ARC Flex Series User manual

FLEX8ES
User’s Manual
FCC Version

Page 1
Table of Contents
Page
1. Introduction 3
2. Radio Controlled Safety 4
3. General System Information
A. Transmitter Handset
1. External Illustration (Standard Push Button Configuration) 5
2. InternalIllustration 6
B. Receiver Unit
1. ExternalIllustration 7
2. InternalIllustration 8
4. Function Settings
A. Transmitter Handset
1. SystemChannelSettings 9
2. Push Button Functions with LED Displays
a. Standard Push Button Configuration (Transmitter Toggle) 10
b. Standard Push Button Configuration (A/B Selector) 11
c. Inline Push Button Configuration (Transmitter Toggle) 12
d. Inline Push Button Configuration (A/B Selector) 13
3. Channel Change via Push Buttons 14
4. Program4-digitSecurityCode 15
5. I-Chip 16
B. Receiver Unit
1. SystemChannelSettings 17
2. Auxiliary Functions
a.ON/OFFPushButtonFunction 18
b. Magnet ON/OFF Push Button Function 18
c.ExternalWarningFunction 18
d. Auxiliary STOP Push Button Function 18
e.MomentaryContact 18
f.ToggledContact 19
g. Pitch & Catch Function 19
3. Receiver Auto-Scanning Settings 19

Page 2
4. Dip-switch Settings
a. Interlocked Functions 20
b. Non-interlocked Functions 21
5. Jumpers Settings 22
6. I-Chip Programming Port 23
7. Voltage Settings 23
5. SystemChannelsTable 24
6. Receiver Installation
A.OutputRelayContactDiagram 25
B.Pre-InstallationPrecautions 26
C. Step-By-StepInstallation 26~27
D. SystemTesting 27
7. Operating Procedure
A. Transmitter Operation
1. General Operating Procedure 28~29
2. A/B Selector Push Button Operating Procedure 29
3. Pitch & Catch Operating Procedure 29
4. Automatic Channel Scanning Operating Procedure 30
5. Changing Transmitter Batteries 30
B. Status Light Indicators & Warnings
1. Transmitter STATUS Light Indication 31
2. Receiver STATUS Light Indication 32
3. Receiver SQ Light Indication 32
4. Receiver POWER Light Indication 32
5. Receiver COM Light Indication 32
C. TroubleShootingTips 33
8. SystemSpecifications 34
9. SpareParts 35
10. EU Declaration of Conformity 36

Page 3
1. Introduction
The FLEX radio remote control systems are designed for control of industrial equipment and machinery
such as overhead traveling cranes, jib cranes, gantry cranes, tower cranes, electric hoists, winches, monorails,
conveyor belts, mining equipment and other material handling equipment where wireless control is preferred.
Each FLEX system consists of a transmitter handset and receiver unit. Other standard-equipped
accessories include transmitter waist belt, spare transmitter power key, clear vinyl pouch, “AA” alkaline
batteries, compass direction decal sheet and user’s manual.
List of notable features include:
* 62 user-programmable channels – Advanced synthesized RF controls with 62 built-in channels, no
more fixed channel and fragile quartz crystals to break.
* Automatic channel scanning receiver – No more hassle of climbing up the crane to change receiver
channels.
* Over one million unique ID codes (20bit) – Each and every Flex system has its own unique ID codes
and serial number, never repeats.
* Advanced controls – The Flex system utilizes advanced microprocessor controls with 32bit CRC and
Hamming Code, which provide ultra fast, safe, precise, and error-free encoding and decoding.
* Unique I-CHIP design – The I-CHIP functions in a way that is very similar to SIM card used on
mobile phones, with the ability to transfer system information and settings from one transmitter to
another without the hassle of resetting the spares.
* Reliable push buttons – The in-house designed push buttons with gold-plated contacts are rated for
more than one million press cycles.
* Low power consumption – Requires only two “AA” Alkaline batteries for more than 150 hours of
operating time between replacements.
* Ultra-durable nylon and fiberglass composite enclosures – Highly resistance to breakage and
deformation even in the most abusive environments.
* Full compliance – All systems are fully complied with the FCC Part-15 Rules, European Directives
(Safety, EMC, R&TTE, Machinery) and Industry Canada Specifications (IC).

Page 4
2. Radio Controlled Safety
Flex radio remote control system should be operated by persons with sufficient amount of knowledge
and skill in crane operation and safety. Persons being trained to operate a radio remote controlled crane
should possess the knowledge of all hazards peculiar to radio remote controlled crane operation, ability to
judge distance and moving objects, equipment capacity and radio remote controlled safety rules. Radio
remote controlled cranes should not be operated by any person with insufficient eyesight, hearing, illness,
and under influence of drugs and medications that may cause loss of crane control.
Below are some general operating safety tips that should be strictly followed when operating a radio
remote controlled crane.
1. Prior to crane operation always check the transmitter handset for any damage that might inhibit proper
crane operation.
2. Always check if the red emergency stop button is working properly prior to crane operation.
3. Check the Status LED on the transmitter for any signs of low battery power (refer to page 31).
4. Check the Status LED on the transmitter for any signs of irregularities (refer to page 31).
5. The crane limit switches should be checked prior to crane operation or at the beginning of each shift.
When checking limit switches the hoist should be centered over an area free of personnel and
equipment.
6. If the power to the crane is removed, the operator should turn off the transmitter power immediately
until the power to the crane is restored.
7. If the crane fails to respond properly to operator’s command the operator should stop operation, turn
the transmitter power off, and then report the condition to their supervisor.
8. The transmitter power should be turned off after each use. If the transmitter handset is not in use
always turn the power off and stored it in a safe or designated location. Never leave the transmitter
handset unattended in the working area.
9. Make sure the system is not set to the same channel as any other Flex systems in use within a distance
of 300 meters (900 feet).
10. Never operate a crane or equipment with two transmitter handsets at the same time unless they are
programmed with “Pitch & Catch” function. For information on the “Pitch & Catch” feature, please
refer to page 19 and page 29 of this manual.

Page 5
3. General System Information
A. TRANSMITTER HANDSET
1. External Illustration (Standard Push Button Configuration)
(Fig.01) (Fig.02)
1. Emergency Stop Button 9. Push Button #5
2. Removable Power Key Switch 10. Push Button #7
3.PushButton#2 11.StrapRing
4.PushButton#4 12.SystemInformation
5.PushButton#6 13.SystemChannel
6.PushButton#8 14.CraneNumber
7.PushButton#1 15.BatteryCover
8. Push Button #3 16. Approval Information

Page 6
2. Internal Illustration
(Fig.03) (Fig.04)
1.EncoderBoard 6.I-CHIP
2. Arial Antenna 7. Function Dip-Switch
3. Transmitting Module 8. Channel Dip-Switch
4. Status LED Display 9. Battery Contact Mechanism
5.Function LED Displays

Page 7
B. RECEIVER UNIT
1. External Illustration
(Fig.05)
1. Shock Mount 6. COM LED Display
2. External Antenna Jack 7. Output Contact Diagram
3. Power LED Display 8. System Information
4. Status LED Display 9. Cord Grip
5.SQLEDDisplay

Page 8
2
3
4
1
5
2. Internal Illustration
(Fig. 06)
1. AC Line Filter 4. Decoder Module
2. Power Transformer 5. Output Relay Board
3. Receiving Module

Page 9
71423 56 8
CHANNEL
71 423 56 8
4. Function Settings
A. TRANSMITTER HANDSET
1. System Channel Settings
(Fig. 07)
Set the transmitter channel by adjusting the channel dip-switch located on the backside of the
transmitter encoder board (refer to Fig. 07 above). Only the first six (6) positions are used for channel
programming (refer to Fig. 08 below). The system channels table located on page 24 illustrates which
dip-switch setting corresponds to which channel. Once the transmitter channel is altered do make sure
to change receiver channel as well. The channel on both transmitter and receiver must be identical in
order for system to work. To change receiver channel please refer to page 17.
Example: Top slot →“1”
(Fig.08) Bottom slot →“0”
The above dip-switch setting “1 0 0 1 0 0” corresponds to “channel 36” in the system channels table
on page 24.

Page 10
52134 867
FUNCTION
LED 1LED 2LED 3LED 4
2. Push Button Functions with LED Displays
A. Standard Push Button Configuration (Transmitter Toggle)
Set transmitter toggle (latching output relay) function by adjusting the 8-position function
dip-switch located on the backside of the transmitter encoder board (refer to Fig. 09 below).
The LED 1 through LED 4 shown inside the shaded box (see below) illustrates which LED on
the transmitter will light up when the designated push button (PB5 ~ PB8) is pressed.
(Fig.09)
DIP PB5 PB6 PB7 PB8
1 00000000 Normal Normal Normal Normal
2 00000101 Normal Normal Normal LED 4
3 00000110 Normal Normal LED 3 LED 4
4 00000111 Normal LED 2 LED 3 LED 4
5 00001000 LED 1 LED 2 LED 3 LED 4
* PB5…PB8 →Push button number
* Normal →Normal momentary contact
* LED 1…LED 4 →Transmitter toggled with designated LED Display

Page 11
B. Standard Push Button Configuration (A/B Selector)
There are four (4) different types of A/B selector sequence available on the Flex system.
Choose the one that is most suitable for your application.
Type-A selector sequence : A →B →A →B …
Type-B selector sequence : Off →A →B →Off →A →B …
Type-C selector sequence : A →B →A+B →A →B →A+B …
Type-D selector sequence : Off →A →B →A+B →Off →A →B →A+B …
DIP PB5 PB6 PB7 PB8
6 00101111 Normal Normal A/1&2 Normal
7 00110000 Normal Normal B/1&2 Normal
8 00110001 Normal Normal C/1&2 Normal
9 00110010 Normal Normal D/1&2 Normal
10 00110011 Normal Normal Normal A/3&4
11 00110100 Normal Normal Normal B/3&4
12 00110101 Normal Normal Normal C/3&4
13 00110110 Normal Normal Normal D/3&4
14 00110111 Normal Normal A/1&2 A/3&4
15 00111000 Normal Normal A/1&2 B/3&4
16 00111001 Normal Normal A/1&2 C/3&4
17 00111010 Normal Normal A/1&2 D/3&4
18 00111011 Normal Normal B/1&2 B/3&4
19 00111100 Normal Normal B/1&2 C/3&4
20 00111101 Normal Normal B/1&2 D/3&4
21 00111110 Normal Normal C/1&2 C/3&4
22 00111111 Normal Normal C/1&2 D/3&4
23 01000000 Normal Normal D/1&2 D/3&4
* PB5…PB8 →Push button number
* Normal →Normal momentary contact
* A/1&2…D/3&4 →A/B Selector type with designated LED Display (LED 1&2 or LED 3&4)

Page 12
C. Inline Push Button Configuration (Transmitter Toggle)
The push button arrangement for inline push button setup starts from top to bottom and then
from right column to left column (refer to Fig. 10 below). To set inline push button
configuration please refer to JP4 and JP5 jumpers setting on page 22. With inline push
buttons configuration, PB1 & PB2 still corresponds to output relay K1~K2, PB3 & PB4
corresponds to relay K5~K6, etc…
(Fig. 10)
DIP PB5 PB6 PB7 PB8
24 00000000 Normal Normal Normal Normal
25 00000101 Normal Normal Normal LED 4
26 00010100 Normal Normal LED 3 LED 4
27 00010101 Normal LED 2 LED 3 LED 4
28 00010110 LED 1 LED 2 LED 3 LED 4
* PB5…PB8 →Push button number
* Normal →Normal momentary contact
* LED 1…LED 4 →Transmitter toggled with designated LED Display

Page 13
D. Inline Push Button Configuration (A/B Selector)
There are four (4) different types of A/B selector sequence available on the Flex system.
Choose the one that is most suitable for your application.
Type-A selector sequence : A →B →A →B …
Type-B selector sequence : Off →A →B →Off →A →B …
Type-C selector sequence : A →B →A+B →A →B →A+B …
Type-D selector sequence : Off →A →B →A+B →Off →A →B →A+B …
DIP PB5 PB6 PB7 PB8
29 01110011 Normal Normal A/1&2 Normal
30 01110100 Normal Normal B/1&2 Normal
31 01110101 Normal Normal C/1&2 Normal
32 01110110 Normal Normal D/1&2 Normal
33 00110011 Normal Normal Normal A/3&4
34 00110100 Normal Normal Normal B/3&4
35 00110101 Normal Normal Normal C/3&4
36 00110110 Normal Normal Normal D/3&4
37 01110111 Normal Normal A/1&2 A/3&4
38 01111000 Normal Normal A/1&2 B/3&4
39 01111001 Normal Normal A/1&2 C/3&4
40 01111010 Normal Normal A/1&2 D/3&4
41 01111011 Normal Normal B/1&2 B/3&4
42 01111100 Normal Normal B/1&2 C/3&4
43 01111101 Normal Normal B/1&2 D/3&4
44 01111110 Normal Normal C/1&2 C/3&4
45 01111111 Normal Normal C/1&2 D/3&4
46 10000000 Normal Normal D/1&2 D/3&4
* PB5…PB8 →Push button number
* Normal →Normal momentary contact
* A/1&2…D/3&4 →A/B Selector type with designated LED Display (LED 1&2 or LED 3&4)

Page 14
3. Channel Change via Push Buttons
Other than CHANNEL dip-switch on the encoder board, the transmitter channel can also be changed
directly on the push buttons. Please refer to the instruction below on how to change transmitter
channel via push buttons.
a. Press and hold PB1, PB2 and PB3 and rotate the power key to START position at the same time.
A series of green and red blinks will appear on the Status LED showing the current channel
setting. A green blink represents the tens (+10) and a red blink represents the units (+1).
Examples: 2 green blinks followed by 5 red blinks represents channel 25.
6 red blinks represents channel 06.
+
b. Select new channel by pressing PB1 and PB2 on the transmitter. Press PB1 to increment the
units (+1) and PB2 to increment the tens (+10).
Examples: Press PB2 two times and then PB1 four times will give you channel 24.
Press PB1 nine times with give you channel 09.
c. When finished, the newly selected channel will appear on the Status LED via series of green and
red blinks again.
d. Exit the channel programming by turning off the transmitter power.
e. Make sure the receiver channel is set identical to the transmitter. Please refer to page 17 and
page 30 on how to change receiver channel.
f. Please note that when the CHANNEL dip-switch inside the transmitter is changed, the priority
will revert back to the new channel set on the CHANNEL dip-switch.
g. Please note that when channel is set beyond channel 62 via PB1 and PB2 (i.e. channel 63, 68, 88,
etc…), the system will recognize it as channel 62.

Page 15
4. Program 4-digit Security Code
Prior to rotating the transmitter power key-switch to START position to begin operation, you must first
enter a 4-digit security code in order to proceed further. When this 4-digit security code is input
correctly, a green light will appear on the Status LED. Please refer to the instruction below on how to
program the 4-digit security code.
a. Press and hold PB1, PB2, PB3 and PB4 and rotate the power key to START position at the same
time.
+
b. A constant orange light will appear on the Status LED telling you that you are in the security
code programming mode.
c. For newly purchased system with the security code function deactivated (default setting), press
PB1 four times (1111) to activate the security code function. At this time the Status LED on the
transmitter will blink orange slowly telling you that the 4 digits entered is correct. Then select
your own 4-digit security code by pressing PB1, PB2, PB3 or PB4 on the transmitter (four
presses randomly). At this time a fast orange blinks is displayed on the Status LED telling you to
reconfirm the 4-digit security code you have just entered. A green light will appear once you
have re-entered the same 4-digit security code again (programming completed). If red light is
shown on the Status LED after you have re-entered the security code (incorrect input), then you
must reset the transmitter power and then repeat step a, b and c again.
Steps: Press and hold PB1~PB4 and rotate power key to START position →constant orange →
press PB1 four times (for new systems) or 4-digit security code →slow orange blinks →enter
the new 4-digit security code →fast orange blinks →re-enter the same 4-didgit security code
again →green light.
d. If you wish to cancel the security code function, then repeat a, b, c above and press PB1 four
times as your new security code (security code function disabled).
e. If you do not remember the 4-digit security code, then you must contact your dealer or
distributor for further assistance.

Page 16
5. I-Chip
I-CHIP functioned in a way that is very similar to a SIM card inside a mobile phone, which stores
information such as your phone number, account number, phone book and other settings. I-CHIP
works exactly the same way, as it stores information such as system serial number/ID code, channel
and push button configurations.
When replacing a transmitter handset, just take the I-CHIP out of the old transmitter and install it into
the new one (refer to Fig. 11 below). The new transmitter handset will then operate according to the
information stored in the I-CHIP unless the settings on both Channel and Function dip-switch are
changed thereafter. Basically the microprocessor will operate according to the last setting change
either on I-CHIP or the dip-switches.
For safety purposes, system serial number/ID code stored inside the I-CHIP can not be changed
directly on the transmitter encoder board. Only channels and push button configurations can be
changed directly on the encoder board via Channel and Function dip-switches. There are only two
ways that you can change transmitter serial number/ID code; 1) via I-CHIP programming port located
on the decoder module inside the receiver unit, please refer to page 23 on how to program the I-CHIP
(serial number/ID code) via receiver unit; 2) via an external I-CHIP programmer or duplicator unit
available from the factory. Please ask your local dealers for assistance if your system requires serial
number/ID code adjustments.
(Fig. 11)

Page 17
71 423 56 8
INTEXT 123 56 847
B. RECEIVER UNIT
1. System Channel Settings
(Fig. 12)
Even though Flex system is equipped with automatic channel scanning receiver, the user can also set
the receiver channel manually. Please refer to page 30 on how automatic channel scanning receiver
works.
Set the receiver channel by adjusting the channel dip-switch located on the receiver module (refer to
Fig. 12 above), only the first six (6) positions are used for channel programming (refer to Fig. 13
below). The system channels table located on page 24 illustrates which dip-switch setting corresponds
to which channel. Once the receiver channel is altered do make sure to change transmitter channel as
well. The channel on both transmitter and receiver must be identical in order for system to work. To
change transmitter channel please refer to page 9.
Example: Top slot →“1”
(Fig.13) Bottom slot →“0”
The above dip-switch setting “1 0 0 1 0 0” corresponds to “channel 36” in the system channels table
on page 24.

Page 18
ON
OFF
OFF
Aux
STOP
2. Auxiliary Functions
a. ON/OFF Push Button Function
The user can set any of the two adjacent push buttons on the transmitter to behave like a
mechanical ON & OFF rocker switch (refer to page 20 on how to set to this function).
When “On” output relay is closed (“On” push button pressed), the “Off” output relay will
open automatically, or vise versa.
b. Magnet ON/OFF Push Button Function
The user can set any of the two adjacent push buttons on the transmitter to control a magnet.
To activate the magnet just press the push button with the Magnet symbol. To deactivate the
magnet, for safety purpose, you must first press and hold the Magnet push button and then
press the OFF push button. Press the OFF push button by itself can not deactivate the magnet
(refer to page 20 on how to set to this function).
c. External Warning Function
The user can install an external warning device (rotating lights, horn, etc…) to a special
“Function output relay” located inside the receiver. The user can choose which push button
pairs or crane motions he desired to have external warnings when push button is pressed
(refer to page 20 on how to set to this function).
d. Auxiliary STOPPush Button Function
The auxiliary STOP function acts as a 2nd emergency stop button. Other than by emergency
stop button and transmitter power key switch, the receiver MAIN is also deactivated when
this auxiliary stop push button is pressed (refer to page 21 on how to set to this function).
e. Momentary Contact
When push button is released the output relay corresponds to that push button will open (refer
to page 21 on how to set to this function). This type of contact is usually applies to external
application such as horns or buzzers.

Page 19
41 32 65 87
4132 65 87
42317856
41 2 3 65 78
f. Toggled Contact
When push button is released the output relay corresponds to that push button will remained
closed (maintained contact) until next time the user presses the same push button again (refer
to page 21 on how to set to this function). This type of contact is usually applies to external
application such as lights.
g. Pitch & Catch Function
This function allows two operators controlling one crane from opposite ends of a cross or long
travel (refer to page 21 on how to set to this function). When set to “Pitch & Catch” make sure
the 2nd transmitter is set to the next upper channel (channel X*+1). For example, if the system is
preset at “Ch.01” then the channel of the 2nd transmitter should be set to “Ch.02”. Furthermore,
the dip-switch position #7 and #8 on the receiving module should be set to “10”, this will allow
the receiver to scan only Ch.01 and Ch.02 (please refer to the illustration below). On the other
hand, since there are only 62 available channels on the Flex system, the system preset at channel
62 is ineffective because the 2nd transmitter can not be set to Ch.63. If your system is preset at
Ch.62 do make sure to change it to another channel.
3. ReceiverAuto-Scanning Settings
Receiver Channel Dip-switch
↓
(1) →Scanning all 62 channels (manufacture preset)
For standard operation
(2) →Single fixed channel (channel X*)
Auto scanning function disabled
(3) →Scanning 2 channels only (channel X*, channel X*+1)
For Pitch & Catch, Tandem, and Random Access operation with 2 receivers
(4) →Scanning 3 channels only (channel X*, channel X*+1, channel X*+2)
For Random Access operation with 3 receivers
* Channel X →Channel set on the receiving module
Example: If the first 6 dip-switch positions on the receiving module is set to Ch.01 (“000000” or
“000001”), when set to 2-channel scanning (type-3 above), then the receiver will only
scan Ch.01 and Ch.02.
This manual suits for next models
6
Table of contents
Other ARC Remote Control manuals
Popular Remote Control manuals by other brands
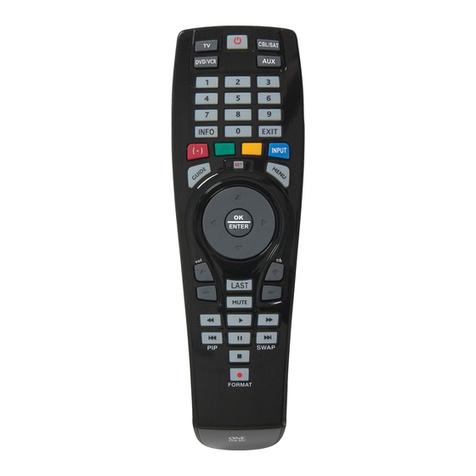
One Forall
One Forall OARC04G user guide
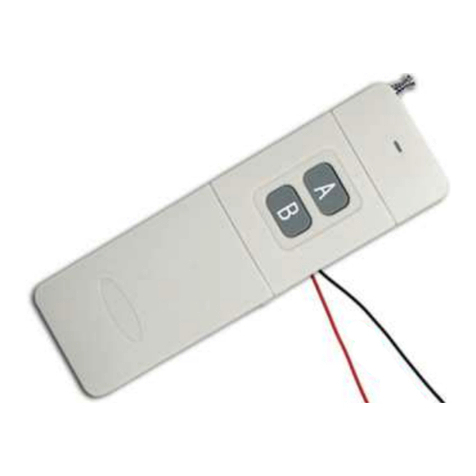
SHENZHEN GUIYUAN INDUSTRY DEVELOPMENT
SHENZHEN GUIYUAN INDUSTRY DEVELOPMENT 0021044 quick start guide
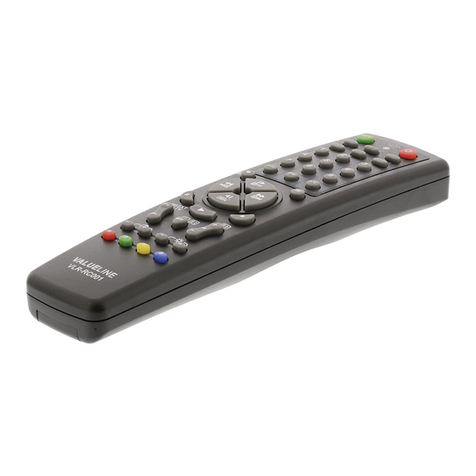
Basic XL
Basic XL BXL-RC001 manual
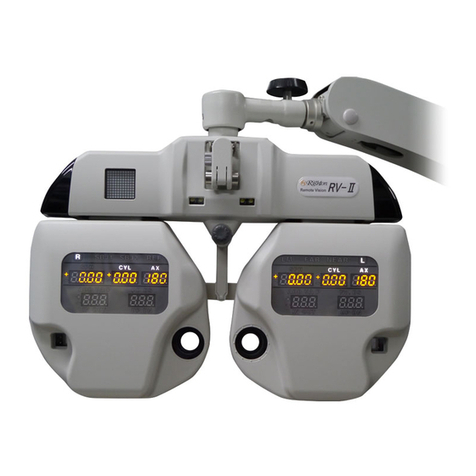
Right On
Right On RVII quick reference
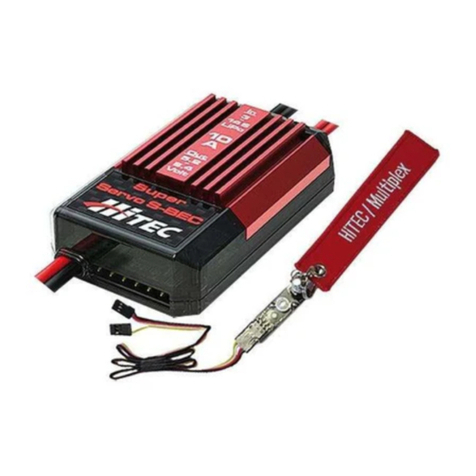
Hi-Tec
Hi-Tec Super Servo S-BEC instruction manual
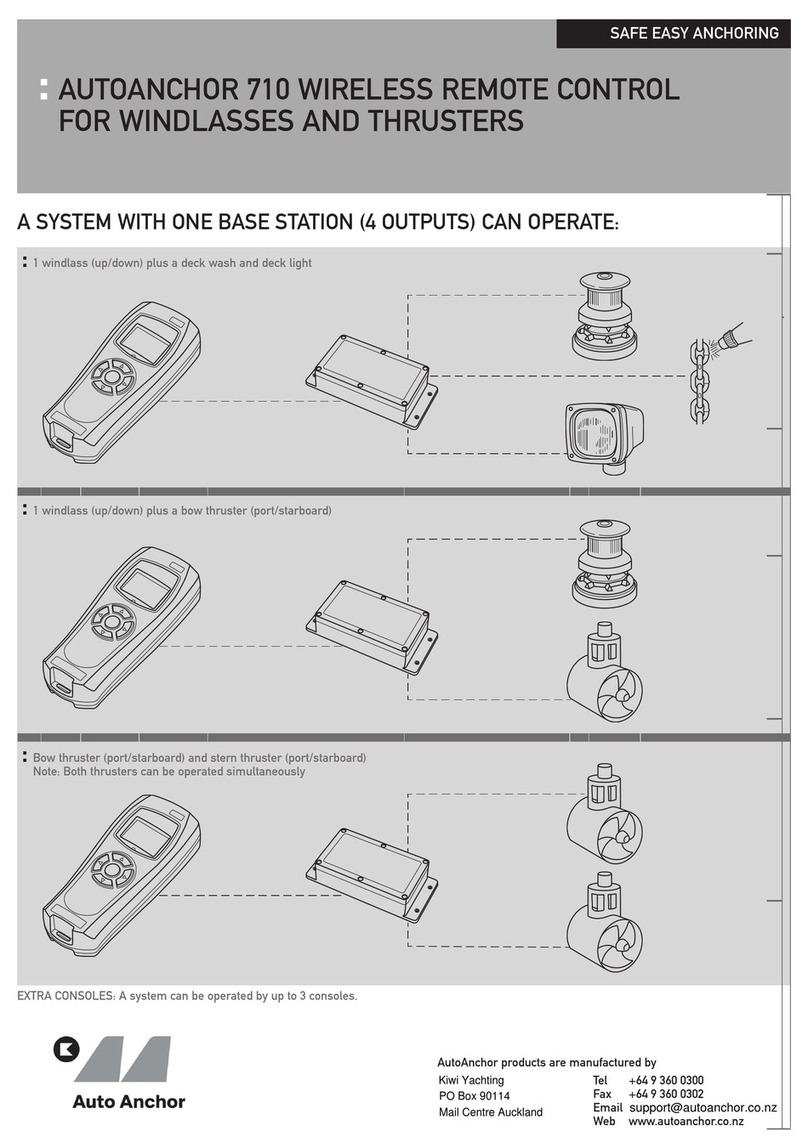
Auto Anchor
Auto Anchor AutoAnchor 710 manual