ARAG Orion 2 VisualFlow 46212A Series Quick start guide

46212AXXXXX
46222AXXXXX
ELECTROMAGNETIC FLOWMETER
INSTALLATION, USE AND MAINTENANCE

LEGEND SYMBOLS
=Generic danger
=Warning
CONTENTS
LEGEND SYMBOLS ................................................................................................................................................................................ 2
1 PRODUCT DESCRIPTION....................................................................................................................................................................... 3
1.1 Intended use................................................................................................................................................................................... 3
2 INSTALLATION ........................................................................................................................................................................................ 3
2.1 Dimensions (mm)............................................................................................................................................................................ 3
2.2 Assembly ........................................................................................................................................................................................ 4
2.3 Electric connections........................................................................................................................................................................ 5
2.4 Hydraulic connections..................................................................................................................................................................... 5
3 PRELIMINARY SETUP FOR USE ........................................................................................................................................................... 6
3.1 Access to "COST" setup menu....................................................................................................................................................... 6
3.2 Setting the flow-meter constant....................................................................................................................................................... 6
3.3 Notes on programming ................................................................................................................................................................... 6
3.4 "OPT" Advanced menu ................................................................................................................................................................... 7
3.5 "MODE" Operation mode................................................................................................................................................................ 7
3.6 "UNIT" Unit of measure .................................................................................................................................................................. 7
3.7 "VAL" Valve operation time ............................................................................................................................................................. 7
4 USE .......................................................................................................................................................................................................... 8
4.1 Mode 0 - Mode 2 Use ..................................................................................................................................................................... 8
4.2 Mode 1 Operation........................................................................................................................................................................... 9
5 MAINTENANCE ..................................................................................................................................................................................... 10
5.1 Troubleshooting ............................................................................................................................................................................ 10
5.2 Technical data................................................................................................................................................................................11
6 GUARANTEE TERMS ............................................................................................................................................................................ 12
7 DISPOSAL AT THE END OF SERVICE ................................................................................................................................................. 12
8 CONFORMITY DECLARATION............................................................................................................................................................. 12
This manual is an integral part of the equipment to which it refers and must accompany the equipment in case of sale or
change of ownership. Keep it for future reference; ARAG reserves the right to modify the specications and instructions
regarding the product at any time and without prior notice.

3
1 PRODUCT DESCRIPTION
The Orion 2 Visual Flow electromagnetic owmeter is a device that enables measurement of the quantity of liquid passing through it.
Using a principle of electromagnetic measurement (there are no moving mechanical parts inside it), the owmeter outputs a signal to the computer
proportional to the liquid ow that goes through it; Orion 2 Visual Flow displays the owrate calculated according to the data received from the owmeter
and the value of the owmeter constant previously set.
Furthermore Orion 2 Visual Flow can be used as a lling owmeter; this function enables the setting of the quantity of liquid with which the tank is to
be lled during loading and by using the Pump Stop Kit (optional) enables loading to be stopped when the set value has been reached.
1.1 Intended use
This device is designed to work on agricultural machinery for crop spraying applications.
The machine is designed and built in compliance with EN ISO 14982 standard (Electromagnetic compatibility - Forestry and
farming machines), harmonized with 2014/30/UE Directive.
The owmeter must not be used to measure the passage of hydrocarbons, ammable, explosive or toxic liquids. The owmeter is
not suitable for contact with liquids for human consumption. Use for sales transactions is not allowed.
2 INSTALLATION
Install the owmeter at least 20 cm from the elements
that could cause turbulence inside the tubes (valves,
bends, constrictions, etc.).
The owmeter can be installed in a horizontal or vertical
position.
CAUTION:
For proper sealing of the owmeter, use
ARAG assembly kit ONLY (Ref. ARAG
General catalogue - Accessories for series
863/873/463/473 modular valves).
ARAG is not liable for damage to the system,
persons, animals or things caused by the use
of material other than specied.
2.1 Dimensions (mm)
CODE DN F L A A1 HH1
46212AG1313 4 G 3/4 185
103 117 96 169
46212AG3333 4 G 3/4 184
46212A01313 5 G 3/4 185
46212A03333 5 G 3/4 184
46212A11313 7 G 3/4 185
46212A13333 7 G 3/4 184
46212A21313 10 G 3/4 185
46212A23333 10 G 3/4 184
46212A31414 14 G 1 185
46212A33434 14 G 1 184
46212A41414 18,5 G 1 185
46212A43434 18,5 G 1 184
46212A41515 18,5 G 1 1/4 189
46222A51616 28 G 1 1/2 199
46222A61616 28 G 1 1/2 199
46222A61717 28 G 2 234
46222A71717 28 G 2 234
Fi g . 1
Fig. 2
Tab. 1

4
2.2 Assembly
To ensure trouble-free operation, comply with the indicated installation layout (Fig. 3a and Fig. 3b).
The connector must NEVER be positioned upwards.
- Comply with the correct uid inlet-outlet direction, as indicated by the arrow printed on the owmeter body (Fig. 4).
Use inlet and outlet pipes of the same diameter as the internal passages of the owmeter; for any reference, see table 4(Chap. 5 - Technical
data).
HORIZONTAL ASSEMBLY
VERTICAL ASSEMBLY
Fig. 3a
Fig. 3b
Fig. 4

5
2.3 Electric connections
The Orion 2Visual Flow owmeter has been designed to be connected to ARAG devices (computers, screens, displays) but can also be connected
to equipment made by other manufacturers as long as they are designed for owmeters of this typology.
When used as a lling owmeter, the owmeter should ONLY be connected to ARAG appliances.
ARAG is not liable for damage to the system, persons, animals or things caused by incorrect or inadequate installation of
the owmeter. In the event of damage to the owmeter, caused by incorrect or unsuitable assembly, any form of guarantee is
automatically rendered null and void.
Color Position Connection
Black 1GND
Red 2+12 VDC
Green 3Signal
(square wave)
Yellow 4Pump check
2.4 Hydraulic connections
For connection to the system, use appropriate ttings (Ref. ARAG General catalogue).
Avoid bends and constrictions before connections and on tubes.
Regarding connections, use tubes and ttings properly sized for the operating pressure of the system.
The tightening of hose tails should be made with special metal clamps ensuring perfect sealing even at high pressures.
The connection by means of threaded ttings should be done taking operating pressure into account.
CAUTION: For the implementation on already operating systems it is necessary to follow all safety rules described herein.
System assembly and start-up must be carried out by expert personnel according to the safety rules so as to ensure the same
safety level of the system the owmeter is going to be installed in.
Tab. 2

6
3 PRELIMINARY SETUP FOR USE
3.1 Access to "COST" setup menu
The right "constant" needs to be programmed in order to visualize the data on the display correctly.
WARNING: this data has already been entered in the production phase.
If the value measured by the owmeter is different from the actual sprayed value, the precise constant that needs
to be entered can be calculated by using the following formula:
[quantity measured by the device] x [constant indicated on the owmeter body]
[actual sprayed quantity]
Therefore, when the constant that is either calculated or shown on the label applied to the side of the owmeter
(g. 5) needs to be veried or calculated, access the "COST" menu by holding down the [RESET] button during
startup until the "COST" page is displayed:
• Flowmeter constant (1 ÷ 29999 - EU: cm/imp - US:inch/imp)
3.2 Setting the ow-meter constant
1) After having been turned ON, as shown in par. 3.1, the display alternately ashes the currently set value of the ow-meter constant and
the word "COST".
2) To modify the value, keep the keys pressed simultaneously until the "SET" screen appears.
3) Set the ow-meter constant using the [TOT] key to increase it and the [RESET] key to decrease it; keep the keys pressed to enable
quick-modication.
4) To conrm the setting, keep the keys pressed simultaneously until the "SAVE" screen appears.
The display alternately ashes the currently set ow-meter constant and the "COST" screen.
The display shows values greater than 9999 (pls/l - pls/gal) with the aid of graphic elements on the display as shown below:
When symbol " "is displayed, the constant value is to be
calculated as follows:
Constant = Displayed value + 10000
e.g.
2500 + 10000 = 12500
When symbol " " is displayed, the constant value is to be
calculated as follows:
Constant = Displayed value + 20000
e.g.
2500 + 20000 = 22500
3.3 Notes on programming
After having modied a parameter in the "OPT" Advanced menu, to return to the Main menu turn the device off and then on again.
When you are modifying a parameter or are in a Menu other than the Main menu and you do not press a key within 10 seconds, the display will
automatically return to the Main menu.
When modifying a numerical value, keep the key pressed to enable quick modication.

7
3.4 "OPT" Advanced menu
Upon installation of the owmeter in the lling system some settings are needed to properly display the lling
data:
• Operation mode
• Unit of measure
• Valve operation time
To access the Advanced menu, keep the key pressed while switching ON the device until the "OPT" screen
appears.
3.5 "MODE" Operation mode
It is possible to set three different operating modes:
MODE 0 = Tank lling count with pump stop control (0000 ÷ 9999 EU: l [predened setting] - US: Gal).
MODE 1 = Flowrate display.
MODE 2 = Tank lling count with pump stop control (0 ÷ 999,9 EU: l - US: Gal).
12 3 4
1) Press in succession to display the enabled operation mode; the value alternates with the message "MODE".
2) To modify the value, keep the keys pressed simultaneously until "SET" screen appears.
3) Press in succession to select the mode you wish to use.
4) To conrm the setting, keep the keys pressed simultaneously until "SAVE" screen appears.
The display alternatively ashes the set operation mode and "MODE" screen.
3.6 "UNIT" Unit of measure
It is possible to choose the units of measure for displaying data:
EU = Europa (l - l/min) [predened setting].
US = USA (Gal - Gpm).
123 4
1) Press in sequence to display the type of current unit of measure; the value alternates with the message "UNIT".
2) To modify the value, keep the keys pressed simultaneously until "SET" screen appears.
3) Press to select the unit of measure you wish to use.
4) To conrm the setting, keep the keys pressed simultaneously until "SAVE" screen appears.
The display alternatively ashes the set unit of measure and the "UNIT" screen.
3.7 "VAL" Valve operation time
This parameter lets you set the time it takes the valve installed on the system to complete its closing operation; setting this value the owmeter enables
to anticipate the exact moment in which closing begins, thus avoiding the introduction of a greater amount of product when the set value is reached.
VAL = 0 ÷ 20 sec.
12 3 4
+
1) Press in succession to display the "VAL" valve operation time.
2) To modify the value, keep the keys pressed simultaneously until "SET" screen appears.
3) Press to enter the operation time value using TOT key (increase) and RESET key (decrease); keep the keys pressed to enable quick
modication.
4) To conrm the setting, keep the keys pressed simultaneously until "SAVE" screen appears.
The display alternately ashes the set operation time and "VAL" screen.

8
4 USE
When using the system, the owmeter sends impulses to the computer, which, according to the constant value previously set, indicates the instant ow.
A LED in the connector slot indicates the status of the device (Fig. 6):
LED OFF:
the device is not powered.
LED ON NOT FLASHING with low light intensity:
the device is powered but it does not detect liquid passage.
LED ON FLASHING with high light intensity:
the device is powered and it detects liquid passage.
La frequenza dell'intermittenza è proporzionale alla portata.
Orion 2 Visual Flow owmeter can only detect conductive uids with a conductivity equal to 50 μS/cm (Ref. Tab. 4 - Par. 5.2).
- Do not aim pressurised water onto the equipment.
- Respect the device’s rated power requirement (12 Vdc).
- If arc welding is required, ensure that owmeter power is off and disconnect the power cables, if necessary.
- Use the owmeter only within the ow limits given in the “Technical data” table. Outside these limits, the owmeter could give incorrect
data and therefore lead the operator or the automatic system to make errors.
ARAG cannot be held responsible for damage caused to persons, animals or things by incorrect or unsuitable use of the owmeter or its parts.
4.1 Mode 0 - Mode 2 Use
4.1.1 Displaying data
The following parameters can be displayed during operation:
Total liquid introduced into the tank 0 ÷ 9999 (EU: l - US: Gal) - "Mode 0"
0 ÷ 999,9 (EU: l - US: Gal) - "Mode 2"
Instantaneous rate 0 ÷ 999,9 (EU: l/min - US: Gpm)
4.1.2 Setting the amount of liquid to load into the tank
In this operation mode the owmeter displays the total amount of liquid to load into the tank:
+
12 3 4
After having been turned on, the display shows the amount of liquid to load into the tank; to modify it, proceed as follows:
1) Press RESET key until "FILL" screen appears.
2) Set the amount of liquid to load into the tank using TOT key (increase) and RESET key (decrease); keep the keys pressed to
enable quick modication.
3) To conrm the setting, keep the keys pressed simultaneously until "SAVE" screen appears.
4) The set amount of liquid to load into the tank is displayed preceded by "TOT" screen.
Fig. 6

9
4.1.3 Mode 0 - Mode 2 Operation
12
34 5
1) After having been turned on, the display shows the amount of liquid to load into the tank.
2) To start the loading procedure, keep TOT key pressed until "STRT" screen appears; the amount of total liquid loaded into the tank is
displayed in real time.
3) Press TOT key to display the instantaneous rate of the liquid loaded into the tank, preceded by "LIT" (or "GAL") screen. Press the key
again to display the amount of liquid introduced into the tank.
4) When the set value has been reached, the display alternately ashes "END" screen and the total amount of liquid loaded into the tank.
If the Pump Stop Module is present, the lling device will automatically stop; otherwise, it should be stopped manually.
5) To complete tank lling, press RESET key: the display will go back to the beginning of the lling procedure, showing an amount of liquid
to load into the tank preceded by "TOT" screen.
4.1.4 Interrupting/Stopping before reaching the programmed amount
12 3 4
1) During the lling process, you can temporarily stop the pump (*) by pressing RESET key; "STRT" screen appears.
If the instantaneous quantity is displayed, "STRT" screen does not appear: in this case, press TOT key to display it.
2) To resume loading, press RESET key again.
3) To complete loading before reaching the set value, press the keys simultaneously until "END" screen appears.
4) The count will end and the display will show the programmed amount of liquid.
(*) The loading can be automatically started/stopped only if owmeter is connected to ARAG Pump Stop Module (code
4622BA50000.200). If not, the owmeter will not be able to start or stop the pump on its own and will work as a display only.
4.2 Mode 1 Operation
4.2.1 Displaying data
12 3 4
After having been turned on, the display shows the parameters read for Total liquid introduced into the tank and Instantaneous rate
using the previously set unit of measure (EU / US):
• Total liquid introduced into the tank = 0,00 ÷ 9999 (EU: l - US: Gal).
• Instantaneous rate = 0,0 ÷ 999,9 (EU: l/min - US: Gpm).
4.2.2 Resetting the liquid introduced into the tank counter
12 3
1) Access the total amount of liquid introduced into the tank display (Par. 4.1.2).
2) To reset the total amount of liquid introduced into the tank, keep RESET key pressed until "RST" screeen appears.
3) At this point the display will show "TOT" screen followed by the reset total quantity counter.

10
4.2.3 Reaching the full scale
12
1) The counter displays this screen when the full-scale value (9999 liters - Gal) is reached, and it therefore becomes necessary to reset the
counter.
2) To reset the count of the total amount of liquid introduced into the tank, keep RESET key pressed until "RST" screen appears.
5 MAINTENANCE
- After every spraying operation, ush the pipe with clean water.
- In case of malfunction, and at any rate at the end of every season, clean the owmeter pipe with a special detergent.
- Do not use metal or abrasive objects for cleaning the duct.
- Do not use solvents or petrol for cleaning the external parts of the device.
5.1 Troubleshooting
FAULT CAUSE REMEDY
The owmeter does not read any value No power supply • Check the owmeter wiring.
The value read by the owmeter is not
linear or stable Presence of turbulence or air in the circuit • Check the circuit.
The owmeter shows incorrect data
Incorrect programming • Check programming concerning the
displayed data.
Problems with the sensors • Contact the nearest Assistance Centre.
Problems with the owmeter
The owmeter shows the message Endscale value has been
reached
• Reset the display following the
procedure described in the section on the
displayed value. Tab. 3

11
5.2 Technical data
Power supply 10 ÷ 16 Vdc
Max. absorption 300 mA
Min. liquid conductivity 50 μS/cm
Working temperature 0 °C ÷ 60 °C
32 °F ÷ 140 °F
Storage temperature -30 °C ÷ 80 °C
-22 °F ÷ 176 °F
Material Nylon / Brass / Polypropylene /
Stainless Steel Inox
Dimensions (mm) 185÷234 (depending on the model) x 117 x 169
Weight 906 ÷ 1670 g (depending on the model)
CODE Thread Internal
passages Pulses
lt/1’ US GPM bar PSI bar PSI BSP mm pls/l pls/GAL
46212AG1313 0,3÷6 0.08÷1.6 20 290 0,3 4 G 3/4 4 6000 22710
46212AG3333 0,3÷6 0.08÷1.6 40 580 0,3 4 G 3/4 4 6000 22710
46212A01313 0,5÷10 0.13÷2.6 20 290 0,3 4 G 3/4 5 6000 22710
46212A03333 0,5÷10 0.13÷2.6 40 580 0,3 4 G 3/4 5 6000 22710
46212A11313 1÷20 0.3÷5 20 290 0,3 4 G 3/4 7 3000 11355
46212A13333 1÷20 0.3÷5 40 580 0,3 4 G 3/4 7 3000 11355
46212A21313 2,5÷50 0.6÷13 20 290 0,5 7 G 3/4 10 1200 4542
46212A23333 2,5÷50 0.6÷13 40 580 0,5 7 G 3/4 10 1200 4542
46212A31414 5÷100 1.3÷26 20 290 0,5 7 G 1 14 600 2271
46212A33434 5÷100 1.3÷26 40 580 0,5 7 G 1 14 600 2271
46212A41414 10÷200 2.6÷53 20 290 0,5 7 G 1 18,5 300 113 5
46212A43434 10÷200 2.6÷53 40 580 0,5 7 G 1 18,5 300 113 5
46212A41515 10÷200 2.6÷53 20 290 0,5 7 G 1 1/4 18,5 300 113 5
46222A51616 20÷400 5÷106 20 290 0,2 3 G 1 1/2 28 150 568
46222A61616 30÷600 8÷158 20 290 0,5 7 G 1 1/2 28 100 378
46222A61717 30÷600 8÷158 20 290 0,5 7 G 2 28 100 378
46222A71717 40÷800 11÷211 20 290 0,5 7 G 2 28 75 284
Tab. 4

12
6 GUARANTEE TERMS
1. ARAG s.r.l. guarantees this apparatus for a period of 360 day (1 year) from the date of sale to the client user (date of the goods delivery note).
The components of the apparatus, that in the unappealable opinion of ARAG are faulty due to an original defect in the material or production
process, will be repaired or replaced free of charge at the nearest Assistance Centre operating at the moment the request for intervention is made.
The following costs are excluded:
- disassembly and reassembly of the apparatus from the original system;
- transport of the apparatus to the Assistance Centre.
2. The following are not covered by the guarantee:
- damage caused by transport (scratches, dints and similar);
- damage due to incorrect installation or to faults originating from insufficient or inadequate characteristics of the electrical system, or to alterations
resulting from environmental, climatic or other conditions;
- damage due to the use of unsuitable chemical products, for spraying, watering, weedkilling or any other crop treatment, that may damage the
apparatus;
- malfunctioning caused by negligence, mishandling, lack of know how, repairs or modications carried out by unauthorised personnel;
- incorrect installation and regulation;
- damage or malfunction caused by the lack of ordinary maintenance, such as cleaning of lters, nozzles, etc.;
- anything that can be considered to be normal wear and tear.
3. Repairing the apparatus will be carried out within time limits compatible with the organisational needs of the Assistance Centre.
No guarantee conditions will be recognised for those units or components that have not been previously washed and cleaned to remove residue of
the products used.
4. Repairs carried out under guarantee are guaranteed for one year (360 days) from the replacement or repair date.
5. ARAG will not recognise any further expressed or intended guarantees, apart from those listed here.
No representative or retailer is authorised to take on any other responsibility relative to ARAG products.
The period of the guarantees recognised by law, including the commercial guarantees and allowances for special purposes are limited, in length of
time, to the validities given here. In no case will ARAG recognise loss of prots, either direct, indirect, special or subsequent to any damage.
6. The parts replaced under guarantee remain the property of ARAG.
7. All safety information present in the sales documents regarding limits in use, performance and product characteristics must be transferred to the
end user as a responsibility of the purchaser.
8. Any controversy must be presented to the Reggio Emilia Law Court.
7 DISPOSAL AT THE END OF SERVICE
Dispose of the system in compliance with the established legislation in the country of use.
8 CONFORMITY DECLARATION
The declaration of conformity is available at www.aragnet.com, in the relevant section.

Note
13

D20345_GB-m01 11/2017
Via Palladio, 5/A
42048 RUBIERA (Reggio Emilia) - ITALY
Tel. +39 0522 622011
Fax +39 0522 628944
www.aragnet.com
info@aragnet.com
Only use genuine ARAG accessories or spare parts to make sure manufacturer guaranteed safety conditions
are maintained in time. Always refer to the internet address www.aragnet.com
This manual suits for next models
18
Table of contents
Other ARAG Measuring Instrument manuals

ARAG
ARAG DigiWOLF 4627 Series Quick start guide

ARAG
ARAG DigiWOLF 4628405 User manual

ARAG
ARAG 853 Series Service manual
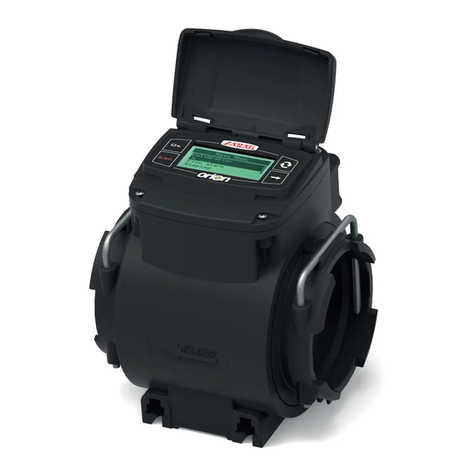
ARAG
ARAG orionX Quick start guide
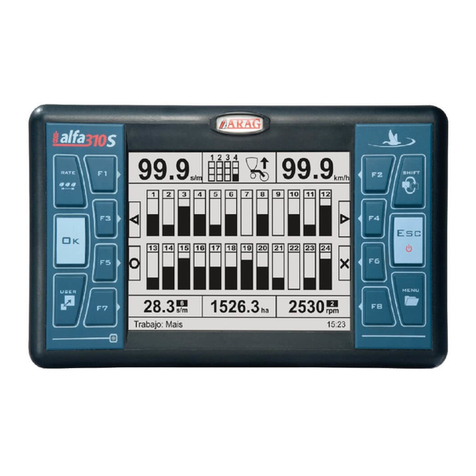
ARAG
ARAG alfa 310S User manual
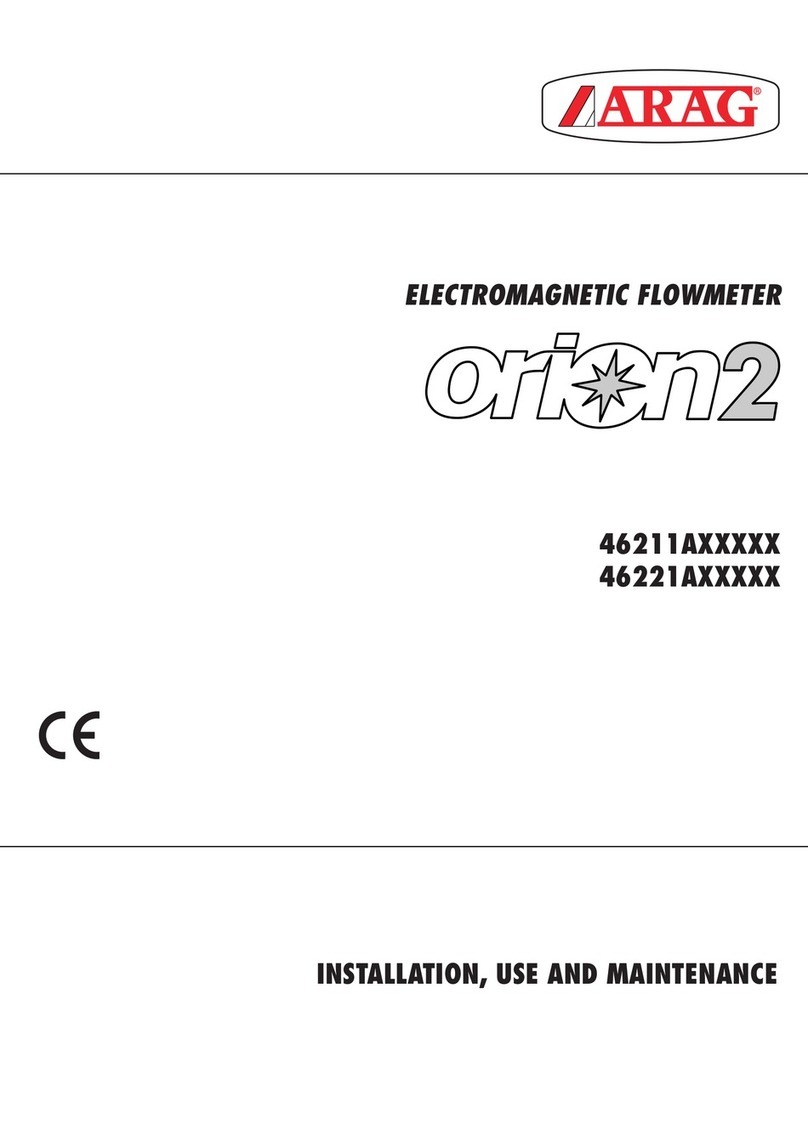
ARAG
ARAG Orion 2 46211A Series Quick start guide

ARAG
ARAG orion 462A Series Quick start guide
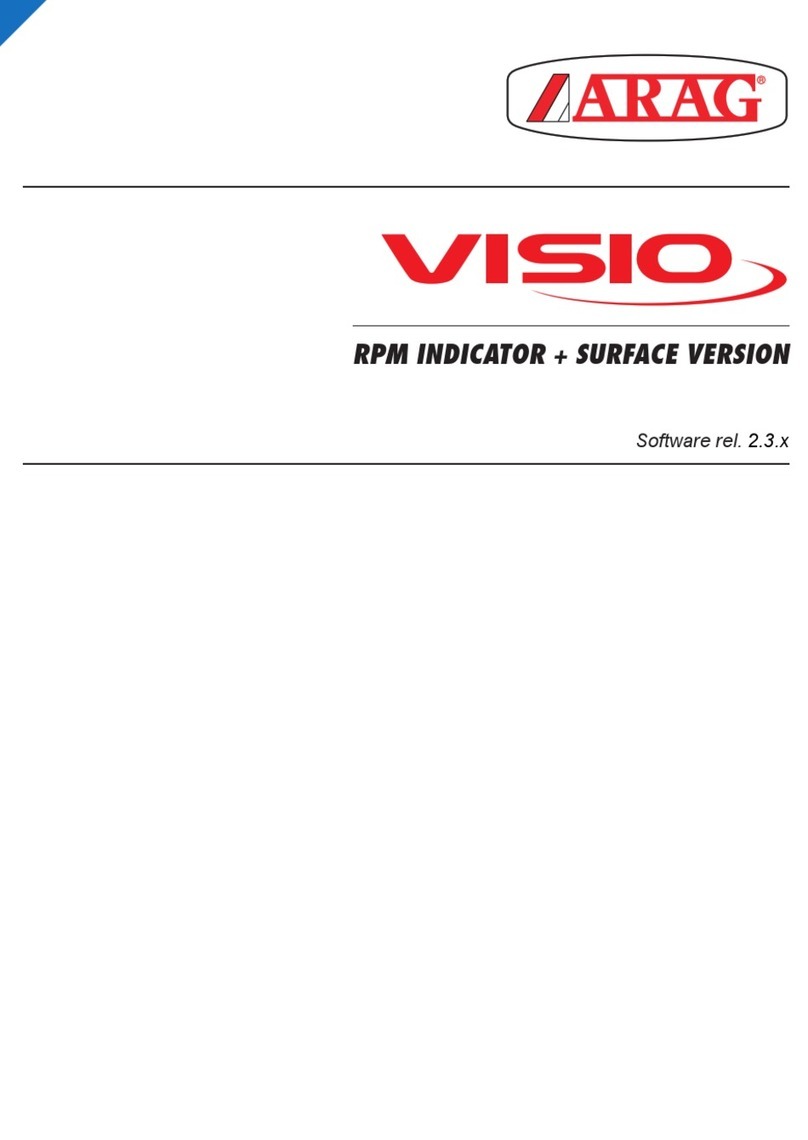
ARAG
ARAG Visio User manual

ARAG
ARAG Orion Quick start guide