV
0÷850
Ω
resistance signal 0...850 Ω
Line resistance
(1)
0.00
÷
50.00 Ω
total resistance of leads for 2-wire RTD sensors and 850 Ω 0.00 Ω
Thermocouple
cold tip
temperature
Auto
0.1÷ 60.0 °C
automatic or constant compensation of temperature of the
cold junction of thermocouples, Auto = 0.0°C Auto
Decimal dot
position/resolution
None
0, no point
(2)
or resolution 1 °C for temperature
Position 1
(0.1°C)
Position 1
0.0
(2)
or resolution 0.1 °C for temperature
Position 2
0.00
(2)
Position 3
0.000
(2)
Start of the input scale -199.9 ÷ 1999.9 °C or -9999 ÷ 19999 units (2) – indication for 0 mA, 4 mA, 0 V,
2 V, 0 mV, 0 Ω - start of the input scale -100.0 °C
End of the input scale -199.9 ÷ 1999.9 °C or -9999 ÷ 19999 units (2) – indication form 20 mA, 10 V,
60 mV, 850 Ω - end of the input scale 800.0 °C
Filtration
(3)
1
÷
10
digital filtration of measurements (response time)
1
Offset calibration zero offset:
-
50.0
÷
50.0 °C
or
-
500
÷
500
units
(2)
0.0 °C
Slope calibration
sensitivity (gain):
85.0
÷
115.0 %
100.0 %
Notes: (1) - in the case of 3-wire sensors, the Line resistance parameter must be equal to 0.00 Ω (automatic compensation)
(2) - applies to analogue inputs (mA, V, mV, Ω)
(3) - in the case of FiLtration=1 the response time is equal to 1 s, in the case of FiLtration = 10 it is equal to at
least 2.5 s. Higher degree of filtration means a "smoother" measured value and a longer response time, which
is recommended in the case turbulent measurements (e.g. water temperature in the boiler without an agitator)

20
12.4. CONTROL AND ALARMS OPTIONS
The programmable architecture of the controller enables using it in many fields and applications. Before the
operation of the device starts, it is necessary to set the parameters according to specific requirements. A detailed
description of the output operation configuration is given in the following subchapters. The company setting
(default configuration) are the following: outputs P1/SSR1÷ P4/SSR4 related to inputs IN1÷IN4, constantly
switched on control of the ON-OFF type with hysteresis, setpoint values P=P1, optional analogue outputs
(mA/V) 5÷8 switched off.
The Control and alarms options menu consists of sets of parameters grouped in the way shown in the table
below (12.4).
Table 12.4. Items in the Control and alarms options menu
Name of parameters set
Description
Output 1 (P1/SSR1)+
5 (mA/V), IN1
÷
Output 4 (P4/SSR4)+ 8 (mA/V), IN4
4 identical sets of configuration parameters for individual bi-state outputs
(P/SSR) and their related optional analogue outputs (mA/V) and binary inputs
(BIN); a detailed description is given in chapter 12.4.1
Set of
PID1
parameters
÷
Set of PID8 parameters
8 independent parameters sets for control of the PID type, the sets can be assi-
gned to different setpoint values; a detailed description is given in chapter 12.4.2
Program 1÷ Program 4
4 parameters
sets for 12
-
section program control, the programs can be freely
assigned to control outputs; a description is given in chapter 12.4.3
12.4.1. OUTPUT (P/SSR, mA/v) AND FUNCTION INPUT ( IN, F1) CONFIGURATION
Outputs can be assigned to measurement inputs and their mathematic formulas completely independently from
the measured values presented for the measurement channels. For outputs that are not related to any displayed
measurement channels, the Quick configuration screen (chapter 11.7) is not available and the operating
parameters of those outputs must be configured in the Control and alarms options menu. The device also
enables configuration of the output operation time. If the control/alarm status depends on the real time cloc , it is
necessary to program the Control time and Start and End of time control parameters, respectively, and to set the
State of control after power up parameter to the No change value. If it is necessary to start the control for a
strictly defined time (timer function), it is necessary to additionally use the functionalities offered by the program
control (chapter 12.4.3). Moreover, at any time, the user can chec the control status using the [F] button and the
[Start]/[Stop] and [F1] buttons available in the Quick configuration screen, as well as the optional function
inputs BIN. Detailed descriptions of the configuration parameters and problems related to the operation of the
control outputs can be found in the following table and in the successive subchapters.
Table 12.4.1. Configuration parameters in the Control and alarms options menu for the selected output (numbers 1÷4)
Parameter Range of variability of the parameter and description
Default
settings
Assignment of control
signal
None
- the output is switched off or can wor only in the manual mode
Measurement
from the input
IN i (for
i=1÷4)
menu items (values) the same as for the
Measured value to be displayed
parameter in the Display channels configuration menu (chapter 12.2)
Program
a
uxiliary output 1
÷
4
- output controlled from the program
control level (related to the program and the status of the output set by
the parameters Auxiliary output selection and Auxiliary output state for any
of the sections of Program 1÷4; a description is given in chapter 12.4.3)
Other manuals for AR654
1
Table of contents
Other APAR Controllers manuals
Popular Controllers manuals by other brands
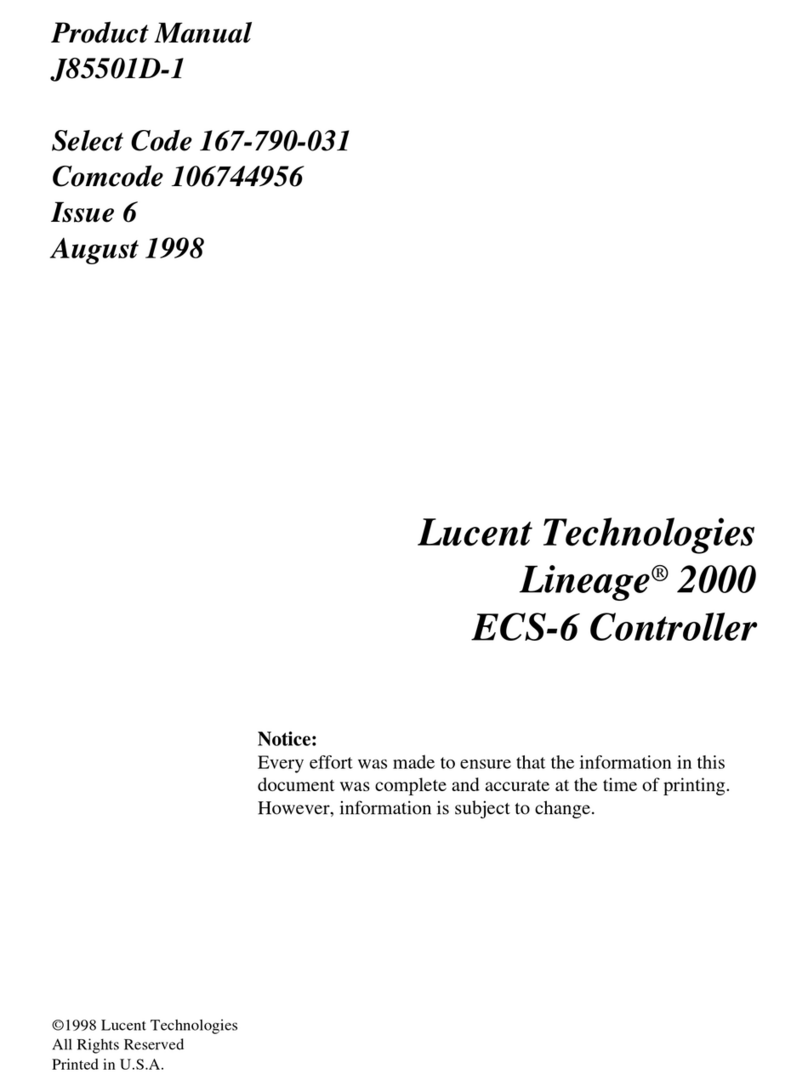
Lucent Technologies
Lucent Technologies LINEAGE 2000 ECS-6 product manual
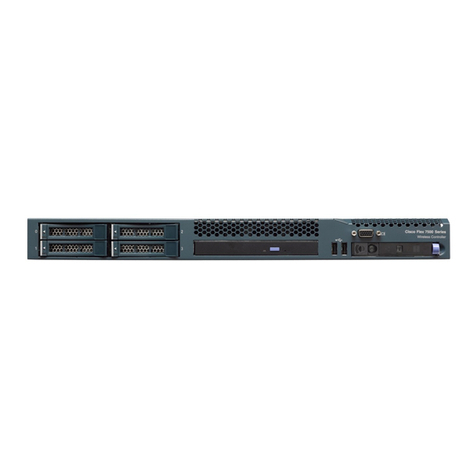
Cisco
Cisco Flex 7500 Series Deployment guide
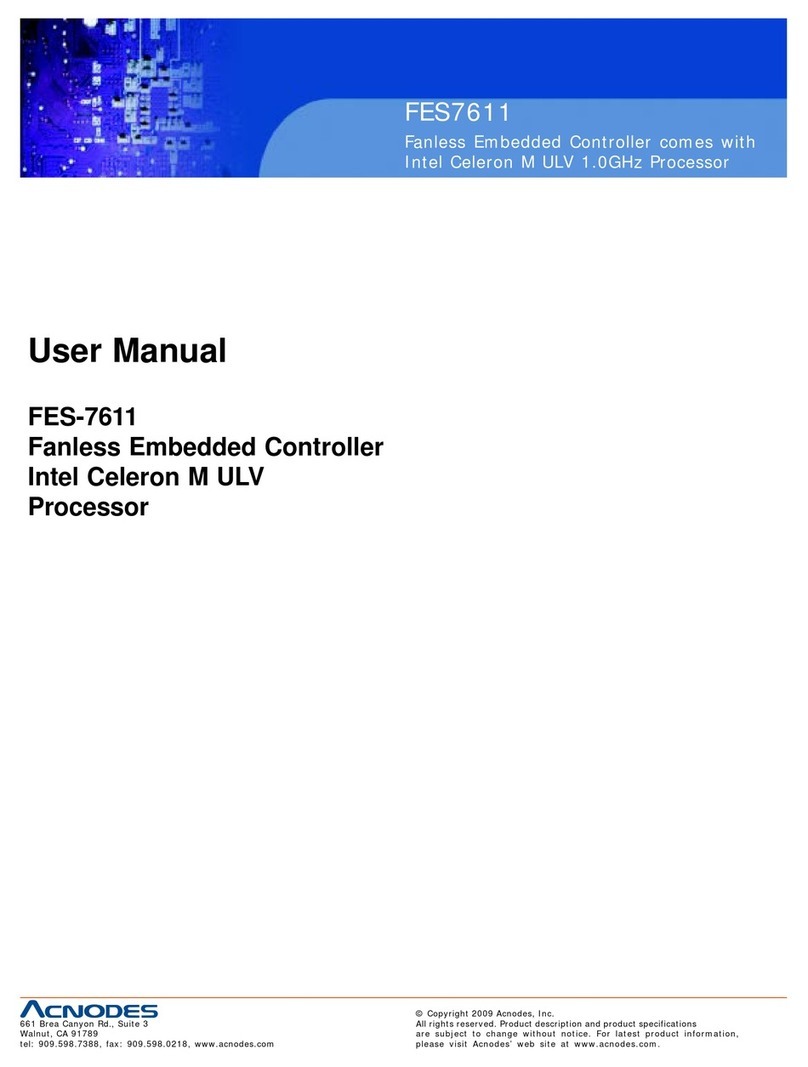
Acnodes
Acnodes FES7611 user manual

Samson
Samson 42-36 Mounting and operating instructions
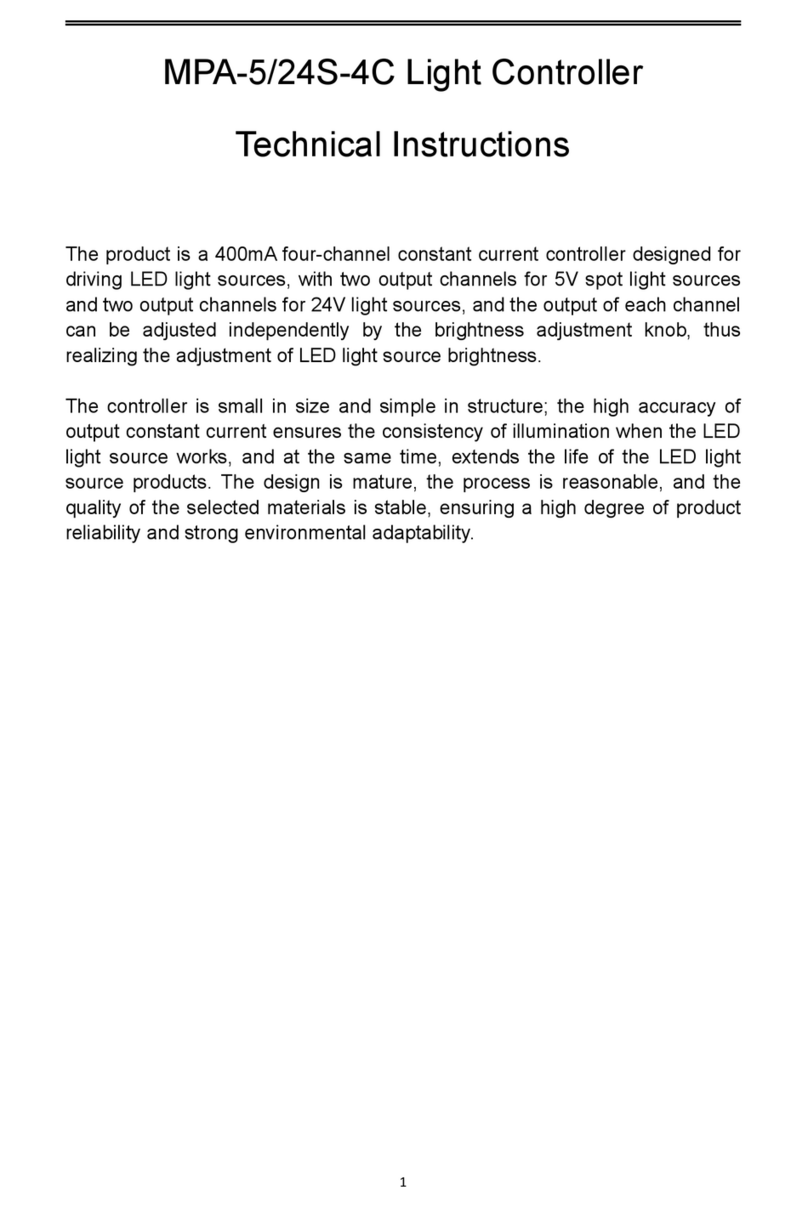
Mvotem Optics
Mvotem Optics MPA-5S-4C Technical instructions
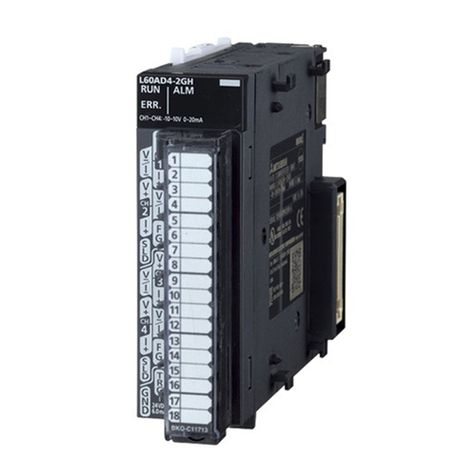
Mitsubishi Electric
Mitsubishi Electric MELSEC L series user manual