APE 50 User manual

800-248-8498
www.apevibro.com

Page Le Intenonally Blank

GENERAL INFORMATION
Quick Reference Guide
This Quick Reference Guide will assist
you in nding the informaon you’re
looking for.
A Table of Contents is included aer
the Foreword.
MAINTENANCE
REFERENCE / NOTES
TROUBLE SHOOTING
REPLACEMENT PARTS
Descripon:
50/75/80 BB AUGER

READ THIS MANUAL THOROUGHLY
BEFORE OPERATING
AND / OR WORKING ON THE
EQUIPMENT
1. Read and follow any safety instrucons in the
CATERPILLAR ENGINE OPERATOR’S MANUAL.
2. Only well-trained and experienced personnel should
aempt to operate or maintain this equipment.
3. NEVER adjust, lubricate or repair the unit when it is
in operaon or lied above ground level.
4. NEVER remove, paint over and/or cover warning
or safety labels. If labels become damaged or
unreadable, replace immediately.
5. All personnel should wear approved safety clothing,
including HARD HARTS, SAFETY SHOES, SAFETY
GLASSES and HEARING PROTECTION when near this
equipment.
6. Do NOT stand any closer to this equipment than
necessary when it is in operaon. Parts may
loosen and fall. Dirt and rocks may fall from
ighng. NEVER stand under operang or elevated
equipment.
7. When maintaining and/or repairing the equipment,
NEVER substute parts not supplied or approved in
wring by APE.
Do NOT weld or ame cut on this
equipment.
8. NEVER use or store ammable liquids on or near
the engine.
9. Insure that all liing equipment, including cranes,
wire rope, slings, hooks, shackles, etc., are properly
sized for the worst case loads ancipated during
operaons.
10. If there are any quesons about the weights,
specicaons or performance of the unit, contact
APE before handling and/or operang the
equipment.
11. If the equipment is to be used for anything other
than drilling plumb holes, contact APE before using
the unit.
12. Check wire rope clips for ghtness and wire ropes
for wear daily.
13. Insure that ground vibraons will not damage or
collapse adjacent structures or excavaons.
14. Remove all tools, parts and electrical cords before
starng the unit.
(These precauons must be followed at all mes to ensure personal and equipment safety.)
DANGER
WARNING
NOTICE
DANGER indicates a hazardous situaon which, if
not avoided, will result in death or serious injury.
WARNING indicates a hazardous situaon which, if
not avoided, could result in death or serious injury.
NOTICE is used to address pracces not related to
personal injury
NOTE
• NOTE indicates informaon that may help or
guide you in the operaon or service of the
equipment.
DISCLAIMER:
This unit was tested and ushed before leaving
our facility. In order to help provide years of
trouble free usage, please review the following
documentaon and make sure to clean and ush
the eld piping before connecng it to the power
unit.
Refer to schemac diagrams and the BOM (Bill of
Materials) for component part specicaons and
recommended spare parts.

When operang in an enclosed
area, exhaust fumes should be piped
outside.
Connued breathing of exhaust
fumes may prove FATAL.
15. When servicing baeries, do NOT smoke or use
an open ame in the vicinity. Baeries generate
explosive gas during charging. There must be
proper venlaon when charging baeries.
16. When lling the fuel tank, do NOT smoke or use an
open ame in the vicinity.
17. If abnormal equipment operaon is observed,
disconnue use immediately and correct the
problem.
18. Do NOT leave the equipment control pendant (radio
control) unaended.
19. Store oily rags in approved containers and away
from the engine exhaust system.
20. Make sure that the Auger rotaon switch is in
NEUTRAL before starng the Power Unit engine.
21. Do NOT adjust and/or set the hydraulic pressures
higher or lower than those specied in this Manual.
22. NEVER operate this equipment with hydraulic hoses
that are damaged or ‘kinked’. Replace damaged
hoses immediately.
23. Do NOT li and/or support hydraulic hoses with
wire rope slings.
24. NEVER aempt to connect Quick Disconnects (QDs)
when the Power Unit is running.
25. Do NOT pull on and/or aempt to move equipment
with the hydraulic hoses.
26. Do NOT aempt to locate hydraulic leaks with your
hands. High-pressure leaks can penetrate skin
and cause severe damage, blood poisoning and/or
infecon.
27. Do NOT aempt to repair leaks while the
equipment is in operaon.
28. Do NOT aempt to ghten and/or loosen ngs
and/or hoses when the machine is in operaon.
29. Power Unit must always be placed on level, stable
ground.
30. Do NOT remove Power Unit heat shields. Do NOT
aempt to use the Power Unit without heat shields.
Severe res may result.
A properly maintained re
exnguisher, suitable for oil res,
MUST be kept in the
immediate vicinity of equipment
operaons.
31. When moving and/or transporng this equipment,
insure that the vehicle or vessel is of sucient
capacity to handle the load. Make sure that the
equipment is properly ed down.
32. When moving and/or transporng this equipment,
be sure that the QD Dust Caps are ght and that
the cap safety cables are in place. Be sure that all
equipment parts are ght and/or properly secured
before shipment. Unsecured parts may vibrate
loose and fall during transport causing injury and/or
property damage.
33. Rounded and/or damaged bolt heads and/or
nuts should be replaced so that proper torque
values may be obtained. Proper torque values are
necessary to prevent parts on this equipment, leads
and/or crane booms from loosening and/or falling.
(Refer to the torque chart in this manual for the
proper values.)
34. KEEP HANDS AWAY FROM ROTATING FLIGHTING,
AUGER SHAFT AND/OR ROTARY JOINT.
35. KEEP HANDS, FEET AND TOOLS WELL CLEAR OF THE
FLIGHTING GUIDES.
36. Do NOT allow clothing, hoses, ropes, etc., to
become entangled in, or wrap around, rotang
ighng, Auger sha and/or rotary joint.
37. When operang in a closed area, pipe exhaust
fumes outside. (Warning: Breathing exhaust fumes
can cause serious injury or even death.)
38. Make sure the control pendant is in the “LOCAL”
posion before starng the unit.
39. NEVER stand under hammer at any me and keep
you eyes on the hammer when it is in operaon.
40. When loading or unloading the power unit using a
forkli, the forks must be placed under the enre
depth of the unit.
(These precauons must be followed at all mes to ensure personal and equipment safety.)

WARRANTY INFORMATION
American Piledriving Equipment, Inc. (APE)
warranes new products sold by it to be free from
defects in material or workmanship for a period of
two (2) years aer the date of delivery to the rst
user and subject to the following condions:
• APE’s obligaon and liability under
this WARRANTY is expressly limited to
repairing or replacing, at APE’s opon,
any parts which appear to APE upon
inspecon to have been defecve in
material or workmanship. Such parts
shall be provided at no cost to the user, at
the business establishment of APE or the
authorized APE distributor of the product
during regular working hours.
• This WARRANTY shall not apply to
component parts or accessories of
products not manufactured by APE,
and which carry the warranty of the
manufacturer thereof, or to normal
maintenance (such as engine tune-up)
or normal maintenance parts (such as
lters).
• Replacement or repair parts installed in
the product covered by this WARRANTY
are warranted only for the remainder of
the warranty as if such parts were original
components of said product.
• APE makes no other warranty, expressed
or implied, and makes no warranty
of merchantability of tness for any
parcular purpose.
• APE’s obligaons under this WARRANTY
shall not include any transportaon
charges, costs of installaon, duty, taxes
or any other charges whosoever, or any
liability for direct, indirect, incidental or
consequenal damage or delay.
• If requested by APE, products or parts for
which a warranty claim is made are to be
returned, transportaon prepaid, to APE.
ANY IMPROPER USE, INCLUDING OPERATION
AFTER DISCOVERY OF DEFECTIVE OR WORN
PARTS, OPERATION BEYOND RATED CAPACITY,
SUBSTITUTION OF ANY PARTS WHATSOEVER,
USE OF PARTS NOT APPROVED BY APE OR ANY
ALTERATION OR REPAIR BY OTHERS IN SUCH A
MANNER AS, IN APE’S JUDGMENT, AFFECTS THE
PRODUCT MATERIALLY AND ADVERSELY, SHALL
VOID THIS WARRANTY.
ANY TYPE OF WELDING ON APE’S EQUIPMENT
WILL VOID THE WARRANTY UNLESS AUTHORIZED
IN WRITING BY APE
NO EMPLOYEE AUTHORIZED TO CHANGE THIS
WARRANT IN ANY WAY OR GRANT ANY OTHER
WARRANTY UNLESS SUCH CHANGE IS MADE IN
WRITING AND SIGNED BY AN OFFICER OF APE,
INC.
OIL MUST MEET ISO CLEANLINESS CODE 17/15/11.
OIL THAT DOES NOT MEET CLEANLINESS CODE
WILL VOID THE WARRANTY

FOREWORD
DISCLAIMER:
This unit was tested and ushed before leaving our facility. In order to help provide years of trouble-free
usage, please review the following documentaon and make sure to clean and ush the eld piping before
connecng it to the power unit.
Refer to schemac diagrams and the BOM (Bill of Materials) for component part specicaons and
recommended spare parts.
When calling APE, always have the equipment serial number on hand in order to obtain quicker service.
This manual covers the APE 50BB Auger installaon, maintenance and use.
This manual provides the necessary informaon to operate and maintain APE equipment. The listed
procedures are to be performed by qualied personnel who have an understanding of the equipment and who
follow all safety precauons.
All informaon given in this manual is current and valid according to the informaon available at the me
of publicaon. American Piledriving Equipment, Inc. reserves the rights to implement changes without prior
noce.
Using this manual:
• Refer to the Table of Contents for the page locaon of applicable secons.
• All weights and measurements are in English and Metric units.
• Any revisions to this manual will appear on the Revision Record page at the back of this manual.
The revisions themselves will be aached to the back of the manual and entled ADDENDA with
references back to the page in queson in the original manual.
• Please visit www.apevibro.com for product data sheets and manual.

TABLE OF CONTENTS
GENERAL INFORMATION ........................................ 1
Safety / Warning Labels .............................. 1
Daily Checklist ............................................ 2
Liing the Auger Drill ................................ 3
Connecng / Filling the Hydraulic Lines ..... 4
Commissioning Procedure ......................... 5
Flushing the Hydraulic System ................... 5
Air Bleed Procedure ................................... 5
Break-In Period ........................................... 6
Fluid Cleanliness ......................................... 6
Operang Pressures ................................... 7
Operang Temperatures ............................ 7
Valves ......................................................... 9
TROUBLESHOOTING ............................................. 10
Hydraulic Schemac ................................. 10
MAINTENANCE ..................................................... 11
Maintenance Chart .................................. 11
Storage ..................................................... 12
Roune Maintenance ............................... 13
REPLACEMENT PARTS ........................................... 14
Complete Auger ....................................... 14
Liing Bale ................................................ 16
Grout Swivel ............................................. 17
18” Guide ................................................. 19
Drive Manifold ......................................... 20
REFERENCE / NOTES ............................................. 21

SPECIFICATIONS
50 BB
DIMENSIONS
Overall Length 37 in (94 cm)
Overall Width 52 in (132 cm)
Overall Height 88 in (224 cm)
Low Speed High Torque
Torque 9,688 -lbs per 1000 PSI 1,339 kgm per 69 bar
Max Pressure 5,800 psi 400 bar
Rotaon Speed 36 rpm
Max Flow 120 gpm @ 3.3 gal / rev 454 lpm @ 12.6 lit / rev
Max Horse Power 406 hp 303 kW
High Speed Low Torque
Torque 4,844 -lbs per 1000 PSI 670 kgm per 69 bar
Max Pressure 5,800 PSI 399.6 bar
Rotaon Speed 72 rpm
Max Flow 120 gpm @ 1.7 gal / rev 454 lpm @ 12.6 lit / rev
Max Horse Power 320 hp 239 kW
Misc Specicaons
Crowd Force 150,000 lbs 68,039 kg
Suspended Weight 4,530 lbs 2,055 kg
ID of Output Sha 3 in 76.2 mm
ID of Rotary Joint 3 in 76.2 mm
Adapters 3 inch / 4 inch

SPECIFICATIONS
75 BB
DIMENSIONS
Overall Length 37 in (94 cm)
Overall Width 52 in (132 cm)
Overall Height 88 in (224 cm)
Low Speed High Torque
Torque 12,150 -lbs per 1000 PSI 1,680 kgm per 69 bar
Max Pressure 5,800 psi 400 bar
Rotaon Speed 30 rpm
Max Flow 120 gpm @ 3.3 gal / rev 454 lpm @ 15.8 lit / rev
Max Horse Power 508 hp 379 kW
High Speed Low Torque
Torque 6,075 -lbs per 1000 PSI 840 kgm per 69 bar
Max Pressure 5,800 PSI 400 bar
Rotaon Speed 60 rpm
Max Flow 120 gpm @ 1.7 gal / rev 454 lpm @ 7.9 lit / rev
Max Horse Power 406 hp 303 kW
Misc Specicaons
Crowd Force 150,000 lbs 68,039 kg
Suspended Weight 4,630 lbs 2,100 kg
ID of Output Sha 3 in 76.2 mm
ID of Rotary Joint 3 in 76.2 mm
Adapters 3 inch / 4 inch

SPECIFICATIONS
80 BB
DIMENSIONS
Overall Length 37 in (94 cm)
Overall Width 52 in (132 cm)
Overall Height 88 in (224 cm)
Low Speed High Torque
Torque 14,572 -lbs per 1000 PSI 2,015 kgm per 69 bar
Max Pressure 5,075 psi 350 bar
Rotaon Speed 30 rpm
Max Flow 125 gpm @ 5 gal / rev 473 lpm @ 18.9 lit / rev
Max Horse Power 401 hp 300 kW
High Speed Low Torque
Torque 7,266 -lbs per 1000 PSI 1,004.56 kgm per 69 bar
Max Pressure 5,075 PSI 350 bar
Rotaon Speed 61 rpm
Max Flow 125 gpm @ 2.5 gal / rev 473 lpm @ 9.5 lit / rev
Max Horse Power 328 hp 245 kW
Misc Specicaons
Crowd Force 150,000 lbs 68,039 kg
Suspended Weight 4,630 lbs 2,100 kg
ID of Output Sha 3 in 76.2 mm
ID of Rotary Joint 3 in 76.2 mm
Adapters 3 inch / 4 inch

Page 1
GENERAL INFORMATION
Safety / Warning Labels
This informaon is important when
contacng APE for replacement parts or
other informaon.
* Model
* Serial No.

Page 2
GENERAL INFORMATION
Daily Checklist
Check the enre unit prior to and during set-up each day or at the beginning of each shi
Prior to starng the unit or at the beginning of each shi, check the following:
• Visually inspect all bolts, nuts and screws.
• Grease Sheave pin.
• Grease Grout Swivel
• Visually inspect all hydraulic ngs for leaks. If a leak is found or suspected, shutdown the power
unit. If a ng appears to be damaged, replace with a new ng.
It is absolutely imperave that no dirt or other impuries be permied to contaminate
the hydraulic uid. Any contaminaon will drascally shorten the life of the high-pressure
hydraulic system.
Vibraon loosens bolts. Check them thoroughly.

Page 3
GENERAL INFORMATION
Liing the Auger Drill
The following instrucons apply to all procedures
associated with the motor. Read these instrucons
carefully and follow them closely.
• Use necessary Personal Protecve
Equipment (PPE) when working with the
motor.
• Support the motor properly. Make
sure that the motor cannot fall over or
accidentally turn around.
• Use only appropriate equipment and
aachments for liing and transferring
the motor.
• Always use the liing equipment properly
and check the load bearing capacity.
• Prevent unintended use of the motor
during installaon and maintenance
procedures by prevenng the
pressurizaon of the hydraulic lines.
• The operang temperature of the motor
may be over 60° C (140° F) which is hot
enough to cause severe burns.
Beware of hot hydraulic uid when
disconnecng the hydraulic connecons

Page 4
GENERAL INFORMATION
Connecng the hoses is one of the most crical
aspects of commissioning an APE driver. Take
extreme care to keep these connecons absolutely
clean. This procedure is one of the most common
ways for foreign parcles to be introduced into a
hydraulic system.
New hydraulic uid is NOT clean oil!
Oil must meet ISO cleanliness code
17/15/11
• Connect the hose bundle.
Make sure all connecons are
properly ghtened
• Fill the motor case with clean
hydraulic uid
Connecng / Filling the Hydraulic Lines
CAUTION
While lling the hydraulic lines, the drill
motor sha will rotate.
Please do the following:
• Set the engine at idle
• Run at idle for about 10
minutes to ll the lines
• Energize ‘Drive Fwd’ - The
motor sha will rotate slowly
and push any remaining air in
the lines back to the reservoir
Pressurizing the system while there is air
entrained in the uid may cause damage
to
the components.
Let the system run at idle for an
addional 10 minutes to allow the air
to rise into the airspace of the hydraulic
reservoir.

Page 5
GENERAL INFORMATION
Commissioning Procedure
Do not start the motor if the air bleeding
procedure has not been carried out.
Stressing an unused motor with full power
may cause premature wear or failure.
Ensure that the following steps are met before
starng a new or rebuilt auger drill:
• The hydraulic circuit of the motor is
ushed
• The motor is installed appropriately
• An air bleeding procedure is carried out
• The reservoir of the hydraulic system is
full
During the inial stages of starng a new or rebuilt
helical driver, please consider the following:
• Do NOT run the motor immediately with
full power
• Increase the load and speed of rotaon
gradually
• Observe the motor and the hydraulic
system for external leaks or abnormal
noises during the commissioning
procedure
• Start the motor break-in period
Flushing the Hydraulic System
Prior to connecng the motor as part of the
hydraulic system, the hydraulic circuit of the motor
must always be ushed. This is done by circulang
the hydraulic uid through a lter installed in place
of the motor.
Flushing the hydraulic system should be performed
aer every service and/or repair.
The helical pile driver is usually shipped with the
drive motor hoses full of hydraulic oil and the unit
may be used immediately.
If the drive hoses have been removed from the
driver motor they will need to be lled before full
speed operaon.
The air bleeding procedure is carried out to
completely ll the housing of the motor with
hydraulic uid. Air is removed from the housing
with air bleeding screws as follows:
• Connect port ‘C2’ to a drain line and feed
hydraulic uid into the motor via port ‘C1’
throughout the air bleeding procedure.
• Locate the topmost air bleed screw of the
housing
• Unscrew the air bleeding screw by half
a turn and let the air escape from the
housing
• Close the screw when only hydraulic uid
is pouring through it
• Tighten the screw to a torque of 28 lbf/
(39 +/- 3 Nm)
Air Bleed Procedure

Page 6
GENERAL INFORMATION
New motors require a break in procedure.
The motor achieves its nal properes during
the rst hours of use. All new and recondioned
motors should go through an inial break-in period.
Items to consider during this period:
• Break-in should last for, at least, the rst 8
hours of use.
• The power output should remain under 50% of
the maximum power capacity of the motor.
• To limit the power output, constrain the
working pressure, speed of rotaon or both.
• The working pressure should be curbed so that
pressure peaks which last over 2 seconds (2s)
remain under 75% of the allowed pressure.
During this break-in period, the moving
parts of the motor wear against each
other. This means the wear of the parts
sets to a stable state for the enre service
life of the motor.
Break-In Period
It is imperave that the hydraulic uid is
kept clean to a minimum
ISO Code 17/15/11
New hydraulic uid is NOT clean oil
(See aached document ‘Understanding ISO
Codes)
(See Warranty document regarding uid
cleanliness)
Bulk oil does not typically meet the cleanliness
standards required by APE equipment.
Fluid Cleanliness

Page 7
GENERAL INFORMATION
Operang TemperaturesOperang Pressures
The Operang Temperature references the internal
temperature of the motor.
Take into consideraon the following requirements:
• 70°C (158°F) – Avoid going over this Operang
Temperature for improved service life
• 85°C (185°F) – Highest permissible intermient
Operang Temperature
• -35°C (-31°F) – Lowest permissible Operang
Temperature
• 60°C (140°F) – Temperature dierence between
the motor and the hydraulic uid
The Operang Temperature may be measured from
the hydraulic uid returning from the motor. Take
into account the temperature of the hydraulic uid
returning from the case drain line.
Charge Pressure
The charge pressure is used to ensure that the
pistons of the motor stay constantly engaged to the
cam ring. Depending upon the operaon funcon,
the charge pressure is required either in the feed
or return line (working line ports A or B).
The recommended charge pressure is 200PSI
or 13.8 bar higher than the case pressure. The
actual required charge pressure depends upon the
viscosity and ow rate of the hydraulic uid.
The required charge pressure in the return line
(back pressure) is only 73psi (5 bar) higher than
the case pressure if the motor is NOT switched to
paral displacement or short circuit connecon.
Charge pressure that is too low may cause the
pistons to disengage from the cam ring causing
A claering noise when the pistons re-engage.
This condion will cause damage to the driver
motor.
Constant use with a charge pressure that is too
low may cause premature wear or failure of the
motor.
Case Drain
The case drain line is the return line for the driver
housing cavity. Case pressure is induced by the
pressure drop in the case drain line. The case drain
line is connected to port ‘C2’ on the motor and
‘DR2’ port on the drive manifold.
It is imperave that the case drain has an
unobstructed route back to the hydraulic
reservoir. If a case drain lter is required, consult
the factory for proper sizing.

Page 8
GENERAL INFORMATION
The APE Auger Drill has a 2-speed direct
drive Radial Piston Motor.
Full Displacement Mode:
• All of the pistons are engaged to deliver
maximum torque
• Full displacement mode is limited to ½
maximum output speed
Half Displacement Mode:
• ½ of the pistons are engaged to deliver
double speed
• Half displacement mode is limited to ½
maximum output torque
Changing displacement while drilling is permissible.
To ‘shi on the y’ it is necessary to hold the
displacement shi spool in posion with a
minimum of 650PSI.
A 2-posion, 4-way, Pilot Valve is required to select
displacement.
Full
Displacement
Acvate
Port: Y2
Drain
Port: Y1
Half
Displacement
Acvate Port:
Y1
Drain
Port: Y2
NOTE: In some applicaons the maximum
pressure seng for half displacement mode
must be lowered due to through-put horsepower
limitaons internal to the motor. Refer to the
data sheet of the specic motor installed.
When the motor is transioning from full
displacement to half displacement, the load
induced pressure will double.
When the motor is transioning from half
displacement to full displacement, the ow
requirement will double.
AVOID SHIFTING FROM HALF TO FULL WHEN
THE MOTOR IS TURNING IN
EXCESS OF ½ OF THE MAXIMUM SPEED.

Page 9
GENERAL INFORMATION
Valves
The drill has an integral valve package designed
to protect the motor from damage. (Refer to the
hydraulic schemac Figure 7 / Page 19 for details)
• Pressure lters clean the hydraulic uid
going to the drill motor and manifold in
the forward and reverse direcons.
• Vented Relief Valves - VR1 and VR2: Limit
the maximum pressure that the drill
motor is exposed to. When the load
induced pressure exceeds the seng
of the vented relief, the valve will open
creang a short circuit around the drill
motor.
• The vented Relief Valve may be set
to a lower seng by energizing the
Direconal Valve (DV1) which connects
the pilot secon of VR1 and VR2 to the
secondary Pilot Relief Valve (RV1).
• Some motors are limited in their capacity
to carry ‘through-out horsepower’
when they are in the high speed/half
displacement mode.
• Check Valves - CV2 and CV3: These
isolate the pilot secons of VR1 and VR2
from each other.
• Counterbalance Valves - CB1 and CB2:
These are in-line with the drill motor and
set at 400PSI. Their primary funcon is
to maintain ‘charge pressure’ to the drill
motor.
• Hot Oil Shule Valve - HOS1: This will
shi when the drill is acvated to direct
oil ow from the low-pressure side to
ush the case of the drill motor.
• Flow Control Valve - FC2: This regulates
the amount of case ushing ow.
• Check Valves - CV4 and CV5: These
connect the high-pressure side when
the drill is acvated. This will supply the
Accumulator with pressurized hydraulic
uid to be stored for addional charge
pressure.
• Flow Control Valve - FC1: This limits
the rate of ow being diverted to the
Accumulator.
• Pressure Reducing Valve – PRV: This is
a normally open valve that will close
when the pressure being stored in the
Accumulator exceeds the PRV seng. If
the pressure in either motor line drops
below this seng, the PRV will open
thus allowing the uid stored in the
Accumulator to keep the motor ports
pressurized.
• Check Valves - CV6 and CV7: These
create direct ow from the Accumulator
circuit to the low-pressure side of the
drill motor.
• Pop O Valve - PO1: This is intended to
protect the drill motor case from over-
pressurizaon.
Other manuals for 50
2
This manual suits for next models
2
Table of contents
Other APE Tools manuals
Popular Tools manuals by other brands

Triton
Triton Maxi ETA300 Operating and safety instructions
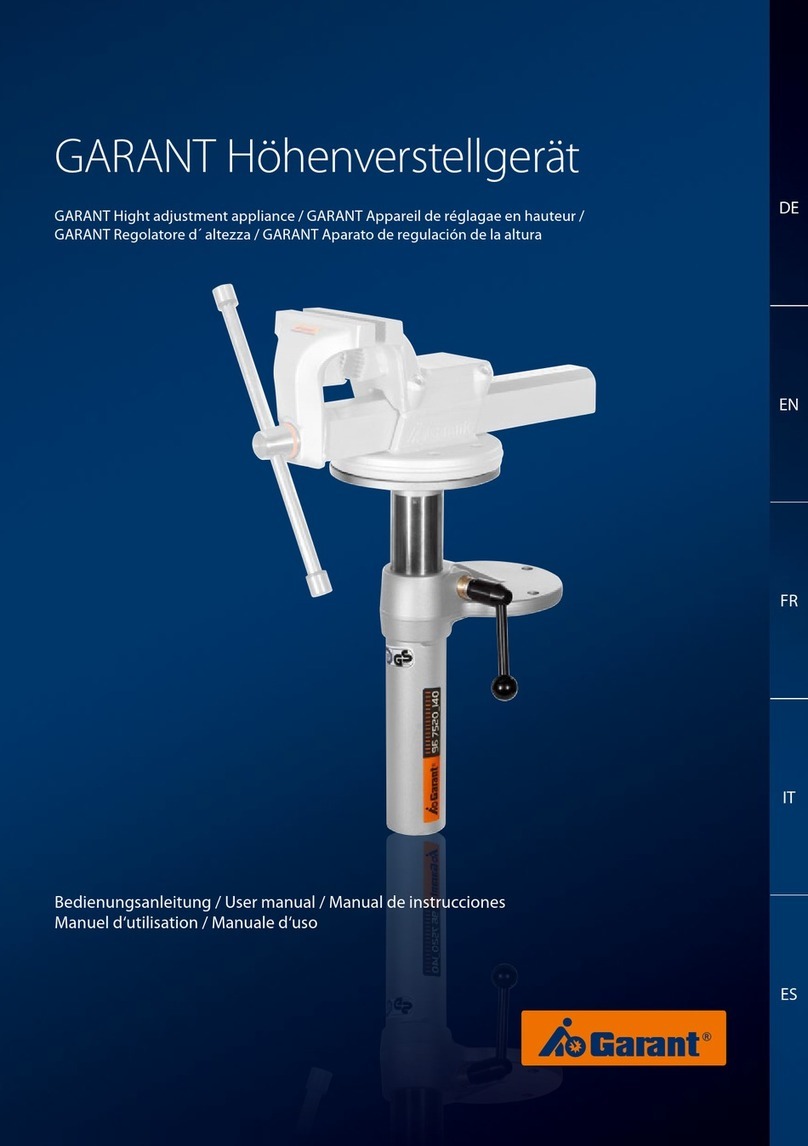
GARANT
GARANT 967520 user manual

Leister
Leister GHIBLI AW Repair instructions
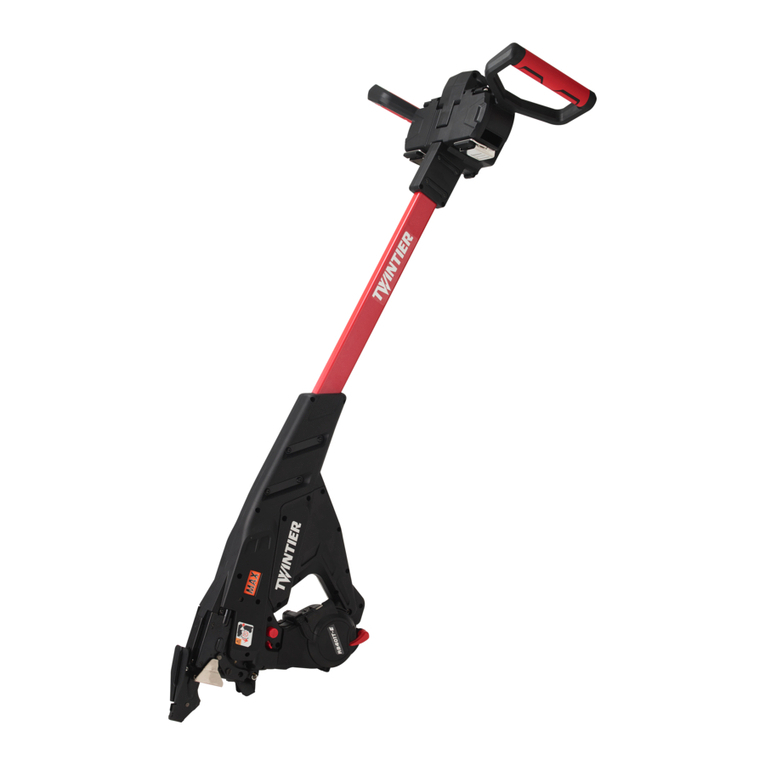
Max
Max ReBar Tier Twintier RB401T-E Instruction manual and safety instructions

Nitto Kohki
Nitto Kohki Super Hand ASH-900 instruction manual
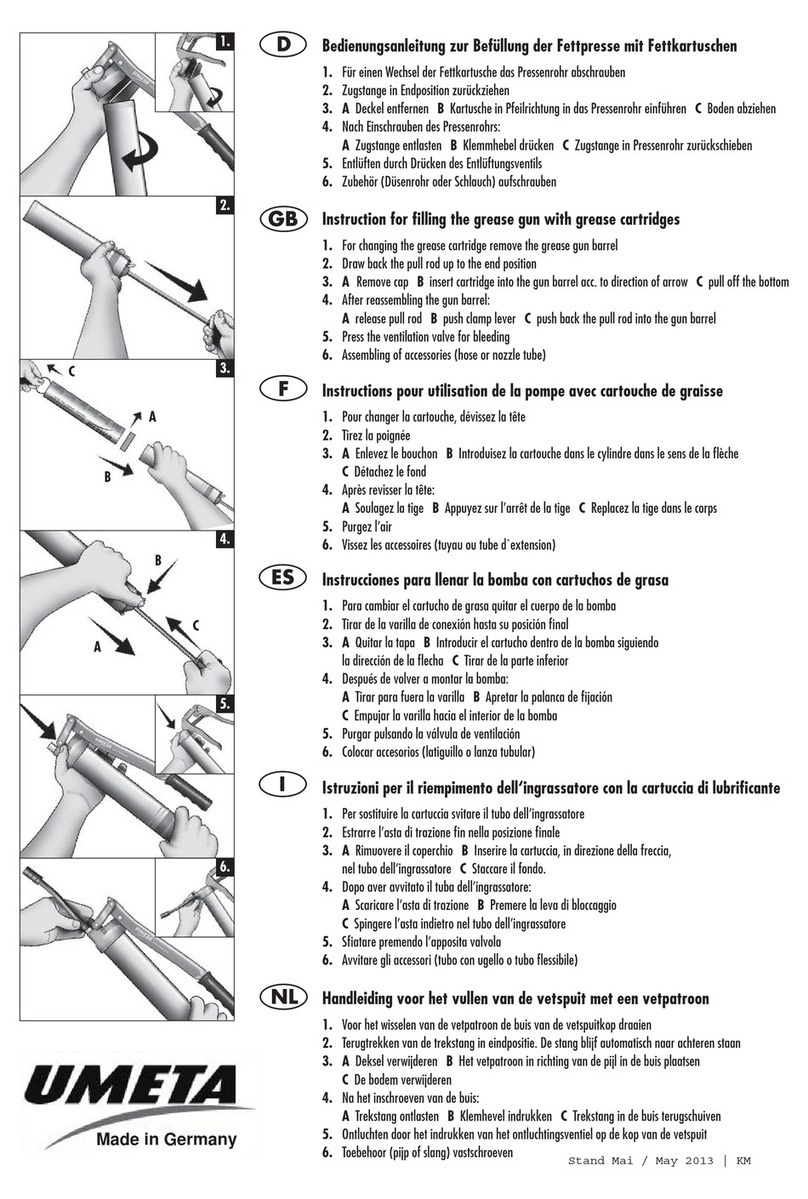
UMETA
UMETA 85/PK Silver instructions